Power Max AKD58-50 User manual

Page 1 of 16
Automatic sewing machine Servo controller instructions
Preface
CAUTION:
Please read this manual carefully, also with
related manual for the machinery before use the
controller. For installing and operating the
controller properly and safely, qualified
personnel are required.
This product is designed for specified sewing machines and must
not be used for other purposes.
If you have any problem or any comment, please feel free to
contact us.
Safety Instruction
(1) All the instruction marked with sign must be absolutely
observed or executed; otherwise, personal injuries or risk to the
machine might occur.
(2) This product should be installed and operated by persons
with appropriate training only.
(
3
)
Before connecting power supply cords to power sources, it’s
necessary to make sure that the power voltage is in the range indicated
on the product name plate.
(4) Make sure to move your feet away from the pedals while
power on.
(5) Turn off the power and remove plug prior to the following
operations:
■ Connecting or disconnecting any connectors on the control box;
■ Repairing or doing any mechanical adjustment;
■ Threading needle or raising the machine arm;
■ Machine is out of work.
(6) Make sure to fasten all the fasteners firmly in the control
boxes prior to the operation of the system.
(
7
)
Allow an interval of at least 30 seconds before repapering the system
after power off.

Page 2 of 16
Brown(AC220V)
Blue(Ineutral
wire)
Yellow green
(Ground wire)
Control Box cable
ControlBox Control box cable plug
Yellow green
Brown(AC220V)
Blue(Ineutral
wire)
Yellow green
(Ground wire)
(8) Repairs and maintenance work may be carried out by special
trained electronic technicians.
(9) All the replacement parts for repairing must be provided or
approved by the manufacturer.
(10) The controller must be firmly connected to a properly
grounded outlet.
(11) Ground wire installation (special attention).
CAUTION:
Be sure to connect the controller to a properly grounded
outlet. If the grounding connection is not secured, you
may run a high risk of receiving a serious electric shock,
and the controller may operate abnormally.
1. Basic parameters
2. Secure wiring and grounding
The system is powered and ready for use, you must ensure that the AC input is
securely grounded (Figure 2-1). System grounding wire is yellow and green lines, make
sure the ground wire securely connected to the machine head (such as connecting to the
head of the screw), in order to ensure the safe use, and prevent abnormal situation
Fig.2 -1 Controller power wiring diagram
Controller Type AKD58-50
Max. Sewing Speed(r/min)7000
Voltage Range AC 220±20% V 50/60HZ
Output Power 550W
Max. Torque 3.5Nm
Environment 0℃~40℃

Page 3 of 16
1
2
3
4
5
6
7
8
9
10
1
2
3
4
5
8
9
10
11
12
6
7
13
14
传感器
Sensor
电机电源
Motor Power
脚踏板
Pedal
电机编码器
Encoder
操作面板
Operation Panel
灯
Lamp
翻抬开关
Safety SW
机头电磁铁
Machine Head
Sclenoid
抬压脚电磁铁
Foot Lifter
CAUTION
Ensure all power cord, signal wire and grounding wire not be
pressed by other matter or over-twisted ,and not be too close to
belt and belt wheel, keep 3cm-distance for safety.
A 1Ф/220V power from a 3Ф/380V Power source Connection (See Fig.2-2):
CAUTION
If the system have no Neutral point, then this servo motor is not
suitable for this connection.
Fig. 2-2 Three-phase power wiring diagram
3. Definition of controller interface
Connections between control box and other accessories are illustrated in Fig.3-1.
Plug these connectors into the corresponding sockets in control box.
Fig.3-1 The controller of interface schematic diagram

Page 4 of 16
* The drive ability of the LED jack:
Which the rated current is100mA and the rated voltage is 5V, the output current is adjustable.
Recommendatory LED diode parameter as follows:
VF:Min. = 3.0V,Max. = 3.6V (test condition IF = 20mA);
Peak Forward Current:Max. = 80mA;
Continuous Forward Current :Max. = 35mA
4. Operation Panel Instruction
4.1 Appearance and key
The front operation panel(See Fig4-1)is provided with a status indicator divided、
LCD display area and keys operation area.
Fig.4-1 Automatic bag sewing Chinese panel display
There are13 keys in the key operation area that used to set the over lock sewing
machine kinds of operation control parameters. There are 4 display lights at the top of
the Panel that used to display real-time it operating status. F-SENSOR lights and
B-SENSOR lights indicate front edge sensor and back sensor to status, light is lit indicate
cloth cover sensor, light is not lit indicates that the sensor is not blocked; RUN light is lit
indicates the rotation of the motor running; SAFE light is lit indicates a safety switch open.
Table 2 shows function of each key.
Table2: Following form is the instruction of each key:
No KEY Description
1 Main menu key:Return to the main interface, or work with other key.
Caution: Please check if all connectors match or not, pins
are found right definition or not.
Status Indicator
LCD Display Area
Key Operation Area

Page 5 of 16
2
Automatic mode selection keys: The sensor is open, pressed in succession followed by
optional automatic or semi-automatic mode.
3
Suck selection keys: When sewing is selected suction mode, continuous press are optional
before suction, back suction, before and after suction ,and suck the closure of four modes.
4 Speed selection key: To set the maximum sewing speed.
5
Trimming selection key: When sewing is selected trimming mode, continuous press are
optional front trimming, back trimming, front and back trimming ,and trimming the closure of four
modes
6
Edge mode selection key: When sewing is selected working mode of mop wheel, continuous
press are optional before mop wheel, rear mop wheel, before and rear mop wheel ,and the mop
wheel closure of four modes.
7 Save to determine key: To save the parameters set.
8 Up arrow keys: When setting parameters, increasing the value at the cursor.
9 Down arrow keys: When setting parameters, decreasing the value at the cursor.
10
Left arrow key: When setting parameters, move the cursor to the left; Front trimming length
shortcuts.
11
Right arrow key: When setting parameters, move the cursor right; Back trimming length
shortcuts.
12
Machine headlight key: To adjust machine headlight brightness, followed by optional 0-4
consecutive press.
13
Sensor selection key: To open or close the electric eye. Electric eye closure enters full manual
mode, the sensor does not work; to open electric eye sensor is working, and then enter the
semi-automatic mode or fully automatic mode.
14 Speed selection key: To set the maximum sewing speed.
15 Special function keys: User-defined extensions settings.
4.2 The main interface and function key setting
The control panel is correctly inserted corresponding interface electrical control box;
confirm security turn on the power. Boot for about 2 seconds, the LCD will display the

Page 6 of 16
main interface, shown in Figure4-2. If it is not a normal display and a fault alarm, please
refer to Chapter 3 false alarms table, deal with the corresponding failure or contact the
manufacturer.
Fig. 4-2 System main interfaces
In Fig. 1-2 system main interface, press the key, then displays the current
settings for automatic sewing machine working status, shown in Fig.4-3.
Fig. 4-3 the current operating mode
Wherein, the icon shows electric eye switch status, the icon shows the current
trimming mode, the icon shows the current mop wheel mode, the icon shows the
current suction mode. Press the key to return to the main interface. If you do not
operate for about 10 seconds, the system will automatically return to the main interface
mode.
In the main interface (show to fig.1-2), respectively press the function key
(, , , , , ), you can change corresponding to the operating mode. Press
the key; you can set the maximum operating speed of the sewing machine.
Pass and keys to move the cursor, and keys to change the number. After it
is set, press the key to exit and return to the main interface.
4.3 Work mode setting
Automatic sewing machine system according to need can work in manual mode,
semi-automatic mode, automatic electric control mode and automatic foot control mode.
Wherein the manual mode entirely by foot pedals to control the sewing machine
operation, this time electric eye closed, detection and automatic trimming function is
invalid; semi-automatic mode is defined by the sensors and pedal to control sewing
machine operation, this time electric eye open, pedals and trimming are valid; Automatic
power control mode is completely controlled by the electric eye sensor automatic sewing
machine presser foot, start, and stop trimming cycle operation; automatic mode through
POWERMAX AKD58
Auto -- EC
--ON F-ON
- OFF F-ON

Page 7 of 16
the foot control electric eye sensor control automatic presser foot, by the foot pedal
before starting sewing. During sewing foot pedal will be suspended after the sewing step
before proceeding to continue automatic sewing processes. Automatic mode is entirely
controlled by the electric eye sensor to sewing machine is running automatically, this
time electric eye open, pedals do not control the sewing machine, the timing of each
function only by the electric eye automatic detection and control.
Table3: overlock sewing pattern corresponding relationship
Sewing mode Electric eye on or off fully automatic mode selection
full manual mode off invalid
semi-automatic on semi-automatic
automatic electric control on automatic electric control
automatic foot control on automatic foot control
Example: If the current to full manual mode, the actual status at this time electric eye
switch is off, the main interface shown in Figure 4-4.
Fig. 4-4 full manual system main interface
Press the key, then displays the current state of electric eye switch, shown in Figure
4-5.
Fig.4-5 electric eye switch off Fig.4-6 electric eye switch on
Press the key again, electric eye switch immediately opens, displaying electric eye
switch is turned on, as shown in Figure 4-6, then press the key to confirm automatic
sewing mode, if the current mode is automatic sewing mode, shown in Figure 4-7; when
the current sewing mode is semi-automatic mode, shown in Figure 4-8.
Fig.4-7 full automatic mode Fig.4-8 semi-automatic mode
In the current electric eye switch remains open in the case, press the key, in fully
-- SEW MODE --
Semi-Auto
-- SEW MODE --
AUTO – FC
--SENSOR SW--
ON
--SENSOR SW--
OFF
POWERMAX AKD58
Manual

Page 8 of 16
automatic and semi-automatic mode switching. After it is set, press the key to exit.
4.4 The maximum speed setting
Press the key, then the system will run set to the current maximum speed shown
in Figure 4-9.
Fig.4-9 system current maximum speed Fig. 4-10 set system maximum speed
Then you can use the keys to move the cursor, keys to change the number, the
maximum speed is displayed after the change shown in Figure 4-10. After setting, press
the key to exit.
4.5Front and back trimmings length shortcuts of adjustment
In the main interface, the 、key can be respectively front and back trimmings
length shortcuts adjustment, 、key to change the numbers, which will be effective
simultaneously. As shown in figure 4-11.
Fig. 4-11 Front and back trimmings length setup
4.6 Sensor sensitivity automatic detecting function
Before using this function, please make sure that the bed is no cloth and all sensor
surface with no dust and thread occlusion. Then in the main interface system (which is
valid only in the interface), long press the key interface will jump, release it to enter
the sensor sensitivity function of automatic detection, As shown in figure 4-12.
Fig. 4-12 The sensor sensitivity of automatic detection enter to interface
---- FTRIM LEN ----
0 9
Please put the fabric, Front
and back the sensor cover!
---- MAX SPEED ----
4 5 0 0
---- MAX SPEED ----
3 0 0 0

Page 9 of 16
Please follow the prompts the fabric placed on the bed, and completely covers front
and back sensor, system according to the fabric thickness shows the sensitivity of
maximum and minimum value, such as a fabric is shown below:
Fig. 4-13 The sensor sensitivity of maximum and minimum value
After successful completion, the system will prompt the user to remove cloth, can
work normally. The following:
Fig. 4-14 The sensitivity automatic of success
4.7 The fabric suction mode of quick adjustment
Press enter to suction mode setting, The fabric suction mode quick adjustment.
As shown in the figure below (in an air suction mode are available):
Fig. 4-13 The suction mode setting interface
At this time, press 、,key can enter to fabric suction of quick adjustment
interface wind patterns, such as the display:
Fig. 4-14 The fabric suction mode interface
After entering, through 、key to change the numerical suction mode of different
fabric selection, a total of three species, such as:
--Fabric suction mode--
Fabric long suction 2
-- suction set --
Front suction open
Automatic detection of
success , Remove the cloth!
Front: 0512 ~~ 0968
Back:0536 ~~ 1024

Page 10 of 16
Fig. 4-15 The fabric suction of three species
5. Advanced Features
5.1 Conversion between the Chinese and English
In the main interface, press key + key to complete the switch in English, as
shown in Figure 5-1 and 5-2, press key + key to switch back to the Chinese interface.
Fig.5-1 chinese interface Fig.5-2 english interface
5.2 Technicians parameter settings
In the main interface under, press key + key, to enter the technician parameter
setting's password interface, shown in Figure 5-3.
Fig.5-3 password interface
Technician’s parameter password can press and keys to move the cursor,
press and keys to change the number, the initial password is 0000. Enter the correct
password; press the key to enter the machine repair parameter settings shown in
Figure 5-4.
Fig. 5-4 the machine repair parameter settings
Figure 2-4 shows the current system parameter list. The before two digits of the
parameter number, the last four digits of the parameter value. Text below the parameter's
instructions. You can press and keys to move the cursor, press and keys to
change the number, select the number of different parameters and setting the
corresponding parameter values. If you need to save and exit, press key, otherwise
press key.
--Fabric suction mode--
Fabric long 2
--Fabric suction mode--
Run to full 0
--Fabric suction mode--
Fabric interval 1
0 0 0 0 0 3
Auto Foot Mode
PD: 0 0 0 0
Tech Paras Set
POWERMAX AKD58
Auto -- EC
POWERMAX AKD58
全自动-- --电控 +

Page 11 of 16
5.3 Restore factory settings
In the main interface, press key+ key, enter the correct password, press key
to enter the technician parameters. Select the 62 parameters and corresponding values
to 2008, shown in Figure5-5.
Fig.5-5 Parameter reset to factory
In Figure 5-5 interface, press for two seconds until the screen show in Figure 5-6,
wait for about 5 seconds, the buzzer rang long after the recovery is complete(Hint: the
recovery process should not turn off the power or unplug the panel!). After the completion
of the operation is proposed to re power on reset time.
Fig.5-6 Parameter reset to factory
5.4 Automatic test mod
In the main interface press key+ key to enter the automatic test setup
interface, you can press and keys to switch running time, stop time, test time,
press and keys to change the corresponding figures. Running time, stop time in
units of 0.1 seconds, the unit test time is 10 minutes.
Fig.5-7themaininterface Fig.5-8automatictestparametersettinginterface
In Figure 5-8 interface, press key+ key again, which enters the automatic
testing process, shown in Figure 5-9, then light foot pedalling to start the automatic test.
Fig.5-9 automatic test run interface
To exit test mode to run automatically, you can press key+ key, the motor
stops running, the automatic end of the test and return to Figure 5-8 interface, press
AUTO TEST STATU
TESTING!!!
AUTO TEST PARA
Run Time: 30
POWERMAX AKD58
Auto -- EC
Restoring !!!
Default Paras
6 2 2 0 0 8
Factory Reset
+

Page 12 of 16
the key again to return to the main interface.
5.5 Monitor Mode
In the main interface, press key+ key to enter monitor mode, you can view the
current system parameters, the specific content shown in Table4.
Table4: monitor mode parameter
Parameter No. Comment
1 0 Counter stitches
11 Counter trimming
2 0 DC Bus Voltage
21 Motor speed
2 2 One phase current
2 3 Initial angle
2 4 Mechanical angle
2 5 Sampling value of pedal voltage
2 6 Motor/machine head run ratio
2 7 Motor total run time
2 8 Sampling value of potentiometer at machine head
2 9 DSP Software version number
Monitor
status
3 0-3 F History Error Code Recorder 8
6 Technician parameter setting
In the main interface, key+ key to enter the technician parameters, Table 5 can view and
modify the parameters, mainly the system speed, a variety of automatic feature set, pedal settings and
parameters transfer functions.
Table 5: Technician mode parameter:
Parameter
byte Default Rang Comment
0 0 1 0-3 Auto foot lifter setup:0 off ; 1 Before foot lifter; 2 Back foot lifter;
3 Before and Back foot lifter
01 0 0/1 Speed mode: 0 automatic; 1 pedal control speed
speed 0 2 0 0/1 The needle stop position: 0 up needle position; 1 down needle
position

Page 13 of 16
Parameter
byte Default Rang Comment
0 3 0 0/1 Foot lifter setup when the needle stop in the middle position: 0
off; 1 automatic foot lifter
0 4 1 0/1 Manaul stitch suck mode: 0 off;1 on
0 5 3000 2 0 0-4 200 Automatic sewing speed
0 6 5000 4 0 0-6 5 0 0
Maximum sewing speed
0 7 1 0 /1 Semi automatic continuous sewing:
0 automatic stop back trimming ; 1 Tread the pedal for sewing
0 8 2 0 /1 / 2
Semi automatic constant speed:
0 Full constant speed; 1 The pedal control it when the two
sensor is effectively at the same time; 2 Full pedal control
0 9 200 100-800 Minimum speed
0 A 300 100-800 Treading needle speed (retain)
1 0 20 0-50
Front sensor operation and effective number of stitches (front
sensor sensor automatically go pin number, completed after
the sensor still no sense if you stop pin)
11 20 1-50
Number of needle between the two sensors (front sensor
signal disappeared, after the sensor is sensed to continue
sewing needle;
1 2 2 1-50 The before Trimming delay needle (FB = 11 signal start count
needle)
1 3 9 1-50 The back Trimming delay needle (FB = 0 0 signal start count
needle)
1 4 1 1-50 The before suction start needle (FB = 1 0 signal start count
needle)
1 5 0 0-5000 The before suck delay time (ms)
1 6 1 1-50 The back suction start needle (FB = 0 0 signal start count
needle)
17 300 100-5000 The back suck off delay time(ms)
Automatic
function
setup
1 8 1 0-1 Suck mode: 0 when the motor is running long suction; 1
automatic mode suction

Page 14 of 16
Parameter
byte Default Rang Comment
1 9 200 100-5000 When it is running suction of delay time, long suction can be
back stepped or manual trimming Close
1 A 3000 0-5000 Automatic mode is completed, parking, needle of number
running speed
1 B 10 10-5000 Start sewing delay time (Retain)
1 C 10 1-99 Stop delay pins ( rear sensor signal disappeared after count
sewing needle number,FB=00 signal begins to count )
1 D 10 0-99 Automatic mode is completed, parking, rear number of stitches
1 E 500 0-5000 Automatic mode is completed, parking, walking up the end of
the solenoid valve A new opening time ms
1 F 500 0-5000 New solenoid valve A is closed,new solenoid valve B is open ,
open time ms
2 0 10 1-1000 The before sensor response time
21 680 0-1024 The before sensor sensitivity(According translucent fabric
manually adjust the sensitivity of sensor)
2 2 680 0-1024 The back sensor sensitivity(According translucent fabric
manually adjust the sensitivity of sensor)
2 3 280 10-2000 The before foot lifter retention time(FB=10singal begins to
count)
2 4 1 1-2000 The back foot lifter start up delay time(back trimming stop ,it
begins to count )
2 5 3 1-600 Foot lifter protection time 100ms
2 6 30 20-800 The before foot lifter stop of delay time(ms) (press down foot to
start sewing the interval)
Peripheral
function
setup
27 0 0/1
Automatic mode recognized work cycle:
0: After trimming before halfway out of the cloth, not after
trimming action, once again put the cloth will not be executed
before the cut line, until after the cut line, be considered a work
cycle ends.

Page 15 of 16
Parameter
byte Default Rang Comment
1:Regardless of whether the thread trimming after completion,
as long as the cloth out, are recognized as a work cycle. Again
into the fabric, which began a new working cycle and run
before trimming
2 8 0 0/1 It is running manual trimming:
0 off; 1 on
2 9 1 0/1 Safety switch:
0 off; 1 on
2 A 70 1-1000 Trimming keep start time
2 B 20 1-20 Acceleration sensitivity ( direct drive head can be set to a
larger value; belt drive can not be set too big, otherwise
2 C 20 1-20
Deceleration sensitivity ( The direct drive head can be set to a
larger value; The belt drive can not be set too big, otherwise
vibration, noise is big. The parameter does not affect the motor
output)
2 D 1000 200-1200 The medium speed value ( RPM )
2 E 50 25-200 The low speed value (RPM)
2 F 250 20-600 Full manual mode foot lifter delay time ms
3 A 100 0 ~800 Pedal press foot lifting confirm time
3 B 1 0/1
Run to up needle position after Power on:
0: no action
1: action
3 C 0 0/1/2/3
Special operating modes:
0: Operator mode (common functions)
1: Simple sewing mode (no needle stop up or down)
2: Measured motor initial angle (no need to remove the belt)
3: Calculate the gear ratio mode (requires needle sensor, and
can not take off the belt)
operational
control
3 D 0 0~31 Torque boost up at low speed :
0:no action 1~31:31 levels Torque boost up

Page 16 of 16
Parameter
byte Default Rang Comment
3 E 1 0/1
Stop pin mode:
0:Constant speed tackle mode (in the belt transmission,
Parking is not precision) 1:back pull mode(PMX)
6 0 0 It is running time reset
61 1 0/1/2
Translating Parameter
0:no action
1:Download parameters( the panel will parameter from panel
to controller )
2:Upload parameters ( the panel will parameter from controller
to panel)
6 2 - - Restore storage parameter(Only restore parameters to
operators, and vendors and maintenance )
Operation
6 3 0 1/2 Backup current parameter as user parameter for restore
(restore)
7 Recovery processing and maintenance
Table 6: Error handling and maintenance
error
code meaning error
code meaning
01 hardware overflow 11 machine head needle positioning failure
02 software overflow 12 motor original angle checking failure
03 system under-voltage 13 Motor HALL failure
04 over-voltage when the machine is off 14 DSP Read/Write EEPROM failure
05 over-voltage in operation 15 Motor over-speed protection
06 solenoid circuit failure 16 Motor reversion
07 electrical current checking circuit failure 17 HMI51 Read/Write EEPROM failure
08 locked motor roller 18 Motor overload
09 brake circuit failure 20 Lack of oil alarm
10 HMI communication failure 21 Sensor error
386P0116C
2014-2-19
Table of contents
Other Power Max Controllers manuals
Popular Controllers manuals by other brands
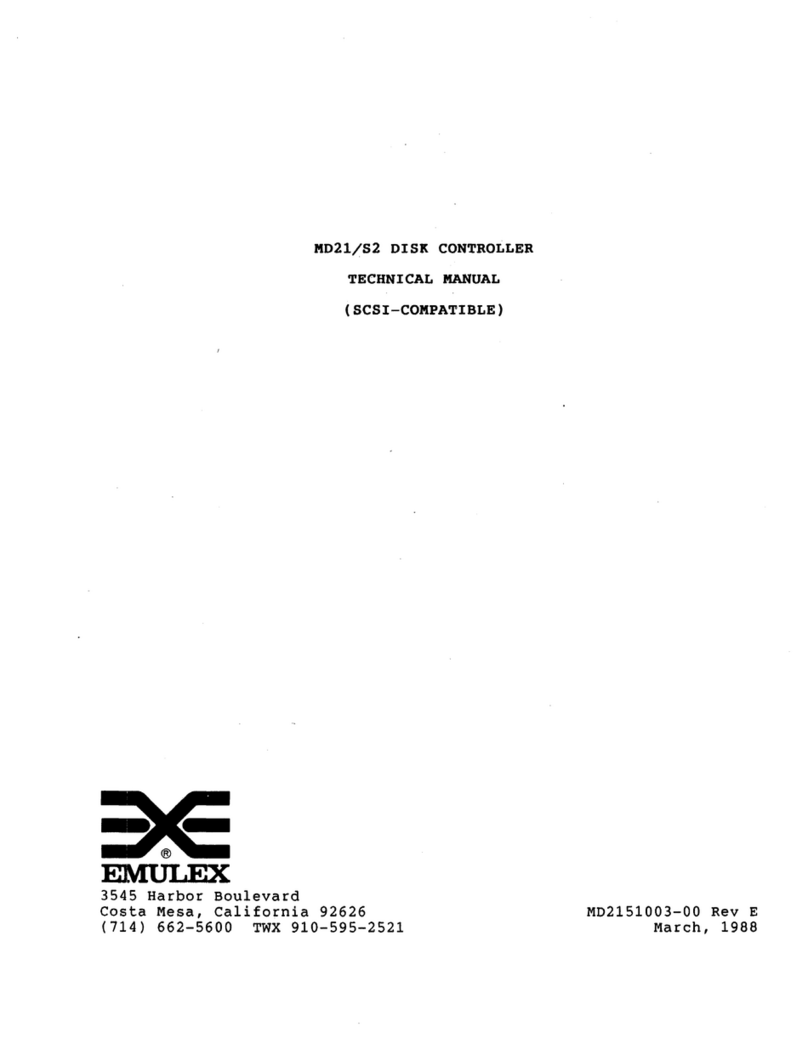
Emulex
Emulex MD21/S2 Technical manual
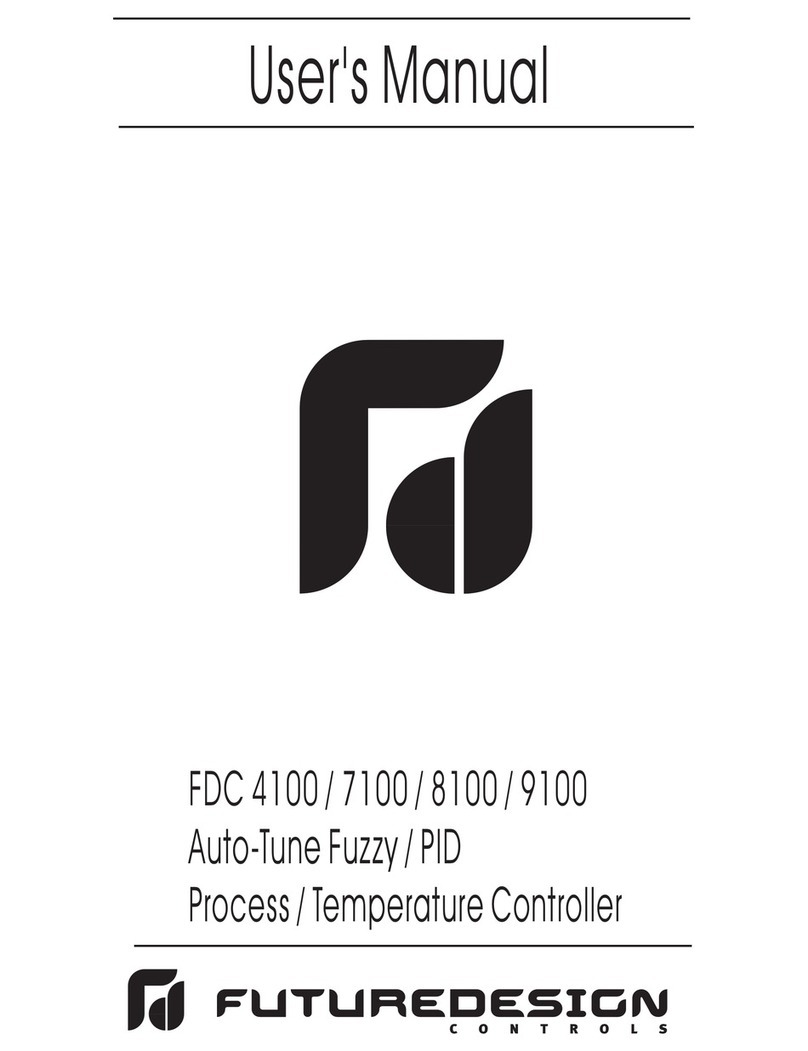
Futuredesign controls
Futuredesign controls UM100 user manual
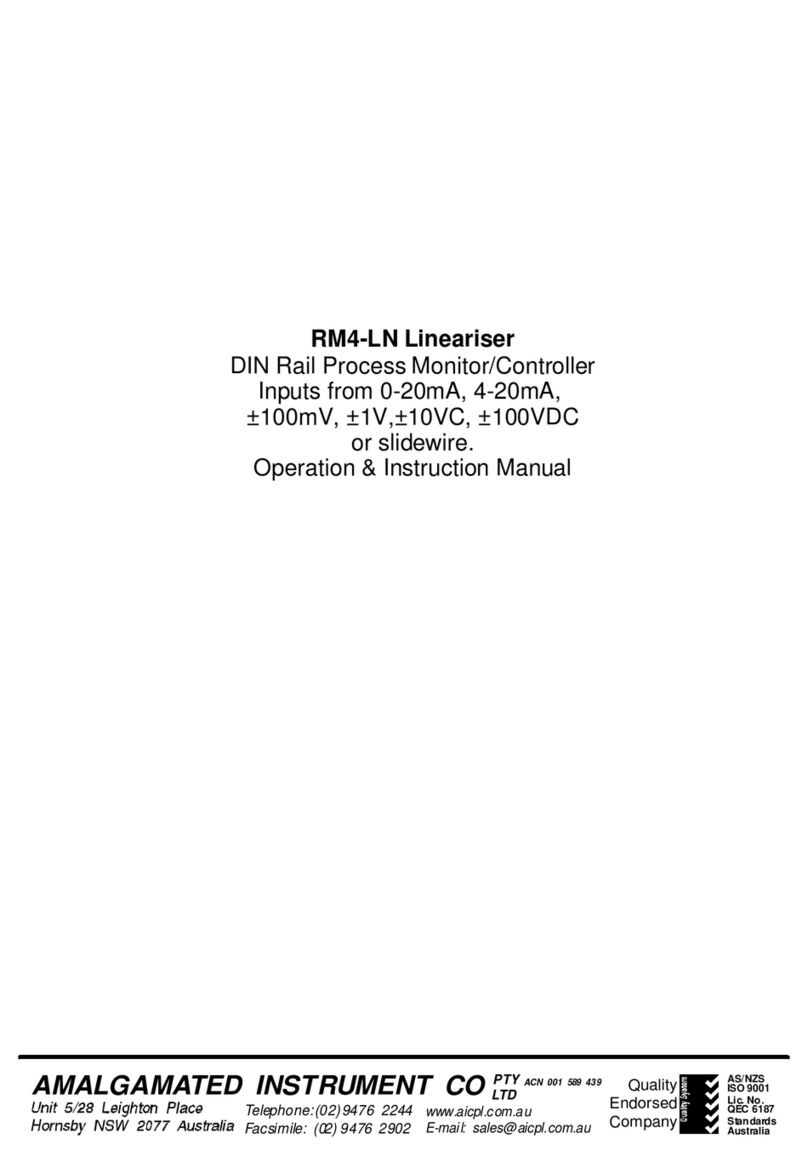
AMALGAMATED INSTRUMENT
AMALGAMATED INSTRUMENT RM4-LN Operation & instruction manual
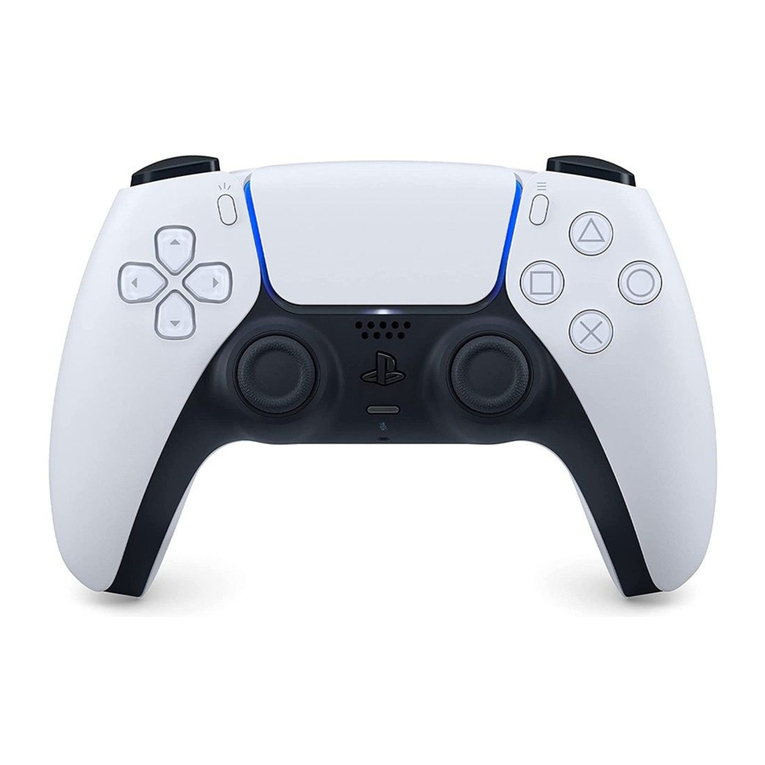
Sony
Sony PlayStation DualSense CFI-ZCT1G user manual

AQUARAY
AQUARAY SmartControl 8 operating instructions
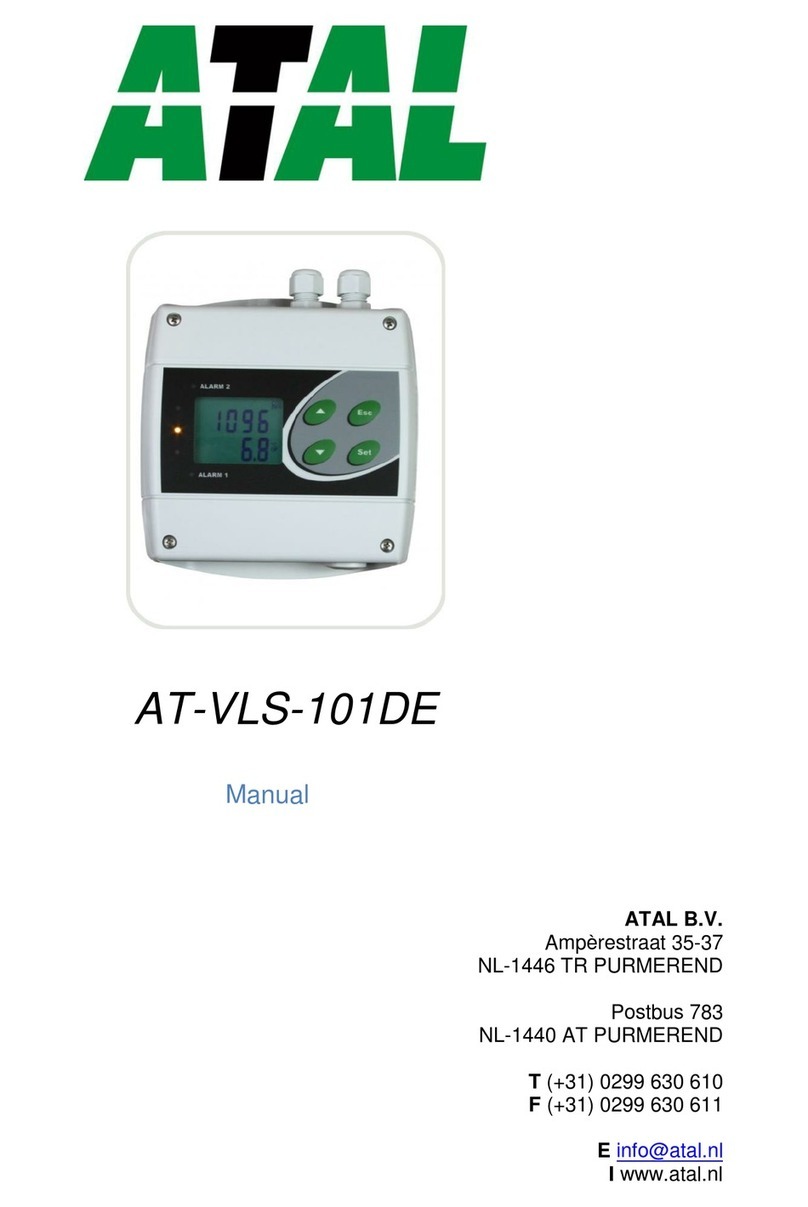
Atal
Atal AT-VLS-101DE quick guide