ritetemp R422D Operating and safety instructions

rite-temp
INSTALLATION &
MAINTENANCE GUIDE
WATER CHILLERS®

IMPORTANT –READ BEFORE INSTALLING
INSTALLATION INSTRUCTIONS
A. RECEIVING AND INSPECTION
1. Immediately upon receiving shipment, equipment should be inspected for evidence of any damage received in transit. If shipping
damage has occurred, a claim should be made with the transportation company, and the local Rite-Temp representative should be
advised of nature of damage.
2. Equipment should be inspected for compliance with original order acknowledgement (equipment model numbers, voltages, etc.).
B. RIGGING
1. Equipment should be lifted in a near level condition to prevent undue stress on structural members.
C. MOUNTING
1. Equipment should be mounted on a smooth, hard, level surface.
2. Mounting surface should be rigid, and provisions should be made to prevent noise transmission (structural) to surrounding areas.
3. Air cooled equipment should not be installed under low structural overhangs which can cause condenser air recirculation or
restriction.
4. Adequate Area (approx. 1 unit width) must be provided around equipment for unrestricted air flow and service. Two units side by
side should have a minimum of 1 ½ unit width between them.
5. Care should be taken to prevent air from other sources from entering condenser if this air is at an elevated temperature.
6. Indoor design equipment must be installed in a protected enclosure.
D. PIPING
1. All piping must be in accordance with applicable local and state codes.
2. Refrigerant piping (split systems) should be designed and installed in accordance with recommended practices as outlined in ARI
or ASHRE piping guide. (Engineering Guide #1 for air conditioning systems.)
3. Water piping (Chillers) should be designed and installed to meet application requirements. Provisions (Ethylene or Propylene
Glycol) must be made to prevent freezing if design ambient temperatures dictate.
4. When piping is completed, a thorough leak test should be performed before evacuation start-up. Do not exceed 150 psig test
pressure on low side of system.
E. WIRING
1. All local and state codes must be strictly adhered to and good electrical practices should be followed to achieve the best
installation possible.
2. Power wiring to equipment must be adequately sized for minimum ampacity as shown on unit nameplate. A disconnect should be
located adjacent to unit for both safety and servicing purposes.
3. Equipment wiring diagram should be examined and thoroughly understood before field wiring connections are made.
4. Power supply should be checked to be certain that supply voltage agrees with equipment nameplate. Serious damage to
compressors and motors can occur if improper voltage is applied.
5. Use copper conductors ONLY.
F. ROTATION DIRECTION OF THREE PHASE SCROLL COMPRESSORS
1. Scroll compressors will only compress in one rotational direction. Direction of rotation is not an issue with single phase
compressors since they will always start and run in the proper direction. Three phase compressors will run in either direction
depending upon the phasing of the power. Verification of proper rotational direction must be made by observing that the
suction pressure drops and the discharge pressure rises when the compressor is energized. Reverse rotation also results in an
elevated sound level as well as substantially reduced current draw compared to forward rotation.

G. SYSTEM EVACUATION (SPLIT SYSTEM ONLY)
1. With refrigerant piping completed and leak tested, equipment is ready to evacuate. Do not use compressor to evacuate system. A
quality vacuum pump capable of 350 micron vacuum is necessary for adequate and dependable system vacuum. Moisture in a
refrigeration system can cause corrosion, expansion valve freeze-up and oil sludge.
2. attach vacuum pump to both high and low side of system through compressor service valves and evacuate to 350 microns (all
service valves, hand valves, and solenoids must be open during evacuation). It is suggested that vacuum pump be run for a period
of time after vacuum has been reached.
3. Service should be provided by a qualified EPA refrigeration technician only.
H. START-UP
1. This will involve checking and adjusting of all safety and operation controls (pressure and temperature controls have been set at
the factory; however, it is still desirable to confirm that settings are correct and controls function properly). Do not attempt to
disengaged or bypass safety controls without some means of stopping compressor in event of extreme high or low pressure
conditions that could damage the equipment. If controls fail to function at set point, determine cause and correct. Jumping any
safety control other than for testing purposes is dangerous to personnel and equipment, and nullifies equipment warranty.
2. The bottom opening is the pump outlet to your process. The bottom opening is the pump outlet to your process. The middle
opening is the return inlet water coming back to the reservoir tank. Fit a union and a tee in the return line. Bring the make-up
water line to the tee. This is used to fill the chiller and system.
3. With the chiller switch OFF, turn on the MAINPOWER to the chiller. Even though the chiller switch is off, the main power will
activate the compressor crankcase heater to warm up the oil and burn off any Freon that has migrated into the crankcase (this
feature is standard in ALL compressors with the exception of scrolls). Allow the compressor(s) to warm overnight, or at least six
hours. This is a one time procedure for start-up. However, if the main power is off for over 24 hours, (four hours if outside in
cold weather), then the warm-up procedure should be repeated.
4. To fill chiller, open the city water and fill at a SLOW RATE. When water comes out of the ½” top vent opening it means the
reservoir tank is full. SHUT WATER OFF. Open all valves to process and start chiller for about 15 seconds to fill lines and
equipment. STOP CHILLER. Open city water again at a SLOW RATE till water again comes out of the vent pipe. SHUT THE
WATER OFF. The system is full and ready for use.
I. SHUT DOWN
1. Equipment which will not be required to operate for a period of time should be secured by storing refrigerant charge in the
receiver or condenser. On units with coolers or water cooled condensers, special precautions must be taken to completely drain
the vessels to prevent freezing if ambient should be below 32*F.
2. Inspect system for possible worn or faulty components and repair if required.
J. SYSTEM RESTART AFTER SHUT DOWN
1. Thorough leak test should be performed.
2. Coil(s) should be checked for dirt accumulation or obstruction and cleaning if necessary.
3. Refill water system and purge all air from system.
4. Energize crankcase heaters and allow a minimum of 12 hours operation before compressor restart.
5. Install gauges, start system and check for correct refrigerant charge, and proper system operation and balance.
K. MAINTENANCE
1. The system should be checked periodically. Use only the services of an EPA qualified refrigeration technician for inspection and
maintenance checks or service operations.
2. Water Treatment (Chillers and Water Cooled Condensing Units) –The water should be tested by a local testing agency and their
recommendations adhered to.
3. Air Cooled Condenser –The inlet side of the condenser coil must be kept clean through a regular prevention maintenance
program. ]
4. Periodically checks all electrical connections for possible loose or corroded terminals. Repair as necessary.

POSSIBLE CAUSES OF CONTROL FAILURES AND RECOMMENDED CORRECTIVE ACTION:
CAUSE CORRECTION
Temperature Control Setting too low Readjust to proper setting. VCheck catalog or submittal data.
Cooler flow incorrect Balance flow to catalog or submittal requirements.
Low refrigerant charge Pull charge, weigh in amount listed on data plate (charge critical).
Restricted liquid line Check valves and dryer.
Thermal expansion valve adjustment Adjust superheat to approximately 10* - 12* F at the compressor.
LINE SIZES
LIQUID LINE SIZES
DISCHARGE LINE SIZES
Net
Evaporator
Capacity
R422D
Net
Evaporator
Capacity
R422D
25
50
100
150
25
50
100
150
3,000
1/4
1/4
1/4
1/4
3,000
3/8
3/8
3/8
3/8
4,500
1/4
1/4
3/8
3/8
4,500
3/8
3/8
1/2
1/2
6,500
1/4
1/4
3/8
3/8
6,500
3/8
1/2
1/2
1/2
8,500
1/4
3/8
3/8
3/8
8,500
3/8
1/2
1/2
5/8
12,000
3/8
3/8
3/8
1/2
12,000
1/2
1/2
5/8
5/8
18,000
3/8
3/8
1/2
1/2
18,000
1/2
5/8
3/4
3/4
24,000
3/8
1/2
1/2
1/2
24,000
5/8
5/8
3/4
7/8
30,000
3/8
1/2
1/2
5/8
30,000
5/8
3/4
7/8
7/8
36,000
1/2
1/2
5/8
5/8
36,000
5/8
3/4
7/8
7/8
42,000
1/2
1/2
5/8
5/8
42,000
3/4
3/4
7/8
1 1/8
48,000
1/2
5/8
5/8
3/4
48,000
3/4
7/8
1 1/8
1 1/8
54,000
1/2
5/8
5/8
3/4
54,000
3/4
7/8
1 1/8
1 1/8
60,000
1/2
5/8
3/4
3/4
60,000
3/4
7/8
1 1/8
1 1/8
72,000
5/8
5/8
3/4
3/4
72,000
7/8
1 1/8
1 1/8
1 1/8
90,000
5/8
3/4
7/8
7/8
90,000
7/8
1 1/8
1 1/8
1 3/8
120,000
3/4
3/4
7/8
1 1/8
120,000
1 1/8
1 1/8
1 3/8
1 3/8
150,000
3/4
7/8
1 1/8
1 1/8
150,000
1 1/8
1 3/8
1 3/8
1 5/8

BASIC SINGLE HOOK-UP TO CHILLER WATER
CHILLER
EQUIPMENT
TO BE COOLED
SUPPLY VENT
VENT WARMOUT
TO DRAIN
COLDIN
WARMIN
COLDOUT
SUPPLY HEADER1" NPT
RETURN HEADER1 1/4" NPT
If chiller is installed outside, or
exposed to low temperature, it
must have antifreeze. The
crankcase heater must be wired
direct to stay on continuously.
Use any std. water pipe. DONOT plumb with smaller size pipe than noted on this print. The bypass line is necessary if units to be cooled have self
acting shut-off valves. Water must circulate through chiller at all times for proper operation and temperature control. Place bleeder valve at highest
point and fill unit untilwater discharges frombleeder. Close bleeder -- unit is full. Shut off outside water supply.
BASIC MULTIPLE HOOK-UP TO CHILLER WATER
EQUIPMENT
TO BE COOLED
SUPPLY
WATER
VENT
VENT
TO DRAIN
WARM
IN
COLDOUT
CHILLER
EQUIPMENT
TO BE COOLED

TROUBLESHOOTING
Compressor will not run.
a) Main switch open.
Circuit breakers open
a) Close switch
b) Fuse blown
b) Check electrical circuits and motor winding for shorts or grounds. Investigate
for possible overloading. Replace fuse or reset breakers after fault is corrected.
c) Thermal overloads
tripped or fuses blown
c) Overloads are auto. Reset. Check unit closely when unit comes back on line.
d) Defective contactor or
coil
d) Repair or replace
e) System shut down by
safety devices
e) Determine type and cause of shut-down and correct it before resetting safety
switch.
f) No cooling required
f) None. Wait until unit calls for cooling.
g) Liquid line solenoid
will not open
g) Repair or replace coil
h) Motor electrical trouble
h) Check motor for opens, short circuit, or burnout
i) Loose wiring
i) Check all wire junctions. Tighten all terminal screws.
Compressor noisy or vibrating.
a) Flooding of refrigerant into crankcase
a) Check setting of expansion valve
b) Improper piping support on discharge coil or liquid
line*
b) Relocate, add, or remove hangers
c) Worn compressor
c) Replace
High Discharge Pressure
a) Condenser water insufficient or temperature too
high
a) Readjust water regulating valve. Investigate ways
to increase water supply
b) Fouled condenser tubes (water cooled
condenser). Clogged spray nozzles (evaporative
condenser). Dirty tube and fin surface (air cooled
condenser)
b) Clean
c) Non-condensable in system
c) Purge the non-condensables
d) System overcharged with refrigerant*
d) Remove excess
e) Discharge shut off valve partially dosed
e) Open valve
f) Condenser undersized*
f) Check condenser rating tables against the
operation
g) High ambient conditions*
g) Check condenser rating tables against the
operation

Discharge Pressure
a) Faulty condenser temperature regulation
a) Check condenser control operation
b) Suction shut-off valve partially closed
b) Open valve
c) Insufficient refrigerant in system
c) Check for leaks. Repair and add charge
d) Low suction pressure
d) See Corrective Steps for low suction pressure below
e) Compressor operating unloaded
e) See Correction Steps for failure of compressor to load
up below
f) Condenser too large*
f) Check condenser rating table against the operation
g) Low ambient conditions*
g) Check condenser rating tables against the operation
Suction Pressure
a) Lack of refrigerant
a) Check or leaks. Repair and add charge
b) Evaporator dirty
b) Clean chemically
c) Clogged liquid line filter-drier
c) Replace cartridge(s)
d) Clogged suction line or compressor suction
gas strainers
d) Clean strainers
e) Expansion valve malfunctioning
e) Check and reset for proper superheat. Replace if
necessary
f) Condensing temperature too low
f) Check means for regulating condensing temperature
g) Compressor will not unload
g) See Corrective Steps for failure of compressor to
unload
h) Insufficient water flow
h) Adjust gpm.
Compressor will not unload or load up
a) Defective capacity control
a) Replace
b) Unloader mechanism defective
b) Replace
c) Faulty thermostat stage or
broken capillary tube
c) Replace
d) Stages not set for application
d) Reset thermostat setting to fit application

Compressor Loading - Unloading Intervals too short
a) Erratic water thermostat
a) Replace
b) Insufficient water flow
b) Adjust gpm.
Little or no oil pressure
a) Clogged suction oil strainer
a) Clean
b) Excessive liquid in crankcase
b) Check crankcase heater. Reset expansion valve for
higher superheat. Check liquid line solenoid valve
operation
c) Oil pressure gauge defective
c) Repair or replace. Keep valve closed except when
taking readings
d) Low-oil pressure safety switch defective
d) Replace
e) Worn oil pump
e) Replace
f) Oil pump reversing gear stuck in wrong
position
f) Reverse direction of compressor rotation
g) Worn bearings
g) Replace compressor
h) Low oil level
h) Add oil
i) Loose fitting on oil lines
i) Check and tighten system
j) Pump housing gasket leaks
j) Replace gasket
k) Flooding of refrigerant into crankcase
k) Adjust thermal expansion valve
Compressor loses oil
a) Lack of refrigerant
a) Check for leaks and repair. Add refrigerant
b) Velocity in risers too low*
b) Check riser sizes
c) Oil trapped in line*
c) Check pitch of lines and refrigerant velocities
d) Excessive compression ring blow-by
d) Replace compressor

Motor overload relays or circuit breakers open
a) Low voltage during high load conditions
a) Check supply voltage for excessive line drop
b) Defective or grounded wiring in motor or
power circuits
b) Replace compressor motor
c) Loose power wiring
c) Check all connections and tighten
d) High condensing temperature
d) See Corrective Steps for high discharge pressure
e) Power line fault causing unbalanced voltage
e) Check supply voltage. Notify power company. Do not
start until fault is corrected
f) High ambient temperature around the
overload relay
f) Provide ventilation to reduce heat
g) Failure of second starter to pull in on part-
winding start system
g) Repair of replace starter or time delay mechanism
Compressor thermal protector switch open
a) Operating beyond design conditions
a) Add facilities so that conditions are within allowable
limits
b) Discharge valve partially shut
b) Open valve
c) Blown valve plate gasket
c) Replace gasket
Freeze protection opens
a) Thermostat set too low
a) Reset to 40 F or above
b) Low water flow
b) Adjust gpm.
c) Low suction pressure
c) See "Low Suction Pressure"
*REMOTE CONDENSER MODELS

WARRANTY INFO
THANK YOU FOR PURCHASING A RITE-TEMP WATER CHILLER. WE ENCOURAGE YOU TO READ THE ENTIRE
INSTALLATION MANUAL BEFORE ATTEMPTING TO INSTALL THE CHILLER.
IF YOU ENCOUNTER ANY PROBLEMS OR HAVE ANY QUIESTIONS, CALL US IMMEDIATELY. OUR STAFF OF
TECHNICIANS ARE ON HAND TO ASSIST YOU DURING THE HOURS OF 7:00am TO 4:00pm (CENTRAL TIME)
MONDAY THROUGH FRIDAY.
OUR TOLL FREE TELEPHONE NUMBER IS: 800/462-3120
IN WARRANTY REPLACEMENT PARTS
Should you require replacement parts for Rite-Temp equipment, they may be obtained by calling the factory directly.
When requesting in warranty replacement parts, it is necessary to furnish the equipment model and serial number, part description, and
shipping information. Upon determination that the defective part is in warranty, a return authorization expires after 30 days and returned
parts will no longer be accepted.
Should you have any questions please call the factory directly.
BASIC WARRANTY
RITE-TEMP MFG., INC. MAKES NO WARRANTY OF MERCHANTABILITY AND NO WARRANTY OF FITNESS FOR
ANY PARTICULAR PURPOSE, NOR DOES IT MAKE ANY WARRANTY, EXPRESS OR IMPLIED, OF ANY NATURE
WHATSOEVER WITH RESPECT TO PRODUCTS SOLD BY RITE-TEMP OR THE USE THEREOF EXCEPT AS IS
SPECIFICALLY SET FORTH ON THE FACE HEREOF, EVEN THOUGH IT MAY HAVE BEEN NEGLIGENT, RITE-TMEP
SHALL IN NO EVENT BE LIABLE FOR DIRECT, INDIRECT SPECIAL, INCIDENTAL, CONSEQUENTIAL OR PENAL
DAMAGES. RITE-TEMP MAKES NO WARRANTY OF ANY KIND, EITHER EXPRESS OR IMPLIED, TO ‘CONSUMERS’
AS THAT TERM IS DEFINED IN SEC. 101 OF PUMBIC LAW 93-637, THE MAGNUSON-MOSS WARRANTY –FEDERAL
TRADE COMMISSION IMPROVEMENT ACT.
Rite-Temp Mfg., Inc. warrants to the original Purchaser-User that products manufactured by Rite-Temp shall be free from defects in
material and workmanship under normal use and service for a period of twelve months from date of shipment from Rite-Temp plant.
There is an additional four –year warranty on the original compressors only.
The obligation of Rite-Temp under this warranty is limited to Rite-Temp repairing or replacing, free of cost to Purchaser-User F.O.B.
factory, any part of parts that in the judgment of Rite-Temp show evidence of defect provided that upon Rite-Temp authorization the said
part or parts be returned to Rite-Temp, transportation prepaid, for inspection and judgment. Under this warranty Rite-Temp assumes no
responsibility for the expense of labor or materials necessary to remove a defective part or install repaired or new parts.
This warranty is issued only to the original Purchaser-User, is not transferable, applies only to a unit installed within the USA, its
territories or possessions and Canada and is in lieu of all other warranties express or implied. Rite-Temp neither assumes nor authorizes
any other person to assume any liabilities not herein stated.
Rite-Temp shall not be liable for any damage or delays occurring in transit, for any default or delays in performance caused by any
contingency beyond its control including war, government restrictions or restraints, strikes, short of reduced supply of raw materials, fire,
flood or other acts of God, not for damage or loss of any products, refrigerant, property, loss of income or profit due to malfunctioning of
said unit.
THE FOREGOING IS IN LIEU OF ALL OTHER WARRANTIES, EXPRESS OR IMPLIED, NOTWITHSTANDING THE
PROVISION OF THE UNIFORM COMMERCIAL CODE, THE MAGNUSON-MOSS WARRANTY-FEDERAL TRADE
COMMISSION IMPROVEMENT ACT, OR ANY OTHER STATUTORY OR COMMON LAW, FEDRAL OR STATE.

DO NOT USE
AUTOMOTIVE
-OR-
RV ANTI-FREEZE
RITE-TEMP RECOMMENDS
USING EITHER ETHYLENE
GLYCOL OR PROPYLENE
GLYCOL

rite-temp
Water Chillers®
Distributed By:
RITE-TEMP
MANUFACTURING, INC.
PO BOX 1275
1704 S. 1ST STREET
ROGERS, AR 72757
800/462-3120 PH
479/986-0727 FAX
www.ritetemp.com
Table of contents
Popular Chiller manuals by other brands
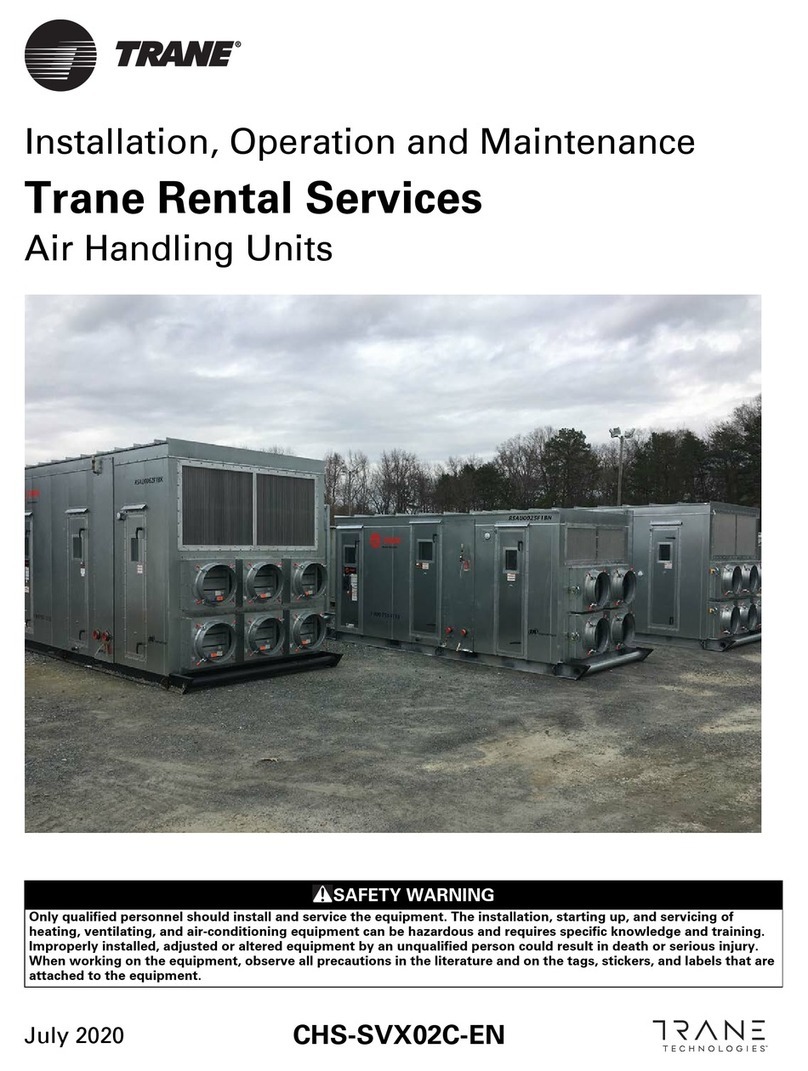
Trane
Trane TCCA ACCOMPANIMENT TO THE INSTALLATION, OPERATION AND MAINTENANCE MANUAL

Carrier
Carrier Flotronic 30GB Wiring, controls and troubleshooting
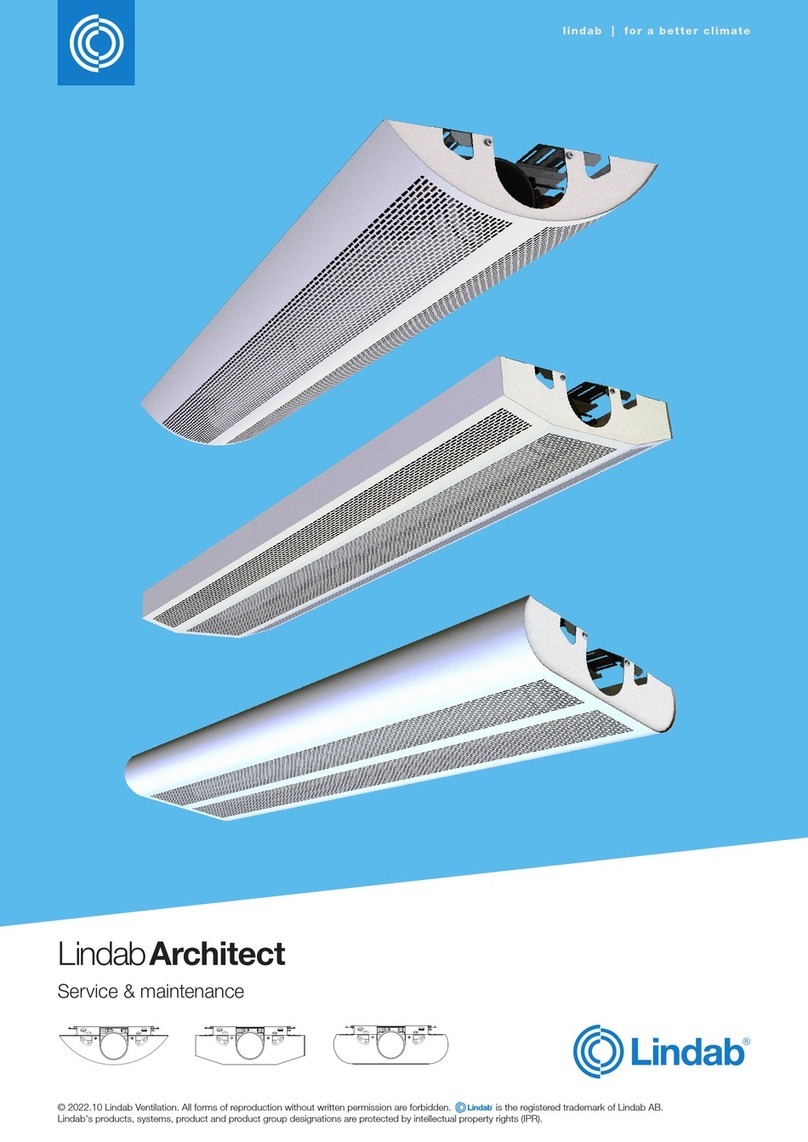
Lindab
Lindab ARCHITECT Luna Service & Maintenance
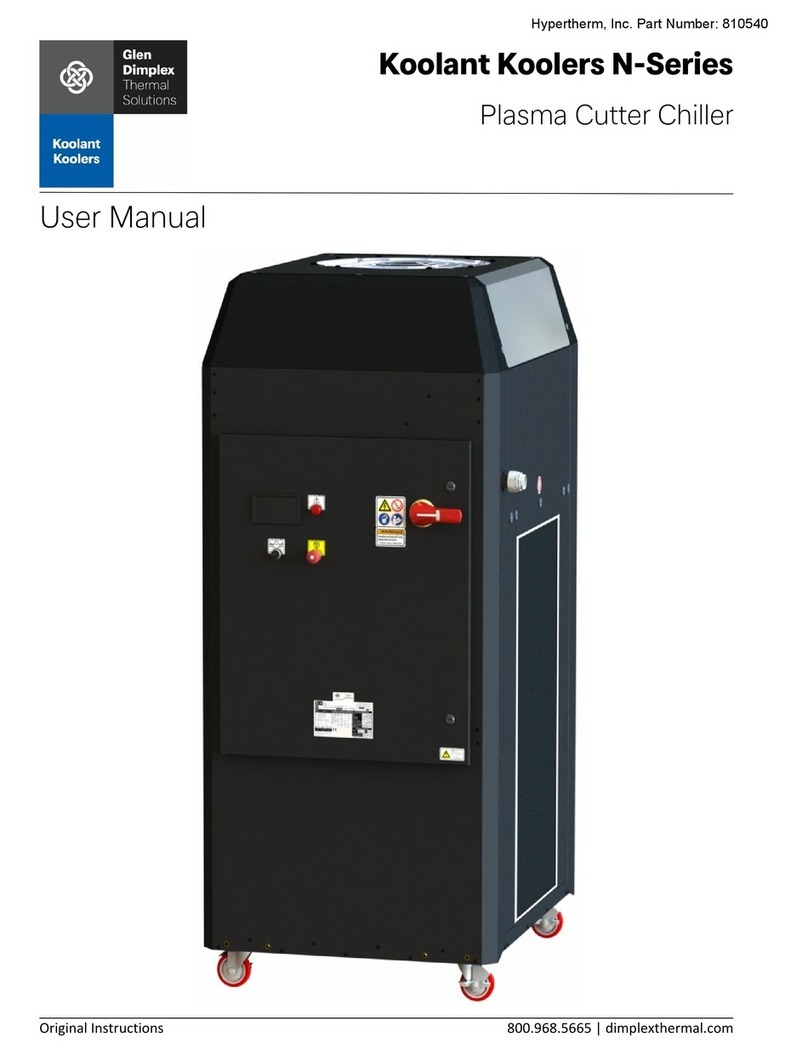
Hypertherm
Hypertherm Koolant Koolers N-Series user manual
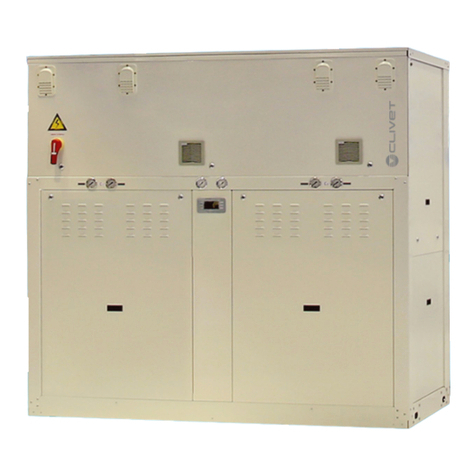
CLIVET
CLIVET MSE-XSC3 90.4 Installation and operating manual
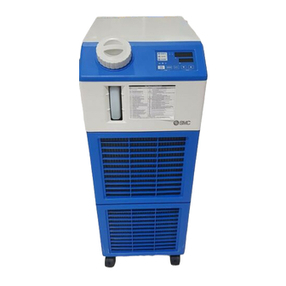
SMC Networks
SMC Networks HRS050-A*-20 Series Operation manual
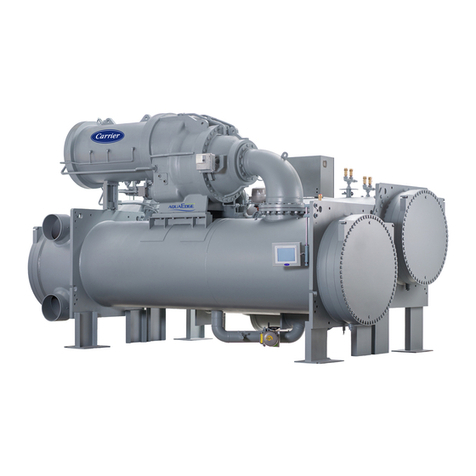
Carrier
Carrier AquaEdge 19XR Controls operation and troubleshooting
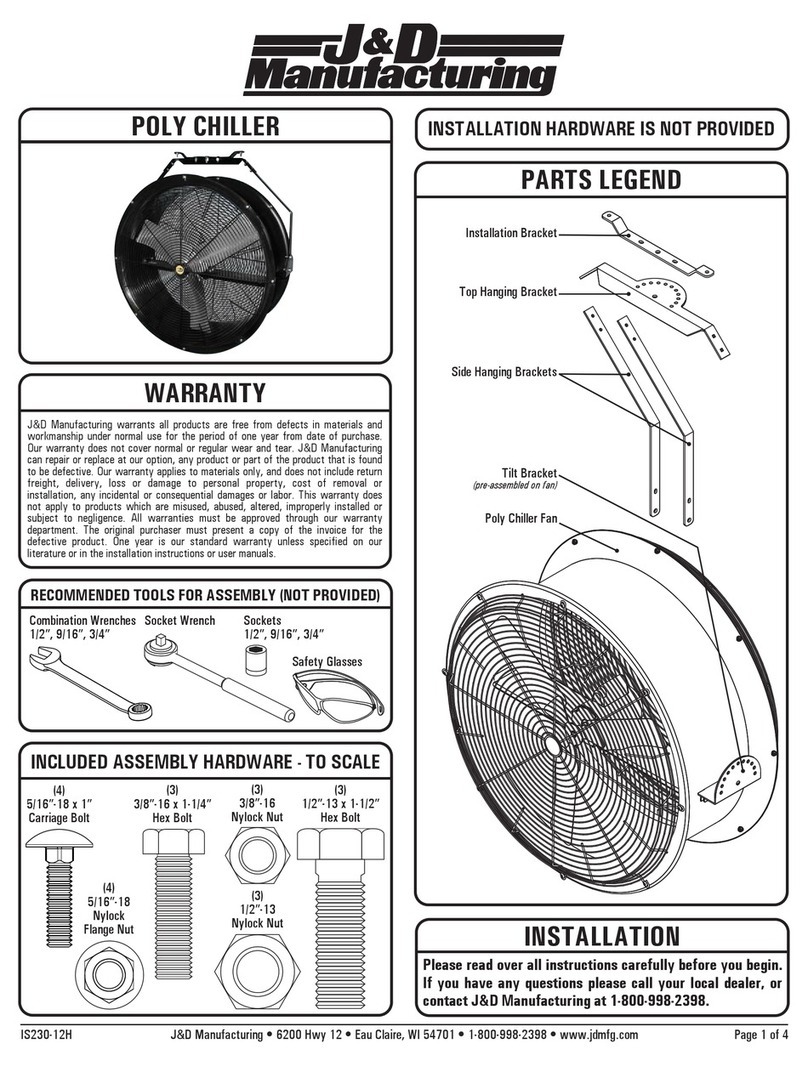
J&D MAnufacturing
J&D MAnufacturing VPRF363 quick start guide

Multistack
Multistack Airstack ASPX Series Operation and maintenance manual

Carrier
Carrier 19DK Product data

York
York YVAA Installation, operation & maintenance instructions
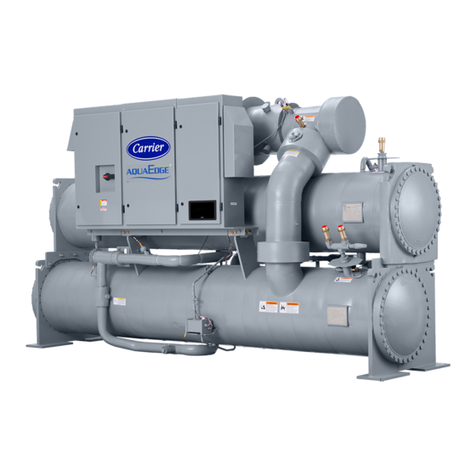
Carrier
Carrier EVERGREEN 23XRV installation instructions