PRINCO L3610 User manual

Instrumentation designed
with the user in mind
INSTRUCTION MANUAL
PRINCO MODELS L3610 & L3610R
CONTINUOUS LEVEL TRANSMITTERS
with NULL-KOTE™
PRINCO INSTRUMENTS INC.
1020 INDUSTRIAL BLVD.
SOUTHAMPTON, PA 18966
TEL: 800-221-9237, 215-355-1500
FAX: 215-355-7766
WEB SITE: www.princoinstruments.com
E-MAIL: [email protected]
Rev. 1, 9 May 02

Table of Contents
i
Section 1. Description 1-1
A. General Description 1-1
B. Functional Description 1-1
C. L100 Series Probes Description 1-5
Section 2. Specifications
A. 1. L3610 & L3610R Continuous Level Transmitters 2-1
A. 2. L100 Series Probes 2-1
Section 3. Installation 3-1
A. Inspection 3-1
B. Mounting 3-1
C. L3610 Electrical Connections (Integral Units) 3-4
D. L3610R Electrical Connections (Remote Units) 3-7
E. Installation in Hazardous Areas 3-7
F. Ground Isolation 3-8
Section 4. Adjustments and Operation 4-1
A. Factory Pre-calibration 4-1
B. Cancellation of Coating Effects 4-1
C. Initial Checkout 4-1
D. Calibration Procedure 4-2
E. Diagnostic Indicators and System Troubleshooting 4-4
F. Field Re-setting of Measurement Range, Cancellation Mode
and Output Mode 4-7
Section 5. Equipment Service 5-1
A. Getting Help 5-1
B. Warranty Statement 5-1
Illustrations
Figure 1-1. L3610 Dimensional Drawing (Integral Unit)1-4
Figure 1-2. L3610R Dimensional Drawing (Remote Unit) 1-4
Figure 1-3. Typical 1" NPT Mounted Probe (Model L101) 1-5
Figure 1-4. Typical 3" Flange Mounted Probe (Model L127) 1-6
Figure 1-5. Typical Dual Flexible Probe (Model L115) 1-6

Table of Contents
ii
Figure 3-1. Probe Mounting Locations 3-2
Figure 3-2. L3610 Unit 3-wire Electrical Connections, 24 Vdc 3-5
Figure 3-3. L3610 Unit 4-wire Electrical Connections, 24 Vdc 3-6
Figure 3-4. L3610 Unit 4-wire Electrical Connections, 115 Vac 3-6
Figure 3-5. L3610R Electrical Connections 3-7
Figure 3-6. L3610 FM Approval Drawing 3-9
Figure 4-1. L3610 & L3610R Control and Indicator Locations 4-3
Figure 4-2. Ground Continuity, Breached Probe and Probe
Response Checks 4-7
Figure 4-3. Ground Isolation and Switch Locations 4-8
Tables
Table 4-1. Percent of Range to Current Conversion Table 4-2

Section One
Description
1-1
A. General Description
Princo Models L3610 and L3610R are multi-featured, high technology, RF impedance sensing,
continuous level transmitters. Null-Kote™ circuitry permits operation in a wide variety of
process materials, regardless of dielectric, conductivity, viscosity or coating characteristics.
The output signal, typically 4 to 20 mA, is directly proportional to the level being measured and
can be wire transmitted to a remote meter, controller, recorder, etc. Meter scale calibration may
be in percent of level or specific units (i.e. gallons, inches, etc.) related to the application. The
L3610 will drive any current sensing device which has an input impedance of 500 ohms or less.
Self-diagnostic circuits give an immediate indication of many application or installation related
problems such as bad ground connections, breaches or pinholes in the probe sheath, and
moisture in the electronic housing.
The Model L3610 ("integral unit") is packaged in an explosion-proof, weatherproof aluminum
housing. Probe connections are made reliably and automatically when the probe is screwed
into the electronic housing.
The Model L3610R ("remote unit") allows the electronic controller to be installed in a location
removed from the process storage vessel. It consists of a standard L3610 electronic chassis
mounted inside a clear-covered, plastic, NEMA 4X housing which is connected to a Model L216
"remote head" via a Model L214 tri-axial cable. Standard cable length is 25 feet. Connection to
the probe is made by simply screwing the L216 onto the probe's 1-inch NPT fitting.
Available accessories which enhance the application of the L3610 include Models S954, S960
and S975 indicators. Refer to Section 1.B.4 for descriptions.
Models L3610 and L3610R are covered by Princo's 10-year warranty. Refer to Section 5.B for
details.
B. Functional Description
1. RF Impedance Theory
The Princo L3610 works on the concept of monitoring changes in RF impedance between two
sensing elements. The two sensing elements are the "active" element of the probe and the
"ground reference", which is either a second probe element or a metal tank wall. The two
elements are, effectively, the two plates of a capacitor. The electronic unit produces a 100KHz
test signal that is applied across the probe elements and is monitored for changes in amplitude
and phase angle.
The primary component of the measurement is the capacitive element (with a -90º phase shift,
100% resistive being the 0º reference point). With no process material touching the probe, the
dielectric material between the two probe elements is air, which by definition has a dielectric
constant of 1.00. As the process level rises, it displaces air as the dielectric. Since the process
material has a higher dielectric constant than air, capacitance increases, RF impedance
decreases and RF current flow increases, in direct proportion to level change.
The secondary component of the measurement is the resistive component. Buildup of a
conductive process material coating on the probe produces increased RF current flow. This
coating can be defined electronically as a complex resistive-capacitive network. Due to the
resistive component, the phase angle of the measurement shifts away from a pure -90º.

Section One
Description
1-2
The resistive component of the coating is proportional to the capacitive component of the
coating and to the increased current flow produced by the coating. Therefore, by monitoring the
magnitude of the phase shift away from the -90º point, the signal processing circuitry of the
electronics is able to apply a proportional correction to the RF signal, thus subtracting out the
error caused by the coating. The corrected RF signal is ultimately rectified and amplified to
produce a proportional DC current output.
Many, if not most, process applications are water-based and, therefore, electrically conductive.
If the probe elements were both bare metal, the first contact with the process material would
short the capacitive plates producing an exceptionally high current flow. Covering one or both of
the probe elements with an insulating material such as Teflon or Kynar solves this problem.
Now, with no process material touching the probe, capacitance is determined by the combined
dielectrics of air and the probe insulation material in series. As the process rises, it displaces
the air and effectively shorts the gap between the two probe elements. Now, capacitance is
determined by the dielectric of the Teflon or Kynar insulation alone, producing a directly
proportional increase in capacitance and RF current flow as level rises. Process linearity is
determined solely by the uniformity of the thickness of the insulation material.
Linearity of non-conductive process measurements depends upon uniform, parallel spacing of
the probe elements. Probes used for non-conductive applications normally have at least one
element insulated. This is to reduce the magnitude of error that would be caused by a small
amount of conductive moisture in the process, such as might result from condensation.
2. Signal Processing
The L3610 is factory set on the appropriate RF capacitive measurement range as required for
the specific application, based on a capacitance span calculated for the specific application.
Normally, the range is not re-set in the field. The RF signal, proportional to level and corrected
for coating error, is rectified and filtered into a proportional DC voltage. This signal is processed
by a series of DC amplifiers and ultimately converted into a proportional DC current or DC
voltage output signal.
Front panel ZERO and SPAN adjustment pots set the span of the DC amplifiers within the pre-
set range. The pots are set at the factory relative to calculated zero and span capacitance
values for the specific probe and application. They are re-adjusted by the user if need requires.
3. Basic Features
•RF Impedance Sensing Technology with Null-Kote™
The L3610 uses RF impedance technology, proven in tens of thousands of applications.
With no moving parts, the measurement depends solely on its modern, electronic circuitry,
ensuring years of dependable operation.
•Coating Cancellation
Null-Kote™ technology allows the cancellation of the build-up on the probe of most process
materials. Units are factory set for either Mode A (non-conductive) or Mode B (conductive)
process coating cancellation. Coating cancellation is effective within specified limits.
•Superior Temperature Stability
The L3610 electronics is designed to provide temperature stability superior to that of
previous generations of level transmitters. This allows successful, repeatable
measurements in many short span, low dielectric applications.
•Self Diagnostic Feature

Section One
Description
1-3
Provides instantaneous, visual indication of the two most common failure modes -shorted
and open probe conditions. The A DIAGNOSTIC LED indicates shorted condition; the B
DIAGNOSTIC LED indicates open condition.
•Output Signal
Standard 4 to 20 mA output with optional 0 to 5Vdc and 0 to 10 Vdc outputs available.
•Remote Mounting
Optional, Model L3610R, remote mounting configuration is available. This allows mounting
of electronic unit in a cabinet, control room, etc., connected to probe by tri-axial cable.
Standard cable length is 25 feet; optional lengths available.
•FM Approval
The L3610 is Factory Mutual Approved as a measurement system when used with various
L100 Series Probes as defined in Figure 4-2. The L3610R is not FM approved.
•Conformal Coating
An insulating coating (conformal coating) is applied to all circuit boards to protect the
circuitry against condensation of moisture.
•10-Year Warranty
Quality backed by limited 10-year warranty. Refer to Section 5 for details.
4. Accessories
•Model S960 Series Digital Process Indicators
LED display digital indicator which accepts any input current range between 0 and 50mA. A
6 digit display can be programmed for nearly all engineering units. Programmable digital
filtering enhances stability.
An optional totalizer/ linearizer can be used to totalize or integrate signals up to a maximum
display value of 999,999. It features independent scaling and a low signal cut-out to suit a
variety of signal integration applications. Additionally, nine slopes and offsets can easily be
programmed with this option to linearize transducers and non-linear outputs, such as square
law devices. Peak/valley (max/min) reading memory, display hold and a signal re-zeroing
(tare) function are also included and they are easily recalled and controlled by either the
front panel or remote switch. All readings are retained at power-down.
Optional dual relays with parallel solid state outputs are fully programmable to operate in a
wide variety of modes to suit many control or alarm applications. Refer to Princo Bulletin
S-91-2 for specifications.
•Model S975 Digital Loop-Powered Indicator
Small, easy-to-read, 3½ digit, 4-20mA loop powered LED indicator in NEMA 4X rated
housing. Can be scaled in percentage of range, 4 to 20 mA, or for one of many engineering
units. Refer to Princo Bulletin L-02-1 for specifications.
•Model S954 Analog Meter
Typically scaled to read 0 to 100% of range span relative to a 4 to 20 mA input. Suitable for
panel mounting or can be mounted in a weatherproof housing. Refer to Princo drawing
#A90-S954 CD1 for dimensional details.

Section One
Description
1-4
Figure 1-1
L3610 Dimensional Drawing (Integral Unit)
Figure 1-2
L3610R Dimensional Drawing (Remote Unit)

Section One
Description
1-5
C. L100 Series Probes
1. General Description
Princo offers a wide variety of probes for use with its continuous transmitters and multi-point
controllers. Although the measurement technology remains the same, as outlined in the
previous section, different probe designs are suited for different applications.
Electrical, chemical and mechanical considerations affect probe selection. Electrically, a ground
reference must be present and the probe must be built to provide proper response.
Chemically, the probe must be compatible with the process material. It must be immune to
attack and must offer no chance of contaminating the process.
Mechanically, the probe must be able to withstand the pressure and temperature extremes of
the application. In addition, turbulence, consistency, viscosity, abrasion and mounting
configuration also play a role in probe selection. A flexible probe is required where probe length
exceeds 236 inches or where physical restrictions, such as lack of headroom, prevent
installation of a rigid probe.
Single element probes (L101, L104 and L109) are often used in situations where a metal tank
wall can provide an adequate ground reference (second element). Non-metallic vessels require
dual element probes, as do most non-conductive process applications where probe response
and/or linearity would be inadequate using the vessel wall as a ground reference.
Dual element probes are made with either parallel (L115, L116, L127, L128) or concentric
(L102, L107) elements. Dual concentric probes provide the best response for low dielectric, low
consistency, non-conductive processes as well as minimizing the effects of agitation.
Probe sheathing (Teflon, Kynar, or bare) is chosen with regard to chemical compatibility, as well
as probe response and ability to withstand abrasion.
All Princo continuous level probes connect to their respective electronic units by means of a 1"
NPT threaded hub. The "ground" contact is made by the threads themselves. The "active"
contact is made by the spring-loaded pin which projects from the center of the hub NPT fitting.
Probes mount to the storage vessel by means of various sizes of flanges, NPT connectors and
TRI-CLAMP™ fittings. Refer to Section 2.2 for details.
For detailed listings and specifications for Princo Continuous Level probes, consult Princo
Bulletin L-96-4.
Figure 1-3
Typical 1" NPT Mounted Probe (Model L101)

Section One
Description
1-6
Figure 1-4
Typical 3" Flange Mounted Probe (Model L127)
Figure 1-5
Typical Dual Flexible Probe (Model L115)

Section Two
Specifications
2-1
A. Specifications
1. L3610 AND L3610R CONTINUOUS LEVEL TRANSMITTERS
•TYPE
Continuous level to current transmitter, high frequency, impedance sensing.
•SPAN RANGE
From 0.5 to 100 feet typical. Shorter and longer spans available with special probes.
Consult Factory.
•OUTPUT SIGNAL
4 to 20 mAdc into 500 ohms is standard. 0 to 5 Vdc and 0 to 10 Vdc outputs optional.
•REPEATABILITY/ LINEARITY
0.5% of span over entire range span, process dependent
•AMBIENT TEMPERATURE RANGE
-30 to 150 °F (-34 to 66 °C)
•TEMPERATURE STABILITY
Maximum error of 0.25% per 30°F change, or within 1.5% over entire 180°F ambient
temperature span.
•PROCESS CONDUCTANCE ALLOWED
Tolerates process coating conductance up to 5000µS (200 ohms of composite resistance).
•REMOTE MOUTING DISTANCE
Up to 50 feet (cable connected) for all but the shortest span values.
•POWER REQUIREMENTS
104 to 126 Vac, 50 to 60Hz, 5 watts; or 207 to 253 Vac, 5 watts; or 21 to 26 Vdc, 5 watts.
•ELECTRONIC HOUSING
Heavy-duty, cast aluminum.
Explosion-proof for: Class I, groups C & D; Class II, groups E, F & G.
Weather proof: NEMA 4.
•FM APPROVAL
The L3610 is Factory Mutual Approved as a measurement system when used with various
L100 Series Probes as defined in Figure 4-2. The L3610R is not FM approved.
2. L100 SERIES PROBES
•TYPE
Single and dual element continuous, RF impedance level probes.
•DESCRIPTION BY MODEL NUMBER
The below list includes the most commonly used probes. Princo also makes other variations for special
applications.

Section Two
Specifications
2-2
MODEL
NO. ELEMENT
CONFIGURATION TYPE VESSEL
CONNECTION INSULATION
OPTIONS
L101 Single Rigid 1" NPT B, KP, KS, TP, TS
L104 Single Rigid 1", 2", 3" OR 4"
TRI-CLAMP™ B, KP, KS, TP, TS
L102 Dual Concentric Rigid 1½" NPT B, KP, KS, TP, TS
L107 Dual Concentric Rigid 1" NPT B, KS, TP, TS
L109 Single Flexible 1" NPT KW, TW
L113 Dual Parallel Flexible 1" NPT KW, TW
L115 Dual Parallel Flexible 3" Flange KW, TW
L116 Dual Parallel Flexible 3" Flange KW, TW
L127 Dual Parallel Rigid 3" Flange B, KP, KS, TP, TS
L128 Dual Parallel Rigid 3" Flange KP, KS, TP, TS
B = Bare (No insulation)
KP = Kynar® Pipe (60 mil Kynar over carbon steel)
KS = Kynar Sheath (17 mil Kynar over 316 SS rod)
TP = Teflon® Pipe (60 mil PFA Teflon over 316 SS rod)
TS = Teflon Sheath (17 mil Teflon over 316 SS rod)
KW = Kynar Wire (20 mil Kynar over 316 SS wire rope)
TW = Teflon Wire (12 mil Teflon over copper wire)
•PRESSURE / TEMPERATURE RATINGS
Pressure Rating (PSI) at Temperature Indicated (ºF)Model
Number Probe
Covering -300
-40
100
250
300
400
500
Teflon or Bare
1250
1250
1250
550
450
350
0
L101, L102,
L104, L107,
L109, L113 Kynar
1000
1000
250
0
Teflon or Bare
2751275127512251
2101
1801
0
L115, L116,
L127, L128 Kynar
2751
2751
2251
0
NOTES:
1. Rating of Carbon Steel 150 lb. flange. For higher ratings, consult factory.
2. Temperature Limits: Bare or Teflon covered probes: -300ºF (-184ºC) to 500ºF
(260ºC); Kynar covered probes: -40ºF (-40ºC) to 300ºF (149ºC). For
temperatures beyond these limits, consult factory.
•SELECTION GUIDE / PHYSICAL DIMENSIONS
Refer to Princo Bulletin L-96-4, Continuous Probe Selection Guide

Section Three
Installation
3-1
A. Inspection
The L3610 and L3610R Transmitters are supplied with one of the Princo L100 Series Level
Probes. The Transmitter and Probe are shipped in separate packages.
Carefully remove each package's contents and check each item against the packing list. Inspect
each item for shipping damage. In particular, check the spring-loaded connection pin, located on
the threaded hub end of the Probe (see Figures 1-3, 1-4 and 1-5). This pin provides the
necessary electrical connection from the Transmitter bottom printed circuit board, to the active
element of the Probe. Make sure this pin is not missing, bent, jammed, or otherwise damaged.
If the Probe is sheathed in Teflon or Kynar, then carefully inspect the condition of the sheathing.
Make sure the sheathing forms a smooth continuous coverage over the element. Discontinuities
in the sheathing material, which breach through to the metal underneath, will render the Probe
useless in most applications. Report any such damage immediately to the factory.
CAUTION !
Care must be exercised when handling probes that incorporate an insulating sheath. Do not
allow the sheathed sensing element to come in contact with a rough or sharp surface, as this
may cause a breach in the insulating sheath, and render the probe inoperable.
B. Mounting
1. Headroom
Proper specification of a Princo Model L100 Series Probe must take into consideration the
amount of space available above the storage vessel from which the Probe can be lowered into
the vessel. This aspect must be considered prior to probe selection and ordering.
In a situation where headroom limits the use of a rigid type probe, a flexible cable type probe
can be used. Refer to Figure 1-1 for electronic housing dimensions. A typical cable probe with a
3-inch flange adds about 3½ inches to the height. Additional headroom is needed to remove
the lid and access the top panel controls and terminal blocks.
2. Mounting Location
Single element probes use the metal tank wall as a ground reference. If they are used in non-
conductive applications, they must be mounted close to the sidewall of the tank (6 to 8 inches
recommended) and should maintain an equidistant spacing from the sidewall, as the spacing
affects measurement linearity. (Princo generally recommends use of factory-made dual
element probes for this reason.) When it is impossible to mount the sensing probe close to the
sidewall, at least try to favor an off-center mounting. In conductive applications, single element
probes may be mounted anywhere relative to metal tank walls. Refer to Figure 3-1.
Dual element probes have a built-in ground reference and generally can be mounted anywhere
relative to tank walls, irregardless of whether the process is conductive or non-conductive.
Be careful not to mount probes any closer than necessary to such devices as baffles, agitators,
heaters, etc. This is especially important when the process is non-conductive. When the
process is conductive, it is only necessary to have adequate physical clearance, since there
should be little or no adverse electrical effects due to proximity of these devices.
Whether the process is conductive or non-conductive, try to mount the probe in an area where
the level is stable and representative. Mounting near an input flow or near splashing might

Section Three
Installation
3-2
create artificially high level readings. Mounting in a vortex created by a mixer might give an
atypically low reading.
Figure 3-1
Probe Mounting Locations

Section Three
Installation
3-3
3. Ground Reference
Normally, dual element probes (probes with built-in ground references) are used in non-metallic
storage vessels. A single element probe may be adapted to the same purpose by supplying a
ground reference. The ground reference should be a metal rod, equal in length to the Probe.
The reference should be mounted parallel to the length of the Probe, no greater than 6 to 8
inches from it.
The reference must be electrically connected to the Transmitter chassis ground, either directly
to the terminal strip ground terminal, or indirectly, by wiring it to the threaded hub of the probe or
to the metal housing of the electronic unit. In any case, perform Ground Continuity Check,
Section 4.E.6.a to ensure that a good ground connection exists.
If the process is non-conductive, non-parallel spacing between the probe and the ground rod will
negatively affect the linearity of the level readings. Also, the probe response will decrease as
the distance between the two elements increases.
4. Flange or NPT Mounting
Princo L100 Series Probes are normally mounted by means of a flange (typically two or three
inch insertion hole diameter) or an NPT type fitting (standard size is one inch).
a) Flange Type. Slip the Probe tip into the storage vessel entry port. Lower the Probe into the
vessel, until the probe flange seats and aligns with the corresponding mating surface on the
storage vessel. Fasten the flange to the vessel using the appropriate metal fasteners, gaskets,
and sealing compounds, as required by the specific installation.
CAUTION!
Single element flange type probes must be fastened to the storage vessel with metal fasteners,
such that electrical continuity exists (zero ohms) between probe flange and metal storage
vessel. NPT type probes must be fastened to the storage vessel such that electrical continuity
(zero ohms) exists between the probe NPT hub and the metal storage vessel. Do not use any
kind of thread lubricant on the NPT threads. If lubrication and/or sealing are required, a small
amount of Teflon tape can be used. Refer to Section 4.E.6.a for ground continuity testing.
b) NPT Type. Slip the Probe tip into the storage vessel NPT threaded entry port. For probes
sheathed with Teflon or Kynar, it is recommended to temporarily line the entry port with
cardboard or plastic sheeting to avoid skiving the probe sheathing while guiding the probe
through the opening. Lower the Probe into the vessel until the Probe lower hub NPT fitting seats
into the vessel NPT receptacle. Tighten the Probe lower hub NPT threads into the storage
vessel NPT receptacle using an appropriately sized wrench on the Probe hub hex head fitting
5. Cable Probe Tie-Down
Princo flexible cable type probes incorporate either a weight or a tie-down at the probe tip,
which is designed to keep the sensing element taunt as it is immersed in the process material.
Refer to Figure 1-5.
If the process material is agitated or is turbulent in any way, it may be necessary to fasten the
Probe tip to the bottom of the storage vessel. This can be accomplished by using a light cable or
nylon rope, looped through the hole in the bottom of the weight or tie-down and, in turn, through
a hook fitting in the bottom of the storage tank.
Do not apply excessive downward force to the cable sensing element through the tie-down. It is
not necessary and could potentially damage the probe.
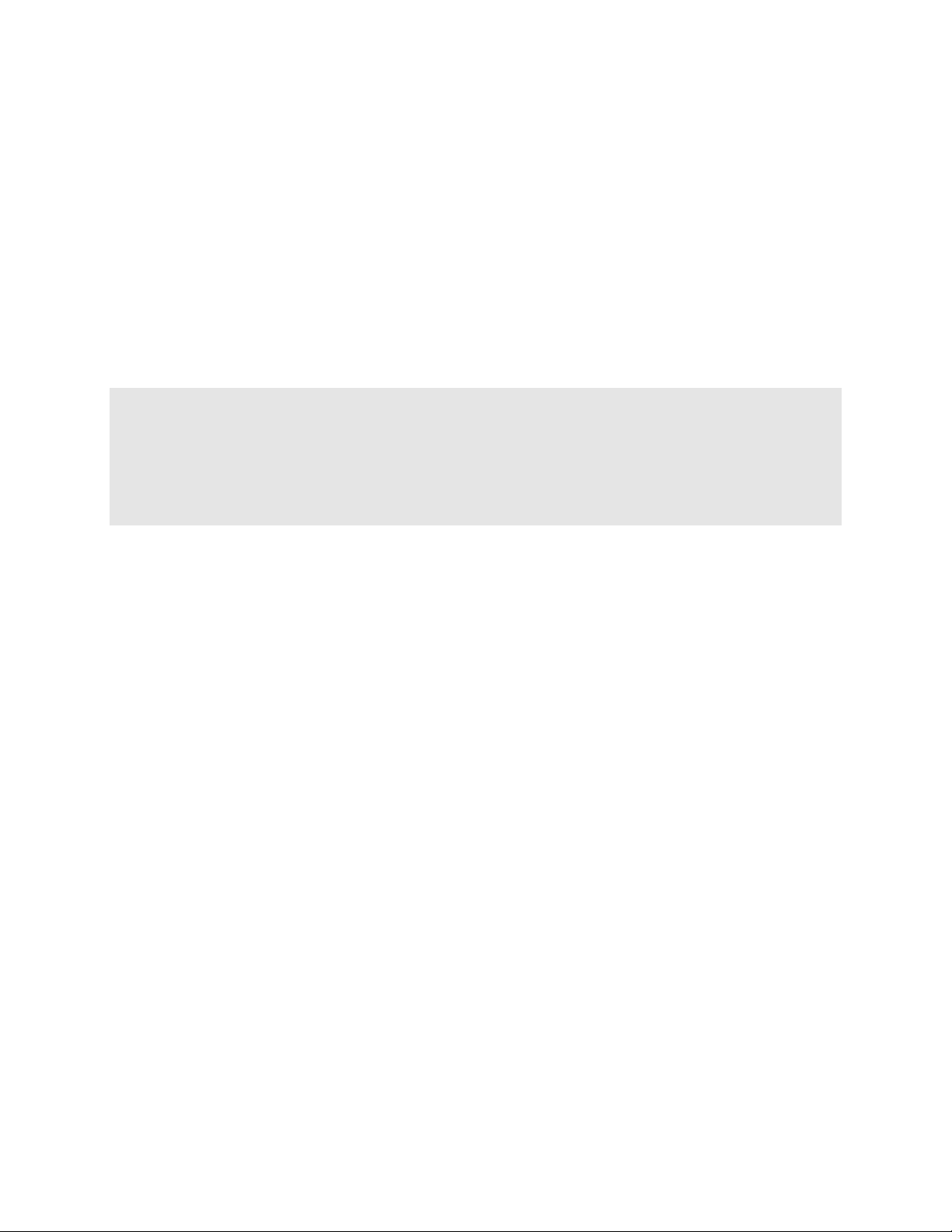
Section Three
Installation
3-4
Also, note that the weight or tie-down is not an electrically active part of the probe. That is, it
stands below the zero level of the measured process material. Standard weight length is six
inches. Standard tie-down length is three inches.
Teflon spacers on dual element probes (L113, L115, & L116) are designed to keep the dual
cables equidistant. Try to maintain even spacing between them, and avoid crossing of cables
by excessive twisting, as this will affect accuracy and linearity.
6. Electronic Housing Mounting
The electronic chassis of "integral" units (L3610) is contained within a cast aluminum housing.
It is mounted onto the top of the probe by threading the housing's bottom NPT opening onto the
probe hub's 1" NPT connector. As with the probe to tank connection, electrical continuity must
be maintained through the threaded connection.
NOTE
Do not use any type of thread lubricant on the NPT probe mounting threads or the NPT threads
which mount the electronic housing. Application of thread lubricant may cause faulty or improper
ground connection. If required, Teflon tape may be used as a thread seal for either threaded
connection. If Teflon tape thread sealant is used, the installer should make an electrical
continuity check with a hand held ohmmeter. Less than 1 ohm resistance should exist between
the storage vessel and the electronic housing. See Section 4.E.6.a.
The spring-loaded pin projecting from the middle of the probe NPT fitting should now be
pressing against the underside of the bottom circuit board of the electronic chassis. This may
be verified visually through the 1" NPT wiring port on the side of the housing. If the pin is failing
to make contact, stretch the spring-loaded pin out further with a pair of pliers. To access the
spring-loaded pin, either unthread the housing from the probe hub, or lift the electronic chassis
out of the housing after removing the two 8-32 screws which hold it in. Hint: If the spring-loaded
pin is properly contacting the circuit board, you will feel the chassis being pushed upward by it
as you loosen the two 8-32 screws.
With "remote units" (L3610R), the procedure is basically the same, except that it is the Model
L216 Remote Head which is threaded onto the probe NPT fitting. The electronic chassis is
contained in a clear-covered, plastic, NEMA 4X housing that is mounted in a location of the
customer's choosing and connected by tri-axial cable to the probe via the L216 circuit board.
C. L3610 Electrical Connections (Integral Units)
Remove the lid of the L3610 Transmitter in preparation for connection of signal and power
wires. Before drawing wires into the equipment housing, remove the electronic circuit board
chassis. This may be done by removing the two 8-32 chassis mounting screws and lifting the
chassis off of the mounting posts and out of the housing. Bring the signal/power wires into the
Transmitter housing through the 1" NPT wiring port. Leave enough slack in each wire to make
connection to the terminal block at the top of the Transmitter.
Replace the electronic chassis in the housing, the flat side of the printed circuit boards facing
the wiring port. Slide the chassis onto the mounting posts, keeping the wires toward the housing
inner wall, so as not to interfere with the chassis. Replace the two 8-32 mounting screws and
tighten firmly to ensure proper chassis electrical ground connection.

Section Three
Installation
3-5
WARNING!
For installation which must be explosion-proof, and/or weatherproof, it is the customer's
responsibility to install conduit seals which meet applicable safety standards and/or
weatherproof requirements.
Connect the power and signal wires to the terminal strip as according to the appropriate wiring
diagram: Figure 3-2 for 24 Vdc, 3-wire; Figure 3-3 for 24 Vdc, 4-wire; and figure 3-4 for 115 Vac
and 230 Vac. Make certain wires are installed with correct polarity orientation.
Figure 3-2
L3610 3-Wire Electrical Connections, 24Vdc Input

Section Three
Installation
3-6
Figure 3-3
L3610 4-Wire Electrical Connections, 24Vdc Input
Figure 3-4
L3610 4-Wire Electrical Connections, 115Vac Input

Section Three
Installation
3-7
D. L3610R Electrical Connections (Remote Units)
The Model L214 tri-axial cable connects the probe to the L3610R electronic chassis through two
three-connection terminal blocks. One is located on the circuit board of the L216 Remote Head.
The other is on the electronic chassis mounting plate inside the plastic NEMA 4X housing.
Refer to Figure 3-5 for the wiring diagram. Note that the wiring order on both terminal blocks is
the same from left to right -Red (guard), Clear (active), and Black (ground). The cable may be
drawn through the 1" NPT port on the side of the L216 housing and connected accordingly.
Likewise, the other end of the cable can be drawn through one of the two ½ " NPT wiring ports
on the control unit housing and connected to its terminal block.
The power and current output wires can be drawn through the other ½" wiring port and
connected appropriately as per figure 3-5.
Figure 3-5
L3610R Electrical Connections
E. Installation in Hazardous Areas
The outline which follows points out some of the major requirements of the NEC's (National
Electric Code) Section 501, as it relates to typical level control installations.
WARNING!
For applications which MUST BE explosion-proof and/or weatherproof, it is the customer's
responsibility to install the required conduit, seals, wiring, etc., which meet national, as well as
applicable local and plant safety codes.
For Class 1 locations, rigid metal conduit must be used. At least five full threads of the conduit
must be tightly engaged in the enclosure. Conduit seal fittings must also be used. These seal
fittings, must be filled with an approved sealing compound and must be installed within 18

Section Three
Installation
3-8
inches (or closer) of the enclosure. Conduit seals are also required when the conduit passes
from a hazardous area into a non-hazardous area. Water drain seal fittings eliminate or
minimize the effect of water that tends to collect in the conduit or enclosure due to
condensation.
Approved wire type, such as mineral-insulated wire, is required for use in Division 1
installations. Certain types of metal-clad cable or shielded non-metallic sheathed cable are
permitted in Division 2 installations. When multi-conductor cables are used in the conduit, the
outer jacket must be cut away in such a manner that allows the sealing compound to surround
each insulated wire as well as the jacket.
The preceding information should act as guide to assist the customer/installer in satisfying their
responsibility for producing safe installations in hazardous area.
F. Ground Isolation
Ground Isolation refers to the degree of electrical isolation between an instrument’s “circuit
common” (SIG -) terminal, and “earth ground” (G) terminal. An instrument without ground
isolation has a direct electrical connection between its signal minus terminal and chassis
ground.
The standard L3610 unit is shipped from the factory without ground isolation. If ground isolation
is required, it can be easily provided in the field by cutting open the ground isolation jumper wire
(JA1) and connecting a Ground Isolation Capacitor between the G and the SIG -terminals on
the terminal block. The jumper wire is located on the top printed circuit board. The Ground
Isolation Capacitor is a 0.4 µF, 500 Vdc ceramic capacitor which is available from the factory as
Princo part number A60-3610-25. Refer to Figure 4-3.
There are several situations where ground isolation is required:
•The negative signal leg drives a ground referenced input to a Computer (PLC).
•The metal storage vessel resides at an electrical potential that is elevated above “earth
ground”.

Figure 3-6
L3610 FM Approval Drawing
3-9
This manual suits for next models
1
Table of contents
Popular Transmitter manuals by other brands

Minebea Intec
Minebea Intec PR 5230 Instrument manual
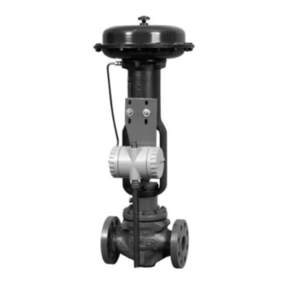
Emerson
Emerson Fisher 4210 instruction manual
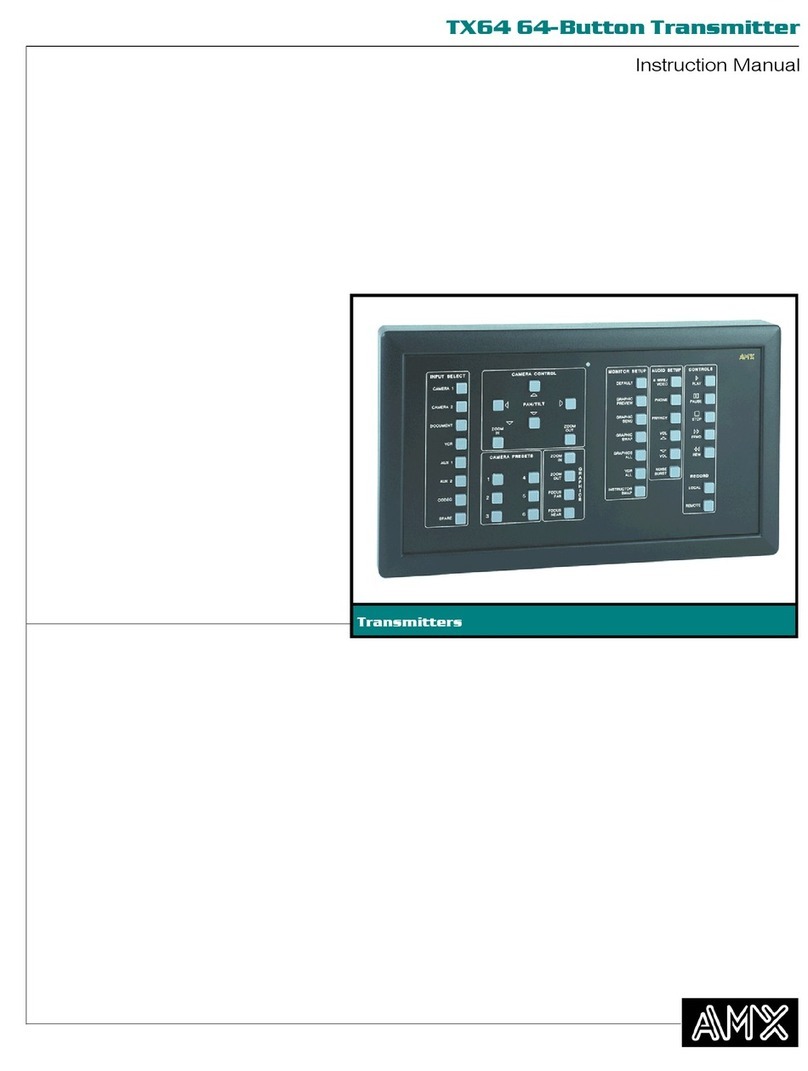
AMX
AMX TX64 instruction manual
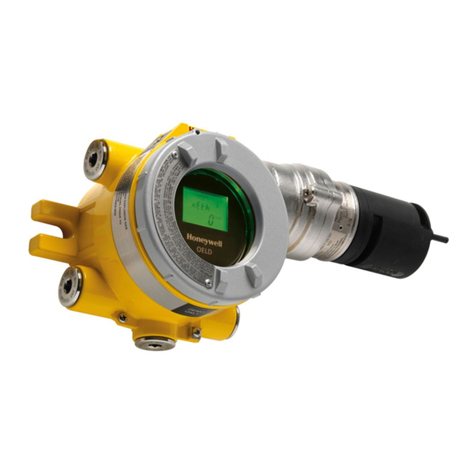
Honeywell
Honeywell OELD operating instructions

American Fibertek
American Fibertek MT-1890 instruction manual

Camille Bauer
Camille Bauer KINAX WT 707-SSI operating instructions
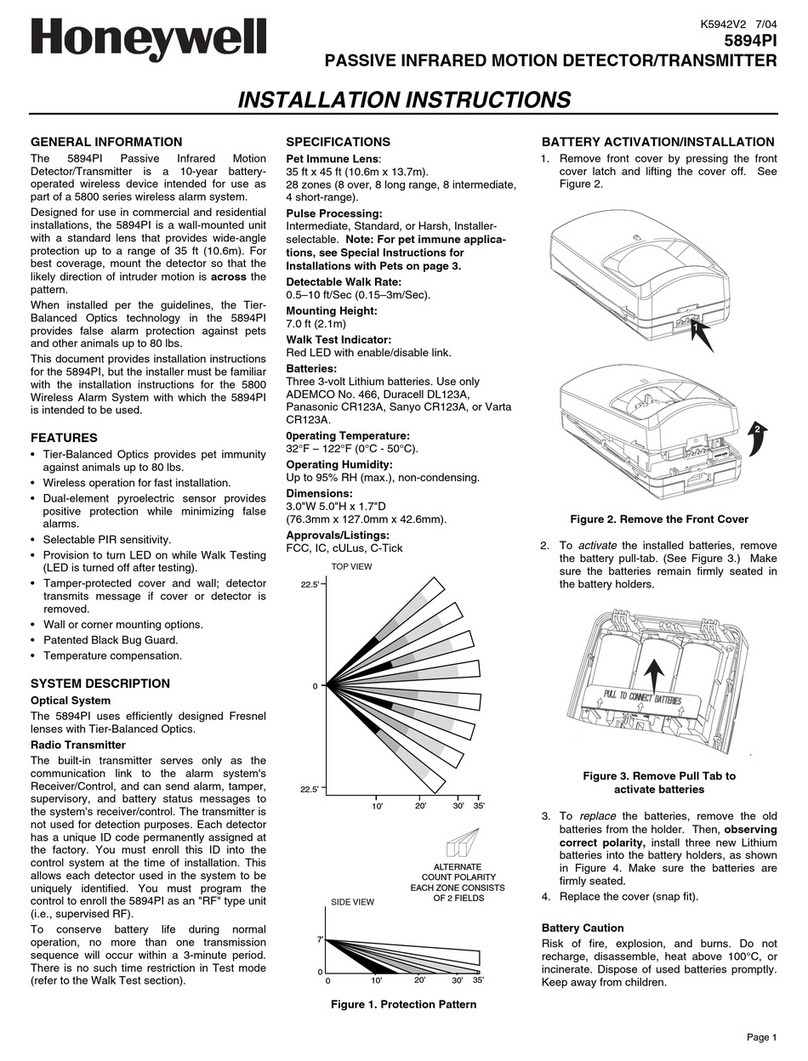
Honeywell
Honeywell 5894PI - Ademco Wireless PIR Motion Sensor installation instructions
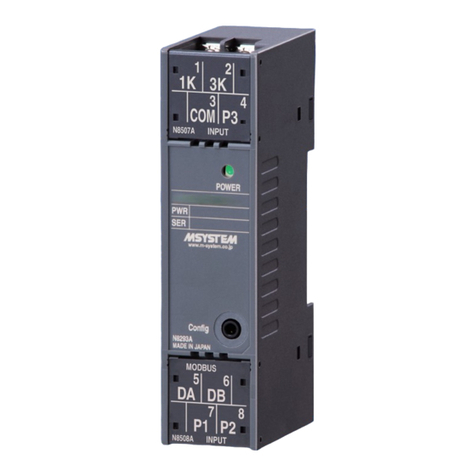
M-system
M-system M5XU-1-R instruction manual
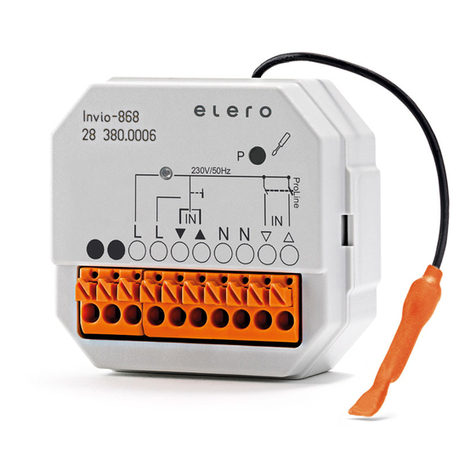
elero
elero Invio-915 operating instructions
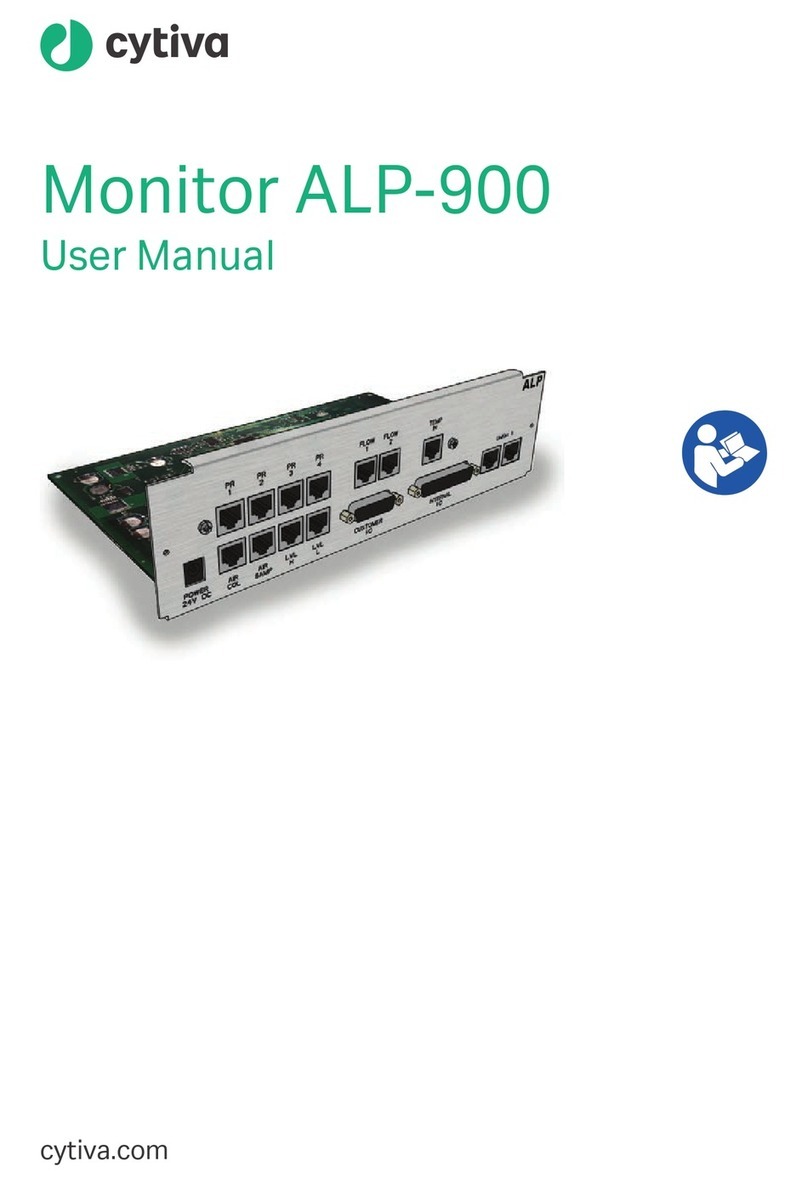
cytiva
cytiva Monitor ALP-900 user manual
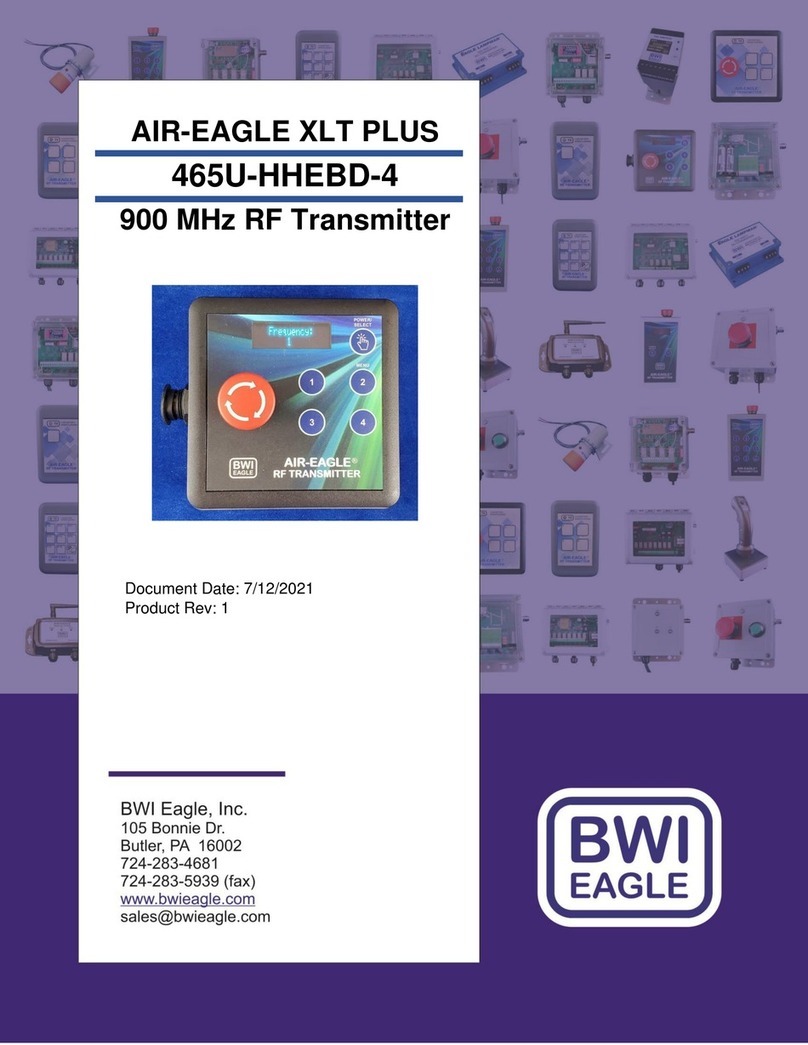
BWI Eagle
BWI Eagle AIR-EAGLE XLT PLUS 465U-HHEBD-4 quick start guide

TR-Electronic
TR-Electronic ID-200 user manual