PMA KS 50-1 User manual

±Universal continuous/switching
version, i.e. reduced stocks
±100 ms cycle time, i.e. also
suitable for fast control loops
±Freely configurable analog
output, e.g. as process value
output
±Customer-specific linearization
for all sensors
±Settings can be blocked via
password and internal switch for
high security
±Extended temperature range up
to 60 °C allows mounting close to
the process
±Easy 2-point or offset
measurement correction
±Emergency operation after
sensor break by means of the
„output hold“ function
±Logical combination of digital
outputs, e.g. for general alarm
±Programmer with 10 segments,
bandwidth and „end“ signal
±RS 422/485 Modbus RTU
interface
±Built-in transmitter power supply
±Splash-water proof front (IP 65)
APPLICATIONS
ØFurnaces and ovens
ØBurners and boilers
ØPlastics processing
ØHot runners
ØDriers
ØClimatic chambers
ØHeat treatment plants
DESCRIPTION
The universal temperature controller
KS 50-1 is intended for universal,
precise, and cost-effective control tasks
in all branches of industry. For this, the
unit provides simple 2-point (on/off)
control, continuous PID control, or
3-point stepping control. The process
value signal is connected via a universal
input. A supplementary analog input can
be used for heating current
measurement or as an external set-point
input.
Every KS 50-1 has three process outputs
that can be 3 relays or 2 relays plus a
universal output. This universal output
can be used for operating a solid-state
relay, a continuous current/voltage
output or to energize a two-wire
transmitter. Optionally there are two
additional opto coupler outputs.
The selectable function „start-up“
ensure increased lifetime of
high-performance electrical heating
elements (e.g. hot runner moulds).
Plug-in module
KS 50-1 controllers are built as plug-in
modules. This enables them to be
replaced very quickly without tools, and
without disturbing the wiring.
Self-tuning during start-up and to the
setpoint
This new function determines the
optimum settings for fast line-out
without overshoot. With three-point
controller configuration, the „cooling“
parameters are determined separately,
thus ensuring an optimum match to the
process. By pushing a button the
KS 50-1 determines the best control
parameters at the actual setpoint. This
function does not require oscillation, and
performs a minimal deviation of the
process value.
Display and operation
Clear information are given by ten
indicator LEDs in the front panel that
display operating mode, I/O states, and
errors. The Ò-key switches the
controller into the manual mode directly.
If required, the direct switch over can be
disabled or the key can be configured
e.g. reset the latched alarms. By the
flexibly applicable function key an
external switch can be omitted in many
cases, because one can start now e.g.
the boost function directly.
Front interface and Engineering Tools
Control parameter adjustment in
seconds has now also been
implemented in the KS 50 class of
instruments. Via the BlueControl
software incl. its simulation functions,
and especially the convenient BluePort®
front panel interface, the required set-up
KS 50-1
Universal Industrial Controller
BluePort®Front interface and BlueControl software
Maintenance manager and error list
Start-up circuit and boost function
Manual gain scheduling
Self-Tuning to the setpoint without oscillation
Monitoring of heating current and output circuit
3-point controller for water, fan and oil cooling
universal line

for a specific control task can be
determined without a detailed study of
the operating instructions.
Off cause almost all adjustments can be
done comfortably over the instrument
front. (see page 7, BlueControl)
Password protection
If required, access to the various
operating levels can be protected with a
password. Similarly, access to a
complete level can be blocked.
TECHNICAL DATA
INPUTS
SURVEY OF THE INPUTS
Input Used for:
INP1 x (process value)
INP2 Heating current, ext. set-point
di1 Operation disabled, switch-over
to second set-point SP.2,
external set-point SP.E, fixed
correcting variable Y2, manual
operation, controller off, disable
auto/manual function, reset of
stored alarms, boost, parameter
set 1 ↔2
di2 (option)
di3 (option)
PROCESS VALUE INPUT INP1
Resolution: > 14 bit
Decimal point: 0 to 3 decimals
Limiting frequency: 2 Hz
Digital input filter: adjustable 0,000...9999 s
Scanning cycle: 100 ms
Measured value
correction: 2-point or offset correction
Thermocouples (Table 1)
Input impedance: ≥1M
Ω
Effect of source resistance: 1µV/Ω
Cold junction compensation
Max. additional error ±0,5 K
Sensor break monitoring
Sensor current: ≤1µA
Operating sense configurable (see page 4)
Resistance thermometer
Connection: 3-wire
Lead resistance: max. 30 Ω
Input circuit monitor: Break and short circuit
Resistance measuring range
The BlueControl software can be used to
match the input to the sensor KTY 11-6
(characteristic is stored in the controller).
Physical measuring range: 0...4500 Ω
Linearization segments 16
2 KS 50-1
96 (3.78”)
48 (1.89”)
min.48 (1.89’’)
10
(0.4”)
1...10
0.04-0.4”
118 (4.65”)
45 +0,6
(1.77” )
+0 .02
125
126
SP.X run
Err
Ada
92 +0,8
(3.62’’
)
+0 .03
KS 50-1 universal
Dimensions (mm):
U
Logic
di2
di3
UT
Option
RXD-B
GND
RXD-A
TXD-B
TXD-A
RS485 RS422
Modbus RTU
RGND
DATA B
DATA A
L
N
90...250V
24V AC/DC
+24V DC
24V GND
mA
mA
0..10 V*
HC
di1
INP1
INP2
OUT3
OUT2
OUT1
1
2
3
4
7
5
8
6
9
10
11
12
13
14
15
1
3
4
5
6
7
8
9
10
11
12
13
14
15
17
(2)
(16)
OUT5
OUT6
Electrical connections:
* Pay attention to the internal switch!
Safety isolation
Functional isolation
Mains supply
Process value input INP1
Supplementary input INP2
Digital input di1
Relay outputs OUT1,2 RS 422/485 interface
Relay output OUT3 Digital inputs di2, 3
Universal output OUT3
Transmitter supply UT
OUT5, OUT6
Galvanic isolations:
Thermocouple Range Accuracy Resolution (∅)
L Fe-CuNi (DIN) -100...900 °C -148...1652 °F ≤2 K 0,1 K
J Fe-CuNi -100...1200 °C -148...2192 °F ≤2 K 0,1 K
K NiCr-Ni -100...1350 °C -148...2462 °F ≤2 K 0,2 K
N Nicrosil/Nisil -100...1300 °C -148...2372 °F ≤2 K 0,2 K
S PtRh-Pt 10% 0...1760 °C 32...3200 °F ≤2 K 0,2 K
R PtRh-Pt 13% 0...1760 °C 32...3200 °F ≤2 K 0,2 K
special -25 ...75 mV ≤0,1 % 0,01 %
Table 1 Thermocouple ranges
Type Sensor current Range Accuracy Resolution (∅)
Pt100
0,2 mA
-200...850 °C -328...1562 °F ≤1 K 0,1 K
Pt1000 -200...200 °C -328...392 °F ≤2 K 0,1 K
Resistance*4500 Ω≤0,1 % 0,01 %
* The characteristic of a KTY 11-6 is preadjusted (-50...150°C)
Table 2 Resistance transducers
Range Input resistance Accuracy Resolution (∅)
0-10 Volt ≈110 kΩ≤0,1 % 0,6 mV
0-20 mA 49 Ω(voltage requirement ≤2,5 V) ≤0,1 % 1,5 µA
Table 3 Current and voltage

Current and voltage signals
Span start, end of span: anywhere within
measuring range
Scaling: selectable -1999...9999
Linearization: 16 segments, adaptable
with BlueControl
Decimal point: adjustable
Input circuit monitor: 12,5% below span start
(2mA, 1V)
SUPPLEMENTARY INPUT INP2
Resolution: > 14 bit
Scanning cycle: 100 ms
Accuracy: better 0,1 %
Heating current measurement
via current transformer
Measuring range: 0...50 mA AC
Scaling: adjustable -1999..0,000..9999 A
Current measurement range
Input resistance approx. 120 Ω
Span: configurable within
0 to 20mA
Scaling: adjustable -1999...9999
Input circuit monitor: 12,5% below span start
(4..20mA →2mA)
CONTROL INPUT DI1
Configurable as direct or invers switch or
push-button !
Connection of a potential-free contact
suitable for switching „dry“ circuits.
Switched voltage: 2,5 V
Switched current: 50 µA
CONTROL INPUTS DI2, DI3
(OPTION)
Configurable as switch or push-button !
Optocoupler input for active triggering
Nominal voltage: 24 V DC, external
Current sink (IEC 1131 Type 1)
Logic „0": -3...5 V
Logic „1": 15...30 V
Current requirement: approx. 5 mA
TRANSMITTER SUPPLY UT(OPTION)
Output: 22 mA / ≥18 V
If the universal output OUT3 is used
there may be no external galvanic
connection between measuring and
output circuits!
OUTPUTS
SURVEY OF THE OUTPUTS
Output Used for
OUT1
OUT2
(relay)
Control output
heating/cooling or
Open/Close, limit contacts,
alarms, programmer end *
OUT3
(Relay or logic) as OUT1 and OUT2
OUT3
(continuous)
Control output, process
value, set-point, control
deviation, transmitter
supply 13V/22mA
OUT5
OUT6
(Optocoupler) as OUT1 and OUT2
OPTION
* All logic signals can be OR-linked !
RELAY OUTPUTS OUT1, OUT2
Contacts: 2 NO contacts with
common connection
Max. contact rating: 500 VA, 250 VAC, 2A at
48...62 Hz, resistive load
Min. contact rating: 6 V, 1 mA DC
Operating life (electric): 800.000 duty cycles
with max. rating
OUT3 USED AS RELAY OUTPUT
Contacts: Potential-free
changeover contact
Max. contact rating: 500 VA, 250 VAC, 2A at
48...62 Hz, resistive
load
Min. contact rating: 5 V, 10 mA AC/DC
Operating life (electric): 600.000 duty cycles
with max. rating
Note:
If the relays OUT1...OUT3 operate
external contactors, these must be fitted
with RC snubber circuits to
manufacturer specifications to prevent
excessive switch-off voltage peaks.
OUT3 AS UNIVERSAL OUTPUT
Galvanically isolated from the inputs.
Freely scalable
DA-converter limiting frequency T90:50ms
Limiting frequency of the complete
continuous controller: > 2 Hz
Resolution: 11 bits
Current output
0/4...20 mA, configurable.
Signal range: 0...approx. 21,5 mA
Load: ≤500 Ω
Load effect: 0,02%/100Ω
Resolution: ≤22 µA (0,1%)
Error: ≤40 µA (0,2%)
Voltage output
0/2...10V, configurable
Signal range: 0...11 V
Load: ≥2k
Ω
Load effect: no effect
Resolution: ≤11 mV (0,1%)
Error: ≤20 mV (0,2%)
OUT3 used as transmitter supply
Output: 22 mA / ≥13 V
OUT3 used as logic output
Load ≤500 Ω0/≤20 mA
Load > 500 Ω0/> 13 V
OUTPUTS OUT5, OUT6 (OPTIONAL)
Galvanically isolated opto-coupler outputs.
Grounded load:
common positive control voltage.
Output rating: 18...32 VDC; =70 mA
Internal voltage drop: =1 V with I max
Protective circuit: built-in against short
circuit, overload, reversed polarity
(free-wheel diode for relay loads).
KS 50-1 3

4 KS 50-1
FUNCTIONS
Control behaviour
•Signaler with asymmetric adjustable
switching differential (ON/OFF
controller)
•PID controller (2-point and
continuous)
•Delta / Star / Off or 2-point controller
with switch over from partial to full load
•2 x PID (heating/cooling)
•3-point stepping controller
Two parameter sets for manual gain
scheduling
Self-tuning control parameters or
adjustable manually via front keys or
BlueControl software.
Behaviour with 2- and 3-point controllers
•Standard behaviour:
For precise matching of the required
output value at the output signal
limits, the controller changes the
cycle times for heating and cooling
automatically and continuously.
•With constant cycle times:
The length of the shortest heating
and cooling pulse is adjustable.
•Water cooling linear
(heating=standard):
To ensure a sufficient cooling effect,
the cooling function starts only after
reaching an adjustable temperature
value. The pulse length is adjustable,
too and remains constant for all
output values.
•Water cooling nonlinear
(heating=standard):
The general function is described
above but the controller additionally
takes in consideration that the water
cooling is usually much stronger than
the heating (thus preventing
unfavorable behavior when changing
from heating to cooling).
Set-point functions
•Adjustable set-point gradient
0,01...9999 °C/min
•Set-point control
•Set-point/cascade control
•Program controller with 10 segments
(set-point/section time)
Behaviour with sensor break
or short circuit:
•Control outputs switched off
•Switch-over to a safe output value
•Switch-over to a mean output value
(PID controller)
SP
setpoint
power-on disturbance
t
SP.St
process value Start-up circuit
When the process is controlled towards
the start-up set-point, the output value is
limited. The start-up set-point is kept
constant during the start-up holding
time. After that, the main setpoint SP is
controlled. If a disturbance reduced the
process value, the start-up circuit is
activated again.
185°C
190°C
+5°C
190°C
195°C
195°C
200°C
200°C
205°C
200°C
205°C
210°C
215°C
215°C
220°C
Master
KS 50-1
Sl
aves
KS 90-1, KS 50-1, KS 40-1
KS 40-1 universal
123OK
SP.x run
Err
Ada
126
125
KS 40-1 universal
123OK
SP.x run
Err
Ada
126
125
KS 40-1 universal
123OK
SP.x run
Err
Ada
126
125
KS 40-1 universal
123OK
SP.x run
Err
Ada
126
125
KS 40-1 universal
123OK
SP.x run
Err
Ada
126
125
KS 40-1 universal
123OK
SP.x run
Err
Ada
126
125
KS 40-1 universal
123OK
SP.x run
Err
Ada
126
125
180°C
KS 50-1 universal
123OK
125
126
SP.x run
Err
Ada
F
Modbus Master function supports setpoint changes e.g. in extruder applications
or
or
or
OUT1
OUT2
OUT3
INP1
di1
INP2
di2
di3
HCA
y1
FAi.1
FAi.2
LP.AL
y2
HC.AL
LrES
HC.SC
man
C.off
Y.2
L_r mLoc
yPID
xw
Ò
Ì
weff
xeff
8888
run
time
(Y2/SP2)
PEnd
SP.2
ÈÌ
SP.E
SP.2
ÈÌ
#
SP.E
OUT6
OUT5
OUT1
Example of the linkage of the internal functions:
setpoint processing with programmer, boost function and start-up circuit
controller function with loop monitoring
limit monitoring, configurable with latch and suppression
heating current monitoring
output processing with logic or-combination and inverting
analog inputs with logical sensor fail signal
digital inputs, function key and Ò-key with lock function

SPECIAL FUNCTIONS
Boost-Function
The boost function provides a short-term
increase of the set-point, e.g. with hot
runner control, in order to clear nozzles
of “frozen” rests of material.
Start-up circuit
For temperature control, e.g. with hot
runners. High-performance heating
elements with magnesium oxide
insulation must be heated slowly, to
remove any humidity and to prevent
destruction.
Modbus Master
The KS 90-1 can be configured as
Modbus Master. This enables it to
transmit user-specified signals or
parameters cyclically to all connected
Slave controllers. For example, the
following applications are possible:
•Set-point shifting relative to the
set-point adjusted in the Slave (see
picture)
•matching of control parameters, limit
contacts, etc.
•Limiting the output value (override
control OVC)
•...
LIMIT SIGNALLING FUNCTIONS
Max., Min. or Max./Min. monitoring with
adjustable hysteresis.
Signals which can be monitored:
•Process value
•Control deviation
•Control deviation with suppression
during start-up or set-point changes
•Effective set-point
•Output signal Y
•Control deviation always compared to
internal setpoint SP even if SP2 or
SP.E is activated.
Functions
•Input signal monitoring
•Input signal monitoring with latch
(reset via front key or digital input)
•Adjustable discriminator time of
0...9999 seconds
Several limit signals or alarms can be
OR-linked before being output.
Applications: Release of a brake with
motor actuators, general alarms, etc.
ALARMS
Heating current alarm
•Overload and short circuit
•Open circuit and short circuit
Limit value adjustable 0...9999 A
Control loop alarm
Automatic detection if there is no
response of the process to a change of
output value.
Sensor break or short circuit
Depending on selected input type, the
input signal is monitored for break and
short circuit.
MAINTENANCE MANAGER
Display of error signals, warnings, and
latched limit messages in the error list.
Signals are latched, and can be reset
manually.
Possible signals in the error list:
Sensor break, short circuit, reversed polarity
Heating current alarm
Control loop alarm
Fault during self-tuning
latched limit messages
e.g. re-calibration warning
(If the adjusted operating hours are exceeded a
message is displayed)
e.g. maintenance interval of actuator
(If the adjusted switching cycles are exceeded a
message is displayed)
Internal fault (RAM, EEPROM, ...)
OPERATION AND DISPLAY
Display
Process value: LED with 7 segments, 10,5 mm
Lower display: LED with 7 segments, 7,8 mm
Operating functions
The functions of the Ò-key and the
è-key are configurable:
Function Òè
Remote (no front operation) X
SP.2 (2nd setpoint) X
Y.2 (2nd output value) XX
SP.E (external setpoint) XX
Manual operation XX
C.OFF (controller function off) XX
Lock of manual key X
Reset of latched limits and error list XX
Boost X
Parameter set ½ X
Programmer run/stop X
Several functions can be combined e.g.
SP.2 and parameter set switch-over
(gain scheduling) with only one key.
KS 50-1 5
KS 50-1 universal
123OK
125
126
SP.X run
Err
Ada
F
green “OK”-LED
process value
Programm run
selftuning is active
error list
setpoint, actuating value, parameter
Enter-key
operation keys
3 yellow LEDs for the output states
second or external setpoint
ramp is active
automatic/manual-key
configurable function-key
front interface
manual operation
BluePort
Display and operation:
125
126
SP.x run
Ada
Err
Flashing Error LED indicates active alarm
in the error list:

POWER SUPPLY
Depending on version:
AC SUPPLY
Voltage: 90...260 VAC
Frequency: 48...62 Hz
Power consumption approx. 7 VA
UNIVERSAL SUPPLY 24 V UC
AC voltage: 20,4...26,4 VAC
Frequency: 48...62 Hz
DC voltage: 18...31 V DC
Power consumption: approx: 7 VA (W)
BEHAVIOUR WITH POWER FAILURE
Configuration, parameters, and adjusted
set-points, control mode:
Non-volatile storage in EEPROM
BluePort®FRONT INTERFACE
Connection of PC via PC adapter (see
„Accessories“). The BlueControl
software is used to configure, set
parameters, and operate the KS 50-1.
BUS INTERFACE (OPTION)
Galvanically isolated
Physical: RS 422/485
Protocol: Modbus RTU
Transmission speed:
2400, 4800, 9600, 19.200 bits/s
Address range: 00...99
Number of controllers per bus: 32
Repeaters must be used to connect more
controllers.
ENVIRONMENTAL CONDITIONS
Protection modes
Front panel: IP 65
Housing: IP 20
Terminals: IP 00
Permissible temperatures
For specified accuracy: 0...60°C
Warm-up time: < 15 minutes
Temperature effect: < 100ppm/K
For operation: -20...65°C
For storage: -40...70°C
Humidity
75% yearly average, no condensation
Shock and vibration
Vibration test Fc (DIN 68-2-6)
Frequency: 10...150 Hz
Unit in operation: 1g or 0,075 mm
Unit not in operation: 2g or 0,15 mm
Shock test Ea (DIN IEC 68-2-27)
Shock: 15g
Duration: 11ms
Electromagnetic compatibility
Complies with EN 61 326-1
•Complies with the immunity
requirements for continuous,
unattended operation
•Complies with the emmission
requirements class B for rural areas
•Surge disturbances may increase the
measurement error
GENERAL
Housing
Material: Makrolon 9415,
flame-retardant
Flammability class: UL 94 VO, self-extinguishing
Plug-in module, inserted from the front
Safety tests
Complies with EN 61010-1 (VDE 0411-1):
Over voltage category II
Contamination class 2
Working voltage range 300 VAC
Protection class II
Certifications
Type test to DIN 3440
With certified sensors it can be used in:
•Heat generating plants with outflow
temperatures up to 120°C to DIN
4751
•Hot-water plants with outflow
temperatures above 110°C to DIN
4752
•Thermal transfer plants with organic
transfer media to DIN 4754
•Oil-heated plants to DIN 4755
UL certification (applied for)
6 KS 50-1

Electrical connections
Depending on version:
•Flat-pin connectors 1 x 6,3 mm or
2 x 2,8 mm to DIN 46 244
•Screw terminals for conductor
cross-section from 0,5 to 2,5 mm²
Mounting
Panel mounting with two fixing clamps
at top/bottom or left/right
Close mounting possible
Mounting position: not critical
Weight: 0,27 kg (9.52 oz)
Accessories supplied with unit
Operating instructions
2 fixing clamps
ACCESSORY EQUIPMENT
BlueControl (Engineering Tool)
PC-based program for configuring,
setting parameters, and operating
(commissioning) the KS 50-1 controller.
Moreover, all the settings are saved, and
can be printed on demand.
Depending on version, a powerful data
acquisition module is available, complete
with trend graphics.
Visibility mask
The BlueControl software can be used
to blind out parameters in the
instrument. Thus, only alowed
parameters can be changed on side.
Safety relevant parameters are invisible!
Simulation
The built-in simulation serves to test the
controller settings, but can also be used
for general training and observing the
interaction between controller and
control loop.
Software requirements
Windows 95/98/NT/2000.
Configurations that can only be
implemented via the BlueControl
software (not via the front-panel keys):
•Customer-specific linearizations
•Enable „forcing“ for inputs/outputs.
Forcing allows to write the analog and
digital inputs and outputs via Modbus
interface.
•Adjustment of limits for operating
hours and switching cycles
•Switch-over to 60 Hz mains
frequency
•Master/slave configuration
•Disable operator actions and
operating levels, plus password
definition
•Prevent automatic optimization of
cycle times T1, T2
Hardware requirements:
A PC adapter (see „Accessories“) is
required for connecting the controller.
Updates and demo software can be
downloaded from:
www.pma-online.de
KS 50-1 7
Functionality Mini Basic Expert
parameter and configuration setting yes yes yes
controller and control loop simulation yes yes yes
download: writes an engineering to the controller yes yes yes
online mode/ visualisation SIM only yes yes
creation of user defined linearizations SIM only yes yes
configuration of extended operating level SIM only yes yes
upload: reads an engineering from the controller SIM only yes yes
basic diagnosis function SIM only yes yes
file, save engineering data no yes yes
printer function no yes yes
online documentation, help system no yes yes
measurement correction (calibration procedure) no yes yes
program editor SIM only SIM only yes
data acquisition and trend function SIM only SIM only yes
network and multiuser licence no no yes
personal assistant function no no yes
extended simulation no no yes
extended diagnostic and service functions no no yes
BlueControl, versions and functionality:
Two parameters are blinded out:

PMA
Prozeß- und Maschinen- Automation GmbH
P.O. Box 31 02 29
D-34058 Kassel
Tel.: +49 - 561- 505 1307
Fax: +49 - 561- 505 1710
E-mail: [email protected]
Internet: http://www.pma-online.de
Your local representative:
Printed in Germany - Edition 0207- Subject to change without notice - 9498 737 40513
KS5 0 1 00 00
Flat-pin connectors 0
Screw terminals 1
90..250V AC, 3 relays 0
24VAC / 18..30VDC, 3 relays 1
90..250V AC, 2 relays + mA/logic 2
24VAC / 18..30VDC, 2 relays +mA/logic 3
no option 0
RS422/485 + UT + di2, di3 + OUT5/6 1
Standard configuration 0
Configuration to specification 9
no manual 0
manual german D
manual english E
manual french F
Standard 0
UL certified U
DIN 3440 certified D
ORDERING INFORMATION
Description Order no.
Current converter 50A AC 9404-407-50001
PC adapter, for connecting the BlueControl software to the BluePort®9407-998-00001
Standard rail adapter 9407-998-00061
Adhesive set of physical dimension labels with 31 different dimensions
and 4 empty labels 4012-140-66041
Operating manual German 9499-040-62818
Operating manual English 9499-040-62811
Operating manual French 9499-040-62832
BlueControl Mini German/English/French www.pma-online.de
BlueControl Basic German/English/French 9407-999-11001
BlueControl Expert German/English/French 9407-999-11011
ACCESSORIES
Other manuals for KS 50-1
1
Table of contents
Other PMA Temperature Controllers manuals
Popular Temperature Controllers manuals by other brands
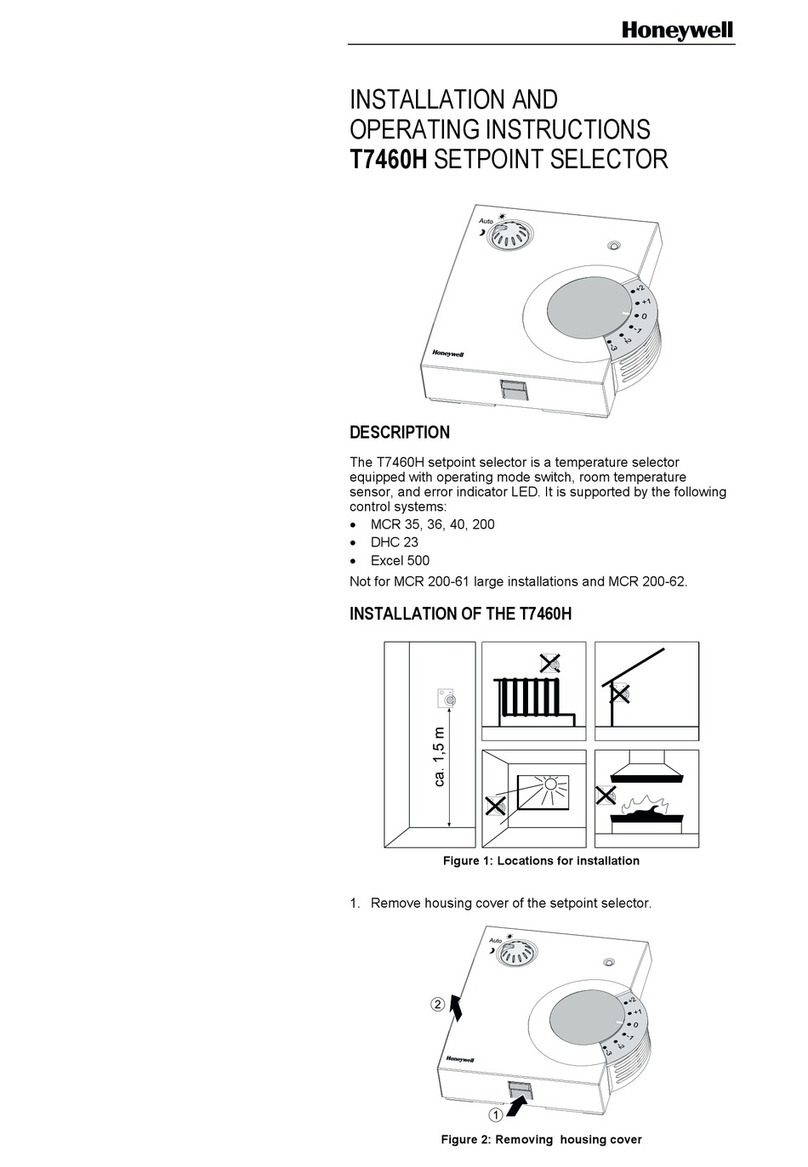
Honeywell
Honeywell T7460H Installation and operating instructions
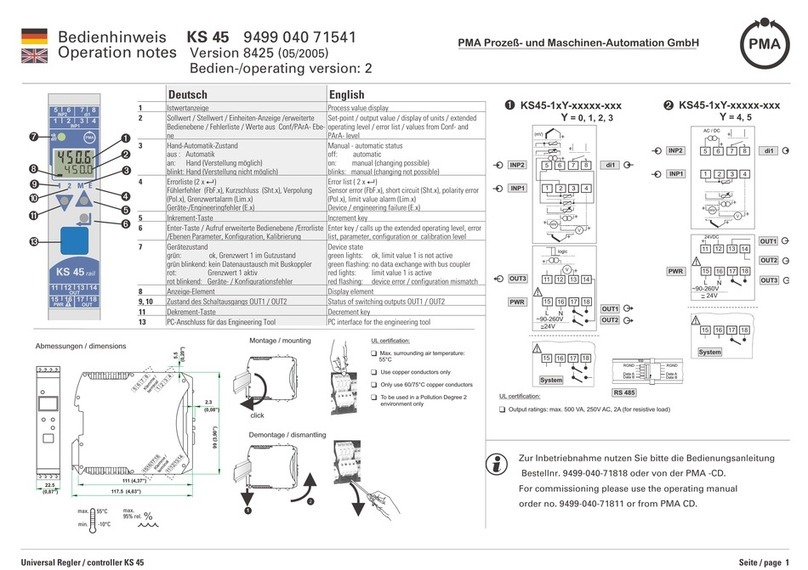
West Control Solutions
West Control Solutions KS 45 Operation Notes
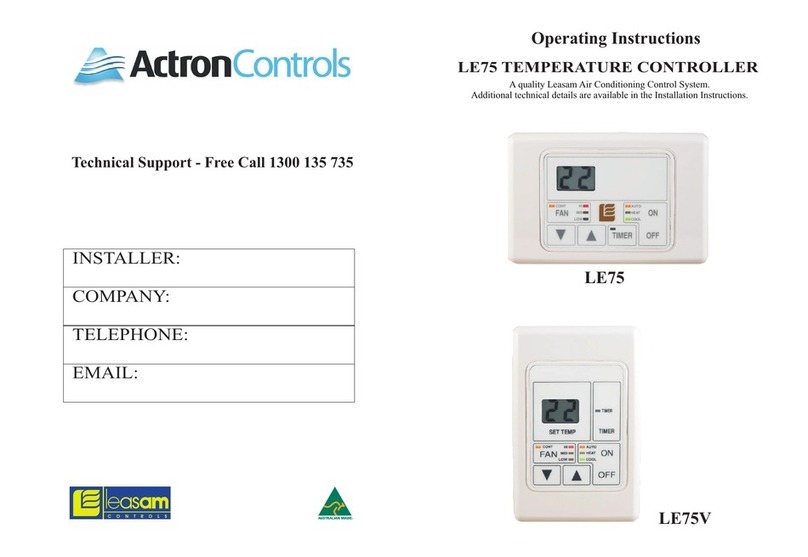
ActronControls
ActronControls LE75 operating instructions
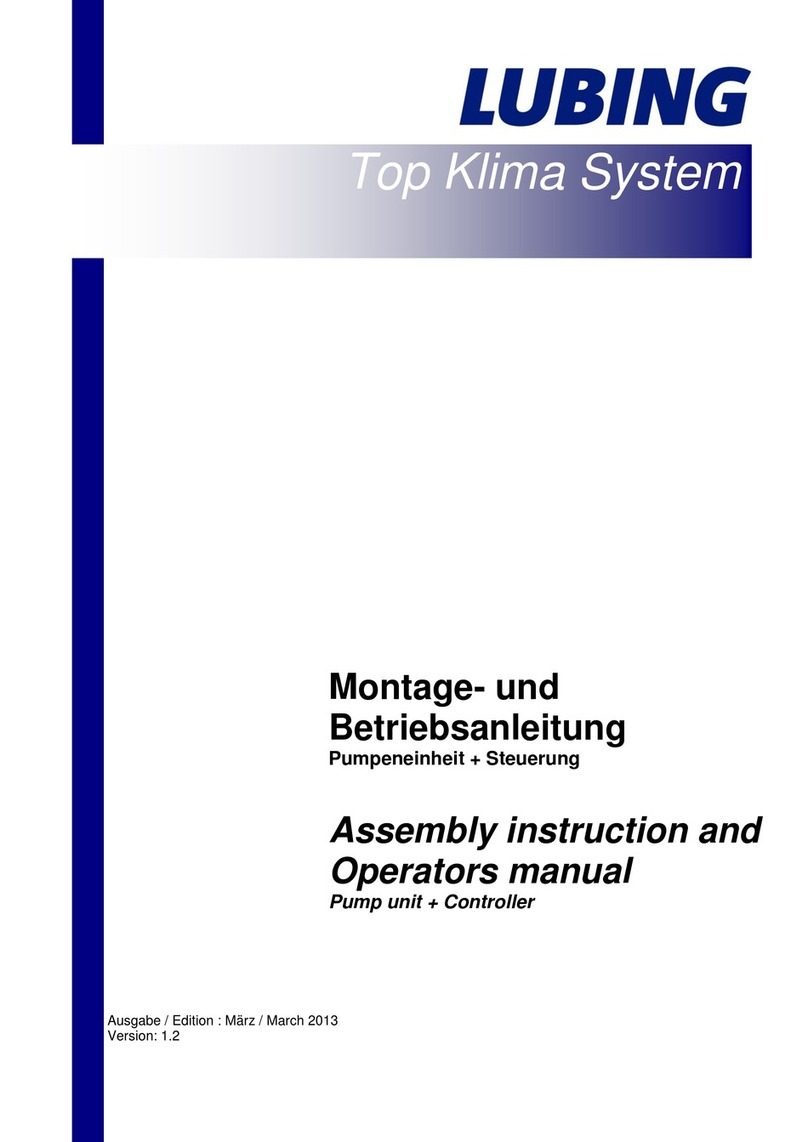
Lubing
Lubing Top Climate System Assembly instructions and operator's manual
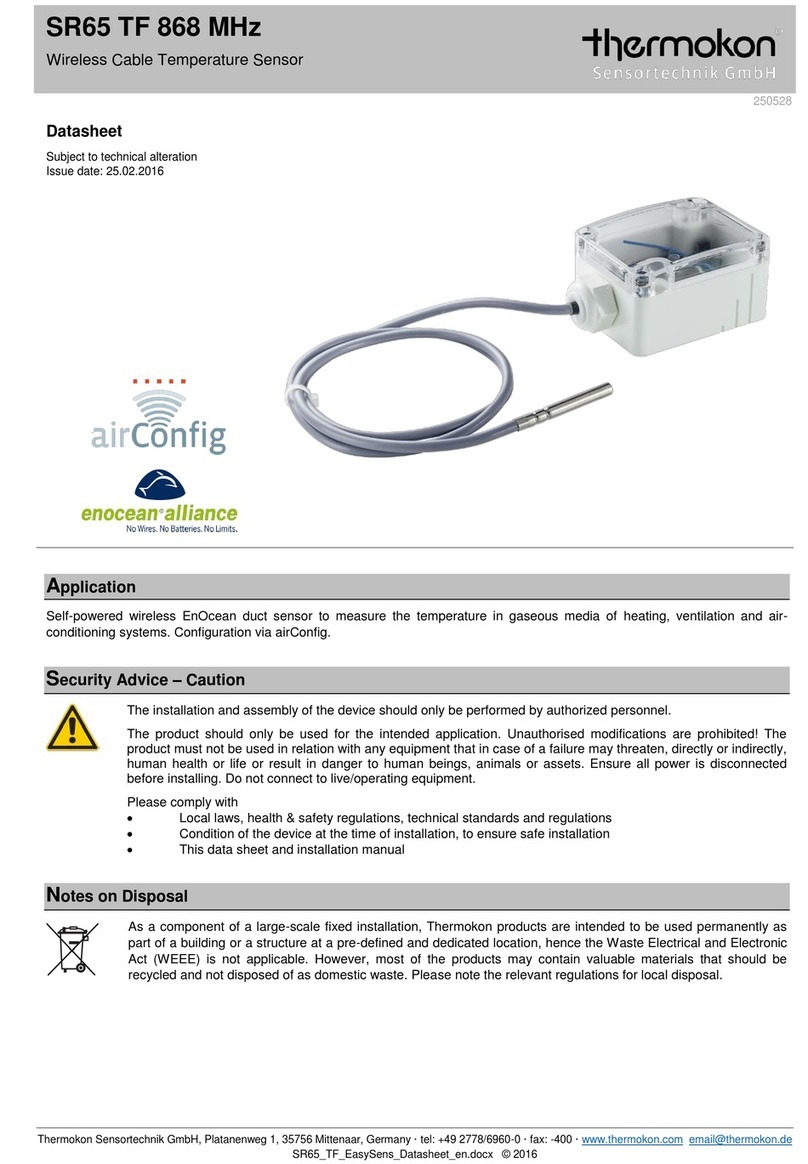
Thermokon
Thermokon SR65 TF quick start guide
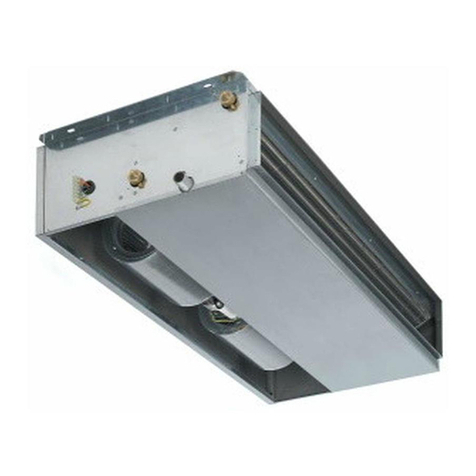
MAXA
MAXA HCN Series Installation, Use and Technical Manual