DAYLIFF SUNVERTER 4 Installation instructions

SUNVERTER 4
AC SOLAR PUMP CONTROLLER
Installation &
Operating Manual


CONTROLLER SPECIFICATIONS
1.
1
2.
SYMBOLS & WARNINGS 3
INDEX
© Davis & Shirtliff Ltd 2023
Contents herein are not warranted
2.1 Purchase Inspection 3
2.2 Installation 3
2.3 Wiring 4
2.4 Connection 4
3. INSTALLATION & WIRING 5
2.5 Running 4
3.4 Wiring Diagram
8
4.2 Panel Layout and Instruction 19
4.4 View Running Data 21
4.5 View Historical Data 22
4.6 View or Modify the Control Parameter 22
4.7 Function Parameter Description 23
3.1 Installation Environment Requirements 5
4. OPERATION & CONTROL 18
3.6 Single Phase Motor Wiring Installation
14
3.7 Water Level Switch Installation & Wiring Instruction
4.3 Panel Operation 21
15
4.1 Initial Settings before rst Operation 18
2.6 Hybrid Operation 4
2.7 Others 5
3.3 Installation Method 6
3.8 Others
16
3.9 Hybrid Installation
16
3.2 Installation Direction 6
3.5 Electrical Connection
12
4.8 Common Function Description 26

SERVICE & MAINTENANCE
6.
32
6.1 Routine Inspection & Maintenance 32
6.2 Requirement of Inspection & Maintenance 32
6.3 Main Points for Inspection & Maintenance 32
6.4 Inspection & Replacement of the Damageable Part
33
Filter Capacitor
6.5 Storage 33
TERMS OF WARRANTY
7.
34
5. TROUBLE SHOOTING 27
5.1 Fault Code Description & Solutions 27
5.2 Fault Abnormal Code Description 27
5.3 Faulty Inquiry & Reset 29
5.4 Other Codes Description 29

1
1. CONTROLLER SPECIFICATIONS
The Dayliff Sunverter 4 is the latest update of the established Sunverter range of advanced
AC/DC inverters specially designed for solar-powering AC motors in various water
pumping applications. As well as a general upgrade of the electronics and functionality an
important new feature is hybrid capability that enables concurrent operation with direct AC
power from mains or generator supply while prioritising solar supply. It is adaptable to all
AC motor types and can be retro fitted to existing AC supply installations in solarisation
projects. Particular features include;
• Hybrid capability with the option of DC solar power, generator or mains grid power
inputs
• Patented MPPT (Maximum Power Point Tracking) capability providing fast response,
good stability and up to 99% efficiency.
• Fully automatic operation with up to 8 years storage capacity of operating data.
• Supports motor soft start and gives full motor protection
• User friendly LED display interface with comprehensive display information
• Integral remote monitoring and control capability available on all units which is
activated by signing up to the unique iDAYLIFF Service.
• Strong IP65 rated enclosure for enhanced component protection
• Built-in PV array disconnect switch and fuse, for system isolation
Congratulations on selecting a Dayliff Sunverter 4. It is manufactured to
the highest standards and if installed and operated correctly will give
many years of efcient and trouble free service. Careful reading of this
Installation Manual is therefore important, though should there be any
queries they should be referred to the equipment supplier.
Sunverter 4
Water Tank
Solar Panel
Pump
Generator
Grid
High Level
Control
Low Level
Control
Capacitor box (1phase)
PV Array Disconnect
Switch

2
CONTROLLER FUNCTIONALITY
The controller offers the following control functions:
• Settable minimum and maximum frequency and open circuit voltage.
• Display of operating parameters including frequency, voltage, amperage, input
power and pump speed.
• Protection against over and under voltage, over current, system overload and
module over temperature.
• Fault detection with error code display.
• Selectable hybrid modes that prioritise solar supply as well as maximise output
through optimal blending of both power supplies.
ŸPower saving mode (CRUISE) - limit the maximum AC input power, hence saving
energy.
INSTALLATION
Dayliff Sunverter 4 controllers are surface mounted and should be provided with a housing
for water and heat protection. Due to the high operating voltages proper earthing is
essential, which must be done by a qualified electrician. As a rule, all PV powered solar
pumping systems should be provided with a solar module array with a nominal output
about 30% greater than the motor size. In hybrid applications, higher array MPP voltage is
specified to allow achievement of larger solar supply share of hybrid power supply. The
arrays should be wired in a combination of series and parallel connections to ensure that
the correct voltage is available into the inverter. It is important that the connection
arrangement is approved by the pump supplier.
OPERATING CONDITIONS
Altitude: 0-2,000m**
0 0
Ambient Temperature: -20 C to 60 C ***
Relative Humidity: 0-95% (non condensing)
Frequency: 0-60Hz
CONTROLLER DATA
**If the altitude is over 2,000m, the rated output current should be derated by 10% for every 1,500m increase in height
Model
Motor
Rated
Power
(kW)
Output
Current
(A)
2.2
Weight
(kg)
Dimensions (mm)
WH D
Rated
Voltage
14
266 111 5.5
Max
DC
Input
Voltage
VDC
440
1.1 8.6 125-360
180-360
1.5 1x240V 11
250-360
296
MPP
Voltage
VDC,
Solar
MPP
Voltage
VDC,
Hybrid
125-370
180-370
SV4/3.0M
SV4/1.5M
SV4/2.2M
250-370
All dimensions in mm
***When operating in a small enclosed space, such as a cabinet, ensure the inverter is adequately cooled to prevent high internal temperature.

3
2. SYMBOLS AND WARNINGS
Check the inverter before installation. Do not install if it is
damaged or with missing parts, else may cause accidents.
CAUTION
To ensure good cooling effect, the inverter must be installed
vertically with at least 10cm space at the sides and 30cm at
the top and bottom.
CAUTION
2.1 Purchase Inspection
2.2 Installation
CAUTION
Sunverter is normally wall mounted. Ensure that the
mounting backplate can support the weight of the inverter.
Misuse of this Inverter will result in re, serious injury, or even
death. It can also cause low or middle-level injury to persons
or equipment damage.
CAUTION
Suitable for indoor installation with sufcient ventilation. Do
not install under direct sunlight. Keep away from dust and
moisture.
2.3 Wiring
Wiring must be performed by a qualied electrical
professional, else may cause electric shock or re.
WARNING
Always ensure input power is isolated before wiring and
connection; else may cause electric shock or re.
WARNING
Earth terminal must be reliably grounded, or else inverter
enclosure may be electried.
WARNING
The selection of solar array, motor and inverters should be
reasonable, in case of doubt, consult nearest dealer.
NOTE

4
2.5 Running
Do not change wiring and connection when the inverter is
powered, else may cause electric shock.
WARNING
CAUTION
To prevent equipment damage, refrain from making random
changes to the function parameters of the inverter.
CAUTION
The temperature of heat sink is normally high during running
and it should not be touched, else may cause burns.
Make sure all the wiring and connection are correctly
connected before powering on, or else may damage the PV
disconnect switch or cause re.
CAUTION
To avoid the risk of re, make sure to securely tighten the
terminal using the specied torque.
CAUTION
Do not connect capacitor or phase-advanced LC/RC noise
lter with inverter output.
CAUTION
2.4 Connection
CAUTION
Do not switch off DC or AC power to the inverter while the
pump is running. The disconnect switch and/or MCB should
only be operated after the inverter is in stop mode otherwise
there will be damage .
2.6 Hybrid Operation
2.7 Others
WARNING
Maintenance and inspection must be performed by a
qualied technician.
WARNING
Do not disassemble the inverter during operation. The
inverter must be powered off atleast 5 minutes before
conducting maintenance and inspection and this is to avoid
the residual voltage of electrolytic capacitor in major loop
causing personal injuries.

5
WARNING
At the end of its design life, the inverter should be disposed
as industrial waste. During incineration, the electrolytic
capacitor may explode and some parts may produce toxic
and harmful gas.
Environment
Factor
Ambient Humidity
Requirements
5 ~ 95% (No dew condensation)
Ambient
Temperature -20°C ~ +60°C
Storage
Temperature
-40°C ~+70°C When operating in a small enclosed space
such as a cabinet, ensure enhanced cooling to avoid the
internal temperature exceeding the ambient temperature
requirements.
Vibration Less than 0.5g
Altitude
0~2,000m, If the altitude is over 2,000m, the rated
output current of the inverter should be derated by 10%
for every 1,500m increase in height.
Installation Site
Indoor and outdoor use. To protect the inverter from direct
sunlight or rain, it is advisable to install it in shaded areas
when used outdoors.
Install the inverter on flame retardant surface with sufficient
heat dissipation space and good ventilation.
Install the inverter on a firm support that fully bears the
inverter weight.
Keep away from electromagnetic radiation sources and
locations with high incidence of lightning or the presence of
flammable, explosive, corrosive gases, as well as radioactive
substances. Stay away from areas with excessive dust, oil
mist, or steam.
Install the inverter in a place where data observation and
maintenance are convenient.
Do NOT install the inverter in a place accessible to children.
Do NOT install the inverter in residential or commercial
spaces where noise would be a concern.
3. INSTALLATION AND WIRING
3.1 Installation Environment Requirements
Installation of the inverter according to the specified environmental conditions is the
precondition for ensuring long-term normal and stable operation of the inverter.

6
3.2 Installation Direction
ŸLeave enough installation space between inverter and other objects nearby to
ensure good ventilation and heat dissipation. As shown on Fig 1, install the
0
inverter vertically or backwards with maximum 10 inclination angle Do NOT
install horizontally or transversely.
ŸInstall the inverter at a height that is convenient to operate and read in the LCD
display screen
Fig 1: Installation Direction Diagram
NOTE
The installation surface should be at and closely attached to
the inverter bottom surface to ensure good heat dissipation.
NOTE
If multiple inverters are to be installed in the same cabinet, it
is recommended to adopt side by side installation. If two
inverters are to be installed longitudinally, a guide plate
should be added in the middle.
3.3 Installation Method
ŸChoose the installation place and drill holes according to the size and shape of
support plate. The recommended diameter of holes is 6±1mm and the depth is
with 30±2mm.
ŸUse the matching expansion screws to fix the support plate on the wall with a
tightening torque of 1.5Nm.
ŸMount the inverter, screw the matching screws (M4*14) on the side to fix it.
Tightening torque is 1.0Nm.
A >100mm
B>100mm

7
NOTE
The installation surface should be at and closely attached to
the inverter bottom surface to ensure good heat dissipation.
If the installation surface is not at, a wind deector can be
installed on the back of the inverter in advance to enhance
the heat dissipation capacity.
NOTE
The expansion bolts provided by manufacturer are suitable
for installation on concrete walls. If the inverter is to be
mounted on wooden walls, select the expansion bolt suitable
for wooden wall mounting, and ensure the expansion bolts
are long enough to penetrate at least 1/2 of the wall
thickness.
Fig 2: Mounting Hole
Diagram
Fig 3: Inverter Mounting
Installation Diagram

48
3.4 Wiring Diagram
Fig 4: System Wiring Diagram

9
DC Input
Connected to positive pole of
solar array
PV+
Socket Terminal Description Connection Description
PV-
Three - Phase
AC Input
R
Connected to earth cable
Connected to R phase of grid
Connected to negative pole of
solar array
SConnected to S phase of grid
TConnected to T phase of grid
Single - Phase
AC Input
LConnected to L phase of grid
NConnected to N phase of grid
Connected to earth cable
AC Input
Connected to U phase of
three-phase motor/auxiliary
winding terminal A single
p h a s e m o t o r w i t h n o
capacitor/ L terminal of single
phase motor with capacitor
U/A
W/C
V/M Connected to V phase of
three-phase motor/auxiliary
winding terminal M single
p h a s e m o t o r w i t h n o
capacitor/ N terminal of single
phase motor with capacitor
Connected to W phase of
three-phase motor/winding
common terminal C of single-
phase motor with no capacitor
Connected to earth cable
CAUTION
The input/output terminals vary depending on the model.
Please refer to inverter socket and terminal description.

NOTE
For single-phase pumps, remove the external capacitor
before wiring
10
Water level sensor signal
input terminal for tank
Tank water level signal input, open circuit is normal,
short circuit is abnormal. Function setting through
Pr15, default value 7
TANK-COM
Terminal Terminal Name Function Description
Well water level signal input, open circuit is
abnormal, short circuit is normal. Function setting
through Pr17, default value 6.
WELL-COM
Multi function switch input
terminal
Woltman water meter signal input. Function setting
through Pr19, default value 0.
MUX-COM
+24V power supply
24V power supply, maximum output current 300mA;
can be used as power supply of communication
module, external sensor or miniature relay
+24V-COM
+10V power supply
10V power supply, maximum output current 50mA;
can be used as power supply of an external
potentiometer with resistance value range of 1k
Ω~5kΩ
+10V-GND
RS485 communication
interface
Interface for communication with wired external host
or inbuilt wireless communication module. (Default
setting enable the communication with inbuilt
imodule, if needed for external host, relevant
advanced parameter must be modified)
A-B
Analog input terminal
Water level sensor signal input or pressure sensor
signal input.
Range: DC 4~20mA, 0-10V depending on the
jumper connection at the board
A1N-GND
N o r m a l o p e n r e l a y
contact Contact drive capability:
AC250V, 3A, cosØ = 0.4
DC30V, 1A
TNO -TCOM
N o r m a l c l o s e r e l a y
contact
Water level sensor signal
input terminal for Well
TNC - TCOM

411
NOTE
In order to ensure communication quality, use twisted
shielded pair cable as communication cable.
NOTE
All analog, digital, power and signal cables should be
separated to avoid entanglement.
Model Solar Array
2
Cable (mm )
2
AC Cable (mm )
SV4/3.0M
SV4/1.5M
SV4/2.2M
CAUTION
To maintain proper system functionality, it is crucial to choose
the cable size in accordance with the table above.
NOTE
(+)/(-) L/N R/S/T, U/V/W
2
Earth Cable (mm )
PE
Signal Cable
2
(mm )
4
2.5
4
6
2.5
4
6
2.5
41.5
2.5
1.5
1.5
The recommended cable should be used under the conditions
0
of ambient temperature < 40 C, cable length <100m and
working current < rated current.

412
3.5 Electrical Connection
Step 1 : Prepare all the input/output cables as shown in Fig 5.
Step 2: Using the hex screwdriver open the upper cover of the inverter, pass the cable
through the waterproof PG terminals at the bottom. The tightening torque is 0.8Nm for
power terminal and 0.6Nm for the signal terminals. Insert the PV input cable into the
MC4 terminal located at the PV+/PV- position as shown in Fig 6. Note the positive and
negative poles.
Fig 5: Cable Preparation Diagram.
Single Core Cable Stripping
Diagram
Single-Core Strip 10mm at A
Power Cable
Cable Type Process Description
Strip 50mm at A and 10mm at B
Multi-Core Strip 50mm at A and 5mm at B
Control Signal Cable
Multi-Core Cable Stripping
Diagram
Crimping Diagram

413
Step 3: After finishing the wiring, tighten the bottom waterproof PG terminal with a
tightening torque of 7Nm and lock the upper cover. Fix the earth cable to the ground
screw at the bottom of the housing.
Fig 6: Wiring Diagram
Fig 7: Shell Grounding Operation Diagram
Step 4: Turn the knob of the DC disconnect switch on the right side of the inverter to
“ON” position as shown in Fig 8, solar power supply then is connected and inverter
starts.
Fig 8: DC Disconnect Switch Operation Diagram

414
Fig 9b: Single Phase Wiring without External Capacitor Box
Capacitor Box
3.6 Single Phase Motor Wiring Instruction
To wire single phase motors to the Sunverter 4, if the motor has an external capacitor
box, wire as per Fig 9a. where you connect the SV4 terminals A and M to the capacitor
box. If the motor does not have an external capacitor box, wire as per Fig 9b, where
you connect the SV4 terminals A, M, & C to the motor. It should be noted that flow rate
and head performance may be reduced by as much as 15% when capacitors are
removed.
*Capacitors in terminal box for surface pumps
CAUTION
Ensure to connect the wires according to the instructions,
incorrect connection may lead to abnormal operation of the
system.
Wiring
If the single-phase motor windings connection cannot be identified, follow these steps:
Step 1: Resistance Test
Label the winding cables A, B, and C for ease in identification.
Test the resistance between each pair of the connection parts with a multimeter and
note the Ohm readings. See example below of readings taken and calculations to help
identify correct winding.
ŸReading from Point A - B - 7Ω
ŸReading from Point A - C - 5Ω
ŸReading from Point C - B - 12Ω
Fig 9a: Single Phase Wiring with External Capacitor Box

415
3.7 Water Level Switch Installation and Wiring Instruction
ŸThe water level switch is installed in the well for dry running protection or installed in
the water tank for overflow protection.
ŸWater level switch requires vertical installation with maximum 10° inclination
angle. The installation position should be slightly higher than the pump outlet
position in the well, while in the water tank it should be slightly lower than highest
water level.
ŸTo wire for well application, pass the water level switch cable through the
waterproof PG terminal and connect to the WELL-COM terminals(remove the
short-circuit strip between the two first), for tank application, connect to the I1
TANK-COM terminals.
Fig 10: Water Level Switch
Installation for Well/Tank
Fig 11: Water Level Switch
Wiring Diagram
Calculation
ŸAdd all A’s = 12Ω -> Lowest Reading = 'Common" winding - C
ŸAdd all B’s = 19Ω -> Highest Reading = 'Start/Auxiliary" winding - A
ŸAdd all C’s = 17Ω -> Second Highest Reading = 'Run/Main" winding – M
Connect the motor to the Inverter A, M, C port.
Step 2: Water Flow Test (to confirm the Resistance Test)
If the measured resistance in step 1 appears to have little difference, then compare
water flow during operation to determine if the wiring is correct. Keep C port wiring
unchanged, exchange the wiring of A and M and observe the water flow. The wiring
with bigger water flow should be the correct wiring.
From the above steps, the connection ports A, M,C of single phase motor can be
confirmed

416
Model
SV4/3.0M
SV4/1.5M
SV4/2.2M
AC Breaker (A)
50
25
40
ŸIf the inverter is far from the motor (>100m), it is recommended to install an output
reactor or filter.
ŸFor optimal performance, it is advised to incorporate input and output reactors,
dedicated filters, and magnetic rings at the inverter's input and output connections.
These components effectively reduce noise and prevent interference with other
components or systems.
ŸConsult nearest Dayliff dealer for the extra accessories such as AC disconnect/ AC
breaker combiner, surge suppressor and reactors.
3.9 Hybrid Installation
The SV4 series solar pumping inverter incorporates a hybrid power input feature,
combining PV and AC power sources. The PV input is connected to the bus circuit using
an anti-reverse diode, while the AC power input is rectified through a rectifier bridge
and then linked to the bus circuit. This allows simultaneous connection of both power
sources, facilitating the utilization of hybrid power to drive the water pump motor.
Hybrid Mode
Solar priority mode (Pr6=1) default.
Where there is both AC and PV power inputs, inverter adjusts pump running speed
prioritising solar power and only blends with AC power when there is insufficient solar
power. Insufficient solar power is detected when the pump speed falls below the set
weak light frequency value (Pr.14).
AC+PV blending (Pr6=0)
In the presence of both AC and PV power inputs, the inverter drives the pump at its
designated speed. The utilization of solar power is greatly enhanced during periods of
high solar irradiance, typically reaching approximately 1000 W/m².
ŸAC circuit breaker (rated current 25A or above) should be installed as protection
switch for AC power input.
ŸThe inverter has one pair of DC input terminals. If the solar modules are multi-
paralleled, an additional solar combiner box is necessary.
ŸThe inverter must be grounded reliably and the grounding cable properly sized and
as short as possible. If possible, the inverter should be grounded separately.
ŸIn areas with high incidence of lightning, it is recommended to install an external
surge protector at the power input of the inverter.
3.8 Others
Table of contents
Other DAYLIFF Controllers manuals
Popular Controllers manuals by other brands

Stephill
Stephill SSDP30-70 Series User & Fault Finding Guide
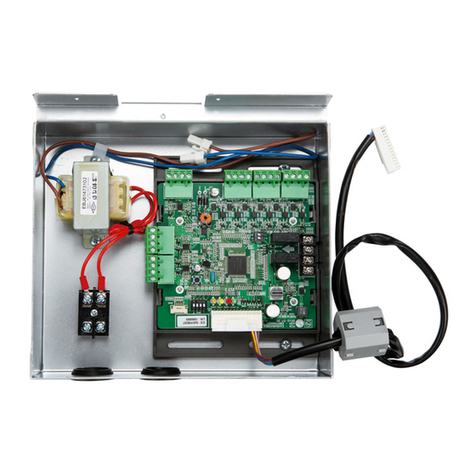
LG
LG PWFCKN000 installation manual
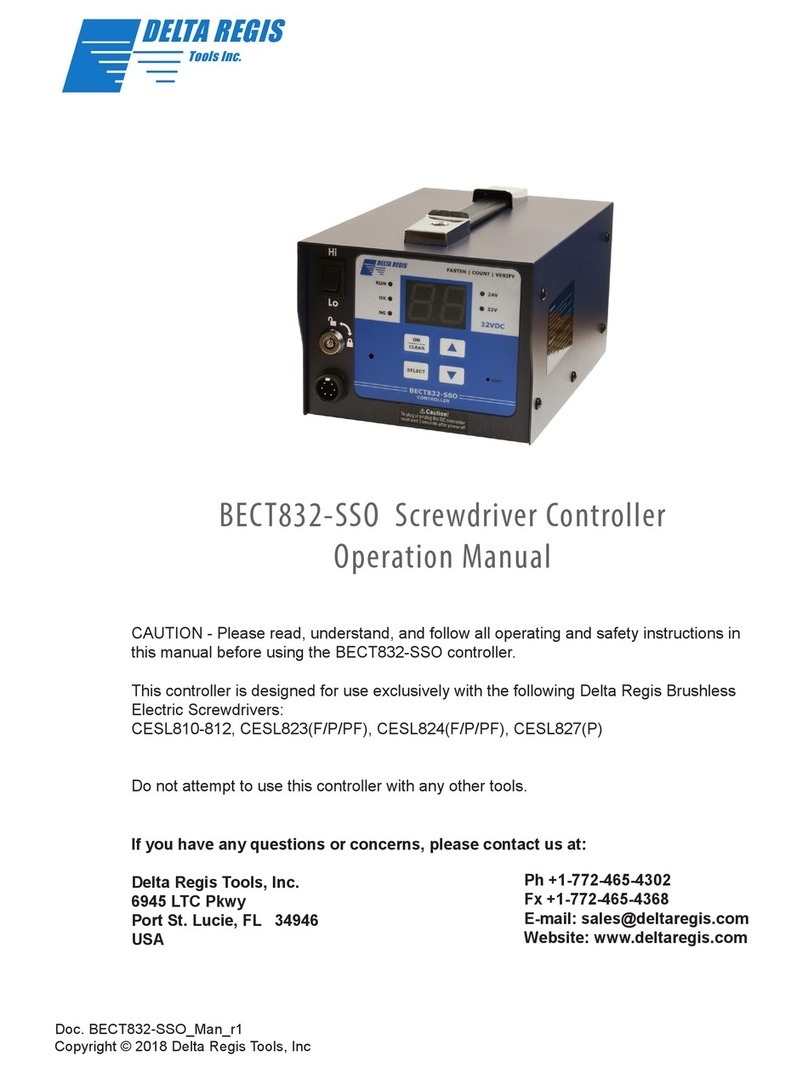
Delta Regis
Delta Regis BECT832-SSO Operation manual
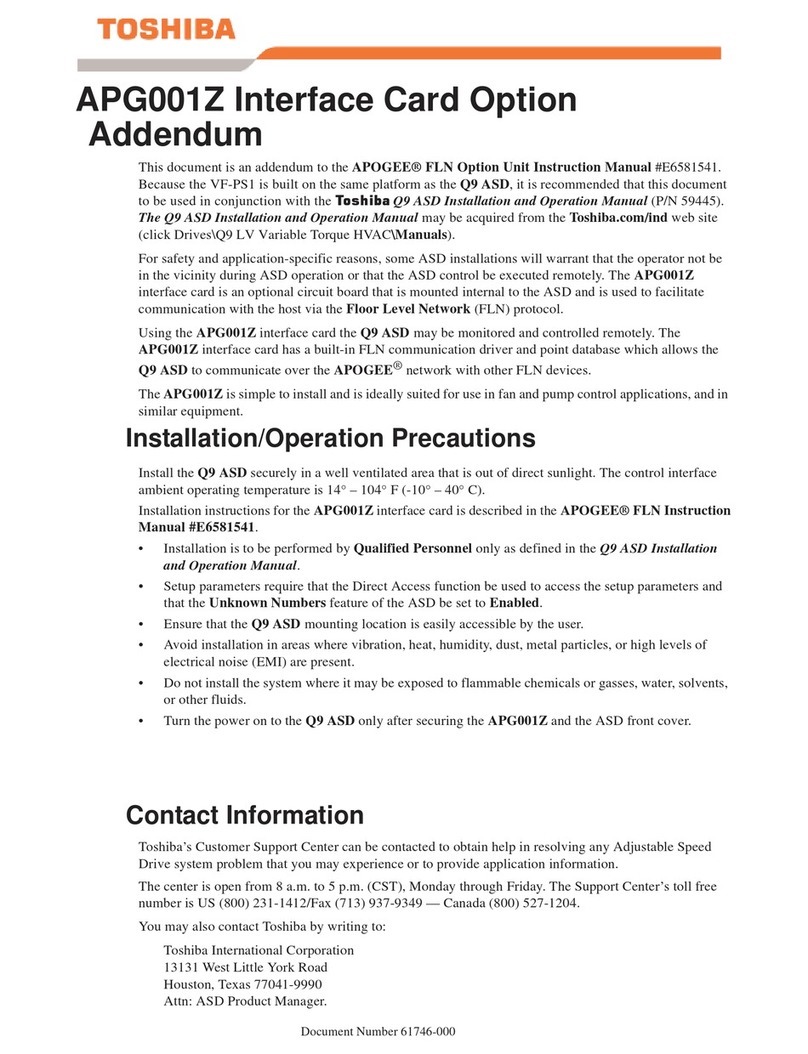
Toshiba
Toshiba APOGEE FLN APG001Z Installation & operation

Leviton
Leviton Decora NE515 installation instructions

Tech Novitas
Tech Novitas Olbers-10KVA user manual