Sensus 441-S User manual

RM-1350 R7
Sensus Metering Systems
Installation
and
Maintenance
Instructions
Model 441-S Regulator
THE GAS INDUSTRY

2
Installation and Maintenance Instructions
Model 441-S Regulator
Maximum
Working Maximum
Regulator 441 Body Pressure Inlet
Body Type Materials of Body Pressure
Cast Iron
Screwed End (ASTM A126-71 250 psi
(2" Pipe Size Only) Class B)
Cast Iron
Flanged (ASTM A126-71 175 psi
ANSI 125 FF Class B) 100 psi
Ductile Iron
Flanged (ASTM A395-71 575 psi
ANSI 250 RF gr 60-40-18)
Cast Steel
Flanged (ASTM A126-70a 720 psi
ANSI 300 RF gr WCB)
Installation and Start-Up
1Thoroughly purge inlet piping to remove dirt and debris which
could damage the regulator or impair its operation. If this
cannot be done, a filter or strainer should be installed ahead
of the regulator.
Make certain that regulator is free of any dirt or foreign matter
that might have collected.
2Place regulator in the line with high pressure connected to the
inlet side (be sure that shipping screens or covers, if used,
are removed from the inlet and outlet).
Tighten bolts on flanges evenly.
Where required, the regulator may be inverted.
CAUTION
It is the user's responsibility to assure that all regulator vents
and/or vent lines exhaust to a non-hazardous location away from
ANY POTENTIAL sources of ignition. Where vent lines are used,
it is the user's responsibility to assure that each regulator is
individually vented and that common vent lines ARE NOT used.
3From the 1/2" union 60 extend pipe or tubing to the control
connection into the outlet piping. This control piping should
not be less than 1/2" in size and should be adequately
protected against breakage (regulators go wide open if the
control line is broken).
The regulator will work to deliver the pressure, for which it is
adjusted, at that point in the outlet piping where the control
connection is located.
In general, the control connection should be at least 8 pipe
diameters from the regulator and should be in as straight a
run of pipe as possible.
The control connection should be clean and smooth,
free of rough edges, welding “icicles”. etc.
4Where outlet piping increases in size near the regulator,
it is generally preferable to locate the control connection in
the larger size.
The 1/2" union 60 contains a small orifice, approximately
1/16" diameter. This orifice should not be removed. Also,
make certain this orifice is open and free of foreign material.
Check all connections for leaks.
CAUTION
Turn gas on very slowly. If an outlet stop valve is used,
it should be opened first. Do not overload the diaphragm with a
sudden surge of inlet pressure. Monitor the outlet pressure
during start-up to prevent an outlet pressure overload.
5Put the regulator into operation as follows: (refer to page 8)
a. Slowly open the downstream control line valve (A).
b. Slowly open the downstream block valve (B).
c. Very slowly open the upstream block valve (C).
d. Set the adjusting screw 10 for the required outlet pressure.
Turn it clockwise to increase the pressure counterclockwise
to decrease it. Only make this adjustment when gas
is actually flowing through the regulator.
e. After adjustment is complete, the locknut 11 should be
tightened firmly and the seal cap 1replaced.
6To shut down, carefully close valves C, B, and Ain that order.
CAUTION
The diaphragm case vent must be positioned to protect against
flooding, drain water, ice formation, traffic, tampering, etc. The
vent must be protected against nest building animals, bees,
insects, etc. to prevent vent blockage and minimize the chances
for foreign material from collecting in the vent side of the
regulator diaphragm.
7The vent connection is an escape path for flammable gas
and it must be located and/or piped so that potential
discharge occurs in a safe area away from buildings,
open flames, collection areas, arcing devices, etc.
Regulators that are installed indoors or in a non-vented
area must be vented to the outside. Simply run vent piping
from the regulator vent connection to a non-hazardous
location on the outside away from ANY POTENTIAL sources
of ignition. The vent piping must be connection size
or larger and piped to a safe area. The vent discharge
must be protected against the potentials outlined
in instructions #2 and #10.
8For outdoor installations, it is recommended that the
regulator be installed so that the regulator vent faces
downward to avoid the potential for water or other foreign
matter entering the regulator and interfering with the
proper operation of the regulator.
Maximum Inlet Pressures

3
Installation and Maintenance Instructions
Model 441-S Regulator
Servicing and Adjustment
General Notes
1Make sure the regulator is entirely depressured before servicing.
2A quick visual inspection of the valve can be made by
removing inspection plates 38 from the sides of the body.
They also provide greatly improved access to the valve
when servicing or adjusting.
3The valve and body parts are interchangeable with other
441 Regulators (441-57S, 441-X57, 441-VPC,
441-2100, etc.).
4Use lubricants sparingly and with care to avoid exposing
tacky surfaces to the gas stream. Such surfaces could
cause accumulation of dirt on close clearance parts.
Use moly or silicone-type lubricants. Avoid the use of
petroleum base types.
Lubricate stem 24, guide 50h, and stem O-ring 23 with dry
silicone lubricant to help assure free movement and a tight
seal.
An application of lubricant to the other O-rings and the
tetraseals in the regulator will help assure their tightness.
To Remove Valves
1Remove seal cap 1, back off adjusting screw 10, remove
housing cover 5, and spring 14.
2Remove bottom plate 33, and side plates 38.
3Insert an Allen wrench through side inspection opening and
loosen Allen screw 50h.
4Unscrew lower valve assembly and remove through bottom
opening (50h unscrews from 24).
5Unscrew upper valve assembly and remove through side
opening (50e or 50j unscrews from 24).
Note:
a. If upper valve assembly is too large to remove through side
opening, then remove it through bottom opening by also
removing outlet orifice 29, (remove cap screws 26 to
remove orifice, and, if tight, jack out using cap screws
in jacking holes).
b. Entire valve assembly may be removed intact through
bottom opening by also removing orifice 29. This method
leaves the lock-up adjustment undisturbed.
c. Use care with orifice gasket 27.
6To disassemble upper and/or lower valve assembly, remove
nuts 50a.
To Replace and Adjust Valves
1Assemble upper valve assembly (parts 50a, 50b, 50c, 50d,
50e, 50f, 50g, 50j), and lower valve assembly (parts 50a,
50b, 50c, 50d, 50h). Firmly tighten nuts 50a. (Also, 50i
should be firmly tightened against 50a).
2Insert upper valve assembly and screw into place by a few
turns (50e or 50i screws into 24 but should be loose by
1/2 to 1 turn).
3If orifice 29 was removed, reinstall it.
4Inset lower valve assembly and screw into place by a few
turns (50h screws into 50e).
5Turn upper valve assembly so Allen screw 50g is accessible
through side inspection opening.
6Make the valve lock-up adjustment as follows:
a. Hold upper valve against its seat. This can be done by
hand, reaching through side inspection opening.
b. While holding the upper valve against its seat, screw
lower valve assembly upwards until the lower valve also
touches its seat. When both upper and lower valves are
touching their seats they are correctly adjusted for tight
lock-up.
c. Firmly tighten Allen screw 50g. This locks the adjustment
by evenly and tightly locking 50h and 50e together.
Note: If the entire valve assembly was removed intact and
Allen screw 50g has not been loosened, the assembly may
be reinstalled without making the lock-up adjustment.
7Screw entire valve assembly up (50e or 50i screws into 24)
until it bottoms. Then back off 1/2 to 1 full turn - this is
important.
8Replace side plates 38.
9Replace bottom plate 33. Match bottom end of 50h into 31
and/or 32 and then turn bottom plate either way
to first matching bolt hole position.
To Remove Orifices
1Remove outlet orifice 29 per applicable steps 1 through 5
under section “To Remove Valves”.
2Remove inlet orifice 28 as follows:
a. Remove seal cap 1, back off adjusting screw 10, remove
housing cover 5and spring 14.
b. Remove bottom plate 33 and then unscrew valve assembly
by grasping 50h and turning (50e or 50i unscrews from
24).
c. Remove diaphragm case assembly by first opening union
60 and removing cap screws 34.
d. Remove cap screws 26 and remove inlet orifice 28.
If orifice is tight, jack out cap screws in jacking holes.
Use care with gasket 27.
e. When replacing diaphragm assembly, the threaded
connection between 24 and 50e or 50i should be
screwed together until it bottoms and
then backed off 1/2 to 1 turn - this is important
CAUTION
Regulators are pressure control devices with numerous moving
parts subject to wear that is dependent upon particular
operating conditions. To assure continuous satisfactory
operation, a periodic inspection schedule must be adhered to
with the frequency of inspection determined by the severity of
service and applicable laws and regulations.

failure of the regulator to lock-up. The allowable over
pressurization is the lowest of the maximum pressures permitted
by federal codes, state codes, Bulletin RDS-1498, or other
applicable standards. The method of providing over pressure
protection could be a relief valve, a monitor regulator, a shut off
device or any similar device.
Temperature Limits
The Model 441-S Regulator can be used for flowing temperatures
from -20°F to 150°F.
Buried Service
The Model 441-S Regulator is not recommended for buried service.
Condensed Parts List
For complete parts list and list prices please refer to RP 1350.
When ordering parts for a 441-S regulator, include pipe size,
model number, inner valve size, and serial number if possible.
Maximum Emergency Pressure
The maximum pressure the Model 441-S regulator inlet may be
subjected to under abnormal conditions without causing damage
to the regulator is 125 psi.
The Maximum pressure the regulator outlet may be subjected to
without causing damage to the internal part of the regulator is:
10" Diaphragm set-point + 4 psi
12" Diaphragm set-point + 3 psi
14" Diaphragm set-point + 2 psi
16" Diaphragm set-point + 1 psi
18" Diaphragm set-point + 1 psi
20" Diaphragm set-point + 1 psi
The set-point is defined as the outlet pressure a regulator is
adjusted to deliver.
If any of the above pressure limits are exceeded, the regulator
must be taken out of service and inspected. Damaged or
otherwise unsatisfactory parts must be repaired or replaced.
The maximum pressure that can be safely contained by the
diaphragm case is:
10" Diaphragm 15 psi
12" Diaphragm 10 psi
14" Diaphragm 10 psi
16" Diaphragm 5 psi
18" Diaphragm 5 psi
20" Diaphragm 5 psi
Safely contained means no leakage as well as no bursting. Before using
any of the above data, make sure this entire section is clearly understood.
Other Gases
The Model 441-S is mainly used on natural gas services; however,
this regulator will perform equally as well on other gases. When
using the Model 441-S Regulator on other gases, the regulator
capacities must be adjusted using the correction factors on page 5.
4
Installation and Maintenance Instructions
Model 441-S Regulator
To Change Spring
1Remove seal cap 1, back off adjusting screw 10, remove
housing cover 5, and remove spring 14.
2Insert the new spring. Be sure it nests correctly onto part 15.
3Complete as per steps 7, 8 and 9 under "To Assemble 441-S".
To Service Diaphragm
1Remove seal cap 1, back off adjusting screw 10, remove
housing cover 5, and remove spring 14.
2Remove bolts 42 and then carefully remove upper diaphragm
case 43.
3Turn diaphragm assembly counterclockwise until 24 unscrews
from 50e or 50i, then remove assembly and inspect
diaphragm.
4If a new diaphragm 20 is required, remove nut 16 and
disassemble.
5Reassemble diaphragm assembly (parts 16, 17, 18, 19, 20,
21, 22, 23, 24).
6Screw diaphragm assembly back into place (24 screws into
50e or 50i until it bottoms) then back off 1/2 to 1 full turn
this is important.
7Carefully reinstall upper diaphragm case 43. Diaphragm must
not be pinched between upper and lower cases, 43 and 40.
Tighten bolts 42 evenly.
8Replace spring, etc., per steps 6 through 9 under
“To Assemble 441-S”.
To Assemble 441-S
1Install orifice 28 through top opening.
2Install valve assembly and orifice 29 per applicable steps 1
through 6 under “To Replace and Adjust Valves” (except that
50e or 50i does not yet screw into 24).
3Install centerpiece and lower diaphragm case, 36 and 40.
4Install diaphragm assembly and upper case 43 per steps
5 through 7 under “To Service Diaphragm”.
5Replace bottom plate 33. Match bottom end of 50h into 31
and /or 32, and then rotate bottom plate either way to first
matching bolt hole position.
6Insert the spring. Be sure it nests correctly onto part 15.
7Insert top spring button 12. Be sure it is nested correctly
on the spring.
8Install housing cover 5. Be sure ball 13 is in place and the
lower end of adjusting screw 10 goes in the hole in button 12.
9Set adjusting screw 10 for desired outlet pressure,
firmly tighten nut 11 and replace seal cap 1.
Over Pressurization Protection
Protection must be provided for the downstream piping system
and the regulator's low pressure chambers to assure against the
potential over pressurization due to a regulator malfunction or a

3" Model 441-S
Illustration Part
Number Description Number
26 Hex Cap Screw, 1/4"–20 x 1/2" Lg., 910001
120,000 tensile
27 O-Ring, for Orifices 950818
2-1/8" Inlet Orifice, plated steel 090-20-028-00
2-1/8" Inlet Orifice, stainless steel 090-20-028-50
28 1-3/4" Inlet Orifice, plated steel 090-20-028-02
1-3/4" Inlet Orifice, stainless steel 090-20-028-52
1-1/2" Inlet Orifice, plated steel 090-20-028-03
1-1/2" Inlet Orifice, stainless steel 090-20-028-53
2-1/8" Outlet Orifice, plated steel 090-20-029-00
2-1/8" Outlet Orifice, stainless steel 090-20-029-50
29 1-3/4" Outlet Orifice, plated steel 090-20-029-02
1-3/4" Outlet Orifice, stainless steel 090-20-029-52
1-1/2" Outlet Orifice, plated steel 090-20-029-03
1-1/2" Outlet Orifice, stainless steel 090-20-029-53
Valve Assembly, 2-1/8", brass trim, 090-20-515-30
Buna-N (Black, 50-55 Duro)
Valve Assembly, 2-1/8", stainless
steel trim, Buna-N 090-20-515-50
(Black, 50-55 Duro)
50 Valve Assembly, 2-1/8", brass trim, 090-20-515-40
Polyurethane (Red, 65-75 Duro)
Valve Assembly, 2-1/8", stainless
steel trim, Polyurethane 090-20-515-60
(Red 65-75 Duro)
Valve Retainer, standard, stainless 090-20-018-30
50b steel, 2-1/8"
Valve Retainer, v-port wings, 090-20-012-51
stainless steel, 2-1/8"
Molded Valve, 2-1/8", Buna-N 090-20-315-00
50d (Black, 50-55 Duro) all trim
Molded Valve, 2-1/8", Polyurethane 090-20-315-02
(Red, 65-75 Duro) all trim
All Models 441-S
Illustration Part
Number Description Number
1a Tetraseal (or O-Ring) 1-3/4 x 2" 904092
4Hex Cap Screw, 5/16" – 18 x 3/4" 910028
6Spring Cage Cover Gasket 090-16-066-30
7Vent Cap, 1/4" NPT 137-02-505-02
9Spring Cage Gasket 090-16-066-60
13 Thrust Bearing, 3/8" diameter 930510
stainless steel ball
16 Hex Steel Nut, 5/8" – 18 905993
18 Seal Gasket, 2 used 014-76-179-03
7" Diaphragm 090-78-150-21
10" Diaphragm 090-70-150-20
12" Diaphragm 090-71-150-20
20 14" Diaphragm 090-72-150-20
16" Diaphragm 090-73-150-20
18" Diaphragm 090-74-150-20
20" Diaphragm 090-75-150-20
23 O-Ring, 11/16" I.D. 7/8" O.D. 934013
24 Diaphragm Connecting Stem, 090-16-058-00
stainless steel
41 Hex Steel Nut, 3/8" – 16 920853
42 Hex Cap Screw, 3/8" – 16 x 1-3/8" Lg. 903568
45 Travel Indicator Assembly
5
Installation and Maintenance Instructions
Model 441- Regulator
2" Model 441-S
Illustration Part
Number Description Number
26 Hex Cap Screw, 1-4"–20 x 1/2" Lg., 910001
120,000 tensile
27 O-Ring, for Orifices 904832
1-3/4" Inlet Orifice, plated steel 090-16-028-00
28 1-3/4" Inlet Orifice, stainless steel 090-16-028-50
1-1/2" Inlet Orifice, plated steel 090-16-028-01
1-1/2" Inlet Orifice, stainless steel 090-16-028-51
1-3/4" Outlet Orifice, plated steel 090-16-029-00
29 1-3/4" Outlet Orifice, stainless steel 090-16-029-50
1-1/2" Outlet Orifice, plated steel 090-16-029-01
1-1/2" Outlet Orifice, stainless steel 090-16-029-51
Monitoring
The Model 441-S Regulator makes an excellent monitor. It can act
as a standby regulator installed in series, which assumes control if
a failure in the operating regulator permits the outlet pressure to
exceed the set-point. It can be located in either the upstream
or the downstream position.
When a Model 441-S Regulator is used to monitor a regulator with
an identical inner valve (another 441 Regulator), the total maximum
capacity through both regulators can be figured at 70% of the
capacity of one regulator alone. This applies with the monitor
located either up or downstream.
For use with gases not listed above, please contact your Sensus
Metering Systems representative or distributor for recommendations.
0.60
Specific gravity of the gas
Correction Factor =
Type of Gas Correction Factor
Air (specific gravity 1.0) 0.77
Propane (specific gravity 1.53) 0.63
1350 BTU Propane-Air Mixture
(specific gravity 1.20) 0.71
Nitrogen (specific gravity 0.97) 0.79
Dry CO2(specific gravity 1.52) 0.63
For other non corrosive gasses use the following formula:

16
10
11
13
12
15
14
17
18
19
20
21
22
23 24
25
28 27
26
29
27
26
32 33
34 35
1a
5
4
1
6
7
8
943
42
40
41
36a
60
60
34
35 36
37a
37
38
39
45
a
b
c
d
e
g
a
b
c
d
h
50
6
Installation and Maintenance Instructions
Model 441-S Regulator
2" and 3" Model 441-S
Illustration Part
Number Description Number
Guide Bushing with Pin, brass 090-16-385-01
32 Guide Bushing with Pin, 090-16-385-03
stainless steel
34 Hex Cap Screw, 1/2" – 13 x 1-1/4" 910106
35 Tetraseal (or O-Ring), 904085
4-3/8" x 4-5/8"
36a Tetraseal, 4" x 4-1/4" 904084
37 Centerpiece, Stem Bushing 090-16-373-00
37a Aluminum Seal Ring 090-26-178-00
39 Tetraseal (or O-Ring), 904078
3-1/4" x 3-1/2"
Valve Assembly, 1-3/4",
brass trim, Buna-N 090-16-515-27
(Black, 50-55 Duro)
Valve Assembly,
1-3/4", stainless steel trim, 090-16-515-50
50 Buna-N (Black, 50-55 Duro)
Valve Assembly, 1-1/2",
brass trim, Buna-N 090-16-515-31
(Black, 50-55 Duro)
Valve Assembly, 1-1/2",
stainless steel trim, 090-16-515-51
Buna-N (Black, 50-55 Duro)
50a Valve Retaining Nut, 5/8" – 18 905564
2" and 3" Model 441-S (continued)
Illustration Part
Number Description Number
Valve Retainer, standard,
steel,1-3/4" 090-16-018-00
Valve Retainer, standard, 090-16-018-30
stainless steel, 1-3/4"
Valve Retainer, v-port wings, 090-16-012-53
stainless steel, 1-3/4"
50b Valve Retainer, standard, steel, 090-16-018-01
1-1/2"
Valve Retainer, standard, 090-16-018-31
stainless steel, 1-1/2"
Valve Retainer, v-port wings, 090-16-012-52
steel, 1-1/2"
Valve Retainer, v-port wings, 090-16-012-55
stainless steel, 1-1/2"
50c O-Ring, 5/8" x 13/16" 934012
Molded Valve, 1-3/4", Buna-N 090-16-315-00
(Black, 50-55 Duro) all trim
Molded Valve, 1-1/2", Buna-N 090-16-315-01
50d (Black, 50-55 Duro) all trim
Molded Valve, 1-3/4", Polyurethane 090-16-315-02
(Red, 65-75 Duro) all trim
Molded Valve, 1-1/2", Polyurethane 090-16-315-03
(Red, 65-75 Duro) all trim
50e Female Valve Stem, brass 090-16-116-00
Female Valve Stem, stainless steel 090-16-116-01
Adjustment Clamp Screw, Soc. Hd. 903486
50g Screw, 10–24 x 1/2" Lg.
Adjustment Clamp Screw, 090-16-046-01
for 1-1/2" valve only
50h Male Valve Stem, brass 090-16-016-01
Male Valve Stem, stainless steel 090-16-016-02
2" and 3" Model 441-S

23
24 25
34
4
5
6
7
8
9
45 43
42
41
40
35
1
1a
36
37
60
34
37a
ia
bc
de50
fg
ab
c
52
j
b
b
10
11
12
13
14
15
16
17
18
19
20 21
22
26
27 28
29 27
26
30
31
30
35 32
38
39
36a
Molded Valve, 3", Buna-N 090-22-315-00
(Black, 50-55 Duro) all trim
Molded Valve, 2-1/8", Buna-N 090-22-315-01
(Black, 50-55 Duro) all trim
Molded Valve, 1-3/4", Buna-N 090-22-315-04
50d (Black, 50-55 Duro) all trim
Molded Valve, 3", Polyurethane 090-22-315-02
(Red, 65-75 Duro) all trim
Molded Valve, 2-1/8", Polyurethane
(Red, 65-75 Duro) all trim 090-22-315-03
Molded Valve, 1-3/4", Polyurethane 090-22-315-05
(Red, 65-75 Duro) all trim
50e Female Valve Stem, brass 090-22-016-40
Female Valve Stem, stainless steel 090-22-016-41
50f Adjustment Clamp Ring, 090-22-043-02
stainless steel
50g Adjustment Clamp Screw, Soc. Hd. 903494
Screw, 1/4" – 20 x 3/4" Lg.
50h Male Valve Stem, stainless steel 090-22-116-01
Stem Extension, stainless, 090-22-058-40
50i for 20" diaphragm only
Stem Extension, stainless, 090-22-058-41
for 18" and smaller diaphragms
Travel Stop, for 3" valves 090-22-040-51
52 Travel Stop, for 2-1/8" and 090-22-040-55
1-3/4" valves
4" Model 441-S (continued)
Illustration Part
Number Description Number
7
Installation and Maintenance Instructions
Model 441-S Regulator
4" Model 441-S
Illustration Part
Number Description Number
26 Hex Cap Screw, 3/8"–16 x 3/4" Lg., 910053
120,000 tensile
27 O-Ring, for orifices 905583
3" Inlet Orifice, plated steel 090-22-028-00
3" Inlet Orifice, stainless steel 090-22-028-50
28 2-1/8" Inlet Orifice, plated steel 090-22-028-02
2-1/8" Inlet Orifice, stainless steel 090-22-028-52
1-3/4" Inlet Orifice, plated steel 090-22-028-01
1-3/4" Inlet Orifice, stainless steel 090-22-028-51
3" Outlet Orifice, plated steel 090-22-029-00
3" Outlet Orifice, stainless steel 090-22-029-50
29 2-1/8" Outlet Orifice, plated steel 090-22-029-02
2-1/8" Outlet Orifice, stainless steel 090-22-029-52
1-3/4" Outlet Orifice, plated steel 090-22-029-01
1-3/4" Outlet Orifice, stainless steel 090-22-029-51
30 Hex Cap Screw, 3/8" – 16 x 1" Lg. 910055
31 Spin Stop Plate 090-22-040-01
32 Guide Bushing, brass 090-22-074-00
Guide Bushing, stainless steel 090-22-074-01
Hex Cap Screw, 5/8" – 11 x 1-1/2" 910157
34 Hex Cap Screw, 5/8" – 11 x 1-3/4" 910158
for ductile bottom plate
35 Tetraseal (or O-Ring), 904080
6-1/4" x 6-1/2"
36a Tetraseal (or O-Ring), 4" x 4-1/4" 904084
37 Centerpiece Stem Bushing 090-16-373-02
37a Aluminum Seal Ring 090-26-178-00
39 Tetraseal (or O-Ring), 904083
4-1/4" x 4-1/2"
Valve Assembly, 3", brass trim, 090-22-515-30
Buna-N (Black, 50-55 Duro)
50 Valve Assembly, 3", stainless steel, 090-22-515-50
trim, Buna-N (Black, 50-55 Duro)
Note: For other Valve Assemblies see RP 1350
50a Valve Retaining Nut, 3/4" – 16 090-22-034-00
Valve Retainer, standard, iron, 3" 090-22-018-03
Valve Retainer, standard, stainless 090-22-018-00
steel, 3"
Valve Retainer, v-port wings, 090-22-012-20
iron, 3"
Valve Retainer, v-port wings, 090-22-012-40
stainless steel, 3"
Valve Retainer, standard, 090-22-018-01
50b iron, 2-1/8"
Valve Retainer, standard, stainless 090-22-018-31
steel, 2-1/8"
Valve Retainer, v-port wings,
stainless steel, 2-1/8" 090-22-012-51
Valve Retainer, standard, stainless 090-22-018-34
steel, 1-3/4"
50c O-Ring, 13/16" x 1" 904173
Description
4" Model 441-S

Outlet Pressure Ranges – Spring and Diaphragm Combinations
Spring Diaphragm Size – Nominal Inside Diameter
Part Spring (Outside Diameter in parenthesis, Dim.“G” above)
Number Color 20" (23-1/8") 18" (20-5/8") 16" (18-5/8") 14" (16-3/8") 12" (14-3/4") 10" (13-1/8")
090-70-021-00 Aluminum 4
1⁄4" to 6" w.c. 4 1⁄4" to 4 3⁄4" w.c. 5 1⁄4" to 7" w.c. 7" to 10 1⁄2" w.c. 8 1⁄2" to 13" w.c.
090-70-021-01 Green 4 3⁄4" to 7" w.c. 4 3⁄4" to 6 1⁄2" w.c. 7" to 10 1⁄2" w.c. 8 1⁄2" to 12" w.c. 10 1⁄2" to 17" w.c.
090-70-021-02 Yellow 5 1⁄4" to 8 1⁄2" w.c. 6" to 10 1⁄2" w.c. 8 1⁄2" to 15 1⁄2" w.c. 10 1⁄2" to 17" w.c. 12" to 23" w.c.
090-70-021-03 Gray 8 1⁄4" to 13" w.c. 10 1⁄2" to 17" w.c. 14" w.c. to 1 psi 17" w.c. to 1 1⁄4psi 21" w.c. to 1 1⁄2 psi 1 1⁄4to 2 psi
090-70-021-04 Blue 9 1⁄2" to 20" w.c. 16 1⁄2" to 21" w.c. 21" w.c. to 1 3⁄4psi 21" w.c. to 2 psi 1 1⁄4to 2 1⁄2psi 1 1⁄2to 3 1⁄4psi
090-70-021-05 Red 1 1⁄2to 3 3⁄4psi 1 3⁄4to 4 psi 2 1⁄2to 6 psi
2" Model 441-S
3" Model 441-S
4" Model 441-S
Springs are colored for identification. When shipped, the regulator is equipped with the lightest spring suitable for the maximum outlet pressure
specified on order. If outlet pressure conditions change, replace spring accordingly to above table for best operation. For best performance use
the largest diaphragm for the spring and pipe size selected.
For pressures below 4" w.c. install the Model 441-S upside down.
M(Minimum Service Space)
Remove Vent
(If Required)
Vent
10 11
1
G
E60
Downstream
Control Line
Control
Connection
A
D
NF
Inlet
441-S
Outlet
(Minimum Service Space)
C
Bypass (If Required)
Regulator F (Face to Face)
Body Type 2" Pipe 3" Pipe 4"Pipe
Screwed 10" – –
Flanged ANSI 125 10" 11-3/4" 13-7/8"
Flanged ANSI 250 10-1/2" 12-1/2" 14-1/2"
Flanged ANSI 300 10-1/2" 12-1/2" 14-1/2"
Pipe Size DE GMN
of 441-S
2" 6" 24" See 5" 7"
3" 6" 24" Table 5" 7"
4" 9-1/2" 26" Below 5" 8"
© Sensus Metering Systems 2007 Made in USA
805 Liberty Boulevard
DuBois, PA 15801
800-375-8875
Fax: (814) 375-8460
www.sensus.com
Limited Warranty
Seller warrants the Goods to be free from defects in materials manufactured by Seller and in Seller’s workmanship for a period of (one(1) year) after tender of delivery (the “Warranty Period”). THIS LIMITED WARRANTY
(A) IS IN LIEU OF, AND SELLER DISCLAIMS AND EXCLUDES, ALL OTHER WARRANTIES, STATUTORY, EXPRESS OR IMPLIED, INCLUDING, WITHOUT LIMITATION,
ANY WARRANTY OF MERCHANTABILITY OR FITNESS FOR A PARTICULAR PURPOSE, OR OF CONFORMITY TO MODELS OR SAMPLES;
(B) does not apply to any Goods which have been (I) repaired, altered or improperly installed; (II) subjected to improper use or storage; (III) used or incorporated with other materials or equipment,
after Buyer or anyone using the Goods has, or reasonably should have, knowledge of any defect or nonconformance of the Goods; or (IV) manufactured, fabricated or assembled by anyone other than the Seller;
(C) shall not be effective unless Buyer notifies Seller in writing of any purported defect or nonconformance within (thirty (30) days) after Buyer discovers or should have reasonably discovered such purported
defect or nonconformance; and
(D) shall only extend to Buyer and not to any subsequent buyers or users of the Goods. Buyer shall provide Seller access to the Goods as to which Buyer claims a purported defect or nonconformance;
upon request by Seller, Buyer shall, at its own risk and expense, promptly return the Goods in question to Seller’s Plant.
Authorized Distributor:
Typical Arrangement and Dimensions (Indoor or outdoor Installation)
The 441-S should not be used for inlet pressures exceeding 100 psig.
Becken 02/07 3M
Table of contents
Other Sensus Controllers manuals
Popular Controllers manuals by other brands
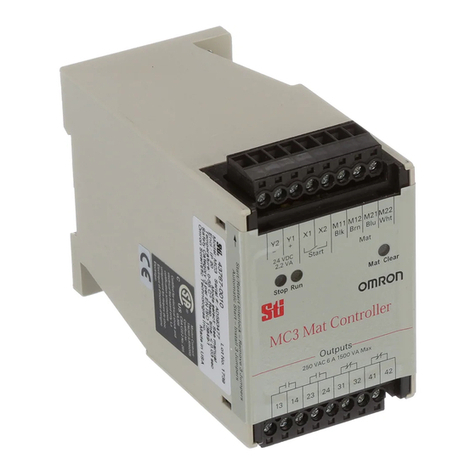
Omron
Omron MC3 Series Installation and operating manual
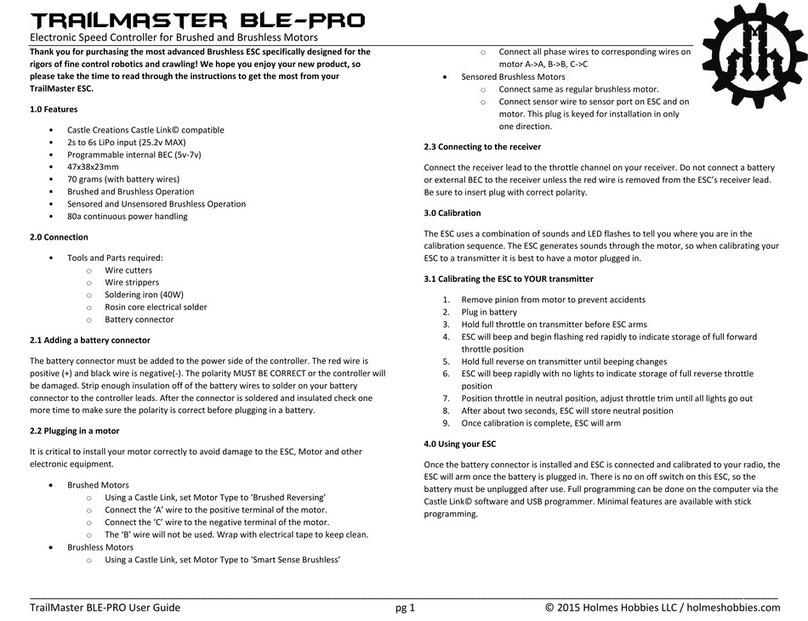
TrailMaster
TrailMaster BLE-PRO user guide
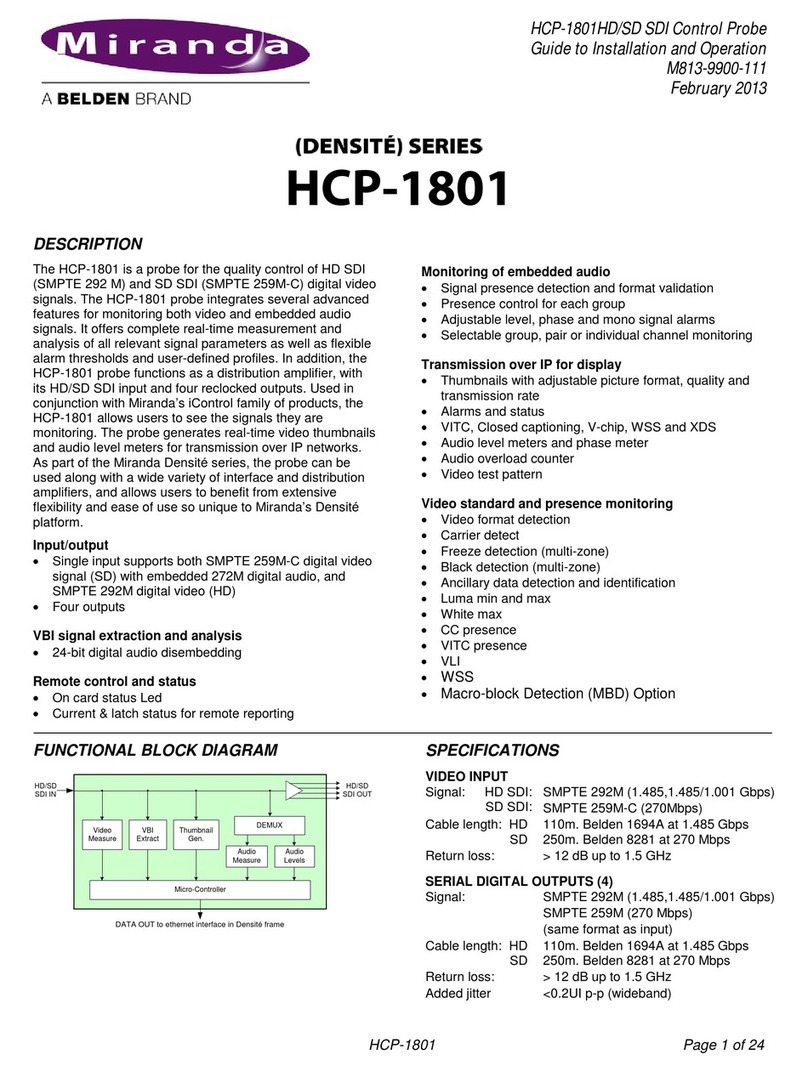
Belden
Belden Miranda DENSITE Series Guide to installation and operation
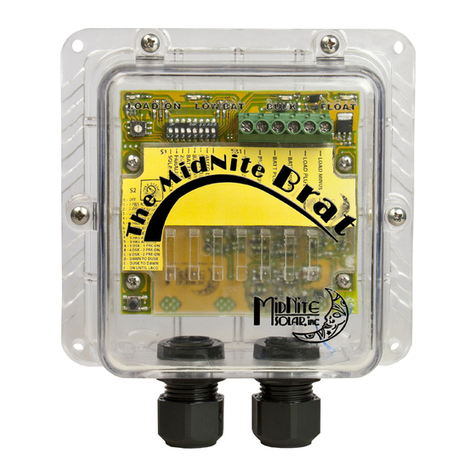
MidNite Solar
MidNite Solar Brat quick start guide
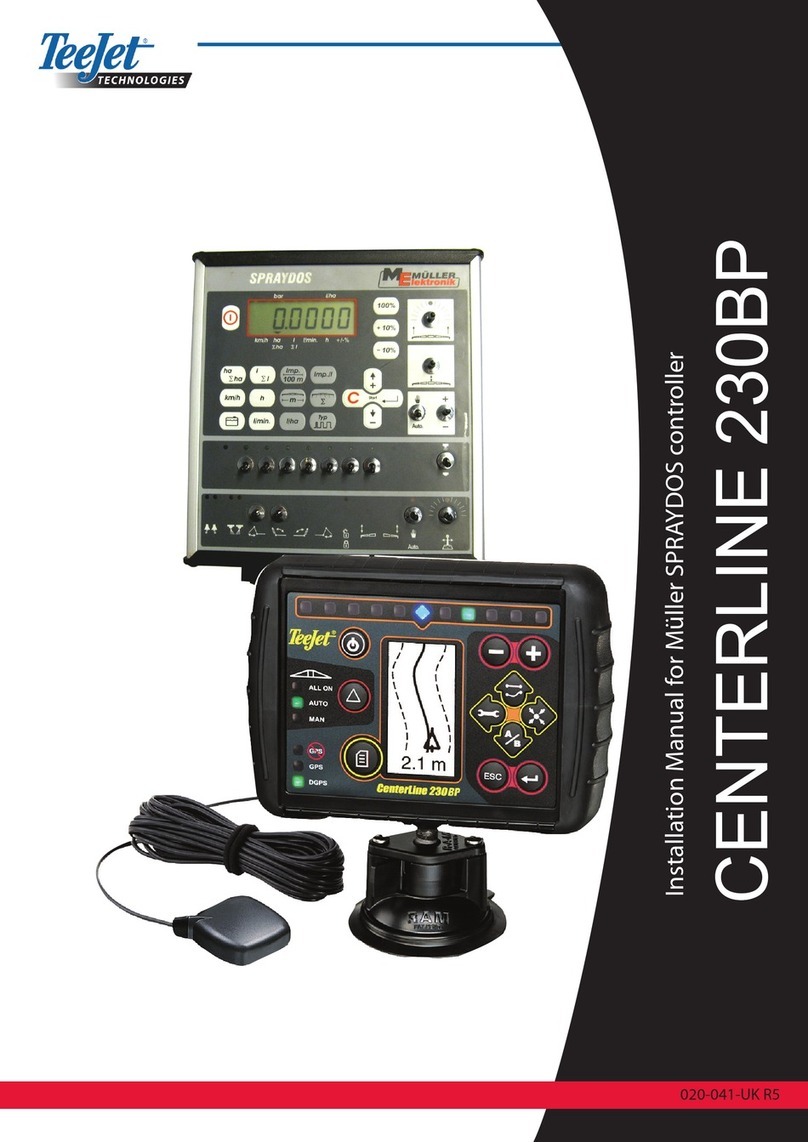
TeeJet Technologies
TeeJet Technologies Centerline 230BP installation manual
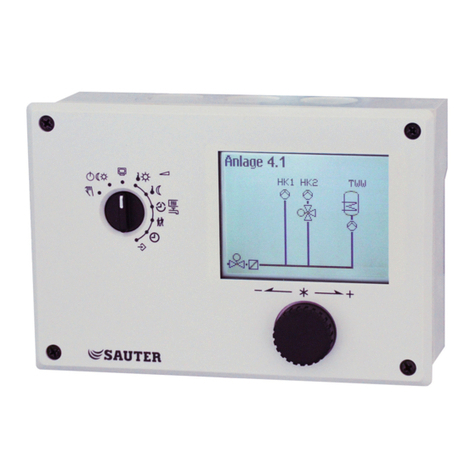
sauter
sauter EQJW146F002 Short manual