Ormec Generation III 20 User manual

-~
ARTISAN
®
~I
TECHNOLOGY
GROUP
Your definitive source
for
quality
pre-owned
equipment.
Artisan Technology
Group
Full-service,
independent
repair
center
with
experienced
engineers
and
technicians
on staff.
We
buy
your
excess,
underutilized,
and
idle
equipment
along
with
credit
for
buybacks
and
trade-ins
.
Custom
engineering
so
your
equipment
works
exactly as
you
specify.
•
Critical
and
expedited
services
•
Leasing
/
Rentals/
Demos
• In
stock/
Ready-to-ship
•
!TAR-certified
secure
asset
solutions
Expert
team
ITrust
guarantee
I
100%
satisfaction
All
tr
ademarks,
br
a
nd
names, a
nd
br
a
nd
s a
pp
earing here
in
are
th
e property of
th
e
ir
r
es
pecti
ve
ow
ner
s.
Visit our website - Click HERE

Generation
GenerationGeneration III
IIIIII
Model 20/40 Motion Controllers
Installation & Operation Manual
GN3-040f
Copyright (c) 1990-1994
Ormec Systems Corp.
All rights reserved
19 Linden Park
Rochester, NY 14625
(585) 385-3520
June 27, 1994

‘
Copyright Notice
Copyright 1990, 1991, 1993, and 1994 by Ormec Systems Corp. All rights reserved.
This manual and any software it may describe, remain the exclusive property of
Ormec Systems Corp. No part of either may be reproduced in any form without the
prior written permission of ORMEC.
Warranty
ORMEC extends no warranty with respect to the merchantability or fitness of this
product for any particular purpose. It is the customer’s responsibility to determine
whether it is suitable for the specific application and whether it meets the performance,
reliability, and safety requirements of that application. ORMEC reserves the right to
make improvements to the product as well as this documentation at any time without
notice.
Terms and Conditions of Sale
All products sold or otherwise provided by ORMEC are made available subject to
ORMEC’s published Standard Terms and Conditions of Sale.
UL Recognized Component
Generation III
Model 20 and Model 40 Motion Controllers
are now recognized under the
Component Program of Underwriters Laboratories Inc. in both the United States and
Canada. These new UL Recognized Units may be distinguished from previous units by
the UL trademark symbols shown below.

Generation III Table of Contents
Table of Contents
___________________________________________________________________________________
Welcome .................................................................. 1
General Description .......................................................... 3
2.1 General Description ................................................. 3
2.2 Model 20/40 Features ................................................ 4
Model 20 Model Number Description .................................. 4
Model 40 Model Number Description .................................. 4
2.3 Modular Construction ................................................. 5
2.4 DSP Axis Modules ................................................... 5
DSP Axis Module Model Number Description ............................ 5
2.5 Servodrive Compatibility ............................................... 6
2.6 Servomotor Compatibility .............................................. 6
MAC-A Series Motors ............................................. 6
MAC-B Series Motors ............................................. 6
MAC-C Series Motors ............................................. 7
MAC-E Series Motors ............................................. 7
Installation ................................................................. 9
3.1 Motion Controller Installation ........................................... 9
Receiving & Inspection ............................................ 9
Input Power - TB1 ............................................... 9
System Power Wiring & Interlocks - TB6 .............................. 10
Emergency Stop, No-Fault Interlock & I/O Power - TB6 ................... 11
Integral Discrete I/O - TB2 to TB5 ................................... 13
Extended I/O Connector - J3 ....................................... 15
Pamux I/O Expansion Connector - J3 ................................ 15
Serial Port Connector - J2 ......................................... 16
Keyboard Interface Connector - J8 .................................. 16
MotionDATATM Connectors - J4 & J5 ................................. 17
MotionDATATM Connector Pinout .............................. 17
MotionNETTM Port Connectors - J6 & J7 .............................. 18
MotionNetTM Connector Pinout ................................ 18
RS-422/485 Serial Communications with the MotionNETTM Port ........ 19
ModbusTM Communications .................................. 19
3.2 Memory Cards ..................................................... 19
Memory Disks .................................................. 19
MotionCARDTMs ................................................ 19
3.3 DSP Axis Modules ................................................. 20
Axis Addresses ................................................ 20
Setting Axis Addresses ........................................... 20
Model 20 Unit-ID and Axis Installation ................................. 21
Model 40 Unit-ID and Axis Installation ................................. 22
DSP Axis Interface Connectors - J11 & J12 ............................ 23
SAC-E Series Axis Interface ....................................... 25
SAC-S Series Axis Interface ....................................... 26
Pacer Encoder Axis Interface ....................................... 27
DSP I/O Header Connector - J10 ................................... 27
DSP I/O Header Connector - J10 (Old Version DSP) ..................... 29
page i GN3-040

Generation III Table of Contents
DSP Sensor Header Connector - J10 (for earlier model DSP Axis Modules) ..... 31
DSP Axis Module Configuration Jumpers .............................. 33
3.4 Video Display Adapter .............................................. 37
Analog Monitor Connector - CN1 .................................... 37
Digital Monitor Connector - CN2 ..................................... 38
Video Adapter VGA Installation ..................................... 38
Video Adapter Monochrome Installation ............................... 39
Video Adapter EGA Installation ..................................... 39
MDA/EGA Connector - J1 ......................................... 40
Video Adapter Installation ......................................... 40
3.6 GN3-422 Serial Communications Adapter ................................ 41
Device Configuration - Factory Default Settings Summary .................. 41
Device Configuration - Port 1 & Port 2 ................................ 41
Port Enable/Disable - Switches Port 1 & Port 2 position 8 .................. 42
Interrupt Request ................................................ 42
Driver Enable .................................................. 42
RS-232 and RS-422/485 Configuration ................................ 43
DB-9 Pin Description ............................................. 44
Use with the ITM-270s and/or AND-Series Alphanumeric Displays ............ 44
Device Configuration - Switches S1 & S2 .............................. 44
Port Enable/Disable - Switches S1 & S2, Pin 8 .......................... 45
Interrupt Request ................................................ 45
Driver Enable .................................................. 45
RS-232 and RS-422/485 Configuration ................................ 45
DB-9 Pin Description ............................................. 46
Use with the ITM-270s and/or AND-Series Alphanumeric Displays ............ 46
3.8 GN3-232 Serial Communications Adapter ................................ 47
Device Configuration - Header JP1 .................................. 47
Connector Pin Assignments ....................................... 47
Operation ................................................................. 49
4.1 Powerup ......................................................... 49
4.2 System Status LEDs ................................................ 50
4.3 Initial Configuration ................................................. 52
Getting Started ............................................................. 53
5.1 Test Run Preparation ............................................... 53
Motion Controller Checks ......................................... 53
Servomotor Checks .............................................. 54
Apply Control Power ............................................. 54
5.2 MotionPROTM Servo Development Software ............................... 54
5.3 Test Running Your System ........................................... 54
Product History ............................................................. 55
6.1 Model 20/40 (GN3-20 & GN3-40) History ................................. 55
6.2 DSP Axis Module (GN3-AQ & GN3-A2) History ............................ 56
Specifications .............................................................. 59
7.1 General Specifications .............................................. 59
7.2 Power Specifications ................................................ 59
Power Requirements ............................................. 59
Outgoing Power ................................................ 60
7.2 Battery Specifications ............................................... 62
7.3 Interface Specifications .............................................. 62
GN3-040 page ii

Generation III Table of Contents
Serial Port - J2 ................................................. 62
MotionDATATM Interface J4 & J5 ..................................... 62
MotionNETTM Interface J6 & J7 ..................................... 62
DSP I/O Header - J10 ............................................ 63
DSP Axis Interface Connector - J11 &J12 .............................. 65
7.4 Mechanical and Environmental Specifications .............................. 66
Terms & Mnemonics ........................................................ 67
APPENDIXES
A Model 20/40 Installation Diagram A-1
B System Wiring Diagrams
System Wiring with S-Series Servodrive(s) B-1
System Wiring with E-Series Servodrive(s) B-2
C Model 20/40 Interface Diagrams
Power Panel Layout Diagram (Model 20/40 - Top View) C-1
I/O Panel Layout Diagram (Model 20/40 - Front View) C-2
Interface Panel Layout Diagram (Model 20 - Bottom View) C-3
Interface Panel Layout Diagram (Model 40 - Bottom View) C-4
Integral Discrete I/O and Interlock Interface Schematics C-5
Extended Discrete I/O (or Pamux Interface) Schematics C-6
MotionNET and Serial Port Interface Schematics C-7
MotionDATA Interface Schematic C-8
D DSP Axis Module Interface Schematics
Axis A Input Circuitry D-1
Axis A Output Circuitry D-2
Axis B Input Circuitry D-3
Axis B Output Circuitry D-4
Component Location Diagram D-5
Axis A Input Circuitry (Old version DSP) D-6
Axis A Output Circuitry (Old version DSP) D-7
Axis B Input Circuitry (Old version DSP) D-8
Axis B Output Circuitry (Old version DSP) D-9
Component Location Diagram (Old version DSP) D-10
E DSP Interface Cables & Accessories
CBL-AE/NN E-Series Axis Interface Cable E-1
CBL-AS/NN S-Series Axis Interface Cable E-2
CBL-AET/NN E-Series to Terminal Block Axis Interface Cable E-3
CBL-AST/NN S-Series to Terminal Block Axis Interface Cable E-4
TBC-D25/NN Axis Terminal Block E-5
CBL-AT/NN DSP to Axis Terminal Block Cable (Old version DSP) E-6
CBL-AR3/NN DSP Axis Terminal Block Cable (ver. 3.0 and later) E-7
CBL-QE25/NN EDR-25S Pacer Encoder Axis Interface Cable E-8
CBL-DSP-IO/NN DSP I/O Cable & Terminal Block E-9
CBL-DSP-TB/NN DSP Sensor Terminal Block & Cable (Rev A) E-10
CON-2Q DSP Axis Interface Connector E-11
page iii GN3-040

Generation III Table of Contents
F Serial and I/O Interface Cables
CBL-SER/PC Serial Coil Cord to IBM-PC F-1
CBL-SER/AT Serial Coil Cord to IBM-AT F-2
CBL-MOD8/NNN Shielded 8-wire modular cable F-3
CON-MOD8-ITM Connector from CBL-MOD8 to ITM-270 F-4
CBL-ITM-PWR/NN ITM-270 Power Cable F-5
CBL-EIO/NNN Extended I/O Cable F-6
CBL-DIO/N Extended I/O Cable to MIO-002-24 I/O Rack F-7
CBL-422-ITM/NNN Cable from GN3-422 to ITM-270 F-8
CON-422-MOD8 Connector from GN3-422 to CBL-MOD8 F-9
CBL-422-TL/NNN Cable from GN3-422 to Tinned Leads F-10
CBL-ITM-TL/NNN Cable, ITM-270 to Tinned Leads F-11
CON-MOD8-TB Connector, CBL-MOD8 to Terminal Block (Old version) F-12
CON-MOD8-TB2 Connector, CBL-MOD8 to Terminal Block F-13
G Motor and Encoder Interface Cables
CBL-SMACE/NN Encoder Cable, MAC-E Series Motors G-1
CBL-SMAC/NN Encoder Cable, MAC-S Series Motors G-2
CBL-SMAC1/NN Motor Cable for E007-015, A010-015 & B025-080 G-3
CBL-SMAC2/NN Motor Cable for MAC E016-030 & A030-055 G-4
CBL-SMAC3/NN Motor Cable for MAC E002-003 & B010-020 G-5
CBL-SMAC4/NN Motor Cable for MAC A110 G-6
CBL-SMAC5/NN Motor Cable for MAC B110 G-7
CBL-SMAC6/NN Motor Cable for MAC B200, B330 & C290 G-8
CBL-SMAC7/NN Motor Cable for MAC C410 & C560 G-9
CBL-SMACF/NN Motor Fan Cable for MAC-C560 G-10
H Model 20/40 Internal Wiring
Model 20/40 Internal Wiring H-1
Model 20/40 Motherboard Locators H-2
Model 20/40 Internal MotionDATA Cabling H-3
Memory Disk Installation H-4
GN3-040 page iv

Generation III Welcome
Chapter 1
Welcome
___________________________________________________________________________________
1.0 Welcome
This manual tells you about ORMEC’s Generation III Model 20 & 40 motion
controllers and accessories... providing a detailed description of the Generation
III hardware and information for installing, operating and "getting started" with
your new Generation III motion control system.
The manual is divided into the following chapters:
Chapter 1 Welcome introduces you to this manual and its organization.
Chapter 2 General Description provides an overview of the Generation III
product family. It includes descriptions of the Model 20 & 40
Motion Controllers, the DSP Axis Modules and compatible
servomotors and servodrives.
Chapter 3 Installation provides instructions on installing your unit. It also
provides a complete hardware description of the Generation III
controller interfaces, including detailed information on each
interface to the unit.
Chapter 4 Operation explains the powerup and initial configuration
approach utilized by Generation III.
Chapter 5 Getting Started provides detailed instructions on how to run
your Generation III unit for the first time.
Chapter 6 Product History provides a chronological revision history for
the Model 20/40 Motion Controllers and DSP Axis Modules.
Chapter 7 Specifications provides detailed specifications for the product.
These specifications include environmental, mechanical and
electrical interface specifications as well as references to the
interface schematics in the Appendixes.
Chapter 8 Terms & Mnemonics provides definitions for terms specific to
motion control and/or ORMEC’s motion control products.
Appendixes Appendixes contain detailed drawings which document the
Generation III dimensions, system interface, DSP Axis Module
interface, as well as associated interface cables and
accessories. See the Table of Contents for details.
GN3-040 page 1

Generation III Welcome
NOTE: This manual concentrates on providing Generation III controller
hardware and cabling documentation. Detailed information on ORMEC’s
MotionBASIC®programming language is found in the on-line MotionBASIC®
Hypertext Software Manual. A diskette containing the MotionBASIC®
Hypertext Software Manual software is included at the end of this manual. A
hard copy is included in the MotionPROTM manual.
page 2 GN3-040

Generation III General Description
Chapter 2
General Description
___________________________________________________________________________________
2.1 General Description
The ORMEC Generation III Model 20 & 40 Motion Controllers are industrially
hardened computers designed especially for high performance control of
automation using servomotors. They are fully compatible with ORMEC’s lines
of brushless servomotors and drives.
At the heart of both the Model 20 and 40 is a 12-Mhz Intel 80C186 main
processor. It is interfaced through dual-ported "shared memory" to DSP Axis
Modules which are controlled by Texas Instruments Digital Signal Processors
operating at 40 Mhz. This powerful architecture provides the foundation for
general purpose motion control programmed in ORMEC’s industrialized
superset of Microsoft BASIC called MotionBASIC®. The combination of a main
processor from Intel’s premier family of microprocessors and Digital Signal
Processors for axis control provides speed and performance while maintaining
the ease-of-use associated with interpreted BASIC.
The Model 20 provides two PC-AT style I/O slots and is designed for systems
which have between 11/2 and 4 axes of motion control. For 11/2 to 2 axis
systems, the second slot can be used for various communications options such
as a video controller, a PLC network interface or additional serial interfaces.
The Model 20 can provide 21/2 to 4 axes of control for many applications.
Examples of this are systems interfaced via ModbusTM or an MMI-840 Industrial
Terminal, which provides an 8-line by 40-character display.
The Model 40 provides four PC-AT style I/O slots and is designed for systems
which have between 21/2 and 8 axes of motion control.
Generation III motion controllers provide electronic gearing for a virtually
unlimited number of servomotors using ORMEC’s proprietary MotionDATATM
communications capability. This feature can be used to either closely
coordinate the motion of multiple servomotors with each other, or coordinate
some number of servomotors with the motion of an external pacer encoder.
GN3-040 page 3

Generation III General Description
2.2 Model 20/40 Features
• 80C186, 16-bit CMOS high integration microprocessor operating at 12 Mhz
• optional 80C187 math co-processor
• powerful MotionBASIC®programming with hypertext on-line manual
• powerful and easy to use MotionPROTM motion programming environment
on an IBM-PC or compatible
• 16-bit IBM-PC/AT style backplane for DSP Servo Modules and expansion
boards; Model 20 and 40 have 2 and 4 slots respectively.
• RS-232 Serial Port for program development and troubleshooting
• RS-422/485 communications port for either MotionNETTM or auxiliary serial
communications
• integral Watchdog Timer and Emergency Stop circuitry
• 22 built-in diagnostic LEDs
• dual PCMCIA standard memory card slots are standard on the Model 40
and optional on the Model 20
• 16 discrete I/O points for machine control use Opto-22 style modules
• optionally add 24 TTL level I/O points which are compatible with Opto-22
style I/O racks or the Opto-22 Pamux system
• Opto-22’s Pamux I/O system provides a combination of up to 512 optically
isolated digital and 12-bit analog I/O points
• IBM-PC/AT compatible keyboard interface is standard on the Model 40 and
optional on the Model 20
• optional EGA or monochrome video adapter for Operator Interface
• optional single or dual-channel RS-422 Serial Interfaces
2.2.1 Model 20 Model Number Description
GN3-20/1 Generation III Model 20, 115 VAC Input
Options:
1) for 230 VAC input, change the /1 to a /2
2) to add a math co-processor, add an M
3) to add an absolute encoder backup battery, add a B
4) to add MotionCARD/Memory Disk Support, add a C
5) to add an IBM/PC-AT Keyboard Interface, add a K
6) to add an extended I/O (Pamux) Interface, add an I
GN3-20/2MBCKI Generation III Model 20 with all options
2.2.2 Model 40 Model Number Description
GN3-40/1 Generation III Model 40, 115 VAC Input
Options:
1) for 230 VAC input, change the /1 to a /2
2) to add a Math co-processor, add an M
3) to add an absolute encoder backup battery, add a B
4) to add an extended I/O (Pamux) Interface, add an I
GN3-40/2MBI Generation III Model 40 with all options. Note that
MotionCARD/Memory Disk Support
and a
Keyboard
Interface
are standard.
page 4 GN3-040

Generation III General Description
2.3 Modular Construction
• compact panel mountable steel enclosure (19.5"h x 6.0"w x 10.5"d)
• industrially hardened switching power supplies use either 115 or 230 VAC
power and include a built-in switch/circuit breaker as well as a line filter for
noise immunity
• isolated 24 VDC power supply for optically coupled discrete I/O is standard
2.4 DSP Axis Modules
There are two models of DSP Axis Modules including a dual axis unit, and a
single axis unit with an auxiliary pacer encoder interface. They both use a 40
Mhz Texas Instruments Digital Signal Processor (DSP) to provide axis control
algorithms. The DSP is interfaced to the main processor through a dual-port
RAM shared memory interface for maximum speed and flexibility. DSP Axis
Module features are overviewed below:
• Texas Instruments TMS-320C25 DSP operating at 40 Mhz
• direct digital loop control with up to 5 Khz servo update rates provide wide
loop bandwidth for high positioning accuracy and response
• quadrature feedback 4x decoding with positioning rates to 1.2 MBit per
second
• position, velocity or torque mode control
• total elimination of analog drift errors and extremely quiet loop operation
using direct digital processing of both position and velocity loops with 32 bit
intermediate calculation accuracy
• software controlled position, speed, and current limits
• velocity and acceleration feedforward for minimum tracking errors and
response times
• fully compatible with ORMEC torque mode servodrives through the
individual Axis Interface Connectors
• pacer encoders for electronic gearing are interfaced through any of the DSP
Axis Modules’ interface connectors
• proprietary MotionDATATM communications from DSP to DSP allows tightly
coordinated multi-axis motion
• servodrive remote enable and reset functions are provided by optically
coupled outputs
• open feedback wire detect provided on all differential quadrature feedback
inputs
• failsafe servodrive alarm detection using optically isolated input
• servodrive alarm decoding is provided by three optically isolated inputs
• shared memory data interface to main processor
• writable control store for DSP program storage is loaded from the main
processor at powerup
2.4.1 DSP Axis Module Model Number Description
GN3-DSP-AQ Single Axis DSP Module with Pacer Encoder Interface
GN3-DSP-AQ/A Single Axis DSP Module with Pacer Encoder Interface
with 4-channel 12-bit A/D converter option
GN3-DSP-A2 Dual Axis DSP Servo Control Module
GN3-DSP-A2/A Dual Axis DSP Servo Control Module with 4-channel
12-bit A/D converter option
GN3-040 page 5

Generation III General Description
2.5 Servodrive Compatibility
ORMEC’s SAC Series current mode servodrives provide the following features
and benefits:
• operation on unisolated standard line voltages of either 115 or 230 VAC
• wide range of output power from 50 watts to 6.1 kilowatts
• high peak torque (current), typically three times rated current for a few
seconds and twice rated torque for up to a minute
• wide current loop bandwidth for high positioning accuracy and response
• safety and diagnostic protection features include servo bus overvoltage,
undervoltage, overload, overcurrent, open phase detection, loss of feedback
detection, main circuit breaker trip, excess regeneration or drive CPU failure
• diagnostics provided by a seven segment LED Alarm Indicator with codes
transmitted to the DSP Axis Module through the Axis Interface Cable
• fully compatible with our MAC Series AC Brushless Servomotors
2.6 Servomotor Compatibility
The MAC Series AC Brushless Servomotors provide exceptional performance
as overviewed below:
• continuous torque from 1.6 lb-in to 560 lb-in RMS, conservatively rated
• peak torque from 4.2 lb-in to 935 lb-in
• maximum speeds from 1,500 to 4,500 RPM
• high torque inertia ratios of the motors mean more delivered power for high
performance applications
• durable construction includes no brushes, high thermal efficiency frame and
rugged bearings
• built in position transducer, with up to 24,000 counts per revolution
• low torque ripple, particularly compared with other brushless motors
2.6.1 MAC-A Series Motors
• Maximum Speed: 4,000 RPM
• Continuous stall torques: 10 to 110 lb-in
• Peak Torques: 26 to 257 lb-in
• Peak Acceleration: greater than 50,000 rad/sec2(even the largest unit)
• Rated Power: 0.43 to 4.2 HP
• Position Encoder Resolution: 6,000 cts/rev (1500 linecount)
• compatible S-Series servodrives use three phase 230 VAC incoming power
• Optional multi-revolution absolute encoders available
2.6.2 MAC-B Series Motors
• Maximum Speed: 2,500 RPM
• Continuous stall torques: 10 to 330 lb-in
• Peak Torques: 26 to 675 lb-in
• Peak Acceleration: up to 28,888 rad/sec2(largest unit is 5,315 rad/sec2)
• Rated Power: 0.21 to 6.1 HP
• Position Encoder Resolution: 24,000 cts/rev (6000 linecount)
• compatible S-Series servodrives use three phase 230 VAC incoming power
• Optional multi-revolution absolute encoders available
page 6 GN3-040

Generation III General Description
2.6.3 MAC-C Series Motors
• Maximum Speed: 1,500 to 2,000 RPM
• Continuous stall torques: 290 to 560 lb-in
• Peak Torques: 570 to 945 lb-in
• Peak Acceleration: up to 4,488 rad/sec2(largest unit is 4,337 rad/sec2)
• Rated Power: 4.1 to 8.2 HP
• Position Encoder Resolution: 24,000 cts/rev (6000 linecount)
• compatible S-Series servodrives use three phase 230 VAC incoming power
• Optional multi-revolution absolute encoders available
2.6.4 MAC-E Series Motors
• Maximum Speed: 4,000 or 4,500 RPM
• Continuous stall torques: 1.6 to 23 lb-in
• Peak Torques: 4.2 to 59 lb-in
• Peak Acceleration: up to 62,000 rad/sec2(largest unit is 17,900 rad/sec2)
• Rated Power: 0.07 to 0.9 HP
• Position Encoder Resolution: 6,000 cts/rev (1500 linecount)
• Compact & inexpensive
• compatible E-Series servodrives use single phase incoming power at 115 or
230 VAC (depending on model)
• Optional multi-revolution absolute encoders available
GN3-040 page 7

Generation III General Description
This page is intentionally left blank.
page 8 GN3-040

Generation III Installation
Chapter 3
Installation
___________________________________________________________________________________
3.1 Motion Controller Installation
3.1.1 Receiving & Inspection
ORMEC Motion Controllers and their associated accessories are put through
rigorous tests at the factory before shipment. After unpacking, however, check
for damage which may have been sustained in transit. The bolts and screws
should all be tight, and motor output shafts should rotate freely by hand. Check
the motion controller and any of the accessories for bent or broken components
or any other physical damage before installing.
3.1.2 Panel Mounting & Environment
Panel mounting data is available in the Specifications Section and Appendix A.
The motion controller’s environment should be maintained as follows:
• Temperature should be between 0 and 55C.
• If the electrical panel is subjected to vibration, mount the unit on shock
absorbing material.
• Avoid use in corrosive atmospheres which may cause damage over time.
• Select a location with minimum exposure to oil, water, hot air, high
humidity, excessive dust or metallic particles.
• The proper mounting orientation for the motion controller is vertical on a
panel using the mounting holes (4) on the base plate.
3.1.3 Input Power - TB1
Motion Controllers are available to operate on either 115 VAC or 230 VAC
power (50/60 Hz). A servodrive control power output is provided at terminals r
and twhich is interlocked with the integral switch/circuit-breaker on the top of
the unit. Use of this feature as illustrated in Appendix B eliminates the need
for additional switches and/or circuit breakers, and assures that servodrive
power will be disabled whenever power is removed from the Motion Controller.
To use this feature, the input voltage selected must match the voltage for
the selected servodrive’s control power. All ORMEC servodrives are
GN3-040 page 9

Generation III Installation
available with 230 VAC control power; some of the lower power E-Series are
also available with 115 VAC control power.
Input power connections are made on terminal block TB1, located on the top of
the unit. The label near TB1 indicates the input voltage of the unit. Copper
wire with an 80oC temperature rating, 10 AWG maximum, is recommended for
terminal block TB1 wiring. The maximum terminal block screw torque is 5 in-
lbs. Connections to TB1 are described below:
_________________________________________________________________________________
Symbol Name Description
L1, L2 Input Power Single-phase 115 or 230 VAC, +10%, -15%, 50/60 Hz, with a switch and two 10 amp
circuit breakers (one in each line). In most installations, these terminals would be
wired with 14 gauge wire. The maximum continuous input power requirement of the
Model 20/40 is 175 watts. Maximum servodrive control power for E-Series is 30 watts
per axis; S-Series is 60 watts per axis. If external fusing is required in the power feed
to the Model 20/40, 10 amp slow-blow fuses are recommended.
FG Frame Ground Connect to the enclosure chassis and earth ground, preferably with AWG 8 or larger
braid.
r, t Servodrive Single-phase 115 or 230 VAC, +10%,-15%, 50/60 Hz. This output power is
Control Power switched by the power switch and 10 amp circuit breakers in the Model 20/40. In
most installations, these terminals would be wired with 14 gauge wire.
___________________________________________________________________________________
3.1.4 System Power Wiring & Interlocks - TB6
Both Motion Controllers provide integrated emergency stop and fault interlocks
through terminal block TB6. Also provided on TB6 are terminals for the
+24 VDC I/O power supply provided in the unit; the internal +5 VDC power
supply; and also the input connections to the
I/O Power Bus
.
System wiring diagrams for standard ORMEC servodrives, which include the
recommended safety and fault interlocks for a typical system, are provided in
Appendix B. The primary features of these system wiring diagrams are:
• Servomotor power, called
Main Power
, is switched by the
Main Power
Contactor
.
• For the
Main Power Contactor
to be enabled, both the
E-Stop Pushbutton
and the
No Fault Relay
must be closed.
• For the
No Fault Relay
to be closed, three conditions must be satisfied:
1) there must be no computer diagnostic faults, including powerup
diagnostics, run-time diagnostics and the watchdog timer function;
2) there must be 24 volts applied to the
ES
input at TB6; and
3) there must be no drive faults from any standby or active servodrives.
• Pressing the normally-open
E-Stop Reset Pushbutton
as shown provides
the 24 volts to the
ES
input, and as long as the other conditions are
satisfied, the Model 20/40 will close the
No Fault Relay
contact.
• Assuming the
E-Stop Pushbutton
is closed, the
Main Power Contactor
will
be enabled, and its auxiliary contact,
MP-AUX
, will close maintaining the
required 24 volts at the
ES
input.
• If a fault occurs in the Model 20/40, or any of the servodrives which are in
Output, Torque, Velocity or Position control modes, the normally-open
page 10 GN3-040

Generation III Installation
No Fault Relay
contact will be opened, removing
Main Power
by disabling
the
Main Power Contactor
.
There are many acceptable variations of these System Wiring Diagrams, which
can provide different features such as 24 VDC or 115 VAC operation of the
E-Stop Pushbutton
; 115 or 230 VAC operation of the and
Main Contactor
coil
for motor power. If using a variation, it should incorporate the primary features
as described above and in Appendix B. Contact the ORMEC Service
Department with any questions you may have in this area.
Copper wire with an 80oC temperature rating, 12 AWG maximum, is
recommended for terminal block TB6 wiring. The maximum terminal block
screw torque is 5 in-lbs.
Before applying power, refer to Test Run Preparation in Chapter 4.
3.1.5 Emergency Stop, No-Fault Interlock & I/O Power - TB6
The Emergency Stop, No-Fault Interlock, and I/O power connections are made
at a "pluggable" terminal block on the Discrete I/O board. This terminal block is
located at the lower left of the front of the unit under the removable cover. See
Appendix C-5 for a description of fuses F1-F19 on the DIO Board as well as
the ORMEC and Littelfuse part numbers.
___________________________________________________________________________________
Signal Location Function Description
V TB6-1 I/O Power Bus The
I/O Power Bus
connects all terminals labelled Vand C
which are distributed on the
Integral Discrete I/O
terminal
blocks TB2-TB5. Its purpose is to facilitate field wiring of
discrete I/O without requiring additional terminal blocks.
This connection is to the voltage side of the
I/O Power Bus
,
and would normally be either:
1) connected to TB6-2 if the user decides to use the
internal +24 VDC isolated power supply to provide power
to the I/O Power Bus, or
2) connected to 115 VAC if the user decides to use 115
VAC for the
I/O Power Bus
.
24 TB6-2 +24 VDC Power This fully isolated +24 VDC power supply rated at 2.0 A is
provided for Emergency Stop and Servodrive interlocks, as
well as user I/O.
It would normally be used to:
1) power the Emergency Stop Reset Pushbutton;
2) power +24 VDC discrete inputs for operator inputs, limit
switches, PLC interfaces, etc; and
3) power an MMI-840 Operator Interface Terminal (1/4 amp
max) if one is used.
It would not normally be used to power 24 VDC coil outputs,
and if intending to use it for this purpose, the user should
watch power requirements carefully and use noise prevention
measures such as flyback diodes across each coil.
GN3-040 page 11

Generation III Installation
Signal Location Function Description
ES TB6-3 Emergency Stop Input The E-Stop input must have +24 VDC applied to it for full
operation. If removed, an emergency stop of all motors will
occur. The system wiring diagrams in Appendix B provide an
E-STOP RESET pushbutton to initially establish the voltage,
allowing the No-Fault Relay to pull up. The +24 volts is then
maintained by the MP-AUX auxiliary contact of the Main
Power Contactor. For more detail, see the System Interlock
description in the Operation Chapter.
C TB6-4 I/O Power Bus Common Common side of
I/O Power Bus
; see the description under
TB6-1 above.
R2 TB6-5 +24 VDC Return Return for the isolated +24 VDC power supply.
R2 TB6-6 +24 VDC Return Return for the isolated +24 VDC power supply.
24 TB6-7 +24 VDC Power Additional connection to the +24 VDC isolated power supply.
NF TB6-8 No Fault Relay Contact This fully isolated, normally-open held-closed, relay
NF TB6-9 No Fault Relay Contact contact will be held closed as long as there is power to the
unit, there is no internal fault
and
+24 VDC is applied to the
Emergency Stop input. The System Wiring Diagrams in
Appendix B show this contact being used to drive the coil of
the Main Power Contactor which controls the electromotive
power to the servodrive. In the case of a system with multiple
motion controllers, the No Fault Relay Contacts may be wired
in series.
SH TB6-10 Shield Point Connection to the chassis frame for shielding cables
connecting to the +5 VDC main power supply.
+5 TB6-11 +5 VDC Power Connection to the +5 VDC main power supply. Connections
to this power supply should always be made with a shielded
twisted pair cable to maintain integrity of the +5 VDC internal
power supply.
R5 TB6-12 +5 VDC Common Common of the +5 VDC main power supply.
___________________________________________________________________________________
page 12 GN3-040

Generation III Installation
3.1.6 Integral Discrete I/O - TB2 to TB5
16 Integral Discrete I/O points are standard. These I/O points are located
under the removable front cover of the unit. Connections to them are made at
four pluggable terminal blocks, which are located on the left side of the unit and
also provide multiple tie points to the selected
I/O Power Bus
for convenience.
A cable-tray is provided down the left side of the unit with the wiring designed
to exit at the lower left of the unit as it’s mounted on the panel.
Mounting sites are provided for Opto-22 style I/O Modules, allowing a variety of
I/O choices. The I/O circuit board features 90 mil thickness and multiple
standoffs for ruggedness, as well as plug-in fuses and integral LED status
indicators for each I/O point which are visible through the cover.
All of these I/O points are individually configurable from MotionBASIC®as either
inputs or outputs using the IO.MODE@ variable. In addition, these I/O points
can be configured to be "latched" asserted on either "high" or "low" transitions
of the input voltage. They can also be used as "interrupts" using the
ON EVENT DIO@
capability provided in MotionBASIC®.
Copper wire with an 80oC temperature rating, 12 AWG maximum, is
recommended for terminal block TB2-TB5 wiring. The maximum terminal block
screw torque is 5 in-lbs.
See Appendix C-5 for a description of fuses F1-F19 on the DIO Board as well
as the ORMEC and Littelfuse part numbers.
GN3-040 page 13
This manual suits for next models
1
Table of contents
Other Ormec Controllers manuals
Popular Controllers manuals by other brands
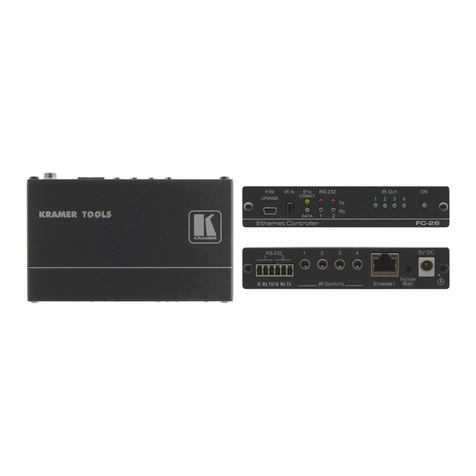
Kramer
Kramer FC-26 quick start guide
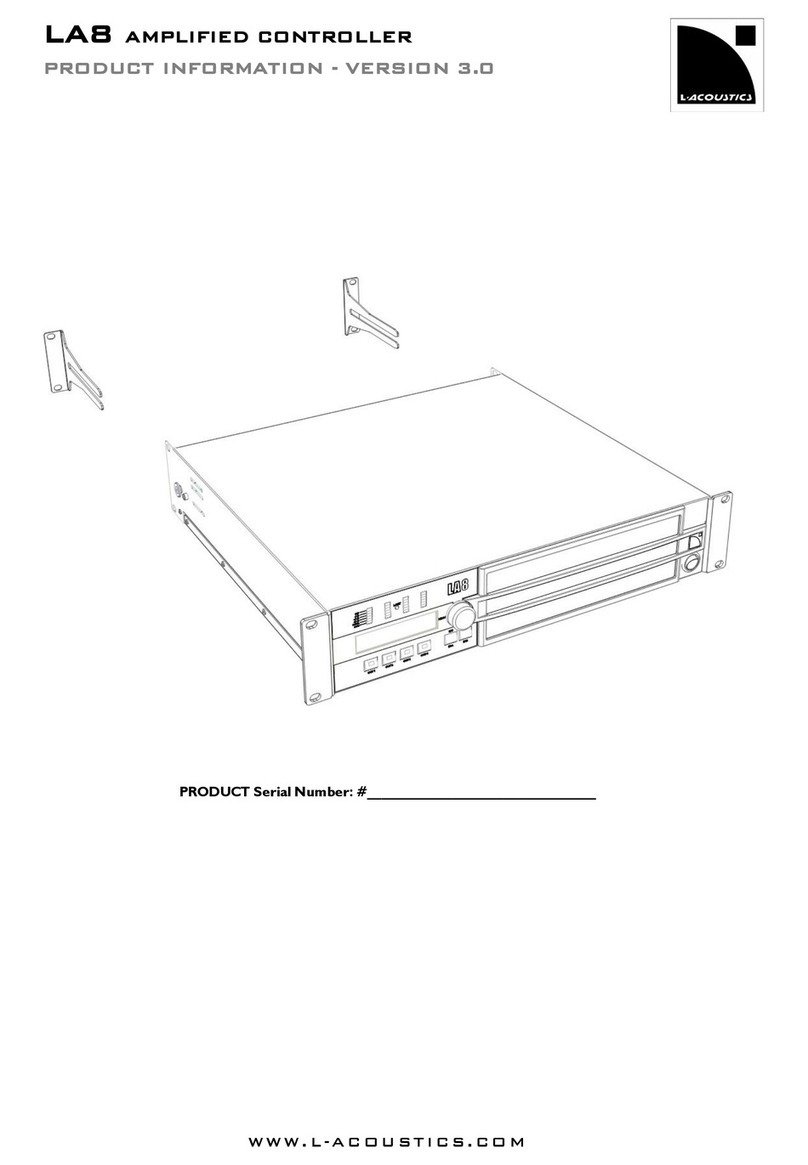
L-Acoustics
L-Acoustics LA8 Product information
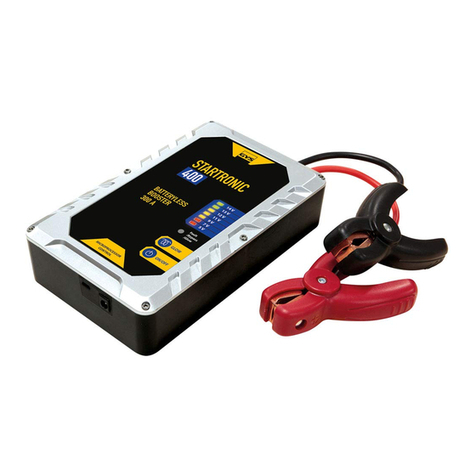
GYS
GYS STARTRONIC 400 manual
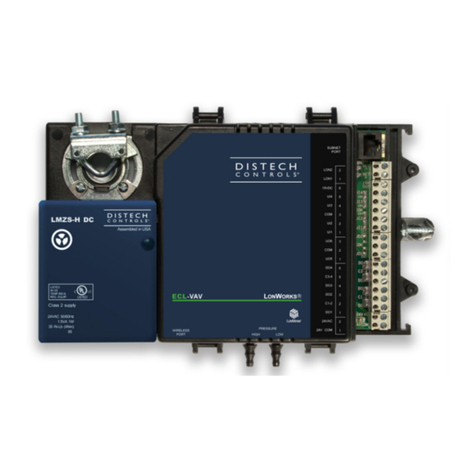
Distech Controls
Distech Controls ECL-VAV Series Hardware installation guide
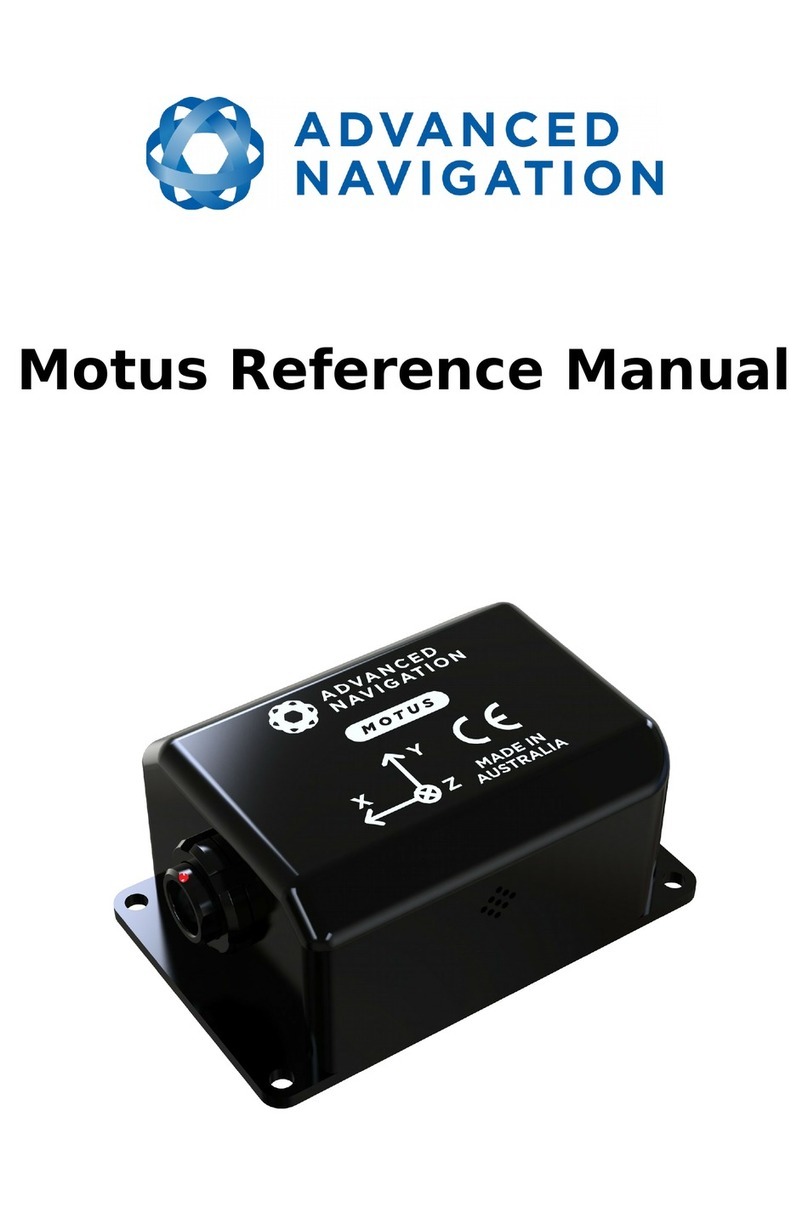
Advanced Navigation
Advanced Navigation Motus Reference manual
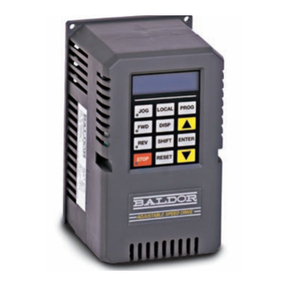
Baldor
Baldor ID15J1F50-ER Installation and operating manual