Shugart SA810 User manual


TABLE OF CONTENTS
Page
TABLEOFCONTENTS
..............................................................
i
LIST OF FIGURES
...................................................................
iii
LIST OF TABLES
....................................................................
iv
ABBREVIATIONS/MNEMONICS
.......................................................
iv
SECTION I INTRODUCTION
.........................................................
1-1
1. 1 General Description . . . . . . . . . . . . . . . . . . . . . . . . . . . . . . . . . . . . . . . . . . . . . . . . . . . 1-1
1.2 Specifications Summary
................................................
1-1
1.2.1 Performance Specifications
........................................
1,.-1
1.2.2
Functional Specifications
.........................................
1-2
1.2.3
Physical Specifications
...........................................
1-2
1.2.4
Reliability Specifications
..........................................
1-3
1.3 Functional Characteristics
...............................................
1-3
1.3.1 Electronics
....................................................
1-3
1.3.2
Drive Mechanism
...............................................
1-4
1.3.3
Positioning Mechanism
...........................................
1-4
1.3.4
Read/Write Heads
..............................................
1-4
1.3.5
Recording Formats
..............................................
1-4
1.4
Functional Operations
.................................................
1-4
1.4.1 Power Sequencing
..............................................
1-4
1.4.2
Drive Selection
.................................................
1-4
1.4.3
Motor On
.....................................................
1-4
1.4.4
Track Accessing
................................................
1-6
1.4.5
Step Out
.....................................................
1-6
1.4.6
Step
In
.......................................................
1-6
1.4.7
Side Selection (SA860 Only)
....
_.
__
..............................
1-7
1.4.8
Read Operation
...............................
'
.................
1-8
1.4.9
Write Operation
........................
"
.......................
1-9
1.4.10
Sequence
of
Events
............................................
1-10
SECTION
II
ELECTRICAL INTERFACE
.................................................
2-1
2.1 Introduction
........................................................
2-1
2.2
Signal Interface
......................................................
2-1
2.2.1 InputLines
...................................................
2-1
2.2.2
Input Line Termination
..........................................
2-3
2.2.3
Drive Select 1-4
................................................
2-3
2.2.4
Side Select (SA860 Only)
........................................
2-3
2.2.5
Direction Select
................................................
2-4
2.2.6
Step
........................................................
2-4
2.2.7
Write Gate
....................................................
2-4
2.2.8
Write Data
....................................................
2-4
2.2.9
Motor On (Alternate Input)
.......................................
2-4
2.2.10
In
Use (Alternate Input)
.........................................
2-4
2.2.11
External Write Current Switch (Alternate Input)
........................
2-4
2.2.12
Output Lines
......................
:
..........................
2-5
2.2.13
. Track 00
....................................................
2-5
2.2.14
Index
......................................................
2-5
2.2.15
Sector (Hard Sector Only)
.......................................
2-5
2.2.16
Ready
......................................................
2-5
2.2.17
Read Data
...................................................
2-6
2.2.18
Sep
Data
....................................................
2-6
2.2.19
SepClock
...................................................
2-6
2.2.20
Write Protect . . . . . . . . . . . . . . . . . . . . . . . . . . . . . . . . . . . . . . . . . . . . . . . . . 2-6
2.2.21 True Ready
..................................................
2-6
2.2.22
Disk
Change (Optional Output)
..............................
;
....
2-6
2.2.23
Two Sided (Optional Output)
.....................................
2-6
2.2.24
Alternate
I/O
Pins
.............................................
2-6

TABLE
OF CONTENTS (CONT.)
2.3
Power Interface
......................................................
2-6
2.4
Frame Grounding
....................................................
2-7
SECTION
III
PHYSICAL INTERFACE
..................................................
3-1
3.1
Introduction
........................................................
3-1
3.2
Jl/Pl
Connector
...................................................
3-1
3.3
J2/P2
Connector
..................................................
3-2
SECTION
IV
DRIVE PHYSICAL SPECIFICATIONS
.......................................
4-1
4.1
Introduction
........................................................
4-1
4.2
Mechanical Dimensions
...........................................
~
...
4-1
4.3
Mounting
..........................................................
4-1
4.4
Stacking Dual Drives
.................................................
4-1
SECTION V ERROR RECOVERY
.....................................................
5-1
5.1 Write Errors
.......
. . . . . . . . . . . . . . . . . . . . . . . . . . . . . . . . . . . . . . . . . . . . . . . . . 5-1
5.2
Read Errors
........................................................
5-1
5.3
Seek
Errors. . . . . . . . . . . . . . . . . . . . . . . . . . . . . . . . . . . . . . . . . . . . . . . . . . . . . . . . . 5-1
SECTION
VI
RECORDING FORMAT
...................................................
6-1
6.1
Recording Format (Single Density)
.......................................
6-1
6.1.1
Bit
Cell
.....................................................
6-1
6.1.2
Byte
.......................................................
6-2
6.2
Recording Format (Double Density)
......................................
6-2
6.3
Rules of Encoding
...................................................
6-3
6.3.1
FM
Encoding
.................................................
6-3
6.3.2
MFM
Encoding
...............................................
6-3
6.4
Tracks and Recording Formats
..........................................
6-3
6.4.1
Tracks
......................................................
6-3
6.4.2
Track Format
.................................................
6-3
6.4.3
Hard Sector Recording Format
....................................
6-3
6.4.4
Soft Sector Recording Format
....................................
6-3
6.4.5
Typical Track Index Format
......................................
6-3
SECTION
VII
CUSTOMER INSTALLABLE OPTIONS
......................................
7-1
7.1 Introduction
.......................................................
7-1
7.2
External Write Current Switch . . . . . . . . . . . . . . . . . . . . . . . . . . . . . . . . . . . . . . . . . . 7-5
7.3
Two-Sided Status (Optional Output
SA860
only)
...........................
7-5
7.4
Disk Change (Optional Output)
.........................................
7-5
7.5
Side Selection Using Direction Select (SA860 only)
..........................
7-6
7.6
Side Selection Using Drive Select (SA860 only)
.............................
7-6
7.7
In
Use Alternate Input . . . . . . . . . . . . . . . . . . . . . . . . . . . . . . . . . . . . . . . . . . . . . . . . 7-7
7.8
Motor On Without Selecting Drive
.......................................
7-7
7.9
Motor On by Optional Motor
On
and
Drive Select
...........................
7-8
7.10
Motor
Off
Delay
....................................................
7-8
7.11 Radial Ready
.....................................................
7-9
7.12
Stepper Power Down
...............................................
7-10
7.13
Write Protect Optional Use
...........................................
7-10
SECTION
VIII
OPERATION PROCEDURES
.............................................
8-1
8.1
Introduction
......................................................
8-1
8.2
Diskette Loading
and
Handling
........................................
8-1
8.2.1
Write Protect: Shugart 8-Inch Diskettes
...........................
8-2
8.2.2
Write Protect:
IBM
Diskettes
...................................
8-2
SECTION
IX
PACKAGING;
..........................................................
9-1
APPENDIX A MACHINE LEVEL CODE INFORMATION
....................................
A-I
APPENDIX B ORDERING INFORMATION
..............................................
B-1
ii

Figure
Number
Title
LIST OF FIGURES
Page
1-1
SA810/860
Half-Height Floppy
Disk
Drive
.................................
1-0
1-2
SA810/860
Functional Diagram
...........
.
............................
1-5
1-3 Track Access Timing, Standard Seek
......................................
1-6
1-4 Track Access Timing, Buffered
Seek
.......................................
1-7
1-5 Read Initiate Timing . . . . . . . . . . . . . . . . . . . . . . . . . . . . . . . . . . . . . . . . . . . . . . . . . . . 1-7
1-6 Read Signal Timing
(FM
Encoding) . . . . . . . . . . . . . . . . . . . . . . . . . . . . . . . . . . . . . . . . 1-8
1-7
FM
and
MFM
Code
Comparisons
.........................................
1-8
1-8 Write Initiate Timing
...................................................
1-9
1-9
SA810/860
General Control
and
Data Timing Requirements
....................
1-10
2-1
SA810/860
Interface Connections
........................................
2-2
2-2 Interface Signal Driver/Receiver
..........................................
2-3
2-3 Index Timing
........................................................
2-5
2-4 SectorTiming
.......................................................
2-5
2-5
DC
PowerProfile
.....................................................
2-7
3-1 Interface
Connectors-
Physical Locations
..................................
3-1
3-2
Jl
Connector Dimensions
..............................................
3-2
3-3
J2/P2
Connector
.....................................................
3-2
4-1 Physical Dimensions
...................................................
4-2
6-1 Data Pattern. . . . . . . . . . . . . . . . . . . . . . . . . . . . . . . . . . . . . . . . . . . . . . . . . . . . . . . . . 6-1
6-2
Bit
Cell
.............................................................
6-1
6-3 Byte
...............................................................
6-1
6-4 Data Bytes
..........................................................
6-2
6-5
FM
and
MFM
Encoding
................................................
6-4
6-6 .
SA810/860
Hard Sector Recording Format
(FM)
.............................
6-4
6-7
MFM
Track Format Comparison
..........................................
6-5
6-8
MFM
Index Pre Address Mark
...........................................
6-6
6-9 Index Address Mark
FM
................................................
6-6
6-10
MFM
Index Address Mark
..............................................
6-7
6-11
10
Address Mark
FM
..................................................
6-7
6-12
MFM
10 Address Mark
.................................................
6-7
6-13
MFM
Pre ID/Data Address Mark
.........................................
6-8
6-14
Data Address Mark
FM
. . . . . . . . . . . . . . . . . . . . . . . . . . . . . . . . . . . . . . . . . . . . . . . . . 6-8
6-15 Deleted Data Address Mark
FM
..........................................
6-8
6-16
MFM
Data Address Mark
...............................................
6-9
6-17
MFM
Deleted Data Address Mark
.........................................
6-9
7
-1
PCB
Component
Locations
(P
/N
25227
and
25247) . . . . . . . . . . . . . . . . . . . . . . . . . . 7-3
7-2 PCB
Component
Locations
(P
/N
25249)
...................................
7-4
7-3 External Write Current Option
........
. . . . . . . . . . . . . . . . . . . . . . . . . . . . . . . . . . . 7-5
7-4
Disk
Change Timing
...................................................
7-5
7-5
Disk
Change Circuit
...................................................
7-6
7-6 Side Selection Using Direction Select
......................................
7-6
7-7 Side Selection Using Drive Select
.........................................
7-7
7-8 Motor On Without Selecting Drive Circuit . . . . . . . . . . . . . . . . . . . . . . . . . . . . . . . . . . . 7-8
7-9 Motor On by Opt. Motor
On
and
Drive Select Circuit
...........................
7-9
7-10 Radial Ready Circuit.
..................................................
7-10
7-11 Write Protect Circuit
...................................................
7-10
8-1 Loading
the
SA810/860
...............................................
8-1
8-2 Diskette Write Protect . . . . . . . . . . . . . . . . . . . . . . . . . . . . . . . . . . . . . . . . . . . . . . . . . . 8-2
8-3 Write Protect Notch Specifications
........................................
8-2
9-1
SA810/860
Packaging
................................................
9-1
9-2 Pallet Loading
.......................................................
9-2
iii

LIST OF TABLES
Table
Number Title Page
2-1 DC Power Requirements
...............................................
2-7
3-1 Recommended
Jl
Connectors
...........................................
3-2
7-1 Customer
Cut/Add
Trace Options
........................................
7-2
A-I
Machine Level
Code
Information
.........................................
A-I
B-1 Ordering Information
..................................................
B-1
ABBREVIATIONS/ MNEMONICS
AM
Address Mark
MFM
Modified
FM
CRC
Cyclic Redundancy Check
MLC
Machine Level
Code
CRT
Cathode-ray Tube
PCB
Printed Circuit Board
DS
Drive Select
PLL
Phase Locked Loop
FM
Frequency Modulation SEP Separated
10
Index
VFO
Variable Frequency Oscillator
LED
Light Emitting Diode
WG
Write Gate
ABOUT THIS MANUAL
This manual
(P
/N
39216-2) supersedes
all
earlier manuals.
All
earlier editions may be discarded.
While every effort has been made to ensure that the information provided herein
is
correct, please notify us
in
the
event of an error or inconsistency. Direct any comments on the form at the back of this manual to:
Shugart
Technical Publications
475
Oakmead Parkway
Sunnyvale, CA
94086
(408) 733-0100
iv


FIGURE 1.1. SA810/860 HALF·HEIGHT FLOPPY DISK DRIVE
1·0

1.1
GENERAL
DESCRIPTION
SECTION I
INTRODUCTION
The
compact
SA810
single-sided
and
SA860
double-sided half-height 8-inch floppy disk drives offer a reliable, low
cost, high performance solution for OEM data storage applications which require maximum capacity in
the
smallest
space possible. The
SA810/860
drives are half the height of the Shugart SA801 floppy disk drive,
fit
in comfor-
tably with a CRT, require
no
ac voltage,
and
offer up to
1.6
megabytes of unformatted capacity.
The
SA810/860
offers the
follOWing
standard features:
a. Half-height sizing:
2.31
in. (59 mm) high by
8.55
in. (217 mm) wide by
12.00
in. (305 mm)
deep
b. Interface
and
media compatibility with Shugart
SA801/851
disk drives
c. Low
heat
dissipation
d. Fast access time
{3
ms track to
track}
e. Quiet operation
f.
Low media wear
due
to low mass
head
g. Rapid start dc drive motor--Iess than
one
revolution {eliminates ac requirements}
h. Phase-Locked Loop Crystal Referenced Motor
Speed
Control
i. Media compatible with
SA801/851
plus
IBM
3740
j.
Single or double density
k.
0.8/1.6M
Bytes (unformatted capacity)
1.
Write protect
and
programmable door lock for improved data security
m. Internal write current switching
n. TRUE READY alerts the system that the drive
is
ready to
send
or receive
data
o. Buffered seek
p. Single or multiple drive dc Motor
On
control
q. Multiple jumper options
r.
Shugart's proprietary Bi-Compliant
read/write
heads with straddle erase elements
s. Extended reliability
t. Activity light
u. Solid die cast chassis
v.
Light weight
w.
Inline dc
and
I/O
connectors
The
SA810/860
provides the best solution to the user looking for a compact, low cost,
and
reliable 8-inch floppy
disk drive. The
SA810/860
is
the most versatile disk drive
on
the market. This drive
is
backed by an engineering
department that
is
recognized as the largest, most experienced group
in
the entire floppy industry.
The
SA810/860
is
the ultimate solution for small business systems, intelligent terminals, personal
computer
systems,
and
program
storage equipment.
1.2
SPECIFICATIONS
SUMMARY
1.2.1
Performance
Specifications
Capacity
Unformatted
Per
Disk
Per Surface
Per
Track
SA810
Single/Double Density
400/800
k bytes
400/800
k bytes
5.2/10.4
k bytes
1-1
SA860
Single/Double Density
0.8/1.6
M bytes
400/800
k bytes
5.2/10.4
k bytes

IBM
Format
(128 byte sectors)
Per
Disk
Per Surface
Per Track
Transfer Rate
Latency (average)
Access Time
Track to Track
Settle Time
One
Track Seek & Settle
Average (including settle)
Motor Start Time
Worst Case
Typical
SA810
Single/Double Density
250/500
k bytes
250/500
k bytes
3.3/6.66
k bytes
250/500
k bits/sec
83
ms
3 ms
13 ms
16 ms
89
ms
165 ms
120
ms
1.2.2
Functional
Specifications
Rotational
Speed
Recording Density
(inside track)
Flux Density
Track Density
Tracks
Index
Encoding Method
Media Requirements
Soft Sectored
32
Sector Hard Sectored
Alignment Diskette
360
rpm
3268/6536
bpi
6536
fci
48
tpi
77
1
FM/MFM
SA100/102
SAI01/103
SA120
1.2.3
Physical
Specifications
Environmental Limits
Ambient Temperature:
Relative Humidity:
Maximum Wet Bulb:
DC Voltage Requirements:
Operating
50°
to
115°F
(9.9°
to
46.1
°C)
20%
to
80%
85
OF
(29.4°C)
Storage
-8°
to
122<?F
(-22.2°
to 50°C)
1% to 95%
no
condensation
+ 24.
00
±
2.4
V dc @
1.
0 A typ, 1.7 A max., 100 mV ripple.
+5.00
±
0.25
V de @
0.7
A typ,
1.0
A max.,
50
mV ripple.
NOTE
SA860
Single/Double Density
500/1000
k bytes
250/500
k bytes
3.3/6.6t)
k bytes
250/500
k bits/sec
83
ms
3 ms
13 ms
16 ms
89
ms
165 ms
120 ms
360
rpm
3408/6816
bpi
6816
fci
48
tpi
154
1
FM/MFM
SA150
SA151
SA122
Shipping
-40°
to
144°F
(-40° to
62.2°C)
1% to
95%
no condensation
If the stepper motor
is
energized
by
the controller during the single motor start-up time, the drive will ex-
ceed the +
24
V de current specification of 1.7 A maximum. Under this condition, the current specifica-
tion
is
2.2
A maximum.
1-2

Mechanical Dimensions
Width =
8.55
in
(217 mm)
Height =
2.31
in
(59 mm)
Depth =
12.00
in
(305 mm)
Weight =
7lbs
(3
kg)
Mounting
Top
loading
Diskette Horizontal Label
Up/Down
Diskette Vertical Label Left/Right
Power Dissipation:
10
watts (34 BTU/hr) Standby
28
watts (96 BTU/hr) Typical
50
watts (171 BTU/hr) Maximum
1.2.4
Reliability
Specifications
Mean Time Between Failure:
10,000
Power On Hours
under
typical usage.
Preventive Maintenance: Not required.
Mean Time to Repair:
30
Minutes
Component
Life: 5 years
Error Rates:
Soft Read Errors:
Hard Read Errors:
Seek
Errors:
Media Life:
1
per
109 bits read
1
per
10
12
bits read
1 per 106 seeks
Passes
per
Track:
3.5
x 106
Insertions:
30,000
+
1.3
FUNCTIONAL CHARACTERISTICS
The
810/860
floppy disk drives consist of:
a. Read/Write
and
Control Electronics
b. Drive Mechanism
c. Precision Track Positioning Mechanism
d. Read/Write
Head
(s)
1.3.1
Electronics
The
electronics are packaged
on
one
PCB which contains:
a. Index Detector Circuits (Sector/Index for Hard Sectored Media)
b.
Head
Position Actuator Driver
c. Read/Write Amplifier
and
Transition Detector
d. Write Protect
e. Drive Select Circuits
f.
Spindle Motor Control
g.
Data/Clock
Separation Circuits
(FM
Only)
h. Drive Ready Detector Circuit
i. Drive True Ready Detector Circuit
j. Side Select Circuit (Used
on
SA860
only)
k.
In
Use
and
Door Lock Circuits
1.
Internal
and
External Write Current Switching
m. Power On Reset Circuit
n. Activity LED
1-3

1.3.2
Drive Mechanism
The
Head
Positioning Actuator moves
the
read/write
head{s} to
the
desired track
on
the
diskette.
The
head{s}
is
loaded
onto
the diskette when the
door
knob
is
closed. If
no
diskette
is
inserted when the
door
knob
is
closed, the
heads
will
not touch each other.
The
dc drive motor
under
phase
locked loop
speed
control (using
an
integral tachometer) rotates the spindle at
360
rpm. A contracting collet/spindle assembly provides precision media positioning
and
clamping to ensure data inter-
change. A diskette ejector places the diskette within reach of the operator when the diskette
is
unclamped.
1.3.3
Positioning
Mechanism
The
read/write
head
assembly
is
accurately positioned through
the
use of a precision HeliCam V-groove lead
screw with a flat nutfollower which
is
attached to the
head
carriage assembly. Precise track location
is
accomplished
as the lead screw
is
rotated
in
discrete increments
by
a stepper motor.
1.3.4
Read/Write
Heads
The
proprietary
head
{s}
is
a single element ceramic
read/
write
head
with straddle erase elements to provide erased
areas between data tracks. Thus, normal interchange tolerances between media
and
drives
will
not
degrade
the
signal to noise ratio
and
diskette interchangeability
is
ensured.
The
read/write
head{s)
is
mounted
on
a carriage which
is
located
on
precision carriage ways. The diskette
is
held
in
a plane perpendicular to the
read/write
head
(s)
by a platen located
on
the base casting. This precise registration
assures perfect compliance with
the
read/write
head{s}. The
read/write
head{s}
is
in
direct contact with the
diskette. The
head
surfaces have been designed to obtain maximum signal transfer to
and
from the magnetic sur-
face of the diskette with minimum
head/diskette
wear
due
to
the
low mass suspension system.
1.3.5
Recording Formats
The
format of the data recorded
on
the diskette
is
totally a function of the host system. This format can be designed
around
the user's application to take maximum advantage of the total available bits that can be written
on
anyone
track.
Figure 1-2 provides a functional diagram of the
SA810/860.
For a detailed discussion of the various recording for-
mats, refer to Section
VI.
1.4
FUNCTIONAL OPERATIONS
1.4.1
Power
Sequencing
Applying dc
power
to the
SA810
or
SA860
can be
done
in
any sequence; however, during
power
up,
the
WRITE
"GATE
line must be held inactive or at a high level. After application of dc power, a
90
ms delay should be introduc-
ed
before a seek operation or before the control output signals are valid. After powering
on,
the initial position of
the
read/write
heads
with respect to the data tracks
on
the media
is
indeterminant.
In
order to assure
proper
posi-
tioning of the read/write
heads
after power
on
and
internal write current
SWitching
at the
proper
track, a STEP
OUT operation should be performed until the TRACK
00
line becomes active (recalibrate).
1.4.2
Drive
Selection
Drive selection occurs when the DRIVE SELECT line
in
the drive
is
activated. Only the drive with this line active
will
respond to input lines or gate output lines. Under normal operation, the DRIVE SELECT line enables the input
and
output
lines, starts the spindle motor, locks the door,
and
lights the Activity LED
on
the front of the drive.
1.4.3
Motor On
In
order for the host system to read
or
write data, the dc drive motor must be turned on.
In
the standard configura-
tion, this
is
accomplished by activating
the
line DRIVE SELECT. A
165
ms delay must be introduced after ac-
tivating this line (or the TRUE READY line may be monitored) to allow the motor to
come
up
to
speed
before
reading
or
writing can be accomplished.
All
motors
in
a daisy chain configuration can be turned
on
with
the
op-
tional MOTOR ON line or the spindle motor may be activated
when
both MOTOR ON
and
DRIVE SELECT are
present. Refer to paragraphs
7.8
and
7.9.
1-4

READ
DATA
-
SEP
DATA
(FM) READ WRITE
LOGIC
f.-
-.
PROTECT
SEP
CLOCK
(FM) ASSM
~
DRIVE SIDE
SELECT SELECT DISKETTE
WRITE
DATA
..
.
WRITE
GATE
-
WRITE
WRITE
CURRENT
(OPT) LOGIC STEPPER
_
WRITE
PROTECT
ACTUATOR
H.
I
~
j
I'
R/WO
~
cJ,
R/W1
R/W
HEAD
TRACK
SIDE ASSM.
.
40 SELECT POWER
ON
.
~
DOOR
RESET
\.
MOTOR CLOSED
·SIDE
SELECT
SWITCH
STEP
I
DIRECTION/
*SIDE
SELECT
(OPT.) INDEX/
DRIVE/*SIDE
SELECT
(OPT.) SECTOR
DETECTOR
MOTOR
ON
(HEAD
LOAD)
(OPT.L
IN USE (OPT.) t
.
TWO
SIDED
(OPT.)
CONTROL
TRACK
00 LOGIC
INDEX
IN USE
...
-p
LED
SECTOR
READY/TRUE READY (OPT.)
TRACK
-00
TRUE
READY
(OPT.)
...
~
-SENSOR
_
DISK
CHANGE
(OPT.)
ALTERNATE
I/O (2
lines)
DOOR
LOCK
.
*SA860 ONLY
SOLENOID
FIGURE 1·2. SA810/860 FUNCTIONAL DIAGRAM 39216·02·A

In
the
standard
configuration, the host system turns off
the
motor by deactivating
the
DRIVE SELECT line. This
should be
done
if
the drive has not received a
new
command
within
2.6
seconds (16 revolutions of diskette) after
completing
the
execution of a
command.
This
will
ensure maximum
motor
and
media life. Also, the
2.6
second
delay function
can
be
done
by the drive by jumpering
the
optional Motor Off delay. Refer to
paragraph
7.10.
1.4.4
Track
Accessing
Seeking the
read/write
heads
from
one
track to
another
is
accomplished by:
a. Activating DRIVE SELECT line.
b. Selecting desired direction utilizing DIRECTION SELECT line.
c. WRITE GATE being inactive.
d. Pulsing
the
STEP line.
Multiple track accessing
is
accomplished by
repeated
pulsing of the
STEP
line until the desired
number
of steps
have
been
input. Each pulse on the
STEP
line
will
cause the
read/write
heads
to
move
one
track either
in
or
out
depending
on
the DIRECTION SELECT line.
Head
movement
is
initiated
on
the
leading
edge
of the
STEP
pulse.
Pulses received at less
than
a 3 ms period, but greater
than
15
p,S,
will
be stored in a buffer which
will
then
issue step
commands
to the drive stepper motor at a 3 ms pulse rate. Pulses received at greater
than
a 3 ms period
will
step
the
drive at
the
same
rate they are received.
The
first step begins
upon
receipt of
the
first
step pulse.
1.4.5
Step
Out
With the DIRECTION SELECT line at a plus logic level (2.5 V to
5.25
V), a pulse on
the
STEP line
will
cause
the
read/write
head(s) to
move
one
track away from the center of the disk. The pulse(s) applied to the
STEP
line must
have
the
timing characteristics shown
in
figure 1-3
or
figure 1-4.
1.4.6
Step
In
With
the
DIRECTION SELECT line at a minus logic level
(0
V to
0.4
V), a pulse on
the
STEP line
will
cause
the
read/write
heads
to
move
one
track closer to
the
center of the disk. The pulse(s) applied to the STEP line must
have the timing characteristics shown
in
figure 1-3 or figure 1-4.
DC POWER
-I--------------~u~-------------
DRIVE SELECT I
I
--------------~i~2------------------
DIRECTION SELECT
________
OUT
~
I IN
i~
STEP
-I1--11'S
~
1-
1
1'5
MIN
~~S
_I
1-16
ms MIN
-I
r-
1
1'5
MIN
---------~
~--
11'5
MI~
~
~
3 ms MIN"
-1
1---3
ms MIN"
*3
ms
is
the
minimum
frequency for a standard seek. Pulses received at less than a 3
ms
frequency
will
go
into
a buffered seek mode. See figure
1-4.
39216·03·A
FIGURE 1·3. TRACK ACCESS TIMING, STANDARD SEEK
1-6

DC POWER I
~
--------------~l~l---------------
DRIVE SELECT I
DIRECTION SELECT
___
1
___
_
~
--1~1:1
.s
r---
-
I
------_
.......
' --
--
OUT
~----------------
STEP
90
ms
MIN
LJlJ
1 /ls
MIN~
rI
15"s
MIN"
.~
r-2.~
ms
MAX
~
15/l8
MIN**
I 2.9
ms
MAX"
*
After
the
last
step
pulse
has been
issued
the
drive
may
be
deselected.
The
drive
ignores
any
change
to
the
DIRECTION SELECT
line
when
no
further
step
pulses
are received.
This
frees
the
controller
to
issue
instructions
to
other
drives
while
the
first
drive
completes
the
step
commands
stored
in
the
buffer.
**Pulses received at
less
than
a 3
ms
period
will
be
stored
in a
buffer
which
will
then
issue
step
com-
mands
to
the
drive
stepper
motor
at a 3
ms
pulse
rate. Pulses received at
greater
than
a 3
ms
per-
iod
will
step
the
drive
at
the
same rate
they
are received. The
first
step
begins
upon
receipt
of
the
first
step
pulse. 39216·31
FIGURE 1·4. TRACK ACCESS TIMING, BUFFERED SEEK
1.4.7
Side
Selection
(SA860
Only)
Head
selection
is
controlled via the
I/O
signal line designated SIDE SELECT. A plus logic level
on
the
SIDE
SELECT line selects the
read/write
head
on
the side asurface of the diskette. A minus logic level selects the side 1
read/write
head. When switching from
one
side to
the
other, a 100
JLS
delay
is
required after SIDE SELECT
changes state before a read or write operation can be initiated. Figure 1-5shows the use of SIDE SELECT prior to a
read
operation.
DC
POWER
DRIVE SELECT
STEP
SIDE SELECT
(SA860 ONLY)
WRITE GATE
~~------------------------------~u~----------
I
'--------------------------------------------~l~~------------
.--------------------------------~l~~---------------
1-100
"s
-----------------------------~?~~-------------
VALID READ DATA
------------------
*Or
when
TRUE READY
comes
active. 39216-04
FIGURE 1·5. READ INITIATE TIMING
1-7

1.4.8
Read
Operation
Reading
data
from the
SA810/860
drive
is
accomplished by:
a. Activating DRIVE SELECT line.
b. Selecting
head
(SA860 only).
c. WRITE GATE being inactive.
The
timing relationships required to initiate a read
sequence
are
shown
in figure 1-5. These timing specifications are
required
in
order to guarantee that the position of the
read/write
head
has stabilized prior to reading.
The
timing of
READ DATA
(FM)
is
shown
in
figure 1-6.
READ DATA
SEP DATA
SEP CLOCK
A
I
LJ
I
B
I A
I
4.00
itS
NOM
U I
~
l.--200
± 50 ns
I
U
~I
~200
±
50ns
A B A
I U II
U U
A = LEADING EDGE OF BIT MAY
BE
± 400 ns FROM ITS
NOMINAL
POSITION.
B = LEADING EDGE OF BIT MAY
BE
± 200 ns FROM ITS
NOMINAL
POSITION
..
FIGURE 1·6. READ
SIGNAL
TIMING
(FM ENCODING)
39216·05
The
encoding scheme of the recorded data
can
be
FM
or MFM. The first of these, FM, provides single-density
recording.
The
superior efficiency of
MFM
permits the bit cell period to be half that of the
FM
code,
thereby pro-
viding double-density recording. Differences
among
FM
and
MFM
encoding are concerned with
the
use of clock
bits
in
the
write data stream.
FM
encoding rules specify a clock bit at the start of every
bit
cell.
MFM
encoding rules allow clock bits to
be
omitted
from
some
bit cells, when either the preceding bit cell
or
the current bit cell contains a data bit.
See
figure 1-7.
a o o o
BIT
CELLS
D D D D D
FM
--..
2F
~
MFM
FIGURE 1·7. FM
AND
MFM
CODE
COMPARISONS
1-8

In
both of these encoding schemes, clock bits are written at
the
start of their respective bit cells
and
data
bits
at
the
center of their bit cells.
The
timing of the
read
signals, READ DATA, SEPARATED DATA,
and
SEPARATED CLOCK are shown
in
figure 1-6
(FM
encoding).
In
the
standard
SA810/860,
data separation of
FM
data
is
performed by the drive electronics. Data bits are
presented to the controller
on
the
SEP
DATA line
and
clock bits are presented
on
the
SEP
CLOCK line.
In
systems
using
MFM
encoding, data separation
is
performed outside the drive.
In
such cases,
the
READ DATA line carries
both clock bits
and
data bits. Separation of
MFM
encoded
read
data should be controlled
by
a phase-locked loop
circuit.
For additional information regarding the use of
MFM
encoding, refer to paragraph
6.2.
1.4.9
Write
Operation
Writing data to the
SA810/860
is
accomplished by:
a. Activating DRIVE SELECT line.
b. Selecting
head.
c.
Activating WRITE GATE line.
d. Pulsing WRITE DATA line with data to be written.
e.
Head
current switching.
The timing relationships required to initiate a write data
sequence
are shown
in
figure 1-8. These timing specifica-
tions are required in
order
to guarantee that the
read/write
head
position has stabilized prior to writing.
Write data encoding can be
FM
or
MFM.
If
MFM
is
used, the write data should be
precompensated
to counter the
effects of bit shift.
The
amount
and
direction of compensation required for any given bit
in
the data strea'm
depends
on
the pattern
it
forms with nearby bits.
For more details regarding data encoding and formatting for
SA810/860
drives, refer to Section
VI.
DC POWER
DRIVE
SELECT
STEP
I--
90
ms MIN
-----I
I I
1-
'65
ms
MIN1
-I----.U
r-9~~S~--1
--------11
r100
I(S
MIN
SIDE SELECT
~
I !
(SA860 ONLY)
WRITE GATE
16 ms MIN'
r-i
I_--------------~
-I
i-
4
'SMIN
-------..U
U
WRITE DATA u
*
Or
when TRUE READY comes active
FIGURE 1·8. WRITE INITIATE
TIMING
1-9
39216·07·A

1.4.10
Sequence
Of
Events
The
timing diagram shown
in
figure 1-9 illustrates the necessary
sequence
of events with associated timing restric-
tions for
proper
operation.
DC POWER
VALID CONTROL
~90ms
MIN
AND
OUTPUT SIGNALS 90 I
DRIVE SELECT
SIDE SELECT
(SA860 ONL
Y)
DIRECTION
SELECT
STEP
TRUE READY
WRITE GATE
WRITE DATA
VALID READ
DATA
SIGNAL
ms
MIN
----.
I I
I I
I
ss
~500mSMAX
*r--,
*,--'
, ,
,I
1_
100
;.--
~
I
~\~
___
...L.'
~I
---\:~\~-------
r-
MAX
SS
~S
I
1
1 s I
{m~t
1
S~
_II
T--
.....
l---\S\oS---------
M)N
~
r-
HMIN~
Mf~
....
~
1 /ls MIN
~S
90
m~
II
Ln
1 /ls I
tn.J~----\'t-----
MIN
..
~
~
~NOTE2~16ms
NOTE
2~
-.J
t....MIN
16
ms-.i
l.-
II
~6
m~1
MI~r------J
--·L
~
----"S'"S---
II~IN
r-16
ms
I I I
SS
I MIN I
...
I..
I I 100
••
MIN
;;
~
J.oI-f----~----''---
NOTE 1
~
r-
4 /ls MIN I
~
L16
~.
lnf1ru~I--
1-
MIN
~
r-
50 /ls MIN
---:"'-~-NO-TE
l=tnfWJ
\~
NOTE
1:
165
ms
minimum
delay
must
be
introduced
after
DRIVE SELECT
to
allow
time
for
the
dc
motor
to
reach 360 rpm
or
the
optional
TRUE READY line
must
be
monitored.
NOTE
2:
If
performing
standard seeks, the
minimum
frequency is 3
ms
between steps. If
utilizing
the drive in
the
buffered
seek mode
of
operation the frequency shall be
15
p..s
to
2.9
ms
between pulses.
*
After
the last
step
pulse has been issued, the drive may be deselected. The drive ignores any change
to
the
DIRECTION SELECT line when no
further
step
pulses
are received.
This
frees the
controller
to
issue
instructions
to
other
drives
while
the
first
drive
completes
the
step
commands
stored in the
buffer.
39216·08·A
FIGURE 1·9. SA810/860 GENERAL CONTROL AND DATA TIMING REQUIREMENTS
1-10

SECTION
II
ELECTRICAL
INTERFACE
2.1
INTRODUCTION
The interface of the
SA810/860
Diskette Drive
can
be divided into two categories:
a. Signal
b. Power
The following paragraphs provide the electrical definition for each line.
See
figure 2-1 for
all
interface connections.
2.2
SIGNAL INTERFACE
The signal interface consists of two categories:
a. Control
b. Data Transfer
All
lines
in
the signal interface are digital
in
nature and either provide signals to
the
drive (input),
or
provide signals
to the host (output), via interface connector
Pl/
J1.
2.2.1
Input
Lines
There are twelve signal input lines. Nine are standard
and
three are user installable options (refer to Section VII).
The input signals are of three types. those intended to be multiplexed
in
a multiple drive system, those not intended
to be multiplexed.
and
those which
will
perform the multiplexing.
The input signals which are intended to do the multiplexing are:
a. DRIVE SELECT 1
b. DRIVE SELECT 2
c.
DRIVE SELECT 3
d. DRIVE SELECT 4
The input signals to be multiplexed are:
a. SIDE SELECT
b. DIRECTION SELECT
c.
STEP
d. WRITE GATE
e. WRITE DATA
The input signals which are not multiplexed are:
a. MOTOR ON
(May
be optionally multiplexed. Refer to
paragraph
7.9.)
b.
IN
USE
c. EXTERNAL WRITE CURRENT SWITCH
2-1

HOST
~
DC
-~.fT.
GND
-=-
FRAME GND
MAX FEET
10
FT
FLAT RIBBON
OR
20
FT TWISTED PAIR
EXTERNAL WRITE CURRENT
SWITCHING'
TRUE READY'
TWO
SIDED'
+
DISK
CHANGE'
SI
DE
SELECT' +
IN
USE'
MOTOR
ON'
(HEAD LOAD)
INDEX
READY
SECTOR
DRIVE SELECT 1 (SIDE SELECT
OPT)
+
DRIVE SELECT 2 (SIDE SELECT
OPT)
+
DRIVE SELECT 3 (SIDE SELECT
OPT)
+
DRIVE SELECT 4 (SIDE SELECT
OPT)
+
DIRECTION SELECT (SIDE SELECT
OPT)
+
STEP
WRITE DATA
WRITE GATE
TRACK
00
WRITE PROTECT
READ DATA
SEP DATA
SEP CLOCK
......
+5
V
DC
X
+5
V RETURN
......
""
+24
V
DC
X+
24
V RETURN
'"
TWISTED PAIR
'JUMPER
ENABLED ALTERNATE I/O LINES.
+ SA860 ONLY
SA81
01860
J1
2 1
8 7
10
9
12
11
14 13
16
15
18 17
20
19
22
21
24
2:3
26 25
28 27
30 29
32
31
34
33
36 35
38 37
40
39
42
41
44
4"
46 45
48 47
50
49
3 J2 4
1 2
5
am
FIGURE 2·1. SA810/860 INTERFACE CONNECTIONS
2-2
~
-
39216·09

The input circuit lines have the following electrical specifications.
See
figure 2-2 for the
recommended
circuit.
True = Logical zero =
Vin
±
0.0
to +
0.4
V @
lin
=
40
rnA (max)
False = Logical
one
= Vin ±
2.5
to +
5.25
V @
lin
=
250
f-tA
(open)
Input Impedance =
220/330
ohms
MAX 10 FEET I
RIBBON OR
20
FEET TWISTED
PAIR
+5V
7414
39216·10
FIGURE 2·2. INTERFACE
SIGNAL
DRIVER/RECEIVER
2.2.2
Input
Line
Termination
The
SA810/860
has been provided with a removable resistor pack for terminating the eight input lines.
In
order
for the drive to function properly, the last drive
on
the interface must have these eight lines terminated.
Termination of these lines can be accomplished
by
either of two methods:
a. As shipped from the factory, the resistor pack
is
installed in location U9. These packs
can
be
removed
from
all
drives except the last
one
on the interface.
b. External termination may be used provided the terminator
is
beyond the last drive. Each of
the
lines should be terminated
by
using a
220/330
ohm, 1/4 watt resistor, pulled
up
to
+5 V dc.
The
same
removable resistor pack
is
also prOVided for terminating the optional input lines.
2.2.3
Drive
Select
1·4
DRIVE SELECT, when activated
to
a logical zero level, enables
the
multiplexed I/O lines, starts
the
spindle motor,
energizes the
stepper
motor, locks the door,
and
lights the activity LED.
In
this
mode
of operation, only the drive
with this line active
will
respond
to
the input lines
and
gate the output lines.
Four separate input lines, DRIVE SELECT 1, DRIVE SELECT 2, DRIVE SELECT 3,
and
DRIVE SELECT 4, are
prOVided so that up to four drives may be multiplexed together
in
a system
and
have separate DRIVE SELECT
lines. Traces DS1, DS2, DS3,
and
DS4
have been prOVided to select which DRIVE SELECT line
will
activate the
interface signals for a unique drive. As shipped from the factory, a shorting plug
is
installed
on
DSl.
To
select
another
DRIVE SELECT line, this plug should be moved to the appropriate OS pin.
2.2.4
Side
Select
(SA860
Only)
This interface line defines which side of a two-sided diskette
is
used for reading
or
writing. An
open
circuit, or logical
one,
selects the
read/write
head
on
the
side 0 surface of the diskette. A short to ground, or logical zero, selects the
read/write
head
on
the side 1 surface of the diskette. When switching from
one
head
to the other, a
100
f-tS
delay
is
required before any read or write operation
can
be initiated.
Two optional methods of side selection are available
and
can be implemented by
the
user through appropriate
jumper connections. These options are described
in
paragraphs
7.5
and
7.6.
2-3
This manual suits for next models
1
Table of contents
Other Shugart Computer Hardware manuals
Popular Computer Hardware manuals by other brands

Moxa Technologies
Moxa Technologies C104P user guide
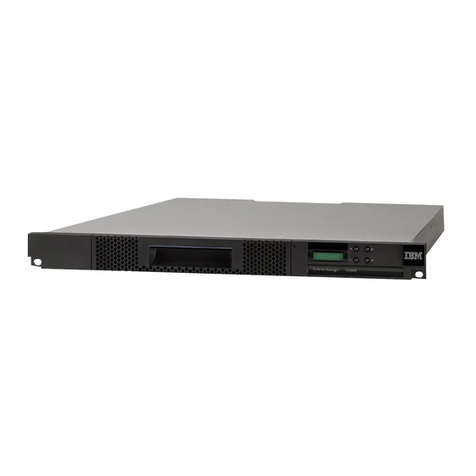
Lenovo
Lenovo IBM TS2900 Product guide
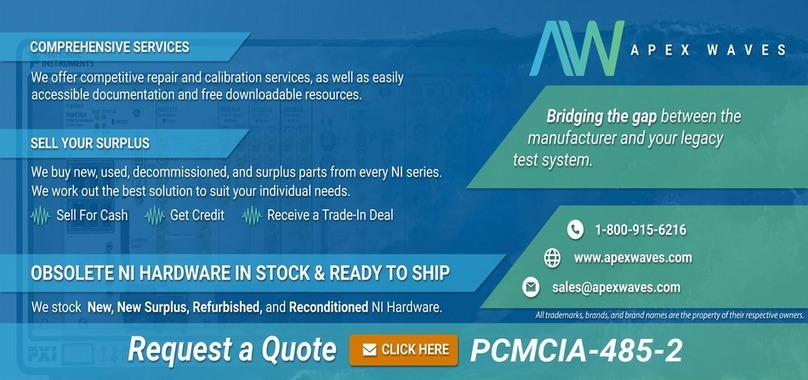
National Instruments
National Instruments PCMCIA Serias Getting started
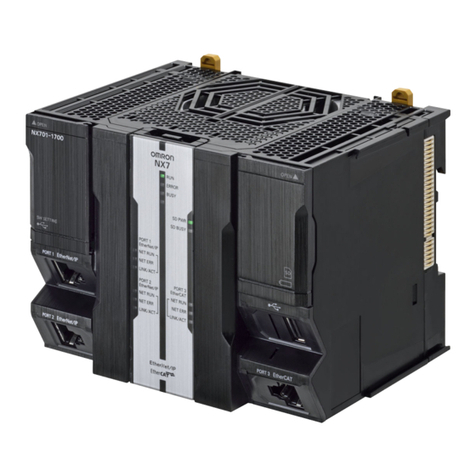
Omron
Omron Sysmac NJ-series user manual
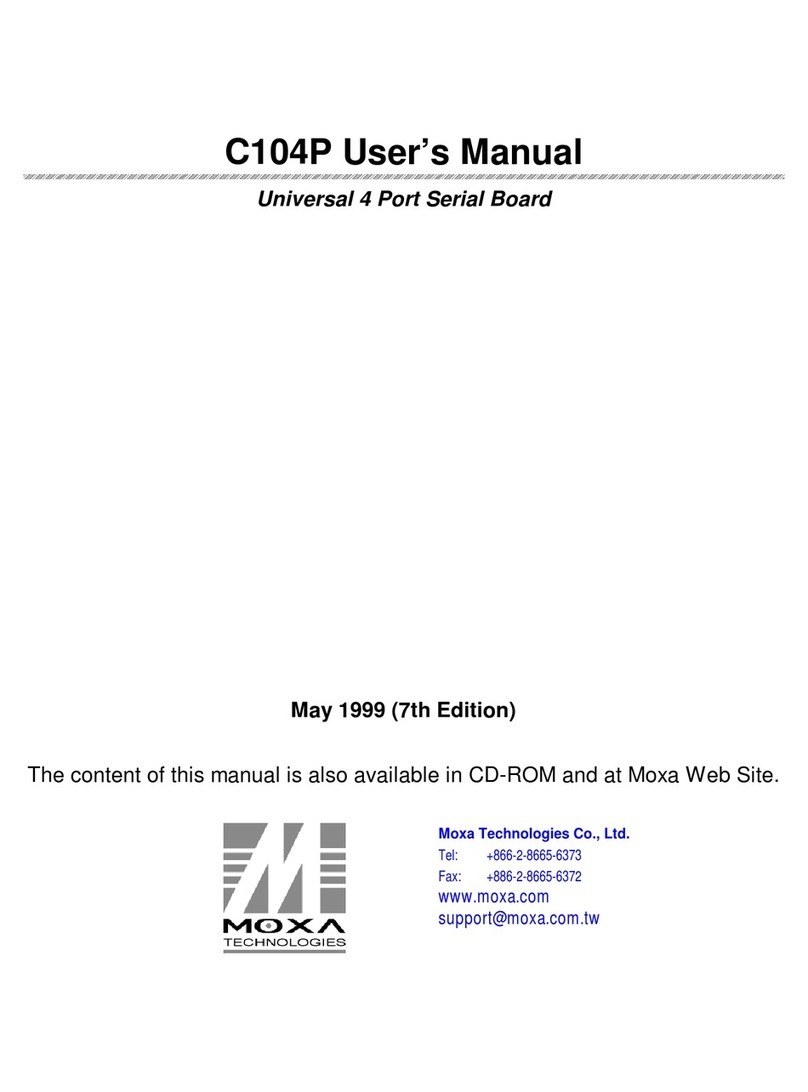
Moxa Technologies
Moxa Technologies C104P user manual
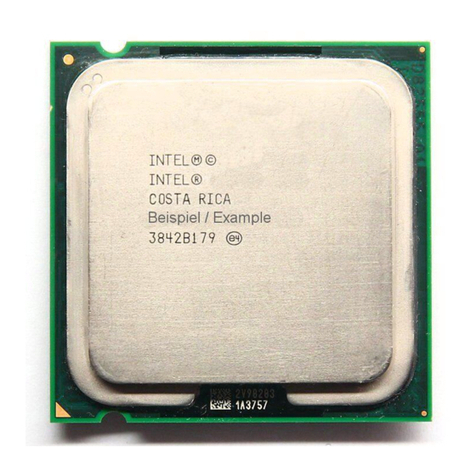
Intel
Intel E6420 - Core 2 Duo Dual-Core Processor datasheet
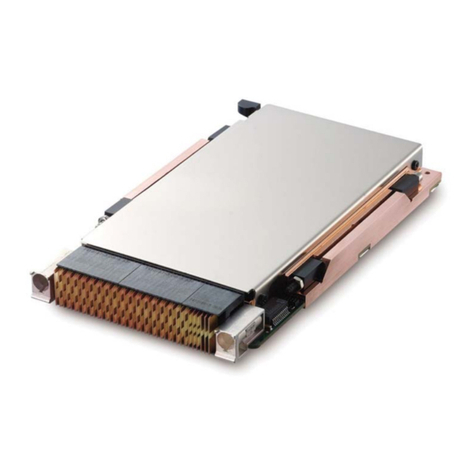
ADLINK Technology
ADLINK Technology VPX3000 Series manual
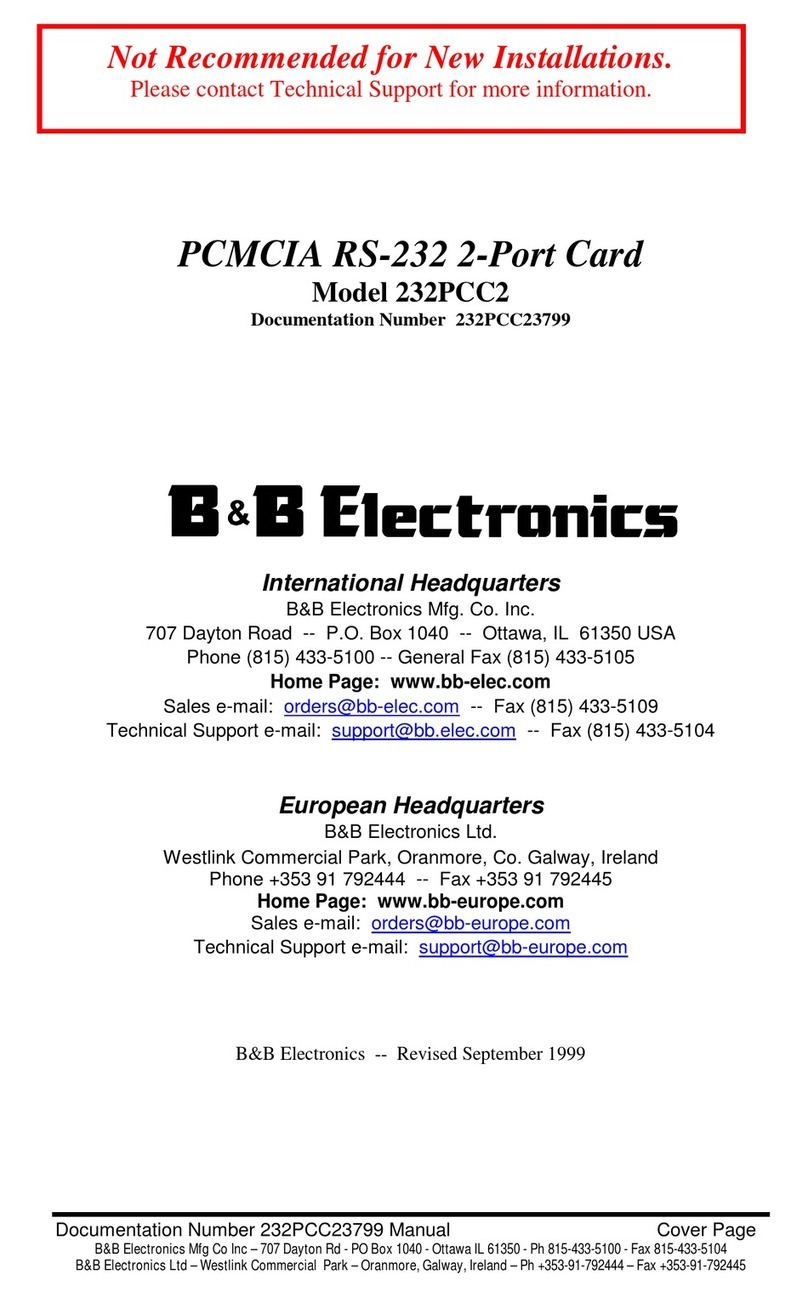
B&B Electronics
B&B Electronics PCMCIA 232PCC2 owner's manual
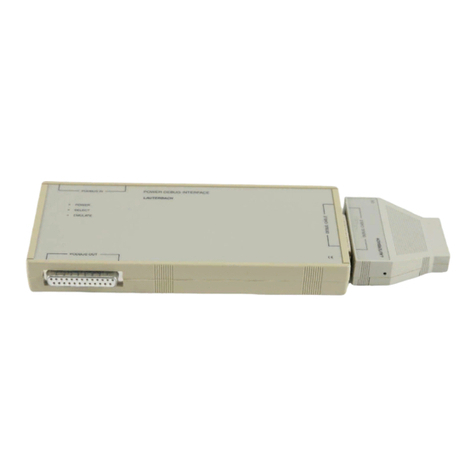
Lauterbach
Lauterbach TRACE32-ICD manual
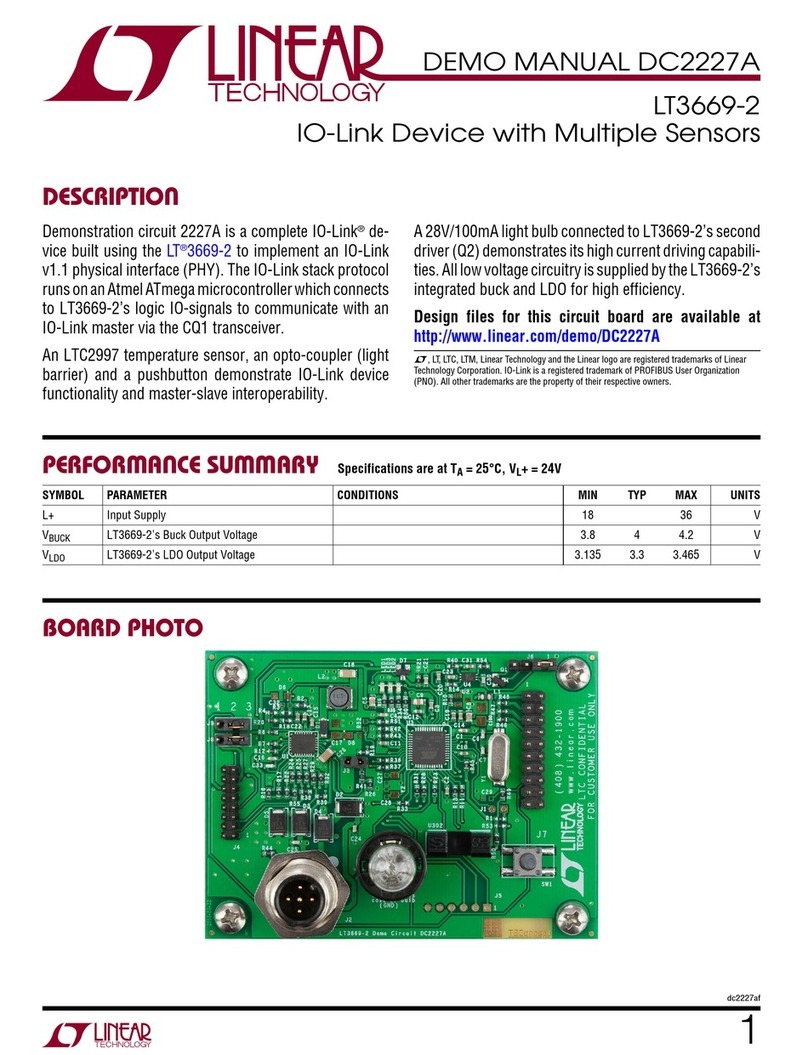
Linear Technology
Linear Technology LT3669-2 manual

Silicon Laboratories
Silicon Laboratories BRD4259A user guide
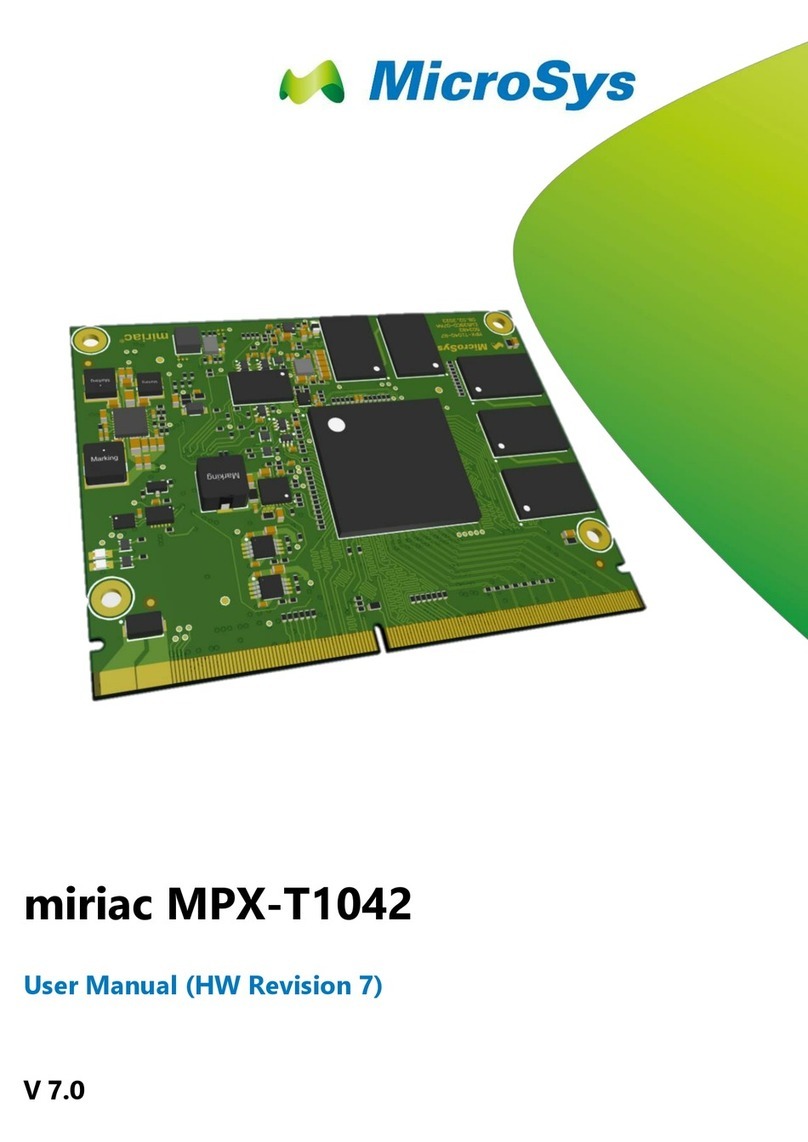
MicroSys
MicroSys miriac MPX-T1042 user manual