ProAir TPK 21 LT Operating instructions

Pressure Dew Point Monitoring Device !
TPK 21 LT
Functional description and operating instructions


Table of contents
1.
Scope of Delivery
1
2.
General dangers and precautions
2
2.1.
Safety instructions for electrical connection
2
2.2.
Safety instructions for compressed air systems
3
3.
Important application notes
4
3.1.
Avoiding damage to the measuring probe
4
3.2.
Calibration and measuring accuracy
4
3.3.
Intended application
5
4.
Humidity measurement in compressed air systems
5
5.
Function
5
6.
Mounting of the device
6
6.1.
Safety instructions
6
6.2.
Application notes
6
6.3.
Procedure for installation
7
6.4.
Mounting
7
7.
Connection at the compressed air network
8
7.1.
Direct stationary assembly at the compressed air line
8
7.2.
Stationary assembly via hose
8
7.3.
Application of a pre-filter / water separator
9
7.4.
Mounting examples
9
7.5.
Adjustment of measurement chamber choke
10
7.6.
Connection of power supply
11
7.7.
TPK Start-up
12
7.8.
For the rarest of the cases…
12
8.
Operation
13
8.1.
Views of unit
13
8.1.1.
Front view
14
8.1.2.
Side view (from the right)
15
8.1.2.1.
Connection to power supply
15
8.1.3.
View (from below)
16

Table of contents
8.2.
Display
16
8.2.1.
Description of display
17
8.2.1.1.
Description of main screen
17
8.2.1.2.
Description info screen
18
8.2.2.
Adjustment of display fields
19
8.2.2.1.
Possible display variation concerning the different fields
20
8.3.
Personalising Password
22
8.4.
Adjustment of national languages
27
8.5.
Information
30
8.6.
Switching the heating(Heater) system On and Off
33
8.7.
Factory settings
36
8.8.
Outputs
39
8.9.
Touchscreen calibration
44
8.10.
Measurement value simulation
47
8.11.
Statistics Reset
52
8.12.
Reset Fault Memory
55
8.13.
Quit Alarm
58
8.14.
Quit Service
61
8.15.
Filter
64
8.16.
Units setting
67
8.17.
Setting the Date / Time
70
8.17.1.
Setting the Date
70
8.17.2.
Setting the Time
74
9.
Configuration of Relay Adjustments
78
9.1.
Setting Source (Output Parameters)
80
9.2.
Setting the Relay Switching Characteristics
81
9.3.
Setting the Limit Values
82
10.
Configuration of Analog Output
84
10.1.
Selection of desired Source (Output Parameter)
86
10.2.
Selection of the desired analog output value
87

Table of contents
10.3.
Configuration of lower analog output value
88
10.4.
Configuration of upper analog output value
89
11.
Configuration of Alarm Output
90
11.1.
Setting of desired alarm value 1
91
11.1.1.
Setting of desired measurement - channel (source)
91
11.1.2.
Setting Pre-alarm
93
11.1.3.
Setting Main-alarm
98
11.1.4.
Setting delay
103
12.
Setting of desired alarm value 2
105
12.1.
Technical Datas
107
13.
Appendix
109
13.1.
Menu structure
110
13.1.1.
Menu item: Main
110
13.1.2.
Menu item: Out
111
13.1.3.
Menu item: Alarm
112
13.2.
System References and Messages
113
13.3.
EG-Conformance Details
114
13.4.
Guarantee
114
13.5
Accessories
115
13.5.1.
Connecting optional accessories
116
13.5.2.
PIN - Assignment for Conctor
117
13.5.3.
Voltage supply from an external source of supply
119
13.6.
Trouble Shooting Guide
120
13.6.1.
The measured value is flow dependent and too high (i.e. too humid)
120
13.6.2.
The measured value is too high (i.e. too humid)
120
13.6.3.
The measured value is too low (i.e. too dry)
121
13.6.4.
The measured value varies significantly
121
13.7.
Service and Calibration
122


1 Scope of Delivery
1
!
Please read the operating instructions before using this device. In addition to the
operating instructions, important information is provided regarding installation,
initial start-up and troubleshooting in each of the relevant chapters.
The pressure dew-point monitor is supplied ready to use. The scope of delivery includes the
AC adaptor, stylus, stylus holder (which may be attached to the dew-point meter) and
relevant operating instructions.
You may also require:
-Mounting tools, screws and wall plugs
-6 / 4 mm compressed - air - hose (WARNING! Use only PTFE hoses!).
-further nipples, reducers and adapter pieces, if the device is to be integrated into a pipeline.
- Electrical accessories for connection to higher-level overriding control devices.
- Optional accessories, such as external indicator lights, terminal adapters and PC cables!
(see accessories overview).

2 General dangers and precautions
2.1 Safety instructions for electrical connection
2
Please read the following warnings prior to initial start-up! The symbols used in the
operating instructions are intended to call your attention to the safety risks. It is not
enough to simply observe the symbol. It is important to read the full text provided in
the safety instructions!
This symbol indicates a potential risk to humans, equipment or the environment. The
information provided must be strictly observed in order to prevent risks.
This symbol indicates important instructions for use and tips that are important in
order to successfully complete tasks, and which must be strictly observed to ensure
good results.
!
!
!
The device must only be supplied with extra-low voltage. The device's other
electrical connections must also only be connected with electronic components
that are operated via an extra-low voltage supply.
Contact with live parts may result in death. Installation of the controller and
maintenance work must therefore only be carried out by trained personnel. The
power supply must be turned off for installation and servicing.
Also avoid touching the plug or any other electronic components when the
power is switched off. Electrostatic phenomena may damage electronic
components.
The product is not intended to control systems with safety-related functions. Even
during normal operation there is a risk of unexpected malfunction, for example
due to a surge or the failure of a component. The user must make sure that no
damage can occur as a result of a malfunction or undefined device status. This
can be achieved, for instance, through the use of redundant components or
safety circuits.
Incorrect screw tightening torques at the connecting terminals or the use of
unsuitable tools can damage the terminal, resulting in damage to insulation or
the contacts. Poorly connected cables can come loose during operation, posing
a considerable risk to safety. Contact resistance at clamp connections results in
increased heat production that can cause a fire to start. Incorrectly wired
connections can destroy electrical components and result in other damage.
!

2.2 Safety instructions for compressed air systems
3
In the case of unforeseen events, the energy stored in compressed air can cause
material damage or result in injury. The risk increases with the operating
pressure of the system. All work must therefore be performed by appropriately
trained personnel. Appropriate care is necessary when performing any work on
the compressed-air system in order to avoid damage!
The loud venting noise produced upon uncontrolled opening of pressurised lines
can damage hearing or startle other people in the vicinity.
At high flow rates, foreign bodies in the air stream can behave like projectiles
and cause injury to the skin or eyes.
The built-in measuring chamber with sensor is designed to handle pressures of
up to 17 bar. This maximum permissible operating pressure must not be
exceeded. Upstream components must be dimensioned according to the
system's operating pressure and temperature.
The warranty will become null and void if the sensor housing is opened, the
sintered cap removed or in the event of improper handling or the use of force.
!

3 Important application notes
3.1 Avoiding damage to the measuring probe
3.2 Calibration and measuring accuracy
4
Measuring devices are sensitive and must be handled with care:!
Avoid shocks, impacts and vibrations.
The sintered filter protects the sensor against mechanical stress and contamination.
Do not remove the filter. Only use the probe if the sintered filter is undamaged!
Prior to installation, check that there is no condensation, oil or dirt at the measuring
point! Should this be the case, repair and dry out the system!
The measuring system is not suitable for use with compressed air with a high oil content,
as directly covering the sensor with a film of oil impairs its response, blocks the pores of
the filter and damages the filter choke.
As a rule of thumb: If you have any questions, contact the manufacturer.
Do not attempt to experiment with the device as you may cause faults and damage
to occur!
!
Prior to delivery, the pressure dew-point sensor is adjusted and tested by means of a complex
calibration procedure involving several temperatures and humidity points. It is not possible for
the end user to calibrate the device.
Please observe the permissible temperature range for use. Excessive temperatures reduce the
measuring accuracy. The probe will be damaged if the temperature limit is exceeded.
The specified data, in particular the desired measuring accuracy, are valid at a temperature of
20°C. In principle, the lower the temperature at the sensor, the more accurate the measurement
result. If possible, measurements should be taken in a cool area, or the gas should be cooled to
ambient temperature.
With proper use, the probe will have a lifespan of many years. Nevertheless, to prevent errors,
it is important that the sensor be calibrated once a year, according to the manufacturer's
specifications. This particularly applies when the probe is used in critical applications within the
lower dew-point measuring range.

3.3 Intended application
4 Humidity measurement in compressed air systems
5 Function
5
The new TPK 21 LT is intended to be used to measure the pressure dew points, pressure
and temperature of clean, oil-free compressed air, which is free of any abrasive,
corrosive, caustic, toxic, flammable and combustible components. For the scope of
application and the calibrated measuring range, please refer to the technical data.
!
In the industrial sector, quality requirements for compressed air are becoming ever stricter.
Humidity and condensation are not permitted in compressed air and often cause damage to
machines and lead to reduced production quality. Compressed-air dryers are commonly used.
When used correctly, these reduce the moisture content of the air and ensure the production
of high-quality compressed air.
However, problems with dryers are often detected very late on, usually when damage has
already occurred. A large quantity of humidity will have already entered the compressed-air
network, and considerable efforts will be required to dry the system out again. The high
quality standards of the industrial sector call for continuous, reliable and stable long-term
monitoring of the humidity content. This is the only way to detect problems early, before any
damage has occurred.
With its large measuring range, the new TPK series is the ideal measuring system for
monitoring refrigeration, adsorption and membrane dryers. The device is primarily intended
for stationary applications but is also suitable for use as a portable measuring device thanks
to its simple connection system.
If compressed air is not dried before being fed into the compressed-air network, significant
quantities of condensate can form in the pipe network, resulting in the malfunctioning of
valves and pneumatic components, ultimately leading to loss of production. The pressure dew
point in compressed-air systems is therefore a key factor in determining air quality and should
be measured in all systems.
The new TPK series offers the ideal device for monitoring compressed-air quality (humidity,
pressure and temperature) and giving timely warning, before any damage has occurred.
The series has a built-in measuring chamber with a protection filter and filter choke, as well as
a plug connection for a 7.2 mm NW compressed-air socket. Power is supplied via the mains
adapter provided. Initial set-up of the measuring system therefore requires no interference
with the compressed-air network, nor any electrical installation work. Alternatively, the
measuring system can be installed on the compressed-air line to avoid the loss of scavenging
air.

6 Mounting of the device
6.1 Safety instructions
6.2 Application notes
6
The device must only be used for its intended purpose.
Installation of the controller and maintenance work must only be carried out by
trained personnel. The power supply must be turned off for installation and
servicing. The applicable safety regulations must be observed! All work on the
compressed-air system must be carried out under pressure-free conditions.
The device must only be operated with extra-low voltage. This also applies to all
external connections, such as the relay outputs.
!
The air quality at the site of installation must be checked prior to assembly. Repairs
must be made to the system in the case of any water or oil leakages. Contact with
large quantities or water or oil may damage the sensor.
The compressed air must be drawn from the upper side of the pipe. The device
must be mounted above the compressed-air line so that any condensation
produced in the event of failure cannot flood the measuring chamber.
Use only suitable materials. The materials used must be impermeable to water
vapour. Therefore please do not use regular polyurethane hoses! The only
recommended material for flexible hose connections is PTFE ("TEFLON"). All metals
are suitable down to -30°Ctpd. Below this, stainless steel is the preferred choice.
Avoid using excessively long sample-gas lines or unnecessary connectors.
The sensors on upstream components must not diffuse water vapour into the
surrounding environment! Please use only high-quality components, e.g. ball
valves with PTFE seals.
Carefully seal all points of connection with the sensor or measuring chamber.
However, never use anaerobic liquid sealants, as these maydamage the sensor
element!
Heavy particle loads will clog the filter or filter choke over time, resulting in a
delayed response. In critical cases, an additional fine filter must be installed
upstream of the measuring device.
!

6.3 Procedure for installation
6.4 Mounting
7
If using compressed air of unknown quality, use a condensate separator or particle
filter. Additional components must be suitable for the intended use!
In EMC-critical environments the measuring chamber should be electrically isolated
from the metal pipes of the compressed-air network. The use of a PTFE or
Polypropylene double nipple is an example of a suitable solution.
Installation involves the following steps:
- Mounting of the device, if necessary.
- Connection to the compressed-air network
- Adjustment of the filter choke, if necessary
- Connection to the power supply
- Initial start-up
- Setting of the switching points
- Testing and function control
If the device is operated as a portable device or is connected using a standard coupling, as
described below, no further mounting is required.
When mounting onto a machine, the device can be kept level by using mounting brackets. A
drilling template can be found in the appendix of this manual.

7 Connection at the compressed air network
7.1 Direct stationary assembly at the compressed air line
7.2 Stationery assembly via hose
8
In the case of stationary use, the device is usually installed downstream of the dryer/filter,
enabling the entire system to be monitored. It may also be installed at any point further
downstream in the distribution system in order to
monitor subsegments or the air supply entering a
particular machine.
In order to avoid unnecessary compressed-air
consumption through loss of scavenging air, the
measuring chamber with the sensor should preferably
be directly installed into the compressed-air line.
To prevent the accumulation of condensation in the
event of a fault, the measuring chamber must be
screwed vertically into the line from the top.
Extremely high flowrates or sudden pressure changes
should be avoided, as these may damage the sensor
element.
If a spur line is required for connection, this should
only be a few centimetres long, otherwise the
response will be impaired, especially at low dew-point
values. If longer spur lines are used, the choke must be opened onto the measuring chamber
and set to approximately 60 l/h.
Long, vertical spur lines impair the response or result in incorrect measured values.
!
The device may be alternatively connected to the compressed-air supply via a Teflon connection
line through the built-in measuring chamber with choke. To ensure correct functioning and
guarantee measuring accuracy there must be a throughflow of air. The basic flow rate can be set
at the choke. In order to avoid unnecessarily high loss of scavenging air, the flow at the rated
pressure can be set to 60 l/h by means of a flow meter. Check from time to time that there is air
flowing at the adjusting screw. If the choke is closed, the measuring device displays values that
are too high or triggers an alarm

7.3 Application of a pre-filter / water separator
7.4 Mounting examples
9
Depending on the state of the compressed-air system and distribution network, it is possible for
dirt, condensate or oil to leak out from the measuring point. In order to avoid damage to the
probe in such critical areas of application, a water separator with a fine filter can be connected
upstream of the device. The upstream components must not alter the moisture content of the air or
unduly impair the response. We can provide you with a list of suitable components upon request.
The device is suitable for a variety of applications. The flexible design of the measuring chamber
allows it to be easily adapted to the intended use:
Connection to a 7.27,2 mm NW quick coupler:
This connection can be quickly and easily performed
within minutes, without any complex installation.
-An NW 7.2 plug-in nipple with a 3/8" thread is
connected to the underside of the device.
-The device is connected directly to the coupling, and no
further mounting is required.
-The choke is set to approximately 60 l/h (factory setting,
as delivered).
!
Permanent connection to a compressed air line:
This type of connection is ideal when there is only a short
distance to the main line because no purge air is consumed.
-Underneath, a 3/8" double nipple is mounted and
connects to the pipe.
-In the case of direct connection to a main line, the choke is
closed.
-For greater connection distances or spur lines, the choke is
set to approximately 60 l/h.
!

7.5 Adjustment of measurement chamber choke
10
Connection via a compressed-air hose:
This connection variant is ideal, for example, if the device is
intended for portable use or mounted onto a machine or
panel.
-Underneath, the 3/8" thread is fitted onto a 6/4 mm
hose.
-The choke is set to approximately 60 l/h for stationary
applications (factory setting, as delivered). If used as a
portable device for rapid measurements the setting should
be changed to approximately 240 l/h.
-NOTE: Use only PTFE hose for the connection.
!
The choke's factory default setting is a 60 l/h basic flow rate at a pressure of 10 bar. So long
as the choke has not been adjusted, no adjustment is usually required, provided that this is the
desired flow rate.
Depending on the type of connection, the choke can be closed to avoid the loss of scavenging
air. This is done by fully tightening the Allen screw using the socket spanner provided.
If used as a portable device for rapid measurements the basic flow rate should be set to
approximately 240 l/h. To do this, the choke is opened until the screw is in line with the top
edge of the measuring chamber. The venting noise can clearly be heard in this position. The
response is faster with a high basic flow rate.
To reset the choke to 60 l/h for stationary applications, a flow meter is required, which is fitted
over the screw using a flat seal. The desired flow rate is achieved by repeatedly adjusting and
checking the flow.
Precise adjustment of the desired flow rate is particularly important in the case of stationary
applications, because too high a flow rate results in high operating costs.

7.6 Connection of power supply
11
The device is operated with extra-low voltage. A suitable mains adapter is
provided.
The power supply unit is plugged into the lower M12 socket.
No complex electrical installation is necessary, and the device is immediately
ready for operation
The AC adaptor with Europlug is of a high-quality design with a wide-range
input. It is suitable for a 90 - 240 V power supply and is therefore suitable for
Europe-wide use.
How to connect with mains adapter
Do not try to force the connector
when plugging it in.
!
Connection Diagram FGPx remote probe
Follow the guidelines for plugs and
sockets!!
8 Bedienung
8.1 Geräteansichten
13
Allgemeine Hinweise zur Beschreibung der Bedienabläufe
Alle Abbildungen des Displays, Zahlenwerte und dargestellte Konfigurationen sind
Beispiele, welche zur Erklärung und Verdeutlichung der übermittelten Inhalte verwendet
werden. Die tatsächliche Anzeige bei Ihrem Gerät kann entsprechend den gewählten
Einstellungen oder der Umgebungsbedingungen abweichen.
!
Seitenansicht
(von rechts)
Frontansicht
Ansicht
(von unten)
Ansicht
Isometrisch
DC 24 V
Temperatur
18.8

7.7 TPK Start-up
7.8 For the rarest of the cases…
12
The device immediately starts up when plugged into the power supply. There are no other
switches. The first measured values are displayed immediately after turning on the device. The
measured values are likely to fall immediately following connection to the compressed-air network.
The values will stabilise after a short time. Depending on the system, the following values should
be set:
- For refrigeration dryers: approx. 0 to 7°Ctdp
- For an additional membrane dryer: approx. -20 to -10°C
If the device does not start up, please check the following points:
- Is power arriving at the mains socket ?
- Is the mains plug correctly plugged in ?
- Is the M12 socket of the power supply correctly connected to the device ?
- Does the power supply unit deliver 24 V DC voltage (external power supply units ?
If you have examined all the possible causes and still have not managed to rectify the
malfunction, please immediately contact our customer service department. Do not
open the device, as this will invalidate the warranty claim !
!

8 Operation
8.1 Views of unit
13
General information on the description of the operating procedures
All images of the displays, numerical values and configurations are used by way of
example to explain and clarify the information provided. The actual display on your
device may differ according to the selected settings or ambient conditions.
!
Side view
(from the right)
Front view
View
(from below)
View
Isometric
8 Bedienung
8.1 Geräteansichten
13
Allgemeine Hinweise zur Beschreibung der Bedienabläufe
Alle Abbildungen des Displays, Zahlenwerte und dargestellte Konfigurationen sind
Beispiele, welche zur Erklärung und Verdeutlichung der übermittelten Inhalte verwendet
werden. Die tatsächliche Anzeige bei Ihrem Gerät kann entsprechend den gewählten
Einstellungen oder der Umgebungsbedingungen abweichen.
!
Seitenansicht
(von rechts)
Frontansicht
Ansicht
(von unten)
Ansicht
Isometrisch
DC 24 V
Temperatur
18.8

8.1.1 Front view
14
Warning- / Signal LED
LCD touch-display
Choke-adjustment screw
Built-in measuring chamber
Standard NW 7,2 plug-in nipple
(suitable for direct connection to the
compressed-air coupling)
Alarm LED
1
2
3
4
Assignment of the M-12 connection sockets:
Alarm output connection
Relay output connection
Analog output connection
Connection for external mains
adapter
1
2
3
4
Table of contents
Other ProAir Measuring Instrument manuals
Popular Measuring Instrument manuals by other brands

PureAire
PureAire KF-25 instruction manual
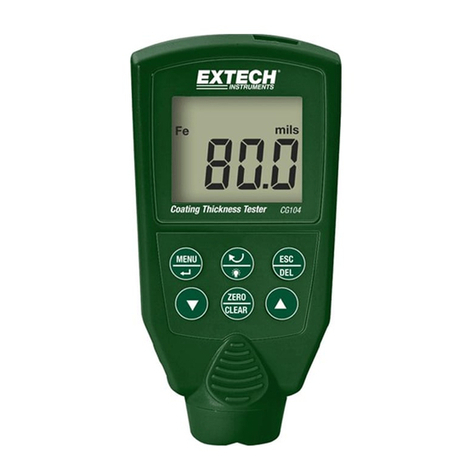
Extech Instruments
Extech Instruments CG104 user manual
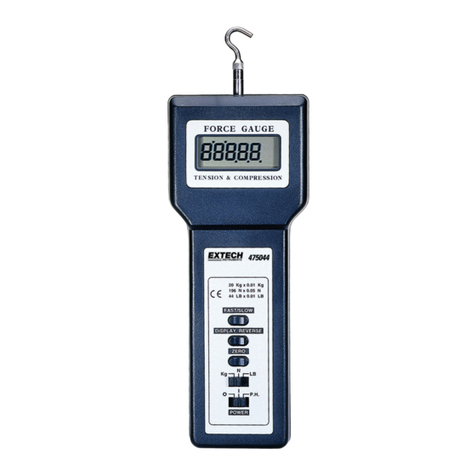
Extech Instruments
Extech Instruments 475040 user guide
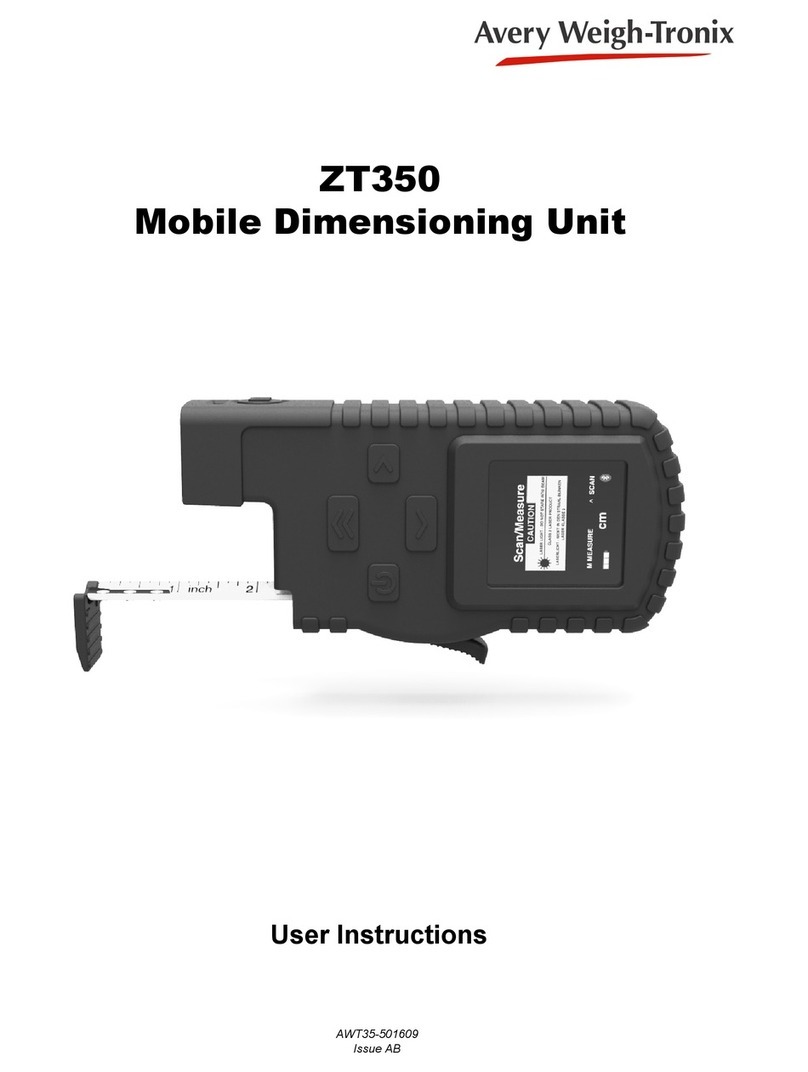
Avery Weigh-Tronix
Avery Weigh-Tronix ZT350 User instructions
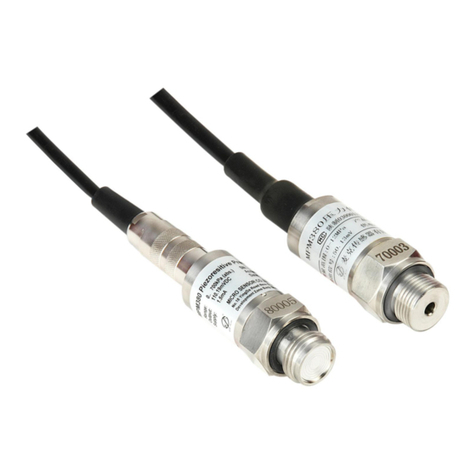
Microsensor
Microsensor MPM380 Operation manual
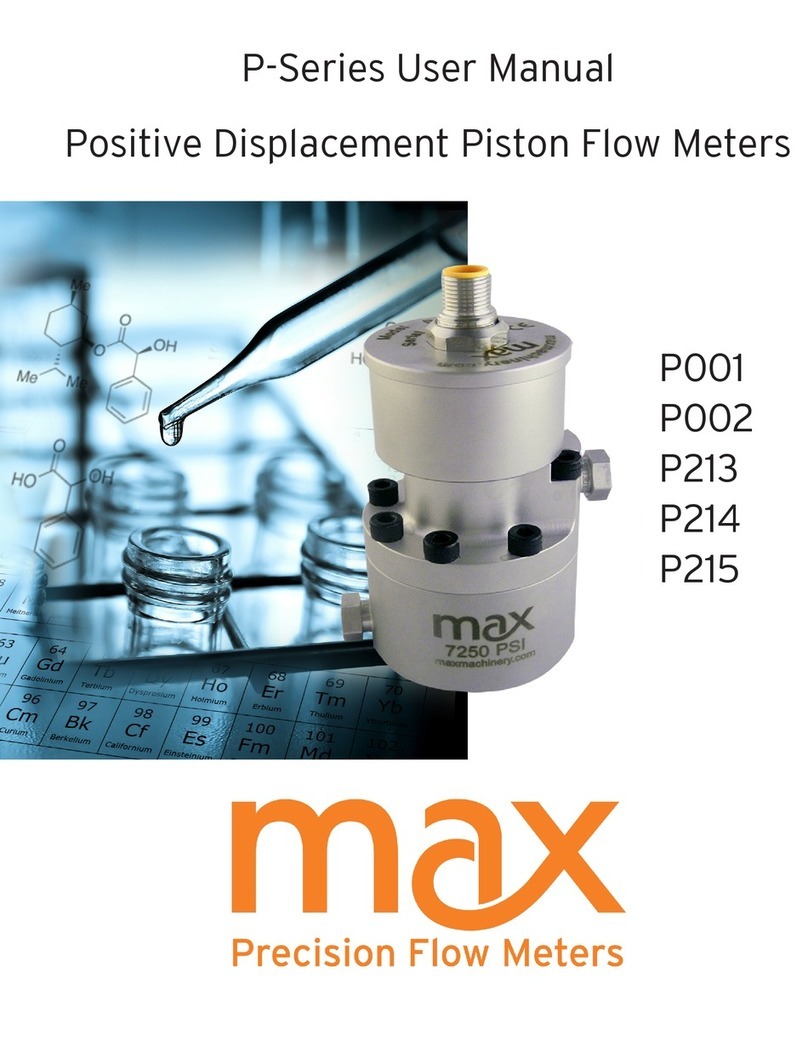
Max Machinery
Max Machinery P Series user manual