Performance Tool M547 User manual

WARNING!
READ, UNDERSTANDAND FOLLOW ALL INSTRUCTIONSAND WARNINGS BEFORE
OPERATING THIS TOOL. FAILURE TO DO SO MAY RESULT IN PERSONAL INJURY
AND/OR PROPERTY DAMAGEAND WILL VOID WARRANTY.
1/8" Micro Die Grinder
OWNER’S MANUAL
Stock Number M547
SPECIFICATIONS:
Collet size (IN.)................................................1/8
Air pressure (P.S.I.) .............................................90
Average air consumption (C.F.M.) ...................................2
Free speed (R.P.M.) .........................................54,000
Air inlet (N.P.T.)................................................1/4
Hose size (I.D.)..............................................3/8 in.
Hose length (IN.) ...............................................42
Tool length (IN.) ...............................................6.0
Weight (LBS) ................................................1.76
Specifications are subject to change without notice.
LIMITED WARRANTY
PERFORMANCE TOOL® extends only the following warranties, and only to original retail purchasers. These war-
ranties give specic legal rights. Except where prohibited by local law, the law of the State of Washington governs
all warranties and all exclusions and limitations of warranties and remedies. There may be other rights which vary
from state to state.
PERFORMANCE TOOL® warrants the product to be free from defects in materials and workmanship under
normal use and service. A defective product may be returned for a free replacement within 90 days from the date
of pur-chase, provided that product is returned to place of purchase immediately after discovery of defect. After 90
days and up to one year from date of purchase, PERFORMANCE TOOL® will replace at no charge any parts
which our examination shall disclose to be defective and under warranty.
These warranties exclude blades, bits, punches, dies, bulbs, fuses, hoses, and other consumables which must be
replaced under normal use and service. These warranties shall not apply to any product or part which is used for a
purpose for which it is not designed, or which has been repaired or altered in any way so as to affect adversely its
performance or reliability, nor shall these warranties apply to any product or part which has been subject to
misuse, neglect, accident or wear and tear incident to normal use and service.
PERFORMANCE TOOL® does not authorize any other person to make any warranty or to assume any liability in
connection with its products.
Except for warranties of title and the limited express warranties set forth above, PERFORMANCE TOOL® makes
no express or implied warranties of any kind with respect to its products. In particular, PERFORMANCE TOOL®
makes no implied warranty of merchantability and no implied warranty of tness for any particular purpose, except
that for goods purchased primarily for personal, family or household use and not for commercial or business use,
PERFORMANCE TOOL® makes an implied warranty of merchantability (and, if otherwise applicable, an implied
warranty of tness for a particular purpose), but only for the particular qualities or characteristics, and for the dura-
tion, expressly warranted above.
The laws on limitation of implied warranties may differ from state to state, so the above limitations may not apply in
all cases.
PERFORMANCE TOOL® shall not be liable for consequential, incidental or special damages resulting from or in
any manner related to any product, or to the design, use, or any inability to use the product. The sole and exclusive
remedy for a defective product or part shall be the repair, or replacement thereof as provided above. The laws on
limitation of remedies or on consequential, incidental or special damages may vary from state to state, so the
above limitations may not apply in all cases.

IMPORTANT SAFETY INFORMATION
1. Keep work area clean. Cluttered areas invite injuries.
2. Observe work area conditions. Do not use machines or power tools in damp or wet
locations. Don’t expose to rain. Keep work area well lighted. Do not use electrically
powered tools in the presence of flammable gases or liquids. Do not bring combustible
materials near the tools.
3. As with any tool, use common sense when operating. Do not wear loose clothing or
jewelry that could become caught by moving parts, causing injury. Operate tool a safe
distance from yourself and others in the work area.
4. Keep children away. Children must never be allowed in the work area. Do not let them
handle machines, tools, hoses or extension cords.
5. Store idle equipment. When not in use, tools must be stored in a dry location to inhibit
rust. Always lock up tools and keep out of reach of children and other untrained
persons. Switch off all unused electrical tools when stored. Tools are dangerous in the
hands of untrained users.
6. Always wear approved eye protection when using tools. If raising dust, wear a suitable
mask.
7. Work Safe. When wearing gloves to operate the tool, make sure that the gloves do not
interfere with operating the Trigger. Test your gloves with the Trigger before attaching
the unit to an air source. Keep your finger away from the Trigger until you are ready to
work. Never start the tool unless you have a firm grip with both hands and you are
positioned at your work piece or area. Before using the tool, know what is directly
underneath the work area or work piece. The tool can quickly penetrate material. If
working directly on the ground, make sure you are not directly above shallow cables,
lines, or pipes. Keep your limbs and body clear of the tool. If an accessory or
attachment breaks off, the tool tends to surge forward suddenly. Operate tool a safe
distance from yourself and others in the work area. Make sure the immediate area is
clear of other people or animals. Spectators must stay at a safe distance. Never point
the tool or the air hose (not included) at anyone. Keep proper footing and balance at
all times. Do not reach over or across running machines, hoses, etc.
8. Do not operate any tool if under the influence of alcohol or drugs. Read warning labels
on prescriptions to determine if your judgment or reflexes are impaired while taking
drugs. If there is any doubt, do not operate any tool.
9. Be sure air is in OFF position when connecting tool to air supply.
10. Use only those accessories that are designed for use with tools. For example, with
impact wrenches do not use ordinary sockets. Use impact sockets for all air tools.
11. Be sure to disconnect tool from air supply before changing accessories, performing
service on tool and when not in use.
12. Follow air source manufacturers' directions for connection of regulators, filters, and
other accessories to air source. Do not install quick couplers directly on tool as they
put unnecessary strain on the air inlet threads possibly causing them to wear out
prematurely. Instead, install them on a short length of air hose attached to the tool.
WARNING!
READ, UNDERSTAND AND FOLLOW ALL INSTRUCTIONS AND
WARNINGS BEFORE OPERATING THIS TOOL. FAILURE TO DO
SO MAY RESULT IN PERSONAL INJURY AND/OR PROPERTY
DAMAGE AND WILL VOID WARRANTY.
IMPORTANT SAFETY INFORMATION
ASSEMBLY / INSTALLATION
1. You will need to prepare the Die Grinder hose to connect to the oiler and the oiler to
connect to the included Quick-disconnect Coupler Plug. Wrap the end of the Die Grinder
hose and the male end of the oiler with pipe thread sealer tape.
2. Connect the oiler to the inlet on the die grinder hose, then connect the female quick
connect plug to the oiler. Insert the plug into a Quick-Disconnect coupler on a 3/8" ID Air
Source Hose.
Note: If you are not using an automatic oiler system, before operation, add a few drops of
Pneumatic Tool Oil to the airline connection. Add a few drops more after each hour of
continual use.
3. Set the air pressure on your compressor to 90 PSI. Do not exceed the recommended air
pressure of 90 PSI.
4. Check the air connection for leaks. Once you are satisfied there are no leaks, turn off the
air compressor and disconnect the tool.
Clean air of correct air pressure is recommended for the power supply for this tool. A
maximum of 90 PSI at the tool is recommended for most air tools of this class. Check
specifications section for recommended pressure. (Depending on length of air hose and
other circumstances, air pressure at compressor may need to be increased to 100 PSI to
ensure 90 PSI at the tool.)
Water in the air hose and compressor tank contributes to reduced performance and
damage of the air tool. Drain the air tank and filters before each use and as necessary to
keep the air supply dry.
Hose length over 25’ causes loss in line pressure. Increase hose I.D. or increase
compressor pressure to compensate for the pressure loss. Use an in-line pressure
regulator with gauge if air inlet pressure is critical.
AIR SOURCE
13. Check for damaged parts. Before using any tool, any part that appears damaged
should be carefully checked to determine that it will operate properly and perform its
intended function. Check for alignment and binding of moving parts; any broken parts
or mounting fixtures; and any other condition that may affect proper operation. Any
part that is damaged should be properly repaired or replaced by a qualified technician.
14. Maintenance. For your safety, maintenance should be performed regularly by a
qualified technician using original PERFORMANCE TOOLS® replacement parts.
Failure to do so can lead to accidents for the operator. Use of any other parts will void
the warranty. Only use accessories intended for use with this tool. Approved
accessories are available from Performance Tool®. Use only accessories that are
recommended by the manufacturer for your model. Accessories that may be suitable
for one tool may become hazardous when used on another tool.
WARNING: Repetitive motions or exposure to vibration may be harmful to your hands and arms.
WARNING: This product and its packaging contain a chemical known to the State of California
to cause cancer, birth defects, or other reproductive harm.
WARNING: The warnings, cautions, and instructions discussed in this instruction manual cannot
cover all possible conditions and situations that may occur. It must be understood by the
operator that common sense and caution are factors which cannot be built into this product, but
must be supplied by the operator. Read and understand all of the instructions provided in the
instruction manual of this product, as well as, any other tool (s) used with this product.
2. 3.

1. Do not put additional pressure on the machine. This will only reduce sanding efficiency
and shorten the tool's life. We recommend the air pressure of this grinder at 90 PSI.
2. When using the grinder be careful not to exert excessive force. Too much force could be
hazardous if it caused the cutting tool spindle to bend or break.
3. DO NOT allow tool to free run for an extended period of time as this will shorten its life.
4. Lubricate the air motor with a good grade of air tool oil and drain the tank daily. Grit or
gum deposits in the tool may cut power and may be corrected by cleaning the air
strainer and flushing out the tool with gum solvent oil.
• Never install a carbide tipped or steel circular saw blade for use on this Die Grinder.
• Never install a wood carving blade, carving disc with chain saw cutters, or a cutting
carving disc on this Die Grinder.
• All accessories must be rated for at least 54,000 RPM. Wheels and other accessories
running over rated speed can fly apart and cause injury.
• Use eye and ear protection. Always wear ANSI approved impact safety goggles.
• Wear a full face shield if you are producing metal filings or wood chips. Wear an ANSI
approved dust mask or respirator when working around metal, wood, and chemical
dusts and mists.
• WARNING: Some dust created by power sanding, sawing, grinding, drilling, and other
construction activities, contain chemicals known [to the State of California] to cause
cancer, birth defects or other reproductive harm. Some examples of these chemicals are:
1. Lead from lead-based paints;
2. Crystalline silica from bricks and cement or other masonry products;
3. Arsenic and chromium from chemically treated lumber.
• Your risk from these exposures varies, depending on how often you do this type of
work. To reduce your exposure to these chemicals: work in a well ventilated area, and
work with approved safety equipment, such as those dust masks that are specially
designed to filter out microscopic particles.
OPERATION
Air Inlet
Adjustable Throttle
PARTS LIST
INDEX DESCRIPTION QTY INDEX DESCRIPTION QTY
1 Clamping nut 1
2 Collet 1
3 Front cover 1
4 Collet foundation 1
5 Ball bearing 1
6 Spacer 1
7 Lateral disc 1
8 Cylinder 1
9 Rotor 1
10 Rotor blade 4
11 Pin 1
12 Bearing plate 1
13 Ball bearing 1
14 Intake plate 1
15 Sleeve 1
16 Intake tube 1
17 Hose Plug 1
18 Pin 1
19 Sliding knob 1
20 Bearing bushing 1
21 O-ring 1
22 Screw 1
23 Read end holder 1
4. 5.

TROUBLESHOOTING
Problem
Tool runs slowly. Air flows
slightly from exhaust:
Tools will not run. Air flows
freely from exhaust:
Tool will not shut off:
Solution
• Check air inlet filter for
blockage.
• Flush and [our air tool
lubricating oil into air inlet as
per instructions.
• Operate tool in short bursts
quickly reversing rotation
back and forth where
applicable.
• Drain air tank and supply
line
• Use PTFE tape at all fittings
and joints. Check tool for
worn or damaged O-rings &
seals.
• Pour air tool lubricating tool
into air inlet.
• Operate tool in short bursts
of forward and/or reverse
rotation where applicable.
• Tap motor housing gently
with plastic mallet.
• Disconnect supply. Free
motor by rotating drive
shank manually where
applicable
• Replace as necessary.
• Replace "O" ring.
Probable Cause
• Motor parts jammed with
dirt particles
• Power regulator in closed
position
• Air flow blocked by dirt
• Air leakage
• One or more motor vanes
stuck due to material build
up.
• Worn/damaged wear & tear
parts.
• "O" rings throttle valve
dislodged from seat inlet
Oil tool before each use. 4 to 5 drops of a good grade Air Tool Oil placed in the air inlet is
sufficient. Use proper air pressure and CFM rating listed for this tool.
Drain water from hoses and compressor tank. Water in the air supply line will cause
gumming and loss of power. Clean the air filter on the supply line and flush the tool with
gum solvent or a 50/50 mix of air tool oil and kerosene. It may be necessary to
disassemble the tool to properly clean and re-lubricate.
LUBRICATION & MAINTENANCE
Motor
Oil
Trans.
Fluid
Brake
Fluid
Water
Whip
hose
Air Tool
Oil
YesNo
TROUBLESHOOTING
The following form lists the common operating system with problem and solutions. Please
read the form carefully and follow it. Always be sure you are using a tool suited for the
torque requirements of the job at hand.
WARNING: If any of the following symptoms appears during your operating, stop using
the tool immediately, or serious personal injury could result. Only a qualified persons or an
authorized service center can perform repairs or replacement of tool.
Disconnect tool from air supply before attempting repair or adjustment. When replacing
O-rings or Cylinder, lubricate with air tool oil before assembly.
Problem
Tool runs at normal speed
but loses power under load
:
Solution
• Lubricating clutch housing.
• Check for excess clutch oil.
Clutch cases need only be
half full. Overfilling can
cause drag on high speed
clutch parts, i.e. a typical
oiled/lubricated wrench
requires 1⁄2 ounce of oil.
• NOTE: Heat usually indicates insufficient
grease in chamber. Severe operating
conditions may require more frequent
lubrication.
• Increase line pressure,
Make sure compressor
matches tool's air pressure
and consumption needs.
Probable Cause
• Motor parts worn
• Cam/clutch worn or sticking
due to lack of lubricant
• Insufficient air supply
Note: Repairs should be carried out by a qualified person.
6. 7.
Check out the collection of air tools & compressors we offer.
Table of contents
Other Performance Tool Grinder manuals

Performance Tool
Performance Tool W50001 User manual
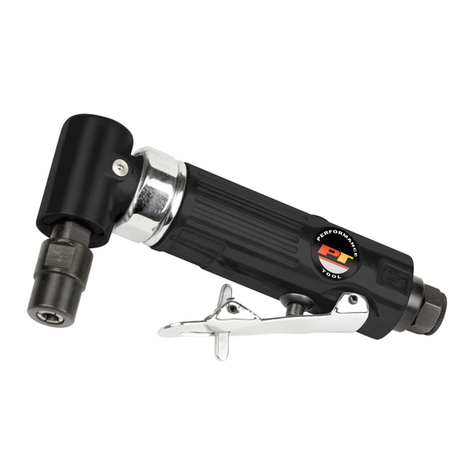
Performance Tool
Performance Tool M656 User manual
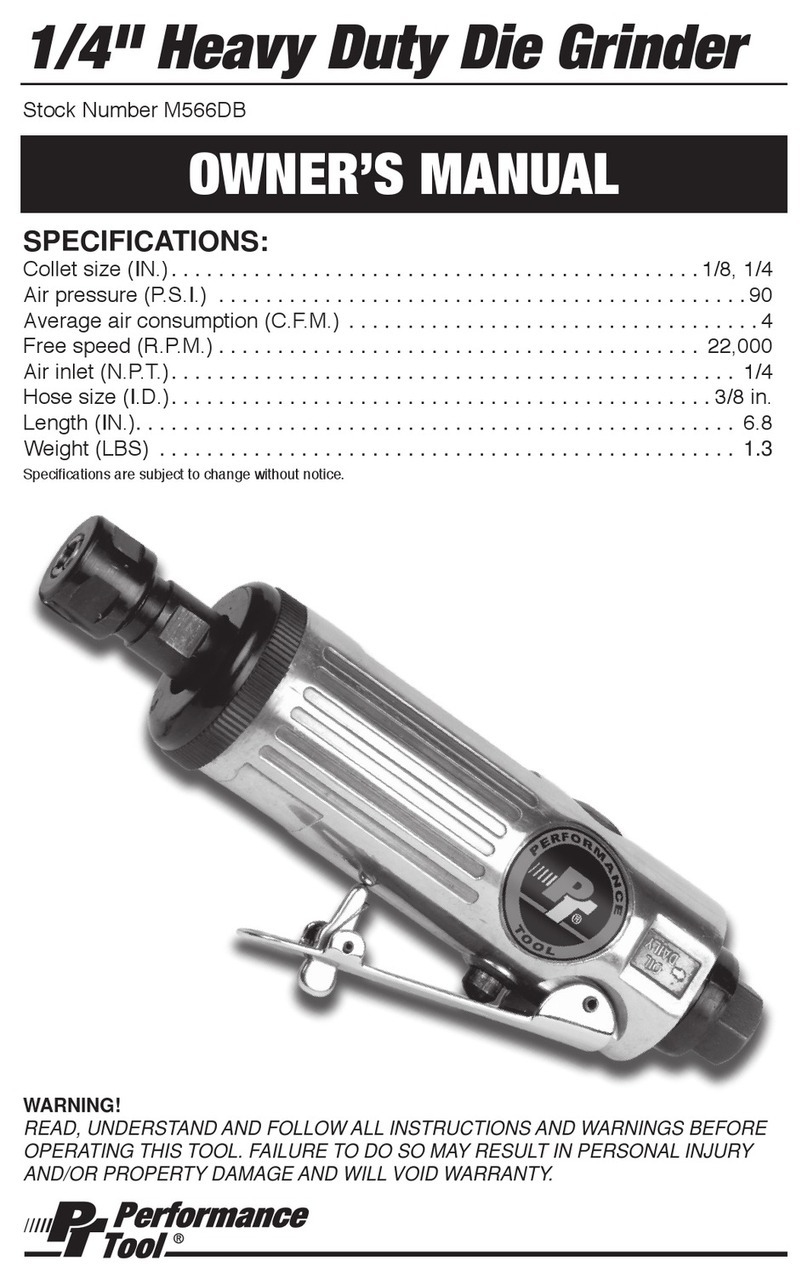
Performance Tool
Performance Tool M566DB User manual
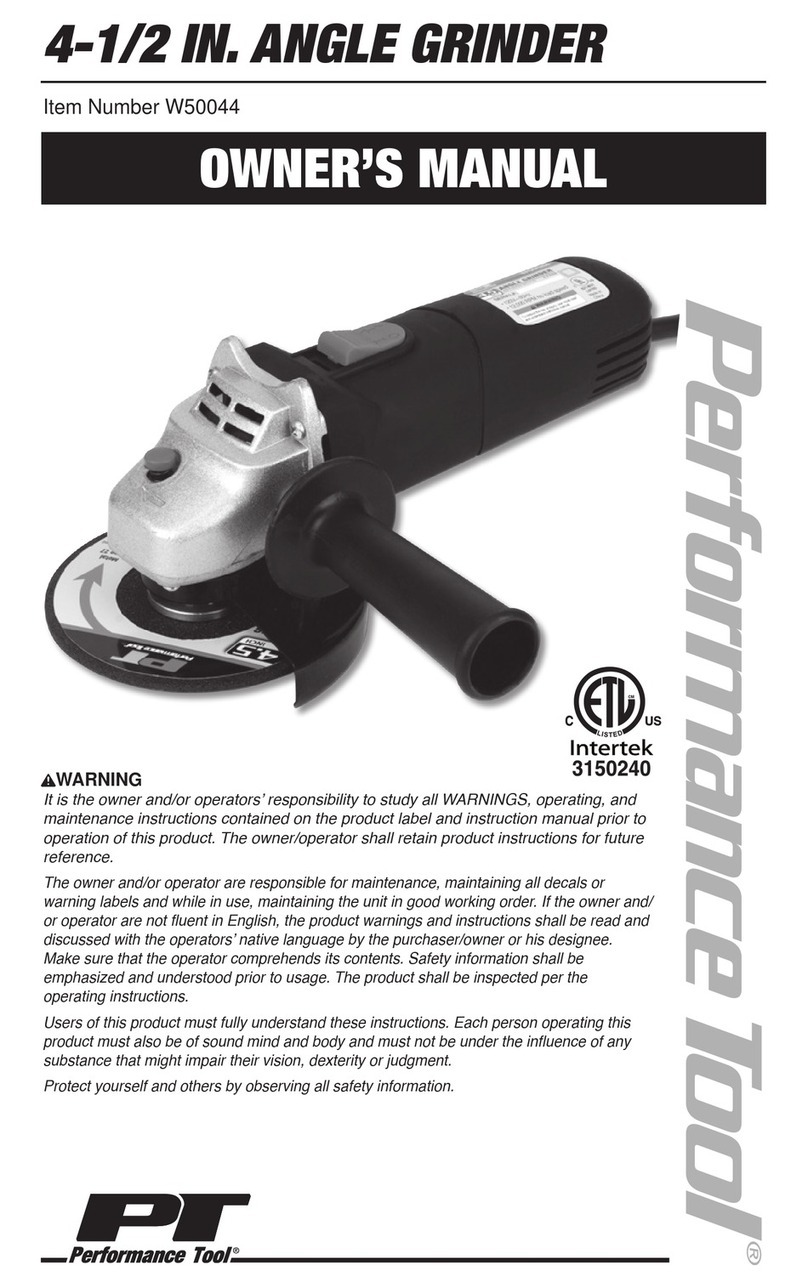
Performance Tool
Performance Tool W50044 User manual
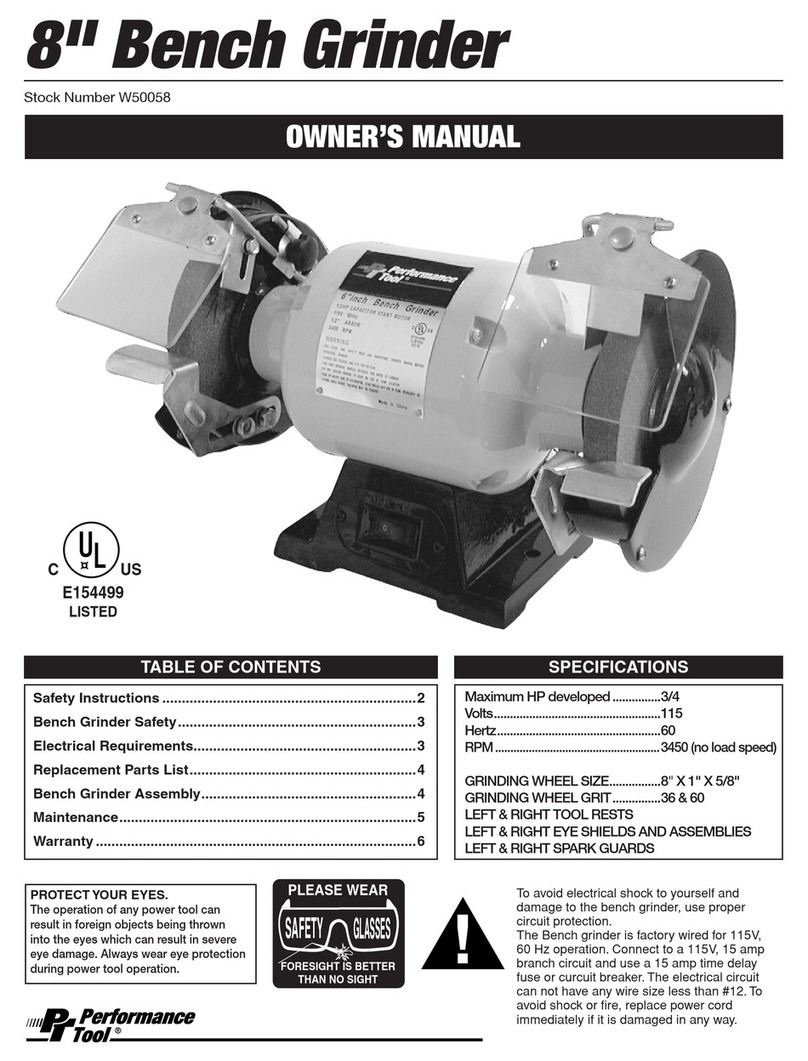
Performance Tool
Performance Tool W50058 User manual
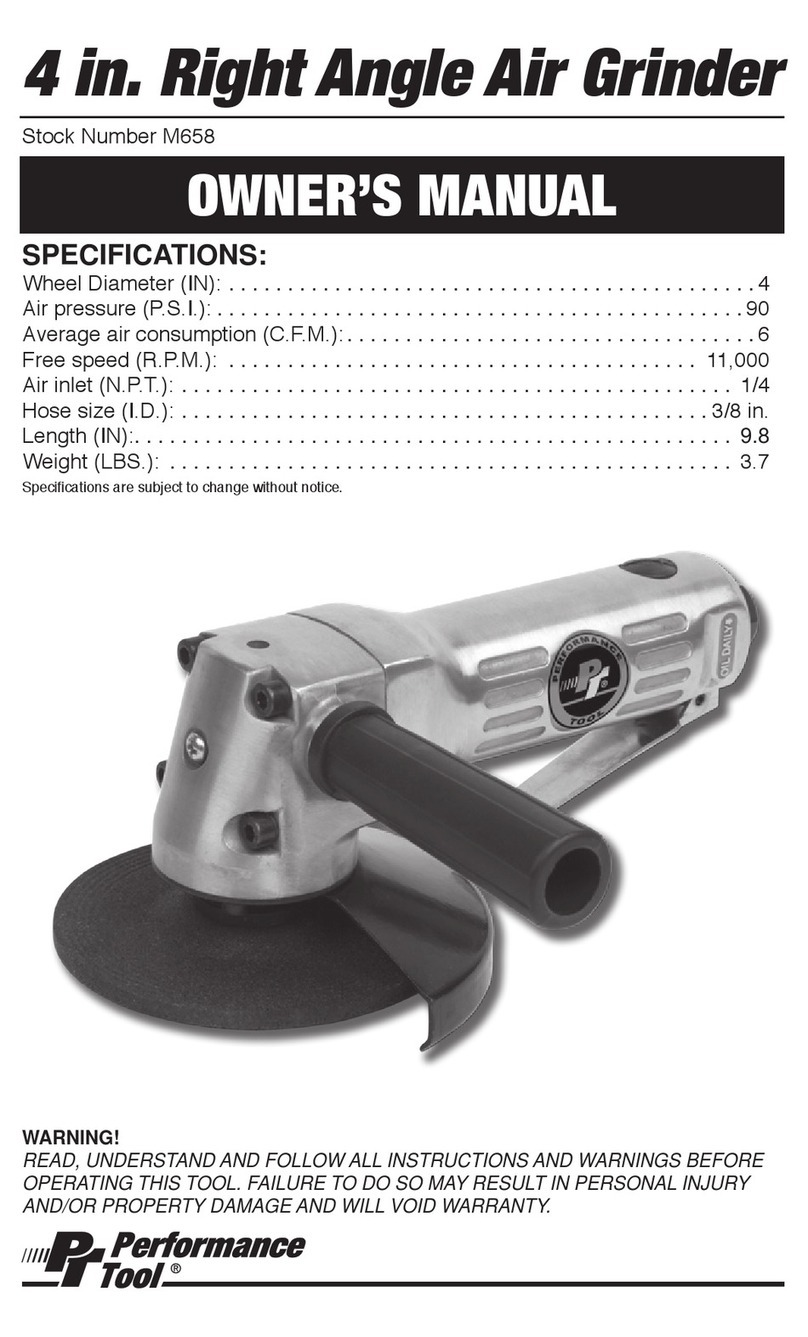
Performance Tool
Performance Tool M658 User manual
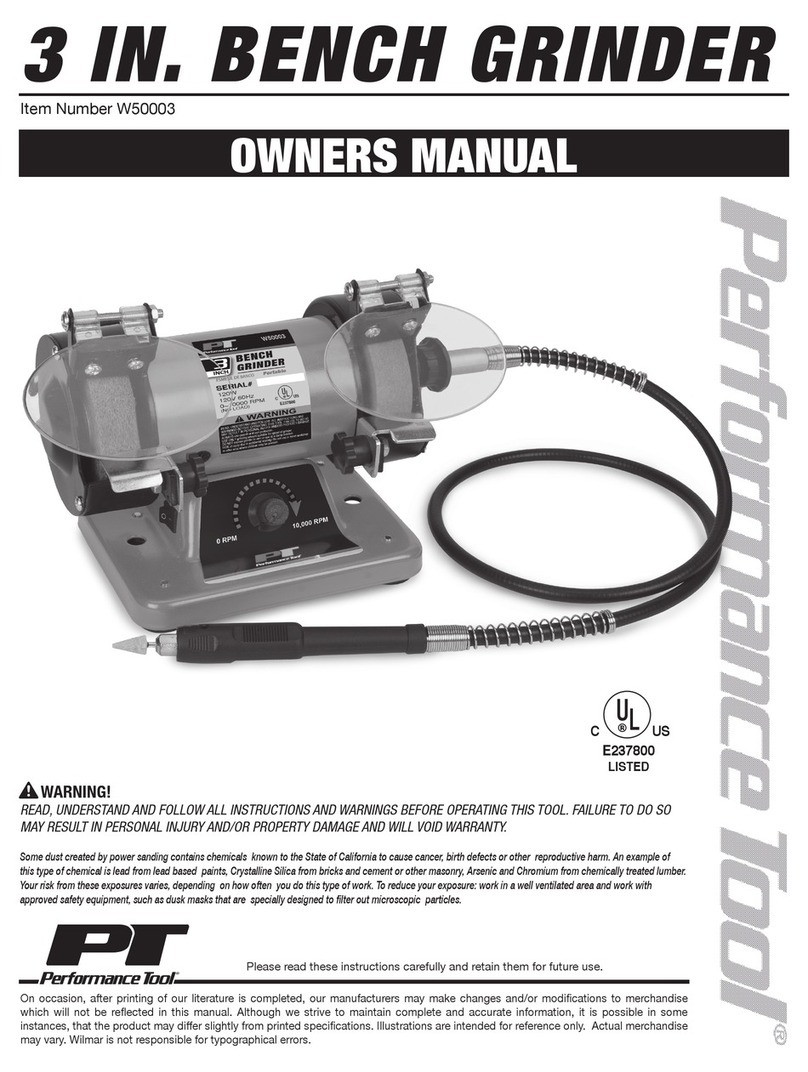
Performance Tool
Performance Tool W50003 User manual