PHP PH52W User manual

®
PH52W ENGINE HEATER
Technical Description
Installation Instructions
Operating Instructions
Troubleshooting and Parts


2
Table of Contents
Introduction 3
Heater Warnings 4
Specications 5
Heater Kit List 6
Main Components and Operating Concept 8
Heater Mounting 9
Exhaust & Combustion Air Intake Connections 11
Heater Plumbing 13
Fuel System 15
Electrical Connections 18
Operating Switch 20
Heater Operation 26
Troubleshooting & Parts 29
Heater Components 30

3
Introduction
Thank you for purchasing our PH52W heater kit.
The PH52W heater is designed to preheat your engine by using on-board diesel fuel and
battery systems. Operation is simple and the heater provides a safe and reliable alternative to
cold engine starting or need for electrical plug ins.
Please take a moment to familiarize yourself with this manual, safety warnings and heater
requirements before installing or operating your heater.

4
Heater Warnings
Special Notes
Note: Highlight areas requiring special attention or clarication.
Warning
Caution
Caution - Operational Considerations
Indicates that personal injury or damage to equipment may occur unless specic guidelines
are followed.
Indicates that serious or fatal injury may result if specic guidelines are not followed.
• The installation of this kit requires trained decision-
making concerning locating and integrating components,
tying components together, rerouting, or relocating OEM
components, etc.
• It is impossible to describe all of the safety and operational
considerations in the installation instructions. Therefore,
the technician must exercise professional judgment to
achieve a safe and quality installation.
• Read and understand this manual before attempting to
install the heater.
• Failure to follow all these instructions could cause serious
or fatal injury.
• Ensure a proper mixture of water and antifreeze to prevent
coolant from Freezing.
• Ensure that the coolant ow can never be blocked while
heater is in operation.
• Blocking coolant ow can result in extreme pressure,
bursting hoses and release of scalding coolant.
This heater is not designed for use with straight bio-diesel
(Blends of bio-diesel up to 10% are acceptable)
Operating outside of these conditions may plug the heater
with soot and result in combustion failure.
This heater is not designed to operate continuously at
altitudes above 1500 meters (4920’).
Operating in these conditions may plug the heater with soot
and result in combustion failure.
• Heater must be turned o while re-fueling.
• Do not install heater in enclosed areas where combustible
fumes may be present.
• Exhaust pipe must maintain a minimum a distance of
50mm (2”) from any ammable or heat sensitive material.
• Ensure there are no leaks in the fuel system.
• Ensure that exhaust fumes cannot enter passenger
compartments.
Warning - Installation Hazards
Warning - Burn Hazards
Bio-Diesel
High Altitudes
Warning - Explosion Hazards
Warning - Fire Hazards
Warning - Asphyxiation Hazards

5
Specications
Performance Specifications
Heating Mode High
Heating Capacity kW/hr (BTUs/hr) 5.0 (17,060)
Fuel Consumption L/hr (US Gal/hr) 0.6 (0.16)
Power Consumption - WATT 56
Power Consumption In Standby - WATT 27
Start-up Power Consumption - WATT < 135
Min. Coolant Through-put L/hr (US Gal/hr) 250 (66)
Fuel Type Diesel
Nominal Voltage 12 Volt
Lower Voltage Limit 10.5 / 21.0 Volts over 20 seconds
Upper Voltage Limit 16.0 / 32.0 Volt over 20 seconds
Overheat Protection 115º C (239º F)
Allowed Ambient Temperature -40º C to 80º C (-40º F to 176º F)
Weight 2.5 kg (5.5 lbs)
Above Specications (± 10%)
15cm (5.75”)
22cm (8.5”) 9cm (3.5”)
Principal Dimensions
*Figure O1 22cm (8.5”)
15cm (5.75”)
9cm (3.5”)

6
Heater Kit List
QTY
1
1
QTY
1
QTY
1
QTY
1
1
2
1
1
QTY
1
QTY
1
Part Number
P52W-X303
NPN
Part Number
P52W-X701
Part Number
P52W-T301
Part Number
U65D-X519
U65D-X522
NPN
U65D-X502
NPN
Part Number
P52W-T601
Part Number
P52W-T802
Description
5 kW Engine Heater Boxed Version
Note: Contents of the kit will vary for Boxed Version. Kit list is based on Universal Kit Version.
Description
Operating Switch
2 Sided Mounting Tape
Description
Mounting Bracket
Description
Wiring Harness
5M (16’) Power Harness, 20A Fuse
5M (16’) Fuel Pump Harness
7.5M (25’) Switch Harness, 5A Fuse
0.3M (12”) Coolant Pump Harness
Description
Flexible Stainless Steel Exhaust, 0.6M x 22mm
Combustion Air Intake Tube, 0.6M x 22mm
“P” Clamp
24 – 26 mm Exhaust Clamp
24 – 26 mm Combustion Air Hose Clamp
Description
Coolant Pump
Description
5 kW Engine Heater

7
Heater Kit List
QTY
1
1
1
1
4
1
1
12
Part Number
U65D-X405
P52W-T401
U65D-X407
U65D-X414
U65D-X409
U65D-X704
U65D-X406
U65D-X401
Description
Fuel Pickup Tube & Fuel Tube Hardware Kit
- Compression Fitting
- Large Flat Washer
- Small Flat Washer
- Large Rubber Gasket
- Large Hex Nut
- Brass Hex Nut
- Brass Securing Body
Fuel Metering Pump
Fuel Pump Holder
Black Rubber Fuel Line, 0.3M (12”) 7mm ID
5mm x 50mm Fuel Line Connectors
“Z” Mounting Bracket
Clear Plastic Fuel Line, 5M (16’) 2mm ID
Small Fuel Line Clamps, 9-11 mm
QTY
1
2
4
6
6
4
2
11
Part Number
U65D-X704
U65D-X706
NPN
NPN
NPN
NPN
NPN
NPN
Description
“Z” Mounting Bracket
“L” Brackets
M6 x 15 Screws
M6 x 25 Screws
M6 Hex Nuts
M6 Flat Washers
#8 Self Drilling Screws
6mm Lock Washers

8
Main Components and Operating Concept
Main parts of PH52W Engine Heaters
Here is a basic overview of the operation of the heater.
• Fuel is delivered to the heater via the heater’s fuel pump.
• Combustion air is delivered to the heater via the heaters 12v combustion air blower.
• Fuel is atomized and the fuel / air mixture is ignited using a glow pin.
• The ame is contained in a ame tube and exhaust gases expelled.
• The heater’s coolant pump takes cold coolant from the engine, circulates it through the heater’s
water jacket, then it pumps hot coolant back to the engine.
*Figure O2
1. Overheat Sensor
2. Heat Exchanger
3. Temperature Sensor
4. Coolant Inlet
5. Atomizer
6. Glow Pin / Flame Sensor
7. Coolant Outlet
8. Blower Motor
9. Combustion Air Blower
10. Return Coolant
11. Coolant Pump
12. Fuel Metering Pump
13. Combustion Air Inlet
14. ECU
15. Fuel Inlet
16. Exhaust Outlet
17. Flame Tube
18. Heat Exchanger

9
Heater Mounting
Mounting Considerations:
• Protect from road spray
• Mount below engine coolant level to avoid air blockage.
• Keep coolant hoses short to maximize ow and minimize heat loss.
• Keep power wiring short to minimize voltage drop.
• Keep fuel lines short to ensure good combustion.
Suggested Locations:
• Step box
• External storage compartments (Not inside cab)
• Inside frame rail
• Inside engine compartment
Note: PHP boxed version can be used to simplify your installation and protect your investment.

10
Heater Mounting
*Figure M1
*Figure M2 *Figure M3
Heater Mounting Bracket PHP Boxed Version
Mounting:
Mount the heater using the mounting bracket provided with the installation kit.
Provide shielding as required to protect the heater from environmental conditions.
Orientate the heater within permissible mounting congurations shown in Figure M1.
Do not mount the heater inside passenger compartments where poisonous exhaust fumes may be inhaled.
Guard the heater against excessive road spray to minimize corrosion and avoid ingestion of debris.
Warning - Asphyxiation Hazard
Caution

11
Exhaust & Combustion Air Intake Connections
The combustion air intake channels clean air into the heater. It can be eliminated if not required to ensure
clean air intake.
The exhaust tube channels exhaust safely away from the heater and vehicle. It also assists in providing a
required amount of back pressure required to balance the combustion process.
Exhaust Considerations:
• The exhaust is made using a heat resistant, 22mm exible, stainless steel tube.
• Secure the exhaust tube to the heater using the exhaust clamp provided.
• Discharge exhaust away from passenger compartment.
• Ensure exhaust fumes cannot be sucked into combustion air intake.
• Install exhaust pipe with incline for moisture run o.
• Drill a small drain hole at low point if proper incline cannot be maintained.
• Route the exhaust pipe from the heater using “p” clamps provided.
• Route away from the vehicle slip stream.
Combustion Air Intake Considerations:
• The combustion air intake is made from a exible, water resistant, paper / aluminum compound.
• Secure the combustion air intake tube to the heater using the clamp provided.
• Draw air from a clean air source away from water, dust and exhaust.
• The combustion air opening must be kept free at all times.
• Install combustion air intake tube with an incline for moisture run o.
• Route the combustion air intake using“p” clamps provided.
• Route away from the vehicle slip stream.

12
Exhaust & Combustion Air Intake Connections
The exhaust is hot, keep a minimum of 5 cm (2”) clearance from any heat sensitive material.
Route exhaust beyond the skirt of the cab and outside of the frame area.
Failure to comply with this warning could result in Carbon Monoxide Poisoning.
Combustion Air Intake
Max. 1M (3’)
Exhaust
Min. 0.2M (8”) Max. 2M (6’)
*Figure A1
Warning - Fire Hazard
Warning - Asphyxiation Hazard

13
Heater Plumbing
Understand that connecting your heater to the engine makes it an integral part of the engine’s cooling
system. It is impossible to describe all of the safety and operational considerations in these installation
instructions. Therefore, the technician must exercise professional judgment to achieve a safe and quality
installation. It is important to try to optimize the coolant ow to get the best heat distribution and heater
operation.
Installation Procedure:
• Plan the heater plumbing circuit.
• Install the coolant pump in a protected location close to the heater (Note: Pump is pre-installed in the
boxed version)
• Install ttings, valves and run hoses as required.
• Bleed the air out of the system (Run engine to help circulate coolant).
• Top up coolant as required.
• Test the heater to ensure proper ow.
*Figure P1

14
Heater Plumbing
Follow these guidelines and considerations:
• There are a few plumbing accessories included with the kit (Connectors and molded hoses)
• Use 3/4” hoses to optimize coolant ow.
• Keep the pick up and return points as far apart as possible.
• Take coolant from a high pressure point of the engine (ie. back of block)
• Return coolant to a low pressure point of the engine (ie. engine’s coolant pump).
• Use ball valves to isolated the system when not in use.
• Take the coolant from a low point on the engine to minimize aeration.
• Mount heater and coolant pump low to allow the purging of air.
• Consider using insulation around the hoses.
• A heat exchange can be incorporated into the system. However, ensure that the heater ow can never be
completely blocked by a ow control valve.
• Do not work on the plumbing system when it is hot or under pressure.
• Do not work on the heater or plumbing system when the heater or engine are in operation.
• Always wear safety gloves and appropriate eye protection.
• Ensure system has pressure relief protection limiting maximum system pressure to 15 PSI (1 bar).
• Coolant ow must never be blocked during heater operation (ie. ow control valves).
Tech Tip:
Test the ow by feeling the incoming and outgoing hoses. In a system with proper coolant ow, the output
temperature will not exceed the input temperature by more than 10°C (18°F).
The coolant liquid must contain at least 10% antifreeze all year round as a corrosion protection.
*Figure P2
Warning - Burn & Explosion Hazards
Caution
Out
IN

15
Fuel System
The PH52W fuel pump and fuel system are the heart of the heater. The fuel pump not only delivers fuel to
the heater but also controls the amount of fuel delivered. The pump is designed to operate like an electric
solenoid and works using electric pulses. Each time it is energized, it provides a measured dose of fuel. It
is critical to the heater’s operation to stay within parameters outlined below and only use the components
provided. (Figure F1)
System Layout & Considerations
• Keep the length of the fuel system short as possible.
• Mount the fuel pump as close to the fuel pickup as possible (pump pushes better than it sucks).
• Minimize vertical rise.
• Mount the fuel pump in a protected location away from road spray.
• Choose a mounting location for the fuel pickup pipe that is close to the heater and oers installation
access.
• Design your fuel system so that Figure F1 fuel line limits are not exceeded.
*Figure F1
1. Heater
2. Fuel Pickup Pipe
3. Fuel Metering Pump
4. Fuel Tank
5. 9-11 mm Clamp
6. 5.0 mm Rubber Fuel Line
7. 5.0 mm Rubber Connector
8. 3.0 mm Clear Plastic Fuel Line
Max. 2 M (12’) Max. 6 M (20’)
Max. ½ M (18”)
Max. 1 M (6, 6”)

16
Fuel System
Fuel Pump Mounting
• Using the bracket and rubber mount provided, install fuel pump as shown. (Figure F2)
• Isolating the pump with the rubber holder helps to minimize noise created during operation.
• Ensure that the proper mounting angle is observed to avoid cavitation. (Figure F3)
Fuel Source
• Connect directly into the fuel tank using our dedicated fuel pickup tube.
• Teeing into the existing vehicle fuel lines is not recommended.
• There are three common methods to install a fuel pickup tube.
• Use NPT / compression ttings if available
• Use spare fuel gauge plate if available
• Drill dedicated holes into the tank.
Fuel Pickup Pipe
*Figure F2 *Figure F3
*Figure F4
15 ° to
vertical
Securing Nut
Large Steel Washer
Rubber Washer
Small Steel Washer
(Inside Tank)
Compression
Fitting Adapter Fuel Pickup Tube
Brass Adapter Base

17
Fuel Pick-Up Pipe Installation (Drill Option)
• Drill mounting holes in tank to accommodate pick-up pipe as shown in Figure F4
• Drill the two (1/4”) holes rst. (Figure F5)
• Drill a 7/8” hole. (Figure F6)
• Mount the fuel pick-up assembly pipe as shown.
• Position pick-up pipe 4” from bottom of tank (1”for at tanks)
Fuel Line Connections
• Route fuel lines from the fuel pick-up pipe to the heater.
• Use only fuel lines provided (Other sizes or types of fuel lines may inhibit proper fuel ow)
• Make proper butt joints using clamps and connector pieces as shown.
• Use a sharp utility knife to cut plastic fuel lines to avoid fuel line pinching.
Fuel System
*Figure F5 *Figure F6
2 x 6mm (1/4”)
Ø22 mm (7/8”)
24mm (0.93”)

18
Electrical Connections
Electrical System Installation
Connect the heater harness as follows:
• Route cables using either an existing cable passage or drill holes as required.
• Seal the hole around the cables and make sure they are protected from chang and pinching.
• Cut each harness section to length and install terminals and connectors as required.
• Below is a summary of the wiring connections required.
*Figure E1
Coolant
Pump
Battery
20 amp
Fuse
5 amp
Fuse
Timer
Heater
Fuel
Pump

19
Main Harness Wiring Legend
Note: There are no corresponding numbers on the connector. Numbers are for reference only.
Open end view of main heater harness connector
Electrical Connections
A. Main Heater Harness Connects switch and power harness to the heater harness.
Refer to Main Harness Connections Legend for details.
B. Power Harness 2 Core, 5M (16’) Long – Red & Black
• Route power harness section from heater to vehicle batteries.
• Cut to required length.
• Connect red wire to fuse link and install terminal.
• Attach ring terminal to battery (+).
• Connect brown wire to battery (-) using ring terminal provided.
• Install 20 amp main fuse (Last step of installation)
C. Switch Harness 5 Core, 8M (25’) Long – Red, Brown, Yellow, Blue, Green
• Route switch harness section from heater to switch location.
• Cut harness to length and attach wiring terminals
• Install terminals into connector so they match the wire colours from the operating
switch. Yellow is a spare wire.
• Attached connector to operating switch
• This circuit is protected by a 5 amp fuse located near the main harness connection.
D. Fuel Metering Pump Harness 2 Core, 5M (16’) Long – Purple & White
• Route fuel metering pump harness to fuel pump.
• Cut to required length.
• Install wiring terminals, protective seals and connector block (No polarity required –
Connect either wire to either terminal).
E. Coolant Pump Harness 2 Core, 0.3M (1’) Long – Black & Orange
• Connector is pre-installed.
• Route coolant pump harness to coolant pump and connect.
Terminal Wire Color Function
1. Red Main “+” Positive Feed
2. Yellow Spare
3. Green Switch
4. Orange Coolant Pump “+”
5. White Fuel Pump
6. Black Main “-” Negative Feed
7. Brown Switch
8. Blue Switch
9. Black Coolant Pump “-”
10. Purple Fuel Pump
Table of contents
Other PHP Heater manuals
Popular Heater manuals by other brands
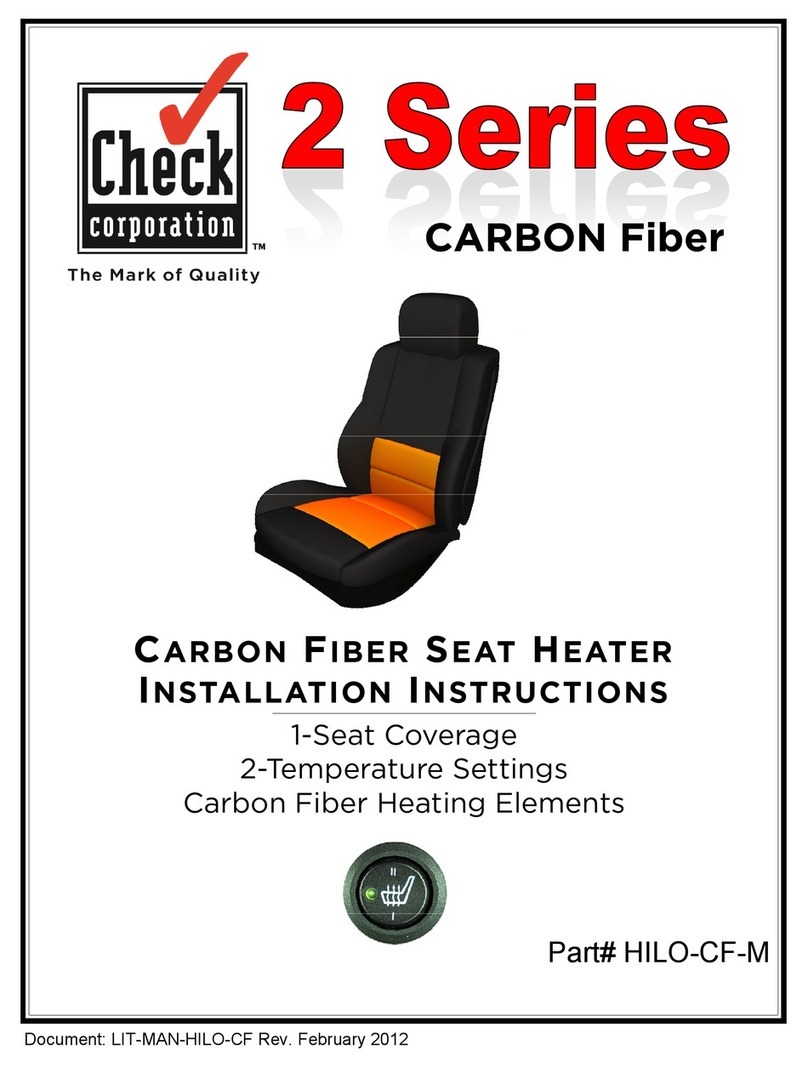
Check corporation
Check corporation 2 Series installation instructions
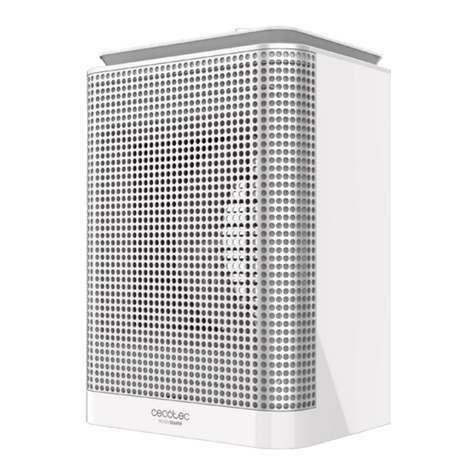
cecotec
cecotec Ready Warm 6150 Ceramic Rotate Style instruction manual

Charmate
Charmate CMK302 quick start guide
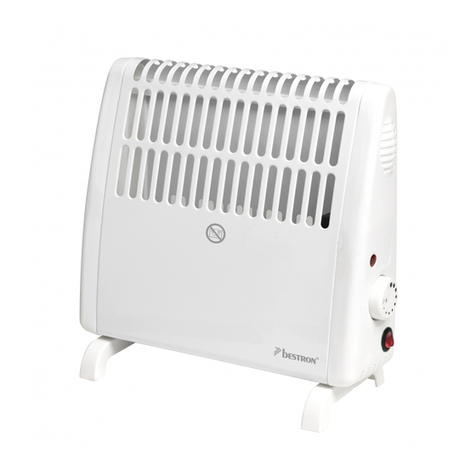
Bestron
Bestron ABH401 instruction manual
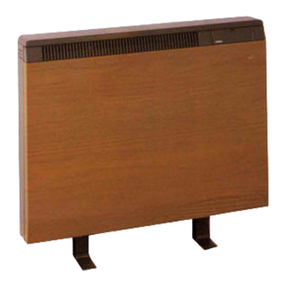
Dimplex
Dimplex XT12 installation instructions

Haverland
Haverland ULTRAD instruction manual