Quanser 3 DOF User manual

Quanser 3 DOF Hover
User Manual
3 DOF Hover
Quanser Inc.
2013

© 2013 Quanser Inc., All rights reserved.
Quanser Inc.
119 Spy Court
Markham, Ontario
L3R 5H6
Canada
info@quanser.com
Phone: 1-905-940-3575
Fax: 1-905-940-3576
Printed in Markham, Ontario.
For more information on the solutions Quanser Inc. offers, please visit the web site at:
http://www.quanser.com
This document and the software described in it are provided subject to a license agreement. Neither the software nor this document may be
used or copied except as specified under the terms of that license agreement. All rights are reserved and no part may be reproduced, stored in
a retrieval system or transmitted in any form or by any means, electronic, mechanical, photocopying, recording, or otherwise, without the prior
written permission of Quanser Inc.
3 DOF HOVER User Manual 2

CONTENTS
1 Presentation 4
2 System Description 5
2.1 Components 5
2.2 System Specifications 7
3 System Setup 9
3.1 Assembling the 3 DOF Hover 9
3.2 Balancing the 3 DOF Hover 9
3.3 Typical Connections 9
4 Testing and Troubleshooting 13
4.1 Motor 13
4.2 Encoder 13
5 Technical Support 14
3 DOF HOVER User Manual v 1.0

1 PRESENTATION
The Quanser 3 DOF Hover experiment, shown in Figure 1.1, consists of a helicopter model mounted on a fixed
base with two propellers that are driven by DC motors. The front propeller controls the elevation of the helicopter
nose about the pitch axis and the back propeller controls the side to side motions of the helicopter about the yaw
axis.
The Quanser 3 DOF Hover system consists of a frame with four propellers. The frame is mounted on a three
degree of freedom pivot joint that enables the body to rotate about the roll, pitch and yaw axes. Each propeller
generates a lift force and the lift forces are used to control the pitch and roll angles. The total torque generated by
the propeller motors causes the body to move about the yaw axis. One set of propellers in the system are counter-
rotating propellers such that the total torque in the system is balanced when the thrust of the four propellers are
approximately equal. The axes angles are all measured using high-resolution encoders. The encoder and motor
signals are transmitted through a slip ring mechanism, which allows the yaw axis to rotate continuously about 360
degrees.
Figure 1.1: Quanser 3 DOF Hover
In Section 2 the components composing the Quanser 3 DOF Hover are described and the system specifications are
given. Section 3 explains how to setup the system and gives the wiring procedure.
Caution: This equipment is designed to be used for educational and research purposes and is not
intended for use by the general public. The user is responsible to ensure that the equipment
will be used by technically qualified personnel only.
3 DOF HOVER User Manual 4

2 SYSTEM DESCRIPTION
2.1 Components
Section 2.1.1 lists the components on the Quanser 3 DOF Hoverplant and 2.2 summarizes the system specifications.
2.1.1 Quanser 3 DOF HoverOverall Components
The components comprising the Quanser 3 DOF Hoversystem are labeled in Figure 2.1, Figure 2.2, and Figure 2.3,
are described in Table 2.1. The motors, propeller assemblies, and encoders are described in more detail below.
ID # Component ID # Component
1 Propeller shield 11 Base platform
2 Motor 12 Front motor connector
3 Clip 13 Right motor connector
4 Roll axis encoder 14 Back motor connector
5 Pitch axis encoder 15 Yaw motor connector
6 Yoke 16 Roll encoder connector
7 Encoder/motor circuit 17 Pitch encoder connector
8 Body frame 18 yaw encoder connector
9 Slip ring 19 Left motor connector
10 Propeller
Table 2.1: Quanser 3 DOF Hovercomponents
Figure 2.1: Quanser 3 DOF Hover base components
3 DOF HOVER User Manual v 1.0

Figure 2.2: Quanser 3 DOF Hover plant components
Figure 2.3: Quanser 3 DOF Hover propeller assembly components
2.1.2 DC Motors (Components #2)
The Quanser 3 DOF Hover has four DC motors: the front and back motors that mainly control the system about the
pitch axis and the left and right motors that primarily move it about the roll axis.
Each DC motor is a Pittman Model 9234. It has an electrical resistance of 0.83 Ωand a current-torque constant of
0.0182 N.m/A. The rated voltage of the motor is 12 V but its peak voltage can be brought up to 22 V without damage.
See [1] for the full specifications of this motor.
3 DOF HOVER User Manual 6

Caution: Pitch motor input: ±24V, 5A peak, 3A continuous.
2.1.3 Propellers (Components #10)
The pitch and yaw propeller assemblies are composed of the actual propeller, which is directly mounted to the motor
shaft, and the aluminum propeller shield. The propellers used for both the pitch and yaw motors are Graupner
20/15 cm or 8/6''. The pitch motor/propeller has an identified thrust-force constant of 0.119 N/V and a thrust-torque
constant of 0.0036 N-m/V. The thrust-force constant describes the lifting force of propellers when working in the pitch
and roll axes. The thrust-torque constant is used to determine the amount of voltage needed to rotate the hover
system about its yaw axis.
Caution: The propellers rotate at high speeds. Always make sure the propeller shields are installed when in
operation and stay clear of the system.
2.1.4 Encoders (Components #4 and #5)
The Quanser 3 DOF Hover experiment has three encoders used to measure the angle of pitch, yaw, and roll axes. In
quadrature mode, each encoder has a resolution of 8192 counts per revolution. Thus the effective position resolution
is 0.0439 degrees about the yaw, pitch, and roll axes.
2.2 System Specifications
The main parameters of the Quanser 3 DOF Hover is summarized in Table 2.2. The motor and encoder specifications
are listed in Table 2.3 below. Finally, Table 2.4 lists various dimensions, masses, and inertias of the Quanser 3 DOF
Hover system.
Symbol Description Value Unit
KtTorque thrust constant of motor/propeller 0.0036 N-m/V
KfForce-thrust constant of motor/propeller 0.1188 N/V
LDistance between pivot to each motor 0.197 cm
mhover Total moving mass of the system (body, four pro-
peller assemblies, etc.)
2.85 kg
JyEquivalent moment of inertia about yaw axis. 0.110 kg-m2
JpEquivalent moment of inertia about pitch axis 0.0552 kg-m2
JrEquivalent moment of inertia about roll axis. 0.0552 kg-m2
Table 2.2: 3 DOF Hover model parameters
Symbol Description Value Unit
RmArmature resistance of motor 0.83 Ω
KtCurrent-torque constant of motor 0.0182 N-m/A
JmRotor moment of inertia of motor 1.91 ×10−6kg-m2
mmMass of DC motor 0.292 kg
KEC Encoder resolution (in quadrature mode) 8192 counts/rev
Encoder sensitivity gain 7.67 ×10−4rad/counts
Table 2.3: 3 DOF Hover motor and encoder specifications
3 DOF HOVER User Manual v 1.0

Symbol Description Value Unit
mshield Mass of propeller shield 0.167 kg
mprops Mass of propeller, propeller shield, and motor as-
sembly
0.754 kg
mshaft Mass of metal shaft rotating about yaw axis 0.151 kg
Lshaft Length of metal shaft rotating about yaw axis 0.280 m
Jshaft Moment of inertia of metal shaft about yaw axis end
point
0.0039 kg-m2
Table 2.4: Various 3 DOF Hover mass, length, and inertia parameters
3 DOF HOVER User Manual 8

3 SYSTEM SETUP
3.1 Assembling the 3 DOF Hover
The Hover system comes partially disassembled and this section explains how to install the system and do some
device-only wiring. Connecting the 3 DOF Hover to the amplifiers and the data acquisition device is explained in
Section 3.3.
Follow these steps to setup the 3 DOF Hover system:
1. Place the base of the 3 DOF Hover, Component # 11 shown in Figure 2.1, on a table or on the floor.
2. Assemble the body to the main base by aligning the pitch/roll encoder frame, i.e., the yoke shown in Figure
2.2 as Component #6, with the top of the base and tighten the thumb screws.
Caution: Once the body is installed on the support base, do not lift the system from the helicopter body.
Always carry from the base with one hand and stabilize the body with the other hand. Never
apply extreme loads in the vertical direction!
3. Connect the flat 5-pin connector from the pitch encoder (Component #5 in Figure 2.2), i.e., the encoder that
is labeled Pitch, to the 5-pin connector on the Encoder/Motor Circuit, Component #7 in Figure 2.2. Align the
GND pin #1 on the cable to the BR pin on the Encoder/Motor circuit.
4. Connect the flat 5-pin to 5-pin-stereo-DIN cable from the roll encoder (Component #4 inFigure 2.2) to the
5-pin-stereo-DIN connector on the Encoder/Motor circuit board that is labeled ENCODER.
5. Connect the flat 5-pin-stereo-DIN to 5-pin-stereo-DIN cable from the four motors (Component #2 in Figure 2.2)
to the 5-pin-stereo-DIN connector on the Encoder/Motor circuit board that is labeled MOTORS.
Caution: Exposed moving parts. Ensure all obstructions that may interfere with the complete 360-degree
axial motion of the helicopter are removed before performing any experiment.
3.2 Balancing the 3 DOF Hover
Before running the experiments, the frame of the 3 DOF Hover must be horizontal with the ground when the system
is at rest.
1. Using the supplied with weight clips, Component #3 in Figure 2.2, move the clips around the edge of the circular
frame until the frame is balanced, i.e., parallel with the floor.
2. The system is always balanced before being shipped. However, some re-adjustments to the weights may have
to be made as the wires from the body to the base do affect the balance.
3.3 Typical Connections
This section describes the typical cabling connections that are used by default for the Quanser 3 DOF Hover system.
The encoders are connected directly to the data-acquisition device and provide the necessary position feedback to
control the helicopter. The data acquisition (DAQ) device outputs a control voltage that is amplified and drives the
front, back, left, and right motors. Figure 3.1 illustrates the wiring between a generic data acquisition device, the
Quanser 3 DOF Hover base, and a four-channel amplifier. These connections are described in detail in Section
3.3.1 and summarized in Table 3.1.
3 DOF HOVER User Manual v 1.0

Caution: If the equipment is used in a manner not specified by the manufacturer, the protection provided by
the equipment may be impaired.
Note: Your configuration may be different. For instance, you may have a DAQ with more channels than the one
presented in Figure 3.1 or have four single-channel amplifiers that do not require any Emergency Stop (in which
case, you would omit connection #12).
Figure 3.1: Typical connections of the 3 DOF Hover Experiment
3 DOF HOVER User Manual 10

Cable # From To Signal
1 DAQ: Analog Output
#0
Amplifier 0: Command Command signal sent to amplifier
for the front motor.
2 DAQ: Analog Output
#1
Amplifier 1: Command Command signal sent to amplifier
for the back motor.
3 DAQ: Analog Output
#2
Amplifier 2: Command Command signal sent to amplifier
for the left motor.
4 DAQ: Analog Output
#3
Amplifier 3: Command Command signal sent to amplifier
for the right motor.
5 Amplifier 0: To Load Quanser 3 DOF
Hover: Front Motor
(D/A 0)
Amplified voltage that is applied to
the front DC motor.
6 Amplifier 1: To Load Quanser 3 DOF
Hover: Back Motor
(D/A 1)
Amplified voltage that is applied to
the back DC motor.
7 Amplifier 2: To Load Quanser 3 DOF
Hover: Left Motor
(D/A 2)
Amplified voltage that is applied to
the left DC motor.
8 Amplifier 3: To Load Quanser 3 DOF
Hover: Right Motor
(D/A 3)
Amplified voltage that is applied to
the right DC motor.
9 3 DOF Hover: Pitch
Encoder (ENC 0) con-
nector
DAQ: Encoder #0 Measured pitch angle.
10 3 DOF Hover: Roll En-
coder (ENC 1) connec-
tor
DAQ: Encoder #1 Measured roll angle.
11 3 DOF Hover: Yaw En-
coder (ENC 2) connec-
tor
DAQ: Encoder #2 Measured yaw angle.
12 Emergency Stop
switch
Amplifier E-Stop con-
nector
Disables the amplifier when the red
button is pressed down. If the E-
Stop switch is connected, the am-
plifier can only be enabled if the red
knob is in the released position.
Table 3.1: Quanser 3 DOF Hover system wiring summary
3.3.1 Wiring Details
Follow these steps to connect the Quanser 3 DOF Hoversystem:
1. Make sure your data acquisition (DAQ) device has been installed and tested. See the specific DAQ documen-
tation for details.
2. Make sure everything is powered off before making any of these connections. This includes turning off your
PC and the amplifier.
3. Connect one of the connectors on the 2x RCA to 2x RCA cable from the Analog Output Channel #0 on the
terminal board to the Amplifier 0 Amplifier Command connector. This is illustrated by connection #1 in Figure
3.1.
4. Connect the other line of the 2XRCA to 2XRCA cable from the Analog Output #1 connector on the terminal
board to the Amplifier 1 Amplifier Command connector. This is illustrated by connection #2 in Figure 3.1.
3 DOF HOVER User Manual v 1.0

5. Connect a 4-pin-DIN to 6-pin-DIN cable from Amplifier 0 To Load (3x Amplifier Command) connector, to the
Pitch Motor (D/A 0) connector on the Quanser 3 DOF Hoverplant. This is illustrated by connection #3 in Figure
3.1.
6. Connect another 4-pin-DIN to 6-pin-DIN cable from the Amplifier 1 To Load (3x Amplifier Command) connector,
to the Yaw Motor (D/A 1) connector on the Quanser 3 DOF Hoverplant. This is illustrated by connection #4 in
Figure 3.1.
7. Connect a 5-pin-stereo-DIN to 5-pin-stereo-DIN cable from the Encoder 0 connector on the terminal board, to
the Pitch Encoder (ENC 0) connector on the Quanser 3 DOF Hoverplant. This is illustrated by connection #5
in Figure 3.1.
8. Connect another 5-pin-stereo-DIN to 5-pin-stereo-DIN cable from the Encoder 1 connector on the terminal
board to the Yaw Encoder (ENC 1) connector on the Quanser 3 DOF Hoverplant. This is illustrated by con-
nection #6 in Figure 3.1.
Caution: Encoders should be directly connected to the data acquisition device using a standard 5-pin
DIN cable. DO NOT connect the encoder cable to the amplifiers!
9. Connect the emergency stop switch to the E-Stop connector on the amplifier. This is illustrated by connection
#7 in Figure 3.1.
10. Connect the USB cable of the supplied joystick to a USB port on the PC. The system should detect the joystick
and automatically install the driver (you will be prompted). See the corresponding joystick User Manual for
more information on the setup procedure.
11. If your amplifier has a Gain setting switch, make sure you set the amplifier Gain to 3 when using the
Quanser 3 DOF Hoverexperiment.
12. Turn ON the rear power switch of the amplifier.
3 DOF HOVER User Manual 12

4 TESTING AND TROUBLESHOOT-
ING
This section describes some functional tests to determine if your system is operating normally. It is assumed that
the Quanser 3 DOF Hoveris connected as described in Section 3.3. To carry out these tests, it is preferable if the
user can use a software such as QUARCror LabVIEW™ to read sensor measurements and feed voltages to the
motor. Alternatively, these tests can be performed with a signal generator and an oscilloscope.
4.1 Motor
4.1.1 Testing
Ensure the motors are operating correctly by going through this procedure:
1. Apply approximately 4V to Analog Output Channel #0 on the DAQ to verify that the front propeller rotates.
2. Similarly, apply 4V to Analog Output Channel #1, 2, and 3 to verify that the back, left, and right motors, respec-
tively, are rotating.
4.1.2 Troubleshooting
If the motor is not responding to a voltage signal, go through these steps:
• Review the RCA and motors connections in Section 3.3.
• Ensure the power amplifier is powered on and operational, e.g., when using the Quanser VoltPAQ-X4, verify
that the green LED lit.
• Check that the data acquisition device is functional. Go through the DAQ User Manual for troubleshooting
guidelines.
• Ensure the voltage is actually reaching the motor terminals (use a voltmeter or oscilloscope).
• If the E-Stop is connected, make sure the red button is in the upper, released position.
4.2 Encoder
4.2.1 Testing
Follow this procedure to test each encoder on their respective motors:
1. Measure Encoder Input Channel #0 and rotate the pitch angle, i.e., axis about the front and back propellers,
up and down. Verify if any counts are being outputted.
2. Measure Encoder Input Channel #1 and rotate the roll angle, i.e., axis about the left and right propellers, up
and down. Verify if any counts are being outputted.
3. Measure the Encoder Input Channel #2 and rotate the yaw angle. Rotate the hover about the yaw axis one
full rotation and verify that 8192 is being measured (in 4x quadrature mode).
3 DOF HOVER User Manual v 1.0

Note: Some data acquisition systems do not measure in quadrature and, in this case, one-quarter of the expected
counts are received, i.e., 2048 counts. Make sure the details of the data-acquisition system being used is known.
The counters on the Quanser DAQ boards measure in quadrature and therefore a total of four times the number of
encoder lines per rotation, e.g., a 2048-line encoder results in 8192 integer counts for every full rotation.
4.2.2 Troubleshooting
If the encoder is not measuring properly, go through this procedure:
• Review the encoder connections in Section 3.3.
• Check that the data acquisition device is functional. Go through the DAQ User Manual for troubleshooting
guidelines.
• Check that both the A and B channels from the encoder are properly generated and fed to the data-acquisition
device. Using an oscilloscope, there should be two square waves, signals A and B, with a phase shift of 90
degrees. If this is not observed then the encoder may be damaged and need to be replaced. Please see
Section 5 for information on contacting Quanser for technical support.
5 TECHNICAL SUPPORT
To obtain support from Quanser, go to http://www.quanser.com/ and click on the Tech Support link. Fill in the
form with all the requested software and hardware information as well as a description of the problem encountered.
Also, make sure your e-mail address and telephone number are included. Submit the form and a technical support
representative will contact you.
3 DOF HOVER User Manual 14

REFERENCES
[1] Pittman. LO-COG DC Servo Motors 8000, 9000, 14000, 2010.
3 DOF HOVER User Manual v 1.0
Other manuals for 3 DOF
3
Table of contents
Popular Microcontroller manuals by other brands
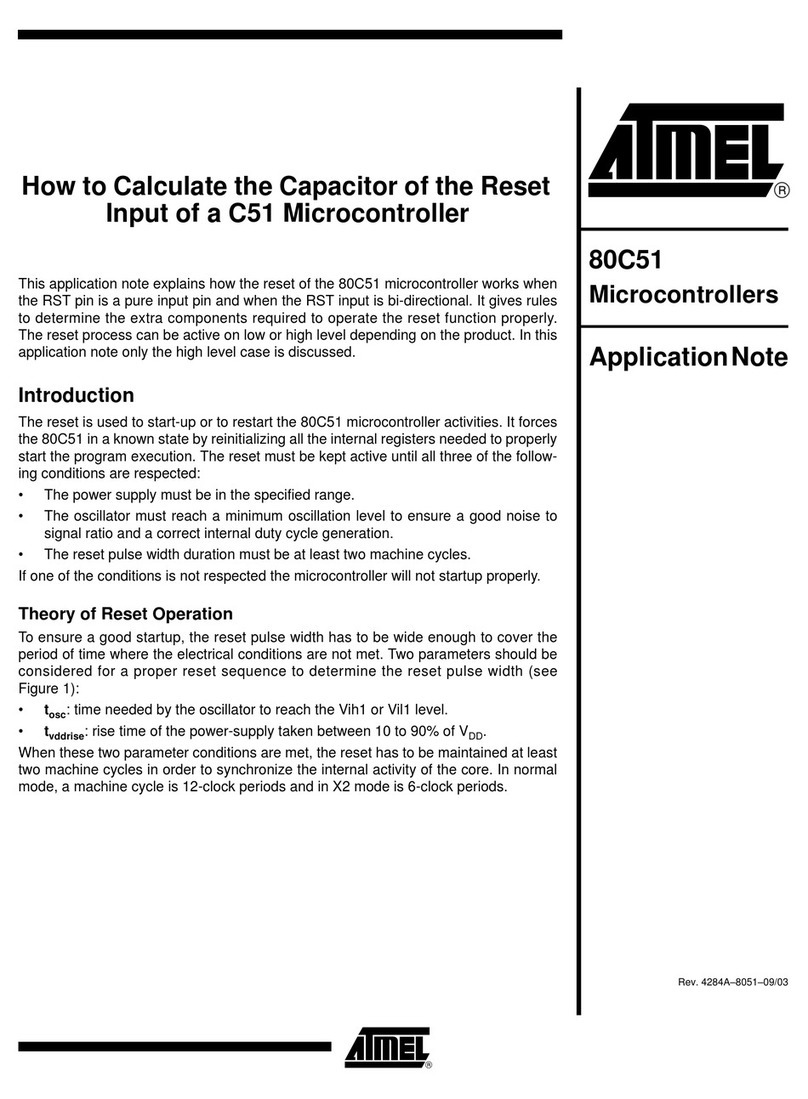
Atmel
Atmel 80C51 Application note
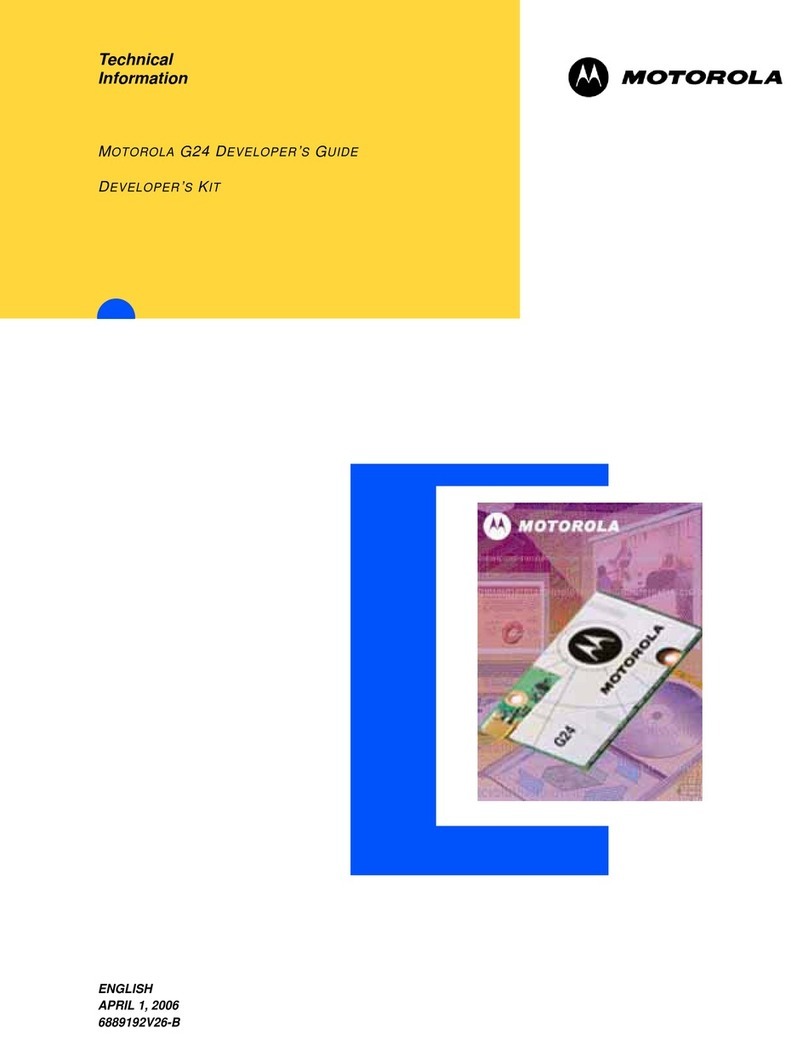
Motorola
Motorola G24 Guide Developer's guide
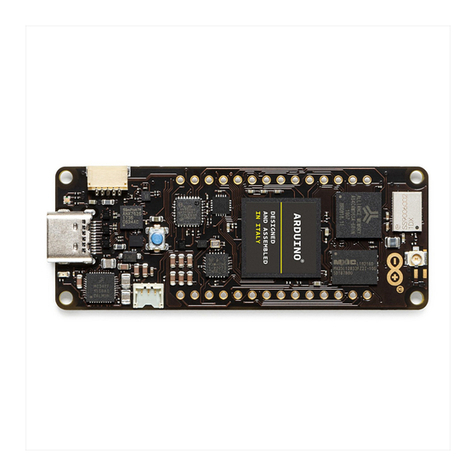
Arduino
Arduino Portenta H7 Lite Product reference manual
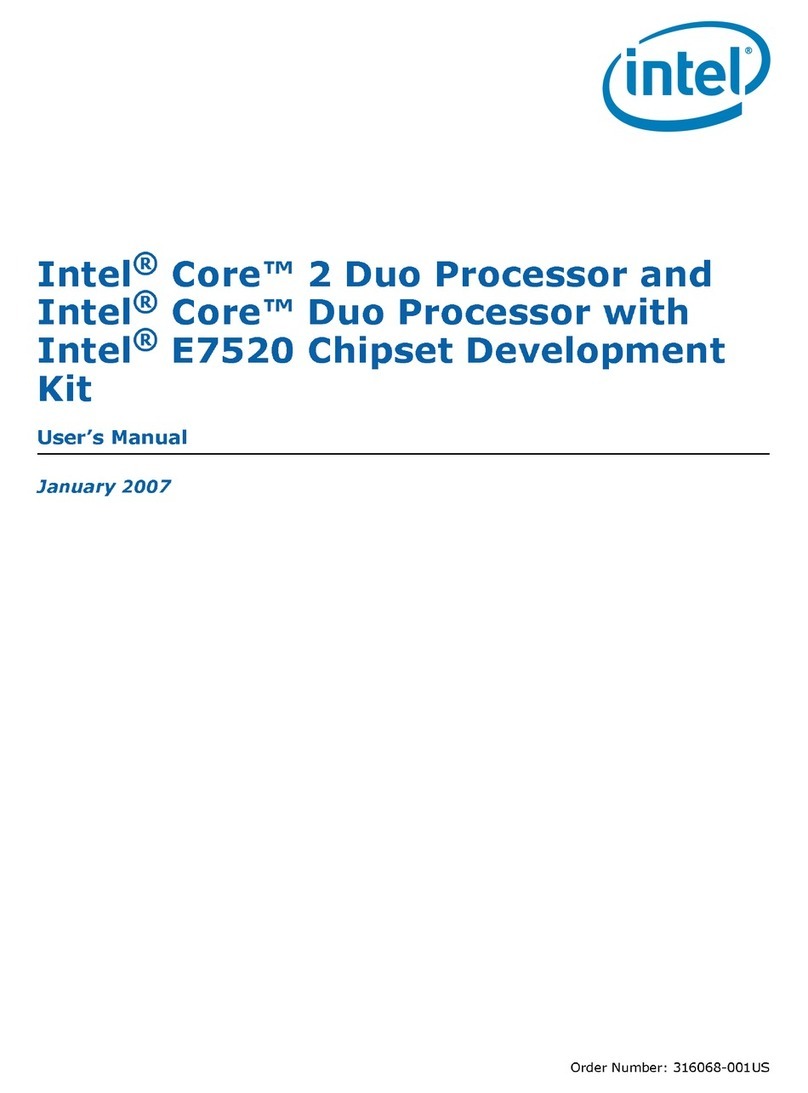
Intel
Intel BX80539T2500 - Core Duo 2 GHz Processor user manual
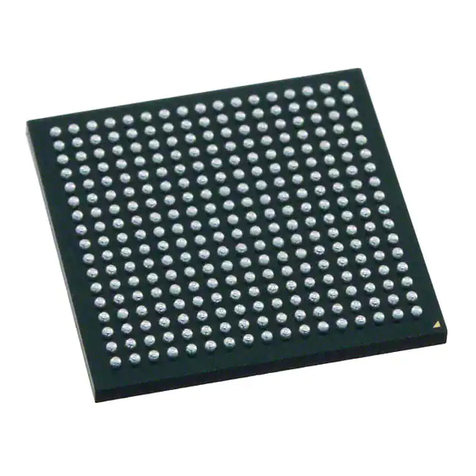
STMicroelectronics
STMicroelectronics SPEAr300 Reference manual
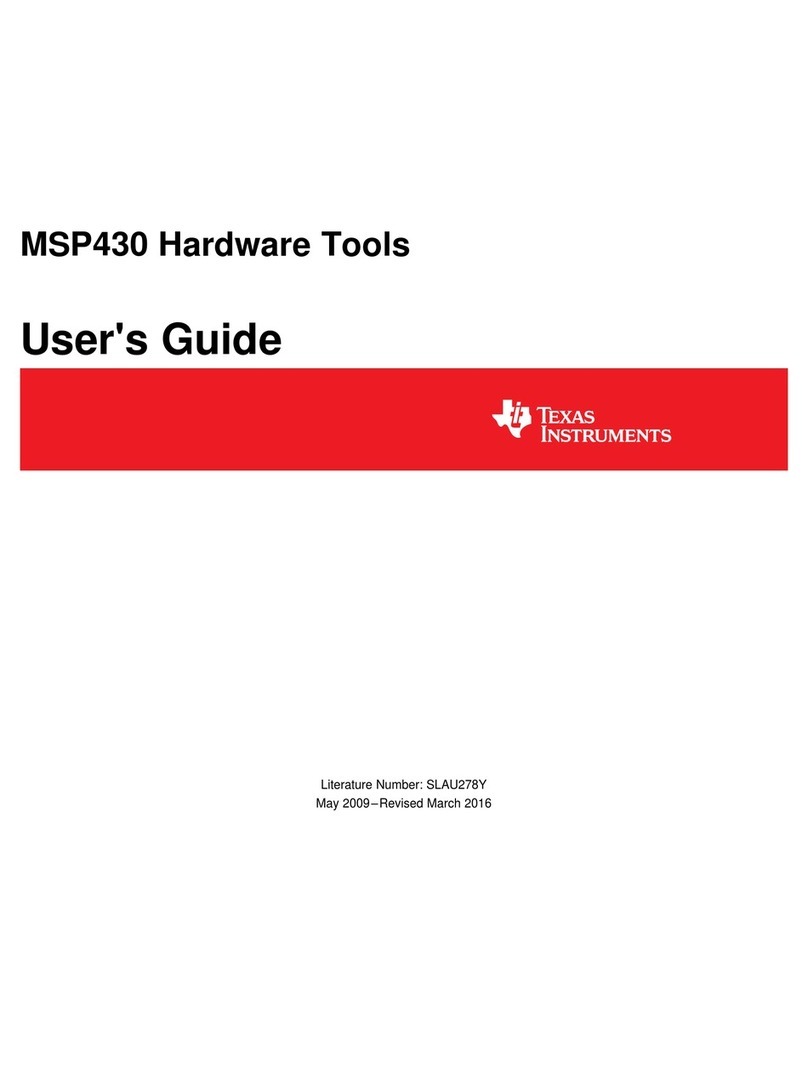
Texas Instruments
Texas Instruments Serial Programming Adapter MSP430 user guide
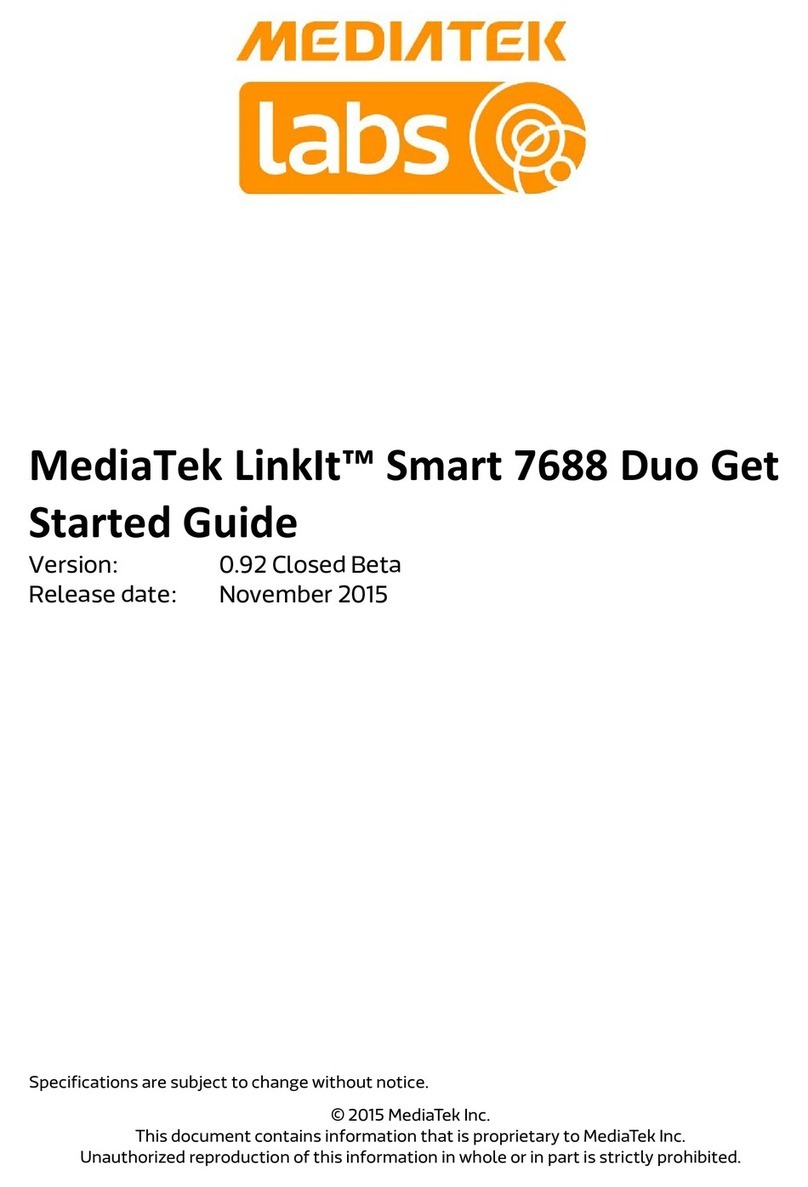
MEDIATEK
MEDIATEK LinkIt Smart 7688 Duo Get started guide
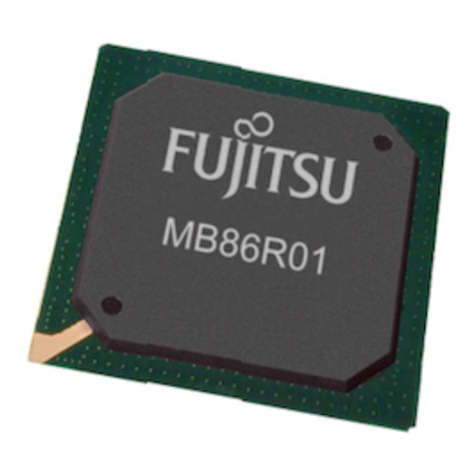
Fujitsu
Fujitsu MB86R01 Application note
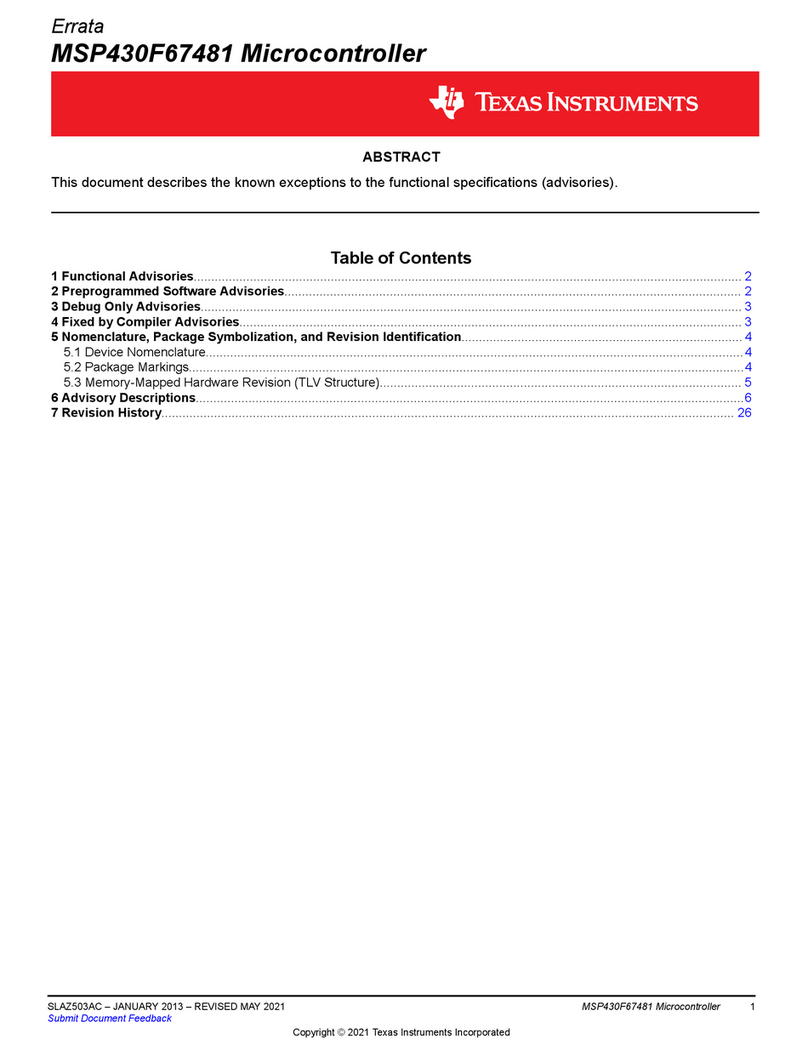
Texas Instruments
Texas Instruments MSP430F67481 manual
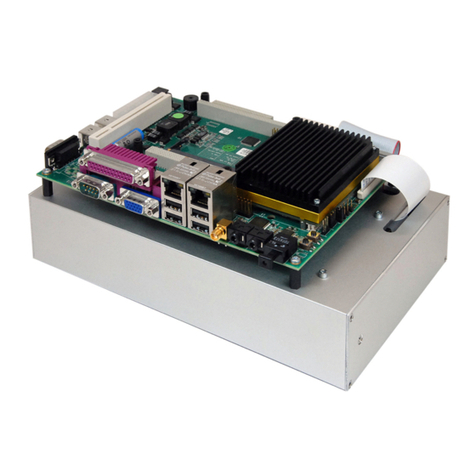
DIGITAL-LOGIC
DIGITAL-LOGIC SM800/900DK Technical user's manual

Lattice Semiconductor
Lattice Semiconductor MachXO2 Pico quick start
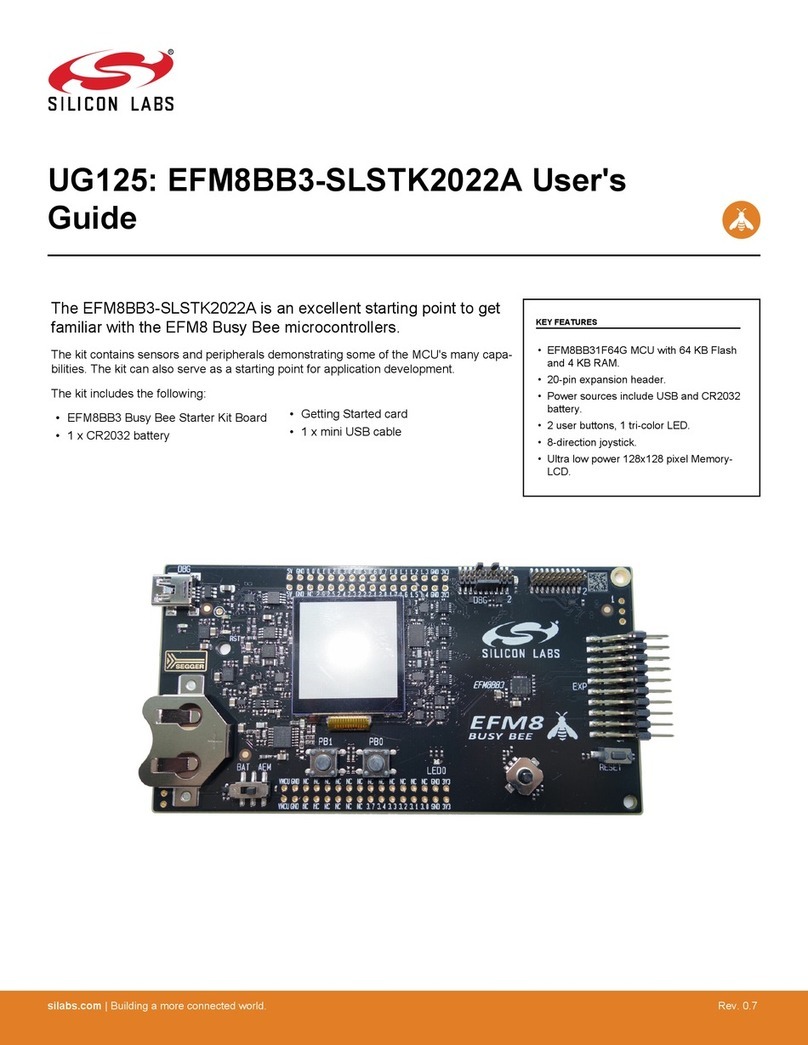
Silicon Laboratories
Silicon Laboratories EFM8BB3-SLSTK2022A user guide