Permalert PAL-AT AT30C User manual


PAL-AT Installation Manual
2
Notice
The information contained in this manual, including but not limited to any product specifications, is subject to
change without notice.
PERMALERT (PERMALERT), A DIVISION OF PERMA-PIPE, INC., PROVIDES NO WARRANTY WITH REGARD
TO THIS MANUAL OR ANY OTHER INFORMATION CONTAINED HEREIN AND HEREBY EXPRESSLY
DISCLAIMS ANY WARRANTIES, INCLUDING IMPLIED WARRANTIES, OF MERCHANTABILITY OR FITNESS
FOR ANY PARTICULAR PURPOSE WITH REGARD TO ANY OF THE FOREGOING. PERMALERT ASSUMES
NO LIABILITY FOR ANY DAMAGES INCURRED DIRECTLY OR INDIRECTLY FROM ANY TECHNICAL OR
TYPOGRAPHICAL ERRORS OR OMISSIONS CONTAINED HEREIN OR FOR DISCREPANCIES BETWEEN THE
PRODUCT AND THE MANUAL. IN NO EVENT SHALL PERMALERT BE LIABLE FOR ANY INCIDENTAL,
CONSEQUENTIAL, SPECIAL, OR EXEMPLARY DAMAGES, WHETHER BASED ON TORT, CONTACT OR
OTHERWISE, ARISING OUT OF OR IN CONNECTION WITH THIS MANUAL OR ANY OTHER INFORMATION
CONTAINED HEREIN OR THE USE THEREOF.
Caution --This manual may not be up-to-date.
Please check the PermAlert website, www.permalert.com, for the latest revision of this manual.
The manual is typically revised at least once a year. The revision date is on the back cover.
Contact techsupport@permalert.com for technical assistance with the PAL-AT system.

Table of Contents
Safety Information ............................................................................................ 7
1 Introduction ............................................................................................... 8
1.1 General Description .......................................................................................................... 8
1.2 Applications ...................................................................................................................... 8
1.3 Receiving and Handling Precautions ................................................................................ 8
1.4 Materials and Equipment Normally Supplied by PermAlert .............................................. 8
1.5 Materials and Equipment Normally Supplied by Installing Contractor .............................. 9
2 PAL-AT Alarm/Locator Panel ................................................................. 10
2.1 Alarm/Locator Panel Installation ..................................................................................... 10
2.2 Terminals........................................................................................................................ 11
2.3 Power Connection .......................................................................................................... 11
2.4 Audible Alarm Wiring ...................................................................................................... 11
2.5 Control Relays ................................................................................................................ 11
2.6 Communications ............................................................................................................. 14
2.6.1 Port 1 - RS-485/RS-232 ....................................................................................... 14
2.6.2 Port 2 - RS-232 .................................................................................................... 14
2.6.3 Ethernet ............................................................................................................... 14
2.6.4 Ethernet Auto-Negotiate Selection ...................................................................... 15
2.7 Replaceable Parts ............................................................................................... 15
2.7.1 Battery ................................................................................................................. 15
2.7.2 24 VDC Fuse ....................................................................................................... 15
2.8 Contrast Adjustment ....................................................................................................... 15
2.9 Impedance Jumper Setting............................................................................................. 16
2.10 UL ................................................................................................................................... 16
2.11 FCC and CE Compliance Requirements ........................................................................ 16
3 Zener Barrier Panel ................................................................................. 17
3.1 Introduction..................................................................................................................... 17
3.2 Panel Installation ............................................................................................................ 17
3.3 Panel Wiring ................................................................................................................... 19
3.4 Zener Barrier Assembly (ZBA) Installation ..................................................................... 19
3.5 Fuse Protection .............................................................................................................. 19
3.6 Allowable Cables and Probes......................................................................................... 19
4 Jumper Cable and Junction Box Installation ........................................ 20
4.1 Jumper Cable ................................................................................................................. 20

PAL-AT Installation Manual
4
4.2 Calibration Points ........................................................................................................... 21
4.3 Junction Boxes ............................................................................................................... 21
5 Cable Installation in Secondary Contained Piping ............................... 22
5.1 General .......................................................................................................................... 22
5.2 Pull Points ...................................................................................................................... 23
5.3 Cable Splices ................................................................................................................. 25
5.3.1 Factory Installed Fiber Pull Rope to Continuous Pull Wire Rope Splice .............. 25
5.3.2 Wire Rope to Wire Rope Splice ........................................................................... 26
5.3.3 Wire Rope to Wire Rope Splice (alternate).......................................................... 27
5.3.4 Wire Rope to Leak Detection Cables .................................................................. 28
5.4 Installation of the Continuous Pull Rope ........................................................................ 30
5.5 Installing Sensor and Jumper Cables ............................................................................. 32
5.6 Air Testing ...................................................................................................................... 35
6 Installation of Direct Buried Sensor Cable ............................................ 36
6.1 General .......................................................................................................................... 36
6.2 Installing the Sensor Cable ............................................................................................ 37
6.3 Above Ground Storage Tanks ........................................................................................ 40
7 Cable Installation for Raised Floor and Ceilings .................................. 42
7.1 General .......................................................................................................................... 42
7.2 Install the Sensor Cable ................................................................................................. 42
7.3 Locator Chart ................................................................................................................. 43
7.4 Calibration and end of run Access Points ...................................................................... 43
8 Cable Connectors ................................................................................... 44
8.1 General .......................................................................................................................... 44
8.2 Cable Connector Installation .......................................................................................... 44
8.2.1 CAGOLD and CATFH Connectors for Sensor Cables AGW-Gold, AGT-Gold,
TFH-Gold and TFH .............................................................................................. 44
8.2.2 CAJMP Connectors for Jumper Cables JMP-U/-UD ........................................... 47
8.2.3 CAJPP Connectors for Jumper Cables JPP and JMP ......................................... 49
8.2.4 CAGOLD Connector for ATP Cable .................................................................... 50
8.3 Shrink Tubing ................................................................................................................. 52
8.3.1 Cable Type TFH .................................................................................................. 52
8.3.2 Cable Types AGW-Gold, AGT-Gold and TFH-Gold ............................................ 53
8.3.3 Cable Types JMP-U/-UD, JPP and JMP ............................................................. 54
8.4 Cable and Connector Testing Procedures ..................................................................... 54
8.4.1 General................................................................................................................ 54
8.4.2 Continuity Test .................................................................................................... 54

PAL-AT Installation Manual
5
8.4.3 Alternative System Test ....................................................................................... 55
8.4.4 Insulation Test ..................................................................................................... 55
8.5 Cable Connections to Panels ......................................................................................... 55
8.5.1 General ................................................................................................................ 55
8.5.2 Ferrule Installation in PAL-AT Panel .................................................................... 55
8.5.3 Ferrule Installation in Zener Barrier Panel ........................................................... 57
8.5.4 ATP Cable Connection at PAL-AT ....................................................................... 59
9 Probes ..................................................................................................... 60
9.1 UL Requirements ........................................................................................................... 60
9.2 Probe Integrator Selection .............................................................................................. 60
9.3 Probe Installation ............................................................................................................ 60
9.4 PHLR Hydrocarbon Probe .............................................................................................. 62
9.4.1 Cleaning Sensor Elements Procedure ................................................................. 63
9.4.2 Testing the Probe ................................................................................................ 64
9.4.3 Troubleshooting ................................................................................................... 64
9.4.4 Calibrating the Probe ........................................................................................... 64
9.5 Typical Installations ........................................................................................................ 65
9.6 Probe Tests .................................................................................................................... 70
10 ATP Cable in Polyurethane Foam Insulation ........................................ 72
10.1 General .......................................................................................................................... 72
10.2 Pipe Installation Precautions .......................................................................................... 72
10.3 System Configuration ..................................................................................................... 72
10.4 Calibration Points ........................................................................................................... 72
10.5 ATP Cable and Connector Testing Procedures.............................................................. 72
10.5.1 Continuity Test ..................................................................................................... 73
10.5.2 Insulation Test ..................................................................................................... 73
10.5.3 Insulation Test with Wet Cloth ............................................................................. 74
10.6 Start of Run .................................................................................................................... 74
10.7 ATP Cable Splices ......................................................................................................... 75
10.8 ATP Cable at Tee Connections ...................................................................................... 77
10.9 End of Run Termination ................................................................................................. 78
10.10 Requirements for Field Joints with Wind-Down End Seals .................................. 79
Appendix A – Special Instructions ............................................................... 80
A.1 Supply Power ................................................................................................................. 80
A.2 Control Drawing .............................................................................................................. 80
A.3 Zener Barrier Panel (ZBP) .............................................................................................. 80
A.4 Probe Integrator ............................................................................................................. 80
A.5 Probe Integrator Static Precautions ................................................................................ 80

PAL-AT Installation Manual
6
A.6 ZBP Enclosure Fittings ................................................................................................... 81
WARRANTY .................................................................................................... 83

PAL-AT Installation Manual
7
Safety Information
Please Read This Installation Manual
Please take the time to read this installation manual carefully. It will help you set up and operate your system
properly. Failure to follow these instructions may impair the safety of the equipment. Please save this
installation manual for future reference.
For your safety
Caution: To reduce the risk of fire or electric shock, do not expose the PAL-AT to rain or moisture.
This symbol alerts the user to the presence of uninsulated, dangerous voltage within the system
enclosure that may be of sufficient magnitude to constitute a risk of electric shock.
This symbol alerts the user to the presence of important operating and maintenance instructions in
this manual.
Approvals and Certifications
Regulatory Compliance Statements
FCC Class A Notice
This device complies with part 15 of the FCC Rules. Operation is subject to the following two conditions.
1. This device may not cause harmful interference, and
2. This device must accept any interference received, including interference that may cause undesired operation
NOTE: This equipment has been tested and found to comply with the limits for a Class A digital device, pursuant to Part 15 of the FCC
Rules. These limits are designed to provide reasonable protection against harmful interference when the equipment is operated in a
commercial environment. This equipment generates, uses, and can radiate radio frequency energy and, if not installed and used in
accordance with this instruction manual, may cause harmful interference to radio communications.
Operation of this equipment in a residential area is likely to cause harmful interference in which case the user will be required to correct the
interference at his own expense.
Changes or modifications not expressly approved by the party responsible for compliance could void the user’s authority to operate the
equipment.
The party responsible for product compliance:
Perma-Pipe, Inc.
6410 W. Howard St.
Niles, IL 60714
CAUTION: TO REDUCE THE RISK OF ELECTRIC SHOCK,
TURN OFF POWER BEFORE OPENING ENCLOSURE DOOR.
REFER ALL SERVICING TO QUALIFIED PERSONNEL

PAL-AT Installation Manual
8
1 Introduction
1.1 General Description
This PAL-AT® Installation Manual is intended for use as a general installation guide for PAL-AT
alarm/locator panels, sensor cable, cable connectors, and probes. Users (installers) should independently
evaluate the suitability of this information and PermAlert's products for their application and specific
installation. If you receive a PermAlert product not described in this manual, contact PermAlert for the
appropriate instructions. PermAlert is a division of Perma-Pipe, Inc. Refer to the PermAlert website,
permalert.com, for the latest revision of manuals and product data sheets.
1.2 Applications
The PAL-AT system consists of an electronic microprocessor-based alarm/locator panel that monitors
sensor cables and/or probes. The sensor cable may be installed in many applications including:
secondary contained piping; directly in the ground adjacent to fuel pipes or tanks; computer room
subfloors; cleanroom subfloors, or any area where liquids need to be detected. There are several PAL-
AT models available including:
AT30C: Monitors 1 cable up to 3,000 ft [900 m].
AT75C: Monitors 1 cable up to 7,500 ft [2300 m].
AT30K: Monitors 4 cables each up to 7,500 ft [2300 m].
Applications monitoring cables in hazardous locations must use a Zener Barrier Panel (see section 3).
1.3 Receiving and Handling Precautions
The following general precautions should be observed:
1. Do not use substitute materials or short cut recommended procedures. Understanding and
following this guide is essential to avoid installation problems.
2. Collect the needed quantities of all materials well in advance of scheduled work.
3. Check the packing list against received items. Report immediately any shortages or damaged
materials to the delivering carrier.
4. All cable must be tested immediately upon receipt following the cable test procedures contained
in this manual. Report immediately to PermAlert any cables that fail the tests. Failure to report
within ten workdays of receipt of goods shall waive the purchaser's right to file a warranty claim.
5. The recommended minimum bend radius for all sensor and jumper cables is 1.5” [38mm].
6. Care must be taken to store all PAL-AT components in a dry and protected area at all times.
Electronic alarm/locator panels and sensor cable should be wrapped and sealed with plastic.
7. System drawings, provided by the designer, should indicate the extent, general location, and
arrangement of leak detection equipment, cable, and probes. The contractor (installer) should
become familiar with all details of the installation before proceeding.
8. Electrical work should be performed by a qualified electrician.
1.4 Materials and Equipment Normally Supplied by PermAlert
Each system may include the following items as quoted:
1. Leak detection/location alarm panel
2. Leak sensor cable
3. Jumper cable
4. Cable connector assemblies
5. Adhesive backed cable mounts (CMA) furnished for attachment of sensor cable to flat surfaces
6. Probe assembly, including a PT10 Probe Integrator installed in a NEMA 4X [IP66] junction box
with 60' of jumper cable and one cable connector assembly
7. Watertight junction boxes conforming to NEMA 4X [IP66].

PAL-AT Installation Manual
9
Maximum No. of
Cable Connectors
in Enclosure
Enclosure Dimensions
1 6" x 6" x 4"
[150 mm x 150 mm x 100 mm]
2 8" x 6" x 4"
[200 mm x 150 mm x 100 mm]
4 10" x 8" x 4"
[250 mm x 200 mm x 100 mm]
8. Watertight cord grips
9. Shrink tubing for cable connectors
10. Non-corrosive RTV adhesive/sealant for cable connectors
1.5 Materials and Equipment Normally Supplied by Installing Contractor
Each system may require the installing contractor to supply the following items:
1. Pull rope, 1/8" [3 mm] diameter, 7 strands, steel wire rope aircraft cable. For installation of cable in
fiberglass or other plastic piping systems, use plastic coated (non-vinyl) wire rope. Provide pull rope
in quantities equal to 120% of system length. (Included with Perma-Pipe piping systems)
2. Cable spool rack or stand
3. PVC electrical tape
4. Miscellaneous pipe nipples, unions, and fittings, as required to provide watertight jumper cable
connections to sensor cable.
5. 1" rigid or liquid-tight flexible electrical conduit, as required, for installation of jumper cable within
manholes, pits, and buildings. Use 1" conduit hub, OZ Gedney CH-100, or equal, connection to
junction boxes.
6. Electrical conduit, junction boxes, and wiring, as required.
7. Ohmmeter for testing jumper cables and sensor cables.
8. 1000-volt megger for testing ATP sensor cable.
9. Hole saw or knockout punch.
10. Construction adhesive mastic for attachment of cable mounts to unsealed concrete surfaces
11. Hot air gun for shrink tube application on cable connector assemblies

PAL-AT Installation Manual
10
2 PAL-AT Alarm/Locator Panel
2.1 Alarm/Locator Panel Installation
The PAL-AT panel is designed to be permanently mounted indoors in a dry area. The enclosure is rated
Type 12 [IP52]. It must not be located in direct sunlight to prevent excessive heat buildup. In all
installations, the ambient temperature surrounding the PAL-AT panel must be within the limits
below. The equipment is designed to be safe in the following range of environmental conditions:
a) Indoor use;
b) Altitude up to 6,560 ft [2000 m];
c) Temperature -4°F [-20°C] to 122°F [50°C];
d) Maximum relative humidity 95%;
e) Pollution degree 2.
Warning: Do not mount the PAL-AT panel in a hazardous location. The panel must be in an
ordinary location even though sensor cables may be located in hazardous locations. Refer to the
Zener Barrier Panel section of this manual.
Mount the PAL-AT panel securely to a wall, using ¼” [M6] hardware in the 4 holes on the back of the panel
(see figure 2-1). If it is mounted to a typical ½” plasterboard wall, use ¼” x 1 ½” [M6 x 40mm] lag screws
to secure it to the studs (nominal 2” x 4” [50mm x 100mm]). The panel can also be mounted to steel
mounting channel struts using ¼” [M6] machine screws.
The PAL-AT panel is connected to the sensor cable using jumper cable (Type JMP-U, JMP-UD or JPP).
An exception to this requirement is ATP cable that uses 50’ [15 m] of ATP for jumper (see section 9). At
least 50' [15 m] of jumper cable (65' [20 m] if JPP) must be connected between the panel and the
connection to the sensor cable.
The jumper cable must be run in a separate conduit from the power supply cable. All conduit fittings must
be appropriately rated and installed properly to maintain the rating of the enclosure. All electrical
connections must comply with local codes. Remove the system board from the white back panel (six
#6-32 screws) before drilling holes in the enclosure for conduit openings to prevent damage and
contamination from metal shavings.
Models AT30C, AT75C and AT30K
Mounting Dimensions
Figure 2-1

PAL-AT Installation Manual
11
2.2 Terminals
The terminals on the PAL-AT system board use a quick-connect design that provides an easy, fast and
robust connection. A flat blade screwdriver, 1/8” [3.5 mm], is used to press down on the terminal lever
and open the terminal for easy wire insertion. Release the lever, and the wire is tightly clamped. The
acceptable wire size for connection to any terminal, including the mains, is 28 - 12 AWG [0.08-2.5
mm2]. The terminals can accommodate solid or stranded wires. If ferrules are used with stranded
wire, the maximum wire size is 14 AWG [1.5 mm2]. Refer to the detail located at the upper right side
of figures 2-2 and 2.3. Caution: The lever only travels 1/8” [3.5 mm] to open the terminal completely,
and only requires 5 - 8 lbs [2-4 kg] force. Do not exceed these limits or the terminal will be
damaged.
2.3 Power Connection
The PAL-AT must be permanently wired to instrument-quality power using appropriate certified conduit,
fittings, and wiring. Refer to figures 2-2 and 2-3 wiring diagrams for details. The PAL-AT contains a universal
power supply. The power requirement is 110-240 VAC, 50 / 60 Hz, 0.3 A / 50 VA.
A suitable external over-current protection device, such as a fuse or circuit breaker (15 A), and disconnect
device is recommended. The over-current protection and disconnect devices shall be installed on all
ungrounded conductors, i.e. the terminal marked hot (L) (and neutral (N) terminal if ungrounded for 240
VAC). The disconnect device shall be located near the equipment and marked with appropriate ON (l) OFF
(O) markings as specified by local codes. The ground conductor shall have green with a yellow stripe
insulation and be connected to the grounding connection on the upper right corner of the back panel as
shown. Installation should be performed by qualified personal in accordance with local codes and
procedures.
The PAL-AT can also be powered by a 24 VDC, 1 A / 24 VA, over-current protected power source at terminal
T5. Fuse F1 on the PAL-AT system board protects the 24 VDC input. It is a 2A, 250 V, time-delay, 5 x 15
mm fuse.
Caution - Before accessing the PAL-AT panel, the panel must be disconnected from the power
source and isolated from any hazardous voltage present in the panel, e.g. relay wiring.
Three internal switches on the system board control the power source utilized by the panel. These switches
are intended for use by service personnel. Set the AC Power Switch (SW3) and the 24 VDC Power Switch
(SW1) in the down, or “OFF” position. Next, set the Input Power Select Switch (SW2) to either VAC or VDC
depending on the desired power source. The panel is controlled by SW3 for AC power or SW1 for DC
power.
2.4 Audible Alarm Wiring
An internal 90-dBA pulse horn is supplied. An optional chime alarm is available. The wiring for the horn
is a 2-wire cable connected to terminal strip T6. The red wire must be connected between the “+” terminal
on the horn and the “+” T6 terminal. The black wire must be connected between the “-” terminal on the
horn and the “-” T6 terminal. The terminal provides 24 VDC @ 10 mA.
2.5 Control Relays
PAL-AT has 3 to 6 SPDT output relays, depending on the model, rated for 250 VAC, 10 A. They are
labeled “Fault Alarm”, “Common Alarm” and “Cable x”, where x=1 to 4 for the appropriate cable number
(see figures 2-2 and 2-3). The relay contacts are labeled in their unpowered or “on-the-shelf” condition.
The fault relay energizes when the panel is powered and monitors for a power fault.
The common alarm relay switches state in response to any fault condition. The # key can be pressed to
reset the common alarm relay to its normal state and deactivate the internal audible alarm for up to 96
hours. The default reset time is 12 hours.
The cable relay(s) will activate when a fault is detected and will reset when the fault returns to normal or
the alarm queue is cleared. The default setting is to activate for all alarms, but it is firmware selectable to
activate in response to only leak and probe active alarms.
Control devices or auxiliary equipment should be connected to the cable relay(s) so they will not
be reactivated when the alarm is silenced. PAL-AT is shipped with the common alarm and cable

PAL-AT Installation Manual
12
relays configured to operate in a normally de-energized mode, so they energize when the panel is
in the alarm state (see the PAL-AT Operating Manual for changing relay configuration).
Figure 2-2
Wiring Diagram for PAL-AT Models AT30C & AT75C

PAL-AT Installation Manual
13
Figure 2-3
Wiring Diagram for PAL-AT Model AT30K

PAL-AT Installation Manual
14
2.6 Communications
PAL-AT is provided with several options for communication. The options include:
Port 1 – RS-485/RS-232
Port 2 – RS-232
Ethernet - RJ-45 connector
Refer to the PAL-AT Operating Manual for complete operating details and firmware configuration.
2.6.1 Port 1 - RS-485/RS-232
Port 1 can be configured for RS-485 or RS-232 (refer to figures 2-2 and 2-3). To configure it for RS-485,
jumper J2 should be placed in the top position. Then the two jumpers at J1 can be set to select either full
(top positions) or half-duplex (bottom positions).
Full duplex is available using two twisted-pairs connected to T1 terminals R+, R-, T+ and T-.
Half duplex, or 2-wire RS-485, requires a jumper wire connecting terminal R+ to T+ and a jumper from R-
to T-. Each PAL-AT is a full load for the RS-485 network. A crimp ferrule is recommended to connect
each incoming RS-485 lead to the corresponding jumper wire to insure a solid connection of the two wires
in the T1 terminals.
All RS-485 cables in the network should be properly terminated as per EIA RS-485
recommendations. Typically the network is a daisy-chain configuration and two 120 ohm
termination resistors are installed, one at each end of the network. Shields of the network cables
should be connected together and grounded at only one point.
Port 1 can be configured for RS-232 by moving J2 to the bottom position. Then a 3-conductor cable
should be connected to T1 terminals GND, R1 (receive) and T1 (transmit). The baud rate is configured
via the PAL-AT firmware.
2.6.2 Port 2 - RS-232
RS-232 communications through port 2 requires a 3-conductor cable connected to T1 terminals GND, R2
(receive) and T2 (transmit). The baud rate is configured via the PAL-AT firmware.
2.6.3 Ethernet
An Ethernet RJ-45 jack provides a TCP connection to the PAL-AT. There are three ports available to
handle different protocols: port 1024 for ASCII data (PALCOM), port 502 for Modbus TCP, and port 1050
for Modbus RTU over TCP.
An optional BACnet gateway is also available. Refer to Modbus to BACnet Converter Instructions (DOCID:
PPPA-PRC-CSV-006) for more information.
Refer to the PAL-AT Operating Manual for complete operating details and firmware configuration.

PAL-AT Installation Manual
15
2.6.4 Ethernet Auto-Negotiate Selection
By default, the PAL-AT is shipped with the Ethernet port permanently set to 100Mb / Full duplex.
Optionally, the port can be set to auto negotiate speed and duplex when required. This is most often
required when hard setting the switch port isn’t possible to allow 100Mb / full duplex, or when connecting
to a network that otherwise requires auto negotiation (i.e. Gigabit networks).
Ethernet auto negotiation is set through the placement of a jumper on the Auxiliary Header “J4”. The
header is located to the lower left of the power supply. Refer to Figure 2.3 for the exact location.
NOTE: System must be power cycled after changing the jumper position.
2.7 Replaceable Parts
Caution - Before accessing the PAL-AT panel, the panel must be disconnected from the power
source and isolated from any hazardous voltage present in the panel, e.g. relay wiring.
2.7.1 Battery
Battery BT1 on the PAL-AT system board maintains the clock settings when the panel is off. Jumper J5,
located above the battery, must be set “On” (left position) to enable the battery. The battery is a 3 V lithium
type.
Replace Battery With Energizer CR2025 Only. Use of Another Battery May Present A Risk of
Fire or Explosion.
Caution, Battery May Explode if Mistreated. Do Not Recharge, Disassemble or Dispose Of in
Fire.
It can be obtained locally or through PermAlert. It is replaceable by gently lifting the retaining clip to remove
the old battery and sliding in the new one. Be careful to install the battery correctly. The lettering on the
battery (+) should be facing out.
2.7.2 24 VDC Fuse
In addition to a user supplied external overcurrent protection device, fuse F1 on the PAL-AT system board
protects the 24 VDC input. It is a 2 A, 250 V, time-delay, 5 x 15 mm fuse. It can be obtained locally or
through PermAlert.
2.8 Contrast Adjustment
The contrast of the LCD can be adjusted by turning the contrast adjustment screw on the system board
(see figures 2-2 and 2-3). This may be necessary to get the best viewing angle, depending on the
No Jumper or jumper not in active
position (across right pins or on 1 pin).
Default as shipped.
Fixed 100Mb full duplex
permanently set (Legacy)
Jumper active in position 1
Auto Negotiate

PAL-AT Installation Manual
16
mounting height of the PAL-AT panel.
2.9 Impedance Jumper Setting
Refer to figures 2-2 and 2-3 for positioning the impedance jumper. The 2-pin jumper is placed in position
A, B, C, or D according to the type of cable and whether a Zener Barrier Assembly (for hazardous
locations) is connected to the selected cable. The position should be:
Jumper Position Cable Type Zener Barrier Ass’y Installed
A ATP only No
B ATP only N/A
C All others No
D All others Yes
2.10 UL
PAL-AT is listed by Underwriters Laboratories, Inc. for installation in ordinary locations. The optional Zener
Barrier Panel must be installed if any leak detection circuits are located in hazardous locations.
CAUTION - The maximum operating voltage allowed in the PAL-AT panel is 250 VAC. In
addition, the voltage on any wires to the control relays must be limited to 250 VAC.
2.11 FCC and CE Compliance Requirements
Each PAL-AT system is supplied with several "ferrite blocks" (PermAlert part # 8058207) to comply with
FCC and CE regulations for a Class A digital device. The sensor cables, jumper cables, and all
communications wires must pass through two blocks before exiting the enclosure (see figure 2-4). All
relay wires and power wires must pass through one block.
Figure 2-4
Ferrite Block Assembly

3 Zener Barrier Panel
3.1 Introduction
The optional Zener Barrier Panel (ZBP) is available for connection to PAL-AT when leak detection cables
and probes are installed in hazardous locations. It provides intrinsically safe output circuits for use in Class
I, Division 1 Groups C and D hazardous locations (Zone 0, Group IIB) when used with PAL-AT sensor
cables, jumper cables, and probes, installed in accordance with the instructions in this manual. Refer to
Appendix A, Special Instructions, for intrinsic safety requirements.
The ZBP also functions as a surge suppressor and reduces the chance of damage to the internal Zener
Barrier Assemblies (ZBA) and PAL-AT from external voltage spikes, e.g. nearby lightning strikes.
3.2 Panel Installation
The ZBP is designed to be permanently mounted indoors in a dry, non-hazardous location. The
enclosure is rated Type 4, 12 [IP66] (see figures 3-1, 3-2, and 3.3). The enclosure must not be located in
direct sunlight to prevent excessive heat buildup. In all installations, the ambient temperature
surrounding the panel must not be less than -4°F [-20°C] and not exceed 140°F [60°C]. Relative
humidity must be less than 95% (non-condensing).
The ZBP must be located adjacent to the PAL-AT panel. Each Zener Barrier Assembly (ZBA) in the
panel has a 5 ft [1.5 m] cable connected to the cable plug in the PAL-AT. The cable must be run in
conduit between the two panels.
The jumper cable from the ZBP to the sensing cable in the hazardous location must be routed in
conduit. All conduit fittings must be appropriately rated and installed properly to maintain the rating of the
enclosures. All electrical connections must comply with local codes. Seal-offs may be required to prevent
vapors from traveling into the ZBP.
Figure 3-1
Zener Panel Mounting

PAL-AT Installation Manual
18
Figure
3-2
PAL-AT and Zener Barrier Panel
Figure 3-3
Zener Barrier Panel (ZBP) Wiring
PAL-AT AT30C/AT75C/AT30K OPTIONAL ZBP
CLASS I, DIVISION 1, GROUP C
AND D HAZARDOUS LOCATIONS
(ZONE 0 AND 1, IIB).
ORDINARY
LOCATION
CABLE
CONNECTOR
CABLE TO
ORDINARY
LOCATIONS
CABLE TO
ZBP FOR
HAZARDOUS
LOCATIONS CABLE OUTPUT
TO HAZARDOUS
LOCATION
ZENER
BARRIER
ASSEMBLY
ZBA
OUTPUT
RELAYS
2 PORTS
RS-485/
RS-232
USB
DC POWER SW ITCH
24 VDC INPUT
SURGE
SUPPRESSOR
REPLACEMENT
FUSE
AC POWER SWITCH
110-240 VAC INPUT
-
+
#4#3#2
#1
143
2

PAL-AT Installation Manual
19
3.3 Panel Wiring
The standard Zener Barrier Panel (ZBP) includes one zener barrier assembly (ZBA) and has provisions to
install three additional ZBA’s. Each ZBA has a 2” [50 mm] coaxial cable lead, a 5’ [1.5 m] coaxial lead and
a 2” [50 mm] ground wire.
The 5’ [2 m] cable should be routed through conduit and connected to the appropriate cable plug in the
PAL-AT panel. The jumper cable to the PAL-AT sensing string should be connected to the fuse holder
and adjacent terminal blocks for the appropriate cable number. The jumper cable should have a ferrule
on the center conductor and two ferrules on the braid. Refer to section 8, Cable Connectors, for details.
A customer supplied earth ground wire, minimum 12 AWG [4 mm2], must be connected between
the ground connection on the upper right corner of the white back plate of the enclosure and the
ground bus of the power distribution panel.
3.4 Zener Barrier Assembly (ZBA) Installation
Refer to figure 3-3 to install a ZBA.
1. If an existing ZBA is to be replaced, loosen the four screws on the terminal strip for the ground wire,
coaxial cable center conductor, and two coaxial cable braid wire ferrules. Lift the ZBA out of the mounting
clip. Remove the end of the 5 ft. long cable from the connector in the PAL-AT panel.
2. Position and rotate the new ZBA so the 2” ground wire aligns with the appropriate ground terminal
(green/yellow terminal). Note the ground terminal for barrier #4 is on the opposite side of the fuse holder
as the other barriers. Loosely insert the ground wire, the coaxial center conductor ferrule and two braid
wire ferrules into the ground terminal, fuse holder and adjacent terminals. The ground wire ferrule is a
snug fit in the terminal and may have to be rotated slightly to insert fully.
3. Press and hold the ground wire fully inserted into the ground terminal, while tightening the terminal screw.
Next, press and hold in place the coaxial center conductor ferrule into the fuse terminal and tighten the
terminal screw. Similarly, press, hold and tighten each of the braid wire ferrules. Snap the zener barrier
assembly into the plastic holder. The 5’ [1.5 m] cable should be routed through conduit and connected
to the appropriate cable plug in the PAL-AT panel.
3.5 Fuse Protection
Each Zener Barrier Assembly is protected from external voltage surges by a replaceable fuse in the
terminal strip fuse holder. The 5 x 20 mm fuse is rated 250 mA, 250 V, fast-acting (Littelfuse 0217.250 or
equal). A replacement may be purchased from PermAlert (part # 8067989) or obtained locally.
3.6 Allowable Cables and Probes
Refer to Appendix A – Special Instructions for the PAL-AT control drawing and additional intrinsic safety
requirements for hazardous areas. The following cables, probes, and probe integrators supplied by
PermAlert comply with the allowable electrical characteristics:
Part No. Cable Type Part Number Probe Type Part Number Probe Type
8017705 AGW-Gold 8027888 PHLR-S 8027920 PSTV-L
8017700 AGT-Gold 8027889 PHLR-L 8027633 PTHL-S
8017640 TFH-Gold 8027911 PHLR-P-S 8027970 PTHL-L
8017635 TFH 8027912 PHLR-P-L 8027629 PT10-SC
8017715 JMP-U 8027623 PFS-S 8027932 PT10-SO
8017718 JMP-UD 8027910 PFS-L 8027930 PT10-LC
8017685 JPP 8027624 PSTV-S 8027934 PT10-LO
Note: A PWS probe or a probe integrator connected to a customer supplied probe having an
exposed conductive surface, may not be connected to a ZBA.

PAL-AT Installation Manual
20
4 Jumper Cable and Junction Box Installation
4.1 Jumper Cable
1. Jumper cable (types JMP-U, JMP-UD, or JPP) is used to connect sensor cable segments and probes
in series to form the sensing circuit (sensing string). Jumper cable is not affected by occasional contact
with water and can be installed in building and vaults. In underground locations and areas where
damage may occur to the jumper cable, electrical conduit should be used to provide protection. In wet
environments or areas subject to flooding, cable connectors on jumper cable should be located in
watertight electrical junction boxes (NEMA 4 or 4X) [IP66].
2. At least 50' [15 m] of jumper cable (65' [20 m] for type JPP) must be installed from the PAL-AT panel
or Zener Barrier Panel to the first section of sensor cable or probe. An exception is connecting to ATP
cable (see section 10).
3. Table 4-1 lists the length of jumper installed at the very end of a sensing string. A cable connector
must be installed to terminate the end of the last jumper cable section and a threaded plastic cap is
supplied to cover the connector.
4. Refer to section 9, table 9-1 for additional jumper cable required in a probe section.
5. Where possible, jumper cable connections to sensor cable should be made within the monitored area.
PermAlert recommends the use of OZ Gedney, or equal, cord grips installed as shown in figure 4-1.
Cord grips must clamp only jumper cable or TFH cable. The plastic outer braid on TFH cable must be
pulled back so the cord grip is located on the smooth outer jacket.
6. Check the cable/connector assembly with an ohmmeter in accordance with the cable testing
procedures contained in this manual.
7. The recommended minimum bend radius for all jumper cables is 1.5” [38mm].
Table 4-1
End of System Jumper Cable Length
System Length
ft / [m]
JMP-U/UD
End Jumper Length
ft / [m]
JPP
End Jumper Length
ft / [(m]
0–2500 / [0-750] 30 / [9] 40 / [12]
2500-5000 / [750-1500] 50 / [15] 65 / [20]
5000-7500 / [1500-2300] 100 / [30] 125 / [40]
Other manuals for PAL-AT AT30C
1
This manual suits for next models
2
Table of contents
Popular Control Panel manuals by other brands
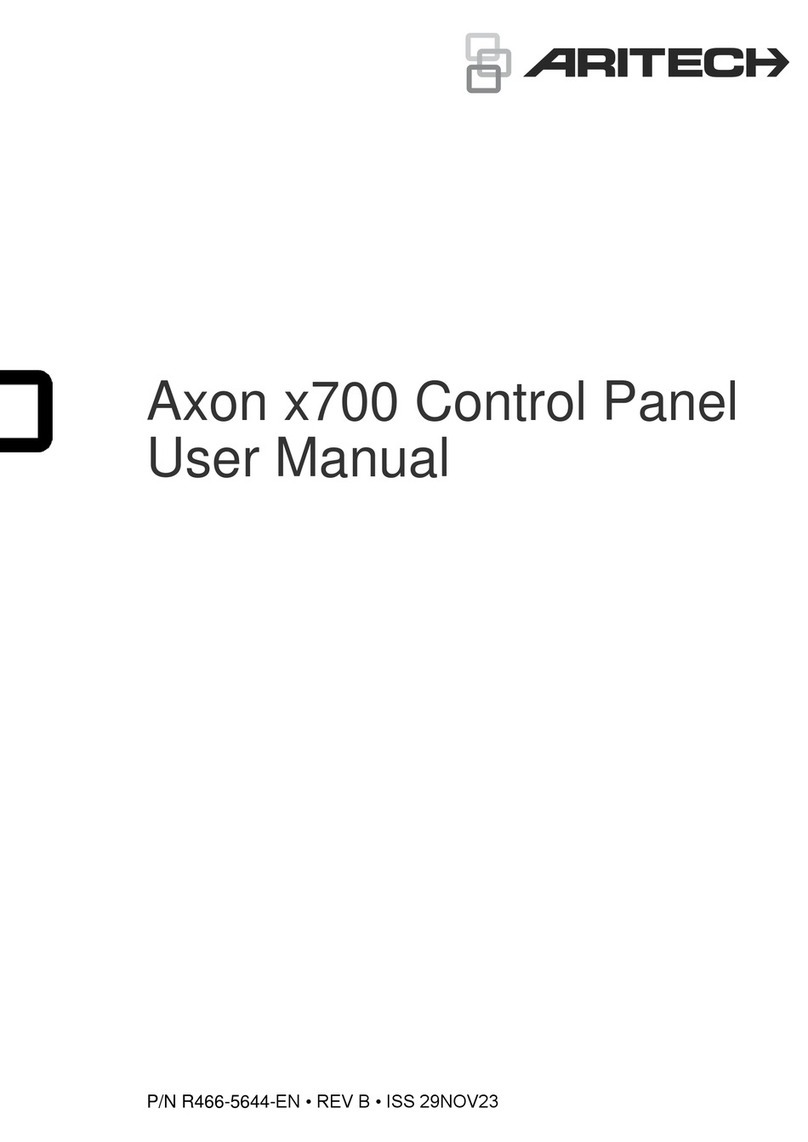
Aritech
Aritech Axon x700 user manual

Riello
Riello CBD 35 Instruction booklet
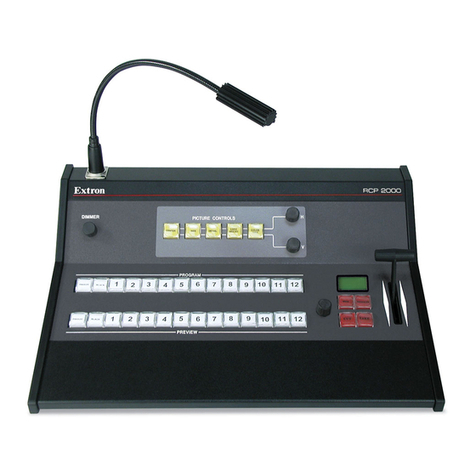
Extron electronics
Extron electronics RCP 2000 user guide
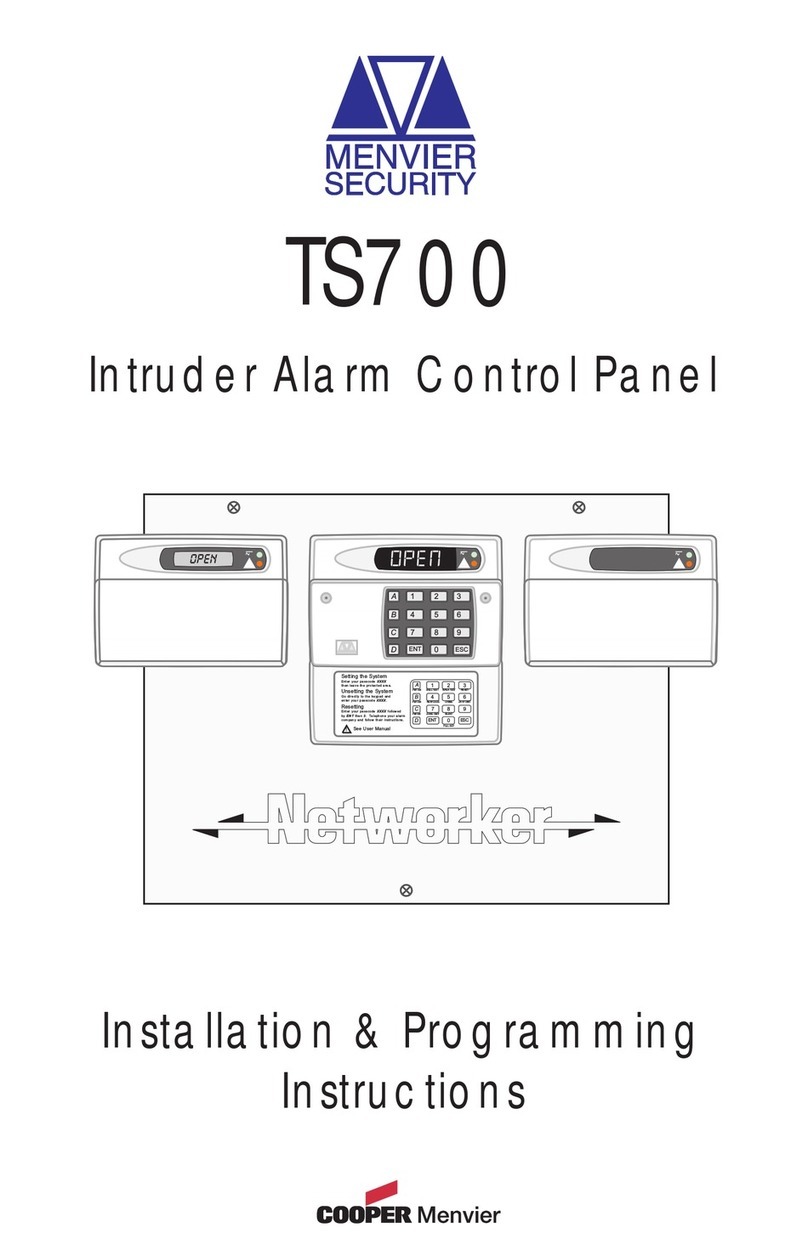
Menvier Security
Menvier Security TS700 Installation & programming instructions
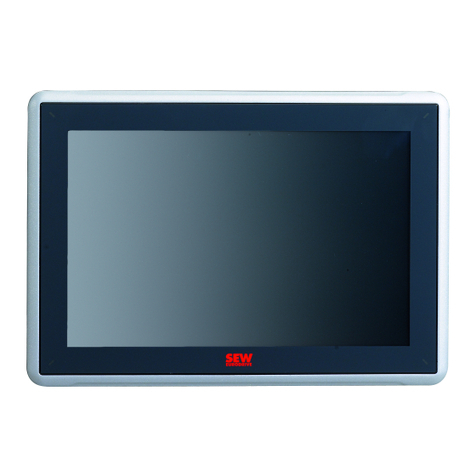
SEW-Eurodrive
SEW-Eurodrive DOP11C operating instructions
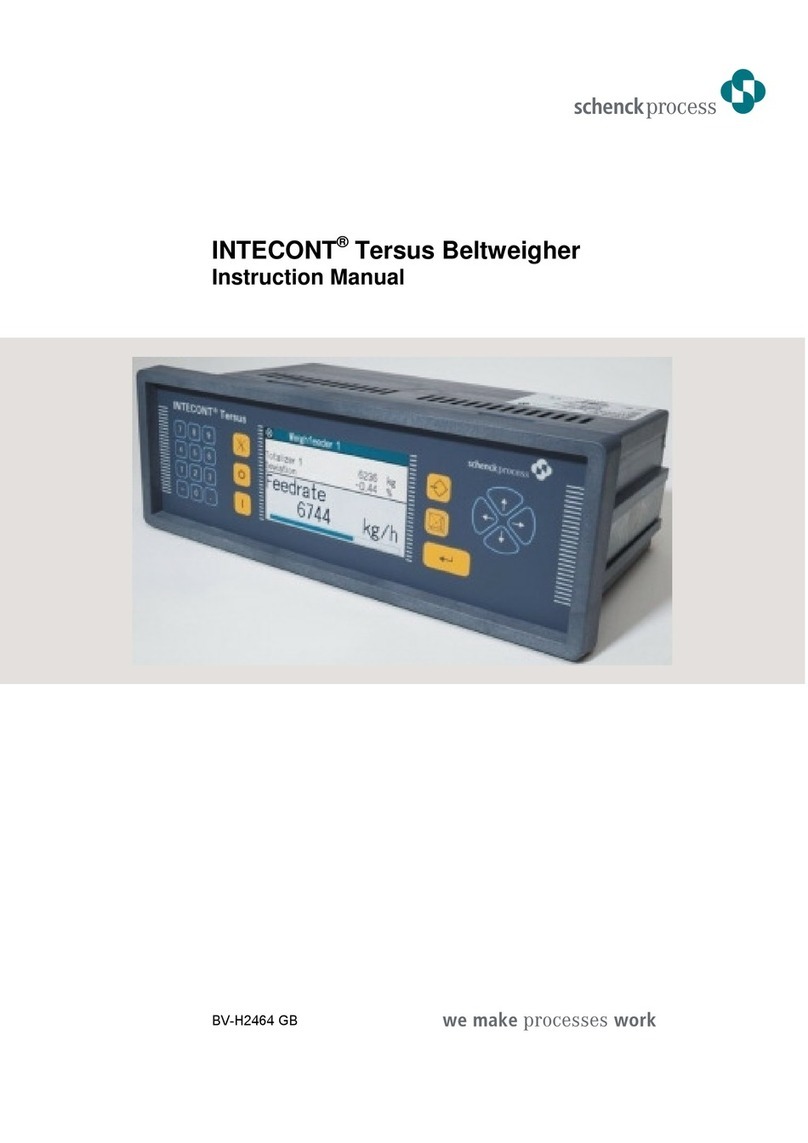
Schenck process
Schenck process Intecont Tersus Beltweigher instruction manual