SIGMAKOKI OptoSigma PGC-04-U User manual

SC40401-K10-15002A
2nd
1 Copyright 2018, SIGMAKOKI Co.,Ltd.
Pulse-Generating Controller
PGC-04-U

SC40401-K10-15002A
2nd
2 Copyright 2018, SIGMAKOKI Co.,Ltd.
Notes regarding these materials
・ These materials are intended as a reference to assist our customers in the use of
the SIGMAKOKI CO., LTD. Product best suited to the customer’s application; they
do not convey any license under any intellectual property rights, or any other rights,
belonging to SIGMAKOKI CO., LTD. or a third party.
・ SIGMAKOKI CO., LTD. assumes no responsibility for any damage, or infringement
of any third-party’s rights, originating in the use of any product data, diagram, charts,
programs, or algorithms contained in these materials.
・ All information contained in these materials, including product data, diagrams,
charts, programs and algorithms represents information on products at the time of
publication of these materials, and are subject to change by SIGMAKOKI CO.,LTD.
without notice due to product improvements or other reasons.
・ When using any or all of the information contained in these materials, including
product data, diagrams, charts, programs, and algorithm, please be sure to evaluate
all information and products. SIGMAKOKI CO., LTD. assumes no responsibility for
any damage, liability or other loss resulting from the information contained herein.
・ SIGMAKOKI CO., LTD. products are not designed or manufactured for use in
equipment or system that is used under circumstances in which human life is
potentially at stake. SIGMAKOKI CO., LTD. products cannot be used for any
specific purposes, such as apparatus or systems for transportation, vehicular,
medical, aerospace, nuclear, or undersea repeater use.
・ The prior written approval of SIGMAKOKI CO., LTD. is necessary to reprint or
reproduce in whole or in part these materials.
・ If these products or technologies are subject to the Japanese export control
restrictions, they must be exported under a license Japanese government and
cannot be imported into a country other than the approved destination.
Any diversion or re-export contrary to the export control laws and regulations of
Japan and/ or the country of destination is prohibited.

SC40401-K10-15002A
2nd
3 Copyright 2018, SIGMAKOKI Co.,Ltd.
Contents
For Your Safety ...................................................................................................................4
Chapter 1: Before You Begin.............................................................................................6
1-1.Package Contents.....................................................................................................6
1-2.Overview....................................................................................................................6
1-3.PGC-04-U System Diagram......................................................................................7
1-4.Parts and Functions..................................................................................................7
Chapter 2: Connection Flow..............................................................................................9
2-1.Connection setup various drivers, the SERVO-PACK...........................................9
2-2.Connection with various drivers ...........................................................................10
2-3.Connection between PGC-04-U and stage’s sensor ............................................15
2-4.Setting of drivers and servopack...........................................................................16
2-5.Connection between PGC-04-U and motoried stage/ Driver...............................21
2-6.Connection between driver and motorized stage (at the time of standard cable
use).................................................................................................................................22
2-7.Interface with PC.....................................................................................................22
2-8.Driver installation Method......................................................................................23
2-9.Power Supply ..........................................................................................................23
Chapter 3: Settings...........................................................................................................24
3-1.Memory Switch settings.........................................................................................24
3-2 Memory Switch contents list and detailed settings .............................................24
3-3.LAN settings............................................................................................................36
Chapter 4: Feature............................................................................................................38
4-1.Command ................................................................................................................38
4-2. Program functions.................................................................................................55
4-3.Emergency STOP....................................................................................................59
Chapter 5: Rotation Stage................................................................................................60
Chapter 6: Specifications.................................................................................................61
6-1.Specifications..........................................................................................................61
6-2.Connector Pin Assignments ..................................................................................62
6-3.Outlines....................................................................................................................64

SC40401-K10-15002
1st
4
Copyright 2015, SIGMAKOKI Co.,Ltd.
For Your Safety
Before using this product, read this manual and all warnings or cautions in the documentation provided.
Only Factory Authorized Personnel should be changes and/or adjust the parts of controller.
The Symbols Used in This Manual
! WARNING ! CAUTION
This symbol marks warnings that should be read
and used to prevent serious injury or death.
This symbol indicates where caution should be used
to avoid possible injury to yourself or others, or
damage to property.
The above indications are used together with the following symbols to indicate the exact nature of the warning or
caution.
Examples of Symbols Accompanying Warnings and Cautions
△Symbols enclosed in a triangle indicate warnings and cautions. The exact nature of
the warning or caution is indicated by the symbol inside (the symbol at left indicates
risk of electrocution).
○Symbols enclosed in a circle mark indicate prohibitions(actions that must not be
performed).The exact nature of the prohibition is indicates by the symbol inside or
next to the circle mark (the symbol at left indicates that the product must not be
disassembled).
●Symbols inside a black circle mark actions that must be performed to ensure safety.
The exact nature of the action that must be performed is indicated by the symbol
inside (the symbol at left is used in cases in which the AC adapter must be unplugged
to ensure safety).
Symbols on the product
The symbol mark on the product calls your attention. Please refer to the manual, in the case that you
operate the part of the symbol mark on the product.
! This symbol labeled on the portion calls your attention.

SC40401-K10-15002A
2nd
5 Copyright 2018, SIGMAKOKI Co.,Ltd.
Disclaimer of Liability
① SIGMAKOKI CO., LTD. does not accept liability for damages resulting from the use of this product or
the inability to use this product.
② SIGMAKOKI CO., LTD. does not accept liability for damages resulting from the use of this product
that deviates from that described in the manual.
③ SIGMAKOKI CO., LTD. does not accept liability for damages resulting from the use of this product in
extraordinary conditions, including fire, earthquakes, and other acts of God, action by any third party,
other accidents, and deliberate or accidental misuse.
④ If the equipment is used in a manner not specified by the SIGMAKOKI CO., LTD., the protection
provided by the equipment may be impaired.
WARNING
●Do not use this product in the presence of flammable gas, explosives, or corrosive substances, in areas
exposed to high levels of moisture or humidity, in poorly ventilated areas, or near flammable materials.
●Do not connect or check the product while the power is on.
●Installation and connection should be performed only by a qualified technician.
●Do not bend, pull, damage, or modify the power or connecting cables.
●Do not touch the products internal parts.
●Connect the earth terminal to ground.
●Should the product overheat, or should you notice an unusual smell, heat, or unusual noises coming
from the product, turn off the power immediately.
●Do not turn on the power in the event that it has received a strong physical shock as the result of a fall
or other accident.
●Do not touch the stage while operation.
●Use dry clothes only for cleaning the equipment.
!

SC40401-K10-15002A
2nd
6 Copyright 2018, SIGMAKOKI Co.,Ltd.
Chapter 1: Before You Begin
1-1.Package Contents
Purchasers of the Controller should find that the package contains the items listed below. Check the
package contents using the following checklist. Contact your retailer as soon as possible in the event that
you should find that any item is missing or damaged.
About the setting of the Memory Switch of this controller, you can set it by sample software.
Sample software are available for download our website.
WEB http://www.global-optosigma.com/en_jp/software/sample_en.html
1-2.Overview
This controller (below PGC-04-U) is a Pulse-generator type 4-axis Controller.
PGC-04-U can be connected to the various motor drivers.
When PGC-04-U connected to an ordinary personal computer via an USB, LAN interface, the stage can
be accurately moved to the desired position by simple commands sent from the PC.
Can be manually operated by a Handy Terminal (JS-300, JB-400, JD-100).
PGC-04-U
□PGC-04-U Controller
□User’s Manual (This Manual)
Option
□PAT-POW (DC24V Power Supply)

SC40401-K10-15002A
2nd
7 Copyright 2018, SIGMAKOKI Co.,Ltd.
1-3.PGC-04-U System Diagram
1-4.Parts and Functions
PGC-04-U Front Panel
8) Power Supply Terminal
1) POWER LED 3) USB Connector
9) DRIVER1~4 Connector
2) Emergency STOP Connector 6) I/O Connector
4) ETHERNET Connector
5) OPTION Connector
PGC-04-U
External I/O control
Please interface with 10120-3000PE by 3M
Company.
USB Cable
LAN Cable(*1)
Control
from PC
*1) In case of connection between PC and PGC-04-U directry please use cross cable, and in
case of connection through HUB please use straight cable.
MDR Cable JS-300/JB-400/JD-100
5-phase Stepping Driver MC-S0514ZU ext.
2-phase Stepping Driver A8576-0415Y ext.
Servopack SGDV-2R9EP1A
α_step Driver AR series
Exe)HPS60-20-M5 /HPS60-20-M2 /HPS60-20-MA /HPS60-20-ML
Motor Cable and encoder Cable
PGC-*** Cable
7) FG Terminal

SC40401-K10-15002A
2nd
8 Copyright 2018, SIGMAKOKI Co.,Ltd.
1) POWER LED :Lights up when powered.
2) Emergency Stop Connector :It connects with Emergency Stop Switch. Please refer to「4-3 Emergency
STOP」for further details.
3) USB Connector :When control by USB Interface(Serial) through PC, please use USB.
4) ETHERNET Connector :In case of connection through Ethernet from PC, connect with using
straight or cross LAN cable.
5) OPTION Connector :When control by JS-300/ JB-400 or JD-100.
※)About the usage of OPTION(JS-300/JB-400/JD-100), confirm various
User’s manuals.
6) I/O Connector :It interfaces with input/output signal for external devices.
7) FG Terminal :It is Terminal for Frame Ground. Please connect to Earth in the actual
environment.
8) Power Supply Terminal :Supply Power (DC +24V 1.4A)
9) DRIVER Connector 1~4 :Connects to the cable attached to the Driver/ Servo-pack in use.
For your own safety, make sure POWER is OFF before connecting every cable.
Make sure to set up and wire the cable supplying DC+24V and FG_GND to the PGC-04-U so
that the maximum length of cable is not longer than 2m.
Power supply, use a DC power supply with primary side and the secondary side is reinforced
insulation.
In addition, wire the power supply separate from the motor drivers and servo -pack.

SC40401-K10-15002A
2nd
9 Copyright 2018, SIGMAKOKI Co.,Ltd.
Chapter 2: Connection Flow
2-1.Connection setup various drivers, the SERVO-PACK
When shipped from the factory, because it is a stepping motor driver setting, when connecting the α_step
driver and servo-pack(SGDV series), Please change the settings to the following procedure.
When connecting a 2-phase stepping motor driver and 5-phase, the setting of this item is unnecessary.
① Remove the cover on top of the PGC-04-U. (Remove M2.6 dish bis × 8)
※
※※
※)When removing the top cover, a power supply, Plese carry it out in a state of power
supply OFF by all means.
② Replace jumper pin of following Fig.2-1 in the AM side (α_step motor and AC servo motor side)
from the SP side (stepping motor side). AX1,2,3,4 shows the AXIS1,2,3,4 respectively. Therefore,
change the setting of the axis you want to change.
JP forAXIS1 setting : JP11,12 , JP for AXIS2 setting : JP13,14
JP forAXIS3 setting : JP15,16 , JP for AXIS4 setting : JP17,18.
※
※※
※)Setting the jumper pin except theabove is unnecessary. Do not change it.
Example) When changing AXIS1 to the AC servo setting, it becomes like Fig.2-2.
Fig.2-1 for setting the jumper pin
AX1(AXIS1)
AX2(AXIS2)
AX3(AXIS3)
AX4(AXIS4)
AM
SP
AM
SP

SC40401-K10-15002A
2nd
10 Copyright 2018, SIGMAKOKI Co.,Ltd.
Fig.2-2 example) 1 Axis AC servo jumper pin setting (Set to the AM side of the JP11, 12)
③ Setting of ②After finishing, please attach the upper cover removed in ①
2-2.Connection with various drivers
Connecting PGC-04-U and various drivers, please use a “DRIVER1 - 4” connector. Please refer to the
following list for the pin assignment of the “DRIVER1 - 4” connector.
No. Description Function
1 PP+ +pulse output
2 PP-
3 PM+ -pulse output
4 PM-
5 CLR (ERC) Clear-signal output (AC_SRV and ALPHA setting)
6 Servo_ON/STEP4 Servo_ON-signal output (AC_SRV/ALPHAsetting)
/ STEP4-signal output (STEPNG setting)
7 P_Reset/STEP3 P_Reset-signal output (ALPHA setting)
/ STEP3-signal output (STEPNG setting)
8 ALM_RST/STEP2 ALM_Reset-signal output (AC_SRV setting)
/ STEP2-signal output (STEPNG setting)
9 CCM/STEP1 CCM-signal output (ALPHA setting)
/ STEP1-signal output (STEPNG setting)
10 FREE/H.O FREE-signal output (ALPHA setting)
/ H.O-signal output (STEPNG setting)
11 #RES Power_ON_Reset-signal output
12 Auto_Config Auto_Config-signal input output (for only sigmakoki products.)
13 ALARM_IN(Driver) ALARM-signal input
The AM side
Jumper

SC40401-K10-15002A
2nd
11 Copyright 2018, SIGMAKOKI Co.,Ltd.
14 INP Positioning completion signal input (COIN/END-signal input)
15 TIM+ (Z_P+) TIM(PCO)/Z phase-signal input ※1
16 TIM- (Z_P-)
17 LS+ +LS(+Limit Sensor) input
18 LS- -LS(-Limit Sensor) input
19 ORG ORG(Origin sensor) input
20 NEAR NEAR(Near Org sensor) input
21 24V DC24V output
22 24V
23 5V DV5V output
24 5V_ with 180ΩDV5V with 180Ω
25 GND GND
26 GND
※1) About the TIM/Z_P-signal, refer to “2-1 Connection setup various drivers, the SERVO-PACK”. It
becomes the line-driver tray setting in AM side setting, photo-coupler tray setting in SP side setting.
At the use of SGDV and α_step, AM setting. At the use of MC-S0514ZU,SP setting.
When you connect various drivers, please use a standard cable (option) or please connect various driver
connection of P12 – P14 after reference.
Coution Use a shield-cable for a connection cable.
Coution Use less than 2m of connection cable. In addition, wire it to become as short as
possible.

SC40401-K10-15002A
2nd
12 Copyright 2018, SIGMAKOKI Co.,Ltd.
1) When it connects with the AC servo pack SGDV series (product made in Yaskawa Electric
Corporation)
When you connect with the AC servo pack SGDV series, please connect using standard cable
(PGC-ACS), or, please connect the following connection after reference.
※
※※
※)When use an AC servo pack, AM side setting, please while referring to a 2-1 clause.
※
※※
※)When use an AC servo pack, please make setting of the memory switch(Axis:29 - 32) AC
SRV setting.

SC40401-K10-15002A
2nd
13 Copyright 2018, SIGMAKOKI Co.,Ltd.
2) When it connects with theα_STEPAR series (product made in OrientalMotor)
When you connect with theα_STEP AR series, please connect using standard cable (PGC-ARD),
or, please connect the following connection after reference.
※
※※
※) When use an α_STEP, AM side setting, please while referring to a 2-1 clause.
※
※※
※) When use anα_STEP, please make setting of the memory switch(Axis:29 - 32) ALPHA
setting.

SC40401-K10-15002A
2nd
14 Copyright 2018, SIGMAKOKI Co.,Ltd.
3) When it connects with the Five phase stepping motor driver MC-S0514ZU (product made in
SIGMAKOKI)
When you connect with the MC-S0514ZU, please connect using standard cable (PGC-S0514ZU),
or, please connect the following connection after reference.
※
※※
※) When use an MC-S0514ZU, SP side setting, please while referring to a 2-1 clause.
※
※※
※) When use an MC-S0514ZU, please make setting of the memory switch(Axis:29 -
32)STEPNG setting.
*1) PGC-04-U 13pin is ALARM_IN, so when using MC-S0514ZU, please be sure to connect with GND.
When being open, it'll be a driver alarm.

SC40401-K10-15002A
2nd
15 Copyright 2018, SIGMAKOKI Co.,Ltd.
2-3.Connection between PGC-04-U and stage’s sensor
When connecting various stage sensors (LS+, LS-, ORG, NEAR), please use standard cable (option) or
connect according to the following circuit diagram.
※
※※
※) Please set input logic(polarity (NORMAL OPEN/NORMAL CLOSE)) of each sensor by a memory
switch (Sensor:1-12), according to the sensor you use.
※
※※
※) Please use a limit sensor(LS+, LS-) of each axis by identical logic. It isn’t possible to use LS+,
LS- by different logic (polarity).

SC40401-K10-15002A
2nd
16 Copyright 2018, SIGMAKOKI Co.,Ltd.
2-4.Setting of drivers and servopack
The following setting is needed to connect PGC-04-U and various driver, servopack.
①AC servopack SGDV siries (YASKAWA Electric Corporation) setting
1)Setting change preparations of SGDV series
When changing the setting of a SGDV series, exclusive software Sigma Win+ is used.
Please download Sigma Win+ from YASKAWA Electric Corporation HP
(http://www.e-mechatronics.com/download/tool/servo/sgmwinpls/index.html)
2)Connect PC and Servopack
Please connect a PC in which Sigma Win+ is installed and a servopack.
Please connect by a USB cable (the servopack side: Micro-B type).
And, please connect a servopack and a servomotor (stage).
(A SIGMAKOKI’s standard motor is SGMMV-A1E2A21. A SIGMAKOKI’s standard servopack is
SGDV-2R9EP1A.)
Fig2-3 Connection composition
PC
Servopack
SGDV
-
2R9EP1A
USB Cable Servomotor
SGMMV
-
A1E2A21
Encoder Cable
Motor Cable
Power supply for
Servopack

SC40401-K10-15002A
2nd
17 Copyright 2018, SIGMAKOKI Co.,Ltd.
3)Servopack settings
After a connection, please supply a servo pack with electricity. After supplying electricity, please start
Sigma Win+. When connecting for the first time, please confirm the connection of a servo pack in
"Search".
When the connection is confirmed, connected servo pack and servomotor are indicated.
After choosing the servo pack you’d like to set, please click “Connect”.
Next, please choose“Edit Parameters(U)” in Sigma Win+ screen.A parameter editing screen is
indicated.

SC40401-K10-15002A
2nd
18 Copyright 2018, SIGMAKOKI Co.,Ltd.
Please set the following parameter in parameter edit.
○Pn002 : Default(0000H) ⇒ Change(0100H)
Uses absolute encoder as an incremental encoder.
○Pn200 : Default(0000H) ⇒ Change(2001H)
Input filter(~4Mpps)and order pulse form are CW+CCW、positive logic.

SC40401-K10-15002A
2nd
19 Copyright 2018, SIGMAKOKI Co.,Ltd.
○Pn20E : Default(4) ⇒ Change(131072)
Electronic Gear Ratio (Numerator) Encoder resolution of SGMMV-A1E2A21 Set value 131072
※
※※
※But, when the reduction gear ratio isn't 1/1, please set a figure which matches the
reduction gear ratio.
○Pn210 : Electronic Gear Ratio (Denominator)
First the amount of transfer of 1 pulse is decided.
In case of X stage of reduction gear ratio: 1/1, please calculate as follows and input.
Screw lead:p(mm), The amount of transfer per 1 pulse :u(um)
Electronic Gear Ratio (Denominator) = (p×1000)/u
(※
※※
※Please make electronic gear ratio an integer.)
example) When SGMV26-100(screw lead:2mm) made of SIGMAKOKI is set as amount of transfer
0.1µm per pulse.
Electronic Gear Ratio (Denominator) = (2×1000)/0.1
= 20000
※
※※
※) Please set electronic gear ratio in 4000≧
≧≧
≧Pn20E/Pn210≧
≧≧
≧0.001 area
When exceeding this area, 『
『『
『Parameter Setting Error』
』』
』occurs.
※
※※
※) Please set memory switch (axis: 9-12) PLS_RATE of PGC-04-U according to the above.
○Pn50A : Default(2100H) ⇒ Change(8100H)
P-OT Signal Mapping is changed.

SC40401-K10-15002A
2nd
20 Copyright 2018, SIGMAKOKI Co.,Ltd.
○Pn50B : Default (6543H) ⇒ Change (6548H)
N-OT Signal Mapping is changed.
The parameter to which setting is necessary is as mentioned above.
Please change other parameters as the need arises.
Please confirm details of a servo pack by manual,etc.from YASKAWA Electric Corporation
WEB(http://www.e-mechatronics.com/product/servo/index.html).
②α_STEP AR series (product made in OrientalMotor) setting
1)ARD-K(α_STEP driver)setting
The setting is changed by the front switch of driver.
○Resolution
Please set resolution per motor 1 round by SW1-No.3/No.4
SW3 SW4 Resolution
OFF ON 500 P/R
OFF OFF 1000 P/R
ON ON 5000 P/R
ON OFF 10000 P/R
Default (1000 P/R)
※
※※
※) Please set memory switch (axis: 9-12) PLS_RATE according to the above.
○Please use pulse input system by default:2 pulse input system.
Please confirm details of α_STEP driver by manual,etc.from ORIENTAL MOTOR Co. , Ltd.
WEB(http://www.orientalmotor.co.jp/products/stepping/ar_dc/features/).
Table of contents
Other SIGMAKOKI Controllers manuals
Popular Controllers manuals by other brands
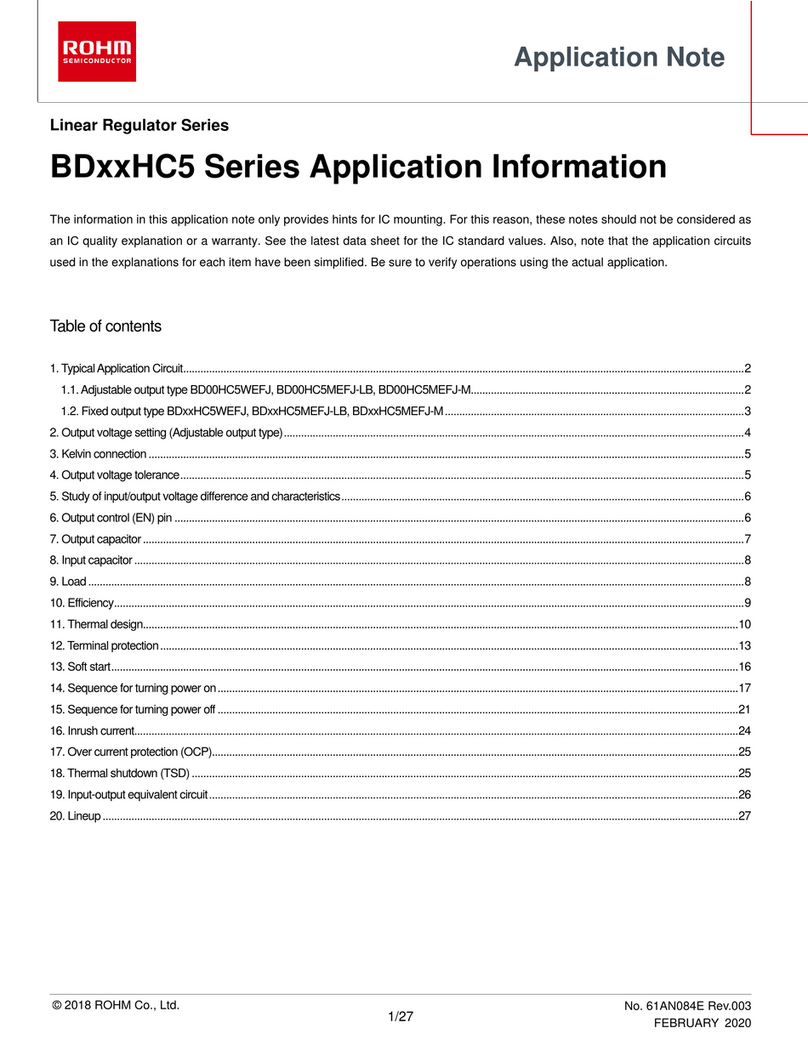
Rohm
Rohm BD HC5 Series Application Information

Honeywell
Honeywell Touchpoint Plus user guide
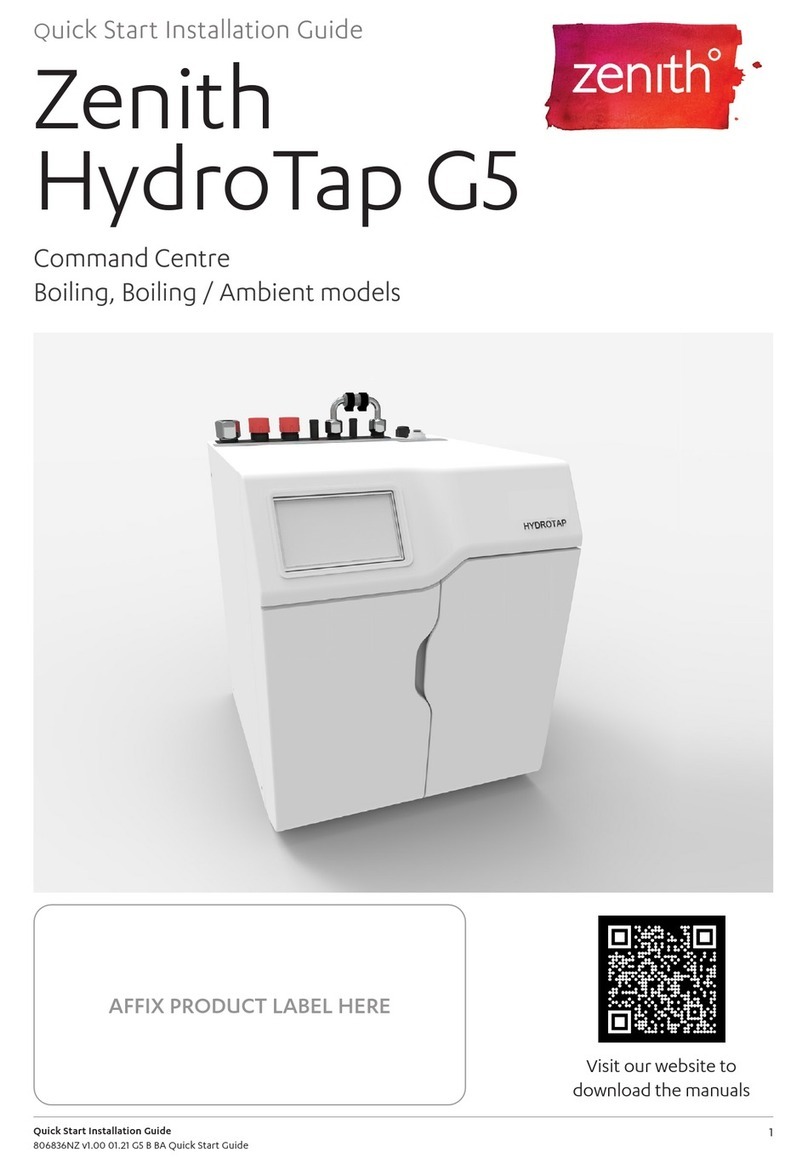
Zenith
Zenith HydroTap G5 Quick start installation guide
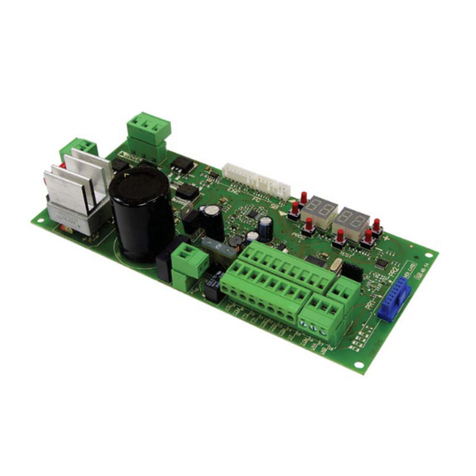
Roger Technology
Roger Technology B70/1DC instructions
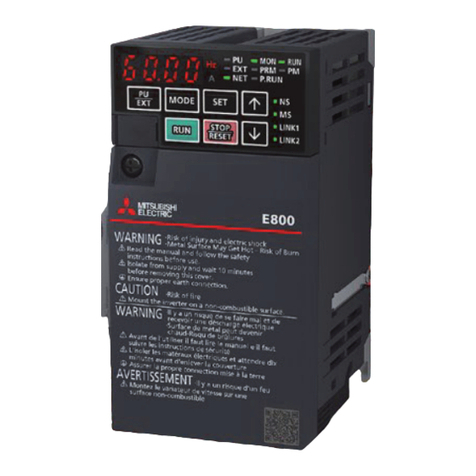
Mitsubishi Electric
Mitsubishi Electric MELSEC iQ-F Series Quick connection guide
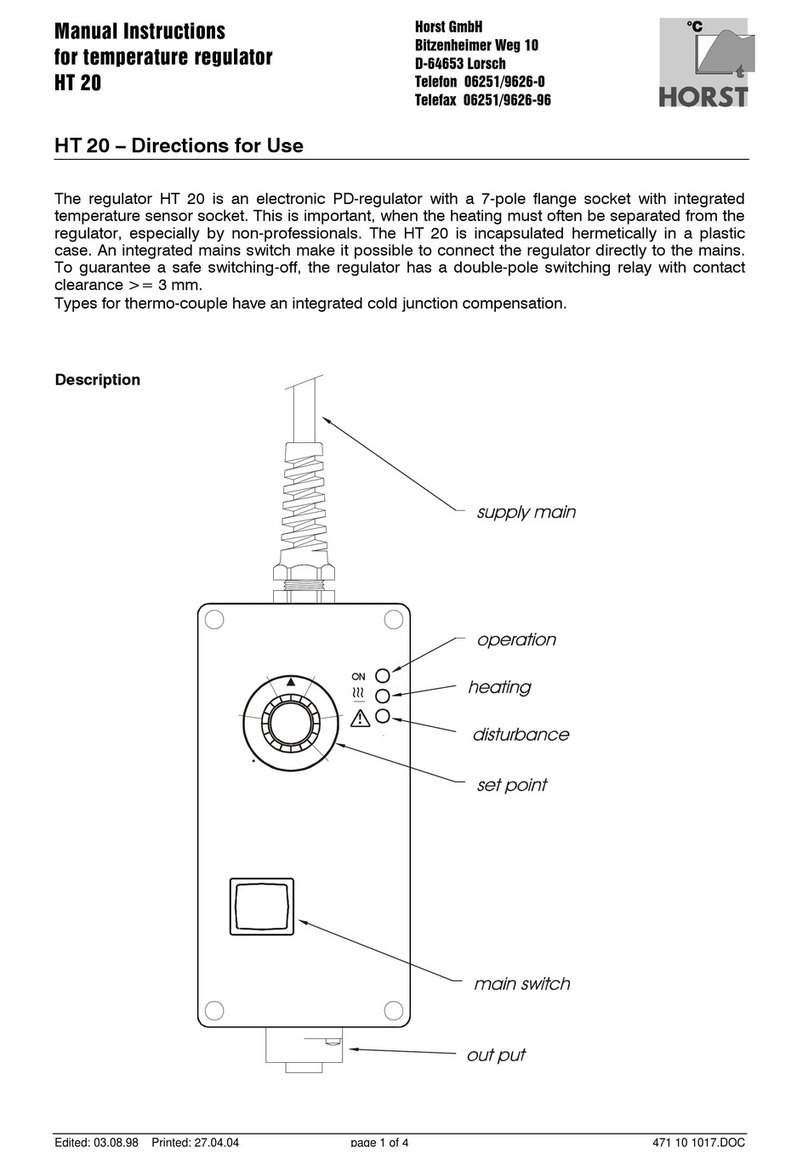
Horst
Horst HT 20 Manual instructions