Seg CA01H User manual

CONTROL ACTUATOR CA01H~CA120H
Ver. 1.0
SHIN HWA Eng.Co.,Ltd.
CONTROL ACTUATOR
INTRUCTION MANUAL
CA-01H ~ CA120H
Shin Hwa Eng Co., Ltd

Ver. 1.0
SHIN HWA Eng.Co.,Ltd.
CONTROL ACTUATOR
CA01H~CA120H
Contents
1
Product description ............................................................................................... 3
1-1
Overview .................................................................................................................... 3
1-
General matters ......................................................................................................... 3
1-3
Characteristics ........................................................................................................... 3
1-4
Standard specification ................................................................................................ 4
1-5
Terminology of CA ...................................................................................................... 4
Installation ............................................................................................................. 5
-1
Structure .................................................................................................................... 5
-
Transport and Installation ........................................................................................... 5
Transport . .................................................................................................................. 5
Place for Installation ................................................................................................... 5
Installation .................................................................................................................. 5
Caution for Installation of Control Actuator ................................................................. 6
How to install control actuator .................................................................................... 6
Matters to check before operation .............................................................................. 6
-3
Limit switch adjustment (CA01H~CA10H FB, AB option type) .................................... 6
Position limit switch adjustment method ..................................................................... 6
Torque limit switch ...................................................................................................... 7
-4
Limit switch adjustment (In RB, SB option) ................................................................. 8
Position limit switch adjustment method ..................................................................... 8
Torque Limit Switch .................................................................................................... 9
-5
Adjustment of Resistance (Potentiometer:Jp-30)...................................................... 10
-6
Adjustment of Current Transmitter .......................................................................... 10
-7
Adjustment of balancing relay (SBR-10) ................................................................... 1
-8
How To adjust STP-07 (Indicator) ............................................................................. 14
3
Maintenance ........................................................................................................ 15
3-1
Troubleshooting ....................................................................................................... 15
4
Basic Circuit Diagram (Standard) ........................................................................ 16

3
Ver. 1.0
SHIN HWA Eng.Co.,Ltd.
CONTROL ACTUATOR
CA01H~CA120H
1 Product description
1-1 Overview
The Control Actuator is made by combining all components such as a decelerator, motor,
limit switch, overload torque switch, current transmitter, manual handle instrument, and
remote control box. It is standardized for precise operation.
This product simply opens and closes by remote control a damper or a valve with bad
conditions such as a high position, a high temperature, and much dust. Thus, it is the most
ideal for the latest factory facilities which are advanced and complex.
The Control Actuator is operated by an electric signal communication, and can perform a
servo control with a computer or a controller. It is an effective equipment to save energy and
reduce costs in automatic control of temperature, pressure, and flux.
It is an electric controller, whose maintenance and control are easy. It has a high reliability
and has been broadly used in industries such as iron manufacture, cement, chemical
factories, and fans and boilers for power plants for a long time.
1-2 Genera matters
The Control Actuator is to open and close a damper, valve, or the like by In addition, it can
make a proportional operation in accordance with a received signal if combined with a
potentiometer.
Thanks to its special gear structure, it is small and easy to install.
Every type of this product has a torque switch, and uses a continuous rating motor.
It has a dustproof, drip proof structure.
1-3 Characteristics
The Control Actuator uses the principle of epicycle for the gear structure, and it can perform
the normal operation and the reverse operation of the manual handle even when it is
operating with the motor with power supply.
Even while it is being electrically driven, you can randomly operate the manual handle with
no mechanical burden.
As well, it is designed to be self-locking by using the number of teeth of the worm and the
wheel, and has a structure where manual operation can be easily done immediately when
an emergency occurs.
The internal structure has the machine unit and the electric unit separated from each other.
They are completely airtight to give no impact on the electric unit.
The type with the Local Control Box attached has an automatic-manual converting control
box attached as one body.
It can easily convert to automatic and manual.
Since a torque switch, which is a mechanical overload protection device, is mounted, when
a load greater than the rated output is applied, the power supply is blocked to prevent
the product from being damaged.

4
Ver. 1.0
SHIN HWA Eng.Co.,Ltd.
CONTROL ACTUATOR
CA01H~CA120H
1-4 Standard specification
1-5 Termino ogy of CA
C A -
0 1
H □ □
Model name : Control Actuator
Category of output torque
ex: 01 = 15kgf-m , 10 : 100kgf-m
Manual handle : Every type of the CA series
has a manual handle attached
Control method
S : On-Off Control
R : Feed Back Signal 0~1kΩ
F : Feed Back Signal 4~20mA DC
A : Auto Type (Balancing Relay)
(Command Signal 4~20mA)
(Feedback Signal 4~20mA)
With local box attached : B
Structure
: Full-shut, outdoor
type
Humidity : 85% or lower
Operating angle : 90˚ Standard
painting color
: Munsell 7.5BG 6/1.5
Ambient temperature
: -20˚C~60˚C
Input signal
: Contact point signal
: Current signal (4~20mA
DC)
Operating speed : 60sec/90˚
MODEL
Rated
Torque
(kgf-m)
Timing
50/60Hz
(sec/90˚)
Motor
Power(W)
(Phase)
Rating
(min)
Voltage
(V)
Frequency
(Hz)
Weight
(kg)
Rev. of
Manual
Handle
(turn/90˚)
Handle
oper.
force
(kg)
CA-01H
15
36/30
25(Φ1/Φ3)
30
Φ1 220
/
Φ3 440
50/60
23 22 9
CA-02H
25 25(Φ1/Φ3)
28 22 13
CA-05H
50 60(Φ1/Φ3)
71 24 16
CA-10H
100 90(Φ1/Φ3)
87 72 13
CA-20H
200 200(Φ3)
440
110 236.2 8
CA-40H
400
42/35
400(Φ3) 230 260 15
CA-80H
800 750(Φ3) 230 236 17
CA-120H
1200 1500(Φ3) 230 303 19
Ex) HAB Type

5
Ver. 1.0
SHIN HWA Eng.Co.,Ltd.
CONTROL ACTUATOR
CA01H~CA120H
2 Insta ation
2-1 Structure
When you maintain and check the Control Actuator, please refer to the below diagram.
Fig.-1. Control Actuator structure
2-2 Transport and Insta ation
Transport
When you transport this product, please avoid an accident such as fall and impact.
Place for Installation
- There is no special limit in the place for installation of the Control Actuator, but if it is exposed
to an environment with bad conditions for a long time, you had better use a proper protection
device.
- As well, you had better secure proper space around the Actuator for maintenance and repair.
Installation
- When you install the Control Actuator in a mounting place selected in advance for installation,
firmly fixate the Actuator with four bolts.
- Connect the lever arm and the corresponding lever.
- The operation angle is correctly adjusted before delivery, and you do not need to adjust it.
If you need to adjust it:
① Give a current signal (a contact point signal in case of opening/closing control and angle
control) to put the Actuator in a complete opening (or closing) position.
② Turn off the power supply, and separate the cover on the rear surface of the Actuator from
the main frame. Here, avoid giving a damage to the gasket.
③ Readjust the Position Limit Switch to fit the contact point.
(Refer to Clause 7 later for how to adjust the Limit Switch.)
④ Here, check if the needle of the indicator is in the complete opening (or closing) position
before adjusting.
⑤ Fit the gasket and the cover, close them, and tighten with a bolt.
- Please consult the manufacturer when changing the direction of rotation of the output shaft

6
Ver. 1.0
SHIN HWA Eng.Co.,Ltd.
CONTROL ACTUATOR
CA01H~CA120H
Caution for Installation of Control Actuator
① Never give an impact on the output axis of the product. It is a slow equipment with the
total operation time of 30-60 seconds, but a momentary torque by shock makes a great
vibration and can give a damage to the gear, motor, or the like.
② You must the axis lines of the output axis of the product and the corresponding axis parallel
and on the same line as much as possible.
If the axis lines are not parallel or not on the same line, a load can be applied to the output
axis of the product, causing a shorter life and a damage to a connecting link.
How to install control actuator
Fig.-2. How to install CA
Matters to check before operation
① Check if the Control Actuator is firmly installed on the device to control.
② Check if the damper or the valve smoothly operates. In addition, check if the subject to
control is completely opened or closed and if it receives an excessive pressure.
2-3 Limit switch adjustment (CA01H~CA10H FB, AB option type)
Position limit switch adjustment method (based on clock direction in view of output shaft)
① Please note “Fig-1. CA structure” and check limit
switch position.
② In “Fig-3. Limit switch and cam arrangement” upper
horse-shoe sensor LS P is close sensor and below
horse-shoe sensor LS1P is open sensor.
③ Horse-shoe sensor LS1P and LS P are available
position control and signal control respectively.
④ In order that dial gauge meet into 0% exactly, after
loosing ⓐneedle fixed bolt and adjust ⓑneedle
(Note Fig-4)
Fig-3. Limit switch and
cam arrangement

7
Ver. 1.0
SHIN HWA Eng.Co.,Ltd.
CONTROL ACTUATOR
CA01H~CA120H
⑤ Adjustment of limit switch (LS1) for clock direction position control.
When dial gauge is positioned in 0%, please note
“Fig-5 Limit cam adjustment (Close)” use flat screw
driver, LS P CAM should be rotated slightly into
arrow direction and matched until LS lamp is on.
⑥ Upon setting LS P, signal control shall be
automatically matched.
⑦ Adjustment of limit switch (LS1) for counter-clock
direction position control.
When dial gauge is positioned in 100%, the “Fig-6.
Limit cam adjustment (Open)”, LS1P CAM should be
rotated slightly into arrow direction and matched
until LS lamp is on.
⑧ Upon setting LS1P, signal control shall be matched automatically.
⑨ After adjusting limit switch cam, tighten upon bolt and cam should be fixed into cam shaft.
Check the stop position by running the actuator electrically, and repeat the above process
if the stop position is incorrect
Torque limit switch
① Do not operate randomly because it was adjusted when
dispatching our factory.
② In standard mode, it is normal condition when rated
torque switch LSF lamp and LSR lamp are off.
How to adjust
LS1P
CAM
LS P
CAM
Fig-6. Adjustment of limit cam (open)
Fig-7. Torque limit switch lamp
Fig-4. Adjustment process of
dial gauge
<Inside indicator for HAB Type>
How to adjust
LS1P CAM
LS P CAM
Fig-5. Adjustment of limit cam (close)

8
Ver. 1.0
SHIN HWA Eng.Co.,Ltd.
CONTROL ACTUATOR
CA01H~CA120H
2-4 Limit switch adjustment (In RB, SB option)
Position limit switch adjustment method (In viewing of output shaft, it is based on clock
direction-Open)
① In Fig-8, upon ea of limit switch LS , LS4 are close direction (clock), below ea limit
switch LS1, LS3 are open (Counter-clock)
direction
② Limit switch LS1, LS are limit switch for
position control and LS3, LS4 are limit switch
for signal control.
③ It should be matched between dial gauge and
damper operation direction.
For example if the damper direction is the
closing direction, the dial gauge should be 0%
④ Actuator should be operated with complete
close by auto and manual method.
⑤ Dial gauge should be matched into 0% exactly.
Unscrew set screw which is fixed to needle, and
adjust it into 0%
⑥ Before adjustment of built-cam, loose cam edge’s
bolt (cam axis bolt from Fig-8.), keep condition
that cam may be operated manually.
⑦ The adjustment of limit switch(LS ) for
close(clock direction) position control limit switch
(LS ) should be slightly rotated into arrow
direction and matched until there are happening on small sound and move into LS CAM
with arrow (clock) direction by using flat screw driver when dial gauge indicates in 0%
(note Fig-10,11)
(Please check whether stop position is correct or not after moving actuator with electric
power supply.)
⑧ In Case that actuator stop position is not exact, please do above process 1- times
repeatedly and match.
Fig-9. Procedure of adjusting
the dial
Fig-10. How to adjust
Limit switch cam
Fig-11. How to adjust
limit switch cam2
Clockwise
Fig-8. Arrangement of limit switch
Cam edge’s bolt

9
Ver. 1.0
SHIN HWA Eng.Co.,Ltd.
CONTROL ACTUATOR
CA01H~CA120H
⑨ Adjustment for open (CCW) direction limit switch
(LS4) must move before control limit switch (LS ) as
the Fig-1 , with equal LS CAM operation method to
LS4 CAM.
(LS4CAM should be operated a little (around 3˚~5˚)
in advance before LS CAM)
⑩ Open (CCW) direction position control limit
switch(LS1) must be matched with arrow (CCW)
direction so that limit switch sound may be click when
indicator is 100%
⑪ Adjustment for open (CCW)direction limit switch
(LS3) must move before control limit switch (LS1) ,
with equal LS1CAM operation method .
(It should be operated a little (around 3˚~5˚) in
advance before LS1CAM.)
Torque Limit Switch
① Owing that it was adjusted in our factory with rate torque base, so in site it should not be
operated randomly.
Fig-15. Torque limit switch
Fig-13. How to adjust
limit switch1 cam
Counter-Clockwise
Fig-12. How to adjust
limit switch4 cam
Clockwise
Fig-14. How to adjust
limit switch3 cam
Counter-Clockwise

10
Ver. 1.0
SHIN HWA Eng.Co.,Ltd.
CONTROL ACTUATOR
CA01H~CA120H
2-5 Adjustment of Resistance (Potentiometer:Jp-30)
Let the position check needle indicate 50% on the scale plate manually or electrically.
Hold the potentiometer with your hand and lift up.
And hold the “Adjustment plate” and rotate it so that
the point is positioned as shown below (Fig-17.)
(Red point is marked on the “Adjustment plate”)
After that, gently place the potentiometer on its
orginal state
If positioned as shown below, 500Ω will be output
(The potentiometer’s output is 0 ~ 1000 Ω)
2-6 Adjustment of Current Transmitter (CA-□□HF TYPE)
(Feedback Signal : DC 4 ~ 20 mA)
It is attached for “F” type of control method in “1-5 terminology” (Feedback signal : DC 4-
0mA)
The Current Transmitter is a device that changes an input resistance signal into an output
current signal.
Check if the power supply is turned on. When the power supply is on, it is normal for the
LED to flicker with an interval of 0.5 seconds.
Control the Actuator to the position of completely closing automatically.
Finish the ' -5 Adjustment of Potentiometer', and check if the control is completely done.
If the LED flickers (with a shorter interval than 0.5 seconds), it means the resistance value
is out of range
Measure the current between P1 and N1 of the terminal block, and check if it makes DC
4mA.
If DC 4mA is not made, push the R/I Converter Zero control switch for three to four seconds
to set to DC 4mA.
And let the Actuator to the status of completely opening by turning automatically.
Measure the current between the P1 terminal and the N1 terminal to check if DC 0mA is
made.
Fig.-16. Position of the scale plate
Fig.-17. Adjustment of resistance
Adjustment
plate

11
Ver. 1.0
SHIN HWA Eng.Co.,Ltd.
CONTROL ACTUATOR
CA01H~CA120H
If DC 0mA is not made, push the SPAN control switch on the R/I Converter for three to four
seconds to set to DC 0mA.
After actuator return to complete close position, measure current of P1 and N1, If DC4mA
is not measured, repeat above process and if there is near to DC4mA, the adjustment is
completed.
Repeat above (4)-(10) article over times, adjust it, so that output value is near to it as
possible.
Generally Zero , Span value is set as above method , but in case that there are difference
among devices of installation place , please execute minute adjustment as following method .
value adjustment of ZERO, SPAN use MODE SWITCH and in that time KEY modification is
as followings.
Under the condition that actuator is closed completely, push Mode switch one time and
adjust with Zero/Span switch and do minute adjustment into 0% position (4mA).
After completing above (15) article process, actuator should be keep complete opening, and
push Mode switch one time again and with Zero/ Span switch, execute minute adjustment
into 100% position ( 0mA) by Zero/Span switch.
After completing minute adjustment, push Mode switch one time again, and escape.
(It should push 3 times, escape completely.)
Fig-18. adjustment of current transmitter
Fig-19. Adjustment of current transmitter

1
Ver. 1.0
SHIN HWA Eng.Co.,Ltd.
CONTROL ACTUATOR
CA01H~CA120H
2-7 Adjustment of ba ancing re ay (SBR-10)
After setting dial gauge, limit switch, resistance, and then adjust SBR-10.
Put selector switch of local box into remote position.
push SW3 (Auto Scan) button switch for 3-4 seconds.
In this time, the auto lamp flickers and operates to set the output value (4- 0mA DC ).
And the operating takes around 1 0-180seconds. (while the operating, do not operate
arbitrary)
If the auto lamp flickers rapidly and
actuator stops working, Please check
whether resistance signal or resistance
using angle is normal or not.
(When the dial gauge is 50%, you can
see red point on the
resistance(potentiometer))
When the operating is completed, press
the SW3 (Auto scan) button switch for
3~4seconds to complete the operation
A fault lamp flickers when the input
signal is blocked or when the
polarity(+,-) of the input signal changes
or when the resistance is out of
output(100~900Ω)
In normal case, you can adjust the balancing relay as above.
But if the installation site is deviated from the actuator, you can fine-tune it as shown below
Fig.-19. Adjustment of balancing relay

13
Ver. 1.0
SHIN HWA Eng.Co.,Ltd.
CONTROL ACTUATOR
CA01H~CA120H
If you want to convert the action direction of actuator, you can adjust it as shown below
① To change open and close, No. and No.3 switch must be change from its current position
to the opposite position
② After that, short the two points of the marked switch “SW1” for 3 to 5seconds as shown.
③ When LS1 and LS lamps flicker 3 to 5 times at same time, then LSF and LSR lamps
blink 3 to 5 times at the same time, and then the LS lamps turn on and off, the action
direction of actuator changes its direction from forward to reverse.
④ When LSF and LSR lamps flicker 3 to 5 times at same time, then LS1 and LS lamps
blink 3 to 5 times at the same time, and then the LS1 lamps turn on and off, the action
direction of actuator changes its direction from reverse to forward.
Fig.-20. Fine-adjustment of balancing relay
Current
position
Opposite
SW1

14
Ver. 1.0
SHIN HWA Eng.Co.,Ltd.
CONTROL ACTUATOR
CA01H~CA120H
2-8 How To adjust STP-07 (Indicator)
When input signal is 4mA, in order to show output signal correctly, setting of indicator must
be as followings.
- Input signal should be adjusted into 4mA and push following picture’s Switch-1 for ~3
second.
- The setting is complete when the “CL ” mark on LED plate flashes and returns normal state.
When input signal is 0mA, in order to show output signal correctly, setting of indicator must
be as followings.
- Input signal should be adjusted into 0mA and push following picture’s Switch- for ~3
second.
- The setting is complete when the “OP ” mark on LED plate flashes and returns normal state.
If push Switch-1 or Switch one times shortly, it is move into Zero and Span output signal
setting mode.
Function of CL1 (OP1) is signal setting Mode which Actuator shows Zero / Span’s normal
position.
If pushing limit operation alarm signal switch-1 or switch shortly, it is Zero/Span output signal
position setting, and after extinguishing CL1 /OP1, if indicator indicates “%”mark, use
Up/Down switch and finish to set desired position(%), it will be automatically set after waiting
for a while.
(In output setting mode, the function shall be converted into Switch-1= Down, Switch- = UP)
Fig.-21. How to adjust STP-07
Switch-1 Switch-2

15
Ver. 1.0
SHIN HWA Eng.Co.,Ltd.
CONTROL ACTUATOR
CA01H~CA120H
3 Maintenance
3-1 Troub eshooting
Symptom Expected Cause How To Repair Note
The motor
does not
work.
Power is not supplied. Supply power. In case of three phase,
check R, S, and T.
The position control
switch operates.
Reset to fit the scale
plate.
The torque switch
operates.
Remove the cause for
overload.
Reset the switch.
(Never randomly set.)
The overload relay
operates.
Remove the cause for
overload.
Reset the set value.
(Never randomly set.)
The fuse is broken. Replace the fuse. In case of three phase
The condenser is
damaged.
Replace the
condenser. In case of single phase
The brake does not
work. Replace the brake.
The motor
does not stop
with the
position
control
switch.
The motor makes a
reverse rotation.
Connection is made
with two lines among
three lines changed.
It is in case of three
phase, and it does not
apply to the standard.
The position control
switch is changed.
The position control
switches (LS1, LS2)
are used by being
changed.
It does not apply to the
standard.
The switch setting is
defective. Reset.
The switch is defective.
Replace the switch.
When the
torque switch
operates, the
motor does
not stop.
The motor makes a
reverse rotation.
Connection is made
with two lines among
three lines changed.
It is in case of three
phase, and it does not
apply to the standard.
The torque switch is
changed.
The position control
switches (LSR, LSF)
are used by being
changed.
The switch is defective.
Replace the switch.

16
Ver. 1.0
SHIN HWA Eng.Co.,Ltd.
CONTROL ACTUATOR
CA01H~CA120H
4 Basic Circuit Diagram (Standard)
4-1 For Proportiona Contro (Using Ba ancing Re ay & Potentiometer)
Single phase (Up to CA10H) Three phase (Up to CA10H)
Three phase (More than CA20H)

17
Ver. 1.0
SHIN HWA Eng.Co.,Ltd.
CONTROL ACTUATOR
CA01H~CA120H
4-2 For Opening Contro (Using Current Transmitter & Potentiometer)
Single phase (Up to CA10H) Three phase (Up to CA10H)
Three phase (More than CA20H)

18
Ver. 1.0
SHIN HWA Eng.Co.,Ltd.
CONTROL ACTUATOR
CA01H~CA120H
4-3 For Opening Contro (Using Potentiometer)
Single phase (Up to CA10H) Three phase (Up to CA10H)
Three phase (More than CA20H)

19
Ver. 1.0
SHIN HWA Eng.Co.,Ltd.
CONTROL ACTUATOR
CA01H~CA120H
4-4 For Opening Contro (Using Potentiometer)
Single phase (Up to CA10H)
Three phase (Up to CA10H)
Three phase (More than CA20H)

0
Ver. 1.0
SHIN HWA Eng.Co.,Ltd.
CONTROL ACTUATOR
CA01H~CA120H
SHINHWA ENG. Co., Ltd.
Manufacturer information
Company Name : SHIN HWA ENG Co., Ltd
Address : 4 Cheongneungdae-ro ( 80B - L ), Namdong gu,
Incheon Korea
ZIP CODE : 1695
Tel : 8 -3 -817-8030
Fax : 8 -3 -815-8036
E mail : 8030@seg.co.kr
Website : http://www.seg.co.kr
COPYRIGHT 0 0(C) Shin Hwa Eng Co., Ltd .ALL RIGHTS RESERVED
This manual suits for next models
1
Table of contents
Other Seg Controllers manuals
Popular Controllers manuals by other brands
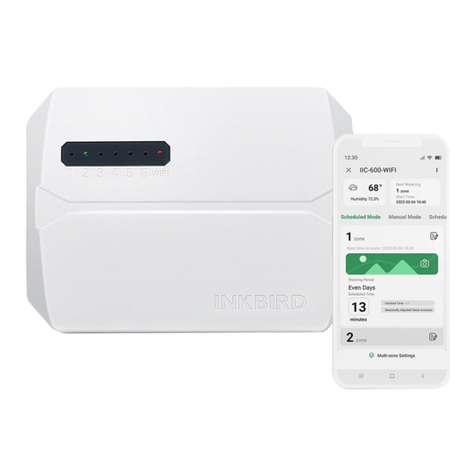
Ink Bird
Ink Bird IIC-600-WIFI user manual
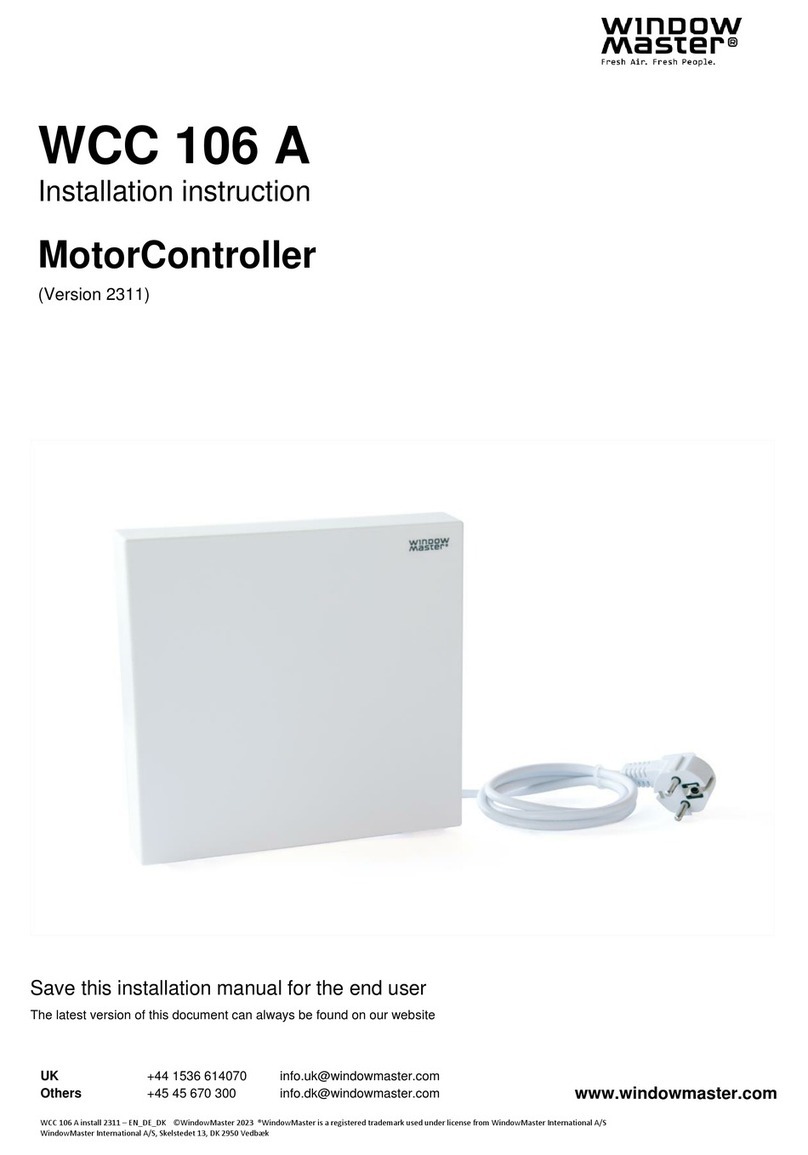
WindowMaster
WindowMaster WCC 106 A installation instructions
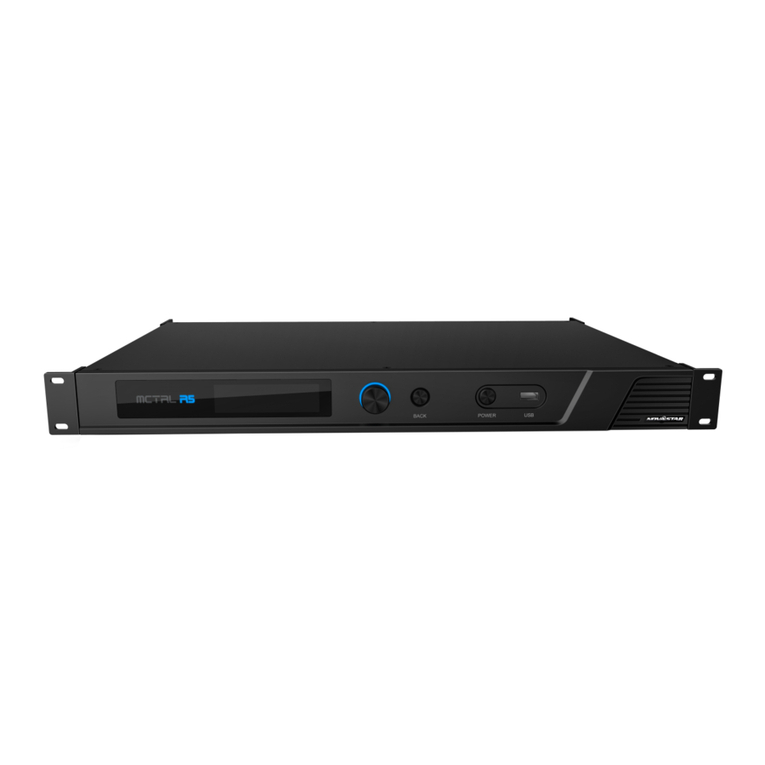
NovaStar
NovaStar MCTRL R5 user manual
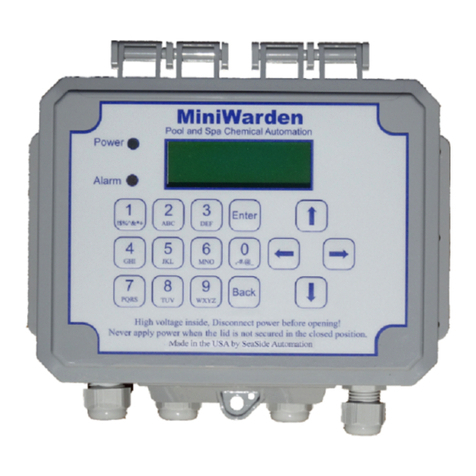
Seaside
Seaside MINI WARDEN Installation & operation

Thermo Solar
Thermo Solar SR34 Installation and operating instructions
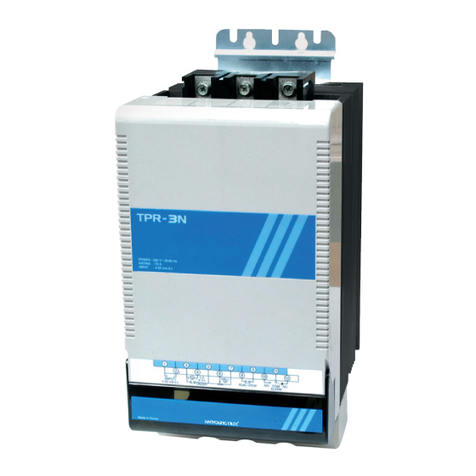
HANYOUNG NUX
HANYOUNG NUX TPR-3N instruction manual
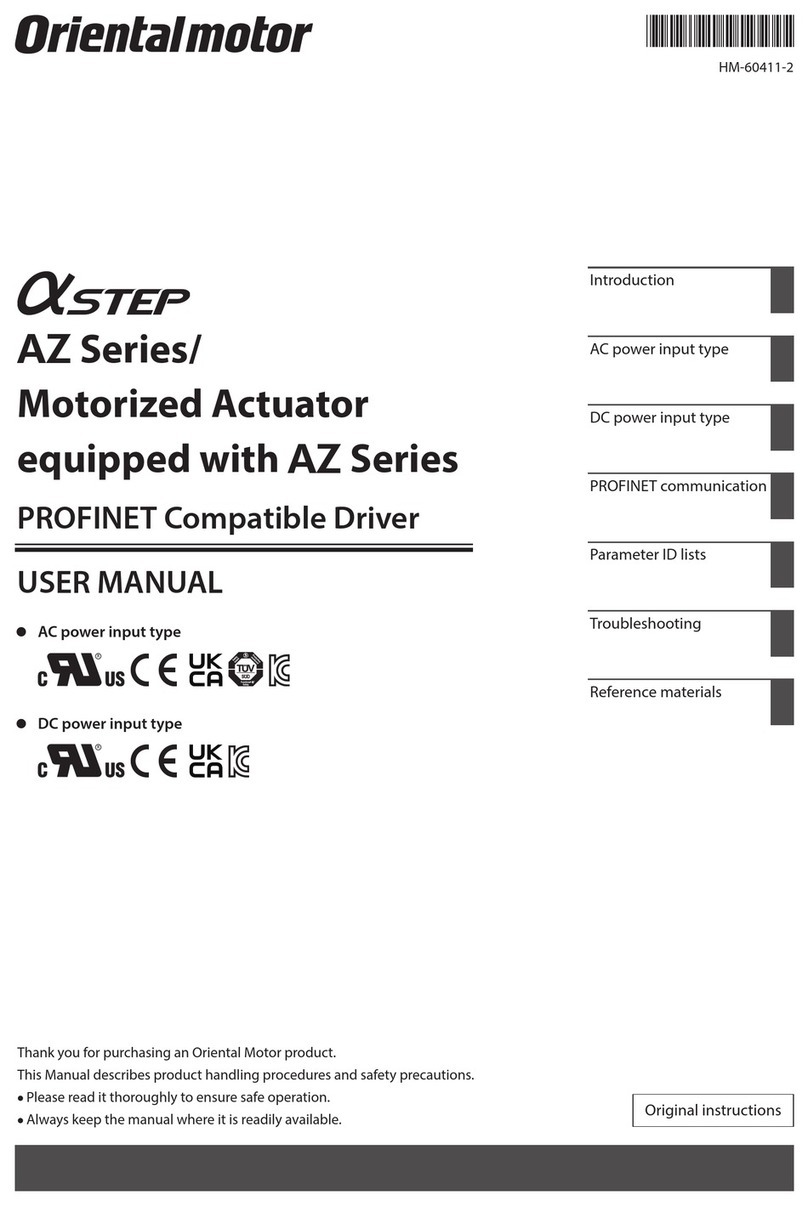
Oriental motor
Oriental motor aSTEP AZ Series user manual
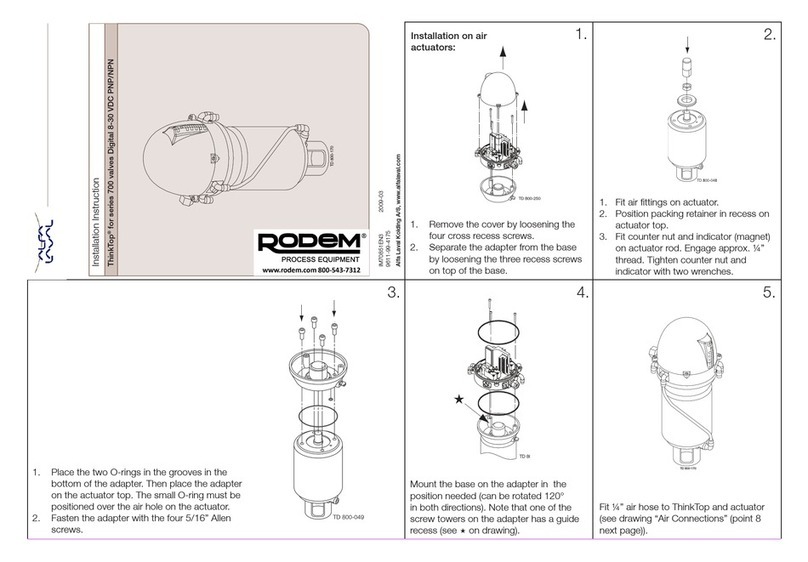
Alfalaval
Alfalaval ThinkTop Basic Installation instruction
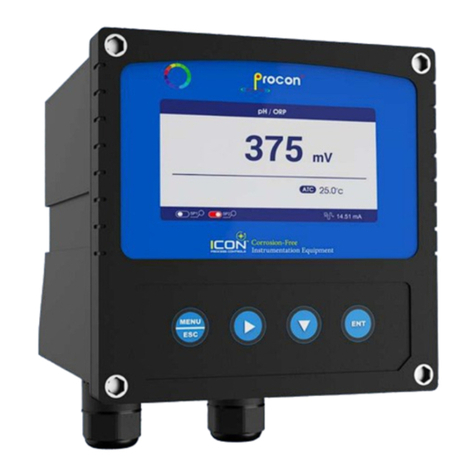
ICON
ICON ProCon D400 Series operating manual
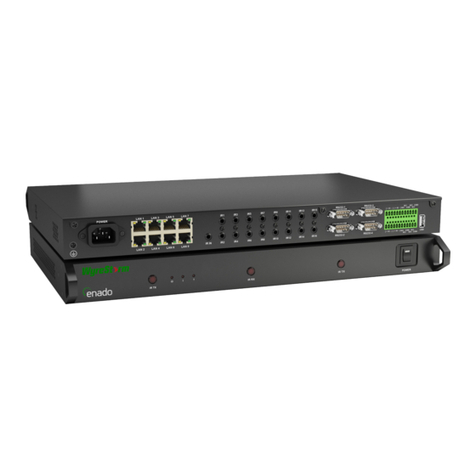
Wyrestorm
Wyrestorm Enado ENA-001-010 installation guide
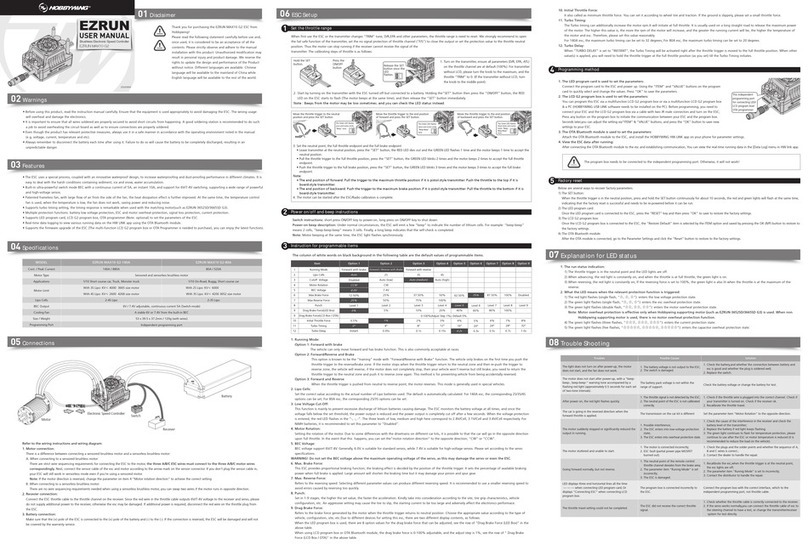
Hobby-Wing
Hobby-Wing EZRUN MAX10 G2-140A user manual
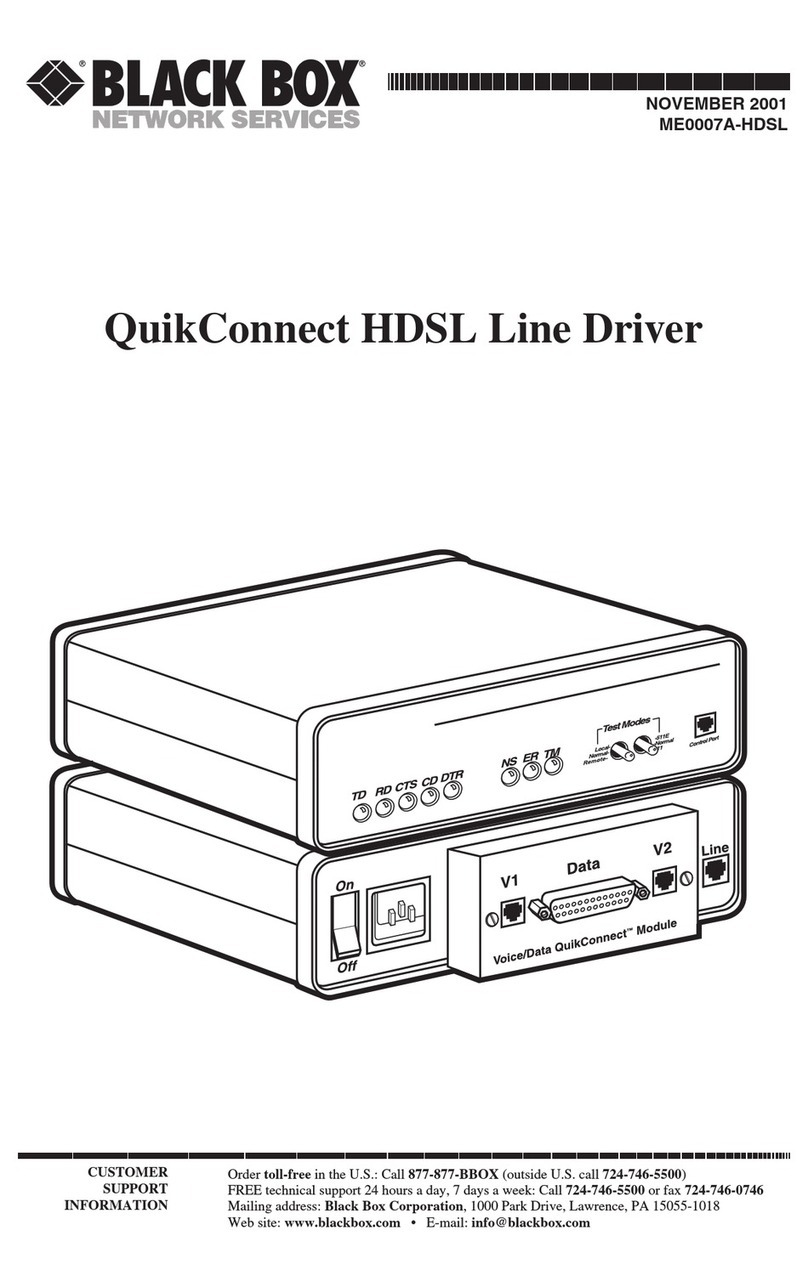
Black Box
Black Box QuikConnect ME0007A-HDSL manual