Linkam Scientific Instruments LinkPad T96 User manual

T96 LinkPad User Guide
Linkam Scientific Instruments
USER GUIDE
1.1.0

This page is intentionally blank

© 2017 Linkam Scientific Instruments Ltd.
3
v1.1.0
Table of Contents
...................................................................................................................................................................4Introduction
...................................................................................................................................................................5Important Notices
.................................................................................................................................................................................................... 5Warranty
.................................................................................................................................................................................................... 5Technical Support
.................................................................................................................................................................................................... 5Feedback
...................................................................................................................................................................6Controlling the stage
.................................................................................................................................................................................................... 8Basic stage controls
.................................................................................................................................................................................................... 9Profiles and Ramps
.............................................................................................................................................................................................. 9
Creating a profile
.............................................................................................................................................................................................. 10
Running The Profile
...................................................................................................................................................................11Stage Specific Controls
.................................................................................................................................................................................................... 11Vacuum stages
.................................................................................................................................................................................................... 12Pressure stages
.................................................................................................................................................................................................... 13Motorised XY stages
.................................................................................................................................................................................................... 15Tensile stages
.................................................................................................................................................................................................... 18DSC stages
.................................................................................................................................................................................................... 19Humidity control
...................................................................................................................................................................21Options and Information
.................................................................................................................................................................................................... 21Connected hardware
.................................................................................................................................................................................................... 22Option board Information
.................................................................................................................................................................................................... 23Sample Calibration
...................................................................................................................................................................25Troubleshooting
.................................................................................................................................................................................................... 25Control and connection Errors

© 2017 Linkam Scientific Instruments Ltd.
4
v1.1.0
Introduction
Welcome to your LinkPad Manual. This guide will explain the use ofthe optional LinkPad Controller.

© 2017 Linkam Scientific Instruments Ltd.
5
v1.1.0
Important Notices
·
Please check that your Linkam equipment has not been damaged duringtransit. If there is any evidence of external damage DONOTSWITCH ON
ANY ELECTRICAL ITEMS.
·
Contact Linkam or their appointed distributor immediately. Your warranty may be impaired if Linkam is not informed ofany transport damage
within 7 working days ofdelivery.
·
NOattempt should be made to repair or modify the equipment in any way, as there are no user replaceable parts.
·
No attempt should be made to open the case except by qualified personnel as hazardous voltages are present.
·
In order to use this equipment succes sfully, plea se take time to read this ma nual a ll the way through before using it.
·
The Linkpad is designed to be used in conjunction with a Linkam T96 temperature controller. Please refer to the T96 Controller manual before
use.
Warranty
This equipment has a warranty against defects in material and workmanship for a period of12 months from the date of shipping. Linkam will either
repair or replace products that prove to be defective. For warranty service or repair, this product must be returned to Linkam or a designated
service facility.
The warrantyshall not apply to defects resulting from interfacing, unauthorized modification or misuse, operation outside of the environmental
specifications for the product, or improper site preparation or maintenance.
Technical Support
Any technical questions or queries should be addressed to the Technical Support Department at the address shown below and on the back ofthis
manual.
Tel: +44(0)1737 363 476
Email: support@linkam.co.uk
Feedback
Your feedback will be greatly appreciated, please email us directly info@linkam.co.uk

© 2017 Linkam Scientific Instruments Ltd.
6
v1.1.0
Controlling the stage
This section explains how to use the LinkPad to control the basic functions of your Linkam stage.
The display screen is touch sensitive, so you can simply operate the Linkpad byfinger touches.
If you are using the LinkPad concurrently with the optional LINK software and a PC connection, only sensor data such as temperature will be shown.
The power indicators still operate as does the Setup button.

© 2017 Linkam Scientific Instruments Ltd.
7
v1.1.0
When the LinkPad is connected to a temperature controlled stage without any additional features (such as vacuum or motor control)you will see
the followingscreen:
1. Current stage temperature
2. Heating / Cooling rate
3. Temperature Limit
4. Hold time
5. Liquid nitrogen pump speed (only present if an LNP96 is connected to the T96)
6. Start control
7. Heat override control
8. Cool override control
9. Pause control
10. Ramp number display / Ramp options
11. Next ramp control
12. Previous ramp control
13. Settings and Information
14. Volume icon
15. Computer control icon
16. Sample Calibration icon
17. Stage power input display
18. Feature control functions (only present when an LNP96 is connected or a stage with additional features is in use)

© 2017 Linkam Scientific Instruments Ltd.
8
v1.1.0
Basic stage controls
Heating or coolingthe Stage
To set the desired target temperature, tap on the limit control (3)and a keypad will appear:
Enter the required value by tappingon the numbers. The currently set limit and the range ofacceptable limit values for the connected stage are
shown to the left of the keypad.
To set the desired rate of temperature change, tap on the Rate control (2)and a keypad will appear:
Enter the desired rate using the keypad. The currently set rate and the range of acceptable rate values are displayed to the left ofthe keypad. The
units can be changed between °C/minute and °C/hour from this keypad. Changingthe units will update the acceptable range ofvalues.
To set the hold time, which is the amount oftime the system will maintain the target temperature once reached, tap on the Hold control (4)and a
keypad will appear:
Enter the desired hold time in hours, minutes and seconds.
If usinga system with a liquid nitrogen pump (LNP), the LNP speed value (5)will default to automatic. This means that the system will control the
flow rate of liquid nitrogen to match the rate oftemperature change specified. Ifyou wish to manuallycontrol the speed of the liquid nitrogen flow,
tap on the LNP speed (5)and a keypad will appear:
Tap on 'Man'to change the pump to manual mode and enter the desired pump speed as a percentage of maximum speed, with 100 being maximum
speed.
Note: That usingthe LNP in this way may impact the accuracy ofthe rate of temperature change. We recommend using the LNP in automatic mode
where possible.
Note: Ifyou are usinga stage with a Peltier element that cools usingthe thermoelectric effect, such as the PE120, there are no additional settings
needed for cooling. Aresistance heated stage such as the THMS600 cannot cool below ambient temperature without the use ofan LNP.
Once the required values have been set, begin the experiment by taping on the start button (6). This will change to a stop button while the system is
active. The experiment can be paused at any time by taping on the pause control (9).
The Heat override (7)or Cool override (8)controls can be tapped at any time duringan experiment to force the stage to heat or cool at the currently
set rate. These controls will not function unless there is a currently active ramp.

© 2017 Linkam Scientific Instruments Ltd.
9
v1.1.0
Profiles and Ramps
On the LinkPad 'Ramp'refers to an individual group of settings (rate, limit, hold time, etc.)that make up one step in an experiment, and a profile is a
combination of ramps that makes up a complete experiment.
For example a profile could consist of3 ramps, with the first being set to increase from ambient temperature to 100°C at 50°C/min, the second to
heat from 100 to 150 at 10°C/min and the third to heat from 150 to 160 at 1°C/min and hold at 160 for 10 minutes. An example ofa 4 ramp profile is
shown below:
The following section describes how to configure, save, import and export these temperature profiles.
Creating aprofile
Aprofile is created byenteringvalues into multiple ramps and setting a start ramp and an end ramp.
To select a ramp to edit, tap on either the ramp up control (11)or the ramp down control (12). Once the desired ramp is selected, its properties can
be edited by tappingon the blue 'Ramp' display - the followingoptions dialogue will appear:
1. Copy ramp
2. Paste ramp
3. Clear Profile
4. Clear ramp
5. Set start ramp
6. Set end ramp
7. Toggle cycle mode
The copy ramp control (1)will copyall the values in the currently selected ramp into memory, these values can be then pasted into another ramp via
the paste ramp control (2).
The clear profile control (3)will reset all ramps to default values and the clear ramp control (4) will reset the currently selected ramp to zero values.
The clear ramp control cannot be used on ramp 1.
The set start ramp control (5) sets the currently selected ramp to be the first in the profile. Use this ifyou wish your profile to start on a ramp other
than ramp 1. The set end ramp control (6) sets the currently selected ramp to be the end ramp of the profile. This can not be applied to ramp 1.
The start ramp of the profile will be highlighted in darkblue and the end ramp will be highlighted in red. When an experiment is in progress the
currentlyactive ramp will be highlighted in light blue.
The cycle mode control (7) will toggle ramp cyclingon and off. When this is on the profile will return to the start ramp once it finishes the end ramp,
whereas when it is offthe profile will finish once it completes the end ramp. When cycle mode is engaged the screen is updated to reflect this.
Note: Aprofile will finish ifit reaches a ramp with a rate setting of0.
Start
ramp
End
ramp
Active
ramp
cycle
mode

© 2017 Linkam Scientific Instruments Ltd.
10
v1.1.0
Once the required values have been entered on each ramp, the start and end ramps configured and cycle mode set as required the profile is
complete and ready to use.
The profiles are automatically saved.
RunningThe Profile
1. Current stage temperature
2. Heating / Cooling rate
3. Temperature Limit
4. Hold time
5. Liquid nitrogen pump speed (only present if an LNP96 is connected to the T96)
6. Start control
7. Heat override control
8. Cool override control
9. Pause control
10. Ramp number display / Ramp options
11. Next ramp control
12. Previous ramp control
13. Settings and Information
14. Volume icon
15. Computer control icon
16. Sample Calibration icon
17. Stage power input display
18. Feature control functions (only present when an LNP96 is connected or a stage with additional features is in use)
Starting
Once the profile value(s)are entered, simplytouch the start button (6)to begin the heatingor coolingof the stage.
The ramp status (10)will change to show which ramp is in progress and the power indicator (17)will show a red bar which rises and falls with the
amount of power fed to the stage. Ifselected the current and voltage will also be displayed.
At anytime the rate limit or time may be changed bysimply touchingon any ofthe displayed values (2,3,4,5)and entering a new value.
Pause heating/cooling or the hold time
Touchingthe pause button (9)during the profile will stop the heating/coolinguntil either the heat (7)or cool (8)button is pressed or the limit is
changed.
If the limit has been reached, touching the pause will stop the time countdown. Touching the pause or changingthe hold time will begin the
countdown.
Touchingthe heat, cool buttons or changing the limit again will exit the hold time and the time value will disappear.
Limit reached
When the limit is reached, the hold time ifset will be shown and will begin to count down. Ifa hold time is zero then the next ramp will be started.
If the next rate value is zero or the stop ramp is reached then the profile will stop.
Heat and Cool buttons
The heat (7) and cool (8) buttons are used to override the profile settings e.g. ifheatingto a limit of 200 and an event occurs you can quickly cool by
simply touching the cool button (8).
LINK or Computer Control
When the T96 and LinkPad are used with a USB or serial connection (for example to the LINK software) then the LinkPad operation is limited to the
stop button only. This is shown on the LinkPad by the computer control icon (15) illuminating. In order to re-enable full LinkPad control simply
disconnect the computer software control (in LINK, select Controller ->Disconnect, and to reconnect computer control in LINK , select Controller ->
Connect)

© 2017 Linkam Scientific Instruments Ltd.
11
v1.1.0
Stage Specific Controls
The LinkPad display will change depending on the stage type connected to it, givingcontrol over the unique functions ofeach specific stage.
Vacuum stages
This section applies to all stages with the ability to hold a vacuum, for example the THMS350V or TS1500V.
The only additional information displayed for vacuum stages with no motorised vacuum valve (MV196)is the current vacuum level, in mBar, mTorr or
kPa. There are no additional controls.
Systems with the motorised vacuum (MV196)valve will see the followingadditional information:
1. Motorised valve status indicators
2. Vacuum level control
3. MV196 (motorised valve)operation
To set the vacuum level tap on the vacuum control (2)and enter the required value.
Mororised valve statusindicators:
These indicators show at a glance the status ofthe valve.
·
The Max indicator (1) will be illuminated blue when the vacuum level is at maximum -i.e. this light will be illuminated when the valve is in its fully
closed position.
·
The Atmos indicator (2)will be illuminated blue when the stage is at atmospheric pressure.
·
The Movingindicator (3)will be red when the valve motor is active, and green when it is idle.
MV196 motorised valve operation
This screen is for controllingthe motorised valve manually, as opposed to via a pre-set ramp. When a ramp is in progress these controls will be
greyed out and inaccessible.
·
tap the Atmos button (1)to set the stage pressure to atmospheric pressure.

© 2017 Linkam Scientific Instruments Ltd.
12
v1.1.0
·
tap the Max vacuum button (2)to set the stage pressure to the lowest it can attain.
·
tap the blue value under Set point (3)to manually set a pressure level and tap the start button (4)to confirm.
Expansion board setup
All vacuum capable stages will have a vacuum expansion board fitted to their T96 controller, which has the followingsetup screen, accessed by
taping on the setup bar and tapingon the blue arrow:
The onlychanges that can be made are to switch the displayed units between mBar, mTorr and kPa. This cannot be changed while a profile is active.
Systems shipped with a MV196 motorised vacuum valve will also be fitted with a motor control expansion board:
No changes can be made on this screen, it is for information only.
Pressure stages
This section applies to all stages that can be pressurised to above atmospheric pressure, IncludingTHMS600PSand CCR1000
The onlyadditional information displayed for pressure stages is the pressure, in Bar or Mpa (1). There are no additional controls.
Expansion board setup
All pressure capable stages will have a pressure expansion board fitted to their T96 controller which has the followingsetup screen, accessed by
tappingon the setup bar and tappingon the blue arrow:

© 2017 Linkam Scientific Instruments Ltd.
13
v1.1.0
The onlychanges that can be made are to switch the displayed units between Bar, MPa and Torr. This cannot be changed while a profile is active.
Note: Linkam recommends the use ofa pressure gauge with these stage types. Ifyou do not have one please contact Linkam Scientific or your local
distributor.
Motorised XY stages
This section applied to stages with motorised XY movement, such as the MDS600.
Additional main screen display items:
When a motorised stage is connected, the main control screen will display the followingadditional information:
1. X axis position
2. Yaxis position
3. MDS motor indicator
4. Stop motion control
5. Manual motor control
The X and Y position values (1) and (2)are the distance in µm from the zero position (which can be set at anyphysical location). Positive values
indicate a position above/right ofthe zero point, whereas negative values indicate a position below/left of the zero point.
The indicator light (3)will be green while the motors are at rest and will switch to red when the motors are in motion.
Tap the stop motion control (4)to stop motor movement at anytime. Heating will not be stopped when this control is used.

© 2017 Linkam Scientific Instruments Ltd.
14
v1.1.0
Manual motor control
These controls are used to move the sample carrier to a specific position.
1. X Axis position control
2. YAxis position control
3. Velocity control
4. Go to zero position
5. Set zero position
The X axis (1)and Yaxis (2)controls move the sample carrier to the position set, which is in µm from the zero position. tap on the control and a
keypad will appear where a position value can be set. tap on the number to enter a new position and tap enter to accept and move to the new
position.
The velocity control (3) adjusts the speed at which the sample carrier will move when using the controls on this screen. It does not affect the joystick
controlled movement or the scanning movement. Speeds can be set by tapingon the blue value and enteringthe required velocity on the resulting
keypad.
The go to zero control (4) will move the sample carrier to the currently set zero position.
The set zero control (5) will set the current position of the sample carrier as the zero point. This will change the XPos and YPos values on the main
screen to zero without physicallymoving the sample carrier.
Note: Ifusinga camera see the section on camera alignment in the optional LINK software manual and for stage alignment please see the manual
for your Linkam stage.
Scanning
Motorised stages in combination with the optional LINK software and Linkam digital camera can 'scan' an area ofyour sample that is larger than the
field ofvision. It does this bytakingan image of the field of vision, movingthe sample to the next field of view in the defined area and takinganother
image. Once all images are taken it will stitch the images together into one large image.
Please contact your local Linkam Distributor for more details.

© 2017 Linkam Scientific Instruments Ltd.
15
v1.1.0
Expansion Board Setup
All motorised stages will have two motor control expansion boards fitted which have the following setup screen (both screens are identical, barring
that one is for X and one is for YAxis movement), accessed by taping on the setup bar and tapingon the blue arrow:
No options can be changed on this screen, it is for information only.
Tensile stages
This section applies to the TSTrange ofstages, which include the TST350, TST350E and TST250V.
Additional main screen display items:
When a tensile stage is connected, the main control screen will display the followingadditional information:
1. Distance between Jaws /Stress value
2. Force being applied /Strain value
3. Current velocity
4. Tensile control panel
5. Manual Tensile Control/Tensile Setup
6. Current jaw status indicators
7. Tensile pause button
Current jaw status (6) shows the current motion status ofthe jaws. If they are currently in motion the movingindicator will be red, and green when
theyare stationary. The open and closed indicators will light up blue when the jaws are in their fully open and closed positions respectively.
Atensile motion pause button (7)will appear when the stage motors are currently in motion. It will appear as a stop symbol when the motors
are started and when taped it will pause the motor operation and change to a start symbol . Tap the button again to resume motion. Heating
will not be paused when this control is used.
Note: Select between Distance/Force and Stress/Strain display in the force tab in option board setup screen. In order for Stress/Strain values to be
accurate you must enter values for sample width and thickness in the Tensile setup screen.
Tensile Control Panel
These controls are used to set the tensile parameters of a ramp.

© 2017 Linkam Scientific Instruments Ltd.
16
v1.1.0
1. Jaw movement direction (opening/closing)
2. Step distance (micrometers)
3. Jaw speed (micrometers per second)
4. Force applied (newtons)
5. Movement type (step/cycle/velocity/force)
·
Step movement moves the jaws apart in discreet steps ofthe distance set.
·
Cycle movement cycles the jaws open and shut bythe set distance.
·
Velocity mode moves the jaws in the specified direction at the specified velocity.
·
Force mode will apply a constant force value to the sample.
Set the tensile parameters ofthe current ramp usingthese controls.
Manual Tensile Function
This screen is for controllingthe tensile functions manually, as opposed to via a pre-set ramp. When a ramp is in progress these options will be
greyed out and inaccessible.
1. Graphical representation of jaw state
2. Zero force control
3. Zero distance control
4. Jaw direction (open/close)
5. Step distance
6. Jaw velocity
7. Force
8. Action type (step/cycle/velocity/force)
9. Start action
Set up your desired action, and tap the start action button (9)to perform the action. the Zero force (2)and distance (3) controls allow you to set the
force and distance readings to zero prior to startingthe action. The movement ofthe tension jaws will be shown on the graphical representation (1)
Tensile Setup
Use this screen to set calibration values for your TSTsystem
1. Proportional force
2. Integral force
3. Derivative force
4. Sample width
5. Sample height (thickness)
6. Calibration distance between jaws
Proportional (1), Integral (2) and Derivative (3)(PID)are values for Constant Force. These values should onlybe changed after discussion with Linkam
Scientific asthey have been found to give a reasonable PID control feedback for force based on a number ofsamples.
Sample width (4)and Sample Height (5)are values allowing the system to accurately calculate Stress/Strain. Ifyou have selected Stress/Strain as a
display output you must enter the values for your sample here.
The calibration distance between jawssetting (6)should NOT be used.
Expansion Board Setup
All Tensile stages will have an motor control expansion board fitted which has the followingsetup screen, accessed by tapingon the setup bar and
taping on the blue arrow:

© 2017 Linkam Scientific Instruments Ltd.
17
v1.1.0
No options can be changed on this screen, it is for information only.
Tensile stages will all also have a force control board.
·
Change the display between force/distance and stress/strain by usingthe display radio buttons (1)
·
Strain can be expressed in two different ways, as "engineering strain"and "true strain". Engineering strain is the ratio ofthe change in length to
the original length, whereas the true strain is similar but based on the instantaneous length ofthe specimen as the test progresses. Choose
between true and engineering strain usingthe strain radio buttons (2). Tick the % box ifyou wish to show the strain in percent
·
The 'Show calibrated values'check box (3)switches the display between the raw output from the transducer, and the calibrated value. The
default is to display the calibrated values.
·
To change the default speed at which the jaws move, tap on the default speed setting (4). A keypad will appear where you can choose a speed.
·
The Calibrate control (5)will open the tensile calibration screen.
Tensile Calibration

© 2017 Linkam Scientific Instruments Ltd.
18
v1.1.0
If the force transducer in the stage is changed for any reason (such as swapping between the 20Nand 200N transducer) a distance calibration must
be performed. To begin this, tap on the 'Length'button, which will pop up a confirmation dialogue:
Make sure the jaws are free of obstructions and tap the OK button to continue, which will return you to the main control screen while the calibration
takes place. This process is automatic, the tensile displays will change to 'Cal'versions while this is happening, as below:
While these readings show 'DCal'and 'FCal'do not operate the stage, the readings will revert to normal once the calibration is complete and the
system is ready for use.
Important note: The Force calibration button is only for use by Linkam Scientific and requires a password to access. Do not attempt to use this
control.
DSC stages
This section applies to the DSC600, DSCX600 and DSC450 stages only.
The onlyadditional information displayed for a DSC600 or DSCX600 stage is the DSC count (1). There are no additional controls. Please see your
DSC600 stage manual for an explanation of DSC counts.

© 2017 Linkam Scientific Instruments Ltd.
19
v1.1.0
The onlyadditional information displayed for a DSC450 stage is the Dsc value in mW (1). There are no additional controls. Please see your DSC450
stage manual for further information.
Please note it is not possible to record data using the LinkPad. The DSC stages should ideallybe controlled using the optional LINK software.
Expansion board setup
DSC600, DSCX600 and DSC450 stages will have a DSC sensor expansion board fitted to their T96 controller, which has the following setup screen,
accessed by tapingon the options bar and taping on the blue arrow:
No changes can be made on this screen, it is for information only.
Humidity control
This section applies ifyou have a Linkam RH95 humidity controller attached to your system.
Additional main screen display items:
When an RH95 is attached to the T96 controller, the LinkPad main screen will display the followingadditional items:

© 2017 Linkam Scientific Instruments Ltd.
20
v1.1.0
1. Humidity sensor temperature
2. Relative humidity reading
3. Relative humidity control
4. Manual RH95 control
·
The humiditysensor also contains a temperature sensor. The RhTemp display (1)shows the current temperature at the humidity sensor in
degrees Celsius.
·
The Rh reading (2) shows the current humidity ofthe chamber as a percentage.
·
The desired Rh% for the current ramp can be set usingthe RH control (3).
Manual RH95 Control
This screen provides information on the current status ofthe RH95 and manual humidity controls. These controls can only be used when the system
is inactive, if there is a ramp in progress theywill be greyed out and inaccessible.
1. Graphical display of the RH95 system status
2. RH95 water bottle temperature
3. Heater wire power level.
4. Drying time display
5. Swap time display
6. RH% manual control
7. Start button
8. Drying control
·
The graphical display(1) will update to show which desiccant tube is currently dryingout byhighlighting it in red, and a blue arrow will appear
next to the currentlyactive tube.
·
The water temperature display (2) shows the temperature of the water bottle in the RH95.
·
The humiditysupply tube has a heater wire inside it to maintain the air temperature. The power display (3)shows the power beingput into this
heater wire as a percentage ofmaximum.
·
The dryingtime display (4)shows the amount of time remainingon the current drying cycle, which is the currently inactive desiccant tube being
dried out.
·
The swap time display (5)shows the amount of time remaining before the active tube is swapped, and a dryingcycle started on the previously
active tube.
·
The Rh setpoint control (6) is used to manuallyset a Rh% without linking to a heating or cooling ramp.
·
The start button (7) will begin changing the chamber humidity to that set in the Rh setpoint control.
·
The dryingcontrol (8)begins a dryingcycle. This flows warm air through both desiccant tubes to dry them out. This action should be performed
after you first receive your RH95 system.
Table of contents
Other Linkam Scientific Instruments Controllers manuals
Popular Controllers manuals by other brands
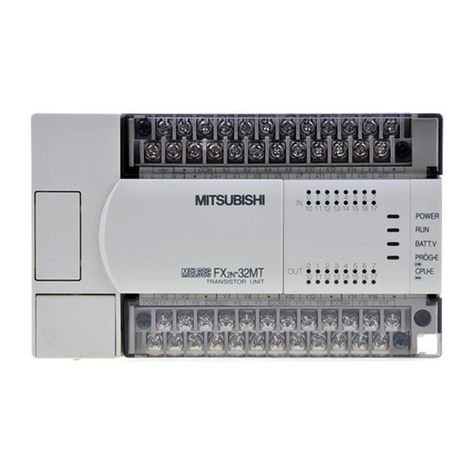
Mitsubishi Electric
Mitsubishi Electric MELSEC FX Series Structured programming manual
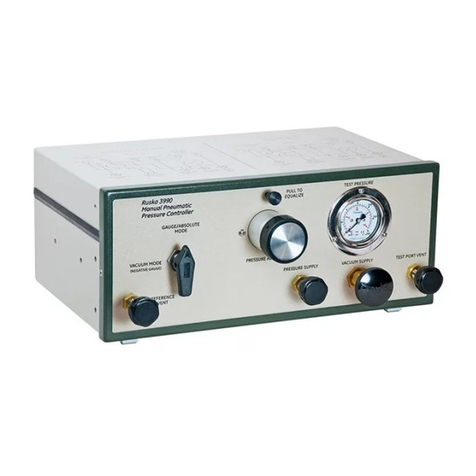
Fluke
Fluke CalPower RUSKA 3990 Series user manual
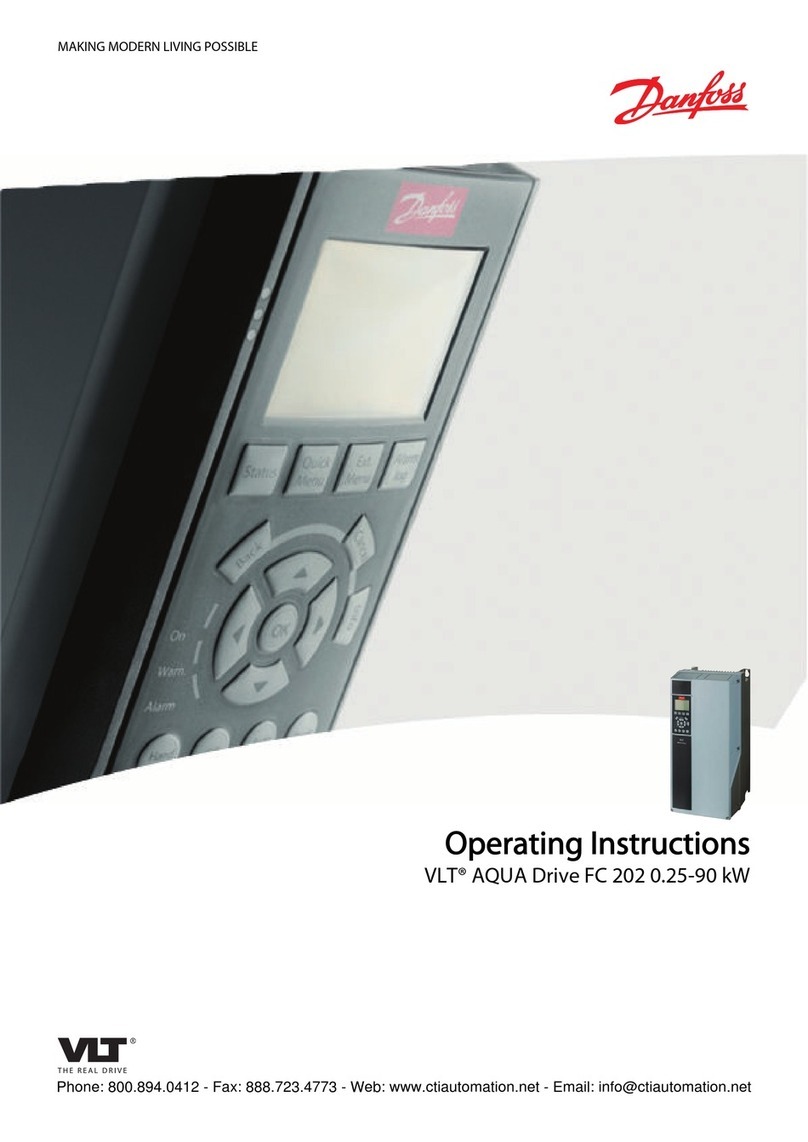
Danfoss
Danfoss VLT AQUA Drive FC 202 operating instructions
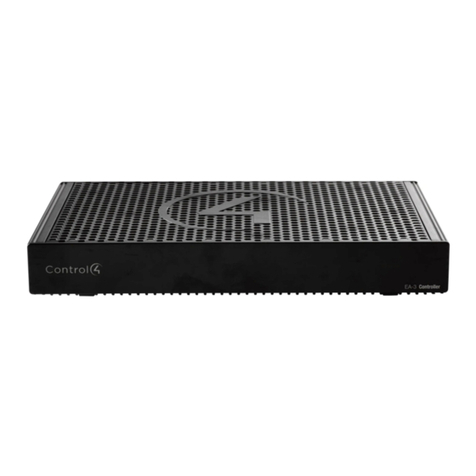
Contro l4
Contro l4 C4-EA3-V2 installation guide
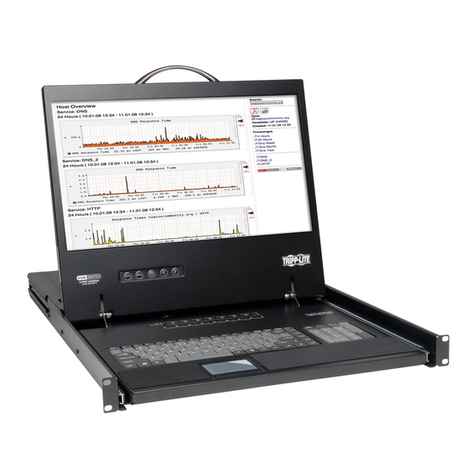
Tripp Lite
Tripp Lite NetController B040-008-19 quick start guide
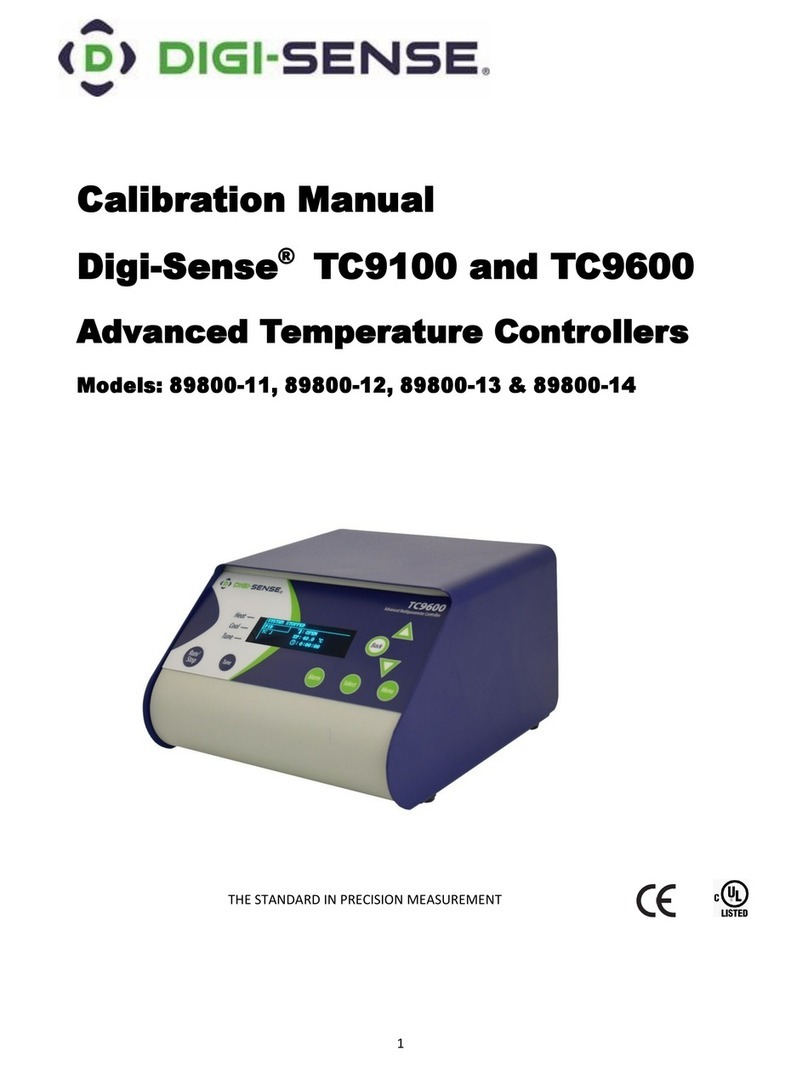
Digi-Sense
Digi-Sense TC9600 Advanced Calibration manual