Sharp MODEL R-2197 User manual

R-2197
SHARPCORPORATION
SERVICEMANUAL
S9811R2197PJ/
MICROWAVE OVEN
MODEL R-2197
In interests of user-safety the oven should be restored to its
original condition and only parts identical to those specified
should be used.
TABLE OF CONTENTS Page
CAUTION, MICROWAVE RADIATION............................................................................................................. 1
WARNING..........................................................................................................................................................1
PRODUCT SPECIFICATIONS ......................................................................................................................... 2
GENERAL INFORMATION................................................................................................................................2
APPEARANCE VIEW ....................................................................................................................................... 3
OPERATION SEQUENCE................................................................................................................................ 4
FUNCTION OF IMPORTANT COMPONENTS ................................................................................................ 5
SERVICING ...................................................................................................................................................... 6
TEST PROCEDURE ......................................................................................................................................... 8
TOUCH CONTROL PANEL ASSEMBLY ........................................................................................................14
COMPONENT REPLACEMENT AND ADJUSTMENT PROCEDURE ........................................................... 21
MICROWAVE MEASUREMENT .................................................................................................................... 27
WIRING DIAGRAM ......................................................................................................................................... 28
PICTORIAL DIAGRAM ................................................................................................................................... 29
CONTROL PANEL CIRCUIT ...........................................................................................................................30
PRINTED WIRING BOARD .............................................................................................................................31
PARTS LIST ................................................................................................................................................... 32
1000W/ R-2197
DEF
ON
NO.
X2
CHECK

R-2197

R-2197
1
SERVICEMANUAL
MICROWAVE OVEN
R-2197
GENERAL IMPORTANT INFORMATION
This Manual has been prepared to provide Sharp Corp. Service
engineers with Operation and Service Information.
It is recommended that service engineers carefully study the entire
text of this manual, so they will be qualified to render satisfactory
customer service.
CAUTION
MICROWAVE RADIATION
Service engineers should not be exposed to the microwave
energy which may radiate from the magnetron or other micro-
wave generating devices if it is improperly used or connected.
Allinputandoutputmicrowaveconnections,waveguides,flanges
andgasketsmustbesecured.Neveroperatethedevicewithout
a microwave energy absorbing load attached. Never look into
an open waveguide or antenna while the device is energized.
WARNING
Never operate the oven until the following points are ensured.
(A) The door is tightly closed.
(B) The door brackets and hinges are not defective.
(C) The door packing is not damaged.
(D) The door is not deformed or warped.
(E) There is not any other visible damage with the oven.
Servicing and repair work must be carried out only by trained
service engineers.
Allthe partsmarked"*"onparts listareusedatvoltages morethan
250V.
Removal of the outer wrap gives access to potentials above 250V.
All the parts marked "∆" on parts list may cause undue microwave
exposure,bythemselves, orwhen they aredamaged, loosenedor
removed.
SHARP CORPORATION
OSAKA, JAPAN
PRODUCT SPECIFICATIONS
GENERAL INFORMATION
APPEARANCE VIEW
OPERATING SEQUENCE
FUNCTION OF IMPORTANT
COMPONENTS
SERVICING AND
TROUBLESHOOTING GUIDE
TEST PROCEDURE
TOUCH CONTROL PANEL
COMPONENT REPLACEMENT
AND ADJUSTMENT PROCEDURE
MICROWAVE MEASUREMENT
WIRING DIAGRAM
PARTS LIST

2
R-2197
GENERAL INFORMATION
WARNING
THIS APPLIANCE MUST BE EARTHED
IMPORTANT
THE WIRES IN THIS MAINS LEAD ARE COLOURED IN ACCORDANCE WITH THE FOLLOWING CODE:
GREEN-AND-YELLOW : EARTH
BLUE : NEUTRAL
BROWN : LIVE
PRODUCT DESCRIPTION
SPECIFICATION
ITEM DESCRIPTION
Power Requirements 230 - 240 Volts
50 Hertz
Single phase, 3 wire earthed
Power Output
1000 W nominal of RF microwave energy (measured by method of IEC 705)
Operating frequency 2450 MHz
Case Dimensions Width 520 mm
Height 309 mm including foot
Depth 406 mm
Cooking Cavity Dimensions Width 351 mm
Height 211 mm
Depth 372 mm
Control Complement Touch Control System
Timer (0 - 99 minutes and 99 seconds)
Microwave Power for Variable Cooking
Repetition Rate;
P-HI...........................................Full power throughout the cooking time
P-90 .............................................................approx. 90% of Full Power
P-80 .............................................................approx. 80% of Full Power
P-70 .............................................................approx. 70% of Full Power
P-60 .............................................................approx. 60% of Full Power
P-50 .............................................................approx. 50% of Full Power
P-40 .............................................................approx. 40% of Full Power
P-30 .............................................................approx. 30% of Full Power
P-20 .............................................................approx. 20% of Full Power
P-10 .............................................................approx. 10% of Full Power
P-0 .............................................No power throughout the cooking time
DOUBLE QUANTITY pad
EXPRESS DEFROST pad
Number pads
SELECT TIME pad
STOP/CLEAR pad
SELECT POWER pad
START pad
SET pad
CHECK pad
SIGNAL pad
Set Weight Approx. 17 kg

R-2197
3
APPEARANCEVIEW
1. Digital Readout
2. DOUBLE QUANTITY pad
3. EXPRESS DEFROST pad
4. Number pads for time and memory program-
ming
5. SELECT TIME pad
6. STOP/CLEAR pad; touch to stop operation of
oven and clear remaining heating time
7. SELECAT POWER pad for setting variable
power level
8. START pad; touch to operate oven after door
is closed and time is set
9. SET pad for setting memory
10.CHECK pad for checking memory
11.SIGNAL pad for setting signal sound
OVEN
1. Oven light
2. Ceramic shelf
3. Control panel
4. Cavity face plate
5. Door latch openings
6. Door latches
7. Door hinges
8. Door seals and sealing surfaces
9. Door handle
10.Ovendoorwithsee-throughwindow
11.Air ventilation cover and openings
12.Power supply cord
13.Air intake openings
14.Outer case cabinet
TOUCH CONTROL PANEL
12 11
710
9
54 3
13 14
8
1
2
6
DEF
ON
NO.
X2
CHECK
1
3
4
6
8
11
2
5
7
9
10

4
R-2197
OPERATION SEQUENCE
OFF CONDITION
Closing the door activates the 1st. latch switch, 2nd. latch
switch and stop switch.
IMPORTANT:
When the oven door is closed, the contacts COM-NC
of the monitor switch must be open. When the mi-
crowave oven is plugged in a wall outlet (230 - 240V
50Hz), the line voltage is supplied to the noise filter
and the control unit.
Figure O-1 on page 28
1. The oven display will show . .
MICROWAVE COOKING CONDITION
ProgramdesiredcookingtimebytouchingSELECTTIME
pad and the NUMBER pads. When the START pad is
touched, the following operations occur:
Figure O-2 on page 28
RELAY CONNECTED COMPONENTS
RY-2 power transformer
RY-3 oven lamp/antenna motor/fan motor
1. The line voltage is supplied to the primary winding of
thehighvoltagetransformer. The voltageisconverted
to about 3.3 volts A.C. output on the filament winding
and high voltage of approximately 2300 volts A.C. on
the secondary winding.
2. The filament winding voltage (3.3 volts) heats the
magnetronfilamentandthehighvoltage(2000volts)is
senttothevoltagedoubling circuit, where it isdoubled
to negative voltage of approximately 4000 volts D.C..
3. The 2450 MHz microwave energy produced in the
magnetron generates a wave length of 12.24 cm. This
energyischannelledthroughthewaveguide(transport
channel)intothe oven cavity,wherethe food isplaced
to be cooked.
4. Whenthecookingtimeisup,asignaltoneisheardand
the relays RY2 + RY3 go back to their home position.
Thecircuitstotheovenlamp,highvoltagetransformer,
fan motor and antenna motor are cut off.
5. Whentheoven door isopenedduring a cookingcycle,
the switches come to the following condition.
Switch Contact Condition
During Oven Door
Cooking Open(No cooking)
1st. latch switch COM-NO Closed Opened
2nd.
latch switch COM-NO Closed Opened
Stop
switch COM-NO Closed Opened
Monitor Switch COM-NC Opened Closed
Thecircuittothehighvoltagetransformer,fanmotor,oven
lamp and antennamotor are cut off when the 1st. latch
switch, 2nd. latch switch and stop switch are made open.
Shown in the display is remaining time.
6. MONITOR SWITCH CIRCUIT
The monitor switch is mechanically controlled by the
oven door, and monitors the operation of the 1st. latch
switch, the 2nd. latch switch and the relay RY2.
6-1. When the oven door is opened during or after the
cycleofacookingprogram, the 1st. latch switch2nd.
latchswitch andstopswitchmustopentheircontacts
first. After that the contacts (COM-NC) of the monitor
switch can be closed.
6-2. When the oven door is closed, the contacts (COM-
NC) of the monitor switch must be opened. After that
thecontactsofthe1st. latch switch, 2nd.latchswitch
and stop switch are closed.
6-3. Whentheovendoorisopenedandthecontactsofthe
1st. latch switch, 2nd. latch switch and the relay RY2
remain closed, the fuse M10A will blow, because the
monitorswitchisclosed andashortcircuitiscaused.
POWER LEVEL P-0 TO P-90 COOKING
When Variable Cooking Power is programmed, the line
voltageissupplied tothepower transformer intermittently
through the contacts of relay (RY-2) which is operated by
the control unit within a 32 second time base. Microwave
power operation is as follows:
VARI-MODE ON TIME OFF TIME
Power 10(P-HI) 32 sec. 0 sec.
(100% power)
Power 9(P-90) 30 sec. 2 sec.
(approx. 90% power)
Power 8(P-80) 26 sec. 6 sec.
(approx. 80% power)
Power 7(P-70) 24 sec. 8 sec.
(approx. 70% power)
Power 6(P-60) 22 sec. 10 sec.
(approx. 60% power)
Power 5(P-50) 18 sec. 14 sec.
(approx. 50% power)
Power 4(P-40) 16 sec. 16 sec.
(approx. 40% power)
Power 3(P-30) 12 sec. 20 sec.
(approx. 30% power)
Power 2(P-20) 8 sec. 24 sec.
(approx. 20% power)
Power 1(P-10) 6 sec. 26 sec.
(approx. 10% power)
Power 0(P-0) 0 sec. 32 sec.
(0% power)
Note: The ON/OFF time ratio does not correspond with
the percentage of microwave power, because
approx. 2 seconds are needed for heating of the
magnetron filament.

R-2197
5
DOOR OPEN MECHANISM
The door is opened by grasping the door handle, refer to
Figure D-1.
When the door handle is grasped, the handle lever is
pulled. And then the upper and lower latch heads are
moved upward by the handle lever, and they are re-
leased from the latch hook. Now the door will open.
Figure D-1. Door Open Mechanism
1ST. LATCHSWITCHAND2ND. LATCHSWITCH
AND STOP SWITCH
1. Whentheovendoorisclosed,thecontacts(COM-NO)
of each switch must be closed.
2. When the oven door is opened, the contacts (COM-
NO) of each switch must be opened.
MONITOR SWITCH
1. Whenthedoorisclosed,thecontacts(COM-NC)must
be opened.
2. When the door is opened, the contacts (COM-NC)
must be closed.
3. Iftheovendoorisopenedandthecontacts(COM-NO)
of the 1st. latch switch, 2nd. latch switch and relay
(RY2) fail to open, the fuse M10A blows immediately
after closing the contacts (COM-NC) of the monitor
switch.
CAUTION: BEFORE REPLACING A BLOWN FUSE
M10ATESTTHE1ST.LATCHSWITCH,2ND.
LATCH SWITCH, RELAY (RY2), MONITOR
SWITCH AND MONITOR RESISTOR FOR
PROPER OPERATION. (REFER TO CHAP-
TER “TEST PROCEDURE”).
FUSE M10A 250V
1. If the wire harness or electrical components are short-
circuited,thisfuseblowstopreventanelectricshockor
fire hazard.
2. This fuse blows when the 1st. latch switch, 2nd. latch
switch and relay (RY2) remain closed with the oven
door open and when the contacts (COM-NC) of
monitor switch closes.
FUNCTION OF IMPORTANT COMPONENTS
HIGH VOLTAGE FUSE 0.75A
Thehighvoltagefuseblowswhenthehighvoltagerectifier
or the magnetron is shorted.
THERMAL CUT-OUT 145˚C (MAGNETRON)
Thisthermalcut-outprotectsthemagnetronagainstover-
heating. If the temperature goes up higher than 145˚C
because the fan motor is interrupted or the ventilation
openings are blocked, the thermal cut-out will open and
line voltages to the high voltage transformer will be cut off
and the operation of the magnetron will be stopped. The
thermal cut-out will not resume.
THERMAL CUT-OUT 125˚C (OVEN)
The thermal cut-out located on the top of the oven cavity
isdesignedtopreventdamagetotheovenifthefoodinthe
oven catches fire due to over heating produced by im-
propersettingofthecooking time or failureofcontrolunit.
Under normal operation, the oven thermal cut-out re-
mains closed. However, when abnormally high tempera-
turesarereachedwithintheovencavity,theoventhermal
cut-out will open at 125˚C causing the oven to shut down.
The thermal cut-out will not resume.
MONITOR RESISTOR
The monitor resistor prevents the fuse M10A bursting
when the fuse M10A blows due to the operation of the
monitor switch.
NOISE FILTER
The noise filter assembly prevents radio frequency inter-
ference that might flow back in the power circuit.
ANTENNA MOTOR
The antenna motor rotates the stirrer antenna located on
the bottom of the oven cavity, so that the food on the
ceramic shelf is cooked evenly during cooking. The an-
tenna motor may turn in either direction.
COOLING FAN MOTOR
The cooling fan motor drives a blade which draws exter-
nal cool air. This cool air is directed through the air vanes
surrounding the magnetron and cools the magnetron.
This air is channelled through the oven cavity to remove
steam and vapors given off from the heating food. It is
then exhausted through the exhausting air vents at the
oven cavity.
Latch Hook
Latch Switch
Lever A
Latch Switch
Lever B
Latch Switch
Lever C
Latch Head
Latch Head
Handle
Lever
Door
Handle
Latch
Lever 2nd. Latch Switch
Monitor
Switch
Stop Switch
1st . Latch Switch

6
R-2197
When troubleshooting the microwave oven, it is helpful to
followtheSequenceofOperationinperformingthechecks.
Many of the possible causes of trouble will require that a
specifictestbe performed.Thesetests aregivena proce-
dure letter which will be found in the “Test Procedure”
section.
IMPORTANT: If the oven becomes inoperative because
of a blown fuse M10A in the 1st. latch
switch - 2nd. latch switch - relay(RY2)-
monitor switch - monitor resistor circuit,
check the 1st. latch switch, 2nd. latch
switch, relay(RY2), monitor switch and
monitor resistor before replacing the fuse
M10A.
TROUBLESHOOTING GUIDE
REMEMBER TO CHECK 3D
1) Disconnect the supply.
2) Door opened, and wedged open.
3) Discharge high voltage capacitor.
WARNING: AGAINST THE CHARGE OF THE
HIGH-VOLTAGE CAPACITOR.
The high-voltage capacitor remains charged about
60 seconds after the oven has been switched off.
Wait for 60 seconds and then short-circuit the con-
nection of the high-voltage capacitor (that is, of the
connectingleadofthehigh-voltagerectifier)against
thechassiswiththeuseofaninsulatedscrewdriver.
Sharprecommendthatwhereverpossiblefault-findingis
carriedoutwiththesupplydisconnected.Itmayin,some
cases,benecessarytoconnectthesupplyaftertheouter
case has been removed, in this event carry out 3D
checks and then disconnect the leads to the primary of
the high voltage transformer. Ensure that these leads
remain isolated from other components and the oven
chassis. (Use insulation tape if necessary.) When the
testing is completed carry out 3D checks and reconnect
the leads to the primary of the high voltage transformer.
When all service work is completed and the oven is fully assembled, the microwave power output should be checked
and microwave leakage test should be carried out.
SERVICING
WARNING TO SERVICE PERSONNEL
Microwaveovenscontaincircuitrycapableofproducingveryhighvoltageandcurrent.Contactwithfollowingpartswill
result in electrocution.
Highvoltagecapacitor,Highvoltagetransformer,Magnetron,Highvoltagerectifierassembly,Highvoltagefuse,High
voltage harness.
REMEMBER TO CHECK 4R
1) Reconnect all leads removed from components dur-
ing testing.
2) Replace the outer case (cabinet).
3) Reconnect the supply.
4) Run the oven. Check all functions.
Microwaveovensshouldnotberunempty.Totestforthe
presence of microwave energy within a cavity, place a
cup of cold water on the oven turntable, close the door
and set the power level to HIGH (100%) and set the
microwave timer for two (2) minutes. And push the start
key. When the two minutes has elapsed (timer at zero)
carefully check that the water is now hot. If the water
remains cold carry out 3D checks and re-examine the
connections to the component being tested.

R-2197
7
TEST PROCEDURE
CONDITION
PROBLEM
POSSIBLE CASE
AND
DEFECTIVE PARTS
Home fuse or circuit
breaker blows when
power cord is plugged into
wall outlet.
Fuse M10A blows when
power cord is plugged into
wall receptacle.
. does not appear
in display when power
cord is first plugged into
wall outlet.
Oven lamp does not light
when door is opened.
Oven lamp lights but fan
motor and antenna motor
do not operate.
Oven does not go into
cook cycle when START
pad is touched
Oven seems to be
operating but little or no
heat is produced in oven
load. (Food incompletely
cooked or not cooked at
all at end of cook cycle.)
Oven goes into a cook
cycle but extremely
uneven heating is
produced in oven load
(food).
Oven does not cook
properly when
programmed for Cooking
Power 5 mode. (Operates
properly on Cooking
Power 10 (HIGH) mode.)
"EE9" Maximum time is
exceeded.
OFF
CONDITION
COOKING
CONDITION
ERROR MODE
MAGNETRON
HIGH VOLTAGE TRANSFORMER
H.V. RECTIFIER ASSEMBLY
HIGH VOLTAGE CAPACITOR
THERMAL CUT-OUT
1ST. LATCH SWITCH
2ND. LATCH SWITCH
FUSE M10A
HIGH VOLTAGE FUSE
NOISE FILTER
TOUCH CONTROL PANEL
KEY UNIT
EXCEED MAX. HEATING TIME
RELAY (RY3)
RELAY (RY2)
FOIL PATTERN ON P.W.B.
LOW VOLTAGE
WRONG OPERATION
DIRTY OVEN CAVITY
MISADJUSTMENT SWITCH
SHORTED IN POWER CORD
OVEN LAMP OR SOCKET
COOLING FAN MOTOR
ANTENNA MOTOR
SHORT OR OPENED WIRING
MONITOR SWITCH
STOP SWITCH
A B C D E E E E F G H I I
JK L M M N CK RE RE RECK CK CK CK

8
R-2197
A MAGNETRON TEST
TEST PROCEDURES
PROCEDURE
LETTER COMPONENT TEST
CARRY OUT 3D CHECKS.
Isolate the magnetron from high voltage circuit by removing all leads connected to filament terminal.
Totestfor anopencircuitfilament useanohmmeter to makeacontinuity testbetweenthemagnetron
filament terminals, the meter should show a reading of less than 1 ohm.
Totest forshort filamentto anodecondition, connectohmmeterbetweenoneofthefilamentterminals
and the case of the magnetron (ground). This test should be indicated an infinite resistance. If a low
or zero resistance reading is obtained then the magnetron should be replaced.
MICROWAVE OUTPUT POWER (1 litre load)
The following test procedure should be carried out with the microwave oven in a fully assembled
condition (outer case fitted). Microwave output power from the magnetron can be measured by way
of IEC 705, i.e. it is measured by how much power the water load can absorb. To measure the
microwave output power in the microwave oven, the relation of calorie and watt is used. When P(W)
heating works for t(second), approximately P x t/4.187 calorie is generated. On the other hand, if the
temperature of the water with V(ml) rises ∆T (°C) during this microwave heating period, the calorie of
the water is V x ∆T.
Measuring condition:
1. Container
The water container must be a cylindrical borosilicate glass vessel having a maximum material
thickness of 3 mm and an outside diameter of approximately 190 mm.
2. Temperature of the oven and vessel
The oven and the empty vessel are at ambient temperature prior to the start the test.
3. Temperature of the water
The initial temperature of the water is (10±2)°C.
4. Selecttheinitialandfinalwatertemperaturesothatthemaximumdifferencebetweenthefinalwater
temperature and the ambient temperature is 5°C.
5. Selectstirring devicesand measuringinstrumentsinordertominimizeadditionorremovalofheat.
6. The graduation of the thermometer must be scaled by 0.1°C at minimum and be an accurate
thermometer.
7. The water load must be (1000±5) g.
8. “t”ismeasured while themicrowavegeneratoris operatingatfullpower. Magnetron filamentheat-
up time is not included.
NOTE:Theoperation timeofthe microwaveovenis“t +2”sec. (2sec.ismagnetron filamentheat-uptime.)
Measuring method:
1. Measure the initial temperature of the water before the water is added to the vessel.
(Example: The initial temperature T1 = 11°C)
2. Add the 1 litre water to the vessel.
3. Place the load on the centre of the shelf.
4. Operate the microwave oven at HIGH for the temperature of the water rises by a value ∆T of
(10 ±2) K.
5. Stir the water to equalize temperature throughout the vessel.
6. Measure the final water temperature. (Example: The final temperature T2 = 21°C)
7. Calculate the microwave power output P in watts from above formula.
NEVER TOUCH ANY PART IN THE CIRCUIT WITH YOUR HAND OR AN INSULATED TOOL
WHILE THE OVEN IS IN OPERATION.
The formula is as follows;
P x t / 4.187 = V x ∆T P (W) = 4.187 x V x ∆T / t
Our condition for water load is as follows:
Room temperature ........... around 20°C Power supply Voltage.............. Rated voltage
Water load..................................1000 g Initial temperature.............................. 10±2°C
Heating time.............................. 42 sec.
P = 100 x ∆T

R-2197
9
Initial temperature .................................................................................................. T1 = 11°C
Temperature after (42 + 2) = 44 sec ...................................................................... T2 = 21°C
Temperature difference Cold-Warm....................................................................... ∆T1 = 10C
Measured output power
The equation is “P = 100 x ∆T” ................................................ P = 100 x 10°C = 1000 Watts
JUDGMENT: The measured output power should be at least ±15 % of the rated output power.
CAUTION: 1°C CORRESPONDS TO 100 WATTS. REPEAT MEASUREMENT IF THE POWER IS
INSUFFICIENT.
TEST PROCEDURES
PROCEDURE
LETTER COMPONENT TEST
1000g
1000g
1000g
T1˚C T2˚C
Heat up for 44 sec
B HIGH VOLTAGE TRANSFORMER TEST
WARNING: High voltage and large currents are present at the secondary winding and
filamentwindingofthehighvoltagetransformer.Itisverydangeroustowork
near this part when the oven is on. NEVER make any voltage measurements
of the high-voltage circuits, including the magnetron filament.
C HIGH VOLTAGE RECTIFIER ASSEMBLY TEST
CARRY OUT 3D CHECKS.
Isolate the high voltage rectifier assembly from the HV circuit. The high voltage rectifier can be tested
usinganohmmetersettoitshighestrange.ConnecttheohmmeteracrosstheterminalB+Cofthehigh
voltagerectifierandnotethe readingobtained.Reversethemeter leadsandnotethissecond reading.
The normal resistance is infinite in one direction and more than 100 kΩin the other direction.
CARRY OUT 4R CHECKS.
NOTE: FOR MEASUREMENT OF THE RESISTANCE OF THE RECTIFIER, THE BATTERIES OF
THEMEASURINGINSTRUMENTMUSTHAVEAVOLTAGEATLEAST6VOLTS,BECAUSE
OTHERWISE AN INFINITE RESISTANCE MIGHT BE SHOWN IN BOTH DIRECTIONS.
CARRY OUT 3D CHECKS.
Disconnect the leads to the primary winding of the high voltage transformer. Disconnect the filament
and secondary winding connections from the rest of the HV circuitry. Using an ohmmeter, set on a low
range, it is possible to check the continuity of all three windings. The following readings should be
obtained:- a. Primary winding ................................ approximately 1.3 Ω
b. Secondary winding ............................ approximately 86 Ω
c. Filament winding......................................... less than 1 Ω
If the readings obtained are not stated as above, then the high voltage transformer is probably faulty
and should be replaced.
CARRY OUT 4R CHECKS.
BC
HIGH VOLTAGE RECTIFIER
D HIGH VOLTAGE CAPACITOR TEST
CARRY OUT 3D CHECKS.
A. Isolate the high voltage capacitor from the circuit.
B. Continuity check must be carried out with measuring instrument which is set to the highest
resistance range.
C. Anormalcapacitorshowscontinuityforashorttime(kick)andthenaresistanceofabout10MΩafter

10
R-2197
TEST PROCEDURES
PROCEDURE
LETTER COMPONENT TEST
ESWITCH TEST
CARRY OUT 3D CHECKS.
Isolate the switch to be tested and using an ohmmeter check between the terminals as described in
the following table.
Table: Terminal Connection of Switch
Plunger Operation COM to NO COM to NC
Released Open circuit Short circuit
Depressed Short circuit Open circuit
COM; Common terminal,
NO; Normally open terminal
NC; Normally close terminal
If incorrect readings are obtained, make the necessary switch adjustment or replace the switch.
CARRY OUT 4R CHECKS.
F THERMAL CUT-OUT TEST
CARRY OUT 3D CHECKS.
Disconnectthe leadsfromthe terminalsofthe thermalcut-out.Then usinganohmmeter, makeacontinuity
test across the two terminals as described in the below.
Table: Thermal Cut-out Test
Temperature of "ON" Temperature of "OFF" Indication of ohmmeter
Parts Name condition (closed circuit). condition (open circuit). (Whenroomtemperature
(˚C) (˚C) is approx. 20˚C.)
Thermal cut-out 125˚C This is not resetable type. Above 125˚C Closed circuit
Thermal cut-out 145˚C This is not resetable type. Above 145˚C Closed circuit
If incorrect readings are obtained, replace the thermal cut-out.
An open circuit thermal cut-out (MG) indicates that the magnetron has overheated, this may be due
to resistricted ventilation, cooling fan failure or a fault condition within the magnetron or HV. circuit.
An open circuit thermal cut-out (OVEN) indicates that the food in the oven cavity may catch fire, this
may be due to over heating produced by improper setting of the cooking timer or failure of the control
panel.
CARRY OUT 4R CHECKS.
GBLOWN FUSE M10A
CARRY OUT 3D CHECKS.
Ifthefuse M10A isblownwhen the doorisopened, check the1st.latch switch, 2nd.latchswitch, relay
RY2, monitor switch and monitor resistor.
If the fuse M10A is blown, there could be a short or ground in electrical parts or wire harness. Check
them and replace the defective parts or repair the wire harness.
CARRY OUT 4R CHECKS.
CAUTION: Only replace fuse M10A with the correct value replacement.
it has been charged.
D. A short-circuited capacitor shows continuity all the time.
E. An open capacitor constantly shows a resistance about 10 MΩbecause of its internal 10MΩ
resistance.
F. When the internal wire is opened in the high voltage capacitor shows an infinite resistance.
G. The resistance across all the terminals and the chassis must be infinite when the capacitor is
normal.
If incorrect reading are obtained, the high voltage capacitor must be replaced.
CARRY OUT 4R CHECKS.

R-2197
11
CARRY OUT 3D CHECKS.
Disconnect the leads from the motor. Using an ohmmeter, check the resistance between the two
terminals as described in the table below.
Table: Resistance of Motor
Motors Resistance
Fan motor Approximately 219 Ω
Antenna motor Approximately 11 kΩ
If incorrect readings are obtained, replace the motor.
CARRY OUT 4R CHECKS.
TEST PROCEDURES
PROCEDURE
LETTER COMPONENT TEST
IMOTOR WINDING TEST
CARRY OUT 3D CHECKS.
Disconnect the leads from the terminals of noise filter.
Usingan ohmmeter,check betweentheterminalsasdescribed
in the following table.
MEASURING POINTS INDICATION OF OHMMETER
Between N and L Approx. 680 kΩ
Between terminal N and WHITE Short circuit
Between terminal L and RED Short circuit
If incorrect readings are absorbed, replace the noise filter unit.
CARRY OUT 4R CHECKS.
HNOISE FILTER TEST
J HIGH VOLTAGE FUSE TST
CARRY OUT 3D CHECKS.
If the high voltage fuse is blown, there could be a short in the high voltage rectifier or the magnetron.
Check them and replace the defective parts and the high voltage fuse.
CARRY OUT 4R CHECKS.
CAUTION: Only replace high voltage fuse with the correct value replacement.
Thetouchcontrolpanel consists ofcircuitsincludingsemiconductors such asLSI,ICs,etc. Therefore,
unlikeconventionalmicrowaveovens,propermaintenancecannotbeperformedwithonlyavoltmeter
and ohmmeter.
Inthisservicemanual, the touchcontrolpanel assembly isdividedintotwo units, ControlUnitandKey
Unit and troubleshooting by replacement is described according to the symptoms indicated.
1. Key Unit Note : Check key unit ribbon connection before replacement.
The following symptoms indicate a defective key unit. Replace the key unit.
a) When touching the pads, a certain pad produces no signal at all.
b) When touching a number pad, two figures or more are displayed.
c) When touching the pads, sometimes a pad produces no signal.
2. Control Panel
The following symptoms indicate a defective control unit. Before replacing the control unit.
perform the key unit test (Procedure L) to determine if control unit is faulty.
2-1 In connection with pads
a) When touching the pads, a certain group of pads do not produce a signal.
b) When touching the pads, no pads produce a signal.
2-2 In connection with indicators
a) At a certain digit, all or some segments do not light up.
b) At a certain digit, brightness is low.
c) Only one indicator does not light up.
d) The corresponding segments of all digits do not light up; or they continue to light up.
K CONTROL PANEL ASSEMBLY TEST
FUSE
M10A
NL
DISCHARGE RESISTOR 680 kΩ
NOISE SUPPRESSION COIL
LINE BYPASS
CAPACITOR
0.0033µF/ AC 250V
DISCHARGE
RESISTOR 10MΩ
LINE BYPASS
CAPACITOR
0.0033µF/ AC 250V
LINE CROSS CAPACITOR 0.068µF/ AC 250V
NOISE FILTER

12
R-2197
TEST PROCEDURES
PROCEDURE
LETTER COMPONENT TEST
e) Wrong figure appears.
f) A certain group of indicators do not light up.
g) The figure of all digits flicker.
2-3 Other possible troubles caused by defective control unit.
a) Buzzer does not sound or continues to sound.
b) Clock does not operate properly.
c) Cooking is not possible.
LKEY UNIT TEST
If the display fails to clear when the STOP/CLEAR pad is depressed, first verify the flat ribbon cable
ismarkinggoodcontact,verifythatthedoorsensing switch(stop switch)operatesproperly;thatisthe
contactsareclosedwhenthedoorisclosedandopenwhenthedoorisopen.Ifthedoorsensingswitch
(stopswitch)isgood, disconnect theflatribboncable that connectsthekeyunit to the controlunitand
make sure the door sensing switch is closed (either close the door or short the door sensing switch
connecter). Use the Key unit matrix indicated on the control panel schematic and place a jumper wire
betweenthepinsthatcorrespond totheSTOP/CLEAR padmarkingmomentarycontact.If thecontrol
unitrespondsbyclearingwithabeepthekeyunitisfaultyandmustbereplaced.Ifthecontrolunitdoes
notrespond,itisa faulty and mustbereplaced. Ifa specific pad does notrespond,theabove method
may be used (after clearing the control unit) to determine if the control unit or key pad is at fault.
CARRY OUT 3D CHECKS.
Removetheouter case andcheckvoltage between PinNos.3 and 7ofthe 3 pinconnector(A) on the
control unit with an A.C. voltmeter.
The meter should indicate 230-240 volts, if not check oven circuit.
Relay Test
Check voltage at the relay coil with a D.C. voltmeter during the microwave cooking operation.
DC. voltage indicated.......... Defective relay.
DC. voltage not indicated.... Check diode which is connected to the relay coil. If diode is good,
control unit is defective.
RELAY SYMBOL OPERATIONAL VOLTAGE CONNECTED COMPONENTS
RY2 Approx. 12.0V D.C. High voltage transformer
RY3 Approx. 12.0V D.C. Oven lamp / Antenna motor / Fan motor
CARRY OUT 4R CHECKS.
M RELAY TEST
CARRY OUT 4R CHECKS.
5
6
3
4
1
11131519
12141620
17
18
2
7
8
9
0
SELECT
TIME
SELECT
POWER
STOP/
CLEAR
START SET
CHECK
SIGNAL
DOUBLE
QUANTITY
EXPRESS
DEFROST
G12
G11
G10
G 9
G 1 G 2 G 3 G 4 G 5 G 6 G 7 G 8

R-2197
13
TEST PROCEDURES
PROCEDURE
LETTER COMPONENT TEST
N
PROCEDURES TO BE TAKEN WHEN THE FOIL PATTERN ON THE PRINTED WIRING BOARD
(PWB) IS OPEN
Toprotect theelectronic circuits,this modelis providedwithafinefoilpatternaddedtotheinputcircuit
on the PWB, this foil pattern acts as a fuse. If the foil pattern is open, follow the troubleshooting guide
given below for repair.
Problem: POWER ON, indicator does not light up.
CARRY OUT 3D CHECKS.
STEPS OCCURRENCE CAUSE OR CORRECTION
1The rated AC voltage is not present at Check supply voltage and oven power cord.
Power terminal of CPU connector (CN-A).
2The rated AC voltage is present at primary Low voltage transformer or secondary circuit defective.
side of low voltage transformer. Check and repair.
3 Only pattern at "a" is broken. *Insert jumper wire J1 and solder.
(CARRY OUT 3D CHECKS BEFORE REPAIR)
4 Pattern at "a" and "b" are broken. *Insert the coil RCILF2003YAZZ between "c" and "d".
(CARRY OUT 3D CHECKS BEFORE REPAIR)
NOTE: *At the time of these repairs, make a
visual inspection of the varistor for
burning damage and examine the
transformer with tester for the pres-
ence of layer short circuit (check pri-
mary coil resistance).
If any abnormal condition is detected,
replace the defective parts.
CARRY OUT 4R CHECKS.
(17)
a
b
cd
(CT1)
(J1)
(J7)
(TB1)
12
P
VRS1
(VRS2)
POWER
7

14
R-2197
11) Relay Driving Circuit
This is a circuit for driving output relay by IC1 output.
12) Door Sensing Switch Circuit
This is a circuit for driving IC1 to detect door opening/
closing.
2. Key Unit
The key unit is composed of a matrix circuit in which
when a key it touched, one of signals P30--P34
generated by the LSI, is passed through the key and
returned to the LSI as one of signals P24--P27.
This model has 20 Memory pads.
Whenthe ovenis shipped,Memorypad1to10areset
as follows: fig.1.
Memory No. Cook Time Output Power
1 10 sec. 100%
2 20 sec. 100%
3 30 sec. 100%
4 45 sec. 100%
5 1 min. 100%
6 1 min. 15 sec. 100%
7 1 min. 30 sec. 100%
8 2 min. 100%
9 2 min. 30 sec. 100%
0 3 min. 100%
(fig. 1)
This model has a double quantity pad. When the oven
is shipped, Magnification "1.7" is preset in the double
quantity pad.
This model has an express defrost pad. When the
oven is shipped, express defrost is set as follows:
fig.2.
1 STAGE 2 STAGE 3 STAGE
FORMULA P = 0.2T P = 0.15T P = 0.65T
POWER 60 % 40 % 20 %
T : Total cooling time (fig. 2)
When 1/2 total cooking time is passed, the signal
will sound and "CHECK" indicator will flash
TOUCH CONTROL PANEL ASSEMBLY
OUTLINE OF TOUCH CONTROL PANEL
Thetouchcontrolsectionconsistsofthefollowingunitsas
shown in the touch control panel circuit.
(1) Control Unit
(2) Key Unit
The principal functions of these units and the signals
communicated among them are explained below.
1. Control Unit
Signal of key touch and oven function control are all
processed by one microcomputer.
1) Power Supply Circuit
This circuit changes output voltage at the secondary
side of the low voltage (T1) transformer to voltages
required at each part by full wave rectifying circuit,
constant voltage circuit, etc..
2) ACL Circuit
This is an Auto-clear Circuit, i.e., a reset circuit, which
enables IC1 to be activated from initial state.
3) Power SYNC Signal Generating Circuit
This is a circuit for generating power SYNC signal by
virtue of the secondary side output of transformer T1.
This signal is used for a basic frequency to time
processing and so on.
4) Clock Circuit
Thisisacircuitforcontrollingclockfrequencyrequired
for operating IC1.
5) IC1 (Main Processor)
This is a one-chip microcomputer, responsible for
controlling the entire control unit.
6) IC2 (Memory Processor)
Thisisa memoryIC,responsibleformemory function.
7) IC3
This is a IC for driving light emitting diode.
8) Display Circuit
This is a circuit for driving light emitting diode by IC1
output.
9) Key Input Circuit
Thisisacircuitfortransmittingkeyinputinformationto
IC1.
10) Sound-body Driving Circuit
This is a circuit for driving sound body by IC1 output.
DESCRIPTION OF LSI
LSI(IZA897DR)
The I/O signal of the LSI(IZA897DR) is detailed in the following table.
Pin No. Signal I/O Description
1 VCC IN Power source voltage: +5V.
VC voltage of power source circuit input.
2/3 VEE/AVSS IN Connected to GND
4 VREF IN Connected to VC. (+5V)
5-6 AN7-AN6 IN Terminal not used.

R-2197
15
7-8 AN5-AN4 IN Terminal to change functions according to the model.
Signal in accordance with the model in operation is applied to set up its function.
9-10 AN3-AN2 IN Terminal not used.
11 AN1 IN Input signal which communicates the door open/close information to LSI.
Door closed; "L" level signal (0V).
Door opened; "H" level signal (+5V).
12 AN0 IN Terminal not used.
13 P55 OUT Magnetron high-voltage circuit driving signal.
To turn on and off the cook relay. In 100% power level operation, "H" level during
cooking; "L" level otherwise. In other power level operation
(90,80,70,60,50,40,30,20,10or0%),"H"and"L"levelisrepeatedaccordingtopower
level.
Power level ON OFF Power level ON OFF
100% 32sec. 0sec. 40% 16sec. 16sec.
90% 30sec. 2sec. 30% 12sec. 20sec.
80% 26sec. 6sec. 20% 8sec. 24sec.
70% 24sec. 8sec. 10% 6sec. 26sec.
60% 22sec. 10sec. 0% 0sec. 32sec.
50% 18sec. 14sec.
14-15 P54-P53 OUT Terminal not used.
16-18 P52-P50 IN Terminal not used.
19 P47 OUT Signal to sound buzzer.
This signal is to control the 2.5kHz con-
tinuous signal through IC3.
A: key touch sound.
B: Guidance sound.
C: Completion sound.
20 P46 OUT Oven lamp, Fan motor and Antenna motor driving signal. (Square Waveform :
50Hz)
To turn on and off the shut-off relay (RY3). The
Square waveform voltage is delivered to the
RY3drivingcircuit andrelays(RY2,COOK RE-
LAY) control circuit.
21 P45 OUT Digit selection signal.
Therelationbetweendigitsignalanddigitare
as follows:
Digit signal Digit
P42..................... 1st.
P43....................2nd.
P44.....................3rd.
P45..................... 4th.
Normally, one pulse is output in every ß
period, and input to the grid of the light-
emitting diode.
22-24 P44-P42 OUT Digit selection signal.
Signal similar to P45.
25 INT1 IN Signal synchronized with commercial power source frequency.
This is basic timing for all time processing of LSI.
26 P40 IN Connected to GND through resistor.
Pin No. Signal I/O Description
+5V
GND
32 sec.
ON
OFF
A
0.12 sec
2.4 sec
1.2 sec
+5V
GND T
200µsec.
200µsec.
1.2 sec
B+5V
GND
C+5V
GND
H
L
20 msec
During cooking
H
L
+5V
ß(50Hz)
P42
P43
P44
P45
GND
H : +5V
L : GND
20 msec

16
R-2197
27 RESET IN Auto clear terminal.
SignalisinputtoresettheLSItotheinitialstatewhenpowerissupplied.Temporarily
setto"L"levelthe momentpowerissupplied,atthistimetheLSIisreset.Thereafter
set at "H" level.
28 P71 OUT Memory (EEPROM) clock output.
29 P70 IN/OUT Memory (EEPROM) data input/output.
30 XIN IN Internal clock oscillation frequency setting input.
The internal clock frequency is set by inserting the ceramic filter oscillation circuit
with respect to XOUT terminal.
31 XOUT OUT Internal clock oscillation frequency control output.
Output to control oscillation input of XIN.
32 VSS IN Connected to GND.
33 P27 IN Signal coming from touch key.
When either one of G-12 line keys on key matrix is touched, a corresponding signal
out of P30, P31, P32, P33, P34 will be input into P27. When no key is touched, the
signal is held at "L" level.
34 P26 IN Signal similar to P27.
When either one of G-11 line keys on key matrix is touched, a corresponding signal
will be input into P26.
35 P25 IN Signal similar to P27.
When either one of G-10 line keys on key matrix is touched, a corresponding signal
will be input into P25.
36 P24 IN Signal similar to P27.
When either one of G-9 line keys on key matrix is touched, a corresponding signal
will be input into P24.
37-38 P23-P22 OUT Terminal not used.
39-40 P21-P20 OUT Segment data signals.
The relation between signals and indicators are as follows:
Signal Segment Signal Segment
P21,P20 ..........1 P05,P04 .............7
P17.P16 ..........2 P03,P02 .............8
P15,P14 ..........3 P01,P00 .............9
P13,P12 ..........4
P11,P10 ..........5
P07,P06 ..........6
41-48 P17-P10 OUT Segment data signal.
Signal similar to P21.
49-56 P07-P00 OUT Segment data signal.
Signal similar to P21.
57-59 P37-P35 OUT Terminal not used.
60 P34 OUT Key strobe signal.
Signalappliedtotouch-keysection.ApulsesignalisinputtoP27,P26,P25andP24
terminals while one of G4 line keys on key matrix is touched.
61 P33 OUT Key strobe signal.
Signalappliedtotouch-keysection.ApulsesignalisinputtoP27,P26,P25andP24
terminals while one of G5 line keys on key matrix is touched.
62 P32 OUT Key strobe signal.
Signalappliedtotouch-keysection.ApulsesignalisinputtoP27,P26,P25andP24
terminals while one of G6 line keys on key matrix is touched.
63 P31 OUT Key strobe signal.
Signalappliedtotouch-keysection.ApulsesignalisinputtoP27,P26,P25andP24
terminals while one of G7 line keys on key matrix is touched.
64 P30 OUT Key strobe signal.
Signalappliedtotouch-keysection.ApulsesignalisinputtoP27,P26,P25andP24
terminals while one of G8 line keys on key matrix is touched.
Pin No. Signal I/O Description
+5V
GND
ß(50Hz)

R-2197
17
When the memory IC (IC2) or control unit is exchanged, input the relay timing to the memory IC (IC2), referring to the
"How to input the relay timing". Otherwise the oven will make a big noise when starting.
How to input the relay timing ... Flashing / ... 0.1sec BUZZER
PAD DISPLAY INDICATOR PHONE
(Door close) .
.
CHECK . CHECK No.
CHECK 8 2 6 8 CHECK
(user total count)
SIGNAL
SIGNAL
DOUBLE 3 4 5 6
QUANTITY (service total count upper figure 3456XX)
7 7 No.
(after 1 sec.) 3 8 6 9
SET 0
3. 8. 4. 9 3 8 4 9 x 4
SET 3 8 4 9
CHECK .
X24C02P is a 2K-bit, serial memory, enabling CMOS to be erased/written electrically. This memory is constructed with
256registersx8bits,enablingindividualaccess,readandwriteoperationstobeperformed.Detailsofinput/outputsignal
for IC2 are as shown in the following diagram.
2-2 Memory IC (IC2)
FUNCTIONAL DIAGRAM
E PROM
256 x 8
2
START
STOP
LOGIC
CONTROL
LOGIC
SLAVE ADDRESS
REGISTER
COMPARATOR
H.V. GENERATION
TIMING
& CONTROL
64
YDEC
8
DATA REGISTER Dout
CK
3
1
5
64
XDEC
START CYCLE
INC
LOAD
WORD
ADDRESS
COUNTER
R/W
PIN
Dout
ACK
(6) SCL
(5) SDA
(4) Vss
(3) Vcc
Table 1. Relation between Pin Nos, and Signals
A0
A1
A2
VSS
VCC
TEST
SCL
SDA
TOP VIEW
1
2
3
4
8
7
6
5
Pin No. Signal I/O Description
1-3 A0-A2 IN Connected to +5V.
4 VSS IN Connected to GND.
5 SDA IN/OUT Serial data input/output : input/outputs data to IC1.
6 SCL IN Clock signal input : input/outputs sireal data at every one pulse.
7 TEST IN Connected to GND.
8 VCC IN Connected to +5V.

18
R-2197
approx. 1M ohm
ECB
IC
KIA7805P1
321Transistor
DTA123ES
DTB143ES
DTC143ES
DTD143ES
TOUCH CONTROL PANEL SERVICING
transformer.
4) Re-install the outer case (cabinet).
5) Re-connect the power supply cord after the outer
case is installed.
6) Run the oven and check all functions.
A. On some models, the power supply cord between the
touch control panel and the oven itself is so short that
the two can’t be separated. For those models, check
and repair all the controls (sensor-related ones in-
cluded) of the touch control panel while keeping it
connected to the oven.
B. On some models, the power supply cord between the
touchcontrolpanelandtheovenproperislongenough
thatthey maybe separatedfromeachother.Forthose
models,therefore,itispossibletocheckandrepairthe
controls of the touch control panel while keeping it
apartfromtheovenproper;inthis caseyoumustshort
both ends of the door sensing switch (on PWB) of the
touch control panel with a jumper, which brings about
anoperationalstate that isequivalenttothe ovendoor
being closed. As for the sensor-related controls of the
touchcontrolpanel,checkingthemispossibleifdummy
resistor(s) with resistance equal to that of the controls
are used.
(2)Servicing the touch control panel with power sup-
ply from an external power source:
Disconnect the touch control panel completely from
the oven proper, and short both ends of the door
sensing switch (on PWB) of the touch control panel,
which brings about an operational state that is equiva-
lent to the oven door being closed. Connect an exter-
nal power source to the power input terminal of the
touch control panel, then it is possible to check and
repair the controls of the touch control panel it is also
possible to check the sensor-related controls of the
touch control panel by using the dummy resistor(s).
4. Servicing Tools
Tools required to service the touch control panel
assembly.
1) Soldering iron: 30W
(It is recommended to use a soldering iron with a
grounding terminal.)
2) Oscilloscope: Single beam, frequency range: DC-
10MHz type or more advanced model.
3) Others: Hand tools
5. Other Precautions
1) Before turning on the power source of the control unit,
removethealuminiumfoil applied for preventingstatic
electricity.
2) Connect the connectors of the key unit to the control
unit being sure that the lead wires are not twisted.
3) After aluminium foil is removed, be careful that abnor-
mal voltage due to static electricity etc. is not applied
to the input or output terminals.
4)Attachconnectors,electrolyticcapacitors,etc.toPWB,
making sure that all connections are tight.
5) Be sure to use specified components where high
precision is required.
1. Precautions for Handling Electronic Components
This unit uses CMOS LSI in the integral part of the
circuits. When handling these parts, the following
precautions should be strictly followed. CMOS LSI
haveextremelyhighimpedanceat itsinputand output
terminals.Forthis reason,itis easilyinfluencedby the
surrounding high voltage power source, static elec-
tricity charge in clothes, etc. and sometimes it is not
fully protected by the built-in protection circuit.
In order to protect CMOS LSI.
1) When storing and transporting, thoroughly wrap them
in aluminium foil. Also wrap all PW boards containing
them in aluminium foil.
2) When soldering, ground the technician as shown in
the figure and use grounded soldering iron and work
table.
2. Shapes of Electronic Components
3. Servicing of Touch Control Panel
We describe the procedures to permit servicing of the
touch control panel of the microwave oven and the
precautions you must take when doing so. To perform
the servicing, power to the touch control panel is
available either from the power line of the oven itself
or from an external power source.
(1)Servicing the touch control panel with power sup-
ply of the oven:
CAUTION:
THE HIGH VOLTAGE TRANSFORMER OF THE
MICROWAVE OVEN IS STILL LIVE DURING SERV-
ICING PRESENTS A HAZARD.
Therefore, before checking the performance of the
touch control panel,
1) Disconnect the power supply cord, and then re-
move outer case.
2) Open the door and block it open.
3) Discharge high voltage capacitor.
4) Disconnect the leads to the primary of the power
transformer.
5) Ensure that these leads remain isolated from other
components and oven chassis by using insulation
tape.
6) After that procedure, re-connect the power supply
cord.
After checking the performance of the touch control
panel,
1) Disconnect the power supply cord.
2) Open the door and block it open.
3) Re-connect the leads to the primary of the power
Other manuals for MODEL R-2197
1
Table of contents
Other Sharp Microwave Oven manuals
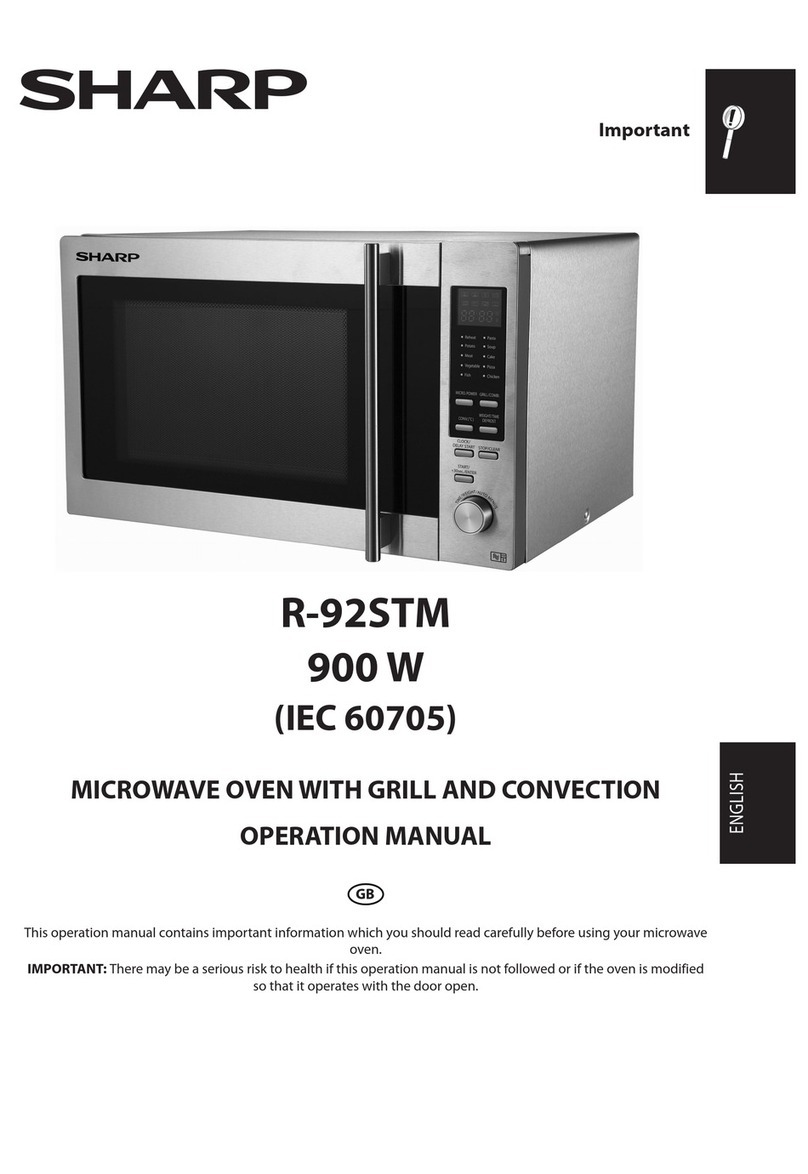
Sharp
Sharp R-92STM User manual
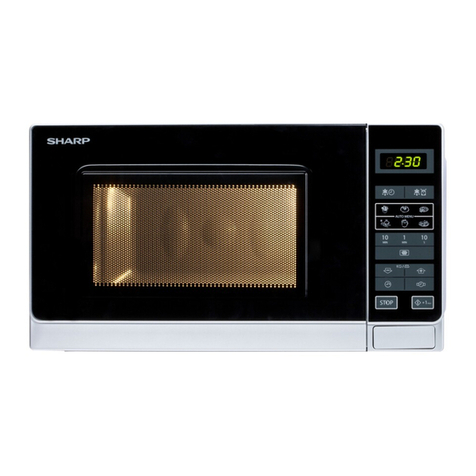
Sharp
Sharp R242INW User manual
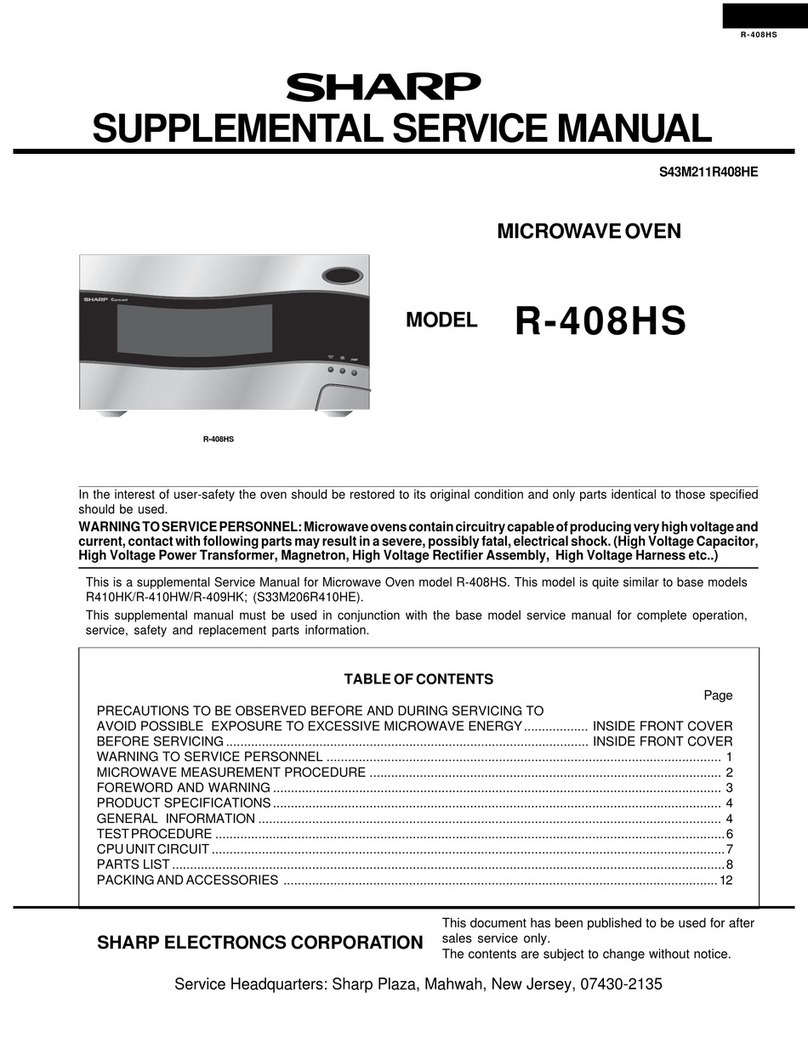
Sharp
Sharp R-408HS User manual
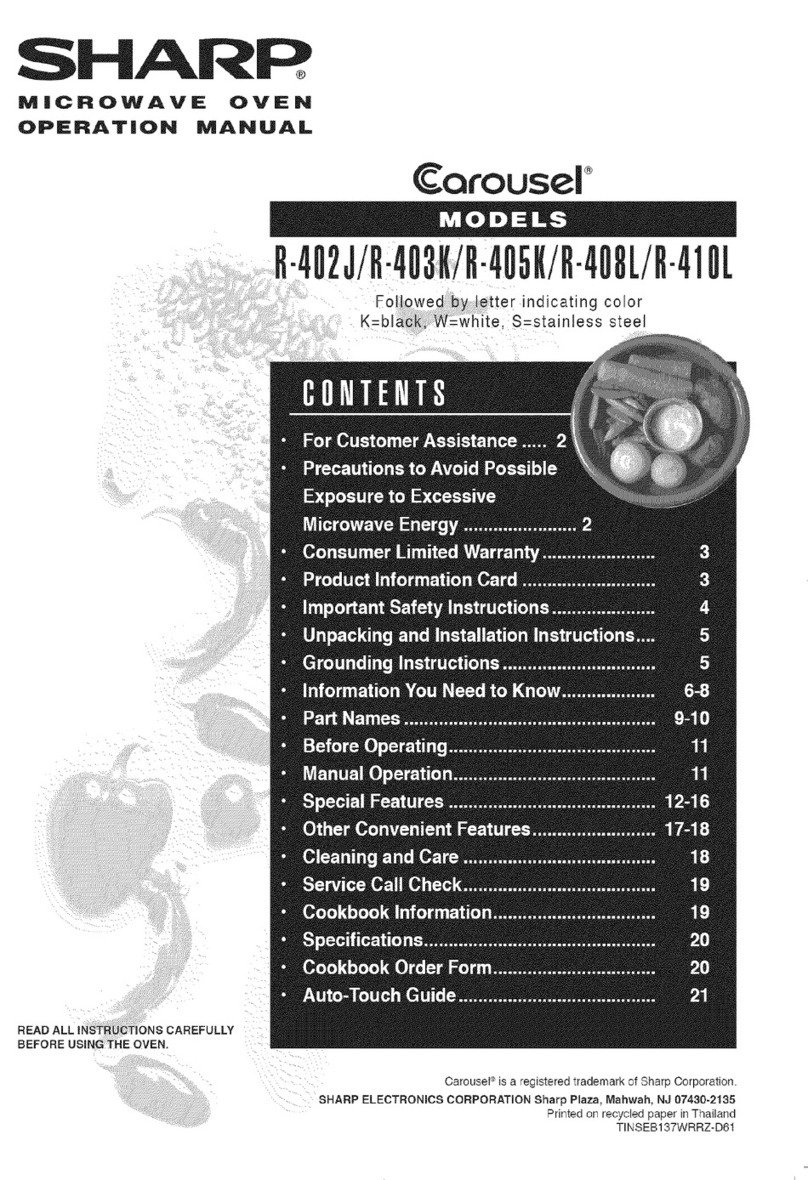
Sharp
Sharp R-402J User manual

Sharp
Sharp R-204 Instruction Manual
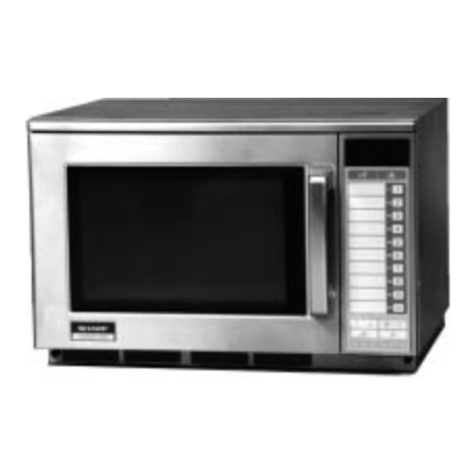
Sharp
Sharp R-2397 User manual
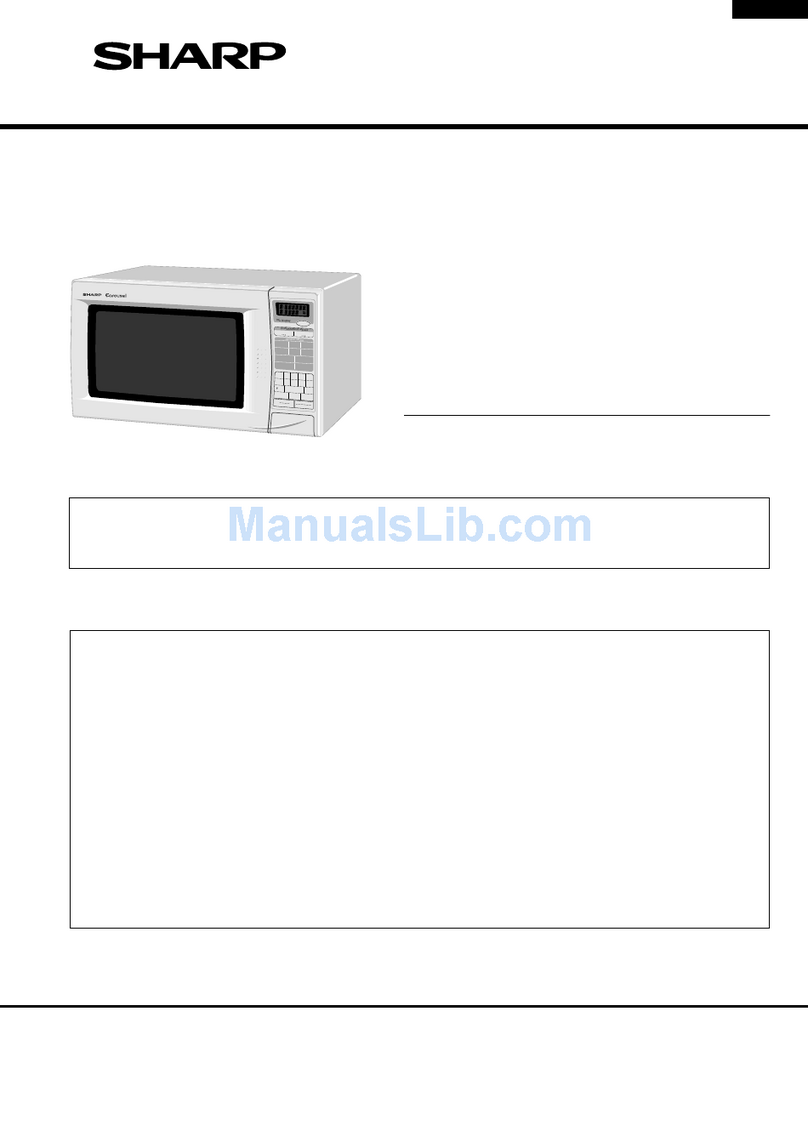
Sharp
Sharp R-450B User manual
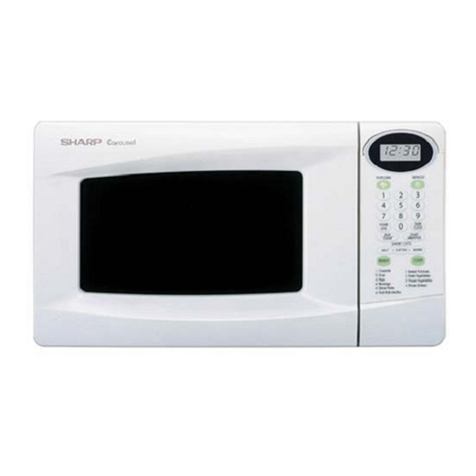
Sharp
Sharp R-220KK User manual
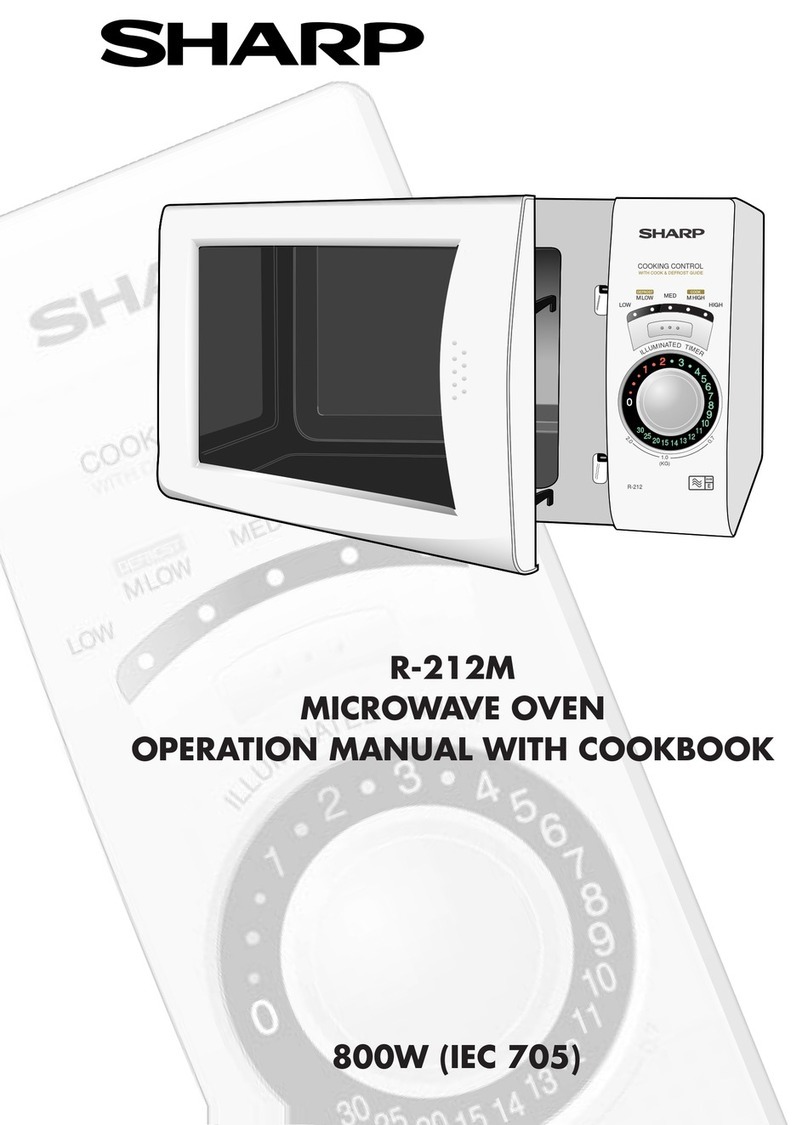
Sharp
Sharp R-212M Instruction Manual
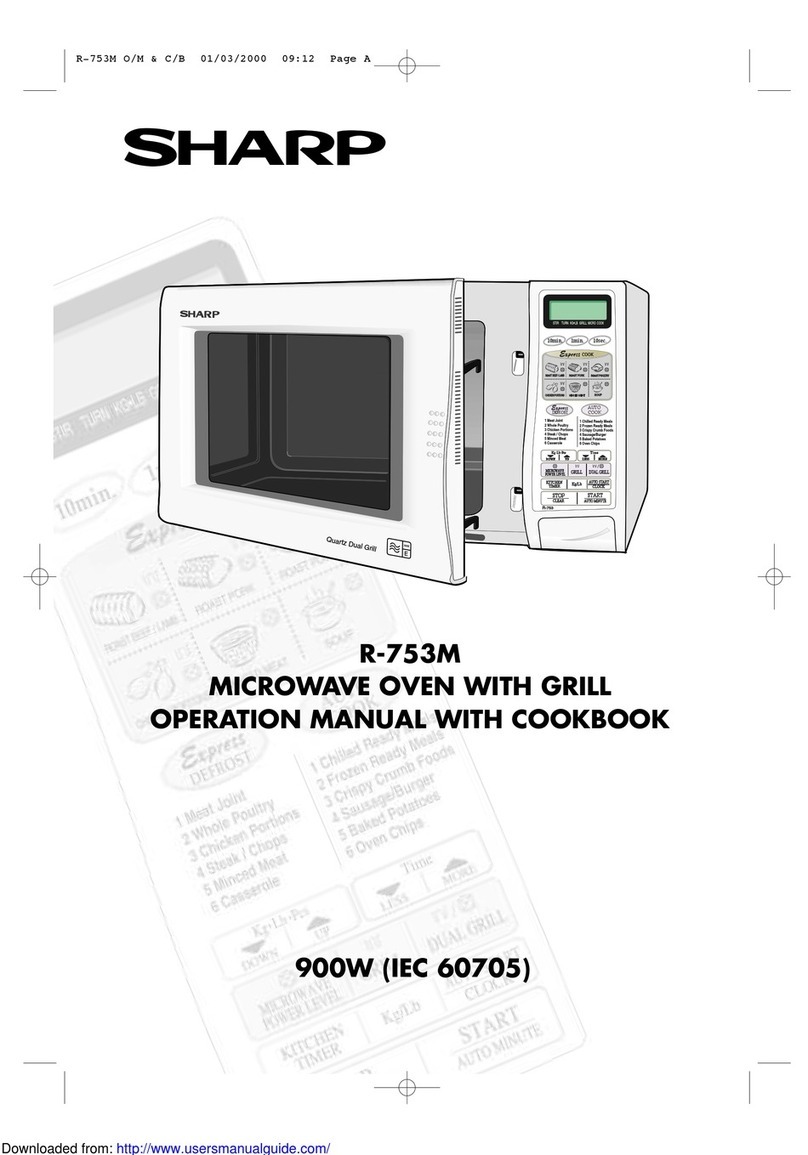
Sharp
Sharp R-753M Instruction Manual
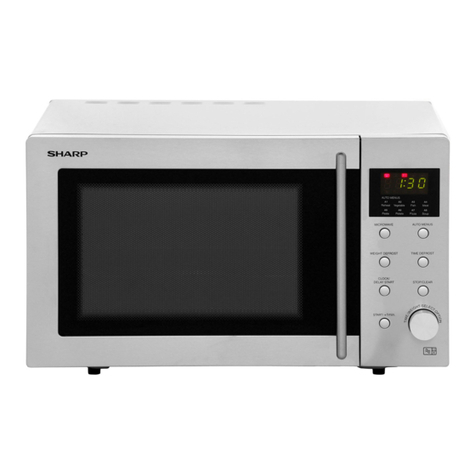
Sharp
Sharp R-28STM User manual

Sharp
Sharp R-319FW User manual
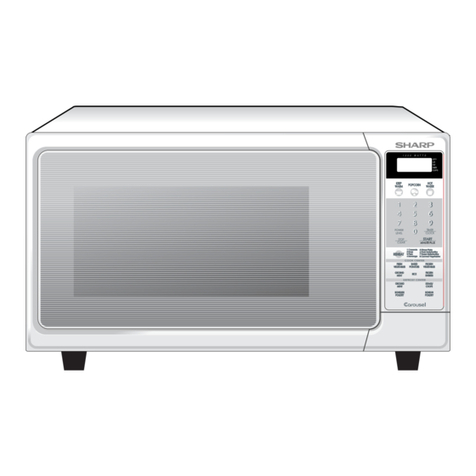
Sharp
Sharp R-310HK User manual
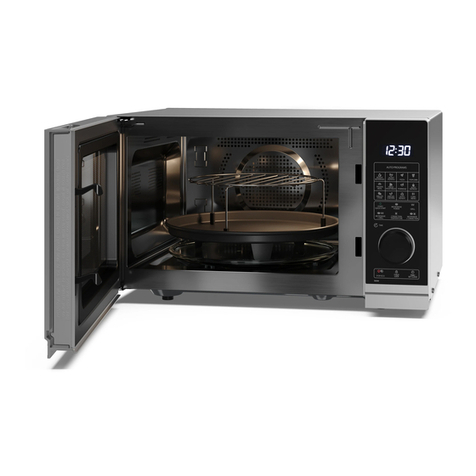
Sharp
Sharp YC-PC254A User manual
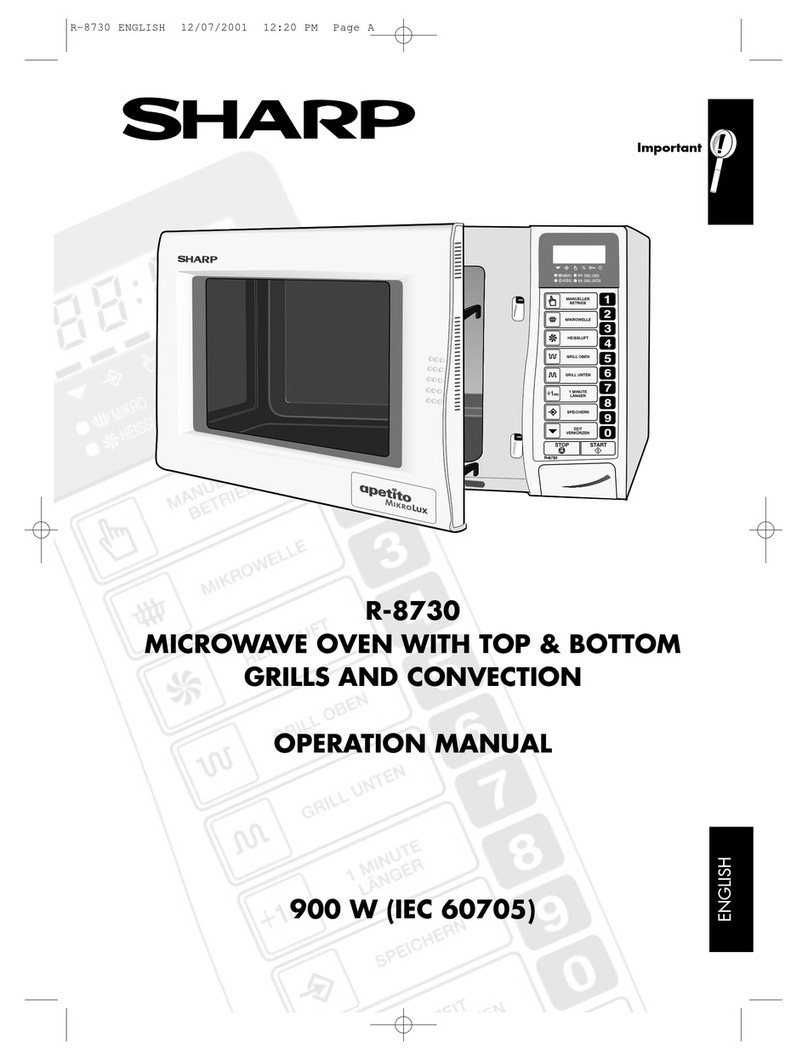
Sharp
Sharp R-8730 User manual
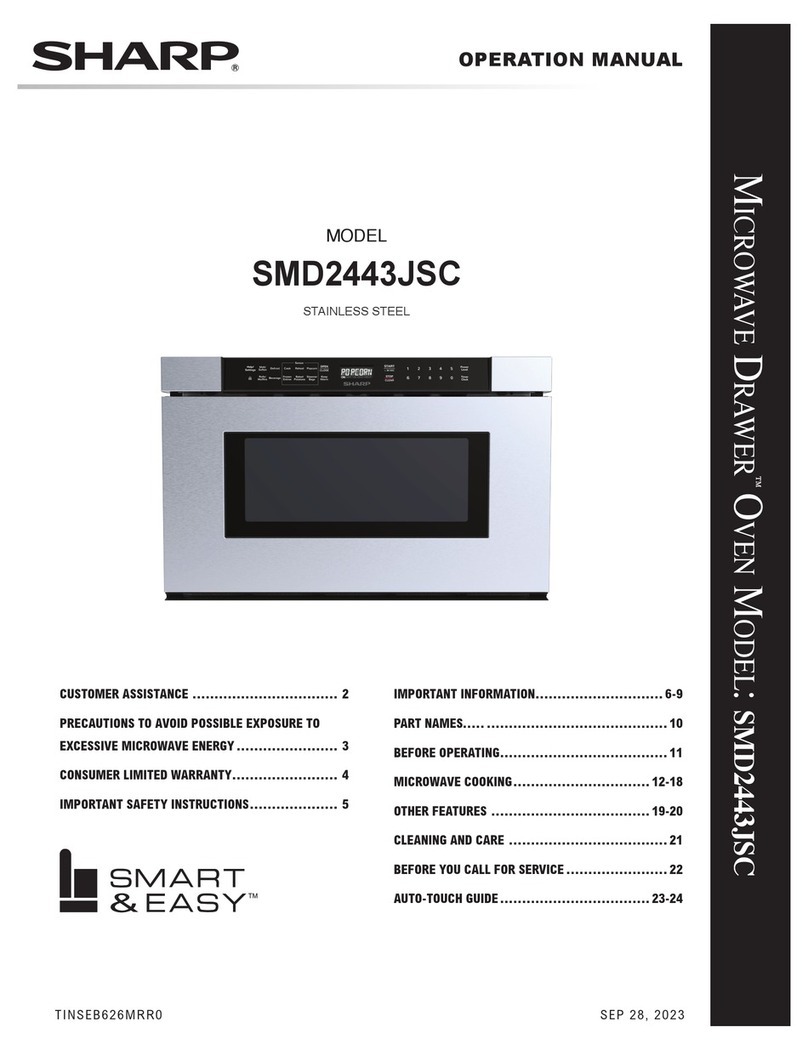
Sharp
Sharp Microwave Drawer SMD2443JSC User manual
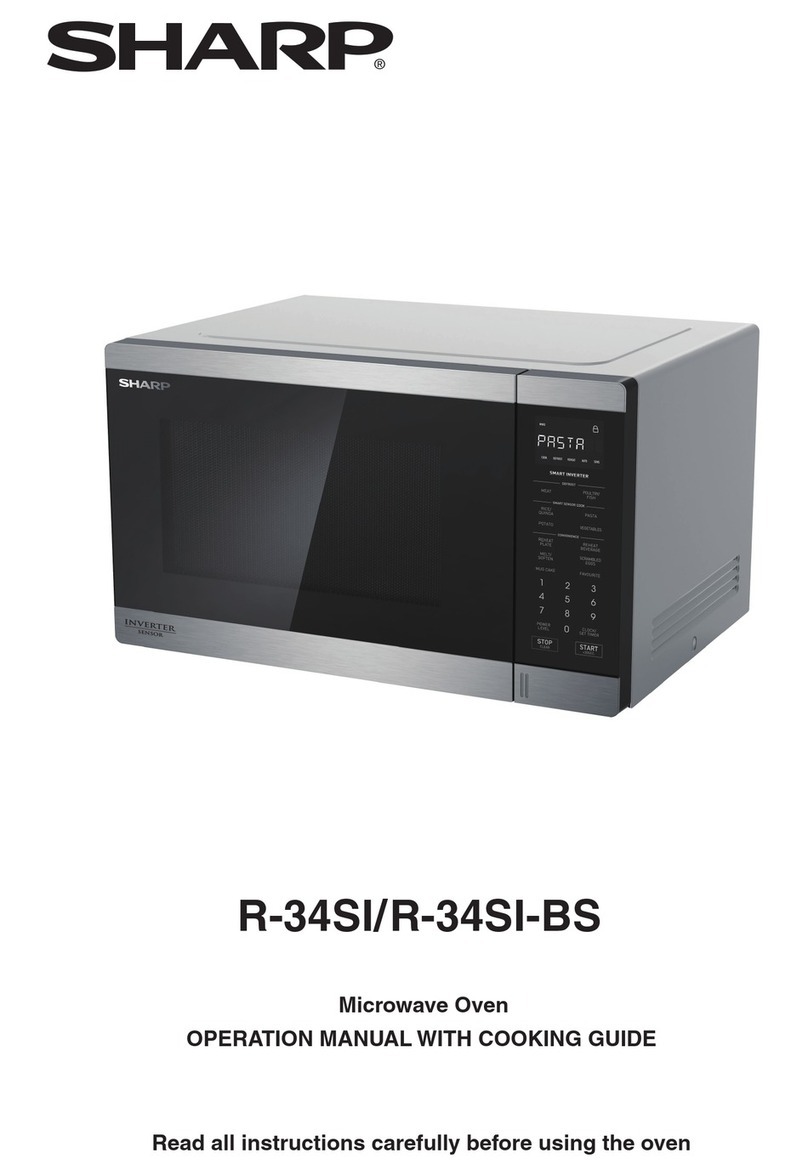
Sharp
Sharp R-34SI User manual
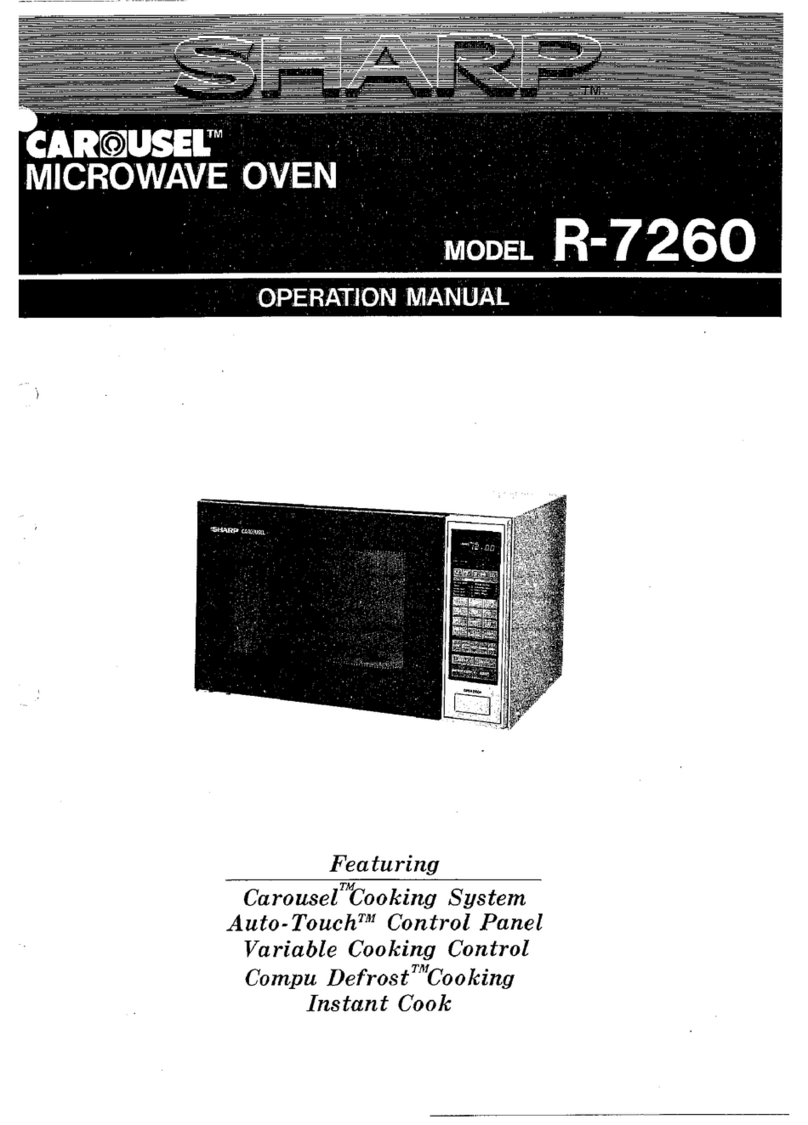
Sharp
Sharp Carousel R-7260 User manual
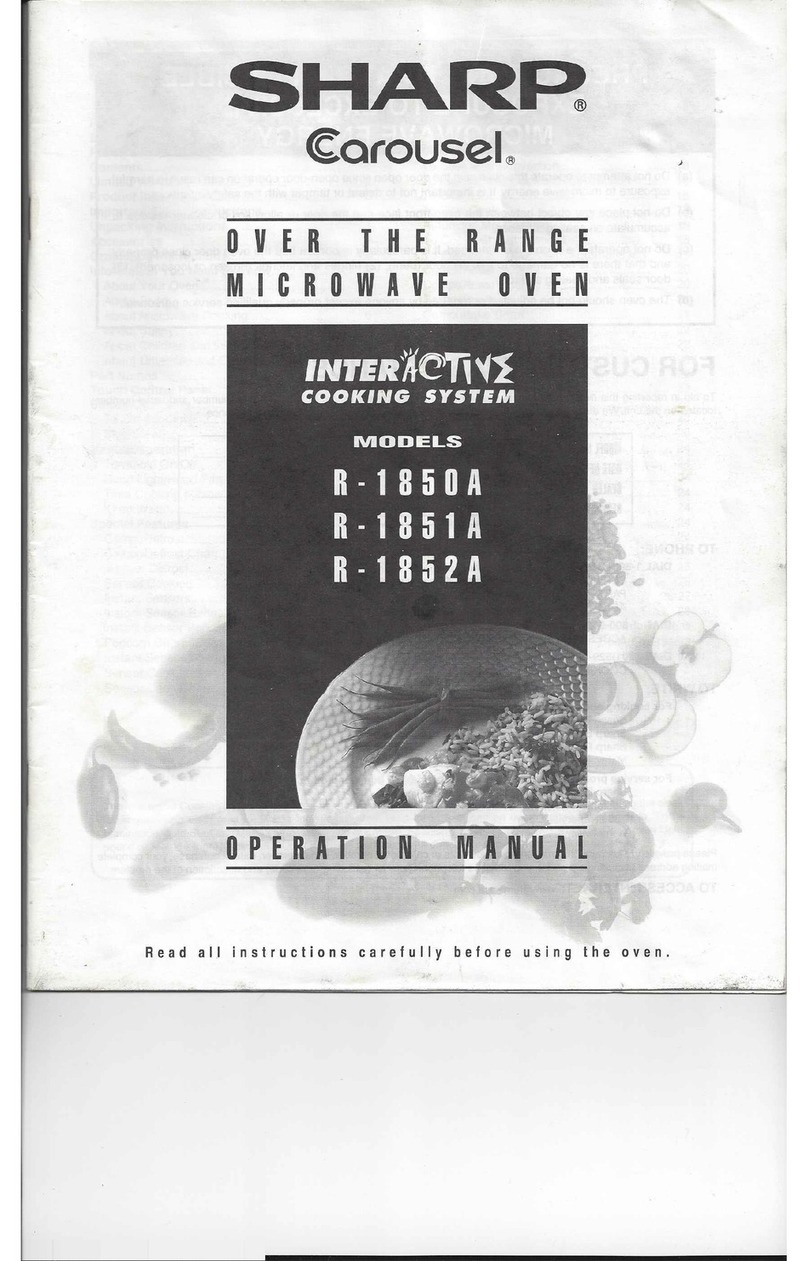
Sharp
Sharp Carousel R-1852A User manual

Sharp
Sharp R-959(SL)M-AA User manual