RINEER 15 Series Operating instructions

Standard Motor
Two Speed Motor
HYDRAULICS, INC.
HYDRAULICS, INC.
R
M
A
N
U
F
A
C
T
U
R
E
R
O
F
H
Y
D
R
A
U
L
I
C
M
O
T
O
R
S
15 Series
Repair Manual
331 BREESPORT * SAN ANTONIO, TX 78216 * (210) 341-6333 FAX (210) 341-1231





WARNING: RINEER RECOMMENDS FOLLOWING ALL STANDARD SHOP SAFETY PRACTICES SPECIFICALLY INCLUDING WEARING OF EYE PROTECTION.
1
2
3
4
5
6
7
8
5
1) Remove snap ring
WARNING: Use caution
when removing snap ring.
If released accidentally it
can become an airborne
hazard.
1) Pry out shaft seal plate
with two screw drivers.
2) Remove seal plate o-
ring from groove in bearing
bore.
1) Loosen and remove 8
each 10-32 bolts.
2) Pry off seal plate with
screw driver.
Loosen and remove 8
each 3/8" bolts with 5/16"
socket head wrench.
1) Press shaft out of
bearing box.
2) Proceed to step 9,
disregarding steps 11 & 12
1) Loosen clamp screw in
lock nut.
2) Unscrew lock nut and
remove.
Lift up on the bearing box
to remove from motor.
1) Two of the 3/8" bolt
holes are provided with
jack screw threads.
2) Insert a piece of 1/4"
round stock by 2-1/2" long
into each jack screw hole
3) Screw two 7/16-14 bolts
into the jack screw threads
until the bearing box is free
of the motor.
REMOVAL OF SHAFT SEAL
REMOVAL OF WHEEL MOTOR SEAL
PLATE AND BEARING BOX
DISASSEMBLY OF WHEEL MOTOR
BEARING BOX

WARNING: RINEER RECOMMENDS FOLLOWING ALL STANDARD SHOP SAFETY PRACTICES SPECIFICALLY INCLUDING WEARING OF EYE PROTECTION.
9
10
11
12
13
14
15
16
6
1) Remove front housing
2) Note: Two 5/16" ball
checks and one main body
o-ring may be dislodged
and fall free.
1) Mark one side of the
motor for proper assembly,
paying careful attention
that the cartridge will not
be installed upside down.
2) Secure the motor prior
to loosening the 5/8-11
bolts.
With the seal plate removed,
press shaft and ball bearing
out of front housing.
1) Remove snap ring from
shaft.
2) Press shaft out of
bearing.
1) Replace plate on
rotor/stator cartridge.
2) Turn rotor/stator
cartridge over.
3) Repeat steps 14 & 15.
1) Remove o-ring and
springs with a small
screwdriver.
2) Remove dowels pins.
1) Place cartridge on any
object which will hold it off
the table.
2) Remove two each 10-32
place screws.
3) Remove timing plate.
Lift up rotor/stator cartridge
and remove from the rear
housing.
DISASSEMBLY OF FRONT
HOUSING AND SHAFT
DISASSEMBLY OF ROTOR/STATOR
CARTRIDGE

WARNING: RINEER RECOMMENDS FOLLOWING ALL STANDARD SHOP SAFETY PRACTICES SPECIFICALLY INCLUDING WEARING OF EYE PROTECTION.
17 21
22
23
24
18
19
20
7
1) Remove the rotor.
2) Remove both the rotor
and stator vanes.
3) Note: On motors
manufactured prior to
1987, rotor vane slots and
rotor vanes should be
numbered so that vanes
can be reassembled in the
same vane slot.
Inspect all springs and
seals. We recommend
replacement of all seals
and springs whenever the
motor has been
disassembled.
Inspect all parts and
replace any parts which
obviously show excessive
wear or damage.
VANES: Normal wear results
in slight flattening of vane tips
which does not impair motor
performance. Replace vane if
radius is reduced by 50%.
Clearance between the rotor
vane and rotor vane slot
varies with the vane
selection. The design allows
the vane to "lean" slightly in
the slot, providing the
required mechanical seal.
Note: Measure the rotor
and stator length to the
fourth decimal point and
supply measurement when
ordering rotor, stator, or
vanes.
STATOR: Normal wear results
in polishing of cam form which
does not impair motor
performances.
Noticeable wear may be
apparent along the corner of
one side of the staor vane
slot. This does not necessarily
require replacement of the
stator, but may slightly affect
volumetric efficiency.
ROTOR: Normal wear
results in polishing of rotor
faces which does not impair
motor performance.
Examine the rotor vane
slots closely. Polishing
down in the slots is normal,
but if there is any indication
of a "pocket" forming in the
wall of the slot, the rotor
should be replaced.
PLATES: Normal wear
results in marking of timing
plates which does not
impair motor performance.
Replacement of the timing
plate is required if any
smearing, galling, or heat
cracks are present.
INSPECTION AND REPLACEMENT
OF PARTS

WARNING: RINEER RECOMMENDS FOLLOWING ALL STANDARD SHOP SAFETY PRACTICES SPECIFICALLY INCLUDING WEARING OF EYE PROTECTION.
25
26
27
28
29
30
31
32
8
1) Reverse the procedures
in steps 17, 16, 15, and 14
2) NOTE: Make sure that
the radiused edge of each
stator vane points to the
rotor and the radiused
edge of each rotor vane
points to the stator.
3) NOTE: Make sure
springs are seated in the
bottom of the spring pocket
in both the rotor and stator.
1) Press bearing onto shaft.
2) Install snap ring.
Press shaft and bearing
assembly into front
housing by pressing on the
outer race of bearing.
1) Place seal in seal plate.
2) Place seal plate o-ring
into groove in the front
housing.
3) Press seal plate into
front housing.
4) Install snap ring.
5) Proceed to step 30.
1) Install main body o-ring
into front housing.
2) Install ball checks into
front housing.
3) Place a small amount of
grease over ball checks
and o-ring.
4) Wipe off excess grease.
1) Place rotor/stator
cartridge onto rear housing.
2) NOTE: Make sure
assembly marks from step 3
are lined up.
1) Install dowel pins into
rear housing.
2) Install ballchecks into
rear housings.
3) Install main body o-ring.
1) Reverse the procedures in
steps 8 thru 3.
2) Screw lock nut onto shaft
until all threads are engaged.
3) Tighten clamp screw until
lock nut turns with a slight
drag.
4) Tighten lock nut until
desired rolling drag of bearing
is obtained - see procedure
Page 9.
5) Tighten clamp screw
6) Tighten all seal plate bolts.
ASSEMBLY OF ROTOR/STATOR
CARTRIDGE
ASSEMBLY OF FRONT HOUSING
ASSEMBLY OF WHEEL MOTOR
FRONT HOUSING
ASSEMBLY OF MOTOR

WARNING: RINEER RECOMMENDS FOLLOWING ALL STANDARD SHOP SAFETY PRACTICES SPECIFICALLY INCLUDING WEARING OF EYE PROTECTION.
33
34
35
36
B
A
9
1) Install dowel pins into
rotor/stator cartridge.
2) Pour a small amount of
clean oil into the cartridge.
3) Install front housing onto
rotor/stator cartridge.
4) Make sure alignment
marks are lined up.
1) Install 5/8-11 bolts.
2) Torque bolts to 50 ft./lbs.
1) Rotate shaft in both
directions to assure that the
shaft turns smoothly.
2) Torque motor to 190 ft./lbs.
3) Rotate shaft again in both
directions to assure that the
shaft turns smoothly.
NOTE: Spool should be
oriented as shown for two
speed motors with model
codes 62, 63, 68, & 69.
NOTE: Slight design
variations may exist in
motors manufactured
either before or after the
printing of this manual.
SPOOL ASSEMBLY FOR THE
TWO SPEED MOTOR
1) Clean ALL assembly parts w/ lacquer thinner.
2) Dip clampnut and clamping bolt separately in lacquer thinner.
(Steps 3 thru 10 must be conducted to completion ONE assembly at a time.)
3) Press bearing cups into bearing housing. Make sure they are pressed completely against bearing shoulders.
4) Coat inner race of large cone with #609 (green) Loctite and press cone onto the shaft. Make sure the cone is completely against the shoulder of the shaft.
5) Insert shaft and large cone into bearing housing.
6) Coat inner race of small cone with #609 (green) Loctite and press small cone onto shaft.
7) Apply #272 (red) Loctite to the clampnut threads of the shaft. Apply #242 (blue) Loctite to the threads of the clamping bolt and install in the clampnut.
8) Spin clampnut onto shaft with the "B" face towards bearings. After the nut threads are fully engaged, but prior to the nut contacting the bearings,
tighten the clamping bolt until there is drag on the clamping nut (see note Fig. 1). Tighten the nut until a 20 to 30 inch pound rolling torque is achieved.
9) Tighten clamping bolt on clampnut to 70 inch pounds and recheck rolling torque. Apply inspectors lacquer to head of the bolt.
10) Allow a minimum of 24 hrs. to dry.
Figure 1
CUTAWAY
Note:
The slit in the clampnut
allows for loose
assembly on the shaft.
Once in position, the
clampnut clamping bolt
MUST be tightened to
a slight drag in order to
correctly engage the
threads on the shaft to
achieve the clamp
force required.
FACE
"A"
CLAMPING BOLT
FACE
"A"
FACE
"B"
WHEEL MOTOR SHAFT AND BEARING ASSEMBLY PROCEDURE

Information:
Bolt Torque -
Main Bolts (5/8-11): 190 ft. lbs.
Seal Plate (3/8-16)
(Wheel Motor only): 45 ft. lbs.
Grease used for bolt threads
and o-ring retention:
Pennzoil 707L RED
Shaft seal assembly lube:
Mobilgrease special
with Moly
Seal Kits:
Standard 15 series seal kit
#0150940
Standard 15 two speed seal kit
#0150940
Standard 15 wheel motor seal kit
#0150936
331 Breesport San Antonio, Texas 78216
210-341-6333 Fax: 210-341-1231 e-mail: sales@rineer.com
W
HEEL M
O
T
O
R
S
T
AN
D
A
R
D
M
OT
O
R
T
WO S
P
E
ED
M
OT
OR
Popular Engine manuals by other brands
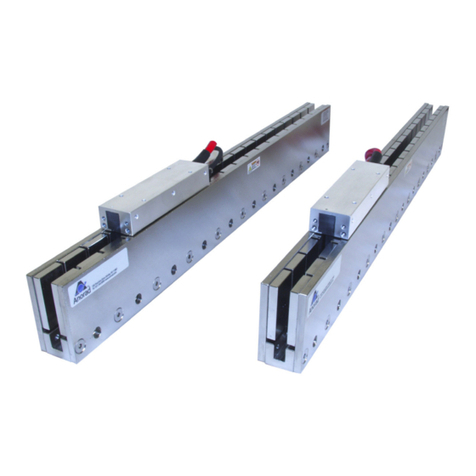
Rockwell Automation
Rockwell Automation ANORAD LZ Series user manual

MTU
MTU 20V4000L63 operating instructions
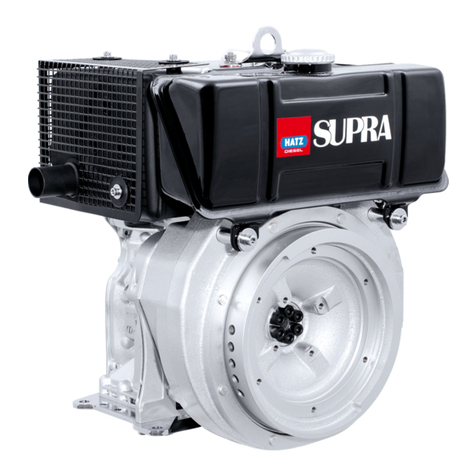
Hatz
Hatz 1D41. Original instruction book
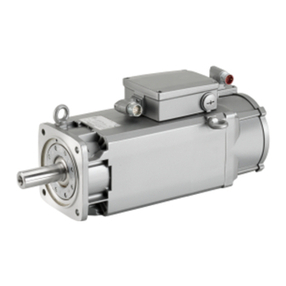
Siemens
Siemens SIMOTICS M-1PH8 Operating instructions & installation instructions
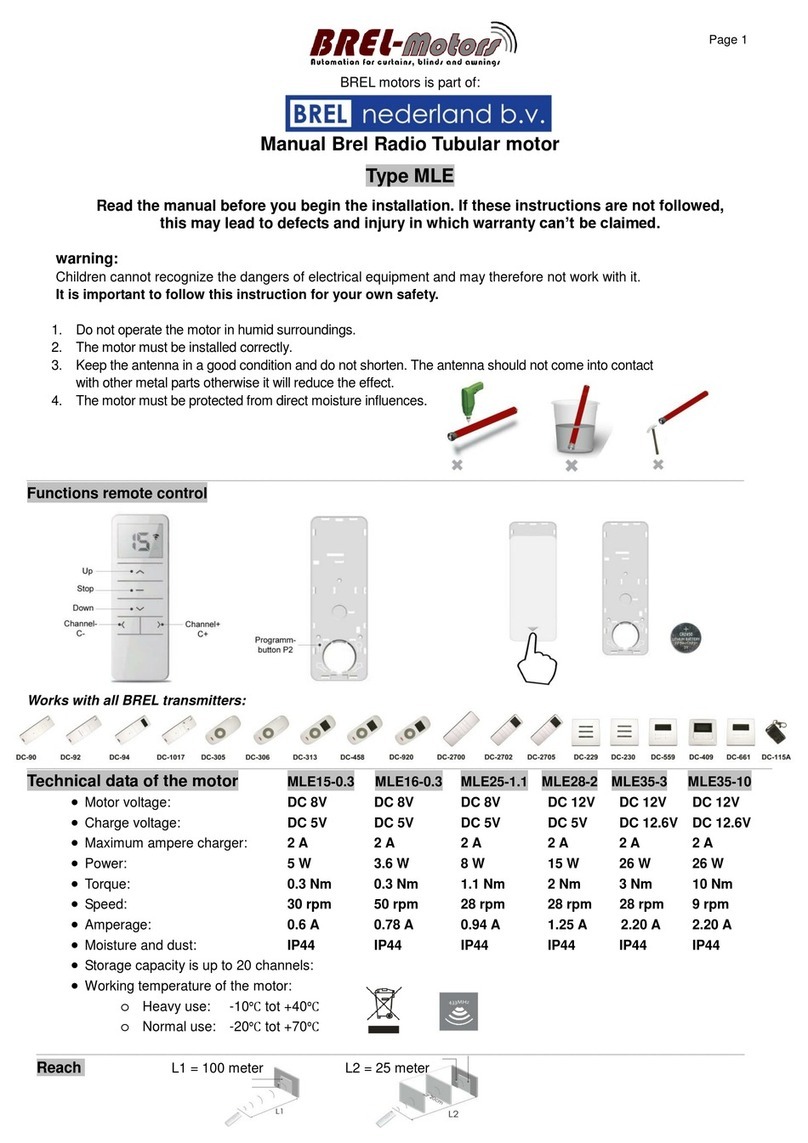
brel-motors
brel-motors MLE Series manual
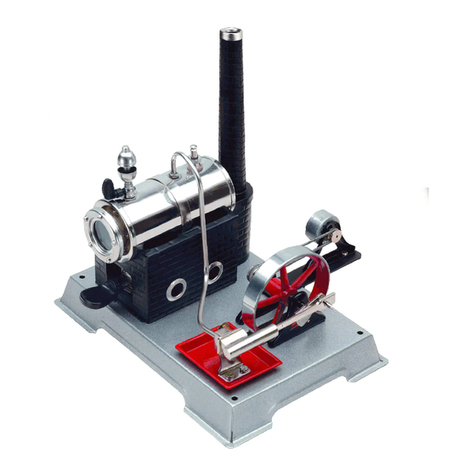
Wilesco
Wilesco D100E user manual