Plettenberg MST60-80 Quick start guide

Operational Manual Plettenberg Motor control MST-60-80 V5.1
S. 1
MST60-80
Plettenberg Elektromotoren GmbH & Co. KG
Rostocker Str. 30
D-34225 Baunatal
Telefon: +49 (0) 56 01 / 97 96-0
Fax: +49 (0) 56 01 / 97 96-11
Internet: http://www.plettenberg-motoren.com
e-Mail: [email protected]

Operational Manual Plettenberg Motor control MST-60-80 V5.1
S. 2
Table of Contents
Chapter Seite
1 Introduction . . . . . . . . . . . . . . . . . . . . . . . . . . . . . . . . . . . . 3
2 Technical Data . . . . . . . . . . . . . . . . . . . . . . . . . . . . . . . . . 4
3 Drawing including connections . . . . . . . . . . . . . . . . . . . . 5
4 Mounting and connection rules . . . . . . . . . . . . . . . . . . . 6
5 connectors and pin assignment . . . . . . . . . . . . . . . . . . . 7
6 Trouble free and safe operation . . . . . . . . . . . . . . . . . . . . 7
7 Safety functions . . . . . . . . . . . . . . . . . . . . . . . . . . . . . . . . 8
8 Safety notes . . . . . . . . . . . . . . . . . . . . . . . . . . . . . . . . . . . . 9
9 Initial operation of the drive system . . . . . . . . . . . . . . . . . 11
10 LED indicator functions . . . . . . . . . . .. . . . . . . . . . . . . . . . 12
11 Standard Setup Values . . . . . . . . . . . . . . . . . . . . . . . . . . . 13
12 RS232-Interface-Parameters . . . . . . . . . . . . . . . . . . . . . . 13
13 RS232-Interface-Protocol-Description . . . . . . . . . . . . . . 13
14 RS232-Interface-Commands . . . . . . . . . . . . . . . . . . . . . . 14
15 Sensor Phase Mapping . . . . . . . . . . . . . . . . . . . . . . . . . . . 16
16 Legal terms and conditions . . . . . . . . . . . . . . . . . . . . . . . 17

Operational Manual Plettenberg Motor control MST-60-80 V5.1
S. 3
1 Introduction :
This manual describes the features, installation and operation of
Plettenberg motor control MST60-80.
Please read the instruction manual carefully and completely before
using the controller. Disregarding the hints and instructions can be fatal
and can cause lethal injuries! The limitation of the length of the battery
input cables is mandatory(see chapter 4).
If you have questions please do not hesitate to contact us.
The engine control MST60-80 has been specially developed for the use
with brushless Plettenberg electric motors with sensors. Brushless
motors from other manufacturers can only be connected, if they are
equipped with 3 Hall sensors in 120 ° electrical arrangement. We
assume no guarantee for the proper functioning of the MST60-80 with
motors from other manufacturers.
The MST60-80 can drive brushless motors electrically up to 240000 rpm.
A 20-pole motor, for example, makes 10 electrical revolutions doing one
shaft rotation. The maximum speed for such a 20-pole motor is
calculated: 240000rpm / 10pole pairs = 24000rpm.
The powerful 32-bit microprocessor allows a sensitive and fast motor
control in conjunction with a very universal use. The measured values
are displayed in real time on the RS232 interface in plain text so that
they can be evaluated with a PC or other microprocessor control easy.
The firmware of the MST60-80 can be updated. However, it has to be
sent to the factory for update.

Operational Manual Plettenberg Motor control MST-60-80 V5.1
S. 4
2 Technical Data :
Weight: approx. 230g without connectors
Length: 112mm with flange, 95mm without flange
Width: 56mm
Height: 19 mm without connector
Protection class: IP40
Maximum Speed: 240000rpm electrical
Maximum continuous power 4800W
Maximum short term power 7200W
Battery voltage range 12V to 52V nominal
Permissible supply voltage 10 to 60V
Maximum current 120A / 80A continuous current (at 25 ° C ambient temperature)
At 50 ° C ambient temperature, the continuous current is 65A.
At 75 ° C ambient temperature, the continuous current is 46A.
The continuous current data refer to standard atmosphere (1013 mbar 25 ° C) and
mounted to a heatsink with 5°C/W.
By forced cooling (forced ventilation with a fan or air flow), the allowable continuous
current can be increased.
5V power supply (Max 50mA) for Hall sensors and electronic throttle and electronic brake
pedal.
Two 0-5V analog inputs for throttle and brake function. One digital input for activating the
reverse function.
An additional analog input for motor temperature monitoring.
A RS232 interface for outputting the current measured values and changing of the
parameter of the controller. This can also be used for direct control without the analog
inputs.

Operational Manual Plettenberg Motor control MST-60-80 V5.1
S. 5

Operational Manual Plettenberg Motor control MST-60-80 V5.1
S. 6
4 Mounting and connection rules:
If the controller is mounted in a closed case, the warm air must be replaced accordingly or
cooled. At 80A phase current the dissipated heat is about 15W.
On the top are five terminals with M3 threat (Max. torque is 1.3Nm), three of them are for
the motor phase connections and two for battery plus and battery minus. There is also the
6 pole sensor connector and the 12 pole control connector on the top.
The motor phase A should be connected with the red motor phase at Plettenberg motors.
The motor phase B should be connected with the white motor phase at Plettenberg motors.
The motor phase C should be connected with the blue motor phase at Plettenberg motors.
Caution: The sum of all battery cables (plus and minus) should be less than 1m. If several
batteries are connected in series, the length of the connecting cables between the battery
packs must be added to the battery cable length. For example, if you use 33cm battery
cables length for the MST60-80 you have 100cm – 2 x 33cm = 34cm total cable length left
for the battery pack. The allowed cable length depends also on the current, so if you are
using the controller at higher currents than the nominal current, the allowed cable length is
shorter. At 140A full throttle current the allowed cable length is 58cm, resulting in 29cm
plus and 29 cm minus total.
Warning: Exceeding the permissible length of the battery wiring, the motor controller may
be damaged. The motor controller is not protected against reverse polarity. If the battery is
reversed, the motor controller may be damaged. Use an appropriate fuse (eg Littelfuse
BF1 58V 100A 142.5631.6102, 142.7010.6102, MEGA-fuse 58V 100A) between the
battery pack and controller. As a safety disconnect switch (emergency stop) we
recommend Tyco Electronics KILOVAC EV100 and KILOVAC EV200 series.
A protective diode must be installed which, when the connection between the battery and
the control unit is interrupted, draws the stored energy from the motor inductivity into the
battery if current flows through the motor. The protective diode must be installed in parallel
with the serial circuit fuse and safety disconnect switch. Anode to plus motor controller and
cathode to battery plus. We recommend a VS-100BGQ100 or STPS80170CW diode to
archive the best protection.
Warning: Never operate the controller with significant load on a power supply without
permission from us. At partial throttle the input current of the controller could have high
current spikes, which could cause overvoltage spikes, if using a power supply instead of a
battery. These spikes can destroy the motor controller and/or the power supply. Never use
the brake function, if using a power supply. At braking the energy is feed back to the power
supply, the resulting overvoltage may destroy the power supply and/or the controller.
Reversing the direction: If you want to reverse the direction of rotation, swap the sensor
cable A and B and the motor phases B with C.
Please note that the possible cable length of the RS232 cable depends on the used line
driver and the used cable. At cable length over 2m we recommend a shielded CAT5 cable
for the RS232 connection.

Operational Manual Plettenberg Motor control MST-60-80 V5.1
S. 7
5 connectors and pin assignment:
Please read the assembly instructions of the Harwin Datamate J-Tek series carefully:
https://cdn.harwin.com/pdfs/C005XX_M80_and_M83_Datamate_Series_Connectors.pdf
We recommend the crimp tool M22520/2-01 selector setting 6 with the positioner
T5747/K1419.
Row1 uneven pin numbers, row2 even pin numbers
Sensor connector Harwin 6-pole: M80-5100642 / M80-4610642
Pin assignment hall sensor and motor temperature sensor:
Pin1: Sensor-C green
Pin2: +5V (20mA) red
Pin3: Sensor-B white
Pin4: GND black
Pin5: Sensor-A yellow/orange
Pin6: NTC (47k) blue
The sensor cable shield should be connected with sensor GND(pin4). Do not connect the
sensor cable shield with the motor case and/or with the motor controller case.
Control connector Harwin 12-pole: M80-5101242 / M80-4611242
Pin1: Brake input (aux), analog input 0-5V
Pin2: Throttle input, analog input 0-5V
Pin3: RxD
Pin4: NC do not connect
Pin5: TxD
Pin6: Impulse input, 5V Digital input
Pin7: reverse switch (0V forward, 5V reverse)
Pin8: +5V (30mA) Potentiometer supply
Pin9: GND
Pin10: CAN-H
Pin11: CAN-L
Pin12: Digital output(max. 60V/2A) or controller power supply(only as option!)
The shield of the RS232 cable should be connected with pin9 GND. Do not connect the
shield with the motor case and/or with the motor controller case. Connect the shield only
on one side of the cable.
6 Trouble free and safe operation:
The sum of all battery cable (plus and minus together) may not exceed 1m. Warning:
Exceeding the length of the battery wiring, the motor controller may be damaged.
The motor controller is not protected against reverse polarity. Warning: If the battery is
connected in reverse, the motor controller may be damaged. Use in the battery pack an
appropriate fuse (eg Littelfuse BF1 58V 100A 142.5631.6102, 142.7010.6102, MEGA-fuse
58V 100A).
The 5V power supply can deliver a maximum of 50mA. If the Hall sensors of the motor
need in total of 20mA, 30mA are left for accelerator and brake pedals are available.
Therefore check the power consumption of these components.

Operational Manual Plettenberg Motor control MST-60-80 V5.1
S. 8
Warning: Even a short-term short-circuit on the 5V supply at the control connector leads
to the failure of the power supply of the Hall sensors. This can cause a defect at the motor
controller if the engine is running.
7 Safety functions :
Over voltage protection: At over 63V input voltage the MST controller switches off. If the
input voltage rises over 66V the controller can be damaged.
Under voltage protection: Below 10V input voltage the MST controller switches of to
protect the internal power supply voltages.
Motor temperature protection: If the motor temperature is exceed the motor temperature
limit the MST controller switches off to protect the motor.
Controller temperature protection: If the controller temperature is exceed the controller
temperature limit the MST controller switches off to protect the motor.
High pedal protection: To avoid that the controller went to full throttle in case the minus
wire to the throttle potentiometer is broken, the MST controller switches off, if the voltage
at the analog input exceed 4.95V for safety.
Sensor error: If the positions sensors gives faulty signals the MST controller switches of
to protect the motor and the controller.

Operational Manual Plettenberg Motor control MST-60-80 V5.1
S. 9
8 Safety notes :
Over 60V battery voltage you leave the range of the Safety Extra Low Voltage! The
wiring must be carried out at supply voltages above 60V only by qualified persons.
It must be considered the relevant technical standards. Touching the motor
terminals with the engine running with more than 60V battery voltage can cause
injuries. Therefore, the wiring has to be made at battery voltages over 60V that no
power contacts can be touched.
Be careful with motors driving rotating parts.
If drive battery pack is connected, never stand in the hazard area of the rotating parts!
Technical defects in electrical and mechanical systems can lead to an unexpected start of
the motor and / or loose parts can greatly hurt you or persons located nearby! Only use
the controller when property and personal damages are excluded! We are not
responsible for the use in passenger-carrying equipment (see section 16 Legal Terms and
Conditions)!
The controller is not protected against reverse polarity and confusion.
Never mix up with PLUS MINUS (reverse polarity)! This results in damage to the
controller!
Never connect the drive battery on the motor connecting cable (confusion), this can
lead to irreparable damage!
Never operate the controller with significant load on a power supply without
permission from us. At partial throttle the input current of the controller could have
high current spikes, which could cause overvoltage spikes, if using a power supply
instead of a battery. These spikes can destroy the motor controller and/or the power
supply. Never operate the controller with a power supply, when using the braking
function. At braking the energy is feed back to the power supply, the resulting
overvoltage may destroy the power supply and/or the controller.
Do not connect an external voltage source at the 5V sensor supply. Exceeding 5.5V on
this connection may cause damage to the controller.
Never disconnect the drive battery with the engine running from the controller. This may
damage the controller. If you have activated the safety disconnect switch (emergency
stop) with the engine running, so a test run of the controller with a current-limited power
supply without load is necessary. Only if it is ensured that the controller is without damage,
the controller can be put into operation again.
Never disconnect the drive battery with the engine running from the controller. This
may damage the controller. If you have activated the safety disconnect switch (emergency
stop) with the engine running, so a test run of the controller with a current-limited power
supply is necessary. Only if it is ensured that the controller is without damage, the
controller can be put into operation again.
Never exceed the maximum length of the cables between the controller and battery
(max. length 2x50 cm). The internal battery wiring must be as short as possible.
Always disconnect the drive battery from the controller, if you do not use this
longer period or if you want to charge the battery.
The monitoring functions can’t detect every possible abnormal operating condition. The

Operational Manual Plettenberg Motor control MST-60-80 V5.1
S. 10
current limit does not protect the controller against short circuit between the motor cables.
In case of a short circuit immediately switch off the motor to avoid permanent damage to
the motor controller!
Also a current limitation at stalled motor will protect the motor only if the maximum allowed
current of the motor is higher than the current limitation value of the controller. For
example, if a 20A rated motor operated at the MST60-80, the current monitoring in the
case of blocking will not detect an excessive current and the motor may be destroyed.

Operational Manual Plettenberg Motor control MST-60-80 V5.1
S. 11
9 Initial operation of the drive system:
For the first test of the wiring of the drive system, we recommend to use a current limited
power supply. A power supply with an output voltage of 12V will do the job. At the first time
please use only low throttle, if the motor is running rough or only vibrates, put the throttle
back to zero and disconnect the battery cables.
Please check in this case the connection between the controller and the motor. There exist
only 6 combinations to connect the motor phases:
After the MST controller is connected to the battery voltage the controller send on the
RS232-Interface a small short instruction including the actual control parameters:
* Kommandoliste:
* 's' Serieller Sollwert
* 'p' Poti Sollwert
* 'i' Impuls Sollwert
* 'f' Forward
* 'r' Reverse
* '0' Off
* 'b' Brake
* 'm' 100% PWM(max)
* '9' 90% PWM
* '8' 80% PWM
* '7' 70% PWM
* '6' 60% PWM
* '5' 50% PWM
* '4' 40% PWM
* '3' 30% PWM
* '2' 20% PWM
* '1' 10% PWM
* '+' +1% PWM
* '-' -1% PWM
* 'g'+0.1% PWM
* 'l'-0.1% PWM
* 'w' write setup
* 'h' Help
MST60-80
Input = Analog
AnalogStop/Start/Full/BrakeMax = 500mV/ 549mV/4499mV/4499mV
Controller Phase A
Controller Phase B
Controller Phase C
Motor Phase A
Motor Phase B
Motor Phase C
Motor Phase A
Motor Phase B
Motor Phase C
Motor Phase B
Motor Phase A
Motor Phase A
Motor Phase C
Motor Phase C
Motor Phase B
Motor Phase C
Motor Phase C
Motor Phase B
Motor Phase B
Motor Phase A
Motor Phase A

Operational Manual Plettenberg Motor control MST-60-80 V5.1
S. 12
ImpulsStop/Start/Full = 1150µs/1200µs/1900µs
For. Throttle Inc/Dec = 328 / 328
For. Throttle Max/Min = 100% / 3%
Rev. Throttle Inc/Dec = 66 / 328
Rev. Throttle Max/Min = 100% / 3%
Brake Inc/Dec = 66 / 328
Brake Max/Min = 100% / 5%
Voltage Max/Min = 60.0V/ 10.0V
Phase/BatteryAmp Max = 120.0A/120.0A
Temp Max Motor/Power = 100°C / 110°C
Motor RPM Limit = 240000
Motor Polepairs = 1
10 LED indicator functions:
LED continuous light : No error
LED 1x Blinking : Error 0x0001 under voltage
LED 2x Blinking : Error 0x0002 over voltage
LED 3x Blinking : Error 0x0004 over current
LED 4x Blinking : Error 0x0008 over temperature controller
LED 5x Blinking : Error 0x0010 over temperature motor
LED 6x Blinking : Error 0x0020 Motor blocked
LED 7x Blinking : Error 0x0040 Sensor error
LED 9x Blinking : Error 0x0100 Error Analog input(voltage too high)
LED 10x Blinking : Error 0x0200 Error Impulse width

Operational Manual Plettenberg Motor control MST-60-80 V5.1
S. 13
11 Standard Setup Values:
Input = Analog
AnalogStop/Start/Full/BrakeMax = 500mV/ 549mV/4499mV/4499mV
Impuls Stop/Start/Full = 1150µs/1200µs/1900µs
For. Throttle Inc/Dec = 328 / 328
For. Throttle Max/Min = 100% / 3%
Rev. Throttle Inc/Dec = 66 / 328
Rev. Throttle Max/Min = 100% / 3%
Brake Inc/Dec = 66 / 328
Brake Max/Min = 100% / 5%
Voltage Max/Min = 60.0V/ 10.0V
Phase/BatteryAmp Max = 120.0A/120.0A
Temp Max Motor/Power = 100°C / 110°C
Motor RPM Limit = 240000
Motor Polepairs = 1
12 RS232-Interface-Parameters :
115kbaud 8 Databits, no parity, 1 Stopbit.
13 RS232-Interface-Protocol-Description:
Data on the RS232 interface in analog mode:
T=3.649V,a=0.000V,PWM= 787,U= 34.9V,I= 3.7A,RPM= 1482,con= 28°C,mot= 26°C
T=4.964V,a=0.000V,PWM=1000,U= 35.0V,I= 4.0A,RPM= 1896,con= 28°C,mot= 26°C
„T“ means Throttle input, the big letter shows that it is active.
„a“ means Aux input (Brake), the small letter shows that the brake is inactive at the
moment as the throttle input has priority over the brake input.
„U“ is the Input voltage
„I“ is the Phase current (no average function and no synchronization with the commutation)
„RPM“ is the motor speed in rpm
„con“ is the power stage temperature
„mot“ is the motor temperature
If the brake is active the “a“ change to “A“ and the “T“ changes to “t“:
t=0.000V,A=2.501V,PWM= 500,U= 35.0V,I= 0.0A,RPM= 0,con= 28°C,mot= 26°C
The Data on the RS232 interface in serial mode:
S=3.649V,a=0.000V,PWM= 787,U= 34.9V,I= 3.7A,RPM= 1482,con= 28°C,mot= 26°C
„S“ shows that the serial control mode is active.

Operational Manual Plettenberg Motor control MST-60-80 V5.1
S. 14
14 RS232-Interface-Commands :
1 Byte Commands:
"s": switch to serial RS232 Input
"p": switch to analog input(Poti)
"i" : switch to impulse input(compatible with model radio control)
"f": forward
"r": reverse
"0": Motor off
"b": Brake
"m": 100% PWM(maximum)
"9": 90% PWM
"8": 80% PWM
"7": 70% PWM
"6": 60% PWM
"5": 50% PWM
"4": 40% PWM
"3": 30% PWM
"2": 20% PWM
"1": 10% PWM
"+": +1% PWM
"-": -1% PWM
"g": +0,1% PWM(V2 or higher)
"l": -0,1% PWM(V2 or higher)
"t" : activate 2s Timeout at the serial Interface(V2 or higher)
"h": help
"a": switch to adjust Mode
"e": exit adjust Mode
2 Byte Commands:
"sd": set default
"sp": show parameter
"wp": write parms
"se": show the last 8 errors

Operational Manual Plettenberg Motor control MST-60-80 V5.1
S. 15
5 Byte Commands(only in Adjust Mode)
"rp": RPM limit[1000RPM] "rp100" = 100000U/min
"cl": current limit[A] "cl100" = 100A
"il": input current limit[A] "cl100" = 100A(V5 or higher)
"uv": under voltage [V] "uv020" = 20V
"ov": over voltage[V] "ov100" = 100V
"mt": motor temperature limit [°C] "mt100" = 100°C(V3 or higher)
"ct": controller temperature limit [°C] "ct110" = 110°C(V3 or higher)
"ti": throttle increase forward "ti001" = +1count/ms "ti010" = +10count/ms
"td": throttle decrease forward "td001" = -1count/ms "td010" = -10count/ms
"tl": throttle limit forward in % "tl100" = 100% "tl050" = 50%
"tm": throttle minimum forward in % "tm010" = 10% "tm050" = 50%
"ri": reverse throttle increase "ri001" = +1count/ms "ri010" = +10count/ms
"rd": reverse throttle decrease "rd001" = -1count/ms "rd010" = -10count/ms
"rl": reverse throttle limit in % "rl100" = 100% "rl050" = 50%
"rm": reverse throttle minimum in % "rm010" = 10% "rm050" = 50%
"bi": brake increase "bi001" = +1count/ms "bi010" = +10count/ms
"bd": brake decrease "bd001" = -1count/ms "bd010" = -10count/ms
"bl": brake limit [%] "bl100" = 100% "bl050" = 50%
"bm": brake minimum [ %] "bm010" = 10% "bm050" = 50%
"af": analog input full throttle voltage "af500" = 5.00V
"ah": analog input halt motor voltage "ah050" = 0.50V
"as": analog input start motor voltage "as060" = 0.60V
"ab": analog input full brake voltage "ab500" = 5.00V(V5 or higher)
"if": impulse input full throttle "if200" = 2.0ms
"ih": impulse input halt motor "ih100" = 1.0ms
"is": impulse input start motor "is110" = 1.1ms
"pp": motor pole pairs count "pp001" = 2-Poles
"ot": output time RS232 [ms] "ot200" = 200ms ( minimum 7ms) (V4 or higher)
RS232 Command examples:
1. CR/LF is not necessary
2. After connecting the supply voltage to the MST60-80 controller the analog input is active
by default. If you want to use the serial control input, you have to send „s“ after the
initialization of the controller.
Examples:
If you want to run the motor forward with 10% throttle PWM you send „1f“.
If you want to increase the throttle PWM to 33% you send „3+++“.
If you want to increase to maximum throttle you send „m“.
If you want to switch off the motor current you send a „0“.
If you want to brake with 10% brake PWM you send a „1b“.
If you want to increase the brake PWM to 33% you send „3+++“.
If you want to run the motor with 8% throttle PWM you send „1--r“.
If you want to change a parameter you have to switch the MST into the adjust mode by
sending an „a“. That is only possible if the motor does not run.
For example if you want to change the pole pair count to 10 pole pairs(20 pole motor) that
the MST sending the shaft speed instead of the electrical speed on the RS232 interface
send an „a“ for adjust mode, after that you send „pp010“ for 10 pole pairs and „e“ for exit
adjust mode. If you want to store the changed parameter, you have to leave the adjust
mode by sending a “wp” instead of the “e”.

Operational Manual Plettenberg Motor control MST-60-80 V5.1
S. 16
15 Sensor Phase Mapping :
Commutation Sequence Forward
Step1
Step2
Step3
Step4
Step5
Step6
Error1
Error2
Phase A(U)
+ Z - - Z + Z Z
Phase B(V)
Z + + Z - - Z Z
Phase C(W)
- - Z + + Z Z Z
Sensor A 1 1 0 0 0 1 0 1
Sensor B 0 1 1 1 0 0 0 1
Sensor C 0 0 0 1 1 1 0 1
Commutation Sequence Reverse
Step1
Step2
Step3
Step4
Step5
Step6
Error1
Error2
Phase A(U)
- - Z + + Z Z Z
Phase B(V)
Z + + Z - - Z Z
Phase C(W)
+ Z - - Z + Z Z
Sensor A 1 1 0 0 0 1 0 1
Sensor B 0 0 0 1 1 1 0 1
Sensor C 0 1 1 1 0 0 0 1
Z: high impedance, +:plus, -:minus, 1:>3V, 0:<2V

Operational Manual Plettenberg Motor control MST-60-80 V5.1
S. 17
16 Rechtliches:
Es wird keine Haftung übernommen für Sach- und Vermögensschäden,
sowie Sach- und Vermögensfolgeschäden:
durch unsachgemäße Handhabung.
an sämtlichen Fluggeräten wie Ultraleichtflugzeugen, Drachen, Fallschirmen,
Flugmodellen, Raketen, Drohnen, Hängegleitern und Gleitseglern oder deren
Teilen, sowie Schäden durch Grounding von o.g. Fluggeräten .
an fremden Luftfahrzeugen oder Luftfahrzeugteilen
durch Anwendungen aller Art, die dem deutschen Kriegswaffengesetz
unterliegen.
Generell ausgeschlossen sind Vermögens- und Vermögensfolgeschäden.
Die Steuerung wurde nicht den für Flugzeugen vorgeschriebenen Sicherheits- und
Dauertests unterzogen. Es wird keinerlei Haftung übernommen für Personen- bzw.
Sachschäden, Sachfolge- und Vermögensschäden, sowie Vermögensfolgeschäden
beim und durch den Betrieb in manntragenden Fluggeräten!
Im Zweifel holen Sie bitte eine schriftliche Zustimmung für den Betrieb in Ihrer
speziellen Anwendung ein.
Grundsätzlich gelten unsere Allgemeinen Geschäftsbedingungen.
Table of contents
Popular Controllers manuals by other brands
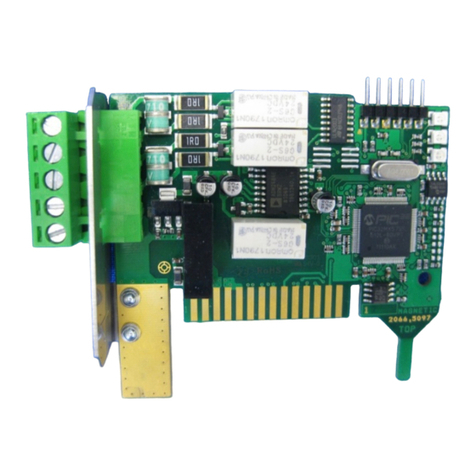
Magnetic Autocontrol
Magnetic Autocontrol MGC-PRO Technical manual
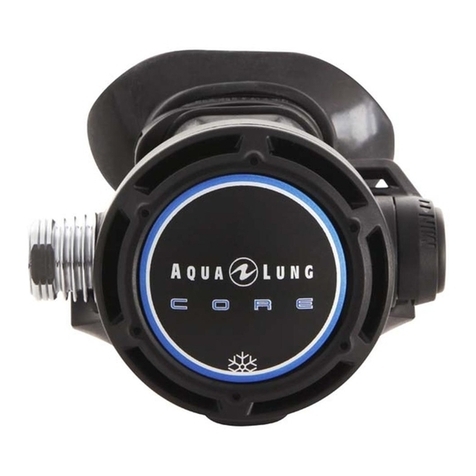
Aqua Lung
Aqua Lung CORE Service manual
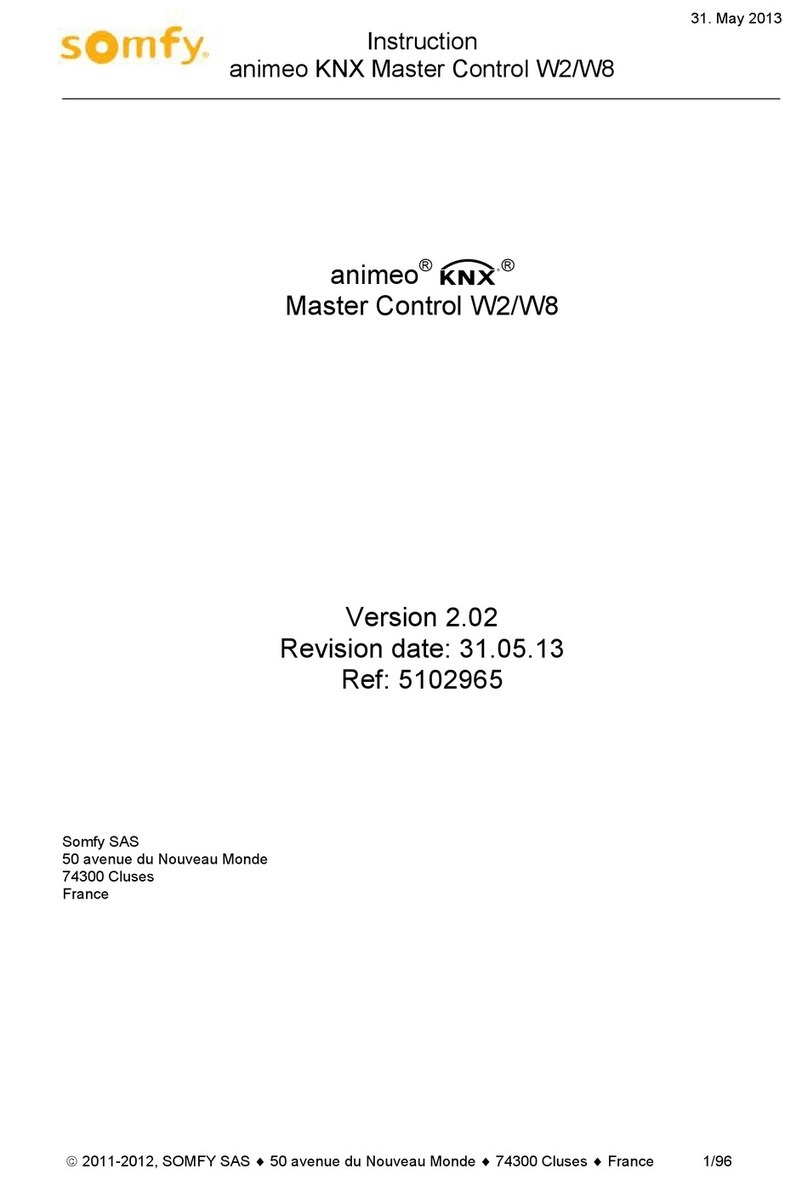
SOMFY
SOMFY animeo KNX Master Control W2 Instruction
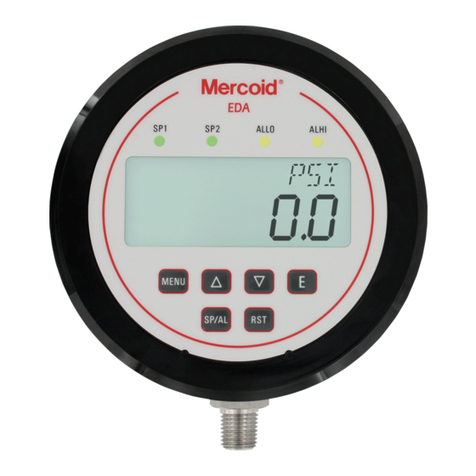
Mercoid
Mercoid EDA series Installation and operating instructions
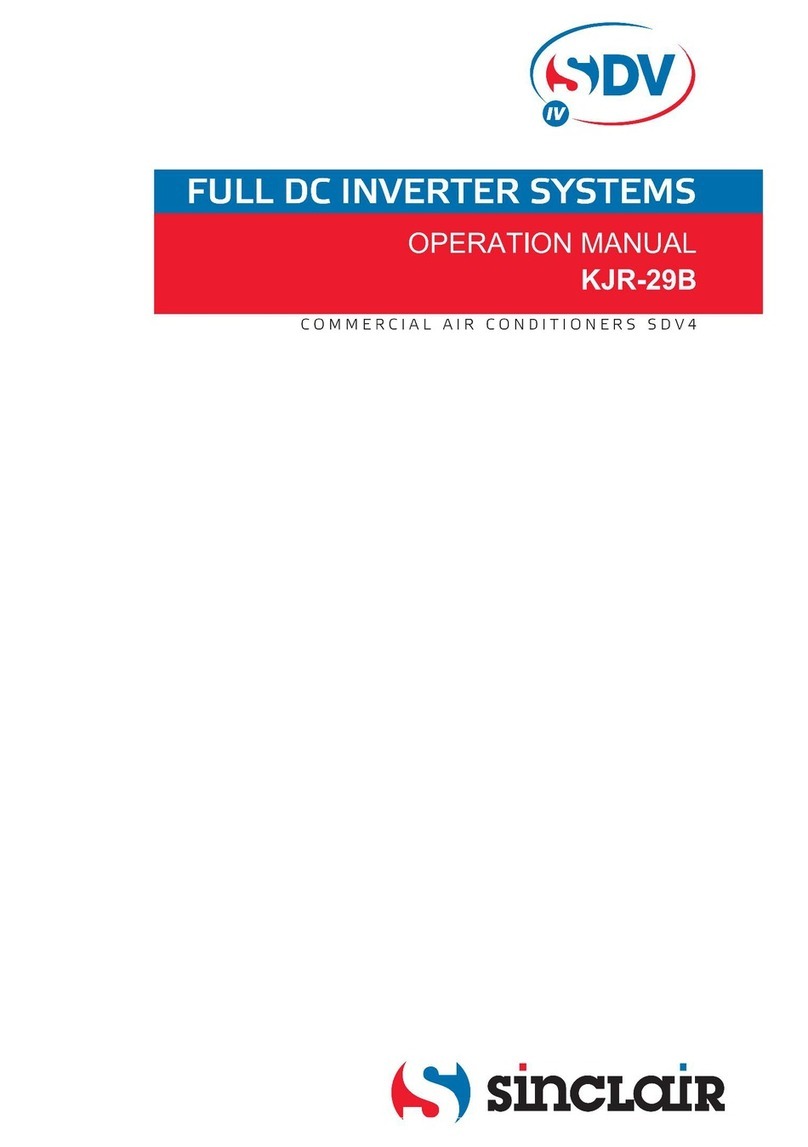
Sinclair
Sinclair KJR-29B Operation manual
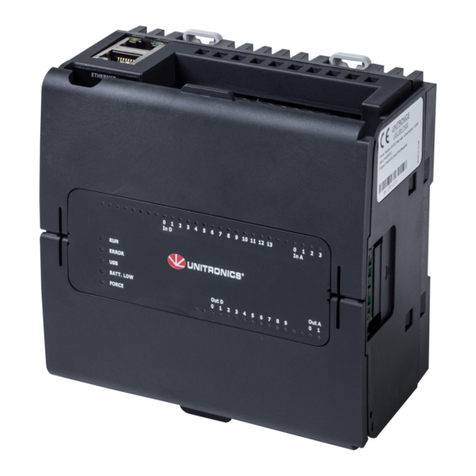
Unitronics
Unitronics UniStream PLC Series installation guide
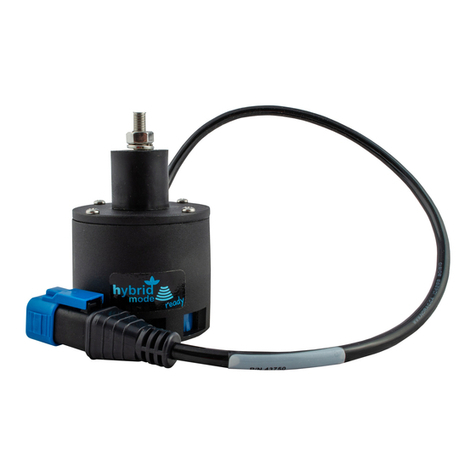
Norac
Norac UC5 Topcon X30 installation manual
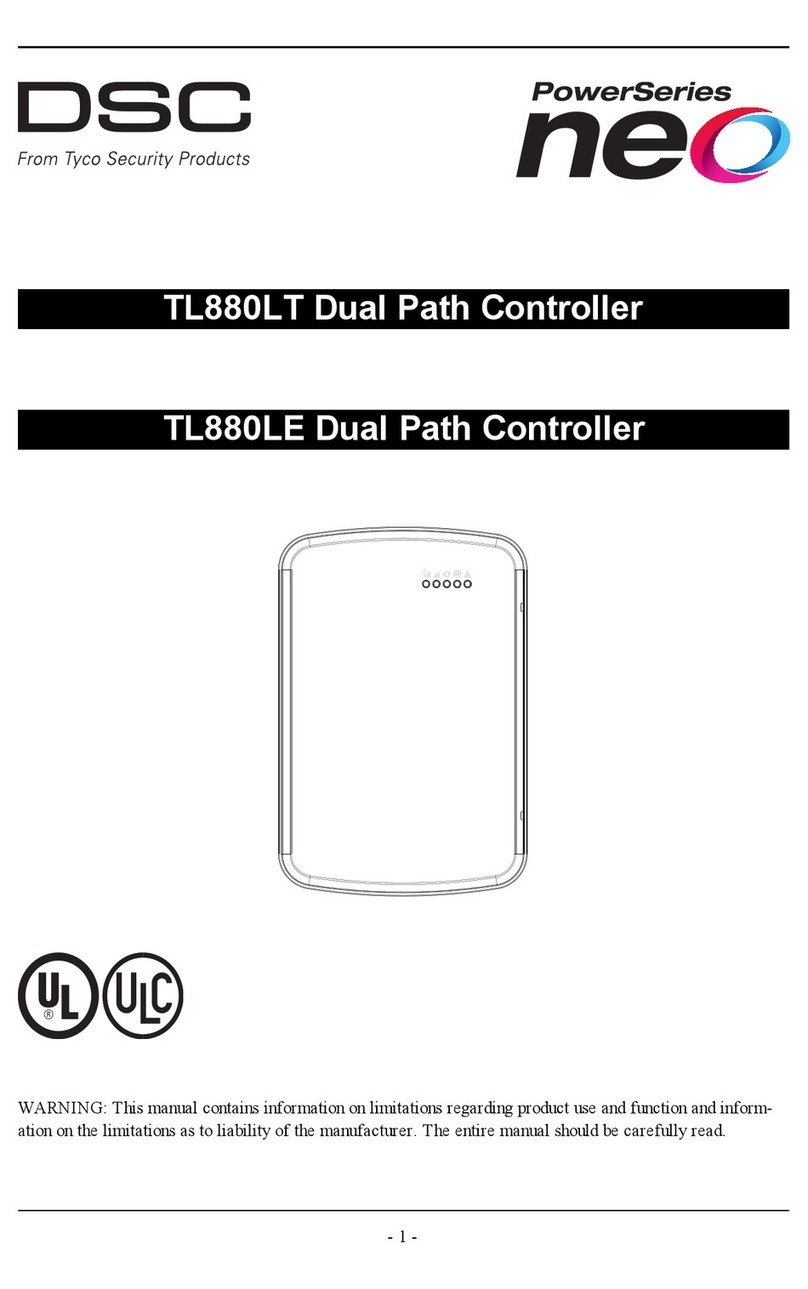
Tyco Security Products
Tyco Security Products DSC Neo Power Series manual
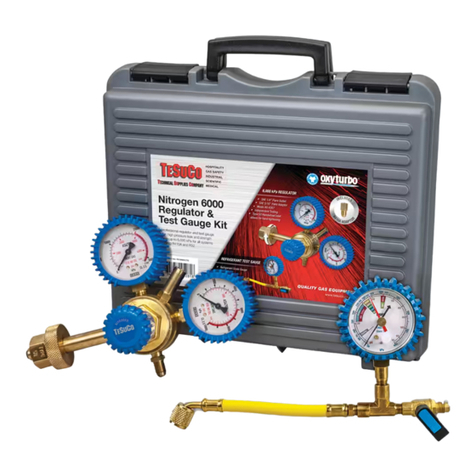
TeSuCo
TeSuCo Oxyturbo Nitrogen 6000 operating instructions
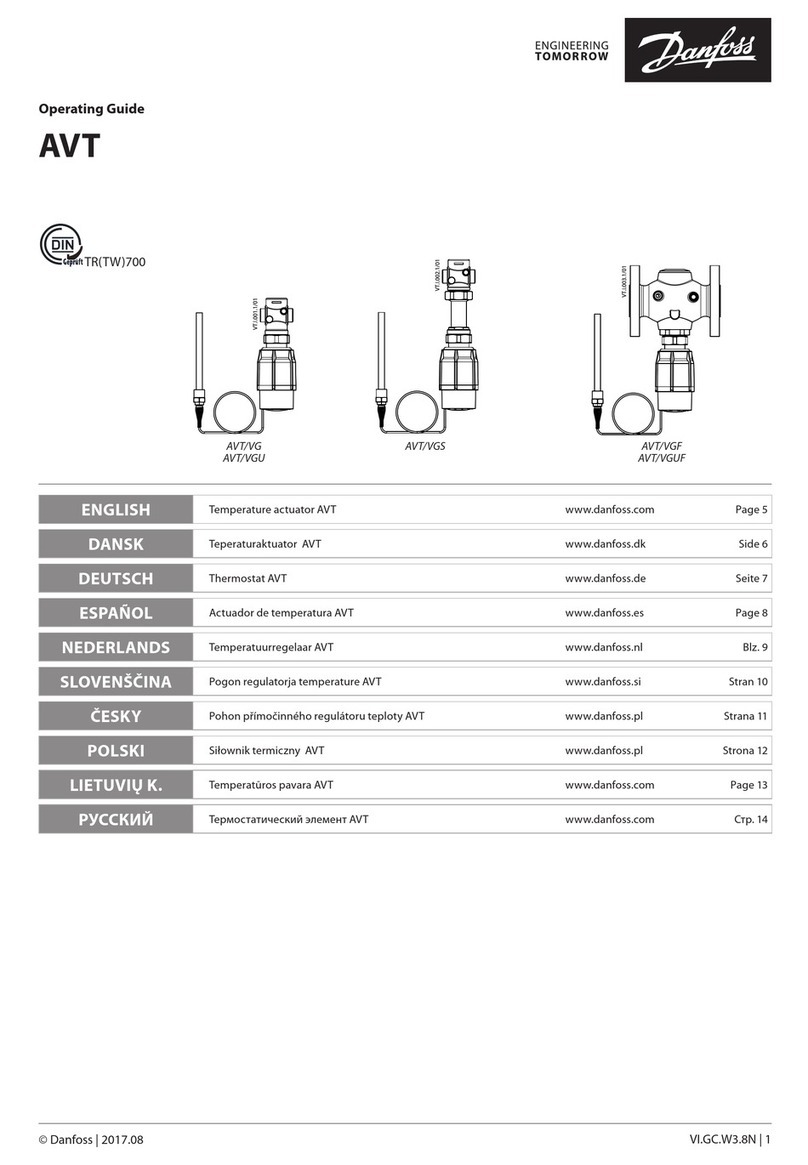
Danfoss
Danfoss AVT/VG operating guide
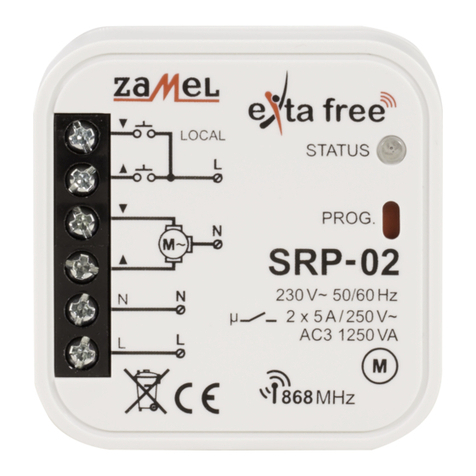
Zamel
Zamel RZB-03 instruction manual
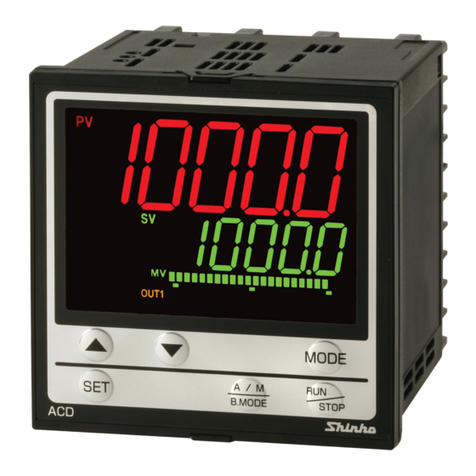
Shinko
Shinko ACD-13A Communication instruction manual