Rotronic hygrogen2 User manual

E-M-HG2-S-V1_04
Rotronic AG
Bassersdorf, Switzerland
Document code Unit
HygroGen2 humidity and temperature
generator: Instruction Manual Instruction Manual
Document Type
Page 1of 46
Document title
© 2009-2010; Rotronic AG 1E-M-HG2-S-V1_04
Instruction Manual

E-M-HG2-S-V1_04
Rotronic AG
Bassersdorf, Switzerland
Document code Unit
HygroGen2 humidity and temperature
generator: Instruction Manual Instruction Manual
Document Type
Page 2of 46
Document title
© 2009-2010; Rotronic AG 2E-M-HG2-S-V1_04
HygroGen 2 - Quick Start Guide:
Congratulations on selecting the HygroGen humidity and temperature generator; the unit will enable
you to perform accurate and rapid humidity and temperature calibrations for many years. Before
starting to use the instrument there are a few key points you should pay close attention to:
1. Unpacking
Carefully remove the HygroGen from the packaging and visually inspect for any signs of damage and
check the supply contents defined on page 4. Report any damage or missing parts immediately to your
supplier.
2. Pre-checks
First check that the water reservoir is empty by inserting the HG-Fill syringe and trying to extract water.
If you find that the unit was shipped with water, immediately report this to your supplier and do not
power the unit.
3. Installation and Safety
Before using the instrument, please read Sections 1.1 and 4.1 and take particular note of the content.
4. Power shutdown
Incorrect shutdown procedures can lead to failure of the HygroGen. Please read Section 4.9 and take
note of the content.
5. Getting started
After taking note of the guidance above:
•Fill the water reservoir with distilled water as described in Section 2.1
•Check power connection
•Switch on the instrument
•Allow to stabilise to set-points

E-M-HG2-S-V1_04
Rotronic AG
Bassersdorf, Switzerland
Document code Unit
HygroGen2 humidity and temperature
generator: Instruction Manual Instruction Manual
Document Type
Page 3of 46
Document title
© 2009-2010; Rotronic AG 3E-M-HG2-S-V1_04
Contents
Quick Start Guide ............................................................................................................................................................................................................. 2
Manual contents .............................................................................................................................................................................................................. 3
Introduction to the HygroGen, Contents of the standard supply..................................................................................................................................... 4
Part Identification and Screen Diagrams................................................................................................................................................................... 5 to 8
Section 1: Operation .........................................................................................................................................................................................................
1.1 Before Switching On, Switching On, Automatic/Manual Mode ................................................................................................................ 9
1.4 Setting Temperature and Humidity Set-Points, Below Ambient Temperature Operation, Humidity Map ....................................... 10-11
1.6 Above Ambient Temperature Operation, Programmer Function ........................................................................................................... 11
1.8 Water in the Chamber ............................................................................................................................................................................ 12
1.9 Low Water Level Alarm, Switching Off.................................................................................................................................................... 13
Section 2: Maintenance & Servicing .................................................................................................................................................................................
2.1 How to Fill the Water Reservoir, Overfilling the HygroGen .................................................................................................................... 14
2.3. How to Empty the Water Reservoir, How to Change the Desiccant ...................................................................................................... 15
2.5 Choice of Desiccant, Molecular Sieve Desiccant (Factory Standard),...................................................................................................... 16
2.7 Regeneration of Molecular Sieve Desiccant, Silica Gel Desiccant, Regeneration of Silica Gel Desiccant ................................................ 17
2.10 Drierite Desiccant, Regeneration of Drierite Desiccant , Blue-to-Pink Self-Indicating Desiccant,
HygroGen Door Removal and Refitting, HygroClip Probe Removal and Refitting................................................................................. 18
2.15 HygroGen External Cleaning ................................................................................................................................................................. 19
2.16 HygroGen Internal Cleaning, HygroGen Servicing................................................................................................................................. 20
2.18 Water Quality ....................................................................................................................................................................................... 21
Section 3: Connecting Ancillary Equipment.....................................................................................................................................................................
3.1 USB keyboard and mouse, DVI Monitor, Rotronic USB devices.............................................................................................................. 22
3.4 Connecting a Chilled Mirror Instrument, Sample Loop Operation.......................................................................................................... 23
Section 4: Installation Safety & Transit.............................................................................................................................................................................
4.1 Installation, Power Isolation, Earthing, Earth Leakage Current, Over Current Protection, Voltage Rating ............................................ 24
4.7 Conductive Pollution, Preparing the Unit for Transit or Storage............................................................................................................. 25
4.9 Power management ............................................................................................................................................................................... 26
4.10 Shutdown procedures .......................................................................................................................................................................... 27
Section 5: HW4 Embedded................................................................................................................................................................................................
5.1 HW4 Setup and Getting Started ............................................................................................................................................................. 28
5.2 HW4 Installation and Registration, HW4 Support, HW4 Upgrades........................................................................................................ 28
Section 6: Calibration Reference Opions and Uncertainty ..............................................................................................................................................
6.1 Humidity Calibration Reference Options ................................................................................................................................................ 29
6.2 Internal RH Probe Reference, External RH Probe Reference .................................................................................................................. 30
6.4 Chilled Mirror Humidity Reference ......................................................................................................................................................... 31
6.5 Practical Guidance - Chilled Mirror Reference........................................................................................................................................ 32
Section 7: Practical User Notes ........................................................................................................................................................................................
7.1 Probe insertion depth, Stabilisation time ............................................................................................................................................... 33
7.3 Avoiding condensation, Dessicant choice, Calibrating or adjusting HygroClip probes ........................................................................... 34
Section 8: HygroGen Settings and Updates ......................................................................................................................................................................
8.1 HygroGen settings, water level, dessicant, monitor setup ..................................................................................................................... 35
8.5 Date and time, Controller / HW4 Software Update................................................................................................................................ 36
Section 9: HygroGen Screen Messages ......................................................................................................................................................................... 37
Section 10: HygroGen Specification .............................................................................................................................................................................. 38
Section 11: HygroGen Order Codes.......................................................................................................................................................................... 39-40
Section 12: HygroGen Warranty Statement ................................................................................................................................................................. 41
Section 13: Manufacturer & Service Centre Contact Information ............................................................................................................................... 42
Appendices
Appendix 1 - HygroGen Uncertainty Framework - Internal RH probe
Appendix 2 - HygroGen Uncertainty Framework - External RH probe
Appendix 3 - HygroGen Uncertainty Framework - Chilled Mirror Reference
Appendix 4 - Dew Point Uncertainty Analysis

E-M-HG2-S-V1_04
Rotronic AG
Bassersdorf, Switzerland
Document code Unit
HygroGen2 humidity and temperature
generator: Instruction Manual Instruction Manual
Document Type
Page 4of 46
Document title
© 2009-2010; Rotronic AG 4E-M-HG2-S-V1_04
Introduction to the HygroGen
HygroGen is a generator of controlled % relative humidity and temperature environments, primarily for use in
calibrating humidity instrumentation, but also well suited to the calibration of temperature instrumentation,
specifically those used for the measurement of temperature in air.
It is completely self-contained, requiring no external resources except mains power, and is light enough to be
portable for use on-site. This allows technicians to perform calibrations in the laboratory, workshop or on-site.
When used on site, the benefit of a full system calibration can significantly reduce calibration workload in checking
each element of a system and obviate the need to remove instruments from the installation location.
The HygroGen uses a mixed flow method for generating the %rh required by the user, a desiccant cell provides a
source of low humidity, and a piezoelectric humidifier generates high humidity. A Peltier element is used for
heating and cooling the chamber. Measurement and control is provided by a combination of a ROTRONIC
HygroClip probe, an embedded Platinum Resistance Thermometer (PRT) and a multi-loop controller with a touch
screen user interface. Set-points are input using the touch screen front panel display.
The key advantage of the HygroGen is the rapid time to reach equilibrium of the set values, which means that a
multiple-point calibration check can be performed in minutes, rather than hours. With integrated temperature
control, calibrations can always be performed at a defined and constant temperature, irrespective of the ambient
conditions, making the HygroGen suitable for on-site calibrations. It is also possible to calibrate equipment over
their typical working temperature and humidity conditions.
HygroGen includes an embedded controller running a Windows operating system that has had all configuration
settings removed from user access or manipulation. Essential functions can be accessed through menus described
in the HygroGen Settings Section.
The convenience of PC functionality and a USB interface enables the use of Rotronic HW4 software and USB
peripherals such as a keyboard and mouse. Nine USB connections are fitted to the front and back of the HygroGen.
Rotronic USB instruments can be connected to HW4 software through this same interface so that standard
Rotronic calibration adjustment functions can be performed without the need for a separate PC. An external DVI
monitor interface is also included so that HW4 can be displayed full size by the user.
Contents of the Standard Supply Package:
HG2-S HygroGen generator
HG2-DES Desiccant cell filled with molecular sieve
IEC mains cable
HG2-FILL Water fill syringe (with tube)
HC2-S HygroClip control probe with calibration certificate1)
Sample Loop connector cover plugs
This Manual
Chamber door (according to customer's order) 2)
HW4 software ID number
USB memory stick including saved test data and user manual.
1) The calibration certificate included will vary according to the country of supply
2) In some countries, the chamber door is delivered with the HygroGen. Due to the diversity of chamber doors and bungs, these normally are to
be ordered separately and may be delivered in separate packaging.

E-M-HG2-S-V1_04
Rotronic AG
Bassersdorf, Switzerland
Document code Unit
HygroGen2 humidity and temperature
generator: Instruction Manual Instruction Manual
Document Type
Page 5of 46
Document title
© 2009-2010; Rotronic AG 5E-M-HG2-S-V1_04
Part and Screen Identification Diagrams
Figure 1: Front of HygroGen
1) Power switch
2) USB ports
3) Touch screen controller
4) Water port
5) Desiccant cell
6) Chamber door
7) Probe aperture bung
8) Handle
Figure 2: Rear of
HygroGen
1) Sample loop return
2) Sample loop outlet
3) USB ports
4) DVI monitor interface
5) Ethernet socket (service use)
6) Type label
7) Fan outlet
8) Electrical mains connection
9) Power switch

E-M-HG2-S-V1_04
Rotronic AG
Bassersdorf, Switzerland
Document code Unit
HygroGen2 humidity and temperature
generator: Instruction Manual Instruction Manual
Document Type
Page 6of 46
Document title
© 2009-2010; Rotronic AG 6E-M-HG2-S-V1_04
Figure 3: HygroGen Screens
The HygroGen controller consists of four primary screens that are accessed using the forward or back
buttons in a loop:
Secondary Screens are accessed through touch screen buttons. Examples are shown below; sub-screens
and their use are described later in the relevant Section of this manual.
•Program edit
•Monitor-setup
•Pt100 Reference
•Date & time
•Update

E-M-HG2-S-V1_04
Rotronic AG
Bassersdorf, Switzerland
Document code Unit
HygroGen2 humidity and temperature
generator: Instruction Manual Instruction Manual
Document Type
Page 7of 46
Document title
© 2009-2010; Rotronic AG 7E-M-HG2-S-V1_04
Figure 4: Controller Primary Screen
1) Menu access (top left corner HOME)
2) Parameter identification °C
3) Actual chamber temperature
4) Temperature set point
5) Temperature control status indicator
6) Automatic/Manual selection
7) Parameter identification %rh
8) Actual chamber humidity
9) Humidity set-point
10) Humidity control status indicator:
11) Automatic/Manual selection
12) Back to previous screen
13) Access programmer function
14) Access HW4 software
15) Power off
16) Forward to next screen
Figure 5: Trend Screen
1) Graphical trend display
2) Parameter/set point display selection
3) °C actual and set point values
4) %rh actual and set point values
5) Date and time settings
6) Back to previous screen
7) Access programmer function
8) Access HW4 software
9) Power off
10) Forward to next screen
Figure 6: Programmer Screen
1) Scroll back/forward through programs
2) Program number and name
3) Scroll set-points of displayed program
4) Step and set-point conditions
5) Run/stop displayed program
6) Program/step time display
7) Back to previous screen
8) Access programmer function
9) Access HW4 software
10) Power off
11) Forward to next screen

E-M-HG2-S-V1_04
Rotronic AG
Bassersdorf, Switzerland
Document code Unit
HygroGen2 humidity and temperature
generator: Instruction Manual Instruction Manual
Document Type
Page 8of 46
Document title
© 2009-2010; Rotronic AG 8E-M-HG2-S-V1_04
Figure 7: Program Edit Screen
1) Graphical display of program
2) Program step number
3) Temperature set-point
4) Humidity set-point
5) Set-point duration
6) Insert new program step
7) Delete program step
8) Scroll across set-point steps
9) Current program number and name
10) Temperature set-point stability criteria
11) Humidity set-point stability criteria
12) Make set-point temperature only
13) Forward to next screen
Figure 8: Settings Screen
1) Water level display
2) Desiccant condition display
3) External monitor set up
4) Date and time settings
5) Software update utility
6) HG information access
7) Back to previous menu
8) Access programmer function
9) Access HW4 software
10) Power off
11) Forward to next screen
Figure 9: Set-Point Entry Pop-Up
At any time, the user can change humidity or
temperature set-points by simply touching
the set-point on screen. This pop-up will
appear, and either the touch screen or where
connected the keyboard/mouse used to input
desired values.

E-M-HG2-S-V1_04
Rotronic AG
Bassersdorf, Switzerland
Document code Unit
HygroGen2 humidity and temperature
generator: Instruction Manual Instruction Manual
Document Type
Page 9of 46
Document title
© 2009-2010; Rotronic AG 9E-M-HG2-S-V1_04
Section 1: Operation
1.1 Before Switching On
Ensure the operator has read and implemented Section 4 of this manual “Installation, safety and transit”
Check there is no water in the chamber - see Section 1.8
If the unit is being switched on for the first time, or after storage or transit, please fill the
water reservoir, as described in the ‘How to Fill the Water Reservoir’ - Section 2.1 (page 13)
If the unit is used in a manner not specified by ROTRONIC, the function and protection provided by the
unit may be impaired.
Note: The feet on the rear panel are for standing the unit for service purposes, and to ensure a sufficient
air gap behind the unit. The unit will not operate in the vertical position.
1.2 Switching On
1) Ensure the electrical mains supply is correctly plugged in and switched on.
2) Switch the unit on by pressing the Power Switch (figure 1) once.
3) The fans within the unit will switch giving an immediate audible indication the unit is powered.
4) The controller will power up and settle to the controller primary screen in figure 3.
On power up:
•The temperature and humidity set-points default to the last set values.
•The temperature control defaults to automatic mode (controlling the temperature)
•The humidity control defaults to manual mode
If the ‘Low Water Level’ alarm is displayed then the unit should be filled as described
in the ‘How to Fill the Water Reservoir’ Section 2.1. Humidification is disabled until
water is filled.
1.3 Automatic/Manual Mode
Both temperature and humidity control can be set to automatic or
manual. Automatic mode results in the unit attempting to adjust to the
temperature (or humidity) in the chamber to match the set-point value.
Manual mode (automatic/manual selection displays ‘Off’) prevents the
unit from trying to control the chamber.
The automatic or manual status of both the temperature and humidity control is displayed on the
controller primary screen (figure 4). To toggle the humidity or temperature control loop between
automatic and manual press the automatic/manual selection for temperature or humidity.

E-M-HG2-S-V1_04
Rotronic AG
Bassersdorf, Switzerland
Document code Unit
HygroGen2 humidity and temperature
generator: Instruction Manual Instruction Manual
Document Type
Page 10 of 46
Document title
© 2009-2010; Rotronic AG 10 E-M-HG2-S-V1_04
1.4 Setting Temperature and Humidity Set-Points
The temperature and humidity set-points are set by touching the set-point
value on the primary controller screen. When in automatic mode the set-
point value can be adjusted by entering the desired set point value in the
pop-up window that is displayed.
NOTE: To aid a smooth and efficient transition between temperature set-points the controller is
programmed to suspend humidification during changes in temperature. Once the chamber temperature
is within 0.7°C of the temperature set-point, the humidity control is activated.
When set-point combinations that resolve a low dew point condition (i.e. 0°C, 5%rh = -36°C dew point)
are input, make sure that the desiccant is dry enough to achieve the desired value. Check the desiccant
condition on screen (Figure 8) and consult maintenance records to establish when the desiccant was last
changed. Stabilisation time to low RH conditions will be longer than normal as the chamber and internal
surfaces need to be very dry.
Once the HygroGen has reached a stable condition, the Auto/Manual button will change colour to
green.
1.5 Below Ambient Temperature Operation
If the chamber is cooling (or maintaining a temperature below ambient), then the heat pump assembly
inside the chamber will necessarily be below the chamber temperature. If the humidity in the chamber
is high, the cool heat pump assembly can bring the local air temperature below the dew point, causing
condensation to occur on the internal heat pump assembly. If run under these conditions for extended
periods condensation will collect in the chamber. This will not affect chamber performance within
normal operating ranges (though it will increase the time to achieve low humidity). Water in the
chamber can be removed using an absorbent tissue. Ensure the HygroGen is switched off before
manually drying the chamber.
When operating the unit at high humidity and chamber temperatures of more than a few degrees below
ambient the following procedure will minimise condensation in the chamber during stabilisation.
1. Set-point temperature to approximately ambient
2. Set-point humidity to that desired and allow the HygroGen to stabilise
3. Set the humidity control to Manual (as described in Automatic/Manual Mode Section 1.3).
4. Apply the temperature set-point to that desired and allow the HygroGen to stabilise
5. Wait for the Humidity reading to fully stabilise (may take 15 to 20 minutes)
6. Set the humidity control loop to Automatic
It is recommended that the chamber door is not opened when the chamber temperature is below the
ambient temperature as water vapour from the atmospheric air introduced will condense out in to the
chamber. The dehumidification of the chamber takes longer at lower chamber temperatures.

E-M-HG2-S-V1_04
Rotronic AG
Bassersdorf, Switzerland
Document code Unit
HygroGen2 humidity and temperature
generator: Instruction Manual Instruction Manual
Document Type
Page 11 of 46
Document title
© 2009-2010; Rotronic AG 11 E-M-HG2-S-V1_04
Humidity Map
1.6 Above Ambient Temperature Operation
At high temperature and high relative humidity conditions it is necessary to allow the unit to stabilize to
ensure minimal condensation. It is recommended that for making measurements over 45 °C and 80 %rh
that the HygroGen temperature be permitted to equilibrate for 20 minutes before high humidity is
introduced. It is also recommended that under these conditions the desired %rh level is achieved in
incremental steps, allowing stabilisation at each. If the unit is operated at high temperature and high
humidity for prolonged periods it is strongly recommended that the chamber is thoroughly
dehumidified prior to switching the unit off.
1.7 Programmer Function
The HygroGen programmer function enables the user to pre-define a series of RH and/or temperature
set-points. This is typically used to run a routine sequence of calibration steps without user intervention
to change set-points.
The Programmer Screen includes three pairs
of buttons:
Program – Identifies the program number and
its description. You can use the << and >>
buttons to scroll through the saved programs.
Step – Identifies the set-point within the
program and its values. You can use the << and
>> buttons to scroll through the steps. (SP = Set-
Point)

E-M-HG2-S-V1_04
Rotronic AG
Bassersdorf, Switzerland
Document code Unit
HygroGen2 humidity and temperature
generator: Instruction Manual Instruction Manual
Document Type
Page 12 of 46
Document title
© 2009-2010; Rotronic AG 12 E-M-HG2-S-V1_04
Play/stop – Starts or stops the program and displays the Run and Step timing information
Program Run Time – Defines how long the current program has been running.
Step Remaining - Defines how long the current program step has left to run.
Below these, there is a display of the current control value and set-point
To edit the programs, either press/click a set-point value or the ‘Edit’ key.
This opens the Program Edit screen as shown. The
set-point steps are numbered, and below each
step it is possible to change the set point values
and step duration. Steps can also be deleted if
required. A graphical representation of the
program is shown above each point.
Below the edit screen the program number and
name is displayed (this can be edited using a
keyboard). Temperature and humidity stabilisation
criteria can be changed below this. These values
define when the set-point has been reached and is
stable; once the control is within this tolerance;
timing of the step duration begins. If set to zero, no stabilisation criteria are applied, and the timing of
the step duration begins immediately.
1.8 Water in the Chamber
Under some operating conditions (illustrated as hatched regions shown in Section 1.5) water droplets
may form in the unit chamber. This will not affect chamber performance within normal operating ranges
(though it will increase the time to achieve low humidity) and can be removed using an absorbent
tissue. Ensure the HygroGen is switched off before manually drying the chamber.
Before using the HygroGen, check that there is no visible water inside the chamber. If the HygroGen has
been shipped without being emptied, water may enter the chamber from the water reservoir. If the last
condition run by the HygroGen was at high humidity, and the unit not correctly shut down (see below),
condensate may have formed. In both cases, report findings to the shipper or last user. Remove excess
water using absorbent tissue and initially run the HygroGen at an elevated temperature (40°C) and low
RH set-point to dry the system before calibrations are run.

E-M-HG2-S-V1_04
Rotronic AG
Bassersdorf, Switzerland
Document code Unit
HygroGen2 humidity and temperature
generator: Instruction Manual Instruction Manual
Document Type
Page 13 of 46
Document title
© 2009-2010; Rotronic AG 13 E-M-HG2-S-V1_04
1.9 Low Water Level Alarm
The HygroGen requires water to create high levels of humidity returning from
the internal saturator. The unit will inform the operator if the water level in the
reservoir is too low with a visual ‘Low Water Level’ alarm prompt on the
controller screen. This prompt may be dismissed by following the-on screen
instructions. When the ‘Low Water Level’ appears replenish the reservoir with
≈50 ml of water.
If the water level in the saturator persistently falls below ≈20 ml, a ‘Humidity
Disabled’ warning is triggered and humidification is disabled to prevent damage to the humidifier.
Humidification will not be re-activated until the water level is restored.
An alarm icon shows in the top right-hand corner of the screen when a warning condition
exists.
Water level may be checked at any time within the settings screen. The water level
sensor is for indication only; observe the volume specified within Section 2.1 when
adding or removing water. The fill syringe (HG2-FILL) supplied with the HygroGen
includes volume markings to assist in this respect.
Note: If the ‘Low Water Level’ message appears on the controller screen during use,
the HygroGen can be topped up with 50 ml of distilled water. This will bring the total
water content of the reservoir to approximately 80 ml. Ensure the electrical supply to the
HygroGen is disconnected during filling.
1.10 Switching Off
Before switching off the HygroGen the chamber should be dried to avoid condensation occurring within
the HygroGen chamber. If you use the master power switch, you should first dry the chamber by setting
a low RH value.
The touch screen power button shuts the HygroGen down
in a controlled manner (see also 4.10). Pressing this button
opens a screen as shown; either wait 30 seconds or
confirm Shut Down. This initiates a sequence that conditions the
HygroGen chamber to a safe state that eliminates the possibility of
condensation formation during cooling. The HygroGen automatically
reduces the chamber RH before powering down (see Section 4.10 for a full description of
Transit/Shutdown modes).

E-M-HG2-S-V1_04
Rotronic AG
Bassersdorf, Switzerland
Document code Unit
HygroGen2 humidity and temperature
generator: Instruction Manual Instruction Manual
Document Type
Page 14 of 46
Document title
© 2009-2010; Rotronic AG 14 E-M-HG2-S-V1_04
Section 2: Maintenance and Servicing
2.1 How to Fill the Water Reservoir
The HygroGen requires 30…80 ml of distilled water in the internal reservoir. Insufficient water will
deactivate the humidification system. Excessive water may result in poor humidification; poor drying
and water in the chamber (Section 1.8).
To correctly fill the HygroGen:
1) Place the HygroGen on a level surface.
2) Disconnect the electrical supply to the HygroGen.
3) Insert the tube of the dosing syringe 10 mm in to the Water Port and extract any residual water.
4) Depress the collar on the Water Port, remove the dosing syringe tube. Wipe up any spilt water
with an absorbent cloth immediately.
5) Charge the dosing syringe with 80 ml of distilled water. Insert the end of the dosing syringe tube
firmly into the Water Port and discharge the syringe steadily (if water leaks during this operation
the filler tube is not correctly inserted in the Water Port).
6) Depress the collar on the Water Port to remove the dosing syringe tube. Wipe up any spilt water
with an absorbent cloth immediately.
7) Restart the HygroGen and check the water level indication in the Settings screen.
2.2 Overfilling the HygroGen
Overfilling of the unit will result in poor humidification and in extreme cases water may be pumped into
the chamber. If the HygroGen is overfilled the humidifier should be fully emptied and then refilled with
50 –80 ml of water (as described in above). If there is water present in the chamber of the HygroGen,
this should be removed using an absorbent cloth. Ensure the HygroGen is switched off before manually
drying the chamber.

E-M-HG2-S-V1_04
Rotronic AG
Bassersdorf, Switzerland
Document code Unit
HygroGen2 humidity and temperature
generator: Instruction Manual Instruction Manual
Document Type
Page 15 of 46
Document title
© 2009-2010; Rotronic AG 15 E-M-HG2-S-V1_04
2.3 How to Empty the Water Reservoir
1) Place the HygroGen on a level surface.
2) Disconnect the electrical supply to the HygroGen.
3) Insert the tube of the dosing syringe 10 mm in to the Water Port and extract any residual water.
4) Depress the collar on the Water Port, remove the dosing syringe tube. Wipe up any spilt water
with an absorbent cloth immediately.
Note: The HygroGen should always be emptied if it is being shipped or stored (see Preparing
the Unit for Transit or Storage). This will prevent ingress of water in to the chamber should the
unit be inverted, and prevent possible frost damage.
2.4 How to Change the Desiccant
The HygroGen requires the desiccant to dry air passed through it in order to reduce
the humidity in the chamber. The desiccant condition is available within the ‘Settings’
screen (figure 8). This is an approximate indication of the dew point within the dryer
cell. Readings should be observed only when the HygroGen is drying to a low set-
point this ensures that the desiccant cell measurement sensor is being purged by a
flow of gas from the desiccant cell. If the HygroGen does not reach low RH set-points
in the normal time, check the desiccant condition and replace as required.
To remove the desiccant cell from the unit, it should be pulled perpendicular to the
front panel of the unit. The cell is held in place tightly to maintain an air-tight seal; a
gentle twist will help removal. Changing the desiccant should be undertaken in a
ventilated area.
Observing the diagram below, remove the cap and pour out the used desiccant
material and replace. This should be performed in a timely manner to avoid
absorption of water vapour into the dry desiccant. See Section 2.7 for information on
how to regenerate used desiccant.
It is necessary to ensure that the cell is replenished with the same volume of
desiccant as is removed. It may be necessary to tap the desiccant beads down to
ensure there are no excess air gaps. If the desiccant cell is not fully filled, the drying
performance of the HygroGen will be impaired. Remember to replace the foam insert (that fits between
the cell cap and the desiccant) before replacing the cell cap and spring clip. Application of silicone grease
on the desiccant cell cap ‘O’ ring will help ease removal and refitting.

E-M-HG2-S-V1_04
Rotronic AG
Bassersdorf, Switzerland
Document code Unit
HygroGen2 humidity and temperature
generator: Instruction Manual Instruction Manual
Document Type
Page 16 of 46
Document title
© 2009-2010; Rotronic AG 16 E-M-HG2-S-V1_04
Desiccant Cell
5a – Cell cap
5b – Retaining clip
5c – Cell body
Caution: Do not use dusty
desiccants as the dust
may be passed into the
chamber.
2.5 Choice of Desiccant
The HygroGen is supplied from the factory with the desiccant cell packed with molecular sieve. A variety
of desiccant materials may be used in the HygroGen desiccant cell. Some of these are outlined below,
including their effectiveness and health and safety implications. Dusty desiccants should be avoided as
the dust may be passed in to the HygroGen chamber. Material Safety sheets for the desiccants supplied
by ROTRONIC are available on request.
2.6 Molecular Sieve Desiccant (Factory Standard)
Molecular sieves have the appearance of small opaque tan beads. Molecular sieves are synthetically
produced, highly porous crystalline metal-alumina silicates. They have many internal cavities that are
linked by window openings of precise diameters. It is these diameters (measured in Angstroms) that
classify molecular sieves. Adsorption occurs only for molecules with smaller diameters than these cavity
openings. Larger molecules will be excluded from adsorption. Preferentially adsorbed are molecules of
greater polarity. This makes molecular sieves ideal for adsorption of water from air and liquids, as water
molecules are both polar and very small.
Molecular sieves will absorb water molecules and other contaminants from liquids and gases down to
very low levels - often just 1 part per million. Molecular sieve’s desiccant properties differ from silica gel
in a number of ways. They absorb water vapour more rapidly and they will reduce water vapour to
much lower levels than silica gel, making their use essential when a very dry atmosphere is required.
They perform more effectively as moisture absorbers at higher temperatures (greater than 25°C) than
silica gel does. Molecular sieve desiccant contains less than 1% quartz, classed as a carcinogen in the EU.

E-M-HG2-S-V1_04
Rotronic AG
Bassersdorf, Switzerland
Document code Unit
HygroGen2 humidity and temperature
generator: Instruction Manual Instruction Manual
Document Type
Page 17 of 46
Document title
© 2009-2010; Rotronic AG 17 E-M-HG2-S-V1_04
2.7 Regeneration of Molecular Sieve Desiccant
Molecular sieve desiccant may be regenerated by heating, however unless effectiveness of the
regenerated molecular sieve can be determined it is recommended that new molecular sieve desiccant
is used. This can be ordered from ROTRONIC.
To regenerate molecular sieve remove it from the desiccant cell and heat it at 175 °C for at least 3…5
hours in a dry environment (do not use a gas oven). After heating, transfer the desiccant to a sealed
container and allow cooling to room temperature. Check the effectiveness of the regeneration by
measuring the % relative humidity of the dried desiccant prior to recharging the desiccant cell.
2.8 Silica Gel Desiccant
Silica gel is an amorphous form of silicon dioxide, which is synthetically produced in the form of hard
irregular granules (having the appearance of crystals) or hard irregular beads. A micro porous structure
of interlocking cavities gives a very high surface area (800 square metres per gram). It is this structure
that makes silica gel a high capacity desiccant. Water molecules adhere to the gel surface because it
exhibits a lower vapour pressure than the surrounding air. When equilibrium of equal pressure is
reached, no more adsorption occurs. Thus the higher the humidity of the surrounding air, the greater
the amount of water that is adsorbed before equilibrium is reached. Self-indicating silica gel changes
colour once it has become saturated offering an easy method of checking if it is necessary to replace.
Silica gel does not perform well at low temperatures and rapidly becomes saturated at low relative
humidity. Silica gel is suitable for approximately ambient temperature use, where relative humidity
below approximately 30% is not required. There is minimal health and safety implications, non-
indicating (white), and orange to green self-indicating silica gels are non-toxic.
2.9 Regeneration of Silica Gel Desiccant
As a general rule saturated silica gel desiccant will require a minimum of 4-6 hours at a temperature of
between 105-130 °C throughout the entire desiccant bed for the reactivation process to be effective and
reduce the adsorbed moisture to less than 2% by weight. Heating to higher temperatures will damage
the desiccant. Reactivation should be carried out in a ventilated electric oven. A sealed oven will limit
the moisture liberated and prevent efficient reactivation. Gas ovens and microwave cookers are not
suitable for reactivation. After reactivation the desiccant must be placed in a sealed container and
allowed to cool.
For most situations it recommended that new silica gel is used unless a proven process for regeneration
can be implemented. Regeneration can be carried out repeatedly, although eventually the beads will
lose their colour. Replacement Orange to Green self-indicating silica gel can be ordered from ROTRONIC.
2.10 Drierite Desiccant
Drierite is anhydrous calcium sulphate. It is of neutral pH, constant in volume, chemically inert except
towards water, insoluble in organic liquids and refrigerants, non-disintegrating, non-wetting, non-toxic,
non-corrosive, non-channelling, generally recognized as safe (GRAS) by the FDA, not regulated by OSHA,
economical to use, and can be regenerated repeatedly for reuse. Moisture absorption is good across the
range of conditions encountered in the HygroGen.

E-M-HG2-S-V1_04
Rotronic AG
Bassersdorf, Switzerland
Document code Unit
HygroGen2 humidity and temperature
generator: Instruction Manual Instruction Manual
Document Type
Page 18 of 46
Document title
© 2009-2010; Rotronic AG 18 E-M-HG2-S-V1_04
2.11 Regeneration of Drierite Desiccant
For the regeneration of Drierite the granules may be spread in layers one granule deep and heated for 1
hour at 210 ° C. The regenerated material should be placed in a storage container and sealed while hot.
The colour of self-indicating Drierite may become less distinct on successive regenerations due to the
migration of the indicator into the interior of the granule and sublimation of the indicator. The structure
of the Drierite granules can break down during regeneration. If the result is dusty it should not be
reused in the desiccant cell. Replacement Drierite desiccant can be ordered from ROTRONIC.
2.12 Blue-to-Pink Self-Indicating Desiccant
Until recently most self-indicating desiccants used a small concentration (between 0.5 and 3.0 % weight
for weight) of moisture sensitive cobalt chloride indicator. This is blue when anhydrous and changes to
pink as it adsorbs moisture and becomes saturated, returning to blue as it is regenerated. European
Commission Directive 98/98/EC (amendment to 67/548/EEC) has re-classified cobalt chloride as a
potential carcinogen.
2.13 HygroGen Door Removal and Refitting
To open the HygroGen chamber or remove the door, grip firmly and simply twist the door anti-
clockwise. In the event that this proves difficult, cool the chamber first. Occasional application of
silicone grease around the door ‘O’ ring seal will ease movement.
Replacement can be in any position, and requires only a gentle clockwise twist.
2.14 HygroClip Probe Removal and Refitting
In the event that the control probe requires recalibration, set the HygroGen temperature and RH control
to manual and remove the door. Reach into the chamber and unscrew the HygroClip probe retaining
collar until it can be disconnected from its mounting connector. Take care not to cross the threads on
the collar when refitting.
To minimise HygroGen downtime, a pre-calibrated replacement probe can be fitted in place of the
existing probe. Contact Rotronic or your local supplier for advice.

E-M-HG2-S-V1_04
Rotronic AG
Bassersdorf, Switzerland
Document code Unit
HygroGen2 humidity and temperature
generator: Instruction Manual Instruction Manual
Document Type
Page 19 of 46
Document title
© 2009-2010; Rotronic AG 19 E-M-HG2-S-V1_04
2.15 HygroGen External Cleaning
Prior to cleaning, the unit must be disconnected from the electrical mains supply, as described in Power
Isolation Section 4.2.
External surfaces:
The external surfaces of the HygroGen may be cleaned with a lint-free cloth dampened with a mild soap
solution. Care must be taken not to allow fluids in to any of the apertures or mains socket on the unit.
Touch screen:
1) Clean the screen before turning it on. It is much easier to see dirt and fingerprints on a dark
screen and a cool screen is less likely to leave streaks.
2) Use a lint-free cloth rather than a paper towel, as paper towels can potentially scratch the
screen. Moisten the cloth with distilled water or a cleaner specifically formulated for touch
screens (screen cleaners are available online and at electronics stores). Do not use glass cleaners
that contain ammonia or alcohol as they may damage the screen over time.
3) Spray cleaner onto the cloth rather than directly onto the screen. Gently wipe the screen with
the damp cloth, and then use a dry cloth to wipe any excess moisture.
4) Pre-moistened wipes specifically designed to clean touch screens are convenient and can also
provide anti-static protection
Filter:
The fan inlet filter can be cleaned using a vacuum cleaner to remove any particulates. The filter material
is replaced during servicing.

E-M-HG2-S-V1_04
Rotronic AG
Bassersdorf, Switzerland
Document code Unit
HygroGen2 humidity and temperature
generator: Instruction Manual Instruction Manual
Document Type
Page 20 of 46
Document title
© 2009-2010; Rotronic AG 20 E-M-HG2-S-V1_04
2.16 HygroGen Internal Cleaning
Prior to cleaning, the unit must be disconnected from the electrical mains supply, as described in Power
Isolation Section 4.2.
Periodically it is recommended that the internal surfaces of the
HygroGen chamber sleeve are inspected and wiped clean of any
visual residues using a lint-free cloth moistened with distilled water.
Care should be taken to avoid mechanical damage to the control
probe and sampling tubes inside the chamber. The HygroClip
control probe may be removed by unscrewing the retaining
aluminium collar in an anti-clockwise direction and carefully pulling
the probe from its locating connector. Replacement requires that
the probe is gently rotated until the connector keys allow the probe
to insert. DO NOT USE ANY MECHANICAL FORCE during removal or
refitting.
Some humidity instruments are used in environments where chemical contaminants may be present.
Should these transfer to the HygroGen, this may result in drift of the RH control probe, so during
calibration of the control probe should large deviations occur, this may be due to external
contamination. If you believe this to be the case, or wish to purge the internal pipe work and chamber of
the HygroGen, replace the desiccant with Granular Activate Charcoal (GAC) and run the unit at 40 °C and
5 %rh for 6 hours. Any volatile compounds within the HygroGen will be absorbed into the GAC.
2.17 HygroGen Servicing
The unit does not require routine user maintenance beyond that described in this Section; in particular
the ‘How to Fill the Water Reservoir’ and ‘How to Change the Desiccant Cell Sections. Should the unit
develop a fault or exhibit errant performance the unit should be switched off, disconnected, labelled as
a potential hazard and the manufacturer or service centre contacted (Section 13).
For optimum performance ROTRONIC recommend that the HygoGen is serviced on an annual basis
(every 12 months) through an approved HygroGen service centre, details of which can be found in
Section 13 of this manual.
Under no circumstance should the unit be opened by personnel unauthorised by the
manufacturer. Doing so will void the manufacturer’s warranty, and expose potentially
dangerous electrical hazards.
Other manuals for hygrogen2
1
Table of contents
Popular Portable Generator manuals by other brands

STEELE PRODUCTS
STEELE PRODUCTS SP-GG1000E owner's manual
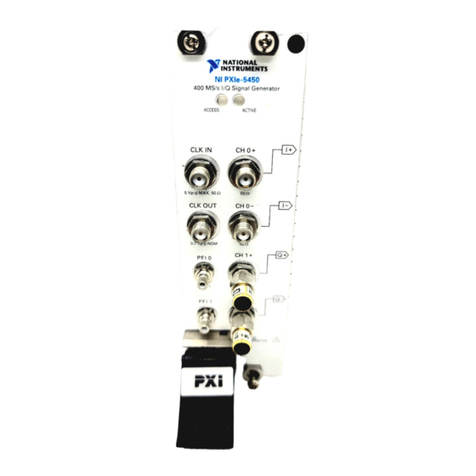
National Instruments
National Instruments NI PXIe-5450 SAFETY, ENVIRONMENTAL, AND REGULATORY INFORMATION
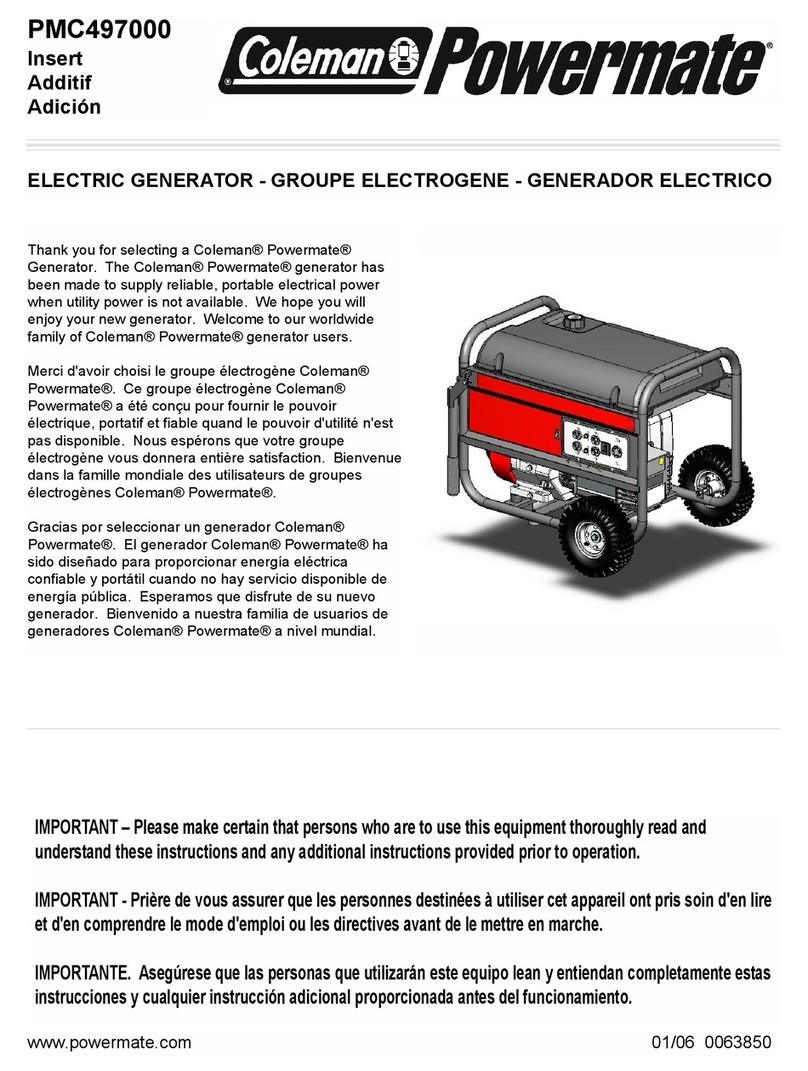
Powermate
Powermate PMC497000 owner's manual
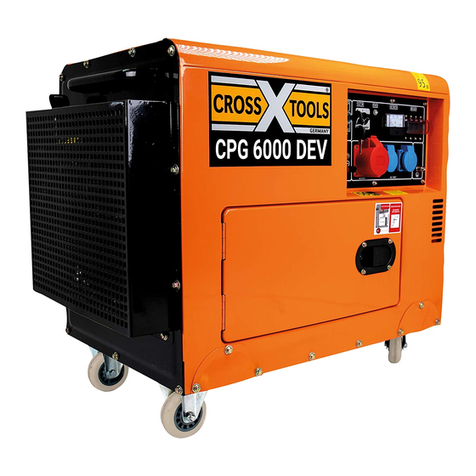
Cross Tools
Cross Tools CPG 6000 DEV Operating instruction
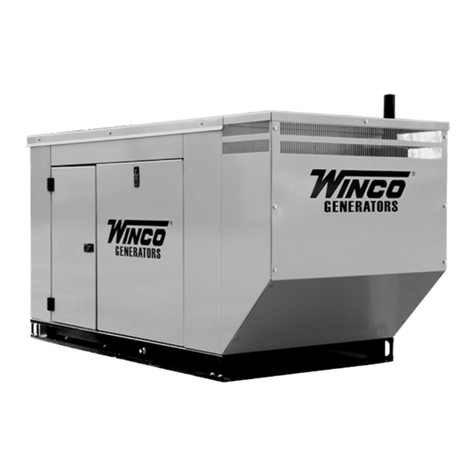
Winco
Winco DR12I4/1 Installation and operator's manual
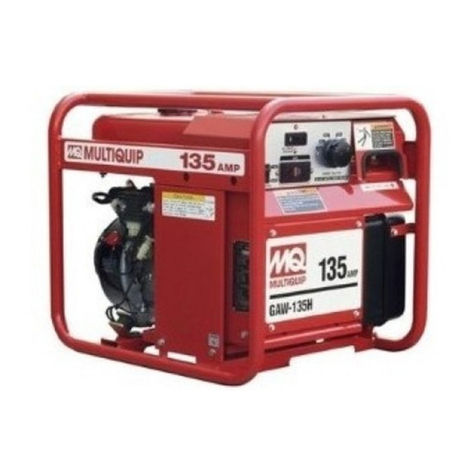
MULTIQUIP
MULTIQUIP GAW-135H Operation and parts manual