Quest Controls TELSEC MP2x User manual

Rev 2.1 10/21/21
TELSEC® MP2x
User Guide

Rev 2.1 10/21/21
CRITICAL APPLICATIONS DISCLAIMER
QUEST PRODUCTS ARE NOT INTENDED OR AUTHORIZED FOR USE IN ANY APPLICATION THAT REQUIRES
FAIL-SAFE OPERATION, OR ANY SYSTEM THAT IS RESPONSIBLE FOR PROVIDING DETECTION,
MONITORING OR CONTROL OF CRITICAL SAFETY, LIFESAVING OR LIFE-SUPPORT CONDITIONS,
FUNCTIONS OR OPERATIONS (INCLUDING BUT NOT LIMITED TO FIRE DETECTION, ALARMING, OR
SUPPRESSION), OR ANY APPLICATION WHEREIN A FAILURE OR MALFUNCTION OF THE PRODUCT MAY
LEAD TO SEVERE PROPERTY OR ENVIRONMENTAL DAMAGE, PERSONAL INJURY OR DEATH.
FCC Compliance Statement
This device complies with part 15 of the FCC Rules. Operation is subject to the following two conditions:
(1) This device may not cause harmful interference, and (2) this device must accept any interference
received, including interference that may cause undesired operation.
FCC Caution: Any changes or modifications not expressly approved by the party responsible for
compliance could void the user’s authority to operate this equipment.
COPYRIGHT NOTICE
Copyright © 2021 by Quest Controls, Inc. (Quest). The material discussed in this publication is the
proprietary property of Quest. Quest retains all rights to reproduction and distribution of this
publication
Specifications are subject to change without notice.

Rev 2.1 10/21/21
Revision History
Date
Rev #
Modifications
By:
10/21/21
2.1
Changed MP2x images
K. Nickel
10/18/21
2.0
Updated Modbus register map and added sections 5 & 6
K. Nickel
1/27/21
1.0
Initial release
K. Nickel

Rev 2.1 10/21/21
Table of Contents
1 Overview...............................................................................................................................................1
1.1 Getting Started..............................................................................................................................1
2 Product Specifications...........................................................................................................................2
3 Installation ............................................................................................................................................3
3.1 Mounting the MP2x ......................................................................................................................3
3.2 Powering and Grounding ..............................................................................................................3
3.3 Wiring inputs.................................................................................................................................4
3.4 Wiring for Modbus........................................................................................................................6
3.5 Line Termination...........................................................................................................................7
3.6 Line Polarization............................................................................................................................7
3.7 Wiring Outputs..............................................................................................................................8
4 Local Operation.....................................................................................................................................8
4.1 Power LED .....................................................................................................................................8
4.2 Relay Outputs................................................................................................................................8
4.3 Restoring to Factory Defaults .......................................................................................................8
5 Configuring the MP2x ...........................................................................................................................9
5.1 Using the MP2 to Make Changes..................................................................................................9
6 Input Register Map .............................................................................................................................12
6.1 Thermistor Inputs........................................................................................................................12
6.2 Voltage and Current Transducers ...............................................................................................13
6.3 Digital Inputs...............................................................................................................................14
Appendix A –Modbus Register Table.........................................................................................................15
Appendix B –SD Card Update.....................................................................................................................26
Contact Information....................................................................................................................................27

Rev 2.1 10/21/21 - 1 - TELSEC©MP2X User Guide
1Overview
The TELSEC®MP2x is an expansion module that can be added to an MP2 to increase the number of
points available for monitoring and controlling a facility. Up to fifteen MP2x units can be connected to
an MP2 using an RS485 network. The MP2x is a Modbus device that can be queried for data from any
Modbus primary polling device using Modbus RTU protocol. The MP2x has 32 universal inputs for
monitoring temperature, humidity, contact closures and any 0-6 VDC or 0-20 mA sensors. Each
individual input may be scaled and displayed in the proper engineering units. Additionally, there are four
Form C outputs that can be used for controlling devices based on commands from the primary Modbus
device or remotely enabled by a user. This user guide is intended to provide basic operational
information for programming and status review of the MP2x System. Please contact Quest for
additional information and or questions about the operation of the system.
1.1 Getting Started
The TELSEC®MP2x is simple to setup and program which allows you to start monitoring your facility
quickly. The basic steps are listed below along with a chapter reference for this manual:
1. Mount the MP2x in the desired location (section 3.1)
2. Power the system. (Section 3.2.1)
3. Connect the inputs to be monitored to the system. (Section 3.3)
4. Connect the serial port to the MP2. (Section 3.4)
5. Wire the digital outputs. (Section 3.7)

Rev 2.1 10/21/21 - 2 - TELSEC©MP2X User Guide
2Product Specifications
Specifications
Part number: 151088-32
▪Inputs: 32 universal inputs supporting 0-5 VDC, 4-20 mA, thermistor & contact closure
▪Outputs: 4 form C digital outputs. Contact rating: 0.5 A @ 60 VDC
▪Serial interface: RS485 serial port
▪Serial Protocols Supported: Modbus RTU read and write
▪I/O terminal: removable screw terminals support up to 12 AWG wire
▪Power: dual feed 24-48 VDC, 3.7 W max.
▪Ambient operating temperature: 23° to 131°F (-5° to 55°C), 0-95% RH Non-condensing
▪Dimensions: 13.15 W x 4.15 L x 1.63 H in. (334 x 105 x 41 mm)
▪Weight: 1 lb. (454 g)
▪Warranty: 1 Year
Specifications subject to change without notice

Rev 2.1 10/21/21 - 3 - TELSEC©MP2X User Guide
3Installation
All local and national electrical safety codes (NESC®) must be followed when installing the MP2x. If
there is any contradiction in this manual and those standards, then the installer must follow the local
and national codes. Use copper conductors only. The TELSEC®MP2x is designed for mounting on a wall
or within a rack. Rack mounting is accomplished by using the optional (not included) mounting ears for
a 19 or 23” rack. Contact your Quest representative to order the Rack Mounting Ear kit (PN 150989).
3.1 Mounting the MP2x
Install the MP2x in the desired location using #8 hardware to connect the two mounting tabs to the wall.
For mounting in a 19” rack, use the optional mounting ears Quest p/n 150989.
12.6"
13.2"
4.2" 3.6"
Figure 1 - TELSEC®MP2x Dimensions
3.2 Powering and Grounding
3.2.1 Powering the MP2x
Follow all national and local electrical codes when powering the MP2x. Quest recommends a minimum
of 18AWG conductor for powering. The TELSEC®MP2x will operate from 18-65 VDC power (50 mA max
at 48 VDC). The power input is isolated from the rest of the system and will work on either a positive or
negative DC system. The MP2x supports power from a dual (A & B) feed DC power system to provide
redundancy in case one of the feeds is lost. Connect the power source A and B (optional) to the MP2x
observing the polarity markings on the enclosure. Quest recommends fusing each power source at 1 A.
Reverse polarity will not damage the unit, but it will not operate until corrected. It is recommended that
all input wiring be completed with no power to the system. Turn on power once all wiring is verified.
3.2.2 Grounding the MP2x
There is a ground post on the left and right side of the chassis. Place a ground wire using a minimum 12
AWG conductor from the Electrical panel ground bus (or other approved grounding point) to the ground
terminal on the MP2x. Follow national and local codes and practices for properly grounding the system.

Rev 2.1 10/21/21 - 4 - TELSEC©MP2X User Guide
3.3 Wiring inputs
Wire each input to be used between the input terminal (1-32) and a common terminal (C). There is a
common terminal available for every two inputs available for termination. The MP2x does not provide
power for sensor operation thus any device requiring power will need an external power source to
operate properly. Refer to the silkscreen on the enclosure for location of each input and common
terminal. The inputs will support any sensor that is a 10k Type III thermistor: 0-6 VDC or 0-20 mA analog
sensors. In addition, the system accepts dry contact closures or wet contact closures up to 65 VDC.
3.3.1 Thermistors
Thermistors are resistive devices and do not have polarity. Connect one lead to the input terminal of
the desired input and the second lead to a common terminal. Quest recommends using shielded and
stranded cable for all analog sensors. Connect the shield of the cable to chassis ground on the MP2x.
Cut the drain wire and isolate the shield at the sensor end of the cable.
Typical of all Quest thermistor
temperature sensors
Quest “Bullet Style” probe
Not polarity sensitive
Figure 2 - Thermistor Temperature Sensor Wiring
3.3.2 Voltage Sensors
The TELSEC®MP2x can read and scale any linear voltage input from 0 to 6 VDC. Sensors requiring power
must be externally powered. Contact Quest for the Input Scaling spread sheet to determine the correct
number for the Low and High Custom scale factors.

Rev 2.1 10/21/21 - 5 - TELSEC©MP2X User Guide
24 VDC
Power supply
+-
TEMP
RH
Sensor Power
Sensor Output
Common Ground
Reference
Figure 3 - Wiring Voltage Sensors
3.3.3 Current Sensors
The TELSEC®MP2x can read and scale any linear current input from 0 to 20 mA. An external 249-ohm
resistor (recommend 1% tolerance) is required to convert the signal to voltage and will require an
external voltage source to power the sensor. Contact Quest for the Input Scaling spread sheet to
determine the correct number for the Low and High Custom scale factors.
Sensor Power
Sensor Output
Common Ground
Reference
24 VDC
Power supply
+-
249 Ohm
Resistor
Figure 4 - Wiring a 4-20mA Sensor

Rev 2.1 10/21/21 - 6 - TELSEC©MP2X User Guide
3.3.4 Contact Closures
The TELSEC®MP2x supports dry contact closures or wet contacts up to 65 VDC. A wet contact is an input
where there is an external voltage present. A dry contact has no voltage present and the MP2x provides
the sensing voltage. The detection points for determining ON/OFF status are greater than 2.8 VDC and
less than 0.8 VDC. There is no transition when the voltage is between these two values. Both wet and
dry input types are connected between the input terminal and a common terminal. For Wet inputs the
voltage must be between 0VDC and up to +65VDC. Negative voltages are not supported.
Monitor Switch
Figure 5 - Wiring Contact Closures
3.4 Wiring for Modbus
The MP2x has a serial port labeled COM 1 which is used to connect this device to a Modbus primary
polling device. The MP2x will listen for request and respond with the data being requested.
1. Connect no more than 32 Modbus devices per Modbus serial port
2. The maximum overall Modbus cable network length is 3,000 feet.
3. For normal applications, use Belden Cable #8102 or equivalent. This cable has two twisted pairs
and a separate foil shield. For applications requiring a more mechanically robust cable, use
Belden Cable #9842. This cable has two twisted pairs, a separate shield and a separate braided
shield.
4. Use one of the twisted pairs for the D0 (-) and D1 (+) connections and use the second twisted
pair for the C/Common connections. The cable shields must never be used for the C/Common
connections.
5. All the D0 (-) pins from every Modbus device on the network must be connected together. The
same is true with the D1 (+) pins, and the C/Common pins.
6. Connect the Modbus devices together in a daisy-chain configuration only. In this configuration,
the cable from the first Modbus device connector goes directly to the connector of the second
Modbus device, then from that connector directly to the connector of the third Modbus devices,
and so on. No star, ring or tree cabling network configurations, or additional cable stubs are
allowed.
7. Connect all the cable shields together so that they form one continuous connection from one
end of the Modbus cable network to the other. If a braided shield is also included in the cable,
then connect all of them together as well. If there is a mix of braided and non-braided shields in
the cabling network, then connect the braided shields together and then to the foil shields of
the nearest non-braided cable. At no time are any shields to be left floating.

Rev 2.1 10/21/21 - 7 - TELSEC©MP2X User Guide
8. At the MP2, connect the cable shield to the protective (protected) earth ground. The cable
shields must not be connected to earth ground anywhere else in the cabling network except at
this point.
Ground Shield at MP2
ground post
Figure 6 - Modbus Wiring MP2 to MP2x
3.5 Line Termination
1. At each end of the Modbus cable network daisy-chain, there must be an end of line termination
resistor. Connect a 1/2W 120-ohm resistor across the D0 and D1 conductors of the end devices.
2. If the MP2x is at one end of the Modbus cable network, then use the built in End of Line resistor.
Remove the cover of the MP2x and locate DIP switch in the front right corner of the board. SW3
is for COM1. Press switch number 2 down (middle switch) to enable the end of line terminating
resistor. If the MP2x is not the last device on the Modbus cable network, then move switch 2 to
the up position. No more than two-line terminations are allowed per Modbus cable network.
3.6 Line Polarization
When there is no data activity on an RS-485 balanced pair, the lines are not driven and, thus susceptible
to external noise or interference. To ensure the receiver line stays in a constant state, when no data
signal is present, some devices need to bias the network. Polarization of the pair must be implemented
at one location for the entire Serial Bus. Generally this is at the primary device such as the MP2. Other
devices must not implement any polarization. Refer to the manual of the device you are monitoring to
determine if line biasing is required.
Line polarization should be accomplished (if needed) from the Primary polling device. Leave switches 1
& 3 in the up position on the MP2x. Refer to Figure 7.
Figure 7 - Modbus End of Line and Line Polarization Jumpers
COM 1

Rev 2.1 10/21/21 - 8 - TELSEC©MP2X User Guide
3.7 Wiring Outputs
There are four form C relays available for control of external devices based upon alarm conditions or
time schedules. Place wire between the common and normally open or normally closed terminals for
each output on the MP2x. The relays are designed for Class 2 wiring and are rated for a maximum of 1
amp at 24VAC or 30VDC, 0.3 A @ 60VDC.
Figure 8 - Wiring Outputs
4Local Operation
4.1 Power LED
Once the TELSEC®MP2x is installed and powered, the system will start operating. Under normal
operation the green Power LED will flash at one second intervals to indicate the system is operating
properly. Occasionally there may be a pause in this operation if the system is saving data to flash
memory. If the LED is off for longer than one minute, then check the power connection and cycle
power to the unit. If the LED is constantly on longer than a minute, then cycle power to the system to
see if it goes back to normal operation of flashing the LED.
4.2 Relay Outputs
The normally open/normally closed terminations on the unit refer to when the output is de-energized.
Outputs can be operated by sending Modbus RTU write commands to turn on/off the outputs. See the
register map in section for further details.
4.3 Restoring to Factory Defaults
The TELSEC®MP2x has a small access hole on the right side for the cold start switch. Holding this switch
in for approximately 15 seconds during a power up (cycle power off then back on) will cause the system
to erase all programmed settings and go back to the factory defaults. During the Cold Start process, you

Rev 2.1 10/21/21 - 9 - TELSEC©MP2X User Guide
will see both the power LED and Alarm LED flash simultaneously every second. After a few seconds, the
alarm (red)LED will be illuminated solidly. Release the cold start switch once the alarm LED is on solid.
5Configuring the MP2x
The MP2x is designed to work without any programming requirements. Though there are a few settings
that can be changed via Modbus RTU if needed. For example, the default address of the MP2x is 247. If
you want to change the address of the MP2x because you have multiple units then you would connect
the MP2x to a Modbus polling software such as “Modbus Poll” or use the MP2 to change the address.
The following registers can be changed to meet your application:
Control Registers
Function Code
Register
Description
Read/Write
Notes
Holding Register
(FC3/FC6)
(FC16) for write
multiple
0
Slave Address
R/W
1-247
Default 247
1
Baud Rate
R/W
Enumerated:
0 –300, (not supported)
1 –600, (not supported)
2 –1200,
3 –2400,
4 –4800,
5 –9600,
6 –19200,
7 –38400,
8 –57600,
9 –115200
Default 9600
2
Data Mode
R/W
Enumerated:
0 –8N1,
1 –8E1,
2 –8O1,
3 –8N2, (not supported)
4 –8E2,
5 –8O2
Default 8N1
3
Product ID
RO
1
4
Firmware
Revision
RO
convert to hex to get
Kernel version and
Filesystem versions. Initial
build 1542 (hex 0606)
5
Reset
WO
Must write 57005 to data
register for reset
5.1 Using the MP2 to Make Changes
As mentioned, the MP2 can be used to make changes to the default settings of the MP2x. Below is a
brief description of how to use the MP2. Please review the MP2 user manual for information on the
product.
1. Connect the MP2x to the MP2 at either Com 1 or Com 2 serial port.
2. Log into the MP2 web server and configure the unit to use Modbus. Go to
Settings/General/Serial Ports. Select the serial port you want to use on the MP2 and configure it

Rev 2.1 10/21/21 - 10 - TELSEC©MP2X User Guide
for Modbus, 9600 baud and 8-N-1 (these are the MP2 defaults). Press Save Settings and wait for
the system to restart.
3. Go to Program/Modbus (Port #) where # is the port number you just configured.
4. Create a new Device by clicking on the Add new device button. Enter the address of 247 and
give the device a name. Click on the Done button.
5. The new device will be added to the list. Click on the down arrow for the device and then the
Add new point button.
6. Enter a 4-character ID this is used for reference in the system. This value can be what every you
want. I.e. TMP1 for temporary 1 point. Enter a display name, function code will be 3- Holding
register, and then enter the register number and format (use Word). Press the Done button and
then Save Settings. Note the system will automatically save if you do not press the save button
within 120 seconds.

Rev 2.1 10/21/21 - 11 - TELSEC©MP2X User Guide
7. Repeat step 5 for any additional registers you want to change such as baud rate or data mode.
These settings typically don’t need to be changed unless you have other devices on the Modbus
485 network that need to operate at different settings. Note: all devices must have the same
baud rate and data mode setting but have a unique address.
8. Go to Status/Modbus Status (Port #) where # = the port number used. The system should be
displaying the created point with the current value of 247 (the default address).
9. Click on the write button and change the address to the desired value which will be stored in
non-volatile flash memory.

Rev 2.1 10/21/21 - 12 - TELSEC©MP2X User Guide
10. The MP2x will now respond at the new address.
If you have multiple MP2x units, you can repeat these steps turning them on (or connecting them to the
MP2) one at a time and change the address. After completion, you can remove address 247 from the
system if it is not going to be used.
6Input Register Map
The MP2x inputs are universal meaning they can support Thermistors (10K Type III), 0-6VDC or 0-20 mA
transducers, Dry Contact closures or Wet Contact closures. To eliminate program requirements on the
MP2x, we provided 10 different registers for each input. Select the appropriate register to poll based on
the type of sensor connected to the input. The complete register map can be found in Appendix A –
Modbus Register Table.
6.1 Thermistor Inputs
Connect a 10K type III thermistor to the desired input and then define the input in the MP2. Reference
the Modbus map for temperature sensors and select the desired reading. The example below shows
defining a Modbus point in the MP2 to look at input 10 on the MP2x and display the data in Celsius using
the floating-point register.

Rev 2.1 10/21/21 - 13 - TELSEC©MP2X User Guide
6.2 Voltage and Current Transducers
Connect the voltage or current transducer to the MP2x and then define the Modbus point in the MP2
using the Modbus register map for “Input values as counts from the adc output. See the notes section
where the number of counts vary based upon the type of transducer and load resistor (for mA sensors)
used. Example: defining a humidity sensor that reads 0-100% over 4-20mA output using a 249-ohm load
resistor. The register map shows to use a multiplier of 163 per mA when using a 249-ohm resistor. The
input reading would then be from 652 counts at 0%RH (4mA) and 3,260 counts at 100%RH (20mA). The
range would be 2608 counts (3,260-652) over 0-100% which would be a multiplier of 0.038
(100%RH/2608 counts). The last step would be to add an offset since the range starts at 4mA instead of
0mA. The MP2 applies the offset after the multiplier so the offset would be in the desired engineering
units of %RH which in this case would be -25. The definition using input 20 on the MP2x would be as
follows:

Rev 2.1 10/21/21 - 14 - TELSEC©MP2X User Guide
6.3 Digital Inputs
Inputs on the MP2x that are digital inputs whether they are dry contact closures or wet can be
connected to the unit and then defined for polling in the MP2x. Digital inputs can be either dry normally
open, dry normally closed, wet normally open or wet normally closed. Wet contacts mean there is an
external voltage being used. This voltage can be 0-60VDC. Refer to the register map and select the
appropriate register based on the type of input being monitored. For example, if you connect a dry
normally closed contact to input 15 of the MP2x and want it to show a 1 (ON) when open and a 0 (OFF)
when closed then define the Modbus point as follows:

Rev 2.1 10/21/21 - 15 - TELSEC©MP2X User Guide
Appendix A –Modbus Register Table
Analog Input Table
To read the raw output of the A to D converter in Thermistor Mode
Function Code
Register
Description
Read/Write
Notes
Input Register (FC4)
0
Input 1 Raw Thermistor
RO
raw counts 0-4095
Thermistor mode
1
Input 2 Raw Thermistor
2
Input 3 Raw Thermistor
3
Input 4 Raw Thermistor
4
Input 5 Raw Thermistor
5
Input 6 Raw Thermistor
6
Input 7 Raw Thermistor
7
Input 8 Raw Thermistor
8
Input 9 Raw Thermistor
9
Input 10 Raw Thermistor
10
Input 11 Raw Thermistor
11
Input 12 Raw Thermistor
12
Input 13 Raw Thermistor
13
Input 14 Raw Thermistor
14
Input 15 Raw Thermistor
15
Input 16 Raw Thermistor
16
Input 17 Raw Thermistor
17
Input 18 Raw Thermistor
18
Input 19 Raw Thermistor
19
Input 20 Raw Thermistor
20
Input 21 Raw Thermistor
21
Input 22 Raw Thermistor
22
Input 23 Raw Thermistor
23
Input 24 Raw Thermistor
24
Input 25 Raw Thermistor
25
Input 26 Raw Thermistor
26
Input 27 Raw Thermistor
27
Input 28 Raw Thermistor
28
Input 29 Raw Thermistor
29
Input 30 Raw Thermistor
30
Input 31 Raw Thermistor
31
Input 32 Raw Thermistor

Rev 2.1 10/21/21 - 16 - TELSEC©MP2X User Guide
To read the inputs in Fahrenheit as an integer
Function Code
Register
Description
Read/Write
Notes
Input Register (FC4)
32
Input 1 tempF
RO
Rounded to nearest integer
33
Input 2 tempF
34
Input 3 tempF
35
Input 4 tempF
36
Input 5 tempF
37
Input 6 tempF
38
Input 7 tempF
39
Input 8 tempF
40
Input 9 tempF
41
Input 10 tempF
42
Input 11 tempF
43
Input 12 tempF
44
Input 13 tempF
45
Input 14 tempF
46
Input 15 tempF
47
Input 16 tempF
48
Input 17 tempF
49
Input 18 tempF
50
Input 19 tempF
51
Input 20 tempF
52
Input 21 tempF
53
Input 22 tempF
54
Input 23 tempF
55
Input 24 tempF
56
Input 25 tempF
57
Input 26 tempF
58
Input 27 tempF
59
Input 28 tempF
60
Input 29 tempF
61
Input 30 tempF
62
Input 31 tempF
63
Input 32 tempF
Table of contents
Popular Control Unit manuals by other brands
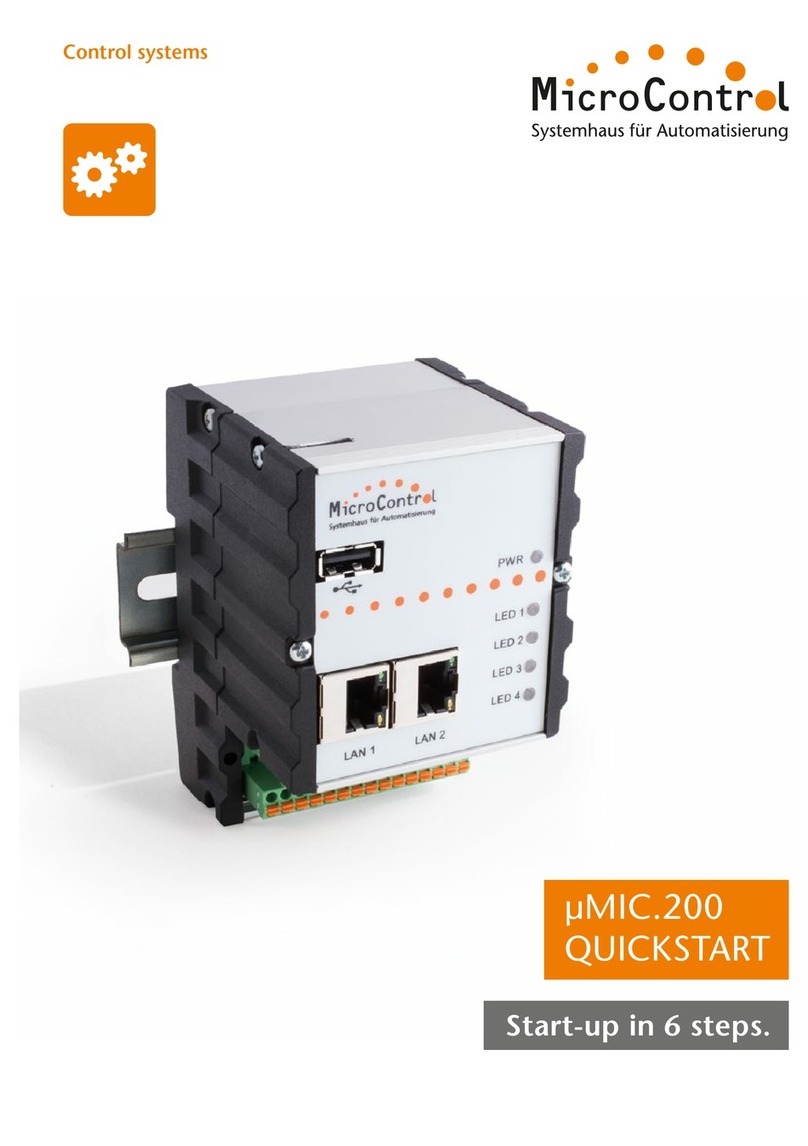
MicroControl
MicroControl uMIC.200 quick start
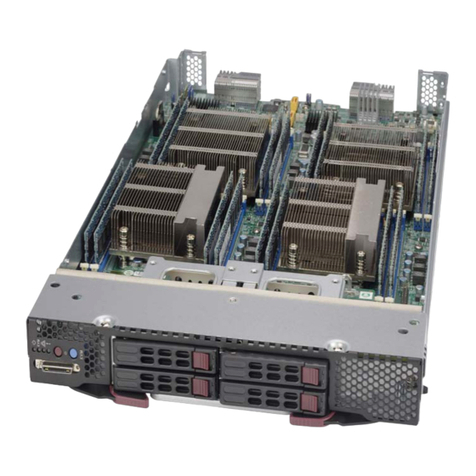
Supermicro
Supermicro SBI-7147R-S4F user manual
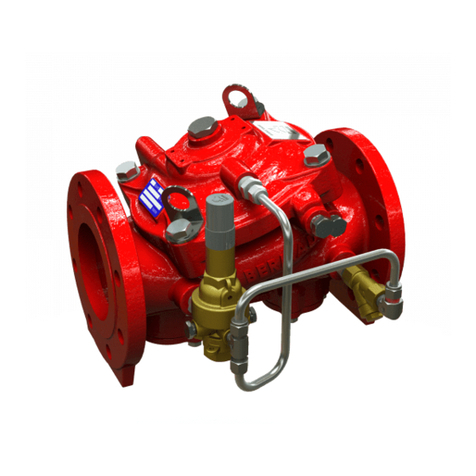
Victaulic
Victaulic 867-42T Installation, operation and maintenance manual
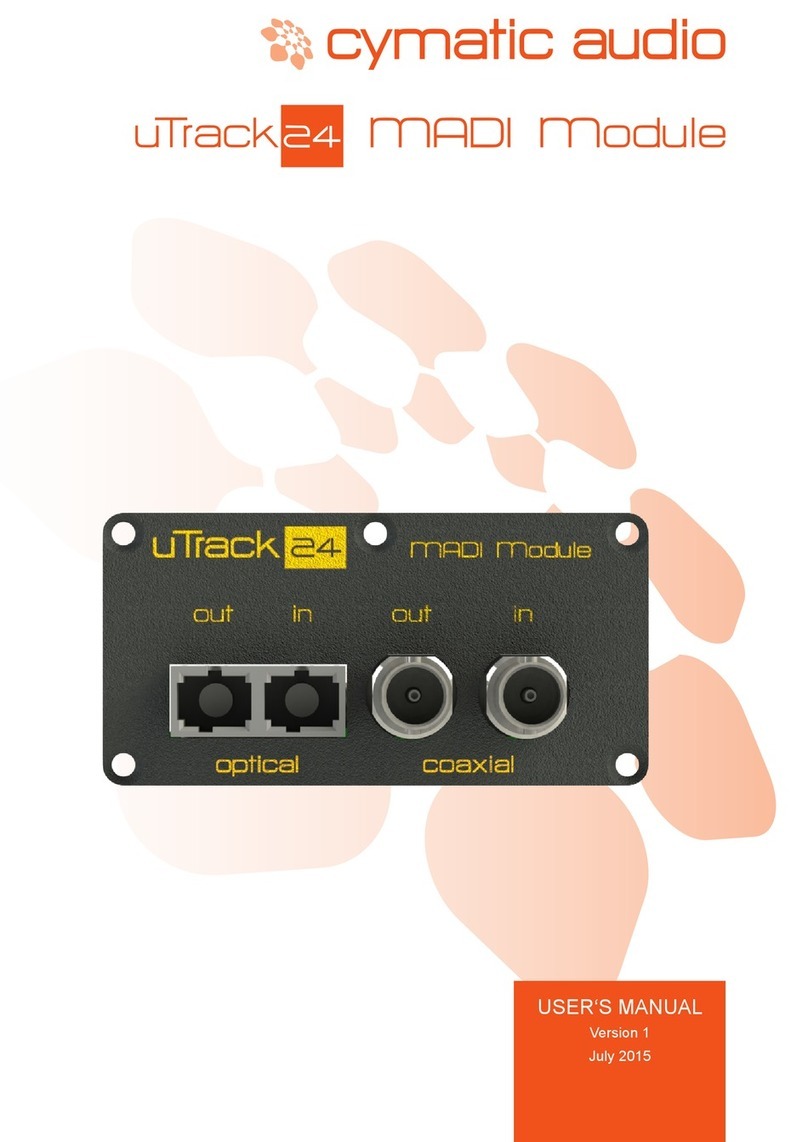
cymatic audio
cymatic audio uTrack 24 user manual

claber
claber Aqua Wireless 8321 manual
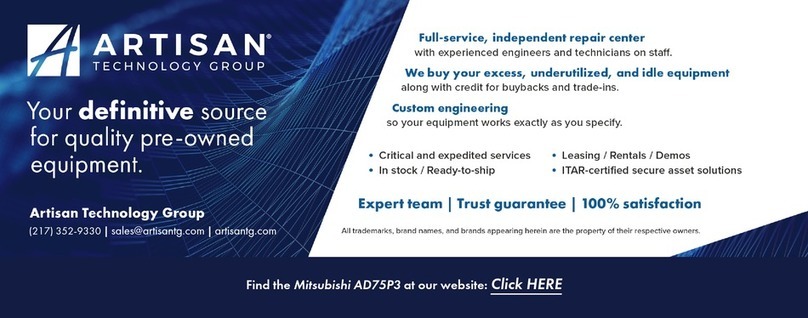
Mitsubishi Electric
Mitsubishi Electric A1SD75P1-S3 user manual