ProFlo PFB Series User manual

ProFlo Inc.
5960 Marion Dr. Denver, CO 80216 USA, Tel +1 720 201 5637
mkraft@profloinc.com; www.profloinc.com
FILTRATION SYSTEM
INSTALLATION & OPERATION
INSTRUCTIONS MANUAL
PFB-SERIES ELECTRIC
SELF-CLEANING SCREEN FILTER

Page 2 of 22
5960 Marion Dr. Denver, CO 80216 USA, Tel. +1 720 201 5637;
mkraft@profloinc.com; www.profloinc.com
FILTRATION SYSTEMS
Table of Contents
1INTRODUCTION ............................................................................................................................................. 3
2SAFETY INSTRUCTIONS .................................................................................................................................. 3
3DESCRIPTION & OPERATION.......................................................................................................................... 4
FILTER ASSEMBLY GENERAL DESCRIPTION................................................................................................................4
FILTER OPERATION GENERAL DESCRIPTION .............................................................................................................5
4TECHNICAL DATA........................................................................................................................................... 6
5INITIAL INSTALLATION & OPERATION............................................................................................................ 7
6MAINTENANCE & PERIODIC CHECKS.............................................................................................................. 9
ELECTRIC MOTOR REMOVAL & INSTALLATION .........................................................................................................9
SHAFT SEALING INSTALLATION ...............................................................................................................................11
BRUSHES SHAFT AND BRUSH UNITS REMOVAL & INSTALLATION ..........................................................................13
FILTRATION SCREEN ASSEMBLY REMOVAL & INSTALLATION .................................................................................14
PERIODIC CHECKS....................................................................................................................................................17
7TROUBLESHOOTING .................................................................................................................................... 18
8IPB.............................................................................................................ERROR! BOOKMARK NOT DEFINED.
9WARRANTY ................................................................................................................................................. 22

Page 3 of 22
5960 Marion Dr. Denver, CO 80216 USA, Tel. +1 720 201 5637;
mkraft@profloinc.com; www.profloinc.com
FILTRATION SYSTEMS
1INTRODUCTION
General
ProFlo congratulates you on purchasing a brand new PFB-Series Electric Self-Cleaning
Screen Filter. This filter now joins the broad product family of filters produced and
supplied by ProFlo for agriculture, municipal water and sewage systems, as well as all
types of industrial applications. All products manufactured by ProFlo are easy to install,
use, service, and operate.
For operation and maintenance of the filter please follow the instructions in this manual.
2SAFETY INSTRUCTIONS
2.1 Prior to installation or handling of the filter, carefully read the installation and
operation instructions.
2.2 Make sure that the filter is drained and electric power is disconnected prior to service
or maintenance.
2.3 Handle the filter carefully when lifting, transporting or installing.
2.4 When installing the filter, avoid splashing water directly on any of the filter parts,
especially on electric components and wiring.
2.5 Confirm that filter weight, when full, is within support construction tolerance.
2.6 Prior to installation, confirm that the line pressure matches the filter’s operational
pressure.
2.7 During installation, use standard flanges and connections only.
2.8 Check that all filter flange bolts are properly secured.
2.9 Be aware that the filter enters a flushing mode automatically, without prior warning.
2.10 Use original parts only when servicing the filter.
2.11 ProFlo can not accept responsibility for any changes or modifications to the
equipment.

Page 4 of 22
5960 Marion Dr. Denver, CO 80216 USA, Tel. +1 720 201 5637;
mkraft@profloinc.com; www.profloinc.com
FILTRATION SYSTEMS
3DESCRIPTION & OPERATION
FILTER ASSEMBLY GENERAL DESCRIPTION
The PFB-SERIES self-cleaning filter enables high quality filtration from grades of 200-4000
µm (micron) from various types of water sources such as sewage, reservoirs, rivers, lakes,
and wells.
The PFB-SERIES filter contains the following parts:
1. Outlet
5. Flushing outlet
2. Screen
6. Electric motor
3. Brush assembly
7. Inlet
4. Brush unit
Figure 1: Filter Assembly

Page 5 of 22
5960 Marion Dr. Denver, CO 80216 USA, Tel. +1 720 201 5637;
mkraft@profloinc.com; www.profloinc.com
FILTRATION SYSTEMS
FILTER OPERATION GENERAL DESCRIPTION
General Operation
Water enters the filter through the “Inlet” (7) and passes through the "Screen" (2), which
purifies the flow by separating smaller particles from the water. The purified water exits
the filter through the "Outlet" (1).
Self-Cleaning Process
As impurities on the "Screen" (2) accumulate, a pressure imbalance is built up between the
internal and external sections of the "Screen" (2).
When the pressures difference between the internal and external sections of the "Screen"
(2) (further - DP) reaches the value preset in the control unit, a series of events are
triggered while the water continues to flow to the user. The flushing valve opens and
pressure is released from the inner side of the "Screen" (2). The "Electric Motor" (6)
simultaneously rotates the "Brushes assembly" (3) around its axis. The "Brush units" (4)
wipe all the dirt accumulated on the inner side of the "Screen" (2) and efficiently clean its
entire surface. The dirt removed them the "Screen" (2) is washed out of the filter to the
drain through the "Flushing outlet" (5).
The flushing cycle takes about 10 seconds. At the end of the flushing cycle, the flushing
valve closes and the operation of the "Electric Motor" (6) is stopped. The filter is now
ready for the next flushing cycle, with clean and filtered water flowing through the “Outlet”
(1).
Figure 1: Filter Assembly

Page 6 of 22
5960 Marion Dr. Denver, CO 80216 USA, Tel. +1 720 201 5637;
mkraft@profloinc.com; www.profloinc.com
FILTRATION SYSTEMS
4TECHNICAL DATA
Standard Characteristics:
Inlet/outlet on an axis of 90°.
Filter housing material of construction: C.S. (Carbon steel).
The filters are electrostatically coated with polyester or epoxy powder at a thickness of
150-200 µm (micron) and oven cured.
Filters are supplied with a stainless steel screen, available in varying size as needed:
200-4000 µm (micron).
Maximum recommended working pressure: up to 10 bar (150 psi).
Minimum operating working pressure during flushing: 1 bar (15 psi).
Maximum water temperature: 65⁰C (150⁰F).
Clean screen pressure loss: up to 0.1 bar (1.5 psi).
Water consumption during flushing (at minimum working pressure): 70 liters (19
gallons).
Filtration grade conversion table
µm
200
300
400
500
800
1000
1500
2000
Mesh
80
55
40
30
20
15
10
8

Page 7 of 22
5960 Marion Dr. Denver, CO 80216 USA, Tel. +1 720 201 5637;
mkraft@profloinc.com; www.profloinc.com
FILTRATION SYSTEMS
5INITIAL INSTALLATION & OPERATION
General
The filter assembly is protectively packed with all parts assembled.
Installation
1. Remove the filter assembly from the wooden pallet.
2. Connect the filter assembly to the inlet and outlet lines.
3. Connect drain line to the outlet of the flushing valves; the line should not constrain the
flushing water flow. As a result the drain line diameter should be at least the diameter
of the flushing valve and not longer than 5 m (17 feet). Verify that water runs freely
out of the drain pipe.
4. Check that all connections are properly secured.
5. Check that all nuts and bolts on the filter periphery are properly tightened and
secured.
6. Set up the control unit according to its operation manual.
Figure 2: Initial Filter Installation

Page 8 of 22
5960 Marion Dr. Denver, CO 80216 USA, Tel. +1 720 201 5637;
mkraft@profloinc.com; www.profloinc.com
FILTRATION SYSTEMS
Initial Operation
1. Gradually open the inlet valve (make sure that the outlet valve, if installed, is open).
WARNING
Take precaution while operating the filter as the filter may enter a flushing mode
automatically, without prior warning.
2. Check the filter assembly and its connections for leaks.
3. Perform a flushing cycle manually according to the operation manual of the control
unit.
4. Verify that the motor starts spinning clockwise (if the motor spins to the opposite
side, change the connections of the electric phases) and stops after a period of time
which is preset in the electronic control unit.
5. Verify that the flushing valve closes at the end of the flushing cycle. The length of the
flushing time period is preset in the electronic control unit.
6. When the filter is clean, verify that the differential pressure between inlet and outlet
does not exceed 0.1 bar (1.5 psi).
7. Set the desired value of differential pressure in the control unit.

Page 9 of 22
5960 Marion Dr. Denver, CO 80216 USA, Tel. +1 720 201 5637;
mkraft@profloinc.com; www.profloinc.com
FILTRATION SYSTEMS
6MAINTENANCE & PERIODIC CHECKS
ELECTRIC MOTOR REMOVAL & INSTALLATION
1. Close the inlet and the outlet line valves.
2. Make sure that the filter is drained and electric power is disconnected prior to service.
3. A qualified technician must carry out the electrical connections.
4. Disconnect the electric motor from the electrical power source. Prior to removal, mark
the electrical wiring connections (according to colors) on the new motor.
5. Unscrew the fasteners (1). Remove the motor cover (2).
6. Unscrew the fasteners (7). Remove the electric motor (3) from the motor adapter.
7. Verify that the shaft splint (4) remains in the groove in the motor shaft (5).
8. Carefully slide the new electric motor (3) onto the motor shaft (5). Verify that the shaft
splint (4) fits into a slot in the motor bore. Install the fasteners (7).
9. Position the motor cover (2). Install the fasteners (1).
10. Connect the electric motor to the electrical power source according to the marking
previously made in step 4.
11. Turn the control unit on.
12. Open the inlet and the outlet line valves.
WARNING
Take precautions while operating the filter because the filter might enter a flushing mode
automatically, without prior warning.
13. Perform a flushing cycle manually according to the operation manual of the control
unit.
14. Verify that the motor is spinning clockwise and the hydraulic flushing valve closes at
the end of the flushing cycle.
15. Check for leaks.

Page 10 of 22
5960 Marion Dr. Denver, CO 80216 USA, Tel. +1 720 201 5637;
mkraft@profloinc.com; www.profloinc.com
FILTRATION SYSTEMS
Figure 3: Electric Motor Removal & Installation

Page 11 of 22
5960 Marion Dr. Denver, CO 80216 USA, Tel. +1 720 201 5637;
mkraft@profloinc.com; www.profloinc.com
FILTRATION SYSTEMS
SHAFT SEALING INSTALLATION
1. Close the inlet and the outlet line valves.
2. Make sure that the filter is drained and electric power is disconnected prior to service.
3. A qualified technician must carry out the electrical connections.
4. Disconnect the electric motor from the electrical power source. Prior to removal,
mark the electrical wiring connections (according to colors) on the new motor.
5. Unscrew the fasteners (1). Remove the motor cover (2).
6. Unscrew the fasteners (8). Remove the electric motor (3) from the motor adaptor (7).
7. Verify that the shaft splint (4) remains in the groove in the motor shaft (5).
8. Unscrew the fasteners (9) holding the motor adaptor (7). Remove the motor adaptor
(7).
9. Unscrew the fasteners (6). Remove the motor shaft (5).
10. Unscrew the fasteners (12). Remove the filter cover (15).
11. Remove the seal (13).
12. Unscrew the seal tightening nut (10).
13. Remove the spinning shaft (14).
14. Remove the special rope seal (11) from the rope seal housing (17) using any narrow
tool. Be careful not to damage the rope seal housing (17).
15. Install the spinning shaft (14) in the sealing rope housing (17) with the grooved part
towards the inside of the filter.
16. Install 3 new rings of special rope seal (11) on the spinning shaft (14); push them down
the shaft towards the inside of the sealing rope housing (17) using any narrow tool.
17. Install the seal tightening nut (10) on the spinning shaft (14), do not tighten it yet.
18. Install the seal (13) into the groove in the filter cover (15) with straight side towards
the filter cover.
19. Position the filter cover (15) on the filter body (16). Verify that the seal (13) is in
groove in the filter cover (15) with straight side towards the filter cover (3). Verify that
pin on the top of the brushes assembly engages the groove on the spinning shaft (14).
Install the fasteners (12).
20. Install the motor shaft (5) on the spinning shaft (14). Install the fasteners (6).
21. Install the motor adaptor (7). Install the fasteners (9).
22. Carefully slide the electric motor (3) onto the motor shaft (5). Verify that the shaft
splint (4) fits into a slot in the motor bore. Install the fasteners (8).

Page 12 of 22
5960 Marion Dr. Denver, CO 80216 USA, Tel. +1 720 201 5637;
mkraft@profloinc.com; www.profloinc.com
FILTRATION SYSTEMS
23. Position the motor cover (2). Install the fasteners (1).
24. Connect the electric motor to the electrical power source according to the marking
previously made in step 4.
25. Slightly tighten the seal tightening nut (10) –see step 30.
26. Turn the control unit on.
27. Open the inlet and the outlet line valves.
WARNING
Take precautions while operating the filter because the filter might enter a flushing mode
automatically, without prior warning.
28. Perform a flushing cycle manually according to the operation manual of the control
unit.
29. Verify that the motor is spinning clockwise, brush units touch the screen and the
hydraulic flushing valve closes at the end of the flushing cycle.
30. Check for leaks. If there is a leak from the seal tightening nut, tighten it a bit more.
Figure 4: Shaft Sealing Removal and Installation

Page 13 of 22
5960 Marion Dr. Denver, CO 80216 USA, Tel. +1 720 201 5637;
mkraft@profloinc.com; www.profloinc.com
FILTRATION SYSTEMS
BRUSHES SHAFT AND BRUSH UNITS REMOVAL & INSTALLATION
1. Close the inlet and the outlet line valves.
2. Make sure that the filter is drained and electric power is disconnected prior to service.
3. A qualified technician must carry out the electrical connections.
4. Unscrew the fasteners (1). Remove the filter cover (2). Mind the electric cables
connected to the motor and the seal (3) in the groove in the cover.
5. Remove the seal (3).
6. Pull the brushes assembly (4) out of the filtration screen assembly.
7. If necessary, remove, replace of brush unit (8) by unscrewing the fasteners (5, 6) or
adjust the position of the brush unit by releasing the fasteners (5, 6) and using the
screw (7).
8. If necessary, install or adjust position of brush unit (8) by using the fasteners (5, 6 and
7).
9. Slide the brushes assembly (4) into the filtration screen. Verify that the end of the
brush assembly (9) fits in the screen bearing (10).
10. Install the seal (3) into the groove in the filter cover (2) with straight side towards the
filter cover.
11. Position the filter cover (2) on the filter body. Verify that the seal (3) is in groove in the
filter cover (2) with straight side towards the filter cover (2). Verify that pin on the top
of the brushes assembly (4) engages the groove on the motor shaft. Install the
fasteners (1).
12. Turn the control unit on.
13. Open the inlet and the outlet line valves.
WARNING
Take precautions while operating the filter because the filter might enter a flushing mode
automatically, without prior warning.
14. Perform a flushing cycle manually according to the operation manual of the control
unit.
15. Verify that the motor is spinning clockwise, brush units touch the screen and the
hydraulic flushing valve closes at the end of the flushing cycle.
16. Check for leaks.

Page 14 of 22
5960 Marion Dr. Denver, CO 80216 USA, Tel. +1 720 201 5637;
mkraft@profloinc.com; www.profloinc.com
FILTRATION SYSTEMS
Figure 5: Brush Assembly & Brush Units Removal & Installation

Page 15 of 22
5960 Marion Dr. Denver, CO 80216 USA, Tel. +1 720 201 5637;
mkraft@profloinc.com; www.profloinc.com
FILTRATION SYSTEMS
FILTRATION SCREEN ASSEMBLY REMOVAL & INSTALLATION
1. Close the inlet and the outlet line valves.
2. Make sure that the filter is drained and electric power is disconnected prior to service.
3. A qualified technician must carry out the electrical connections.
4. Unscrew the fasteners (1). Remove the filter cover (2). Mind the electric cables
connected to the motor and the seal (3) in the groove in the cover.
5. Remove the seal (3).
6. Pull the brush assembly (4) out of the filtration screen assembly (7).
7. Pull the filtration screen assembly (7) out of the filter body using the handles on the
top.
8. If necessary, remove and replace the seals (6) from the filtration screen assembly (7).
9. If necessary, disassemble the screen assembly (7) to sections, and replace the
defective section.
10. Install the seals (6) in the filtration screen assembly (7).
11. Lubricate the seals (6) with silicon grease.
12. Slide the filtration screen assembly (7) into the filter body.
13. Slide the brush assembly (4) into the filtration screen assembly (4). Verify that the end
of brush assembly (5) fits into the screen bearing (8).
14. Install the seal (3) into the groove in the filter cover (2) with straight side towards the
filter cover.
15. Position the filter cover (2) on the filter body. Verify that the seal (3) is in groove in the
filter cover (2) with straight side towards the filter cover (2). Verify that pin on the top
of the brushes assembly (4) engages the groove on the motor shaft. Install the
fasteners (1).
16. Turn the control unit on.
17. Open the inlet and the outlet line valves.
WARNING
Take precautions while operating the filter because the filter might enter a flushing mode
automatically, without prior warning.

Page 16 of 22
5960 Marion Dr. Denver, CO 80216 USA, Tel. +1 720 201 5637;
mkraft@profloinc.com; www.profloinc.com
FILTRATION SYSTEMS
18. Perform a flushing cycle manually according to the operation manual of the control
unit.
19. Verify that the motor is spinning clockwise, brush units touch the screen and the
hydraulic flushing valve closes at the end of the flushing cycle.
20. Check for leaks.
Figure 6: Fine screen assembly Removal & Installation

Page 17 of 22
5960 Marion Dr. Denver, CO 80216 USA, Tel. +1 720 201 5637;
mkraft@profloinc.com; www.profloinc.com
FILTRATION SYSTEMS
PERIODIC CHECKS
Perform annual Periodic Checks at the beginning of the season according to the following
instructions (refer also to safety instructions in chapter 2):
1. Check the condition of the body seal. If necessary, replace the body seal.
2. Verify that all the brush units are in contact with the filtration screen. If necessary,
adjust the position of the brush units or replace them according to "Brushes shaft and
Brush units Removal & Installation."
3. Check the condition of the filtration screen assembly. If defective, replace according to
"Filtration Screen Assembly Removal & Installation."
4. Check the filtration screen seals condition. Lubricate with silicon grease.
5. Check the condition of the bearings, replace if damaged or deformed.
6. Check existence of grease on the motor axis.
7. Check the filter housing for paint damage and corrosion. If required, clean area with
sandpaper and apply a thin layer of basic + epoxy paint.
8. Check for leaks.

Page 18 of 22
5960 Marion Dr. Denver, CO 80216 USA, Tel. +1 720 201 5637;
mkraft@profloinc.com; www.profloinc.com
FILTRATION SYSTEMS
7TROUBLESHOOTING
DP IS HIGHER THAN THE PRE-SET VALUE (FLUSHING DOES NOT START)

Page 19 of 22
5960 Marion Dr. Denver, CO 80216 USA, Tel. +1 720 201 5637;
mkraft@profloinc.com; www.profloinc.com
FILTRATION SYSTEMS
FLUSHING DOES NOT END

Page 20 of 22
5960 Marion Dr. Denver, CO 80216 USA, Tel. +1 720 201 5637;
mkraft@profloinc.com; www.profloinc.com
FILTRATION SYSTEMS
Table of contents
Popular Water Dispenser manuals by other brands

Kenmore
Kenmore ULTRASOFT 250 625.38826 owner's manual
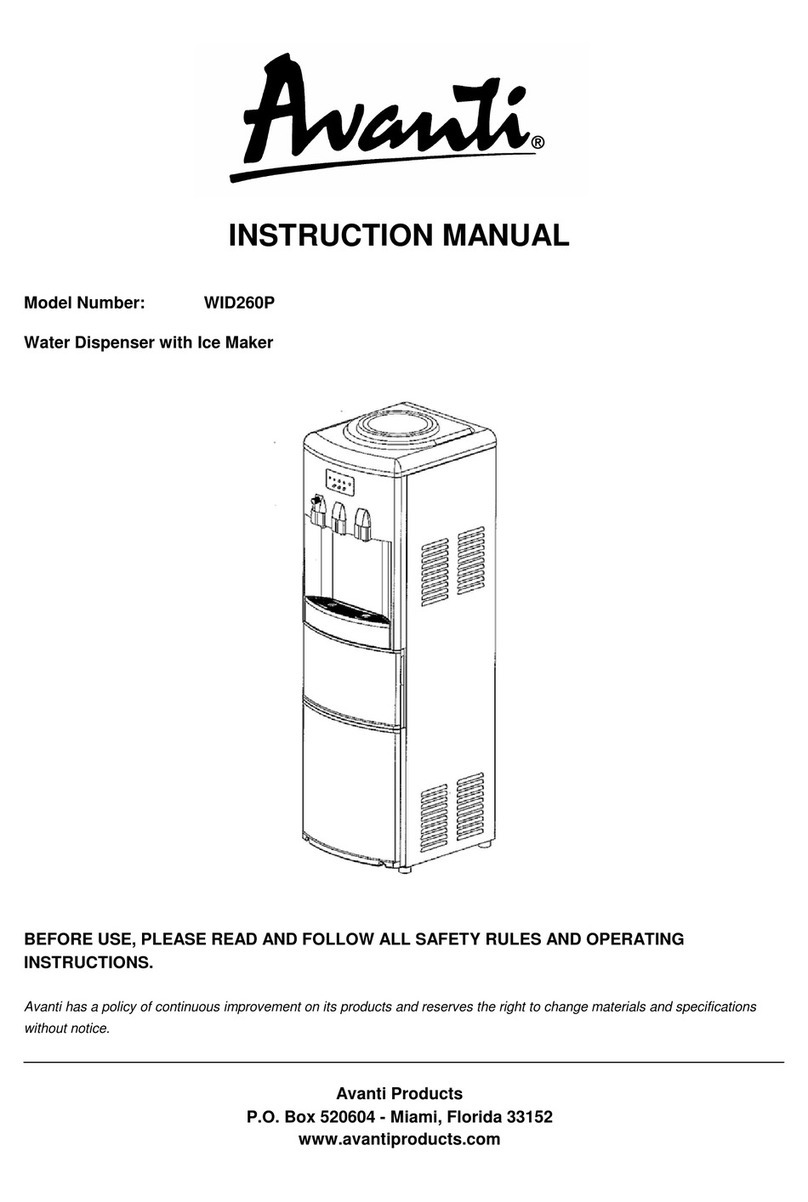
Avanti
Avanti WID260P instruction manual
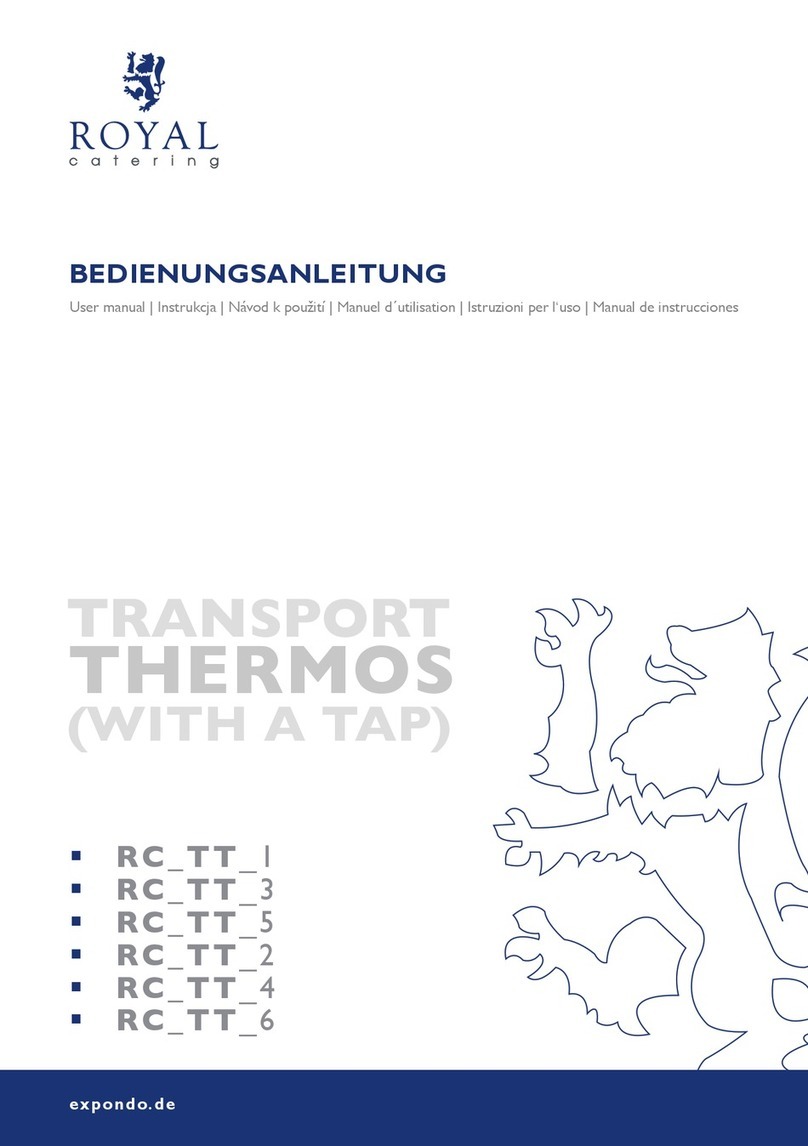
Royal Catering
Royal Catering RC TT 1 user manual

Toro
Toro Aqua-Clear ACS-218-12VDCL Important safety instructions
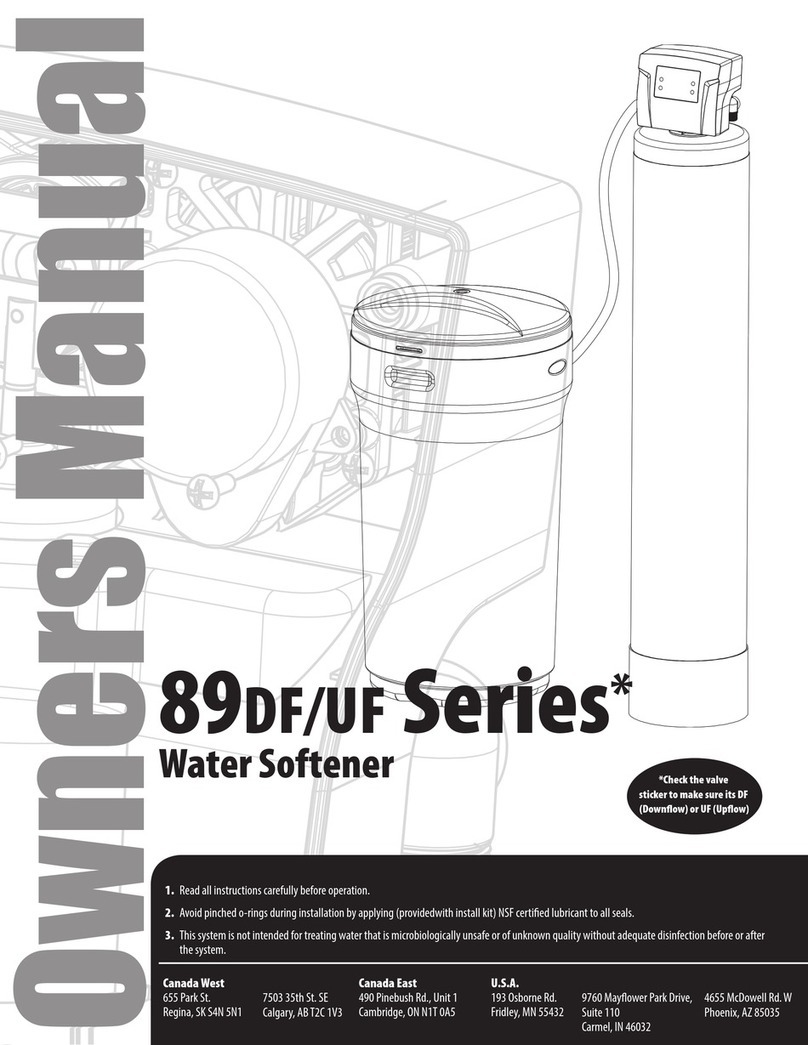
Hydrotech
Hydrotech 89DF Series owner's manual

Everpure
Everpure Water Filter and Cartridge QL2-OW200L Specification sheet

CSI
CSI Signature 2 Series Installation & operation manual

Canature WaterGroup
Canature WaterGroup 185DF Series owner's manual

Addie Water Systems
Addie Water Systems 6700 Service manual
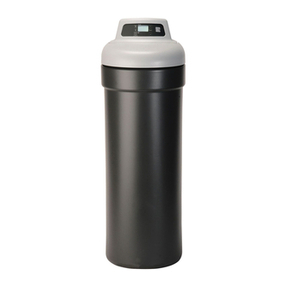
Kenmore
Kenmore IntelliSoft 350 Series owner's manual
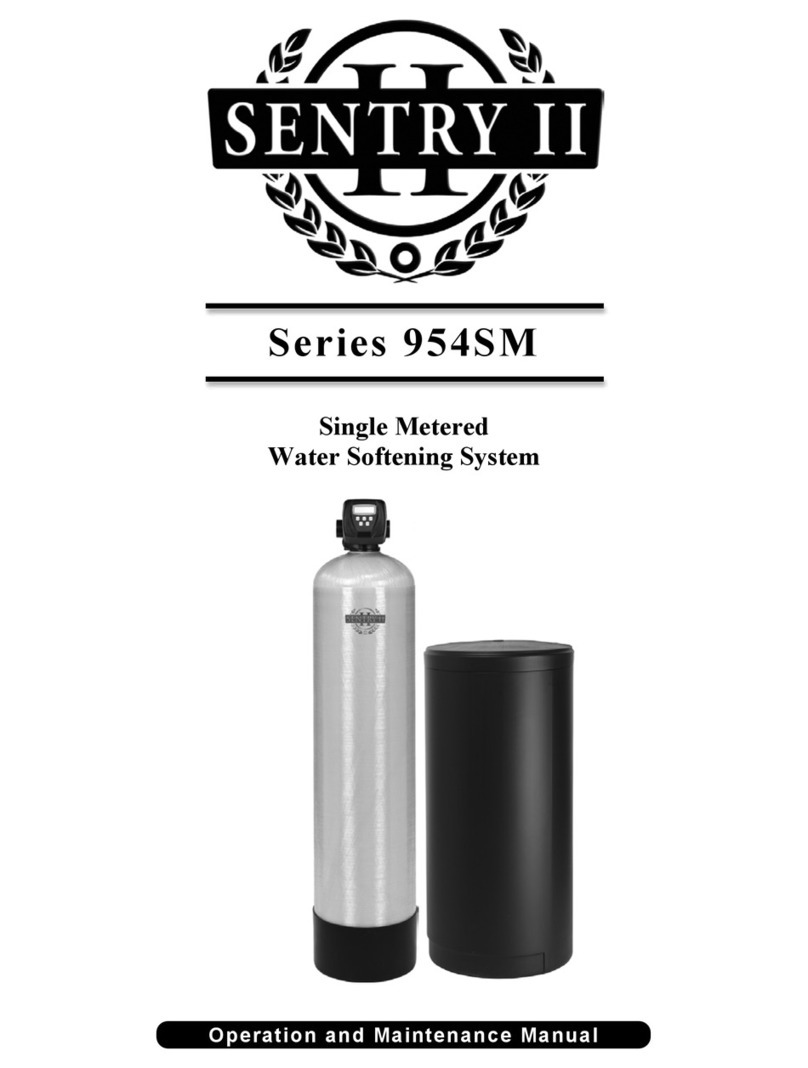
SENTRY II
SENTRY II 954SM Series Operation and maintenance manual

Halsey Taylor
Halsey Taylor HVRFR Series owner's manual