Open Date Digi-3-Coder Specifications

Digi-3-Coder
(Hot Foil Printer)
INSTALLATION DETAILS
OPERATOR INSTRUCTIONS
PARTS LISTING
CIRCUIT DIAGRAMS
Designed and manufactured by:
OPEN DATE EQUIPMENT LIMITED
UNITS 8 & 9 PUMA TRADE PARK
145 MORDEN ROAD
MITCHAM
SURREY
CR4 4DG
UNITED KINGDOM
Tel: 0044 (0) 208 655-4999
Fax: 0044 (0) 208 655-4990
Email: [email protected]
Web site: www.opendate.co.uk
Digi-3-Coder (Issue 1.2) 6 October 2005 Page 1

Digi-3-Coder Index
Description Page
Index 2
Safety Instructions 3
Declaration of Conformity 4
Operating Specifications 5
Installation Procedures 6
Standard Frame Installation 7
Pneumatic Installation Details 8
Electrical Installation Details. 9
Fault And Print Relay Connections 10
Low Air Pressure Connections 11
Solenoid Valve Details 12
Getting Started, Operating Instructions
Initial Setting Procedures 13 - 14
Membrane & LED’s Layout 15
Operator Controls 16
System LED’s & Faults 17
Threading Diagram 18
Operator Instructions 19
Mechanical Fault Finding 20
Print Quality Deterioration 21
Technical Information
Main Circuit Board Connections 22
Wiring Details Plug on Printer 23
Connections Box PCB 24
Wiring Details Connection Cable 25
Dip Switch Settings & Explanations 26
Digi-3-Coder Dimensional Drawing 27
Cassette Spare Parts Drawing 28
Cassette Spare Parts Listing 29
Printer Body Spare Parts Drawing 30
Printer Body Spare Parts Listing 31
Connection Box Spare Parts Drawing 32
Connection Box Spare Parts Listing 33
Cylinder Assembly Spare Parts Drawing 34
Cylinder Assembly Spare Parts Listing 35
Recommended Spares Listing 36
Type Holder Details 37
Foil Sensor Instructions 38
Calibration Method 39
Machine Serial No. Identification. 40
Airborne Noise Emissions. 41
Warranty 42
Open Date Group Companies & Agents. 43
Digi-3-Coder (Issue 1.2) 6 October 2005 Page 2

IMPORTANT SAFETY INSTRUCTIONS
1. Read these instructions carefully. Follow all warnings and instructions marked on the product.
2. Always disconnect the printhead and controller from the mains electricity and air supply before
attempting to clean or service it.
3. Never operate the printhead unless it is installed within the mounting frame supplied. When installed
correctly, the gap between the printer and print base should not be greater than 5mm. (see page 7)
4. Do not use the product near water. Never spill liquid of any kind on to the product.
5. Do not place this product on an unstable stand, table or machine. It may fall causing serious damage to
the product or injury to the operator.
6. Never insert objects of any kind into this product through any openings or gaps as they may touch
dangerous voltage points or short circuit parts that could result in fire or electric shock.
7. This product should only be operated from the type of electrical supply as indicated on the side guard of
the printer. (see page 5 & 39)
8. Ensure that the printhead connection cable is fully secured to the printer, with the bayonet connector
fully locked in place. Failure to do this will result in the machine not being properly earthed.
9. Use only the power cable supplied with the product. The cable supplied is three core mains cable,
utilising one wire as a grounding conductor. This must be connected to a suitable earth point at the
electrical supply. This is a safety feature. If any doubt arises in trying to connect the power cable, please
contact the manufacturer or agent who supplied the product.
10. Do not allow anything to rest on the power cable. Do not locate the product where persons will walk on
the cable.
11. If an extension cable is used with this product, make sure that the total ampere ratings of the equipment
plugged into the extension cable does not exceed the extension cable ampere rating. Also make sure
that the total rating does not exceed the fuse rating.
12. Do not service this product yourself as opening or removing guards may expose you to dangerous
voltage points, major burns and other risks. Refer all servicing to qualified personnel.
13. Do not attempt to use to use this product in areas where explosive gases or substances are present.
14. Once the product is under normal working conditions, care must be taken when removing the type
holder as you can easily burn yourself. There is a yellow warning sign on the type holder access door
indicating a danger. Open the door by gripping it at the side. The type holder can get very hot, it should
only be held by its plastic handle. Never touch the metallic parts, as temperatures could be as high as
220 degrees C.
15. Disconnect the product from the electrical and air supply, referring to servicing by qualified personnel
under the following conditions.
a. If the power cable is damaged or frayed.
b. If the air pipes are damaged in any way.
c. If liquid has been spilled into or if the product has been exposed to rain or water.
d. If the product does not operate normally when the operating instructions are followed. Adjust
only those controls that are covered by the instructions. Improper adjustment may result an
damage needing qualified technicians to restore the product to normal operating conditions.
Digi-3-Coder (Issue 1.2) 6 October 2005 Page 3

EC DECLARATION OF CONFORMITY (Passed EMC Tests, September 2005)
We hereby declare that the following machinery complies with the essential health and safety
requirements of the Machinery Directive 98/37/EC, and the Low Voltage Directive 73/23/EEC
and its amendments, and the requirements of the Electromagnetic Compatibility Directive
89/336/EEC and its amendments.
Machine Description: Hot Foil Printer.
Model: Digi-3-Coder
Type: .....................
Serial number: .....................
Manufactured by: Open Date Equipment Limited.
Address Units 8 & 9, Puma Trade Park,
145 Morden Road,
Mitcham,
Surrey. CR4 4DG
United Kingdom.
The following transposed harmonised European standards have been used.
BS EN ISO 12100: part 1, 2003. Safety of machinery. Basic concepts, general principles for
design. Basic terminology, methodology.
BS EN ISO 12100: part 2, 2003. Safety of machinery. Basic concepts, general principles for
design. Technical principles.
EN294: 1992. Safety of machinery. Safety distances to prevent danger zones being reached by the
upper limbs.
BS EN 563:1994. Safety of machinery. Temperatures of touchable surfaces. Ergonomics data to
establish temperature limit values for hot surfaces.
EN60204: part 1, 1997. Safety of machinery. Electrical equipment of machines. Specification for
general requirements.
Emissions Tests
Generic Standard: EN61000-6-3:2001. Including Conducted Emissions, Radiated Emissions,
Harmonics & Voltage Flicker.
Immunity Tests
Generic Standard: EN61000-6-1:2001. Including Electrostatic Discharge, Radiated
Immunity, Fast Burst Transients, Surge Immunity, Conducted RF Immunity, Magnetic Immunity & Voltage
Dips.
FCC Part 15 Verification , Class A. Conducted and Radiated Emissions.
In addition, this machinery has been designed and manufactured in accordance with:-
PD 5304:2000, Safe use of machinery.
A technical construction file for this machinery is retained at the above address.
Signed: ............................................ Date: ...........................................
Name K.F. Wingfield. Position Service Manager
Signing on behalf of the manufacturer.
Digi-3-Coder (Issue 1.2) 6 October 2005 Page 4

Operating Specifications for Digi-3-Coder
Supply Voltage (Autosensed)
Nominal 230v AC, plus or minus 10% tolerance (207 – 253). 50 or 60 Hertz.
Nominal 115v AC, plus or minus 5% tolerance (109 – 121). 50 or 60 Hertz.
Heater
Single Cartridge Heater, 240 Volt AC, 500 Watt. (Part No. HEA 312070)
Normal temperature range: 70ºC to 220ºC, or 158ºF to 428ºF
Thermistor
Model No. USP5362 (Part No. THE 312080)
Output Relay Contacts
Fault Relay:- Rated at 24V DC, 1 amp current.
Print Relay:- Rated at 24V DC, 1 amp current.
(Both relays utilise common, normally open or normally closed contacts)
Input Print Signals
Voltage Free contacts. (microswitch, relay or plc etc.)
Voltage 10 – 30 Volts AC or DC (polarity unimportant)
Microprocessor
PIC Micro-Processor type:-.
Controlled by a specific designed membrane panel with inbuilt switches etc.
The temperature display is seen through a translucent panel on the membrane.
Solenoid Valve Output
24 Volt DC, 80mA current normally. (Part No. VAL 312034)
Air Pressure required
4.0 to 6.8 bar
Air Consumption
231cc @ 6.8 bar free air per cycle.
Foil Capacity
153 Metres (500 feet)
Foil Indexing
2mm to 16mm in 0.1mm increments. (0.078" to 0.625" in 0.005” Increments)
Dwell Time
10 to 2000 milliseconds.
Print Signal Delay
0 to 999 milliseconds. (Indicated by flashing green LED if activated)
Digi-3-Coder (Issue 1.2) 6 October 2005 Page 5

Digi-3-Coder Installation Procedures
Do not connect the mains supply until you have ensured that correct voltage is being
supplied. (See page 5, Operating Specifications)
If the printer is fitted to a stand alone bracket provided by Open Date Equipment Limited,
connect the electrical supply as required. Connect a 6mm air pipe to the solenoid valve. The
air supply should be fitted with an Air Filter Regulator, not supplied by Open Date
Equipment.
Note!
The air supply received must be clean and dry, any moisture may damage the printer.
Procedures
1. Mount the printer into the frame.
2. Ensure the printer is approximately parallel to the print base, and the
clearance under the printer is approximately 5mm. (See page 7)
3. Place and secure the connecting box in a suitable position, ensuring the cable
socket reaches the printer. (see page 8)
4. Connect the two 6mm air pipes (red & black) to the solenoid valve & the
Printer (see page 8)
5. Connect a 6mm air supply pipe from the solenoid valve to a dry air supply,
through an Air Filter Regulator to control the pressure required. (see page 8)
Note!
Ensure all cables and air pipes are properly fed and do not obstruct the substrate or
printer movements.
Connections
Mains Supply (see pages 5, 9 & 24)
Trigger/Print Signal (see pages 5, & 24)
Solenoid Valve (see pages 12 & 24)
Relays (see pages 10 & 24)
Low Air (see pages 11 & 24)
Settings and Calibration
Dip switch Settings (see page 26)
Calibration of Printer (see page 39)
Digi-3-Coder (Issue 1.2) 6 October 2005 Page 6

Digi-3-Coder Standard Frame Installation
Print Centre Line
Cassette Release Catch
Standard Eurocode Frame
Levelling Nuts, both ends
Print Base
Locking Handle
(Li t Up)
Ensure the Nip Roller is ully engaged.
(Rotate Clockwise until it stops)
Positioning Handle
Maximum 5 mm Gap or Sa ety
Digi-3-Coder (Issue 1.2) 6 October 2005 Page 7

Digi-3-Coder
(Fitted with solenoid Valve)
6mm "RED" Nylon T bing
Connecting Box
6mm "BLACK" Nylon T bing
Air Supply, 4 to 6.8 Bar
(6 mm NylonTubing)
Digi-3-Coder Pneumatic Installation Details
Digi-3-Coder (Issue 1.2) 6 October 2005 Page 8

Connecting Box
Digi-3-Coder Electrical Installation Details
(Fitted with solenoid Valve)
Mains Input Cable
Supply 110 230 Volts AC
(Auto sensed)
Digi 3 Coder
Fuse 2amp Anti Surge (Part No. FUS 503512)
ON / OFF Switch
(Double pole)
Cable Socket Assembly
(Part No. CAB 313019)
1.5 Metres Long
Connection Socket
There are 3 spare Cable glands,to allow
connecting of Print Signals,Fault relays
and Air Switches etc.
Digi-3-Coder (Issue 1.2) 6 October 2005 Page 9

Signal Return
Signal Return
Digi-3-Coder Fault and Print Relay Connections
Max 24v DC (1 amp)
Max 24v DC (1 amp)
Signal Return
Digi-3-Coder Individual Relays & Connections
PRINT RELAY
FAULT RELAY
Both Relays are Rated at 24v DC, 1 amp maximum urrent.
onne tion (High going Low) see below:-
Max 24v DC (1 amp)
Linking the Fault and Print relays will a hieve optimum se urity. If the Print swit h is turned off,
or when any fault o urs the relays will hange state. This will break the signal return
Link Wire
Digi-3-Coder (Issue 1.2) 6 October 2005 Page 10

Remove this Link Wire, if you are fitting a pressure switch.
The Digi-3-Coder supp ied, has the Low Air Pressure option disab ed via a ink wire
within the connections box, see picture be ow:-
Free contacts"
Pressure Switch
(In ine with Air Supp y)
"Must have Vo tage
COM
Digi-3-Coder Low Air Pressure Option
Digi-3-Coder Pressure Switch Connections
N/O
Digi-3-Coder (Issue 1.2) 6 October 2005 Page 11

Manual Test Button
Digi-3-Coder Solenoid Valve Details
(Part No. VAL 312034 without fittings)
Voltage 24 Volt C, 80mA Current normally
(See page 24)
Lock Nut
Lock Nut
(Return Stroke)
Adjusting Screw
(Forward Stroke)
Must be clean & ry Air
Presssure range 4.0 to 6.8 bar
Solenoid Valve
Air Flow Restrictor
Air Flow Restrictor
Mains Air Pipe 6mm
(from Air Filter Regulator)
Electrical Connection Socket
Adjusting Screw
6mm Red Pipe to Printer
6mm Black Pipe to Printer
Digi-3-Coder (Issue 1.2) 6 October 2005 Page 12

Digi-3-Coder Initial Setting Procedure
1. Ensure that printing foil and substrate are compatible. If in doubt, contact foil supplier for
assistance.
2. Remove Type Holder from printhead.
3. Ensure that rubber print base is clean, undamaged and securely retained in position
under printer.
4. Set air pressure regulator to approximately 6 bar (90 PSI)
5. Switch Printer on.
6. Set print dwell time to 120 milli-seconds and temperature to 130ºc (266ºF). allowing
3 to 4 minutes for printer to reach working temperature. (See pages 15 & 16)
7. Load type or die into holder, centrally if possible and fasten securely. Make sure that
typeface is clean. (See page 37 )
8. Load type/die holder into printer and close door. If cold, allow 3 to 4 minutes for holder
to heat up before printing.
9. Remove foil magazine and load foil as detailed in this manual. (See page 18)
10. Re-fit foil magazine, ensuring the pinch roller is engaged first.
11. Ensure that PRINT switch is off.
12. Place a sample of substrate material under printer and press TEST button. Inspect
resulting print.
13. Adjust print levelling screws until a light, uniform print impression is achieved. Lock
levelling screws.
14. Adjust foil index for economical use, according to the print height. (See pages 15 & 16)
15. Press the PRINT switch for automatic operation.
Print Orientation(See page 7)
To rotate the printer and therefore turn the overprint through 90 degrees. Turn printer off, and
disconnect the connection cable. Shut off the air supply and remove both 6mm pipes from the
Printer. Unscrew the clamping handle until the location square on the top of the printhead is
clear of the top rails. Turn the printer to the required position, tighten the clamping handle. Re-fit
the air pipes and connection cable.
Temperature Adjustment (See pages 15 & 16)
• Normal setting is about 130ºc. (266ºF).
•
• Should the print not fully adhere to the substrate then a higher setting may be used.
•
• Small, fine detail print generally requires a lower temperature.
•
• Thermoplastic films and especially polyethylene generally require a lower temperature.
•
• Aluminium foils, paper and untreated polyester require a higher temperature.
See page 39 for temperature calibration
Digi-3-Coder (Issue 1.2) 6 October 2005 Page 13

Digi-3-Coder Initial Setting Procedure (continued)
Print Dwell Adjustment(See pages 15 &16)
• Normal setting is about 120 milli-seconds.
•
• Generally, the larger the print, the higher the setting.
•
• Should the print not adhere fully to the substrate, a higher setting may be used.
•
• Remember, the printhead can only operate during the stationary cycle of the web, if
the print time is longer than this the web may break.
•
• Should the dwell time have to be decreased to accommodate higher production
speeds, it may be necessary to compensate by increasing the temperature setting.
Air Flow Controls(See pages 8 &12 )
The airflow restrictors are usually attached to the solenoid valve exhaust ports. They
work by regulating the speed at which air is exhausted from the air cylinder.
Turning the adjusting screws will alter the exhaust airflow and consequently the print
ram velocity (speed), it also affect noise levels.
Increasing the exhaust airflow from the forward stroke of the print ram will increase the
print pressure. Decreasing the exhaust airflow will reduce print pressure and the
resulting print will be lighter.
For higher speed operation, the exhaust airflow from both the forward and return
strokes will have to be increased.
Digi-3-Coder (Issue 1.2) 6 October 2005 Page 14

Digi-3-Coder (Issue 1.2) 6 October 2005 Page 15

Digi-3-Coder Operator Controls
Temperature Button
To adjust the temperature setting, press and hold down the temperature button and use
the up/down arrow keys to increase or decrease the set point. (Required Temperature)
Range:- Minimum 70ºC (158ºF), Maximum 220ºC (428ºF).
In normal operation, temperatures could fluctuate by up to ±3% from the set point.
Default setting: 130°C - 266°F (See page 26 for temperature options).
Print Dwell Button
To adjust the print dwell setting, press and hold down the print dwell button and
use the up/down arrow keys to increase or decrease the value required.
This adjustment controls the time the type/die face is in contact with the substrate.
Higher numbers indicate longer dwell times.
Range:- 10 to 2000 milliseconds. (0.010 – 2 Seconds)
Default settin
g
: 85 ms
Print Delay Button
To adjust the print delay setting, press and hold down the print dwell button and
use the up/down arrow keys to increase or decrease the value required.
This adjustment controls the delay before printing.
Range:- 0 to 999 milliseconds. (0 – 1 Second)
Default setting: 0. ms (if a delay value has been programmed, the led will flash)
Print Switch
Switches the print signal between external trigger (automatic print cycle) and the
test button feature (manual operation).
Note! The Print LED (green) is illuminated when switched for external triggering
(automatic print cycle).
Ribbon Index Button
To adjust the ribbon index setting, press and hold down the print index button and
use the up/down arrow keys to increase or decrease the value required.
This adjustment controls the amount of ribbon indexed, per print.
Range:- 2 to 16mm, in 0.1mm increments.
Default setting: 13.5mm.
Test Button.
Manually operates the printer (will not operate whilst the Print LED is on).
Digi-3-Coder (Issue 1.2) 6 October 2005 Page 16

Digi-3-Coder System LED Faults
“Any fault will disable the print switch and activate the fault relay”
Thermistor LED on
Thermistor open circuit.
The heater is switched off and the internal alarm is sounding.
Heater LED on
Heater is open circuit and the internal alarm is sounding.
Foil Run Out LED on
At end of foil roll, the LED is on, and the internal alarm is sounding.
Type Holder Door Opened, LED “On”
Type holder door is open, the LED is on and the internal alarm is sounding.
Print Button & Test Print Button trigger signals, are disabled.
Low Air Pressure Switch (If connected)
When air pressure is low, the LED is on, and the internal bleeper is sounding.
External Pressure switch required. (Not supplied as standard)
See separate wiring detail.
Digi-3-Coder (Issue 1.2) 6 October 2005 Page 17

Drive Roller
Brake Arm Roller
Ink (pigment) Outside
Pinch Drive Roller
Take Off Mandrel
Rewind Mandrell
assette Roller
assette Roller
Digi-3-Coder Threading Diagram
Digi-3-Coder (Issue 1.2) 6 October 2005 Page 18

Digi-3-Coder Mechanical Fault Finding
FAULT POSSIBLE CAUSE
Insufficient foil pull. Defective stepper motor.
Drive belt is broken.
Drive pulley loose on stepper motor.
Driven pulley loose on bearing housing.
Pinch roller not engaged.
Drive roller damaged or dirty.
Wrong index amount in settings.
Solenoid operates but printer does not. No or low air pressure.
Air pipe damaged.
Dwell time may need to be increased.
Dirty air supply, contaminating pipes etc.
Printer operates but does not print, i.e.
impression but no print. Printing foil exhausted.
Printing foil not being driven through.
Printing foil not suitable for substrate.
Little or no heat.
Little or not enough dwell time.
Printing foil tracks over to one side. Bent spindle on foil magazine.
Brake arm loose.
Pinch roller misaligned with drive roller.
Type not fitted centrally on type holder.
Foil rewind is loose. Green drive belt worn out or dirty.
Green drive belt is not fitted correctly.
Loose cardboard core on rewind mandrel.
Printer is sluggish. Insufficient air pressure.
Flow restrictors wound in too far.
Faulty valve.
Dirty air supply, contaminating pipes etc.
Digi-3-Coder (Issue 1.2) 6 October 2005 Page 19

Digi-3-Coder Operator Instructions
MAGAZINE REMOVAL (See pages 7 & 18)
To remove the foil magazine, slide the catch away from the type holder access door,
hold in place and withdraw the magazine using the two handles.
FOIL THREADING (See page 18)
1. Fit an empty foil core onto the rewind mandrel.
2. Disengage the pinch drive roller.
3. Remove label from a new roll of foil.
4. Fit new roll of foil onto take-off mandrel (note unwind direction as shown on
threading diagram).
5. Thread foil around all rollers as shown on threading diagram. Note, the gloss
side of the foil should face inwards throughout the foil path.
6. Attach end of foil to empty core on rewind mandrel, gloss side facing inwards.
7. Wind foil on a few turn to track and tension it.
8. Engage pinch drive roller.
RE-FITTING FOIL MAGAZINE
Hold the magazine by the two handles, slide onto the locating pins and push to lock in
place. Press the PRINT switch on.
FITTING TYPE/DIE HOLDER
“Never assume that a Type/die holder is cold”
Only pick up a type/die holder by its handle. Ensure that the face of the magnetic catch
is clean. Open the red type holder access door (the alarm will sound continuously),
align the type/die holder within the two side locators and slide in until the magnet
catches on the end plate. Close the door. (Alarm stops sounding)
FOIL FEED ADJUSTMENT (See pages 15 & 16)
This is used to adjust the amount of foil used per print, adjusting the print index button
to achieve the correct index required. A gap of 1 or 2mm is recommended between
each section of used foil.
Digi-3-Coder (Issue 1.2) 6 October 2005 Page 20
Table of contents
Other Open Date Printer manuals
Popular Printer manuals by other brands
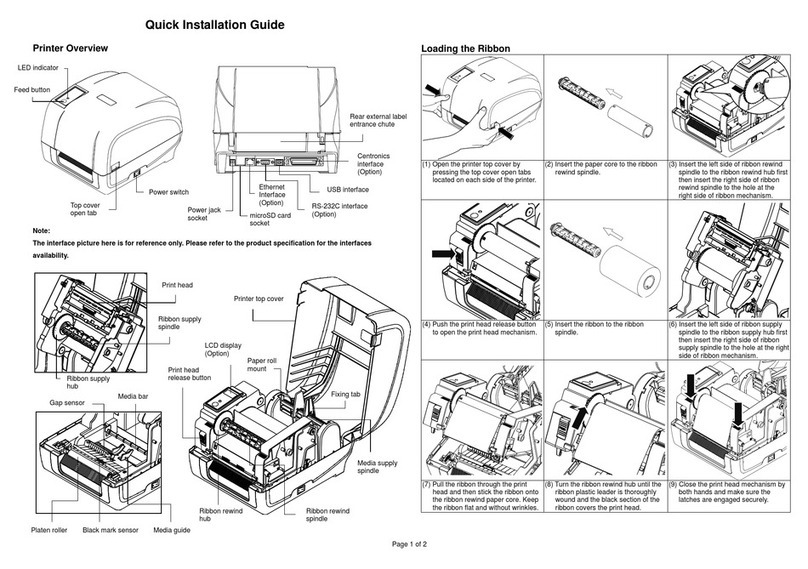
TSC
TSC TA300 Series Quick installation guide
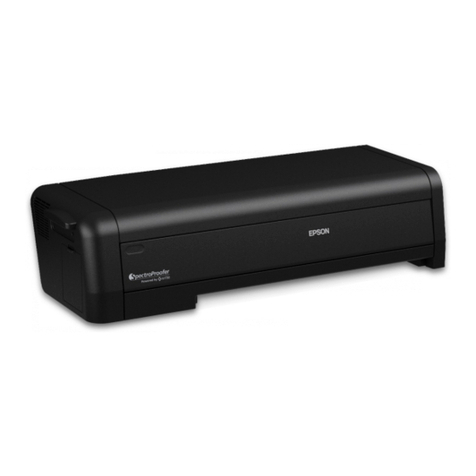
Epson
Epson SpectroProofer Mounter 17" user guide
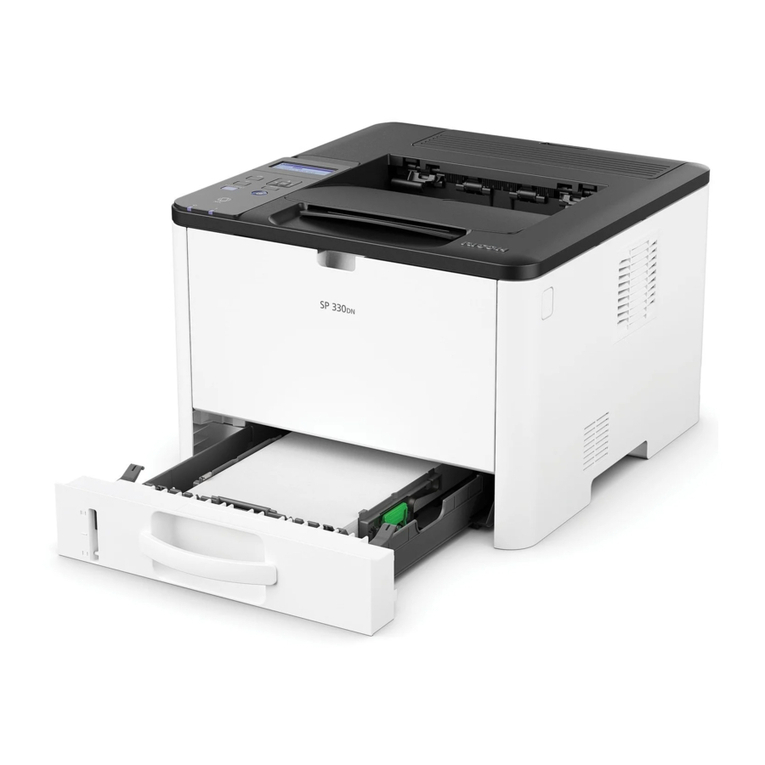
Ricoh
Ricoh SP 330DN Service manual
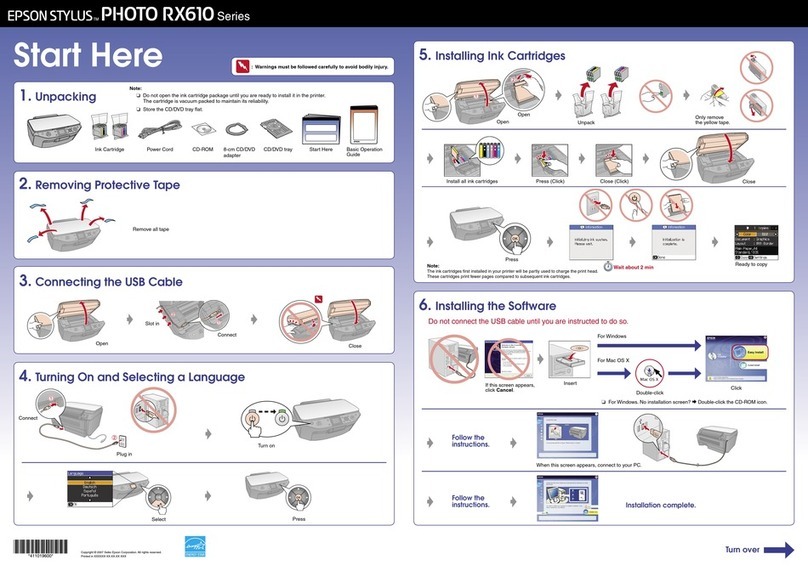
Epson
Epson STYLUS PHOTO RX610 Series Start here
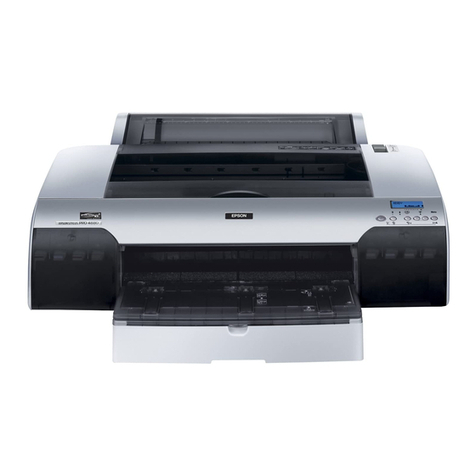
Epson
Epson Stylus Pro 4880 ColorBurst Edition - Stylus Pro 4880... user guide
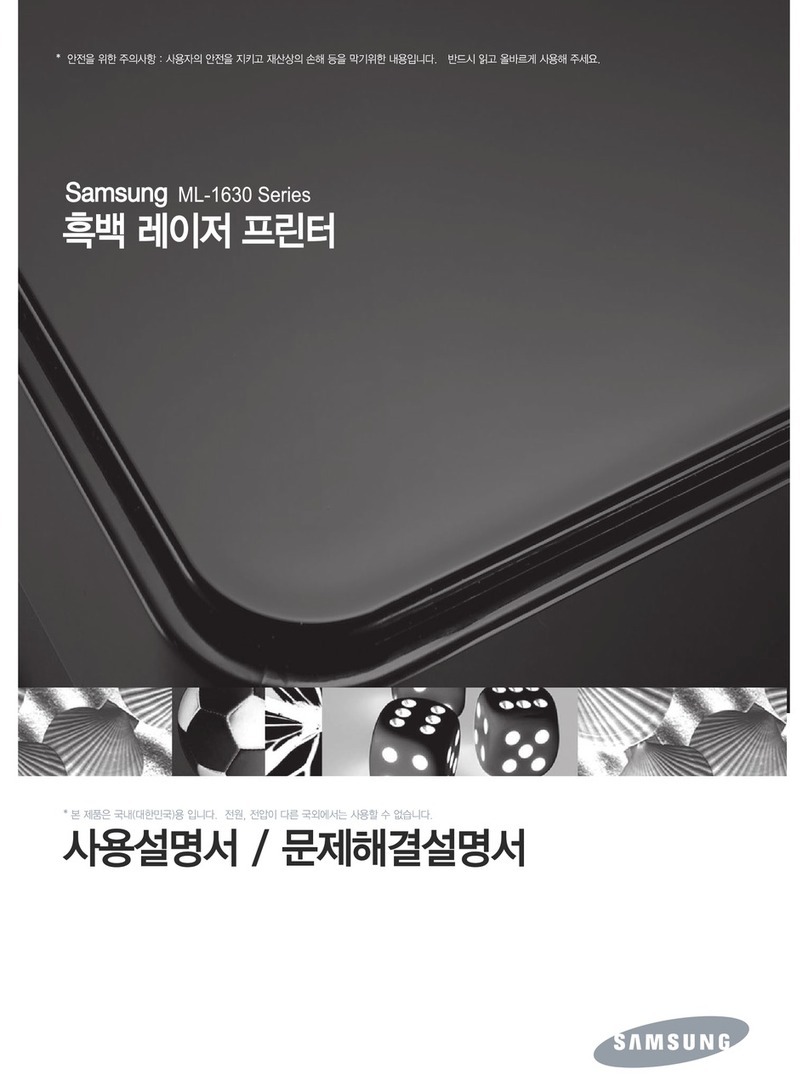
Samsung
Samsung ML-1630W - Personal Wireless Mono Laser... user manual