Ohkura EC5500R User manual

EC5500R
Digital Indicating Controller
Instruction Manual
WXPEC5500R01E
JLY 2005 (1st edition)
All Rights Reserved, Copyright © 2005, Ohkura Electric Co., Ltd.
DRAFT

−1−
For Safety Using
Thank you for purchasing our EC5500R Digital Indicating Controller. For
proper and effective use of full functions of this instrument, please read and
understand this instruction manual well before use.
The following symbol marks are used in this instrument and the instruction
manual for safety using.
Safety Precautions
Warning It is clearly described when dangerous situation for causing
death or serious injury of the user is expected in case of
mishandling.
Caution It is clearly described when dangerous situation for causing
light injury of the user or object damage is expected in case
of mishandling.
Indicate “Caution in handling.” It is described at points were
the instruction manual needs to be reffered for protection of
the user and e
q
ui
p
ment.
Indicate “Protective grounding terminal.” Be sure to provide
grounding before operating the instrument.
Indicate “Caution for electric shock.” It is described at points
where electric shock may occur if instruction is neglected.
To ensure safety in handling the instrument, please be sure to observe the
following warnings/cautions as well as the precautions in this manual.
Warning
To prevent an electric shock, be sure to disconnect this
instrument from the main power supply when wiring it.
(1) To prevent an electric shock, be sure to provide
protective grounding before providing power supply to
this instrument.
(2) Do not cut off the protective grounding conductor or
disconnect protective grounding.
Check that the power supply voltage of this instrument
matches that of the supply source.
Do not operate this instrument in atmosphere containing
inflammable, explosive or corrosive gas, or in environments
where water or steam may be splashed on the product.
To prevent electric shock, be sure to provide wiring after
turning off the power.
General
Protective
grounding
Powe
r
supply
Environment
Input/output
wirin
g

−2−
Caution
Do not use open terminals for other purposes such as relay.
Do not disassemble the inside of the main unit.
[Caution]
(1) Please deliver this instruction manual to the final user.
(2) Be sure to read this instruction manual before handling the
instrument.
(3) If you find any questions, errors or omissions, please
inform our sales personnel.
(4) When you have read this instruction manual, store it safely
near the instrument.
(5) If it is lost, stained or damaged by accident, please inform
our dealer where you purchased the instrument or our sales
representative.
(6) It is forbidden to reprint or copy all or part of this instruction
manual without permission.
It is prohibited to remove or disassemble the unit, printed
circuit board, etc. by anyone except our service personnel
and persons with our approval.
To dispose of this instrument, consign to the special agent as
an industrial waste.
(1) Clean the surface of this instrument with a dry cloth.
(2) Do not use organic solvents.
(3) Cleaning the instrument after turning off the power.
This instruction manual may be revised without prior notice.
(For questions about industrial measuring instruments)
For questions about product handling and maintenance:
0120-17-0096
Input/output
Inside of
instrument
Instruction
manual
Maintenanc
Disposal
Cleaning
Revisions
Toll free
numbe
r

−3−
How to Use This Instruction Manual
This instruction manual consists of “For safety using”, “Table of Contents,”
and “Chapters 1 to 10” as follows. Read the applicable pages to suit your
purpose:
Chapter and title
At purchase
and
installation
In daily
operation
In maintenance
and
troubleshooting
For safety using (pages 1 and 2) ◎◎ ◎
Chapter 1 When Product Arrives ◎
Chapter 2 Installation ◎○
Chapter 3 Wiring ◎○
Chapter 4 Part Names ○○
Chapter 5 Basic Operation and
Setting ○○
Chapter 6 Operation Guidance ○
Chapter 7 List of Items ○
Chapter 8 Operation ○
Chapter 9 Procedure for Major
Functions ○
Chapter 10 Troubleshooting ◎
◎:Be sure to read the chapter ○:Read if necessary.
Type of Instruction Manual
Name Description
1
EC5500R Digital Indicating
Controller Instruction Manual
WXPEC5500R01E
Describes the general
information on EC5500R
including installation, wiring,
operation and functions.
2
RS-232C/RS-422A/RS-485
Interface Instruction Manual
WXPEC5500R02E
Describes the setup,
communication protocol, etc. for
using communication.
3
AO, Isolated Remote SP
Instruction Manual
WXPEC5500R03E
Describes AO, isolated remote
SP wiring, setup and functions.
4
Expansion Interface, Servo
Drive Output Instruction
Manual WXPEC5500R04E
Describes servo drive and
expansion interface wiring, setup
and functions.
This instruction manual describes the information to be referred with
caution when using the product with the following marks:
Caution/reference mark
[Caution] This is cautionary information for correct use of the
instrument. Be certain to read.
[Reference] This is information to help you use the functions of this
instrument more effectively.
There is an item, table, figure or another instruction
manual to be referred at the same time.
This
manual
☞

−4−
Table of Contents
Chapter 1
When Product Arrives.................. 5
1.1 Checking the Accessories ......... 5
1.2 Checking the Type..................... 5
1.3 Display....................................... 6
Chapter 2 Installation.................... 7
Chapter 3 Wiring ........................... 9
Chapter 4 Part Names................. 12
Chapter 5 Basic Operation
and Setting ................................ 13
5.1 Screen Types .......................... 13
5.2 Selection of Group/Item on
Screen ..................................... 14
5.3 Data Setting Procedure ........... 15
5.3.1 Numeric Data....................... 15
5.3.2 Character Data .................... 15
5.4 System Setup .......................... 16
5.5 All Reset .................................. 17
5.6 Setting Items of Each Function 18
5.6.1 Setting up the Controlled
SP Each Time ..................... 18
5.6.2 Switching SP registered
beforehand .......................... 18
5.6.3 Use of Alarms ...................... 19
5.6.4 Gapped Control
(Nonlinear Control) ............. 20
5.6.5 Remote SP .......................... 20
5.6.6 Profiling Control ................... 20
5.7 Key Lock.................................. 21
Chapter 6
Operation Guidance................... 22
6.1 Operation Screen .................... 23
6.2 Parameter Screen ................... 25
6.3 Setup Screen........................... 27
Chapter 7 List of Items................ 31
7.1 Operation Screen .................... 31
7.2 Parameter Screen ................... 32
7.3 Setup Screen........................... 33
Chapter 8 Operation....................38
8.1 Control Method............................ 38
8.2 Automatic Control (AUTO)
and Manual Control (MAN) ........ 38
8.2.1 SP/Output Display Switching..38
8.2.2 AUTO/MAN Switching ............ 39
8.2.3 Setting Output Value at MAN .39
8.3 SP .............................................. 40
8.3.1 Normal SP and Multi SP.........40
8.3.2 Multi SP Setting, Switching
and Ramping .........................40
8.3.3 PV Start..................................41
8.3.4 Anti-overshoot ........................41
8.4 Automatic Tuning....................... 41
8.5 Self Tuning................................. 42
8.6 Selection of Operation Method .. 43
8.7 Power failure and Power restoration
during Operation ........................ 44
Chapter 9 Procedure
for Major Functions..................45
9.1 Alarms........................................ 45
9.1.1 Pause Alarms.........................45
9.1.2 Hysteresis Width ....................45
9.1.3 ON Delay Type.......................46
9.2 Output Limit................................ 46
9.3 Input Functions .......................... 46
9.3.1 Scaling ...................................46
9.3.2 Square root ............................47
9.3.3 Sensor Correction ..................47
9.4 Control RUN/STOP.................... 47
9.5 ON-OFF Control Hysteresis
Width.......................................... 47
9.6 Profiling Control ......................... 48
9.7 Gapped Control
(Nonlinear Control)........................49
9.8 Heating/Cooling Control............. 49
Chapter 10 Troubleshooting.......51

−5−
Cha
p
ter 1 When Product Arrives
1.1 Checking the Accessories
When this product arrives, please check on the accessories and
appearance and check that there is no lacking parts or damages. If you
find any inappropriate parts, inform our dealer where you purchased the
instrument or our sales representative.
This instrument has the following accessories:
Mounting fixture (2) Instruction manual Unit seal (separately sold)
(this document)
1.2 Checking the Type
① ② ③ ⑤ ⑥
⑥Special
①1st output
④Expansion options
⑤2nd output
②Number of output ③Built-in options
output points
ARCNET®is a registered trademark of the U.S. DATAPOINT.
1 Relay
2 SSR drive
3
4
5 4 to 20mA
6 0 to 5mA
7
8 Multi output
0No
ZYes
0No
1 Relay
2 SSR drive
3
4
5 4 to 20mA
6 0 to 5mA
02
1 4 (optional)
0No
2 Isolated remote SP
5AO
6 AO, Isolated remote SP
0No
1ARCNET®
2 Servo drive
3 ARCNET®
Servo drive
EC550□R□□ □□□
[Caution]
When the number of contact output points (standard), contacts DO3 and
DO4 are not output. However, the functions are available and similar
setup to DO1 and 2 is possible. The condition can be checked by
alarm/event display lamp.
④

−6−
1.3 Display
[Reference] Display character correspondence table
The display characters used in this instrument and the alphabets
indicated by them are shown in table below:
Display character
Alphabet ABCDEFGHI JKL
Display character
Alphabet MNOPQRST UVW
[Reference] Protective sheet
Protective sheet is attached on the front face of this instrument for
surface protection. It will use the instrument, remove this sheet.

−7−
Cha
p
ter 2 Installation
Install this product by establishing holes according to the panel cut drawing
and fixing it with the accessory fixtures.
Installation procedure Panel cut
(Unit: mm)
Caution
Attach at locations with stable peripheral temperature in the range of -10
to 55℃. Avoid the following positions:
○ Locations where people can touch the terminal easily
○ Locations with dusts in the air, with corrosive gas
○ Locations with vibration or impact or strong noise
○ Locations with direct sunlight or wind and rain (water is splashed)
○ Locations with direct wind on the back terminal
○ Locations near flammable objects
A
ttach within 30
degrees.
A
ttach within 30
degrees.
Instrument
front
Caution
・Fix with the fixture tightening
torque of 15N・cm or smaller.
・Attach horizontally and upward
angle or 30 degrees or smaller
and no downward angle.
Attachment
procedure
Attachment position
Mounting panel
Fixture
Setscrew
A
ttachment posture
(96×(N-1)+92)
Installation of N pieces
92
120Min.
92
+0.8
−0
+0.8
-0
+1
-0

−8−
External dimension diagram for
Multi-setpoint selector
Multi-setpoint selector
panel cut
External dimension diagram Optional (communication
module) separately sold (*1)
Optional
(communication cable)
separately sold (*2)
Optional (DI cable)
separately sold (*3)
RS-232C RS-422A RS-485
*1 Communication
module
ZE7101A0
110
ZE7101B0408
*2 Communication
cable
HMSU2255
B02
WMSU0075A
01
WMSU0075A
02
*3 DI cable HMSU2695A01:1m
HMSU2695A02:5m
Separately
sold
products
Type
96
96
11.3
(7.4)
100
A
pprox. 175
Panel thickness 10Max.
48 22 75
96
89
5
Panel
44
84 +1
−0
90
+1
−0 2−M4
+0.5
−0

−9−
Cha
p
ter 3 Wirin
g
DI (remote multi SP switching)
B A←Connection only to terminal A
8
4
2
1
SP operated
○
○
○○
○
○○
○○
○○○
Connection
(Normal SP)
Multi SP1
Multi SP2
Multi SP3
Multi SP4
Multi SP5
Multi SP6
Multi SP7
Multi SP8 ○
●
●
●
●
●
●
●
●
●
●
Warning
・Never touch the power supply terminal while the power is supplied.
When the power supply terminal is touched, it gets an electric shock.
・Never touch relay output terminal and alarm output terminal when they
are connected with power supply.
Caution
・Use a round M3.5 press-fitting terminal.
・Use shielded wire and set the signal line (input, AO,
communication, etc.) as far away as possible from the
power line.
・Use the specified compensating lead wire for thermocouple input.
・Lifetime may be shortened if frequently operated for relay contact
output. Use auxiliary relay.
・Attach circuit breaker, switch, etc. on power supply wiring for safety and
clearly label that it is the power supply switch for this instrument.
Servo drive (page 9)
Expansion I/F (page 11)
COM
Connection with exclusive
multi-setpoint selector (page 11)
☞
Correspondence between terminal No. and DI No.
DI No. 1 2 3 4
Terminal No. 1 2 4 8
○indicates ON (short circuit between COM-
applicable terminal) and blank indicates OFF
(open). Do not use terminal B.
7mm

−10−
Thermocouple (TC)
voltage (mV)
Voltage
(V)
Current
(mA)
Resistance tempera-
ture detector (RTD)
Connection
−
⑦
⑧
⑨
⑩
+
●
⑦
⑧
⑨
⑩
+
−−
+
○
○
⑦
⑧
⑨
⑩
A
⑦
⑧
⑨
⑩
B
B
Dual output
1st output 2nd output
Current
SSR
drive
Relay
Load
Load
Load
LoadLoad
Load
Load LoadLoad
Output Single output
Connection
④
③
② −
① +
○
○
②
①
④
③
②
①
④
③
②
①
② −
① +
○
○④ −
③ +
○
○
RS-232C Communication Module Instruction Manual HXZE7101A01E
RS-422A/RS-485 communication module instruction manual
HXPZE7101B04E
☞
Alarm output (ALM)
Connection
Load
250VAC 0.5A (resistive load)
▲
▲
▲
▲
4
3
2
1
Grounding
Type D grounding
(Protective
grounding)
Power supply
100 to 240VA
50 / 60Hz
40
39
38
Current 4 to 20mA DC : Max. 600Ω、0 to 5mA DC : Max. 2kΩ
SSR drive 0 / 15V DC Max.20mA
Relay 250V AC 3A Max. (resistive load)
Remote SP (Optional)
Analog retransmission (optional)
−
+
−
+
○
○
Load
4 to 20mA or
0 to 20mA
output
1 to 5V or 0 to 5V
in
pu
t
AO, Isolated Remote SP
AO, Isolated Remote
SP Instruction Manual
WXPECEC5500R03E
☞
Load
condition
Connection
Connection
Input

−11−
Servo drive (optional)
Connection
⑮
⑯
⑰
⑱
⑲
⑳
CW
M
●
●
●
CW
CCW
Expansion I/F Servo drive
Expansion I/F, servo drive
Expansion Interface, Servo Drive Output Instruction Manual
WXPEC5500R04E
☞
Expansion I/F
(ARCNET®: optional)
Connection
⑬
⑭
⑪
⑫
I/O
A
B
Terminator
Multi setpoint selector: ZE3301
This selector is equipped with external
contacts (binary contacts) for selecting
the multi SP (SP1 to 8) and decimal
contact for customers independently.
●
●
●
●
●
●
●
●
●
●
B A
8
4
2
1
COM
8
7
86
45
24
13
C2
1
C
Spare contacts for customers:
Corresponds to the switch numbe
r
on surface and between terminal C
and each of 1 to 8 is closed.
Controller back face
connectors
Multi setpoint selector back
face terminals
Special cable
HMSU2695A01:1m
HMSU2695A02:5m

−12−
Cha
p
ter 4 Part Names
No. Key/
dial Function Chapter/section
for reference
Switch the screen (Operation, Parameter or
Setup) and the group on screen.
Sec. 5.1, 5.2,
Chapter 6
Switch output indication and automatic
(AUTO)/manual (MAN)operation. Sec. 8.1, 8.2
Give data change permission and move the
digit for data change. Sec. 5.3
Switch the display item within a group and
register the data.
Sec. 5.2, 5.3,
Chapter 6
Switch the groups on Parameter screen and
Setup screen and change the data.
Sec. 5.2, 5.3,
Chapter 6
No. Display Function Reference
□
1Upper Display the PV(process variable) or characters
that indicate the item name. Chapter 6, 7
□
2Lower Display SP(setpoint) or various data (numeric
values or characters). Chapter 7
□
3SP
No.
Used only on Operation screen. Display multi
SP No. (at SP display), output No. (at output
display) or the characters that indicate item.
Chapter 6, 7
No. Lamp Function Reference
①ALM
1- 4
Blink during alarm occurrence or when the
function assigned to each of DO 1〜4 is
executed.
Sec. 5.6.3,
9.1
②OUT Light up at the brightness depending on the
output value. The light goes off at output = 0%.
③MAN
Light up at MAN (manual control). Blink while
the key is pressed at screen switching or
during AUTO/MAN switching standby when the
key is pressed.
Sec. 8.1, 8.2
④TUNE Blink during automatic tuning and light up
during Self tuning. Sec. 8.4, 8.5
⑤REM Light up at communication remote or SP
remote. Sec. 8.6
Setting digit move key
1
2
3
A
UTO/MAN
change key
Screen selection/group
selection key
③MAN operation display
□
3SP No. display
①Alarm/event display
②Output display
□
2Lower display
□
1Upper display
⑤Remote control
display
Setting dial
④Tuning operation
dis
p
la
y
Setting item selection/entry key
4
5
1
2
3
4
5

−13−
Cha
p
ter 5 Basic O
p
eration and Settin
g
5.1 Screen Type
Screen name Description
Operation
screen
This is the screen for indicating/setting of PV, SP, output
value, Tuning and PID necessary for operation.
Parameter
screen
This is the screen for setting/confirming the parameters
including the PID and alarm for operation.
Setup screen This is the screen mainly for determining the system
functions such as input type and control method.
Select with key or dial
and press the key. Or press
Select with key or dial
and press the key.
A
uto
restoration
[Reference] What is normal display?
PV (upper display) and SP (lower display) are displayed at AUTO
operation, and PV and output value (lower display) are displayed at MAN
operation. Normal display is displayed at turning on the power, auto
restoration, returning from Parameter or Setup screen to Operation screen.
☞
[Reference] What is Auto restoration?
It is the function to return to normal display when no key or dial operation
is made for more than 1 minute.
☞
[Reference]
Relationship between the operation of each screen and displayed
information is shown in Chapter 6 “Operation Guidance.” In addition,
detailed information, setting range and initial value for each item is shown
in Chapter 7 “List of Items.”
[Reference] If you are lost on which screen it is,
Press the key several times. The screen can be distinguished by the
information on the upper display.
n (n is a numeric value) … Parameter screen
n (n is a numeric value) … Setup screen
key for approx. 3 seconds.
O
p
eration screen
Parameter screen
Setup screen
Normal display
☞
Press the key for approx. 3 seconds.
Press the key for approx. 3 seconds.
Power startup
A
uto
restoration
☞

−14−
5.2 Selection of Group/Item on Screen
Select the item (use key) after group selection (use key or dial).
Group display on Operation screen
Group display on Parameter screen
Group display on Setup screen
[Reference]What is a group?
There are several “groups” classifying the items by kind on each screen.
Each group is given with a name that indicates the kind. Group name is
displayed on the upper display (except for SP or output display) on
Operation screen and on lower display in group display on Parameter
screen and Setu
p
screen.
[Reference]
When group display of Parameter screen (upper display is n (n is
a group number of 1 to 13)or ) or Setup screen (upper display
is n:(n is a group number of 1 to 13)or ) is displayed, the
group can be changed by the dial as well. When the dial is turned
clockwise, the group changes in the same direction as the key, and in
the opposite direction as the key when it is turned counterclockwise.
Pressing the key when the item in a group is displayed will switch the
dis
p
la
y
to the next
g
rou
p
number.
Item in the group
or dial
To normal
display on
Operation
Item in the group
or dial
To normal
display on
Operation
screen
[Caution]
It is only for group display on Parameter screen or Setup screen where
the group can be selected with the dial. Please note that turning the dial
in other cases will enable setting.
(SP)
Item in the group

−15−
5.3 Data Setting Procedure
Data is classified as “numeric data” and “character data.” Numeric value
blinks when change is enabled for numeric data, and the decimal point
blinks for character data. It is set up by the following procedure:
5.3.1 Numeric Data
Change in SP is shown as an example.
①The lowest numeric value blinks when the key is
pressed or dial is turned by 1 click, indicating that
change is enabled.
②The digit to be changed is selected by pressing the
key. Every time the key is pressed, blinking
value moves in order indicated by the arrow in figure
on the left. The blinking digit is subject for change.
However, value of other digit may be changed as well if
there is carrying/borrowing.
③The value of the subject digit to be changed is changed
by turning the dial. The desired value is set using the
keyordial.
④The value is registered by pressing the key. The
value blinking stops and the display returns to usual
display.
5.3.2 Character Data
Turning ON automatic turning is used as an example.
①The decimal point on the 4th digit blinks when the
key is pressed or the dial is turned for 1 click,
indicating that change is enabled.
②Desired data (character) is selected by turning the dial.
③The data (character) is registered by pressing the
key. Blinking of the decimal point stops.
[Caution]
If there is no key or dial operation for more than 10 seconds while
change is enabled, the value being changed is invalidated (original
value is recovered) and change is disabled.
[Reference] When
is displayed
If is displayed when the key or dial is operated to enable
change, it means that the item cannot be set. display
disappears in approximately 2 seconds and returns to the original display.
Blinks
Blinks
PV
SP
PV
SP
PV
SP
PV
SP
Blinks
Blinks
Blinks

−16−
5.4 System Setup
The basic functions of this controller are as shown in the following table at
factory setting. To use with settings other than that of factory setting,
press the key for about 6 seconds to display the Setup screen and
then change on the specified displays. To change multiple items, change
in the order of the table below:
No. Item Screen
position
Factory setting
1 Input type Input list (page 17) SU1 K1
2 Use of square root (for mV, V, mA input) SU1 Not used
3Scaling SU1 -200 to 1370℃
4Output type (not required for dual output
specification) SU2 mA
5 Control mode SU2 PID
6 Control reverse/direct action SU2 Reverse action
☞
[Caution] Data initialization by change in basic functions
Please note that change in 1 to 6 of the previous page table initializes
other items (returning to the factory setting). Changed item and the
items initialized by it are shown as follows:
Changed item Initialized item
1: Input type All data except SU6 on Setup screen
2: Use of square
root
All data on Operation screen, all data on
Parameter screen except PA2 and PA12, sensor
correction, scaling, PV error upper and lower limit
3: Scaling (when
input is TC or
RTD)
SP, SP No., bias, emergency SP, and PA1 on
Parameter screen, and sensor correction
3: Scaling (when
input is mV, V,
mA)
SP, SP No., bias, emergency SP, up/down rate, all
data in CONT group on Operation screen (except
control RUN/STOP), all data on Parameter screen
except PA2 and PA12, sensor correction, PV error
upper and lower limit
4: Output type
5: Control mode
6: Reverse/direct
action
All data in CONT group on Operation screen
(except control RUN/STOP), all data in PA3 to 11
and PA13 on Parameter screen, PID mode, SP
No./PID No. selection, preset output, use of
present output, use of gapped control, use of
profiling
[Caution]
To change multiple items, be sure to follow the order of the No. The
changed data may be returned to the original factory setting if they are
not changed in order.
Ex.) If input type is changed after changing the control mode, the
control mode returns to the factory setting.
In such cases, check the data and change again if the data is factory
settin
g
.

−17−
Input list
5.5 All Reset
All Reset is the operation to return to the factory setting all parameters
except for basic settings. To perform All Reset, press key and key
simultaneously for more than 3 seconds.
Input Code Input range Input Code Input range
TC (thermocouple) input DC voltage, DC current input
mV
mV
mV
V
V
V
mA
-10.0 to 10.0mV
0.0 to 20.0mV
0.0 to 50.0mV
1.0 to 5.0V
0.0 to 5.0V
0.0 to 10.0V
4.0 to 20.0mA
RTD (resistance temperature
detector) input
Pt
100
-199.9 to 850.0℃
-199.9 to 300.0℃
-150.0 to 150.0℃
B
R
R
S
K
K
K
E
J
J
T
WRe5-
26
N
PR40-20
PLⅡ
U
L
Au-Fe
0 to 1820℃
0 to 1760℃
0 to 1200℃
0 to 1760℃
-200 to 1370℃
0 to 600 ℃
-199.9 to 300.0℃
-199.9 to 700.0℃
-199.9 to 900.0℃
-199.9 to 400.0℃
-199.9 to 400.0℃
0 to 2320℃
0 to 1300℃
0 to 1880℃
0 to 1390℃
-199.9 to 400.0℃
-199.9 to 900.0℃
0.0 to 300.0K
JPt
100
-199.9 to 650.0℃
-199.9 to 300.0℃
-150.0 to 150.0℃
[Caution] Data initialization by All Reset
All Reset maintains the following items and initializes all other items.
Group Maintained item
SU1
Input type, reference junction compensation, square
root, input cutoff level (when square root is used),
scaling
SU2 Output type (at multi output), control mode, control
reverse/direct action, cycle time, output hysteresis width
SU3 DO function selection
SU4 DI function selection, SP No./PID No. selection
SU6 Communication address, Baud rate, communication
type

−18−
5.6 Setting Items of Each Function
This section describes the setting items and the order of setting for each
of the major functions.
5.6.1 Set the Controlled SP Each Time
Orde
r
Item Screen/group Factory
setting
①Set the normal SP. SP 0
②
Set the normal PID and MR (Manual
Reset: at PD control). It can be
calculated automatically by
automatic tuning or Self tuning (only
for PID control).
on
Operation
screen
P: 2.0%
I: 3.00 min.
D: 0.00 min.
MR: 50%
5.6.2 Switching SP registered beforehand
Order Item Screen/group Factory
setting
①Set the use of multi SP to
“Used”.
on Operation
screen Not used
②Set the multi SP. SP 0
③
Set the multi PID and MR
(for PD control). It can be
calculated automatically
by automatic tuning or
Self tuning (for PID control
only).
Manual setting: PA3 to
PA10 (corresponds to
from PID1 to 8) or
on Operation
screen (only PID and
MR in execution)
P: 2.0%
I: 3.00 min.
D: 0.00 min.
MR: 50%
④Set the up/down rate. *1 OFF(0)
⑤Switch the multi SP. *1
on Operation
screen SP0
(normal SP)
※1:Action for ④、⑤ Section 8.3.2 (page 40)
[Caution] Normal SP and Normal PID
They are used as the SP and PID when multi SP is disabled. Normal
SP is set on normal display in AUTO. If multi SP is enabled, 8 kinds
of multi SP and multi PIDs that form couples with each multi SP can
be used beside this normal SP.
☞

−19−
5.6.3 Use of Alarms
Order Item Screen/
group
Factory setting
①Alarm function is
determined. SU3
DO1: Deviation high alarm
DO2: Deviation low alarm
DO3: Deviation absolute value alarm
DO4: Fail (it is not an alarm.)
②Set the alarm
value .
DO1: + scaling width
DO2: - scaling width
DO3: + scaling width
DO4: None Scaling width
③
Set the pause
alarm, hysteresis
width and ON
delay time.
PA1
No pause alarm, hysteresis width = 0,
ON delay time = 0
[Caution] Initialization by changing alarm functions
When alarm function is changed, the alarm value, pause alarm,
hysteresis width and ON delays time for the changed DO No. are
initialized.
[Reference] Alarm type and functions
The types and functions of alarm equipped in this instrument are as
follows. Furthermore, the alarm occurrence conditions in the table
below are those for no pause alarm and 0 hysteresis width and 0 ON
delay time (pause alarm, hysteresis width, ON delay time Section
9.1):
Type Function (alarm occurrence condition)
Deviation high
alarm
When “deviation (SP – PV) > alarm setting
value”
Deviation low
alarm
When “deviation (SP – PV) < alarm setting
value”
Deviation absolute
value alarm
When “deviation (|SP – PV|) > alarm setting
value”
PV high alarm When “PV > alarm setting value”
PV low alarm When “PV < alarm setting value”
SP high alarm When “SP > alarm setting value”
SP low alarm When “SP < alarm setting value”
☞
[Caution]
・Set the functions of ALM (alarm) 1 to 4 and the alarm values at DO1
to DO4 of SU3, PA1.
・When the number of contact output points is 2 (standard), ALM3 and
ALM4 are not outputted. However, functions are available and setting
similar to ALM1 and 2 is possible. The status can be checked with
alarm/event display lamp.
[Reference] What is scaling width?
It indicates “scaling upper limit – scaling lower limit.
☞
☞
Table of contents
Popular Controllers manuals by other brands
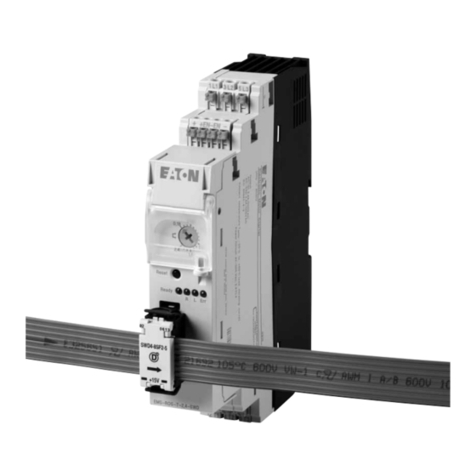
Eaton
Eaton EMS-SWD Series manual
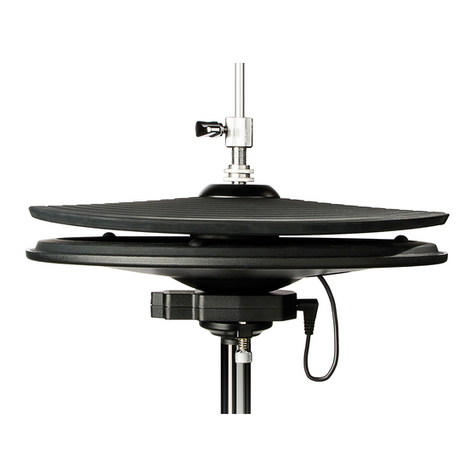
Alesis
Alesis PRO X HI-HAT quick start guide
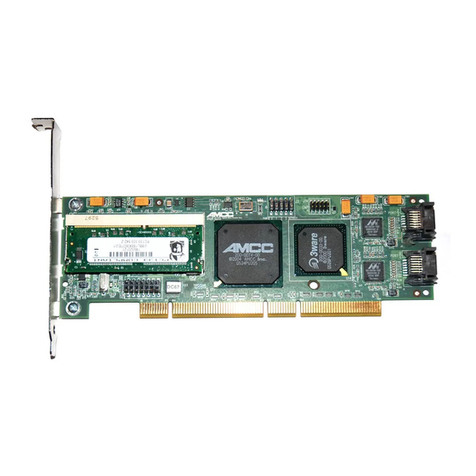
3Ware
3Ware 9000 Series Release notes
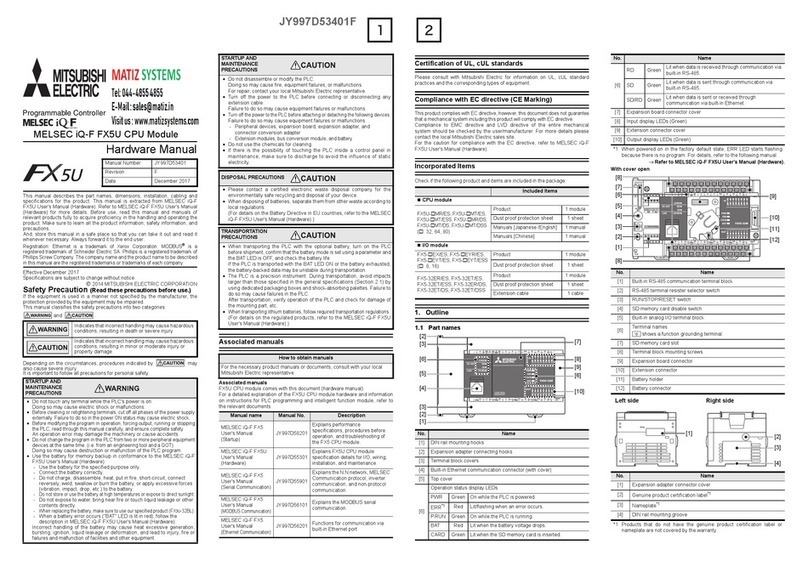
Mitsubishi Electric
Mitsubishi Electric MELSEC iQ-F FX5U CPU user manual
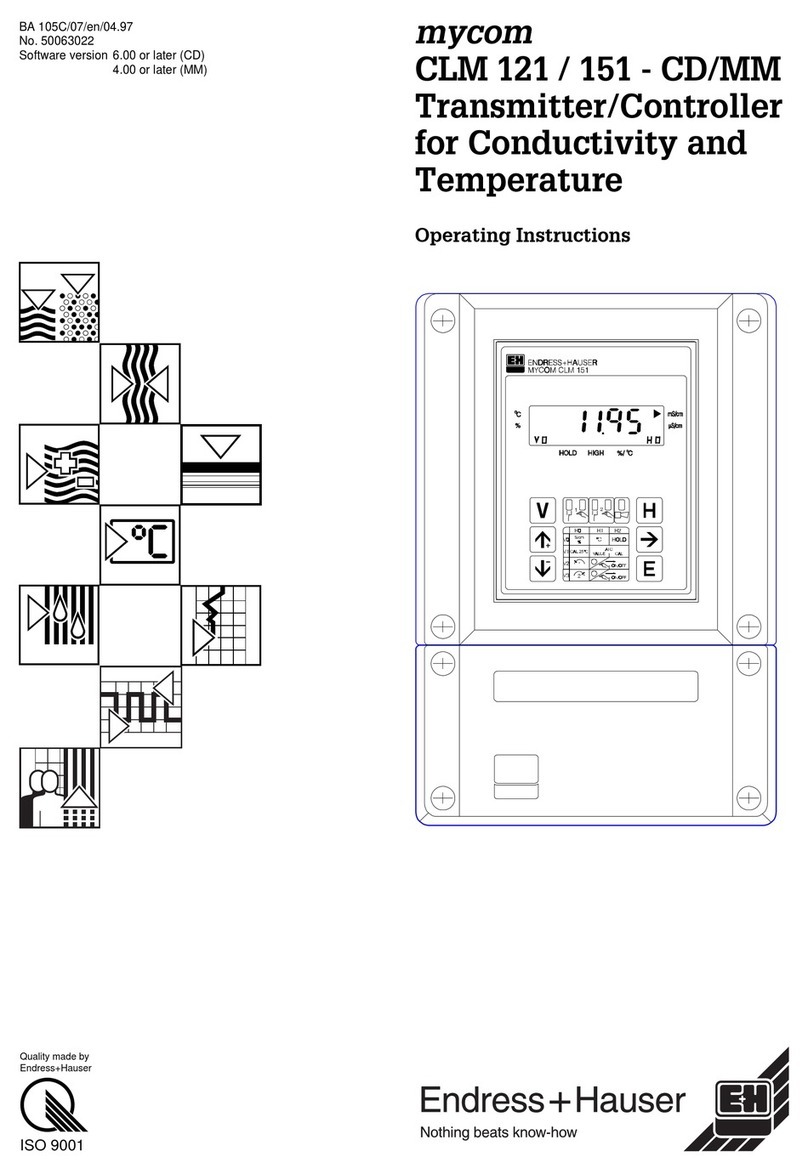
Endress+Hauser
Endress+Hauser mycom CLM 121 operating instructions
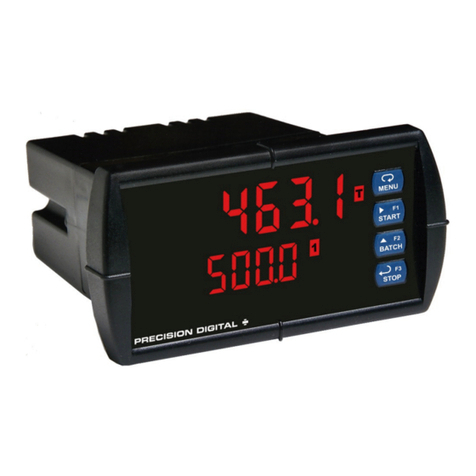
PRECISION DIGITAL
PRECISION DIGITAL ProVu PD6310 instruction manual
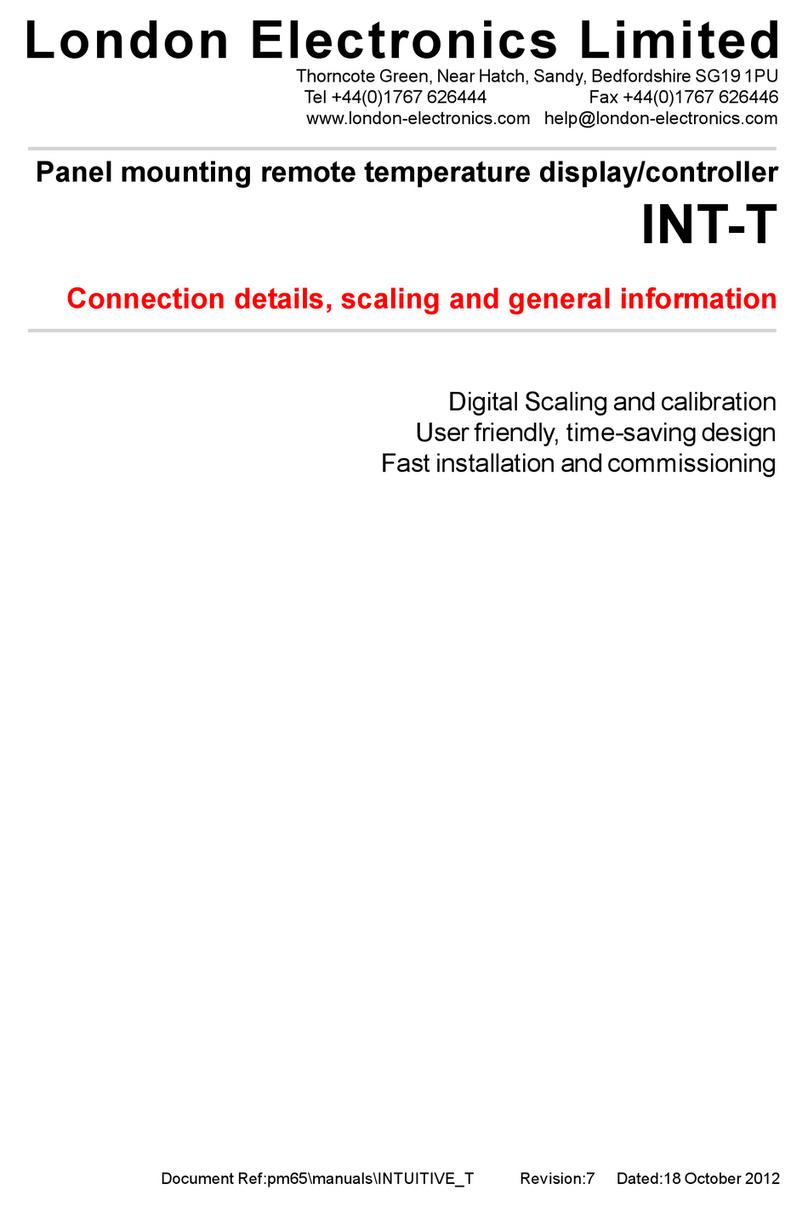
London Electronics
London Electronics INT-T Connection details, scaling and general information
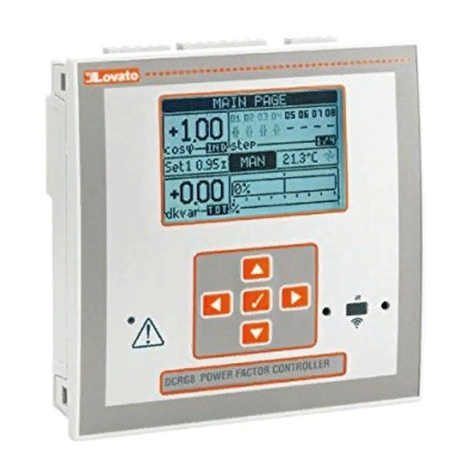
LOVATO ELECTRIC
LOVATO ELECTRIC DCRJ Addendum
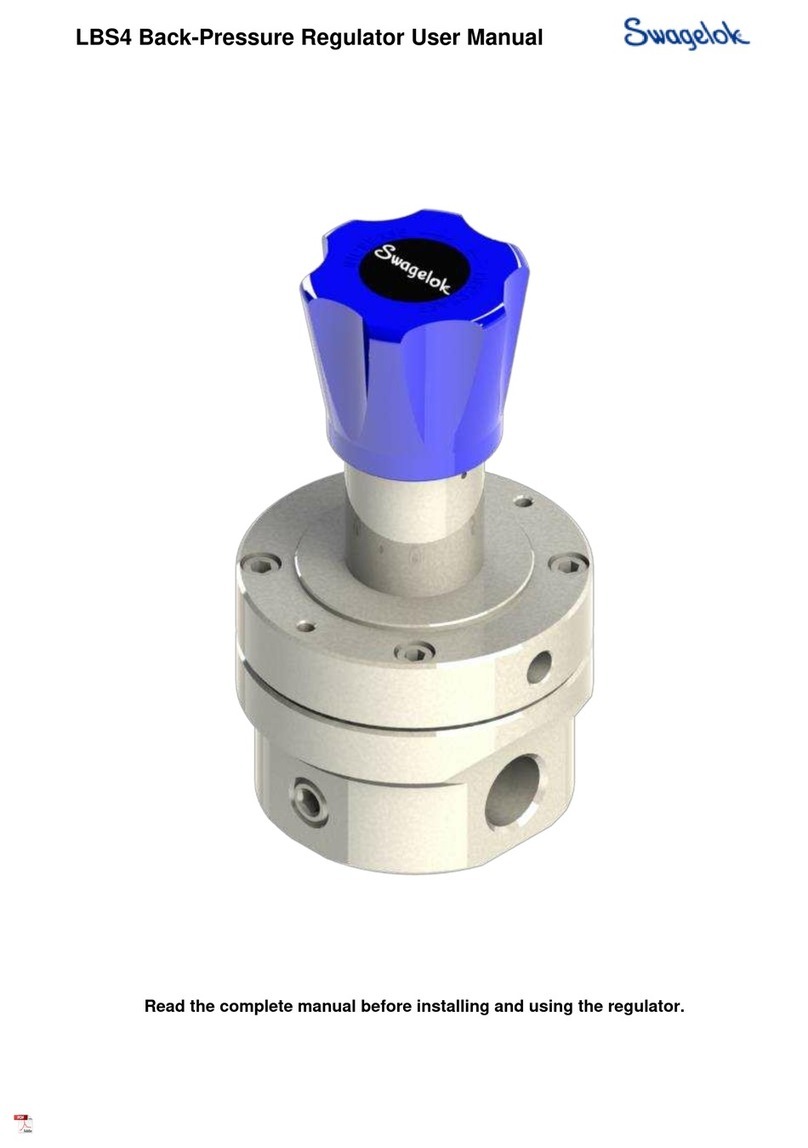
Swagelok
Swagelok LBS4 user manual
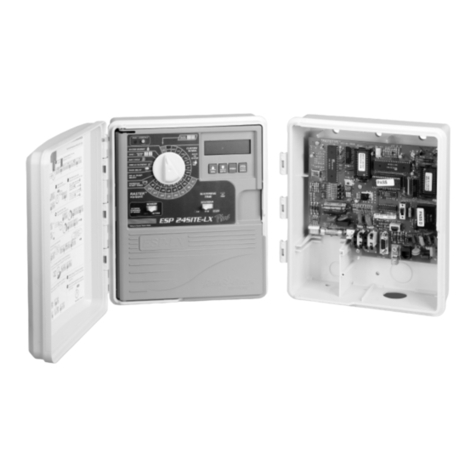
Rain Bird
Rain Bird ESP-LX Plus Series Installation, Connection and Settings
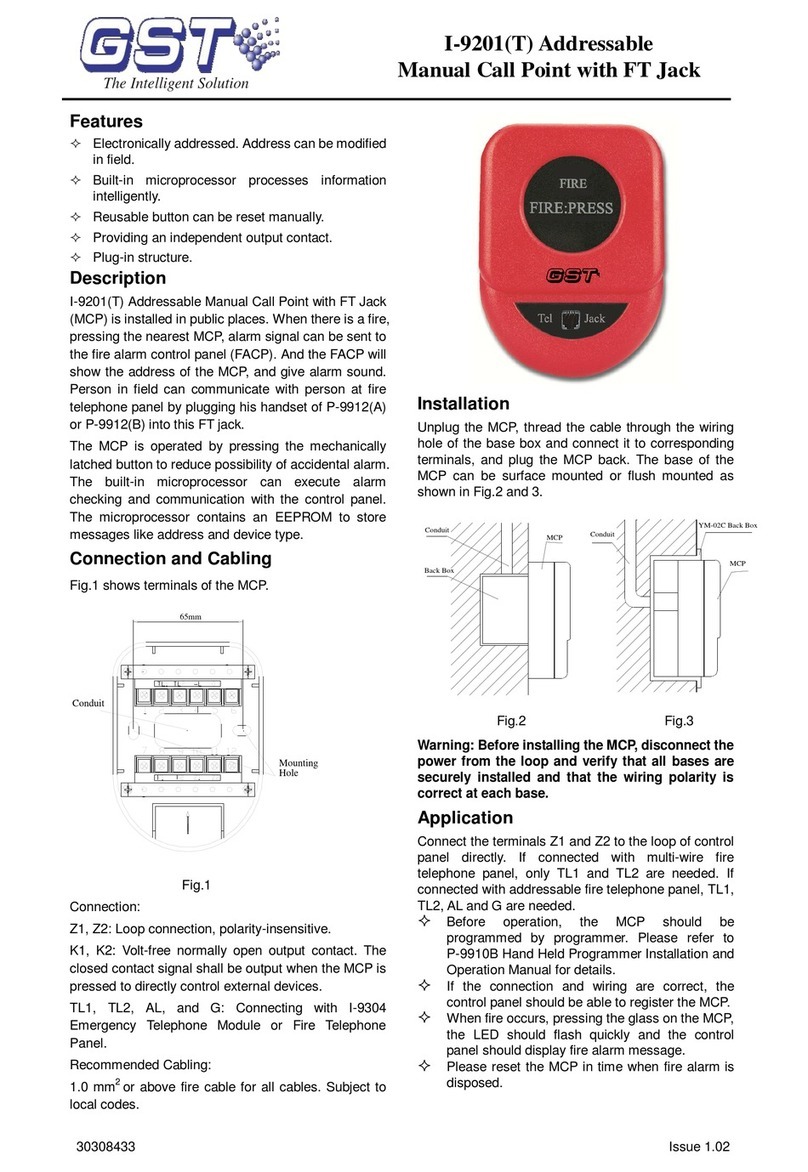
GST
GST I-9201 quick start guide
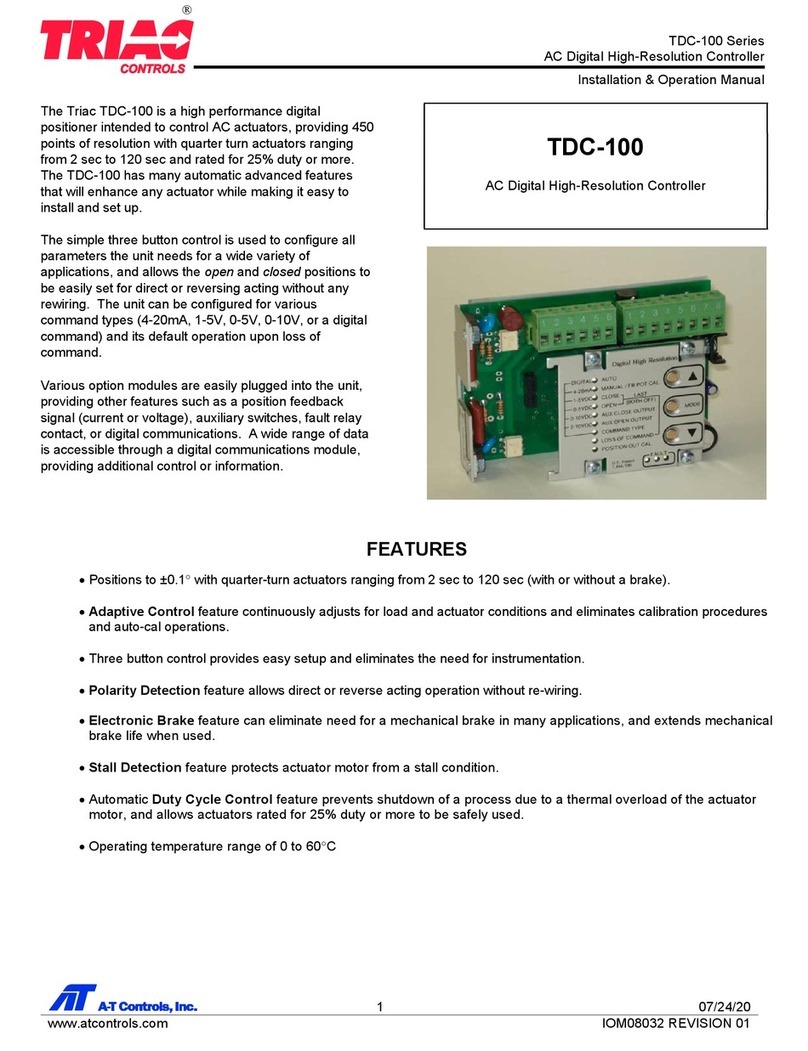
A-T Controls
A-T Controls TRIAC TDC-100 Series Installation & operation manual