QUICK-ROTAN MINI-STOP Q41MSII User manual

Instruction Manual
Part 2
Type
QUICK-ROTAN Elektromotoren GmbH
Königstraße 154
67655 Kaiserslautern
Tel: 0631 / 200 38 80
Fax: 0631 / 200 38 62
E-Mail: [email protected]
www.quick-rotan.com
Englisch 2002-02-21
Q41MSII
QE3760
MINI-STOP

Q-41-MSII-2-EN 02-02-21
Technical updatings reserved!
Contents Page
Part 2
7. Description of the MINI-STOP Drive System 7.1 - 7.6
7.1 Motor QE 3760
7.2 Control system
7.3 Speed control unit SWG2
7.4 External operator panel OC-TOP
7.4.1 External operator panel OC-TOP/AQ
7.4.2 External operator panel OC-TOP/FQ
7.5 Drive System Application
8. Application 8.1 - 8.12
8.1 Sewing without an external operator's control panel
8.2 Sewing with external operator's control panel OC-TOP
8.2.1 Sewing without sewing program (manual sewing)
8.2.2 Sewing with sewing program (programmed sewing)
8.2.3 Sewing programs
8.2.4 Backtack / Darning programs
8.3 Error messages (Malfunction Diagnostics)
9. Programming by the user 9.1 - 9.14
9.1 User programming with operator panel OC-TOP
9.1.1 Direct programming
9.1.2 Parameter programming
9.1.2.1 Programming level A (operator level)
9.1.2.2 Programming level B (technician level)
9.1.2.3 Programming level C (special level)
9.1.3 Reset
9.2 User programming via the Internal Mini Programming Panel (MPF)
9.2.1 Indication 1: Backtack Stitches
9.2.2 Indication 2: Speed
9.2.3 Indication 3: Sewing functions
9.2.4 Indication 4: Control Paramerters
9.2.5 Reset
10. Start of operation 10.1 - 10.4
10.1 Control of the direction of rotation and of the reference position
from the needle bar (needle position NPO)
10.2 Control of the needle positions NP1 / NP2 / NP3 / NP9
10.3 Control of the needle positions for thread trimming (Parameters 704, 705, 706)
10.4 Control of the maximum speed
10.5 Hardware test

Q-41-MSII-2-EN 7.1 02-02-21
7. Description of the MINI-STOP Drive System
The MINI-STOP Drive System is an electronically commutated, brushless DC motor.
The system is composed of the following subassemblies
Fig.7.1
Fig.7.2
Fig.7.3
Fig.7.4
Motor QE3760 (Fig.7.1) with integrated optoelectronic incremental encoder for commutation and
positioning.
Control (Fig.7.2) with
- integrated mains switch
- mains connection with interference rejection circuit
- electronically controlled combinational circuit
- intermediate DC circuit
- motor-driven current inverter
- electronic control for motor control and machine specific functions
Speed control unit SWG2 (Fig.7.3)
Control panel OC-TOP (Fig.7.4 - optional)
7.1 Motor QE3760
The motor is a synchronous motor. It has a permanent-magnetic rotor, a stator with three-phase winding
and an optoelectronic increment encoder for commutation and positioning.
The rated capacity of the motor (shaft capacity) is 370 W in S5 mode. The rated speed of the motor is
6000 rpm, the maximum speed is 9000 rpm.
The motor has two mains leads:
a) four-wire with special quadripolar AMP plug (X1) for connecting the stator coil to the control
system
b) six-wire shielded with nine-pole D-sub plug (X2) for connecting the increment encoder to the
control system.

Q-41-MSII-2-EN 7.2 02-02-21
7.2 Control system
Fig. 7.5 Fig 7.6
The control box is attached to the underside of the machine table by means of the four enclosed screws.
The mains connection is single-phase, using the three-wire cord protruding from the rear and a standard
safety plug.
The control system has peripheral functions
on the front panel (Fig. 7.5):
1 mains switch S1
the Mini control panel (MPF)
contents: an LCD Display with 8 places
and 6 small keys: M+ / M-
C>> / C<<
V+ / V-
on the rear panel (Fig. 7.6):
sockets or connector plugs
X1 quadripole socket for connecting the motor’s stator coil
X2 nine-pole D-sub jack for connecting the motor’s increment encoder
X3 nine-pole D-sub plug for connecting set point adjuster SWG2 (Art. No. 63.012)
X4 nine-pole D-sub plug for connecting the control panel OC-TOP/AP (Art. No. 64.175)
X5 37-pole D-sub jack for connecting the process control system (keys, switches, solenoids,
solenoid valves) on the machine.
S1

Q-41-MSII-2-EN 7.3 02-02-21
The control system is connected with the sewing machine/ sewing equipment via:
inputs (Ex), such as for keys, switches, proximity switches, monitors, and
outputs (Ax),such as for solenoids, solenoid valves, signal indicators.
Function of the inputs (Ex) and the outputs (Ax) in dependence on <799>
E/A Funktion
<799> = 1 <799> = 2 <799> = 3
E1: Chopper Fast scissors -
E4: Program-switch
over
E6: Light barriere Light barriere Light barriere
E13: Flip-Flop Fast scissors
A1: Chopper Fast scissors
forwards
A2: Flip-Flop Chaining-off finger
A3: Chain blowing Chain blowing Chain blowing
A4: Presser foot lift Presser foot lift Presser foot lift
A5: Chain vacuuming Chain vacuuming Chain vacuuming
A6: Thread tension Thread tension Thread tension
release release on
A7: Signal lamp
A8: Motor runs Motor runs Motor runs
A10: Fast scissors
backwards
A16: Count signal Count signal Count signal

7.3 Speed control unit SWG2
The SWG2 is attached to the underside of the machine table with the enclosed brackets and connected
mechanically to the machine’s pedal by means of the enclosed rod assembly.
The mains connection of the SWG2 is by means of a nine-pole connector on plug X3 on the rear
control panel.
The SWG2 is an analogous mechanoelectronic converter, which converts the pedal path into analog
voltage. This analog output voltage of the SWG2 is digitized in the control system so that the pedal path
can be divided into 16 steps (positions).
Level Position Voltage [V] Meaning
0 -2 (full backwards) 0,00 - 0,50 Seam end, thread trimming
1 -1 (a little backwards) 0,50 - 0,94 Presserfoot up
2 0 (neutral position) 0,94 - 1,76 Treadle position 0
3 +1 1,76 - 2,21 Presserfoot down
4 +1 D 2,21 - 2,43 Speed n1
5 +2 D 2,43 - 2,66 Speed n2
6 +3 D 2,66 - 2,90 Speed n3
7 +4 D 2,90 - 3,13 Speed n4
8 +5 D 3,13 - 3,37 Speed n5
9 +6 D 3,37 - 3,60 Speed n6
10 +7 D 3,60 - 3,84 Speed n7
11 +8 D 3,84 - 4,07 Speed n8
12 +9 D 4,07 - 4,31 Speed n9
13 +10 D 4,31 - 4,54 Speed n10
14 +11 D 4,54 - 4,78 Speed n11
15 +12 D 4,78 - 5,00 Speed n12
Pin connection of speed control plug (X3) of the SWG2
0 … 5V control voltage (set point, rated value)
Q-41-MSII-2-EN 7.4 02-02-21
+5V
0V
1
2
3
4
5
6
7
8
9

Q-41-MSII-2-EN 7.5 02-02-21
7.4 External Operator Panel OC-TOP / DQ
Fig. 7.2
The operator panel OC-TOP / DQ (Fig. 7.2) has the following components:
-a display: 16-digit LCD matrix
-14 programming keys:
A+ / A-, B+ / B-, C+ / C-, D+ / D-, P+ / P-, S+ / S-, L+ / L-
-two keys (T9, T10) for selection of the operating mode
-13 keys (T1…T8, T11…T15) for machine functions
-one connector for a light sensor at rear for connection of one or two (with adapter) light sensors
Function of the programming keys in operating mode “manual sewing”
(key T9 is dark key T10 is dark)
-A+/A-/B+/B- adjustment of stitchcount S1 at seam start (vacuum)
-C+/C-/D+/D- adjustment of stitchcount S2 at seam end (vacuum)
Function of the programming keys in operating mode ”programmed sewing”
(key T9 is bright, key T10 is dark)
-A+/A- adjustment of speed nx in program x
-A+/A-/B+/B- adjustment of stitchcount S1 at seam start (chopper)
-C+/C-/D+/D- adjustment of stitchcount S2 at seam end (chopper)
-D+/D- preselection of the program following program x
-P+/P- adjustment of program x (program number x = 01 ... 05)
-S+/S- adjustment of seam section 01 in program x NS = 01 ... 05
-L+/L- adjustment of the cycle counter for stacker activation, if NS = 00
-L+/L- adjustment of stitchcount of the activated NS (01 ... 05)
F8
T6 T7 T9 T10
T1 T2 T4T3 T5
T8 T11 T12 T13 T14 T15
10 0 1/0010

Q-41-MSII-2-EN 7.6 02-02-21
Function of the programming keys in operating mode ”parameter programming”
(key T9 is dark, key T10 is bright)
-P+/P- switch over of the hundreds of the parameter numbers
-S+/S- switch over of the parameter number in the switched on hundred section
-L+/L- programming of the parameter value of the switched on parameter number
Function of the keys T9 and T10 for selection of the operating mode
-T9 dark, T10 dark: manual sewing
-T9 bright, T10 dark: programmed sewing
-T9 dark, T10 bright: parameter programming
Function of the programming keys for machine functions
-T5 function change-over for keys T1 … T4 (shift key)
-T1 chain close-off (<425> = I)
-T5+T1 automatic change-over between program 1 and program 2 (see Item 8.2.2)
-T2 speed during programmed sewing:
variable (treadle-controlled) when T2 is dark or
constant (automatic) when T2 is bright
-T5+T2 no function
-T3 blow chain at seam end
-T5+T3 light barrier start
-T4 no function
-T5+T4 piece counter on display
-T6 vacuum at start of seam
-T7 vacuum at end of seam
-T8 currently no function
-T11 chopper at start of seam
-T12 chopper at end of seam
-T13 presser foot position at sewing stop
-T14 presser foot position at end of seam
-T15 light barrier
Caution: After programming push key T5 till LED goes out
The keys T1...T15 are provided with one signal lamp each (LED). Each LED provides optical feedback
on the control position of the function assigned to each key. If the function is ON, the LED is bright; if
the function is OFF, the LED is dark.

Q-41-MSII-2-EN 8.1 02-02-21
8. Application
The MINI-TOP Type Q41MS is specially designed for overlock machines and is mainly conceived for
light-barrier control.
The connection of the light-barrier is possible either via the the external operators control panel OC-TOP
or directly at the socket X5 at the control box (Input E6).
The drive system includes three different functional sequences.
Selection of the functional sequences is made via parameter <799>.
Sewing work can be manual or programmed. Programmed sewing is only possible in conjunction with
the external oparator panel QC-TOP/DQ
Extent and contents of sewing programs
a) Number of sewing programs: 5
b) To each sewing program can be assigned the following functions
function: adjustment via:
rated stitchcount S1.x via keys A+/A-/B+/B-
rated stitchcount S2.x via keys C+/C-/D+/D-
rated stitchcount S3.x via keys L+/L-
chain vacuuming at start via key T6
chain vacuuming at end via key T7
chopper at start via key T11
chopper at end via key T12
presser foot position at sewing stop via key T13
presser foot position at program end via key T14
light-barrier via key T15
c) Sewing speed (rated speed) for seam sections S1.x and S2.x can be selected via keys A+/A-.
d) Sewing speed can be changed over between constant (automatic) and variable (treadle-controlled)
via key T2.
e) There is the possibility of running various sewing programs consecutively. During programming, the
subsequent sewing program is shown in digits 6 and 7 of the display and is entered via keys D+ or
D-.
00 means that only the current program is run. At the end of the program concerned, return is made
to its beginning.
Display showing
- before or after start, when <605> = II,
Setting the rated stitchcount S1 and S2 is posssible only with the machine stopped.
S1 via keys A+/A-/B+/B-
S2 via keys C+/C-/D+/D-
Sewing program (x), being activated
when T9 (P/M) is pressed (bright)
Rated stitchcount (S1) to
vacuuming OFF at start
Rated stitchcount (S2) to
vacuuming OFF at end
1 0 1 0 xx/00

Q-41-MSII-2-EN 8.2 02-02-21
Display showing
- after start, when <605> = I,
Meaning of the rated stitches S1 and S2
S1 rated stitches at the seam beginning:
- chopper if <799> = 1
- fast scissors or
chain vacuum, if <799> = 2
- thread tension on, if <799> = 3
S2 rated stitches at the seam end:
- chopper if <799> = 1
- fast scissors or
chain vacuum, if <799> = 2
- thread tension off, if <799> = 3
Actual speed
Symbol for actual
speed
4 1604xx/00

8.1 Sewing without Sewing Program (manual Sewing)
8.1.1 Functional sequence 1 (<799> = 1) with stop after seam end (<603> = I)
Functions: chop at start
chop at end
chain vacuuming at start
chain vacuuming at end
thread tension release at start and at end
Switch condition of the keys at the OC-TOP:
Key T9 (P/M) off (dark)
Key T10 (T/E) off (dark)
Key T6 on (bright)
Key T7 on (bright)
Key T11 on (bright)
Key T12 on (bright)
Key T15 on (bright)
Fig. 8.1a
max
bright
dark
0
0
1
0
- 2
+12
1
0
1
0
Pedal
LS
n
(AB)
S 1
<540>
<537>
<541> <545>
<543>
(CD)
S 2
<537>
*
A1Outp.
*
A5Outp.
*
see electrical connections dia
g
ram pa
g
e 12.2
*
A6Outp.
1
0
ML
Motor runs
Thred tension releas
e
Chain vacuum
Chopper
*
Outp. A8
HACK
KESAU
FSL
<542>
<105>
<112>
<110>
<112>
Light-barrier
Q-41-MSII-2-EN 8.3 02-02-21

Q-41-MSII-2-EN 8.4 02-02-21
8.1.2 Functional sequence 1 (<799> = 1) without stop after seam end (<603> = II)
Functions: chop at start
chop at end
chain vacuuming at start
chain vacuuming at end
thread tension release at start and at end
Switch condition of the keys at the OC-TOP:
Key T9 (P/M) off (dark)
Key T10 (T/E) off (dark)
Key T6 on (bright)
Key T7 on (bright)
Key T11 on (bright)
Key T12 on (bright)
Key T15 on (bright)
Fig. 8.1b
max
0
0
1
0
- 2
+12
1
0
1
0
n
(AB)
S 1
<537>
<541> <541>
<543>
(CD)
S 2
< 537>
1
0
ML
HACK
KESAU
FSL
<542>
<105>
<112>
<110>
<112>
<540><540>
(AB)
S 1
bright
dark
Pedal
*
A1Outp.
*
A5Outp.
*
see electrical connections diagram page 12.2
*
A6Outp.
Motor runs
Thread tension release
Chain vacuum
Chopper
*
Outp. A8
Light-barrier
LS

8.1.3 Functional sequence 2 (<799> = 2) with stop after seam end (<603> = I)
Functions: fast scissors at start
fast scissors at end
chain vacuuming at start
chain vacuuming at end
thread tension release at start and at end
Switch condition of the keys at the OC-TOP:
Key T9 (P/M) off (dark)
Key T10 (T/E) off (dark)
Key T6 on (bright)
Key T7 on (bright)
Key T11 on (bright)
Key T12 on (bright)
Key T15 on (bright)
Q-41-MSII-2-EN 8.5 02-02-21
Fig. 8.2a
max
bright
dark
0
0
1
1
0
0
- 2
12 D
Pedal
LS
n
(CD)
S 2
<105> <110>
1
0
(AB)
S 1
ML
KESAU
FSL
Motor runs
<540> <542>
*
Outp. A8
*
. A5Outp
*
. A6Outp
1
1
0
0
*
. A1Outp
*
. A10Outp
Fast scissors forward
Fast scissors backward
SSVW
SSRW
<112> <112>
<545>
*
see electrical connections dia
g
ram pa
g
e 12.2
Thread tension release
Chain vacuum

8.1.4 Functional sequence 2 (<799> = 2) without stop after seam end (<603> = II)
Functions: fast scissors at start
fast scissors at end
chain vacuuming at start
chain vacuuming at end
thread tension release at start and at end
Switch condition of the keys at the OC-TOP:
Key T9 (P/M) off (dark)
Key T10 (T/E) off (dark)
Key T6 on (bright)
Key T7 on (bright)
Key T11 on (bright)
Key T12 on (bright)
Key T15 on (bright)
Q-41-MSII-2-EN 8.6 02-02-21
max
bright
dark
0
0
1
1
0
0
- 2
12 D
Pedal
LS
n
(CD)
S 2
<105> <110>
1
0
(AB)
S 1
<105>
(AB)
S 1
ML
KESAU
FSL
<540> <542> <540>
*
Outp. A8
*
. A5Outp
*
. A6Outp
1
1
0
0
*
. A1Outp
*
. A10Outp
SSVW
SSRW
<112> <112> <112>
Motor runs
Fast scissors forward
Fast scissors backwar
d
Thread tension release
Chain vacuum
*
see electrical connections dia
g
ram pa
g
e 12.2
Fig. 8.2b

8.1.5 Functional sequence 3 (<799> = 3) with stop after seam end (<603> = I)
For Pegasus EX(T) 5214 ... BT250 with stitch lock at the beginning
Functions: chain vacuuming at start
chain vacuuming at end
thread tension on between start and end
chain-off finger between start and end
Switch condition of the keys at the OC-TOP:
Key T9 (P/M) off (dark)
Key T10 (T/E) off (dark)
Key T6 on (bright)
Key T7 on (bright)
Key T15 on (bright)
Q-41-MSII-2-EN 8.7 02-02-21
Fig. 8.3a
max
bright
dark
0
0
1
1
0
0
- 2
12 D
Pedal.
LS
n
1
0Motor runs
Chain vacuum
Thread tension
*
Outp. A8
*
. A5Outp
*
. A6Outp
1
*
. A2Outp Chain-off finger
0
*
see electrical connections diagram page 12.2
(CD)
S 2
<105> <110>
(AB)
S 1
ML
KESAU
FSP (<766>)
<541>
<112> <112>
<543>
KEFI (<766>)
<216> <215>
<545>

8.1.6 Functional sequence 3 (<799> = 3) without stop after seam end (<603> = II)
For Pegasus EX(T) 5214 ... BT250 with stitch lock at the beginning
Functions: chain vacuuming at start
chain vacuuming at end
thread tension on between start and end
chain-off finger between start and end
Switch condition of the keys at the OC-TOP:
Key T9 (P/M) off (dark)
Key T10 (T/E) off (dark)
Key T6 on (bright)
Key T7 on (bright)
Key T15 on (bright)
Q-41-MSII-2-EN 8.8 02-02-21
Fig. 8.3b
max
hell
Dark
0
0
1
1
0
0
- 2
12 D
Pedal
LS
n
1
0
*
Outp. A8
*
. A5Outp
*
. A6Outp
1
*
. A2Outp
0
<216>
*
see electrical connections dia
g
ram pa
g
e 12.2
Motor runs
Chain vacuum
Thread tension
Chain-off finge
r
(CD)
S 2
<105> <110>
(AB)
S 1
<105>
ML
KESAU
FSP (<766>)
<541>
<112> <112> <112>
<543> <541>
KEFI (<766>)
<216> <215>
(AB)
S 1

8.2 Sewing with Program - Functional Sequence 1 (<799> = 1)
Switch Condition of the keys at the OC-TOP: key T9 (P/M) ON (bright)
key T10 (T/E) OFF (not bright)
key T6 ON (bright)
8.2.1 Sewing with Trimming (Chopping) Twice key T7 ON (bright)
key T11 ON (bright)
key T12 ON (bright)
key T15 ON (bright)
Fig. 8.4
Meaning:
S1.x Stitchcount 1 (from light barrier dark to chopper ON at start) within the running program x
(x = 01…25), programmable via keys A+, A-, B+, B-
S2.x Stitchcount 2 (from light barrier to chopper ON at end) within the running program x
(x = 01…25), programmable via keys C+, C-, D+, D-
S3.x Stitchcount 3 (from light barrier bright to thread tension release ON at end) within the
running program x ( x = 01…25)
Condition for thread tension release at end: S3.x ≤S2.x
Display showing before start, when a seam section isn't switched on
Seam section within sewing program
(00 = before start)
Rated speed for start and end
section (S1.x and S2.x)
Number of sewing program
Number of subsequent
sewing program
Number of program sequences until stacker ON
1500 00 xx/00 1
max
bright
dark
0
0
1
0
- 2
+12
1
0
1
0
Pedal
LS
n
(AB)
S1.x
(L)
S3.x
<537>
<541> <545>
<543>
(CD)
S2.x
< 537>
*
. A1Outp
*
. A5Outp
*
. A6Outp
1
0
ML
Motor runs
Thread tension releas
e
Chain vacuum
Chopper
*
Outp. A8
HACK
KESAU
FSL
<540>
*
see electrical connections diagram page 12.2
Light-barrier
Q-41-MSII-2-EN 8.9 02-02-21

Q-41-MSII-2-EN 8.10 02-02-21
In this display, the following can be modified:
- the program (NP): by actuating keys P+ or P-
- the seam section (NS): by actuating keys S+ or S-
- the cycles: by actuating keys L+ or L-, when no seam section is activated
- the subsequent sewing program via key D+ or D-
- the rated speed of the program: by actuating keys A+ or A-.
This speed is limited via parameter <607>.
Display showing before start when a seam section is activated
In this display, the following can be modified:
- the rated stitchcount S1.x via keys A+/A-/B+/B-
- the rated stitchcount S2.x via keys C+/C-/D+/D-
- the rated stitchcount S3.x via keys L+/L-
- the sewing program (NP) via keys P+/P-
- the seam section (NS) via keys S+/S-
Display showing after start, when <605> = II
Display showing after start, when <605> = I
1 0 1 0 01/01 1 2
<
(
(
<
(
(
<
(
(
<
(
(
<
(
(
S1 S2 S3NSNP
Actual speed
Symbol for actual
speed
358040 1/0 1 1 2
Number of the sewing program (NP)
Rated stitchcount S3.x
Rated stitchcount S2.x
1 0 1 0 xx/01 12
Rated stitchcount S1.x
Seam section (NS)

Q-41-MSII-2-EN 8.11 02-02-21
8.2.2 Sewing with Trimming (Chopping) Four Times
Fig. 8.5
The sequence as per Fig. 8.5 is basically the same as that in Fig. 8.4, except for two differently
programmed sections being sewn consecutively.
Section 1 is sewn with program 01 (NP1) and
section 2 with program 02 (NP2).
Interlinking the two programs is made by entering the program number of the subsequent program before
the program number of the running programming:
Display showing for program 01 (NP1) before start
Display showing for program 02 (NP2) before start
Program 01 involves programming of stitchcounts S1.1, S2.1 and S3.1
Program 02 involves programming of stitchcounts S1.2, S2.2 and S3.2
Sewing of the second section can be optically indicated. This requires connection of an indicator light to
output A7 and <563> = I .
1500 02 01 /00 1
1500 0 1 02/00 1
(AB)
S 1.2
<537>
<541> <545>
<543>
(CD)
S 2.2
<537>
(L)
S3.2
max
bright
dark
0
0
1
0
- 2
+12
1
0
1
0
Pedal
LS
n
*
. A1Outp
(AB)
S 1.1
*
. A5Outp
*
. A7Outp
*
. A6Outp
<540> <540>
<537>
<541> <545>
<543>
(CD)
S 2.1
<537>
(L)
S3.1
1
0
0ML
*
Outp. A8
NP2NP1
FSL
HACK
KESAU
*
see electrical connections diagram page 12.2
Motor runs
Thread tension releas
e
Chain vacuum
Chopper
Light-barrier

Q-41-MSII-2-EN 8.12 02-02-21
8.3 Error Messages (Malfunction Diagnostics)
The control system of the drive cyclically tests its own functional condition and the functional condition of
the complete drive system.
Malfunctions are signalled via the display of the external operator panel, for instance:
List of possible error codes:
11
11
1Treadle not in zero position when mains power is turned ON
99
99
9Start lock
1010
1010
10 Machine class, <799> was changed; remedy: turn mains power switch OFF and ON
again
6262
6262
62 Short circuit on 24 V (32 V) DC
6363
6363
63 Overload on 24 V (32 V) DC, load current > 4 amps
6464
6464
64 Power supply monitor: voltage too low (90 V - 150 V)
6565
6565
65 Power electronics not operational after mains power ON, mains power < 130 V
6666
6666
66 Earth short (motor or motor supply line has earth short in one or more phases)
6767
6767
67 Internal malfunction
6868
6868
68 Power electronics shut-off
a) Overcurrent, short circuit in motor or supply line
b) Overvoltage, mains voltage too high (>300 V), motor overloaded while decelerating
c) Undervoltage
7070
7070
70 Machine blocked, no increment from synchronizer at max. motor torque
7171
7171
71 Commutation transmitter plug not inserted
7373
7373
73 Motor overloaded
7575
7575
75 Internal malfunction
9090
9090
90 EEPROM does not exist
9191
9191
91 EEPROM not programmable
9292
9292
92 Start lock while motor running
9393
9393
93 Wrong EEPROM
100100
100100
100-
Internal malfunction
117117
117117
117
In case of error messages ≥≥
≥≥
≥ 62, the motor will stop in undefined positions.
Control system reset possible only by mains power OFF/ON.
ERROR 7 1
Table of contents
Popular Engine manuals by other brands
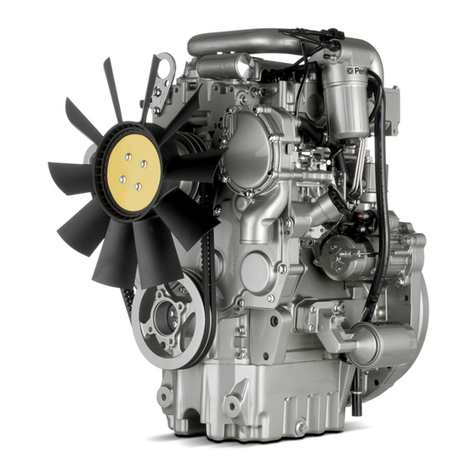
Perkins
Perkins 1103 Workshop manual

Shindaiwa
Shindaiwa DGW300MS/UKV Owner's and operator's manual
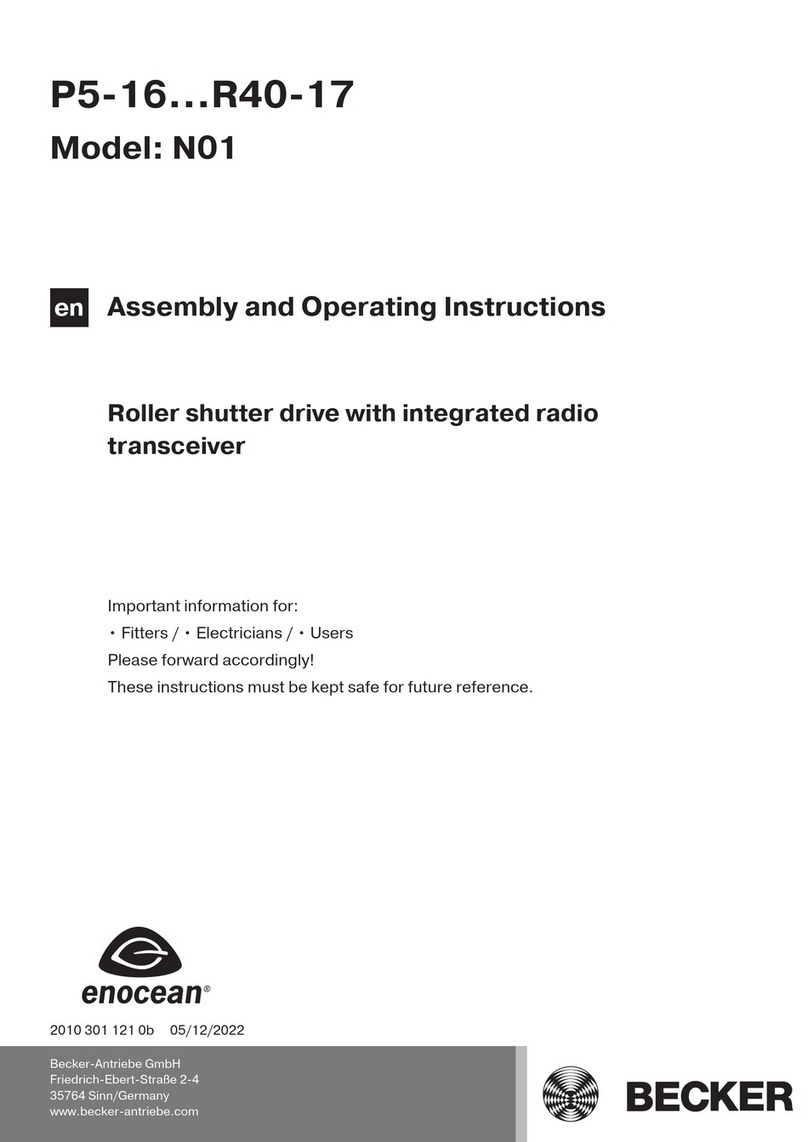
Becker
Becker P5-16-N01 Assembly and operating instructions

woodmizer
woodmizer LT28 G19 Safety, Operation, Maintenance & Parts Manual
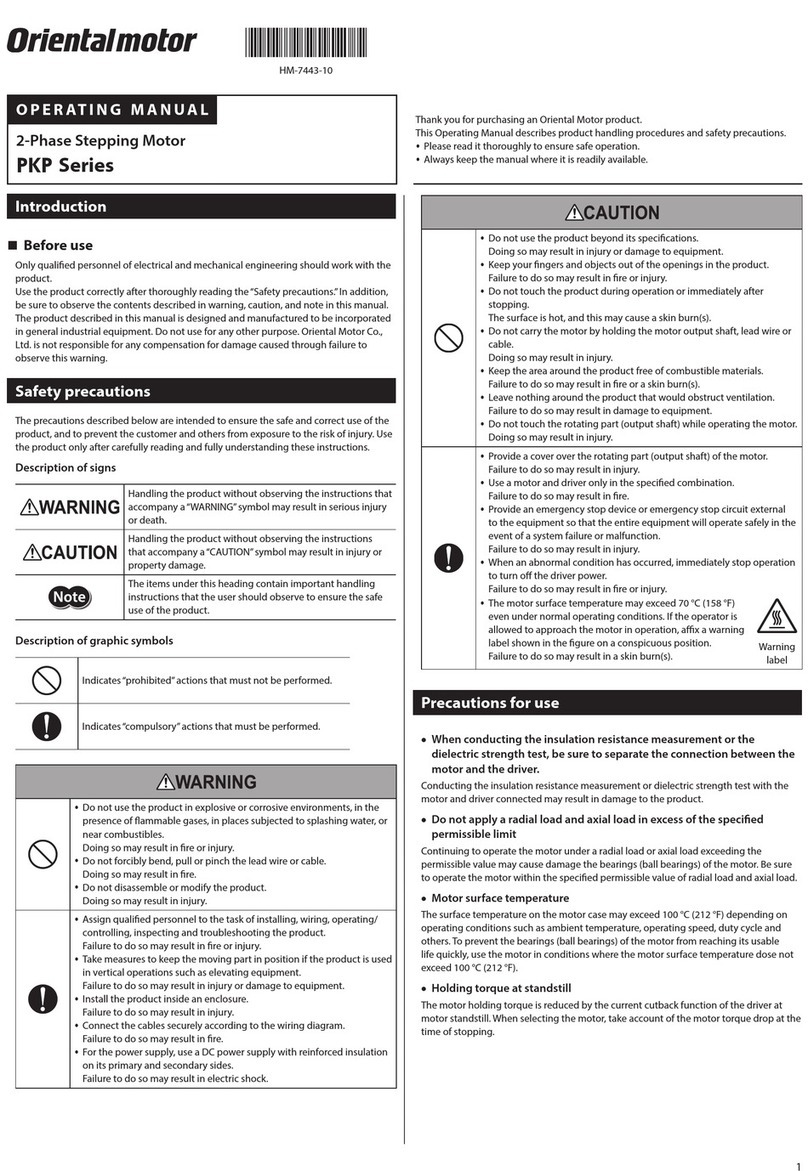
Oriental motor
Oriental motor PKP Series operating manual
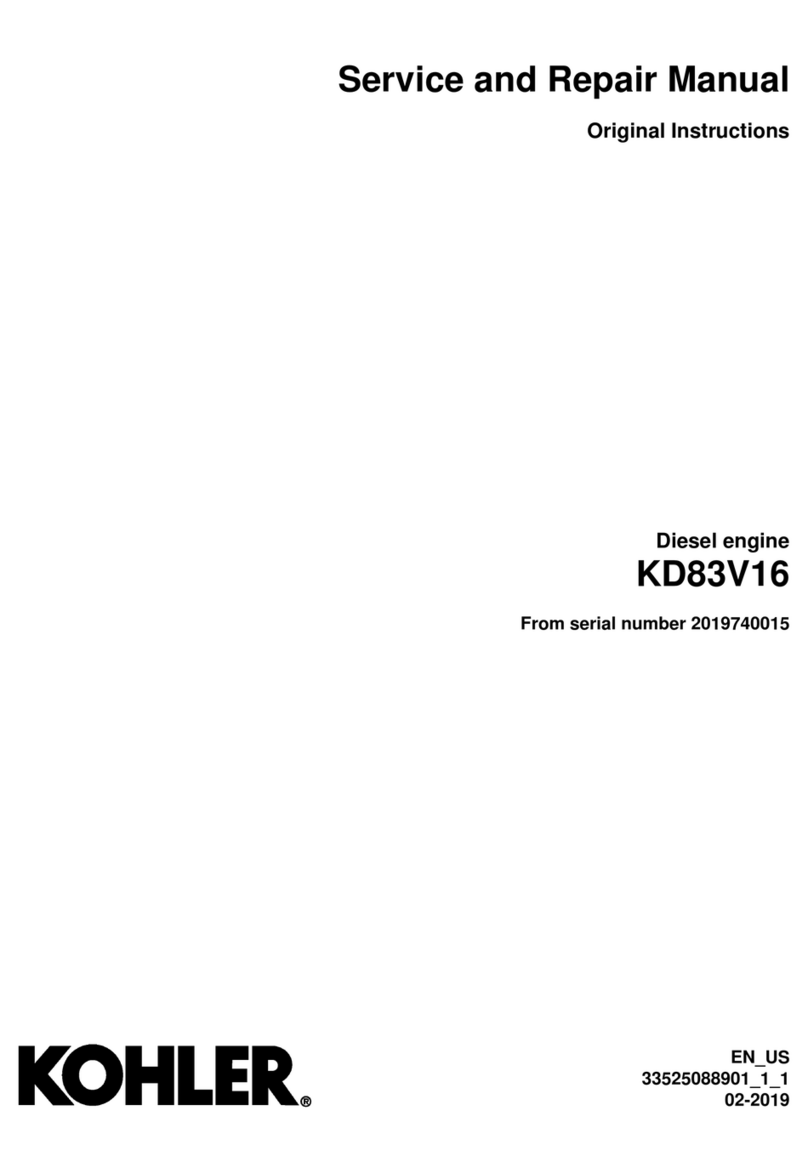
Kohler
Kohler KD83V16 Service and repair manual

Detroit Diesel
Detroit Diesel MBE4000 Service manual
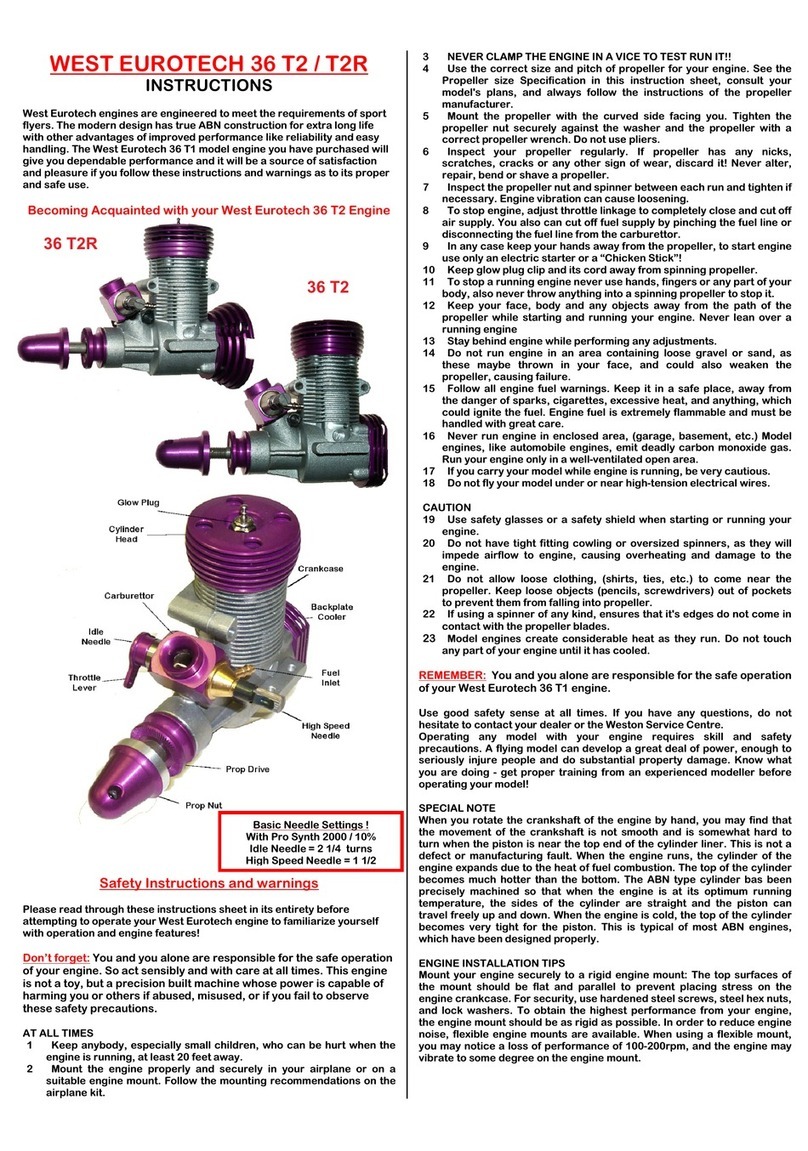
Weston UK
Weston UK WEST EUROTECH 36 T2 instructions
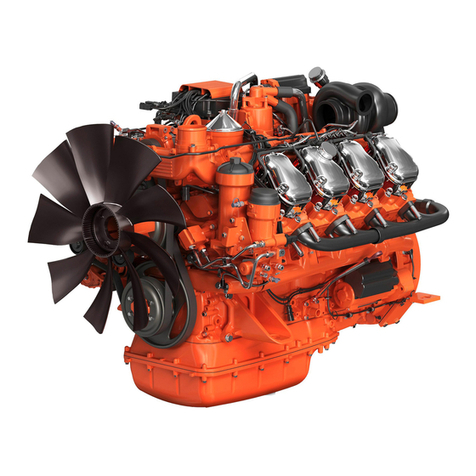
Scania
Scania DC09 installation manual

Enduro
Enduro PRO SM600-1 User Instructions & Parts List

Briggs & Stratton
Briggs & Stratton 290000 Series Operating & maintenance instruction manual
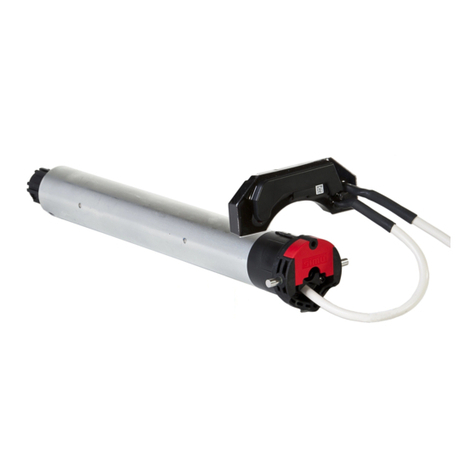
Simu
Simu T5 AUTOSHORT BHz Series Original instructions