Selema DC 4Q A Series User manual

1
www.selema.it
Service Manual
DC 4Q A Series
Series
Precision Servodrive for DC Motors
Service manual
Precision Servodrive for DC motors
Via Monari Sardè, 3 - Bentivoglio (BO) - Italia
+390516640464 - Fax +390516640784 - www.selema-srl.it
DC 4Q A series

2
Service Manual
www.selema.it
DC 4Q A Series
All the informations and concepts included in this user guide are copyright, and are supplied to the
user with the understanding that it may not be copied, disclosed or duplicated in whole or in part for
any purpose not authorised by the factory. All specifications are subject to change without prior
notification.
WARNING - Risk of damage and/or personal injury
Thisdrivesdoesn’tcontainanyuserserviceablepart. Attempting toreplaceanyinternalcomponent,
may result in damage to the unit and/or personal injury. This may also avoid the warranty.
89/336/EECElectromagnetic
EN 55011 Compatibility
EN 550082-1
98/37/EC Safety of Machinery
EN 60204-1
CONDITIONS OF ACCEPTABILITY
The devices shall be installed in compliance with the enclosure, moun ting, spacing, and segregation
requirements of the ultimate application.
These devices are intended as open type equipment. The need to repeat a temperature test shal be
considered in final end use application
These devices are suitable for field wiring
The EC mark that is applied to the drives references to the Low Voltage Directive (2006/95/EC)
and EC Directive on EMC (89/336/EC).
The standard EN 61800-5-1 is applied to ensure conformance with the Low Voltage Directive.
The standard EN 61800-3 is applied to ensure conformance with the EMC Directive.
Inreferencetonoise immunity and noiseemissiontheconvertersfulfiltherequirement to the category
second environment (industrial environment).
If the installation of the drive is carried out differently than described in this manual, the user must
carry out new measures to satisfy the requisites of law.
CE COMPLIANCE:
Agency approvals
Print in Italy rev. 03/2011

3
www.selema.it
Service Manual
DC 4Q A Series
Chapter 1
1.1 Safety and note ......................................................................................................................... 4
1.2 Operation mode and feedback.................................................................................................. 5
1.3 Model and size .......................................................................................................................... 6
1.4 View product.............................................................................................................................. 7
1.5Ambient conditions .................................................................................................................... 8
1.6Ventilation...............................................................................................................................8-9
1.7 Dimensions ............................................................................................................................... 9
Chapter 2
2.0 Signals input and output..................................................................................................... 10-11
2.1 Fault output ............................................................................................................................. 12
2.2 Current request (REQ) .......................................................................................................12-13
2.3 GND ground ............................................................................................................................ 13
2.4Ausiliary power supply +/-9.8V ................................................................................................ 14
2.5 Start input ................................................................................................................................ 14
2.6Analog inputs........................................................................................................................... 15
2.7 Tachogenerator input............................................................................................................... 16
2.8Ausiliary power supply +V........................................................................................................ 16
2.9 Encoder inputs........................................................................................................................ 16
2.10 Limit switch inputs............................................................................................................17-18
Chapter 3
3.0 Power supply construction ................................................................................................. 19-20
3.1 Connections to earth and ground ............................................................................................ 21
3.2 Note about Connections.......................................................................................................... 22
Chapter 4
4.0 Internal adjustements.............................................................................................................. 23
4.1 Brush motor Connections with Encoder feedback ............................................................. 24-25
4.2 Brush motor Connections with Tachogenerator feedback.................................................. 26-27
4.3 Brush motor Connections withArmature feedback .......................................................28-29-30
4.4 Current adjustments................................................................................................................ 31
4.5 Ramp time adjustments.......................................................................................................... 32
4.6 Potentiometer adjustments..................................................................................................... 33
4.7 Dynamic adjustments.............................................................................................................. 34
4.8 Indicator Leds and protections ................................................................................................ 35
Index

4
Service Manual
www.selema.it
DC 4Q A Series
Please read these notes carefully before powering up the drive
Simbols security standard
Caution
Warning of dangerous current present
In case of doubt or in any case you don’t know as to behave yourself, before access to the
drive, power off the device and wait until all the leds are turned off.
May you have attention when you touch the drive because it may be hot.
Danger Sign
All the circuits in the Drive are potential sources of severe electrical shock, so follow these
rules to avoiding possible personal injury.
- Power off the drive and wait until all the leds are turned off before touching, removing,
connecting or any other critical action.
- Never disconnect any connectors before powering down the drive
It is very important meet all applicable safety requirements during installation and operating of any
motion control equipment.Any installer has to assume the responsibility to ensure that he recognizes
and complies all the relevant safety standards.Any installation, not meeting the safety requirements,
may damage the equipment or injury the user.
This motion control equipment shoul be handled, installed, setted-up and maintenanced only by
competent personnel expert and trained in the installation of motion control electronic equipment.
Suchtechniciansshould be awareof potentialelectrical andmechanical hazards.Shall neverbeliable
or have any responsability if the products have been improperly stored, installed, used or maintened,
or if the costumer has permitted any unauthorized modifications, adjustments, and/or repairs to the
products.
Users must keep well clear in mind that this motion control equipment is capable of producing high
forces and rapid movement so they must be used with attention especially during the application
program’s development.
Thismotion control equipmentsare sold asend-usersproductsto be installedonly by practicalstaff in
accordance with all local safety laws and regulations. The device have to be enclosed such that any
part is not be accessible while the system is powered on.
Westronglyreccomendtofollowtheserecommendationsin order to avoid wrong uses of theequipment
that may be impaired all the protections provided by the device.
1.1 Safety and note

5
www.selema.it
Service Manual
DC 4Q A Series
Description
Operation mode
General characteristic
Closing the velocity feedback loop to motor may be done in several different ways to accommodate
most applications. This types of velocity feedback are available with DC brush motors.
Velocity feedback
• DC motor with encoder
• DC motor with internal PWM (Armature)
• DC motor with tachogenerator
This is a drive capable to drive DC brush motors, up to 3Nm. It's a High Performance full four
quadrant drive servo amplifier. The mosfet output power stage is controlled by a 20 Khz PWM (Pulse
Width Modulation) signal that allows it to drive servo motors where high dynamic performance and
precise speed is required.
1.2 Operation mode and feedback
DESCRIPTION
SPEED CONTROL
INPUT It is speed piloting using an analogue
reference (differential or common mode) STANDARD
TORQUE CONTROL
INPUT
It is torque piloting using an analogue
reference. This function allows you to control
the current from the drive. STANDARD
DESCRIPTION
START INPUT Start input, enable the drive with range from
>9Vdc to +30Vdc (min/max) STANDARD
LIMIT SWITCH
INPUTS Clockwise (CW) and Counter-clockwise (CCW)
limit Switch inputs STANDARD
FAULT OUTPUT Fault drive, open collector output 50mA max.
(Normally closed, opens when in protection
mode) STANDARD
1 ANALOG
OUTPUT
1 motor velocity monitor “TEST”, with range +/-
8 Vdc output
STANDARD
LED INDICATOR Four LEDs are located just in front of the
potentiometers and show the current state of
the drive STANDARD

6
Service Manual
www.selema.it
DC 4Q A Series
Specifications
Model available
Size available
The power supply voltage has to be a transformer-isolated voltage
Max size available for model 130 is 7/14A
1.3 Model and size
CURRENT
Size Rated current (A) Peak current (A)*
2/4 2 4
4/8 4 8
7/14 7 14
10/20 10 20
*Peak current during 2 sec
POWER SUPPLY
Model 12 8 - 28 Vdc* 14Vdc**
Model 65 20 - 84 Vdc* 60Vdc **
Model 100 30 - 130 Vdc* 100Vdc **
Model 130 35 - 165 Vdc* 130Vdc **
* min/max power supply **Typical
TECNICAL DATA CHARACTERISTICS
Supply voltage output 0,9 Vdc Input
PWM frequency 20Khz
Operating temperature 0/+45°C
Storage temperature -10/+70°C
Drift analog input 0,5uV/°C
Analog inputs (+/-VEL) +/-10Vdc max, impedance 20Kohm
Velocity monitor output (Test) +/- 8Vdc = max velocity
Power supply output (+V) +5Vdc max. 130 mA
Power supply output (+/-9.8V) +/-9.8Vdc max. 4mA
Encoder max. frequency 300Khz with level >+2,8/24Vdc min/max
Fault drive output NPN 50mA max.
Start input >+9V/+30Vdc (min/max)
Band width (current) 2KHz
Band width (velocity) 150Hz
Minimum Inductance motor 400uH
Weight 0,35kg 10.6oz
Contaminants 2°or better (Norms EN60204 e EN50178)
Altitude Up to 1000m without restrictions, from 1000 to 2000m
power derating 1,5%/100m
Flammability rating 94V-0 Cover material, the PCB and the electronic component
meet 94V-0

7
www.selema.it
Service Manual
DC 4Q A Series
(1) Product Label
(2) Fixing screw
(3) Product Cover
(4) Solder bridges
(5) Adjustement zone
(6) Four calibration Potentiometers
(7) Four Leds
(8) TEST point (Encoder, Tacho or Armature velocity)
(9) M2 Signal terminal 5 pins MC1,5/5-ST-3,81 (pitch 3,81)
(10) M1 Signal terminal 10 pins GMST 2.5/10-G-5,08 (pitch 5,08)
(11) POWER Terminal 4 pins GMST 2.5/5-G-5,08 (pitch 5,08)
1.4 View product
3
2
1
456789
10
11

8
Service Manual
www.selema.it
DC 4Q A Series
Notes during the assembly
Caution: during the wiring of the servodrive in the electrical box, make sure that do not enter leading
wires of copper or iron chips through the slits. Before performing the work cover the holes with a
piece of paper tape. Naturally finished work this tape is removed.
1.6 Ventilation
SIZE
MODEL 2/4 4/8 7/14 10/20
12 N N N N
65 N N N N
100 N N N V
130 N N V N.A
Positioning in the electrical box
Follow the instructions in the positioning of the servodrive in the electrical box.
- The drive is natural convection air flow cooled.
- To ensure the drive cooling and make the installation easier for the operator it must be installed
vertically leaving a free space of at least 20 mm (0,78 inch) on each side of the device.The converter
mustbe mounted verticallyonthe electrical box.In case youwant tomountit horizontally,remove the
cover.
- The electrical box must have suitably filtered air vents.
- Leave the necessary space both above and below the converters.
- Keep the drive from excessive mechanical vibration
Conductive mounting
panel (zinc coated)
Dimensions are
expressed in
millimeters.
1.5 Ambient conditions
Cable duct
Cable duct
N = Standard radiator (operating ambient temperature from 0 to 40°C)
V = Standard radiator + supplementary ventilation (operating ambient temperature from 0 to 45°C)
NA = Not available
This servodrive are intended only for use in close locations. Ambient characteristics: operating tem-
perature from 0 to +40°C. Humidity limits between 5% to 95% non condensing (Pollution degree 2 or
better).
Supplementary ventilation may be requested in accordance to size. See the table below.
202050
50
135
5,3"

9
www.selema.it
Service Manual
DC 4Q A Series
Dimensions in mm and Inch
Supplementary ventilation
V = Standard radiator+fan
cooling below the converter
(operating temperature 0 to
+45°C)
NO
Mounting position
YES
Ifyou need the convertermountedhorizontally,
remove the cover.
1.7 Mechanical dimensions

10
Service Manual
www.selema.it
DC 4Q A Series
The figure below shows the view of the converter terminals.
M1 Signal terminal 10 pins "type GMST 2,5/10-G-5,08"
M2 Signal terminal 5 pins "type MC 1,5/5-ST-3,81"
POWER Terminals 4 pins "type GMST 2,5/4-G-5,08"
On the test point "TEST" you can see the signal of velocity speed.The output from 0 to + /-8V is from
zeroto maximum speed.Atthispoint you cananalyzethe signal when youenableone of thefollowing
velocity feedback.
•Encoder
•Armature
•Tachogenerator
Power connector
2.0 Signals input and output
NOTE: See also the connection diagrams in Chapters 4.1 - 4.2 - 4.3
POWER
+HV (IN) Positive Power supply input
GND (IN) Negative Power Supply input (GND)
+MOTOR (OUT) Motor connection phase +M
-MOTOR (OUT) Motor connection phase -M

11
www.selema.it
Service Manual
DC 4Q A Series
Signal inputs and outputs
M1 CONNECTOR
1 FAULT (OUT) Fault drive, open collector output max. 50mA
Normally closed, opens when the drive in protection mode
2 REQ
REQ:, can be used in 2 distinct modes:
1) Motor Current limit mode (by REQ setting):
A motor current limit mode connect an external resistor to GND reduces
the maximun current. Connect a 1/4W o 1/8W resistor be
tween the
REQ (pin 2) and GND (pin 3) terminals. A 47Kohm external resistor
reduces the current by 50%. (Note: The drive velocity loop remains
active)
2) Torque request (by REQ setting):
Range: +/- 10V, which corresponds to the drives peak current output. In
this mode the velocity loop is automatically disabled.
3 GND Signal Common Ground
Corrisponds to power supply's negative GND input
4 +9.8V (OUT) Power supply +9.8Vdc max 4mA
5 –9.8V (OUT) Power supply –9.8Vdc max 4mA
6 START (IN) Positive drive enable with range >+9Vdc min. to +30Vdc max
7 +VEL (IN) Reference Positive differential input (Velocity command)
8 -VEL (IN) Reference Negative differential input (Velocity command)
9 +TACH (IN) Positive +DT tachogenerator input. This signals corrispond
s to power
supply's negative GND input.
10 -TACH (IN) Negative -DT tachogenerator input.
M2 CONNECTOR
+V (OUT) Power supply +5V max. 130mA
ENC A (IN) Encoder input Channel A (High logic level from >
2,8V to +24Vdc max. Low
logic level <1,5V)
ENC B (IN) Encoder input Channel B (High logic level from >
2,8V to +24Vdc max. Low
logic level <1,5V)
+L.SW (IN) Clockwise (CW) limit Switch input. (High logic level from >
5V to +24Vdc
max). To enable this function, you must open the internal
soldiering point SG
and SH. See chapter 2.10
- L.SW (IN) Counter-Clockwise (CCW) limit Switch input. (High logic level from >
5V to
+24Vdc max).
To enable this function, you must open the internal soldiering
point SG and SH. See chapter 2.10

12
Service Manual
www.selema.it
DC 4Q A Series
Fault drive, open collector output max. 50mA
Normally closed, opens when the drive in protection mode
2.1 FAULT output
(M1 signal terminal pin 1)
Witha voltage (example froma CNCoutput) you cancommand the drivein torque mode.
Applying a signal of +/-10V at REQ, the Drive to supply positive or negative peak current.
The formula to determine the value of Voltage to apply in REQ in order to obtain requested current is
the following:
Example: (Drive size 10/20A, request current 8A)
NOTE:
In current reference the loop of internal velocity automatically excludes itself .
2.2 Current request (REQ)
V(REQ) = 10 * Request current / PKcurrent Drive
V(REQ) = 10 * 8 / 20 = 4V
(M1 signal terminal pin 2)
DRIVE
DRIVE
CNC

13
www.selema.it
Service Manual
DC 4Q A Series
Current output limitation
With an external potentiometer connected from GND and REQ input, you have a limitation of output
current (from zero to max. size) drive's.
Externalpotentiometer(470K-1M
Ohm) 3-10 TURNS
The speed loop remains active and uses the input reference signal +/-VEL.
Connect between terminal and GND terminal REQ a resistor 1/4W or 1/8W. (The figure is used a
potentiometer connected to the rheostat). With external resistance tends to zero ohms, the output
currenttendstozero.Increasing the ohmic valueof resistance, the value of currentsupplied increases.
With 47K of the current is limited to 50% on the Maximum size.The loop motor speed remains active.
2.3 Signal common ground
(M1 signal terminal pin 3)
Signal Common Ground. Corrisponds to power supply’s negative GND input.
DRIVE
CNC

14
Service Manual
www.selema.it
DC 4Q A Series
In the terminals 4 (+9.8 V) and 5 (-9.8V) are available auxiliary supplies to power the potentiometer
reference speed. In the attached drawing below is also added a switch that allows the reversal of
the rotation motor speed .
The current capacity of the output is max + /-4mA
Output +9.8V can also be used to enable the converter
2.4 Ausiliary power supply +/-9.8V
Is possible enable the drive connected the STARTinput with +9.8V output "terminal 4"
The standard drive is furnished in this configuration.
Start enable input has logic range: >+9V to +30Vdc (min/max)
Unconnected Enable input = Drive Not Enabled
Enable Input >+9V to +30Vdc = Drive Enabled
2.5 Start input
(M1 signal terminal pin 4 and 5)
(M1 signal terminal pin 6)
DRIVE
DRIVE
CNC

15
www.selema.it
Service Manual
DC 4Q A Series
The following diagram shows an application utilizing a differential reference from a C.N.C
The +/-VEL in differential mode has a 40Kohm of impedance input.
Differential reference
Speed potentiometer
The following diagram shows an application using speed reference connections from C.N.C in the
Common Mode. This analog in common mode has a 20Kohm of impedance input.
Common mode reference
Thefollowing figureshows an applicationwith speed referenceconnections using aninternal +/-9.8V
powersupply.
The speed potentiometer must have an included value between >5 and <10Kohm.
Speed reference from external potentiometer
2.6 Analog inputs (+/-VEL)
(M1 signal terminal pin 7 and 8)
DRIVE
DRIVE
CNC
DRIVE
CNC

16
Service Manual
www.selema.it
DC 4Q A Series
In the terminals 2 and 3 you can connect the inputs from an incremental encoder for the current
feedback in response to encoder. Signals can come from encoder powered from +5V to +24V).
Minimum high logic level >+2.8V/24Vmax,
Minimum low logic level <1.5V
Encoder can be connected either push-pull (wiresA, B and GND) or line-driver encoder type (wires
+A+ B and GND). Remember to connect the zero encoder with the GND power converter.
View the connections and settings from encoder in chapter 4.1
2.9 Encoder inputs
2.8 Ausiliary power supply +V (out)
(M2 signal terminal pin 1)
On the terminal (+V) is available auxiliary power supply voltage +5V (+12 V on request order). This
output can be used to power the encoder on the motor. The capacity of the output current is
130mA max.
2.7 Tachogenerator input
Tachogenerator input (M1 signal terminal pin 9 and 10)
DRIVE
D.T
The following diagram shows the connection from tachogenerator and the drive DC ONE.
This function is enabled through the following settings on the solder point, and the insertion of RDT
resistance on the adjstustement zone. +TACH "pin 9" corrisponds to power supply’s negative GND
input.
Connect the negative of tachometer to pin 10. Do not exceed voltage as input from tacho value of
50V. Example: If you use a 10V/KRPM no more than 5000rpm
If the motor rotates in an opposite direction to the expected one,switch off and reverse the motor
and tachogenerator connections.
View the connections and settings from tachogenerator in chapter 4.2
(M2 signal terminal pin 2 and 3)

17
www.selema.it
Service Manual
DC 4Q A Series
t's possible to enable clockwise (CW) and counter-clockwise (CCW) motor rotation by connecting
the +L.SW and -L.SW inputs.
They may be used to block motor rotation when the machines overflow contact is intercepted.
The Enable input in regards to this input always has priority. To enable such a function, you
must:
-- Open soldiering point SG and SH (see figure 1)
-- Then connect on said input a positive voltage (between +5Vdc and + 24Vdc) coming from -for
example two N.C. contacts (see figure 2 or 3)
Function: At opening one of the following contacts you enable the motor rotation in the
corresponding direction.
2.10 Limit switch inputs
Note:
- This Drive is factory set with the SG and SH solder bridge close
- DON'T connect any voltage in the +L.SW and -L.SW inputs if the soldiering point SG and SH are
closed
- When one of these said contacts is intercepted the motor stops with the required inertia.
Fig. 1
Fig. 2
Example with external positive voltage
(between +5Vdc and +24Vdc)

18
Service Manual
www.selema.it
DC 4Q A Series
Limit switch inputs (continue)
Example with internal positive voltage (+9.8V)
Fig. 3

19
www.selema.it
Service Manual
DC 4Q A Series
Transformer
VDC = V2 * 1,41
Example: If the secondary transformer V2 is 45Vac, the VDC output is 45*1,41=64Vdc
PAY ATTENTION:
- The drive has zero signal GND in conjunction with the zero power GND, thereby preventing the
following links:
- Use a standard heavy duty power transformer without center taps on the secondary as shown in the
schematic above.
- DO NOT USE AN AUTO TRANSFORMER.
Power transformer (T)
F1
V1 V2
AC
AC
VDC
F2
+HV
(T) TRANSFORMER
GND
C
+
-
AC
POWER
INPUT
3.0 Power supply construction
Normallythe power supplyis builtby atransformer,a bridge rectifierand afiltercapacity.Alternatively,
the power supply can also be of switching type, in this case refer factory by the appropriate sizing.
The converter have to be supplied from an isolating rectified transformer secondary or a DC isolated
powersupply.
Voltage:
Theprimaryvoltagedependson whatisavailable locally fora singlephase. The secondaryvoltage is
calculated from the motor’s voltage at the required operating speed.
The secondary voltage VDC is:
The transformer's nominal power is calculated based upon the sum of power from the single motors
driven:
Where: Pn Motor =Power absorbed motor in (W)
N=Max. speed of motor in RPM.
Cn =Nominal torque of motor in (Nm).
Pn Motor = N * Cn / 9,55
P(VA)=Pn1+Pn2+..
VDC = Vdc motor / 0,85
Vdc motor = E+(Ri * In)
E = Ke * N° / 1000
Where the Vdc motor is a sum of FCEM + the drop R*I for the winding resistance motor
The FCEM of the motor "E", may be calculated by the formula:
Note: In multi-axis applications, the transformer's power can be downgraded by 30%. If the max.
power transformer calculated is over 6KVAcontact the factory.
If the secondary voltage of power supply is VDC, the Vdc motor is calculated by the formula:
Voltage motor

20
Service Manual
www.selema.it
DC 4Q A Series
Capacitor filter (C)
Capacity above the filter effect, helps to recover energy during braking of the motor.
If the converter during braking has the green LED that flashes you must increase the value of the
capacitor (eg. 10.000uF from a 20.000uF)
Fusibili
Fuses (F1) e (F2)
F1 (A) = P (VA) trasfo. / V1
Example: Brush motor with the following data:
In =5 (A)
Ri = 1 (Ohm)
E=48 (V) at nominal speed 3000 (RPM)
Vdc motor = 48 + ( 1 * 5) = 53V
VDC = 53 / 0,85 = 64V
64V is the VDC voltage request for the power supply. You'lluse a transformerwith thesecondary V2
= 64 / 1,41= 45Vac
When you use the transformer with V2= 44/45Vac, it is correct.
Misure unit:
E = Ke *n°/1000 (Vdc)
Im = I motor (A)
Ri = Winding resistance (Ohm)
Ke =Voltage constant (V/kRPM)
n° = MAX speed (RPM)
In regards to the capacitor filter we suggest a working voltage of:
*100VDC for Model 65
*160-200VDC for Model 100 and Model 130
Tipical value is from 4700uF to 10.000uF
Fuses are required on both the primary and secondary of the transformer to protect against harm to
the system and the transformer itself. They need to be of the slow blow type to handle current in-rush
atpower-up. Locate theprimary fuse (F1)onthe hot legof theAC input powerandthe secondary fuse
(F2) on the + side of the secondary output, before the rectifier.
Primary of the transformer: Use the formula below to calculate the correct values:
Secondary of the transformer: Use the table below
Power supply construction (continue)
FUSE F2 (A) SIZE Drive (A)
5 2/4
8 4/8
12 7/14
16 10/20
This manual suits for next models
4
Table of contents
Popular Servo Drive manuals by other brands
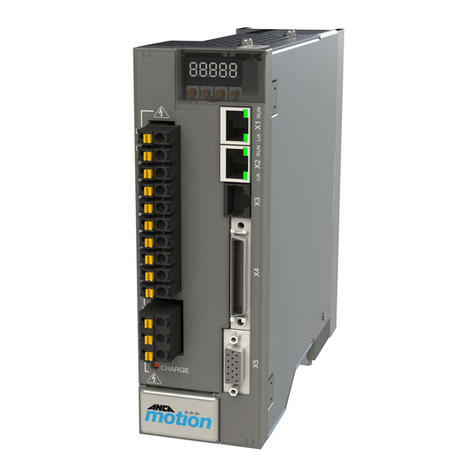
ANCA Motion
ANCA Motion AMD2000 Series user manual

Siemens
Siemens SINAMICS S200 Compact operating instructions
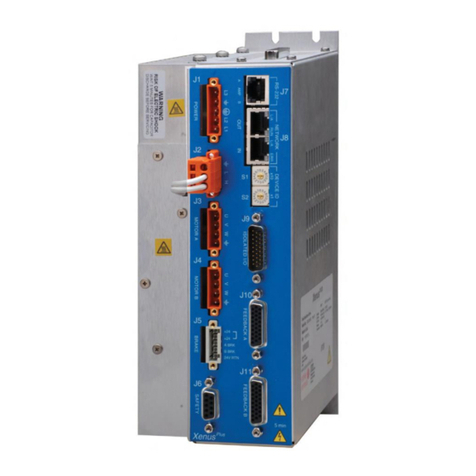
Copley Controls
Copley Controls Xenus Plus Series user guide
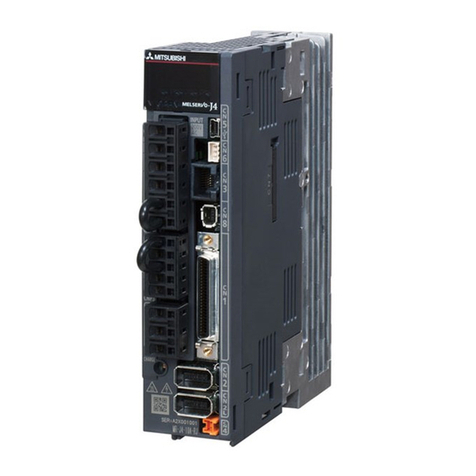
Mitsubishi Electric
Mitsubishi Electric MELSERVO MR-J4-B Series instruction manual
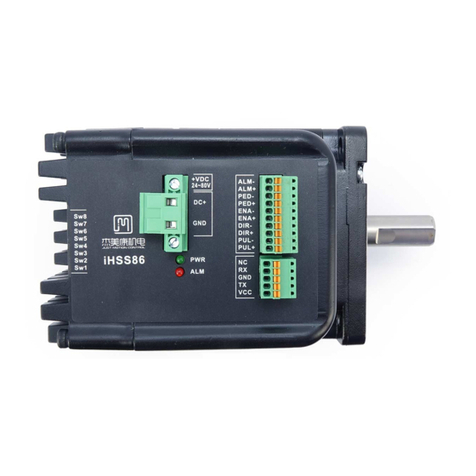
Just Motion Control
Just Motion Control iHSS86 Series user manual
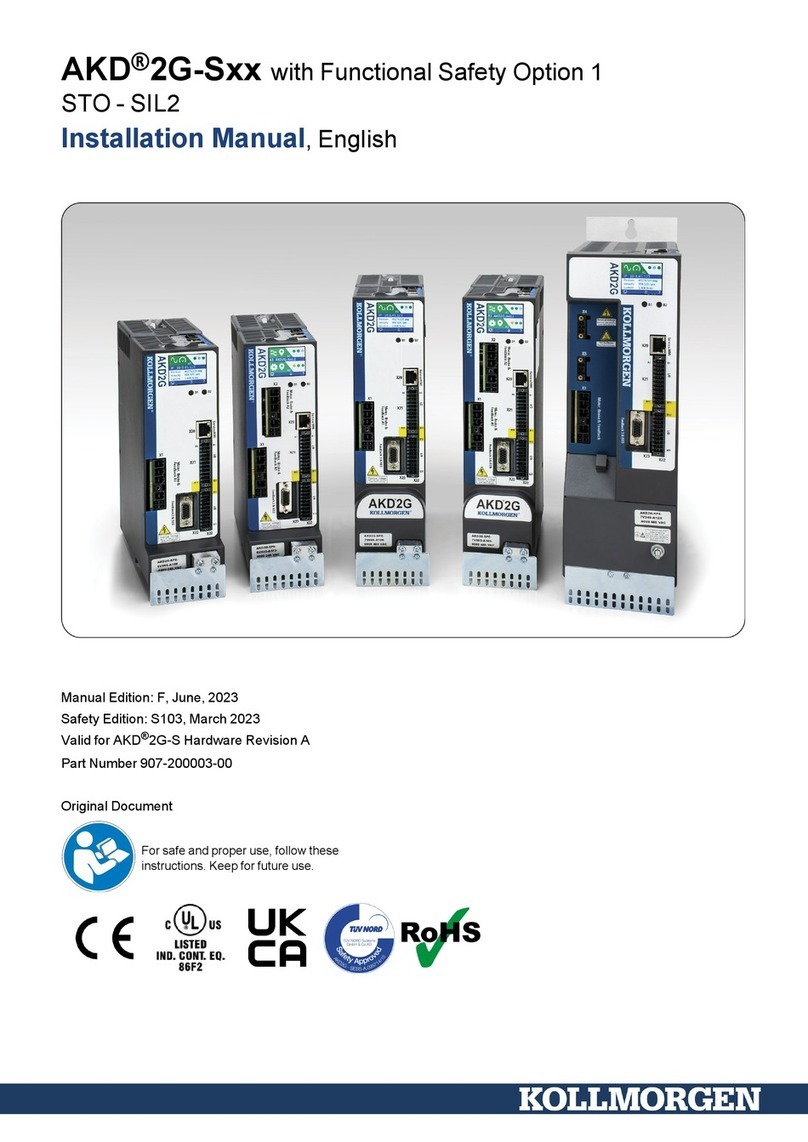
Kollmorgen
Kollmorgen AKD2G-S Series installation manual