Purewords CNC3020 User manual

Small CNC User Manual
Applicable Model:CNC3020/3040/4060 model

Table of Contents
Foreword...............................................................................3
1.Equipment overview.........................................................4
1.1.Equipment packing list..............................................................4
1.2.Names and functions of various parts of the equipment...........5
1.3.Equipment technical parameters..............................................6
2.Equipment installation and commissioning.....................6
2.1.Installation precautions.............................................................6
2.2.Installation instructions......................................................7
2.3.Control software installation...............................................9
2.4.Equipment debugging instructions.......................................9
3.Equipment instructions....................................................10
3.1.Processing flow............................................................10
3.2.Introduction to common functions of Mach3...............12
3.3.Compatible programming software..............................14
4.Tool selection......................................................................14
5.Common material processing parameters......................16
6.Equipment service.............................................................17

Foreword
First of all, thank you for purchasing and using our products. Please read
this instruction before installing your machine, so as not to cause
unnecessary trouble for your installation and use.
The equipment is tested before leaving the factory and meets the
shipping standards. Before using, please read the following precautions
carefully:
1. The machine has been rigorously tested before leaving the factory to
ensure that all functions of the machine are in good condition, but the
machine must be transported by logistics. When receiving the goods,please
make sure that the outer packaging of the product is complete and
unpacking. Please check the goods afterwards. If there is any problem, please
contact the after-sales personnel in time;
2. The machine is connected with the computer by USB, the computer
used for control should be dedicated, and as far as possible, do not install
other unrelated application software;
3.Please ensure that there is a grounding function for the power supply
socket. If there is no grounding, please perform external grounding.
4. This unit uses single-phase AC 220V, 50Hz (single-phase AC110V,
50/60Hz in some areas), if not allowed, please Do not disassemble it in order
to avoid danger;
5. When processing, it is relatively large when it comes to cutting chips.
Especially when processing metal materials, please wear protective glasses to
prevent metal chips from flying out and hurt your eyes.
6. Do not approach the spindle rotating at high speed during machining.
Do not touch the workpiece being processed by hand to avoid danger.
7.If accidents are found during work, please turn off the power in time
and wait for a while before re-use. If the problem is still not solved, please
contact the after-sales personnel.

(1).CNC Engraving machine rack----1 units
(2).CNC Engraving machine control box----1 units
(3).Test machine carving knife----5 Put
(4).Fixed clamp----4 sets
(5).Spindle chuck----1PC
(6).Spindle wrench----1 pair
(7). Allen wrench----5 put
(8). power cable----1 Articles
(9).USB cable----1 Articals
(10).Tool set----1 PC
(11).U disk ----1PC
(12).The axis of rotation----1 PC
(13).The fuse----2PC
(14).Operation manual ----1 PC
(15).software CD----1 PC
(16).Engraving machine spindle cooling pump----1 units(4060 model)
The above items are the packing list when the machine is shipped as
standard. The specific goods are subject to the purchase.
If there is any missing item, please contact customer service.
1.Engraving overview
1.1.Equipment packing list
1
2
3
4
5
678910
11
12
13
14
15
16

1.2.Names and functions of various parts of the equipment
Electric control box
switch description
3020/3040 model
Label
Button name
Key Function
1
switch
Control the power supply of the electric
control box
2
Spindle start switch
3
Spindle speed
control knob
Adjust the spindle switch and spindle speed
4
Emergency stop
button
Pressing the machine in an emergency will
stop immediately
4060 model
Control spindle start and stop
Label
name
Key Function
1
Spindle panel
Display spindle status
2
Water pump
switch
Control the start and stop of the spindle
cooling water pump
3
Spindle start
switch
4
switch
Control the power of the control box
5
Emergency stop
switch
Pressing the machine in an emergency
will stop immediately
Control spindle start and stop

1.3.Equipment technical parameters
SKU
E-3020E-3020A
E-3040E-3040A
E-4060E-4060A
Chinese name
3020 3 axis / 4 axis
3020 3 axis / 4 axis
6040 3 axis / 4 axis
Effective work
schedule
200(X)x300(Y)x55(Z)mm
300(X)x400(Y)x55(Z)mm
395(X)x600(Y)x70(Z)mm
Effective work
schedule
500*390*390(H)mm
610*450*390(H)mm
840*640*460(H)mm
Maximum
thickness
ofmaterial
≤65mm
≤65mm
≤100mm
Maximum
workpiece size
240mm * 425mm
320mm * 525mm
750mm * 480mm
working desk size
240mm * 425mm * 15mm
320mm * 525mm * 15mm
750mm * 480mm * 15mm
Frame material
6061 aluminum alloy +
6063aluminum alloy
6061 aluminum alloy + 6063aluminum
alloy
6061 aluminum alloy +
6063aluminum alloy
Drive unit (X/Y/Z)
1202 Trapezoidal screw
1202 Trapezoidal screw
New 1605 ball screw
Sliding unit X
axis
16mm Chrome plated hard shaft
16mm Chrome plated hard shaft
16mm Chrome plated hard shaft
Slide unit Y axis
16mm Chrome plated hard shaft
16mm Chrome plated hard shaft
20mm Aluminum support opticalaxis
slide
Sliding unit Z
axis
12mm Chrome plated hard shaft
12mm Chrome plated hard shaft
13mm Chrome plated hard shaft
Stepper motor
type
57 2-phase stepper motor -2A
57 2-phase stepper motor -2A
57 2-phase stepper motor -3A
Spindle motor
300W DC
300w DC
800w New water cooled spindle
Spindle speed
0~8000rpm/ min(Stepless
speedregulation )
0~8000rpm / min(Stepless
speedregulation )
0~24000rpm/min
( Frequencyconverter speed
regulation )
Airspeed
0-1000mm / min
0-1000mm / min
0-2500mm / min
Engraving speed
0-1000mm / min
( Differentmaterials )
0-1000mm / min( Differentmaterials )
0-2000mm / min
( Differentmaterials )
Repeatability
≤0.05mm
≤0.05mm
≤0.03mm
Machine weight
21.5KG/23.5KG
25.5KG/27.5KG
51KG/59KG
2.Equipment installation and commissioning
2.1.Installation precautions
(1).This machine uses a USB port to connect to the computer. When installing, you
need to connect the USB cable to the computer.
(2).The computer used for control should be dedicated. Do not install other unrelated
application software and anti-virus software as much as possible. Also, do not connect
to the network. Viruses and other application software may affect the operation of the
machine.
(3).The machine adopts single-phase A C 220V, 50Hz power supply (single-phase A C
110V, 5 0 / 60 0 z z in some areas), please ensure the correct and stable supply voltage;
(4).Since the machine has a frequency converter, the inverter will generate a lot of static
electricity during operation. Please ensure that the grounding function of the power
supply socket of the equipment is normal. If it is not grounded, it will affect the life and
normal operation of the machine.

(5).Please be sure to follow the steps of the engraving machine installation instructions
during installation. The installation may cause the machine to malfunction due to
incorrect installation by the user.
(6).If there is an y problem with the operation of the machine during the machine
debugging process, please contact the after-sales personnel for disposal. Do not
disassemble it without permission, so as to avoid danger;
(7).Do not plug or unplug the terminal at any time while powering on. At the same
time, please note that the interval between the power on and off of the device should be
above 15S. If you do not pay attention to the above problems, it may cause damage to
the control circuit.
2.2.Installation instructions
The machine can be installed by following the instructions below.
Step 1: Install the motor, and install the stepping motors of the three axes to the
corresponding shafts. The locking screws on the couplings are tightened with the
Allen key.

Step 2: Align the wire plug on the motor with the corresponding plug on the machine.
Step 3: Connect the engraving machine frame, electric control box and computer wiring
(refer to the wiring diagram for connection). The aerial plug-in cable is connected
between the rack and the electric control box. The connection will be affixed with
X, Y, Z, A (purchasing A-axis), spindle, spindle cooling water pump (4060 model)
corresponding to the aviation plug and The interfaces with the same identification
after the electric control box are connected one by one. Connect the USB cable
between the electric control box and the computer. Be sure to connect the wiring.
Otherwise, the computer will not be able to control the machine. Finally, connect the
power cable.
3020/3040 model wiring diagram
Label name
Port description
X
X-axis motor
Y
Y-axis motor
Z
Z-axis motor
A
A-axis motor
SPINDLE
Spindle motor
TOOL
Tool set
USB
Connect the data cable to the
computer
4060 model wiring diagram
Label name
Port description
X
X-axis motor
Y
Y-axis motor
Z
Z-axis motor
A
A-axis motor
TOOL
Tool set
PUMP
Spindle motor cooling water pump
VFD
Frequency conversion spindle
USB
Connect the data cable to the
computer

2.3.Control software installation
Software installation computer requirements:
1. desktop computer or laptop;
2. USB port;
3. computer system:WindowsXP/Win7/win8/win10 system;
Our company provides Mach 3 software for testing and testing. It is
only for teaching and personal research. If there is any commercial use,
please buy genuine, thank you! Mach 3 official website:
www.machsupport.com
Basic installation of Mach3 software: Please open the supplied USB flash
drive and find the installation folder.
Please confirm that the USB cable is connected before the software is
installed. Software installation steps: Double click .
Open into the installation interface, and then press the Enter key "Enter",
"Next" or "YES" until The "Finish" installation is complete:
> > Next > Yes > Next > Next > Next > Next > Determine > Finish
> Determine > Next > Yes > Next > Next > Next > Next >Yes > Finish.
2.4.Equipment debugging instructions
Step 1: Double-click to
enter the software and wait for
the software software interface
to load. The first time you start
the software, the computer
will pop up the following dialog
box, please select "BSMotion-
V2.0", "Don't ask me this again"
, "OK"

Step 2: Power on the control box and switch the power switch to ON. At
this time, the emergency reset button “Reset” in the lower left corner
of the computer control interface is flashing. Click the
“Reset” button to cancel the alarm state.
Step 3: After confirming that the emergency reset in the lower left corner
is not flashing, use the arrow keys on the keyboard and Pageup/down to
control the left and right, front and rear, and up and down movements of
the machine to confirm that the machine movement function is normal.
Step 4: Then click on the spindle speed bar in the lower
right corner of the Mach3 software. At this time, the spindle will rotate,
indicating that the spindle speed control function is normal (make
sure the spindle nut is tightened before turning on the speed).
After the above simple debugging, the machine functions are normal.
If you encounter problems, you can consult the after-sales solution.

3.Equipment instructions
3.1.Processing flow
Step 1: the material to be processed is fixed on the machine with the
corresponding fixture. Generally, the thin plate is fixed by double-sided
glue, the rectangle is fixed by a vise, and the shaped workpiece is fixed by
a special fixture.
Step 2: Clamp the tool onto the spindle motor. When clamping the tool, it
is necessary to pay attention to the specifications of the clamping tool. It
must be the same as the programming time. The tool should be locked
with the spindle wrench. After the tool is clamped, it must be checked
whether the tool will be yawed. Otherwise, the quality of the processed
product will be poor. Broken knives, etc. during processing.
Step 3: Open the control software Mach3 on the computer, turn on the
machine power switch, and release the alarm state.
Step 4: manual tool setting operation, press the keyboard “Tab” on the
computer operation interface to call up the “MPG” interface, click the
corresponding button to control the forward/reverse movement of the
machine in the current axis. by To
control the speed of the movement, move the center of the tool nose to
the machining coordinate origin set during programming (for the
convenience of tool setting, the programming is usually set at the four
corners or the center of the material). For example, when programming,
the origin is set in the lower left corner of the material, then we will align
the center of the tool tip with the bottom left corner of the material with
the hand wheel (the spindle speed should be adjusted to about 30% when
the tool is set to prevent the tool from breaking. Knife).

Step 5: Confirm that the “Emergency Reset” in the lower left corner
of the software is not flashing. Click “Zero X”, “Zero Y”, “Zero Z”,
“Zero A”, click “Load G Code”, then there will be loading. G code
pop-up window, file type select "AllFiles" and find the G code you
generated is loaded. After the loading is completed, the corresponding
simulation path will be displayed in the upper right corner of the software
(if there is no simulation path generation, the loaded G code is wrong
or Can't identify it).
Step 6: After the program is read in, adjust the spindle speed to
80%~100% (the spindle speed is set according to the processing
material), then click “Start” to process the machine. If it needs
to be adjusted during the machining process. The speed of the
machining can be controlled by pulling the column bar of the
feed bar.
The above is a simple operation method. For details on the control
software, please refer to “Using Mach3Mill”.
3.2.Introduction to common functions of Mach3

Button name
Button icon
Key Function
Emergency reset
Whenalarming,clickthisbutton to
cancel thealarm.
Load G code
Click this button to import the G
code file.
The program starts
running
After importing the G code
file,Click this button to start running
the program.
Return to program
beginning
Clickthisbuttontoreturntothe
beginningoftheprogramand re-run.
Turn off G code
Close G code file
XYZA coordinate
clear
Afterusingthecorrectorigin
beforemachining,weneedto
clickXYZAtoclearinmach3,
thatis,settheworkpiecezero
coordinate;
Return to origin
Clickthisbuttontoreturntothe
origincoordinates.
Processing feed
speed adjustment
If you need to adjust the processing
speed during
machining,youcanclickthis
columntoadjustthemachining
feedspeed.
Display mode
Flat 2D mode and stereo 3D mode
display Show the processing path,
click this button to switch the
display status
Offline function
Ifyouneedtocheckthestarting point or
running status of the program, you
can click this button to perform
offline simulation. After
offlinelighting, reconnect the
machine and
remembertoswitchback.Otherwise,
the computer cannot control the
machine.
Jog on/off
Similar to a child lock function,
when you click this button, the
computer keyboard will not be able
to control the machine, and the
program can still run online.

3.3.Compatible programming software
Mach3 is a PC software that recognizes international G code and is currently
compatible with most software that generates G code on the market. Since
the user's purchase of the machine is not the same, here are some
recommended G code generation software for common use.
For two-dimensional processing applications such as engraving, milling,
drilling, and cutting, it is recommended to use Wentai, ArtCAM, Beijing
Jinghua software, Type3 and other software, they are compatible with DXF
format files.
PCB board engraving is recommended to use CopperCAM software and is
compatible with Gerber files.
Engraving relief is recommended to use ArtCAM and Beijing
carving software, ArtCAM is suitable for novice learning, Beijing
carving The software is more professional.
UG, MasterCAM, and Powermill are recommended for processing such
as molds, fixtures, and parts. Four-axis stereo processing is recommended
to use Powermill and Beijing Engraving software to make getting started
easie
4. Tool selection
Commonly used tool classification for engraving machines: milling cutters,
engraving knives, drill bits, chamfering knives, ball knives, etc. The tool
usually consists of a shank and a blade. The shank is the part that is clamped
and has no cutting ability. The blade is the part with cutting ability.

List of commonly used tool types
Tool type
Tool name
Tool picture
Tool function
usual format
Milling
cutter
Corn milling
cutter
Mainly used for milling
grooves of non-metallic
materials such as high
temperature resistant plastics
and wood.
Common specifications for tool holders:
3.175 and 4mmCommon specifications
of the blade: 0.6-3.175mm
Single-edged
milling cutter
For the cutting of plastic,
copper, aluminum alloy and
other materials, milling
Common specifications of the
toolholder: 3.175 bladecommon
specifications: 1,2, 3mm
Three-blade
milling cutter
Processing aluminum alloy,
copper and other materials,
milling and milling, can also
be used for processing non-
metal bakelite, plastics,etc.
Common specifications of the
shank:3.175 and 6mm blades commonly
used
Specifications:1,1.5,2,2.5,3,3.5,4,5,6m
m
Carving
knife
Flat bottom
taper carving
knife
Generally used for engraving
PCB board engraving, metal
lettering, embossing process
processing and so on.
Common specifications of the tool
holder: 3.175, 4, 6mm
bladeCommonspecifications: 20°0.1,
0.2, 0.3,30°0.1,0.2, 0.3, 0.4
Drill class
High
speedPCBdrill
head
Suitable for PCB board
drilling, or plastic and other
holes,larger specifications,
can also drill aluminum
alloy materials
Common specifications of the shank:
3.175mm blade commonly used
Specifications: 0.3-3, 4, 5, 6mm
Ball knife
Ball knife
Used for the processing of
some curved spherical
surfaces such as plastic, wood
and metal.
Grinding
head
Jade grinding
head
For the grinding of jade
materials
Tool holder common specifications:
3.175mm

5. Common material processing parameters
Material
name
Processing parameters
Eat the amount of
knife (mm)
Lower knife speed
(mm/min)
Cutting speed
(mm/min)
Spindle speed (r/min)
wood
2
500
1000
20000
Acrylic
1
500
800
16000
PVC
1
500
800
18000
PC
1
500
800
18000
ABS
0.5
500
800
18000
nylon
0.5
500
1000
20000
Double
1
500
1000
20000
Bakelite
1
500
1000
20000
Fiberglass
panels
1
500
1000
20000
Mammoth
0.5
300
800
20000
Beeswax
0.5
300
800
20000
Bone/corner
0.5
300
800
20000
copper
0.25
400
800
20000
aluminum
0.25
400
1000
20000
silver
0.3
400
1000
20000
Zinc
0.2
400
800
20000
magnesium
0.2
400
800
20000
walnut
1
400
800
20000
Ivory fruit
1
400
800
20000
Bodhi
1
400
800
20000
synthetic rock
1
200
300
20000
Seal stone
1
200
300
20000
cobblestone
0.1
200
300
20000
jade
0.1
150
300
20000
Carbon fiber
board
0.3
400
800
20000
The above data is a conservative parameter set by a 3.175mm milling cutter. For reference
only, please adjust according to the actual situation.

6. Equipment service
(1) screw cleaning and lubrication
When the machine is in use, it is a good habit. It is necessary to do a cleaning
work for about one month. The screw, optical axis and bearing cleaning must
work. You can use a clean rag to manually wipe the optical axis of the screw.
The part of the bearing that is not cleaned can be cleaned with a small brush.
After cleaning, the oil can be sprayed with oil to the screw, the optical axis and
the bearing, and then the machine can be moved back and forth for a few times,
such as above the screw. There is also dirt, re-clean with a rag, repeat the
lubrication and clean the action until the screw is shiny and oily.
(2) spindle cleaning and maintenance
During the machining process, the spindle chuck, nut and screw parts are easy to
enter dust and rust. At this time, it is necessary to apply anti-rust oil to the spindle
clamping part to clean the rust of the screw; the chuck and nut are severely rusted.
Replace the collet and nut to ensure that the machine is concentric.
(3) electric control box cleaning
When the controller is used with the machine, sometimes it will enter a lot of dust.
When processing metal materials, it is necessary to clean the dust inside the control
box to prevent conduction and burn out the circuit. We can open the cover of the
controller, use a hair dryer, open the cold air stall, turn the control box upside down,
clean the dust on the circuit board, and clean it, clean it with a small brush.
(4) common consumables replacement
Shaft nuts, chucks, knives, stepper motor couplings, lubricants,
etc., please contact
Supplies Name
Consumables Picture
Supplies Features
Spindle nut
On the clamping spindle, use
the locking tool with the tool
chuck
Tool chuck
On the clamping spindle, use
the locking tool with the tool
nut
Tool
Engraving tools such as
engraving knives, milling
cutters, drill bits, etc.
This manual suits for next models
5
Table of contents
Popular Control System manuals by other brands
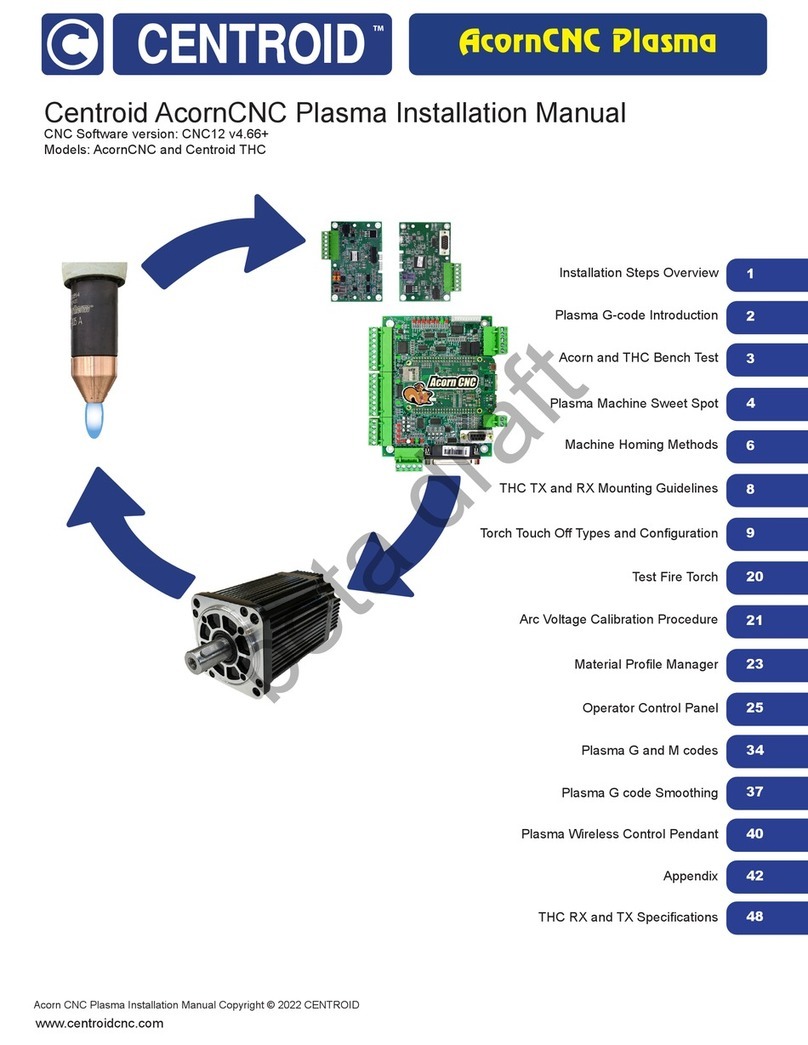
Centroid
Centroid Acorn CNC installation manual
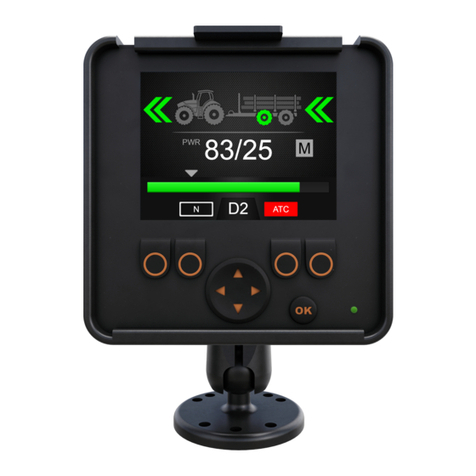
Black Bruin
Black Bruin CTR101 Operation manual
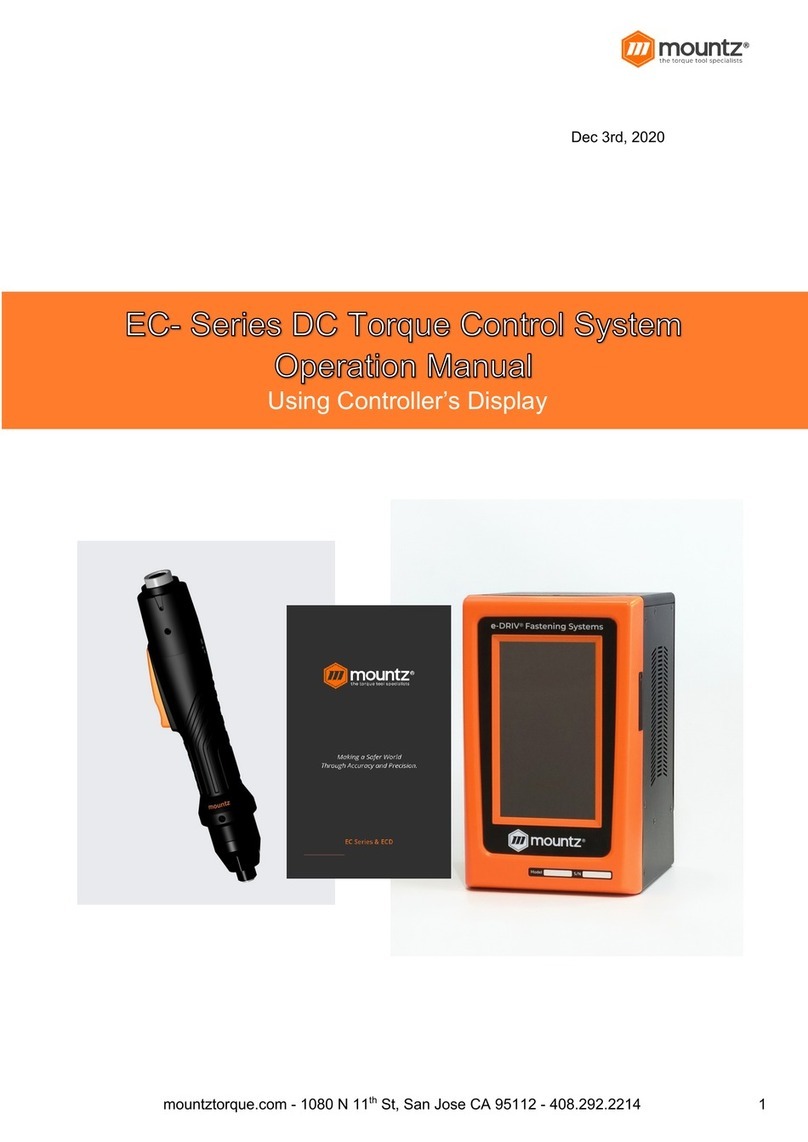
Mountz
Mountz EC Series Operation manual
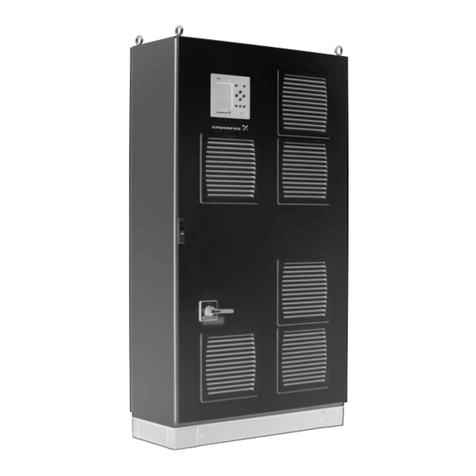
Grundfos
Grundfos Control MPC 2000 Series Installation and operating instructions
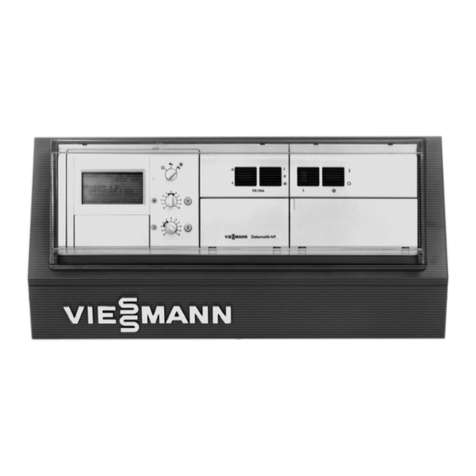
Viessmann
Viessmann Dekamatik-M1 operating instructions
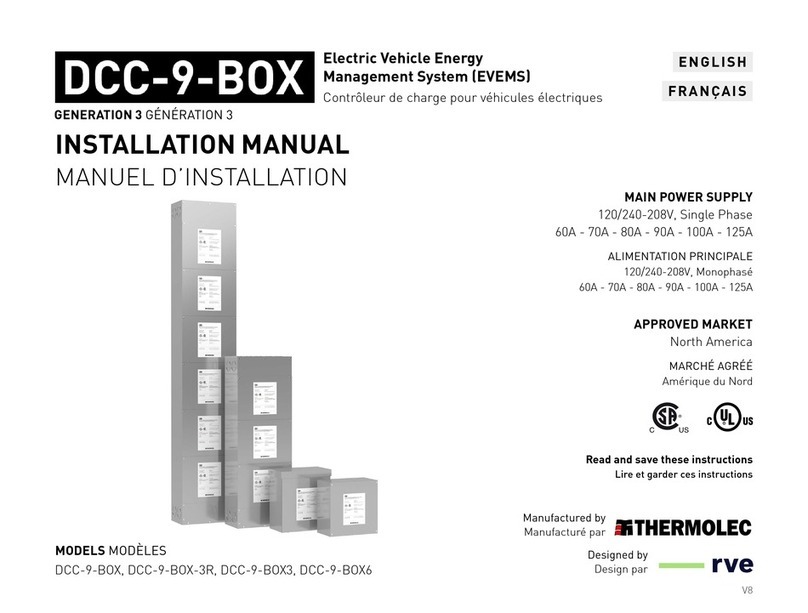
Thermolec
Thermolec RVE DCC-9-BOX3 installation manual