Array Solutions Four Square User manual

Array Solutions Four Square Controller 1
www.arraysolutions.com Array Solutions Ofc: 972 203 2008
350 Gloria Rd. Fax: 972 203 8811
Sunnyvale, TX 75182
Array Solutions
Four Square Array Controller User’s Guide
Figure 1: Array Solutions Four Square Array Steering System
Note: A 180 degree phasing line is included, but not shown
Congratulations!
You have selected one of the finest phased array steering systems made. We have under-rated
the power capability of this system to assure the user high reliability under heavy use such as in a
48 hour radio contest. Please contact us if you have any questions about the product and please
send a picture and description of your station showing the control system installed and in use.
The Four Square Array system has two components: (see Figure 1 above) a relay box that will be
mounted midway between the four verticals and a control box that is connected with a 5-wire
control cable inside the operating room. With this system you will be able to beam in 4 directions
and also take advantage of the OMNI mode for domestic use.
The system is available in standard quadrature feed and an optimized feed version.

Array Solutions Four Square Controller 2
www.arraysolutions.com Array Solutions Ofc: 972 203 2008
350 Gloria Rd. Fax: 972 203 8811
Sunnyvale, TX 75182
Wiring the system:
Take the cover off the switch box and unwrap the circuit board. Wire the control cable before
mounting the board to the box.
You will need a cable with 5 wires. Small gauge wires are fine and will fit inside the boxes better
than large rotor cable. For runs of less than 500 feet #18 or larger gauge stranded wires will be
adequate. The relays draw only 120 ma at 12V DC.
You will also need a regulated DC power supply. A 13.8VDC 1 amp power supply is sufficient.
Please use a reliable power source, since wall wart transformers have a habit of falling out of
plugs and failing in the middle of a contest.
The silk-screen on the PCB indicates where to wire the +12 V DC (+13.8V DC) supply and its
RETURN or GND wire to the Power Supply.
Wire the control switch PCB to the relay box per the following Table 1.
Control Switch PCB Terminal Strip Relay Box Terminal strip
1 - no wire Default position direction A No connection and no terminal 1 in this box
2 - Direction B 2
3 - Direction C 3
4 - Direction D 4
5 - no wire Default position direction A 5 no connection
6 - OMNI directional 6
+12V - wire to your 13.8 V DC supply
GND - Ground return to your DC supply GND return wire back to control switch
Table 1
Lightning Protection:
Array Solutions recommends the use of proper lightning and surge protection at the
station end for both the control and RF cables. MOV protection is included in the Four-
Square relay box. Devices such as the I.C.E. model 348 Transient Suppressor and 303U
Coaxial Impulse Suppressor / Arrestor products that Array Solutions can provide are very
effective. For additional safety, we recommend the use of a multi-terminal connector on a
short length of control cable so you may disconnect the control unit from the control
cable.
Preparation now can save valuable radios later.
Place the control switch PCB inside the control switch and secure the PCB in place with the
rotary switch hardware. The LEDs should just protrude through the holes provided for them.
Use the tie wraps supplied as a strain relief when the control cable is fed through the grommet
hole. Snug the tie wrap next to the hole in the back of the box to prevent the wire from being
pulled and stressing the PCB.
Do the same with the 12V-power wires you will supply through the other grommet hole.
Relay Box:
Route the control cable through the rubber grommet hole in the relay box tray. Use a Ty-wrap™
as a strain relief. The relay box terminal strip is marked to indicate the connection to terminals.
See Table 1 above for the proper connections. There is no terminal 1 since it is the default
position. The relays are bypassed with MOVs, capacitors, and diodes for RF and lightning
suppression. See Fig. 2 below which is a photograph of the inside of the phasing box.

Array Solutions Four Square Controller 3
www.arraysolutions.com Array Solutions Ofc: 972 203 2008
350 Gloria Rd. Fax: 972 203 8811
Sunnyvale, TX 75182
Figure 2.
Figure 2 description: (Please also refer to the schematic received with your System)
J1 Feed line RF connector is where your 50 ohm feed line connects.
The area marked HV capacitor bank – C1 is for placement of HV RF capacitors in parallel with
the vacuum cap. This is the input L network. It is used to match the system to a perfect 1:1
VSWR. Adjust the matching network for the characteristics of your antennas by adding or
removing capacitors, adjusting the vacuum cap, and moving the tap on the coil L1.
Input Match L1 and C1, L-network: Two coil taps, one for 4-square operation and one for omni
operation. Coil taps and capacitors may need slight adjustments for your antennas.
J2 and J3, Delay Phase Line In and Out: These are the two connectors for the 180 degree
phase line. It creates the 180 degree phase delay to the front element of the array.
Antenna Ports J4 to J7: These are the output connectors to the 4 antennas. Each one should
have a ¼ wavelength feed line connected to it. ¼ wavelengths take advantage of the current
forcing properties of this length of transmission line. They can be 50 or 75 ohms.(See note on
next page.)
L2, C2 - 90-120 degree phase shifter: This is the L-network that will cause the required phase
delay to the center elements with respect to the rear element. Adjust it for correct phase and
magnitude.
L3, C3 - 180-240 degree phase line phase shifter LC: This network allows you to use a phase
delay to the front element that is greater than 180 degrees, which is accomplished by the 180
degree delay (phasing) line. You will adjust it for phase -224 degrees, and magnitude.
Control Terminals: Attach the control cable to this terminal strip. It is marked as in the schematic
2, 3, 4, 5, OMNI, and ground. (No connections to #5.)

Array Solutions Four Square Controller 4
www.arraysolutions.com Array Solutions Ofc: 972 203 2008
350 Gloria Rd. Fax: 972 203 8811
Sunnyvale, TX 75182
Setting up the system
The best book on the subject of setting up a four-square antenna array is written by John
Devoldere, ON4UN and is entitled “Low-Band DXing”. If you do not have a copy of this book,
Array Solutions recommends that you obtain a copy of it to learn more about these and other
types of antenna systems. It is available from the ARRL bookstore.
Place the relay box in the center of the array. Use the U-bolt provided to mount the box on a
ground rod, pipe, or tower leg. Feed each vertical with ¼ wavelength of 50 or 75 ohm feed line
(75 ohm feed line will give a little wider bandwidth). The feed lines are not matched for SWR, they
are impedance transformers. Make sure you cut four feedlines to exact quarter-wave lengths for
the frequency you want to operate!
Attach the 180 degree long phasing line to the appropriate ports as well as the input feedline, and
the four ¼ wavelength antenna feed lines. Make sure the delay line is exactly 180 degrees on
your favorite operating portion of the band! Be sure to weather-proof the connectors. There is a
ground lug on the side of the box, use it to secure a good ground connection such as a ground
rod or any other ground system like your tower ground or a radial ground plane. Note: Do not
attach this ground to a raised radial system which must remain floating above ground.
You have set up your verticals into a square; we will define the square as follows for North
America. The antennas are marked from 1 to 4
D A
o 2 o 4
o 1 o 3
C B
The above diagram indicates verticals (o), Antenna number (1-4), and Direction (A-D)
Connect the antennas from the antenna output ports that coincide with the above diagram.
Switching the array pattern is done with the control switch. Position 1is the default position. It is
not supplying any voltage to the switching system. Configure your antennas so that this is your
most important direction. In North America, you probably will want to have this position be North
East towards Europe.
Position two is SE
Position three is SW
Position four is NW
Position five is again NE
Position six is the OMNI directional position

Array Solutions Four Square Controller 5
www.arraysolutions.com Array Solutions Ofc: 972 203 2008
350 Gloria Rd. Fax: 972 203 8811
Sunnyvale, TX 75182
VSWR and Matching
Tuning this unit requires a good Oscilloscope or other instrument that can measure phase and
magnitude. A scope is most useful and we recommend at least a 100-500 MHz scope for good
accuracy. If you have a 30-50MHz scope it will probably be OK.
Hint: Make four wire jumpers 8 inches long with alligator clips to allow you to move coil
taps easily while adjusting the network the first time. Don’t solder the foil taps until you
have the system completely tuned, by replacing the jumpers with the copper foil supplied.
Hook up a signal generator to the input connector, it can be a VSWR antenna analyzer or
rig set to 1 or 2 watts.
Be careful not to put too much power since you can be burned. Tune it to the desired
frequency you intend to use.
First: Tune the normal directional mode tap of the L1-C1 input network.
The goal is to get a fairly good VSWR so that we get some power into the system.
All Antennas and the 180 degree phase line must be connected. Controller set to 1st position - or
default. Tuning the system for good VSWR is a fairly simple procedure and can be done by first
adjusting the tap of the input L network coil for minimum SWR using one of the jumpers you
made. You will also have to adjust C1. If you need more capacitance you may need to try adding
a capacitor by touching it from the input connector side of the coil to ground. If the SWR goes
higher you know you must remove capacitance. If the SWR goes lower, you of course will need to
add capacitance. There are extra ceramic caps included with the system. Repeat this procedure
until you have a good match to your system. Note: These settings will be changed later once you
get everything tuned up so don’t solder any foil taps. We have adjusted the system for a SWR of
less than 1.1:1 at the desired frequency using simulated antenna loads at the factory to give you
a good starting point. Later you will tweak this for a perfect match once everything else is
adjusted.
.
Second: REMEMBER THIS
Don’t get overly finicky about this initial tuning process. It is just to get a “ball park”
setting. You will tweak it again later after the remaining adjustments are made.
Third: Tuning the two Phase shift Networks.
Please review the Theory of Operation section on page 9, and note that each antenna’s physical
characteristics may require different phases and magnitudes on the delayed elements. When it is
stated that the phase should be -224 degrees at .8 of the magnitude of the 0 degree reference
channel, that is based on the model which is made of ¼ WL verticals spaced .25 WL apart. Your
installation may be different if you have sloping elements or other geometrical differences. You
should model your antenna (or have someone model it for you) to derive the correct phase and
magnitudes for the feeders.

Array Solutions Four Square Controller 6
www.arraysolutions.com Array Solutions Ofc: 972 203 2008
350 Gloria Rd. Fax: 972 203 8811
Sunnyvale, TX 75182
Fourth: The L2, C2 -90 to-120 phase shift circuit should be tuned next. (L-network)
Select the 1st default position of your controller switch.
Place scope probes (channel 1) on J4, ANTENNA PORT 1, and trigger the scope on this signal.
Place the channel 2 scope probe on J5, ANTENNA PORT 2.
The probes can be attached to the foil feeding the connector, and the ground leads should be
attached to the same ground point on a ground foil at the connectors or on the connector
mounting screws. Adjust the scope so you get a pattern like that shown in Figure 3 below.
Note that the sine wave on the trigger channel 1 is 8 blocks wide. This is 360 degrees of phase.
To do this use the VARIABLE Time function and stretch the wave so it peaks on 8 blocks. Each
block vertical line is 45 degrees of phase shift and each grid line inside will be 9 degrees of phase
shift. You can see that the lagging sine wave for antenna 2 is adjusted to be about 0.6 X the
amplitude of the 0 degree waveform. Adjust your inductor tap and capacitance to achieve this
approximate waveform. It may change a little as you adjust your next setting, so don’t be too
picky. Mutual coupling will change these patterns as you adjust the system.
Note on your schematic that J5 and J6 are the same phase in the default direction position.
Check J6 to verify it is the same phase and magnitude as J5. If it is not your doing something
wrong. Make sure the controller is in the no 1 position and no relays are pulling in.
Going back and forth from these two phase shift networks will result in a good pattern. If you have
a 3rd scope channel, you can now connect it to J7. Or move your second channel to J7.
Adjust the L3, C3 network for -118 to -225 degrees and magnitude called for in your model.
Figure 3: 90 to 120 degree phase shift adjustment

Array Solutions Four Square Controller 7
www.arraysolutions.com Array Solutions Ofc: 972 203 2008
350 Gloria Rd. Fax: 972 203 8811
Sunnyvale, TX 75182
C3 and L3 comprise the -224 degree network. They take the signal from the 180 degree delay
line and add additional delay along with the ability to adjust the magnitude of the waveform.
Adjust this waveform for the delay and magnitude your model required or approximately as
below. The delayed signal is approx .8 the magnitude of the Channel A reference 0 degree
signal. See Figure 4 below.
Figure 4: -224 degree delay
Now go back and adjust the -111 degree signal, and verify the -224 degree signal has not
changed. Go back and forth until you have the correct phase and magnitudes that your model
requires.
Finally adjust the input VSWR L network L1 and C1 for a 1:1 VSWR
You should be able to tweak it in very well with the vacuum cap and coil tap and achieve a very
low VSWR.
Turn the array by switching the directions with your controller and verify VSWR is relatively
stable. It may vary somewhat. Also re-check the scope patterns, as they should remain the same
but will vary and change output connectors as you steer the array in different directions. Due to
mutual coupling differences the patterns on the scope and VSWR may a small amount. If you see
a large variation there is something wrong. Check all feedlines to your array as well as all the
functions you expect from the schematic. Of course call us with any difficulties.
Now, Tune the Omni Mode tap.
Select the Omni Mode with your controller, and observe the SWR. Tune the ONMI foil tap on the
L-Network coil. You may not be able to achieve a perfect 1.0:1 VSWR in omni mode but it should
be under 1.5:1. This is because the capacitance has been set by the normal 4 square operation,
and is slightly less then desirable. But this should not be an issue in operation.

Array Solutions Four Square Controller 8
www.arraysolutions.com Array Solutions Ofc: 972 203 2008
350 Gloria Rd. Fax: 972 203 8811
Sunnyvale, TX 75182
Front to back optimization technique. WX0B’s trick.
One trick that you can do to get the most of your front to back is to set up a signal source on a
nearby hill or even say 1,000 feet away from your array on the ground. The source can be a
mobile rig, or even a VSWR analyzer set to your intended mid frequency of use.
Locate the source in one of the 4 directions of your array, and make sure it is loud enough to be
40-50 dB over S9 on a good receiver connected to your four square system. You can adjust its
antenna length to achieve this signal strength. Just use a coil of wire in a VSWR analyzer and
string it up in a tree or pole. If it is a mobile unit, adjust the output of the radio to get this signal
level.
Rotate the array so the ”back” of the array is pointing at the signal source. You should be able to
see the signal drop dramatically. But you may be able to improve this further by adjusting the two
delay networks a tiny amount while watching the Signal strength. Move one network for a
minimum S meter dip, and then change the other for more of a dip. Going back and forth you
should be able to create a dip of over 35-45 dB!
Once you are happy with this then again readjust the input matching network for best VSWR.
Congratulations. You now have optimized your Array Solutions Four Square Array Controller.

Array Solutions Four Square Controller 9
www.arraysolutions.com Array Solutions Ofc: 972 203 2008
350 Gloria Rd. Fax: 972 203 8811
Sunnyvale, TX 75182
Theory of operation:
The system consists of four verticals in a square separated by .25 WL (= side of the square)
Quadrature Feeding
The Array Solutions controller can be used to feed all 4 of these verticals in such a way as to
accomplish a quadrature feed to each antenna. Quadrature means fed in 90 degree steps and
with equal drive and current magnitude.
The “rear” element in our diagram above is the one on the closest to us on the axis. It is fed with
1A of current at 0 degrees, the next two elements are diagonally positioned and are fed in phase
with 1A of current at -90 degrees, and finally the “front” element is fed with 1A of current at -180
degrees. The direction of firing is through the diagonal of the 4-square towards the element fed
with -90 degrees current. The array has a forward gain of 5.5 dB over a single vertical.
Note the following diagrams are normalized to 5.5 dB of gain over a single same-type
vertical. Do not confuse 5.5 dBi with real gain, which can be more with full-size quarter-
wave verticals and good ground properties. This is to display the gain over a same type
vertical - ignore the dBi notation and consider it as a dB reference over single vertical.
The take-off angle in this system with this mediocre ground is 23 degrees. But with an excellent
ground radial system and better ground conditions it is possible to lower the angle.
The feed method using an L-network to achieve the required 90 degrees phase shift was
developed by Lewallen, and we refer to it (as in ON4UN’s book) as the Lewallen feed method.
Optimized Feeding
This is probably why you purchased this unit.
Using a phase shift greater than 90 degrees (back element to center elements) and greater than
180 degrees (back element to front element) makes it possible to improve the performance of the
4-square. We developed a system where the phase delay can be adjusted to achieve 90 to 120
degrees (for the center elements) or 180 to 240 degrees (to the front element).
Unlike the hybrid coupler technique where the phase shifts are required to be quadrature (in
90 degree steps and equal current magnitudes) by nature of the concept, our “optimized feed
system” allows the user to optimize the drive current phase shifts and magnitudes since it is
accomplished with variable networks plus (in most cases) a 180 degree phasing line.
Robye Lahlum has developed the mathematics which are published in detail in ON4UN’s book
Low Band DX-ing, edition 4 (an ARRL publication, available June 2005). The systems and the
mathematics make it possible to have absolute control of the exact phase and magnitudes of the
feed currents to each element. Networks can be designed that achieve feed current phase angles
and magnitudes as desired. We are no longer bound to equal current magnitude in each element
and 90 degree phase increments.
Our “optimized feed system” uses a phase shift of -111 degrees to the center elements and -224
degrees to the front element. As explained above the -111 degrees delay is achieved by a simple
L network and the -224 deg. phase sift to the front element is achieved through a 180 deg line,
with, in addition, an L network taking care of the remaining (224-180=) 44 degrees.

Array Solutions Four Square Controller 10
www.arraysolutions.com Array Solutions Ofc: 972 203 2008
350 Gloria Rd. Fax: 972 203 8811
Sunnyvale, TX 75182
Your phase delays and magnitudes may differ. You must model the antenna to get this close.
Later I will suggest a way to optimize the antenna over your ground conditions and mutual
coupling conditions.
See pattern plots below to view pattern differences using the same system, same ground but with
the improved phasing angles. Remember this is normalized to show gain over a single same
type vertical.
We have increased the gain by .66 dB and the front to back radio by 6 dB or more! This can
be easily achieved with your controller by adjusting the 90 degree network for a 111 degree
phase shift and the adding 44 degrees to the 180 degree phase line.

Array Solutions Four Square Controller 11
www.arraysolutions.com Array Solutions Ofc: 972 203 2008
350 Gloria Rd. Fax: 972 203 8811
Sunnyvale, TX 75182
Quadrature Fed Plots

Array Solutions Four Square Controller 12
www.arraysolutions.com Array Solutions Ofc: 972 203 2008
350 Gloria Rd. Fax: 972 203 8811
Sunnyvale, TX 75182
Optimized Fed Plots – More Gain and Front go Back
Specifications
Construction Corrosion resistant NEMA 4X enclosure, weather seals, Amphenol
Teflon SO239s
Power 5 KW CW / 10 KW PEP
VSWR Adjustable for 1:1 perfect match – No dump load
Gain 5.5 dB over single vertical 6.16 dB optimized see theory
Directions 4 directions with an additional Omni-directional feature
Electronic phasing LC network and phase line
Phasing Options Quadrature 90/0/-90 and Optimized 0/-111/-224
Capacitors in networks Temperature stable high current RF capacitors and vacuum caps
Weight and size 15 lbs ~14” x 11” X 8” relay box, 6”x3”x3” controller box
Thank you for purchasing this high quality phasing system.
Many thanks to John, ON4UN for his suggestions to improve this manual.
Other manuals for Four Square
1
Table of contents
Popular Controllers manuals by other brands
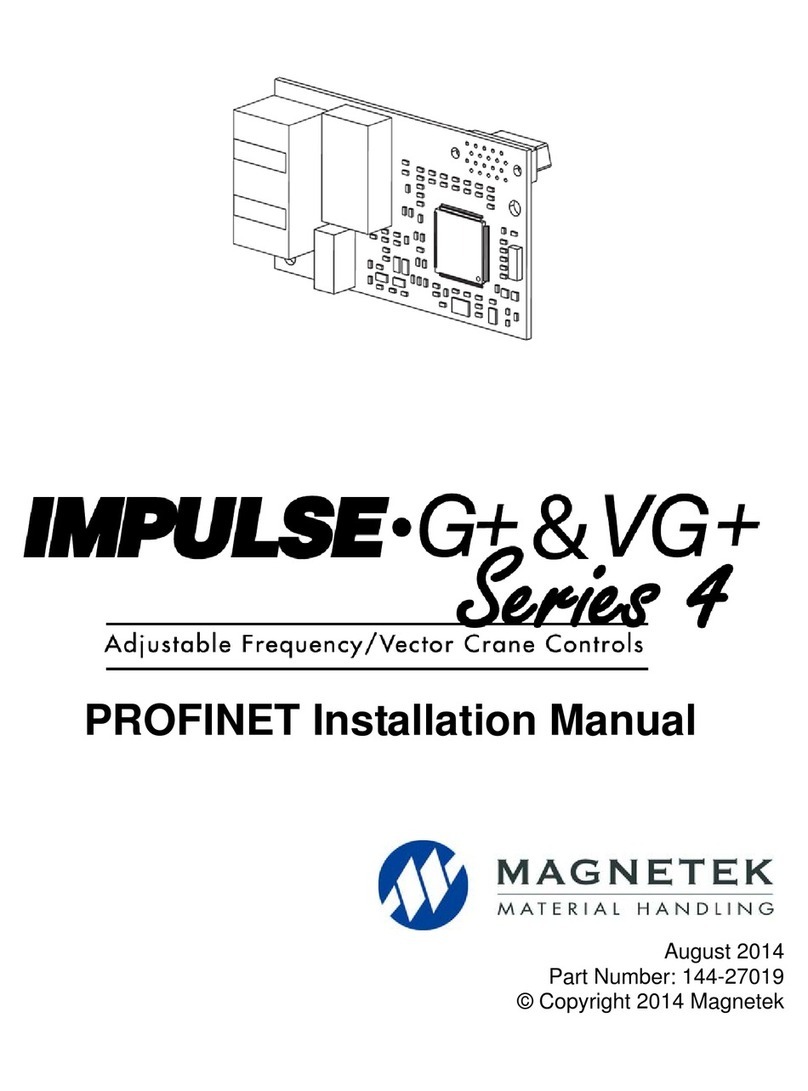
Magnetek
Magnetek IMPULSE G Plus Series 4 installation manual
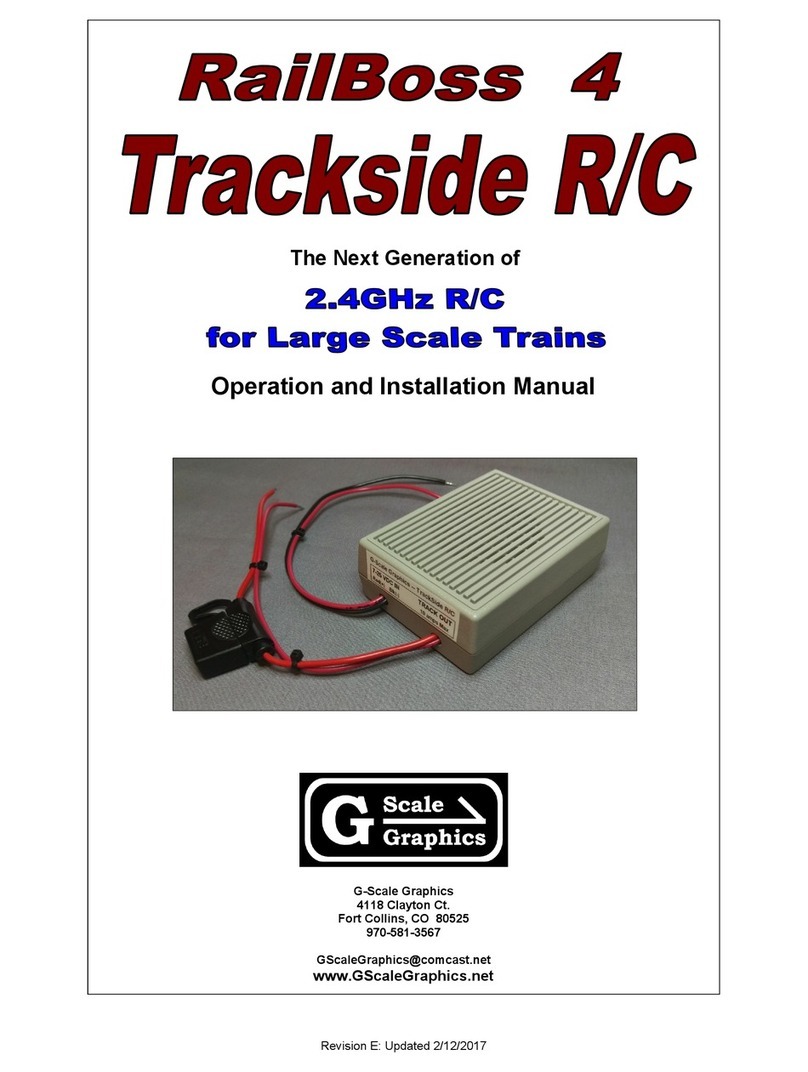
G-Scale Graphics
G-Scale Graphics railboss 4 Operation and installtion manual

Anaheim Automation
Anaheim Automation MDCSL100-050301 user guide
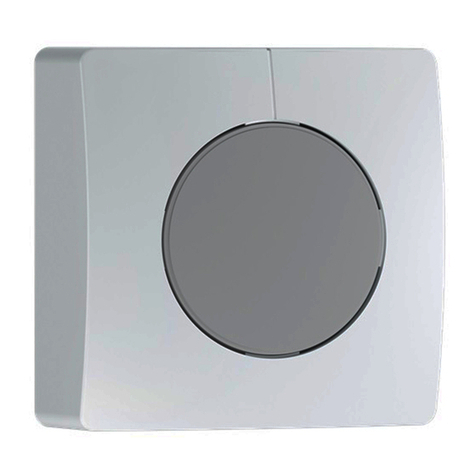
STEINEL
STEINEL NightMatic 5000-3 Information
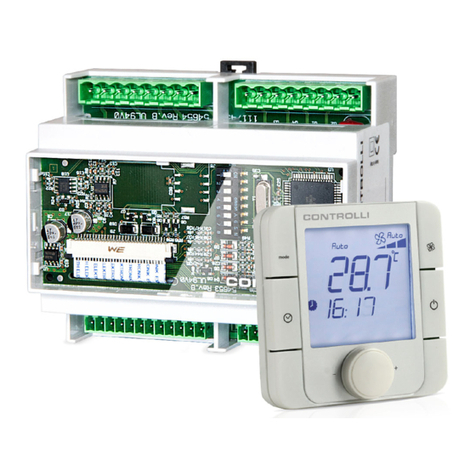
Controlli
Controlli NR9003 Mounting instructions
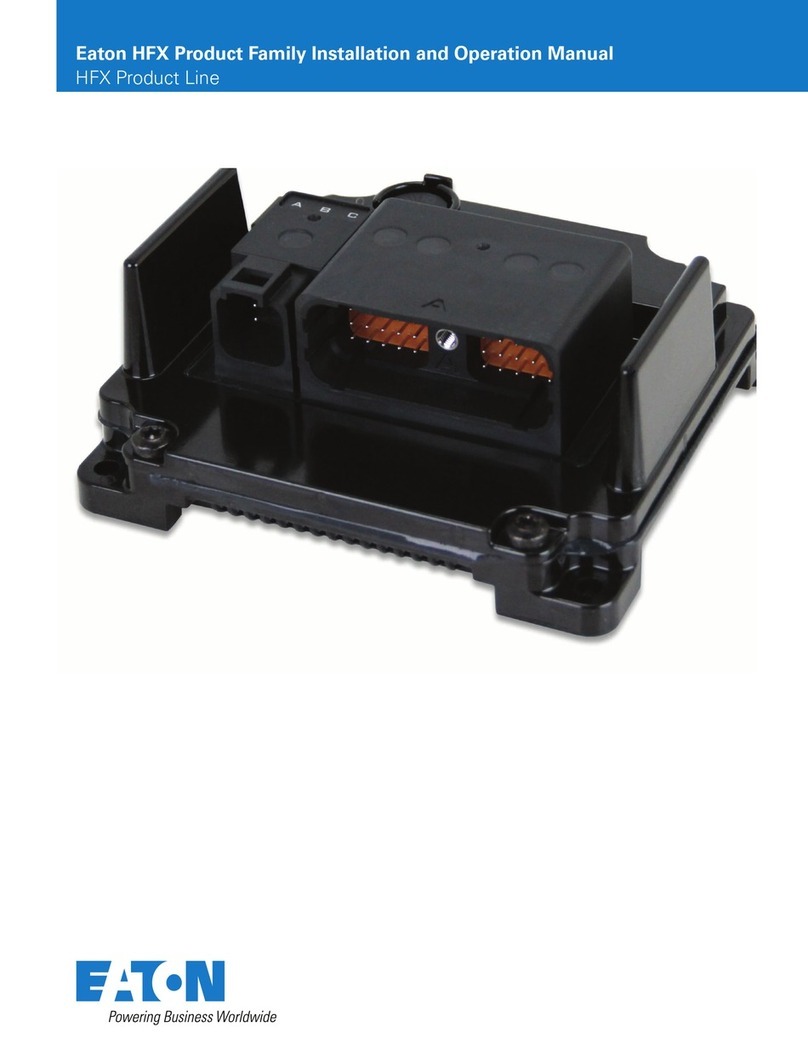
Eaton
Eaton HFX Series Installation and operation manual