PCB Piezotronics 117B02 User manual

Model 117B02
Conformal Calibration Adaptor for Model 117B020, 338 Norma Mag.
Installation and Operating Manual
For assistance with the operation of this product,
contact PCB Piezotronics, Inc.
Toll-free: 800-828-8840
24-hour SensorLine: 716-684-0001
Fax: 716-684-0987
E-mail: [email protected]
Web: www.pcb.com

Manual 21354 Rev E
ECN 50523
Repair and Maintenance
PCB guarantees Total Customer Satisfaction through its
“Lifetime Warranty Plus” on all Platinum Stock Products
sold by PCB and through its limited warranties on all other
PCB Stock, Standard and Special products. Due to the
sophisticated nature of our sensors and associated
instrumentation, field servicing and repair is not
recommended and, if attempted, will void the factory
warranty.
Beyond routine calibration and battery replacements
where applicable, our products require no user
maintenance. Clean electrical connectors, housings, and
mounting surfaces with solutions and techniques that will
not harm the material of construction. Observe caution
when using liquids near devices that are not hermetically
sealed. Such devices should only be wiped with a
dampened cloth—never saturated or submerged.
In the event that equipment becomes damaged or ceases
to operate, our Application Engineers are here to support
your troubleshooting efforts 24 hours a day, 7 days a
week. Call or email with model and serial number as well
as a brief description of the problem.
Calibration
Routine calibration of sensors and associated
instrumentation is necessary to maintain measurement
accuracy. We recommend calibrating on an annual basis,
after exposure to any extreme environmental influence,
or prior to any critical test.
PCB Piezotronics is an ISO-9001 certified company whose
calibration services are accredited by A2LA to ISO/IEC
17025, with full traceability to SI through N.I.S.T. In
addition to our standard calibration services, we also offer
specialized tests, including: sensitivity at elevated or
cryogenic temperatures, phase response, extended high
or low frequency response, extended range, leak testing,
hydrostatic pressure testing, and others. For more
information, contact your local PCB Piezotronics
distributor, sales representative, or factory customer
service representative.
Returning Equipment
If factory repair is required, our representatives will
provide you with a Return Material Authorization (RMA)
number, which we use to reference any information you
have already provided and expedite the repair process.
This number should be clearly marked on the outside of
all returned package(s) and on any packing list(s)
accompanying the shipment.
Contact Information
PCB Piezotronics, Inc.
3425 Walden Ave.
Depew, NY14043 USA
Toll-free: (800) 828-8840
24-hour SensorLine: (716) 684-0001
Repair inquiries: rma@pcb.com
For a complete list of distributors, global offices and sales
representatives, visit our website, www.pcb.com.
Safety Considerations
This product is intended for use by qualified personnel
who recognize shock hazards and are familiar with the
precautions required to avoid injury. While our equipment
is designed with user safety in mind, the protection
provided by the equipment may be impaired if equipment
is used in a manner not specified by this manual.
Discontinue use and contact our 24-Hour Sensorline if:
Assistance is needed to safely operate equipment
Damage is visible or suspected
Equipment fails or malfunctions
For complete equipment ratings, refer to the enclosed
specification sheet for your product.
Definition of Terms and Symbols
The following symbols may be used in this manual:
DANGER
Indicates an immediate hazardous
situation, which, if not avoided, may
result in death or serious injury.

Manual 21354 Rev E
ECN 50523
CAUTION
Refers to hazards that could damage
the instrument.
NOTE
Indicates tips, recommendations and
important information. The notes
simplify processes and contain
additional information on particular
operating steps.
The following symbols may be found on the equipment
described in this manual:
This symbol on the unit indicates that
high voltage may be present. Use
standard safety precautions to avoid
personal contact with this voltage.
This symbol on the unit indicates that
the user should refer to the operating
instructions located in the manual.
This symbol indicates safety, earth
ground.

Manual 21354 Rev E
ECN 50523
PCB工业监视和测量设备 - 中国RoHS2公布表
PCB Industrial Monitoring and Measuring Equipment - China RoHS 2 Disclosure Table
部件名称
有害物质
铅(Pb)
汞
(Hg)
镉
(Cd)
六价铬(Cr(VI))
多溴联苯 (PBB)
多溴二苯醚(PBDE)
住房
O
O
O
O
O
O
PCB板
X
O
O
O
O
O
电气连接器
O
O
O
O
O
O
压电晶体
X
O
O
O
O
O
环氧
O
O
O
O
O
O
铁氟龙
O
O
O
O
O
O
电子
O
O
O
O
O
O
厚膜基板
O
O
X
O
O
O
电线
O
O
O
O
O
O
电缆
X
O
O
O
O
O
塑料
O
O
O
O
O
O
焊接
X
O
O
O
O
O
铜合金/黄铜
X
O
O
O
O
O
本表格依据 SJ/T 11364 的规定编制。
O:表示该有害物质在该部件所有均质材料中的含量均在 GB/T 26572 规定的限量要求以下。
X:表示该有害物质至少在该部件的某一均质材料中的含量超出 GB/T 26572 规定的限量要求。
铅是欧洲RoHS指令2011/65/ EU附件三和附件四目前由于允许的豁免。
CHINA RoHS COMPLIANCE

Manual 21354 Rev E
ECN 50523
Component Name
Hazardous Substances
Lead (Pb)
Mercury (Hg)
Cadmium (Cd)
Chromium VI
Compounds
(Cr(VI))
Polybrominated
Biphenyls (PBB)
Polybrominated
Diphenyl Ethers
(PBDE)
Housing
O
O
O
O
O
O
PCB Board
X
O
O
O
O
O
Electrical Connectors
O
O
O
O
O
O
Piezoelectric Crystals
X
O
O
O
O
O
Epoxy
O
O
O
O
O
O
Teflon
O
O
O
O
O
O
Electronics
O
O
O
O
O
O
Thick Film Substrate
O
O
X
O
O
O
Wires
O
O
O
O
O
O
Cables
X
O
O
O
O
O
Plastic
O
O
O
O
O
O
Solder
X
O
O
O
O
O
Copper Alloy/Brass
X
O
O
O
O
O
This table is prepared in accordance with the provisions of SJ/T 11364.
O: Indicates that said hazardous substance contained in all of the homogeneous materials for this part is below the limit
requirement of GB/T 26572.
X: Indicates that said hazardous substance contained in at least one of the homogeneous materials for this part is above the limit
requirement of GB/T 26572.
Lead is present due to allowed exemption in Annex III or Annex IV of the European RoHS Directive 2011/65/EU.

Drawing Number: 21210
Revision: NR
AN IMPROVED TECHNIQUE FOR
UTILIZATION OF CONFORMAL BALLISTICS
SENSOR CALIBRATION DATA
1
The PCB Series 117B Conformal Ballistics Sensor
(patented) measures chamber pressure in a novel
manner.
The sensitive surface of the sensor, when properly
installed in the gun chamber, conforms or blends in
precisely with the inside surface of the chamber actually
forming a portion of the wall adjacent to the cartridge
case.
When the round is fired, the pressure builds up rapidly
inside the case, obturating the case outward against the
chamber. The force, transmitted through the thin
cartridge case wall stresses the sensor crystals producing
an output charge analogous to chamber pressure.
An exclusive calibration technique has been developed
in conjunction with the conformal sensor, consisting of a
simulated gun chamber which positions the sensor at the
same location as in the test barrel and provides for
hydraulic pressurizations of an actual cartridge case.
Using this system and a reference standard pressure
source, a point by point calibration is performed on
samples of the actual lot of ammunition under test to
take into account transmissibility characteristics of the
cartridge case for each lot of ammunition.
Because a certain amount of pressure is required to fully
obturate the cartridge case in the test chamber, a rather
severe non-linearity is exhibited over the first several
thousand psi of input pressure, i.e. until the cartridge
case is pressed firmly against the inside chamber walls.
Figure 1 illustrates a typical calibration result with .22
caliber rimfire ammunition.
Figure 1: Typical calibration graph
Conformal sensor with .22 caliber rimfire.
As shown in figure 1, the best straight line that can be
drawn through the majority of the data points in the
linear portion of the curve, does not pass through the
origin.
Because of this, the widely accepted zero based best
straight line method of linearity determination cannot be
applied to the conformal sensor. Also, the actual
sensitivity of this sensor may only be specified at one
input pressure level since the sensitivity is not a
constant, but varies with input pressure level.
This paper outlines a simple alternative approach to
utilization of conformal sensor data.
The most universally accepted method of defining
conventional sensor nonlinearity is the full scale error
band method used in conjunction with the zero based
best straight line.

Drawing Number: 21210
Revision: NR
AN IMPROVED TECHNIQUE FOR
UTILIZATION OF CONFORMAL BALLISTICS
SENSOR CALIBRATION DATA
2
Figure 2: Zero based best straight
line method of linearity determination.
To utilize the zero based best straight line method, the
corresponding value of the sensor output is plotted for
each value of input measurand up to full scale as shown
in Figure 2.
A straight line, intercepting the origin as shown, is fitted
to the data points by equalizing the error between the
points below the line and the points above the line.
Error bands, as delineated by the instrument
specification are constructed as shown in figure 2.
Typically, plus and minus one or two percent of full
scale is specified for quartz sensors.
An acceptable instrument is then defined as one whose
data points all fall within this error band.
The "sensitivity" of an instrument so calibrated is simply
the full scale output (charge or voltage) divided by full
scale input pressure, where F.S. output is determined by
the straight line as defined above.
input.S.F output.S.F
ySensitivit (Eq. 1)
The units for sensitivity are commonly pC/psi or
mV/psi.
Note that in this case, the sensitivity is identical to the
slope of the line, since the line does intersect the origin
by previous definition.
The general equation for a straight line in terms of the
dependent variable is:
y = mx + b (Eq. 2)
Figure 3
b in equation 2 is the y axis intercept.
m is the slope of the line defined as:
12
12 xx yy
tanθm
(Eq. 3)
Equation 2, expressed in terms of the independent
variable x is:

Drawing Number: 21210
Revision: NR
AN IMPROVED TECHNIQUE FOR
UTILIZATION OF CONFORMAL BALLISTICS
SENSOR CALIBRATION DATA
3
C
m
y
x (Eq. 4)
Where C is the X-axis intercept.
Equation 4 is directly applicable to the conformal sensor
even through the X variable (psi) becomes the
dependent variable when using the sensor output to
determine pressure.
Consider again the calibration graph of a typical
conformal sensor, shown in figure 4.
To calibrate a conformal sensor, the input pressure is
increased in discrete steps from 0 psi to full scale with
the corresponding output recorded at each step. The
information must be taken only once and only with
increasing pressure. A repeat run on the same cartridge
case will not yield the same values as the initial run due
to work hardening of the cartridge case metal.
Figure 4
At the lower pressures, the sensor has very little output
because there is a certain amount of clearance between
the cartridge case and the chamber wall. Obturation of
the cartridge occurs in this region.
However, when obturation is complete, the sensor
output is then linear with pressure from this point up to
maximum rated pressure.
In the past, a common procedure has been to calibrate
the conformal at the expected nominal pressure, deriving
a sensitivity at this point, e.g. point Po, Qo in figure 4.
The sensitivity determined by dividing output Qo by
corresponding pressure input Po, would then yield the
exact result if the input pressure was always exactly Po.
However, should the input pressure change to Pa, it is
clear that the reading would be in error, as shown in Fig.
4, since the actual sensitivity of the instrument is not the
same at Po, as it is at Pa.
A solution to this problem lies in utilization of equation
4.
C
m
y
x (Eq. 4)
Expressed in terms of sensor transfer parameters, input
pressure and output charge
intercept
(pC/psi)slope (pC)chargeindicated
(psi)pressureIndicated
(Eq. 5)
Where the slope of the line is defined as:
psi
pC
PP QQ
Slope
12
12
(Eq. 6)
and the intercept is the pressure axis intercept.

Drawing Number: 21210
Revision: NR
AN IMPROVED TECHNIQUE FOR
UTILIZATION OF CONFORMAL BALLISTICS
SENSOR CALIBRATION DATA
4
The straight line is the best line that can be constructed
through the linear portion of the curve as shown in
Figure 4 and the pressure intercept (or offset) is the
point at which this line crosses the pressure axis, in psi.
Instead of establishing the sensitivity parameter (which
has been shown to have little meaning for this sensor)
the user now determines the slope as defined in Eq. 6
and the accompanying pressure offset by constructing
the best straight line as described previously.
Pressures P1 and P2 are arbitrarily established at some
point well above and well below the expected nominal
pressure of the test.
The corresponding outputs at these pressures should be
an average of at least 20 cartridges taken from the same
lot of ammunition as is under test.
The main difference between utilization of the data with
this method is that now a constant (pressure offset) must
be added to each reading. However, this can be easily
handled by most data reduction methods in use today.
Example:
In actual practice, this is how a conformal sensor/charge
amplifier system could be utilized:
Assume that averaging the data from 20 consecutive
calibration runs performed on a conformal sensor
yielded a slope of .04 pC/psi and an intercept of 7,500
psi, determined by constructing the best fitting straight
line as described previously.
Assume also that average expected peak pressure is
25,000 psi.
Approximate full scale charge output is:
pC1000pC/psi.04psi25,000
Set range of charge amplifier output to 1000 pC/volt (or
other desired range).
Read peak output voltage of .800 volts during test.
Peak indicated charge is then:
1000 pC/volt x .80 volts = 800 pC
Indicated peak pressure is:
offset
slope
chargepeak
(pk)Pressure
psi7,500
pC/psi.04 pC800
P
P = 20,000 psi + 7500 = 27,500 Psi
As previously stated, this method will yield accurate
results anywhere within the linear portion of the sensor
calibration curve without inherent errors due to
variability of sensitivity with pressure level.
Accuracy should be close to that expected for standard
piezoelectric sensors within the limitation of
transmissibility variations in the cartridge cases.
Simplified standardization techniques for Conformal
Sensor
The technique described by the previous example
outlines one basic method of output signal utilization.
This method in actual practice may be cumbersome for
repeated testing because of the conversions that must be
made from measured charge output to indicated peak
pressure.
Other system scaling methods exist which further
simplify signal utilization.

Drawing Number: 21210
Revision: NR
AN IMPROVED TECHNIQUE FOR
UTILIZATION OF CONFORMAL BALLISTICS
SENSOR CALIBRATION DATA
5
Dial Gain Standardization
Many charge amplifiers feature a calibrated gain pot for
dialing in sensor sensitivity for the purpose of setting
system sensitivity to standardized unit of output voltage
(PCB Model 462A).
To utilize such amplifiers, dial in the actual value of
slope as determined by the calibration graph for the
particular ammunition lot.
Using the slope value effectively displaces the
calibration curve to pass through the origin (0) of the
calibration graph.
See Figure 5.
Figure 5
The indicated peak pressure P2 from the conformal,
which through scale factoring can be read to read
directly in psi (on a digital peak meter for example) is
simply added to the offset pressure to arrive at true peak
pressure, P1 + P2
This process can be further refined to, include a variable
voltage source as a bias in series with the output of the
charge amplifier. This voltage bias can be set to
simulate the offset pressure, and then the true peak
pressure can be read directly. (See figure 6 on the next
page)
Example:
Assume a 20 round calibration lot and attendant graph
yield a slope of .250 pC/psi and an offset of 5,000 psi.
Proceed as follows:
Dial the slope (.250) into the dial gain pot and select a
convenient full scale range over which to operate.
For example, for an expected full scale range of 40,000
psi, select 10,000 units/volt.
Now the indicated peak pressure can be read directly
from a digital peak holding meter such as the PCB
Model 451B.
If the offset supply is not used, simply add the offset
pressure (5,000 psi) to the indicated pressure to arrive at
true peak pressure.
If an offset supply is used as in figure 6 simply dial in
the offset voltage equivalent to offset pressure. Now the
offset will be automatically added and the true peak
pressure can be read directly from the peak meter.

Drawing Number: 21210
Revision: NR
AN IMPROVED TECHNIQUE FOR
UTILIZATION OF CONFORMAL BALLISTICS
SENSOR CALIBRATION DATA
6
Calibrate Signal Insertion
Another method that is useful especially when utilizing
a storage oscilloscope readout is to use a charge
calibrator to inject a full scale charge signal into the
charge amplifier. Multiply the sensor slope value by full
scale pressure to find full scale picocoulombs.
40,000 psi x .250 pC/psi = 10,000 pC
Set the charge calibrator for 10,000 pC and apply this
signal to the input of the amplifier. Now adjust the gain
of the oscilloscope (or charge amplifier if gain adjust is
available) to make full scale equal to a selected number
of oscilloscope divisions.
For example: 6 Div = 40,000 psi
Now the peak value can be determined from the
oscilloscope face or scope photo using a variable scale
or other interpolative methods.
Then, add the offset pressure to this value to determine
true peak pressure.

Drawing Number: 21210
Revision: NR
AN IMPROVED TECHNIQUE FOR
UTILIZATION OF CONFORMAL BALLISTICS
SENSOR CALIBRATION DATA
7
* Adds offset pressure (not available from PCB).
+-

Drawing Number: 21086
Revision: NR
OPERATION MANUAL FOR
CONFORMAL BALLISTICS PRESSURE SENSOR
Series 117B
1
1.0 INTRODUCTION
The Model 117B Conformal Sensor measures
pressure inside metallic cartridges and paper or
plastic shotshell, during firing of the round, without
drilled holes in the round.
The sensor is mounted flush with the chamber walls,
matching the curvature exactly. The expanded
cartridge or shotshell transmits forces through the thin
wall to the sensor.
The Model 117B is a conventional charge output
type sensor using synthetic quartz as the piezoelectric
sensing material.
An alignment guide now standard on all 117B
Models, simplifies installation by automatically
controlling rotational alignment of the sensor, leaving
only the depth adjustment consideration.
2.0 DESCRIPTION
Refer to enclosed installation drawing for outline
dimensions and physical description.
The basic sensor is a probe design with captivated
hollow clamp nut. The clamp nut rotates
independently of the probe body and serves to lift the
sensor out of the mounting port as it is unscrewed.
The alignment device consists of a pin and slotted
clamp assembly which fits tightly over the collar of
the sensor.
The hardened steel pin is accurately aligned with the
axis of the diaphragm curvature and when assembled
into a precisely drilled mating hole in the barrel or
calibration chamber, achieves near perfect rotational
alignment of sensor diaphragm.
The slotted clamp arrangement allows for tolerance in
the location of the guide pin hole in an axial direction
on the test barrel or calibration adaptor.
The precise depth adjustment is obtained by the use
of the correct thickness spacer selected from a set of 9
spacers of various thicknesses supplied with each
sensor.
Once the proper thickness spacer is found, removal
and re-installation now becomes a routine matter.
3.0 INSTALLATION
3.1 PORT PREPARATION
Prepare mounting port in accordance with installation
drawing 117-20 (XX)-90 supplied as part of this
manual.
NOTE: The installation port for the 117B is identical
to that for the 117A.
Drill guide pin hole as shown in installation drawing,
paying particular attention to locating C/L of hole
exactly on C/L of barrel.
Do not use a drill that is worn, as this may cause the
hole to be slightly undersized and the guide pin may
bind as it is drawn into the hole.
It is extremely important that the guide pin hole be
drilled parallel to the sensor mounting port to permit
the guide pin to move freely into the hole.
NOTE: Each model variation of the 117B is designed
to fit in a specific location (measured from the bolt
face) on a specific ammunition caliber. Changing
location and/or caliber will cause a mismatch of
diaphragm curvature with cartridge case diameter
since most cartridge cases are tapered.
3.2 INSTALLING THE SENSOR
After mounting holes have been prepared, proceed
with installation as follows:
1. On most models of 117B, it is not important
which side of the sensor is mounted toward
the muzzle.
However, on certain types of ammunition
(such as 20 mm cannon) which have a severe
taper, the diaphragm has a matching taper in

Drawing Number: 21086
Revision: NR
OPERATION MANUAL FOR
CONFORMAL BALLISTICS PRESSURE SENSOR
Series 117B
2
the curvature. In these latter cases, the
sensor forward side is identified with the
legend “FWD”etched on the guide collar to
which the slotted clamp is attached. The
clamp must be removed to find this legend.
If it does not appear, the sensor may be
mounted with either side toward the muzzle.
2. Loosen slotted clamp, but do not remove
clamp.
3. Select the middle thickness (.014) spacer
from the set of nine (065A19) supplied and
place it around sensor barrel.
4. Begin threading the sensor clamp nut into
the threaded mounting port, sliding slotted
clamp fore and aft as needed to allow guide
pin to fully enter hole.
Continue to turn clamp nut into hole by hand
or using 5/16 open end wrench.
Do not tighten when sensor bottoms.
5. Now tighten the screw closing slotted clamp.
6. Using open end wrench, tighten sensor
clamp nut.
NOTE: It is not necessary to put large amounts of
torque on this nut since a pressure seal is not
necessary. Approximately 5 to 10 ft. lbs. is
sufficient.
7. Now inspect flushness of diaphragm with
inside surface of chamber. This can be
accomplished visually in most cases.
If the diaphragm extends too deeply into the
chamber, select a thicker spacer and repeat
mounting procedure.
If the diaphragm is too deeply recessed,
select a thinner spacer and remount.
Once the proper thickness is found for
perfect flushness, the sensor may be
removed and reinstalled using this same
spacer and the proper depth will be achieved
each time.
NOTE: For best accuracy of results, use
same charge amplifier for calibration and for
actual operation. Use long TC for
calibration, medium or short TC for best
drift free operation.
4.0 POLARITY
Polarity of the Model 117B is negative i.e., the
charge output is negative for increasing pressure
input, making it compatible with inverting type
charge amplifiers.
5.0 CALIBRATION
Calibration of the Models 117B is facilitated by a
calibration adaptor which exactly matches the
chamber dimensions of the cartridge under test. An
actual cartridge case is hydraulically pressurized with
reference pressure to obtain a point-by-point sensor
calibration.
These calibration adaptors can be fabricated by the
user or can be purchased from PCB as our Model
090B calibration adaptor. Simply specify caliber and
longitudinal location of sensor.
For most rimfire applications, the sensor is located
.25 inches forward of the boltface.
For center fire cartridges a location .175 inches back
from the cartridge shoulder is preferred. Consult PCB
for recommendations on sensor locations if questions
arise.
Since most cartridge cases are tapered and diameter is
dependent upon longitudinal location, this location
may not be changed after the sensor is fabricated
since it is essential for proper operation that the
sensor curvature exactly match chamber curvature.

Drawing Number: 21086
Revision: NR
OPERATION MANUAL FOR
CONFORMAL BALLISTICS PRESSURE SENSOR
Series 117B
3
5.1 LOW-END NONLINEARITY
It will be noticed during calibration, especially with
metallic cartridges, that a certain amount of pressure
is necessary before linear output is attained from the
conformal sensor.
This is due to the fact that since the cartridge cases
are made nominally smaller in diameter than the
chamber to allow easy insertion and extraction, the
case must be expanded slightly by the internal
pressure before force can be transmitted to the sensor.
See the enclosed guide “An Improved Technique for
Utilization of Conformal Ballistics Sensor Calibration
Data”for methods of dealing with this topic.
6.0 MAINTENANCE
It is essential for normal operation of the Model 117B
that the insulation resistance be maintained above
1012 ohms. If insulation resistance should deteriorate,
wipe connector with clean cloth or paper wipe dipped
in a solvent compatible with Teflonsuch as
isopropyl alcohol, then bake in oven at 250F for ½
hour.

Drawing Number: 21086
Revision: NR
OPERATION MANUAL FOR
CONFORMAL BALLISTICS PRESSURE SENSOR
Series 117B
4

Drawing Number: 21086
Revision: NR
OPERATION MANUAL FOR
CONFORMAL BALLISTICS PRESSURE SENSOR
Series 117B
5

Model Number
117B-80K CHARGE OUTPUT PRESSURE SENSOR Revision: R
ECN #: 46956
[6]
Performanc
e
ENGLISH S
I
Sensitivity(± 20 %)(for straight oil) 0.14 pC/psi 0.021 pC/kPa [2][3]
Measurement Range 20 to 60 kpsi 138,000 to 414,000 kPa [4]
Maximum Pressure 80 kpsi 552,000 kPa
Resolution 2 psi 14 kPa [5]
Resonant Frequency ≥200 kHz ≥200 kHz
Rise Time(Reflected) ≤2 µ sec ≤2 µ sec
Non-Linearity ≤2 % FS ≤2 % FS
Environmenta
l
Acceleration Sensitivity ≤0.02 psi/g ≤0.14 kPa/(m/s²)
Temperature Range(Operating) -100 to +400 °F -73 to +204 °C
Temperature Coefficient of Sensitivity ≤0.03 %/°F ≤0.054 %/°C
Maximum Flash Temperature 3000 °F 1650 °C
Maximum Shock 20,000 g pk 196 200 m/s² pk
Electrica
l
Output Polarity(Positive Pressure) Negative Negative
Capacitance 9 pF 9 pF [1]
Insulation Resistance(at room temp) ≥101
2
Ohm ≥101
2
Ohm
Physica
l
Housing Material 17-4 Stainless Steel 17-4 Stainless Steel
Diaphragm 17-4 Stainless Steel 17-4 Stainless Steel
Sealing Epoxy Epoxy
Electrical Connector 10-32 Coaxial Jack 10-32 Coaxial Jack
Weight 0.45 oz 13 gm
All specifications are at room temperature unless otherwise specified.
In the interest of constant product improvement, we reserve the right to change specifications without notice.
ICP®is a registered trademark of PCB Group, Inc.
OPTIONAL VERSIONS
Optional versions have identical specifications and accessories as listed for the standard model
except where noted below. More than one option may be used.
M- Metric Mount
NOTES
:
[1] Typical.
[
2
]
Actual slo
p
e is de
p
endent u
p
on material
p
ro
p
erties of cartrid
g
e case
.
[3] For conformal cal. sensitivity will be ±40%.
[4] Calibrated range to 60,000 psi.
[5] Resolution dependent on range setting and cable length used in charge system
.
[6] See PCB Declaration of Conformance PS158 for details
.
SUPPLIED ACCESSORIES:
Model 045B Alignment Guide
Model 065A19 Spacer set, 0.250" ID
Entered: LK Engineer: BAM Sales: WD
C
Approved: BAM Spec Number:
Date: 8/8/2017 Date: 8/8/2017 Date: 8/8/2017 Date: 8/8/2017 117-2010-80
3425 Walden Avenue, Depew, NY 14043
Phone: 716-684-0001
Fax: 716-684-0987
E-Mail: [email protected]

CODE
IDENT. NO.
52681
DWG. NO.
SCALE: SHEET
DRAWN CHECKED ENGINEER
TITLE
UNLESS OTHERWISE SPECIFIED TOLERANCES ARE:
DIMENSIONS IN MILLIMETERS
[ IN BRACKETS ]
XX ± 0.13
ANGLES 2 DEGREES
3425 WALDEN AVE. DEPEW, NY 14043
(716) 684-0001 E-MAIL: sales@pcb.com
DIMENSIONS IN INCHES
DECIMALS XX ±.01
ANGLES 2 DEGREES
FILLETS AND RADII
.003 - .005
DECIMALS X ± 0.3
FILLETS AND RADII
0.07 - 0.13
INSTALLATION DRAWING
44976
1 OF 1
2X
MODEL 117B02
CONFORMAL BALLISTICS SENSOR
XXX ±.005
KSR 2/10/21 KSR 2/10/21 MJK 2/10/21
1
1
2
2
3
3
4
4
A A
B B
3
LOCATE YELLOW DOT TOWARD CASE MOUTH
ALIGNMENT HOLE MAY BE LOCATED EITHER FORE OR AFT OF SENSOR MOUNTING HOLE
MOUNTING TORQUE ON .312 [7.92] HEX: 5-10 FT LBS [6.8-13.6 NEWTON METERS]
CENTERLINE OF .2500 [6.350] HOLE MUST INTERSECT CENTERLINE OF CHAMBER BORE WITHIN .001 [.23]
HOLD THIS DIMENSION TO OBTAIN FLUSH MOUNT
1
2
3
4
5
2
1
4
REVISIONS
REV DESCRIPTION DIN
B UPDATED 065A19 NOTE 50698
44976
PCB Piezotronics Inc. claims proprietary rights in
the information disclosed hereon. Neither it nor any
reproduction thereof will be disclosed to others
without the written consent of PCB Piezotronics Inc.
5
.236 .002 5.99 .05
[]
.710 [18.03]
.250 [6.35]
.46 [11.8]
.89 [22.7]
1.63 [41.4] 3/8-24 UNF - 2A
.312 [7.92] HEX
10-32 UNF - 2ACO-AXIAL
ELECTRICAL CONNECTOR
.320 [8.13]
MODEL 065A19 SPACER SET
CONSISTS OF 9 SPACERS
.317 [8.05] O.D. w/ .252 [6.40] I.D.
.010 [0.25] TO .018 [0.46] THICK
.014 [0.36] NOMINAL
.246 [6.25]
.578 [14.68]CHAMBER
.565 .025 14.35 .64
[]
ALIGNMENT GUIDE
MODEL 045B
.750 [19.05]
.224 [5.69]
.250 [6.35]
.187 [4.74]
.500 [12.70]
.500 [12.70]
.565 .025 14.35 .64
[]
CENTERLINE OF SENSOR HOLE TO BE
PARALLEL WITH ALIGNMENT HOLE
TO WITHIN 15 MIN
UNMODIFIED CARTRIDGE
CASE
.2500.0005 [6.350.013] THRU ONE WALL
.332 [8.43] .474 [12.04]
3/8-24 UNF-2B .425 [10.80]
.177 [4.50] .400 [10.16]
.1875.0005 [4.763.013] .400 [10.16]
Table of contents
Other PCB Piezotronics Adapter manuals
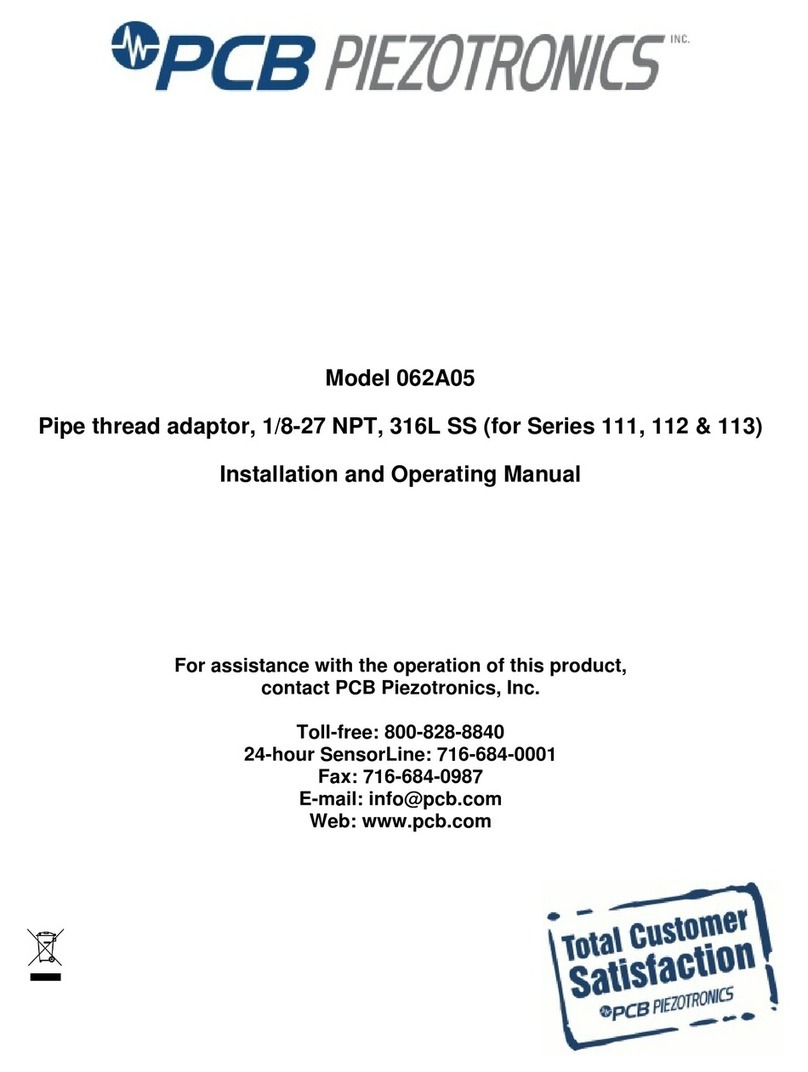
PCB Piezotronics
PCB Piezotronics 062A05 User manual
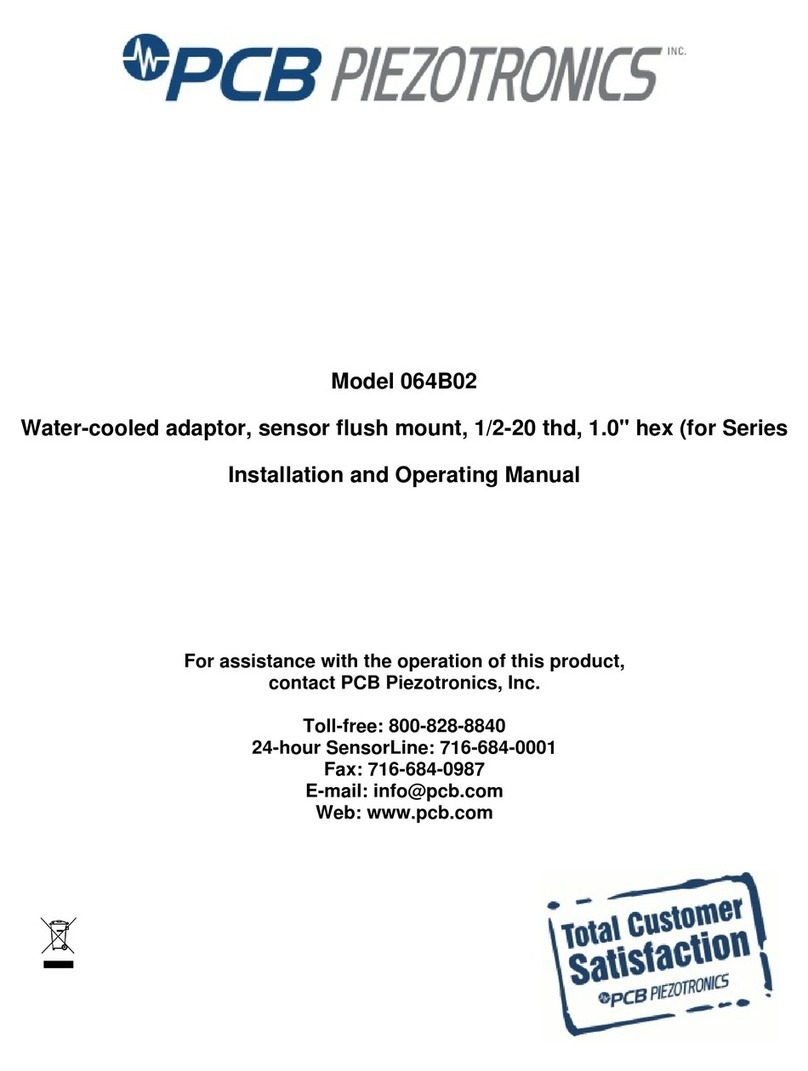
PCB Piezotronics
PCB Piezotronics 064B02 User manual
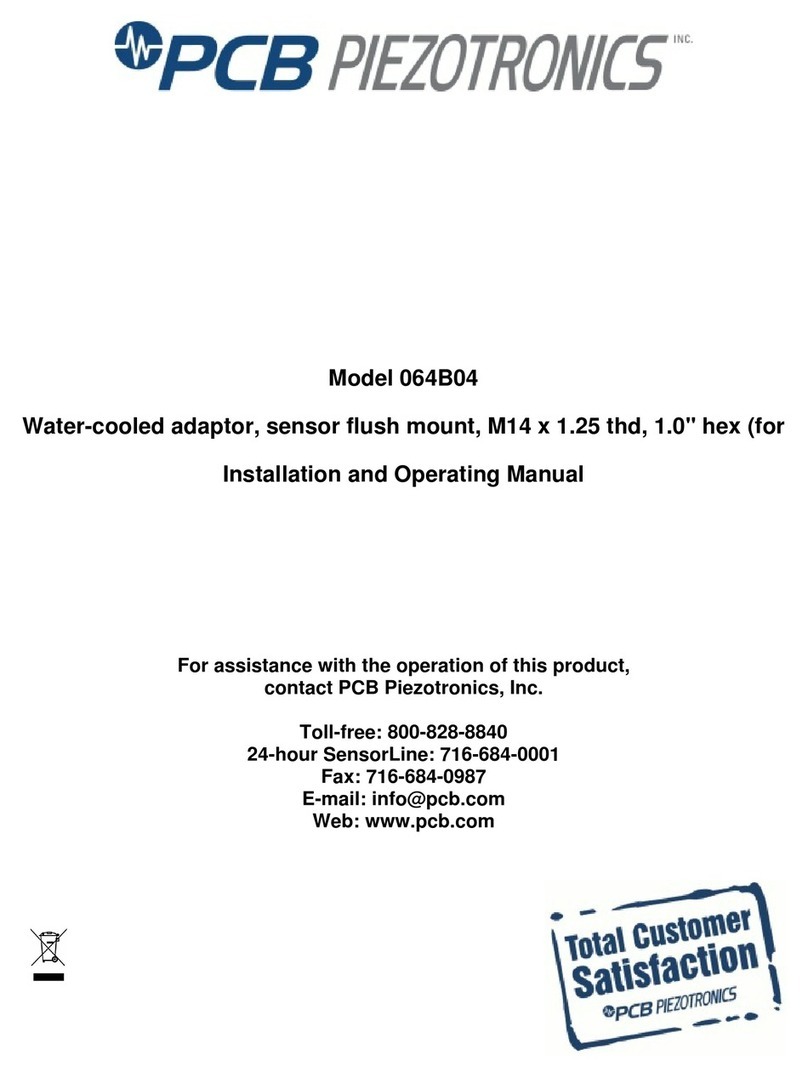
PCB Piezotronics
PCB Piezotronics 064B04 User manual

PCB Piezotronics
PCB Piezotronics M354C10 User manual
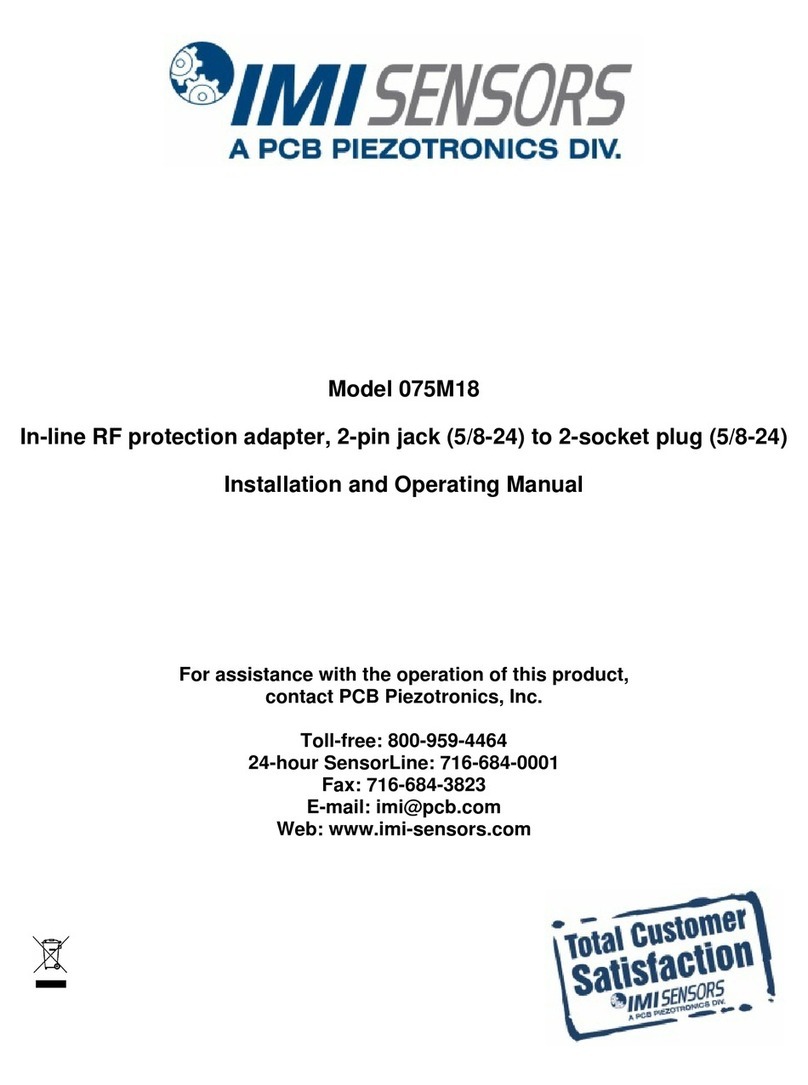
PCB Piezotronics
PCB Piezotronics IMI SENSORS 075M18 User manual
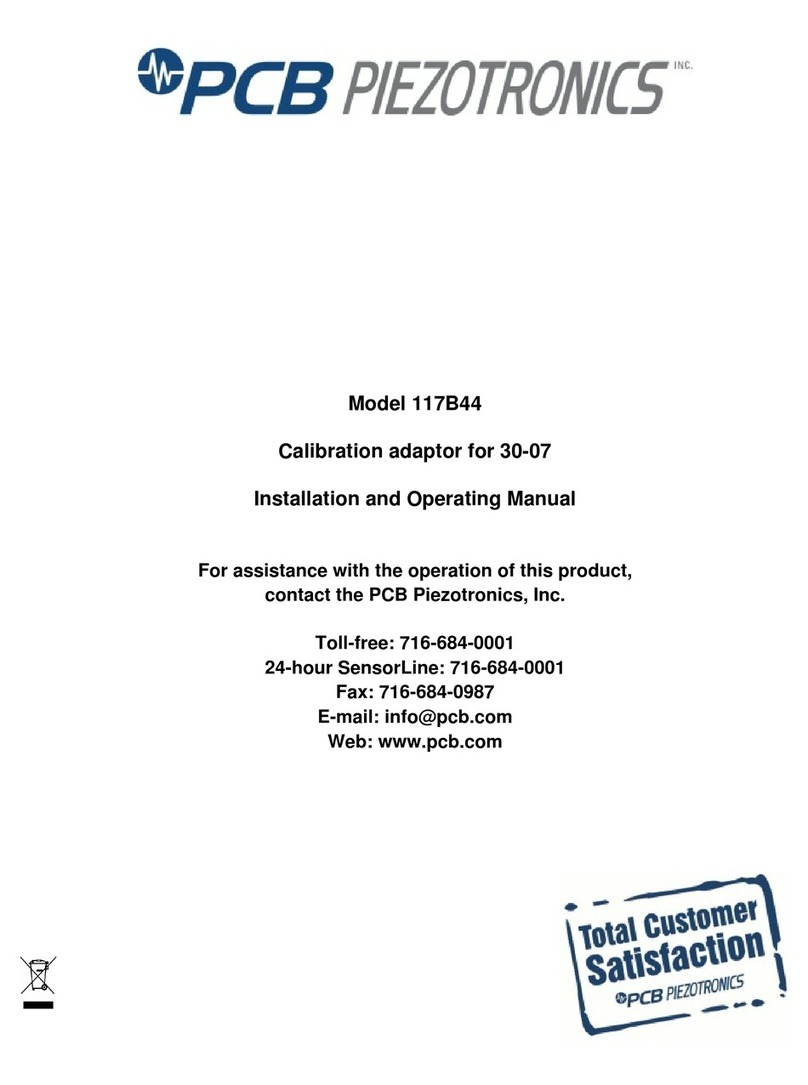
PCB Piezotronics
PCB Piezotronics 117B44 User manual

PCB Piezotronics
PCB Piezotronics 064B01 User manual
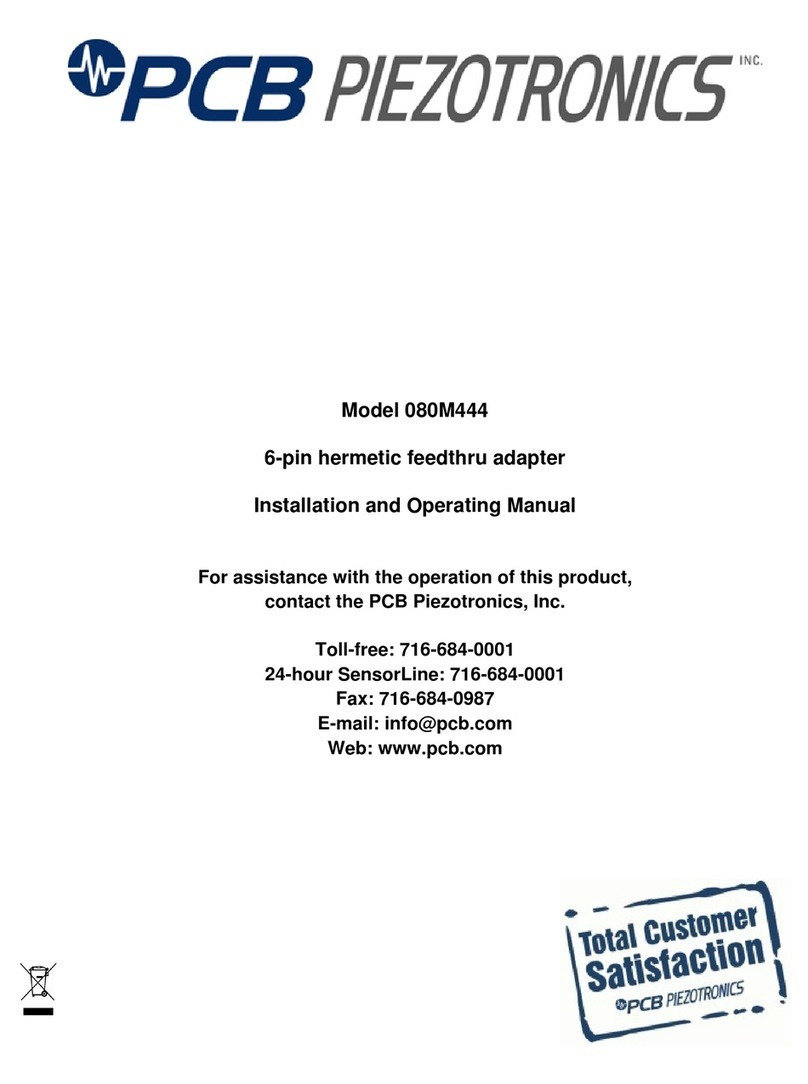
PCB Piezotronics
PCB Piezotronics 080M444 User manual
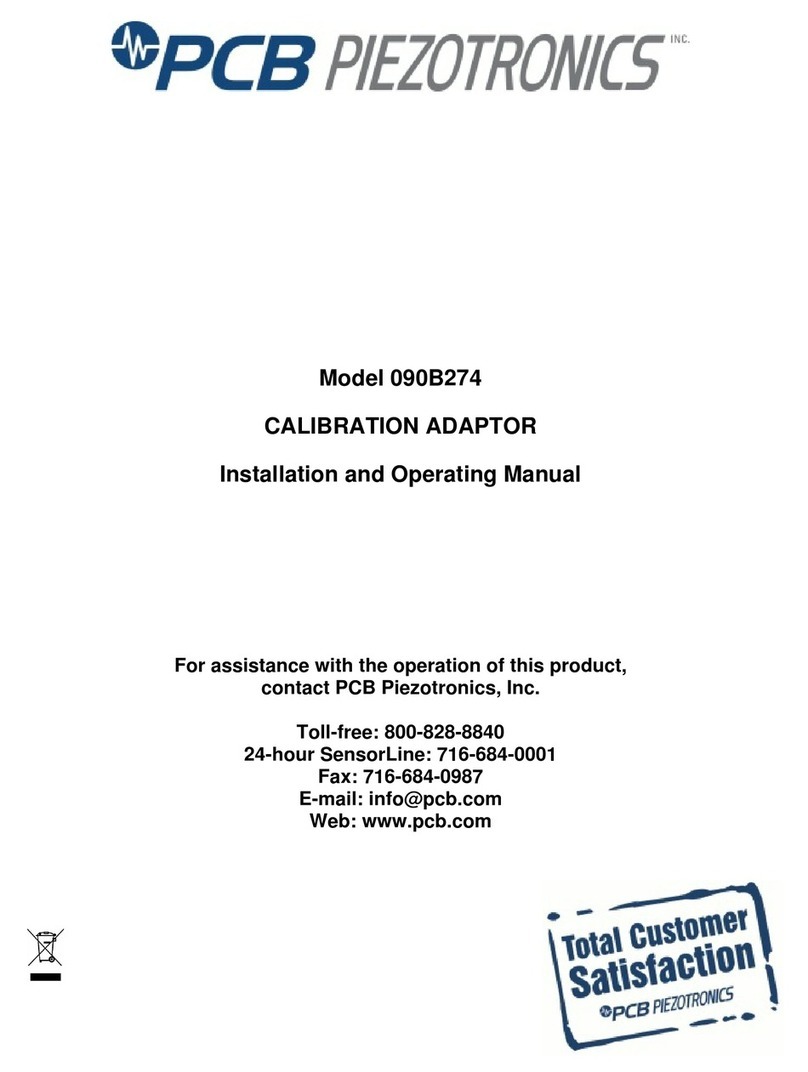
PCB Piezotronics
PCB Piezotronics 090B274 User manual
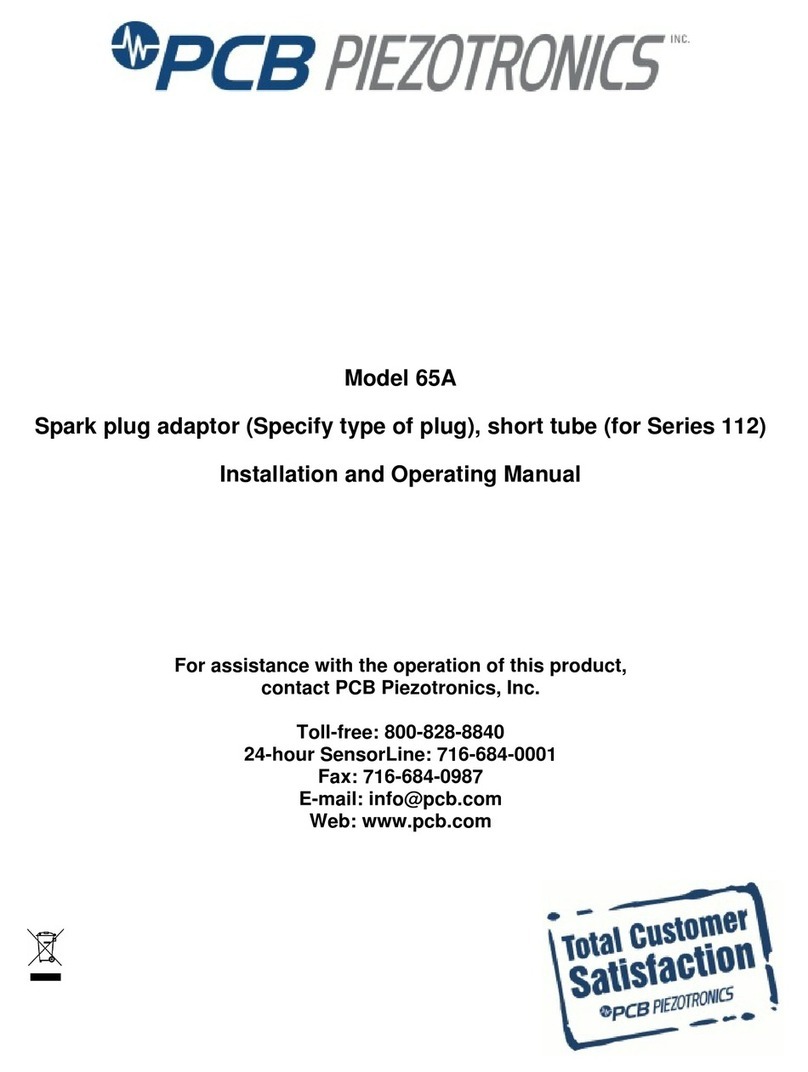
PCB Piezotronics
PCB Piezotronics 65A User manual