Resol FlowCon C User manual

FlowConA
www.resol.de
Handbuch
RESOL FlowConC
Installation
Operation
Commissioning
Thank you for buying this RESOL product.
Please read this manual carefully to get the best performance from this unit.
FlowConC
www.resol.de
Manual
*48002500*
48002500
B

© RESOL 08255 flowcon_c.monen.indd
FlowConC
|2
Safety advice
Please pay attention to the following
safety advice in order to avoid danger
and damage to people and property.
Instructions
Attention should be paid to
- the statutory provisions for preven-
tion of industrial accidents,
- the statutory provisions for envi-
ronmental protection,
- the Health and Safety at Work Act
1974
- Part P of the Building Regulations
2005
- BS7671 Requirements for electrical
installations and relevant safety re-
gulations of DIN, EN, DVGW,TRGI,
TRF and VDE.
These instructions are exclusively
addressed to authorised skilled per-
sonnel.
- Only qualified electricians should
carry out electrical works.
- Initial installation must be effected
by qualified personnel named by the
manufacturer
Appropriate usage
The solar station with the integra-
ted controller may only be used in
the collector circuit of solar ther-
mal systems in compliance with the
technical data specified in these
instructions.
Improper use excludes all liability
claims.
Suject to changes. Errors excepted.
Declaration of conformity
We, RESOL Elektronische Regelungen GmbH, D-45527 Hattingen, declare under
our sole responsibility that our product FlowCon C complies with the following
standards:
EN 55 014-1
EN 60 730-1
According to the regulations of the above directives, the product is labelled with
:
89/336/EWG
73/ 23/EWG
Hattingen, 04.Juli 2007
RESOL Elektronische Regelungen GmbH,
ppa. Gerald Neuse
Scope of delivery:
1 x pump station FlowConC with inte-
grated controller DeltaSol
®C/1
1 x flushing and filling unit (optional)
1 x collector sensor FKP6
2 x store sensor FRP6
1 x wall mounting bracket
1 x accessory bag
2 x screw and dowl
2 x strain reflief
Table of contents
Safety advice.............................................................................................2
1. Pump station with integrated controller......................................... 3
Technical data station ........................................................................ 4
2. Mounting the station.......................................................................... 4
3. Commissioning ................................................................................... 5
3.1 Flushing and filling the solar thermal system.......................................5
3.2 Flushing the store for initial commissioning ........................................5
3.3 Flushing and filling the solar thermal system.......................................6
3.4 Emptying the solar thermal system .......................................................7
4. FlowCheck...........................................................................................7
5. AirStopp .............................................................................................. 7
6. Connection..........................................................................................8
7. Accessories for the station................................................................ 8
8. Integrated controller DeltaSol
®C/3 ..............................................9
Technical data controller...................................................................9
9. Installation.........................................................................................10
10. Examples ........................................................................................... 10
11. Terminal allocation........................................................................... 10
11.1 Terminal Allocation Arrangement 1.....................................................10
11.2 Terminal Allocation Arrangement 2.....................................................11
12. Operation and function ...................................................................11
12.1 Buttons for adjustment...........................................................................11
12.2 System Monitoring Display....................................................................12
12.2.1 Channel display.........................................................................................12
12.2.2 Tool bar.....................................................................................................12
12.2.3 System Screen...........................................................................................12
12.3 Flashing codes...........................................................................................13
13. Initial Commissioning ...................................................................... 14
14. Control parameter and diaplay channels....................................... 15
14.1 Channel overview....................................................................................15
14.2 Functions and options.............................................................................16
15. Electrical connection........................................................................20
16. Troubleshooting................................................................................21
17. Accessories for the controller.........................................................24
Imprint ..............................................................................................24

© RESOL 08255 flowcon_c.monen.indd
FlowConC
3 |
1. Pump station with integrated controller
• IntegratedcontrollerDeltaSol
®C/3
• Outstandingdesign
• Safetyassemblywithsafetyvalveand
manometer
• High-qualitycasingforreducedheatlosses
• FlowCheck
About this product
The pump station FlowCon C is a preinstalled and leak-te-
sted group of fittings for transferring heat from the collector
to the store. It contains important fittings and safety devices
for the operation of the solar thermal system:
•Ballvalvesinowandreturnincombinationwithcheck
valves to prevent gravity circulation
•Airstoppformanualbleedingofthesolarthermalsystem
•FlowCheckfordisplayingtheowrate
•Manometerfordisplayingthesystempressure
•Safetyvalvetopreventinadmissibleoverpressure
•Flushingandllingunit(optional)forushing,llingand
emptying the solar thermal system
The installation and commissioning of the solar station as
well as the connection of electrical components requires
technical knowledge commensurate with a recognised
vocational qualification as a fitter for plumbing, heating and
air conditioning technology, or a profession requiring a com-
parable level of knowledge.The following must be observed
during installation and commissioning:
•therelevantregionalandnationalregulations
•theaccidentpreventionregulationsofthetradeassociation
•thetechnicalandsafetyinstructionsoftheseinstructions
Warning: Risk of scalding
There is a danger of steam emission with safety valves.
Therefore a discharge pipe must be connected to the ¾“
internal thread of the safety assembly. Please observe the
enclosed instructions regarding the safety valve when doing
this.
Attention: Damage to property
The group of fittings must be installed with sufficient spacing
to the collectors because temperatures in the vicinity of the
collectors can be very high.An intermediate vessel may be
necessary for installation in the attic.
Attention: Damage to property
It is imperative that you make sure the EPDM sealing ele-
ments of the solar station do not come into contact with
substances containing mineral oil. Mineral oil products
cause lasting damage to the material, whereby its sealant
properties are lost.
If necessary, ask the manufacturer whether the solar fluid,
fats or installation aids contain mineral oils.
We do not assume liability nor provide warranty for damage
to property resulting from sealants damaged in this way.
Safety instructions
Scope of delivery:
1 x pump station FlowCon C with
integrated controller DeltaSol
®
C/1
1 x flushing and filling unit (optional)
1 x collector sensor FKP6
2 x store sensor FRP6
1 x wall mounting bracket
1 x accessory bag
2 x screw and dowl
2 x strain reflief

© RESOL 08255 flowcon_c.monen.indd
FlowConC
|4
Dimensions:
Height (with insulation): 417 mm
Width (with insulation): 374 mm
Depth (with insulation): 179 mm
Distance centre: 1600 mm
Distance axis/wall:55 mm
Pipe connections: ¾" IT
Connection for expansion vessel set:
3/4" ET, flat sealing
Outlet safety valve: 3/4" IT
Equipment:
Safety valve: 6 bar
Manometer: 0 - 6 bar
Non-return valves:
Opening pressure 200 mm water column,
openable
Material:
Fittings: brass
Seals: EPDM
Insulation: EPP, l= 0,041 W/(m*K)
Technical Data:
Max. permitted pressure: 6 bar
Max. operating temperature: 120°C
Flow rate: 1-20 l /min
160 mm
55 mm
thermometer
flow
thermometer
return
FlowCheck
controller
DeltaSol
®C/3
pump
Airstopp
flushing and
filling unit
(optional)
safety
assembly
manometer
2. Mounting the station
• Determinethemoutingsiteofthestation.
• Takethestationoutofthepacking.Removethefront
half of the insulation.
• Holdtheenclosedwallmountingbracketagainstthe
wall and mark the fastening holes, drill holes and insert
dowels
• Fastenthewallmountingbrackettothewallwiththe
screws.
• Pushthestationagainstthewallmountingbracket.The
station catches and is then attached to to the wall.
• Connectthestationtothesolarthermalsystem.
• Checktheinletpressureoftheexpansionvesseland,
if necessary, adjust it to the local conditions
(P inlet[bar] = 1 bar + DTh [m]*1/10 (DTh = height
difference between collector and station)
• Connect the electrical components of the solar
station: Attach the store and collector sensor and
connect these to the controller. Plug the controller
into a socket.
• Tighten all union nuts and screw connections.
• Attachthefronthalfoftheinsulationtothestation.

© RESOL 08255 flowcon_c.monen.indd
FlowConC
5 |
fig.2
3.1 Flushing and filling the solar thermal
system
Attention: Risk of scalding!
To prevent the solar fluid boiling in the collectors, the
system should not be flushed or filled during periods of
strong sunshine.
Attention: Risk of frost!
Solar thermal systems cannot be completely emptied after
flushing.There is a danger of frost damage if water is used
for flushing. Only use solar fluid to flush and fill the solar
thermal system.
Use a water-propylene glycol mixture as a solar fluid (ma-
ximum 50% propylene glycol).
Instructions for initial commissioning:
The optionally enclosed flushing and filling unit can either
be integrated into the station (below theAirStopp,mounted
by 30° outwards, see fig.2) or installed horizontally at the
lowest point of the solar circuit (see fig.1).
In both cases a filter must be installed between the store
and the solar pump in order to prevent the flushed-out scale
from re-entering the solar circuit.
If the flushing and filling unit is integrated in the solar station,
we recommend an additional fill and drain ball valve at the lo-
west point of the solar circuit, to flush possible scale out.
This flushing process is described in “3.2 Flushing the store
for initial commissioning”.Then continue as described in“3.3
Flushing and filling the solar thermal system”.
3.2 Flushing the store for initial
commissioning
3. Commissioning
• Connectthepressurehoseofaushingandlling
station to the fill ball valve.
• Connecttheushinghoseofaushingandllingstation
to the fill and drain valve at the lowest point of the solar
thermal system.
• Closetheballvalve
• Openthellballvalve(5)andthellanddrainvalve
at the lowest point of the solar thermal system.
• Flushthesolarthermalsystembymeansoftheushing
and filling station until the discharged solar fluid is free
of dirt particles.
• Switchoffthellingpump
• Closethellanddrainvalveatthelowestpointofthe
solar thermal system.
• Removetheushinghosefromthellanddrainval-
ve.
• Closethellballvalve
• Connecttheushinghosetothedrainballvalve.
fig.1

© RESOL 08255 flowcon_c.monen.indd
FlowConC
|6
3.3 Flushing and filling the solar thermal
system
• Disconnecttheexpansionvesselfromthesolar
thermal system.
• Connectthepressurehoseofaushingandlling
station to the fill ball valve (5) of the flushing and filling
unit.
• Connecttheushinghoseofaushingandllingsta-
tion to the drain ball valve (3) of the flushing and filling
unit.
• Closetheballvalve(4)inthecentreoftheushingand
filling unit
• Turntheballvalvesinow(1)andinreturn(2)with
an open-ended spanner (wrench width 14) to a 45°
position. The non-return valves in the ball valves are
now open.
•Open the fill and drain ball valves (3 and 5).
• Flushthesolarthermalsystemusingtheushingand
filling station for at least 15 minutes to remove all air
from the system.
• Duringushing,bleedthesolarthermalsystemseveral
times at the Airstopp until the discharged solar fluid is
free of air bubbles.
• Closethedrainballvalve(3)oftheushingandlling
unit with the filling pump running and increase the
system pressure to approx. 5 bar.The system pressure
can be read from the manometer
• Closethellballvalve(5)andswitchoffthepumpof
the flushing and filling station.
• Checkthemanometertoseewhetherthesystem
pressure reduces and eliminate leaks where necessary.
• Reconnecttheexpansionvesseltotheothercompo-
nents of the solar thermal system.
If it is necessary to set the pressure, observe the
following step:
• Settheoperatingpressureofthesolarthermalsystem
by means of the flushing and filling station (0.3-0.5 bar
higher than the inlet pressure of the expansion ves-
sel).
• Ifyouhaveputtheflushingandfillingstationinto
operation to set the operating pressure, switch off the
filling pump.
• Closethellanddrainballvalvesandopentheball
valve.
• Removethehosesoftheushingandllingstationand
screw the caps onto the fill and drain ball valves.
• Putthenon-returnvalvesinowandreturninopera-
ting position by opening the ball valves with an open-
ball valve: 45°
non-return valve
not operating
flow-through in both
directions
ball valve: 90°
ball valve closed, no
flow-through
ball valve: 0°
non-return valve
in operation, flow-
through only in flow
direction
ended spanner (wrench width 14).
• Manuallyputthesolarthermalpumpinoperationat
the highest RPM level (see controller manual) and let
it circulate for at least 15 minutes
• Duringushing,bleedthesolarthermalsystemseveral
times at the Airstopp, until the discharged solar fluid is
free of air bubbles and increase, if required, the system
pressure to the operating pressure.
3
4
5
1 2

© RESOL 08255 flowcon_c.monen.indd
FlowConC
7 |
• Openthenon-returnvalvesintheballvalvesinow
and return by turning the ball valves to a 45° position
with an open-ended spanner.
• Placeatemperature-resistantcollectioncontainer
under the drain ball valve at the lowest point of the
solar thermal system.
• Openthedrainballvalveatthelowestpointofthe
solar thermal system.
• Openthebleedingdevicesatthehighestpointofthe
solar thermal system, where available
• Disposeofthesolaruidinobservanceoflocalregu-
lations.
3.4 Emptying the solar thermal system
WARNING!
Risk of injury.The discharged fluid can have very high
temperatures. Place the collection container so that
people standing near by are not endangered when the
solar thermal system is being emptied.
4. FlowCheck The FlowCheck is for measurement and display of the
flow rate of 1-20 l/min. In order to guarantee the flawless
function of the measuring device the system must be flushed
and free from foreign substances.
The Airstopp (manual bled valve) is for bleeding the solar
fluid in the solar thermal system.The air precipitated from
the solar fluid gathers in the upper area of the manual bleed
valve (see diagram) and can, if required, be discharged at
the bleeding valve. To guarantee faultless bleeding of the
collector circuit the flow rate in the flow must be at least
0.3 m/s.
Check the system pressure after bleeding and if necessary
increase it to the specified operating pressure.
5. Airstopp
WARNUNG:
Risk of injury caused by very high temperatures. During
bleeding the escaping air and solar fluid can reach tempe-
ratures of over 100 °C.
Bleeding the solar thermal system directly after
commissioning
At first you should bleed the solar thermal system daily
and then weekly or monthly, depending on the volume of
discharged air., in order to achieve optimal efficiency.
Information for operators of solar thermal
systems
Bleed the solar thermal system half-yearly with the manual
bleed valve to achieve optimal efficiency..
Left scale:
Upper edge of
the propeller
Right scale:
Lower edge of
the propeller

© RESOL 08255 flowcon_c.monen.indd
FlowConC
|8
For further information on electrical connection, of
the controller, please see chapter 15.
6. Connection
The controller is already integrated in the station and ready
to plug in. In the case of maintenance or service work, the
controller is to be taken out from the station. Please pay
attention to the followong steps:
• switchoffthesystem,disconnectplugfromthemains
• removethefronthalfoftheinsulation
• unscrewthecross-recessedscrewoffthefrontcoverand
remove it by pulling it upwards
• unscrewthelowercross-recessedscrew,pushthecon-
troller upwards and remove it.
Mounting of the controller has to be carried out in reverse
order.
WARNING!
Always disconnect the controller
from power supply before ope-
ning the housing!
7. Accessories for the station
For installation screw connections are required, which are
not included in the scope of delivery. Self-sealing double
nipples, solder nipples or clamp-ring connections can be
used. For further information, please see product catalo-
gue.

© RESOL 08255 flowcon_c.monen.indd
FlowConC
9 |
• System-Monitoring-Display
• upto4temperaturesensors
Pt1000
• heatquantitymeasurement
• functioncontrol
• user-friendlyoperation
through simple handling
• solaroperatinghourscounter
and thermostat function
• RESOLVBus®
• Realtimeclock
Technical data controller
Housing:
plastic, PC-ABS and PMMA
Protection type: IP 20 / DIN 40050
Ambient temp.: 0 ... 40 °C
Dimensions: 172 x 110 x 46 mm
Mounting: integrated in the pump
station FlowConC
Display: system monitor for system
visualisation,16-segment display, 7-seg-
ment display, pictograms
Operation: 3 push buttons at the
front of the housing
Functions: Differential temperature
controller with optional add-on system
functions. Function control according
to BAW-guidelines, operating hours
counter, tube collector function, ther-
mostat function and heat quantity
measurement
Inputs: for 4 temperature sensors
Pt1000
Outputs: 2 standard relays
Bus: RESOL VBus®
Power supply: 220 ... 240 V~
Total switching capacity:
4 (2) A (220 ... 240) V~
Mode of operation: Type 1.b
Switching capacity per relay:
Electromechanical relay:
2 (1) A (220 ... 240) V~
110
30
62
172
46
The controller DeltaSol
®C/3
is integrated into the pump station
FlowCon C standard solar thermal
systems and ready to plug in.
8. Integrated controller DeltaSol
®C/3
Electrostic discharge can cause da-
mage to electronic components.
High-voltage components.

© RESOL 08255 flowcon_c.monen.indd
FlowConC
|10
9. Installation
10. Examples DeltaSol
®C/3
standard solar system solar system
with afterheating
S1
S2
S4 / TRF
11.2. Terminal allocation Arr 1 Standard solar system with 1 store, 1 pump and 3 sen-
sors. The sensor S4 / TR can be optionally used for heat
quantity measurement.
R1
ARR1
S3 Symbol Specification
S1 collector sensor
S2 store base sensor
S3 store top sensor,
(optional)
S4 / TRF sensor for heat quantity
measurement (optional)
R1 solar pump
Note:
The controller is already integrated in the station and rea-
dy to plug in. In the case of maintenance work and repair,
pay attention to chapter 14 ‚Electrical connection‘!
11. Terminal allocation

© RESOL 08255 flowcon_c.monen.indd
FlowConC
11 |
R2
S1
S2
R1 S3
S4 / TRF
Solarsystemandafter-heatingwith 1 store, 3 sensors
and after-heating.The sensor S4 /TRF can be optionally used
for heat quantity balancing.
ARR 2
11.2 Clamp allocation Arr 2
Symbol Specification
S1 collector sensor
S2 store base sensor
S3 store top sensor /
thermostat sensor
S4 / TRF sensor for heat quantity
measurement (optional)
R1 solar pump
R2 pump for afterheating
1
2
3
backwards
SET
(selection-/
adjustment
mode)
12. Operation and function
12.1 Buttons for adjustment When the hydraulic system is filled and ready for operation,
connect the controller to the mains.
Switch on power supply. After initialisation, the controller
is in the automatic mode with typical settings. Now the
controller is ready for operation with typical settings to suit
that system and normally the factory settings will give close
to optimum operation
The controller is operated by means of the 3 push buttons
below the display. Button 1 is used for scrolling forward
through the menu or to increase the adjustment values.
Button 2 is similarly used for scrolling backwards and redu-
cing values. Button 3 is used for selection of the menu lines
and for confirmation.
In order to access the adjustment mode, scroll down in the
diplay menu and press the forward button (1) for approx.
2 seconds after you have reached the last diplay item. If an
adjustment value is shown on the display, the „SEt“ icon
is displayed. Now, you can access the adjustment mode by
using button 3.
• Pressbuttons1and2inordertoselectachannel
• Brieypressbutton3, willl flash ( -mode)
• Adjustthevaluebypressingbuttons1and2
• Brieypressbuttons3,sothat permanently appears,
the adjusted value will be saved.
forward

© RESOL 08255 flowcon_c.monen.indd
FlowConC
|12
The system monitoring display consists of 3 blocks:channel
display, tool bar and system screen (active arrange-
ment).
The channel display consists of two lines.The upper line
is an alpha-numeric 16-segment display (text display) for
displaying channel names and menu items. In the lower
7-segment display, the channel values and the adjustment
parameters are displayed.
Temperatures and temperature differences are indicated
in°C or K respectively.
12.2.1Channel display
channel display
12.2.2Tool bar
The additional symbols in the tool bar indicate the actual
system status.
tool bar
12.2System-Monitoringdisplay
Complete Monitoring-Display
The system screen (active arrangement) shows the scheme
which has been selected. The screen consists of several
system component symbols, which are - depending on the
current status of the system - either flashing, permanently
shown or „hidden“.
12.2.3System screen
system screen
Symbol standard flashing
relay 1 active
relay 2 active
store maximum limitation
active / maximum store
temperature exceeded
collector cooling function or
recooling function active
antifreeze- function activated collector minimum limitation
or antifreeze function active
collector emergency shutdown
or store emergency shutdown
active
+ sensor defect
+ manual operation active
SET-mode, change of adjust-
ment value is possible

© RESOL 08255 flowcon_c.monen.indd
FlowConC
13 |
sensor
collector 1
pump
Sensor
Zusatzsymbol
Brennerbetrieb
store
store heat exchanger store 2 or afterheating
(with additional symbol)
store top sensor
Collector
with collector sensor
Pumps
Store 1
with heat exchanger
Afterheating
mit Brennersymbol
Temperature sensors
12.3 Flashing codes •Pump symbols are flashing during initialisation phase
•Sensor symbols are flashing if the corresponding sensor
display channel is selected.
•Sensor symbols are flashing in the case of a sensor fault.
•Burner symbol is flashing if the after-heating is active

© RESOL 08255 flowcon_c.monen.indd
FlowConC
|14
1
3
2backwards
forwards
SET
(selection /
adjustment
mode)
1.Switch on power supply.After initialisation, the controller
is in the automatic mode with typical settings. The pre-
programmed system scheme is Arr 1.
2. - select adjustment channel Arr
- change to the -mode (see 2.1)
- select the arrangement via the Arr-index number
- save the adjustment by pressing the button
Now the controller is ready for operation with typical set-
tings to suit that system and normally the factory settings
will give close to optimum operation.
Overview of arrangements:
Arr 1 : standard solar system
Arr 2 : solar system with after-heating
Arr 1 Arr 2
13.Commissioning
When the controller is commissionend for the first time, the arrangement has to
be selected first

© RESOL 08255 flowcon_c.monen.indd
FlowConC
15 |
14. Control parameters and display channels
14.1 Overview of channels
Legend:
x
Corresponding channel is available.
x*
Corresponding channel is available when the corresponding
option is enabled
Only if the option heat quantity measurement is activated
(OHQM), will the corresponding channel be available.
MEDT
Only if an antifreeze (MEDT) other than water orTyfocor
LS/G-LS(MEDT0or3) is used, will the channel anti-
freeze concentration (MED%) be displayed.
Only if the option heat quantity measurement is deactiva-
ted (OHQM), will the corresponding channel be available.
Please note:
Only if temperature sensors are connected, will S3 and S4
be displayed.
channel Arr description page
1 2*
COL x x Temperature collector 1 16
TST x Temperature store 1 16
TSTL x Temperature store 1 base 16
TSTU x Temperature store 1 top 16
S3 x Temperature sensor 3 16
TRF Temperature return sensor 16
S4 Temperature sensor 4 16
h P x Operating hours relay 1 16
h P1 x Operating hours relay 1 16
h P2 x Operating hours relay 2 16
kWh Heat quantity kWh 17
MWh Heat quantity MWh 17
time clock time 16
Arr 1-2 Arrangement
DT O x x Switch-on temperature difference 17
DT F x x Switch-off temperature difference 17
S MX x x Maximum temperature store 1 18
EM x x Emergency temperature collector 1 18
channel Arr description page
1 2
OCX x x Option collector cooling collector 1 18
CMX x* x* Maximum temperature collector 1 18
OCN x x Option minimum limitation
collector 1
18
CMN x* x* Minimun temperature collector 1 18
OCF x x Option antifreeze collector 1 19
CFR x* x* Antifreeze temperature collector 1 19
OREC x x Option recooling 19
O TC x x Option tube collector 19
AH O x Switch-on temp. for thermostat 1 19
AH F x Switch-off temp. for thermostat 1 19
t1O x Switch-on time 1 thermostat 19
t1F x Switch-off time 1 thermostat 19
t2O x Switch-on time 2 thermostat 19
t2F x Switch-off time 2 thermostat 19
t3O x Switch-on time 3 thermostat 19
t3F x Switch-off time 3 thermostat 19
OHQM x Option heat quentity measurement 17
FMAX Maximum flowrate 17
MEDT Antifreeze type 17
MED% MEDT MEDT Antifreeze concentration 17
HND1 x x Manual operation relay 1 20
HND2 x x Manual operation relay 2 20
LANG x x Language 20
PROG XX.XX Program number
VERS X.XX Version number

© RESOL 08255 flowcon_c.monen.indd
FlowConC
|16
Collector temperature
Display of the current collector temperature.
•COL : collector temperature (1-collector system)
COL:
Collector temperature
display range: -40 ...+250 °C
Store temperatures
Display of the current store temperature.
•TST : store temperature (1-store system)
•TSTL : store base temperature,
• TSTU : store top temperature
TST,TSTL,TSTU:
Store temperatures
Display range: -40 ...+250 °C
Sensor 3 and sensor 4
Display of the current temperature at the corresponding
additional sensor (without control function).
•S3 : temperature - sensor 3
•S4 : temperature - sensor 4
Please note:
Only if the temperature sensors are connected (dis-
played), will S3 and S4 be displayed.
S3, S4:
Temperatures at the sensors
S3 and S4
Display range: -40 ...+250 °C
Other temperatures
Display of the current temperature at the sensor.
•TRF : temperature - return
TRF:
other measured temperatures
Display range: -40 ...+250 °C
Operating hours counter
h P / h P1 /h P2:
Operating hours counter
Display channel
The operating hours counter accumulates the solar opera-
ting hours of the respective relay (h P / h P1 / hP2). Full
hours are displayed.
The accumulated operating hours can be set back to zero.
As soon as one operating hours channel is selected, the sym-
bol is displayed. Press the SET (3) button for approx. 2
seconds in order to access the RESET-mode of the counter.
The display symbol will flash and the operating hours
will be set to 0. Confirm the reset with the button in
order to finish the reset.
In order to interrupt the RESET-process, do not press a
button for about 5 seconds. The display returns to the
display mode.
14.2 Functions and options
Time
In this channel the current time is indicated.
Press button for 2 seconds, the hours will then be
displayed. Press the button againg, the minutes will then be
displayed (flashin).The time can be set using buttons 1 and
2 and saved by pressing the button.

© RESOL 08255 flowcon_c.monen.indd
FlowConC
17 |
Heatquantitymeasurementoption
OHQM:Heat quantity
measurement
Adjustment range: OFF ...ON
Factory setting: OFF
Heat quantity measurement is possible if a flowmeter is
used. For this purpose, the heat quantity measurement
option (OHQM)has to be enabled.
The flow rate should be read from the flowmeter (l/min)
and has to be adjusted in the channel FMAX. Antifreeze
type and concentration of the heat transfer medium have
to be adjusted in the channels MEDT and MED%.
Antifreeze type:
0 : water
1 : propylene glycol
2 : ethylene glycol
3 : Tyfocor®LS / G-LS
FMAX:
Flow rate in l/min
Adjustment range 0 ... 20
in 0,1-steps
Factory setting: 6,0
kWh/MWh: Heat quantity
in kWh / MWh
Display channel
MEDT: Antifreeze type
Adjustment range: 0 ...3
Factory setting: 1
MED%: Antifreeze concen-
tration (Vol-) %
When MEDT 0 or 3 is used,
the parameter MED% is
‚hidden‘.
Adjustment range: 20 ...70
Factory setting: 45
The flow rate as well as the reference sensors S1 (flow) and
S4 (return) are used for calculating the heat quantity sup-
plied. It is shown in kWh in the channel kWh and in MWh
in the channel MWh.The overall heat quantity results from
the sum of both values.
The accumulated heat quantity can be reset. As soon as
one of the display channels of the heat quantity is selected,
the symbol is permanently shown on the display. Press
button SET (3) for about 2 seconds in order to access the
RESET mode of the counter.The display symbol will
flash and the heat quantity value will be set to 0. In order to
finish this process, press the button to confirm.
In order to interrupt the RESET process, no button should
be pressed for about 5 seconds.The controller automatically
returns to the display mode.
DT-regulation
Please note: Switch-on temperature difference DO must
be at least 1 K higher than the switch-off temperature-
difference DF.
DT O:
Switch-on temperature diff.
Adjustment range: 1,0...20,0 K
Factory setting: 6.0
DT F:
Switch-off temperature diff.
Adjustment range
0,5 ... 19,5 K
Factory setting 4.0 K
This function is a standard differential control.If the switch-
on differential is reached (DT O), the pump is operated.
If the temperature difference falls below the adjusted
switch-off temperature difference (DT F), the controller
switches off.
Maximum store temperature If the adjusted maximum temperature is exceeded, the store
will no longer be loaded in order to avoid damage caused by
overheating. If the maximum store temperature is exceeded,
will be shown.
Please note:The controller is equipped with a store emer-
gency shutdown function, which prevents the store from
being loaded when the store temperature exceeds 95 °C.
S MX:
Maximum store temp.
Adjustment range: 2..95 °C
Factory setting: 60 °C

© RESOL 08255 flowcon_c.monen.indd
FlowConC
|18
Collector emergency shutdown temperature If the adjusted collector emergency shutdown temperature
(EM) is exceeded, the controller will switch off the solar
pump (R1) in order to protect the system against overheating
(collector emergency shutdown). The factoring setting is
140 °C but it can be changed within the adjustment range
of 110 ...200 °C. (flashing) is displayed.
EM:
Collector emergency shut-
down temperature
Adjustment range:
110 ... 200 °C
Factory setting: 140 °C
CMX:
Collector maximum temp.
Adjustment range:
100 ...190 °C
Factory setting: 120 °C
System cooling When the adjusted maximum store temperature is reached,
the system stagnates. If the collector temperature increases
to the adjusted maximum collector temperature (CMX) ,
the solar pump is activated until the collector temperature
falls below the maximum collector temperature.The store
temperature may increase (subordinate active maximum
store temperature), but only up to 95 °C (emergency shut-
down of the store).
OCX:
System cooling option
Adjustment range: OFF ... ON
Factory setting: OFF
If OREC is additionally enabled: If the store temperature is higher than the maximum store
temperature (S MX) and if the collector temperature is at
least 5 K below the store temperature, the solar system
remains activated until the store is cooled down below the
adjusted maximum temperature (S MX) via the collector
and the pipework.
If the system cooling function is enabled, (flashing) is
shown on the display. Due to the cooling function, the sy-
stem will have a longer operation time on hot summer days
and guarantees thermal relief of the collector field and the
heat transfer fluid.
CMN:
Minimum collector tempe-
rature
Adjustment range: 10 ... 90 °C
Factory setting: 10 °C
Minimum collector function
OCN:
Mimimum collector function
Adjustment range: OFF / ON
Factory setting: OFF
The minimum collector temperature is the minimum
temperature which must be exceeded for the solar pump
(R1) to switch on.The minimum temperature prevents the
pump from being switched on too often at low collector
temperatures. If the temperature falls below the minimum
temperature, (flashing) is shown on the display.
CFR:
Antifreeze temperature
Adjustment range: -10 ...10 °C
Factory setting: 4,0 °C
Antifreeze function
OCF:
Antifreeze function
Adjustment range: OFF / ON
Factory setting: OFF
The antifreeze function activates the loading circuit between
the collector and the store when the temperature falls be-
low the adjusted antifreeze temperature. This will protect
the fluid against freezing or coagulating. If the adjusted anti-
freeze temperature is exceeded by 1 °C, the loading circuit
will be deactivated.
Please note:
Since this function uses the limited heat quantity of the store,
the antifreeze function should be used in regions with few
days of temperatures around the freezing point.

© RESOL 08255 flowcon_c.monen.indd
FlowConC
19 |
Recooling function If the adjusted maximum store temperature (S MX) is
reached, the controller keeps the solar pump running in
order to prevent the collector from being overheated.
The store temperature may increase but only up to 95 °C
(emergency shutdown of the store).
The solar pump is switched on once the collector
temperature is lower than the store temperature. It is
switched off when the store is cooled down to the adjusted
maximum temperature via the collector and the pipework.
OREC:
recooling function option
Adjustment range:
OFF ...ON
Factory setting: OFF
Tube collector function If the controller detects an increase in collector temperature
by 2 K compared to the previously stored collector
temperature, the solar pump will be switched-on for
about 30 seconds in order to detect the fluid temperature.
The current collector temperature will be saved as a
new reference value. If the measured temperature (new
reference value) is exceeded by 2 K, the solar pump will
run for 30 seconds. If the switch-on difference between the
collector and the store is exceeded during the runtime of
the solar pump or the standstill of the system, the controller
will automatically switch to solar loading.
If the collector temperature deacreases by 2 K during
standstill, the switch-on value for the tube collector function
will be recalculated.
O TC:
Tube collector function
Adjustment range:
OFF ...ON
Factory setting: OFF
The thermostat function works independently from the
solar operation and can be used for using surplus energy
or for after-heating.
• AH O < AH F
thermostat function for after-heating
• AH O > AH F
thermostat function for using surplus energy
When the 2nd relay output is active, is displayed.
Thermostat function (Arr = 2)
after-heating use of surplus energy
AH O:
Thermostat switch-on temp.
Adjustment range:
0,0 ...95,0 °C
Factory setting: 40,0 °C
AH F:
Thermostat switch-off temp.
Adjustment range:
0,0 ...95,0 °C
Factory setting: 45,0 °C
t1 E, t2 E, t3 E:
Thermostat switch-on time
Adjustment range:
00:00 ...23:45
Factory setting: 00:00
t1 A, t2 A, t3 A:
Thermostat switch-off time
Adjustment range:
00:00 ...23:45
Factory setting: 00:00
In order to block the thermostat function for a certain pe-
riod of time, there are 3 time frames t1 ...t3. If the function
should be activated only between e.g. 6:00 and 9:00, set
t1 E to 6:00 and t1 A to 06:00.The thermostat function is
continuously activated (factory setting).
If all time frames are set to 00:00 o’ clock, the thermostat
function is continuously activated (factory setting).

© RESOL 08255 flowcon_c.monen.indd
FlowConC
|20
15. Electrical connection
The power supply to the controller must be carried out via
an external power switch (last step!) and the supply voltage
must be 220 ... 240V~ (50 ... 60 Hz). Flexible cables must be
attached to the housing with the enclosed strain relief and
the corresponding screws.
The controller is equipped with 2 standard relays to which
loads such as pumps, valves, etc. can be connected:
•Relay1
18 = conductor R1
17 = neutral conductor N
13 = ground clamp
•Relais2
16 = conductor R2
15 = neutal conductor N
14 = ground clamp
Temperature sensors (S1 to S4) have to be connected
to the following terminals (either polarity):
1 / 2 = Sensor 1 (e. g. sensor collector 1)
3 / 4 = Sensor 2 (e. g. sensor store 1)
5 / 6 = Sensor 3 (e. g. sensor S3)
7 / 8 = Sensor 4 (e. g. sensor TRF)
The mains connection is at the terminals:
19 = neutral conductor N
20 = phase L
12 = ground clamp
mains terminals
fuse
load terminals
sensor terminals ground terminals
WARNING!
Always switch-off power supply
and disconnect the controller
from the mains before opening
the housing!
For control and service work, the operating mode of the
controller can be manually adjusted. For this purpose, select
the adjustment value HND1 / HND2.The following adjust-
ments can be carried out:
Operating mode
• HND1 / HND2
Operating mode
OFF : relay off (flashing) +
AUTO : relay in automatic operation
ON : relay on (flashing) +
HND1 / HND2:
Operating mode
Adjustment range:
OFF,AUTO, ON
Factory setting:AUTO
Language
In this channel, different languages are available.
• dE : German
•En : English
• It : Italiano
• Fr : French
LANG:
Language choice
Adjustment range:
dE, En, It, Fr
Factory setting: En
Electrostatic discharge can lead to damage to elec-
tronic components!
Dangerous voltage!
VBus
910
Table of contents
Popular Heat Pump manuals by other brands
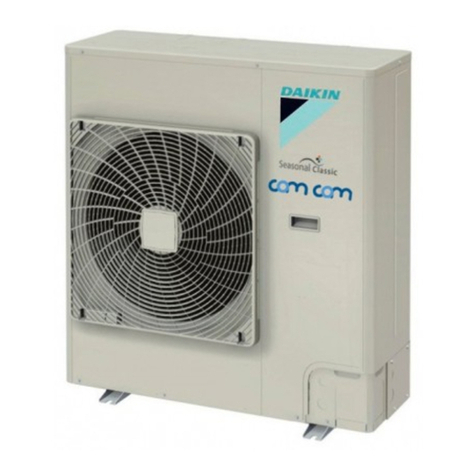
Daikin
Daikin GQI-Eco Series Service manual
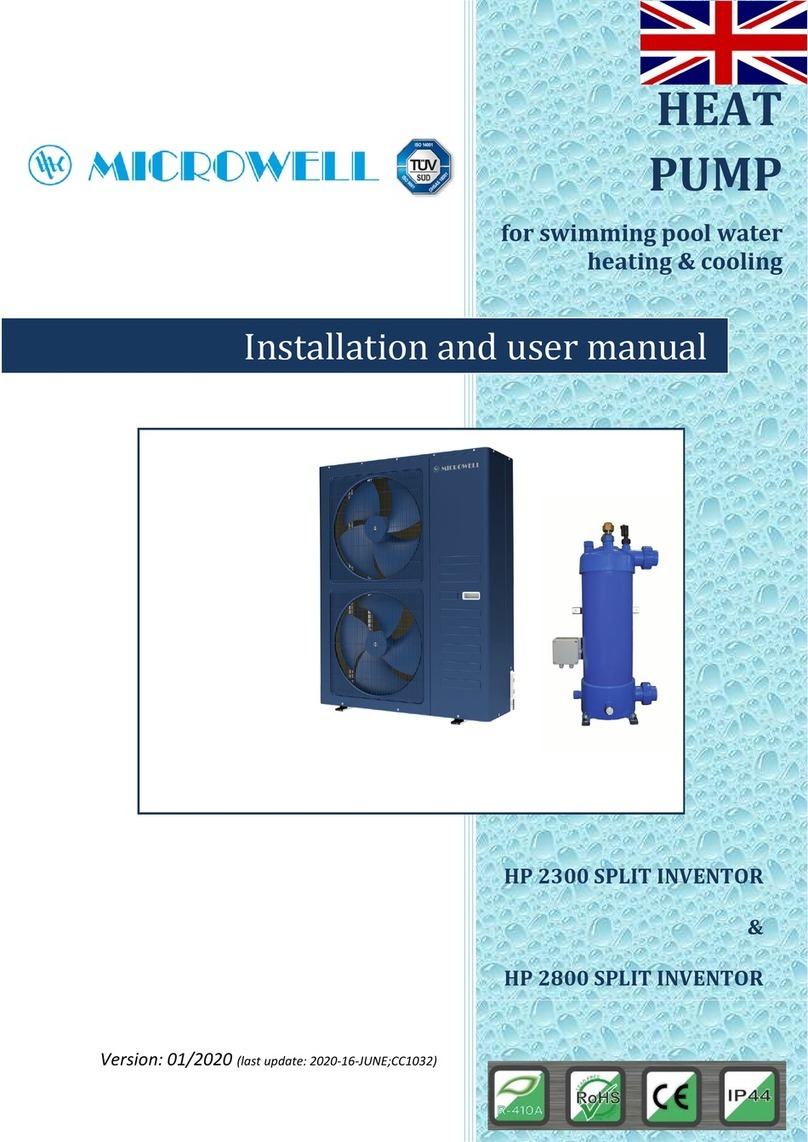
MICROWELL
MICROWELL HP INVENTOR 2300 SPLIT Installation and user manual

Panasonic
Panasonic WH-MDC07H3E5 installation manual
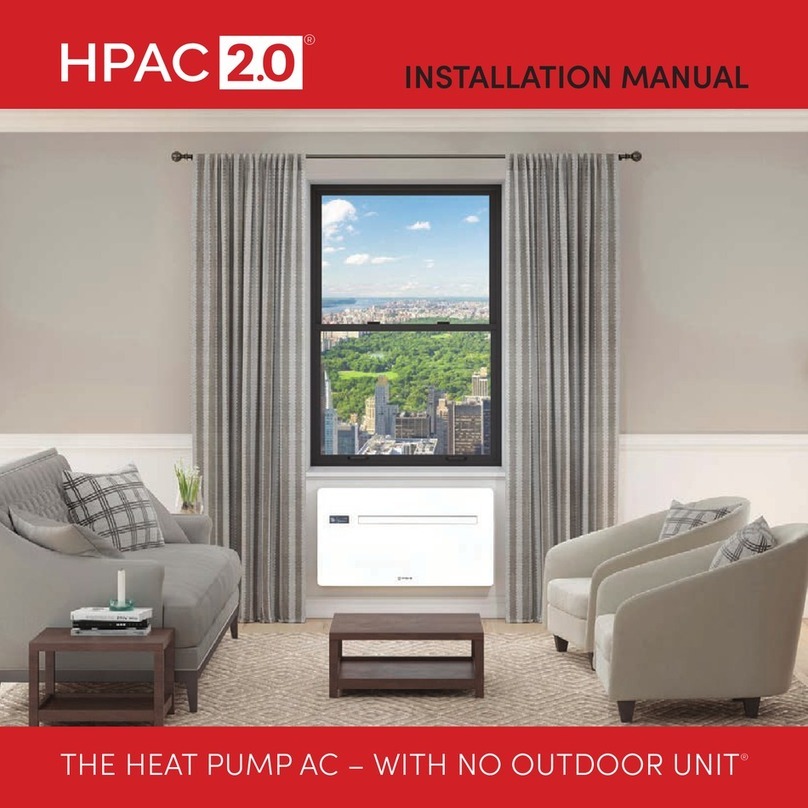
Ephoca
Ephoca HPAC 2.0 installation manual
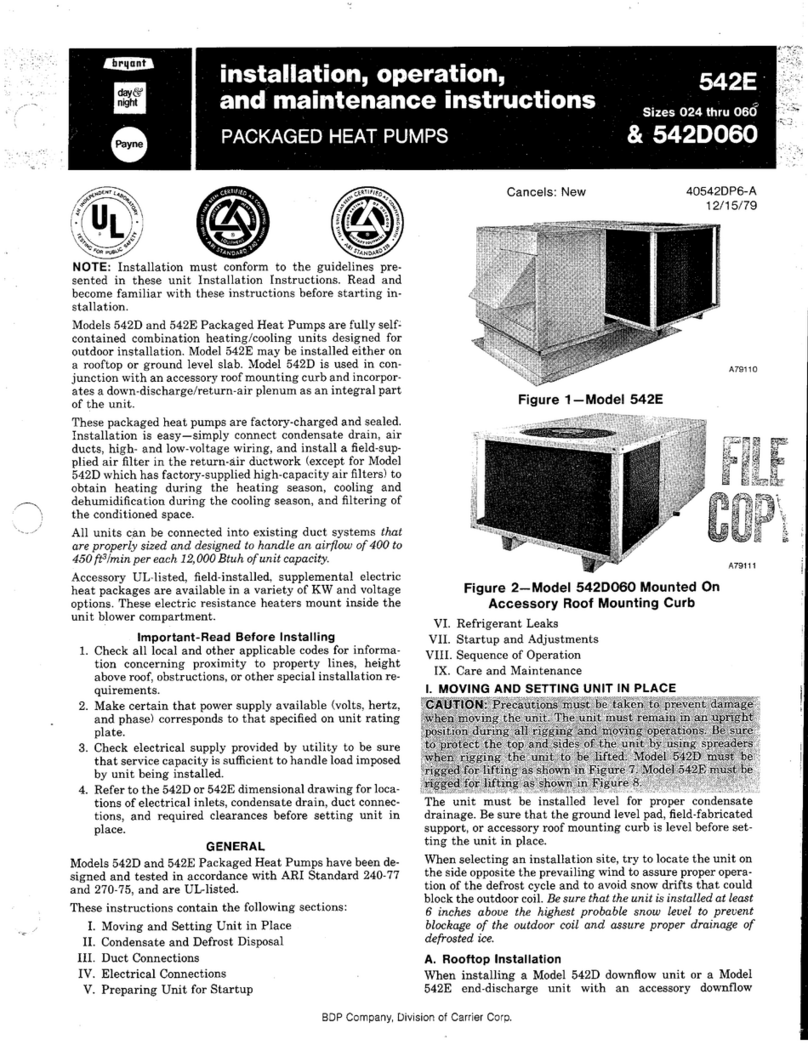
Bryant
Bryant 542D060 Installation, operation and maintenance instructions
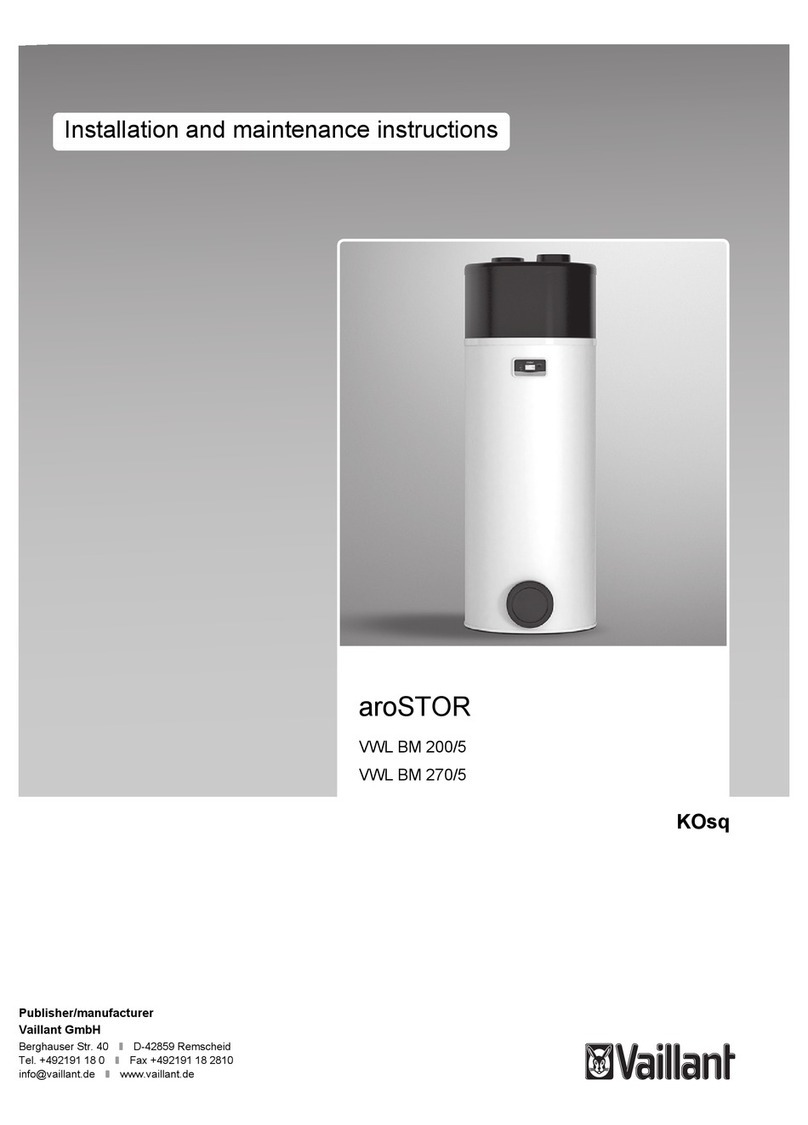
Vaillant
Vaillant aroSTOR VWL BM 270/5 Installation and maintenance instructions

Mitsubishi Electric
Mitsubishi Electric Ecodan PUHZ-W50VHA-BS Service manual

Zodiac
Zodiac POWER FORCE 25 Instructions for installation and use
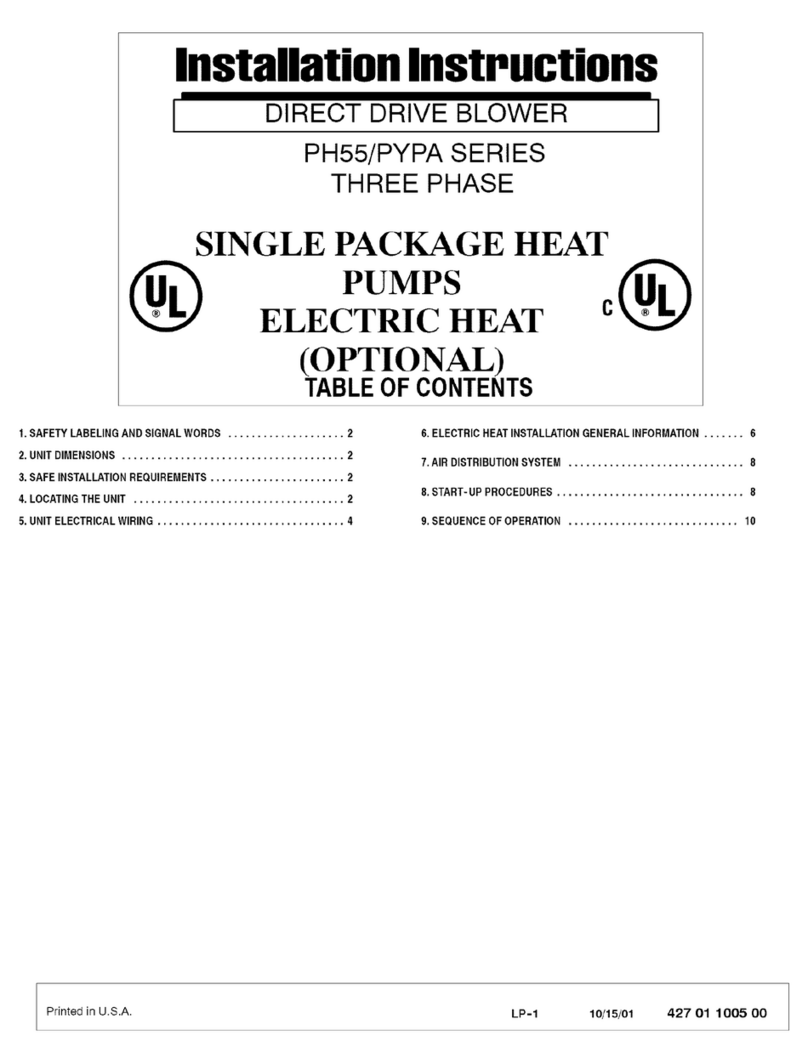
ICP
ICP PYPA Series installation instructions

Nibe
Nibe F730 Installer manual

Sakura
Sakura SXAO-110HAS Installation and service manual
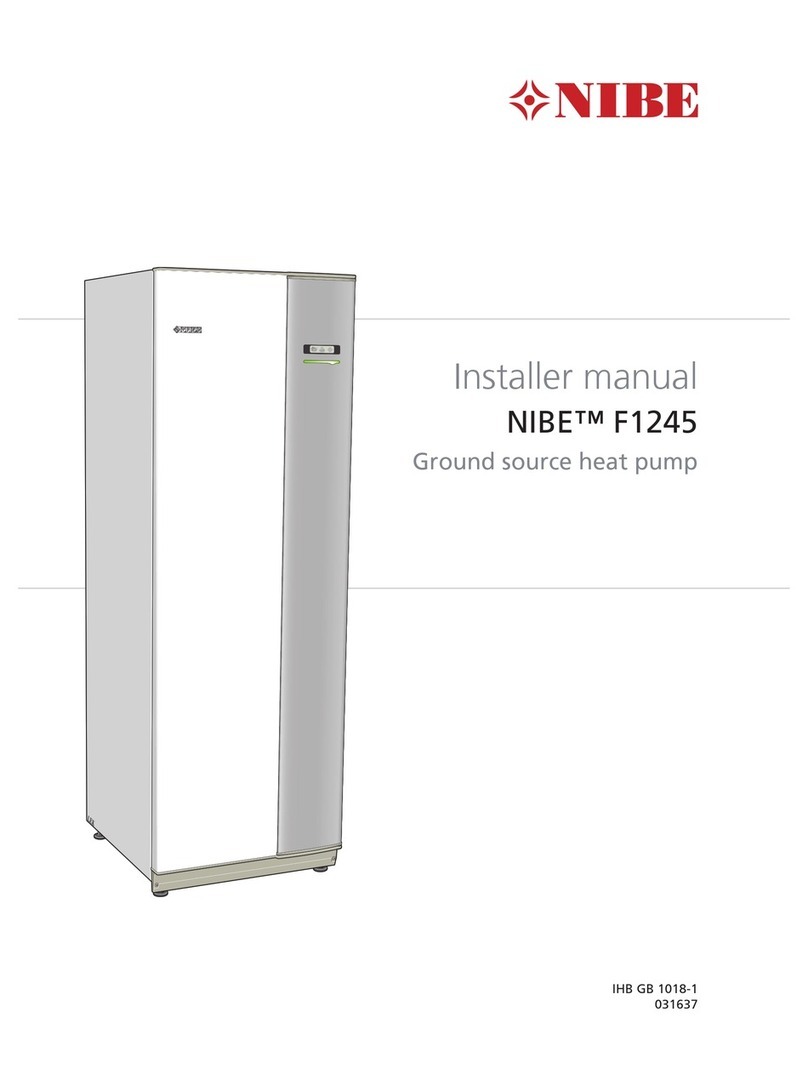
Nibe
Nibe F1245 Installer manual