SFA ZPS 1.3 Service manual

Electronic pump control • Operation and assembly instructions
CONTROL BOX
ZPS 1.3
9001.3
11.19

English...................................... 3
Deutsch..................................... 17
Français .................................... 32
Italiano ..................................... 47
Nederlands................................ 62
Español..................................... 76
Português ................................. 91

CONTENTS
Copyright / Disclaimer - Control Box ZPS 1.3 Installation and Maintenance Manual - Original operating instructions
All rights reserved. The contents of this document must not be reproduced, modified or disclosed to third parties except upon writ-
ten consent from the manufacturer. This document may be subject to change without notice.
Status of the operating instructions: November 2019
1. SAFETY...........................................................pg.4
2. GENERAL INFORMATION............................pg.4
2.1 Areas of application.............................................pg.4
2.2 General characteristics .........................................pg.5
2.3 Technical data .....................................................pg.5
3. OPERATION OF THE CONTROL SYSTEM...pg.6
3.1 Operator control panel and operational elements ....pg.6
3.1.1 Key ..............................................................pg.6
3.1.2 Indications on the display................................pg.7
3.1.3 Normal operation ..........................................pg.7
3.1.4 Parameter setting ...........................................pg.8
3.1.5 Information retrieval .....................................pg.11
3.1.6 Warnings and notices of malfunction..............pg.11
3.2 Assembly and electrical connections.....................pg.12
3.2.1 Mechanical fixings.......................................pg.12
3.2.2 Mains connection.........................................pg.12
3.2.3 Connection of the pump motor.......................pg.13
3.2.4 Connection of the external sensors .................pg.14
3.2.5 Signal contacts ............................................pg.15
3.2.6 Utilisation of the internal sensor .....................pg.15
3.3 Commissioning of the control system.....................pg.15
4. DISPOSAL................................................... pg.16

4
1. SAFETY
WARNING
This device can be used by children who are at least 8 years old
and by people with reduced physical, sensory or mental capacities
or those without knowledge orr experience, if they are properly
supervised or if they have been given instrcutions on safely using
the device and the associated risks have been understood. Children
should not play with the device. Children should not clean or perform
manintenance ont he device without supervision.
ELECTRICAL CONNECTIONS:
The electrical installation must be done by a qualified electrical engineer.
The device's power supply must be connected to ground (class I) and protect-
ed by a high sensitivity differential circuit breaker (30 mA). Devices without
plugs must be connected to a main switch on the power supply which discon-
nects all poles (contact separation distance of at least 3 mm). The connection
must be used exclusively to provide the power to the product.
If the power cord is damaged, to prevent possible danger, it must be replaced
by the manufacturer, customer service team or a similarly qualified individual.
Labelling of notes in the operating instructions
Danger
This term defines a high risk of danger, which can lead to death or serious
injury, if not avoided.
WARNING
Warning
This term defines a hazard which could cause a risk to the machine and its
operation, if it is not taken into account
Dangerous area
This symbol characterises hazards that could lead to death or injury.
Dangerous voltage
This symbol characterises dangers associated with the voltage and provides
information on voltage protection.
Property damage
This symbol, in combination with the keyword ATTENTION, characterises
dangers to the machine and its proper operation.
2. GENERAL INFORMATION
2.1 Areas of application
The single pump control system ZPS 1.3 is principally used for the regulation of liquid levels. For

5
this, various sensors for level measurement can be used: floating switches, dynamic pressure,
air bubble level measurement systems, external 4 - 20mA- sensors. The respective sensors to be
employed can be selected via the control program. Then pump are directly activated by the motor
contactors. Furthermore, the following devices for the error messages will be available: acoustic
signaler, 4 relay alarm contacts potential-free (programmable for: high-water, combined fault,
pump on, pump malfunction, unit working to specification), safety circuits in the form of a turn-on-
and a turn-off-delay, motor current monitoring systems, motor temperature monitoring systems and
flood control sensors guarantee a safe operation of the pump station.
The control system is operated via 6 short travel key switches, the program settings are displayed
on an LCD display. All settings are saved so that they are available when the control system is
restarted. The display language can be changed.
Besides the actual operational parameters, the control system also saves the controlling process
and the pump malfunctions in a record which can be displayed on the LCD display.
2.2 General characteristics
• Clear LCD display
• Hand- Stop- Auto- Function
• 1 acknowledgement button, 2 parameter
select buttons
• Menu which can be switched through
• Internal acoustic alarm
• Programmable operation and collective fault
signal potential-free
• Floating flood control potential-free
• Omnibus fault message potential-free
• Setting via short travel key switches
• Operating hours counter
• Maintenance interval counter
• Pump start counter
• Recording of fault protocol
• Electronic monitoring of the motor current
• Programmable turn-on-delay
• Programmable pump follow-up
• Programmable pump changeover interval
• Switchable service- and ATEX- mode
• Internal pressure sensor
• Level indication in cm
• 2 digital inputs for the thermostatic switch
• 3 digital inputs for the floating switch or reed
sensor
• 1 analogue input for transmitter 4-20mA
• 1 analogue pressure input 0-100(500) mBar
2.3 Technical data
Operating voltage 230V or 400V/AC/50-60 Hz
Voltage of control system 230V/AC/50-60 Hz
Power consumption env. 6VA
Pressure range 0-1mWs
Turn-on-delay 0-180 sec
Follow-up time 0-180 sec
Runtime monitoring 0-300 sec
Motor current limitation 0.5- 14A
Fault protocol memory 32 memory positions
Maintenance interval counter 0 – 365 days, adjustable
Operating temperature range -20 - +60°C
Dimensions 180x180x90 mm
Max. pre-fuse 20A
Potential-free alarm contact 3 A max.
Degree of protection IP 65
Housing Polycarbonate

6
3. OPERATION OF THE CONTROL SYSTEM
The electronic control box is equipped with a key lock. To unlock, please press
and hold (Selection) for 3 seconds. There will be an indication in the display.
Approximately 1 minute after the last actuation of any key the keyboard gets
relocked.
The automatic key lock after 1 minute can be disabled in the menu to facilitate
setting, for example, with maintenance. The automatic key lock is enabled
with the service mode switched-off only.
3.1 Operator control panel and operational elements
3.1.1 Key
(MANUAL)
By pressing this key, the preferred pump is switched on without delay. No other
function of the program is enabled.
The green LED ③of one pump flashes. ATTENTION : If the ATEX mode is enabled,
the pump can only be started if the turn-on level is exceeded !
The green LED is flashing. ATTENTION : The pump will be switched after 2
minutes. A restart of the pump is possible immediately.
Stops the pump motor without follow-up. The green LED goes out.
The pumps are actuated via the level evaluation of the selected sensor (see
point 3.1.4). All monitoring and safety functions are executed according to the
presetting.
③Signal-LED indicating when the pump is
operating :
- green: pump is on
- red: error
② Short travel
key switches
① LCD display
(2 lines with 16
characters)

7
By pressing one of these two keys, the menu is switched to the next menu item in
the indicated direction.
If the menu is enabled, (see key SELECTION ), the set values can be modified
via those keys (some modifications are only possible in the operating mode
“Stop”). The more you press the key, the faster it scrolls.
(Selection/
Stop)
By pressing this key, the set values in the active menu are enabled. The activated
text is starting to flash (modification mode) and can be modified by usin
g
.
By repeatedly pressing these keys, the set value becomes permanent (flashing
stops), which means that it will be saved even if the control system is turned off.
3.1.2 Indications on the display
Normal operation :
During operation of the control system, the upper line of the LCD display indicates the actual liquid
level or the switching status of the floating switch. In the lower line of the display, information about
the actual operational status of the control system of the pump will appear. When the pump is
running, the motor current and the operating condition are displayed alternately. In case of failure,
the actual failure status is displayed (see point 3.1.6). The red LEDs of the pump will be seen red
flashing light.
Parameter setting :
In the upper line, the designation of the parameter is displayed; the lower line displays the current
value of the parameter. The values can be modified by using the keys and as described
in 3.1.1.
Information retrieval :
Information values such as maintenance intervals, operating hours, pump starts and error list can
be displayed and modified in the same way as the control parameters. The error list can save up
to 32 records respectively. The recording is carried out by means of a shift register, which means
that the earliest error is deleted automatically.
3.1.3 Normal operation
During normal operation, the three operating modes are indicated on the display as follows.
Pressed key 2nd line on display Signification
Hand 1 P1 4,7A The pump P1 has been switched on manually.
Stop 1 P1 0,0 A The pump motor is switched off. The level evaluation,
including the flood control, remains enabled.
The pump motor is not activated during
flooding alarm.
Auto 1 P1 4,7A The pump is switches on or off, according to the level
requirement. Here, pump P1 is active at the moment.
WARNING

8
3.1.4 Parameter setting
The following table shows the setting options and the effects of the individual parameters. A
parameter can be selected via the menu selection (see point 3.1.1).
For reasons of safety, the modification mode for the parameters can
only be enabled in the ‘Stop’- operation (key ).
1st line on display 2nd line on display
(set value) Signification
base load OFF Pump off ≤ Pump on Stop level pump
Modifications only during Stop-
operation!
base load ON Start level pump
Modifications only during Stop-
operation!
high water
(High water HW)
Peak load on < HW
And
HW ≤ final value of level
sensor
Flooding- alarm- level
Additionally, this level is constantly
evaluated on the input for the
floating switch HW, independent
from the selected level transmitter.
Thereby, if necessary, 2 different
HV-levels can be realised with 2
different transmitters.
Modification only possible in Stop-
mode !
run-time
(Run-time change after)
is deactivated
until 300 sec.
At transgression of the adjusted time the
pump is stopped shortly.
‘DEACTIVATED’ effects that the pump run is
not stopped abruptly.
This function eliminates potential
accumulations of air in the pump.
Here unto a time above the normal pump-
down time has to be adjusted. A switch
occurs if the requested pump has not
pumped down under the switch-on point
within the adjusted time. After 3 consecutive
the error ‘TIME’ occurs.
WARNING
WARNING

9
1st line on display 2nd line on display
(set value) Signification
delay time 0 to 180 sec The turn-on delay of the pump only functions
after a restart of the control system (e.g.
after a power failure). With “normal” switch
operation via the levels N1 and N2, this
setting is not relevant.
This function may be used to avoid the
simultaneous switch-on of several pumping
station after mains failure.
overrun 0-180 sec. After having reached the turn-off level, the
pump is still running for the adjusted amount
of time.
max. current.
P1
0,0 to 14,0 A If the adjusted value is reached, the
monitoring system of the pump motor current
effectuates the shutdown of the pump,
accompanied by a notice of malfunction.
The malfunction has to be acknowledged
manually by pressing the key .
Attention : If the nominal current is
adjusted to 0 A no monitoring of the motor’s
charging rate occurs !
24 hours start is activated
is deactivated
The pump P1 is briefly started if no request
occurs by the switch-on level within 24
hours.
If the ATEX mode is enabled, the 24h
starting is only taking place if the turn-off
level is exceeded.
acoustic alarm is activated
is deactivated
The internal acoustic transmitter is switched
on or off. This setting has no influence on
the potential-free alarm signal.
interval alarm is activated
is deactivated
The alarm relay for the non-floating alarm
contact is synchronized or produces a
permanent signal.
Therm. fault
Thermostatic switch
P1 TH1 control loop
TH2 control loop
is activated The evaluation of the thermal contacts TH1
(control loop) can be deactivated. If this
contact is open, the pump is shut down
and an error is signalled. After the contact
TH1 (control loop) has cooled down and
been closed again, the pump restarts
automatically.
After cooling down, the activation of the
pump in case of malfunction TH2 can
only be effected by acknowledging the
malfunction by pressing the key .
This contact can not be deactivated by
means of the software. If the pump is not
equipped with thermal contacts, a bridge
has to be inserted as a substitution for TH2.

10
1st line on display 2nd line on display
(set value) Signification
phase error is activated
is deactivated
The energization of all the 3 phases and the
proper phase sequence at the mains input
are monitored.
To be disabled for 230 V pumps.
ATEX - Mode is activated
is deactivated
If the ATEX mode is enabled, it is not
possible to switch on the pump if the turn-off
level is under-run. This also applies for the
HAND function and the 24h starting.
service mode is activated
is deactivated
If the service mode is disabled, it is
not possible to set the parameters. The
modification mode is only possible for the
service mode itself.
level controller
(=Level control)
intern. converter
float switch
4-20mA Interface
Level measurement via dynamic pressure
measurement
Level measurement via floating switch
Level measurement via external sensor
intern. converter matching
(=calibration) By pressing the key sequence
, the zero point of
the internal converter is adjusted. The
adjustment has to be carried out while
the pilot tube is emerged (with barometric
pressure). This adjustment is to be carried
out by a service technician only.
20 mA => level 1 - 1250 cm Final value of the sensor at 20 mA
Signal contact 1-4 Possible signals :
- Fault high water
- Collective fault
- Pump 1 on
- Pump 2 on
- Fault pump 1
- Fault pump 2
- system OK
Kind of signal on contacts 1-4
The collective fault signal can be timed
Language Deutsch, English, etc... Setting of the menu language
DD.MM.YYYY hh:mm see adjustments Date and time
keylock on
off
When the service mode is disabled, if the
keylock function is on, the screen locks after
3 minutes on the Home screen. To enter the
menu, press for 3 seconds.
WLAN reset disabled
Fault protocol DD.MM YYYY default After having pressed the key
the protocol can be paged through by
pressing the keys .
It is not possible to change the data.

11
3.1.5 Information retrieval
The following table shows the signification of the operational data of the control system :
1st line on display 2nd line on display
(informational value) Signification
up time hours: X
(in hours)
Shows the cumulative operating times
of the control system in hours. The
value can be reset to 0 by pressing
the keys .
total pump hours P1 XXXX
(in hours)
Shows the cumulative runtimes of the
pumps in hours. The value can be
reset to 0 (separately for both pumps)
by pressing the keys .
pump starts P1 XXXX
(in number)
Shows the number of pump starts. The
value can be reset to 0 (separately
for both pumps) by pressing the keys
.
next maintenance within days:XXXX
(in days)
Shows the number of days until the
next maintenance. The information
is saved at intervals of 4 hours. The
initial value can be preset between
365 and 0 days.
3.1.6 Warnings and notices of malfunction
The following warnings and notices of malfunction can be indicated on the display. In the fault
protocol, the according data will be recorded :
2nd line on
display Signification Alarm Protocol
signal
Fault load
Current flow below 0,5 A. Either
no pump is connected, or a
phase is lacking.
This malfunction can be suppressed, if for the
motor current monitoring 0.0A are set in the menu
“current limitation“.
If both pump currents are set
to 0,0A, the control system is
running in the test mode. The
pumps are not deactivated. All
functions of the control system
are enabled. The motor current
is not monitored.
Yes Last

12
2nd line on
display Signification Alarm Protocol
signal
Fault pump 1 The motor current monitoring system has detected
an exceedance of the set limit value and has shut
down the pump motor.
Yes IP1
Fault high water The HW-sensor reports an alarm and switches on
the pump. The HW-malfunction acknowledges itself
when the turn-on level is reached.
Yes HW
Fault I<3mA The external sensor is selected, but the current
is <3mA. There might be a disconnection, or
the sensor might be defective. The malfunction
acknowledges itself when the sensor current is
within the normal range.
Yes I<3mA
Fault SW The floating switches are connecting in the wrong
sequence (e.g. the lower floating switch is open
when the upper floating switch closes).
Yes SW
Pump
Fault TH1
Fault TH2
Activation of the thermal control of the pump
motor. The malfunction TH1 acknowledges itself
after the motor has cooled down; TH2 has to be
acknowledged manually.
Yes Pump
TH1
TH2
Phase error A phase of the power supply has failed. Yes Dreh
Fault ATEX The ATEX mode is activated and the level is below
the switch-off point of the selected pump. Yes Atex
Run-time alarm The runtime monitoring of the pump has been
exceeded 3 times in succession. Yes Time
3.2 Assembly and electrical connections
All electrical connections are to be established by an authorised
professional only. Settings and adjustments on the control system
as well as the commissioning of the control system are to be
carried out by qualified persons only.
3.2.1 Mechanical fixation
The control system has to be fixed on an even surface. In order to fasten the control system, the
housing cover has to be opened.
3.2.2 Mains connection
The left cable gland is intended for the cable entry of the mains cable. The separate cables are
to be clamped into the spring terminals in the manner described below. According to the motor
which is used, a single-phase or a three-phase connection can be established.
The power supply has to be secured by an independent all-pole
fuse which can be switched off (max. 20 A).

13
3.2.3 Connection of the pump motor
Either mono-phase or three-phase motors may be connected according to the connection diagram
shown below.
Connection of a 3-phase Motor :
Connection of a single-phase Motor with internal capacitor :
Mains connection
Pump1
Protective conductors
Mains connection
Pump1
Protective conductors
Net
For 230V pumps, a bridge between N-L2 is required in the mains connection.

14
Connection of a single-phase Motor with external capacitor :
3.2.4 Connection of the external sensors
The external sensors are connected by means of the terminal strip on the upper circuit board.
The active sensor can be selected in the menu “level control” and “therm. malfunction”.
If the thermostatic switch TH2 is not necessary, a bridge has to be inserted on this contact point.
The thermostatic switch TH1 can be deactivated via the menu therm. malfunction.
Mains connection
Protective conductors
Net
Pump1
For 230V pumps, a bridge between N-L2 is required in the mains connection.

15
The floating switches have to close when they are floating on the surface. The floating switches
have to be connected floatingly. The required signal voltage is generated in the control system and
amounts to 5V.
Assignment of the float switches:
SWN1 = pump off
SWN2 = pump on
SWHW = high water alarm
For the usage in explosion-prone areas, either floating switches with the
corresponding permission, or intrinsically safe cut-off relays have to be
used.
The external sensor has to supply a measurement current between 4
and 20mA. The final value of 20 mA can be adjusted in the menu, so the
indication may occur in cm.
3.2.5 Utilisation of the internal sensor
A pressure sensor of 0 to 10 kPa is used as an internal sensor (0 to 1mWs, 0 to 100 mbar). Other
measurement ranges can be realised on demand. On the lower side wall, a hose screw connection
6/8mm is located which is intended for the connection of the immersion pipe. The sensor used
is designed as a differential pressure converter, so that barometric variations are eliminated. The
menu item “internal converter – adjustment” serves for the accurate adjustment of the zero point.
In order to equalise possible air leaks inside the pneumatic level
measuring device, the pilot tube has to be fully emerged from the water
after completion of the pumping process. For this purpose, the adjustment
of a follow-up time of the according duration is necessary. Alternatively,
the small-size compressor set for the air bubbler level measurement
system can be used.
3.2.6 Signal contacts
The 4 potential-free signal contacts are located in the upper circuit board (left).
The 4 signal contacts are free and programmable: the contacts 1 and 2 are opened in case of
power failure and the contacts 3 and 4 are closed in case of power failure.
If the power supply of the control is correct, then the signal contacts are closed in case of a fault
or signal.
3.3 Commissioning of the control system
After the complete connection of the pump cables, the mains power supply and the level sensor,
the parameters can be set after the mains voltage has been applied. Only trained personnel are
allowed to set those parameters.
Now the plant can be commissioned by pressing the key . During the conduction of several
test runs, the set switch points have to be checked, and, if necessary, corrected.

16
Checking of the control system without pumps :
In order to be able to check the control system without a pump, the following standard settings are
required :
1. Connect the control system to a single-phase network (connection of N and L1)
2. Set motor current limitations for both pumps to 0.0 A
3. Switch off rotary field
4. Bridge thermal contacts TH2
5. Disable thermic error for the pump.
If the respective level sensors are connected, all program functions can be checked without having
to connect the pump.
4. DISPOSAL
Only for EU-countries
Do not dispose of the control system with the regular household waste!
According to the European directive 2012/19/EG about waste electric and
electronic equipment and the transposition into national law, used electric tools.
have to be collected separately and recycled in an environmentally compliant
manner.

Contact Information
SFA Australia Pty Ltd Unit
10, 25 Gibbes Street,
Chatswood NSW 2067
Phone +1300 554 779
E: GENERAL ENQUIRIES
E: TECHNICAL
SUPPORT
Table of contents
Popular Controllers manuals by other brands

Nordson EFD
Nordson EFD ValveMate 7140 operating manual
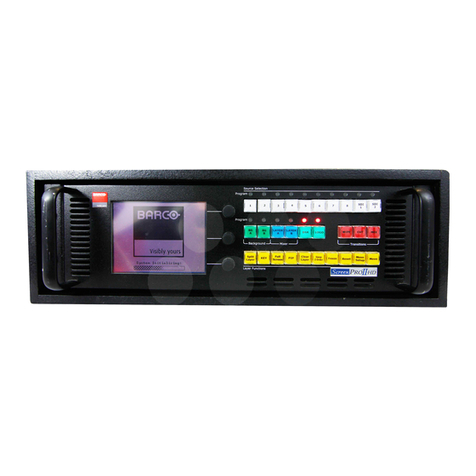
Barco
Barco ScreenPRO II quick start guide

Mitsubishi Electric
Mitsubishi Electric MELSEC FX Series Beginners manual
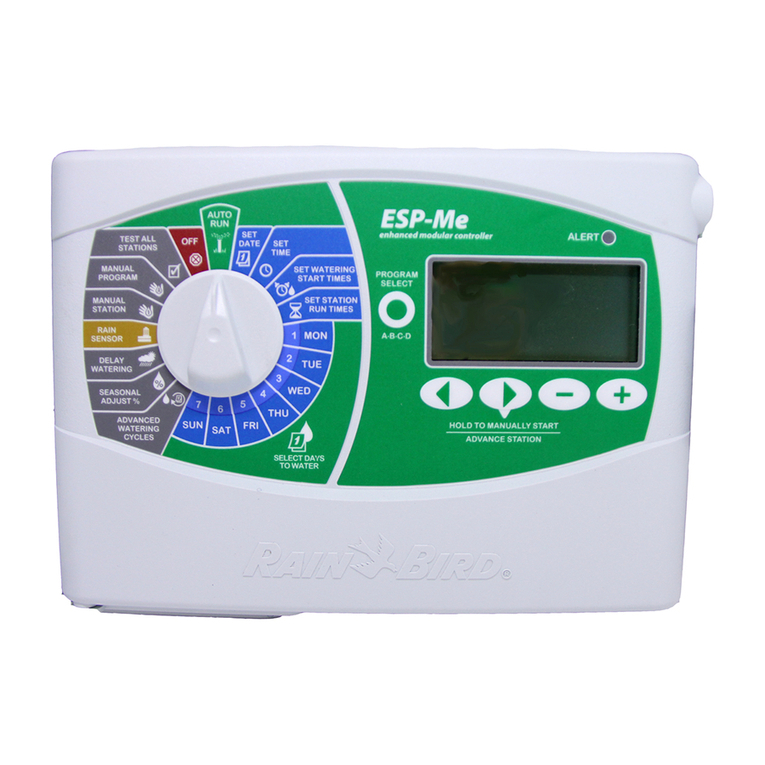
Rain Bird
Rain Bird ESP-Me Advanced user's manual

Kenwood
Kenwood KOS-A210 instruction manual
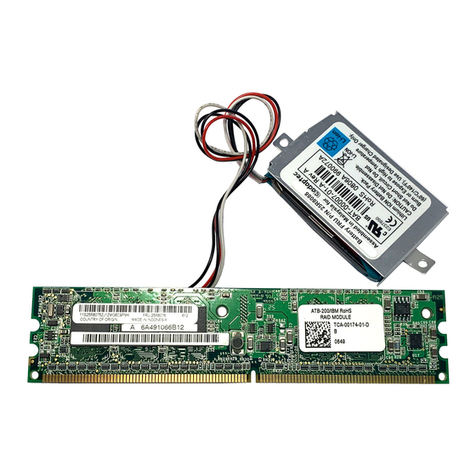
IBM
IBM ServeRAID-8 Series Best Practices and Maintenance Information
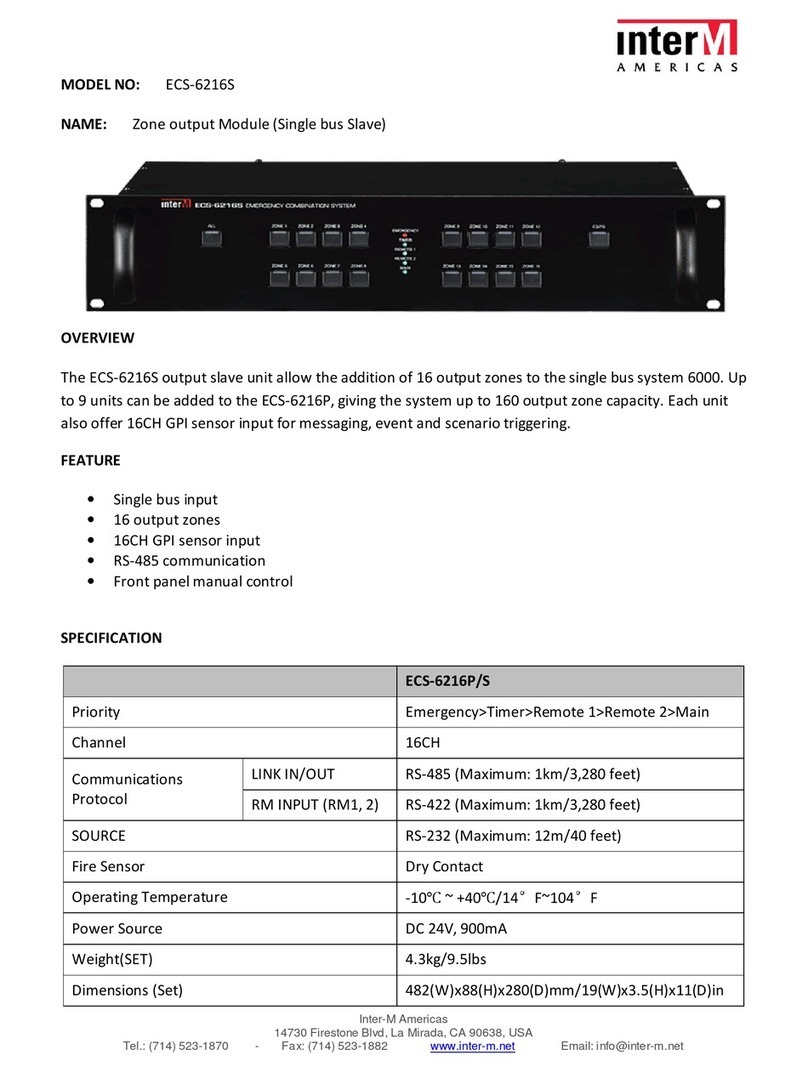
Inter-m
Inter-m ECS-6216S overview
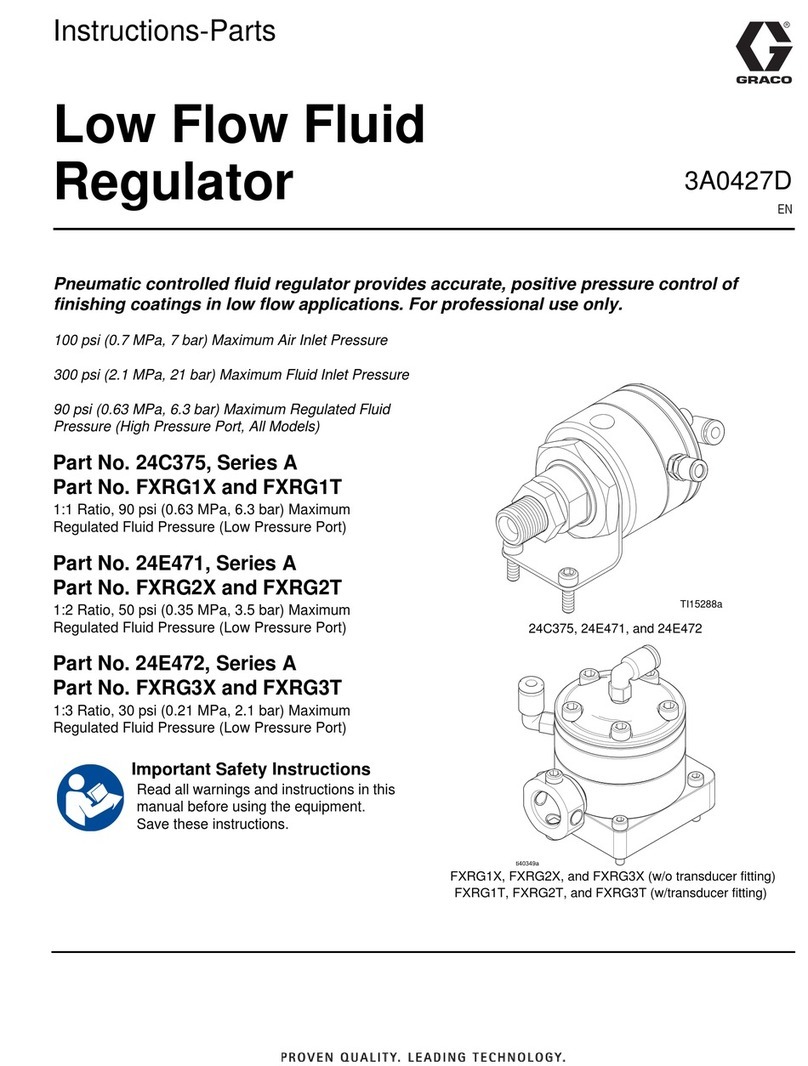
Graco
Graco Series A Instructions - parts
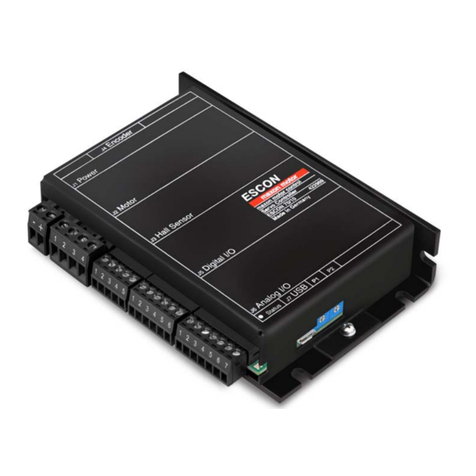
maxon motor
maxon motor ESCON 70/10 Hardware reference
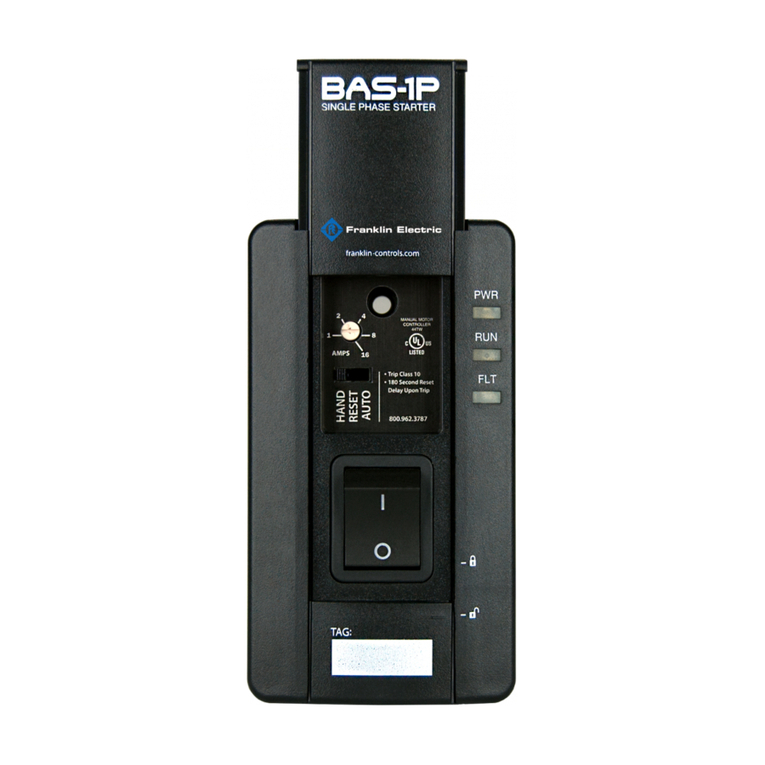
Franklin
Franklin BAS-1P Installation & operation guide
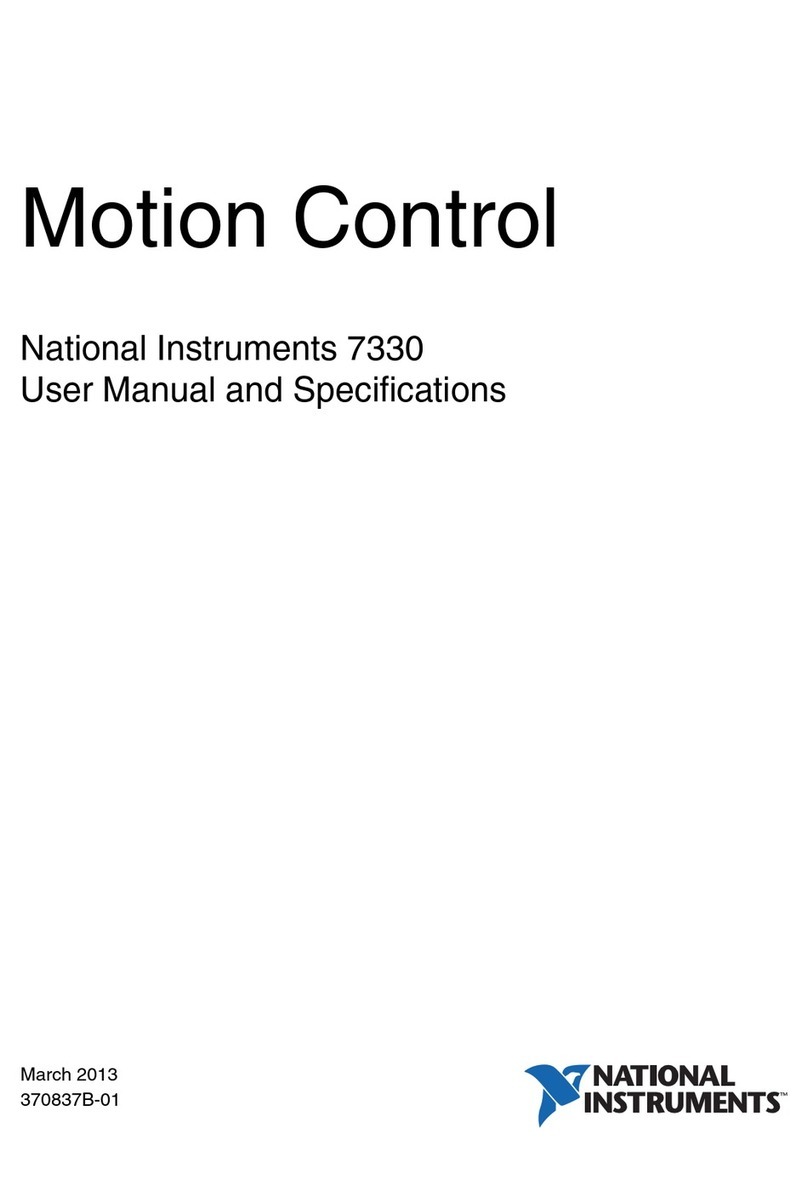
National Instruments
National Instruments 7330 User manual and specifications
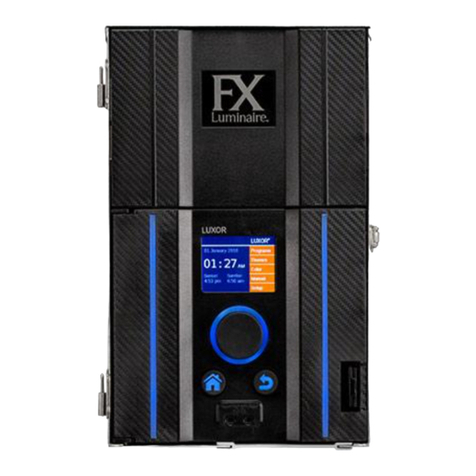
FXLuminaire
FXLuminaire Luxor quick start guide