PowerBox Systems MERCURY SR2 User manual

INSTRUCTION MANUAL
10/2022
P0WErB0x
mErcury Sr2

2PowerBox-Systems − World Leaders in RC Power Supply Systems
Dear PowerBox customer,
Congratulations on your new PowerBox power supply unit! The PowerBox Mercury
SR2 is your rst choice when you need a small, high-performance power supply unit
with maximum functionality. All the features which are usually the preserve of the
larger power supply units are present in the compact PowerBox Mercury SR2: iGy-
ro, servo matching, unrestricted channel assignment and even a door sequencer: it
really is a complete system!
The PowerBox Mercury SR2 provides 16 freely assignable outputs with servo
matching, i.e. the travel of each channel can be adjusted at ve points. If you y mo-
dels with large control surfaces, in which individual control surfaces are actuated
by two servos, the unique auto-match function can be used to match both servos to
each other accurately in a matter of seconds.
The integral iGyro software requires a sensor unit in the form of an iGyro SAT; with
this it can address and adjust three aileron, three elevator and three rudder func-
tions individually. The Setup Assistant simplies the initial adjustments to the gyro
system, reducing the time required to just a few minutes. The rst time the system
is used, the Assistant gathers basic information regarding wing and tail format and
the vector control system - if present. A complex model matrix then works in the
background, calculating which servo needs to be connected to which output, at
the same time linking the corresponding gyro function. A wide range of additional
Expert settings offers total freedom, enabling you to ne-tune the gyro system to
your particular requirements.
In addition the GPSIII or PBS-TAV (True Airspeed Vario) can also be connected to
the FastTrack input, making it possible to vary gyro gain according to airspeed. All
GPS or TAV information is even available for telemetry at the transmitter!
The PowerBox Mercury SR2 supplies a regulated output voltage which can be set
to 6.0V or 7.8V. The two voltage regulators offer generous capacity thanks to the
machined aluminium heatsink on the top and bottom surfaces, enabling the unit to
cope effortlessly with the current-hungry servos used in 3D machines.
The integral door sequencer is capable of controlling one undercarriage system and
up to three wheel doors. If the Setup Assistant is used, it takes just a few minutes
to learn the end-points of door travel, while three pre-dened modes cover the vast
majority of undercarriage processes. Once initially set up, the timing of the process
can be ne-tuned manually to any values you wish.

www.powerbox-systems.com 3
For PowerBox and Jeti pilots it is possible to control and adjust virtually every* as-
pect of the PowerBox Mercury SR2 from your transmitter! Full telemetry for battery
and receiver data is present for all supported systems
*With the exception of the door sequencer and Setup Assistant
.
FEATURES
+ 16 channels
+ High-performance battery backer with high continuous load capacity
+ OLED screen, legible in sunlight
+ Bi-lingual menu system
+ Consistent duplication of all power electronics
+ Redundant electronic switch
+ Servo matching for all 16 outputs
+ Auto matching function
+ Door sequencers with Setup Assistant
+ The latest integrated iGyro technology, using the iGyroSAT as gyro sensor
+ Nine independent gyro outputs for: 3x aileron, 3x elevator, 3x rudder
+ Individual gain control for all nine gyro outputs
+ Special regulatory algorithm for xed-wing models
+ System detects all transmitter mixers
+ Four selectable output voltages: 6.0V or 7.8V
+ Fast basic setup procedure using the sophisticated Assistant
+ Optional GPSIII or PBS-TAV for speed-dependent gyro compensation
+ Telemetry data for PowerBox P²BUS, Futaba S.BUS2, Jeti Ex-BUS, Spektrum SRXL2,
Multiplex M-Link, JR DMSS and Graupner HoTT
+ Transmission of battery, receiver and GPS*/TAV* data
+ Virtually all features can be controlled from PowerBox and Jeti transmitters
+ Selectable servo frame rate: 12ms, 14ms, 16ms, 18ms
+ Servo feedback current suppression
+ High-performance machined heat-sink for optimized heat diffusion
+ Machined, anodized aluminium switch and screen case
+ Compact dimensions
*with GPS III

4PowerBox-Systems − World Leaders in RC Power Supply Systems
1.INITIAL INSTALLATION: GENERAL SEQUENCE OF OPERATIONS
When installing the unit, it is important to keep to the standard sequence described
below, and adhere to the subsequent setup stages, as this ensures that your instal-
lation of the PowerBox Mercury SR2 will be swift and problem-free. The individual
points are explained in full in the remainder of these instructions:
- Mounting the PowerBox, switch and screen
- Connecting the receiver and batteries
- Settings in the Basics menu
- Setting up all the functions at the transmitter
- Carrying out the Setup Assistant
- Carrying out the Door Sequencer Assistant 4
- Assigning all remaining functions in Output Mapping
- Setting up all control surface travels, ight modes, Dual-Rate, Expo etc. at the
transmitter
- Using Servo Matching to equalize servos operating in parallel
- Learning the stick end-points in the iGyro menu 5
- iGyro set-up ight 5
- Fine-tuning the iGyro 5
4 entfällt ohne Fahrwerkstüren
5 entfällt ohne Gyro
2.INSTALLATION, CONNECTIONS
a) Mounting
The PowerBox Mercury SR2 should be mounted in the model on a robust sub-struc-
ture using the four screws, rubber grommets and brass eyelets supplied in the set.
The installed location is not important, but if an iGyro SAT is to be used, the sensor
must be installed perpendicular to the model’s centreline. Ideally the TFT screen
should be in a clearly visible location. The bright screen lighting makes it easy to
read even in sunshine, so no special provisions have to be made here. The screen is
connected to the socket marked Display on the side of the PowerBox.
The switch should be mounted in the fuselage side. As with previous units, a woo-
den doubler should be glued to the inside of the switch aperture - especially if the
fuselage is made of GRP - in order to avoid subjecting the switch to powerful vi-
bration. The set includes a template for the switch aperture. An exposed switch is

www.powerbox-systems.com 5
often undesirable in scale models, and for such applications we offer an alternative
switch in the shape of the MagSensor. However, please note that the SensorSwitch
is required for the programming procedure - unless you are using a PowerBox or
Jeti RC radio system - and for this reason it should always be available for use. The
SensorSwitch is plugged into the socket marked Switch on the side of the Power-
Box.
b) Receivers
Once you have installed the PowerBox Mercury SR2, the screen and the switch, it is
time to connect the receivers. In principle all SRS PowerBox systems are totally reli-
able when used with a single receiver. However, in view of the low cost of a second
receiver compared with the value of the model, we always recommend installing a
second receiver.
Ideally the receivers should be spaced well apart inside the model, as this increa-
ses the likelihood that at least one receiver will have good reception at all times
- even under difcult reception conditions. It is permissible to extend the serial bus
connection between receiver and backer to any length, as the signal is digital, and
therefore extremely resistant to external inuences.
The PowerBox Mercury SR2 can be used with a wide range of radio control sys-
tems: PowerBox CORE P²BUS, Futaba S.BUS2, Jeti EX-BUS, Spektrum SRXL2,
Multiplex M-Link, JR DMSS and Graupner Hott. The rst four systems share one
common feature: servo signals and telemetry data are carried on a bus system, and
this allows the receivers to be connected to the Mercury SR2 using a single patch
lead each. Multiplex and Hott systems require an additional connection between
the TELE- output of the PowerBox and the receiver’s telemetry input.
The PowerBox Mercury SR2 automatically detects the system to which it is
connected. However, when the radio is rst switched on it may take a few seconds
before the system is unambiguously recognised. Once detected, the unit stores the
system type, and it will start immediately next time it is switched on.
• PowerBox ATOM/CORE
Connect one or two receivers to RX1 and RX2 at the P²BUS output. If only one
receiver is to be used, it must be connected to RX1 to provide telemetry transmis-
sion. If a GPS III or a PBS-TAV is connected to the FastTrack input, the Mercury
also delivers this ight data to the transmitter.

6PowerBox-Systems − World Leaders in RC Power Supply Systems
• Jeti EX-BUS
One output of the receivers you intend to use must be set to EX-BUS. The frame
rate should be set to 10ms, and the Failsafe function must be OFF. If you intend
to use only one receiver, then it must be connected to RX1 to transmit telemetry
data. If a GPS III or a PBS-TAV is connected to the FastTrack input, the Mercury
also delivers this ight data to the transmitter.
• Futaba S.BUS2
Connect one or two receivers to RX1 and RX2 at the S.BUS2 output. If only one
receiver is to be used, it must be connected to RX1 to provide telemetry transmis-
sion. This receiver must also be dened as the telemetry receiver at the transmit-
ter. In order to receive telemetry data, you must carry out a Load New process in
the Telemetry Sensor menu; this action completely erases the sensor list. Now
select Slot 16 in the sensor list, and select PowerBox. The telemetry data now
appear in Slot 16 or later. If a GPS III or a PBS-TAV is connected to the FastTrack
input, the Mercury also delivers this ight data to the transmitter.
Note: do not attempt to register the PowerBox as a sensor at the transmitter; this
function is not implemented.
• Spektrum SRXL 2
Connect one or two SPM4651T satellites to the PowerBox Mercury SR2 using
the optional adapter lead set (#9192). If only one receiver is to be used, it must
be connected to RX1 to provide telemetry transmission. At the transmitter you
will now see the battery data displayed under PowerBox Sensor. If a GPS III or a
PBS-TAV is connected to the FastTrack input, the Mercury also delivers this ight
data to the transmitter.
By default, the Mercury works in DX18 compatibility mode.
• Multiplex M-Link
Set the B/D sockets of the receivers you intend to use to SRXL V2. This gives you
sixteen channels. The Failsafe function must be OFF.
To use telemetry, you must disable the Telemetry function of one receiver using
Multiplex Launcher. The Tele output of the PowerBox should be connected to the
Sensor input of the other receiver.
If a GPSIII or a PBS-TAV is connected to the FastTrack input, the Mercury also
delivers this ight data to the transmitter.
Note: do not attempt to register the PowerBox as a sensor at the transmitter;
this function is not implemented.

www.powerbox-systems.com 7
• Graupner Hott
Set one output of both receivers to SUMD-OF16. For example, if the receiver is a
GR16/24, this will be output 8. Connect these outputs to the RX1 and RX2 inputs
of the PowerBox. If a GPS III or a PBS-TAV is connected to the FastTrack input,
the Mercury also delivers this ight data to the transmitter.
For the telemetry function, you must connect the TELE output of the PowerBox to
the Telemetry input of one receiver.
c) Connecting the batteries
It is possible to use 2S LiPo, 2S LiIon, 2S LiFePo or 5S NiMH batteries with the
Mercury SR2. We recommend that you use our PowerPaks, which feature integral
charge electronics. The fundamental rule regarding battery size is that one battery
on its own should be capable of powering the model reliably.
If you intend to assemble your own batteries, please note that correct polarity is
vitally important. The unit does not include reverse polarity protection, as this would
involve performance losses.
3.SWITCHING ON AND OFF
This is the procedure for switching the PowerBox on: hold the SET button pressed
in until the LED glows red. Continue to hold it pressed in while you also press but-
tons I and II briey to conrm the switching process. This method enables you to
switch the batteries on individually; for example, in order to check that both packs
are working properly, and deliver sufcient current when all the control surfaces
are moved.
The same procedure is used to switch off.
Note: Only one receiver (Bind A or Bind B) can transmit telemetry!
Note: Connecting a battery to the PowerBox with incorrect polarity, even very
briey, will immediately destroy the voltage regulators!

8PowerBox-Systems − World Leaders in RC Power Supply Systems
The OLED screen now displays the following image:
Analogue and digital battery voltage display. The scale of the analogue display
is matched to the battery type you have selected. The supplementary digital
display states the exact value.
Digital current display: shows the current which is drawn from each battery
individually.
Display of the voltage which is actually available at the output.
The consumed capacity is displayed separately for both batteries. It can also
be reset from the transmitter using a channel.
At this point the status of the receivers, gyro and GPS are displayed.

www.powerbox-systems.com 9
4. MAIN MENU
To access the menu you need to hold the SET button pressed in for about 2 - 3 se-
conds, after which you can select the desired menu using buttons I and II.
Press the SET button once you have selected a menu point. You can now alter the
values and settings using buttons I and II.
The “Rotary Menu” shown above contains the following sub-menus:
• iGyro
Here you will nd all the settings relating to the iGyro. These features are only
available if an iGyroSAT is connected to the unit.
• ServoMatching
If you have servos which are mechanically inter-connected, you can use this sub-
menu to adjust them to match each other using a ve-point curve. You will also
nd the Auto Matching function here.
• Sequenzer
At this point you can set up the door sequencer, either manually or with the help
of the Assistant.
• Output Mapping
In this menu you can assign all 16 outputs directly to any transmitter channel, to
a Gyro output or the door sequencer.
• Input Mapping
The transmitter channels are assigned to the iGyro or sequencer here.

10 PowerBox-Systems − World Leaders in RC Power Supply Systems
• Basics
This menu is used to alter fundamental settings such as the language or frame
rate.
• Assistent
Always use the Setup Assistant when you are preparing a new model for its rst
ight. This is where the transmitter input channels are determined, the model type
selected, and the servos assigned to the outputs. In just a few minutes the pri
mary functions can be ready for use, and the Assistant procedure makes it much
easier to set up the gyro functions at a later stage.
• Reset/Update
At this point you can reset individual ranges. The Update point activates the Data
port for connection to a PC using the USB interface lead (#9020).
5. BASIC SETTINGS
Before you start using the primary functions (with the help of the Setup Assistant)
and connect the servos, you should enter the basic settings in the General Settings
menu.
• Radio control system
This menu point cannot be selected manually. As already mentioned, the unit au-
tomatically detects the radio control system. If you have already connected your
receivers and bound them to the transmitter, you will see at this point the radio
control system it has detected.

www.powerbox-systems.com 11
• Regulator output
Hier stellen Sie die Ausgangspannung ein. Sie können zwischen 6.0V und 7,8V
wählen.
Bei HV Servos empfehlen wir die 7,8V Option: Damit haben Ihre Servos nach dem
Einschalten eine längere Zeit konstantes Drehmoment und Geschwindigkeit. Die
kurzzeitig höhere Spannung der Akkus nach dem Laden wird auf ein Niveau her-
abgesetzt, welches der Akku länger halten kann.
• Frame rate
Diese steht standardmäßig auf 16ms. Damit funktionieren alle gängigen Servoty-
pen zuverlässig. Digitalservos können eine bessere Performance erreichen, wenn
Sie die Framerate auf 12ms stellen. Ältere Analogservos dagegen können bei zu
niedrig eingestellter Framerate heiß werden und nden die Stellposition nicht
exakt.
• Battery type
At this point you should enter the battery type, to enable the unit to match the
graphical display to the characteristics of the battery you are using.
• Capacity
The capacity counter can be operated in count-up or count-down mode:
a) If you wish to display the consumed capacity, set 0mAh at this point. The
capacity counter now counts up.
b) If you wish to see a count-down display, enter the capacity of your battery at
this point.
In both cases it is possible to access the Input Mapping menu and assign a chan
nel which is used to reset the battery capacity. The default assigned setting here
is channel 16.
• Language
Select German or English as menu language.
6. SETUP ASSISTANT
The Setup Assistant is designed to help you complete basic channel and servo as-
signments quickly and easily. We recommend that you continue to use the Setup

12 PowerBox-Systems − World Leaders in RC Power Supply Systems
Assistant even if you are very familiar with the workings of PowerBox products.
You should also use the Assistant even if you (temporarily) do not wish to use an
iGyro SAT.
On the one hand the Assistant simplies operations, because the menu initially re-
fers to outputs in general terms, such as DIRECT-xy, but once you have completed
the Assistant it uses specic designations, for example, Right aileron … etc.
On the other hand, it is possible to retro-t an iGyro SAT without having to re-pro-
gram the battery backer. All assignments are already complete, and even the servo
matching is maintained.
Note: When setting up the PowerBox Mercury SR2 for the rst time, please keep to
this sequence:
Before you select the Setup Assistant, establish all the primary functions at the
transmitter, ideally with 50% travel. Mixers such as delta, tailerons and thrust vector
must also be programmed at the transmitter before you start. Check the functions
using your transmitter’s servo monitor. At this stage servo centre positions and di-
rections of rotation do not matter.
If you also intend to use an iGyro SAT, you should now install the gyro sensor in a
suitable position, perpendicular to the fuselage centreline, and connect it to the so-
cket marked FastTrack on the PowerBox Mercury SR2. If you are also using a GPS
III or PBS-TAV as telemetry sensor (and for gyro speed compensation), this should
also be connected to the FastTrack input using a Y-lead.
Select the Assistant widget in the Main Menu, and you will see the following dis-
plays:
In the rst display you select the wing type (Normal / Delta) and the tail type (Nor-
mal, Tailerons or V-tail). You can also determine whether the model has a thrust
vector system.
Note: When setting up the PowerBox Mercury SR2 for the rst time, please
keep to this sequence:
Setup Assistant (basic setup) –> Sequencer Assistant –> manual output assig-
nment of all other functions

www.powerbox-systems.com 13
On the next screen you enter the number of servos you wish to assign to individual
control surfaces. The Assistant supports a maximum of three servos per control
surface. This means: if your model is tted with overall four aileron servos, enter 4
behind ailerons.
You will now see further screen displays which vary according to the data you have
already entered. The following illustrations show the aileron channel as an example,
based on the above data:
Now move the aileron stick at the transmitter: the PowerBox checks the input: in this
example four channels should move. Two for the ailerons and two for the tailerons.
The screen shows now which channels have been detected, and the outputs to
which you should connect the servos. Bearing in mind that your individual trans-
mitter’s channel sequence may not be as shown above, you may need to move the
transmitter stick briey and repeatedly until the detected channels appear after the
appropriate functions.
Repeat the procedure with the elevator and rudder functions. After this you will be
asked to enter the Gain channel for the iGyro.
You need to assign a channel with +/-100% travel to a rotary control at the transmit-
ter. Even if you have not connected an iGyro SAT, this action is recommended as it
will make it easier to retro-t the gyro.
If you have selected a thrust vector function, you will see a second query regarding
the sensitivity of the thrust vector control system. This is the method the Assistant
uses to set up the basis for a simple but effective method of adjusting gyro gain in
ight.
Note: If multiple servos are mechanically coupled to a single control surface,
disconnect the linkage to servos 2 and / or 3, as the servos are not yet matched
to each other, and you could stall them!

14 PowerBox-Systems − World Leaders in RC Power Supply Systems
Once you have assigned the Gain control, press Continue to conrm your choice.
If no iGyro SAT is connected, this concludes the Setup Assistant.
If an iGyro SAT is connected, the next step is to establish the installed orientation
of the iGyro SAT:
This is accomplished by moving the model in the directions shown in the graphic
display: rst move the tail of the model up and down two or three times. You will
see that the elevators follow this movement every time - the direction of effect is
not important at this stage.
At the end of the movement hold the model’s tail up and wait until the elevators
return to neutral (centre).
Now repeat the procedure with the rudder (yaw) axis: move the tail to left and right
two or three times – then hold the tail to the right until the rudder returns to neutral.
The Assistant now continues to the process of establishing the directions of effect
(“sense”) and learning the transmitter control end-points. Before you carry out this
procedure, it is essential to set the direction of effect and the end-points of the pri-
mary functions at the transmitter.
Note: This procedure can be awkward to carry out with larger models. However,
there is a simple trick which makes learning the installed position easier: don’t x
the iGyro SAT in the model until after the learning process is complete. During
the learning procedure you simply move the iGyro SAT in the appropriate direc-
tion, rather than the model itself!

www.powerbox-systems.com 15
In this menu the system learns the aileron, elevator and rudder sticks as you hold
each stick in the direction shown on the screen, and press the SET- button.
The Setup Assistant is now nished, but you can still assign additional outputs ma-
nually, carry out the Door Sequencer Assistant, or match multiple servos.
-
7.SERVO MATCHING
The Servo Matching function can be used to adjust all 16 outputs in travel and di-
rection using ve points. Its purpose is to match the travels of multiple servos which
are mechanically interconnected, or which control multiple functions using only a
single channel. For example, the rudder may be coupled to a steerable nosewheel.
Servo matching is divided up over three screen displays: in the rst you select the
output which is to be adjusted; in the second the output is initialised; in the third
display the servo is adjusted.
In the initial Servo Matching screen you should select the output which you wish to
adjust. At this point you can also reverse the output with a button-press, or move
on to Auto-Matching.
Note: At any time, you can repeat the procedure in the Gyro menu for setting the
direction of effect and the end-points. This is absolutely essential in any case if
you adjust the travels or directions of effect of the primary functions while you
are setting up the model.
Note: In contrast to earlier versions of the PowerBox Assistant, it is now pos-
sible to repeat the Setup Assistant at any time. The system retains previously
entered settings, and only overwrites the entries you have changed.

16 PowerBox-Systems − World Leaders in RC Power Supply Systems
• Initializing
It is essential to carry out this step rst.
First centre your transmitter stick, then select Initialize: now move the stick to
both end-points. The screen displays the movement as a bar, and when the mo-
vement is complete, the small red markers remain in place at the end-points.
• Reversing the output
Um den Ausgang schnell umzupolen ohne jeden einzelnen Punkt einzustellen,
wählen Sie einfach mit der SET-Taste Ausgang umpolen aus.
• Start Matching
Select this menu point if you want to adjust the travel of the selected servo ma
nually using ve points. The PowerBox Mercury SR2 switches to this display:

www.powerbox-systems.com 17
The method is very simple: move the transmitter stick to the approximate point
which you wish to alter, then press the SET button. The servo now slowly moves
automatically to this exact point.
Now you can alter the servo curve at this point using buttons I and II.
You don’t need to use the transmitter to maintain the servo position; this makes
accurate settings easier.
Once you have adjusted the curve point to the desired position, press the SET
button again, and the servo slowly travels back to the position corresponding to
the actual stick position.
If you now move the stick, you will see at Input the servo position corresponding
to the transmitter stick position, and at Output the servo position now present at
this servo.
• Auto Matching
The Auto matching function is a completely new development, and this is the rst
PowerBox product to include it. Its purpose is to match the travels of up to three
mechanically interconnected servos accurately over ve points, which it accom-
plishes in just a few seconds.
How does auto matching work?
The PowerBox Mercury SR2 is tted with the latest generation of micro-control-
ler which is capable of measuring the current drawn from both batteries extre-
mely quickly and precisely. The values for measured current are used to match
two or three mechanically linked servos to each other.
This is accomplished by moving each servo to ve points in turn and recording
the lowest current values. The process is carried out in two steps: initially coar-
sely, then nely. A third stage then follows, in which ne-matching is carried out,
taking into account any stiffness in the control surface hinges.
In the initial stage the servos are strained hard against each other for very brief
periods (5 x 100ms). We have carried out hundreds of tests with this procedure,
and have found that it presents no problems to servos - even low-cost examples.
In fact, any linkage and servo must be capable of withstanding this procedure in
any case, otherwise they would not be able to cope with ight loads.
Note: This action causes all the servos which are assigned to this input chan-
nel to move to the selected position. If this were not so, mechanically linked
servos would immediately stall each other!dene Servo sofort gegeneinander
blockieren!

18 PowerBox-Systems − World Leaders in RC Power Supply Systems
Which servo types are suitable for auto matching?
All types of servos are suitable - with one exception: servos which do not beco-
me “soft” when the signal is switched off. There are a few digital servos which re-
main xed at their position even when no signal is present. In steps 1 and 2 of auto
matching this would cause the servos to draw a high current for an extended period,
i.e., for as long as the matching process lasts, and this is not acceptable. Such ser-
vos can only be matched manually!
Start
In the rst servo-matching display you select your main servo under Output. In
most cases this would be - in the case of ailerons - the servo closest to the fusela-
ge. Connect the servo, and set the centre and travel at the transmitter. Initialize the
servo with maximum travels.
Now select Auto Matching. At this moment all the PowerBox Mercury SR2’s other
outputs are switched off, and you will see this screen:
Now connect the second and - if present - the third servo to the appropriate out-
puts, and complete the mechanical linkages. Now set for AUX1 and AUX2 the other
participating outputs. When selected, these outputs are assigned to the same input
channel as the main servo, and initialized. This means that you do not need to set
the assignment of the participants beforehand in Output Mapping, and also do not
need to initialize them.
For example, if you accidentally select the wrong output, and wish to cancel your
choice, the output will be reset to its previous function.
Once you have completed the selection of the participants, move the cursor to Start
Matching: the matching process commences. If you wish to interrupt the process,
you can do this by pressing the SET button.
The procedure is automatically interrupted if the system fails to detect a minimum

www.powerbox-systems.com 19
current value; for example, if a linkage is overloaded at its end-point, or you forgot
to install it.
A matching process for three servos takes about 30 - 40 seconds. You can follow
the current consumption directly on the screen. When the matching is nished, use
the transmitter stick to run the servos to all ve points. A quiet buzz from the servos
in one or other position is normal. If the buzzing stops when you touch the control
surface lightly with your nger, then this shows that the matching process has wor-
ked accurately.
Minor corrections can be carried out at any time under Manual Matching. It is a
good idea to check the servo matching occasionally before and during the ying
season, as servos and mechanical systems are always prone to slight drift in use!
8.DOOR SEQUENCER
The PowerBox Mercury SR2 incorporates a fully programmable door sequencer.
This feature enables you to control the entire process for retracting and extending
the undercarriage and wheel doors using a single channel at the transmitter.
The Sequencer menu is divided into three parts: selection of the function, the actual
set-up screen for manual set-up using the graphic display, and the Setup Assistant.
The illustration above shows the start of the Sequencer once you have initiated the
Assistant. This is clear because the name of the function is shown as DOOR-FL
rather than DOOR-A. The Assistant actually assigns names to the doors according
to your entered data, making subsequent adjustments easier. More on this later.
Regarding the individual menu points:

20 PowerBox-Systems − World Leaders in RC Power Supply Systems
• Switch position
Here the screen shows directly the current position of the assigned channel. If
this position does not coincide with your preferred transmitter switch position,
you can correct it at the transmitter using servo reverse.
• Switched channel
At this point you should dene which transmitter channel is to be used to switch
the sequencer. This setting is also present in Input Mapping. At the transmitter
the switched channel travel should be set to -100% to +100%.
It is important to know that the door sequencer also includes a pause function: if
you use a three-position switch and set it to 0%, the sequence stops at the current
position. From this point you can continue or reverse the sequence according to
the next switch position.
• GEAR UP OUTPUT OFF
At this point you can enter an output which is required to remain at a pre-dened
position when the undercarriage is retracted. For example, this is important if
the model is tted with a steerable nosewheel, as it ensures that the wheel stays
‘straight ahead’ when the noseleg is retracted.
The position of this output is stored when you leave this menu point.
• Function
Here you select the function which is to be adjusted. The sequencer provides
facilities for four individually variable functions. For example, an undercarriage
with three wheel doors (individually controlled) needs four functions: three doors
+ retracts (valve or electronic unit).
Up to four travel points can be set up for each function. Each travel point is
dened with a servo position and a time (delay) after the start point.
• Manual Setup
This menu enables you to set up and adjust the individual functions, and also
ne-tune the timing and position of functions which the Assistant has already
set up for you.
Caution! If you were to set the wrong output at this point - for example, the
elevator channel - then the elevator channel would be switched off when you
retract the undercarriage! The results of this are obvious, so please take parti-
cular care when setting up this point.
This manual suits for next models
1
Table of contents
Other PowerBox Systems Power Supply manuals
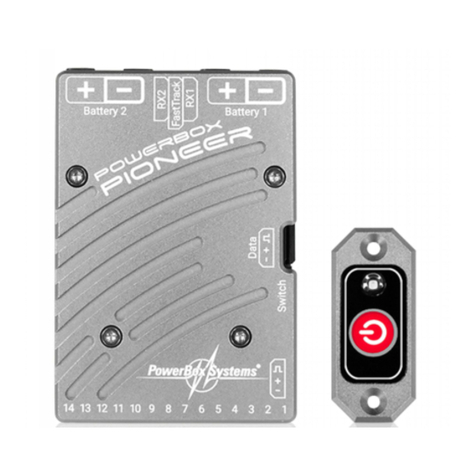
PowerBox Systems
PowerBox Systems PowerBox Pioneer User manual
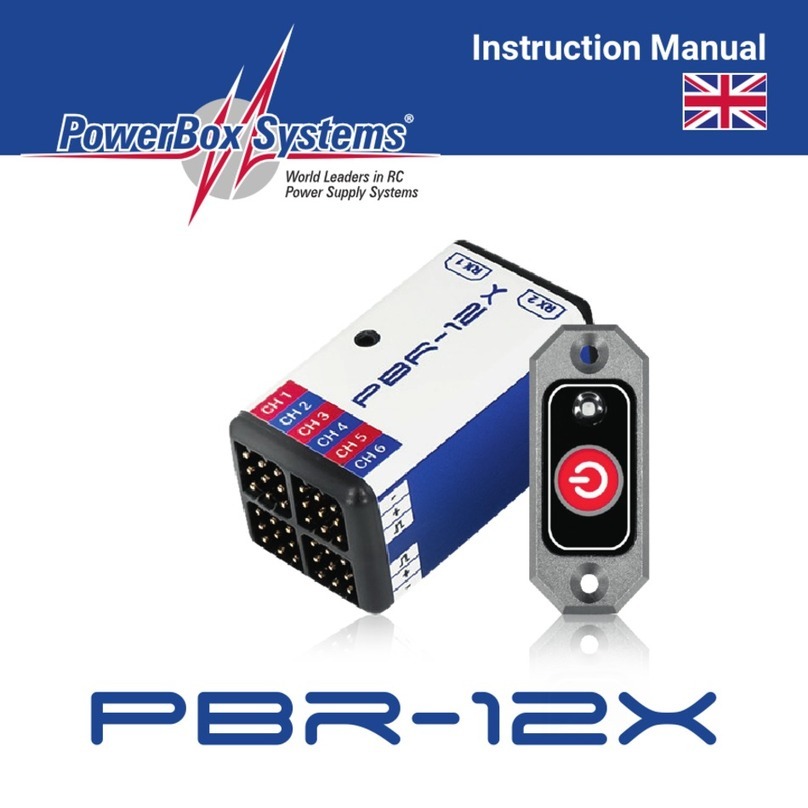
PowerBox Systems
PowerBox Systems PBR-12X User manual
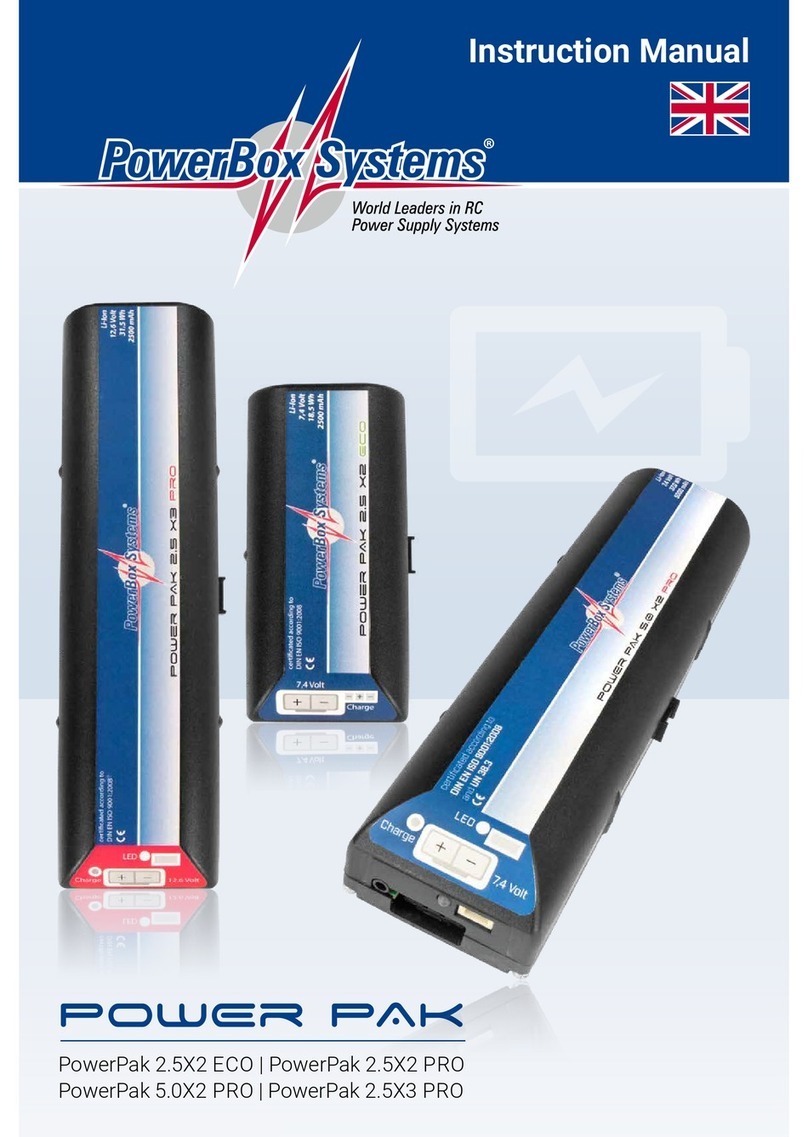
PowerBox Systems
PowerBox Systems PowerPak Series User manual
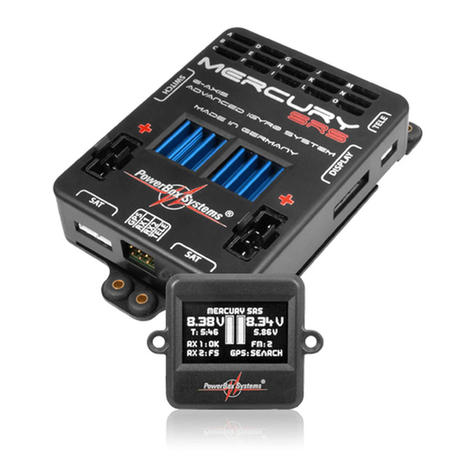
PowerBox Systems
PowerBox Systems Mercury SRS User manual
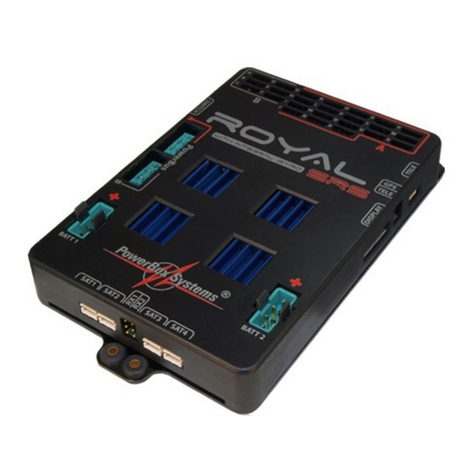
PowerBox Systems
PowerBox Systems Royal SRS User manual

PowerBox Systems
PowerBox Systems BaseLog User manual
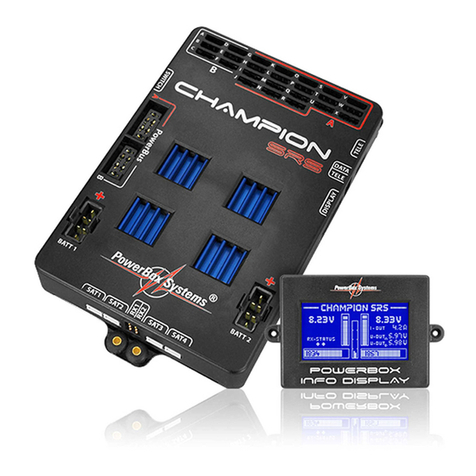
PowerBox Systems
PowerBox Systems Champion SRS User manual
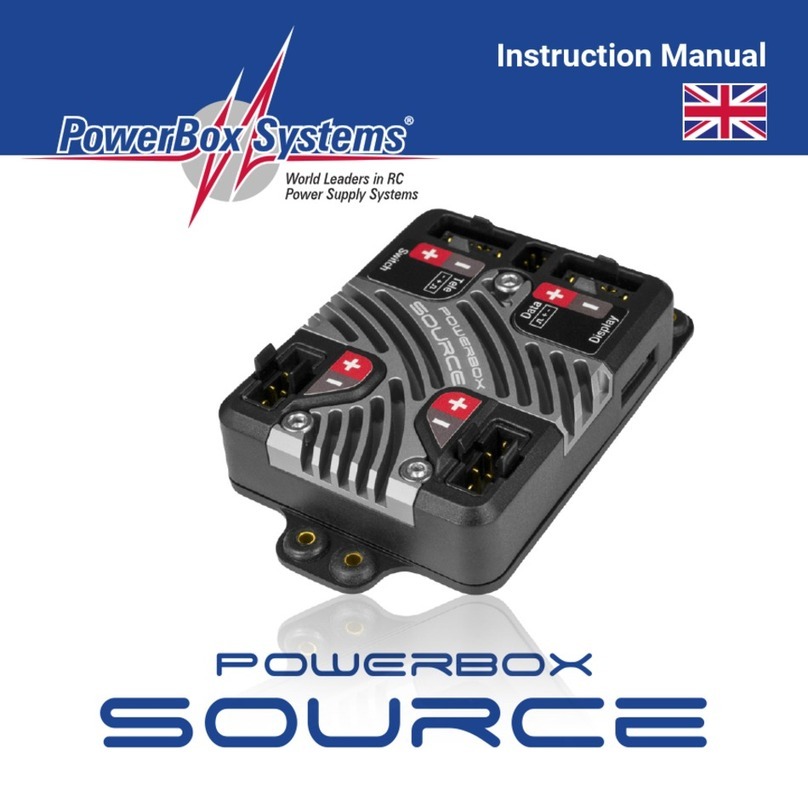
PowerBox Systems
PowerBox Systems PowerBox Source User manual
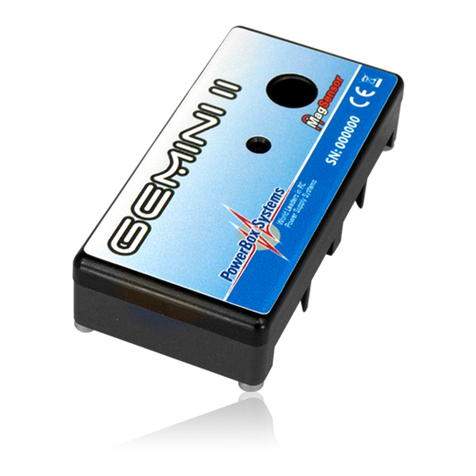
PowerBox Systems
PowerBox Systems GEMINI II User manual
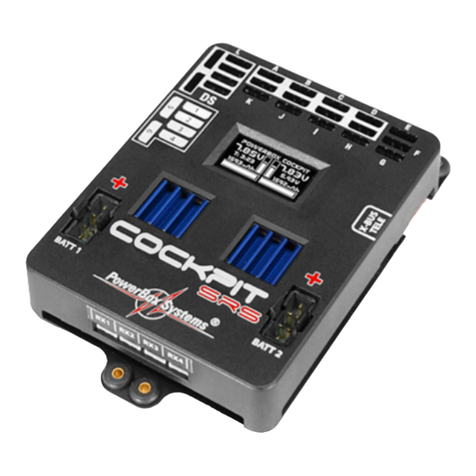
PowerBox Systems
PowerBox Systems cockpit User manual