Rhymebus RM5G User manual

RM5G
Series
RHYMEBUS INVERTER
AC MOTOR CONTROLLER

Pre-quality Satisfied Service
(KP-201C)
Analog Keypad
(KP-202C)
Digital Keypad
http://www.rhymebus.com.tw
V1.1 2004.9 Revised
http://www.rhymebus.com.tw
RHYMEBUS CORPORATION
.
V1. 2004.6.9 Revised
1
0
RHYMEBUS CORPORATION V1 .0 2004 .1 .9
V1 .62007.1Revised

Thank you for choosing the RHYMEBUS " RM5G Series "high-function,
inverter. This instruction manual gives information on installation,wiring,
parameter unit operation, etc. as well as maintenance and inspection
procedures. However, it is essential to read this manual carefully to use
the equipment safely, correctly, and to it's full capability. Please forward
this manual to the end user.
FOR FOREWORD

Please read this manual thoroughly prior to installation, wiring, operation,
maintenance and trouble shooting. Also, any statement and symbol
denoted by "DANGER" or "CAUTION" should be read carefully.
DANGER : Indicate dangerous cases that accompany the
possibility of death or serious injury caused by
erroneous handling not in accordance with manual.
CAUTION :Indicate dangerous cases that accompany the
possibility of medium or light injury or material
damage caused by erroneous handling not in
accordance with manual.
*Note : that although CAUTION indicate
medium or light injury or material damage
can be caused, there is possibility of serious
injury.
Note :
that installation, wiring, operation and trouble shooting can be performed
only by experienced peoples who know the principles, constructions,
properties and operational procedures of inverter, can prevent damages,
and read this manual completely.
SAFETY PRECAUTIONS

• Low noise
• High torque
• Automatic voltage regulation
• User friendly
• Restart after instantaneous power interruption
• 9 levels for speed settings and 5 independent acc/dec time settings
• 6 digits display
• Programmable inputs and outputs
• Store and copy settings by using KP-201C digital keypad
• Connect to the external indicators for displaying the status of inverter
• Energy saving
• RM5G series apply to the constant torque loaded; RM5P series apply to the
variable torque loaded.
• Low noise
Using IGBT by which the maximum switching frequency of sinusoidal PWM
is 10kHz to 15kHz, the motor is operated smoothly and efficiently with low noise.
• High torque
At low speed, the torque compensation by which the compensated torque can be
above 150% of rated torque is provided for smooth start in the case of heavy
load.
• Automatic voltage regulation (AVR)
In spite of the fluctuation of power source, output voltage of inverter can be kept
at the desired level.
• User friendly
There are two types of operating keypad, one for advanced applications and the
other for usual use. User can choose one of them to function inverter easily and
properly. Besides, the connector between inverter and keypad is the same as that
of telephone. The remote control is then easily realized with maximum distance
of 25 m.
• Restart after instantaneous power interruption
If the power source is shutdown during running, the functions of recording the
speed of motor before power interruption and resuming that after restart are
provided.
INTRODUCTIONS
Features
dB
Ordinary
Ordinary
inverter
Current waveform(at 10Hz)
RM5G
RM5G(IGBT)
( rpm / min)
Motor speed
0 500 1000 1500 1800
80
70
60
50
40
30

• 9levels for speed settings and 5 independent acc/dec time settings
There are 5 independent acc/dec time settings in the 9 steps speed level. The
setting range is 0.0~3200.0 seconds. Speed from 0Hz to 60Hz , the minimum
acceleration time is 0.015 sec.(except free running), the maximum acceleration
time is 19200000 sec. (about 222 days).
• 6 digits display
There are 8 status of inverter can be displayed (frequency, speed, voltage,
current , etc).
• Programmable inputs and outputs
There are 17 functions programmed by using input terminals X1~X6 and 12
functions programmed by output terminals, Y1 and Y2 (open collector), and
two relay output.
• Connect to the external indicator for displaying the status of inverter
There are 3 external indicators(96mm x 48mm, 5 digits)can be used
simultaneously to indicate the inverter status such as frequency, speed, voltage,
current, and line velocity etc. Therefore, it is not needed to use the other
instruments or sensors such as CT etc., and the cost and wiring will be reduced.
• Energy saving
Under the light load condition, the less energy is outputted for the purpose of
saving energy.
• Store and copy settings
The settings can be stored in KP-201C and download to other inverter . This
function is useful in the case of several inverters with the same data settings. If
any alarm occurs during copy, the keypad will show “Wr_F” and copying will
stop.
Note: Check the version of software(F_000) first, only the same version
software inverter then it can be do the store and copy setting function.
Store inverter
parameters to
KP-201C
Factory setting
rd_EE Wr_EE
Write KP-201C
parameters to
inverter
Factory setting

CHAPTER 1 INSPECTIONS AT PURCHASE
(1) Confirmation of product ·································································1
(2) Standard specifications ···································································2
CHAPTER 2 INSTALLATIONS AND CONFIRMATIONS
(1) Basic setup ······················································································4
(2) Environment ···················································································4
(3) Descriptions of terminals and wiring diagram ·······························6
(1) Digital keypad (KP-201C) ····························································17
(2) Analog keypad (KP-202C) ···························································17
CHAPTER 4 OPERATIONS OF KEYPADS
(1) Settings of digital keypad (KP-201C) ··········································18
(2) Settings of analog keypad (KP-202C) ··········································23
CHAPTER 5 LIST OF FUNCTION CODE SETTINGS ·················26
CHAPTER 6 DESCRIPTIONS OF FUNCTION CODE SETTINGS
(1) Settings of keypad ········································································33
(2) Multiple speed level settings ························································37
(3) Acc/dec time of multiple speed level············································39
(4) V/F pattern settings ·······································································41
(5) Analog input commands ·······························································43
(6) Upper and lower bound of output frequency·································45
(7) Analog outputs ··············································································46
(8) Settings for motor protection·························································47
(9) Multiple function input terminals ·················································48
(10) Settings of multiple function outputs ··········································54
(11) Frequency detection ····································································59
(12) Gain of the torque boost ·····························································59
(13) Settings of overload detection ····················································60
(14) Settings of stall prevention ·························································61
(15) DC braking ·················································································62
(16) Resumption after instantaneous power interruption ···················63
(17) Jump of frequency ······································································64
(18) Speed tracking ············································································65
CONTENTS
CHAPTER 3 TYPES OF KEYPADS

(19) Settings of creep ·········································································65
(20) External indicators ······································································66
(21) Miscellaneous·············································································67
(22) Settings of KP-202C analogkeypad ···········································69
CHAPTER 7
OPERATIONAL PROCEDURES, MAINTENANCE, AND
TROUBLE SHOOTING
(1) Operational procedure and operations ··········································72
(2) Fault, maintenance and trouble shooting ······································73
APPENDIX A
(1) Outline drawings ···········································································75
(2) Auxiliary control equipment (ACE series) ···································79
(3) Dynamic brake and resistor ··························································80
(4) Selections of motor ·······································································82
(5) Selections of AC reactor (ACL) ···················································83
APPENDIX B
(1) Remote controllers ········································································84
(2) Remote indicators DM-501 ··························································87
APPENDIX 1
DIMENSIONS OF OPENING OF KP-201C AND KP-202C ··········90
APPENDIX 2 SETTINGS MEMO ·····················································91
APPENDIX 3 FAULT DISPLAY ·······················································95
APPENDIX C
(1) Connect braking resistor ·······························································88
(2) Connect D.B.unit 89
·········································································

CHAPTER 1 INSPECTIONS AT PURCHASE
- 1 -
(1) Confirmation of product
Although this product is under a rigorous quality control, the damages
may be made by impact and vibration etc. during transportation.Upon
unpacking of the inverter at site, please check the follows accordingly.
If there is any defect, contact your local dealer at once.
A. Confirmation of appearance
Is there any damage, filth or distortion to the appearance of
inverter?
B. Do the rated capacity and specification shown on nameplate
confirm to your requirements?
RHYMEBUS CORPORATION
INPUT
OUTPUT
PGM No.
SERIAL No.
TYPE RM5G-2015B
3PH 200~240V 50/60Hz
0-400Hz 11KW 46A
Pxxxxx
8021520
8021520
Output current & capacity
Version of software
Serial number
Input power source specification
Model number
C. Model number scheme:
B0152RM5G -
Series Type :
Indicate 380/415/440/460V/480V
Indicate 200/220/240V
Brake type (with internal braking transistor
which is the standard for the inverter with
rated power less than15HP,200Vclass and
20HP,400V class.These standard brake type is
not indicated in the nameplate of the inverter.)
RM5G - G TYPE
4:
2:
015 :
B :
RM5P - P TYPE
Rated power(15HP)
D. Confirmation of accessories
Generally, there is one user's manual. If there are some accessories,
such as braking resistor and AC/DC reactor etc., are ordered please
check inclusively.
E. Please refer to the standard specifications and confirm to your
requirements.
AC
06/07/21, 19:43

~INSPECTIONS AT PURCHASE~
- 2 -
(2) Standard specifications
A. Specification
—
—
—
—
4
42
0
445
585
—
—
—
—
4
30
0
316
415
—
—
—
—
4
25
0
287
377
—
—
—
—
4
20
0
60
232
304
0
160
405
4
17
5
193
253
132
346
4
15
0
165
210
115
295
4
12
5
134
176
84
220
4100
104
150
67
175
4075
84
110
55
145
4
06
0
66
87
44
115
IP00 (IP20 OPTION)
4
05
0
56
73
IP00 (IP20 OPTION)
33
90
4
04
0
46
61
28
74
4
03
0
34
45
22
60
4
02
5
5
30
39
18
46
4
02
0
23
30
13
33
4
01
5
18
24
25
3
,200 ~ 240V,50/60Hz
4010
14
18
17
4007
10
14
2
11
4
00
5
9
2002
2/1.5
3
8
4003
3/2.2
4
6
2001
1/0.75
2
5
4002
2/1.5
3.3
4
2001
2
0.5/0.4
1.3
3
3
200 ~ 240V
0.01 ~ 400.00Hz
1
/3
,200~
240V,50/60Hz
176 ~ 264V,50/60Hz
±5%
IP20
4001
1/0.75
1.9
2.5
3
380 ~ 480V
0.01 ~ 400.00Hz
3
,380 ~ 480V,50/60Hz
332 ~ 528V,50/60Hz
±5%
IP20
RM5G-200V Series
Series No. (RM5G)
Rated power of the motor
(HP/KW)
Rated continuous output
p
ower ( KVA)
Rated continuous output
current ( A)
Rated output voltage (V)
Range of output
f
requency
Power source
(
,V, Hz)
Tolerance of power
s
ource voltage
Tolerance of frequency
f
luctuation
Construction protected
RM5G-400V Series
Series No. (RM5G)
Rated power of the motor
(
HP/KW)
Rated continuous output
p
ower ( KVA)
Rated continuous output
c
urrent (A)
Rated output voltage (V)
Range of output
f
requency
Power source
(
,V, Hz)
Tolerance of power
s
ource voltage
Tolerance of frequency
f
luctuation
Construction protected
2
15
2
12
5
2
10
0
2075
2060
2
05
0
2
04
0
2
03
0
2
02
5
2
02
0
2
01
5
2
01
0
2007
2005
5/3.7
6
00
3
3/2.2
4
7.5/5.5
9
10/7.515/11 20/15
20/18.5
30/2240/30 50/37 60/45 75/55
125/90
150/110
100/75
5/3.7
7
7.5/5.5 10/7.5 15/11 20/15
25/18.5
30/22 40/30 50/37 60/45 75/55 100/75
125/90
150/110 175/132 200/160 250/200 300/220 420/315
PH
PH
PH
PH
PH
PH
PH
PH

~INSPECTIONS AT PURCHASE~
- 3 -
B. Common specification
User interface Digital and analog operating keypads with remote control.
Control
characteristics Voltage vector sinusoidal PWM control.
Range of frequency
control RM5G: 0.1 ~ 400.00Hz / RM5P: 0.1~120.00Hz
Resolution of
frequency setting Digital keypad: 0.01Hz, Analog keypad: 0.06/60Hz
Resolution of output
frequency 0.01Hz
Analog voltage of
frequency setting DC 0 ~ 10V (20KΩ),4 ~ 20mA (500Ω)
Overload current RM5G type: 150% inverter rated current output for 1 minute
RM5P type: 120% inverter rated current output for 1 minute
steps acceleration/
deceleration times Zero sec for free running, 0.1 ~ 3200 seconds for each setting
Braking torque About 20% (For the inverter rated power less than 10 hp, the braking
transistor is included, and braking torque can be about 100%)
V/F pattern The pattern can be set arbitrarily.
Control characteristics
Stall prevention The current of stall prevention can be set arbitrarily
Start and
direction control
FWD/REV control by terminals or by using 3–line sustaining circui
t
M
ultiple functio
n
inputs
Stop command by using the 3-line sustaining circuit, jogging
operation, secondary acc/dec time, multiple-level speed command
1~3, reset, command for fault conditions, command of inhibiting
output ,command of stop by free running, command of frequency
search from the max. frequency, command of frequency search from
the set frequency, acc/dec inhibition command, UP/DOWN
command ,UP/DOWN frequency command clear/enter analog input
select, DC braking enable, current limit enable, primary and
secondary speed select
Input
Analog inputs
Vin-GND(0 ~ 10V)、Iin-GND(4 ~ 20mA)
Multiple function
Running, constant speed, zero speed, frequency detection, overload
detection, stall prevention, under voltage, braking, restart after
instantaneous power interruption, restart after trouble shooting,
fault conditions, programmable contacts a and b.
Operational characteristics
Output
Analog outputs
Analog voltage, DC 0~10 V with adjustable gain, for representing
output frequency, frequency setting, or output current
Displays of keypad
Output frequency, frequency settings, output voltage, DC voltage,
output current, motor speed, line velocity of motor, status of terminals
D
ispla
ys
Displays of external
indicators
There are 3 external indicators (96mm x 48mm, 5 digits) can be used
simultaneously to indicate the frequency, speed, voltage, current,
and line velocity etc.
Fault Display
Over current (OC), over voltage (OE), under voltage (LE),
motor overload (OL), inverter overload (OL1), over heat (OH),
ground fault current(GF), fuse open (SC),
disconnection of KP-202C during running (PAdF).
Diagnostics Disconnection of digital keypad (Err_00, Err_01), EEPROM error (EEr)
Protections
Cooling Force cooling (natural cooling for rated power of 1/2 and 1 HP)
Environment Non-corrosive non-conductive, or non-explosive gas or liquid, and
non-dusty.
Temperature -10℃(14℉) ~+50℃(122℉),non-freezing and non-condensing
Storage temperature
-20℃(-4℉) ~+60℃(140℉)
Relative humidity
90% RH or less (non-condensing atmosphere)
Vibration Lessthan5.9m/sec (0.6G)
Ambient conditions
Altitude Less than 1000m (3280 ft)
2

CHAPTER 2 INSTALLATIONS AND CONFIRMATIONS
- 4 -
(1) Basic setup
The inverters have to be incorporated with some elementary devices
for driving motor. The essentially elementary devices of basic setup are
A. Power source
The power source should be agreed with the specifications of
Inverter.
B. No fuse brake (NFB)
The rating of NFB should be greater than the start current.
C.
Inverter
This is main device of driving motor. Referring to the lists of
standard specifications of inverter, inverter is chosen in
accordance with the specifications of motor driven.
D. Motor
The specifications of motor are determined from the requirement
of applications.
(2) Environment
For correct and safety operation, the operational environment of
inverter should be cared and described as followings
A.
Power source
The power source should be agreed with the specifications of
inverter.
B. Location
For the considerations of heat generated by the operating machine,
inverter has to be installed in the ventilate space. The installations
of inverter are shown as followings.
a. The space of installation is good for power dissipation or not
10cm
or more
5cm
or more
5cm
or more
10cm
or more

~INSTALLATIONS AND CONFIRMATIONS~
- 5 -
b. The cooling is needed if the inverter is installed in an enclosure.
c. If the inverter is installed in an enclosure (suitable for 7.5~420 hp)
and the cooling system is on or outside enclosure, it should be
mentioned that the hole for airflow is adequate or not.
C.
Specifications of the associated accessories
The specifications of the associated accessories have to be in
accordance with the specifications of inverter used. Otherwise, the
inverter will be damaged and the lifetime of inverter will be
decreased.
Fan
Fan RM5G/5P
Inverter
Air Filter
Control
circuits Heat
sink
Panel control Box
Panel control Box
Fan
Fan
RM5G/5P
Inverter
Control
circuits Heat
sink
Ventilation hole
Air Filter

~INSTALLATIONS AND CONFIRMATIONS~
- 6 -
D. Cleaning of environment
The ventilation, cleanliness and moisture of the space in which the
inverter is installed have to be considered.
E. Operator
Only experienced peoples can perform operation and trouble
shooting.
(3) Descriptions of terminals and wiring diagram
A. Wiring diagram
Note that the terminals represented by and are denoted for main
and control circuits, respectively.
a. Wiring diagram for 1/2~5 HP(200V class)/1~5HP(400V class)
※Built-in brake transistor
Terminals of main circuit
3-phase power source
(Single-phase connect
to R,S)
Forward
Vin frequency command
(DC 0~10V)
Induction motor
Grounding
Analog signal
output
(DC 0~10V)
Multi-function
output terminals
(relay output)
(AC 250V/0.5A
COSθ=0.3)
Multi-function
output terminals
(open collector)
(DC 48V/50mA)
RM5G/5P
R
S
T
R
S
T
FWD
REV
Tc1
Tb1
Ta1
Tc2
Ta2
GND
FM+
AM+
U
V
W
PE
P
PR
Braking Resistor(option)
IM
VR 1KΩ,1/4W
DSW1
I
V
P
P
P
Shielded
P
Terminals of control circuit
Reverse
Multi-function input terminal 1
Multi-function input terminal 2
Multi-function input terminal 3
Multi-function input terminal 4
Multi-function input terminal 5
Multi-function input terminal 6
Iin frequency command
(DC 4~20mA)
X1
X2
X3
X4
X5
X6
COM
12V(3)
Vin(2)
Iin
GND(1)
Y1
Y2
CME
Twisted-pair shielded wires

~INSTALLATIONS AND CONFIRMATIONS~
- 7 -
b. Wiring diagram for 7.5~15HP(200V class)/7.5~20 HP(400V
class)
※Built-in brake transistor
※Switch the DIP switch DSW1 on the control board.
“ I ” side: mean Iin-GND inputting current command.
(Factorysetting)
“V” side: mean Iin-GND inputting voltage command.
The setting range set by F_126.
Terminals of main circuit
3-phase power source
(single-phase connect
to R,S)
Forward
Vin frequency command
(DC 0~10V)
Induction motor
Grounding
Analog signal
output
(DC 0~10V)
Multi-function
output terminals
(relay output)
(AC 250V/0.5A
COSθ=0.3)
Multi-function
output terminals
(open collector)
(DC 48V/50mA)
RM5G/5P
R
S
T
R
S
T
FWD
REV
Tc1
Tb1
Ta1
Tc2
Ta2
M-
FM+
AM+
U
V
W
PE
P
PR
Braking Resistor(option)
IM
VR 1KΩ,1/4W
DSW1
I
V
PP P
Shielded P
Terminals of control circuit
Reverse
Multi-function input terminal 1
Multi-function input terminal 2
Multi-function input terminal 3
Multi-function input terminal 4
Multi-function input terminal 5
Multi-function input terminal 6
Iin frequency command
(DC 4~20mA)
X1
X2
X3
X4
X5
X6
COM
12V(3)
Vin(2)
Iin
GND(1)
Y1
Y2
CME
Twisted-pair shielded wires
N

~INSTALLATIONS AND CONFIRMATIONS~
- 8 -
S0 380V 415V 440V 460V 480V
c. Wiring diagram for HP(200V class)/ HP(400V
class)
※In case as build-in brake
transistor, the mark of P1 will
changetoPR.
※ For the up to 400V 40HP, there are small terminals,
ontherightsideofRST,
UVW, which are connected to the wire of cooling fan and
contactor. Be sure connect to the correct required voltage. (Ex.
when power is 380V, then must be connect 0 and 380V. In case
the power change to 460V, please connect to 0 and 460V)
Terminals of main circuit
3-phase power source
Forward
Vin frequency command
(DC 0~10V)
Induction motor
Grounding
Analog signal
output
(DC 0~10V)
Multi-function
output terminals
(relay output)
(AC 250V/0.5A
COSθ=0.3)
Multi-function
output terminals
(open collector)
(DC 48V/50mA)
RM5G/5P
R
S
T
R
S
T
FWD
REV
Tc1
Tb1
Ta1
Tc2
Ta2
M-
FM+
AM+
U
V
W
PE
P
P1
(PR) IM
VR 1KΩ,1/4W
DSW1
I
V
PP P
Shielded P
Terminals of control circuit
Reverse
Multi-function input terminal 1
Multi-function input terminal 2
Multi-function input terminal 3
Multi-function input terminal 4
Multi-function input terminal 5
Multi-function input terminal 6
Iin frequency command
(DC 4~20mA)
X1
X2
X3
X4
X5
X6
COM
12V(3)
Vin(2)
Iin
GND(1)
Y1
Y2
CME
Twisted-pair shielded wires
N
DC Reactor When the DC reactor is used,
disconnect this jumper
20~60HP(200V)/25~75HP(400V)
20~60 25~75


~INSTALLATIONS AND CONFIRMATIONS~
- 10 -
B. Descriptions of terminals
a. Terminals of main circuit
Terminals Symbols Name Descriptions
Power
source R,S,T
(L1,L2,L3) Input AC voltage 3-phase power source
(for 1Φ, 220V, use R and S only)
Motor U,V,W
(T1,T2,T3) Inverter output
voltage 3-phase variable voltage and
frequency output motor
P,N Dynamic brake
terminals Connect to the dynamic brake unit
PR External braking
resistor P and PR terminals connect to an
external braking resistor(option)
Power
and
braking P1 External reactor P and P1 terminals are
short-circuit or connect to an
external reactor for improving
power factor. The factory setting
is short-circuit.
Main Circuit
Grounding PE Grounding Less than 100 Ω for the third
grounding method
b. Main circuit(Terminals subject to change without notice)
(1) 1/2~3HP (Built-in brake transistor)
(3) 7.5~15HP(200V class) and 7.5~20HP(400V class) (Built-in
brake transistor)
(2)
(1)
Grounding
Motor
Resistor
Grounding
Motor
Resistor
Grounding
Motor
Resistor
Grounding
Grounding
(2) 5HP
(Built-in brake transistor)
(200V class)/5HP (400V class)
Please connect PE terminal to metal shell.

~INSTALLATIONS AND CONFIRMATIONS~
- 11 -
PE
NFB
P1
Grounding
Grounding
Grounding
Resistor
Motor
terminal
(4) 20~30HP(200V class)/25~40HP(400V class) (Brake type)
※The polarities of P and N terminals should be wired correctly.
(6) 125~150HP(200V class)/175~420HP(400V class)(connect
dynamic braking unit)
(5) 40~100HP(200V)/50~150HP(400V)(connect dynamic
braking unit)
PE
NFB
DBU
Grounding
Grounding
Grounding
Motor
terminal
Power
PE
NFB
DBU
Grounding
terminal
Grounding
Grounding
Power
※The polarities of P and N terminals should be wired correctly.
※Connect dynamic braking unit, set the F_093(AVR)=0.
※
20~60HP (200V Class) / 25~75HP (400V Class) The P1 terminal
will be revised to PR, when brake transistor built in.(Brake type)
※The polarities of P and N terminals should be wired correctly.

~INSTALLATIONS AND CONFIRMATIONS~
- 12 -
c.Terminals of control circuit
Terminals Symbols
Name Descriptions
FWD
Forward
operation
FWD-COM is short-circuit for
forward operation
REV
Reverse
operation
REV-COM is short-circuit for
reverse operation
X1 Multiple function
input terminal 1
Function is determined by
F_052
X2 Multiple function
input terminal 2
Function is determined by
F_053
X3 Multiple function
input terminal 3
Function is determined by
F_054
X4 Multiple function
input terminal 4
Function is determined by
F_055
X5 Multiple function
input terminal 5
Function is determined by
F_056
X6 Multiple function
input terminal 6
Function is determined by
F_057
COM
C
ommon of inp
ut
terminals
Common of input terminal
signals
Vin
Voltage type of
frequency
command input
Input range 0 ~ 10V
Input
terminals
Iin
Current type of
frequency
command input
DSW1-> I side
(current input)
DSW1-> V side
(voltage input)
Input range
DC4~20 mA (2~10V)
/0~20mA(0~10V)
The range determined by F_126
+12V
Reference
v
oltage of contr
ol
signals
12V reference voltage with
maximum current 20mA
Control circuit
Power
Source
GND
Ground of
control signals Ground of control signals
Other manuals for RM5G
1
Table of contents
Other Rhymebus Controllers manuals
Popular Controllers manuals by other brands
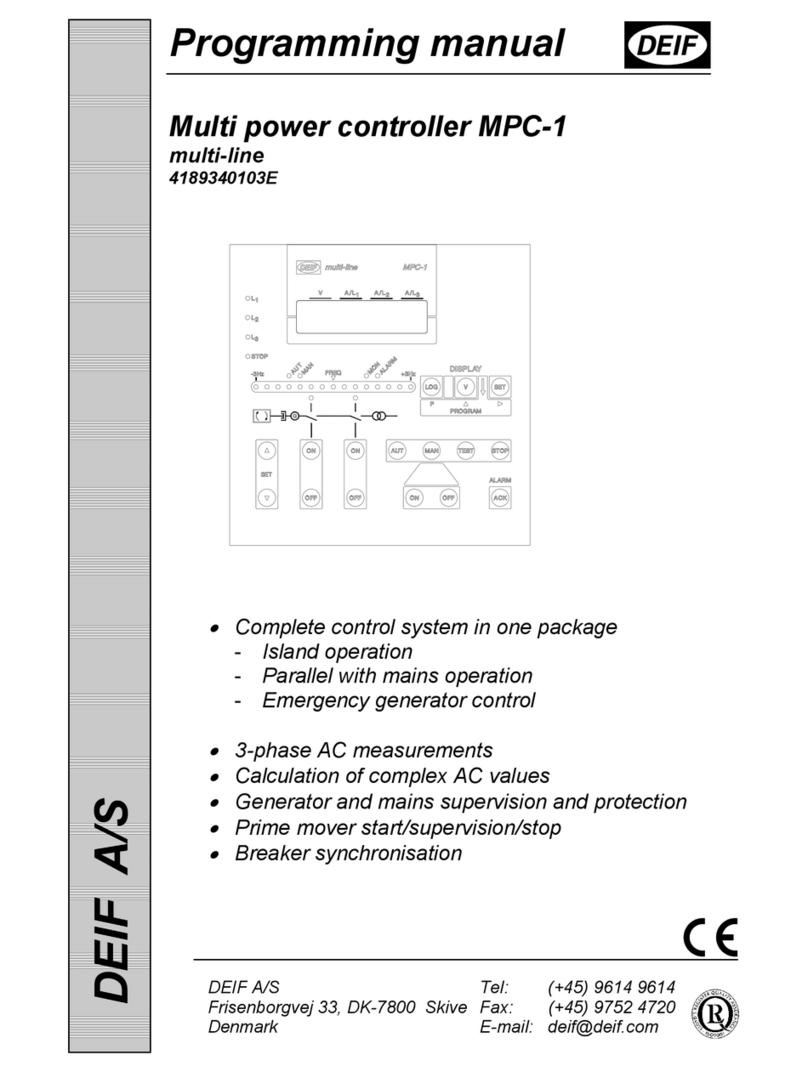
Deif
Deif MPC-1 Programming manual
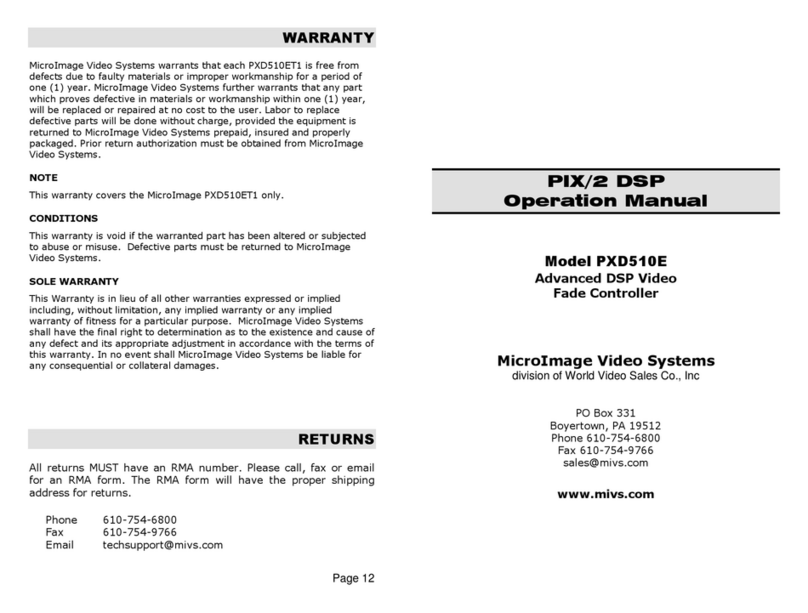
MicroImage Video Systems
MicroImage Video Systems PXD510E Operation manual
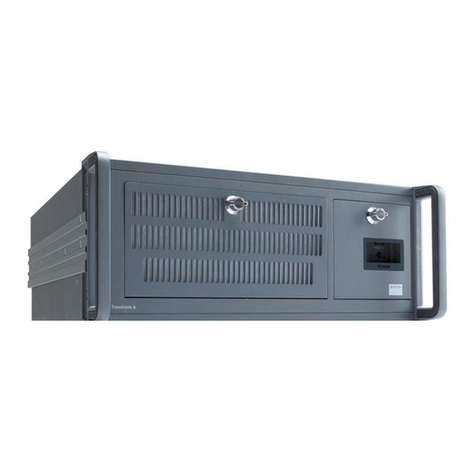
Barco
Barco TransForm A series user manual

Taconova
Taconova NOVASTAT RF DIGITAL manual
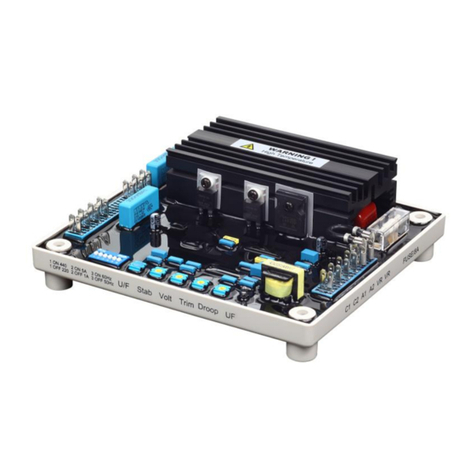
Kutai electronics
Kutai electronics EA125-8 Operation manual
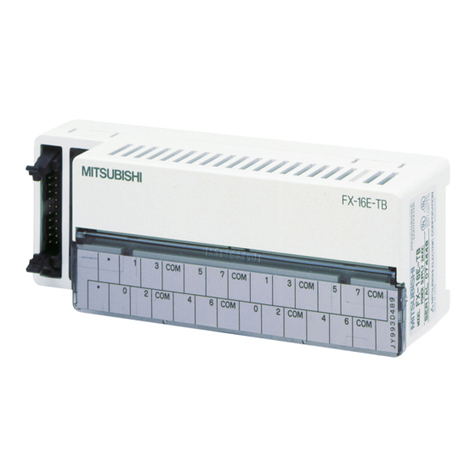
Mitsubishi Electric
Mitsubishi Electric MELSEC-F FX-16E-TB user guide