SCHUNK TENDO Turn DSE User instructions

Assembly and Operating Manual
TENDO Turn DSE
Hydraulic expansion toolholder
1General
1.1About this manual
This manual is part of the product and contains important
information for safe and correct use. It must be kept accessible
at all times. Personnel must have read and understood this
manual before starting any work. All safety notes and the
associated specifications in particular must be observed and
complied with. Illustrations may differ from the actual design.
1.2Applicable documents
– General terms of business
– Catalog data sheet of the purchased product
The other applicable documents can be downloaded from
schunk.com.
1.3Warranty
The warranty is valid for 24 months from the date of delivery
from the production facility if the product is used as intended
and in compliance with the prescribed operating data.
Wear parts and parts that come in contact with the tool or
machine are not covered by the warranty.
1.4Illustration of warnings
WARNING
Dangers for persons!
Non-observance can lead to irreversible injury and even
death.
CAUTION
Dangers for persons!
Non-observance can cause minor injuries.
NOTICE
Material damage!
Information about avoiding material damage.
1.5Scope of delivery
– Product
– Assembly and Operating Manual
1.6Accessories
The following accessories for the product are available
separately:
– Test shaft for monitoring the expansion rate
– Allen key for operating the clamping screw
– Hexagon socket wrench for length adjustment
– GZB-S intermediate sleeves for clamping several different
shank diameters
– GZB-S sleeve remover for removing intermediate sleeves
2Basic safety notes
2.1Appropriate use
– The product is used to clamp rotationally symmetric tools.
– The product is intended for industrial use.
– The product is intended for installation in a machine/
automated system. The applicable guidelines for the
machine/automated system must be observed and complied
with.
– The product may only be used and operated within the scope
of the technical data and the specifications in this
manual, }Chap.3.
2.2Inappropriate use
The product is not being used as intended if:
– The information in the technical data is not observed when
using and operating the product }Chap.3.
– The maintenance and storage instructions are not
observed }Chap.5.
– The product is used with heat shrinking technology.
2.3Ambient conditions and operating conditions
The ambient and operating conditions must correspond or be
adapted to the version of the product and the specifications in
the technical data.
2.4Structural changes, spare parts
Structural changes such as modification and reworking, e.g.
additional threads, bore holes or attachments, may only be
carried out with the written approval of SCHUNK. Only use
original spare parts and spares authorized by SCHUNK.
2.5Notes on safe operation
– The product must not be clamped without a tool above 25°C.
– Never combine multiple product extensions.
– Only use SCHUNK intermediate sleeves and always insert up
to the fixed backstop point. The use of intermediate sleeves
can reduce the transmittable torque.
– Long, projecting or heavy tools may only be clamped if the
speed of rotation is reduced according to the ambient and
operating conditions on site. The level of reduction is the
responsibility of the operator and must ensure safe operation
of the product.
– Maintain and service the product on a regular basis.
– Do not remove the air bleed screw (secured with pin or
resin).
– All repair work must be performed by SCHUNK.
– The operational safety and function of the product must not
be impaired by external influences.
– Follow the country-specific applicable safety, accident
prevention, and environmental protection regulations for the
application field of the product.
– Use mechanical screwdrivers only after approval by SCHUNK.
2.6Personnel qualifications
– All operations may only be carried out by personnel that are
qualified and instructed for the respective operation.
– Personnel qualifications must comply with the on-site
country-specific requirements and laws.
2.7Personal protective equipment
– When working on and with the product, follow the
respective country-specific legal requirements for
occupational health and safety, and wear the necessary
personal protective equipment.
– Follow country-specific accident prevention regulations and
the general safety notes.
2.8Transport
To avoid product damage, the transport and handling of the
product must be adapted according to the version, weight and
packaging of the product. If necessary, use additional aids.
3Technical data
Operating temperature range [°C] +20 ... +50
Test temperature for the clamping force control
[°C] +20 ... +25
Max. coolant pressure [bar] 80
Adjustment travel of the length adjustment [mm] 10
Max. speed of rotation [RPM] 10,000
Wrench size, clamping screw A/F 5
Max. tightening torque of the clamping screw
[Nm] 10 … 12
Tolerance tool shank h6
Clamping diameter D1/D2 12 / 20 20 / 25
Permissible transmittable torque [Nm] 65 220
Minimum clamping depth [mm] 33.5 42.5
Permissible radial force F on the
product at 50 mm projecting length of
the tool [N]
500 500
Revolutions of the clamping screw for
pre-loading 1 3/4
Bore diameter, machine interface [mm] 20 H5 25 H5
The loading limits of the spindle holder must be observed.
①Product clamping depth ④ Length-setting range
②Clamping diameter D1 ⑤ Length-setting screw
③Minimum clamping depth ⑥ Clamping diameter D2
3.1Permitted shank types
1. Shank type according to DIN 1835-1 form A and DIN 6535
form HA
2. Shank type according to DIN 1835-1 form B and DIN 6535
form HB (Ø up to 20 mm)
3. Shank type according to DIN 1835-1 form B and DIN 6535
form HB (Ø from 25 mm)
Tool shanks with reliefs (forms 2 and 3) can impair the
balancing grade and concentricity of the overall system.

Copyright:
This manual is protected by copyright. The author is
SCHUNK GmbH & Co. KG. All rights reserved.
Technical changes:
We reserve the right to make alterations for the purpose of
technical improvement.
Document number:0289036
Edition:03.01|23/01/2023|en
SCHUNK GmbH & Co. KG
Spann- und Greiftechnik
Bahnhofstr. 106 – 134
D-74348 Lauffen/Neckar
Tel.+49-7133-103-0
Fax +49-7133-103-2399
schunk.com
0289036
4Operation
4.1Basic information
WARNING
Risk of injury due to ejected parts!
The max. speed of rotation of the machine/automated
system must be reduced when using long, projecting or
heavy tools and with extensions.
WARNING
Risk of injury and material damage due to the expansion
sleeve bursting!
If not used as intended, the expansion sleeve may burst. This
can cause metal shards and oil to be ejected from the
product under high pressure, resulting in serious injury.
•Never heat the product in heat shrink devices; only
perform a tool change using the integrated clamping
screw.
•Do not exceed the specified operating temperature.
CAUTION
Risk of injury from tools with sharp edges!
Sharp edges on tools can cause cuts.
•Wear protective gloves when assembling the tool.
NOTICE
Material damage due to burrs and dirt!
•The tool must be free of burrs and dirt at the shank.
•The machine interface must be free of burrs and dirt.
NOTICE
Material damage due to incorrect minimum clamping
depth!
Too small a clamping depth of the tool leads to a loss of
accuracy and torque on the product.
•Observe the minimum clamping depth of the tool.
NOTICE
Potential impairment of the clamping function and damage
to the product!
If the product is not used as intended, the clamping function
may be impaired or the product may get damaged.
•Only operate the clamping screw by hand.
•Do not adjust the projecting lengths of the tool when the
product is clamped.
4.2Assembly of tool and product
TENDO Turn DSE with one clamping screw
①Clamping screw ③ Length-setting range
②Minimum clamping depth ④ Length-setting screw
TENDO Turn DSE with two clamping screws
①Locking screw ④ Length-setting range
②Clamping screw 2 ⑤ Length-setting screw
③Minimum clamping depth ⑥ Clamping screw 1
TENDO Turn DSE with one clamping screw
1. Unclamp the product by loosening the clamping screw.
NOTE: The clamping screw is not secured against falling out.
2. If required, the projecting lengths of the tool can be
adjusted by screwing the integrated length-setting screw in
or out. Observe the adjustment travel of the length-setting
screw }Chap.3.
3. Insert the tool to the minimum clamping depth or stop.
4. Screw the clamping screw in by hand. Observe the specified
revolution for pre-loading }Chap.3.
✓The tool is pre-loaded.
5. Position the product with pre-loaded tool correctly in the
machine interface and fit up to the stop.
6. Screw the clamping screw in by hand until it reaches the
stop. Observe the maximum specified tightening
torque }Chap.3.
7. Check that the product is in the correct position and
securely clamped in the machine.
IMPORTANT!Safe clamping of the product in the machine
must be ensured!
NOTE: Always clamp the inner diameter first! Only after
clamping the inner diameter is the outer diameter fully
cylindrical.
TENDO Turn DSE with two clamping screws
1. Unclamp the product by loosening clamping screws 1 and 2.
NOTE: Clamping screw 1 is not secured against falling out.
2. If required, the projecting lengths of the tool can be
adjusted by screwing the integrated length-setting screw in
or out. Observe the adjustment travel of the length-setting
screw }Chap.3.
3. Insert the tool to the minimum clamping depth or stop.
4. Screw clamping screw 1 in by hand until it reaches the stop.
Observe the maximum specified tightening
torque }Chap.3
✓The tool is pre-loaded.
5. Position the product with pre-loaded tool correctly in the
machine interface and fit up to the stop.
6. Screw clamping screw 2 in by hand until it reaches the stop.
Observe the maximum specified tightening
torque }Chap.3.
7. Check that the product is in the correct position and
securely clamped in the machine.
IMPORTANT!Safe clamping of the product in the machine
must be ensured!
NOTE: Always clamp the inner diameter first! Only after
clamping the inner diameter is the outer diameter fully
cylindrical.
4.3Tool change
TENDO Turn DSE with one clamping screw
1. Carefully loosen the clamping screw until the product can
be removed from the machine interface. IMPORTANT!If
the clamping screw is turned out too far, the tool is no
longer pre-loaded!
2. Remove the product from the machine interface.
3. Unclamp the product by fully loosening the clamping screw.
NOTE: The clamping screw is not secured against falling
out!
4. Remove tool.
5. Mount new tool }Chap.4.2.
TENDO Turn DSE with two clamping screws
1. Unscrew clamping screw 2 until it reaches the stop.
2. Remove the product from the machine interface.
3. Unclamp the product by fully loosening clamping
screw 1.
NOTE: Clamping screw 1 is not secured against falling out!
4. Remove tool.
5. Mount new tool }Chap.4.2.
5Maintenance and storage
5.1Cleaning the clamping bore
Clean the clamping bore during every tool change with a
cleaning agent containing solvents and a cleaning brush.
5.2Checking the clamping force
Check the clamping force before initial use, after approx. 100
tool changes and at least every 3 months.
1. Unclamp the product by loosening the clamping screw.
NOTE: The clamping screw is not secured against falling
out!
2. Insert the test shaft to the minimum clamping depth.
3. Screw the clamping screw in by hand until it reaches the
stop. Observe the maximum specified tightening
torque }Chap.3.
4. The clamping force is no longer sufficient if the test shaft
can be pulled out of the product with little effort using two
fingers.
In this case, send the product to SCHUNK for inspection.
5.3Lubricating the clamping screw
CAUTION
Allergic reactions if lubricating grease comes into contact
with the skin.
•Wear protective gloves to lubricate the clamping screw.
It is necessary to adapt the cleaning and lubrication of the
clamping screw to the ambient conditions. Especially in the
case of high clamping frequencies, high operating
temperatures, and abrasive dirt or dust. For optimum
lubrication of the clamping screw, we recommend copper
paste MOLYKOTE CU 7439. (100 g tube, ID 9247204).
1. Unscrew the clamping screw from the product.
IMPORTANT!The actuating piston underneath is not
secured against falling out and must not be removed!
2. Clean the clamping screw and actuating thread and check
for damage to the thread flanks. Replace if necessary.
3. Lubricate the clamping screw and actuating thread.
4. Screw the clamping screw into the product.
5. Check the clamping force }Chap.5.2.
5.4Storage
– Lightly oil the entire surface of the product.
– Only store the product in an unclamped state and protected
against corrosion.
– Store the product in a suitable transport container.
– Protect the product from excessive temperature fluctuations.
NOTE: Before recommissioning, clean the product and check
for damage, functionality and tightness!
If you have any questions regarding maintenance and servicing,
our technical after-sales service is available during our business
hours:
Service telephone: +49-7133-103-2956
service.toolholder@de.schunk.com
6Disposal
– Follow local regulations on dispatching product components
for recycling or proper disposal.
– Alternatively, you can return the product to SCHUNK for
correct disposal.
Other SCHUNK Engine manuals
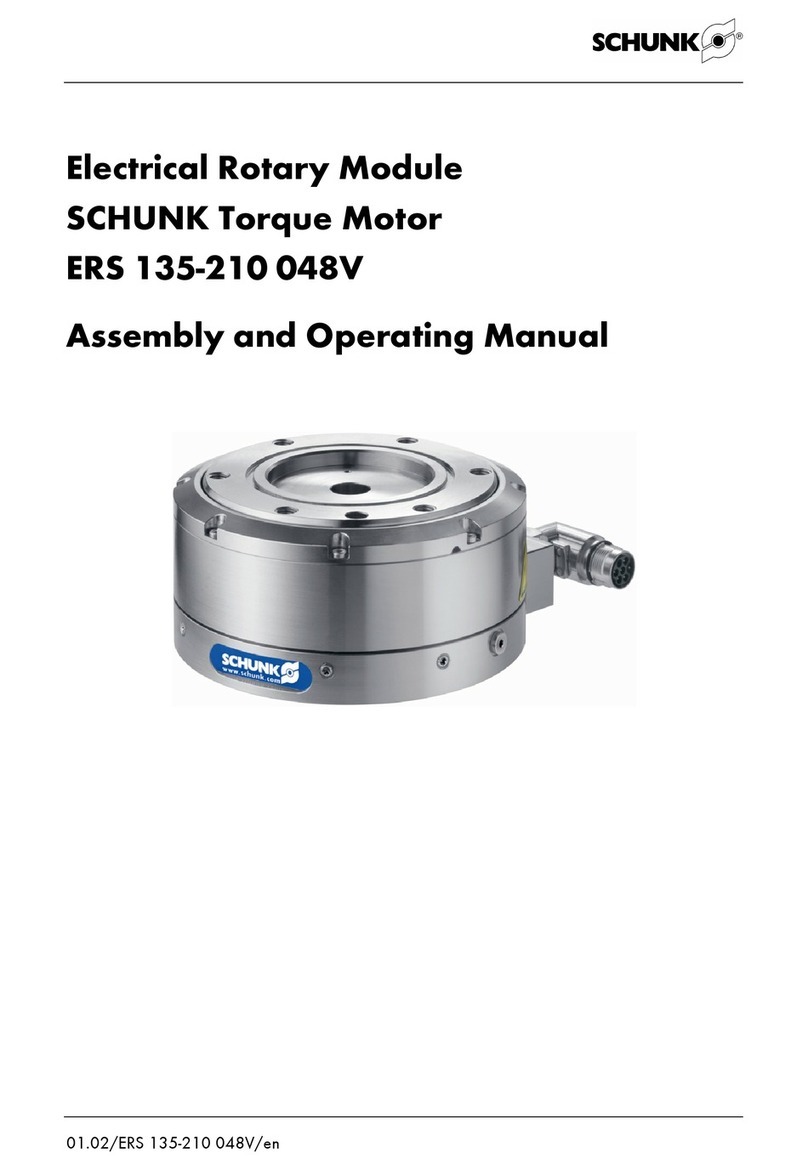
SCHUNK
SCHUNK ERS 135 048V User instructions
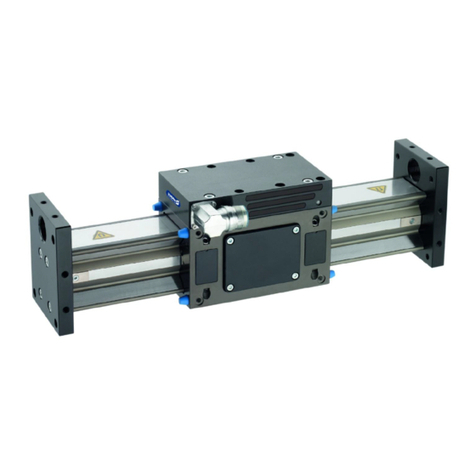
SCHUNK
SCHUNK LDN Series User instructions

SCHUNK
SCHUNK ERS170 User instructions
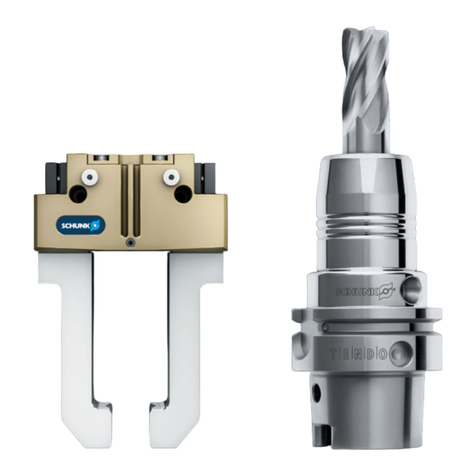
SCHUNK
SCHUNK LDM Series User instructions
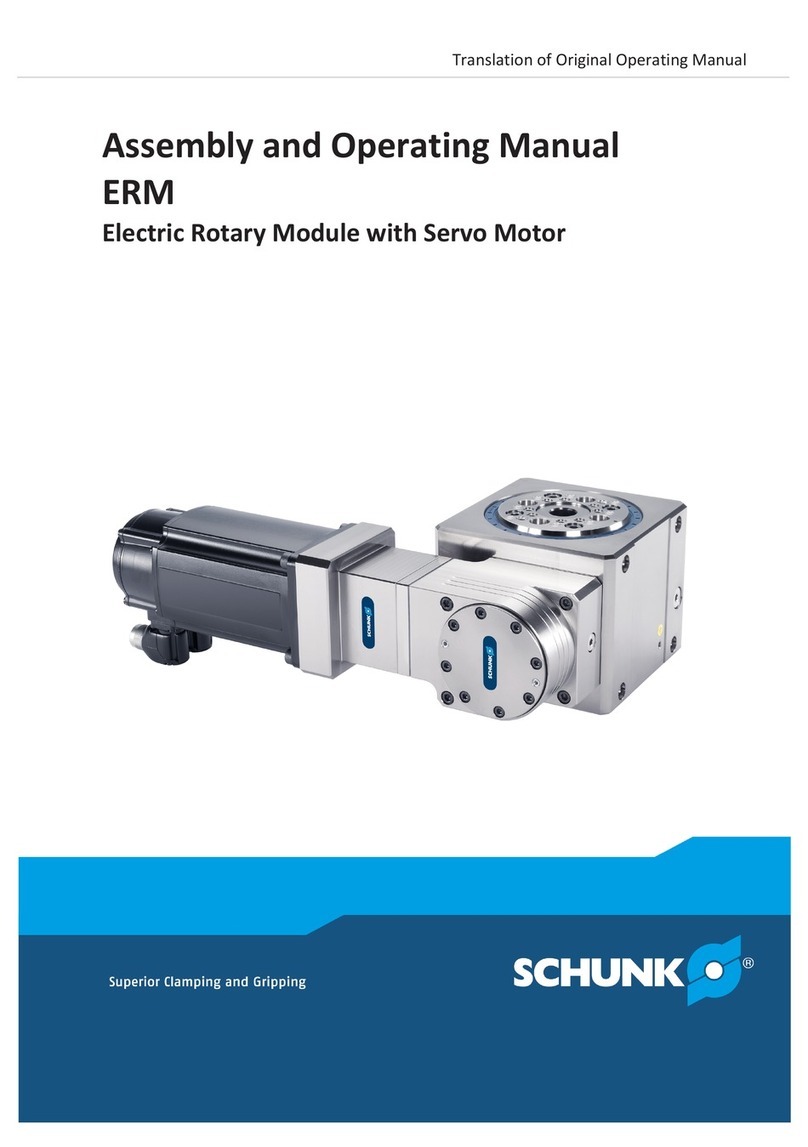
SCHUNK
SCHUNK ERM Series User instructions
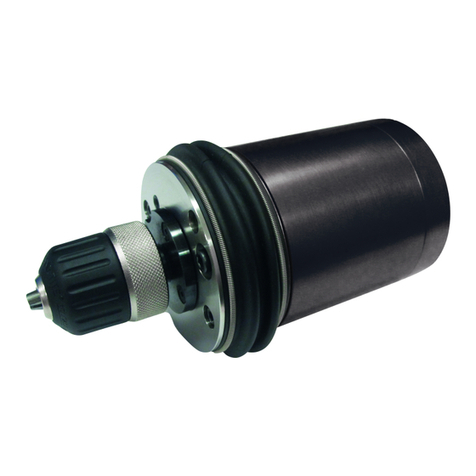
SCHUNK
SCHUNK MFT User instructions
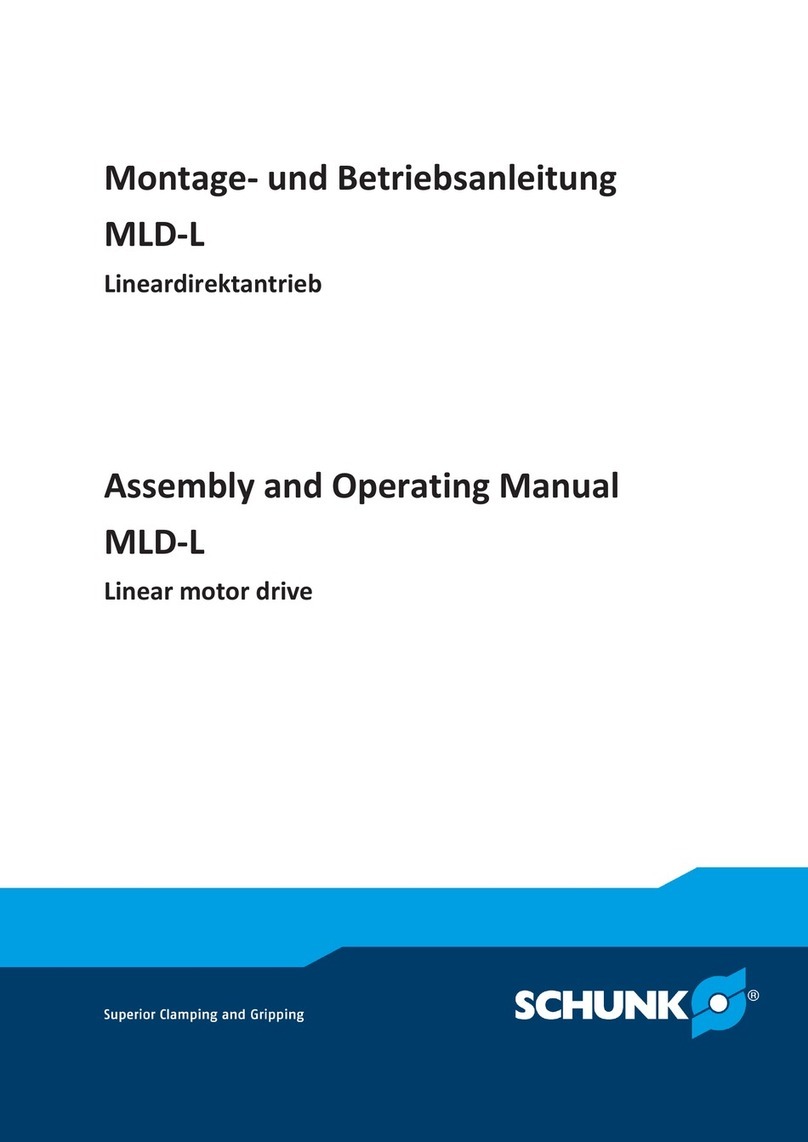
SCHUNK
SCHUNK MLD-L User instructions
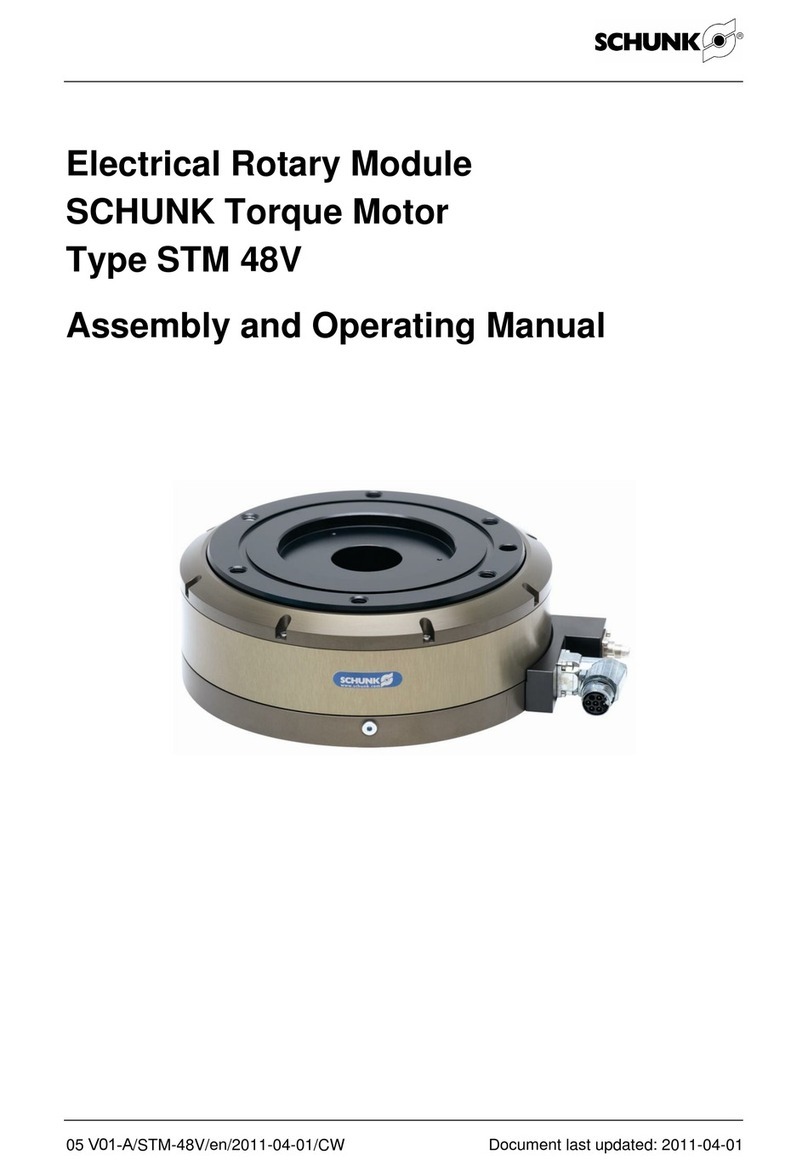
SCHUNK
SCHUNK STM 48V User instructions
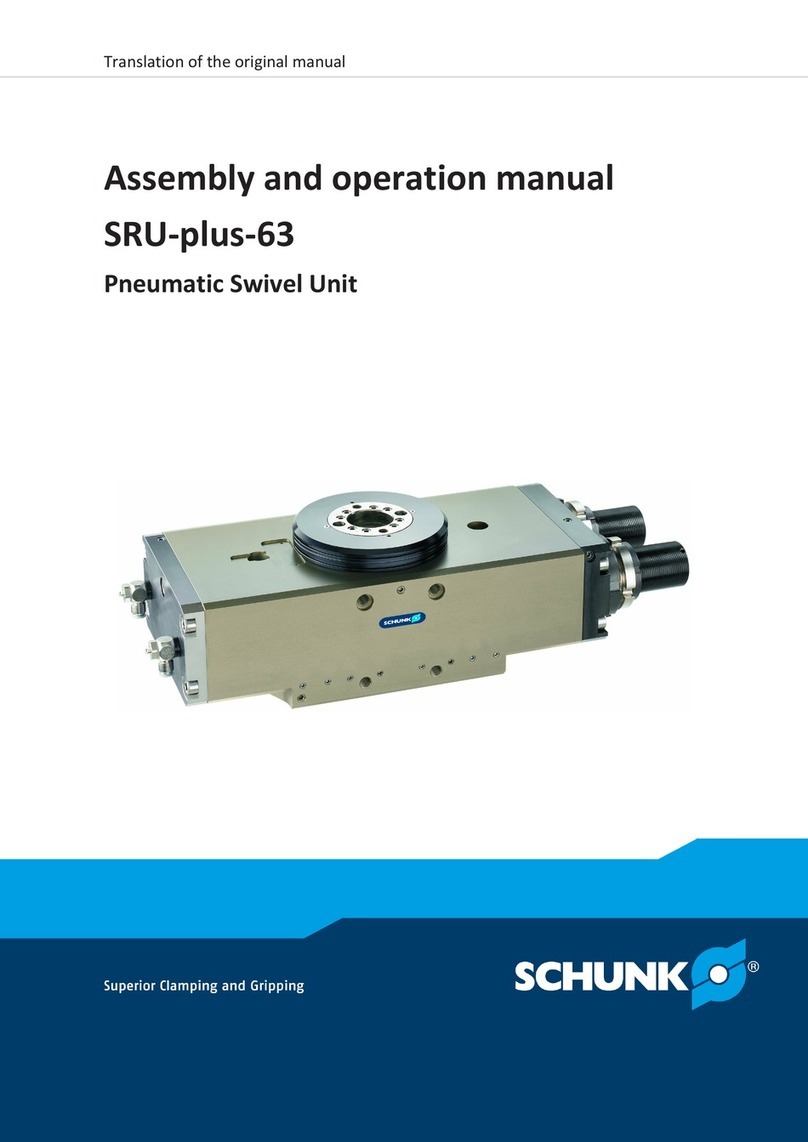
SCHUNK
SCHUNK SRU-plus-63 Installation and operating instructions
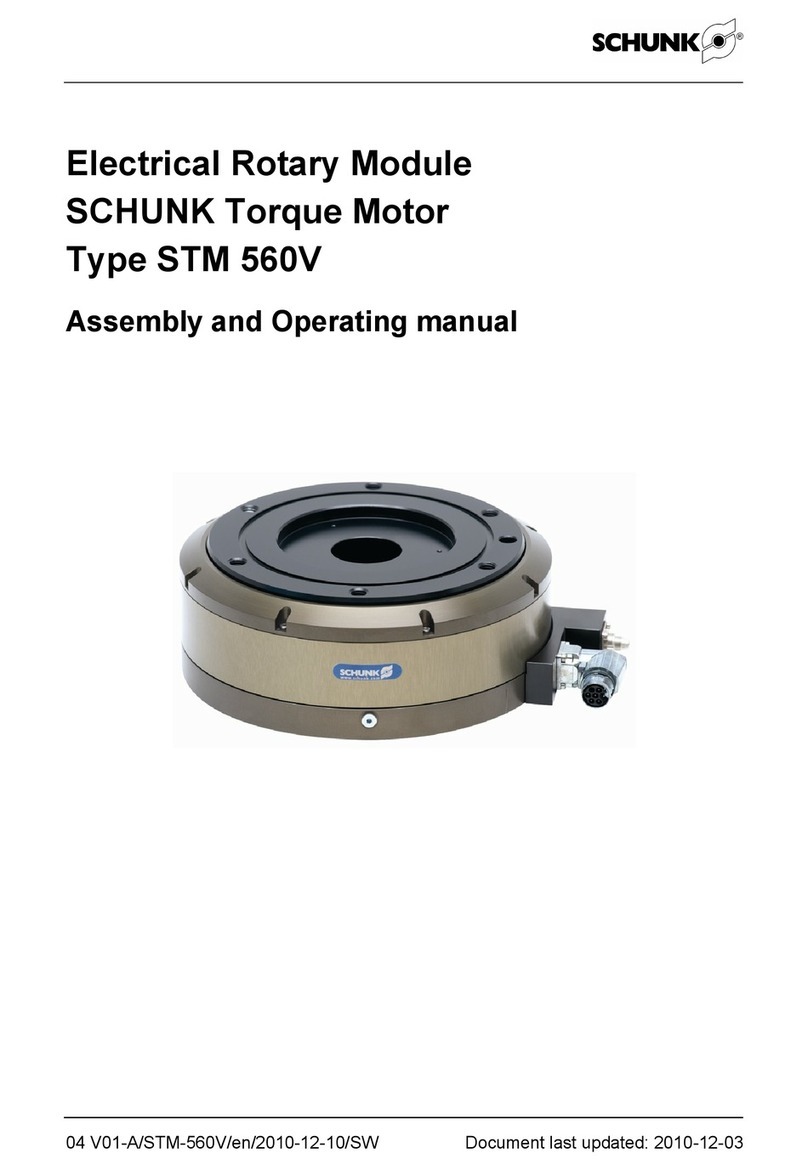
SCHUNK
SCHUNK STM 560V Series User instructions