power automation PA 9000 User manual

PA 9000
STP220 CNC control
Installaon instrucons

Original installation instructions
©2017 Power Automation GmbH
Power Automation GmbH
CNC-Automatisierungstechnik
Gottlieb-Daimler-Str. 17/2
74385 Pleidelsheim
Germany
Telephone: +49-7144-899-0
Fax: +49-7144-899-299
E-mail: [email protected]
Internet: www.powerautomation.com
Version 4.0
2 21.02.2017

Table of contents
1 General information................................................................... 7
1.1 Information on this manual................................................ 7
1.2 Explanation of symbols...................................................... 7
1.3 Limitation of liability............................................................ 9
1.4 Copyright........................................................................... 9
1.5 Warranty terms.................................................................. 9
1.6 Customer service............................................................. 10
2 Safety........................................................................................ 11
2.1 Customer's responsibility................................................. 11
2.2 Personnel requirements................................................... 12
2.2.1 Qualifications................................................................. 12
2.2.2 Unauthorized persons................................................... 12
2.3 Intended use.................................................................... 13
2.4 Unintended use................................................................ 13
2.5 Personal protective gear.................................................. 14
2.6 Specific dangers.............................................................. 14
2.7 Safety devices................................................................. 16
2.8 Machine safety................................................................. 16
2.9 Conduct in a dangerous situation and in case of acci-
dents................................................................................ 17
2.10 Data safety....................................................................... 17
2.10.1 File backup.................................................................... 17
2.10.2 System protection......................................................... 18
2.10.3 PA Recovery Stick......................................................... 20
2.11 Environmental protection................................................. 21
2.12 Labels.............................................................................. 21
3 Design and function................................................................ 25
3.1 Overview.......................................................................... 25
3.2 Brief description............................................................... 26
3.3 EtherCATâ interface......................................................... 27
3.4 PC connectors................................................................. 29
3.5 (X20) PA USB software dongle connector....................... 40
3.6 EtherCATâ-interface (PASIO).......................................... 41
PA 9000 STP220 CNC control
Table of contents
21.02.2017 | 3

3.7 Connection cable CAB STP220 MCP IO EXT................. 42
3.8 Machine Control Panel (MCP)......................................... 43
3.8.1 PDO Data mapping for MCP (EtherCAT Slave)............ 49
3.8.1.1 PLC Mapping.............................................................. 52
3.8.1.2 Spindle Override Switch / G1 Override Switch........... 57
3.8.1.3 G0 Override Switch.................................................... 58
3.8.1.4 MPG Switches............................................................ 59
3.8.1.5 Input bytes.................................................................. 60
3.8.1.6 Output bytes............................................................... 76
4 Technical data.......................................................................... 83
4.1 General specifications..................................................... 83
4.2 Connection values........................................................... 83
4.3 Operating conditions........................................................ 83
4.4 NVsRAM Mini-PCIe card for PA9000 systems................ 84
4.5 Dimension sheet.............................................................. 85
4.6 Electromagnetic compatibility.......................................... 85
4.7 Installation guidelines...................................................... 87
5 Installation................................................................................ 91
5.1 Prerequisites and preparations........................................ 91
5.1.1 General requirements................................................... 91
5.2 Mounting the PA 9000 STP220....................................... 92
6 Transport, packaging and storage......................................... 95
6.1 Transport......................................................................... 95
6.2 Packaging........................................................................ 95
6.3 Storage............................................................................ 97
7 Maintenance............................................................................. 99
7.1 Safety notes..................................................................... 99
7.2 Maintenance schedule..................................................... 99
7.3 Measures after maintenance......................................... 100
8 Troubleshooting..................................................................... 101
8.1 Safety notes................................................................... 101
8.2 Troubleshooting chart.................................................... 102
9 Service and return process................................................... 105
9.1 Service........................................................................... 105
PA 9000 STP220 CNC control
Table of contents
21.02.2017 | 4

9.1.1 Service addresses....................................................... 106
9.2 Spare parts.................................................................... 107
9.3 Return policy and procedure.......................................... 108
9.4 Training.......................................................................... 110
10 Dismounting and decommissioning.................................... 111
11 EC Declaration of Conformity............................................... 113
12 Proof of change...................................................................... 115
13 Glossary.................................................................................. 117
14 Index........................................................................................ 119
PA 9000 STP220 CNC control
Table of contents
21.02.2017 | 5

PA 9000 STP220 CNC control
Table of contents
21.02.2017 | 6

1 General information
1.1 Information on this manual
This installation manual provides important information on how to work
with the control unit safely and efficiently.
The installation manual is part of the control unit, must always be kept
in the control unit's direct proximity and should be available for the per-
sonnel at any time. All personnel working with the control unit are
obliged to have read and understood this installation manual before
starting any work. Strict compliance with all specified safety notes and
instructions is a basic requirement for safety at work.
Moreover, the accident prevention guidelines and general safety regu-
lations applicable at the place of use of the control unit must also be
complied with.
Illustrations in this installation manual are intended to facilitate basic
understanding, and may differ from the actual design of the control
unit.
The enclosed manuals for the installed components apply together
with this installation manual.
1.2 Explanation of symbols
Warnings are identified by pictures. These warnings are introduced by
signal words, which express the severity of a danger.
Pay attention to these warnings and act cautiously in order to avoid
accidents, personal injuries and damage to property.
… indicates an imminently hazardous situation which, if unavoid-
able, will result in death or serious injury.
… indicates a potentially hazardous situation which, if unavoid-
able, could result in death or serious injury.
… indicates a potentially hazardous situation which, if unavoid-
able, may result in minor or moderate injury.
… indicates a potentially hazardous situation which, if unavoid-
able, may result in property damage.
… emphasizes useful hints and recommendations as well as informa-
tion for efficient and trouble-free operation.
The following symbols are used in connection with the safety notes to
highlight particular dangers:
General Information
Warnings
L DANGER
L WARNING
L CAUTION
NOTICE
Special Safety Notes
PA 9000 STP220 CNC control
General informaon
21.02.2017 | 7

… highlights hazards caused by electric current. There is a
danger of serious injury or death if the safety notes are not com-
plied with.
The following symbols and highlights are used to distinguish
instructions, descriptions of results, cross-references and other ele-
ments inside this manual.
.. Highlights a step as part of a procedure of instructions.
ð.. Highlights a state or an automatic process as a result of an
instruction.
n.. Highlights single or unordered instructions and lists.
Ä
“Additional symbols and highlighting” on page 8.. Highlights cross-
references to chapters or sections of this manual.
[Key].. Highlights captions of buttons, fields and other elements of the
software's graphical user interface.
“Menu è Submenu è ”.. Highlights a path to access a menu or sub-
menu in the software's graphical user interface.
Example/Extract.. Highlights verbatim examples and extracts from
configuration files.
L DANGER
Additional symbols and high-
lighting
PA 9000 STP220 CNC control
General informaon
21.02.2017 | 8

1.3 Limitation of liability
All information and notes in this installation manual were compiled
under due consideration of valid standards and regulations, the
present status of technology and our years of knowledge and experi-
ence.
Power Automation can not be held liable for damage resulting from:
ndisregarding this installation manual
nunintended use
nemployment of untrained personnel
nunauthorized conversions
nunauthorized modifications to the software
ntechnical modifications
nuse of unapproved spare parts
nuse in conjunction with machines not deemed compatible by
Power Automation
In case of customized versions the actual scope of delivery can vary
from the explanations and representations in this installation manual,
because of the utilization of additional options or due to the latest tech-
nical changes.
Apart from this, the obligations agreed upon in the delivery contract,
the general terms and conditions, and the delivery conditions of Power
Automation and the legal regulations valid at the time of contract apply.
We reserve the right to make technical modifications in order to
improve usability.
1.4 Copyright
This installation manual is protected by copyright law.
Passing this installation manual on to third parties, duplication of any
kind – even in form of excerpts – as well as the use and/or disclosure
of the contents without the written consent of Power Automation is not
permitted.
Violations oblige to compensation. The right for further claims remains
reserved.
1.5 Warranty terms
The material warranty terms are provided in Power Automation's terms
and conditions as well as inside the sales documents.
Liability
Copyright
Material Warranty
PA 9000 STP220 CNC control
General informaon
21.02.2017 | 9

1.6 Customer service
Our Customer Service is always available for technical information.
For information on whom to contact by phone, fax, e-mail or via the
internet, see Power Automation's address on page 2.
Additionally, Power Automation staff is always interested in receiving
new information and experiences resulting from the use of our prod-
ucts, which could be of great value for future improvements.
Service
PA 9000 STP220 CNC control
General informaon
21.02.2017 | 10

2 Safety
2.1 Customer's responsibility
The control unit is used for commercial purposes. The operating com-
pany is thus subject to the legal obligations concerning industrial
safety.
The safety, accident prevention and environmental protection regula-
tions applicable for the area of application of the machine must be
complied with, along with the safety notes specified in this installation
manual. The following applies in particular:
nThe customer must become familiar with the industrial safety regu-
lations and identify additional dangers which may arise due to the
specific working conditions at the place of use of the control unit,
by means of a risk analysis. These must be converted into oper-
ating instructions for operation of the control unit.
nThroughout the time of use of the control unit the customer must
check whether the operating instructions created by him corre-
spond to the current status of regulations and standards. When-
ever changes in regulations and standards occur, instructions must
be adapted accordingly.
nThe customer must clearly specify the responsibilities for
installation, operation, maintenance, and cleaning.
nThe customer must make sure that all employees who have to
work with the control unit have read and understood these oper-
ating instructions.
In addition, the customer must train and inform his personnel about
potential dangers at regular intervals.
Moreover, the customer is also responsible for keeping the control unit
in technically good condition, and therefore the following applies:
nThe customer must make sure that the maintenance intervals
specified in these operating instructions are complied with.
nThe customer must regularly check all safety features for function
and completeness.
nThe customer must supply his personnel with the necessary pro-
tective equipment.
PA 9000 STP220 CNC control
Safety
21.02.2017 | 11

2.2 Personnel requirements
2.2.1 Qualifications
Danger of injury in case of insufficient qualification!
– Only those persons who have been specified in the corre-
sponding chapters of this installation manual should be
entrusted with the listed types of work.
– Employ certified experts, if in doubt.
Improper operation can lead to severe personal injuries and/or
material damage.
The following qualifications are specified for different areas of activity
listed in the installation manual.
Instructed person
was instructed by the operating company about the duties assigned to
her/him and the possible dangers that may arise from inappropriate
conduct.
Qualified personnel
are able to carry out assigned work and to recognize possible dangers
due to professional training, knowledge, and experience as well as
profound knowledge of applicable regulations.
Skilled electrician
A skilled electrician is able to carry out assigned work and to recognize
and avoid possible dangers due to professional training, knowledge,
and experience as well as profound knowledge of applicable
regulations.
The skilled electrician has been trained specially for his working envi-
ronment and he has profound knowledge of relevant standards and
regulations.
2.2.2 Unauthorized persons
Danger for unauthorized persons!
– Keep unauthorized persons away from the working area.
– If in doubt, address such persons and ask them to leave the
working area.
– Interrupt your work as long as unauthorized persons are in
the working area.
Unauthorized persons, who do not meet the requirements
described in this installation manual, are not aware of the dan-
gers in the working area.
Only persons who are expected to perform their tasks reliably are per-
mitted as personnel. Persons whose reaction capability is impaired,
e.g. through drugs, alcohol or medication are not permitted.
L WARNING
L WARNING
PA 9000 STP220 CNC control
Safety
21.02.2017 | 12

nWhen selecting personnel, ensure that the personnel can work
with the control unit in terms of technical and content aspects.
2.3 Intended use
The control unit is exclusively intended and built for the use described
in this installation manual.
The control unit is to be used exclusively to control CNC machines of a
supported number of axes which are in accordance with the types
cleared by Power Automation. Prerequisite for the intended use of the
control unit is proper configuration as described in the installation man-
uals provided by Power Automation.
Beware of unintended use!
– Operate the control unit as intended only.
– Observe all instructions in this installation manual.
– Observe the permissible ambient conditions and electromag-
netic compatibility mentioned in the technical data.
Any use exceeding the scope of intended use and/or different
application of the control unit can result in hazardous situations.
Claims of any kind for damage resulting from unintended use are void.
The operator is solely responsible for all damage resulting from
unintended use.
2.4 Unintended use
Beware of unintended use!
– In particular, avoid using the control unit for the following pur-
poses as these are regarded as not intended:
– Operation using software not approved by
Power Automation.
– Operation connected to machines/drives not deemed com-
patible by Power Automation.
– Operation using wrong number of axes
– Wrong or missing execution of the maintenance intervals
– Operation by not instructed personnel
Intended Use
Dangers
L WARNING
Unintended Use
L WARNING
PA 9000 STP220 CNC control
Safety
21.02.2017 | 13

2.5 Personal protective gear
Wearing of personal protective gear is required to minimize health haz-
ards and damage when working with the control unit.
nAlways wear the protective equipment that is necessary for the
respective task when working.
nFollow the instructions on personal protective equipment that are
listed in this installation manual and other installation manuals pro-
vided by Power Automation.
nThe environment in which the control unit is installed may require
users to wear additional personal protective gear.
Observe the instructions on personal protective gear provided by
the operating company.
Antistatic gloves
for protection of the hands during the work. Wear the antistatic gloves
always until the work is finished.
ESD clothing
for protection of components susceptible to electrostatic discharge.
Wear the ESD clothing during the work on electrostatic components.
ESD safety pad
for protection of components susceptible to electrostatic discharge. Put
the ESD safety pad on the floor before starting to work.
ESD safety shoes
for protection of components susceptible to electrostatic discharge.
Wear the ESD safety shoes to protect electrostatic-discharge-sensitive
devices due to inadequate derivative electrostatic energy.
Ear protection
for protection of the ears during the work. Wear the ear protection
always until the work is finished.
Ground strap
for protection of components susceptible to electrostatic discharge.
Wear the ground strap on your wrist and connect it to a suitable
equipotential bonding.
Protective glasses
for protection of the eyes during the work. Always wear the protective
glasses until the work is finished.
2.6 Specific dangers
The following section lists the residual risks.
PA 9000 STP220 CNC control
Safety
21.02.2017 | 14

nObserve the safety instructions listed here, and the warnings in
subsequent chapters of this installation manual, to reduce health
hazards and to avoid dangerous situations.
Danger to life caused by electric current!
Touching conductive parts causes a direct danger to life. Damage
to insulations or individual components can cause danger to life.
nIn the event of damage to insulation, switch off the power supply
immediately and have the defective parts repaired.
nWork on the electric system must be carried out only by skilled
electricians.
nBefore maintenance, cleaning or repair work, switch off the power
supply and secure it against being switched on again.
nDo not bridge fuses or make them ineffective. When changing
fuses make sure you use the correct amperage.
nKeep moisture away from conductive parts. This can cause short-
circuits.
nDe-energize the machine for all work on the electrical system.
Uncontrolled operation due to improper installation and configu-
ration!
The control unit's safety relay must be properly integrated into
the CNC machine emergency stop chain. Improper wiring and
configuration of the safety relay may result in uncontrolled opera-
tion of the CNC machine and in consequence may lead to irrever-
sible personal injuries or death.
nOnly operate the CNC machine when the safety relay has been
properly integrated into the machine emergency stop chain.
nOnly let qualified personnel (
Ä
Chapter 2.2.1 “Qualifications”
on page 12) set up the emergency stop chain.
nFor information on safety devices integrated into the machine see
the manual supplied by the machine's manufacturer.
nIf in doubt regarding the configuration, contact the manufacturers
of the CNC machine and the control unit.
Risk of injury due to improper handling of batteries!
Batteries must be handled with special care.
nDo not throw batteries into fire or expose to high temperature.
Explosion hazard!
nDo not charge batteries. Explosion hazard!
nBattery fluid leaking due to wrong usage may cause skin irritation.
Avoid contact with the battery fluid. In case of contact, flush the
battery fluid with large amounts of water. If the battery fluid enters
the eyes, flush immediately with water for 10 min. and consult a
physician without delay.
L DANGER
L DANGER
L WARNING
PA 9000 STP220 CNC control
Safety
21.02.2017 | 15

Malfunction due to discharged buffer battery!
The control unit's CMOS settings are buffered by a battery. If this
battery is discharged completely the CMOS settings are lost. Mal-
functions of the control unit may result.
nFor further information, see
Ä
Chapter 8.2 “Troubleshooting chart”
on page 102.
2.7 Safety devices
Malfunctioning safety devices may pose a fatal risk!
Safety devices must be intact and properly integrated into the
control unit's configuration and software in order to guarantee
safety.
nBefore initial commissioning of the machine, ensure that all safety
devices are fully functional and correctly installed.
nEnsure that safety related inputs/outputs of the CNC control unit
are fully functional and perform as intended.
nNever disable safety devices.
nHeed regulations concerning hardwiring of safety circuits.
Superior CNC Control unit or PLC
For information on required connections between the PA control unit
and safety devices integrated into the CNC machine see the documen-
tation provided by the machine's manufacturer.
Data safety
For information on data safety see
Ä
Chapter 2.10 “Data safety”
on page 17.
2.8 Machine safety
For information on the machine's safety devices and emergency stop
chain see the manual provided by the CNC machine's manufacturer.
The manufacturer of the CNC machine is responsible for the proper
installation of the emergency stop.
L CAUTION
Safety
L DANGER
Superior Control Units
Software
Further Applicable Documents
PA 9000 STP220 CNC control
Safety
21.02.2017 | 16

2.9 Conduct in a dangerous situation and in case
of accidents
nStay informed about locations of first aid equipment (first aid kit,
covers, etc.) and fire extinguishers at the site of installation.
nInstruct personnel about accident reporting, first aid and rescue
facilities at the site of installation.
nDisconnect power supply immediately.
nInitiate first aid measures.
nInform responsible persons at the site.
nCall for rescue service if applicable.
2.10 Data safety
To ensure the ability to restore critical data in case of control unit or
storage malfunctions, internal and external (off-site) backup copies of
all files that are critical to proper machine function must be created
regularly and kept in a secure environment.
To minimize the chance of data loss, it is recommended to protect the
system patition (C:) with the File Based Write Filter (FBWF) and use a
second partition for user data.
Extended system outage in case of data loss!
If backup copies of critical control unit data are not created regu-
larly and kept securely, the control unit configuration would have
to be set up from scratch in case of data loss.
nPay attention to all instructions regarding data safety as given in
this and the other installation manuals provided by Power Automa-
tion.
2.10.1 File backup
A backup solution is preinstalled and configured.
It is neccessary to select and activate the backup-function inside the
CNC.
Personnel: nQualified personnel
nInstructed person
1. Follow the instructions to properly configure the control unit for
use with the intended machine.
2. Ensure that the configuration is functioning as intended.
Preventive Measures
In Case Of Accidents
General Information
L CAUTION
Initial State
Instructions
PA 9000 STP220 CNC control
Safety
21.02.2017 | 17

3. Ensure that the machine data is saved regularly (see
Ä
Chapter
9 “Service and return process” on page 105).
4. Keep a record of all modifications to the configuration done by
the operator.
5. Ensure that backups are updated manually in case of modifica-
tions to the configuration.
2.10.2 System protection
Automated regular anti-virus scanning and manual scanning of files
copied to the control unit are advised by Power Automation as needed.
To protect the system against virus attacs or other system failures, it is
recommended to take the following measures:
nEither don't connect the CNC to the Internet or assure it is con-
nected via a managed firewall.
nBe sure that there is no virus software already behind the firewall
in your intranet. Only then, it is save to use the internal ethernet
connection for data transfer.
nUse only virus free and verified USB memory sticks for data
transfer to the CNC control. Don't allow users to transfer data with
unverified USB memory sticks. If you are not sure whether you can
guarantee this, please consider the usage of a USB-Guardian soft-
ware (see http://www.trinit-soft.de/usb-waechter/).
In Windows 7, the FBWF is already part of the system. There is no
special graphical user interface (GUI) necessary. The FBWF interface
can be started in the taskbar, see Fig. 1.
Initial State
Filebased Write Filter (FBWF)
PA 9000 STP220 CNC control
Safety
21.02.2017 | 18

Fig. 1: Start of the FBWF interface
Click on the little lock and the FBWF interface shows up the folling
window (Fig. 2).
After delivery, the FBWF is in state "enabled". You must put it into the
state "disabled" if you want to install further software on the system
partition, or if you need to do other modifications there.
PA 9000 STP220 CNC control
Safety
21.02.2017 | 19

Fig. 2: Overview FBWF interface
2.10.3 PA Recovery Stick
For various reasons it may become necessary to re-install or to repair
the operating system (Windows 7 Embedded) of the control unit.
Power Automation offers a Recovery Stick which is necessary for re-
installation or repair. for more information about this Recovery Stick
please look into the PA Accessories Manual.
The PA Recovery Stick is an All-in-One Solution for checking, testing
and most of all recovering and restoring the PA 8000 / PA 9000 control.
The main feature of the PA Recovery Stick is to give the user the
ability to recover and restore the complete HDD of his PA 8000 / 9000
control if somehow a data loss or a system crash has occurred. It also
gives the user the opportunity to perform an Antivirus scan if an infec-
tion is suspected. Also located on the PA Recovery Stick are other
helpful tools like a RAM test. The following manual will show what the
various possibilities of the PA Recovery Stick are.
PA 9000 STP220 CNC control
Safety
21.02.2017 | 20
Other manuals for PA 9000
2
Table of contents
Popular Controllers manuals by other brands
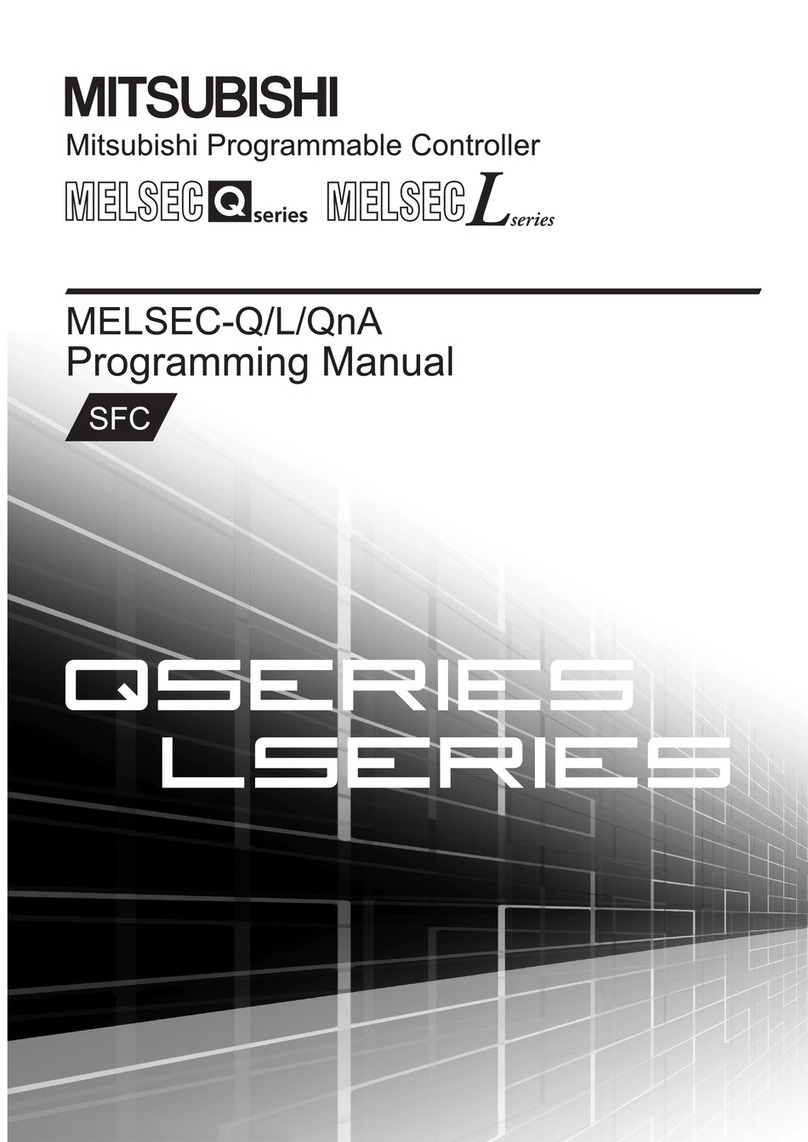
Mitsubishi
Mitsubishi MELSEC Q Series Programming manual
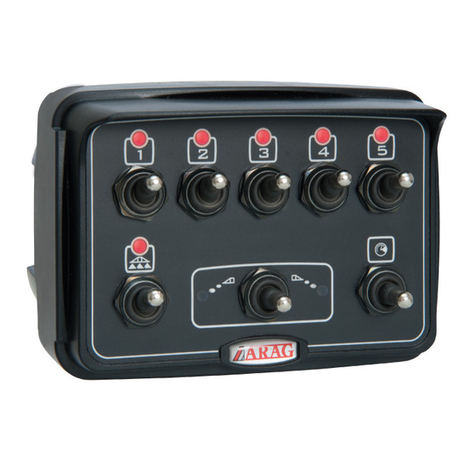
ARAG
ARAG 4669 Series General instruction for installation use and maintenance
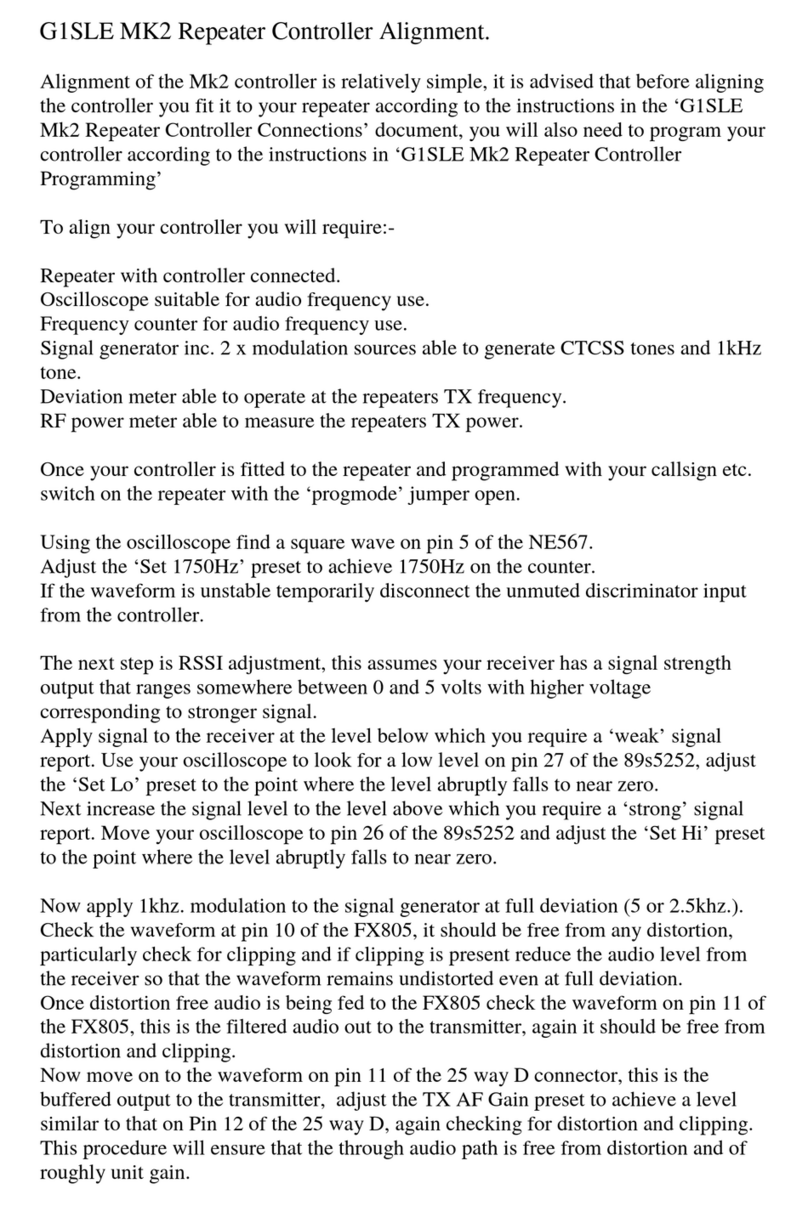
G1SLE
G1SLE MK2 Alignment Guide
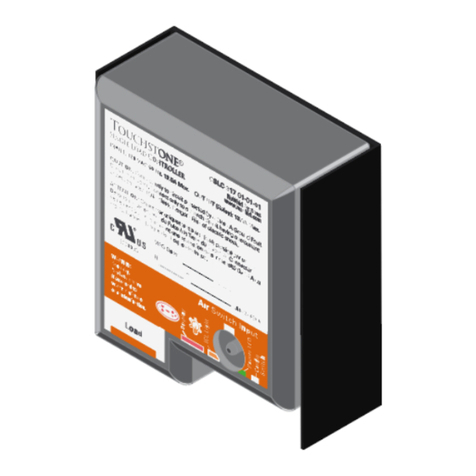
NuWhirl
NuWhirl TOUCHSTONE CSLC-317-02-01-01 Installation & operating manual
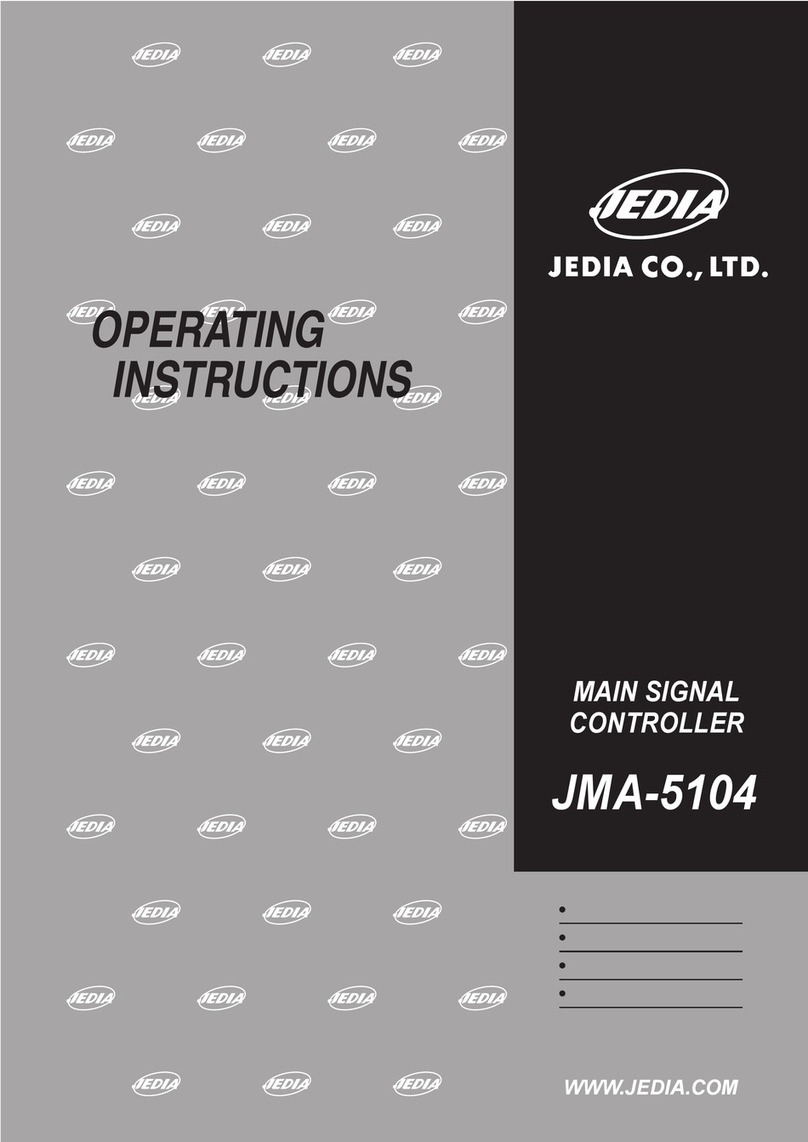
Jedia
Jedia JMA-5104 operating instructions
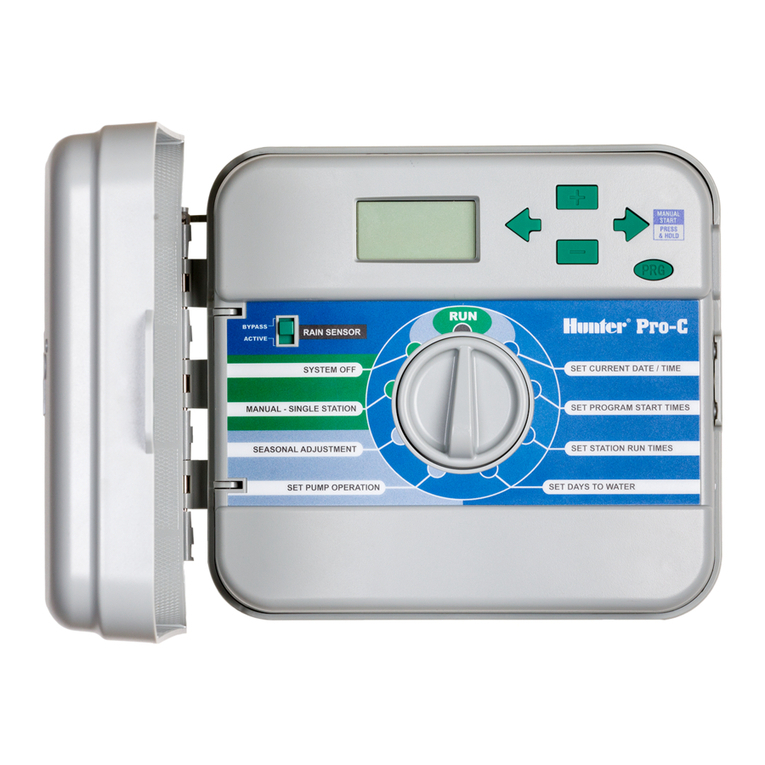
Hunter
Hunter Pro-C Product information
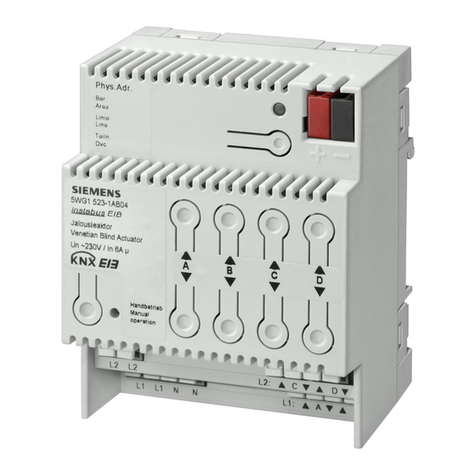
Siemens
Siemens 5WG1 523-1AB04 quick start guide
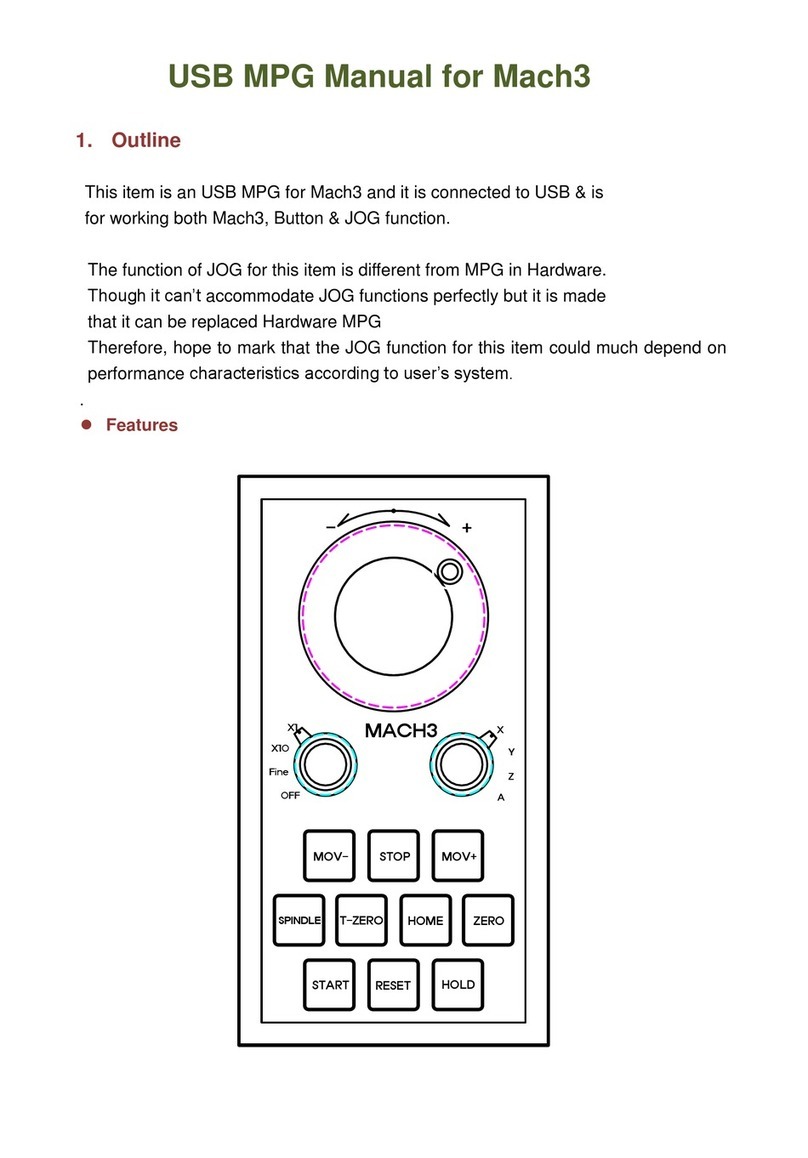
CNC
CNC USB MPG manual
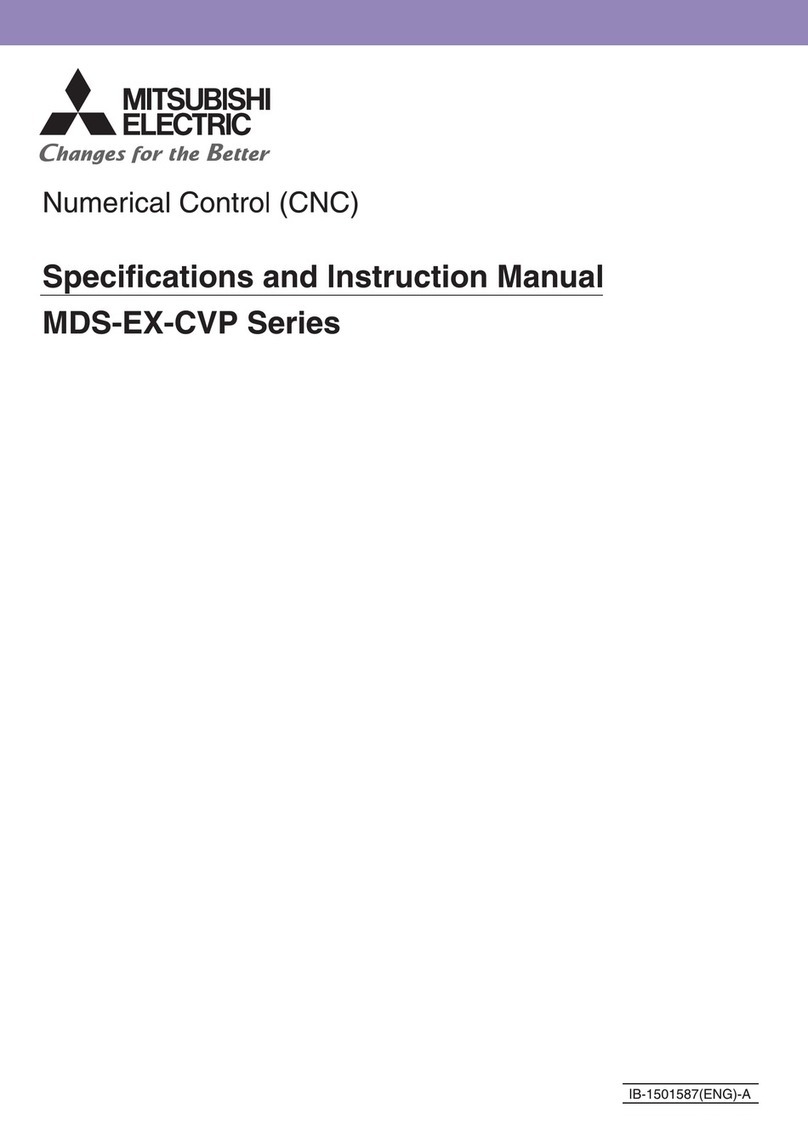
Mitsubishi Electric
Mitsubishi Electric MDS-EX-CVP Series Technical Specification and Instruction Manual
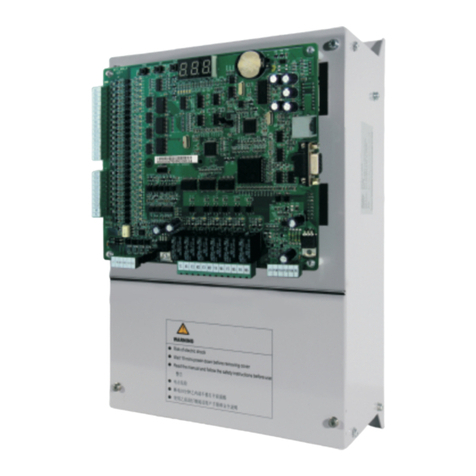
Monarch
Monarch nice3000 user manual
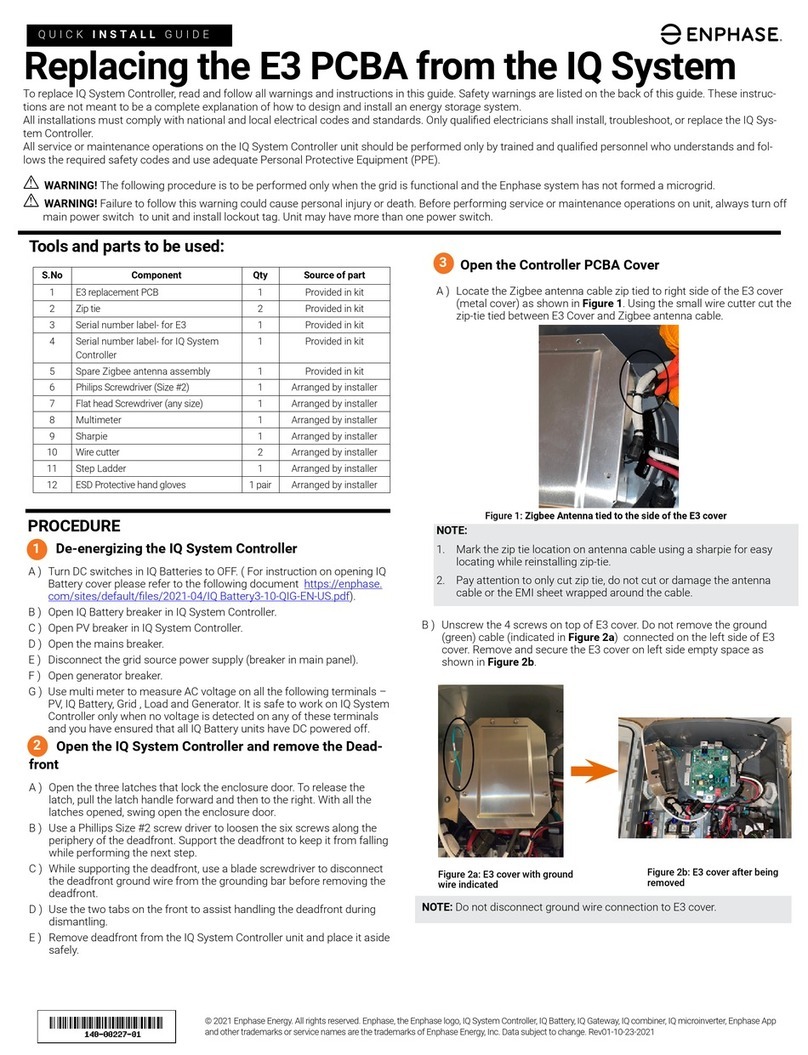
enphase
enphase E3 PCBA Quick install guide
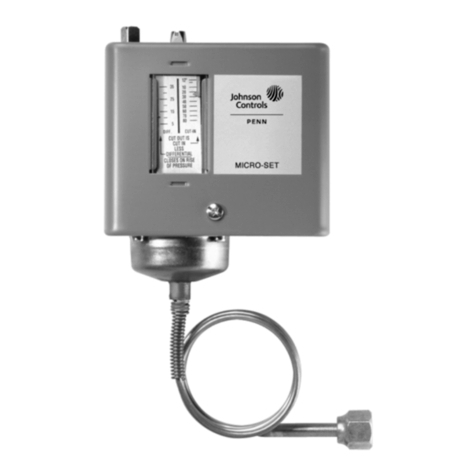
Johnson Controls
Johnson Controls PENN P70AB-2 Installation Sheets Manual