RDS Technology Liftlog 1000 User manual

1
User Guide
Title
Sub Title
Liftlog 1000
Fork Lift Truck
Weighing System
Installation and Calibration

LIFTLOG 1000 –INSTALLATION AND CALIBRATION
2
Electromagnetic Compatibility (EMC)
This product complies with European Council Directive 2004/108/EC when installed and used in accordance with the relevant
instructions.
Service and Technical Support
PLEASE CONTACT YOUR NEAREST DISTRIBUTOR or if unknown, contact the factory for further information.
RDS Technology Ltd, Cirencester Road, Minchinhampton, Stroud, Glos, GL6 9BH, United Kingdom
Our policy is one of continuous improvement and the information in this document is subject to change without notice.
Check that the software reference matches that displayed by the instrument.
This manual refers to Software Issue: GC114 Iss01 rev00
Document Number : S/DC/500-10-795 :
Issue : 1.01
Issue Date 29.9.15
Source file: \UK795110.DOCX
© Copyright RDS Technology Ltd 2015

LIFTLOG 1000 –INSTALLATION AND CALIBRATION
3
Information on Disposal for Users of Waste Electrical & Electronic Equipment
This symbol on the product(s) and / or accompanying documents means that the electronic component(s) of this product should
not be mixed with general household waste at end of life.
RDS mobile machinery electronics are exempt from European WEEE recycling regulations. Regardless, we recommend that
wherever our products are used, the various elements (electrical or otherwise), are disposed of responsibly at their end of life. If
you wish to discard our products, then we advise that if unsure, you contact your local area authority / recycling centre for advice
on the correct method of disposal.
Disposing of our products correctly will help save valuable resources and prevent any potential negative effects on human health
and the environment, which could otherwise arise from inappropriate waste disposal. Penalties may be applicable for incorrect
disposal of waste, in accordance with your national legislation.

LIFTLOG 1000 –INSTALLATION AND CALIBRATION
4
1. INTRODUCTION 6
1.1 Important Information 6
1.2 Important Safety Precautions ! 6
1.3 System Overview 7
1.4 Parts List : Ref. Kit P/LIFTLOG/1000 8
1.5 Hydraulic Fitting Kits (standard unless otherwise specified) 9
1.6 Hydraulic Fitting Kits (options) 11
2. INSTALLATION 12
2.1 Drop Valve / Pressure Sensor 12
2.1.1 Flow Rate Adjustment............................................................................................................................................................... 14
2.2 Reference Sensor 15
2.2.1 Weighing Height without Reference Sensor............................................................................................................................. 16
2.3 Head Unit 17
2.4 Electrical 18
2.4.1 Junction Box.............................................................................................................................................................................. 18
2.4.2 Power Supply ............................................................................................................................................................................ 19
2.4.3 Printer.......................................................................................................................................................................................19
2.4.4 Electrical Connections...............................................................................................................................................................20
2.5 Diagnostics 21

LIFTLOG 1000 –INSTALLATION AND CALIBRATION
5
3. CALIBRATION 22
3.1 Setup Menu 22
3.2 “Full Setup Wizard” 23
3.3 Technician Level Settings 24
3.3.1 Home Screen Functions ............................................................................................................................................................24
3.3.2 Logging Options ........................................................................................................................................................................ 24
3.3.3 Port Setup ................................................................................................................................................................................. 27
3.3.4 Language / Keyboard region ..................................................................................................................................................... 27
3.3.5 Instrument ID............................................................................................................................................................................ 27
3.3.6 Job No. / Ticket No....................................................................................................................................................................28
3.3.7 Save to USB............................................................................................................................................................................... 28
3.3.8 Load from USB .......................................................................................................................................................................... 29
3.3.9 Overload Log.............................................................................................................................................................................30
3.4 Factory Level Settings 31
3.4.1 ‘Auto’ Weight Calibration .........................................................................................................................................................31
3.4.2 Calibration Factors.................................................................................................................................................................... 32
3.4.3 Linear Compensation Factors ................................................................................................................................................... 32
3.4.4 Sensor Setup .............................................................................................................................................................................33
3.4.5 Overload Alarm Setup...............................................................................................................................................................34
3.4.6 Error Log ...................................................................................................................................................................................35
3.4.7 PIN ............................................................................................................................................................................................ 35
3.4.8 Software Reset.......................................................................................................................................................................... 35

LIFTLOG 1000 –INSTALLATION AND CALIBRATION
6
1. Introduction
1.1 Important Information
NOTE: FITTING, CALIBRATION AND MAINTENANCE MUST ONLY BE UNDERTAKEN BY A TRAINED INSTALLER. ANY ATTEMPT BY
UNQUALIFIED PERSONNEL TO INTERFERE WITH OR ALTER THE INSTALLATION OR SETUP OF THE SYSTEM, MAY RESULT IN
DAMAGE TO THE MACHINE, PERSONAL INJURY OR POSSIBLE DEATH!
This manual provides general guidelines that will enable the experienced installer to adapt the system successfully to the
majority of machine makes and models. If you are in any doubt regarding an installation detail for a particular machine, then
further technical guidance and specific installation detail is available from RDS Technology. Log in the website, or contact the
RDS Service and Support Department at the factory.
RDS Technology Ltd does not accept responsibility for faulty operation of the system or consequential damage, as a result of poor
workmanship of installation, or any aspect of component installation that does not comply with the requirements for correct
operation as stated in this manual. The installer is responsible to ensure proper fitting.
1.2 Important Safety Precautions !
In addition to observing site safety requirements, before working on the machine always :-
Make sure that the Attachment is down on the floor, and all pressure is released from the hydraulic system, before slackening
off any hydraulic coupling
Prevent the machine from being accidentally started while working on it e.g. remove the ignition key, place a warning notice
in the cab etc.
Keep other persons in the vicinity of the machine fully aware of your immediate intentions during installation and initial
calibration.

LIFTLOG 1000 –INSTALLATION AND CALIBRATION
7
1.3 System Overview
The Liftlog 1000 is a weighing system designed for use principally on counterbalance fork lift trucks. It measures, displays and
records the net or gross weight lifted, normally based on sensing the lift system hydraulic pressure. Normally, a weighing start
point is established by use of a magnetic Reference position sensor fitted on the lift mast. Without the reference sensor
however, the weighing cycle can be started at any lift height (while still allowing the load sufficient height to drop while
weighing).
Triggering the weighing cycle operates a solenoid on a custom, flow-regulated valve, causing the lift cylinder(s) to drop at a
controlled rate while the hydraulic pressure is measured and averaged over the sampling period. The weight is then displayed
either as a gross weight, or if a tare value has been set, then the net weight can be displayed.
Reference
Sensor
Magnet
Drop Valve
+ Pressure Sensor
T-piece
Remote Weigh Button
and/or Remote Enter
Switch (optional)
Indicator
Indicator
Cable
Power Supply
External Alarm
(optional)
Junction Box

LIFTLOG 1000 –INSTALLATION AND CALIBRATION
8
1.4 Parts List : Ref. Kit P/LIFTLOG/1000
Item
Part No.
Description
Qty
Standard
1
K/DROP/VALVE
Kit - Drop Valve
2
K/G-CAN/SCR/PRT
Kit - Touchscreen Protection
1
3
K/INSTRUMENT
Kit - Power Supply
1
4
K/LIFTLOG/REF
Kit - Reference Sensor
1
5
K/LOAD/COMP/250
Kit - 250 bar Pressure Sensor
1
6
K/RAM/MOUNT/KIT
Kit - “RAM” Mount Kit
1
7
S/AC/411-1-005
Junction Box
1
8
S/CB/410-1-026
Display Unit Cable
1
9
S/CBL/TIE/005
Cable Tie –370mm
5
10
S/F724-003
Cable Tie –6”
2
11
S/FSNR/940221
¼” BSP “Dowty” Seal
1
12
S/HU/435-1-001
Head Unit
1
#
S/DC/500-10-787
Terminator Label
1
#
S/DC/500-10-794
Quick reference Guide
1
#
S/DC/500-10-795
Installation and Calibration Manual
1
#
S/DC/500-10-796
Operation Manual
1
#
K/VHL/INST/053
3/8” BSP High Pressure Hose Kit
1
#
K/VHL/INST/055
½” Low Pressure Hose Kit
1
Optional:
#
Kit - Remote Enter Switch
1
#
Kit - Remote Weigh Button
1
#
Kit - External Alarm
1

LIFTLOG 1000 –INSTALLATION AND CALIBRATION
9
1.5 Hydraulic Fitting Kits (standard unless otherwise specified)
Unless specified otherwise, the following kits are supplied as standard with the main kit (ref. fig.1 overleaf)
Item
Part No.
Description
Qty
Pressure Circuit (Cylinder Return circuit –Feed to Drop Valve)
K/VHL/INST/053
3/8” BSP High Pressure Hose Kit
1
1
S/HY/500-9-099
3/8” BSPF – 3/8”BSPF Hose, 250bar, 1M
1
2
S/HY/500-9-100
¼” BSPF – 3/8” BSPM Adaptor
1
3
S/HY/500-9-101
3/8”BSPM – 3/8” BSPM Adaptor
1
4
S/HY/500-9-102
3/8” BSP “Dowty” Seal
1
5
S/FSNR/940221
¼” BSP “Dowty” Seal
1
#
K/VHL/INST/005
Tapped Port Kit (ref section 1.6 for alternatives)
1
Return to Tank Circuit
K/ VHL/INST/055
½” Low Pressure Hose Kit
1
6 #
S/HY/500-9-103
½” Hose, 25 bar, 2.5M
1
7
S/HY/500-9-101
3/8”BSPM – 3/8” BSPM Adaptor
1
8
S/HY/500-9-102
3/8” BSP “Dowty” Seal
1
9
S/HY/500-9-104
3/8” BSPM – 3/8” BSPF Elbow
1
10
S/HY/500-9-105
½” BSPF Hosetail
1
11
S/FIXING/084
13 –20mm Hose Clip
4
K/ VHL/INST/056
1/2” Low Pressure Tee Kit (ref section 1.6 for alternatives)
1
12
S/HY/500-9-106
½” BSPM Hosetail
3
13
S/HY/500-9-107
3/8” BSPF Equal Tee
1
# Not illustrated.

LIFTLOG 1000 –INSTALLATION AND CALIBRATION
10
Fig 1: Hydraulic Components
Lift Cylinder
return line
LP Tank Return
1
2
3
4
9
7
8
10
12
13
12
12
11
5
Fit as required for either
‘P’ or ‘T’ ports

LIFTLOG 1000 –INSTALLATION AND CALIBRATION
11
1.6 Hydraulic Fitting Kits (options)
Pressure Circuit (Cylinder Return circuit –Feed to Drop Valve)
The correct tee fitting kit should have been specified and supplied for the particular machine. Unless otherwise specified, the
system is supplied with kit K/VHL/INST/005 to drill and tap a 1/8” BSP port at a suitable point in the lift cylinder return circuit.
Return to Tank Circuit
In addition to the standard ½” Hose kit supplied, the correct tee fitting kit should have been specified and supplied for the
particular machine, to tee this hose into the hose returning to the hydraulic tank. Unless otherwise specified, the system is
supplied with kit K/VHL/INST/056 to suit a ½” bore tank return.
The optional LP tee kits are:
K/ VHL/INST/057
¾” Low Pressure Hose Kit
K/ VHL/INST/058
1” Low Pressure Hose Kit
K/ VHL/INST/059
1-1/4” Low Pressure Hose Kit
K/ VHL/INST/060
1-1/2” Low Pressure Hose Kit
NOTE: Low pressure Hose kits are rated to 25 bar.

LIFTLOG 1000 –INSTALLATION AND CALIBRATION
12
To tank
Flow
adjuster
2. Installation
2.1 Drop Valve / Pressure Sensor
Before mounting the valve, fit the pressure sensor to the
valve body using the ¼” “Dowty” seal washer supplied.
Wherever possible, choose a mounting position where it will
be afforded the best protection from the elements. The valve
can be mounted in any orientation, but leaving the flow
adjustment screw accessible.
The drop valve pressure port marked 'P' (Pressure) should be
connected into the lift cylinder return line at a suitable
location, using the appropriate fittings (figure 1).
The drop valve return port marked 'T' (Tank) should be
connected into the hydraulic tank return line from the spool
valve block, using the appropriate fittings (Figure 1).
NOTE: Use PTFE sealing tape for low pressure fittings.
Solenoid
4-20mA
Pressure Sensor
Lift
Cylinder
return

LIFTLOG 1000 –INSTALLATION AND CALIBRATION
13
Typical Drop Valve installation
Tee - lift cylinder
return line to
pressure port 'P'
Tee - return port 'T'
to tank return line
Drop
valve

LIFTLOG 1000 –INSTALLATION AND CALIBRATION
14
Route the pressure sensor lead and solenoid lead back to
the Terminator.
Cable tie at regular intervals following the existing wiring
loom where possible.
Ref. 2.4.4 for wiring connections.
2.1.1 Flow Rate Adjustment
The drop rate may need to be adjusted depending on the particular machine. With the solenoid connected and the head unit
powered up, press the weigh button to energize the solenoid and observe the rate of drop. Slacken the locking nut and turn the
adjuster screw in or out to decrease or increase the drop rate (i.e. approximately 15cm or 6” over the 5 second sampling period).
NOTE: Drop rate can be set with empty forks, since the drop valve keeps the flow rate constant under varying pressure.

LIFTLOG 1000 –INSTALLATION AND CALIBRATION
15
2.2 Reference Sensor
The Reference sensor kit automatically enables the weigh button when the load reaches the weighing position.
Assemble the sensor to the bracket allowing it to project at
least 15mm from the face of the bracket.
Lift the forks to the desired weighing position.
Thoroughly clean the area where the sensor bracket and
magnet are to be positioned, and both the magnet and
bracket mounting face, using a degreasing solvent.
It is recommended to attach the magnet to the hanger
carriage where shown, using theself-adhesive pad supplied.
The position of the bracket determines the weighing height
when the magnet is directly opposite the sensor.
Two M6 mounting holes are provided on the bracket.
However, it is recommended wherever possible to avoid
drilling and tapping, and to attach the bracket to the side of
the mast using the self-adhesive pad supplied.
Allow 10mm clearance between the sensor and the magnet.
NOTE: The centre portion of the self-adhesive pad S/AC/500-4-155 is to attach the magnet, while the remainder is to attach the sensor
bracket. The adhesive can be applied in temperatures down to -10°C.
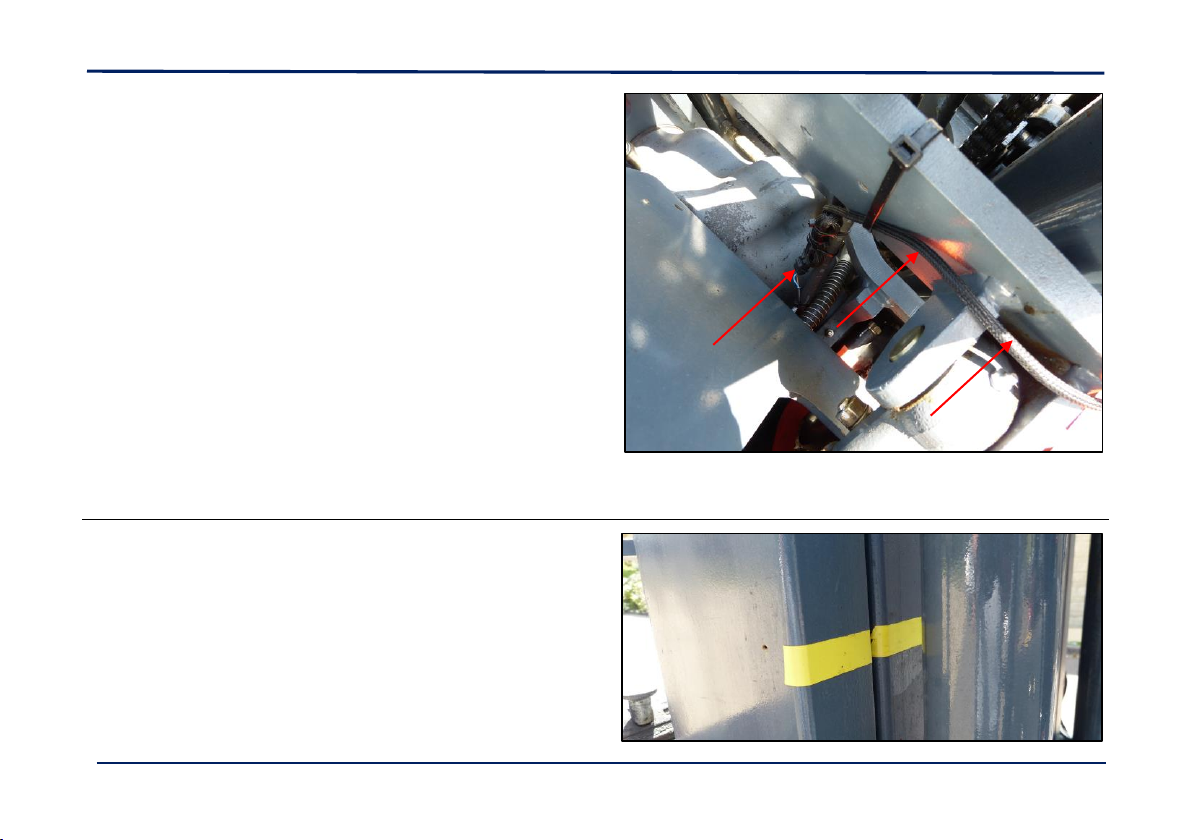
LIFTLOG 1000 –INSTALLATION AND CALIBRATION
16
Cable-tie the sensor lead to the bracket where shown.
Connect the sensor extension lead and route in conduit back
to the Terminator.
Cable tie at regular intervals and following the existing wiring
loom where possible.
Ref. 2.4.4 for wiring connections.
2.2.1 Weighing Height without Reference Sensor
The system can also be operated without a reference sensor.
In this case it is recommended to apply suitable markers on
the mast to indicate when the weighing position is reached.

LIFTLOG 1000 –INSTALLATION AND CALIBRATION
17
2.3 Head Unit
Mount the head to the front panel with the RAM mount as
shown.
NOTE: The head unit can also be mounted off the ROPS pillar using a
“U” Clamp kit (optional
The head unit is dust-tight and splash-resistant, however it is
not rated for constant outdoor use.
For use in an outdoor environment, it is recommended to
mount the unit within a suitable secondary enclosure or
cover (not provided), so that it is afforded adequate
protection from rain and moisture.
Route the head unit cable back to the Terminator. Coil excess
cable next to the Terminator.
Ref. 2.4.1 for wiring connections.

LIFTLOG 1000 –INSTALLATION AND CALIBRATION
18
2.4 Electrical
2.4.1 Junction Box
The Junction Box or "Terminator" as it is also known, provides
for connecting the 18-core head unit cable, all sensors and
the power supply.
The Terminator is not sealed. It must be located where it will
be protected from EXCESSIVE MOISTURE AND DIRT
Cable-tie the cables entering the end of the box to the PCB.
The Base Moulding can be mounted using the screws
provided, or can be left in-line with the cables.
Connect the head unit lead onto the PCB header
The red wire on the 10-way plug goes to pin "R" on the PCB
connector.
The orange/blue wire on the 8-way plug goes to pin "O/B" on
the PCB connector.
Locate the cable grommet onto the moulding, and cable-tie
the head unit lead onto the moulded cable saddle to provide
strain relief.
NOTE: Cable-tie the cables entering the end of the box to the PCB.

LIFTLOG 1000 –INSTALLATION AND CALIBRATION
19
2.4.2 Power Supply
NOTE: The Weightroller Precise operates from an 8 to 30VDC supply, however the solenoid on the drop valve is 12V. Therefore a suitable
voltage dropper must be fitted on vehicles using supply voltages above 12V.
The Terminator is fitted with a varistor for protection from voltage transients, and a power-on LED. The head unit has an integral
On-Off switch, but is normally powered on via the ignition circuit.
Using the power lead provided, connect from a switched live point not exceeding 24V (e.g. from the ignition circuit) to the
terminals marked POWER IN 0V and POWER IN+V.
If you inadvertently have the power supply connections reversed, nothing will work. The head unit has reverse polarity protection
and will not be damaged. The LED on the Terminator PCB will not light if the 0V and +V connections are reversed.
If the instrument does not power up when you switch the ignition on, then:
(a) check you have connected to a suitable point on the vehicle electrical system as described above.
(b) If (a) is OK but the LED is not lit, check the polarity is correct.
(c) If the LED is lit but the head unit does not come on, check that the 18-way connector is properly connected.
Once all is OK, clip the lid on the Terminator. To remove the lid, squeeze the sides of the base inward to release the clips.
2.4.3 Printer
Connect the printer lead onto the 4-way connector ('marked COM 2') in the terminal box. This lead also provides the printer
power supply.
Locate the cable grommet onto the moulding, and cable-tie the head unit lead onto the moulded cable saddle to provide strain
relief.

LIFTLOG 1000 –INSTALLATION AND CALIBRATION
20
2.4.4 Electrical Connections
Route sensor leads inside conduit back to the junction box. Cable-tie the conduit securely to existing hydraulic lines or conduits.
Connect the wires according to the label on the junction box lid :
Input / Output
Wire
Colour
Terminator Connection
Pressure Sensor (on
Drop valve)
Blue
10
"P1"
Brown
4
"P1 +V"
Drop Valve Solenoid
Blue
16
“DROP VALVE 0V”
Brown
6
“DROP VALVE + (BROWN)”
Reference Sensor
Blue
13
"0V"
Brown
20
"REF SENSOR (BROWN)"
Remote Enter
Switch
Blue
14
"REMOTE ENTER 0V (BLUE)"
Brown
9
"REMOTE ENTER SIG (BROWN)"
Remote Weigh
Button
Blue
15
“WEIGH BUTTON 0V (BLUE)”
Brown
18
“REMOTE WEIGH BUTTON (BROWN)”
External Alarm
Blue
13
“0V”
Brown
5
“EXTERNAL ALARM +VE (BROWN)”
Power Supply
Blue
12
“POWER IN 0V (BLUE)”
Brown
1
“POWER IN +V (BROWN)”
Other manuals for Liftlog 1000
1
Table of contents
Popular Forklift manuals by other brands
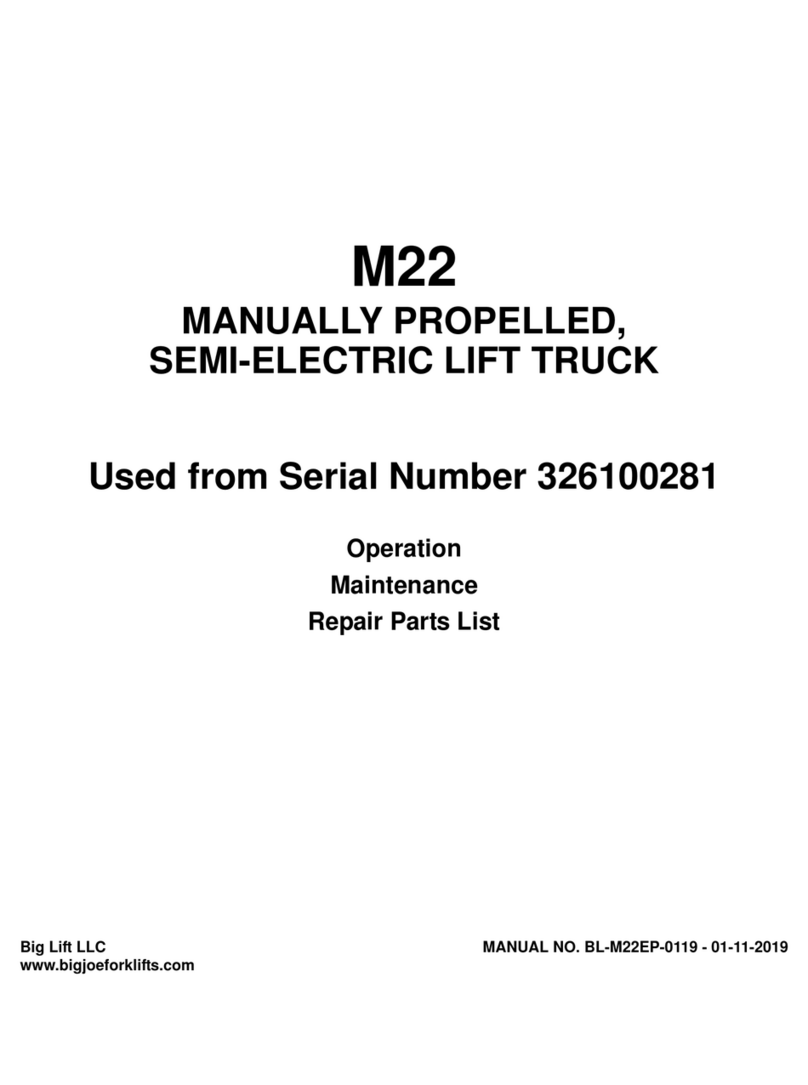
Big Joe
Big Joe M22 Installation, operation, maintenance & repair parts
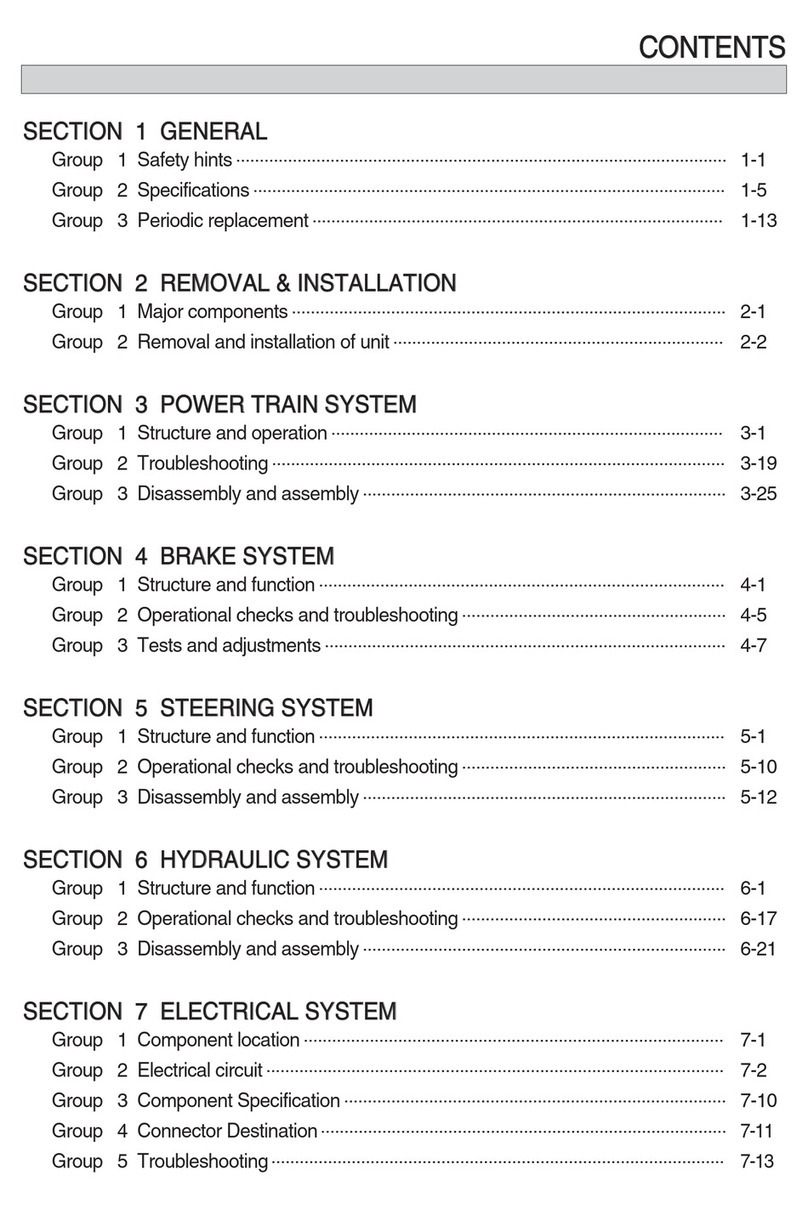
Hyundai
Hyundai 20DT-7 Operation manual
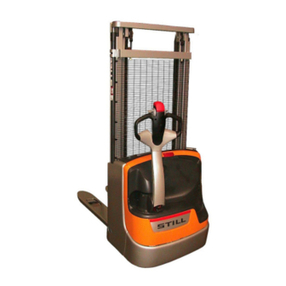
Still
Still EXV 10 Basic Original instructions

Noblelift
Noblelift FE4P44-77N Series Operation and maintenance manual
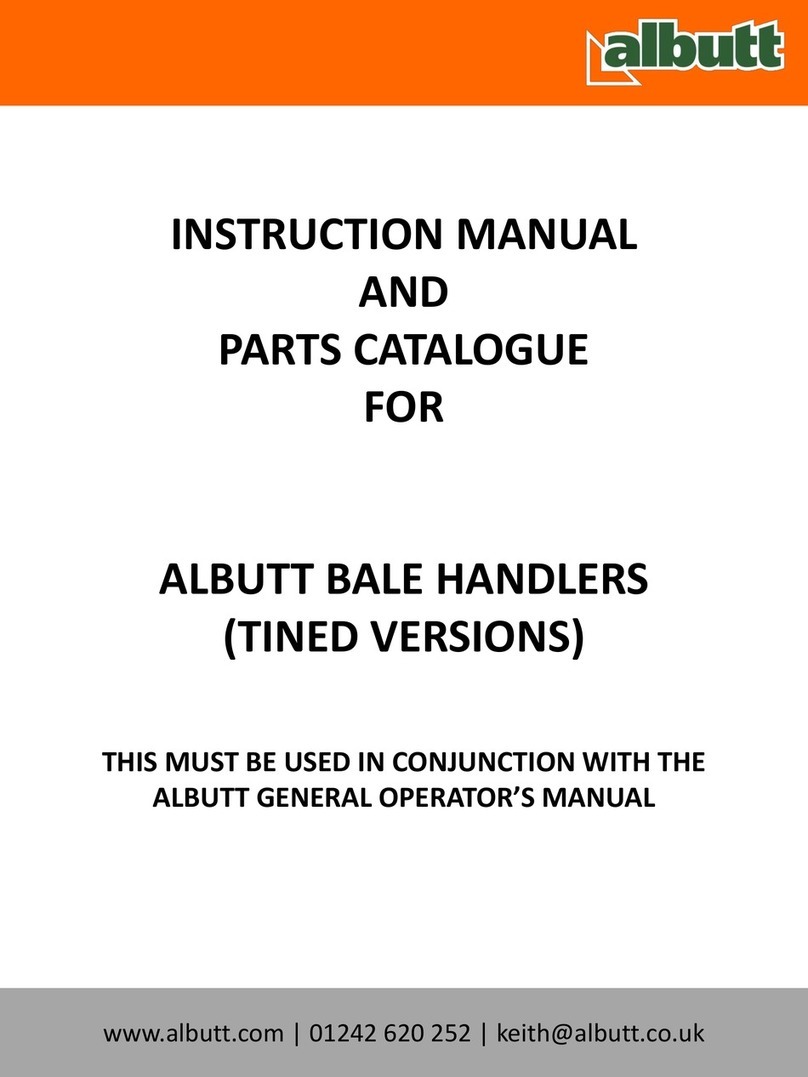
albutt
albutt F100 INSTRUCTION MANUAL AND PARTS CATALOGUE
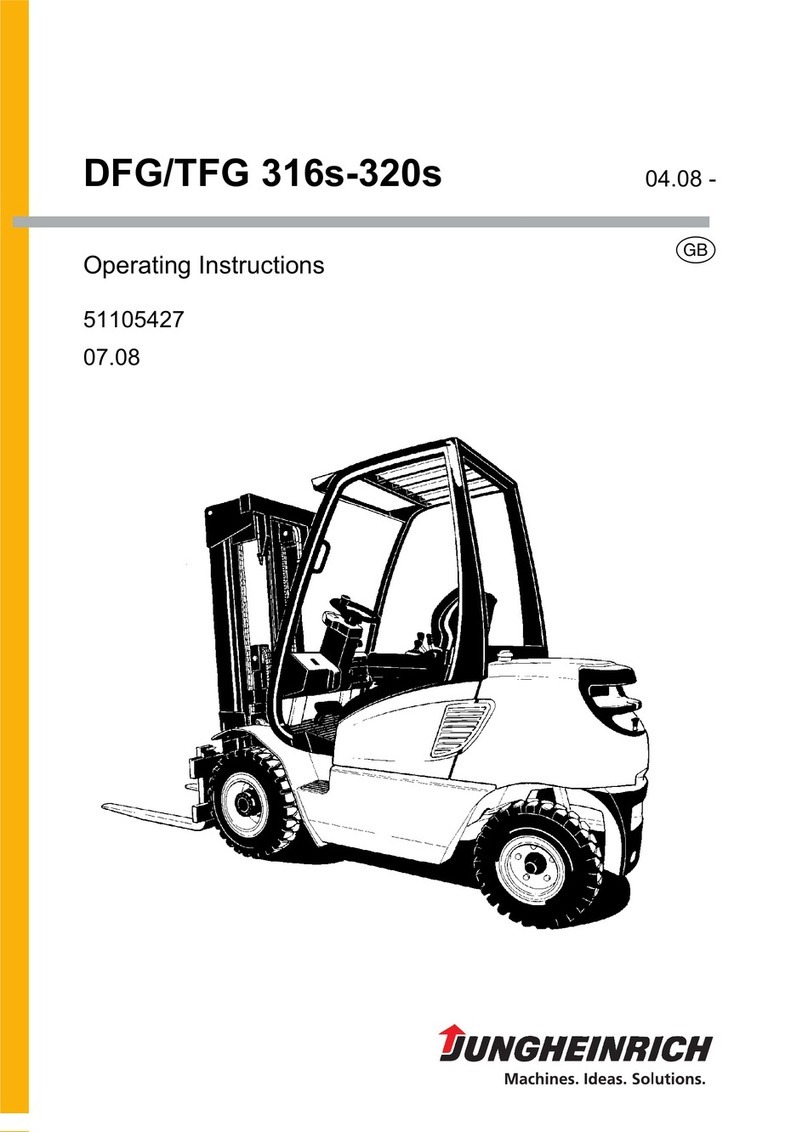
Jungheinrich
Jungheinrich DFG 316s operating instructions