PowerTek CV388-R User manual

POWERTEK
Model CV388-R
10-23-08
Operating and Assembly
Manual
PowerTek Inc.
P.O. Box 3
Lebanon, IN 46052

1
Model CV388-R Parts List
Key Part No. Description Qty.
1 38026 Engine Frame, RH 1
2 38012 Container Frame, 380 1
3 38015 Vertical Upright, 380 1
4 86028 Engine, 9HP Robin 1
5 88046 Turbine Housing, Chipper 1
6 56055 Turbine, Chipper Pro Series 1
7 56107 Turbine Washer 1
8 58036 Inlet, Chipper 6" 1
9 68050 Wheel, Pneumatic 3
10 46233 Filter Support 1
11 46217 Top Support, 462 1
12 56115 Nylon Spacer 3
13 47222 Molded Top, 470 1
14 46228 Filter 1
15 46219 Seal, Molded Top 1
16 46235 Container Latch 1
17 48040 Intake Nozzle 1
18 3120518 Eyebolt 2
19 48038 Spring 2
20 46218 Clevis Pin, Vertical Support 1
21 46310 Container, 44 Gallon, Yellow 1
22 56102 Hose Clamp, 6" 4
23 46103 Exhaust Hose-HD, 6" x 36" 1
25 38029 Hose Support 1
26 38031 Lift Handle 2
27 38028 Hitch Pin 1
28 10665 Collar Clamp, 3/4” 1
29 56032 Turbine Liner, 6” 1
30 38027 Riser, Engine Frame 2
31 3760110 Turbine Bolt 1
32 3120612 Housing Bolt 4
33 3750238 Turbine Set Screw 1
34 2501716 Turbine Key 1
35 45060A Caster Yoke Assembly 1
36 88041 Chipper Knife (included w/Turbine) 2
37 88045 Chipper Inlet 1
38 88036 Chipper Inlet Guard 1
39 35239 Spring, Lock Pin 2
40 3750801 Turbine Lock Washer 1
41 3750905 Chipper Inlet Nut 3
42 160 Remote Pickup, Model 160 1
43 48061 Tow Handle 1
44 38889 Thrust Bearing 1
38596 Decal, Caution Rotating Blades
45132 Decal, Caution Spinning Blades
45133 Decal, Warning Stop Engine
48096 Decal, Danger Stop Engine

2
PowerTek Model CV388-R
3-6-08
1
2
3
5
9
10
12
11
13
14
15
16
17
18
19
20
21
22
23
27
28
7
29
31
34
33 36
37
39
38
40
4
25
41
30
632 28
35
43
42 26
26
44
8

3
PowerTek Assembly Instruction
1. Place frame (2) on blocks and level the frame with axles towards the bottom and frame facing
upwards. Slip wheel (9) over container frame (2) axle pin, trapping 3/4" flatwasher on both
sides of wheel. Secure with 1/8" x 1" cotter key. Slid hub cap over wheel hub. Repeat
procedure with opposite wheel. Fig. 1
2. Attach vertical upright (3) to container frame bracket with 3/8" x 1" HHC and whizlocks. Do
not tighten. Fig. 2
3. Attach eyebolts (18) to vertical upright upper brackets, trapping the brackets between 5/16"
hexnut and 5/16" whizlock nuts. Rotate eyebolts so eyelets face from front to back. Fig. 3
4. Place container (21) in container frame. Install foam seal to molded top where container and
top will make contact. Set top assembly on can with top support bracket astride the vertical
upright. Align pivot hole on top support to hole on vertical upright, do not force fit this
alignment, if holes do not line up, move vertical upright up or down on the frame (2) until
proper alignment is achieved and tighten. Secure with 1/2" x 2 1/2" HHC and nylock nut.
Tighten until slight drag can be felt when pivoting molded top. Pivot top up and attach
springs (19) to eyebolts and spring retainers on top support. Lower top assembly to operating
position and immediately slip clevis pin (20) thru locking pin hole on top support. Secure pin
with 1/8" x 1" cotter key. Attach latch to molded top with 1/4” x 1/2” truss head bolt and 1/4”
whizlock nuts. Fig. 4
5. Attach engine frame assembly (1) to risers (30) and secure with 3/8” x 2 ¼” HHC, flat
washers, and whizlock nuts. DO NOT TIGHTEN. Fig. 5 Slide Thrust Bearing (44) over
caster yoke assembly shaft. (35) Insert shaft through second hole from front of draw plate.
Slip collar clamp (28) over shaft and tighten set screw. Now, tighten all bolts. Fig. 6
6. Attach engine assembly to engine frame plate. Secure with two 5/16" x 1 1/4" HHC and two
5/16" x 3" Hexbolts and 5/16” locknuts. Fig. 7
7. Slip exhaust hose over intake nozzle (17) neck and tighten clamp. Slip hose clamp (22) over
exhaust hose (23) and over turbine housing (5), and tighten clamp. On the intake side bunch
the hose up against the molded top for a good airtight fit. Fig. 8
8. Slip hose clamps over each end of remote hose (42). Attach nozzle assembly to one end and
quick connect to opposite end. Tighten clamps. Attach assembly to inlet (8) Fig. 9
9. Slid hose support (25) to right side of drawbar and slide it forward close to the draw plate.
Secure with 5/16” x 2 1/2” HHC and whizlock nuts included. Fig. 10
10. For manual towing, attach tow handle (43) through the upper hole in hitch pin (27) and secure
with hairpin cotter. Fig. 11
11. Slide one of the Lift handles (26) under the drawbar and centered between the engine plate
and the hose support. Secure with 5/16” x 2 ½” HHC and whizlock nuts. The 2nd Lift handle
attaches to Vertical upright tube (3) as low as it will go. Secure with 5/16” x 2 ½” HHC and
whizlock nuts. Fig. 12
12. Read engine operation instructions and service engine before starting.

4
Note: Bunch a few ribs of
the hose up behind the
hose clamp. This will
make a good tight seal
between hose and top.
Fig. 1
Fig. 4
Fig. 7
Fig. 2 Fig. 3
Fig. 5
Fig. 9Fig. 8
1/8" Cotter Pin
3/4" Flatwasher
3/8" Whizlock Nut (4x)
3/8" x 1" Hexbolt (4x)
Eyebolt (2x)
5/16" Freenut (2x)
5/16" Whizlock Nut (2x)
3/8" x 2 1/4" Hexbolt (4x)
3/8" Flatwasher (4x)
3/8" Whizlock Nut (4x)
1/4" x 1/2" Truss Head (2x)
3/8" x 2 1/8" Clevis Pin
1/2" x 2 1/2" Hexbolt
1/8" Cotter Pin
1/2" Nylon Locknut
1/4" Whizlock Nut (2x)
Not Pictured
(
5/16" x 3" Hexbolt (2x)
5/16" x 1 1/4" Hexbolt
5/16" Locknut (4x)
Not Pictured
(
Fig. 6

5
Fig. 10 Fig. 11 Fig. 12
CHIPPER VAC INSTRUCTIONS
The chipper components on your chipper vac have been fully assembled at the factory.
Your chipper vac is designed to accommodate limbs up to 3” in diameter.
To remove the chipper blades for sharpening or replacement, detach the three 3/8” whizlock nuts and lift
off the chipper chute. Remove the two blades using a 3/16” allen wrench. Sharpen blades and reattach.
Make sure blades are fastened securely.
Keep in mind to periodically tighten all bolts.
Listen for unusual vibration of the air turbine. If excessive vibration is present, stop engine and check for
damage.
CAUTION!!!
*ROTATING CUTTING BLADES*
*KEEP BODY PARTS AND CLOTHING AWAY FROM DRIVEN PARTS IN MOTION*
*AVOID LOOSE CLOTHING*
*WEAR APPROPRIATE GLOVES, EYE AND HEARING PROTECTION*
*ALWAYS STOP ENGINE AND DISCONNECT SPARK PLUG TO SERVICE*

6
OPERATING PROCEDURE
1. Follow engine manufacturer's instructions in preparing engine for operation.
2. Inspect area to be vacuumed and pickup all harmful objects and litter. Rocks and other harmful debris
can do serious damage to vacuum assembly and cause bodily injury.
3. For best vacuuming results operate tractor at manufacturer's recommended speed for best cutting. If
grass is high, mow first and vacuum on the second pass.
4. When mowing keep discharge chute to the outside of cutting area for better cut and efficient pickup of
grass clippings and leaves.
5. Your vacuum is preset to run at approximately 3200-RPM (380), 3800-RPM (385), at no load. Do not
slow down engine.
6. SHUT OFF ENGINE TO UNLOAD.
7. When operating tractor on slope or grade, exercise extreme caution. Do not cut across grade or slope.
Mow directly up and down hills.
8. Periodically check all fasteners for tightness.
9. Listen for unusual vibration of engine or air turbine. If excessive vibration is present, STOP engine and
check for damage to turbine fan.
10.Always shut off tractor engine and vacuum engine before servicing.
11.Replace deflector shield when discharge chute is removed.
12.When removing clogs, SHUT OFF ALL ENGINES.
EXTENDED STORAGE PROCEDURES
1. Wash and clean vacuum, and lubricate any lubrication points.
2. Drain fuel from the tank and run vacuum until fuel is exhausted in carburetor.
3. Drain and change the engine oil.
4. Clean tires and check pressure. Raising and supporting unit with weight off tires is recommended.
5. When storing a unit with Rubbermaid®containers, leave containers latched to top.
POWERTEK WARANTY POLICY
Palmor Products, Inc. will repair or replace, free of charge, any part, or parts that are
defective in material or workmanship or both for a period of one year residential use, and
90 day’s for commercial and rental use. The purchaser will pay transportation charges on
parts submitted for replacement under warranty. For warranty service, contact your local
dealer from whom the unit was purchased. There are no other express or implied
warranties. Some states do not allow limitations on how long an implied warranty lasts,
and some states do not allow the exclusion or limitation of incidental or consequential
damages, so the above limitation and exclusion may not apply to you. This warranty
gives you specific legal rights and you may also have other rights, which vary from state
to state.
POWERTEK, INC.
P.O. BOX 3
Lebanon, In 46052
Phone: 1-877-769-7835 Fax: 765-436-2490
Web Page: www.powertek.us
Other PowerTek Chipper manuals
Popular Chipper manuals by other brands
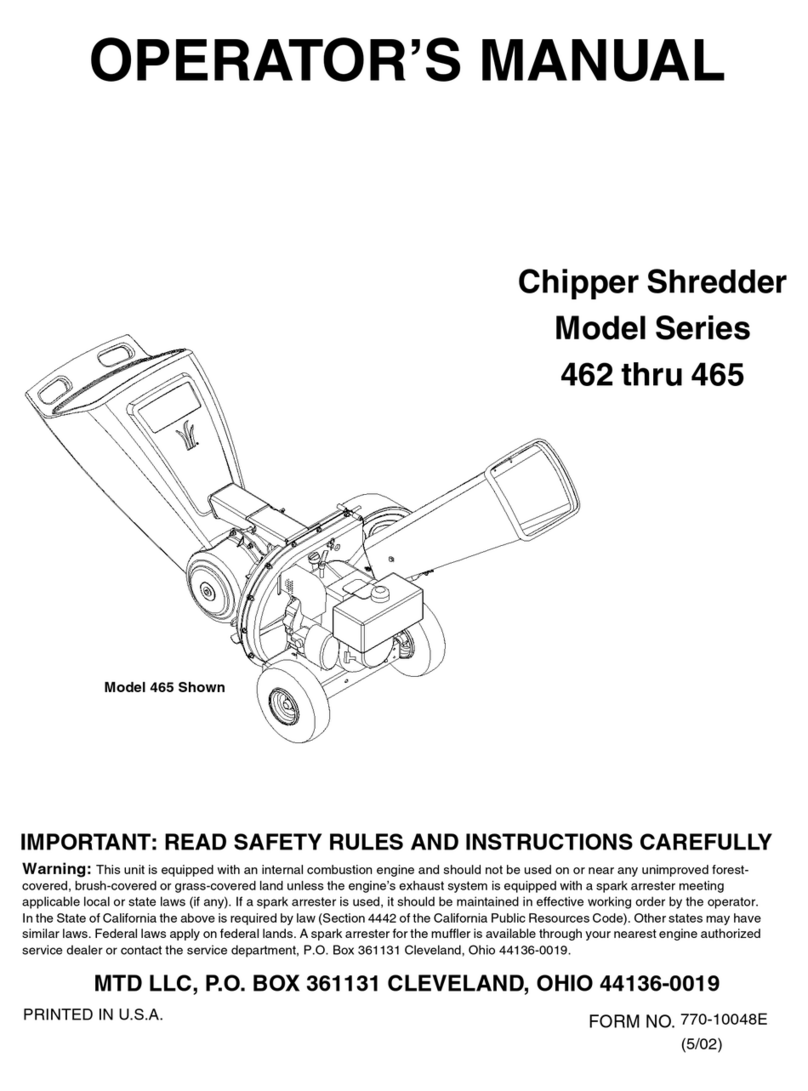
MTD
MTD Series 462 Operator's manual

Timberwolf
Timberwolf Entec TW 190H instruction manual
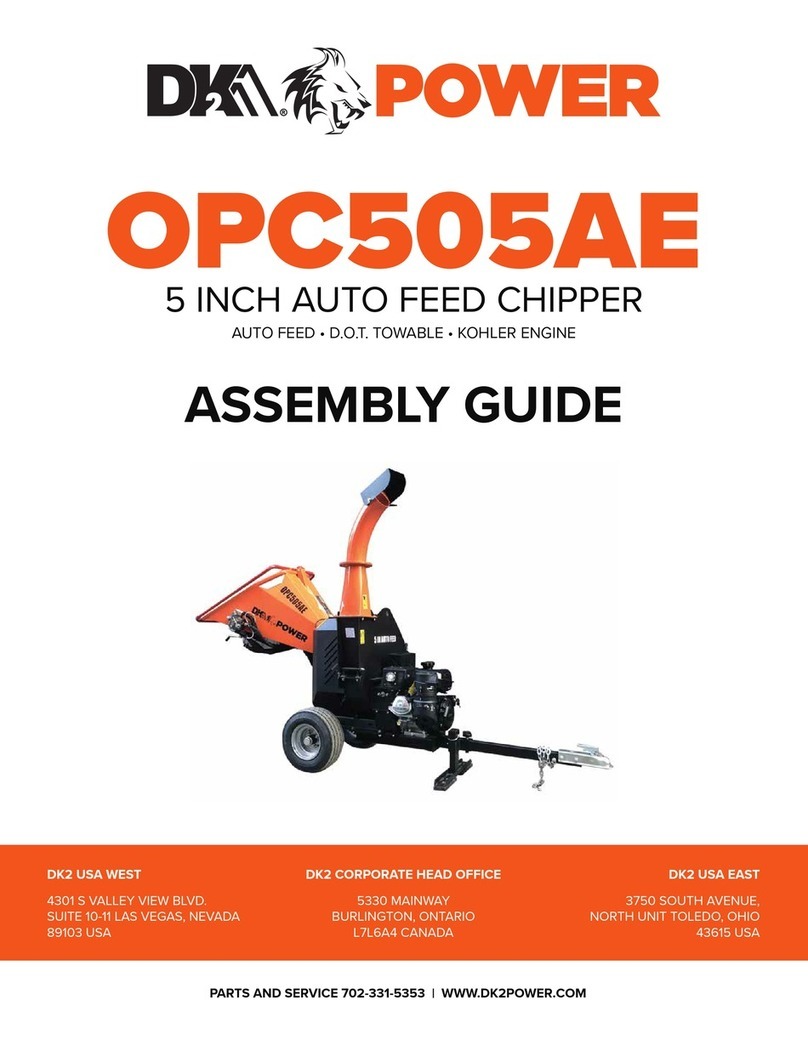
DK2 Power
DK2 Power OPC505AE Assembly guide
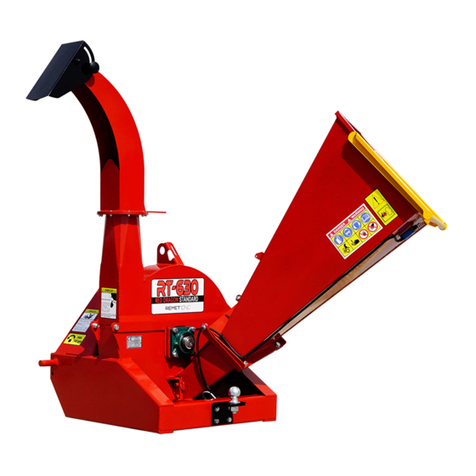
REMET CNC
REMET CNC RT-630 USER MANUAL WARRANTY CARD EXCHANGE PARTS CATALOG
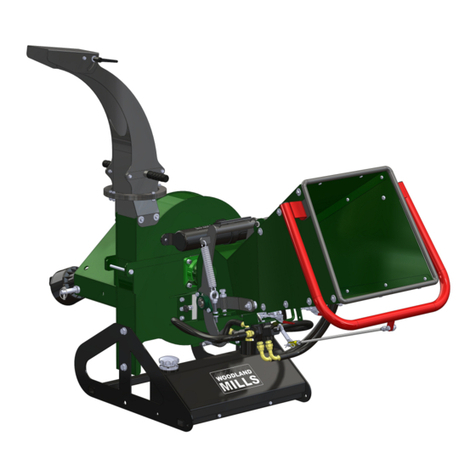
Woodland Mills
Woodland Mills WC46 Operator's manual

Caravaggi
Caravaggi Bio 80 Use and maintenance instruction manual