Seg System A2 H15 Configuration guide

S44-H15E
INSTRUCTION
SYSTEM A2
BELTWEIGHER MODEL H15
General information
Mechanical installation
Electrical installation
Commissioning and operation
Technical information
D
B
A
C

18-08-16 S44-H15E 1-1
S-E-G SYSTEM A2-H15 INSTRUCTION
Table of contents
1. GENERAL 1-2
1.1 System description 1-2
1.2 Belt scale parts 1-2
1.3 Delivery & storage 1-3
2. MECHANICAL INSTALLATION 2-1
2.1 Mechanical installation 2-1
3. ELECTRICAL INSTALLATION 3-1
3.1 General 3-1
3.2 Terminal connections 3-1
3.2.1 Optional 90 - 230Vac/24Vdc module 3-2
3.3 Loadcell connection 3-3
3.4 Power up 3-5
3.5 Serial communication and printout 3-6
4. COMMISSIONING and start-up 4-1
4.1 General description 4-1
4.2 Checklist prior to start-up 4-2
4.3 START-UP procedure 4-3
5. DAILY OPERATION 5-1
5.1 Front Panel 5-1
5.2 Error indications 5-2
5.3 Printout 5-3
6. TECHNICAL INFORMATION 6-1
6.1 Menu system overview: 6-1
6.2 Parameter explanations 6-2
6.3 Controller Specifications 6-7
7. MAINTENANCE 7-1
7.1 Housing maintenance 7-1
8. CE Compliance and Harmonized Standards 8-1
8.1 WEEE Compliance 8-1
8.2 RoHS Compliance 8-1
8.3 CE Compliance 8-1
8.4 EC Declaration of Conformity 8-2
This instruction contains all necessary information to perform a successfull installation, connection and start-up
procedure of the instrumentation.
In order to fully understand the procedures and actions involved, we would like you to spend some time reading
this instruction carefully before installation and operation of this product.
If you should have any further questions, please contact your local S-E-G representative.
The contents of this manual is believed to be correct at the time of printing, the manufacturer reserves the right to
change the contents without notice if so required.
NOTE! This manual is valid for firmware version: June 29 2015. (Indicated in display at power up)

1. GENERAL
1.1 System description
The belt scale controller model H15 is equipped with all the basic belt scale controller functions such as: Flow
indication, Totalising, Status indications etc.
The H15 model designates all parameters basic default values during the start-up procedure.
This means that the controller will be ready to use immediately after a performed start-up procedure, without
putting in hours of endless programming and recording of parameter changes.
1.2 Belt scale parts
The belt scale's main components comprise devices for sensing the load of the material deposited on the belt,
measuring of belt travel, belt position sensor and the controller instrumentation.
Load measurement
This is performed with one or several weighing units installed in the conveyor.
The weighing unit built-in loadcell emits electrical signals proportional to the weight of material
per unit of belt length.
Weighing units are available for different capacities, belt widths and troughing angles.
The weighing unit supplied with each belt scale system is described in separate instructions.
Measuring of belt travel
This movement is measured with a single pulse sensor or a complete tachometer unit. The tachometer must be
brought to rotate at a rate which is proportional to the belt speed. The tachometer and its installation are
described in separate instructions. If an additional belt revolution sensor is connected, automatic belt
profiling compensation is possible. Influences of uneven belts and belt splices can then be almost completely
eliminated, resulting in a much higher totalising accuracy compared to standard belt scale controllers.
Instrumentation
The controller contains software program for processing of all measurement data from the weighing unit and the
tachometer. The controller is equipped with the following features/functions:
- Serial port RS485 with Modbus RTU, ASCII protocol for connection to a printer, PLC, PC etc..
- Built -in active 4-20mA output, galvanically isolated representing indicated flowrate.
- 2 output relays which can be designated different functions; totaliser pulse, flow level, etc.
The resulting processed data such as: Flowrate (t/h), Totalised amount of material, Beltspeed, etc.
Is accessed trough the built in LCD display unit, or remotely via serial communication.
Serial communication is useful for retrieving data intended for administrative purposes or process control. Data
can be transmitted/received in a number of different ways, such as: RS485 or via different optional fieldbus
converters like: Ethernet, TCP/IP, Profibus,etc.
18-08-16 S44-H15E 1-2
S-E-G SYSTEM A2-H15 INSTRUCTION

1.3 Delivery & storage
Measures have been taken to protect the System A2 during shipment by ensuring that all parts which may be
damaged are properly secured. Inspect the equipment on delivery and report any shortages or physical damage
to your SEG representative. If storage is necessary, it should be in a dry and heated building with temperature
between5-50
oC.
18-08-16 S44-H15E 1-3
S-E-G SYSTEM A2-H15 INSTRUCTION

2. MECHANICAL INSTALLATION
2.1 Mechanical installation
When choosing a location for installing the controller, care should be given to avoid an unsuitable environment
even though the enclosure front panel conforms to NEMA 4 (IEC Class IP 65) requirements.
For outdoor installations, protection from weather elements must be provided. The controller is available in water
proof enclosures for this purpose.
The installation place should be situated in a shady area that is never exposed to direct sunlight or rain.
If the mounting surface is damp or wet, spacers (approximately 12 mm thick) should be placed between the
mounting plate and the mounting surface. For dimensions, refer to figure 2.1.
18-08-16 S44-H15E 2-1
S-E-G SYSTEM A2-H15 INSTRUCTION
Panel mount, type -P
weight: 0,5kg
Field enclosure type -W
weight: 3,0kg
Field enclosure type -V
weight: 2,5kg
150
75
190
222
162
B
AC
D
170
4xØ6
258
85
190
222
270
B
AC
D
278
4xØ6
B
AC
D
159
105
29
6xØ3,5
45 45
72 72
136
81
21
CUTOUT:
Figure 2.1 Dimensions

3. ELECTRICAL INSTALLATION
3.1 General
The Controller meet requirements for Í-marking according to EN 55022 (1998) + A1 + A2 and EN 61000-4-3
(2006). In order to ensure maximum EMC-protection and CE-compatibility, it is required that the cable installation
instructions are strictly adhered to.
3.2 Terminal connections
The procedure which must be observed in connecting electrical cables to SEG's weighing systems is described
below.
The weighing system utilizes different cable types.
- Power cable for main voltage to the scale controler.
- Signal cable for connection of load cells.
- Control cables for output relays.
- Signal cable 0/4-20mA output to auxiliary equipment (PLC, PC, printer, remote indicator etc.).
- Signal cable for serial communication RS485 to auxiliary equipment (PLC, PC, Indicator etc.).
Signal cables must be laid with great care to ensure faultless operation of the weighing system. Signal cables may
not be laid near any kind of high power cable. Thus, they may not be laid in a common conduit or a common cable
trough. Signal cables parallel to power cables must be separated by at least 2 m when distance exceeds a few
metres. Shielded cables must be used for all installations, and care must be taken to ensure that the shield is
properly connected inside the cable glands, so that the shield gets proper contact with the controller enclosure.
Signal cable splicing should be avoided. Junction and connection boxes must not permit the entry of any
moisture. Cable clamps must be used for all cables.
18-08-16 S44-H15E 3-1
S-E-G SYSTEM A2-H15 INSTRUCTION
Fig.3.1, Terminal locations
Terminal no. Description
1,01,2,3,4,04 Load cell signal input 0-45mVdc, max 140mA/85 Ohms. Ref. to section 3.3 - 3.4.
5(-), 6(+) Speed/pulse sensor input; S-E-G type F, Relay dry contact or NPN proximity switch.
V+, V-, Ground Power supply 24Vdc (13-30Vdc). Optional 90-230Vac/24Vdc module (PW-24) available.
31, 32, 33 1 RS485 serial port. 31(Gnd), 32(TRx-), 33(TRx+) Ref. to section 3.5.
41,42 1 Digital input for belt position sensor. Contact closure or Proximity switch (NPN or PNP).
51(+),52(-) Analog output 4-20mA (Flowrate), max 350 Ohms.
21,22,23,24 2 Relay ouputs, closing contacts (NO) 24Vdc/1A.
21,22: Totaliser pulse. 23,24: Selectable; Belt running, Flow level, Speed level or Load level.

3.2.1 Optional 90 - 230Vac/24Vdc module
An optional power module (PW-24) for 90-230Vac input with 24Vdc output, is available that fits inside all wall
mounting enclosure versions.
With the module installed, connection to a 115/230Vac mains power line is possible.
The module is being shipped as a separate item, and installation and connection is shown below.
The power module is attached to the enclosed bracket with 2 pcs M3x4 screws. The electrical connection is
preferably done before installation of the unit into the enclosure, for easier access of the screw terminals.The 2
securing M3 lock nuts may be turned 1/2 a turn on the threded pins before attaching the unit, as the holes are cut
out as "keyholes" to simplify attachment.
18-08-16 S44-H15E 3-2
S-E-G SYSTEM A2-H15 INSTRUCTION

3.3 Loadcell connection
A standardized connection technique, using 6-conductor cables, is employed for load cells. Two of these
conductors are for feeding the cells, two for load signal and two for sensing the line resistance. Due to this
connection method, cable lengths up to 500 m are possible (provided the distance to parallel high power cables is
at least 2 m when cable lengths exceed a "few" metres.)
Compensation conductors begin at the load cell's fixed cable which has 4 conductors, 2 of which are branched
with jumpers. The fixed load cell cable has no compensation conductors of its own but is factory calibrated to
match the load cell and must not be shortened unless absolutely necessary.
Connection of load cell cables to the control console depend on the number of load cells plus the distance
between load cells and the control console. SEG's junction and connection box are used for splicing and
interconnection.
Belt scales generally incorporate a pulse generator for detecting belt speed. The signal from the generator is
transmitted by an extra pair of conductors in the same cable used for the load cell signal.
When connecting load cells of other brands than SEG, check that they are compatible with a 12Vdc
supply voltage, and that the max current load does not exceed 140mA (~85 Ohms).
NOTE: Screens for load cell cables are connected to ground only when connected directly to the
controller. In the case where connection boxes are used, special terminals in the connection boxes are
used for the cable shields.
Connection to the controller is made at the terminal board SPS202, Refer to fig. 3.1
Terminal connections:
Term. Function SEG Load cell cable
1: Feed + Yellow
01: Sense + -
2: Load signal + Red
3: Load signal - Green
04: Sense - -
4: Feed - Blue
¤Signal ground. Connect to separate signal ground only, if available.
For Intrinsically safe (Eex) installations: Connect protective ground from zenerbarriers.
Refer to drawing overleaf.
18-08-16 S44-H15E 3-3
S-E-G SYSTEM A2-H15 INSTRUCTION

18-08-16 S44-H15E 3-4
S-E-G SYSTEM A2-H15 INSTRUCTION

3.4 Power up
The control console is designed to operate from a power source that will not apply more than 13-30 Volts DC
between the supply terminals V+ and V- (Negative ground only).
A protective ground connection by way of the grounding terminal is essential for safe operation as well as a good
clean power supply.
Note! A load of 85 - 1000 Ohms between terminals 1-4 is required for the controller to power up, e.g. the load cell
must be connected for the controller to operate correctly.
The controller memory has a lithium back-up battery (CR2450) which must be engaged after power-up to
ensure correct memorisation. As soon as power has been applied to the controller, the battery may be engaged
by pulling the plastic tab on the rear side of the controller.
If the tab has accidentally been pulled before power-up, just connect the controller to 24vdc for power-up and then
disconnect again. This will allow the internal CPU to perform a controlled shutdown, minimizing battery drain.
Note that if the controller will be stored for a long period of time before taken into operation, it will be better not to
engage the battery. Parameter settings can be permanently stored to a flash memory anyway from inside the
menusystem, for future restore without the need for battery to be activated.
The battery will keep the memory with time and date activated for approx. 1 year without power supply.
Regarding battery exchange - contact your local S-E-G representative for information.
18-08-16 S44-H15E 3-5
S-E-G SYSTEM A2-H15 INSTRUCTION
Refer to fig. below:

3.5 Serial communication and printout
System A2 has 1 RS-485 interface. It may also be connected to a RS-232 listener, such as a printer.
3.5.1 Printout:
For printout a printer with minimum 40 character width may be used.
Although the interface is RS485, it may be connected to most printer RS232 interfaces as transmitter only, without
any control signals. Comm. settings under “COM SETUP” menu must be set to “Prn. xyz” format for connection to
RS232 printer interfaces. Consult the printer manual for information regarding data format etc.
Refer to drawing for connection.
3.5.2 Serial communication:
The RS-485 interface follows the TIA/EIA-485 Two-Wire standard. This allows the use of long terminated cables.
RS-485 is designed for a multiple transmitter / multiple receiver system, but can also handle a single transmitter /
single receiver long distance application. The RS-485 can extend communications up to 1000 meters at up to 38
kBaud transmission rate. For shorter distances it handles up to 32 units at baud rates up to 38 kBaud, without any
additional interface.
For data communication System A2 uses MODBUS serial line slave protocol. MODBUS RTU and MODBUS
ASCII transmission modes are supported. Refer to the serial communications specification for system A2
(S44-CSE), wich can be downloaded at www.s-e-g.com/documents for further information.
18-08-16 S44-H15E 3-6
S-E-G SYSTEM A2-H15 INSTRUCTION
237TxEN G Rx+ Rx- Tx+ Tx-
TRx -
TRx +
31
32
33
Gnd
Interface RS232/RS485
System A2 RS485
TRx -
TRx +
31
32
33
Gnd
System A2 RS485
TRx -
TRx +
31
32
33
Gnd
System A2 RS485
2
7
3
4
5
6
204
6
8
7
2
3
5
PC
V28/RS232C
with control
signals
DB 9
DB 25
TRx -
TRx +
31
32
33
Gnd
System A2
2
7
32
3
5
Printer
RS232C
No control
signals
DB 9
DB 25
The serial port interfaces must be terminated
at each end of the loop.
Check jumper JP1 (Closed = terminated) on
terminalboardSPS202onsystemA2.
JP1
Gnd
Rx

4. COMMISSIONING and start-up
4.1 General description
SYSTEM A2 has a startup procedure to enter all the necessary parameters for basic operation by entering a few
parameter datas about the installation.
Before the startup procedure, the controller must be properly installed, with the correct load cell, correct electrical
and mechanical installation. The scale must be empty, since the empty scale value is recorded during setup.
Start up is entered from the menusystem by pushing frontkey D, and scrolling down to menu
“NEW STARTUP ->”. When the controller is powered up for the first time, it will automatically enter the set up
procedure, if no previous installation parameters are available.
The startup procedure will step through and prompt you for all the necessary data and perform an initial zero and
span adjustment. Enter/Change of parameters is described below:
If a change to a previously entered parameter is required, it may be accessed by stepping back through the
parameters, using the D(Up) key.
When a value is changed, keeping the key pressed will change the value with increasing speed. To reduce the
speed, release the key temporarily. Faster speed is achieved by pressing key A(Esc) simultaneously with D(Up)
or C(Down) key.
18-08-16 S44-H15E 4-1
S-E-G SYSTEM A2-H15 INSTRUCTION
> Flow 325tþ>
INFORMATION ->
BAC
D
Front panel, menu mode:
C Down
- Scroll trough menus
- Changing values
DUp
- Enter menusystem
- Scroll trough menus
- Changing values
A Esc / Undo
- Undo value changes
- Exit to previous menu
- Faster changing with key Cand D
B Enter
- Enter into editing mode.
- Accept values or selections.

4.2 Checklist prior to start-up
þ1. Verify that the weighing unit/units are correctly installed. See the instructions for the weighing unit.
þ2. Verify that the correct wiring and cable connections have been made. Refer to section 3 in this
manual.
þ3. Verify that the belt revolution sensor is installed. The belt must have a sensor that senses a fixed
position of the belt once/belt revolution. If no sensor is installed, functions will be the same as for
model H14.
þ4. Verify that the tachometer is installed correctly. Refer to the manual for the tachometer and weighing
unit. If the tachometer is installed with drive type CF,(where the tacho is driven by a heavy wheel,resting
against the belt) you can skip to check no.5 below.
þ4.1 If the tachometer is being driven in any other way, measure the total belt length in cm and move
to step no.5
þ5. The parameter values below will be necessary for the start-up procedure. Make notes of the following
values, so that you have them at hand when performing the start-up procedure.
!Type of load cell installed in the weighing unit; Rated load in kg and output in mV/V.
!Idler distance at the weighing area. To be measured precisely to +/- 1mm. Refer to the instruction
manual for the weighing unit for detailed information.
!Belt length, (only necessary if drive unit CF is not installed).
18-08-16 S44-H15E 4-2
S-E-G SYSTEM A2-H15 INSTRUCTION

4.3 START-UP procedure
Description of start up
If the controller, at power up cannot find any saved previous data, it will automatically go into the start-up mode.
During start-up, a number of selections and values must be entered by means of the front keys.
Below you will find the different steps in the start-up mode together with the selections available.
After completing the start-up procedure, it is recommended that you make a backup from inside the
“SYSTEM DATA” menu to the internal flash memory, saving all your selections and values of the current
set-up.
Although the internal memory has a battery back-up, the saved data can be useful at for example a future
back-up battery exchange.
Display indication:
“Restore No” When first entering the start-up menu, the systems prompts for any previously
backup to the internal memory. At an initial start-up, no saved data is yet
available. If a backup is available, “Yes” can be selected and the system will load any
previously saved settings and return directly to operation mode.
NOTE! Loading older saved settings will overwrite all current settings, including
totalisers, clock, date etc.
To begin a start-up procedure, scroll down to the next step with frontkey C.
“Ld.Cell= 100kg” Enter the rated load of the installed load cell(s) in kg.
The information is normally found on the descriptive label of the load cell.
Note! For S-E-G weighing units, only the rated load of 1 load cell must be entered,
even if several units are installed in a row in the conveyor.
For weighbridges or weighing units with for example 2 load cells on the same idler
(S-E-G type EK-), the sum of the rated load for the installed load cells must be
entered.
“At mV/V= 1.0” Enter the output signal of the installed load cell(s) in mV/V.
The information is normally found on the descriptive label of the load cell.
Note: S-E-G Load Cells are always 1mV/V.
“TotUnit= 1t” Enter the desired resolution of the totalisers in tonnes.
Warning! Selecting a too high resolution may cause the mechanical output relay to lag
behind the internal totalisers.
Max output rate for the relay is 5 pulses/s or 200ms (pulse length = 100ms)
“Idl.Spc=1000.0mm” The distance between the weigh idler and the closest retreat or approach idler.
Enter the value in mm. The idler distance before and after the weighing unit should
preferably be equal in distance.
However, to give the best accuracy, the distance to measure is between the idlers at
both sides of the weighing unit (i.e. two idler lengths) and then divide by two.
Refer to the instructions for the belt weighing unit for further info.
For weigh feeders with weighing plates, refer to theire manuals respectively.
18-08-16 S44-H15E 4-3
S-E-G SYSTEM A2-H15 INSTRUCTION

“PulsLen=20.000mm” Pulse length in mm for each received tacho pulse.
Default value is 20.0mm which corresponds to an S-E-G tacho type F-25 with a 25
hole pulse disc installed with drive unit CF. The circumference of the CF measuring
wheel is 500mm divided with 25 pulses/tacho revolution.
If the tachometer is driven in any other way and the pulse length is not known, this
value may be set to zero (0) and instead the beltlength entered at the next step.
“BeltLen=” Conveyor beltlength in metres.
This will automatically be calculated during the next step, if a value for pulse length
have been entered for “PulsLen=” above..
If pulse length above is set to zero (0), the beltlength corresponding to 1 belt
revolution has to be entered here at this point, before proceeding to the next step.
“Run Belt” Automatic counting of the corresponding number of tacho pulses for one belt
revolution, system tare out, limits for zero setting and recording of belt profile will be
calculated at this point.
When started, the automatic sequence will be as described below:
When belt sensor position is sensed the first time, tare sequence is restarted.
The next time belt position is sensed, belt length and average standard tare is saved
and belt profile recording started. When 3:rd belt position is sensed, belt profile is
saved and auto zero is enabled.”
NOTE 1 If a previous start-up already has been carried out, new limit values for zero
setting of belt will not be calculated. If new values are desired, the parameter values
for “CutOff” and “AutNMax” must be zeroset before “Run belt” is performed.
New values will also be calculated when desired if zeroset before initiating a
“SysZero” from inside the menusystem.
NOTE 2 If a belt revolution sensor has not been installed, step 1-7 on the next page
must be carried out instead.
“Save” Saves all entered values and selections and exits to operation mode.
Auto zero is being started, and after successsfully finished, the belt profile
compensation is being activated. If the belt position sensor signal is lost for 4 belt
revolutions in a row, belt profile compensation will be deactivated (”Signal Error”) and
the previously recorded average tare will be used in the same manner as for a
standard beltscale (Equal to model H14). If the belt position sensor later is regained,
the belt profile compensation can be activated again if a “SysZero” is enabled from
the menu system.
The controller is now set up, but a few important issues remain to handle and consider before finally taking the
beltscale into operation:
1. In order to take full advantage of the belt profile compensation, the calculated limit value for parameter “CutOff”
needs to be reduced. It is recommended to reduce the limit to at least 50% of the current value. In most cases the
limit can be reduced further, improving accuracy even more.
2. Remember to engage the backup battery. Refer to section 3.4. If not, all preset parameters will be lost
when power is being disconnected.
3. It is highly recommended to make an additional memory backup of all settings by enabling this function under
the “SYSTEM DATA” menu. A snapshot of all settings will be stored in the permanent memory for future retrieval
in case of a backup battery failure.
4. If the coneyor is inclined, put in the angle of inclination for parameter “Angle=”under the “SYSTEM DATA”
menu for compensation of weight sensing errors caused by inclination.
NOTE! If an optional “inclination compensator” is connected to the controller, this value will be adjusted for
automatically.
5. If it is possible after the set up to perform an actual weight verification, you will achieve greater accuracy,
correcting for mechanical errors. Refer to section 6.2 “SPAN ADJUST”
18-08-16 S44-H15E 4-4
S-E-G SYSTEM A2-H15 INSTRUCTION

The following procedure 1-7 is only necessary if no belt revolution sensor is
detected / installed. (Procedure will then be the same as for model A2-H14.)
The steps below must then be carried out under “Run Belt”.
1. Make a clearly visible mark on the belt, or use a belt joint as a reference mark.
2. Set the switch inside the connection box(-G) to the TEST position.
(tacho pulses stopped). If there is no switch, connect a jumper wire between
terminal 5 and 6 and arrange it so that it can be quickly and easily disconnected when
counting is terminated.
3. Activate counting by selecting “Yes”. “Pulses 0” will be indicated in the display
window.
4. Start the conveyor.
5. When the reference mark passes a pre-determined point, Set the switch to
the“RUN” position. After one revolution of the belt, i.e. when the reference point
passes the fixed point, return the switch to “TEST”.
6. Press the frontkey “B” (the number of pulses will now be saved).
7. Set the connection box switch back to the “RUN” position, otherwise the
tachometer will not work. If it is possible to see the mark on the belt from where the
controller is located, the tachometer pulses may be stopped or started using the
frontkey “B” only. (this eliminates the use of the switch inside the conn.box -G).
If a tachometer type “SEG CF” is being used, i.e. driven by the return part of the belt,
the corresponding belt length is now automatically displayed under “BeltLen=”.
If you are driving the tacho by other means, or using a contactor input, then you must
accurately measure the belt length and enter the value under “BeltLen=”.
NOTE 1 If a previous start-up already has been carried out, new limit values for zero
setting of belt will not be calculated. If new values are desired, the parameter values
for “CutOff” and “AutNMax” must be zeroset before “Run belt” is performed.
New values will also be calculated when desired if zeroset before initiating a “system
zero” from inside the menusystem.
NOTE 2 If “PulsLen” and “BeltLen” is already known, for example from a previous
start-up, counting pulses for 1 belt revolution is not necessary.
Just select “Yes” (Belt must be stopped at this time) and push enter to confirm.
If start-up is done without belt position sensor and later detected during “SysZero”, it will be used and belt length
readjusted automatically.
18-08-16 S44-H15E 4-5
S-E-G SYSTEM A2-H15 INSTRUCTION

5. DAILY OPERATION
5.1 Front Panel
5.1.1 Front keys, operation mode
18-08-16 S44-H15E 5-1
S-E-G SYSTEM A2-H15 INSTRUCTION
> Flow 325tþ>
Zero Print
-
D
B
AC
D Enter to menusystem
> Flow 325tþ>
Zero Print
-
Zeroset of upper row indications:
- Tare out of belt when running
empty.
A Zeroset depending on
indication
> 35.2 t>Sub1Tot
Zero Print
-
- Zeroset of Subtotal #1 or #2 depending
on which is being indicated.
Subtotal #2 may be password protected.
> Flow 325tþ>
Sub1Tot 35.2 t
Zeroset of lower row indications:
- Zeroset of Subtotal #1 or #2 depending
on which is being indicated.
Subtotal #2 may be password protected.
Flow 325tþ
>>Sub1Tot 35.2 t
- Tare out of belt when running
empty.
C Toggles indication in lower
display row between:
Total, Sub1Tot, Sub2Tot, Flow
and “Zero I Print”
(except for the selection used in
the upper row.)
B Printout
Refer to section 5.3
Zerosetting of Subtotalisers, example:
1. Push frontkey A at indication described to the left
2. Push B (Enter) and select “Yes” with key C or D.
3. Push B to confirm zerosetting.

5.1.2 Display indications, operation mode:
5.2 Error indications
The following error messages may appear on the LCD-display lower row.
To clear the error message if the fault does no longer exist: Push frontkey “C” (Toggle display indication)
> > SIGNAL ERROR< < a) The input load cell signal is negative (-).
Check load cell, wire connections etc.
b) Belt position sensor signal missing for 4 belt revolutions.
Check sensor condition, replace if necessary and enable a new “SysZero”
from the menu system..
> > OVERLOAD < < The input load cell signal exceeds 3mV/V.
Check load cell, wire connections etc.
>CHANGE BATTERY< Exchange backup battery.
Contact your local S-E-G representative for further information.
This message is only indicated once for each power-up, and may be cleared
according to the description above.
18-08-16 S44-H15E 5-2
S-E-G SYSTEM A2-H15 INSTRUCTION
Symbol Description
ÑBelt stopped, not totalising.
ƒBelt running, load on belt / flowrate indication, totalising.
¥Belt running empty, totalising, wait time before empty indication / start of auto tare if selected.
ŸBelt running empty, not totalising.
…Belt running empty, not totalising, auto tare out in progress.
¤Belt running empty, not totalising, auto tare out successfully finished.
‰System tare out with belt profile recording in progress.
> Flow 325tþ>
Total 35.2 t
Activity
Symbol
Lower row indication.
Toggles between: Total, Sub1Tot,
Sub2Tot, Flow and “Zero I Print”
Upper row indication.
Selectable between: Total,
Sub1Tot, Sub2Tot and Flowrate

5.3 Printout
Printout may be initiated by pushing key “B” on the front panel. Correct communication settings must be made
under the “COM SETUP” before connection to printer.
Refer to section 3.5.1
The printed information depends on what selections have been made for display indication.
Refer to the explanations below:
18-08-16 S44-H15E 5-3
S-E-G SYSTEM A2-H15 INSTRUCTION
> Flow 325tþ>
Zero Print
-
D
B
AC
If “Zero I Print” indication is toggled in the lower display, key Bwill initiate printout of the selected indication
on the upper row with time and date.
In the example above, “07.02.21 11:18 Flow 325th”will be printed.
Subsequently, the following will be printed if corresponding indications is selected in the upper row:
“07.02.21 11:19 Sub-1 Total 35.2 t”
“07.02.21 11:20 Sub-2 Total 18.3 t”
“07.02.21 11:21 Master Total 227.7 t”
Remote printout via terminals 41,42 will print Subtotal2 only, with automatic zeroset for each printout.
NOTE! Printout will only be executed once. No new printout can be executed until the totaliser value has been
incremented with 1 digit (Not indicating zero).
If any other indication than “Zero I Print” is indicated in the lower display row, that indicated information will
be printed. Refer to example below:
> Flow 325tþ>
Sub1Tot 35.2 t
The indication to the left will print:
“07.02.21 11:19 Sub-1 Total 35.2 t”

6. TECHNICAL INFORMATION
6.1 Menu system overview:
Push frontkey D for access to the menusystem. Scroll to the desired menu with frontkeys C or D.
Push key B (Ent) to access desired sub menus or parameters.
The SYSTEM DATA and NEW STARTUP menu can be protected with a numerical password. If entered, the
password will be asked for when the menu is being accessed. Note that the password will only be asked for once
for every session inside the menusystem. When the menusystem is exited and reentered, the password will be
asked for again. Entering a password code, will also protect zerosetting of Subtotaliser 2 from the front panel.
A2-H15 menusystem:
18-08-16 S44-H15E 6-1
S-E-G SYSTEM A2-H15 INSTRUCTION
NEW STARTUP ->
Restore
Ld.Cell=
At mV/V=
TotUnit=
Tacho?=
Idl.Spc=
PulsLen=
BeltLen=
Run Blt
Save
INFORMATION ->
Speed
Load
mV/V
mA Out
Tare
TotPart
Sub1Part
Sub2Part
Serial#
System
Prog.date
SYSTEM DATA ->
Angle=
TopDisp=
BkLight=
LoadLev=
FlowLev=
Spd.Lev=
FlowFlt=
mA Max=
AutZERO=
CutOff=
AutZMax=
SysZERO
TotZERO
SPAN ADJUST ->
Cur.Adj=
Val Now=
New Val=
Change
TIME SETUP ->
Year=
Month=
Day=
Hour=
Minute=
TimeSet
COM SETUP ->
BPS=
Format=
ID=
AutoPrn=
PW-Code=
Reg=
Reg.Val=
Backup
Table of contents
Other Seg Controllers manuals
Popular Controllers manuals by other brands
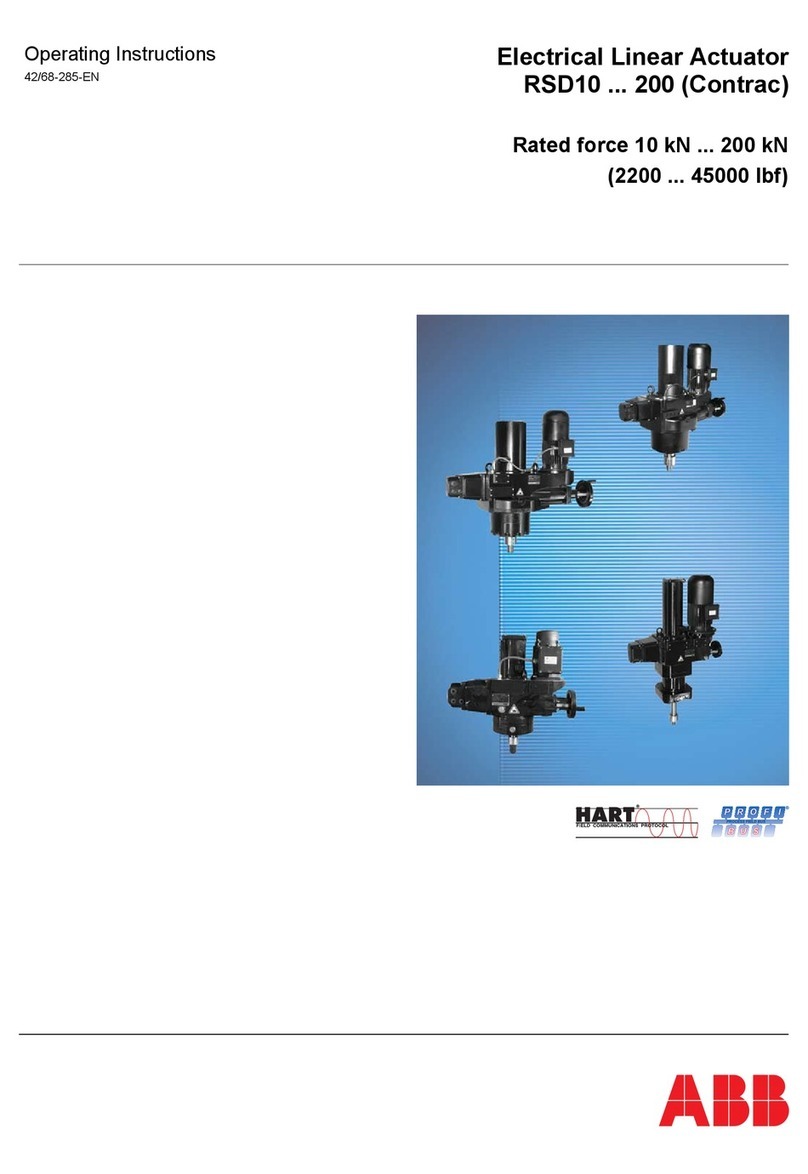
ABB
ABB RSD Series operating instructions

Autonics
Autonics TR1D Series Communications manual
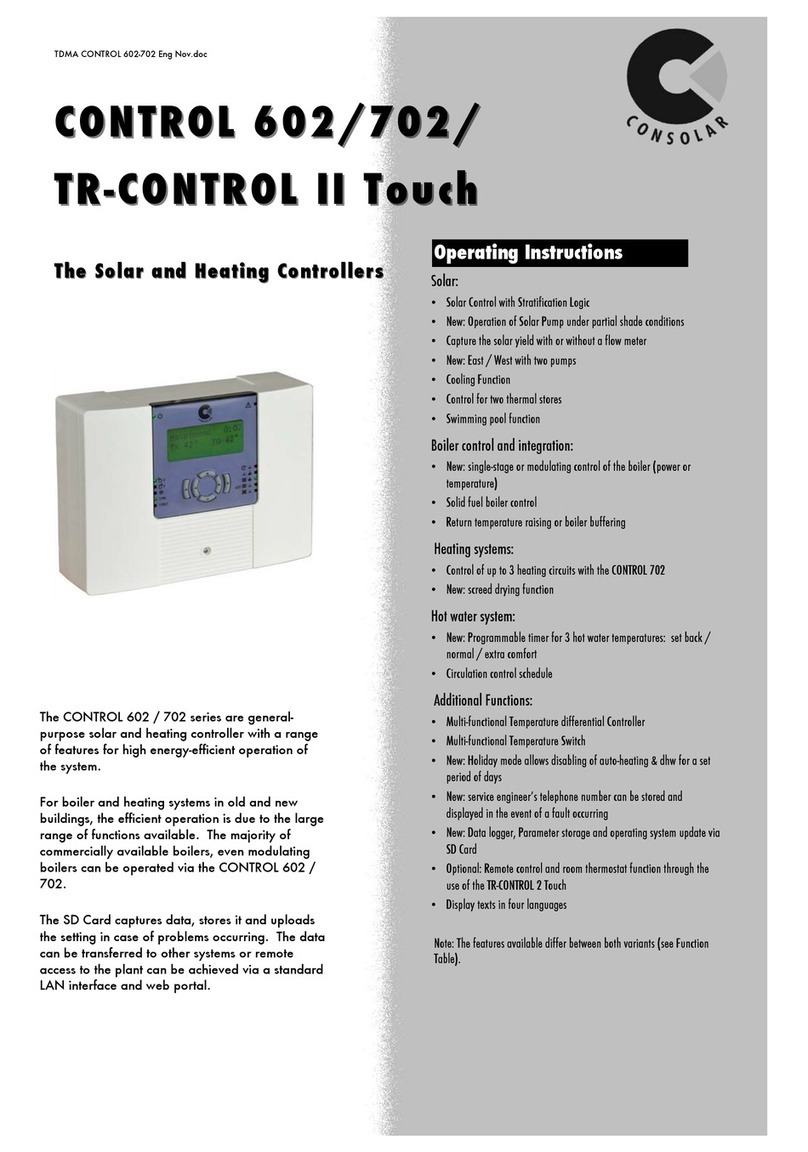
Consolar
Consolar CONTROL 602 operating instructions
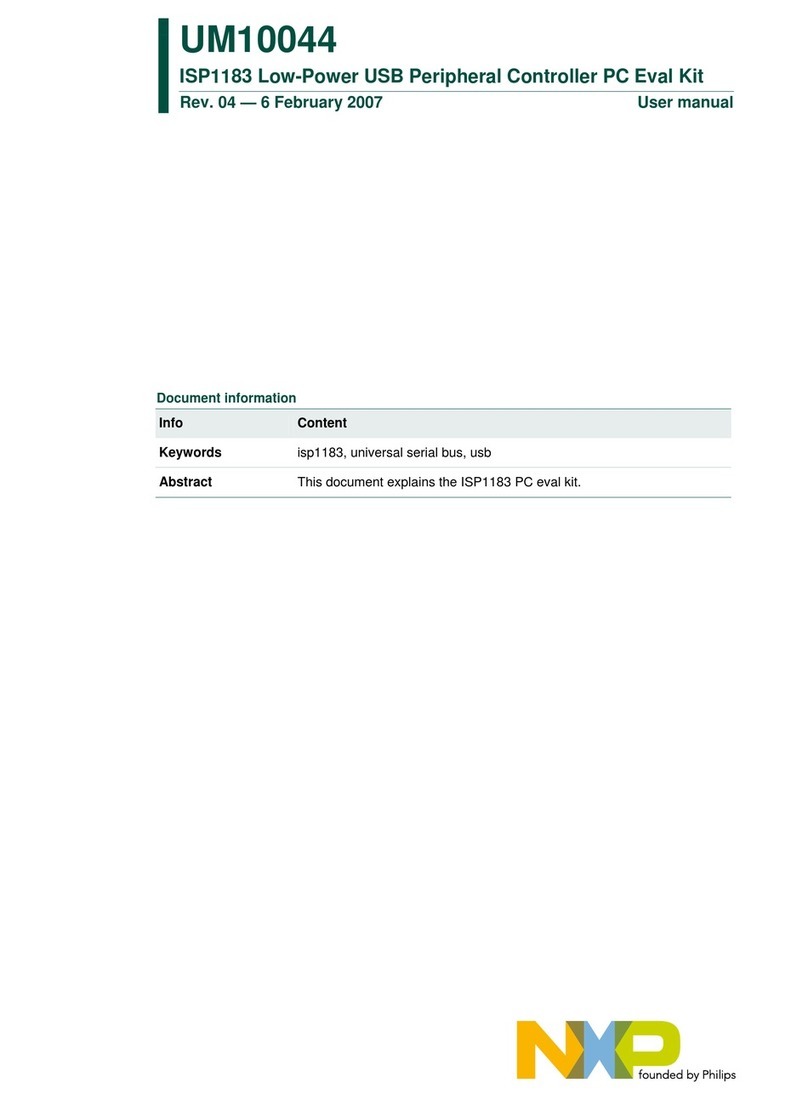
NXP Semiconductors
NXP Semiconductors ISP1183 user manual
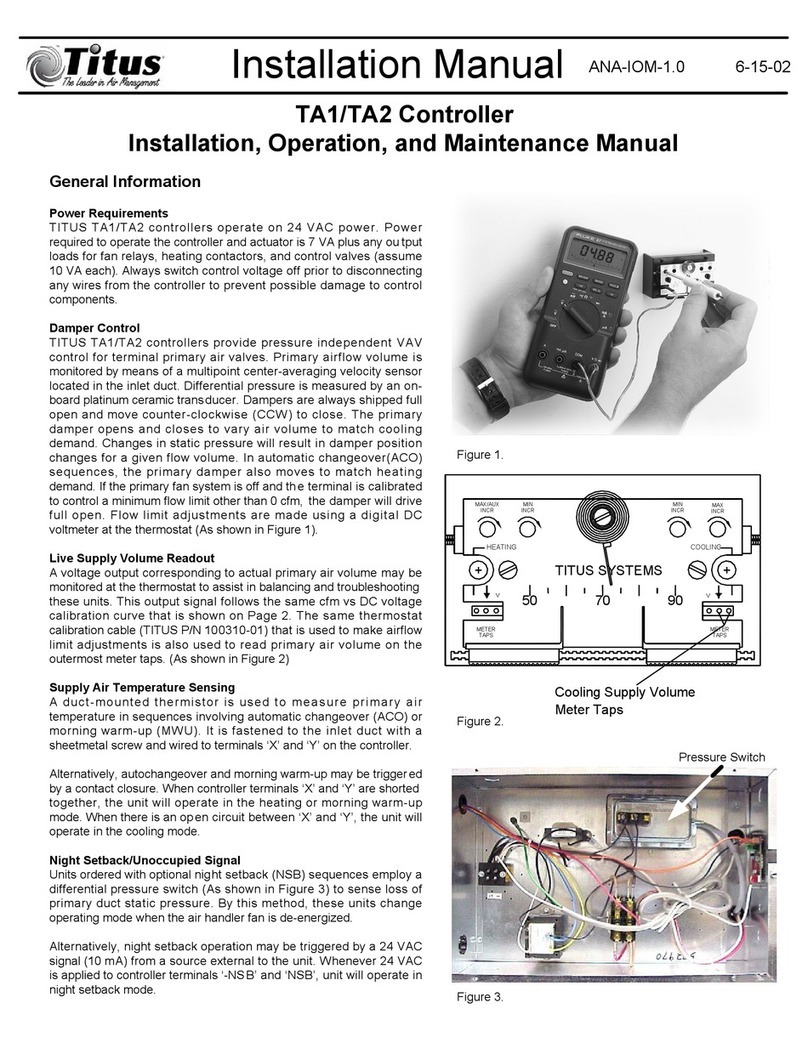
Titus
Titus TA1 Installation, operation and maintenance manual
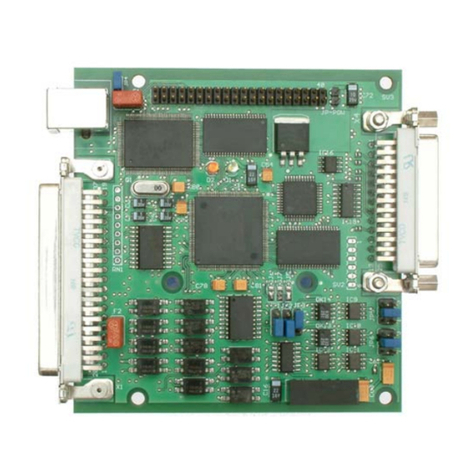
Nutfield Technology
Nutfield Technology USC-1 user manual