SIGMAKOKI OptoSigma HSC-103 User manual

SC12205-K10-15002A 2nd
1 Copyright 2020, SIGMAKOKI Co.,Ltd.
User’s Manual
Three-axis Stage Controller
HSC-103

SC12205-K10-15002A 2nd
2 Copyright 2020, SIGMAKOKI Co.,Ltd.
Notes regarding these materials
・ These materials are intended as a reference to assist our customers in the use of
the SIGMAKOKI CO., LTD. Product best suited to the customer’s application; they
do not convey any license under any intellectual property rights, or any other rights,
belonging to SIGMAKOKI CO., LTD. or a third party.
・ SIGMAKOKI CO., LTD. assumes no responsibility for any damage, or infringement
of any third-party’s rights, originating in the use of any product data, diagram, charts,
programs, or algorithms contained in these materials.
・ All information contained in these materials, including product data, diagrams,
charts, programs and algorithms represents information on products at the time of
publication of these materials, and are subject to change by SIGMAKOKI CO.,LTD.
without notice due to product improvements or other reasons.
・ When using any or all of the information contained in these materials, including
product data, diagrams, charts, programs, and algorithm, please be sure to evaluate
all information and products. SIGMAKOKI CO., LTD. assumes no responsibility for
any damage, liability or other loss resulting from the information contained herein.
・ SIGMAKOKI CO., LTD. products are not designed or manufactured for use in
equipment or system that is used under circumstances in which human life is
potentially at stake. SIGMAKOKI CO., LTD. products cannot be used for any
specific purposes, such as apparatus or systems for transportation, vehicular,
medical, aerospace, nuclear, or undersea repeater use.
・ The prior written approval of SIGMAKOKI CO., LTD. is necessary to reprint or
reproduce in whole or in part these materials.
・ If these products or technologies are subject to the Japanese export control
restrictions, they must be exported under a license Japanese government and
cannot be imported into a country other than the approved destination.
Any diversion or re-export contrary to the export control laws and regulations of
Japan and/ or the country of destination is prohibited.

SC12205-K10-15002A 2nd
3 Copyright 2020, SIGMAKOKI Co.,Ltd.
Contents
For Your Safety...................................................................................................................4
Chapter 1: Before You Begin.............................................................................................6
1-1.Package Contents.....................................................................................................6
1-2. Overview...................................................................................................................6
1-3.The HSC-103 System................................................................................................6
1-4. Parts and Functions.................................................................................................7
Chapter 2: Basic Operations..............................................................................................9
2-1.HSC-103 Connection procedure..............................................................................9
2-2. Connecting to PC and peripheral device...............................................................9
2-3. Connecting Power Cable.......................................................................................10
2-4.USB Driver installation Method .............................................................................10
Chapter 3: Settings...........................................................................................................11
3-1.Memory Switch settings.........................................................................................11
3-2. Memory Switch contents list and detailed settings............................................11
Chapter 4: Using HSC-103 to position Motorized Stages..............................................22
4-1. Feature....................................................................................................................22
4-2.Command ................................................................................................................22
4-3. Program functions.................................................................................................37
4-4 About the use of peripheral equipment ................................................................40
Chapter 5: Rotation Stage................................................................................................41
5-1 Setting item .............................................................................................................41
5-2 Command/ Status ...................................................................................................41
5-3 Speed.......................................................................................................................41
Chapter 6: RUN current setting.......................................................................................42
6-1. Setting the drive current........................................................................................42
Chapter 7: Specifications.................................................................................................43
7-1.Specifications..........................................................................................................43
7-2 Connector Pin Assignments..................................................................................44
7-3. Outlines...................................................................................................................46

4
For Your Safety
Before using this product, read this manual and all warnings or cautions in the documentation provided.
Only Factory Authorized Personnel should be changes and/or adjust the parts of controller.
The Symbols Used in This Manual
! WARNING ! CAUTION
This symbol marks warnings that should be read
and used to prevent serious injury or death.
This symbol indicates where caution should be used
to avoid possible injury to yourself or others, or
damage to property.
The above indications are used together with the following symbols to indicate the exact nature of the warning or
caution.
Examples of Symbols Accompanying Warnings and Cautions
△
Symbols enclosed in a triangle indicate warnings and cautions. The exact nature of
the warning or caution is indicated by the symbol inside (the symbol at left indicates
risk of electrocution).
○Symbols enclosed in a circle mark indicate prohibitions(actions that must not be
performed).The exact nature of the prohibition is indicates by the symbol inside or
next to the circle mark (the symbol at left indicates that the product must not be
disassembled).
●Symbols inside a black circle mark actions that must be performed to ensure safety.
The exact nature of the action that must be performed is indicated by the symbol
inside (the symbol at left is used in cases in which the AC adapter must be unplugged
to ensure safety).
Symbols on the product
The symbol mark on the product calls your attention. Please refer to the manual, in the case that you
operate the part of the symbol mark on the product.
!
This symbol labeled on the portion calls your attention.

SC12205-K10-15002A 2nd
5 Copyright 2020, SIGMAKOKI Co.,Ltd.
Disclaimer of Liability
① SIGMAKOKI CO., LTD. does not accept liability for damages resulting from the use of this product or
the inability to use this product.
② SIGMAKOKI CO., LTD. does not accept liability for damages resulting from the use of this product
that deviates from that described in the manual.
③ SIGMAKOKI CO., LTD. does not accept liability for damages resulting from the use of this product in
extraordinary conditions, including fire, earthquakes, and other acts of God, action by any third party,
other accidents, and deliberate or accidental misuse.
④ If the equipment is used in a manner not specified by the SIGMAKOKI CO., LTD., the protection
provided by the equipment may be impaired.
WARNING
●Do not use this product in the presence of flammable gas, explosives, or corrosive substances, in areas
exposed to high levels of moisture or humidity, in poorly ventilated areas, or near flammable materials.
●Do not connect or check the product while the power is on.
●Installation and connection should be performed only by a qualified technician.
●Do not bend, pull, damage, or modify the power or connecting cables.
●Do not touch the products internal parts.
●Connect the earth terminal to ground.
●Should the product overheat, or should you notice an unusual smell, heat, or unusual noises coming from
the product, turn off the power immediately.
●Do not turn on the power in the event that it has received a strong physical shock as the result of a fall or
other accident.
●Do not touch the stage while operation.
●Use dry clothes only for cleaning the equipment.
!

SC12205-K10-15002A 2nd
6 Copyright 2020, SIGMAKOKI Co.,Ltd.
Chapter 1: Before You Begin
1-1.Package Contents
Purchasers of the Stage Controller should find that the package contains the items listed below. Check
the package contents using the following checklist. Contact your retailer as soon as possible in the event
that you should find that any item is missing or damaged.
□HSC-103 Stage Controller :1
□User’s Manual (This Manual) :1
□AC Power Cable :1
About the setting of the Memory Switch of this controller, you can set it by sample software.
You can download sample programs from our web page.
For the details of the samples, see the manual of each program.
View our home page
http://www.global-optosigma.com/en_jp/software/sample_en.html
1-2. Overview
This controller is three axes stage controller, which has drivers for five-phase stepping motor.
Because this controller has a microstep driver built-in, the smooth movement in high resolving power
is possible.
When the HST-103 is connected to an ordinary personal computer via an USB interface, the stage
can be accurately moved to the desired position by simple commands sent from the PC.
In addition, manual operation is possible facility by connecting JOYSTICK (an optional product).
1-3.The HSC-103 System
3 Axis Stage Controller
HSC-103
USB cable
Control
from PC
MDR cable
MDR14-CA
JS-300/301/JB-400/401
/JD-100/101
Exe) HST-50X /HST-100X /HST-200X /HST-120YAW/HST-160YAW
D15D15A cable
D15D15A-CA
External I/O control
Please interface with 10120-3000PE by 3M
Limited.

SC12205-K10-15002A 2nd
7 Copyright 2020, SIGMAKOKI Co.,Ltd.
1-4. Parts and Functions
HSC-103 Front Panel
HSC-103 Rear Panel
Functions:
①
POWER switch
:
The product is on when the switch is set to ON. Set the switch to
OFF to turn the product off.
②
POWER LED
:
Lights up when powered.
③
Stage driving connector
:
Connect to the motorized stage of your choice. Supports up to
three axes.
④USB connector :
This connector is used when the device is controlled from the
computer via an USBinterface.
⑤OPTION Connector
:
When control by JS-300/301 JB-400/401 or JD-100/101.
※)About the usage of OPTION(JS-300/301/JB-400/401/JD-100/101),
confirm various User’s manual.
⑥I/Oconnector
⑤OPTIONconnector
④USBconnector
⑦ACconnector
③Stage driving connector 1~3
①POWER switch
②POWER LED

SC12205-K10-15002A 2nd
8 Copyright 2020, SIGMAKOKI Co.,Ltd.
⑥I/O Connector
:
The connector accepts a cable for sending and receiving I/O and
control signals to form an external device. and it can connect an
input and output signal and a stop signal to external equipment.
⑦
AC connector
:
This is where you connect the supplied 2.3meter power cable.
●USABLE DETACHABLE POWER CORDS
Type Connecter Cord Attachment plug cap
AC100-120V Use the detachable power cord set attached to the product only.
AC200-240V IEC C-22
Rated 7[A], 250[V]
UL, CSAApproved
Type SJT, No16 AWG Min.
3-Conductors
(Single phased;2-current carrying &
ground)
UL, CSA Approved
NEMA6-15P
Tandem blade
Rated 7[A],250[V]
UL, CSAApproved
Cable length of above Power Supply cord shall be shorter than 4.5[m].
For your own safety, make sure POWER is OFF before connecting every cable.

SC12205-K10-15002A 2nd
9 Copyright 2020, SIGMAKOKI Co.,Ltd.
Chapter 2: Basic Operations
2-1.HSC-103 Connection procedure
First, connect HSC-103 to the motorized stages.
①Please confirm the power switch of the HSC-103 is turning off.
②Connect a standard cable (D15RP-CA/D15D15A-CA) to the connector of the motorized stage.
③Connect the stage to be controlled as the first axis to the STAGE1 connector of the HSC-103
controller. Also connect the stage controlled as the second axis to the STAGE2 connector. Also
connect the stage controlled as the third axis to the STAGE3 connector.
2-2. Connecting to PC and peripheral device
Connect HSC-103 to PC and peripherals (JS-300/301 / JB-400/401 / JD-100/101).
USB interface is used for the connection between the PC and HSC-103.
The USB interface communication parameter at the time of default Value is described below. Please set
the configurations of the PC side according to the following table.
Parameter Descriptions
Baud rate 38400[bps]
Delimiters CR+LF
Parity None
Data bits 8bit
Stop bit 1bit
Flow control Hardware (RTS/CTS) or none (Default value is Hardware)
① Please confirm the power switch of the HSC-103 is turning off.
② Use a genuine USB cable,
③Insert of USB cable to the USB connector on the HSC-103.
Please connect peripheral device according to the procedure from ④to ⑥if you use it.
④Please use a special cable MDR14-CA for the connection of peripheral device.
⑤The one side of MDR14-CA is connected with the connector of the peripheral device.
⑥The connector on the other side of MDR14-CA is connected with the OPTION connector of
HSC-103.

SC12205-K10-15002A 2nd
10 Copyright 2020, SIGMAKOKI Co.,Ltd.
2-3.
Connecting Power Cable
Connect the supplied power cable to the AC connector on the rear panel of HSC-103 to plug the cable
into an outlet. (Ensure that it is grounded.)
2-4.USB Driver installation Method
please use after the installation of the USB-driver in the following content.
(In the case of Windows 7/ Windows 8/ Windows 8.1/ Windows 10)
While the Internet is connected, when connected toHSC-103, the installation of an automatic driver will
start.
*) If unconnected to the Internet, from FTDI’s website on a PC connected to the Internet, please go
to download the driver (VCP Drivers). Then move the driver that download to PC to connect the
HSC-103. Please then perform the installation of the driver.
The FTDI website (http://www.ftdichip.com/index.html)

SC12205-K10-15002A 2nd
11 Copyright 2020, SIGMAKOKI Co.,Ltd.
Chapter 3: Settings
3-1.Memory Switch settings
The Memory Switches store the controller settings.
When changing Memory Switch settings use the Sample software (SGSample), which can be
downloaded from http://www.global-optosigma.com/en_jp/software/sample_en.html
*) After changing Memory Switch, be sure to reboot the power HSC-103.
3-2. Memory Switch contents list and detailed settings
3-2-1 General
No Memory Switch contents Setting Range / Select items Default Value
1 SPD SEL 1~4 1
2 SPD 1 S 1~999999999 10000
3 SPD 1 F 1~999999999 100000
4 SPD 1 R 1~1000 200
5 SPD 2 S 1~999999999 30000
6 SPD 2 F 1~999999999 300000
7 SPD 2 R 1~1000 200
8 SPD 3 S 1~999999999 70000
9 SPD 3 F 1~999999999 700000
10 SPD 3 R 1~1000 200
11 SPD 4 S 1~999999999 100000
12 SPD 4 F 1~999999999 1000000
13 SPD 4 R 1~1000 200
14 IO_LVL ACT HIGH/ACT LOW ACT HIGH
1) SPD SEL:Speed selection at Power ON
Select the initial setting Speed No. at Power ON.
[Setting Range] 1 ~ 4
2)~13) Speed 1~4(S)(F)(R):Speed Setting
Set 4 kinds of travel stage Speed (minimum S, maximum F, and acceleration/deceleration time R) at
Power ON. When JS-300/301(Option) operation and during the internal program behavior, work in this
movement speed setting.
[Setting Range] S:1~999999999 (Unit:0.01[μm/s])
F:1~999999999 (Unit:0.01[μm/s])
R:1~1000 (Unit:[ms])
*) Minimum S values should be set smaller than maximum F at Speed Setting.

SC12205-K10-15002A 2nd
12 Copyright 2020, SIGMAKOKI Co.,Ltd.
14) IO_LVL:I/O Output signal logic Setting
Select Logic (Voltage level) for I/O output signal.
[Select item] ACT HIGH:Lo level (Active High) normally
ACT LOW:Hi level (Active low) normally
3-2-2 INTERFACE
No
Memory Switch contents Setting Range / Select items Default Value
1
BAUDRATE 9600/38400/57600 38400
1) BAUDRATE:Baudrate setting
Set the data communication speed for the USB (Serial communication) Interface.
[Select item] 9600:9600[bps]
38400:38400[bps]
57600:57600[bps]
3-2-3 Axis
No
Memory Switch contents Setting Range / Select items Default Value
1 STG UT1 PULSE/MICRO/DEGREE MICRO
2 STG UT2 PULSE/MICRO/DEGREE MICRO
3 STG UT3 PULSE/MICRO/DEGREE MICRO
4 PLS_RATE1 1~1000000 1000
5 PLS_RATE2 1~1000000 1000
6 PLS_RATE3 1~1000000 1000
7 MOVE1 POS/NEG POS
8 MOVE2 POS/NEG POS
9 MOVE3 POS/NEG POS
10 ORG1 SEL OFF/MINI/CENTER/ORGS/NORM/ZPM/ZPP MINI
11 ORG2 SEL OFF/MINI/CENTER/ORGS/NORM/ZPM/ZPP MINI
12 ORG3 SEL OFF/MINI/CENTER/ORGS/NORM/ZPM/ZPP MINI
13 ORG OFFSET1 0~999999999 0
14 ORG OFFSET2 0~999999999 0
15 ORG OFFSET3 0~999999999 0
16 CONFIG1 ON/OFF ON
17 CONFIG2 ON/OFF ON
18 CONFIG3 ON/OFF ON

SC12205-K10-15002A 2nd
13 Copyright 2020, SIGMAKOKI Co.,Ltd.
1~3) STG_UT1~3:Select the units for display
Set the units used to display position coordinates of OPTION_unit (JS-300/301, JB-400/401).
[Select item] PULSE:Number of pulses
MICRO:Micron m units
DEGREE:Degrees units
4~6) PLS_RATE1~3:Pulse Rate setting(1~3axes))
Set the travel distance per 1 pulse for each axis.
The divisions of the driver set at 40. If the setting is not right, right positioning movement is not possible.
*) Otherwise, it is not able to position correctly. (Setting Unit:0.1[nm] ) *1)
[Setting range] 1~1000000 (0.1[nm]~100[μm]) *1)
*1) If “STG_UT1~4” setting is “DEGREE”, please setting Unit: 0.000001[ °].
7~9) MOVE1~3:Travel direction setting 1~3axis
Set + travel direction for each axis.
[Select item] POS:Positive rotation
NEG:Negative rotation
10~12) ORG1 SEL~ORG3 SEL:Origin reset method setting
Set Origin reset method for each axis.
[Select item] OFF:Origin reset OFF (ORG0)
MINI:ORG1
CENTER:ORG2
ORGS:ORG3
NORM:ORG4
ZPM:ORG5
ZPP:ORG6
*) Regarding each method, please refer to “Origin Reset Method”.
13~15) ORG OFFSET1~3:ORG offset setting
Set ORG offset value for each axis (ORG1、ORG5、ORG6) at the ORG reset.
[Setting range] 0~999999999 (Unit:0.01[μm])
*) When Setting range is set [0], ORG offset value is 0.5[mm].

SC12205-K10-15002A 2nd
14 Copyright 2020, SIGMAKOKI Co.,Ltd.
16~18) CONFIG1~3:Select Auto-Config mode.
Set Auto-Config mode for each axis.
[Select item] ON:
effect
OFF:no
effect

SC12205-K10-15002A 2nd
15 Copyright 2020, SIGMAKOKI Co.,Ltd.
『Origin Reset Method』
There are six types in Origin Reset setting. Please select optimal Origin Reset setting for stage in use
depending upon software.
There are two parameters to do with Origin Reset, which are Origin Reset Speed (S, F, R, M) and Origin
offset (ORG OFFSET). Parameters of each axis can be individually set. Please select the optimum value
according to the software.
In case of when PGO (Z pulse) is used as an Origin sensor, (ORG5 or ORG6), Origin sensor is not in need
at stage since Excitation Reset of motor driver is used.
1, ORG0 Not reset ORGIN position.
2, ORG1 (MINI method compatible, however stage moves to ORG offset value)
ORG OFFSET default value: 0.5[mm].
CW(CCW) Sensor
Detect CW limit sensor
Move 0.5[mm]
Detect CW limit sensor
Move to offset position
ORG reset speed M
ORG reset speed S
ORG reset speed M
ORG reset speed F

SC12205-K10-15002A 2nd
16 Copyright 2020, SIGMAKOKI Co.,Ltd.
3, ORG2 (CENTER method)
4, ORG3 (for 3 sensor use (LS + ORG))
4-1) In case that ORG sensor is set on the inside of CW(CCW) sensor
CCW(CW) Sensor CW (CCW) Sensor
ORG reset speed F
Detect CW limit sensor
ORG reset speed F
Move 0.5[mm]
ORG reset speed M
Detect CW limit sensor
ORG reset speed M
Detect CCW limit sensor
ORG reset speed M
ORG reset speed S
Move 0.5[mm]
ORG reset speed S
Detect CCW limit sensor
LS halfway point
Move to halfway point
between CW/CCW sensor
ORG reset speed F
ORG sensor CW (CCW) Sensor
Detect ORG sensor
Move 0.5[mm]
Detect ORG sensor
ORG reset speed M
ORG reset speed S

SC12205-K10-15002A 2nd
17 Copyright 2020, SIGMAKOKI Co.,Ltd.
4-2) In case that ORG sensor is set beyond limit SW toward CW direction.
Caution1) In case that after detect CW (CCW) sensor, stage move toward CCW direction and then can not
detect ORG sensor (in case of no ORG sensor), stage stop at CCW (CW) sensor position.
5, ORG4 (for 4 sensor (LS+SD+ORG) use.)
5-1) In case that NEAR ORG sensor is on the inside of CW(CCW) sensor.
Detect ORG sensor
ORG sensor
ORG reset speed F
Detect CW limit sensor
Move 0.5[mm]
CW (CCW) sensor
ORG reset speed M
ORG reset speed S
ORG reset speed M
Detect ORG sensor
NEAR ORG sensor
ORG reset speed F
Detect NEAR ORG sensor
Detect ORG sensor
ORG sensor
ORG reset speed S
CW (CCW) sensor

SC12205-K10-15002A 2nd
18 Copyright 2020, SIGMAKOKI Co.,Ltd.
5-2) In case that ORG sensor is beyond NEAR ORG sensor toward CW(CCW) direction.
Caution1) In case that after detect CW (CCW) sensor, stage move toward CCW direction and then can not
detect NEAR ORG sensor (in case of no NEAR ORG sensor), stage stop at CCW (CW) sensor
position.
Caution 2) In case that after detect NEAR ORG sensor, stage move toward CW direction and then can not
detect ORG sensor (in case of no ORG sensor), stage stop at CW (CCW) sensor position.
6, ORG5 (for 3 sensor use (LS+ORG(Z phase)))
NEAR ORG sensor
ORG sensor
ORG reset speed F
Detect CW limit sensor
Detect NEAR ORG sensor
ORG reset speed S
CW (CCW) sensor
ORG reset speed M
Detect ORG sensor
ORG reset speed F
ORG sensor (Z phase)
CW (CCW) sensor
Detect CW limit sensor
Move to offset position
Detect ORG sensor
(z phase)
ORG reset speed M
ORG reset speed S

SC12205-K10-15002A 2nd
19 Copyright 2020, SIGMAKOKI Co.,Ltd.
7, ORG6 (for 3 sensor use (LS+ORG(Z phase)))
ORG reset speed S
ORG reset speed S
ORG reset speed F
ORG sensor (Z phase)
CW (CCW) sensor
Detect CW limit sensor
Move to offset position
After detect ORG sensor
move to 0.5[mm] position
Detect ORG sensor
(Z phase)
ORG reset speed M

SC12205-K10-15002A 2nd
20 Copyright 2020, SIGMAKOKI Co.,Ltd.
3-2-4 Sensor
No
Memory Switch contents Setting Range / Select items Default Value
1 LS LVL1 NM OPEN/NM CLOSE NM CLOSE
2 LS LVL2 NM OPEN/NM CLOSE NM CLOSE
3 LS LVL3 NM OPEN/NM CLOSE NM CLOSE
4 OS LVL1 NM OPEN/NM CLOSE NM OPEN
5 OS LVL2 NM OPEN/NM CLOSE NM OPEN
6 OS LVL3 NM OPEN/NM CLOSE NM OPEN
7 NS LVL1 NM OPEN/NM CLOSE NM OPEN
8 NS LVL2 NM OPEN/NM CLOSE NM OPEN
9 NS LVL3 NM OPEN/NM CLOSE NM OPEN
1~3) LS LVL 1~3: Limit sensor input logoc level setting (1~3axis)
Select limit sensor detecting level (Input logic level) for each axis
[Select item] NM Open:(Normally switch ON by detecting limit sensor from SW OFF condition)
NM Close:(Normally switch OFF by detecting limit sensor from SW ON condition)
4~6) OS LVL 1~3: ORG sensor input logic level setting (1~3axis)
Select ORG sensor detecting level (Input logic level) for each axis.
[Select item] NM Open:(Normally switch ON by detecting ORG sensor from OFF condition)
NM Close:(Normally switch OFF by detecting ORG sensor from ON condition)
7~9) NS LVL 1~3: NEAR ORG sensor input logic level setting (1~3axis)
Select NEAR ORG sensor detecting level (Input logic level) for each axis
[Select item] NM Open:(Normally switch ON by detecting NEAR ORG sensor from OFF condition)
NM Close:(Normally switch OFF by detecting NEAR ORG sensor from ON condition)
Table of contents
Other SIGMAKOKI Controllers manuals
Popular Controllers manuals by other brands
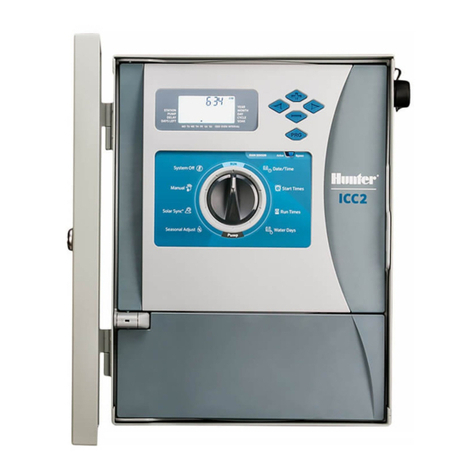
Hunter
Hunter ICC2 Programming instructions
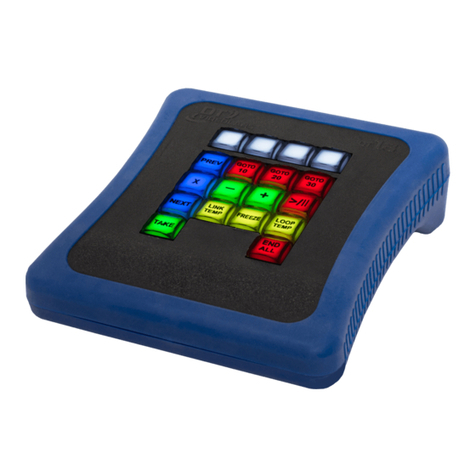
DT VIDEOLABS
DT VIDEOLABS DT18 quick start guide
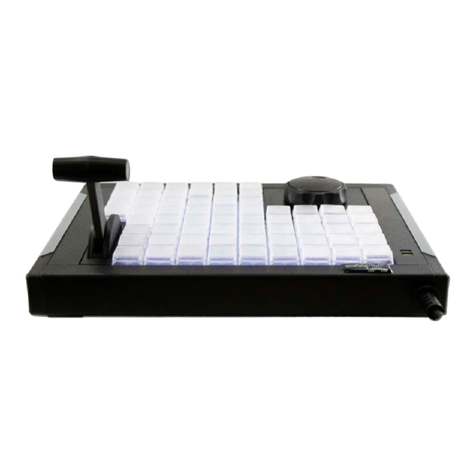
X-keys
X-keys XKE-64 product manual
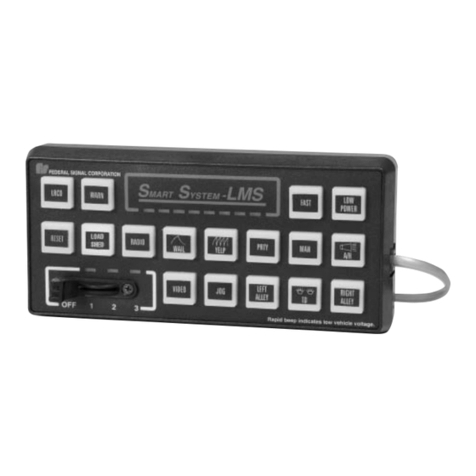
Federal Signal Corporation
Federal Signal Corporation SmartSystem SS2000-LMS Operation and configuration instructions
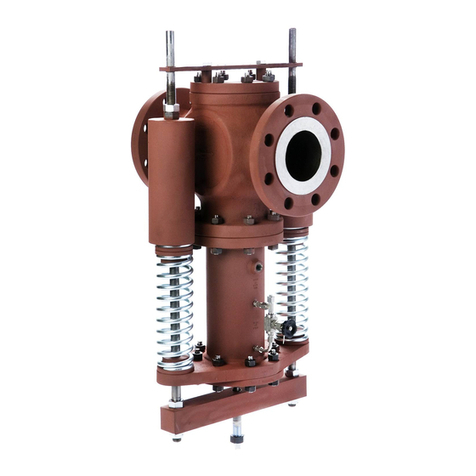
Mankenberg
Mankenberg DM 4 Original operating manual

Emerson
Emerson CSB400 Series instruction manual