Oval EL1810 User manual

1
BATCH CONTROLLER
MODEL EL1810
Every OVAL batch controller is fabricated, tested, inspected, and shipped from our factory under stringent
quality control. In order to maintain its design performance throughout its life, this manual offers the
operator the necessary installation, operation and maintenance information.
Be well familiar with these instructions before you place the controller in service and keep this manual at
the eld location for ready reference.
Also refer to the instruction manual for the pulse generator (owmeter) used.
Ins. No. E-215-7-E

E-215-7-E
2
CONTENTS
1. BEFORE YOU BEGIN ................................................................................. 4
1.1 Conrming the Nameplate.............................................................................. 4
1.2 Transportation Considerations ....................................................................... 4
1.3 Storage Considerations .................................................................................. 4
2. GENERAL ................................................................................................... 5
2.1 Features and Functions.................................................................................. 5
3. PART NAMES ............................................................................................. 5
4. INSTALLATION ........................................................................................... 6
4.1 Outline Dimensions ........................................................................................ 6
4.2 Installation ...................................................................................................... 6
4.2.1 Installation Location (Indoor only) ........................................................ 6
4.2.2 Panel .................................................................................................... 6
4.2.3 Installation ............................................................................................ 6
5. WIRING ....................................................................................................... 7
5.1 Cables for Field Wiring ................................................................................... 7
5.2 Wiring Connections ........................................................................................ 7
5.3 Identifying the External Connection Terminal Block ....................................... 7
5.4 Identifying the External Connection Terminals ............................................... 8
5.5 Flowrate Input and their Terminals ................................................................. 8
5.6 Flow Signal Input Wiring Connections............................................................ 9
5.7 Example of Hookup ...................................................................................... 10
6. FRONT PANEL DISPLAY ......................................................................... 11
6.1 Front Panel Display Functions.......................................................................11
6.2 Control Key Functions (other than batch setup mode and other
setup mode).................................................................................................. 12
6.3 Output Functions .......................................................................................... 13
7. BLOCK DIAGRAM .................................................................................... 16
8. OPERATION.............................................................................................. 17
8.1 Preparation Before Operation....................................................................... 17
8.2 Preoperational Checks ................................................................................. 17
8.3 Operation Sequence..................................................................................... 17
8.4 Conrming the Two-stage Valve Opening and Closure................................ 19
8.5 Description of Batch Operation..................................................................... 19

E-215-7-E
3
CONVENTIONS
Shown in this manual are the signal words NOTE, CAUTION and WARNING, as described in the
examples below:
NOTE: Notes are separated from the general text to bring the user’s attention to important
information.
CAUTION: Caution statements signal the user about hazards or unsafe practices which could
result in minor personal injury or product or property damages.
WARNING: Warning statements signal the user about hazards or unsafe practices which
could result in severe personal injury or death.
9. SETTING UP OR CHANGING PARAMETERS ........................................ 20
9.1 How to Change Parameters (batch setup and other setup modes) ............. 20
9.1.1 Batch Setup Mode.............................................................................. 20
9.1.1.1 Operation (batch setup mode) ............................................ 20
9.1.1.2 Example of Batch Setup ..................................................... 21
9.1.2 Setup Mode........................................................................................ 22
9.1.2.1 Operation (setup mode) ...................................................... 23
9.2 Construction of Internal Assembly................................................................ 24
9.3 Removal of Internal Assembly...................................................................... 24
9.4 Assembling the Internal Assembly................................................................ 25
9.4.1 Installing the Power Supply Board and Output Board........................ 25
9.4.2 Installing the Front Panel.................................................................... 25
9.5 Setup or Change on the Power Supply Board.............................................. 26
9.5.1 A change in the Power to Pulse Generator ........................................ 26
9.5.2 Conguring the Flow Signal Input Circuit for the Companion
Pulse Generator ................................................................................. 26
9.5.3 Input Frequency Division (hardware) Selection.................................. 26
9.6 Setup on the Output Board........................................................................... 27
9.6.1 Buzzer Sound Setup on Alarm (missing pulse, overmeasurement,
and parameter error) Detection.......................................................... 27
9.7 Reconguration on the Display Board.......................................................... 27
9.7.1 Total Counter Output Pulse Width Selection ...................................... 27
10. TROUBLESHOOTING .............................................................................. 28
10.1 Inspection Items ......................................................................................... 28
10.2 Inspection of Fuse ...................................................................................... 29
10.3 Dielectric Test Voltage ................................................................................ 29
10.4 Q&A Controller Behavior in Standby Mode ................................................ 29
11. GENERAL SPECIFICATIONS .................................................................. 30
12. PRODUCT CODE EXPLANATION ........................................................... 31

E-215-7-E
4
1. BEFORE YOU BEGIN
Before leaving the factory, every OVAL product is thoroughly inspected and tested and is shipped in rst-
class condition. When received, it should be carefully inspected for any indication of rough handling during
transit. In this section, instructions necessary for handling this instrument are described. Make yourself
familiar with these instructions. As for other instructions, refer to respective sections.
If you have something to inquire, contact the nearest OVAL authorized service station in your district.
1.1 Confirming the Nameplate
OVAL batch controllers are individually adjusted to the
customer specication.
Make sure, by comparing the model code and ratings
stated on the nameplate or tag attached to the top of
the housing against the GENERAL SPECIFICATIONS
(page 30) and PRODUCT CODE EXPLANATION (page
31), that the product you received conforms to the
specication in your order.
◆When you inquire, please specify the product name,
model No., serial No., ratings, and other pertinent
information.
1.2 Transportation Considerations
(1) The batch controller should be transported and stored in the same package used for transportation
from our factory if circumstances permit.
(2) Avoid giving impact shocks to the batch controller during transportation.
1.3 Storage Considerations
If the batch controller upon receipt is to be stored for extended periods of time before installation,
unexpected problems could arise. In a case like this, the following considerations should be taken:
(1) The batch controller can best be stored in the original package used for transit from the factory.
(2) Select a storage location that meets the following requirements:
Free from rainwater and moisture
Least vibration and impact shock
In the room temperature and humidity environment (around 25°C and 65% R.H.)
✩
✩
✩
Nameplate
(product tag)
Terminal Identification label
Parameters
label
Fig. 1.1 Location of Nameplate
Nameplate
(product tag)
Terminal Identification label
Parameters
label
Fig. 1.1 Location of Nameplate

E-215-7-E
5
2. GENERAL
Combined with a owmeter and a shutoff valve, the batch controller passes a predetermined amount of the
process uid in batching operations. Built around a single chip microprocessor, this versatile, compact, and
lightweight controller is designed for ease of operation. It saves time and effort in many processes, such as
blending materials, dosing with additives, transferring materials from one tank to another, or shipping from
an outlet, at chemical, food, paint plants or elsewhere where streamlined production lines are desired.
2.1 Features and Functions
(1) Easy operation.
Front panel key switches for batch setup, start, stop, and reset for accurate operations.
(2) Accurate batch control.
Valve control output comes in two steps to open and shut off the valve for far more accurate metering
than with a single batch control output.
(3) Simple system conguration.
Can control the system with start, stop, and reset signal arriving from a remotely located point. Also
available is an end-of-batch signal. All these make interlocking with other control systems simple.
(4) Increased process safety.
➀ Valve opens and shuts off in two steps (reducing the initial velocity); this arrangement prevents not
only static electricity generation in the pipeline or in the tank at startup, but also water hammer, or
hydraulic shock, to the pipeline at valve closure.
➁If trouble occurs in the process for some reason, resulting in missing pulses, an overmeasurement,
or parameter errors, an alarm can be made to go off.
(5) Reliable and simple to maintain.
➀Major circuits are built on printed circuit boards for reliability and simple maintenance.
➁All inputs and outputs are isolated from each other by photocouplers.
➂During power cycling, parameters and variables are retained in the E²PROM.
3. PART NAMES
Nameplate
(product tag)
Front panel
Terminal Identification Label Panel-mount Fitting
(two, top and bottom)
Backpanel (with terminal block
for external connections)
Parameter Label
Frames (top, bottom, right, left)
Fig. 3.1 Part Names
NOTES: 1. For terminal blocks for external connections, see Sec. 5.3 on page 7.
2. For the front panel display and controls, see Sec. 6.1 on page 11.

E-215-7-E
6
4. INSTALLATION
4.1 Outline Dimensions
Terminal block
Panel-mount fitting
All dimensions in millimeters
Fig. 4.1 Outline Dimensions
4.2 Installation
4.2.1 Installation Location (Indoor only)
Select an installation site where:
(1) Mechanical vibration, shock and corrosive gases
least exist.
(2) The air is dry and at around room temperature
and stable.
(3) A place where is not exposed to the direct
sunlight.
NOTE: Although the manufacturer guarantees
stated performance at ambient temperatures
from –10 to 50°C, it is recommended that
the instrument be placed in service at room
temperature.
(4) Provide a sufficient working space behind the
instrument – at least 50 centimeters from the
back panel of the instrument to facilitate wiring
and servicing.
4.2.2 Panel
(1)
Use a rigid steel sheet with a minimum thickness of
1.6 millimeters. Recommended thickness is 3.2mm.
(2) If it is required to mount the computers side by
side, dimensions in Fig. 4.2 are suggested.
(3)
Recommended mounting height is given in Fig. 4.3.
4.2.3 Installation
(1) Insert the instrument through the opening in the
mounting panel.
(2) Hook the enclosure hold-down ttings to the slots
in the rear of the enclosure and, conrming that
the instrument is positioned on a level plane,
secure the instrument to the panel with panel-
mount ttings (Fig. 4.1).
All dimensions in millimeters
Fig. 4.2 Panel Cut
All dimensions in millimeters
Fig. 4.2 Panel Cut
All dimensions in millimeters
Batch controller
Fig. 4.3 Mounting Height
All dimensions in millimeters
Batch controller
Fig. 4.3 Mounting Height

E-215-7-E
7
5. WIRING
NOTE: See “WIRING” in the pulse generator instruction manual.
5.1 Cables for Field Wiring
(1) For flowmeter input signal cable, electrostatically shielded, polyethylene insulated, vinyl-sheathed
control cables (CVES, 1.25 to 2mm2, 2- or 3-conductor), or equivalent, must be used.
For output signal cables, insulated, vinyl-sheathed cables (CVV, CVS … JIS C 3401) are suggested.
(2) Cable shields must be connected to terminal “G” of the controller. At the probe end, leave the shield
wire end unprepared.
5.2 Wiring Connections
(1) Conduit work is suggested for eld wiring.
NOTE: In conduit work, use separate conduit for power cables and signal cables in order to minimize
the possibility of stray current pickup.
(2) Route cables sufciently away from other power lines or power circuits, if any, to reduce the possibility
of inductive interference to a minimum.
(3) Use crimp-style terminal lugs for connections and ensure good electrical contact. Connection terminals
are found at rear of the controller (Fig. 5.1).
(4) In applications where an inductive load (valve, counter, etc.) is driven, do not fail to use a surge
suppressor (see Fig. 5.3).
(5) Give a 30-centimeter approx. allowance to the wiring harness to allow internal assembly withdrawal for
servicing.
5.3 Identifying the External Connection Terminal Block
At the rear of the controller, terminal block (terminal Nos. 17-22) secured to the output board and removable
terminals block (terminals Nos. 1-8, 9-16) secured with four screws are found.
CAUTION: Before making wiring connections, verify the validity of flowmeter (pulse generator)
and receiving instrument combination by referring to their product No., tag No., etc.
Front panel
Terminal block
fitting screws
Terminal block for
EXT. connections
Fig. 5.1
Fig. 5.2
Shorting strip If remote operate input STOP is
unused, short out terminals
STOP (19) and COM (20) with
this strip.
Terminal
Nos. 1-8
Rear panel
Terminal
Nos. 17-22
Terminal
Nos. 9-16

E-215-7-E
8
5.4 Identifying the External Connection Terminals
Table 5.1
Term.
No. Label Required Conditions for Connections and Specications
1
Flow Signal Input
SUP.
FLOW SIG
INPUT
Current pulse
[PA14, 15, 25,
NPG60A (E)]
Contact-closure pulse
Open collector pulse
2-wire voltage pulse
(PG20, Coriolis meter)
3-wire open collector
3-wire voltage pulse
[PG30, NPG60A (F),
60 (E3), FLOWPET- EG]
2 SIG.
3 COM.
4
Output to
External
Totalizer
TOTAL COUNT OUTPUT Non-contact relay output, a set of Form “a” contact Capacity: 250V AC/DC 0.15A
Output pulse width: 1ms (standard) or 50ms
5
6
Power
L1 (+) POWER
SUPPLY 85 to 264VAC 50/60Hz
7L2 (–)
8 GND Ground terminal
9
End-of-
Batch
Output
BATCH END OUTPUT Non-contact relay output, a set of Form “a” contact Capacity: 250V AC/DC 0.15A
10
11
Valve Control
Signal
VALVE OPERATION
SIGNAL (SV)
Partial-flow signal (SV): Initial open signal
Relaycontact output, a set of Form “c” contact Capacity: 250VAC, 1A
a
c
b
12
13
14
Valve Control
Signal
VALVE OPERATION
SIGNAL (MV)
a
c
b
Upper-limit flow signal (MV): Full-open signal
Relay contact output, a set of Form “c” contact Capacity: 250VAC, 1A
15
16
17
Remote Control
Input
START
REMOTE
CONTROL
INPUT
a
a
b
START: Form “a” contact
RESET: Form “a” contact
STOP: Form “b” contact
Contact current:
10mA max. at 15VDC
Signal width:
Instantaneous signal
※: 1 sec.
18 RESET
19 STOP
20 COM. NOTE: Short STOP when not in use.
21
Alarm
Output
ALARM OUTPUT An output on detection of missing pulses, overmeasurement, parameter error Relay
contact output, Form “a” output Capacity: 250VAC, 1A
22
NOTE ※:Provide at least 2 seconds between individual signals (see page 10).
5.5 Flowrate Input and their Terminals
Table 5.2
Signal Type Contact-closure Pulse, 2-wire
Voltage Pulse, Open Collector Pulse Current pulse 3-wire open collector pulse
3-wire voltage pulse
Generator PG20, Coriolis owmeter PA 14, 15, 25, NPG60A (E)
PG30, NPG60A (F),
NPG60A (E3),
FLOWPET-EG
Terminals
1—— ○ + ○ SUP.
2○+ ○– ○SIG.
3○– —— ○ COM. (0V)
○: Terminals in use

E-215-7-E
9
5.6 Flow Signal Input Wiring Connections
(1) Contact-closure pulse, 2-wire voltage
pulse,open collector pulse (PG20, Coriolis
owmeter)
(2) Current pulse [(PA14, 15, 25, NPG60A(E)]
Contact-closure
pulse
NOTE:
This does not mean to accept three
different types of pulse generators
at the same time.
EL1810
Terminal block
EL1810
Terminal block
Current pulse
Open collector
Pulse
Voltage pulse
Pulse generator
Pulse generator
Fig. 5.3
Fig. 5.4
Contact-closure
pulse
NOTE:
This does not mean to accept three
different types of pulse generators
at the same time.
EL1810
Terminal block
EL1810
Terminal block
Current pulse
Open collector
Pulse
Voltage pulse
Pulse generator
Pulse generator
Fig. 5.3
Fig. 5.4
(3) 3-wire open collector pulse
3-wire voltage pulse
[PG30, NPG60A (F), NPG60A (E3), FLOWPET-EG]
EL1810
Terminal block
Pulse generator
Fig. 5.5
CAUTION: Before making wiring connections, verify the validity of flowmeter (pulse generator)
and receiving instrument combination by referring to their product No., tag No., etc.

E-215-7-E
10
5.7 Example of Hookup
OVAL flowmeters, Coriolis flowmeters, etc.
1ms (std.) or 50ms
ON duration
1 sec.
1 sec.
3-way
directional
valve Combination
filter/reducing valve
Surge suppressor
Ratings
R: 120Ω
C:
0.1μF 250V AC
Air
supply
1 sec.
2 sec.
min.
2 sec.
min.
Signal duration
Power: 85 to 264V AC, 50/60Hz
Fig. 5.6 Example of Wiring Connections
Output to remote
totalizer counter, etc.
(Non-contact relay output,
Form “a” contact)
End-of-batch output,
LED indicator. etc.
(Non-contact relay output,
Form “a” contact)
START : Form “a” contact)
RESET : Form “a” contact)
STOP : Form “b” contact)
Power
Valve
Alarm output (missing pulses, overmeasurement,
parameter error, or other fault)
Can activate an LED indicator, etc.
(Relay contact output, Form “a” contact)
Two-stage shutoff valve
Flow signal input
Coriolis flowmeter
External connection terminal block
(at the top of controller)
OVAL
FLOWMETER
NOTE: Remote command inputs and front-panel
buttons have their functions in common.
See Sec. 8.3 “Operation Sequence” for
signal input procedures.
CAUTION
If remote control input is not used,
always short across STOP (19) and
COM. (20).
CAUTION
Couple a surge suppressor, etc. in
parallel with inductive load.
(R: 120ΩC: 0.1μF 250V AC)

E-215-7-E
11
6. FRONT PANEL DISPLAY
6.1 Front Panel Display Functions
The front panel has three control keys – STOP/ROT., RESET◀, START/▲at the bottom and three LED
status indicators – STOP, SET, OPE (red, orange, green) at top left. The upper LCD 1 is an 8-digit display
with 7mm high characters and the central LCD 2 is an 8-digit display with 12.7mm high characters.
Operation Indicators
(RUN, MV, SV)
Operation status indicator LEDs
STOP (RED), SET (ORG), OPE (GRN) Operation indicators
(ALM, TC, END)
Tag No. plate
Control keys
STOP (ROT.) RESET () START ()
Fig. 6.1 Front Panel Displays and Controls
Measurement unit label
LCD2 display
Batch setting (8-digit)
LCD1 display
s4ARGETBATCHSETPOINTDIGIT
Displays target batch setpoint only,
while batch process is in progress.
s'RANDTOTALDIGIT
s25.INDICATORSSTANDTHSEGMENTS
light up.)
Labels Functions
LED indicator
STOP Stays on while the batch process is stopped.
SET Comes on while the batch setpoint is changed. ※1
OPE. Stays on while the batch process is in progress.
LED 1 display
RUN Blinks on and off while power is on (in normal operation).
SV, MV Comes on in response to valve control signal output SV or MV. (Stays on until reset.)
ALM Comes on while an alarm output (missing pulse, overmeasurement) is produced.
(Stays on until reset.) ※2
TC Blinks in synchronism with each totalizer count and its output to the remote counter.
END Comes on at the end of batch. (Stays on until reset.)
NOTES: ※1. For information about the batch setup mode, see Section 9.1 on page 20.
※2. ALM does not light upon detection of a parameter error.
CAUTION:
RUN , SV , MV , ALM , TC , and END are indicated using the LCD 1 horizontal
segments in its 1st and 8th digit. The display shows the batch setting on the 6-digit
display field, excluding these 1st and 8th digits at both ends.
In the grand total mode, the display becomes a full 8-digit counter.

E-215-7-E
12
6.2 Control Key Functions (other than batch setup mode and other setup mode)
NOTE: For control key locations, see Fig. 6.1 on page 11.
STOP
ROT. Key functions
Item Functions
Batch in progress Batch stops ( OPE : goes out; Valve control signals SV, MV: close;
LCD 1 SV , MV : go out).
Upon detection of missing
pulses Missing pulses alarm output is reset (LCD 1 ALM : goes out).
LCD1 shows target batch
setpoint or grand total.
LCD 1 screen switches:
Batch setpoint (6-digit) + LED 1 operation indicators
RUN , SV , MV , ALM , TC , END ,
Shown alternately.
Grand total reading (8-digit)
CAUTION:You cannot switch the display from the batch setting to the grand total unless you
reset the current batch process by resetting the missing pulse alarm ALM, end-of-
batch END, and overmeasurement alarm ALM.
RESET
◀Key functions
Item Functions
LCD 1 shows grand total. None
LCD 1 shows batch setpoint
(not in operation)
Batch process reset (LCD 2 batch reading is reset to zero).
End-of-batch output is reset (LCD 1 END : goes out).
Overmeasurement alarm output is reset (LCD1 ALM : goes out).
Parameter error alarm output is reset.
START
▲Key functions
Item Functions
LCD 1 shows grand total. None
LCD 1 shows batch setpoint
(not in operation).
Simultaneously with the start of a batch process (OPE.: comes on),
valve operate signal SV opens (LCD 1 SV : comes on).
CAUTION: Simultaneously with OPE. illumination, the valve operate signal SV opens (LCD
1 SV comes on). If the two-stage open mode remains disabled, the valve operate
signal MV also opens (LCD1 MV comes on), however.

E-215-7-E
13
6.3 Output Functions
NOTE: For the information about the front panel display functions not described in this section, see
Section 6.1 on page 11 and Table 11.1 on page 30.
(1) Alarm Output
Upon detection of missing pulse, overmeasurement, or parameter error, the controller produces an alarm
output.
The LCD 1 ALM then comes on (only upon detection of missing pulses or overmeasurement) and
completes a circuit across terminals 21 and 22 (Relay contact output Form “a” contact) (upon detection of
all alarms).
a. Missing pulse alarm detection (Fig. 6.2)
Following
START
▲
key depression to start a batching process, if no ow pulse signal (terminals 1-2-3)
arrives within the time preset for missing pulse detection, an alarm output is produced. Immediately after
startup, however, time measurement begins approximately 5 seconds later.
For the setup procedure, refer to Sec. 9.1.
[Batch in progress]
Flow pulse signal stop Missing pulse alarm detected
STOP key
(alarm reset)
START key
(Restart)
Missing pulse duration set
ALM indicator
Alarm output
SV, MV indicator/output
Batch end output
Fig. 6.2
b. Overmeasurement alarm detection (Fig. 6.3)
When a ow pulse signal arrives while a batch process is in progress, a target batch quantity will eventually
be reached and an end-of-batch signal is generated. If ow pulses continue to arrive at this point and
exceed a preset overmeasurement quantity, an alarm output is produced.
For the setup procedure, refer to Sec. 9.1.
RESET key
(alarm reset/
batch total reset)
START key
(Batch start)
Fig. 6.3
Batch end
Overmeasurement preset
Overmeasurement alarm detected
ALM indicator
Alarm output
SV, MV indicator/output
Batch end output

E-215-7-E
14
c. Parameter error alarm detection (Fig. 6.4)
When an error in any of parameter settings is found, an alarm output is produced and a data error
message “DATA Err” appears on the display (the LCD 1 ALM does not come on in this case).
Each time STOP
ROT. key is pressed, the LCD 1 display scrolls through the available data, enabling the
operator to identity which parameter causes a problem (see Fig. 6.5).
Following the error identification, press
RESET
◀key to cancel the alarm output.
(A message “DATA Err” disappears and all the data are reset (initialized).)
Following the reset step above, set up the parameters of interest and the target batch quantity once
again according to the specification. See Sec. 9.1 for the setup procedure.
STOP key
(Confirm param.)
RESET key
(Initialize param.)
Parameter error alarm detected
ALM indicator
Reestablish param.Alarm output
“dAtA Err” indicator
Fig. 6.4
STOP
ROT.
PressParameters
s"ATCHSETTINGhBvAPPEARSATLEFTEND
s"ATCHTOTALCOUNT
s'RANDTOTALCOUNT
s3CALEFACTOR
s&REQUENCYREDUCTION
s)NITIALSETTING
s&INALSETTING
s-ISSINGPULSESETTING
s/VERSHOOTSETTING
KEY $ISPLAYEDALTERNATELY
&IG
Messages upon detection of a parameter error alarm
•
•
•

E-215-7-E
15
(2) End-of-batch output
When a ow signal reaches the target batch quantity during a batch process, an output is produced.
The LCD 1 END then comes on and completes a circuit across terminals 9 and 10 (Non-contact relay
output, Form “a” contact).
(3) Scaler
If incoming pulse signal is of unfactored pulses, a constant inherent to the owmeter used is multiplied in
the scaler; conversion takes place into quantities in industrial engineering units of measure in integer; the
resultant quantities are used for batch processes.
For the setup procedure, refer to Sec. 9.1.
(4) Input frequency division (scaling)
There are two approaches in setting up the input frequency division. One is a frequency reduction by
hardware, using a jumper and the other is a frequency reduction by software, using the front panel control
keys.
For the setup procedure, refer to Sec. 9.1 and 9.5.

E-215-7-E
16
7. BLOCK DIAGRAM
LCD 2 Disp. (batch reading 8-digit) LCD 1 Disp. (batch setting 6-digit)
Power to generator
Flowrate signal
input
Remote control input
Power
1,3
4,5
9,10
21,22
11 to 16
2
17,18,19
20
6,7
24V
13.5V
START
RESET
STOP
85 to 264VDC
50/60Hz
Power to
generator
Wave-
shape
Regulated
Voltage
source
Power to
generator
Freq.
divide
Freq.
divide
One-shot
multivibrator
1ms or
50ms
Batching
microprocessor
6-digit
Batch counter
8-digit
Total counter
Scaler
Front-panel
control keys
Display boardPower board Output board
Non-contact
relay
Non-contact
relay
Relay
Relay
Output to external total counter
TC
Non-contact relay output
Form “a” contact
End-of-batch output
END
Non-contact relay output
Form “a” contact
Alarm output
ALM
Relay contact output
Form “a” contact
(missing pulse, overshoot,
param. error)
Valve control signals
SV, MV
Relay output
Form “c” contact, one set each
NOTES
Missing
pulse alarm
Overmeasure
alarm
Com-
pare
Batch setting
Initial setting
Final setting
6-digit
0 to 999 counts
0: No setting
Default: 80 counts
Toggle
switch
RUN ⇔SET
RUN: Run mode
SET : Setup mode
Buzzer
Counter
About A
0 to 15 sec.
0: No alarm
Default: 10 sec.
About B
0 to 99 counts
0: No alarm
Std.: 10 counts

E-215-7-E
17
8. OPERATION
8.1 Preparation Before Operation
(1) Make sure to see that the controller and associated equipment are correctly installed, connected and
wired with no place left unnished.
WARNING
Make sure to see that the power terminals are connected to a source of the rated voltage.
Connecting an incorrect power voltage source may ruin the controller.
(2) Make sure that the shutoff valve is correctly wired and set. For details, see the instruction manual for
the shutoff valve.
8.2 Preoperational Checks
Make sure to see that the shutoff valve operates properly without allowing the flow.
(Run this check daily before operation.)
•
(1) Supply power to the controller. Conrm that LED
STOP indicator becomes illuminated and that
displays LCD 1 and LCD 2 come on.
(2) Enter some arbitrarily set quantity of a batch.
NOTE: See Section 9.1.1.2, “Example of Bach
Setup” on page 21.
(3) Press
START
▲
key to make certain that the
shutoff valve opens.
(4) Press STOP
ROT. key to make certain that the shutoff
valve closes properly.
(5) Repeat steps (3) and (4) above several times to make certain that the shutoff valve opens and closes
properly.
(6) If the controller features remote start and stop, repeat steps (3), (4) and (5) above also at the remotely
located point.
8.3 Operation Sequence
(For information about the control keys, see Section 6. FRONT PANEL DISPLAY on page 12.)
(1) Turn on power.
(2) Allow the LCD 1 display to show the batch setting.
(3) Set the target batch quantity desired.
The unit of measure is indicated on the unit label at lower right below the LCD 2 display.
(4) Press
RESET
◀key to reset the batch total counter of LCD 2.
(5) Press
START
▲key to start up and the controller will start batching operations.
CAUTION
If the controller receives even a single pulse during the transitional time between RESET key
and START key depressions, it will fail to start. (For details, see Question 3 in Section 10.4
Q&A Controller Behavior in Standby Mode.)
key
key
key
Fig. 8.1
key
key
key
Fig. 8.1

E-215-7-E
18
(6) To perform a repeated metering of the last measured batch, all you need is to press the reset key to
bring the total counter of LCD 2 back to zero and then press the start key:
Press
RESET
◀key to reset the total counter.
Pressing
START
▲key readies to restart the last metered measurement.
NOTE: For metering different batches, select a new target batch setting each time.
(7) Emergency shutoff (or temporary interruption)
To bring the controller to an emergency stop, press STOP
ROT. key. The shutoff valve will come to a full
closure.
Pressing
START
▲key will resume operation and continue metering the remaining quantity from the
point of interruption.
In this way, safe and accurate measurement can be achieved.

E-215-7-E
19
8.4 Confirming the Two-stage Valve Opening and Closure
You can conrm the valve opening and closing in two stages by one of the following two approaches:
Once set the initial and final setpoint at “0,” choose a batch setpoint somewhere above “1” and press
START
▲and STOP
ROT. key to verify proper shutoff valve actuation.
If simulated pulses (from OVAL pulse checker PC2201, for example) are available, you can confirm
proper batch operation of the shutoff valve by setting the initial and final setpoint at any point, pressing
START
▲key, and then feeding a simulated pulse train.
NOTE: The target batch setting should be greater than the sum of the initial and nal setting.
8.5 Description of Batch Operation
NOTE: Operation can best be understood by referring to the operation time chart in Fig. 8.2 below.
Upon depression of
START
▲key, the valve opens to a predetermined position (initial owrate). When a
predetermined quantity (from point A to point B) has been delivered, the valve opens fully; when metering
has reached point C, the valve automatically throttles the flow and maintains a predetermined valve
position (nal owrate).
At point D, a closure signal is generated. However, due to a time lag in valve actuation, inherent to the
type of valve used, the valve actually close at point E. If an overshoot, or overmeasurement, exceeds a
predetermined quantity, the controller produces an alarm.
Safe and accurate measurement is thus achieved. In this connection, valve positions A →B and C →D
must be preselected on the part of the valve.
Fig. 8.2 Operation Time Chart
Valve
control
signals
Partial flow signal
(Partial open signal)
High limit
flow signal
(Full open signal)
High limit flow open
(MV: LCD 1 comes on.)
Partial flow open
(SV: LCD 1 1comes on.)
High limit flowrate
Flow
rate
Initial flowrate
Initial partial flow
(Initial setting)
START
signal
STOP
signal
Time
Final flowrate
Overshoot
End of batch
Batch setting
(Target quantity)
Final partial flow
(Final setting)
•
•

E-215-7-E
20
9. SETTING UP OR CHANGING PARAMETERS
Setting up parameters and variables other than those to be set up with controller’s front-panel control keys
requires internal assembly removal since it involves conguring the internal boards of the controller.
NOTE: Defaults (your specications inclusive) appear on the parameter settings label attached to the
side of the controller. ⇒See page 22.
9.1 How to Change Parameters (batch setup and other setup modes)
9.1.1 Batch Setup Mode
To set up a batch, holding STOP
ROT. key depressed for more than 3 seconds while the following conditions
are met.
The front LED SET lights up and the LCD 1 (batch setting) blinks on and off. Target batch setpoint
alteration is now acceptable.
Conditions required for changing batch setpoints
(1) The display does not show the grand total.
(2) A missing pulse alarm has not been detected along with its output.
(3) An overshoot alarm has not been detected along with its output.
(4) An end-of-batch signal has not been produced.
(5) A batch operation is not in progress.
CAUTION: 1. If an alarm output exists, reset it before you work.
2. While the controller is not in the batch operation but is only counting
incoming flow pulses for totalization, a change in batch setting is
acceptable.
9.1.1.1 Operation (batch setup mode)
On seeing the front panel SET illuminated and the whole LCD 1 ickering (in response to the procedure
above), you can change the current setpoint by the following procedure.
Batch Setup Mode comes on and LCD 1 (batch setting) blinks.
6 digits
Batch
setting Change
Figure adjust Shift Setup
A numerical value is finalized
with two control keys.
To RUN mode omes on. To exit without changing any setting
Upon depression of STOP
ROT. key, the value entered is stored in the memory and the LCD 1 display goes
back to the RUN mode.
Table of contents
Popular Controllers manuals by other brands

NTI
NTI Sentry 2100 INSTALLATION & OPERATIONAL INSTRUCTIONS
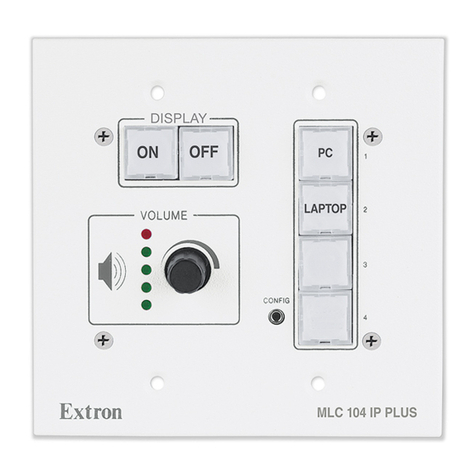
Extron electronics
Extron electronics MediaLink Controllers with IP Link MLC 104 IP... Setup guide
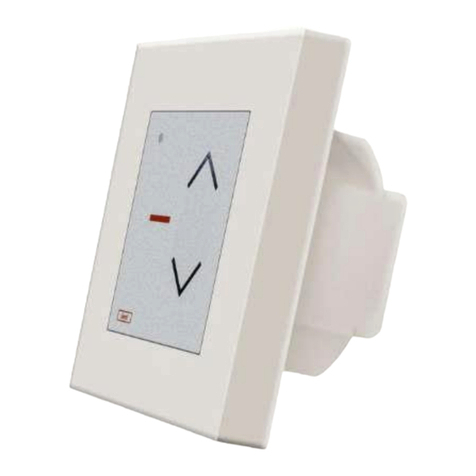
Inel
Inel ST-01RN Series Instructions for installation and use
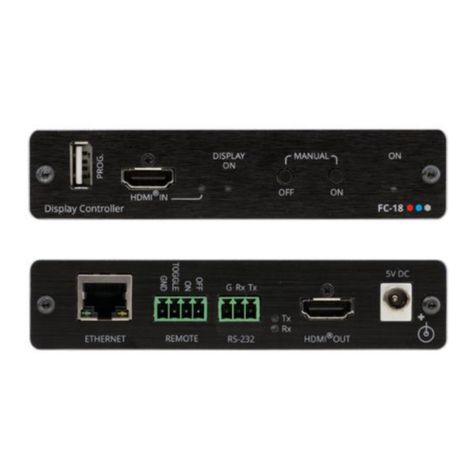
Kramer
Kramer FC-18 quick start guide
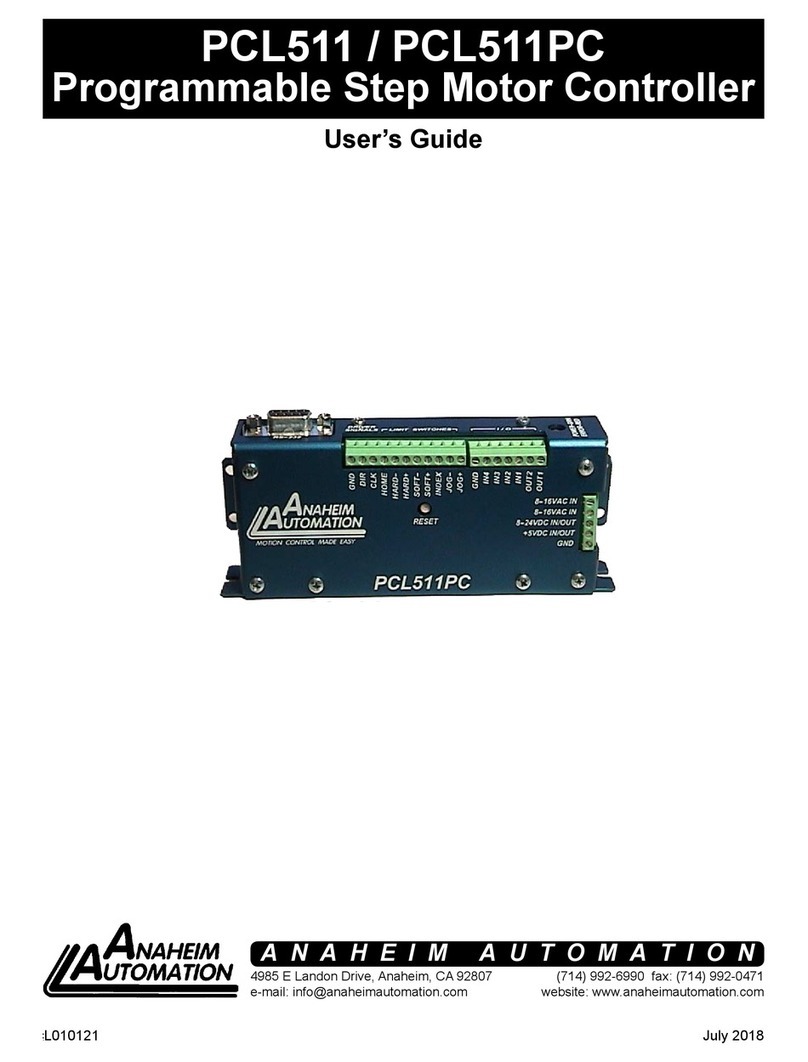
Anaheim Automation
Anaheim Automation PCL511 user guide
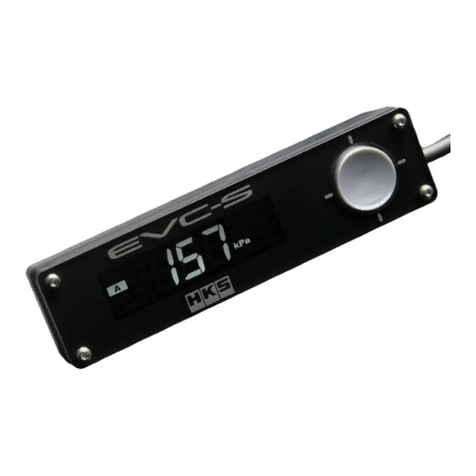
HKS
HKS EVC-S instruction manual
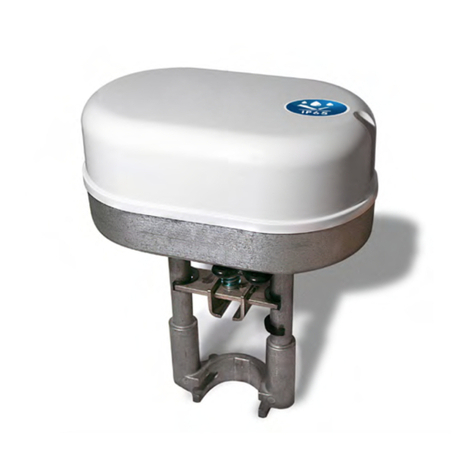
C2AI
C2AI MVE2 65 Series manual
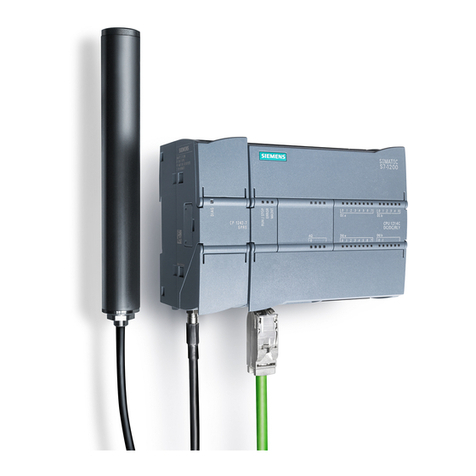
Siemens
Siemens SIMATIC NET S7-1200 operating instructions
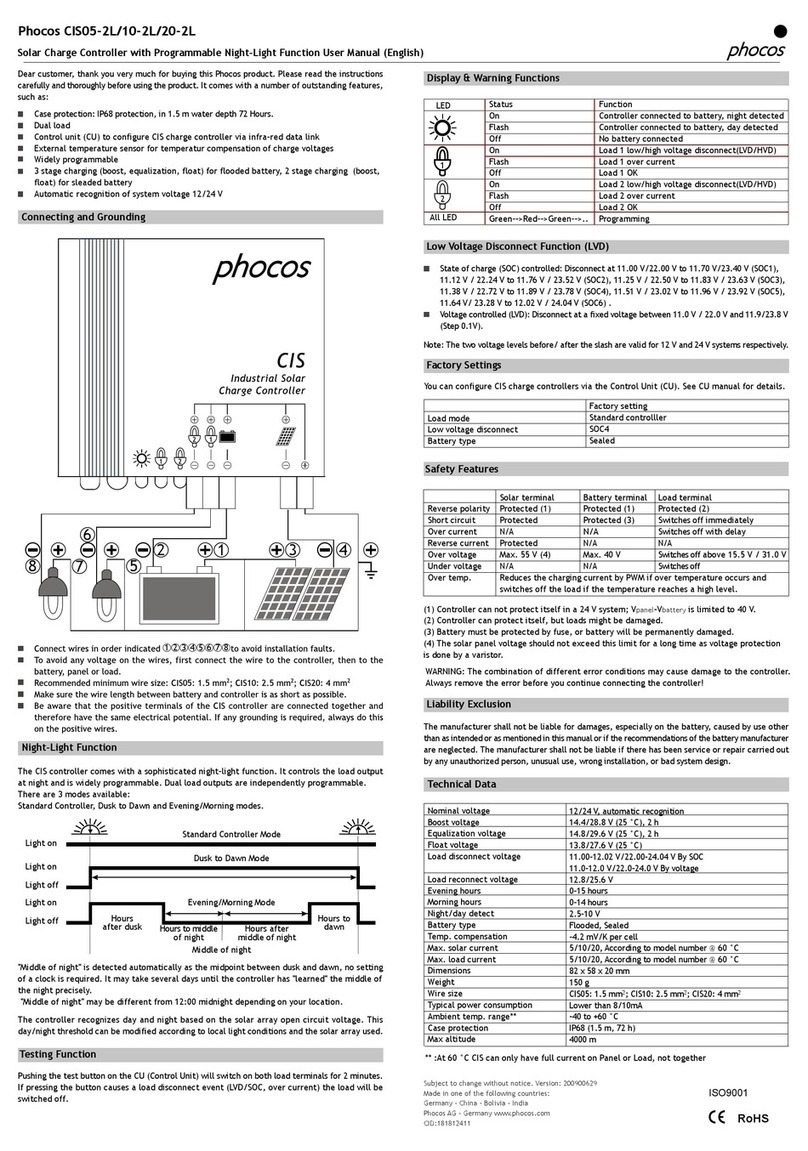
Phocos
Phocos CIS05-2L user manual
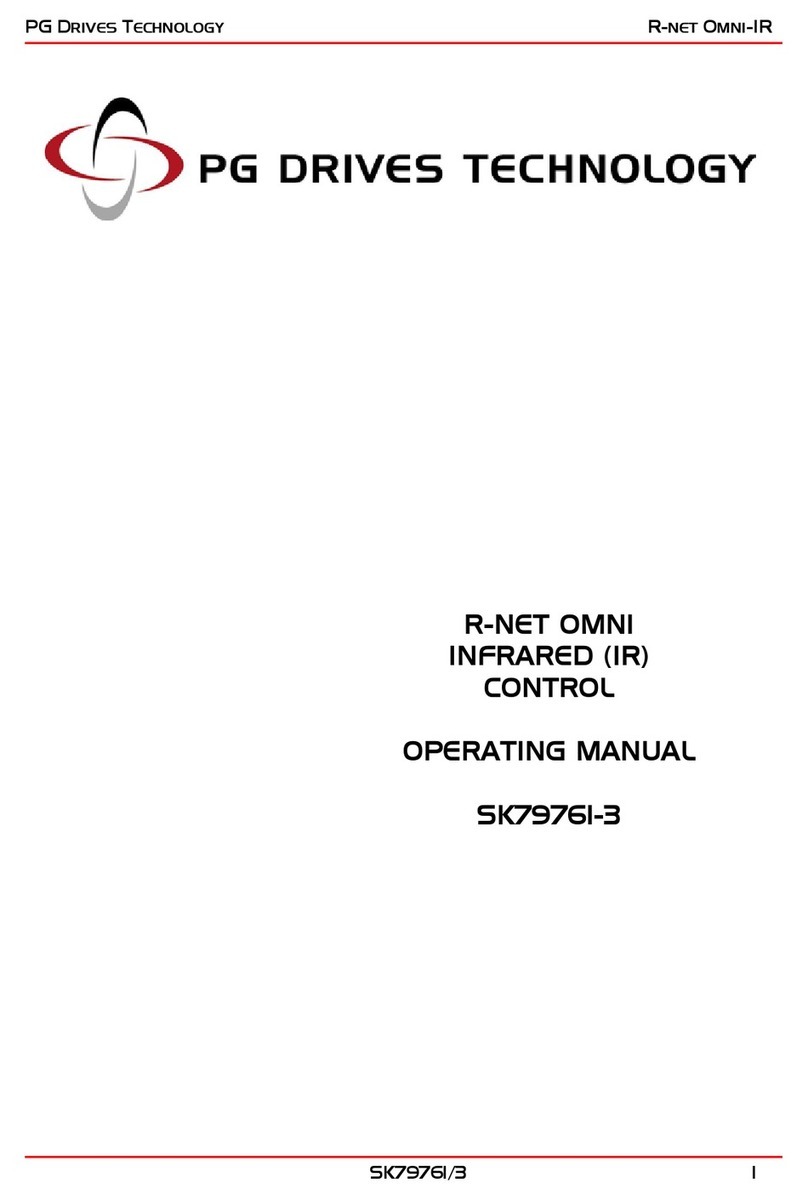
PG Drives Technology
PG Drives Technology SK79761-3 operating manual
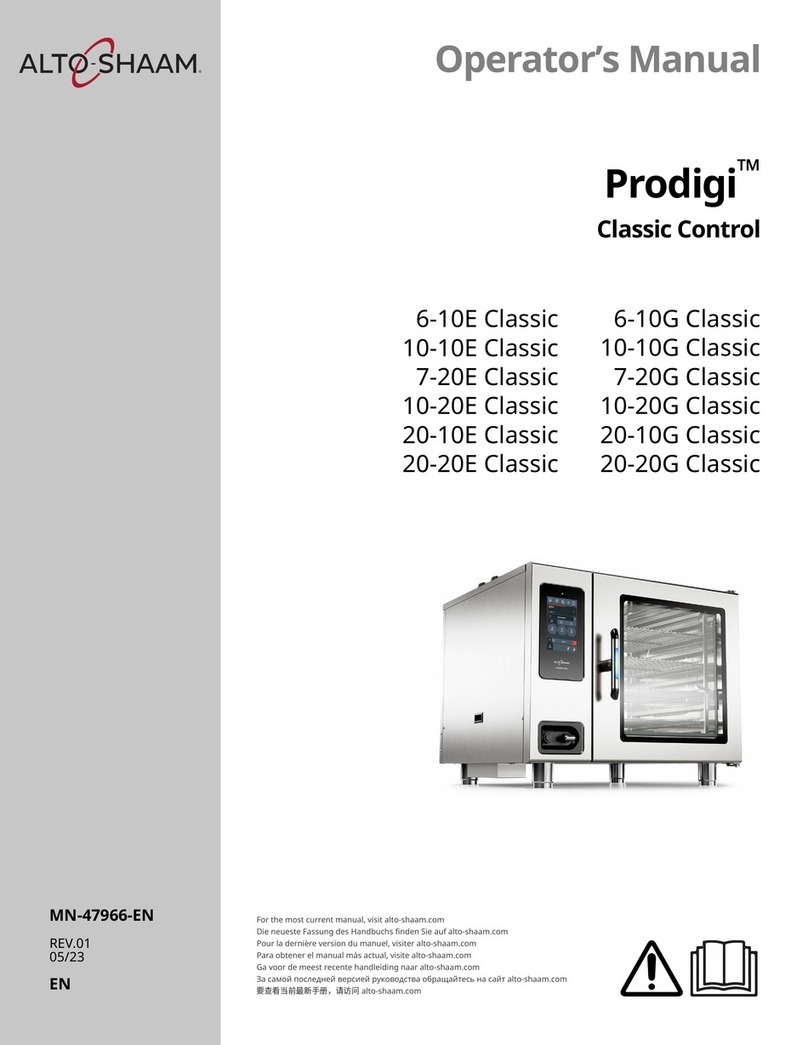
Alto-Shaam
Alto-Shaam Prodigi Classic Control 6-10E Operator's manual
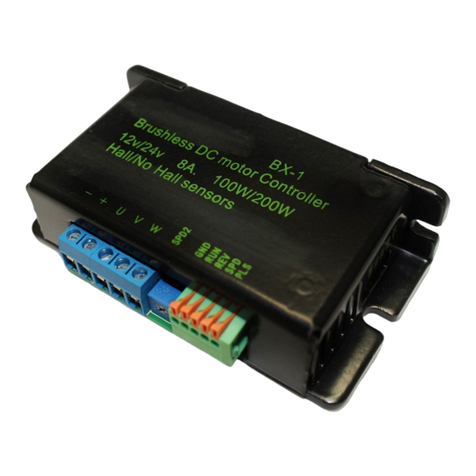
progressive automations
progressive automations LC-241 user manual