OMEX 200 Series User manual

200 Series ECU
Installation Manual
www.omextechnology.com
OMEM200
ENGINE MANAGEMENT SYSTEMS
OMEM200 Installation Manual 2v10


OMEM200 Installation Manual 2v10
3
Contents
1 Introducing Omex Engine Management.......................................................................................................4
2 Standard Functions........................................................................................................................................5
2.1 Crank Position Sensor (CPS)..................................................................................................................5
2.2 Throttle Position Sensor (TPS)................................................................................................................8
2.3 Coolant Temperature Sensor (CTS).......................................................................................................9
2.4 Air Temperature Sensor (ATS)..............................................................................................................10
2.5 Manifold Absolute Pressure (MAP) Sensor...........................................................................................11
2.6 Ignition Coil(s).......................................................................................................................................12
2.7 Shift Light..............................................................................................................................................15
2.8 Tachometer...........................................................................................................................................16
2.9 Fuel Pump.............................................................................................................................................17
2.10 Radiator Fan........................................................................................................................................18
2.11 VTEC Cam Control..............................................................................................................................19
2.12 Full Throttle Gear Shift........................................................................................................................20
2.13 Alt Mode..............................................................................................................................................20
3 Wiring............................................................................................................................................................21
3.1 Semi Assembled Loom Construction....................................................................................................21
3.2 Ready Built Harness..............................................................................................................................21
3.3 ECU Connector.....................................................................................................................................22
3.4 Typical Complete Wiring.......................................................................................................................24

OMEM200 Installation Manual 2v10
4
1 Introducing Omex Engine Management
Thank you for choosing Omex Engine Management. This manual is written to help the user through the
specifics of installing the OMEM200 ECU. It is essential that the user reads the whole of the manual
before attempting to install the system. Incorrect use of the Omex system could potentially lead to
damage to the engine and personal injury. If you have any doubts about fitting these parts then please
contact Omex for help.
Omex may not be held responsible for damage caused through following these instructions, technical,
or editorial errors or omissions. If you have any doubts about fitting these parts or using the software
then please contact Omex for help.

The ECU needs to know engine speed and position in order to supply the correct fuelling and ignition
timing. This is often achieved using the standard sensors, but can involve putting new sensors on the
engine. Engine speed is measured using a pattern of teeth on a crank wheel or flywheel (known as a
trigger wheel). The 200 ECU supports the following patterns;
Ford 36-1 Rover 18-1, 18-1 (distributor ignition only)
Bosch 60-2 Toyota 36-2
Rover K (late) Honda 12+1
If you have any doubt as to whether the trigger pattern on your engine is supported by the 200 ECU,
then remove the sensor, count the pattern of teeth, and contact Omex.
Many older engines do not have a trigger wheel. In this case an external wheel must be fitted. 36-1 is
our preferred pattern. There is a minimum diameter for these wheels dependent on the sensor used,
the trigger pattern, and the engine operating speeds. Typically the larger the trigger wheel diameter the
better. The wheel needs to be mounted on the front pulley. It may also be possible to machine this
pattern into the front pulley wheel, remembering that the pattern must be in a ferrous material for the
sensor to work and if the crank pulley has a damper inbuilt you must mount the trigger wheel onto the
crank side of this damper. Omex can supply general purpose trigger wheels in diameters of 100mm and
140mm.
If installing a trigger wheel of missing tooth type,
ŸAccurately mark TDC.
ŸMount your crank position sensor (CPS) anywhere around the perimeter of the trigger wheel
pointing towards the centre of the wheel such that the sensor can touch the pulley (it will be
spaced out so that it does not touch later). The mount should be strong enough that you can
lean on it and it not move.
ŸMount the trigger wheel so that the missing tooth is approximately 90 degrees after the crank
sensor. (the exact angle can be adjusted in software but for first start of the engine it helps if
you are within 10 degrees of this position). If the crank pulley has a damper inbuilt you must
mount the trigger wheel onto the crank side of this damper.
ŸRun the crank pulley / trigger wheel assembly in a lathe to ensure that the trigger wheel is
exactly central on the pulley.
ŸRefit the pulley / trigger wheel assembly and adjust the sensor-to-wheel gap to 0.3mm-
0.5mm by spacing out the sensor with shims.
ŸRotate the pulley and ensure that the gap does not alter by more than 0.2mm.
Trigger Wheel
OMEM200 Installation Manual 2v10
5
Anti-clockwise rotating engine
at cylinder 1 TDC
90°90°
Clockwise rotating engine
at cylinder 1 TDC
2 Standard Functions
2.1 Crank Position Sensor (CPS)

If machining a trigger pattern into the front pulley then it is usually easiest to machine all of the teeth in,
mount the front pulley, and then remove the tooth pointing at the sensor at 90oBTDC.
There are two types of crank position sensor; MVR and Hall Effect. The Hall Effect type require ignition
switched power to make them work.
2 wire sensors must be MVR. Usually terminal 1 is the signal and terminal 2 the timing ground
3 wire sensors can be either MVR or Hall Effect. If MVR, then usually terminal 1 is the signal, terminal
2 the timing ground and terminal 3 has no connection. If Hall Effect, there is no way of measuring
externally to find which pin has which function; you must find out from the manufacturer.
If the sensor is Hall Effect, a jumper (supplied with the ECU) must be put onto header pins on the ECU
board.
To fit this part you will need to part-disassemble the ECU to gain access to the board. As shown in the
diagram;
·remove screws (1, 2, 3 and 4)
·slide up the end plate (5)
·slide off the lid plate (6)
OMEM200 Installation Manual 2v10
6
Sensor

OMEM200 Installation Manual 2v10
7
Sensor Type Jumper Position
MVR
Hall Effect
JP1
no
jumper

2.2 Throttle Position Sensor (TPS)
The addition of a throttle position sensor allows varying ignition timing with changes in engine load;
similar to a ‘vacuum advance’. This sensor must be placed on the end of the throttle spindle.
Pin-outs
If you have purchased a throttle position sensor from Omex, then the pin-outs for your sensor can be
found on the information sheet with the sensor. If you are using an unknown sensor then you will need
to test the potentiometer to find this information.
Allocate the sensor terminals with numbers 1,2,3. With the sensor disconnected from any wiring use a
multimeterontheresistancesetting(kΩ)tomeasuretheresistancebetweeneachoftheterminalswith
the throttle in an approximate closed position and then with the throttle in an approximate open position
(the absolute position is not important).
Between two of the terminals the resistance will not change as the throttle is opened. This tells us that
the remaining terminal is the signal (Omex orange cable). From the remaining two terminals, one of
them will have a resistance to the signal that is lower when throttle open than when throttle closed, this
is the 5V reference voltage terminal (Omex pink cable). The last terminal must therefore be the sensor
0V (Omex grey cable).
Example;
When the throttle position is moved from closed to open, the resistance does not change between 1
and 3. Therefore, 2 must be the signal (Omex orange). 3 has the lower resistance to the signal with the
throttle open and so must be the 5V (Omex pink), leaving 1 to be the sensor 0V (Omex grey).
OMEM200 Installation Manual 2v10
8
Closed 5200
4300400
123
Open 5200
4004300
123

2.3 Coolant Temperature Sensor
The coolant temperature sensor is required to give the ECU information on the temperature of the
engine‘s coolant, allowing corrections for extreme cold and hot running.
This sensor is optional as this control is only required on engines that are particularly sensitive to coolant
temperature changes.
1 wire Sensor
These sensors are for dashboard coolant gauges and cannot be used with the ECU.
2 wire Sensor
These sensors are correct for use with the ECU. The two wires from the ECU can go either way round
on the terminals.
3 wire Sensor
These rare coolant temperature sensors are a 1 wire sensor and a 2 wire sensor in one package. The
1 wire part is for the vehicle’s dashboard coolant gauge and the 2 wire part is for the ECU. You can find
the correct terminals using a multimeter continuity test. The terminal for the dashboard coolant gauge
has connection to the metal body of the sensor. The two terminals for the ECU connection do not. The
two wires from the ECU can go either way round on the two applicable terminals.
Dashboard Coolant Gauge
A gauge cannot be connected onto the sensor being used for the ECU. The gauge must have its own
separate sensor supplied by the gauge manufacturer.
Retro-fitting
If fitting a sensor to an engine that does not have one as standard, the sensor must be fitted to the
engine side of the thermostat so that it sees the engine’s coolant temperature even when the thermostat
to closed. Omex can supply suitable sensors.
OMEM200 Installation Manual 2v10
9

2.4 Air Temperature Sensor (ATS)
The air temperature sensor is used to give the ECU information on the temperature of the inlet air. This
allows corrections to the ignition timing to suit varying conditions.
This sensor is optional as this control is only required on engines that see large temperature changes,
typically only forced induction engines.
The air temperature should be measured as close to the inlet as possible, preferably in the inlet airbox,
the back of the airfilter, or with forced induction engines, in the inlet plenum. Heat-soak into the body of
the air temperature sensor needs to be minimised so it is preferable when installing the sensor into an
inlet plenum to install it onto a non-metallic section of the inlet. If this is not possible, then a pipe just
before the throttle plate that is insulated from the direct conduction of engine temperature can be used.
The two wires can go onto the sensor either way round.
OMEM200 Installation Manual 2v10
10

2.5 Manifold Absolute Pressure (MAP)
Forced induction engines need a MAP sensor to give the ECU a reading of manifold pressure (boost
pressure). In some cases a MAP sensor is used to measure engine load on NA engines but this is rare.
MAP sensor ratings are absolute rather than boost pressure so 1bar is for normally aspirated (NA)
non-boosted engines, 2bar for up to 1bar boost, 2.5bar for up to 1.5bar boost, and 3bar for up to 2bar
boost.
The MAP sensor will be joined to the inlet plenum by a small diameter tube.
It is not possible to find which wiring terminal has which function externally so this information must
come from the manufacturer of the component.
OMEM200 Installation Manual 2v10
11

2.6 Ignition Coil(s)
The ECU is fitted with two amplified ignition outputs. This allows the following types of ignition;
OMEM200 Installation Manual 2v10
12
yellow
violet
12V from
power relay
Both ignition outputs from the ECU go onto the coil negative terminal. The distributor can be left as
standard but all that is now used are the rotor arm and cap; the advance mechanisms, points etc are
redundant.
These are typically a single pack containing two double-ended coils with 4 HT leads coming directly
from it.
Some engines have wasted spark coil packs that look like 4 individual coils, but are still two double
ended coils and so can still be controlled directly by the ECU. Examples are some Rover K Series and
some small Peugeot engines;
Single Coil and Distributor
Wasted Spark Coil Pack

OMEM200 Installation Manual 2v10
13
The coil should be non-amplified. You can test this by measuring with a multimeter (resistance setting).
Between the 12V terminal and one of the signal terminals (also known as coil negative) a non-amplified
coilwillmeasureapproximately1Ω.AnamplifiedcoilpackwillmeasureseveralkΩ.Amplifiedcoilpacks
can be used if necessary, but are not ideal and the ECU hardware must be modified by Omex to allow
this.
Known wiring
Coil-per-plug
Coil-per-plug ignition coils can be controlled but only with wasted-spark ignition and will require
amplification and the ECU hardware modified.
Ford Type A (early oval connector) 1
2
3
ECU IGN1
+12V supply
ECU IGN2
Violet
Yellow
Ford Type B (later rectangular connector) 1
2
3
ECU IGN2
+12V supply
ECU IGN1
Yellow
Violet
Sagem / Valio (3pin connector) 1
2
3
ECU IGN1
ECU IGN2
+12V supply
Violet
Yellow
Sagem / Valio (4pin connector) 1
2
3
4
ECU IGN1
ECU IGN2
+12V supply
Not used
Violet
Yellow

OMEM200 Installation Manual 2v10
14
Amplified coil-per-plug
ECU IGN1
(violet)
ECU IGN2
(yellow)
trigger pin trigger pin trigger pin trigger pin
chassis
earth
chassis
earth
chassis
earth
chassis
earth
coil cyl 1 coil 3rd
firing
coil 2nd
firing
coil 4th
firing
12V from power relay
trigger pin trigger pin trigger pin trigger pin
chassis
earth
chassis
earth
chassis
earth
chassis
earth
coil cyl 1 coil 3rd
firing
coil 2nd
firing
coil 4th
firing
12V from power relay
ECU IGN1
(violet)
ECU IGN2
(yellow)
Coil-per-plug with external amps
4 way amplifier

2.7 Shift Light
The shift light can be either an LED or a filament bulb of up to 1A current draw. If an LED is used it will
need to be a 12V specific LED or must have an inline resistor fitted. An LED will glow slightly all of the
time then turn on bright at the shift point. Omex can supply shift light LEDs that are fully off normally. If
a filament bulb is used it will be fully off then fully on at the shift point.
OMEM200 Installation Manual 2v10
15
12V
ECU shiftlight
(blue / grey)
12V
ECU shiftlight
(blue / grey)
12V (red)
ECU shiftlight
(blue / grey)
12V
ECU shiftlight
(blue / grey)
12V LED
standard LED
Omex LED
470
Filament bulb max 1 amp

2.8 Tachometer
The tachometer output can directly drive any tachometer that is normally controlled by an ECU. If the
tachometer is from a vehicle where it was originally driven from the coil negative then you may need to
use a ‘tacho driver’ available from Omex to give a voltage spike to trigger the tacho. Some very old
tachos were ‘current’ driven and triggered from coil positive. Omex can supply a convertor box to allow
these to work.
OMEM200 Installation Manual 2v10
16

2.9 Fuel Pump
Although it is normal for the fuel pump to be physically ignition switched, for extra safety it can be ECU
controlled.
When power is first given to the ECU it will turn on the fuel pump output for 2 seconds to prime the fuel
system. When the ECU sees the engine cranking it will turn on the fuel pump output continuously. When
the engine is stopped by turning off the ignition switch the fuel pump output will turn off immediately. If
the engine stops in the event of a crash, the fuel pump output will turn off after 2 seconds.
The fuel pump is not controlled directly by the ECU, it must be controlled through a relay.
OMEM200 Installation Manual 2v10
17
The power supply relay for the coil, can also be controlled by the fuel pump output. Though it is normal
for this to be controlled just by the ignition switch.
Fuel Pump Relay
12V from
battery
12V from
ignition switch
ECU fuel pump
blue / white
Chassis earth
Fuel Pump
85 30
86 87
+
-

OMEM200 Installation Manual 2v10
18
2.10 Radiator Fan
The ECU has two software outputs switchable on coolant temperature values. These would normally
be used for radiator cooling fans. The two outputs may be set to two different temperatures to control
two fans or a single twin speed fan.
The radiator fans are not driven directly by the ECU, they must be controlled through a relay.
Radiator Fan Relay
12V from
battery
12V from
ignition switch
ECU Rad Fan
blue / black
Chassis earth
Fan
85 30
86 87
+
-
Radiator Fan 2 Relay
12V from
battery
12V from
ignition switch
ECU Bay Fan
Yellow / red
Chassis earth
Fan
85 30
86 87
+
-

OMEM200 Installation Manual 2v10
VTECsolenoidsgreaterthan12ΩcanbecontrolleddirectlyfromtheECUoutput,butsomearelower
resistance and will require relay control as they will draw greater electrical currents.
Infinitely variable VTEC (such as Honda i-VTEC, Rover VVC etc) cannot be controlled by this function
and require the Omex 710 ECU.
More than 12 Less than 12
12V from
power relay
12V from
battery
12V from
ignition switch
Relay
Chassis
earth
85 30
86 87
Twin Wire Solenoid
Single Wire Solenoid
12V from
battery
12V from
ignition switch
Relay
ECU VTEC OUT
Yellow / black
85 30
86 87
ECU VTEC OUT
Yellow / black
ECU VTEC OUT
Yellow / black
OMEM200 Installation Manual 2v10
19
2.11 VTEC Cam Control

OMEM200 Installation Manual 2v10OMEM200 Installation Manual 2v10
20
2.12 Full Throttle Gearshift
Full throttle gearshift allows the driver to change gear without lifting the throttle by sending a signal to
the ECU when the gearshift is occurring so that the ECU can retard the ignition to reduce the power
output of the engine, allowing the gears to change.
On a ‘normal’ gearbox that requires clutch depression during the shift, a switch should be placed on the
clutch pedal to signal to the ECU that the shift is occurring. Gearboxes that shift without clutch depression
will require a switch on the lever to indicate the shift occurring.
Pin 10A (white / yellow) must be switched to earth to trigger the full throttle gearshift. Clutch switches
are available from Omex.
Earth
ECU FTG input
White / yellow
2.13 Alt Mode
To activate Alt Mode, a switch is required that supplies 12V to pin 11B (white / orange).
+12v
ECU Alt Mode input
White / orange
This manual suits for next models
1
Table of contents
Other OMEX Control Unit manuals
Popular Control Unit manuals by other brands
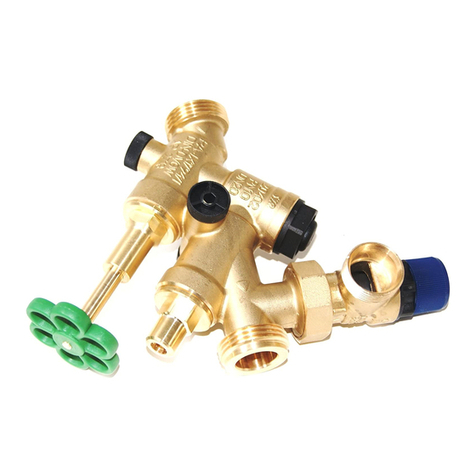
Vaillant
Vaillant 305827 installation instructions
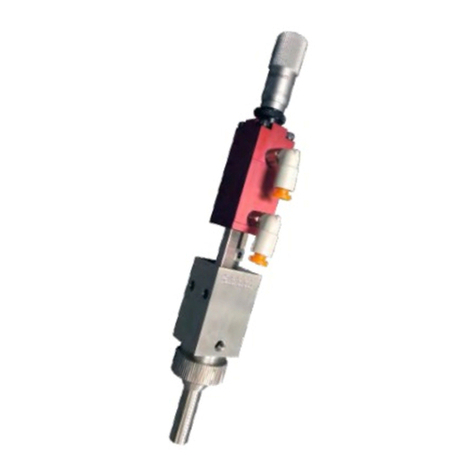
PVA
PVA FCS300 Series Operation manual
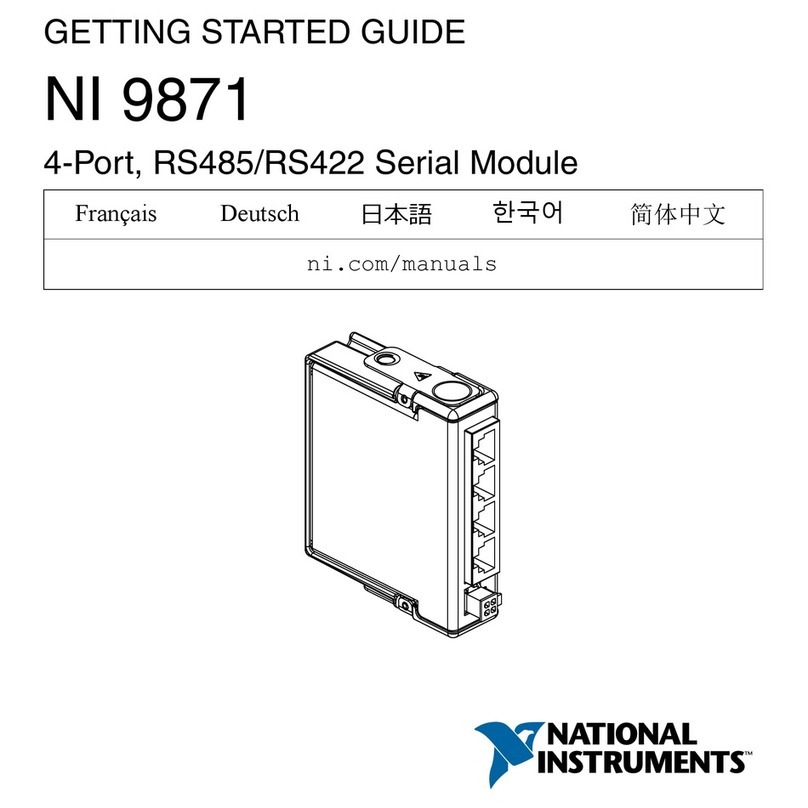
National Instruments
National Instruments 9871 Getting started

Levil Aviation
Levil Aviation BOM manual
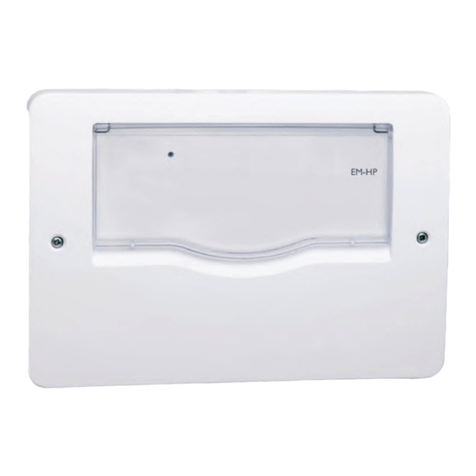
Resol
Resol EM-HP Mounting, connection, operation

IFM Electronic
IFM Electronic Ecomot300 AC2630 operating instructions