Sensia CLIF MOCK LGS-1 Instruction manual

Manual No. 9A-99104500147, Rev. 02
MEASUREMENT
CLIF MOCK™
LGS-1 Liquid and Gas
Sample Pump
Installation, Operation & Maintenance Manual
MODEL: LGS-1

LGS-1 Liquid and Gas Sample Pump
2
Page Left Intentionally Blank

3
Important Safety Information
Terms Used in This Manual
Caution
Caution, risk of electric shock
Attention
Attention, risque d'électrocution
WARNING
A warning identifies information about practices or circumstances
that can lead to personal injury or death, property damage, or
economic loss.
AVERTISSEMENT
Un avertissement identifie des informations sur des pratiques ou
des circonstances pouvant entraîner des blessures corporelles ou
la mort, des dommages matériels ou des pertes économiques.
Caution
Caution statements Indicate actions or procedures which, if not
performed correctly, may lead to personal injury or incorrect function of
the instrument or connected equipment.
Attention
Indiquez les actions ou les procédures qui, si elles ne sont pas
effectuées correctement, peuvent entraîner des blessures ou un
mauvais fonctionnement de l'instrument ou de l'équipement connecté.
Note
Indicates additional information about specific conditions or
circumstances that may affect instrument operation.
Remarque
Indique des informations supplémentaires sur des conditions ou des
circonstances spécifiques pouvant affecter le fonctionnement de
l'instrument.
REVISION HISTORY
REVISION:
DESCRIPTION OF CHANGE:
ISSUER:
APPROVER:
DATE:
1
Initial Release
AK
TMM
January 2011
2
Branding Update
AK
TMM
September
2020

LGS-1 Liquid and Gas Sample Pump
4
Table of Contents
Section 1: LGS-1 Sample Pump Overview..................................................................................6
Description......................................................................................................................................................... 6
Section 2: Specifications..............................................................................................................7
Sample Specification......................................................................................................................................... 7
Sample Size....................................................................................................................................................... 7
Section 3: LGS-1 Sample Pump Installation ...............................................................................8
Air Supply .......................................................................................................................................................... 8
Inline Filter ......................................................................................................................................................... 8
Tubing Connections........................................................................................................................................... 9
Remote Mount Considerations.......................................................................................................................... 9
Fast Loop Considerations................................................................................................................................ 10
Sample Pump Connections............................................................................................................................. 10
Section 4: Setting Sample Size..................................................................................................11
Liquid Service .................................................................................................................................................. 11
Gas Service ..................................................................................................................................................... 11
Section 5: LGS-1 Sample Pump Maintenance...........................................................................13
Sample Pump Components............................................................................................................................. 13
Troubleshooting............................................................................................................................................... 13
Components .................................................................................................................................................... 13
Sample Pump Disassembly............................................................................................................................. 15
Required Tools ................................................................................................................................................ 15
Sample Pump Disassembly............................................................................................................................. 15
Housing Disassembly................................................................................................................................ 16
End Cap Disassembly ............................................................................................................................... 16
Inlet Body Disassembly............................................................................................................................. 16
Purge Valve Disassembly.......................................................................................................................... 17
Sample Pump Assembly.................................................................................................................................. 17
Purge Valve Assembly .............................................................................................................................. 17
Inlet Body Assembly.................................................................................................................................. 18
End Cap Assembly.................................................................................................................................... 18
Housing Assembly..................................................................................................................................... 19
Section 6: Spare Parts List.........................................................................................................20
Appendix A: Publisher Notes.....................................................................................................24
Support ............................................................................................................................................................ 24
Disclaimer........................................................................................................................................................ 24
Contact us........................................................................................................................................................ 26

5
GENERAL
WARNING!
To avoid the risk of electric shock and fire, the following safety instructions must be
observed and the guidelines followed.
The specifications must not be exceeded, and the device must only be applied as
described in the following.
Prior to the installation and commissioning of the unit, the installation guide must be
examined carefully.
If the equipment is used in a manner not specified by the manufacturer, the protection
provided by the equipment may be impaired.
GENERAL
AVERTISSEMENT!
Pour éviter tout risque de choc électrique et d'incendie, les consignes de sécurité de ce
manuel doivent être observées, et les instructions suivies.
Les spécifications ne doivent pas être dépassées, et l'unité ne doit être appliquée que
comme décrit dans le texte suivant.
Ce manuel doit être examiné avec soin, avant l'installation et la mise en service de
l'unité.
Si l'équipement est utilisé d'une manière non spécifiée par le fabricant, la protection
assurée par l'équipement peut être altérée.
INSTALLATION
WARNING!
Installation may only be carried out by electrically skilled and instructed personnel in
accordance with national legislation, including the relevant standards.
All technical data on the instrument is to be observed.
Changes to the design and modifications to the equipment are not permitted.
The equipment shall only be operated as intended and only in undamaged and perfect
condition.
Sufficient segregation must exist between different cables and wires carrying different
types of signal or power and all other circuits.
All wires must be terminated, complete with crimping lugs. Unused cores should be
terminated to the earth bus bar.
INSTALLATION
AVERTISSEMENT!
L’installation ne peut être effectuée que par un électricien qualifié, conformément à la
législation nationale, y compris les normes pertinentes.
Toutes les données techniques sur l'instrument doivent être observées.
Modifications de l'équipement ne sont pas autorisés.
L'équipement ne doit être utilisé comme prévu par le fabriquant et uniquement si il est
en parfait état.
Une séparation suffisante doit exister entre les différents câbles et les fils transportant
différents types de signaux ou de puissance et tous les autres circuits.
Tous les fils doivent être terminés, avec pattes de sertissage. Les noyaux non-utilisés
doivent être terminés au jeu de barres de la terre.

LGS-1 Liquid and Gas Sample Pump
6
Section 1: LGS-1 Sample Pump Overview
DESCRIPTION
The LGS-1 Sample Pump is a pneumatically operated positive displacement pump designed to transfer
samples of liquid or gas into a vented sample receiver or into a pressurized cylinder.
The sampling cycle begins with a signal being sent from the controller circuitry to the solenoid which diverts
instrument or plant air to the sample pump drive piston. When the piston is actuated, pipeline pressure
opens the inlet check valve, allowing pipeline fluid to enter through the inlet of the sample pump and collect
in the sample chamber until the sample chamber attains pipeline pressure. Once pipeline pressure is
reached inside the sample chamber, the inlet check valve closes, sealing the sample chamber from the
pipeline. The fluid sample remains contained inside the sample chamber until the sample pump is cycled.
When the sample pump cycles, the fluid contained in the sample chamber is evacuated through the outlet
valve into the sample receiver. Upon completion of one full sampling cycle, the pipeline fluid is once again
allowed to enter the sample chamber, thus the process repeats itself.
When the pump piston is in the retracted position, the inlet check valve is held open by pipeline pressure.
The outlet check valve is held closed. This condition prevents the sample pump from filling the sample
receiver while the sample chamber fills with the next sample volume.

Section 2: Specifications
7
Section 2: Specifications
SAMPLE SPECIFICATION
SAMPLE MEDIA
Fluid Viscosity Range
100 centistokes maximum
Fluid Temperature Range
-15° to 375°F (-26° to 190°C)
Maximum Particulate Size
0.005 in.
Fluid Flowing Pressure
30 to 1500 psi with 125 psi feed pressure
SAMPLE PUMP
Maximum Supply Pressure to Sample Pump
150 psi
Minimum Operational Cycle Time
5 seconds
Liquid Sample Size Range
0.25 cc to 1.25 cc
Gas Sample Size Range
0.05 cc to 1.00 cc
SAMPLE SIZE
The sample size is set by adjusting the knob on top of the pump See “Setting the Sample Size” section, for
step-by-step instructions.
The sample pump is adjustable for sample volumes ranging from .05 cc to 1.00 cc for gas applications and
0.25 cc to 1.25 cc for liquid applications. The default factory setting for sample size is 0.5 cc at 300 psi using
gas. Calibration is available when operating conditions are supplied by the customer. If an application
requires sample volumes outside the standard ranges, contact Sensia.

LGS-1 Liquid and Gas Sample Pump
8
Section 3: LGS-1 Sample Pump Installation
AIR SUPPLY
The LGS-1 sample pump is actuated by an air supply. In gas applications, the line pressure is often sufficient
to actuate the pump. But in liquid applications and some low-pressure gas applications, air must be supplied
externally. The pipeline pressure of the fluid to be sampled determines the minimum air pressure required to
actuate the pump. It is the customer’s responsibility to provide an air supply that is powerful enough to meet
this requirement for any given application.
The chart in Figure 1 can be used to determine the air pressure requirement for a broad range of pipeline
pressures.
Figure 1: Pump actuation (air) pressure chart
INLINE FILTER
Use of an in-line filter between the probe and sample pump is recommended for optimum sampling
performance. The purge valve manifold at the bottom of the sample pump, see Figure 2, is designed with a
recess to accept a ½-in. OD basket filter. A 40-micron filter is supplied as standard; other sizes are available
upon request. To install a filter, insert it in the bottom inlet of the purge valve manifold before connecting the
sample probe to the sample pump.
0
200
400
600
800
1000
1200
1400
1600
0
40
50
60
70
80
90
100
110
120
125
Pipeline Pressure (psi)
Air Pressure (psi)
Actuation Pressure
Actuation
Pressure

Section 3: LGS-1 Sample Pump Installation
9
Figure 2: Pump actuation (air) pressure chart
TUBING CONNECTIONS
Tubing arrangements will vary, depending on the product sampled (gas or liquid). At a minimum, ¼-in.
stainless steel tubing will be required to connect the air supply from the controller to the sample pump.
A ¼-in. capped port is provided on the sample discharge outlet for connecting sample flow to a receiver.
Figure 3: Pump actuation (air) pressure chart
REMOTE MOUNT CONSIDERATIONS
In remote-mount installations, tubing is required for connecting the sample probe to the purge valve manifold
on the sample pump. When the controller is pipe-mounted, tubing should be sloped between the sample
probe and the sample pump to prevent a water trap. The tubing between the sample probe and the sample
pump should be as short as possible and should be insulated if extreme weather conditions exist.

LGS-1 Liquid and Gas Sample Pump
10
FAST LOOP CONSIDERATIONS
Under some flow conditions, a fast loop plumbing arrangement may be preferred to ensure that only fresh
liquid flow is sampled. This configuration requires an orifice plate, flow straightener, or other flow obstruction
in the pipeline to cause a small differential pressure to ensure that the sample probe collects fresh fluid with
each sample grab. The fast loop should be as short as possible and should be constructed with ¼-in.
stainless steel tubing. The fast loop itself cannot have any device or obstruction which could cause
significant pressure to drop. The fast loop should be insulated if extreme weather conditions exist.
SAMPLE PUMP CONNECTIONS
Install tubing to make the following connections to the sample pump, using Figure 4 for reference.
1. Connect the sample probe to the sample inlet (if sampler is mounted remotely mounted from sample
probe).
2. Connect the sample outlet to the sample receiver.
3. Connect the air output to the actuation pressure port of the pump. This supplies air pressure to actuate
the pump.
4. If a fast loop piping configuration will be used, connect the reinjection line fitting in the side of the purge
valve manifold, see Figure 4, to the low-pressure side of the orifice fitting in the pipeline.
5. Cover the vent hole in the side of the pump with 1/16-17 NPT screen, if necessary, to prevent build-up of
debris in the hole.
Figure 4: Pump tubing connections; note the orientation of the images above with reference to the shutoff
valve (the photo at right is rotated 90 degrees clockwise from position shown on left)

Section 4: Setting Sample Size
11
Section 4: Setting Sample Size
Sample size is set by adjusting the knob at the top of the sample pump to a predetermined height (“h”) above
the flat surface of the pump. The height measurement required directly corresponds to the sample size
desired. Charts for determining corresponding height measurements for liquid and gas samples are provided
on a laminated Sample Setting card that is stored inside the controller enclosure. The laminated card, shown
in Figure 5, also includes a ruler for measuring the adjustment height.
Figure 5: Laminated sample size card for adjusting sample size in the field
LIQUID SERVICE
To set the sample size for liquid sampling, perform the following steps:
1. Use the laminated Sample Setting card, see Figure 5, come with the sample controller and locate the
appropriate chart for liquid or gas sample size.
2. Loosen the adjustment lock nut.
3. Locate the desired sample size in the “CC” column of the Liquid Measurement chart and note the
corresponding height (h) value.
4. Hold the card so that the zero point aligns with the flat surface of the pump and turn the adjustment knob
until its top is in line with the height measurement determined in step 3.
5. Tighten the adjustment lock nut.
GAS SERVICE
To set the sample size for gas sampling, perform the following steps:
1. Loosen the adjustment lock nut.

LGS-1 Liquid and Gas Sample Pump
12
2. Locate the desired line pressure in the chart “CC” column of the Gas Measurement chart and note the
corresponding height (h) value. Find the value (h) that corresponds to the desired sample size and line
pressure.
3. Turn the adjustment knob until the desired height (h) is obtained.
4. Tighten the adjustment lock nut.
Due to the compressible nature of gas, slight adjustments may be required after initial installation to fine tune
the sample pump based on the sampling requirements.

Section 5: LGS-1 Sample Pump Maintenance
13
Section 5: LGS-1 Sample Pump Maintenance
SAMPLE PUMP COMPONENTS
Refer to Figures 6 and 7 as well as Tables 1 and 2 when performing the procedures in this section.
The pump is essentially maintenance-free. Change O-rings annually under routine operating conditions. If
operating in a severe environment, inspect O-rings more frequently and replace, as necessary.
Caution
O-rings are a very fragile and integral part of the assembly. Always
handle O-rings with extreme care to avoid slicing, extruding (force),
tearing, or rolling an O-ring. Any damage to the O-ring will result in a
loss of its sealing ability.
TROUBLESHOOTING
Leaks are the most common cause of pump failure. If sample pressure fails to build during operation,
disassemble the pump and visually observe the inner components. Replace O-rings, and if other
components show signs of excessive wear, consider overhauling the pump. See the Spare Parts list in
Section 6, for kits that contain all necessary replacement parts.
COMPONENTS
Figure 6: Sample pump components
Table 1: Sample Pump Components
Item
Description
Qty.
1
#10-32NF x 1/4" SOC SET SCREW
1
2
NUT, JAM, 7/16-20NC STD. SS
1
3
WASHER, FLAT, 7/16 STD. SS
1
4
END CAP, LGS-1
1
5
HOUSING LGS-1
1
6*
O-RING #218 VITON (REF: PISTON)
1
7**
SPRING, COMPRESSION, LGS-1
1
8
RETAINING RING, INTERNAL
1

LGS-1 Liquid and Gas Sample Pump
14
9
RING, RETAINING K-2 300-62-SS2
1
10*
O-RING #011 VITON
1
11
POPPET, CHECK, LGS-1
1
12
BODY INLET, LGS-1
1
13*
O-RING, VITON, #008
1
14
SEAT, LGS-1
1
15**
SPRING, COMPRESSION CHECK, LGS-1
1
16
RETAINING RING, EXTERNAL
1
17
RETAINER, FILTER BASKET
1
18**
SPRING, SEAT, COMPRESSION, LGS-1
1
19
GUIDE, CHECK SPRING
1
20*
O-RING, VITON, #110
1
21
#8-32NCx3.5" LG. SHCS, SST
4
22**
O-RING, VITON, #016
1
23**
SAMPLE CHAMBER ASSY, LGS-1
1
24*
RING, BACK-UP, TELFON, #011
2
25
RETAINER, O-RING, SAMPLE CHAMBER
1
26
PISTON ROD ASSY, LGS-1
1
27*
O-RING, #125, VITON
1
28*
O-RING #116 VITON
1
29
PISTON, STROKE ADJUSTMENT
1
30
SCREW, SOCKET HD CAP 8-32 X 1 SS
4
31
SCREW, ADJUSTING LGS-1
1
32
KNOB, ADJUSTMENT LGS-1
1
33*
O-RING, VITON, #007
1
34*
O-RING, BUNA-N, #017
1
35
VALVE, PURGE LGS-1
1
36
FILTER, (OPTIONAL)
1
* These items are contained in the Seal Kit listed in the Spare Parts list.
** These items plus the Seal Kit items are contained in the Overhaul Kit listed in the Spare Parts list.
Figure 7: Purge valve manifold components

Section 5: LGS-1 Sample Pump Maintenance
15
Table 2: Purge Valve Assembly Components
Item
Description
Qty.
1
VALVE, PURGE
1
2
SEAT, VALVE LGS MANIFOLD
1
3
NUT, BONNET LGS MANIFOLD
1
4*
O-RING, BUNA-N #013
1
5*
O-RING, VITON #007
1
6
STEM, VALVE LGS MANIFOLD
1
7
HANDLE, VALVE LGS MANIFOLD
1
8
SCREW, FILISTER HD SLT 8-32 X 5/16 SS
1
* These items are contained in the Seal Kit listed in the Spare Parts list.
SAMPLE PUMP DISASSEMBLY
Caution
Prior to disassembling the sample pump, remove pipeline pressure from
the pump and cycle the pump several times to evacuate any gases that
may be trapped in the sample chamber. Attempts to disassemble the
pump without venting the sample chamber can result in bodily injury.
The following instructions reference item numbers that correspond to the numbers displayed in Figures 6
and 7 as well as Tables 1 and 2. Reference these cutaway illustrations and tables frequently during sample
pump disassembly.
REQUIRED TOOLS
The LGS-1 pump can be completely disassembled with a few simple hand tools. An Allen wrench, snap ring
pliers, a small adjustable wrench (for removing the valve body on the purge valve), a flat punch, and a flat
screwdriver are recommended.
SAMPLE PUMP DISASSEMBLY
Prior to total disassembly of the pump, perform the following steps:
1. Loosen the nut (item #2) and back the adjustment screw (item #31) all the way out till it stops. This will
reduce the spring return load to minimum.
2. Loosen the four (4) screws (item #21) 2 complete turns (do not over-loosen the screws). After the screws
are loosened, the housing (item #5), the inlet body (item #12), and the purge valve (item #35) will
separate slightly due to spring load.
3. Using your hands, grasp the housing and inlet body and push them together. There should only be a
slight resistance of approximately 4 to 5 pounds required to bring the housing and inlet body in contact
again.
Caution
If you cannot bring the two parts in contact using minimal hand force, the
sample chamber could contain trapped gases; retighten the four screws
hand-tight and recycle the pump several times again, then repeat the
procedure above. Never—under any circumstance—continue to
disassemble the pump if pressure is retained in the sample chamber.

LGS-1 Liquid and Gas Sample Pump
16
Bodily injury could result. If you cannot evacuate the sample chamber
gases after repeated attempts, contact Sensia for further instruction.
HOUSING DISASSEMBLY
1. To continue disassembly of the pump, remove the four (4) screws (item #21) from the purge valve (item
#35). Hand pressure should be applied to the inlet body and the purge valve to hold them in place as the
screws are removed to offset the force created by the compression spring (item #7) so the pump does
not suddenly burst apart.
2. Slide the inlet body and purge valve straight off the piston rod and remove the compression spring (item
#7). Do not remove the piston assembly (item #26) from the inlet body (item #12) side of the housing
(item #5). Removal from this direction would require passing the piston O-ring over the vent hole in the
housing which could cut the O-ring.
3. Remove the four (4) screws (item #30) from the end cap (item #4) and slide the end cap out of the
housing.
4. Remove the piston assembly (item #26) from the end cap side of the housing. Do not remove the piston
assembly from the inlet body side of the housing. Removal from this direction could cut the piston O-ring
as it passes over the vent hole in the housing.
5. Remove the O-ring (item #6) from the piston assembly.
END CAP DISASSEMBLY
1. Remove O-ring (item #27) from the end cap.
2. To remove the stroke adjustment (item #29) requires removal of the nut (item #2) and washer (item #3).
a. Remove the set screw (item #1).
b. Remove the adjustment knob (item #32).
c. Remove the nut and washer.
d. Replace the adjustment knob on the adjustment screw.
e. Replace the set screw and retighten.
3. Rotate the adjustment knob clockwise until the stroke adjustment completely extends beyond the end
cap.
4. Remove the stroke adjustment from the adjustment screw.
5. Remove the adjustment screw from the end cap.
6. Remove the O-ring (item #28) located inside the end cap.
7. Remove the set screw from the adjustment knob.
8. Remove the adjustment knob from the adjustment screw.
INLET BODY DISASSEMBLY
1. Remove O-ring (item #34).
2. Remove O-ring (item #33).
3. Remove the internal retaining ring (item #8).

Section 5: LGS-1 Sample Pump Maintenance
17
4. Carefully remove the sample chamber assembly (item #23) and the seat assembly from the inlet body.
a. To accomplish this, use a flat punch and gently apply pressure to the check poppet (item #11) stem.
b. Slowly push the two assemblies through the inlet body until the O-ring (item #22) clears the bore.
c. Once the O-ring clears the bore the two assemblies can be easily removed from the inlet body by gently
dumping them in your hand.
5. Remove the internal retaining ring (item #9) from the sample chamber assembly.
6. To remove the O-ring retainer (item #25) from the sample chamber assembly, hold the sample chamber
assembly so the O-ring retainer is facing down and very gently tap the sample chamber assembly against a
hard-clean surface.
7. Remove the back-up ring (item #24) and O-ring (item #10) from the sample chamber assembly.
8. Remove O-ring (item #22).
9. Disassemble the seat assembly as follows:
a. Carefully remove the external retaining ring (item #16) from the check poppet (item #11).
b. Remove the compression spring (item #15).
c. Remove the check poppet.
d. Remove O-ring (item #13) from the check poppet.
e. Remove O-ring (item #20) from the seat (item #14).
10. Disassembly of the sample pump is complete.
PURGE VALVE DISASSEMBLY
1. Remove the purge valve assembly (item #35) from the inlet body (item #12).
2. Remove the compression spring (item #18).
3. Remove the filter basket retainer (item #17) from the purge valve assembly (item #35).
4. Remove the bonnet nut (item #3*) from the purge valve (item #1*).
5. Remove the seat (item #2*) from the purge valve (item #1*).
6. Remove the screw (item #8*) and the handle (item #7*) from the stem (item #6*).
7. Remove the stem (item #6*) from the bonnet nut (item #3*).
8. Remove O-rings (item #4* & item #5*).
SAMPLE PUMP ASSEMBLY
The following instructions reference item numbers that correspond to the numbers displayed in Figure 6 and
7 as well as Tables 1 and 2. Reference these cutaway illustrations and tables frequently during sample pump
assembly.
PURGE VALVE ASSEMBLY
1. Place O-ring (item #5*) on the stem (item #6).
2. Place O-ring (item #4*) on the bonnet nut (item #3*).
3. Install stem (item #6*) into the bonnet nut (item #3*).

LGS-1 Liquid and Gas Sample Pump
18
4. Install the seat (item #2*) into the purge valve (item #1*).
5. Install the bonnet nut (item #3*) into the purge valve (item #1*).
6. Install the handle (item #7*) and the screw (item #8*) to the stem (item #6*).
7. Install the filter (item #36**) into the purge valve assembly (item #36).
8. Install the retainer (item #17) into the purge valve assembly (item #36).
*See Purge Valve diagram for these item numbers.
**Optional.
INLET BODY ASSEMBLY
1. Place O-ring (item #20) on the seat (item #14).
2. Place O-ring (item #13) on the check poppet (item #11).
3. Place the check poppet in the seat.
4. Install the compression spring (item #15) over the stem of the check poppet.
5. Carefully replace the external retaining ring (item #16) over the check poppet (item #11).
6. Install O-ring (item #22) onto the sample chamber (item #23).
7. Insert the O-ring (item #10) and back-up ring (item #24) into the sample chamber assembly.
8. Replace the O-ring retainer (item #25) in the sample chamber assembly.
9. Install the internal retaining ring (item #9) in the sample chamber assembly.
10. Replace the seat assembly and sample chamber assembly into the inlet body.
a. First, place the seat assembly into the inlet body and use your finger to gently push it all the way in until
it bottoms inside the body.
b. Insert the sample chamber assembly into the inlet body until it bottoms.
11. Install the internal retaining ring (item #8).
12. Install O-ring (item #34).
END CAP ASSEMBLY
1. Install the O-ring (item #28) located inside the end cap.
2. Install the adjustment knob (item #32) on to the adjustment screw (item #31).
3. Install the setscrew (item #1) in the adjustment knob.
4. Install the adjustment screw in the end cap and thread all the way in until the groove end of the adjustment
screw clears the opposite end of the end cap.
5. Install the stroke adjustment (item #29) on the adjustment screw.
6. Rotate the adjustment knob counterclockwise until the stroke adjustment is completely retracted inside the
end cap.

Section 5: LGS-1 Sample Pump Maintenance
19
7. Remove the set screw and adjustment knob to place the washer (item #3) and nut (item #2) on the
adjustment screw. Replace the set screw and adjustment knob on to the adjustment screw.
8. Install O-ring (item #27) on to the end cap.
HOUSING ASSEMBLY
1. Install the O-ring (item #6) on the piston assembly.
2. Install the piston assembly (item #26) from the end cap side (grooved end) of the housing (item #5). Do not
install the piston assembly from the inlet body side of the housing. Installation from this direction could cut
the piston O-ring as it passes over the vent hole in the housing.
3. Slide the end cap inside the housing and install the four (4) screws (item #30). Hand-tighten only.
4. Install the compression spring (item #7) onto the piston assembly. Slide the inlet body straight on to the
piston rod. Be careful not to cut the piston rod O-ring (item #10) located inside the sample chamber
assembly.
5. Install the compression spring (item #18) between the inlet body (item #12) and the purge valve (item #35).
6. Install the O-ring (item #33).
7. Install the four (4) screws (item #21) on to the purge valve (item #35), through the inlet body (item #12), and
into the housing, such that the purge valve’s (item #35) handle is in line with the sample out port on the inlet
body (item #12). Hand-tighten the screws only. DO NOT OVERTIGHTEN THE SCREWS.

LGS-1 Liquid and Gas Sample Pump
20
Section 6: Spare Parts List
A seal kit and an overhaul kit provide all the parts required for maintenance of the LGS-1 sample pump. See
the table below for part numbers.
Table 3: LGS-1 Pump Spare Parts
Part Number
Description
9A-50142150715
Overhaul Kit (contains O-rings and springs for full overhaul of the LGS-1
pump)
9A-50142150708
Seal Kit (contains O-rings for the LGS-1 pump and purge valve manifold)
9A-50142200643
Filter, LGS-1, 40-micron
Table of contents
Popular Water Pump manuals by other brands
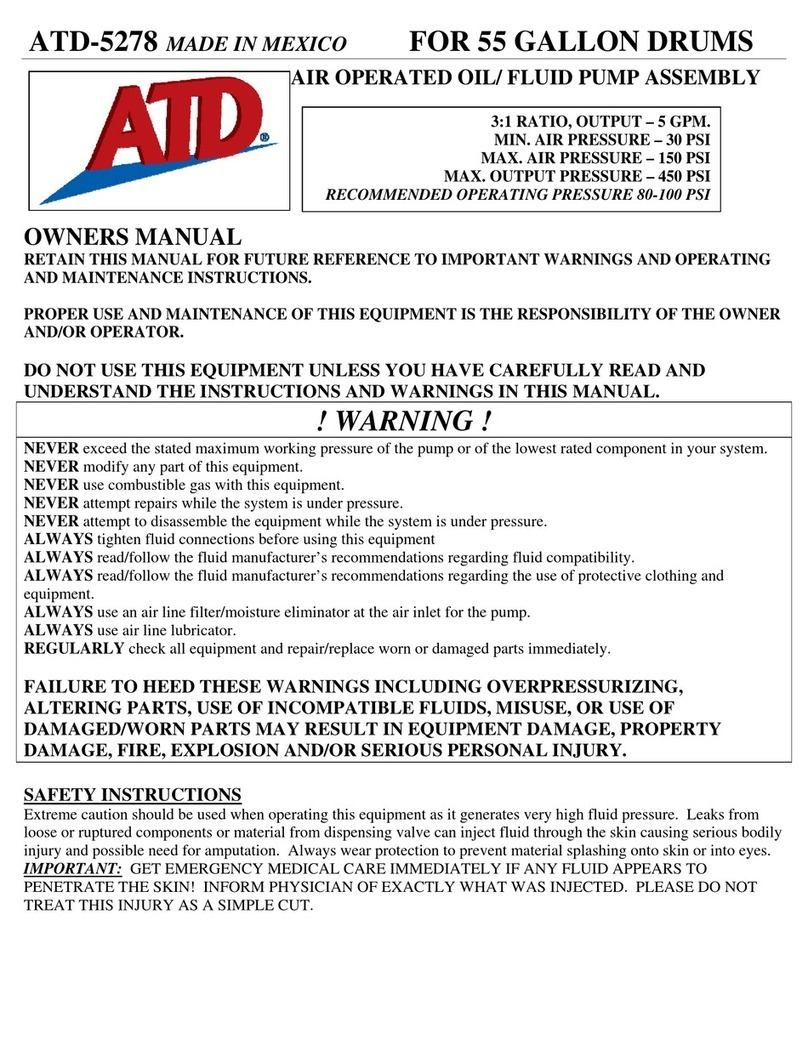
ATD Tools
ATD Tools ATD-5278 owner's manual
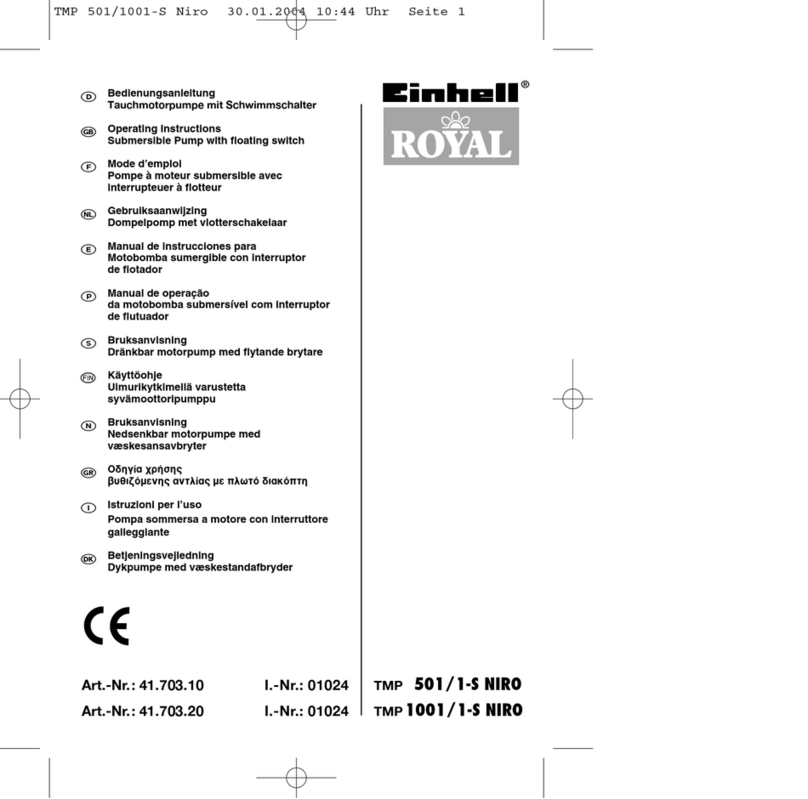
EINHELL
EINHELL ROYAL TMP 501/1-S NIRO operating instructions
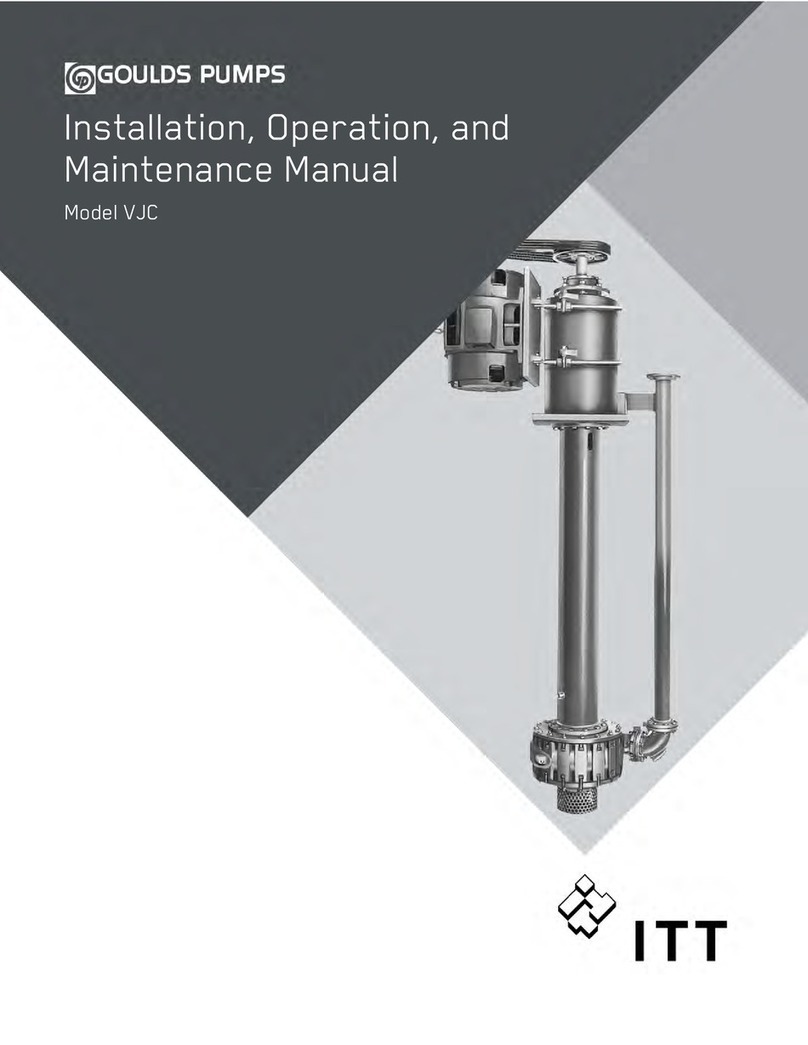
ITT
ITT VJC Installation, operation and maintenance manual
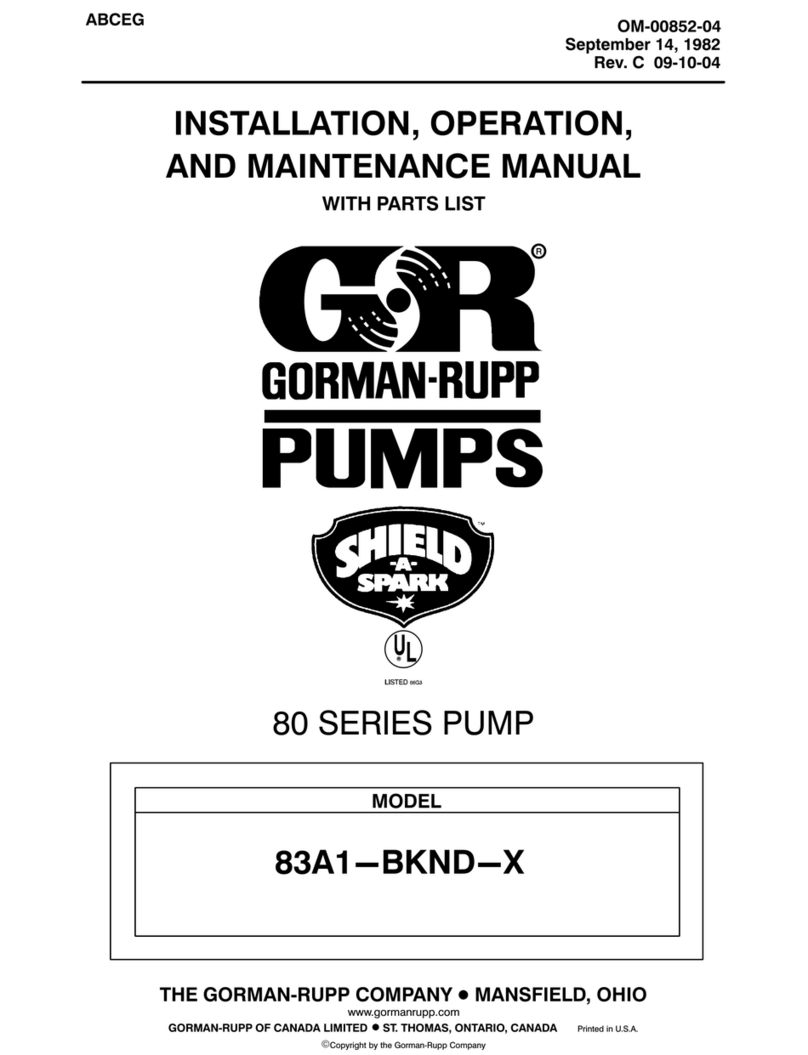
GORMAN-RUPP PUMPS
GORMAN-RUPP PUMPS Shield-A-Spark 80 Series Installation, operation, and maintenance manual with parts list
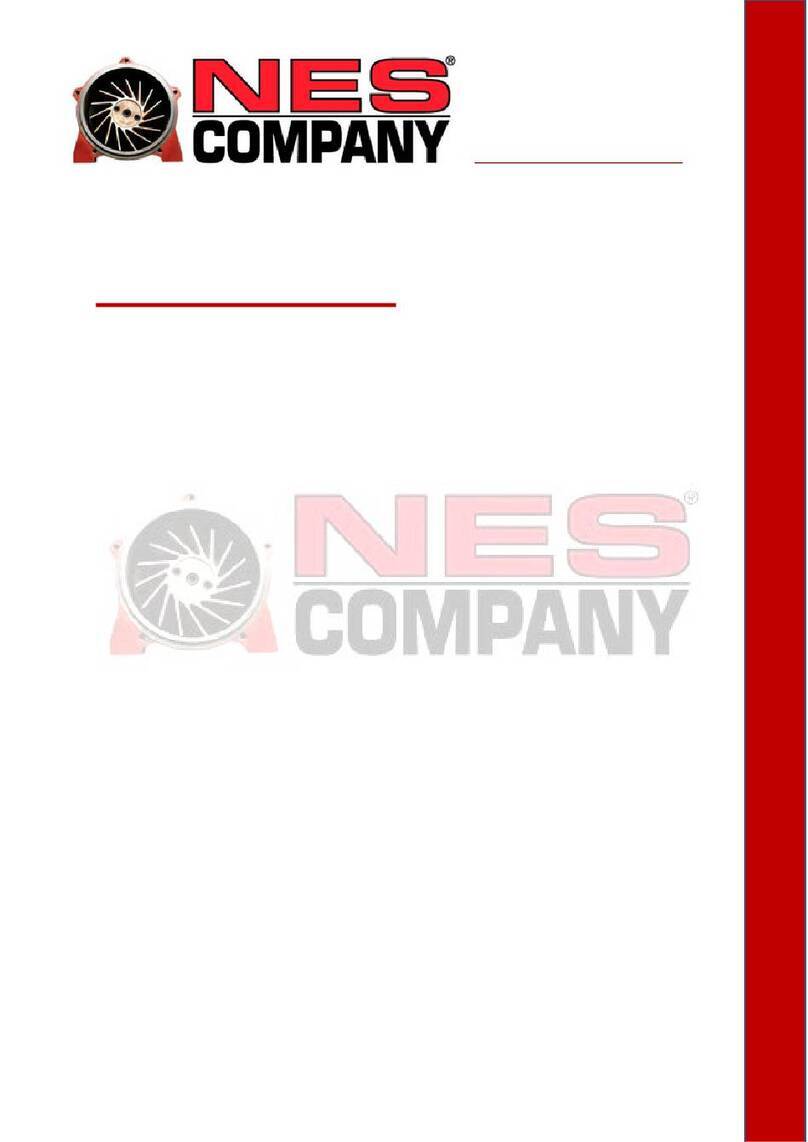
NES
NES NBE Series Operation & maintenance manual
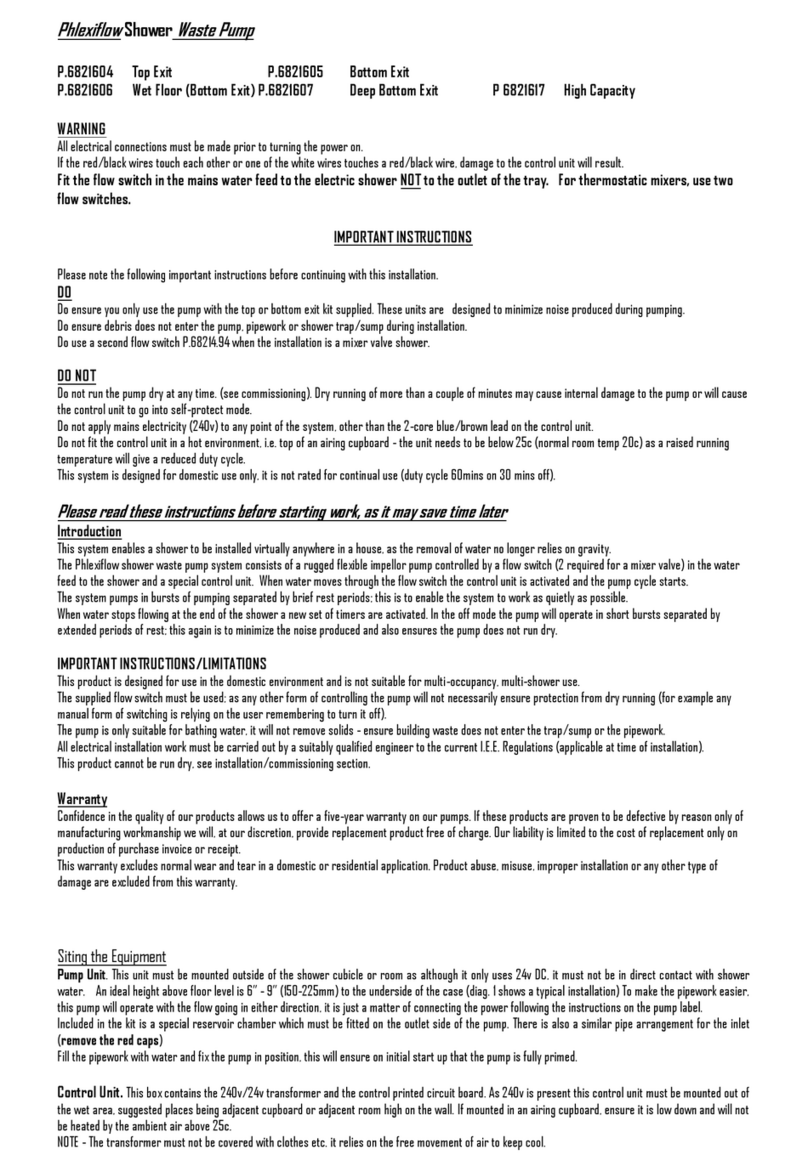
N&C Phlexicare
N&C Phlexicare Phlexiflow P.6821604 Important instructions