Raven 063-3001-002 Operating instructions

1
016-0171-467 Rev. B 4/2015 E21066
Copyright 2015
CAN Switch Box™
Installation and
Operation Guide

016-0171-686 Rev. A, E31924
We Solve Great Challenges.
DISCLAIMER
While every effort has been made to ensure the accuracy of this
document, Raven Industries assumes no responsibility for
omissions and errors. Nor is any liability assumed for damages
resulting from the use of information contained herein.
Raven Industries shall not be responsible or liable for incidental or
consequential damages or a loss of anticipated benefits or profits,
work stoppage or loss, or impairment of data arising out of the
use, or inability to use, this system or any of its components. Raven
Industries shall not be held responsible for any modifications or
repairs made outside our facilities, nor damages resulting from
inadequate maintenance of this system.
As with all wireless and satellite signals, several factors may affect
the availability and accuracy of wireless and satellite navigation
and correction services (e.g. GPS, GNSS, SBAS, etc.). Therefore,
Raven Industries cannot guarantee the accuracy, integrity,
continuity, or availability of these services and cannot guarantee
the ability to use Raven systems, or products used as components
of systems, which rely upon the reception of these signals or
availability of these services. Raven Industries accepts no
responsibility for the use of any of these signals or services for
other than the stated purpose.

1
Overview
The Raven CAN Switch Box is designed to interface with Raven CAN control
consoles and field computers such as the Viper Pro, Envizio Pro, or SCS 5000
and offer product and section control features at the operator’s finger tips.
The CAN Switch Box features:
• Internal boom sense and speed node and CANbus terminator for simplified
cabling and installation. The CAN Switch Box provides section status
information (based upon switch positions) to the product control console or field
computer for section mapping and rate control adjustments.
• Ten section switches for quick boom or implement section control
• Five product control switches for quick product control mode selection
• A Master/Override switch for full boom or implement control
• An Increase/Decrease switch for quick application rate adjustments
• A Logic Power LED
• In addition to the above features, the CAN Switch Box for use with OmniSeed
systems offers implement control switches for raising and lowering the seed
tube openers and controlling the down pressure on the shanks.
Care and Maintenance
Refer to the following items when selecting a mounting location for the CAN
Switch Box and Raven control console.
• The switch box is not weatherproof. Mount the switch box inside of the machine
cab or driver compartment within easy reach of the driver or operator.
• The switch box should be mounted in a location where it will not be jarred during
normal equipment operation. Keep the console and switch box clear of moving
elements within the cab.
• Route all cables to avoid pinching, kinking or damaging the cable and to avoid
tripping hazards.
CAN Switch Box
for OmniSeed Systems
(P/N 063-3001-008)
CAN Switch Box
for Application Systems
(P/N 063-3001-002)

2
Installation
Refer to the following sections to install the console specific mounting bracket and
to connect the CAN Switch Box.
Mounting the CAN Switch Box
Viper Pro Bracket (P/N 107-0171-847)
Note: The Viper Pro mounting bracket may be used to mount the CAN Switch
Box either above or below the Viper Pro field computer.
1. Attach the two tapped half clamps (P/N 107-0171-541) to the mounting bracket
(P/N 107-0171-847) using the four flat head screws (P/N 311-0002-011).
2. Attach the mounting bracket to the Viper Pro field computer using four flat head
bolts (P/N 311-0002-302).
3. Attach the CAN Switch Box to the mounting bracket using two 5/16” screws (P/
N 311-0001-007).
4. Mount the Viper Pro and CAN Switch Box to a sturdy post or bar in the cab
using the remaining half clamps (P/N 107-0171-540) and 7/8” hex bolts
(P/N 311-0049-104).
At Raven Industries, we strive to make your experience with our
products as rewarding as possible. One way to improve this experience
is to provide us with feedback on this manual. Your feedback will help
shape the future of our product documentation and the overall service
we provide. We appreciate the opportunity to see ourselves as our
customers see us and are eager to gather ideas on how we have been
helping or how we can do better. To serve you best, please send an
email with the following information to
-CAN Switch Box™ Installation and Operation Guide
-016-0171-467 Rev. B
-Any comments or feedback (include chapter or page numbers if
applicable).
-Let us know how long have you been using this or other Raven
products.
We will not share your email or any information you provide with anyone
else. Your feedback is valued and extremely important to us.
Thank you for your time.

3
Envizio Pro XL Bracket (P/N 107-0172-197)
Note: The supplied mounting bracket must be attached to the Envizio Pro XL so
that the CAN Switch Box is mounted below the field computer.
1. Set the mounting bracket over the mounting posts on the back of the field
computer.
2. Set the RAM mounting arm over the mounting plate and secure using the
screws supplied with the field computer.
3. Align the CAN Switch Box with the remaining predrilled holes and secure using
screws supplied with the switch box.
Envizio Pro or Envizio Pro II Bracket (P/N 107-0171-841)
Note: The supplied mounting bracket must be attached to the Envizio Pro or
Envizio Pro II field computer so that the CAN Switch Box is mounted below
the field computer.
1. Set the mounting bracket over the mounting posts on the back of the field
computer.
2. Set the RAM mounting arm over the mounting plate and secure using four
screws (P/N 311-0007-015).
3. Align the CAN Switch Box with the remaining predrilled holes and secure using
two lock washers (P/N 313-4000-007) and two screws (P/N 311-0001-007).
SCS 4000/5000 Series Bracket (P/N 107-0171-958)
Note: The SCS 4000/5000 Series bracket must be attached to the console so
that the CAN Switch Box is mounted above the control console.
1. Attach the two tapped half clamps to the mounting plate provided with the SCS
console.
2. Align the CAN Switch Box mounting bracket (P/N 107-0171-958) with the
mounting posts on the back of the SCS console.

4
3. Set the mounting plate over the bracket and secure using the four 1” hex bolts
(P/N 311-0050-105).
4. Attach the CAN Switch Box to the mounting bracket using two mounting screws
(P/N 311-0001-007).
Cable Connections
The CAN Switch Box connects to the control console and CANbus system with
either the SCS 5000 series chassis interface cable (P/N 115-0171-959) or the
Viper Pro/Envizio Pro chassis interface cable (P/N 115-0172-001).
To connect the CAN Switch Box:
1. Connect the 4-pin Deutsch connector on the console or interface cable to the
CANbus port on the back of the CAN Switch Box.
2. Connect the 2-pin Deutsch connector on the console or interface cable to the
switched power port on the back of the CAN Switch Box.
3. If connecting to a Viper Pro or Envizio Pro using the chassis interface cable (P/
N 115-0172-001), connect the round, 3-pin connector on the interface cable to
the speed sensor port on the back of the CAN Switch Box.
Note: If the CAN Switch Box is connected as instructed above, the switch box will
be powered on or off using the Raven console or field computer switched
power. Refer to the console or field computer manual for instructions to
properly power down the console.
CANbus
Mounting Posts
Switched
Power
Speed
Sensor

5
CAN Switch Box Operation
Important: The CAN Switch Box must be used as the primary control interface
for section, master or product control status.
Make sure to toggle the master switch to the off position when closing or
exiting a job to avoid unintentional product application once the field
computer or control console closes application management functions. It
is also good practice to shut off product and section switches when the
application system is not being used.
The CAN Switch Box puts the section and product control modes right at the
operator’s finger tips.
Refer to the following sections for detailed operation of the CAN Switch Box:
Logic Power LED
This LED indicates the status of CAN logic power into the CAN Switch Box. This
LED should be on (solid) during normal operation.
The Logic Power LED will begin flashing if low logic power is supplied to the CAN
Switch Box. Troubleshoot the logic power system before proceeding with
operations.
If this LED is not lit when the Raven console or field computer is powered up,
troubleshoot the CANbus system before starting any system operations.
Increase/Decrease Flow Switch
Note: The INC/DEC switch only controls the selected product in automatic or
manual mode. Refer to the field computer or control console manual for
more information on selecting products during application.
For selected products set to automatic control mode, the INC/DEC switch is used
to increase or decrease the target rate of products selected and actively displayed
on the console or field computer.
In order for this switch to work properly, a ‘Rate Bump’ (Rate +/-) value must be
programmed for each product. Refer to the control console or field computer
operation manual for more information on programming this feature.
For selected products set to manual control mode, holding the INC/DEC switch
will open or close the product control valve, increasing or decreasing the flow of
product respectively. Refer to the control console or field computer operation
manual for instructions on programming products or switching a product to
manual mode.
Section
Switches
Logic
Power LED
Increase/
Decrease Product Control
Switches Master/Override
Switch

6
Master/Override Switch
The master switch toggles all section switches on or off. When the master switch
is in the ‘ON’ position, each section will function according to the corresponding
section switch (see the “3-Way Selectable Section Switches” below). Toggle the
master switch to the ‘OFF’ position to turn all boom or implement sections off.
Hold the master switch to the ‘OVERRIDE’ position to temporarily override any
sections controlled by an optionalAccuBoom system on.
3-Way Selectable Section Switches
The section switches may be used to toggle up to ten individual sections. Raven
field computers are also capable of controlling additional sections using the
section mapping feature to group sections to the same switch. Refer to the field
computer Installation and Operation Manual for additional information.
Note: Envizio Pro software version 3.5 or newer or a Viper Pro controlling an
OmniSeed system are required to access section mapping. Contact a local
Raven dealer for additional information.
Each of the ten section switches may be toggled individually to one of the three
following positions:
• ON - manually control the section on. AccuBoom control of the section is
disabled and will not automatically control this section based on coverage, zone
maps or field boundaries.
• ACCU - AccuBoom automatic section control is enabled for the section. If
installed and properly set up for the active job, the AccuBoom features will
automatically turn sections on or off based upon previous coverage, zone maps
or field boundaries created or active in the job.
Refer to the control console or field computer operation manual for more
information about using the AccuBoom system.
• OFF - manually control the section off. This section will remain off regardless of
AccuBoom control features.
Note: Leave the section switch in the off position for any sections not connected
or controlled by the Raven control console or field computer.
Product Control Switches
Each of the five product control switches may be toggled individually to one of the
three following positions:
• AUTO - The product rate will automatically be controlled by the product control
console or field computer based on the vehicle speed and programmed target
rate. Refer to the control console or field computer operation manual for
information on programming a target rate for controlled products.
• MAN - The product rate must be manually controlled by the operator. The
Raven control console or field computer will not adjust product rate based on
vehicle speed or section status.
• OFF - The programmed product is off. Corresponding control valves, injection
pumps or spinners will remain closed or will not run regardless of section or
master switch changes.

7
CAN Switch Box for OmniSeed Systems
The CAN Switch Box for use with OmniSeed
systems (P/N 063-3001-008) feature two
additional switches configured for controlling
seeder implement functions via a drill control
node connected to the OmniSeed CANbus
control system.
Note: Contact a local Raven dealer for
more information about drill control
nodes and other OmniSeed control
hardware options and features.
Openers Switch
Toggle the openers switch to raise (UP) or
lower (DN) the seed shanks during field
operations.
Note: If the packing pressure settings on the field computer are set to automatic
or manual control, the system will automatically shut off products and seed
rate control sections when the shanks are raised. If packing pressure
control is set to off, the openers switch will only raise and lower the shanks
without changing product or section status.
Packing Pressure Override Switch
The OmniSeed system allows an operator to set the target packing pressure and
an override pressure for use during a field operation.
When the Pressure Override switch is in the down position, the OmniSeed system
will control based upon the target packing pressure setting. Toggle the Pressure
Override to the up position to engage the override pressure setting.
Openers
Switch Down Pressure
Override Switch

8
Troubleshooting
General Issues
Issue Possible
Cause Solution
Console or field
computer does
not power up No power to
console
Check chassis cable battery
connections.
Check chassis cable fuses.
Logic power
LED not lit No power to
CAN Switch Box
Check CAN Switch Box switched power
connection.
Ensure console or field computer is
powered on.
Check chassis cable power and ground
connections.
Check chassis cable fuses.
Console or field
computer not
detecting CAN
nodes
CAN Switch Box
notconnectedto
CANbus
Check CANbus connector on CAN
Switch Box.
Check CAN connections and cabling.
Check CAN terminator on end of
CANbus line.
Check for +12 volts on switched power
connector.
Console not set
up for CANbus
control
Verify that the console or field computer
product control configuration is set to
CAN.
Boom valves do
not turn on Faulty CAN high
current power
connection
Verify high current (HC) power LED on
product controller node is lit. If LED not
lit, refer to troubleshooting information
in control console or field computer
manual.
Boom sections
do not turn off
Remote section
switches in
incorrect
position
Remote section switches must be in the
OFF position to allow the CAN Switch
Box to control sections.

9
Setup Issues
Job Issues
Issue Possible
Cause Solution
Previous
calibration data
lost Poor CAN
connections Refer to the “CAN Troubleshooting”
section on page 11.
Issue Possible
Cause Solution
Section status
displays as
inactive
CAN Switch Box
switches in the
off position Toggle the section and master switches
to the on position.
Automatic
section control
enabled but
sections do not
turn on
Check the speed sensor connection on
the back of the CAN Switch Box.
Move vehicle into a previously
unapplied area and maintain a speed of
at least
0.7 mph [1.1 km/h].
Enable the Override feature on the
control console or field computer
Section status
does not turn
green (ON)
when sections
enabled
Master switch
must be toggled
off at power-up Cycle the master switch off then back
on.
Sections not
properly
configured Verify section setup on the control
console or field computer.
Nodes not
programmed
properly Verify all node calibration data is
entered.
Product function
switches do not
work
Master switch
must be toggled
off at power-up Cycle the master switch off then back
on.
Product
application
turned off
Toggle product control switches to
AUTO or MAN mode to turn product(s)
on.

10
Product applied
to zero rate
zones
Bed creep Adjust hydraulic valve and valve
calibration settings to stop bed creep.
Refer to the control console or field
computer operation manual.
Wrong valve
type installed
A fast close or PWM close valve must
be selected to shut off product
application in zero rate zones. Refer to
field computer or control console
manual for more information about
selecting valve type.
Incorrect valve
setting Check valve or PWM settings.
Sectionswitches
toggled on in
zero rate zones Toggle the section switches to the
ACCU or OFF positions.
Sections
enabled but field
computer not
recording
coverage
Remote section
switches left in
the ON position
Toggle all remote section switches to
the off position. Remote switches will
override the section switch status and
automatic section control features.
Issue Possible
Cause Solution

11
CAN Troubleshooting
Although the control algorithm is located within the CAN node(s), the same
troubleshooting techniques that apply to traditional hard wired control systems still
apply to a CANbus control network. CAN allows for modularization of the control
system, but the behavior of the system remains the same. Flow and speed
sensors, the control valve and any boom valves, are used in the same manner.
The following are some common causes for communication failures:
Issue Possible
Cause Solution
Console or
CANbus cannot
find nodes
Switch Box is
not properly
connected
Check switched power connection.
Check the CANbus connection to the
Switch Box and reinitialize the console
to detect the Switch Box nodes.
Ensure console is powered on.
No power to
Switch Box Check chassis cable power and ground
connections.
Weak or dirty
power to CAN
nodes Verify at least +10V DC is present on
the switched power connector.
Corrosion in
CAN
connections Disconnect and clean the cable
connections
CANbus not
terminated
properly Check the CAN Terminator(s)


016-0171-537 Rev. H, E29761
We Solve Great Challenges.
LIMITED WARRANTY
WHAT DOES THIS WARRANTY COVER?
This warranty covers all defects in workmanship or materials in your
Raven Applied Technology Division product under normal use,
maintenance, and service when used for intended purpose.
HOW LONG IS THE COVERAGE PERIOD?
Raven Applied Technology products are covered by this warranty for
12 months from the date of retail sale. In no case will the Limited
Warranty period exceed 24 months from the date the product was
issued by Raven Industries Applied Technology Division. This warranty
coverage applies only to the original owner and is non-transferable.
HOW CAN I GET SERVICE?
Bring the defective part and proof of purchase to your Raven dealer. If
the dealer approves the warranty claim, the dealer will process the
claim and send it to Raven Industries for final approval. The freight cost
to Raven Industries will be the customer’s responsibility. The Return
Materials Authorization (RMA) number must appear on the box and all
documentation (including proof of purchase) must be included inside
the box to be sent to Raven Industries.
WHAT WILL RAVEN INDUSTRIES DO?
Upon confirmation of the warranty claim, Raven Industries will (at our
discretion) repair or replace the defective product and pay for the
standard return freight, regardless of the inbound shipping method.
Expedited freight is available at the customer’s expense.

016-0171-537 Rev. H, E29761
We Solve Great Challenges.
WHAT IS NOT COVERED BY THIS WARRANTY?
Raven Industries will not assume any expense or liability for repairs
made outside our facilities without written consent. Raven Industries is
not responsible for damage to any associated equipment or products
and will not be liable for loss of profit, labor, or other damages. The
obligation of this warranty is in lieu of all other warranties, expressed or
implied, and no person or organization is authorized to assume any
liability for Raven Industries.
Damages caused by normal wear and tear, misuse, abuse, neglect,
accident, or improper installation and maintenance are not covered
by this warranty.

016-0171-536 Rev. B, E29761
We Solve Great Challenges.
EXTENDED WARRANTY
WHAT DOES THIS WARRANTY COVER?
This warranty covers all defects in workmanship or materials in your
Raven Applied Technology Division product under normal use,
maintenance, and service when used for intended purpose.
DO I NEED TO REGISTER MY PRODUCT TO
QUALIFY FOR THE EXTENDED WARRANTY?
Yes. Products/systems must be registered within 30 days of retail sale
to receive coverage under the Extended Warranty. If the component
does not have a serial tag, the kit it came in must be registered instead.
WHERE CAN I REGISTER MY PRODUCT FOR THE
EXTENDED WARRANTY?
To register, go online to www.ravenhelp.com and select Product
Registration.
HOW LONG IS THE EXTENDED WARRANTY
COVERAGE PERIOD?
Raven Applied Technology products that have been registered online
are covered for an additional 12 months beyond the Limited Warranty
for a total coverage period of 24 months from the date of retail sale. In
no case will the Extended Warranty period exceed 36 months from the
date the product was issued by Raven Industries Applied Technology
division. This Extended Warranty coverage applies only to the original
owner and is non-transferable.

016-0171-536 Rev. B, E29761
We Solve Great Challenges.
HOW CAN I GET SERVICE?
Bring the defective part and proof of purchase to your Raven dealer. If
the dealer approves the warranty claim, the dealer will process the
claim and send it to Raven Industries for final approval. The freight cost
to Raven Industries will be the customer’s responsibility. The Return
Materials Authorization (RMA) number must appear on the box and all
documentation (including proof of purchase) must be included inside
the box to be sent to Raven Industries. In addition, the words
“Extended Warranty” must appear on the box and all documentation if
the failure is between 12 and 24 months from the retail sale.
WHAT WILL RAVEN INDUSTRIES DO?
Upon confirmation of the product’s registration for the Extended
Warranty and the claim itself, Raven Industries will (at our discretion)
repair or replace the defective product and pay for the standard return
freight, regardless of the inbound shipping method. Expedited freight
is available at the customer’s expense.
WHAT IS NOT COVERED BY THE EXTENDED
WARRANTY?
Raven Industries will not assume any expense or liability for repairs
made outside our facilities without written consent. Raven Industries is
not responsible for damage to any associated equipment or products
and will not be liable for loss of profit, labor, or other damages. Cables,
hoses, software enhancements, and remanufactured items are not
covered by this Extended Warranty. The obligation of this warranty is in
lieu of all other warranties, expressed or implied, and no person or
organization is authorized to assume any liability for Raven Industries.
Damages caused by normal wear and tear, misuse, abuse, neglect,
accident, or improper installation and maintenance are not covered
by this warranty.
This manual suits for next models
1
Table of contents
Other Raven Switch manuals
Popular Switch manuals by other brands
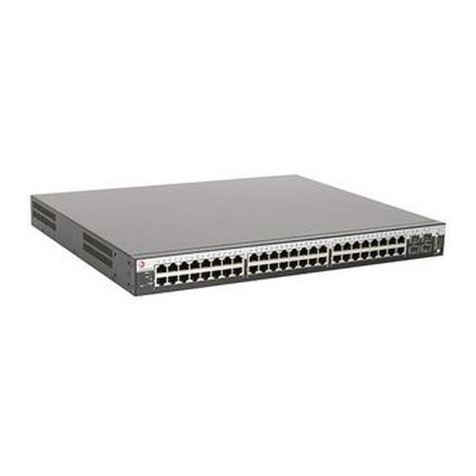
Enterasys
Enterasys SECURESTACK C3 Configuration guide

ZyXEL Communications
ZyXEL Communications VES-1124 - brochure
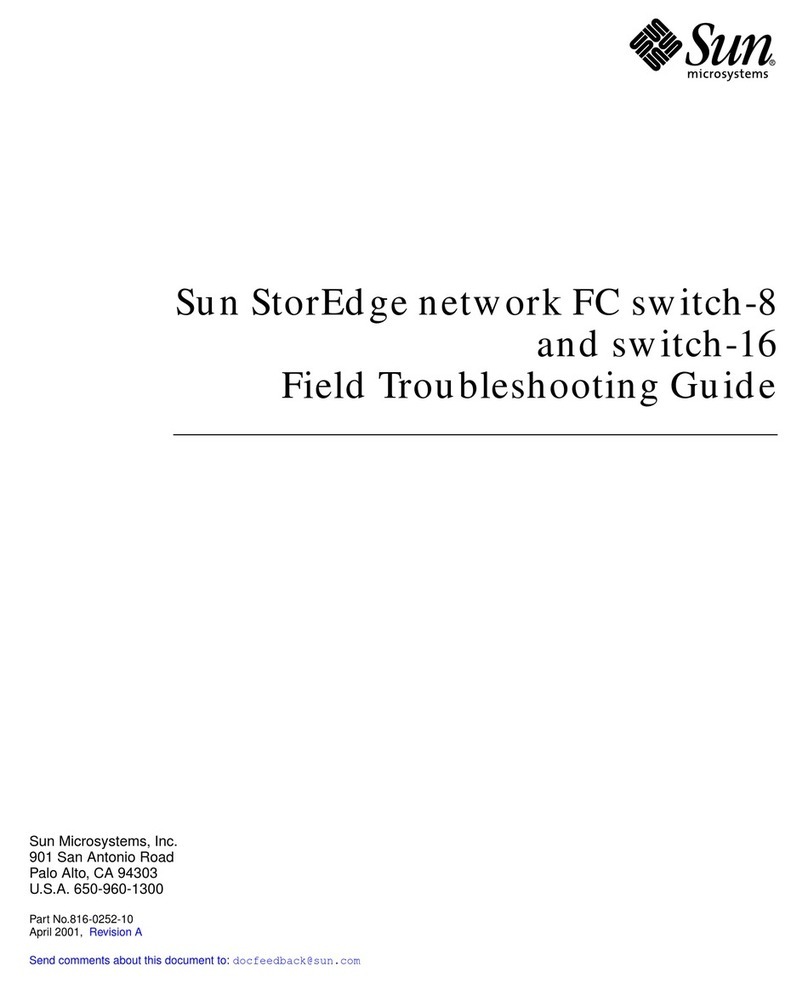
Sun Microsystems
Sun Microsystems Sun StorEdge Switch-8 troubleshooting guide
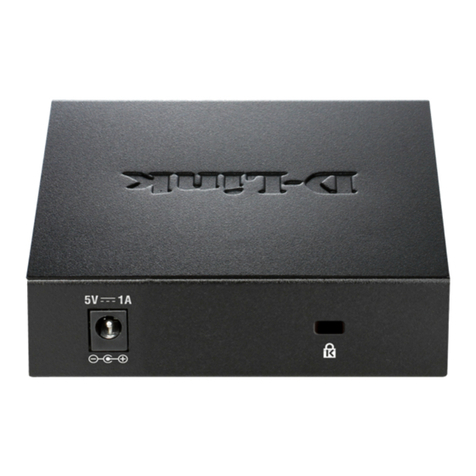
D-Link
D-Link DES-105 user manual
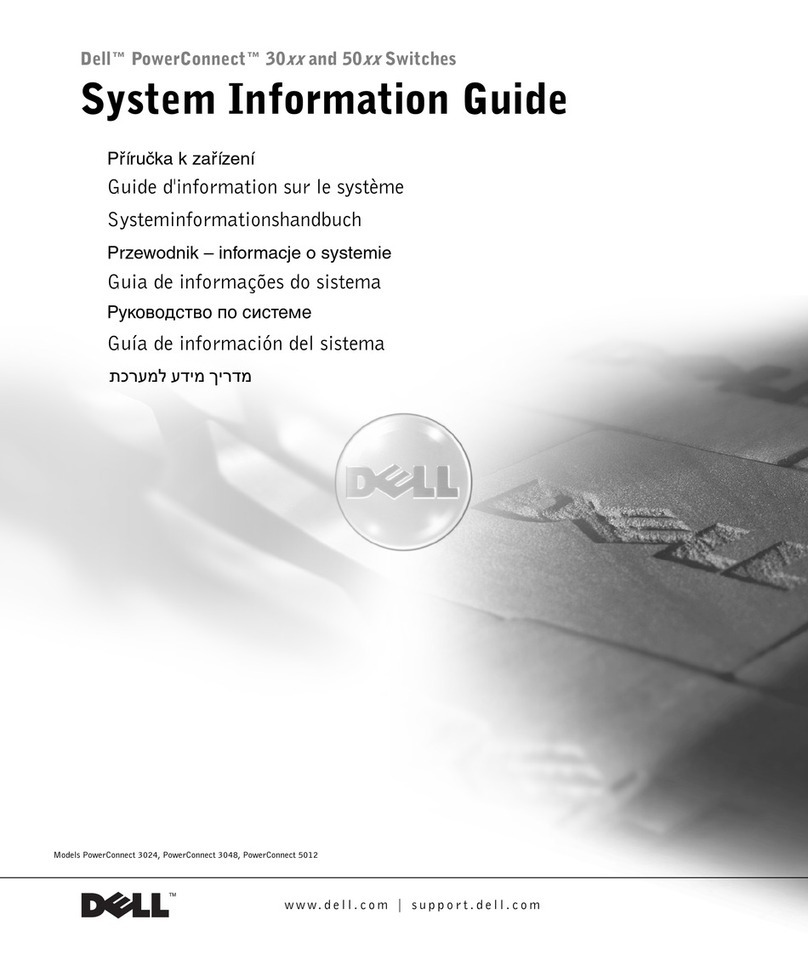
Dell
Dell PowerConnect 3024 System information guide
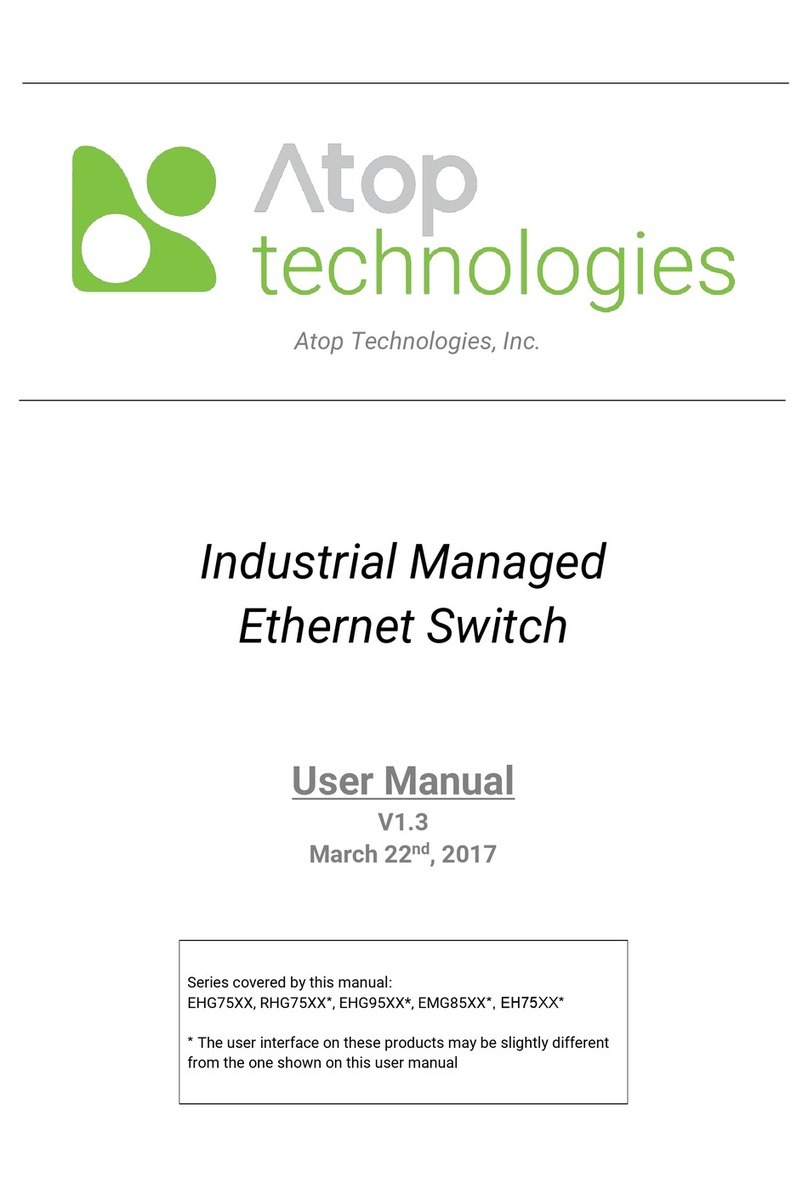
Atop
Atop EHG75 series user manual
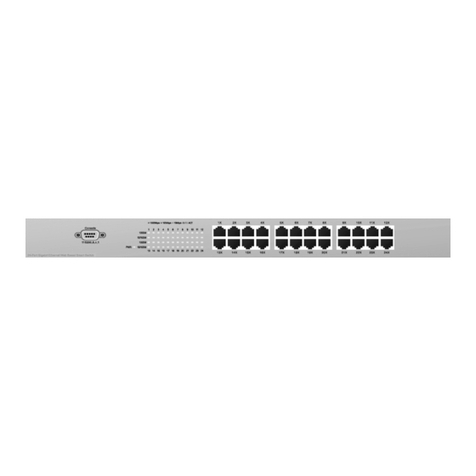
KTI Networks
KTI Networks KGS-2401 installation guide

Belkin
Belkin OmniView SOHO F1DD102L user manual
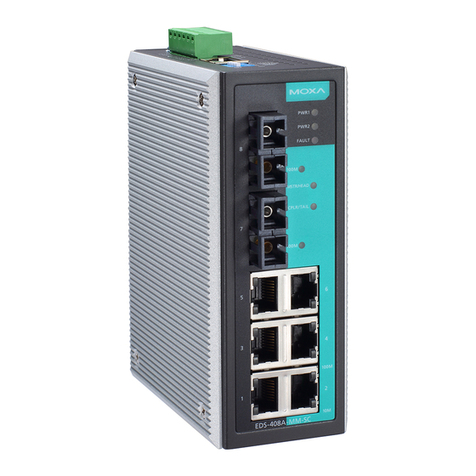
Moxa Technologies
Moxa Technologies EDS-408A user manual

Wizard
Wizard ON-S5700-48GP-4TF installation manual

LEGRAND
LEGRAND Mosaic Manageable switch Installation and configuration guide

Climax Technology
Climax Technology PSS-29ZBS manual