Penny + Giles EICT Assembly instructions

EICT
Installation and set-up guide
Model EICT is the Signal Conditioning Unit for Penny + Giles ICT range of in-cylinder displacement
transducers. It will only drive the transducers with an appropriate Sensor Calibration Module Card
(SCMC) fitted.
Important Note: It is essential that Steps 1 to 7 are completed before connecting a power
supply to the EICT. Incorrect connections may destroy EICT on power up.
Step 1 Remove the four retaining screws to release the cover. Note the position of the gasket
in the cover.
Identify the Sensor Calibration Module Card (SCMC) supplied with the ICT transducer.
Insert the SCMC card into position JP1. (See Fig.1)
Step 2 Unscrew cable glands C1 & C2. (See Fig.1). See note [4] regarding cable diameter.
Single Supply - Pass power
supply cable through gland C1 into
'SUPPLY' zone on EICT board.
Connect the power supply lead
carrying the most POSITIVE
potential (+10 to +60Vdc) to
Terminal 9 [V POS]. Connect the
power lead carrying 0V to Terminal
8 [GND].
Dual Supply - As Single Supply,
BUT, connect most negative power
lead (e.g. -15V) to Terminal 7
[VNEG]. See note [1] for 4-20 mA
output.
A power supply cable screen can be
connected to Terminal 6 [GND].
This is recommended but optional.
Consult your systems engineer if
other options required.
Firmly tighten cable gland lock nut
C1.
Step 3 Pass the ICT cable through gland C2 into 'SENSOR' zone on EICT board. Connect the ICT to
the terminals on the EICT board, as indicated below and shown in Fig.1 & Fig. 5.
Terminal 1 - ICT BLUE [Coil –ve]
Terminal 2 - ICT YELLOW [Coil +ve]
Terminal 3 - ICT GREEN [Case] See Note [2]
Terminal 4 - ICT Screen [Cable Screen] See Note [2]
If a connector option is required, either fitted to the ICT by a connector adapter kit or any
other connector system, refer to Notes [3], [4] & [5].
Firmly tighten cable gland lock nut C2.
Step 4 Locate 'jumper' JP3 on EICT board (see Fig.1). This determines the 'sense' of the
voltage/current output with respect to the ICT core position. Locate the 'jumper' in
the required position (See Fig. 2). The EICT is factory set with JP3 in position 'A'.
Step 5 Locate JP2 on EICT board (see Fig.1).
If required signal output is 0.5 - 4.5Vdc or 4 - 20 mA (i.e, no Voltage Module (VM) output
option card is fitted), fit 'jumper' into position JP2 (across terminals 1& 2). The
EICT is factory set with 'jumper' fitted in this position. Proceed to Step 7.
If required VOLTAGE signal output is anything other than 0.5 - 4.5Vdc (An additional
Voltage Module (VM) output option card is required) then remove 'jumper' from JP2
and store on V(T) LINK PARK terminals. (see Fig.1)
Step 6 If Voltage Module (VM) output option card is selected, identify the VM card. Locate DIP
switch on VM card. (See Fig. 3) Select the required sensor output voltage, using the Switch
Position Matrix Guide (see Fig.4), and set the DIP switch positions accordingly.
Insert Voltage Module (VM) output option card into position JP2. Proceed to Step 7.
If a Current Module (CM) output option card is to be fitted, do not attempt to insert the
card now. Proceed with Steps 5, 7, 8 & 9 as for 0.5 - 4.5Vdc output requirement, as if NO
output option card is fitted. Then, proceed to Step 10.
Step 7 Connect a DMM to :-
Terminal 5 (OUTPUT) +V Output
Terminal 6 (GND) (0V) Ground
Set DMM range to measure output voltage.
Step 8 Move ICT core to the fully 'Lo' position (See Step 4 and Fig. 2) and power up the EICT.
Adjust 'ZERO' trim pot until the required output voltage is achieved on the DMM display.
(0.5Vdc if no output option cards are fitted in JP2)
‘Lo’ Retract (e.g.0.5V) Position A
‘Hi’ Extend (e.g. 4.5V)
‘Hi’ Retract. (e.g. 4.5V) Position B
‘Lo’ Extend (e.g.0.5V)
JP3
JP3
Fig. 2
B A
B A
INNOVATION IN MOTION
Fig.1

Move ICT core to the fully 'Lo' position (See Step 4 and Fig. 2). Adjust 'ZERO' trim pot
until the required output current (4mA) is achieved.
Move ICT core to the fully 'Hi' position and adjust 'GAIN' trim pot until required output
current (20mA) is achieved.
Step 11 Switch off power to EICT.
Remove DMM from Terminal 4 & 5.
Replace cover using screws removed, ensuring all gaskets are present and in the
correct place.
Step 12 Optional, but recommended. Use an indelible pen to mark the configuration settings you
have selected, in the appropriate label area shown on the EICT housing cover. (EICT
type; V o/p [if applicable]; ICT type)
Step 13 The ICT and EICT is now ready for use. Refer to EICT Technical data sheet for full
specification, mounting options and dimensions.
Notes
1Current Module (CM) (4 - 20 mA) 'set-up' is unaffected by Dual Supply option.
Continue to follow set-up guide steps.
2Recommended connections, but optional. Consult your Systems Engineer should other
options be required.
3Make a note of, and check, the ICT Sensor element colour codes (see Fig. 5) relative to
the assigned connector termination identities, to enable the EICT to be correctly
connected.
4Cable diameter must be between 2.5 and 6.0mm diameter to maintain IP66 rating of the
EICT housing.
Make off cable elements to the connector.
5Rapid integrity check for connector and/or transducer.
EICT must be disconnected from the ICT sensor to carry out following check!
Using a DMM, set to the resistance range:
(See Fig. 5 for ICT Sensor cable element colour coding)
i) Measure between connector terminals assigned to Sensor 'yellow' and 'blue'.
Value should lie between 40Ωand 170Ω.
ii) Measure between connector terminals assigned to Sensor 'green' and 'yellow'
and/or 'blue'.
Value should be 'open circuit'.
iii) Measure between connector terminal assigned to 'green' and the Sensor body.
Value should be 'short circuit'.
iv) 'Screen', if used - Connector terminal assigned to 'screen' should be 'open circuit' to
all the other connector terminations and Sensor body unless otherwise specified by
your Systems Engineer.
6Any problems or questions should be e-mailed to [email protected]
For technical assistance contact your local distributor or Penny + Giles at
UK Tel:+44 (0)1202 409409 Email: [email protected]
USA Tel:+1 626 337 0400 Email: [email protected]
Web: www.pennyandgiles.com
Insert
card in this
direction Voltage Module (VM)
output option card
JP1
1
7
82
SW1
14
ON DIP
Switch position matrix guide
ON
OFF
ON
OFF
ON
OFF
ON
OFF
ON
OFF
ON
OFF
ON
OFF
ON
OFF
OUTPUT
-5V to 0V
-2.5V to +2.5V
0V to +5V
-10V to 0V
-5V to +5V
0V to +10V
-7.5V to +7.5V
-10V to +10V
Fig. 3
Fig. 4
(9)
(8)
(7)
(6)
(5)
(4)
(3)
(2)
(1)
VPOS
GND
VNEG
GND
OUTPUT
GND
GREEN
YELLOW
BLUE
+V supply
0V supply
-V supply (Dual supply only)
0V return
Voltage (current) output
CORE
Retract Extend
Case
Screen
Fig. 5
For Dual Supply option. Output over the full range, relative to ground ('GND' 0V) will
appear on Terminal 5 'OUTPUT'. (e.g. In the case of a -10Vto 0 to +10V range, the
output can be trimmed to -10V using the 'ZERO' trim pot.)
Step 9 Move ICT core to the fully 'Hi' position and adjust 'GAIN' trim pot until required output
voltage is achieved.(4.5Vdc if no output option cards are fitted in JP2)
For Dual Supply option. Output over the full range, relative to ground ('GND' 0V) will
appear on Terminal 5 'OUTPUT’. (e.g. In the case of a -10V to 0 to +10V range, the
output can be trimmed to +10V using the 'GAIN' trim pot.)
NOTE: When trimming use 'ZERO' trim pot to set the “most negative” end and 'GAIN'
trim pot to set the “most positive” end of the output signal.
Step 10 If Current Module (CM) output option card is selected, ensure steps 5, 7, 8
& 9 have been completed. Switch off power supply to EICT. There are no user-
configurable options on the Current Module (CM) output option card.
Remove 'jumper' from JP2 and store on V(T) LINK PARK terminals. (see Fig.1) Insert
Current Module (CM) output option card into position JP2. Change DMM (already
connected between terminals 5 & 4) range settings to measure a 4 - 20mA current
output. Power up EICT.
Check that output is 4 - 20mA over the stroke of the ICT core.
If adjustment is required :-
1 2 3 4
Doc.EICT Set-up Guide P201754 issue 2, Septembe 2004
Other Penny + Giles Control Unit manuals
Popular Control Unit manuals by other brands
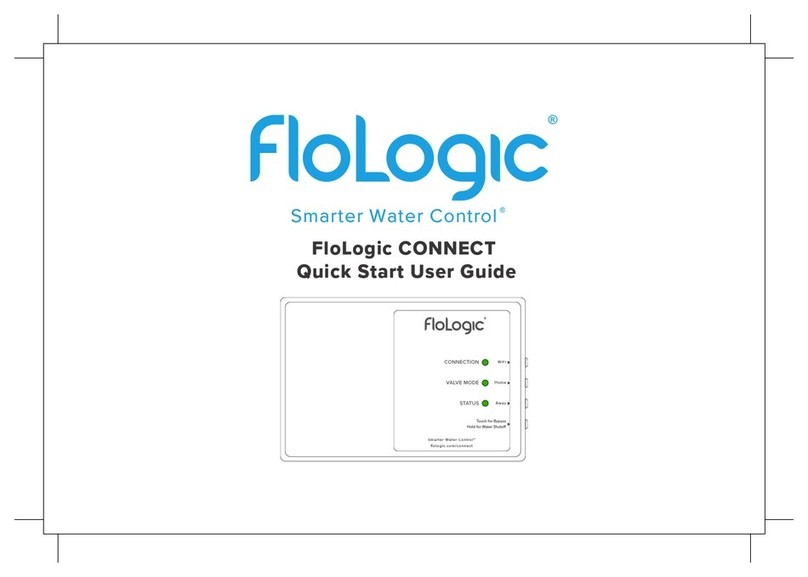
Flologic
Flologic CONNECT Quick start user guide
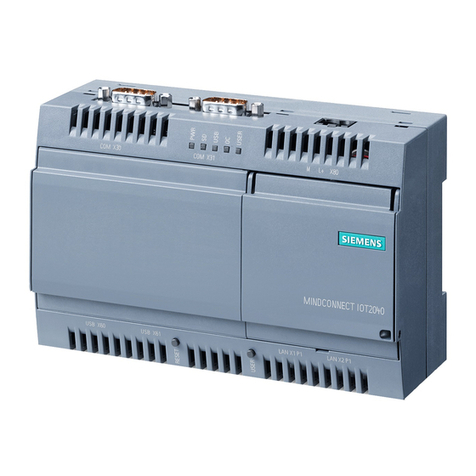
Siemens
Siemens SIMATIC IOT2000 Series operating instructions
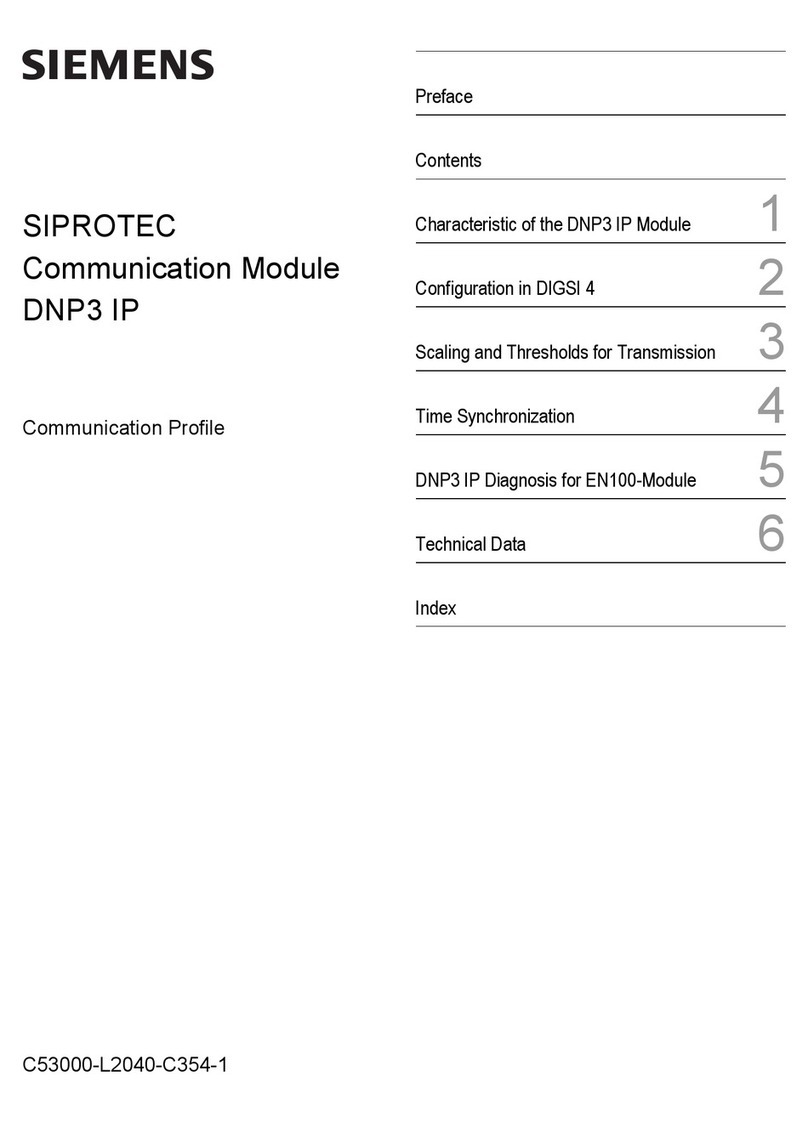
Siemens
Siemens Siprotec DNP3 IP Communications manual
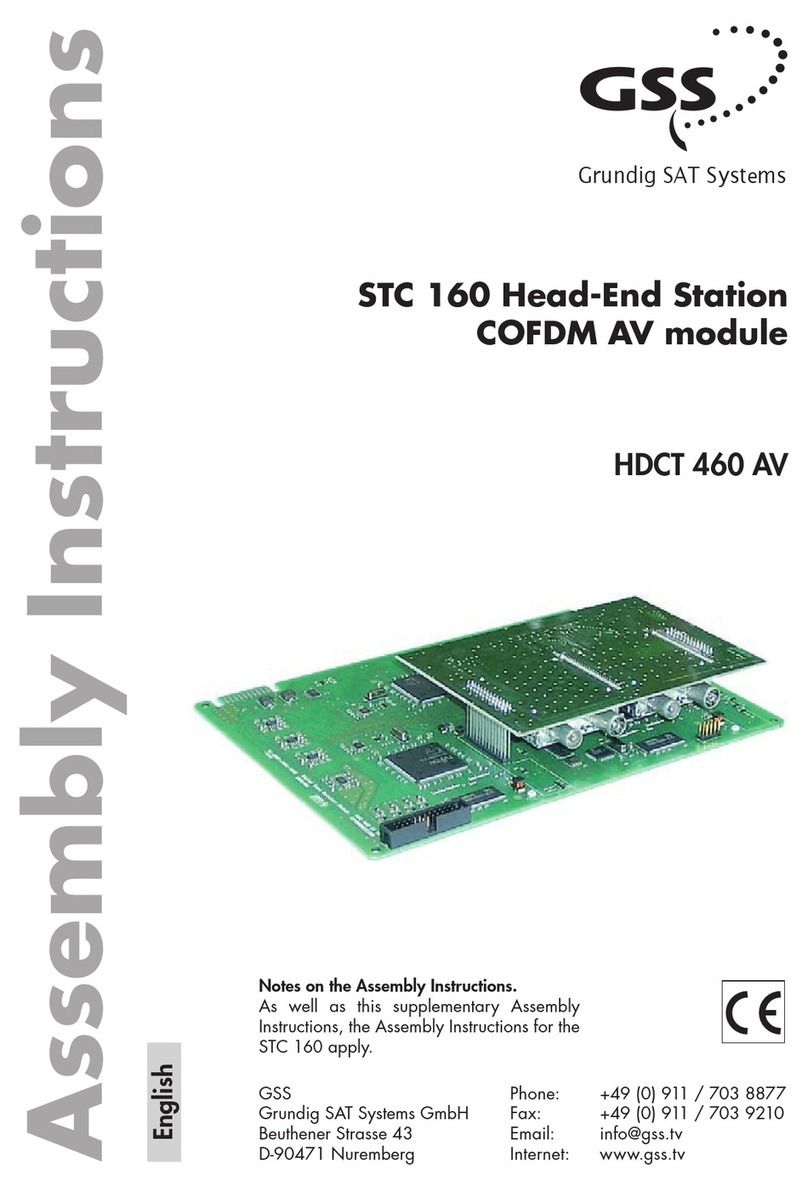
GSS
GSS STC 160 Assembly instructions
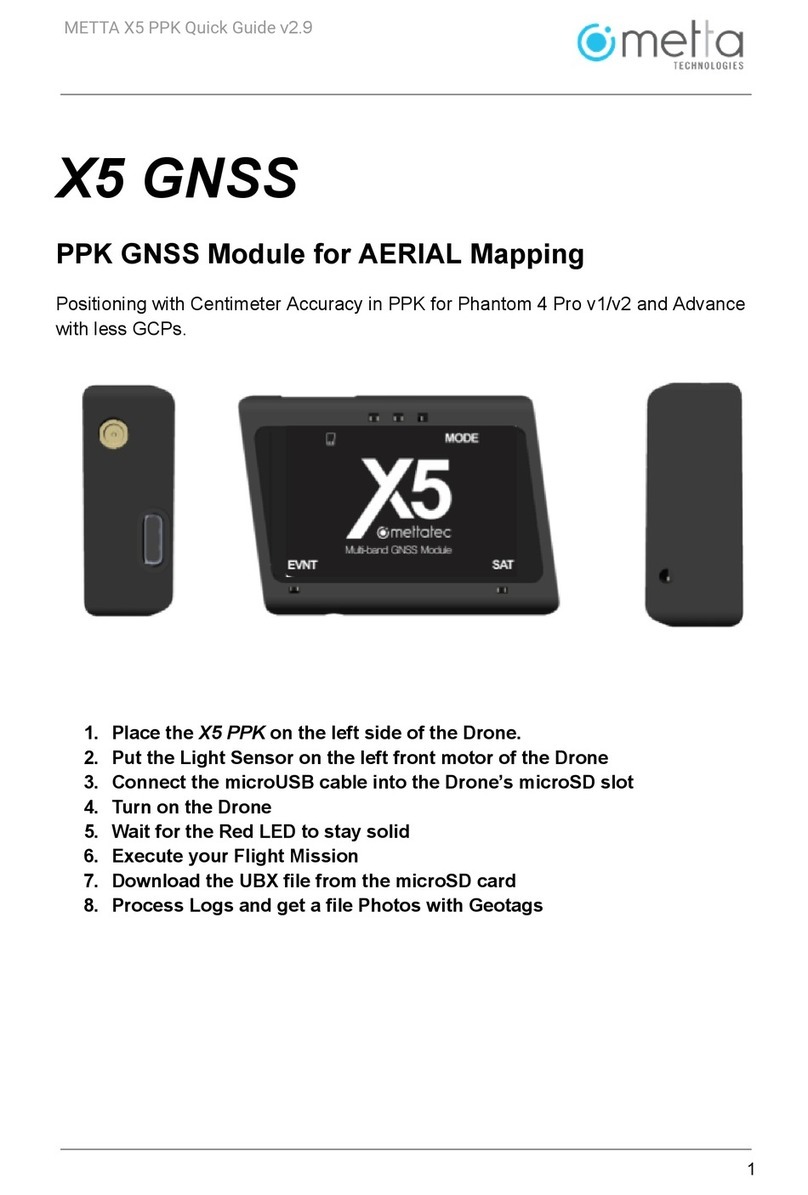
METTA
METTA X5 GNSS quick start guide

Honeywell
Honeywell 5800WAVE - Ademco Wireless Siren Installation and setup guide