Shibaura COMPO ARM BA-III Series User manual

Original Instructions
Keep this manual nearby for future reference.
MODEL:BE30
Side mounted motor axis
ACTUATOR INSTRUCTION MANUAL
ACTUATOR INSTRUCTION MANUAL
S
E
R
I
E
S

Introduction
Before using the COMPO ARM BA-III series, read through and completely understand this instruction manual to
assure correct use.
For general information for the COMPO ARM BA-III Series, refer to CA25 Instruction Manual (Basic Part).
CAUTION
1. About application of this product
•This product is not designed or manufactured to be used in equipment in situations that can affect or endanger
human life.
•When considering this product for operation in special applications (passenger transportation, medical,
aerospace, atomic power, electric power, etc.), please contact our sales section.
•Although this product was manufactured under conditions of strict quality control, you are strongly advised to
install safety devices to forestall serious accidents when it is used in facilities where a breakdown in the
product is likely to cause a serious accident.
2. This equipment does not have an explosion-proof structure. Take utmost care of the operating environment.
3. All efforts have been made to assure the contents of this manual. If you have any questions, or find any
mistakes, however, please contact Shibaura Machine.
4. Shibaura Machine will not be held responsible for any effects caused by using this equipment, regardless of Item
3 above.
5. The contents of this manual are subject to change without prior notice to effect improvements.
Copyright 2022 by SHIBAURAMACHINE CO., LTD..
All rights reserved.
No part of this document may be reproduced in any form without obtaining prior written permission from
SHIBAURA MACHINE CO., LTD..
The information contained in this manual is subject to change without notice to effect improvements.

Contents
Chapter 1 Safety...........................................................................................................................................................1
■1.1 Cautions for safety...........................................................................................................................................1
■1.2 For your safe operation ....................................................................................................................................5
■1.3 Warranty ..........................................................................................................................................................9
Chapter 2 Shipment List.............................................................................................................................................10
■2.1 Shipment list ..................................................................................................................................................10
Chapter 3 Axis Specifications....................................................................................................................................11
■3.1 Axis type and names of individual parts ........................................................................................................11
■3.2 Single axis specification ................................................................................................................................12
Chapter 4 Installing Actuator (Axis) ..........................................................................................................................17
■4.1 Installing Actuator (Axis) ..............................................................................................................................18
■4.2 Robot type for each Axis................................................................................................................................19
■4.3 Parameter values ............................................................................................................................................20
Chapter 5 Precautions for Use....................................................................................................................................22
■5.1 Servo gain setting ..........................................................................................................................................22
■5.2 Fluctuation in sliding resistance during long-term storage.............................................................................25
Chapter 6 Maintenance ..............................................................................................................................................26
■6.1 Precautions for inspection and maintenance work .........................................................................................26
■6.2 Inspection before starting the work................................................................................................................27
■6.3 Periodic inspection.........................................................................................................................................27
■6.4 Maintenance Schedule ...................................................................................................................................28
■6.5 Cleaning.........................................................................................................................................................30
■6.6 Timing belt inspection ...................................................................................................................................30
■6.7 Greasing.........................................................................................................................................................31
■6.8 Motor and belt replacement procedure...........................................................................................................32
■6.9 Changing side mounted motor direction........................................................................................................34
■6.10 Origin position adjustment...........................................................................................................................35
■6.11 Replacement of ball screw ...........................................................................................................................37
■6.12 Replacement of linear guide ........................................................................................................................37
■6.13 Bolt and screw tightening torque .................................................................................................................37
Chapter 7 Spare Parts.................................................................................................................................................38
■7.1 Spare Parts .....................................................................................................................................................38

1
Overview
•This manual describes the axis type expression method, specifications and motor replacement procedures, etc.,
according to the type of axis.
•For the installation, see the instruction manual (installation of actuator) provided separately.
Chapter 1 Safety
■1.1 Cautions for safety
●Before the installation, programming, operation, maintenance and inspection of the equipment, be sure to
read through this manual so that you can use the COMPOARM with safety.
●After you have read this manual, keep it nearby for future reference.
This manual contain the important information to prevent injury to the operators and persons nearby, to prevent
damage to assets and to assure correct use of the equipment.
Make sure that you have well understood the following details (indications and symbols) before reading this manual.
Always observe the information that is noted.
: If you have neglected this instruction and caused a handling error, death or serious injury
may occur.
: If you have neglected this instruction and caused a handling error, human injury or
property damage (damages to houses, household goods and domestic animals) may
occur.
: This gives a brief description of the major points of operation procedures, precautions
and method for effective use of the machine.
Be sure to observe the instructions for ensuring
operation safety of the COMPO ARM.
CAUTION
WARNING
CAUTION

2
WARNING
•Install the safety fences to prevent anyone from entering the working envelope of the robot.
When the door is attached to the safety fence, the robot should be stopped at emergency at the
same time that the door has opened.
•Connect the EMERGENCY STOP pushbutton switch to the emergency stop input terminal of
the controller and mount the same switch at an easy-to-operate place in an emergency.
The EMEGENCY STOP switch must not be reset automatically and cannot be reset negligently by
any person.
•Wiring should be done safely and completely according to the Electrical Installations
Technical Requirements and Interior Wiring Requirements of Japan.
Incorrect wiring will result in an electric shock or a fire.
•The equipment MUST NOT be repaired or modified without prior written permission from the
manufacturer.
Otherwise, an accident or damage will be caused.
•Before the maintenance and inspection, be sure to turn off the controller main power switch.
Take all necessary measures to prevent anyone other than the worker engaged in
adjustment of the robot from negligently turning the power on. (Lock the switch and put a
tag showing "DO NOT turn the power on.")
Also, DO NOT touch the controller interior ten (10) minutes after the power is turned off.
Otherwise, you may get an electric shock due to residual voltage of the capacitor.
•DO NOT touch the motor, heat sink and cement resistor in the controller.
They are too hot and you may get burnt. Before performing inspection, take enough time to cool
them off.
•DO NOT pour water on the equipment interior or exterior, or drain water from it. Otherwise,
you may get an electric shock, or the equipment will be damaged.
When the equipment has contaminated, wipe it off with a hard squeezed cloth. DO NOT use a
thinner, benzine or other organic solvent.
•DO NOT throw away metals, combustibles or other contaminant into the opening of this
equipment.
A fire or an electric shock will be caused.
•DO NOT put your finger or hand on the movable part or opening of the equipment.
Otherwise, you may get injured.
•When using the actuator in other than the horizontal state, be sure to select the actuator with
brake.
Otherwise, the slider will drop at power OFF, and you will be injured.

3
WARNING
•As the equipment is heavy, make sure of its weight and gravity center position and
disconnect the cables when carrying the equipment.
Also, DO NOT carry the equipment with the slider. Otherwise, the slider will move and you will get
injured.
•DO NOT use this equipment for the living body as a massaging machine.
Otherwise, you will be injured due to incorrect teaching or mis-operation.
•This equipment has not a sealed structure. During use, grease of the ball screw or wear of
the belt may scatter from the opening of the equipment.
When using this equipment for food and chemical applications, take appropriate measures against
entry of them.
•Enter the robot type and initialize the memory correctly.
Otherwise, the robot may move unexpectedly and you will be injured.
•DO NOT use this equipment in an atmosphere of inflammable gas or an atmosphere
inducing an explosion.
As this equipment is not explosion-proof, it may explode in the worst occasion.
•DO NOT damage, break, process, forcibly bend, stretch, place a heavy object on or pinch the
cables (power cable, controller cable).
Otherwise, an electric shock or a fire will be caused.
•Should an abnormality such as smoke or nasty smell occur, turn the power off immediately
and stop using the equipment.
If the equipment is used continuously, an electric shock or a fire will be caused.
When using the side mounted motor axis in the vertical condition, be sure to check for the
belt on a regular basis. Replace the belt every 3,000-hour operation.
If the belt whose service life already ended is used continuously, it may be broken or the slider may
drop, and you will be injured.

4
CAUTION
•DO NOT place the equipment at a place where the ambient temperature exceeds 40°C, or
where the temperature changes sharply, causing condensing, or where it is exposed to
direct sunlight.
Additionally, if the equipment is installed at a narrow place, the ambient temperature rises due to
heat generation in the controller itself or external device, which will result in malfunction or
mis-operation of the equipment.
•DO NOT use the equipment at a place where an impact or vibration is involved. Also, DO
NOT use the equipment in an atmosphere where conductive dust, corrosive gas or oil mist
generates.
Otherwise, a fire, electric shock, malfunction or mis-operation will be caused.
•DO NOT use the equipment at a place where too much dust or dirt exists.
If the equipment is used at such a place, it may malfunction because this equipment is not
dust-proof.
•DO NOT use repair parts other than those designated by the manufacturer.
Otherwise, the equipment cannot be operated to its full capacity and will cause malfunction.
•Mount the robot on a highly rigid frame.
If rigidity of the frame is not enough, vibration (or resonance) may be caused during the robot
operation, adversely affecting the operation.
•In the case of power failure, this equipment becomes a free running state. When devices or
work pieces may be damaged by free running of this machine, use an axis equipped with
brake even if the axis is installed horizontally.
This machine does not have a dynamic brake function.
The brake of this machine is a holding brake. The holding brake cannot be used for deceleration.
If you want to use it as a used for deceleration, please contact us.
•Do not apply force to the slider that exceeds the maximum speed of this machine.
It may cause a malfunction.
•Do not connect or disconnect a connector with the controller turned ON.
Malfunction may be caused.
•Take safety measures against fall and scatter of a work piece.
If collision occurs, the axis decelerates suddenly and a work piece may fall and scatter.
•Perform risk assessment for entire equipment and take required protective measures.
•When discarding this product, dispose correctly as an industrial waste.

5
■1.2 For your safe operation
When you use the COMPO ARM BA-III series, be sure to take the measures in conformity to the following
instruction:
This machine is an industrial robot in conformance to the provisions of Paragraph 31of Article 36 of the Ordinance on
Industrial Safety and Hygiene. Necessary cautions are specified in the "Selection", "Installation", "Use", "Periodic
Inspection, etc." and "Education" of the "Technical Guideline on Safety Standards for Use of Industrial Robot"
conforming to theArticle 28 of the Industrial Safety and Health Law. You are requested to read them carefully and
to observe the instructions. The following introduces some of them.
■1.2.1 Safety measures
(1) A safety barrier shall be provided to ensure that any person cannot enter the working area of a robot.
1. The barrier shall have sufficient strength to withstand
the force generated during the work or environmental
conditions. The barrier shall have such a structure
that cannot be easily adjusted, removed or cleared.
2. The safety barrier shall be free from any serrated or
sharp edge or protrusions.
3. The safety barrier shall be designed in a stationary
structure.
4. When a safety barrier is equipped with a door, an
interlock shall be provided so that the robot will be
stopped by opening of the door.
(2) An emergency stop device shall be installed where the robot can be easily stopped by the operator immediately
in the event of emergency.
1. The emergency stop function shall ensure immediate
and reliable stop of a robot when the emergency stop
button switch has been operated by an operator.
2. The emergency stop button shall be red.
3. The emergency stop device shall be located so that it
can be easily pulled, pressed or touched by the
operator, and it can block a beam of light.
4. The emergency stop button shall be structured in such
a way that it is not automatically reset after having
been operated, and cannot be reset carelessly.
(3) For safety, never modify the robot main unit or control device.
No
admittance
Emergency
stop button

6
■1.2.2 Precautions for installation
Observe the following instructions when installing a robot:
(1) The robot shall be laid out to ensure the work space required for robot teaching, maintenance and inspection.
(2) The robot controller, other controllers and stationary operation panel shall be installed outside the movable range
and where the operator can watch the robot operations.
(3) The pressure gauge, hydraulic pressure gauge and other instruments shall be installed in clearly visible positions.
(4) The electric wiring and hydraulic/pneumatic piping shall be provided with protective covers if they may be
damaged.
(5) To ensure effective operation of the emergency stop device in the event of emergency, emergency stop device
switches shall be installed on locations other than the operation panel, as required.
■1.2.3 Precautions for use
Observe the following instructions when using a robot:
[Work within the movable range]
(1) Work provisions
Determine provisions for the following items and perform the work in conformity to them:
1. Root operation methods and procedures required in the work such as startup method and switch handling
method.
2. Speed of robot main unit in teaching.
3. Signaling method for work adjustment among more than one operator.
4. Action to be taken by the operator for each problem.
5. Procedures for confirming the release of the emergency and safety when restarting the robot operation after
the robot operation has been stopped due to the operation of the emergency stop device.
6. Measures to protect against the hazard due to unexpected operation of the robot described below (in addition
to the above items), or the hazard caused by a robot operation error.
- Indication on the operation panel.
- Measures to ensure safety of the operator working within the movable range.
- Working position and posture.
- Prevention of operation error due to noise.
- Signaling method for work adjustment with operators of related devices.
- Error type and evaluation procedure.
7. The work provisions shall meet the requirements of the robot type, installation site and work.
8. The work provisions shall be prepared by consultation with the related operators, manufacturer's engineers
and industrial safety consultant.
(2) Indication on the operation panel
To ensure that the start switch and selector switch will not be carelessly operated by a person other than the
personnel in charge of this work, the switch shall be provided with an easy-to-read indication to show that the
work is in progress. Alternatively, the operation panel cover shall be provided with locking or other means.

7
(3) Measures to ensure the operation safety of the personnel working within the movable range
Any one of the following measures or other measures on the equal or higher level shall be taken so that you can
stop the robot operation immediately in the event of an error when working within the movable range:
1. An adequately authorized supervisor shall be assigned outside the movable range and where the robot
operations can be observed. This supervisor shall be exclusively in charge of the supervision and shall be
responsible for the following:
- The supervisor shall cause the emergency stop device to be operated immediately in the event of an error.
- The supervisor shall ensure that a person other than the personnel in charge of this work is kept outside the
movable range.
2. The emergency stop device switch shall be placed under the control of the person working within the
movable range.
3. A portable operation panel having a structure capable of on/off operation of the power source, oil hydraulic
or pneumatic source shall be used in the work.
(4) Inspection prior to start of the work such as teaching
Prior to start of the work such as teaching, the following items shall be inspected. If any error is detected,
immediately repair the trouble or take other required action.
1. Check if the covering or sheathing of the external power source is damaged or not. (This check must be
made after the power has been turned off).
2. Check if the operation of the robot proper is faulty.
3. Check for the functions of the braking device and emergency stop device.
4. Check if there is any leakage of air or oil from the piping.
(5) Cleaning of working tools
When such working tools as a painting nozzle are mounted on the robot proper, and these working tools must be
cleaned, it is preferred that these tools should be automatically cleaned so that the number of machines entering
the movable range can be minimized.
(6) Release of residual pressure
Before disassembling the pneumatic components or replacing their parts, release the residual pressure in the
drive cylinder.
(7) Operation check
Perform the verification operation without entering the movable range, wherever possible.
(8) Illuminance
The illuminance required for operation safety shall be maintained.
[For automatic operation]
(1) Action before startup
Before starting the robot, check for the following items in advance and determine a signaling method for work
adjustment among related operators.
1. Make sure that there is no person within the movable range.
2. The movable operation panel and tools shall be located at specified positions.
3. There shall be no error indication for the robot or related devices.
(2) Action for automatic operation and in the event of an error
1. Make sure that there is an indication to show that the automatic operation is now in progress, after the robot
has been started.
2. When a problem has occurred to the robot or related device and you have to enter the movable range to take
emergency measures, stop the robot operation, for example, by operating the emergency stop device before
entering the movable range. At the same time, carry a safety plug with you, and ensure that the start switch
is provided with the indication to show that the work is now in progress. Take measures so that any other
person than the operator in charge of the emergency measures cannot operate the robot.

8
Warning label for actuator
Part number: 55620157
WARNING
•Before the installation, programming, operation, maintenance and
inspection of the equipment, be sure to read through this manual so that
you can use the COMPOARM with safety.
•Install the safety fences to prevent anyone from entering the working
envelope of the robot.
•DO NOT put your finger or hand on the movable part or opening of the
equipment. Otherwise, you may get injured.
•When using the actuator in other than the horizontal state, be sure to
select the actuator with brake. Otherwise, the slider will drop at power
OFF, and you will be injured.
For the safety instructions which seem especially important, relevant warning label is
attached to the equipment.
When the label attached to the equipment has peeled off or the characters are defaced and
unreadable, please procure it from our sales agent in your territory by specifying the part
number, and attach it to the original place.
Requesting your cooperation

9
■1.3 Warranty
■1.3.1 Warranty period
This product is warranted for one of the following periods whichever comes first.
(1) For 24 months after shipment from our factory.
(2) For 18 months after installation at the customer's factory.
(3) For 4000 hours of operation.
■1.3.2 Details of warranty
(1) This product is warranted. The scope of the warrant includes the specifications and functions described in the
Specification, catalog and Instruction Manual. We are not responsible for any secondary or incidental damages
caused by the trouble of this product.
(2) We will repair, on a free-of-charge basis, the trouble caused in the handling or use of the product within the
warranty period of this product as described in the Instruction Manual attached to this product. Alternatively,
such trouble will be repaired after the product has been returned to our factory. If the problem is solved by a
dispatch of service personnel to meet the convenience of the customer, we may claim payment from your
company regarding the transportation expenses, lodging expenses or other expenditures not directly related to
the repair of the product.
■1.3.3 Exemption from responsibility
The following cases shall be excluded from the scope of warrant.
(1) The trouble and damage caused by the use of the product according to a method not described in the Instruction
Manual, or by a careless error in use.
(2) Problems caused by chronological changes or wear by use (such as natural fading of paints, deterioration of the
consumable parts*1).
(3) Problems caused by sensory phenomena (e.g. generated noise without affecting the function).
(4) Modification or disassembling not authorized by our company.
(5) Troubles or damages caused by inadequate maintenance and inspection or improper repair.
(6) Troubles or damages caused by natural disaster, fire and other external factors.
(7) Internal data such as programs and points created or modified by the customer.
(8) Problems caused when this product purchased in Japan is brought to an overseas country.
*1:Consumable parts are defined as the parts maintenance replacement parts (spare parts) described in the
Instruction Manual of each product, and the parts (e.g. backup battery) that must be replaced on a periodic basis.
■1.3.4 Precautions
(1) When you have used the product beyond the specifications of the product, we cannot warrant the basic
performances of the product.
(2) Should you fail to observe the instructions given in "WARNING" and "CAUTION" described in the Instruction
Manual, we are not responsible for any personal injury, damages or trouble that may occur.
(3) Please note that the "WARNING" and "CAUTION" described in the Instruction Manual, and other descriptions
are within the scope assumed by our company.
(4) The numerical values given as technical data are theoretical values as a guideline showing the durability and
others. They shall not be construed as indicating warranty. Note that these values are subject to change
according to the conditions of use.

10
Chapter 2 Shipment List
■2.1 Shipment list
When the axis proper is shipped, it is composed of the following parts:
(1) Actuator (axis)
(2) Number of oval bolts attached (M6×30)
The above-mentioned axs-1 will be provided with the bolts in the number shown in the right-hand Table.
Axis stroke (mm)
Attached quantity
100~200
12
250~600
16
650~1000
20
1050~1250
26
(3) Introduction Manual

11
Chapter 3 Axis Specifications
■3.1 Axis type and names of individual parts
■Type of axis
The following shows the axis type:
BE30E-UR-M20N-40X
■Names of individual parts
Frame
Frame cover
Belt cover
Motor cover
Slider
End cover
Slider type
M
Medium slider
L
Long slider
Brake
N
Without brake
B
With brake
Ball screw lead
20
20 mm
10
10 mm
05
5 mm
Option
None
Standard
X
Modified product
Series name
Frame No.
30
Size M
Axis stroke
10
100 mm
15
150 mm
20
200 mm
:
:
A0
1000 mm
A5
1050 mm
:
:
C0
1200 mm
Motor set direction
UR
Right side mounted axis
UL
Left side mounted axis
UU
Right side mounted axis
Type of motor
E
100 W Absolute
F
200 W Absolute

12
■3.2 Single axis specification
■Specifications
Type of axis BE30E-U--
Motor
AC 100-watt servo motor absolute
Drive method
Ball screw 15 Lead 20 mm
Lead 10 mm
Lead 5 mm
Guide method
Linear guide (Double)
Bearing block ... 4 pieces
Maximum payload
mass
(Note 1) (Note 3)
Ball screw lead
Horizontal
Vertical
-
Regeneration
unit used
20 mm
30 kg
3 kg
5 kg
10 mm
55 kg
8 kg
12 kg
5 mm
80 kg
15 kg
22 kg
Maximum speed
(Note 1) (Note 2)
Ball screw lead 20 mm
1200 mm/s
Ball screw lead 10 mm
600 mm/s
Ball screw lead 5 mm
300 mm/s
Static permissible
moment (Note 4)
Medium slider
MR:510 Nm MP:430 Nm MY:370 Nm
Long slider
MR:510 Nm MP:750 Nm MY:650 Nm
Repeated positioning accuracy (Note 5)
±0.01 mm
Resolution
0.01 mm
Rated thrust
Ball screw lead 20 mm
100 N
Ball screw lead 10 mm
200 N
Ball screw lead 5 mm
400 N
(Note 1) This indicates the value when the acceleration/deceleration time is 0.36 s or more.
(Note 2) The maximum speed will be as follows, depending on the axis stroke.
Stroke range
Maximum speed
Lead 20 mm
Lead 10 mm
Lead 5 mm
600 mm or less
1200 mm/s
600 mm/s
300 mm/s
650~700mm
1000 mm/s
500 mm/s
250 mm/s
750~800mm
800 mm/s
400 mm/s
200 mm/s
850~1000mm
600 mm/s
300 mm/s
150 mm/s
1050~1200mm
400 mm/s
200 mm/s
(Note 3) Set the pause time after movement to 1.0 sec or longer.
(Note 4)
MR: Rolling Moment
MP: Pitching Moment
MY: Yawing Moment
(Note 5) Repeatability in one direction during 7 trials at a constant ambient temperature of 20℃. It is
not absolute positioning accuracy. Trajectory accuracy is not guaranteed.
MP
MY
MR

13
Type of axis BF30E-U--
Motor
AC 200-watt servo motor absolute
Drive method
Ball screw 15 Lead 20 mm
Lead 10 mm
Lead 5 mm
Guide method
Linear guide (Double)
Bearing block ... 4 pieces
Maximum payload
mass
(Note 1) (Note 3)
Ball screw lead
Horizontal
Vertical
-
Regeneration
unit used
20 mm
40 kg
3 kg
10 kg
10 mm
80 kg
8 kg
20 kg
5 mm
100 kg
15 kg
40 kg
Maximum speed
(Note 1) (Note 2)
Ball screw lead 20 mm
1200 mm/s
Ball screw lead 10 mm
600 mm/s
Ball screw lead 5 mm
300 mm/s
Static permissible
moment (Note 4)
Medium slider
MR:510 Nm MP:430 Nm MY:370 Nm
Long slider
MR:510 Nm MP:750 Nm MY:650 Nm
Repeated positioning accuracy (Note 5)
±0.01 mm
Resolution
0.01 mm
Rated thrust
Ball screw lead 20 mm
200 N
Ball screw lead 10 mm
400 N
Ball screw lead 5 mm
800 N
(Note 1) This indicates the value when the acceleration/deceleration time is 0.36 s or more.
(Note 2) The maximum speed will be as follows, depending on the axis stroke.
Stroke range
Maximum speed
Lead 20 mm
Lead 10 mm
Lead 5 mm
600 mm or less
1200 mm/s
600 mm/s
300 mm/s
650~700mm
1000 mm/s
500 mm/s
250 mm/s
750~800mm
800 mm/s
400 mm/s
200 mm/s
850~1000mm
600 mm/s
300 mm/s
150 mm/s
1050~1200mm
400 mm/s
200 mm/s
(Note 3) Set the pause time after movement to 1.0 sec or longer.
(Note 4)
MR: Rolling Moment
MP: Pitching Moment
MY: Yawing Moment
(Note 5) Repeatability in one direction during 7 trials at a constant ambient temperature of 20℃. It is
not absolute positioning accuracy. Trajectory accuracy is not guaranteed.
MP
MY
MR

14
■Axis dimensions
[BE30*-UR-****]
Note: The value in parenthesis applies to the axis with a brake.
The "**" portion of the type indicates the ball screw lead.
(20 for the ball screw lead of 20 mm, 10 for the ball screw lead of 10 mm, and 05 for the ball screw lead of 5 mm)
Type
With 100W
motor
Without brake
BE30E-UR-
M**N-10
BE30E-UR-
M**N-20
BE30E-UR-
M**N-30
BE30E-UR-
M**N-40
BE30E-UR-
M**N-50
BE30E-UR-
M**N-60
BE30E-UR-
M**N-70
BE30E-UR-
M**N-80
BE30E-UR-
M**N-90
BE30E-UR-
M**N-A0
BE30E-UR-
M**N-B0
BE30E-UR-
M**N-C0
With brake
BE30E-UR-
M**B-10
BE30E-UR-
M**B-20
BE30E-UR-
M**B-30
BE30E-UR-
M**B-40
BE30E-UR-
M**B-50
BE30E-UR-
M**B-60
BE30E-UR-
M**B-70
BE30E-UR-
M**B-80
BE30E-UR-
M**B-90
BE30E-UR-
M**B-A0
BE30E-UR-
M**B-B0
BE30E-UR-
M**B-C0
With 200W
motor
Without brake
BE30F-UR-
M**N-10
BE30F-UR-
M**N-20
BE30F-UR-
M**N-30
BE30F-UR-
M**N-40
BE30F-UR-
M**N-50
BE30F-UR-
M**N-60
BE30F-UR-
M**N-70
BE30F-UR-
M**N-80
BE30F-UR-
M**N-90
BE30F-UR-
M**N-A0
BE30F-UR-
M**N-B0
BE30F-UR-
M**N-C0
With brake
BE30F-UR-
M**B-10
BE30F-UR-
M**B-20
BE30F-UR-
M**B-30
BE30F-UR-
M**B-40
BE30F-UR-
M**B-50
BE30F-UR-
M**B-60
BE30F-UR-
M**B-70
BE30F-UR-
M**B-80
BE30F-UR-
M**B-90
BE30F-UR-
M**B-A0
BE30F-UR-
M**B-B0
BE30F-UR-
M**B-C0
Stroke X (mm)
100
200
300
400
500
600
700
800
900
1000
1100
1200
Full length L(mm)
361.9
461.9
561.9
661.9
761.9
861.9
961.9
1061.9
1161.9
1261.9
1361.9
1461.9
Weight (kg)
With 100W motor
7.8(8.1)
9.0(9.3)
10.2(10.5)
11.4(11.7)
12.6(12.9)
13.8(14.1)
15.0(15.3)
16.2(16.5)
17.4(17.7)
18.6(18.9)
19.8(20.1)
21.0(21.3)
With 200W motor
8.3(8.9)
9.5(10.1)
10.7(11.3)
11.9(12.5)
13.1(13.7)
14.3(14.9)
15.5(16.1)
16.7(17.3)
17.9(18.5)
19.1(19.7)
20.3(20.9)
21.5(22.1)
Type
With 100W
motor
Without brake
BE30E-UR-
L**N-15
BE30E-UR-
L**N-25
BE30E-UR-
L**N-35
BE30E-UR-
L**N-45
BE30E-UR-
L**N-55
BE30E-UR-
L**N-65
BE30E-UR-
L**N-75
BE30E-UR-
L**N-85
BE30E-UR-
L**N-95
BE30E-UR-
L**N-A5
BE30E-UR-
L**N-B5
With brake
BE30E-UR-
L**B-15
BE30E-UR-
L**B-25
BE30E-UR-
L**B-35
BE30E-UR-
L**B-45
BE30E-UR-
L**B-55
BE30E-UR-
L**B-65
BE30E-UR-
L**B-75
BE30E-UR-
L**B-85
BE30E-UR-
L**B-95
BE30E-UR-
L**B-A5
BE30E-UR-
L**B-B5
With 200W
motor
Without brake
BF30F-UR-
L**N-15
BF30F-UR-
L**N-25
BF30F-UR-
L**N-35
BF30F-UR-
L**N-45
BF30F-UR-
L**N-55
BF30F-UR-
L**N-65
BF30F-UR-
L**N-75
BF30F-UR-
L**N-85
BF30F-UR-
L**N-95
BF30F-UR-
L**N-A5
BF30F-UR-
L**N-B5
With brake
BF30F-UR-
L**B-15
BF30F-UR-
L**B-25
BF30F-UR-
L**B-35
BF30F-UR-
L**B-45
BF30F-UR-
L**B-55
BF30F-UR-
L**B-65
BF30F-UR-
L**B-75
BF30F-UR-
L**B-85
BF30F-UR-
L**B-95
BF30F-UR-
L**B-A5
BF30F-UR-
L**B-B5
Stroke X (mm)
150
250
350
450
550
650
750
850
950
1050
1150
Full length L(mm)
461.9
561.9
661.9
761.9
861.9
961.9
1061.9
1161.9
1261.9
1361.9
1461.9
Weight (kg)
With 100W motor
9.3(9.6)
10.5(10.8)
11.7(12.0)
12.9(13.2)
14.1(14.4)
15.3(15.6)
16.5(16.8)
17.7(18.0)
18.9(19.2)
20.1(20.4)
21.3(21.6)
With 200W motor
9.8(10.3)
11.0(11.6)
12.2(12.8)
13.4(14.0)
14.6(15.2)
15.8(16.4)
17.0(17.6)
18.2(18.8)
19.4(20.0)
20.6(21.2)
21.8(22.4)
[B30*-UR-M***]
[BE30*-UR-L***]

15
[BE30*-UL-****]
Note: The value in parenthesis applies to the axis with a brake.
The "**" portion of the type indicates the ball screw lead.
(20 for the ball screw lead of 20 mm, 10 for the ball screw lead of 10 mm, and 05 for the ball screw lead of 5 mm)
Type
With 100W
motor
Without brake
BE30E-UL-
M**N-10
BE30E-UL-
M**N-20
BE30E-UL-
M**N-30
BE30E-UL-
M**N-40
BE30E-UL-
M**N-50
BE30E-UL-
M**N-60
BE30E-UL-
M**N-70
BE30E-UL-
M**N-80
BE30E-UL-
M**N-90
BE30E-UL-
M**N-A0
BE30E-UL-
M**N-B0
BE30E-UL-
M**N-C0
With brake
BE30E-UL-
M**B-10
BE30E-UL-
M**B-20
BE30E-UL-
M**B-30
BE30E-UL-
M**B-40
BE30E-UL-
M**B-50
BE30E-UL-
M**B-60
BE30E-UL-
M**B-70
BE30E-UL-
M**B-80
BE30E-UL-
M**B-90
BE30E-UL-
M**B-A0
BE30E-UL-
M**B-B0
BE30E-UL-
M**B-C0
With 200W
motor
Without brake
BE30F-UL-
M**N-10
BE30F-UL-
M**N-20
BE30F-UL-
M**N-30
BE30F-UL-
M**N-40
BE30F-UL-
M**N-50
BE30F-UL-
M**N-60
BE30F-UL-
M**N-70
BE30F-UL-
M**N-80
BE30F-UL-
M**N-90
BE30F-UL-
M**N-A0
BE30F-UL-
M**N-B0
BE30F-UL-
M**N-C0
With brake
BE30F-UL-
M**B-10
BE30F-UL-
M**B-20
BE30F-UL-
M**B-30
BE30F-UL-
M**B-40
BE30F-UL-
M**B-50
BE30F-UL-
M**B-60
BE30F-UL-
M**B-70
BE30F-UL-
M**B-80
BE30F-UL-
M**B-90
BE30F-UL-
M**B-A0
BE30F-UL-
M**B-B0
BE30F-UL-
M**B-C0
Stroke X (mm)
100
200
300
400
500
600
700
800
900
1000
1100
1200
Full length L(mm)
361.9
461.9
561.9
661.9
761.9
861.9
961.9
1061.9
1161.9
1261.9
1361.9
1461.9
Weight (kg)
With 100W motor
7.8(8.1)
9.0(9.3)
10.2(10.5)
11.4(11.7)
12.6(12.9)
13.8(14.1)
15.0(15.3)
16.2(16.5)
17.4(17.7)
18.6(18.9)
19.8(20.1)
21.0(21.3)
With 200W motor
8.3(8.9)
9.5(10.1)
10.7(11.3)
11.9(12.5)
13.1(13.7)
14.3(14.9)
15.5(16.1)
16.7(17.3)
17.9(18.5)
19.1(19.7)
20.3(20.9)
21.5(22.1)
Type
With 100W
motor
Without brake
BE30E-UL-
L**N-15
BE30E-UL-
L**N-25
BE30E-UL-
L**N-35
BE30E-UL-
L**N-45
BE30E-UL-
L**N-55
BE30E-UL-
L**N-65
BE30E-UL-
L**N-75
BE30E-UL-
L**N-85
BE30E-UL-
L**N-95
BE30E-UL-
L**N-A5
BE30E-UL-
L**N-B5
With brake
BE30E-UL-
L**B-15
BE30E-UL-
L**B-25
BE30E-UL-
L**B-35
BE30E-UL-
L**B-45
BE30E-UL-
L**B-55
BE30E-UL-
L**B-65
BE30E-UL-
L**B-75
BE30E-UL-
L**B-85
BE30E-UL-
L**B-95
BE30E-UL-
L**B-A5
BE30E-UL-
L**B-B5
With 200W
motor
Without brake
BF30F-UL-
L**N-15
BF30F-UL-
L**N-25
BF30F-UL-
L**N-35
BF30F-UL-
L**N-45
BF30F-UL-
L**N-55
BF30F-UL-
L**N-65
BF30F-UL-
L**N-75
BF30F-UL-
L**N-85
BF30F-UL-
L**N-95
BF30F-UL-
L**N-A5
BF30F-UL-
L**N-B5
With brake
BF30F-UL-
L**B-15
BF30F-UL-
L**B-25
BF30F-UL-
L**B-35
BF30F-UL-
L**B-45
BF30F-UL-
L**B-55
BF30F-UL-
L**B-65
BF30F-UL-
L**B-75
BF30F-UL-
L**B-85
BF30F-UL-
L**B-95
BF30F-UL-
L**B-A5
BF30F-UL-
L**B-B5
Stroke X (mm)
150
250
350
450
550
650
750
850
950
1050
1150
Full length L(mm)
461.9
561.9
661.9
761.9
861.9
961.9
1061.9
1161.9
1261.9
1361.9
1461.9
Weight (kg)
With 100W motor
9.3(9.6)
10.5(10.8)
11.7(12.0)
12.9(13.2)
14.1(14.4)
15.3(15.6)
16.5(16.8)
17.7(18.0)
18.9(19.2)
20.1(20.4)
21.3(21.6)
With 200W motor
9.8(10.3)
11.0(11.6)
12.2(12.8)
13.4(14.0)
14.6(15.2)
15.8(16.4)
17.0(17.6)
18.2(18.8)
19.4(20.0)
20.6(21.2)
21.8(22.4)
[BE30*-UL-M***]
[BE30*-UL-L***]

16
[BE30*-UU-****]
Note: The value in parenthesis applies to the axis with a brake.
The "**" portion of the type indicates the ball screw lead.
(20 for the ball screw lead of 20 mm, 10 for the ball screw lead of 10 mm, and 05 for the ball screw lead of 5 mm)
Type
With 100W
motor
Without brake
BE30E-UU-
M**N-10
BE30E-UU-
M**N-20
BE30E-UU-
M**N-30
BE30E-UU-
M**N-40
BE30E-UU-
M**N-50
BE30E-UU-
M**N-60
BE30E-UU-
M**N-70
BE30E-UU-
M**N-80
BE30E-UU-
M**N-90
BE30E-UU-
M**N-A0
BE30E-UU-
M**N-B0
BE30E-UR-
M**N-C0
With brake
BE30E-UU-
M**B-10
BE30E-UU-
M**B-20
BE30E-UU-
M**B-30
BE30E-UU-
M**B-40
BE30E-UU-
M**B-50
BE30E-UU-
M**B-60
BE30E-UU-
M**B-70
BE30E-UU-
M**B-80
BE30E-UU-
M**B-90
BE30E-UU-
M**B-A0
BE30E-UU-
M**B-B0
BE30E-UR-
M**B-C0
With 200W
motor
Without brake
BE30F-UU-
M**N-10
BE30F-UU-
M**N-20
BE30F-UU-
M**N-30
BE30F-UU-
M**N-40
BE30F-UU-
M**N-50
BE30F-UU-
M**N-60
BE30F-UU-
M**N-70
BE30F-UU-
M**N-80
BE30F-UU-
M**N-90
BE30F-UU-
M**N-A0
BE30F-UU-
M**N-B0
BE30F-UR-
M**N-C0
With brake
BE30F-UU-
M**B-10
BE30F-UU-
M**B-20
BE30F-UU-
M**B-30
BE30F-UU-
M**B-40
BE30F-UU-
M**B-50
BE30F-UU-
M**B-60
BE30F-UU-
M**B-70
BE30F-UU-
M**B-80
BE30F-UU-
M**B-90
BE30F-UU-
M**B-A0
BE30F-UU-
M**B-B0
BE30F-UR-
M**B-C0
Stroke X (mm)
100
200
300
400
500
600
700
800
900
1000
1100
1200
Full length L(mm)
361.9
461.9
561.9
661.9
761.9
861.9
961.9
1061.9
1161.9
1261.9
1361.9
1461.9
Weight (kg)
With 100W motor
7.8(8.1)
9.0(9.3)
10.2(10.5)
11.4(11.7)
12.6(12.9)
13.8(14.1)
15.0(15.3)
16.2(16.5)
17.4(17.7)
18.6(18.9)
19.8(20.1)
21.0(21.3)
With 200W motor
8.3(8.9)
9.5(10.1)
10.7(11.3)
11.9(12.5)
13.1(13.7)
14.3(14.9)
15.5(16.1)
16.7(17.3)
17.9(18.5)
19.1(19.7)
20.3(20.9)
21.5(22.1)
Type
With 100W
motor
Without brake
BE30E-UU-
L**N-15
BE30E-UU-
L**N-25
BE30E-UU-
L**N-35
BE30E-UU-
L**N-45
BE30E-UU-
L**N-55
BE30E-UU-
L**N-65
BE30E-UU-
L**N-75
BE30E-UU-
L**N-85
BE30E-UU-
L**N-95
BE30E-UU-
L**N-A5
BE30E-UU-
L**N-B5
With brake
BE30E-UU-
L**B-15
BE30E-UU-
L**B-25
BE30E-UU-
L**B-35
BE30E-UU-
L**B-45
BE30E-UU-
L**B-55
BE30E-UU-
L**B-65
BE30E-UU-
L**B-75
BE30E-UU-
L**B-85
BE30E-UU-
L**B-95
BE30E-UU-
L**B-A5
BE30E-UU-
L**B-B5
With 200W
motor
Without brake
BF30F-UU-
L**N-15
BF30F-UU-
L**N-25
BF30F-UU-
L**N-35
BF30F-UU-
L**N-45
BF30F-UU-
L**N-55
BF30F-UU-
L**N-65
BF30F-UU-
L**N-75
BF30F-UU-
L**N-85
BF30F-UU-
L**N-95
BF30F-UU-
L**N-A5
BF30F-UU-
L**N-B5
With brake
BF30F-UU-
L**B-15
BF30F-UU-
L**B-25
BF30F-UU-
L**B-35
BF30F-UU-
L**B-45
BF30F-UU-
L**B-55
BF30F-UU-
L**B-65
BF30F-UU-
L**B-75
BF30F-UU-
L**B-85
BF30F-UU-
L**B-95
BF30F-UU-
L**B-A5
BF30F-UU-
L**B-B5
Stroke X (mm)
150
250
350
450
550
650
750
850
950
1050
1150
Full length L(mm)
461.9
561.9
661.9
761.9
861.9
961.9
1061.9
1161.9
1261.9
1361.9
1461.9
Weight (kg)
With 100W motor
9.3(9.6)
10.5(10.8)
11.7(12.0)
12.9(13.2)
14.1(14.4)
15.3(15.6)
16.5(16.8)
17.7(18.0)
18.9(19.2)
20.1(20.4)
21.3(21.6)
With 200W motor
9.8(10.3)
11.0(11.6)
12.2(12.8)
13.4(14.0)
14.6(15.2)
15.8(16.4)
17.0(17.6)
18.2(18.8)
19.4(20.0)
20.6(21.2)
21.8(22.4)
[BE30*-UU-M***]
[BE30*-UU-L***]

17
Chapter 4 Installing Actuator (Axis)
This chapter describes the basic installation procedures for the axis and peripheral equipment.
Installation shall comply with the instructions of this Chapter. If the installation procedure is incorrect, robot
performance cannot be achieved. Not only that, the service life may be seriously reduced.
Precautions for installation
Environment of installation site
(1) The ambient environment for operation shall comply with the following requirements:
Ambient temperature Working temperature: 0C to 40C
Transportation and storage temperature: -10C to 50C
Relative humidity: 30 to 90%RH without dew condensation
Altitude: 1000 m or less
Vibration 0.98 m/s2or less
Dust: Free from conductive dust or dirt
Gas: Free from flammable or corrosive gas
Magnetic field: Free from a nearby device that may generate magnetic field
Radiation: Not in the radiation controlled area
Others: Without greasy fume
(2) This product is not designed as an explosion proof structure. Do not use it in a dusty place. Further, take
sufficient care of the environment since it is not explosion-proof.
(3) Do not use it in a place with an organic solvent or white kerosene..
Of guide or ball screw grease is melted. It may cause malfunction.
Precautions in installation
(1) Do not allow the product to fall down or be collided with other object during the transportation.
(2) Install the product where maintenance and inspection are easier.
(3) Install the controller within the range where it can be reached from the robot proper by a standard cable.
(4) Installation
Install the product on a horizontal installation base.
The installation base shall have the length that allows only the frame portion to be mounted.
The installation base shall be made of a steel plate having a thickness of 9 mm or more where the plate has a
machined surface with flatness of 0.2 or less. Install this product on this base to correct the bend and twist of
the axis frame and to reinforce the axis frame.
Install the oval bolts (installation bolts) of the axis at a pitch of approximately 150 mm.
CAUTION
This manual suits for next models
1
Table of contents
Other Shibaura Controllers manuals
Popular Controllers manuals by other brands
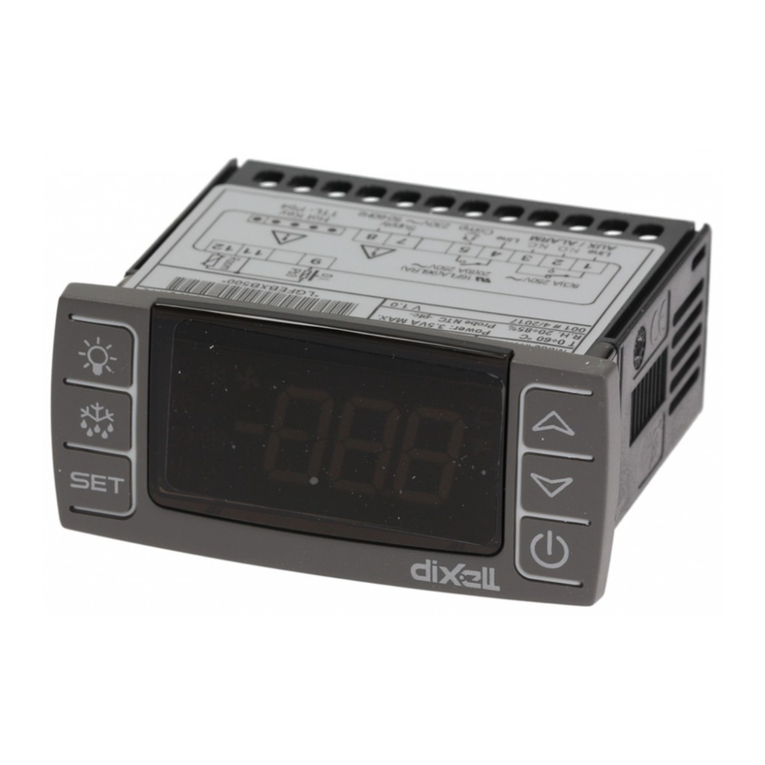
dixell
dixell XR30CX Installation and operating instructions
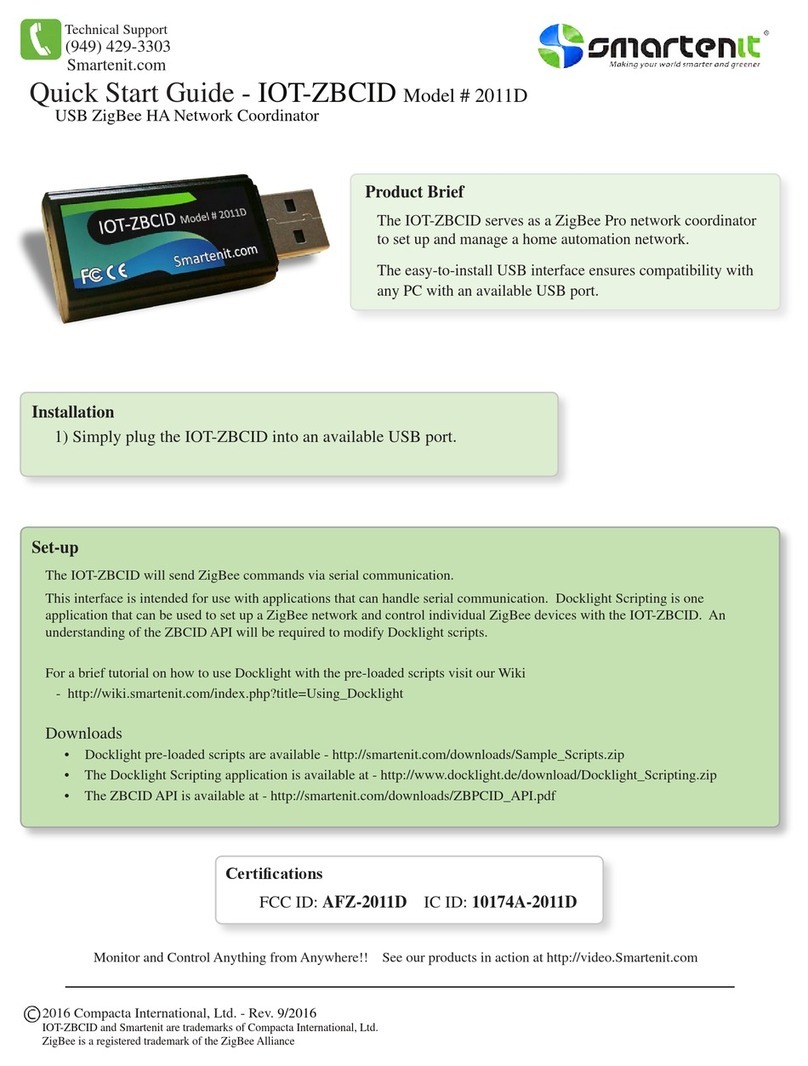
Smartenit
Smartenit 2011D quick start guide
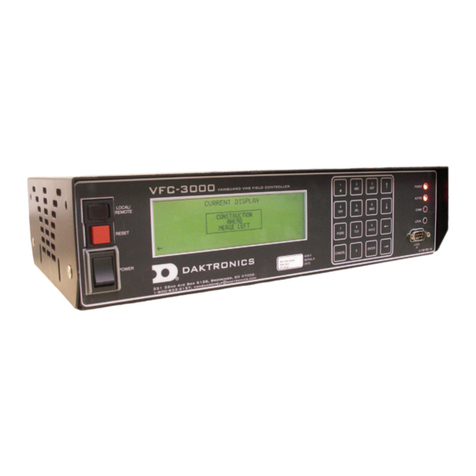
Daktronics
Daktronics VFC-3000 Operation manual
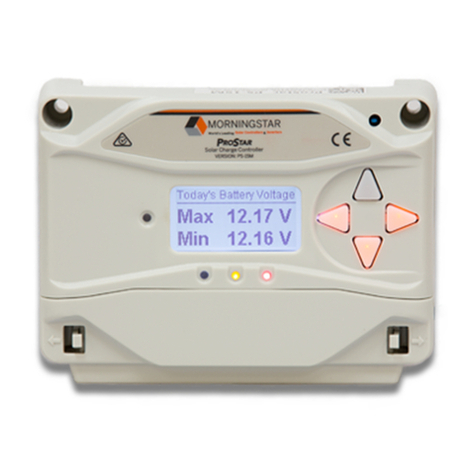
Morningstar
Morningstar ProStar PS-15 Installation, operation and maintenance manual
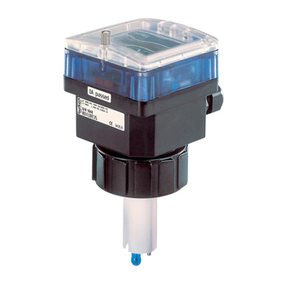
Burkert
Burkert 8205 user manual
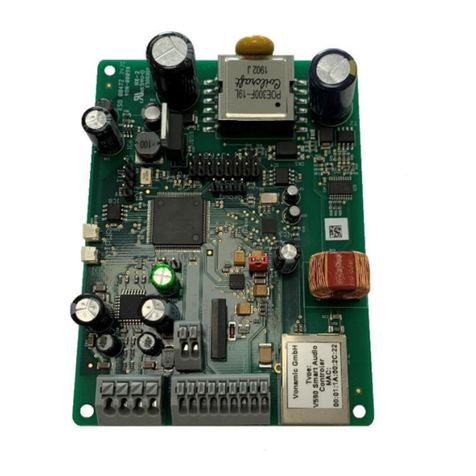
Vonamic
Vonamic VIPCOS 590 Configuration manual