Sensus 461-S User manual

Models 461-S, 461-8S and 461-12S Regulators
Regulators
RM-1330 R7
Installation and
Maintenance Instructions
RM-1330 R8

3a 1a
3
D1
C
Inlet
Minimum
Service Space
D
4"
8" F
Bypass (if required)
Remote Vent (if required)
1" NPT
B
AControl Line
Connection
Control Line
1/4" NPT
Outlet
Vent Cap
3
E
Model D D1 E
461-12S 13-1/4" – 14"
461-8S – 18-3/8" 10-3/16"
461-S (12") – 19-1/2" 14-1/4"
461-S (8-1/2") – 19-1/2" 11"
Regulator Body Type F (Face to Face)
Screwed 6-1/2"
Flanged ANSI 125 FF 10"
Flanged ANSI 250 FF 10-1/2"
2
Maximum
Working
Regulator Body Pressure
Body Type Materials of Body
2" Screwed only Cast Iron 250 psi
Flanged ANSI 125 Cast Iron 175 psi*
Flanged ANSI 250 Ductile Iron 575 psi*
Flanged ANSI 300 Cast Steel 720 psi*
Maximum Inlet Pressures
Regulator Models 461-S, 461-8S, and 461-12S are excellent
general purpose gas pressure regulators for intermediate and
larger loads. Use them for natural gas, air, dry CO2, propane,
butane and other gases.
*Carefully note the following exceptions to the above,
based on diaphragm size:
Diaphragm Diaphragm Maximum Inlet
Size ID Case Material Pressure
12” Cast Iron 100 psi
8-1/2” Cast Iron 175 psi
12” Aluminum 100 psi
8” Aluminum 175 psi
Valve material selection is limited by inlet pressure and
differential:
Valve Maximum Inlet Maximum Pressure
Material Pressure Rating Differential Rating
Buna-N 575 psi 250 psi
Poly-U Red 720 psi 400 psi
Poly-U Tan 1200 psi 600 psi
Typical Arrangement
and Dimensions
(Indoor or Outdoor Installation)
Installation and Start-Up
1Thoroughly purge inlet piping to remove dirt and debris that could
damage the regulator or impair its operation. If this cannot be
done, a filter or strainer should be installed ahead of the regulator.
(see bulletin RDS-1498, Regulator Pressure Ratings).
Make certain that inside of the regulator and piping are free
of dirt, foreign matter, and other debris.
2Install the regulator. Make certain flow through the regulator is
in the correct direction. High pressure connects to the inlet
side. Be sure that shipping screens or covers, if used, are
removed.
On flanges, tighten bolts evenly. On screwed connections,
apply pipe dope to male threads only. Where required,
the regulator may be inverted.
CAUTION
It is the user's responsibility to assure that all regulator vents
and/or vent lines exhaust to a non-hazardous location away from
any potential sources of ignition. Where vent lines are used,
it is the user's responsibility to assure that each regulator is
individually vented and that common vent lines are not used.
3The vent connection is an escape path for flammable gas and
it must be located and/or piped so that potential discharge
occurs in a safe area away from buildings, open flames,
collection areas, arcing devices, etc.
Regulators that are installed indoors, or in a non-vented area
must be vented to the outside. Simply run vent piping from
the regulator vent connection to a non-hazardous location
on the outside away from any potential sources of ignition.
The vent piping must be connection size or larger and piped
to a safe area.
The outlet of the vent piping must allow for the free and
unobstructed passage of air and gas, and must be protected
against the potentials listed in instructions.
Installation and Maintenance Instructions
Model 461-S, 461-8S, and 461-12S Regulator

3
4For outdoor installation, it is recommended that the regulator
be installed so that the regulator vent faces downward to
avoid the potential of water or other foreign matter entering
the vent and interfering with the proper operation of the
regulator.
5Install the control line. It should be sturdy with adequate
protection against breakage (regulators go wide open if control
line is broken). Pitch it to drain away from the regulator, free of
moisture pockets. The control line should be no less than 1/4"
steel tubing or pipe for the 461-12S and 461-8S models and
1/2" steel pipe for the 461-S models.
The regulator will work to deliver the pressure(for which
it is adjusted) at that point in the piping where the control
connection is located.
In general, the control connection should be at least eight
pipe diameters downstream from the regulator and should be
in as straight a run as possible where turbulence is a minimum.
Keep clear of elbows, valves, and other causes of excessive
turbulence.
The control connection should be clean and smooth
inside the pipe to minimize turbulence. It should be located
on the top or side of the pipe, not on the bottom.Where outlet
piping increases in size near the regulator, it is generally
preferable to locate the connection in the larger size.
The unions for the control lines of the 461-S models contain a
small orifice (approximately 1/16" diameter). This orifice should
not be removed. Also, make certain it is open and free of foreign
material.
6Check all connections for leaks.
CAUTION
Turn gas on very slowly. If an outlet stop valve is used,
it should be opened first. Do not overload the diaphragm
with a sudden surge of inlet pressure. Monitor the outlet
pressure during start-up to prevent an outlet pressure overload.
7Put the regulator into operation as follows:
a. Slowly open downstream control line valve (A).
b. Slowly open downstream block valve (B).
c. Very slowly open upstream block valve (C).
d. When start-up and adjustment are completed,
make sure valves (A), (B), and (C) are fully opened.
See diagram page 2
8Set adjusting screw for the required outlet pressure. Turn it clock
wise to increase the pressure and counterclockwise to
decrease it. Only make the adjustment when gas is actually
flowing through the regulator.
Remove the seal cap and, if applicable, loosen locknut
to make adjustment.
After adjustment is complete, locknut (if applicable) should be
tightened firmly and seal cap replaced. The absence of this seal
cap can result in unstable operation.
9To shut down, carefully close valves (C), (B), and (A)
in that order.
CAUTION
1 Keep pipe dope and all other foreign substances
out of the control line.
2 Never install any type of automatic shut-off device,
which closes completely, between the regulator outlet
and the downstream control line connection.
3 The vent must be positioned to protect against flooding,
drain water, ice formation, traffic, tampering etc. The vent
must be protected against nest-building animals, bees,
insects, etc. to protect from vent blockage and minimize
the chances of foreign material collecting in the vent side
of the regulator diaphragm.
Servicing and Adjustment
General Notes
1Make sure the regulator is entirely depressured before
servicing.
2A quick visual inspection of the valve can be made by removing
inspection plates (33) from the sides of the body. These also
provide greatly improved access to the valve when servicing or
adjusting. Valve and body parts are interchangeable with other
model 461 regulators.
3Carefully note location and position of disassembled parts to
be certain reassembly is correct. Inspect each one carefully
and replace those that are worn or damaged or otherwise
unsatisfactory.
4Use lubricants sparingly and with care to avoid exposing
tacky surfaces to the gas stream. Such surfaces could cause
dirt accumulation on close-clearance parts.
Use moly or silicone type lubricants.
Avoid the use of petroleum base types.
It is best to avoid lubricating the stem or the guide.
However, a small amount of silicone spray release agent
to lubricate stem O-ring will help assure free movement and
a tight seal. An application of silicone base lubricant to the
other O-rings and the tetraseals in the regulator will also help
assure their tightness.
CAUTION
Regulators are pressure control devices with numerous
moving parts subject to wear that is dependent upon
particular operating conditions. To assure continuous
satisfactory operation, a periodic inspection schedule
must be adhered to with the frequency of inspection
determined by the severity of service and applicable laws
and regulations.
Installation and Maintenance Instructions
Model 461-S, 461-8S, and 461-12S Regulator

To Service Single Seat Balanced
Valve Assembly
1Remove seal cap 1, 1a or 1b. Mark or measure position
of adjustment 3or 3a. Use this to return adjustment to this
setting during reassembly.
On 461-12S remove adjustment 3and spring 9.
On 461-8S release adjustment 3a and remove cover 5,
button 7a, and spring 9.
On 461-S release adjustment 3a and remove cover 8,
button 7b, and spring 9.
2Remove bottom inspection plate 14.
3Remove locknut 12e, then slip off valve 12d and retainer 12c.
Orifice 18 can be removed with socket wrench (1-1/2" hex
deep socket.) Reassemble in reverse order.
4If it should be necessary to remove stem 12b or valve guide
30, do so by first removing lower diaphragm case 24
(steps 2 through 7 under “To Service Diaphragm” below).
Use socket wrench for 30 (1-1/2” hex deep socket).
5Note – single seat balanced valve does not require
any lock-up adjustment.
6Note : orifice 18 must be same size as stem guide 30
(1” 18 with 1” 30 and 11/16” 18 with 11/16” 30).
Do not use 11/16” size of one with 1” size of the other.
7Replace bottom inspection plate 14.
8Replace parts removed under Step 1 above and return
adjustment to original setting.
To Change Spring
1Remove seal cap 1, 1a or 1b.
On 461-12S remove adjustment 3and spring 9.
On 461-8S release adjustment 3a and remove cover 5,
button 7a, and spring 9.
On 461-S release adjustment 3a and remove cover 8
button 7b, and spring 9.
2Insert the new spring. Be sure it nests correctly onto part 11b.
3Replace remaining parts removed under Step 1.
To Service Diaphragm
1Remove seal cap 1, 1a or 1b. Mark or measure position
of adjustment 3or 3a. Use this to return adjustment to this
setting during assembly.
On 461-12S remove adjustment 3and spring 9.
On 461-8S release adjustment 3a and remove cover 5,
button 7a, and spring 9.
On 461-S release adjustment 3a and remove cover 8,
button 7b, and spring 9.
2Remove bolts 22 and then carefully remove upper
diaphragm case 21.
3Turn diaphragm assembly counterclockwise
(this unscrews 11h from 12b) and remove.
4
To Service Double Seat Balanced
Valve Assembly
1Remove seal cap 1, 1a, or 1b. Mark or measure position of
adjustment 3or 3a. Use this to return adjustment to setting
during reassembly.
On 461-12S remove adjustment 3and spring 9.
On 461-8S release adjustment 3a and remove cover 5,
button 7a, and spring 9.
On 461-S release adjustment 3a and remove cover 8,
button 7b, and spring 9.
2Remove bottom inspection plate 14, and unscrew valve
assembly intact from diaphragm assembly
(12b unscrews from 11h).
3Unscrew orifice 18 with socket wrench (1-1/2" hex deep
socket). Remove orifice 18 and valve assembly intact through
bottom opening.
4If valve assembly does not require changes, replace without
disturbing set screw 12g (top end of 12b screws onto 11h)
until it bottoms and should then be backed off 1/2 turn to 1
full turn).
5If new parts are needed, disassemble valve assembly by
loosening set screw 12g and unscrewing 12h from 12b,
and then unscrewing nut 12e and part 12j.
6Replace parts as required, then reassemble upper half valve
assembly (parts 12a, 12b, 12c, 12d, 12e) and lower half
(parts 12f, 12g, 12h, 12c, 12d, 12j).
7Insert through bottom opening:
a. upper half valve assembly – screw 12b onto 11h until it
bottoms, then back off 1/2 to 1 full turn.
b. orifice 18 – screw firmly into place.
c. lower half valve assembly – screw onto upper half by
3 or 4 turns (12h screws onto 12b).
8Make the valve lock-up adjustment. Seat the upper valve
against orifice 19 while screwing up the lower half valve
assembly (12h screws onto 12b) until the lower valve is
seated against 18. Then, firmly tighten set screw 12g.
To seat the upper valve against orifice 19 either reach it
through the body side opening or remove diaphragm
assembly and pull top end of stem 12b upwards.
Tighten 12g with screwdriver or Allen wrench through body
side opening. If necessary, turn the entire valve assembly
(carefully – do not disturb adjustment) to face 12g toward side
opening. 12g must tighten against flat area at top of 12h to
correctly lock the adjustment.
9Screw entire valve assembly up (top of 12b screws onto lower
end of 11h) until it bottoms.
Then back off 1/2 to 1 full turn – this is important.
10 Replace bottom inspection plate 14. Engage pin in 13
with slot in lower end of 12j, then rotate 14 until holes line up
and install cap screws 16.
11 Replace parts removed under Step 1 above and return
adjustment to original setting.
Installation and Maintenance Instructions
Model 461-S, 461-8S, and 461-12S Regulator

5
4To disassemble diaphragm assembly, remove nut 11a.
When reassembling, note that abrasive side of emery cloth
washers face against diaphragm.
5Screw diaphragm assembly back into place.
11h screws into 12b until it bottoms, then back off 1/2 to 1
full turn – this is important.
6Note: single seat balanced valve does not require
any lock-up adjustment.
7Carefully reinstall upper diaphragm case 21. Diaphragm must
not be pinched between upper and lower cases 21 and 24.
Make sure travel indicator 45 is working. Tighten
bolts 23-22 evenly.
8Insert spring 9. Be sure it nests correctly into part 11b.
Replace remaining parts removed under Step 1 above
and return adjustment to original setting.
Condensed Parts List
All Models
Illustration Part
Number Description Number
1 Seal Cap 143-16-005-00
1a Seal Cap 121-10-005-52
1b Seal Cap 090-00-005-02
2* O-Ring 951357
2a Tetraseal (or O-Ring) 906534
1-1/2" x 1-5/8"
2b Tetraseal (or O-Ring) 904092
1-3/4" x 2"
3* Adjustment Spring Button 143-16-009-00
3a Spring Adjusting Screw 090-16-007-00
4 Hex Nut, 1/2" – 13 906537
4a Hex Steel Nut, 5/8" – 11 921407
5 Housing Cover 121-10-005-51
5a Housing Cover 091-16-080-53
7a Top Spring Button 121-10-009-51
7b Thrust Bearing, stainless steel 930510
ball, 3/8" dia.
7c Top Spring Button 091-16-009-00
8Cap Screws, Hex Hd., 9210029
5/16" – 18 x 7/8" lg.
9 Spring – See Table
*Minimum Recommended Spare Parts
All Models
Illustration Part
Number Description Number
1" Double Seat Valve Assembly, 091-16-515-01
brass trim, Buna-N
1" Double Seat Valve Assembly, 091-16-515-03
stainless steel trim, Buna-N
1" Double Seat Valve Assembly, 091-16-515-11
brass trim, Red Polyurethane
1" Double Seat Valve Assembly,
stainless steel trim, 091-16-515-13
Red Polyurethane
11/16" Double Seat Valve Assembly, 091-16-515-00
brass trim, Buna-N
12 11/16" Double Seat Valve Assembly, 091-16-515-02
stainless steel trim, Buna-N
11/16" Double Seat Valve Assembly, 091-16-515-10
brass trim, Red Polyurethane
11/16" Double Seat Valve Assembly,
stainless steel trim, 091-16-515-12
Red Polyurethane
1" Single Seat Valve Assembly,
stainless steel trim, 091-16-515-51
Red Polyurethane
11/16" Single Seat Valve Assembly,
stainless steel trim, 091-16-515-50
Red Polyurethane
12a* O-Ring, 3/8" x 1/2" 934007
Male Valve Stem, 5-1/16" lg.,
brass, for 1" & 11/16" double 091-16-116-02
12b seat assembly
Male Valve Stem, 5-1/16" lg.,
stainless, for 1" & 11/16" 091-16-116-00
double seat assembly
*Minimum Recommended Spare Parts
Over-Pressurization Protection
Protection must be provided for the downstream piping system
and the regulator's low pressure chambers to assure against the
potential of over-pressurization due to a regulator malfunction
or a failure of the regulator to lock up. The allowable over-
pressurization is the lowest of the maximum pressures permitted
by federal codes, state codes, Sensus bulletin RDS-1498,
or other applicable standards. The method of providing
over-pressure protection could be a relief valve, a monitor
regulator, a shut off device or any similar device.
Temperature Limits
The regulator models 461-S, 461-12S, and 461-8S can be used
for flowing temperatures from -20°F to 150°F.
Buried Service
The regulator models 461-S, 461-12S, and 461-8S
are not recommended for buried service.
Installation and Maintenance Instructions
Model 461-S, 461-8S, and 461-12S Regulator

6
Condensed Parts List
All Models
Illustration Part
Number Description Number
Valve Stem, stainless, for 091-00-016-07
12b 1” single seat assembly
Valve Stem, stainless, for 091-00-016-06
11/16” single seat assembly
Valve Retainer, brass, for 1” 091-16-018-03
double seat assembly (2 used)
Vale Retainer, brass, V Port 091-16-012-04
for 1” double seat (2 used)
12c Valve Retainer, brass, for 11/16” 091-16-018-02
double seat (2 used)
Valve Retainer, stainless, for 1” 091-16-018-01
single or double seat (1 or 2 used)
Valve Retainer, stainless for 11/16” 091-16-018-00
single or double seat (1 or 2 used)
Molded Valve, Buna-N
(Black, 45-55 Duro) for 091-16-315-01
1” double seat all trim
Molded Valve, Buna-N
(Black, 45-55 Duro) for 11/16” 091-16-315-00
double seat all trim
Molded Valve, Polyurethane
(Red, 65-75 Duro) for 1” 091-16-315-11
double seat all trim
Molded Valve, Polyurethane
(Red, 65-75 Duro) for 11/16” 091-16-315-10
double seat all trim
Molded Valve, Viton
(65-75 Duro, stamped V) for 091-16-315-13
12d* 1” double seat all trim
Molded Valve, Viton
(65-75 Duro, stamped V) for 091-16-315-12
11/16” double seat all trim
Molded Valve, Polyurethane
(Red 65-75 Duro) for 1” 091-16-315-51
single seat
Molded Valve, Polyurethane
(Red 65-75 Duro) for 11/16” 091-16-351-50
single seat
Molded Valve, Viton
(65-75 Duro, stamped V) for 091-16-315-58
1” single seat
Molded Valve, Viton
(65-75 Duro, stamped V) for 091-16-315-57
11/16” single seat
Valve Locknut, brass, for 903920
double seat assembly
12e Valve Locknut, stainless, for 920303
double seat assembly
Valve Locknut, 3/8" – 24 Crown 903936
Nylok, for single seat assembly
12f Valve Stem Locking Ring, 091-16-043-01
stainless, for double seat assembly
*Minimum Recommended Spare Parts
Condensed Parts List
All Models
Illustration Part
Number Description Number
12g Set Screw, slotted headless cup 907694
pt. #12-24 x 1/4” lg.
Female Valve Stem, brass, for 091-16-016-00
12h double seat assembly
Female Valve Stem, stainless for 091-16-016-03
double seat assembly
Valve Guide, brass for 091-16-012-00
12j double seat assembly
Valve Guide, stainless for 091-16-012-02
double seat assembly
12m Roll Pin, 1/4” x 1-1/2” lg., 910707
for single seat assembly
O-Ring 3/4” x 1” single 934015
12n* seat assembly
O-Ring 9/16” x 3/4”, for 934011
11/16” single seat assembly
13 Guide Bushing, brass, with pin 091-16-385-02
Guide Bushing, stainless,with pin 091-16-385-03
14 Bottom Inspection Plate,Iron 091-16-004-01
Bottom Inspection Plate, Steel 091-16-004-02
15* Tetraseal (or O-Ring), 2-3/4” x 3” 904079
16 Cap Screws, Hex Hd., 910030
5/16” - 18 x 1” lg.
Body, Screwed, 250 psi, Cast Iron 091-16-001-15
Body Flanged, ANSI 125, 091-16-001-17
FF, Cast Iron
17 Body Flanged, ANSI 250, 091-16-001-18
RF, Ductile Iron
Body Flanged, ANSI 300, 091-16-001-06
RF, Cast Steel
Outlet Orifice, 1” brass 091-16-029-01
18 Outlet Orifice 1” stainless 091-16-029-05
Outlet Orifice, 11/16” brass 091-16-029-00
Outlet Orifice, 11/16” stainless 091-16-029-04
Inlet Orifice, 1” brass 091-16-028-01
19 Inlet Orifice, 1” stainless 091-16-028-05
Inlet Orifice, 11/16” brass 091-16-028-0
Inlet Orifice, 11/16” stainless 091-16-028-04
20 Control Line Piping Assembly 091-16-361-50
20a 1/4” Sq. Hd. Steel Piping Plug 906055
20b 1/4” Malleable Iron Tee 946150
20c Nipple and Plug Assembly 091-00-361-50
Hex Hd. Steel Bolt,
5/16” - 18 x 1” lg. 910030
22 (461-12S, 461-8S, 461-S 12”)
Hex Hd. Steel Bolt,
5/16” - 18 x 1-1/4” lg. 910031
(461-S 8-1/2”)
23 Hex Steel Nut, 5/16” - 18 903859
26* Tetraseal (or O-Ring), 904085
4-3/8” x 4-5/8”
27 Vent Cap, 1/4” 137-02-505-02
*Minimum Recommended Spare Parts
Installation and Maintenance Instructions
Model 461-S, 461-8S, and 461-12S Regulator

7
Condensed Parts List
All Models
Illustration Part
Number Description Number
28 Seal Cap Gasket 091-16-066-00
Valve Stem Guide, stainless,
30 11/16” single seat assembly 091-16-012-52
Valve Stem Guide, stainless,
1” single seat assembly 091-16-012-53
32 Tetraseal (or O-Ring), 904086
1-1/2” x 1-3/4”
33 Ductile Iron Inspection Plate,Side 091-16-072-04
Steel Inspection Plate, Side 091-16-072-01
45 Travel Indicator Assembly 091-00-365-61
Model 461-12S
All Models
Illustration Part
Number Description Number
Diaphragm Assembly,
11 3-1/2” w.c. to 2 psi 121-16-550-51
outlet pressure complete
11a Elastic Stop Nut 29-NE-066 903955
11b Bottom Spring Button 121-10-022-53
11c Diaphragm Pan 121-16-017-50
11d* Molded Diaphragm, 121-16-150-53-001
Buna-N
11f Emery Cloth Washer 121-10-178-50
11h Diaphragm Stud, 121-16-058-52
stainless steel
*Minimum Recommended Spare Parts
Model 461-8S
All Models
Illustration Part
Number Description Number
11 Diaphragm assembly, 2 psi to 121-10-550-55
10 psi outlet pressure complete
11a Elastic Stop Nut 29-NE-066 903955
11b Bottom Spring Button 121-10-022-50
11c Diaphragm Pan 121-10-017-50
11d* Diaphragm, Buna-N 121-10-150-50
11e Upper Plate 121-10-022-52
11f Emery Cloth Washer 121-10-178-50
11g Lower Plate 121-10-079-52
11h Diaphragm Stud, stainless steel 091-16-058-02
Model 461-S
All Models
Illustration Part
Number Description Number
11 Diaphragm Assembly, 12” 091-16-550-01
Diaphragm Assembly, 8-1/2” 091-86-550-02
11a Hex Flexloc Nut 3/8” – 16” 900123
11b Bottom Spring Button 091-16-009-50
11c Upper Diaphragm Plate, 12” 091-16-060-00
Upper Diaphragm Plate, 8-1/2” 091-86-010-00
11d* Diaphragm,12” 091-16-150-00
Diaphragm, 8-1/2” 091-86-150-00
11e Lower Diaphragm Plate, 12” 091-16-060-01
Lower Diaphragm Plate, 8-1/2” 091-86-010-00
11f Seal Washer 014-76-179-03
11g Stat-O-Seal, 3/8” 904985
11h Diaphragm Stud, stainless steel 091-16-058-02
*Minimum Recommended Spare Parts
Maximum Emergency Pressures
For complete Maximum Emergency Pressure information for
Model 461 Regulators, refer to bulletin RDS-1498, Regulator
Pressure Ratings. If the maximum outlet pressure is exceeded,
the regulator must be removed from service and carefully
inspected. Damaged or otherwise unsatisfactory parts must be
replaced before returning the regulator to service.
Monitoring
The 461-S, 461-8S, or 461-12S make an excellent monitor;
a standby regulator installed in series which assumes control if
a failure in the operating regulator permits the outlet pressure to
exceed the set-point.
The fast rate of response enables it to take over quickly where
necessary, and its outstanding performance means that it will
provide excellent standby regulation.
It can be located in either the upstream or the downstream
position.
When a 461 is used to monitor a regulator with an identical inner
valve (another 461, a Model 1100 etc.) the total maximum
capacity through both can be figured at 70% of the capacity
of one of them alone. This applies with the monitor located
either upstream or downstream.
Other Gases
The regulator models 461-S, 461-12S, and 461-8S are mainly used
on natural gas services; however, these regulators will
perform equally well on other gases. When using the regulators
on other gases, the regulator capacities must be adjusted using
the following correction factors.
Type of Gas Correction Factor
Air (specific gravity 1.0) 0.77
Propane (specific gravity 1.53) 0.63
1350 BTU Propane-Air mixture 0.71
(specific gravity 1.20)
Nitrogen (specific gravity 0.97) 0.79
Dry CO2(specific gravity 1.52) 0.63
Correction Factor =
For use with gases not listed above, please contact your
Sensus representative or Sensus Distributor for
recommendations.
0.60
Specific gravity of the gas
Installation and Maintenance Instructions
Model 461-S, 461-8S, and 461-12S Regulator

28
27
a
b
c
d
e
f
11
Inlet
1b 3a
4a
2b
5a
7c
7b
9
21
22
23
d
cb
a
20
h
g
24
d
n
12
a
b
m
e
c
30
16
2
1
3
9
45
22
23
a
b
c
e
h
cdi
13
14
15
16
18
19
20
15
12
ab
d
f
h
11
d
g
f
17
c
a
b
d
f
g
11
3a
4
7a
7b
9
21
22
23
17 12a 15 24
h
2
5
45
2
2a
e
c
461-8S Aluminum
Diaphragm Case
17
33
32
461-S Cast Iron
Diaphragm Case
Capacities at Other Pressures
Capacity for pressure reductions not listed
in the table can be calculated with the
following formula:
1Q = K P0(P- P0)
2Q = KP1
2
Q = maximum capacity of the regulator
(in SCFH of 0.6 specific gravity
natural gas)
K = the “K” factor; the regulator constant
(from Sensus bulletin R-1330, page 6)
P1=absolute inlet pressure (psia)
P2=absolute outlet pressure (psia)
Use formula 1 when P1is less than 1.894
P0
Use formula 2 when P1is greater than 1.894
P0
461-12S
Aluminum Diaphragm Case
Single Seat Balanced
Valve Assembly
Screwed Side
Inspection Plates
Models 461-S, 461-8S and 461-12S Regulators
Installation and Maintenance Instructions
Limited Warranty
Seller warrants the Goods to be free from defects in materials manufactured by Seller and in Seller’s workmanship for a period of one (1) year after tender of delivery (the “Warranty Period"). THIS LIMITED WARRANTY
(a) IS IN LIEU OF, AND SELLER DISCLAIMS AND EXCLUDES ALL OTHER WARRANTIES, STATUTORY, EXPRESS OR IMPLIED, INCLUDING, WITH LIMITATION, ANY WARRANTY OF MERCHANTABILITY OR FITNESS FOR A
PARTICULAR PURPOSE, OR OF CONFORMITY TO MODELS OR SAMPLES; (b) does not apply to any Goods which have been (I) repaired, altered or improperly installed; (ii) subjected to improper use or storage,
(iii) used or incorporated with other materials or equipment, after buyer or anyone using the Goods has, or reasonably should have, knowledge of any defect or nonconformance of the Goods; or (iv) manufactured,
fabricated or assembled by anyone other than Seller, (c) shall not be effective unless buyer notifies Seller in writing of any purported defect or nonconformance with (thirty days) after Buyer discovers or should have
reasonably discovered such purported defect or nonconformance; and (d) shall only extend to Buyer and not to any subsequent buyers or users of the Goods. Buyer shall provide Seller access to the Goods as to which
Buyer claims a purported defect or nonconformance, upon request by Seller, buyer shall, at its own risk and expense, promptly return the Goods in question to Seller’s Plant.
© Sensus 2009 Made in USA 12/09
805 Liberty Boulevard
DuBois, PA 15801
800-375-8875
Fax: (814) 375-8460
www.sensus.com/gas
Authorized
Distributor:
Outlet Pressure Range Spring Color Spring Part No.
3-1/2" to 6-1/2" w.c. Red 143-16-021-03
5" to 8-1/2" wc. Blue 143-16-021-04
6" to 14" wc. Green 143-16-021-05
12" to 28" wc. Orange 143-16-021-06
1 psi to 2 psi Black 143-16-021-07
1-1/2 psi to 3 psi Cadmium 143-16-021-08
Model 461-12S
Diaphragm Outlet Pressure Spring Spring
Size Ratings Color Part No.
8-1/2" 3 to 6 psi Blue 090-70-021-04
5 to 10 psi Red 090-70-021-05
2 to 10" w.c. Aluminum 090-70-021-00
4 to 16" w.c. Green 090-70-021-01
12" 7 to 29" w.c. Yellow 090-70-021-02
1.5 to 1.75 psi. Gray 090-70-021-03
1 to 3.5 psi. Blue 090-70-021-04
Model 461-S
Outlet Pressure Range Spring Color Spring Part No.
1 psi to 2 psi Orange 143-16-021-06
2 psi to 4-1/4 psi Black 143-16-021-07
3 psi to 6-1/2 psi Cadmium 143-16-021-08
6 psi to 10 psi Cadmium (outer) 143-16-021-08
White (inner) 143-16-021-13
Model 461-8S
A
ll products purchased and services performed are subject to Sensus' terms of sale, available at either; http://na.sensus.com/TC/TermsConditions.pdf or 1-800-METER-IT. Sensus reserves the right to
modify these terms and conditions in its own discretion without notice to the customer.
This document is for informational purposes only, and SENSUS MAKES NO EXPRESS WARRANTIES IN THIS DOCUMENT. FURTHERMORE, THERE ARE NO IMPLIED WARRANTIES, INCLUDING WITHOUT LIMITATION,
WARRANTIES AS TO FITNESS FOR A PARTICULAR PURPOSE AND MERCHANTABILITY. ANY USE OF THE PRODUCTS THAT IS NOT SPECIFICALLY PERMITTED HEREIN IS PROHIBITED.
This manual suits for next models
2
Table of contents
Other Sensus Controllers manuals
Popular Controllers manuals by other brands

Brainboxes
Brainboxes BB-400 quick start guide
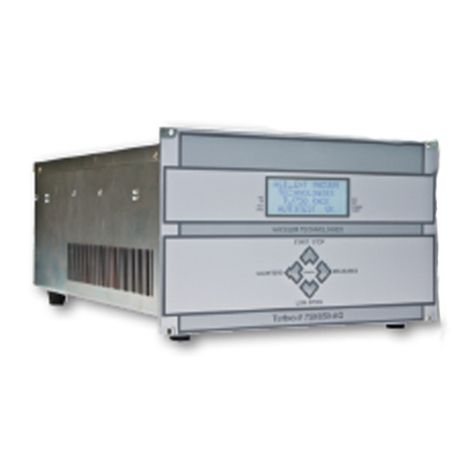
Agilent Technologies
Agilent Technologies Turbo-V 750/850-AG user manual
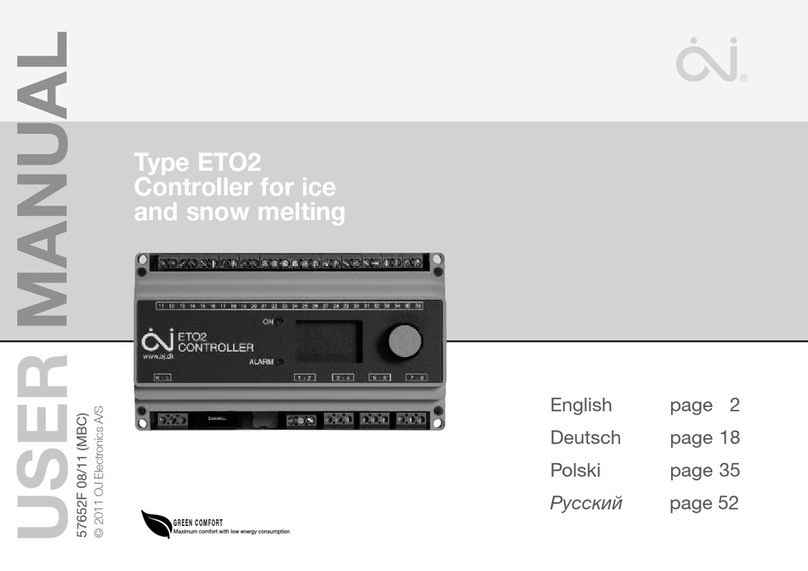
OJ
OJ ETO2 user manual
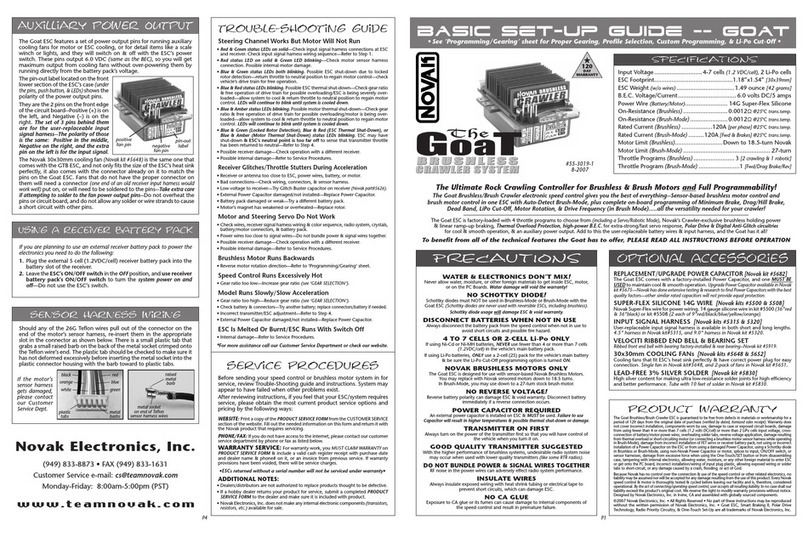
NOVAK
NOVAK GOAT BRUSHLESS CRAWLER SYSTEM - BASIC SETUP GUIDE... Setup guide
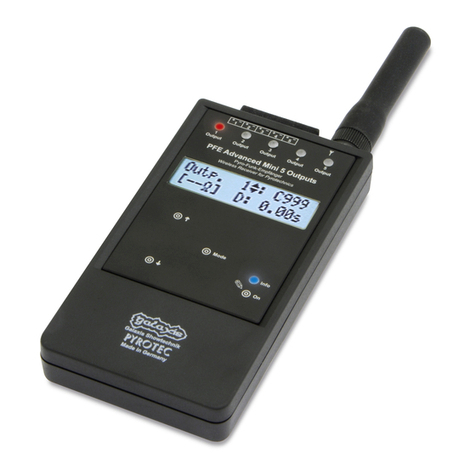
GALAXIS SHOWTECHNIK
GALAXIS SHOWTECHNIK PYROTEC PFE Advanced Mini 5 Outputs user manual
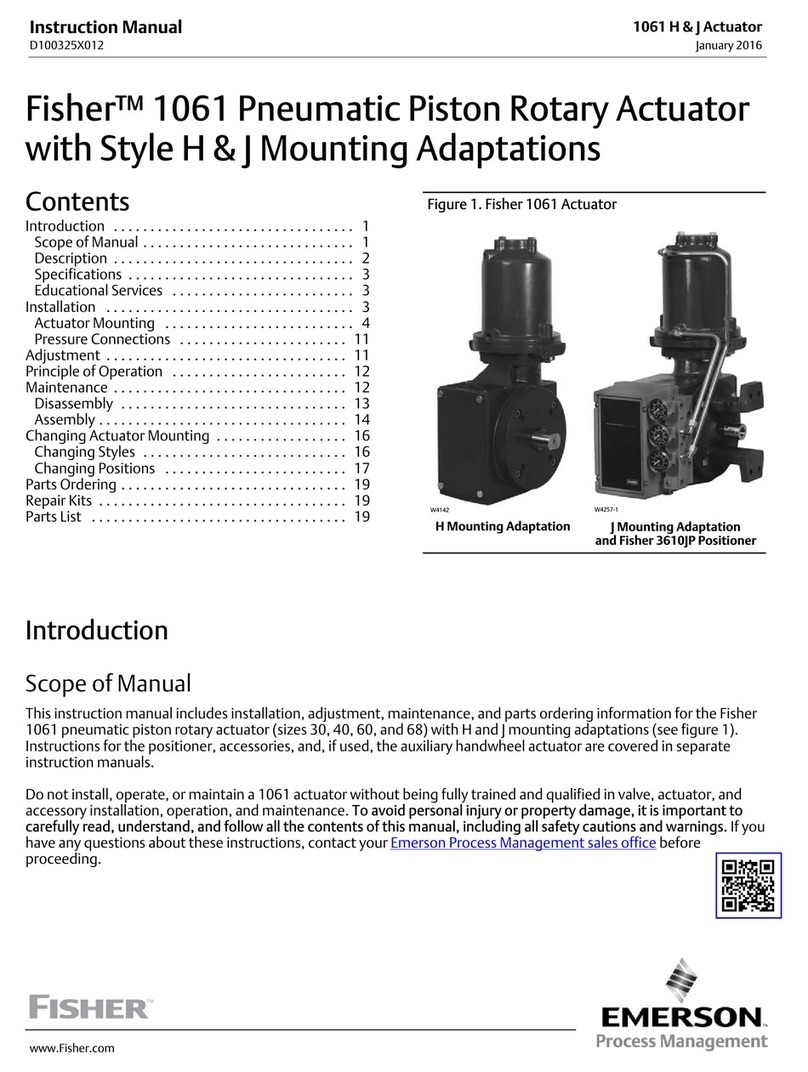
Fisher
Fisher 1061 instruction manual