GE Multilin MM200 Use and care manual

*1601-9033-A5*
GE
Grid Solutions
MM200 Motor Management
System
Communications Guide
MM200 Revision: 1.2x
Manual P/N: 1601-9033-A5
Manual Order Code: GEK-113402D
LISTED
52TL
IND.CONT. EQ.
E83849

© 2016 GE Multilin Incorporated. All rights reserved.
GE Multilin MM200 Motor Management System Communications Guide for revision 1.2x.
MM200 Motor Management System, EnerVista, EnerVista Launchpad, and EnerVista
MM200 Setup are registered trademarks of GE Multilin Inc.
Allen-Bradley, RSLinx DeviceNet-3, RSNetWorx for DeviceNet, EDS Wizard, Allen-Bradley
1770-KFD Driver, and 1747-SDN Scanner Module, are registered trademarks of Rockwell
Automation, Inc.
The contents of this manual are the property of GE Multilin Inc. This documentation is
furnished on license and may not be reproduced in whole or in part without the permission
of GE Multilin. The content of this manual is for informational use only and is subject to
change without notice.
Part number: 1601-9033-A5 (February 2016)

MM200 MOTOR MANAGEMENT SYSTEM – COMMUNICATIONS GUIDE
Safety Words and Definitions
The following symbols used in this document indicate the following conditions:
Indicates a hazardous situation which, if not avoided, will result in death or serious
injury.
Indicates a hazardous situation which, if not avoided, could result in death or serious
injury.
Indicates a hazardous situation which, if not avoided, could result in minor or
moderate injury.
NOTE
Indicates significant issues and practices that are not related to personal injury.
For further assistance
For product support, contact the information and call center as follows:
GE Grid Solutions
650 Markland Street
Markham, Ontario
Canada L6C 0M1
Worldwide telephone: +1 905 927 7070
Europe/Middle East/Africa telephone: +34 94 485 88 54
North America toll-free: 1 800 547 8629
Fax: +1 905 927 5098
Website: http://www.gegridsolutions.com/multilin

MM200 MOTOR MANAGEMENT SYSTEM – COMMUNICATIONS GUIDE

MM200 MOTOR MANAGEMENT SYSTEM – COMMUNICATIONS GUIDE I
Table of Contents
1.COMMUNICATION
S INTERFACES
2.RS485 INTERFACE
(MODBUS RTU)
Modbus Protocol .................................................................................................................................2-1
Electrical Interface ...................................................................................................................................... 2-1
Data Frame Format and Data Rate.................................................................................................... 2-2
Data Packet Format................................................................................................................................... 2-2
Error Checking .............................................................................................................................................. 2-2
CRC-16 Algorithm........................................................................................................................................ 2-3
Timing ............................................................................................................................................................... 2-3
MM200 supported functions.................................................................................................................. 2-4
Modbus Functions ..............................................................................................................................2-4
Function Code 03H..................................................................................................................................... 2-4
Function Code 04H..................................................................................................................................... 2-5
Function Code 05H..................................................................................................................................... 2-5
Function Code 06H..................................................................................................................................... 2-6
Function Code 07H..................................................................................................................................... 2-7
Function Code 08H..................................................................................................................................... 2-8
Function Code 10H..................................................................................................................................... 2-8
Error Responses ........................................................................................................................................... 2-9
Modbus memory map ...................................................................................................................2-10
Format codes.....................................................................................................................................2-19
Performing Commands Using Function Code 10H..........................................................2-25
Using the User Definable Memory Map..........................................................................................2-26
3.FIELDBUS
INTERFACE
Profibus DP.............................................................................................................................................3-1
Profibus power supply configuration................................................................................................. 3-2
Profibus termination .................................................................................................................................. 3-3
Profibus DP-parameterization............................................................................................................... 3-3
Profibus DP-configuration....................................................................................................................... 3-4
Profibus Input Data .................................................................................................................................... 3-6
Profibus Output Data................................................................................................................................. 3-7
Profibus DPV0-Diagnostics ..................................................................................................................... 3-7
Profibus DPV1 ....................................................................................................................................3-16
Profibus DPV1-Acyclic read/write data...........................................................................................3-16
Extended Profibus DPV1 functionality.............................................................................................3-17
Acyclic Read Operation (Modbus functions 03H and 04H) ...................................................3-17
Profibus DPV1-Diagnostics ...................................................................................................................3-18
DeviceNet protocol..........................................................................................................................3-26
DeviceNet power supply configuration ..........................................................................................3-27
DeviceNet setup and configuration (typical) ................................................................................3-28
DeviceNet setup and configuration (ADR) .....................................................................................3-43
DeviceNet Communications ................................................................................................................3-46
Poll data.........................................................................................................................................................3-46
Identity Object (Class Code 01H) ........................................................................................................3-47
Message Router (Class Code 02H).....................................................................................................3-47
DeviceNet Object (Class Code 03H) ..................................................................................................3-48
DeviceNet Connection Object (Class Code 05H).........................................................................3-48
DeviceNet Motor Data - Explicit Object (Class Code A0H)......................................................3-49
DeviceNet Motor Data - Explicit Object (Class Code A1H)......................................................3-51

II MM200 MOTOR MANAGEMENT SYSTEM – COMMUNICATIONS GUIDE
DeviceNet Motor Analog Data - Explicit Object (Class Code A2H) .....................................3-53
DeviceNet - Explicit Motor Analog Data Object, Class Code B0H, Services...................3-55
DeviceNet - Explicit Motor Object, Class Code B1H ..................................................................3-57
A.APPENDIX Change notes .......................................................................................................................................A-1
Revision history............................................................................................................................................ A-1
Warranty.................................................................................................................................................A-2

MM200 MOTOR MANAGEMENT SYSTEM – COMMUNICATIONS GUIDE 1-1
MM200 Motor Management System
Chapter 1: Communications
interfaces
GE
Grid Solutions
Communications interfaces
The MM200 has two communications interfaces:
• RS485
•Fieldbus
NOTE
NOTE: Setpoint changes related to RS485, DeviceNet, and Profibus, require a power cycle to be
activated.
NOTE
NOTE: External power must be present on the Fieldbus port at power-up, in order to correctly
initialize.
NOTE
NOTE: For full details, please refer to the MM200 Communications Guide, to be found on the GE
Multilin web site.

1-2 MM200 MOTOR MANAGEMENT SYSTEM – COMMUNICATIONS GUIDE
CHAPTER 1: COMMUNICATIONS INTERFACES

MM200 MOTOR MANAGEMENT SYSTEM – COMMUNICATIONS GUIDE 2-1
MM200 Motor Management System
Chapter 2: RS485 interface (Modbus
RTU)
GE
Grid Solutions
RS485 inter face (Modbus RTU)
The RS485 interface is a serial two-wire port intended for use as a Modbus RTU slave. The
RS485 port has the following characteristics.
•Address:1to254
• Baud rate: 9600 to 115200 bps
• Supported Modbus function codes: 3, 4, 5, 6, 7, 8, 16
Modbus Protocol
The MM200 implements a subset of the Modicon Modbus RTU serial communication
standard. The Modbus protocol is hardware-independent. That is, the physical layer can be
any of a variety of standard hardware configurations. This includes RS232, RS422, RS485,
fibre optics, etc. Modbus is a single master / multiple slave type of protocol suitable for a
multi-drop configuration as provided by RS485 hardware. The MM200 Modbus
implementation employs two-wire RS485 hardware. Using RS485, up to 32 MM200s can be
daisy-chained together on a single communication channel.
The MM200 is always a Modbus slave. It can not be programmed as a Modbus master.
Computers or PLCs are commonly programmed as masters.
Both monitoring and control are possible using read and write register commands. Other
commands are supported to provide additional functions.
Electrical Interface
The hardware or electrical interface in the MM200 is two-wire RS485. In a two-wire link,
data is transmitted and received over the same two wires. Although RS485 two wire
communication is bi-directional, the data is never transmitted and received at the same
time. This means that the data flow is half duplex.
RS485 lines should be connected in a daisy chain configuration with terminating networks
installed at each end of the link (i.e. at the master end and at the slave farthest from the
master). The terminating network should consist of a 120 W resistor in series with a 1 nF
ceramic capacitor when used with Belden 9841 RS485 wire. Shielded wire should always
be used to minimize noise. The shield should be connected to all of the MM200s as well as
the master, then grounded at one location only. This keeps the ground potential at the
same level for all of the devices on the serial link.

2-2 MM200 MOTOR MANAGEMENT SYSTEM – COMMUNICATIONS GUIDE
MODBUS PROTOCOL CHAPTER 2: RS485 INTERFACE (MODBUS RTU)
NOTE
NOTE: Polarity is important in RS485 communications. The '+' (positive) terminals of every device
must be connected together.
Data Frame Format and Data Rate
One data frame of an asynchronous transmission to or from a MM200 typically consists of
1 start bit, 8 data bits, and 1 stop bit. This produces a 10 bit data frame. This is important
for transmission through modems at high bit rates (11 bit data frames are not supported
by Hayes modems at bit rates of greater than 300 bps).
Modbus protocol can be implemented at any standard communication speed. The MM200
supports operation at 9600, 19200, 38400, 57600, and 115200 baud.
Data Packet Format
A complete request/response sequence consists of the following bytes (transmitted as
separate data frames):
Master Request Transmission:
SLAVE ADDRESS: 1 byte
FUNCTION CODE: 1 byte
DATA: variable number of bytes depending on FUNCTION CODE
CRC: 2 bytes
Slave Response Transmission:
SLAVE ADDRESS: 1 byte
FUNCTION CODE: 1 byte
DATA: variable number of bytes depending on FUNCTION CODE
CRC: 2 bytes
SLAVE ADDRESS: This is the first byte of every transmission. This byte represents the user-
assigned address of the slave device that is to receive the message sent by the master.
Each slave device must be assigned a unique address and only the addressed slave will
respond to a transmission that starts with its address. In a master request transmission the
SLAVE ADDRESS represents the address of the slave to which the request is being sent. In a
slave response transmission the SLAVE ADDRESS represents the address of the slave that is
sending the response.
FUNCTION CODE: This is the second byte of every transmission. Modbus defines function
codes of 1 to 127.
DATA: This will be a variable number of bytes depending on the FUNCTION CODE. This may
be Actual Values, Setpoints, or addresses sent by the master to the slave or by the slave to
the master.
CRC: This is a two byte error checking code.
Error Checking
The RTU version of Modbus includes a two byte CRC-16 (16 bit cyclic redundancy check)
with every transmission. The CRC-16 algorithm essentially treats the entire data stream
(data bits only; start, stop and parity ignored) as one continuous binary number. This
number is first shifted left 16 bits and then divided by a characteristic polynomial
(11000000000000101B). The 16 bit remainder of the division is appended to the end of the
transmission, MSByte first. The resulting message including CRC, when divided by the
same polynomial at the receiver will give a zero remainder if no transmission errors have
occurred.

CHAPTER 2: RS485 INTERFACE (MODBUS RTU) MODBUS PROTOCOL
MM200 MOTOR MANAGEMENT SYSTEM – COMMUNICATIONS GUIDE 2-3
If a MM200 Modbus slave device receives a transmission in which an error is indicated by
the CRC-16 calculation, the slave device will not respond to the transmission. A CRC-16
error indicates than one or more bytes of the transmission were received incorrectly and
thus the entire transmission should be ignored in order to avoid the MM200 performing
any incorrect operation.
The CRC-16 calculation is an industry standard method used for error detection. An
algorithm is included here to assist programmers in situations where no standard CRC-16
calculation routines are available.
CRC-16 Algorithm
Once the following algorithm is complete, the working register “A” will contain the CRC
value to be transmitted. Note that this algorithm requires the characteristic polynomial to
be reverse bit ordered. The MSBit of the characteristic polynomial is dropped since it does
not affect the value of the remainder. The following symbols are used in the algorithm:
—>: data transfer
A: 16 bit working register
AL: low order byte of A
AH: high order byte of A
CRC: 16 bit CRC-16 value
i, j: loop counters
(+): logical exclusive or operator
Di: i-th data byte (i = 0 to N-1)
G: 16 bit characteristic polynomial = 1010000000000001 with MSbit dropped and bit order
reversed
shr(x): shift right (the LSbit of the low order byte of x shifts into a carry flag, a '0' is shifted
into the MSbit of the high order byte of x, all other bits shift right one location
The algorithm is:
1. FFFF hex —> A
2. 0 —> i
3. 0 —> j
4. Di (+) AL —> AL
5. j+1 —> j
6. shr(A)
7. is there a carry? No: go to 8. Yes: G (+) A —> A
8. is j = 8? No: go to 5. Yes: go to 9.
9. i+1 —> i
10. is i = N? No: go to 3. Yes: go to 11.
11. A —> CRC
Timing
Data packet synchronization is maintained by timing constraints. The receiving device
must measure the time between the reception of characters. If 3.5 character times elapse
without a new character or completion of the packet, then the communication link must

2-4 MM200 MOTOR MANAGEMENT SYSTEM – COMMUNICATIONS GUIDE
MODBUS FUNCTIONS CHAPTER 2: RS485 INTERFACE (MODBUS RTU)
be reset (i.e. all slaves start listening for a new transmission from the master). Thus at 9600
baud a delay of greater than 3.5 x 1 / 9600 x 10 x = x 3.65 x ms will cause the
communication link to be reset.
MM200 supported functions
The following functions are supported by the MM200:
• FUNCTION CODE 03 - Read Setpoints and Actual Values
• FUNCTION CODE 04 - Read Setpoints and Actual Values
• FUNCTION CODE 05 - Execute Operation
• FUNCTION CODE 06 - Store Single Setpoint
• FUNCTION CODE 07 - Read Device Status
• FUNCTION CODE 08 - Loopback Test
• FUNCTION CODE 10 - Store Multiple Setpoints
Modbus Functions
Function Code 03H
Modbus implementation: Read Holding Registers
MM200 implementation: Read Setpoints
For the MM200 implementation of Modbus, this function code can be used to read any
setpoints (“holding registers”). Holding registers are 16 bit (two byte) values transmitted
high order byte first. Thus all MM200 Setpoints are sent as two bytes. The maximum
number of registers that can be read in one transmission is 125.
The slave response to this function code is the slave address, function code, a count of the
number of data bytes to follow, the data itself and the CRC. Each data item is sent as a two
byte number with the high order byte sent first.
For example, consider a request for slave 17 to respond with 3 registers starting at address
006B. For this example the register data in these addresses is as follows:
The master/slave packets have the following format:
Table 2-1: MASTER/SLAVE PACKET FORMAT FOR FUNCTION CODE 03H
Address Data
006B 022B
006C 0000
006D 0064
MASTER TRANSMISSION BYTES EXAMPLE DESCRIPTION
SLAVE ADDRESS 1 11 message for slave 17
FUNCTION CODE 1 03 read registers
DATA STARTING ADDRESS 2 00 6B data starting at 006B
NUMBER OF SETPOINTS 2 00 03 3 registers = 6 bytes
total
CRC 2 76 87 CRC error code

CHAPTER 2: RS485 INTERFACE (MODBUS RTU) MODBUS FUNCTIONS
MM200 MOTOR MANAGEMENT SYSTEM – COMMUNICATIONS GUIDE 2-5
Function Code 04H
Modbus Implementation: Read Input Registers
MM200 implementation: Read Actual Values
For the MM200 implementation of Modbus, this function code can be used to read any
actual values (“input registers”). Input registers are 16 bit (two byte) values transmitted high
order byte first. Thus all MM200 Actual Values are sent as two bytes. The maximum
number of registers that can be read in one transmission is 125.
The slave response to this function code is the slave address, function code, a count of the
data bytes to follow, the data itself and the CRC. Each data item is sent as a two byte
number with the high order byte sent first.
For example, request slave 17 to respond with 1 register starting at address 0008. For this
example the value in this register (0008) is 0000.
Table 2-2: MASTER/SLAVE PACKET FORMAT FOR FUNCTION CODE 04H
Function Code 05H
Modbus Implementation: Force Single Coil
MM200 Implementation: Execute Operation
This function code allows the master to request a MM200 to perform specific command
operations.
SLAVE RESPONSE BYTES EXAMPLE DESCRIPTION
SLAVE ADDRESS 111 message from slave
17
FUNCTION CODE 103 read registers
BYTE COUNT 106 3 registers = 6 bytes
DATA 1 (see definition above) 202 2B value in address
006B
DATA 2 (see definition above) 200 00 value in address
006C
DATA 3 (see definition above) 200 64 value in address
006D
CRC 254 83 CRC error code
MASTER TRANSMISSION BYTES EXAMPLE DESCRIPTION
SLAVE ADDRESS 1 11 message for slave 17
FUNCTION CODE 1 04 read registers
DATA STARTING ADDRESS 2 00 08 data starting at 0008
NUMBER OF ACTUAL VALUES 2 00 01 1 register = 2 bytes
CRC 2 B2 98 CRC error code
SLAVE RESPONSE BYTES EXAMPLE DESCRIPTION
SLAVE ADDRESS 111 message from slave
17
FUNCTION CODE 104 read registers
BYTE COUNT 102 1 register = 2 bytes
DATA (see definition above) 200 00 value in address
0008
CRC 278 F3 CRC error code

2-6 MM200 MOTOR MANAGEMENT SYSTEM – COMMUNICATIONS GUIDE
MODBUS FUNCTIONS CHAPTER 2: RS485 INTERFACE (MODBUS RTU)
For example, to request slave 17 to execute operation code 1 (reset), we have the following
master/slave packet format:
Table 2-3: MASTER/SLAVE PACKET FORMAT FOR FUNCTION CODE 05H
The commands that can be performed by the MM200 using function code 05 can also be
initiated by using function code 16.
Function Code 06H
Modbus Implementation: Preset Single Register
MM200 Implementation: Store Single Setpoint
This command allows the master to store a single setpoint into the memory of a MM200
The slave response to this function code is to echo the entire master transmission.
For example, request slave 17 to store the value 2 in setpoint address 04 5C. After the
transmission in this example is complete, setpoints address 04 5C will contain the value
01F4. The master/slave packet format is shown below:
Table 2-4: MASTER/SLAVE PACKET FORMAT FOR FUNCTION CODE 06H
MASTER TRANSMISSION BYTES EXAMPLE DESCRIPTION
SLAVE ADDRESS 1 11 message for slave 17
FUNCTION CODE 1 05 execute operation
OPERATION CODE 2 00 01 operation code 1
CODE VALUE 2 FF 00 perform function
CRC 2 DF 6A CRC error code
SLAVE RESPONSE BYTES EXAMPLE DESCRIPTION
SLAVE ADDRESS 1 11 message from slave
17
FUNCTION CODE 1 05 execute operation
OPERATION CODE 2 00 01 operation code 1
CODE VALUE 2 FF 00 perform function
CRC 2 DF 6A CRC error code
Operation Code Description
1 Reset
2 Lockout Reset
3 Stop
4 Start A
5 Start B
96 Clear Last Trip Data Prompt
99 Clear Counters
102 Clear Maintenance Timer
113 Reset Motor Information
114 Auto Mode
115 Manual Mode
MASTER TRANSMISSION BYTES EXAMPLE DESCRIPTION
SLAVE ADDRESS 1 11 message for slave 17
FUNCTION CODE 1 06 store single setpoint

CHAPTER 2: RS485 INTERFACE (MODBUS RTU) MODBUS FUNCTIONS
MM200 MOTOR MANAGEMENT SYSTEM – COMMUNICATIONS GUIDE 2-7
Function Code 07H
Modbus Implementation: Read Exception Status
MM200 Implementation: Read Device Status
This is a function used to quickly read the status of a selected device. A short message
length allows for rapid reading of status. The status byte returned will have individual bits
set to 1 or 0 depending on the status of the slave device. For this example, consider the
following MM200 general status byte:
The master/slave packets have the following format:
Table 2-5: Function code 7 bitmask
Table 2-6: MASTER/SLAVE PACKET FORMAT FOR FUNCTION CODE 07H
DATA STARTING ADDRESS 2 04 5C setpoint address 04
5C
DATA 2 00 02 data for setpoint
address 04 5C
CRC 2 CB B9 CRC error code
SLAVE RESPONSE BYTES EXAMPLE DESCRIPTION
SLAVE ADDRESS 111 message from slave
17
FUNCTION CODE 106 store single setpoint
DATA STARTING ADDRESS 204 5C setpoint address 04
5C
DATA 200 02 data stored in
setpoint address 04
5C
CRC 2CB B9 CRC error code
MASTER TRANSMISSION BYTES EXAMPLE DESCRIPTION
Bit Function
0Alarm
1Trip
2 Internal fault
3Auto
4 Contactor A
5 Contactor B
6 Contact output 3
7 Drive available (communications control)
MASTER TRANSMISSION BYTES EXAMPLE DESCRIPTION
SLAVE ADDRESS 1 11 message for slave 17
FUNCTION CODE 1 07 read device status
CRC 2 4C 22 CRC error code
SLAVE RESPONSE BYTES EXAMPLE DESCRIPTION
SLAVE ADDRESS 111 message from slave
17

2-8 MM200 MOTOR MANAGEMENT SYSTEM – COMMUNICATIONS GUIDE
MODBUS FUNCTIONS CHAPTER 2: RS485 INTERFACE (MODBUS RTU)
Function Code 08H
Modbus Implementation: Loopback
Test MM200 Implementation: Loopback Test
This function is used to test the integrity of the communication link. The MM200 will echo
the request.
For example, consider a loopback test from slave 17:
Table 2-7: MASTER/SLAVE PACKET FORMAT FOR FUNCTION CODE 08H
Function Code 10H
Modbus Implementation: Preset Multiple Registers
MM200 Implementation: Store Multiple Setpoints
This function code allows multiple Setpoints to be stored into the MM200 memory. Modbus
“registers” are 16-bit (two byte) values transmitted high order byte first. Thus all MM200
setpoints are sent as two bytes. The maximum number of Setpoints that can be stored in
one transmission is dependent on the slave device. Modbus allows up to a maximum of 60
holding registers to be stored. The MM200 response to this function code is to echo the
slave address, function code, starting address, the number of Setpoints stored, and the
CRC.
For example, consider a request for slave 17 to store the value 00 02 to setpoint address 04
5C and the value 01 F4 to setpoint address 04 5D. After the transmission in this example is
complete, MM200 slave 17 will have the following setpoints information stored:
The master/slave packets have the following format:
FUNCTION CODE 107 read device status
DEVICE STATUS (see definition
above)
12C status = 00101100 (in
binary)
CRC 222 28 CRC error code
SLAVE RESPONSE BYTES EXAMPLE DESCRIPTION
MASTER TRANSMISSION BYTES EXAMPLE DESCRIPTION
SLAVE ADDRESS 1 11 message for slave 17
FUNCTION CODE 1 08 loopback test
DIAG CODE 2 00 00 must be 00 00
DATA 2 00 00 must be 00 00
CRC 2 E0 0B CRC error code
SLAVE RESPONSE BYTES EXAMPLE DESCRIPTION
SLAVE ADDRESS 111 message from slave
17
FUNCTION CODE 108 loopback test
DIAG CODE 200 00 must be 00 00
DATA 200 00 must be 00 00
CRC 2E0 0B CRC error code
Address Data
04 5C 00 02
04 5D 01 F4

CHAPTER 2: RS485 INTERFACE (MODBUS RTU) MODBUS FUNCTIONS
MM200 MOTOR MANAGEMENT SYSTEM – COMMUNICATIONS GUIDE 2-9
Table 2-8: MASTER/SLAVE PACKET FORMAT FOR FUNCTION CODE 10H
Error Responses
When a MM200 detects an error other than a CRC error, a response will be sent to the
master. The MSBit of the FUNCTION CODE byte will be set to 1 (i.e. the function code sent
from the slave will be equal to the function code sent from the master plus 128). The
following byte will be an exception code indicating the type of error that occurred.
Transmissions received from the master with CRC errors will be ignored by the MM200.
The slave response to an error (other than CRC error) will be:
SLAVE ADDRESS: 1 byte
FUNCTION CODE: 1 byte (with MSbit set to 1)
EXCEPTION CODE: 1 byte
CRC: 2 bytes
The MM200 implements the following exception response codes:
01 - ILLEGAL FUNCTION
The function code transmitted is not one of the functions
supported by the MM200.
02 - ILLEGAL DATA ADDRESS
The address referenced in the data field transmitted by the
master is not an allowable address for the MM200.
03 - ILLEGAL DATA VALUE
The value referenced in the data field transmitted by the
master is not within range for the selected data address.
MASTER TRANSMISSION BYTES EXAMPLE DESCRIPTION
SLAVE ADDRESS 1 11 message for slave 17
FUNCTION CODE 1 10 store setpoints
DATA STARTING ADDRESS 2 04 5C setpoint address 04
5C
NUMBER OF SETPOINTS 2 00 02 2 setpoints = 4 bytes
total
BYTE COUNT 1 04 4 bytes of data
DATA 1 2 00 02 data for setpoint
address 04 5C
DATA 2 2 01 F4 data for setpoint
address 04 5D
CRC 2 31 11 CRC error code
SLAVE RESPONSE BYTES EXAMPLE DESCRIPTION
SLAVE ADDRESS 111 message from slave
17
FUNCTION CODE 110 store setpoints
DATA STARTING ADDRESS 204 5C setpoint address 04
5C
NUMBER OF SETPOINTS 200 02 2 setpoints
CRC 282 7A CRC error code

2-10 MM200 MOTOR MANAGEMENT SYSTEM – COMMUNICATIONS GUIDE
MODBUS MEMORY MAP CHAPTER 2: RS485 INTERFACE (MODBUS RTU)
Modbus memory map
Modbus Hex Description Min Max Step Units Format Default Size in
Words
ACTUAL VALUES
PRODUCT INFORMATION
30001 0000 Product Device Code --- --- --- --- F22 N/A 1
30002 0001 Hardware Revision --- --- --- --- F15 N/A 1
30003 0002 Firmware Version --- --- --- --- F3 N/A 1
30004 0003 Reserved --- --- --- --- --- --- 1
30005 0004 Modification Number --- --- --- --- F1 N/A 1
30006 0005 Boot Version --- --- --- --- F3 N/A 1
30007 0006 Reserved --- --- --- --- --- --- 1
30008 0007 Serial Number --- --- --- --- F22 N/A 6
30014 000D Order Code --- --- --- --- F22 N/A 16
30036 0023 Reserved --- --- --- --- --- --- 1
30037 0024 Build Date --- --- --- --- F22 N/A 6
30043 002A Build Time --- --- --- --- F22 N/A 4
30047 002E Original Calibration Date --- --- --- --- F18 N/A 2
30049 0030 Last Calibration Date --- --- --- --- F18 N/A 2
30051 0032 Reserved --- --- --- --- --- --- 6
to to Reserved --- --- --- --- --- --- ---
30185 00B8 Reserved 1
LAST TRIP DATA
30186 00B9 Cause of Last Trip --- --- --- --- FC134 N/A 1
30187 00BA Reserved --- --- --- --- --- --- 2
30189 00BC Reserved --- --- --- --- --- --- 2
30191 00BE Reserved --- --- --- --- --- --- 1
30192 00BF Pre Trip Ia --- --- --- AF10 N/A 2
30194 00C1 Pre Trip Ib --- --- --- AF10 N/A 2
30196 00C3 Pre Trip Ic --- --- --- AF10 N/A 2
30198 00C5 Reserved --- --- --- --- --- --- 1
30199 00C6 Reserved --- --- --- --- --- --- 1
30200 00C7 Reserved --- --- --- --- --- --- 1
30201 00C8 Pre Trip Motor Load --- --- --- %F1 N/A 1
30202 00C9 Pre Trip Current Unbalance --- --- --- %F1 N/A 1
30203 00CA Pre Trip Ig --- --- --- AF10 N/A 2
30205 00CC Reserved --- --- --- --- --- --- 1
to to Reserved --- --- --- --- --- --- ---
30229 00E4 Reserved --- --- --- --- --- --- 1
TRIP COUNTERS
30230 00E5 Total Number of Trips --- --- --- --- F1 N/A 1
30231 00E6 Reserved --- --- --- --- --- --- 1
30232 00E7 Overload Trips --- --- --- --- F1 N/A 1

CHAPTER 2: RS485 INTERFACE (MODBUS RTU) MODBUS MEMORY MAP
MM200 MOTOR MANAGEMENT SYSTEM – COMMUNICATIONS GUIDE 2-11
30233 00E8 Mechanical Jam Trips --- --- --- --- F1 N/A 1
30234 00E9 Undercurrent Trips --- --- --- --- F1 N/A 1
30235 00EA Current Unbalance Trips --- --- --- --- F1 N/A 1
30236 00EB Ground Fault Trips --- --- --- --- F1 N/A 1
30237 00EC Motor Acceleration Trips --- --- --- --- F1 N/A 1
30238 00ED Reserved --- --- --- --- --- --- 1
to to Reserved --- --- --- --- --- --- ---
30256 00FF Reserved --- --- --- --- --- --- 1
GENERAL TIMERS
30257 0100 Number of Motor Starts --- --- --- --- F1 N/A 1
30258 0101 Reserved --- --- --- --- --- --- 1
30259 0102 Motor Running Hours --- --- --- hrs F9 N/A 2
30261 0104 Reserved --- --- --- --- --- --- 1
to to Reserved --- --- --- --- --- --- ---
30269 010C Reserved --- --- --- --- --- --- 1
START BLOCKS
30270 010D Overload Lockout --- --- --- --- F1 N/A 1
30271 010E Reserved --- --- --- --- --- --- 1
30272 010F Reserved --- --- --- --- --- --- 1
30273 0110 Restart Block --- --- --- sF1 N/A 1
30274 0111 Reserved --- --- --- --- --- --- 1
to to Reserved --- --- --- --- --- --- ---
30282 0119 Reserved --- --- --- --- --- --- 1
CONTACT/VIRTUAL INPUTS/OUTPUTS STATUS
30283 011A Reserved --- --- --- --- --- --- 2
30285 011C Contact Input 7-1 (Bit Field) --- --- --- --- FC167 N/A 2
30287 011E Reserved --- --- --- --- --- --- 1
to to Reserved --- --- --- --- --- --- ---
30297 0128 Reserved --- --- --- --- --- --- 1
30298 0129 Contact Output 3-1 (Bit Field) --- --- --- --- FC167 N/A 2
30300 012B Reserved --- --- --- --- --- --- 1
30301 012C Reserved --- --- --- --- --- --- 1
SECURITY
30302 012D Current Security Access Level --- --- --- --- F1 N/A 1
30303 012E Reserved --- --- --- --- --- --- 1
30304 012F Reserved --- --- --- --- --- --- 1
STATUS - MOTOR
30305 0130 Motor Status --- --- --- --- FC129 N/A 1
30306 0131 Extended Status --- --- --- --- FC178 N/A 1
30307 0132 Thermal Cap Used --- --- --- %F1 N/A 1
30308 0133 Time to Overload Trip --- --- --- sF20 N/A 2
30310 0135 Drive Status --- --- --- --- FC143 N/A 1
30311 0136 Reserved --- --- --- --- --- --- 1
30312 0137 Command Status --- --- --- --- FC128 N/A 1
30313 0138 Reserved --- --- --- --- --- --- 1
30314 0139 Reserved --- --- --- --- --- --- 1
Modbus Hex Description Min Max Step Units Format Default Size in
Words

2-12 MM200 MOTOR MANAGEMENT SYSTEM – COMMUNICATIONS GUIDE
MODBUS MEMORY MAP CHAPTER 2: RS485 INTERFACE (MODBUS RTU)
to to Reserved --- --- --- --- --- --- ---
30327 0146 Reserved 1
CURRENT METERING
30328 0147 Ia --- --- --- AF10 N/A 2
30330 0149 Ib --- --- --- AF10 N/A 2
30332 014B Ic --- --- --- AF10 N/A 2
30334 014D Iavg --- --- --- AF10 N/A 2
30336 014F Motor Load --- --- --- %F1 N/A 1
30337 0150 Current Unbalance --- --- --- %Ub F1 N/A 1
30338 0151 Ig --- --- --- AF10 N/A 2
30340 0153 Reserved --- --- --- --- --- --- 1
to to Reserved --- --- --- --- --- --- ---
30434 01B1 Reserved --- --- --- --- --- --- 1
TEMPERATURE METERING
30435 01B2 Thermistor --- --- --- ohms F1 N/A 1
30436 01B3 Reserved --- --- --- --- --- --- 1
to to Reserved --- --- --- --- --- --- ---
30466 01D1 Reserved 1
MOTOR STARTING LEARNED DATA
30467 01D2 Learned Acceleration Time --- --- --- sF2 N/A 1
30468 01D3 Learned Starting Current --- --- --- AF10 N/A 2
30470 01D5 Learned Starting Capacity --- --- --- %F1 N/A 1
30471 01D6 Reserved --- --- --- --- --- --- 1
to to Reserved --- --- --- --- --- --- ---
30504 01F7 Reserved --- --- --- --- --- --- 1
LED STATUS FOR GRAPHICAL AND BASIC CONTROL PANEL
30505 01F8 LED Status --- --- --- --- FC144 N/A 2
30507 01FA Reserved --- --- --- --- --- --- 1
to to Reserved --- --- --- --- --- --- ---
30523 020A Reserved --- --- --- --- --- --- 1
USER MAP VALUES
30524 020B User Map Value 1 --- --- --- --- F1 N/A 1
30525 020C User Map Value 2 --- --- --- --- F1 N/A 1
30526 020D User Map Value 3 --- --- --- --- F1 N/A 1
30527 020E User Map Value 4 --- --- --- --- F1 N/A 1
to to Reserved --- --- --- --- --- --- ---
30645 0284 User Map Value 122 --- --- --- --- F1 N/A 1
30646 0285 User Map Value 123 --- --- --- --- F1 N/A 1
30647 0286 User Map Value 124 --- --- --- --- F1 N/A 1
30648 0287 User Map Value 125 --- --- --- --- F1 N/A 1
30649 0288 Reserved --- --- --- --- --- --- 1
to to Reserved --- --- --- --- --- --- ---
30656 028F Reserved --- --- --- --- --- --- 1
SELF TEST
30657 0290 Internal Fault Cause --- --- --- --- FC188 N/A 2
30659 0292 Reserved --- --- --- --- --- --- 2
Modbus Hex Description Min Max Step Units Format Default Size in
Words
Other manuals for MM200
1
Table of contents
Popular Control System manuals by other brands

Tekmar
Tekmar 364 Data brochure
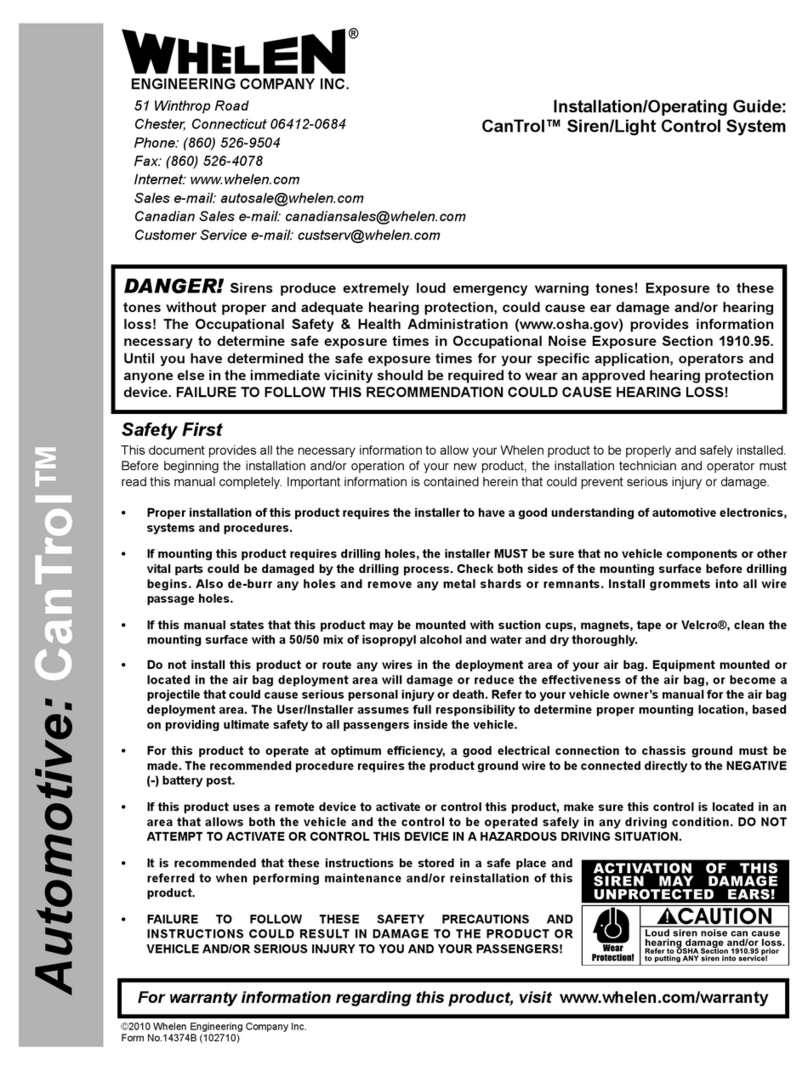
Whelen Engineering Company
Whelen Engineering Company CanTrol Installation & operating guide
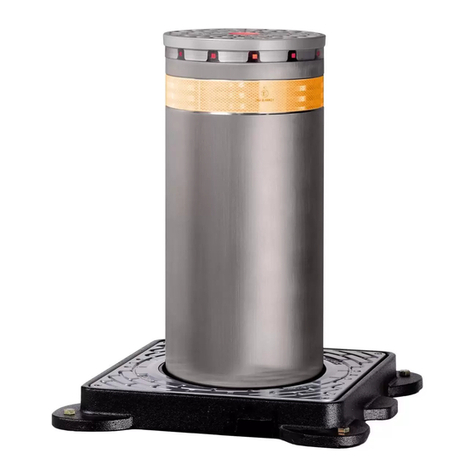
FAAC
FAAC J275 HA 2K20 Translation of the original instructions
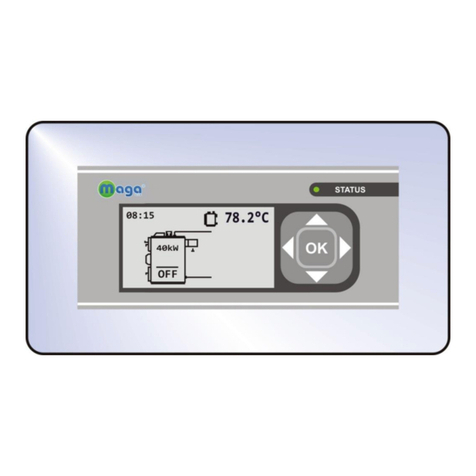
ERS
ERS AK 6000 user manual

Lindsay
Lindsay Barrier Systems X-LITE installation manual
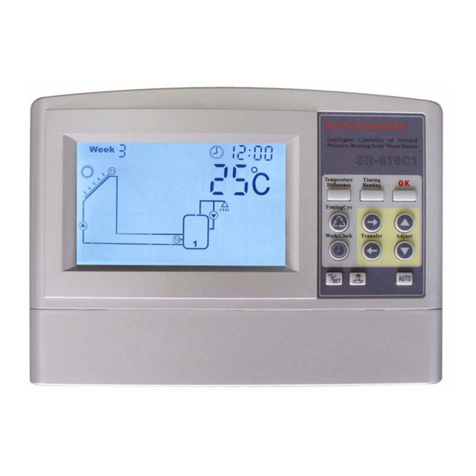
Shuangri Electric
Shuangri Electric SR618C1 Installation and operating manual