Simco PerforMAX IQ Instruction Manual

5200992 Rev F
2257 North Penn Road
Hatfield, PA 19440
(215) 822-2171
customerservice@simcomail.com
www.simco.biz
INSTRUCTIONS
Operation/Maintenance
PerforMAX® IQ
Static Neutralizing System
SIMCO’s PerforMAX IQ is an intelligent air ionization system that
enables the user to be in charge of static electricity. It is designed to
efficiently neutralize electrostatic charges on films, paper, non-wovens
and fabric in web or sheet form. Due to its high output and range, the
PerforMAX IQ is also ideal for applications such as blow molding and
injection molding.
SECTION 1: Description
SECTION 2: Safety
SECTION 3: Features
SECTION 4: Specifications
SECTION 5: Installation
SECTION 6: Operation
SECTION 7: Maintenance
SECTION 8: Replacement Parts
SECTION 9: Warranty

5200992 Rev F
2
(This page intentionally left blank)

5200992 Rev F
3
SECTION 1: Description
SIMCO’s PerforMAX IQ Static Neutralizing System consists of a high
voltage power supply, static neutralizing bar, and optional web monitor
and/or optional computer communication module. The PerforMAX IQ
static bar is available in three different types; tailored for high speed
processes, operating at a distance from the material or intermediate
(hybrid) applications. The PerforMAX IQ web monitor allows multiple
probes to measure web voltages and provide feedback to the system
enabling closed-loop operation of the static neutralizing process. The
PerforMAX IQ communication module provides the ability to remotely
monitor real time system performance and log operating data through a
computer interface.
The high voltage power supply module provides microprocessor
controlled high voltage DC output to the static bar. The high voltage
causes the ionizing pins on the static bar to generate positive and
negative ions. The electric field from the static charge on the material
being processed will attract opposite polarity ions from the static bar
causing the material to be neutralized. The excess ions will either
recombine in air or dissipate to ground.
The static neutralizing bar features current limiting at each individual ion
emitting pin to minimize the risk of hazardous electrical shock if the bar is
touched while in operation. This safety feature does not compromise the
PerforMAX IQ system’s ability to neutralize static charges. The emitter
pins are made of a special alloy to extend the longevity and sharpness of
the points, providing optimal performance of the static bar.
The PerforMAX IQ static bar is tailored to the application. Speed bars
are optimized to operate on high speed webs at distances of 50 to 230
millimeters [2 to 9 inches]. Hybrid bars operate at distances of 150 to
460 millimeters [6 to 18 inches] on webs where the web path is
somewhat variable. Distance bars are designed to operate from 300 to
760 millimeters [12 up to 30 inches] to the material. The variety of
PerforMAX IQ static bars offered allows the user to install the optimum
bar for their static neutralizing needs.
The PerforMAX IQ static bar has a plug-in style high voltage connector
for fast and easy installation. The connector features a pin that “tells”the
PerforMAX IQ power supply what type PerforMAX IQ bar is installed and
optimizes the power supply output for that type of bar.
The web monitor accepts the input from up to four remote web voltage
probes. When installed as part of the PerforMAX IQ system, the web

5200992 Rev F
4
monitor provides feedback on residual web voltages downstream of the
static neutralization bar and provides closed-loop control optimizing
system performance.
The communication module is designed as a port for an Anybus®
CompactCom module. This module provides interface with a wide
variety of standard industrial computer communication protocols allowing
easy integration of the PerforMAX IQ static neutralizing system with
existing networks. The communication module is also available without
the Anybus® port. These units are supplied with a USB adapter that
provides for connection to a personal computer and include software to
monitor and log data from the Performax IQ system.
All PerforMAX IQ optional modules use standard 8-conductor modular
cable and RJ-45 connectors for connection to the Performax IQ system..
They are supplied with 7 foot cable assemblies but longer custom cables
may be used.
Anybus® CompactCom is a registered trademark of HMS Industrial Networks.

5200992 Rev F
5
SECTION 2: Safety
SIMCO recommends that these instructions be read completely before
installation or operation is attempted. Failure to do so could result in
personal injury and/or damage to the equipment.
NOTE –Statements identified with NOTE indicate precautions
necessary to avoid potential equipment failure.
CAUTION –Statements identified with CAUTION indicate potential
safety hazards.
NOTE
This equipment must be correctly installed and properly
maintained. Adhere to the following notes for safe installation
and operation:
1. Read instruction manual before installing or operating
equipment.
2. Only qualified service personnel are to perform installation
and repairs.
3. All equipment must be properly grounded, including the
machine frame to which the equipment is mounted.
4. Disconnect input power to power supply before connecting
or disconnecting static neutralizing bars to the high voltage
power supply.
5. Do not operate system in close proximity to flammable
liquids.
CAUTION –This product is intended to be supplied by a Listed AC
Adapter or Power Unit marked "Class 2" or "LPS" and rated
output 24V DC, 3.75A.
CAUTION –Electrical Shock Hazard
Disconnect input power to high voltage power supply before
connecting or disconnecting static neutralizing bar or
performing any maintenance to the system. Avoid touching
static neutralizing bar when power supply is energized.
CAUTION –Fire Hazard
Do not install or operate static neutralizing bar in close
proximity to any flammable liquids or solvents.

5200992 Rev F
6
SECTION 3: Features
·Three types of PerforMAX IQ static neutralizing bars are available to
suit the specific application.
·Static bar disconnect plug pre-installed on static bar cable for quick
and easy installation. Plug also identifies bar type to power supply
automating power supply set-up.
·Single momentary push-button calibration simplifies set-up.
·Ionization emitter points current limited to enhance operator safety.
·Ionization emitter points of special alloy to extend operating life of
emitter points.
·Continuous “T”slot at back of static bar and mounting brackets for
easy and flexible installation.
·Bar graph display on power supply indicates ionizing performance of
system.
·Indicators on power supply display status of neutralizing system,
power, service required and detection of system faults.
·Relay contact output “echoes”indicators on power supply for remote
sensing and alarm.
·Optional web monitor provides feedback on web charge downstream
of static bar and enables closed-loop control of ionization system.
·Web monitor allows for multiple probe installation.
·Optional computer interface allows for remote monitoring and logging
of the system’s performance.

5200992 Rev F
7
SECTION 4: Specifications
4.1 High Voltage Power Supply
Input Power: 24 VDC, 1.5A from AC adapter
Output Voltage: BPS Basic Power Supply
+/-7kV “Speed Bar”
+/-9kV “Hybrid Bar”
+/-12kV “Distance Bar”
VLPS Voltage Limited Power Supply
+/-7kV “Speed Bar”
+/-8kV “Hybrid Bar”
+/-8kV “Distance Bar”
Dimensions: 202mmL x 123mmW x 106mmH
[7.95”L x 4.85”W x 4.17”H]
Weight: 1.94 kg [4.28 lb]
Max. Operating Temp: 43°C [110°F]
Housing: Aluminum, black epoxy powder coated
High Voltage Connectors: 2 proprietary PerforMAX IQ plug-in outlets
4.2 Static Neutralizing Bar
Nominal Bar Length: 301 to 3961mm Overall Length [11.8”to 156”]
210 to 3870mm Effective Length [8.27”to 152”]
Profile Dimensions: 24mmW x 38mmH [.94”W x 1.50”H]
Weight: 1.2 g/mm [.07 lb/in.)
Max. Operating Temp: 80°C [176°F]
Max. Humidity: 70% RH, no dewing permissible
Housing: Glass-fiber-reinforced polyester
HV Conduit: Flexible nylon tubing, black
Emitter Material: Proprietary alloy specially selected to extend life

5200992 Rev F
8
Emitter Spacing: Speed Bar –30mm [1.18”]
Hybrid Bar –90mm [3.54”]
Distance Bar –180mm [7.09”]
Operating Distance: Speed Bar –50mm to 230mm [2”to 9”]
Hybrid Bar –150mm to 460mm [6”to 18”]
Distance Bar –300mm to 760mm [12”to 30”]
Installation Hardware: Plastic mounting brackets, metal perforated
strips and stainless steel hardware (screws,
washers, nuts).
4.3 AC Adapter
Type “Universal”desktop
Input Power: 100 –240VAC 50/60Hz input
(IEC 60320 C6 inlet)
Output: 24VDC, 3.75A maximum
Dimensions: 132mmL x 60mmW x 34mmH
5.19”L x 2.36”W x 1.34”H]
Weight: 0.45 kg [1.0 lb]
Housing: Thermoplastic, black
4.4 Web Monitor
Input Power: 24VDC, 0.25A from PerforMAX IQ system
Probe Quantity: Total 4 probes maximum
Dimensions: 202mmL x 123mmW x 106mmH
[7.95”L x 4.85”W x 4.17”H]
Weight: 1.12 kg [2.48 lb]
Max. Operating Temp: 43°C [110°F]
Housing: Aluminum, black epoxy powder coated

5200992 Rev F
9
4.5 Web Probe
Operating Distance: 25mm [1”], 50mm [2”], 75mm [3”]
firmware selectable, default: 25mm [1”]
Installation Location: Downstream of static bar
Input Power: from PerforMAX IQ Web Monitor
Purge Connection: ¼”tube quick connect
Purge Flow: 0.14 m3/h [5 CFH] clean, dry air
Dimensions: 110mmL x 35mmW x 37mmH
[4.33”L x 1.38”W x 1.46”H]
Weight: 0.22 kg [0.48 lb]
Max. Operating Temp: 43°C [110°F]
Housing: Aluminum and Stainless Steel
Installation Hardware: Metal perforated strips and stainless steel
hardware (screws, washers, nuts).
4.6 Communication Module
Input Power: 24VDC, 1.0A from AC adapter
Communication Module: Anybus® CompactCom, see Replacement
Parts / Additional Items section for protocols
available (units with Anybus®)
USB Adapter: RS-485 isolated port (units without Anybus)
USB Compatibility: 1.0, 1.1, 2.0
Dimensions: 202mmL x 123mmW x 55mmH
[7.95”L x 4.85”W x 2.15”H]
Weight: 0.77 kg [1.70 lb]
Max. Operating Temp: 43°C [110°F]
Housing: Aluminum, black epoxy powder coated

5200992 Rev F
10
SECTION 5: Installation
Figure 5.1 PerforMAX IQ Static Bar Installation
Figure 5.2 PerforMAX IQ Static Bar Bracket

5200992 Rev F
11
Figure 5.3 PerforMAX IQ High Voltage Connector
Figure 5.4 PerforMAX IQ Web Monitor Probe Installation

5200992 Rev F
12
Figure 5.5 PerforMAX IQ Web Monitor Probe Bracket
Figure 5.6 PerforMAX IQ Connections
(Bar and Power Supply)

5200992 Rev F
13
Figure 5.7 PerforMAX IQ Connections
(Bar, Power Supply and Web Monitor)
Figure 5.8 PerforMAX IQ Connections
(Bar, Power Supply, Web Monitor and Communication Module)

5200992 Rev F
14
Figure 5.9 PerforMAX IQ Connections
(Power Supply to Power Supply)

5200992 Rev F
15
Figure 5.10 PerforMAX IQ Power Supply Alarm Output Connections
Pin Description Pin Description
1 Remote on/off
optocoupler (-) 10 Sensor Relay
(common)*
14 Remote on/off
optocoupler (+) 6 Sensor Relay (normal
closed)*
19 Sensor Relay (normally
open)*
2 Clean Bar Relay
(common)* 11 Power Relay
(common)*
3 Clean Bar Relay (norm
close)* 7 Power Relay (normal
closed)*
16 Clean Bar Relay (norm
open)* 20 Power Relay (normally
open)*
8 Fault Relay (common)*
4 Fault Relay (normally
closed)* 12 Power in (ground)**
17 Fault Relay (normally
open)* 24 Power in (ground)**
9 Bar On Relay
(common)* 13 Power in (+24VDC)**
5 Bar On Relay (normal
closed)* 25 Power in (+24VDC)**
18 Bar On Relay (normally
open)*
*30V 1A Rating on Contacts
**1.6A Rating, Connect pins 12 & 24 in parallel and 13 & 25 in parallel

5200992 Rev F
16
Remote On/Off
Disabled Normally Off
Opto High = Unit ON
Opto Low = Unit OFF
Normally On
Opto High = Unit OFF
Opto Low = Unit ON
Jumper Position at J3 for Remote Control Operation
Figure 5.11 PerforMAX IQ Web Monitor Remote Output Connections
Pin Description Pin Description
1 Power in (+24VDC) 8 Alarm Relay (common)
2 Power in (ground) 7 Alarm Relay (normally closed)
6 Power in (ground) 9 Alarm Relay (normally open)
4 Alarm Relay (common)
3 Alarm Relay (normally closed)
5 Alarm Relay (normally open)

5200992 Rev F
17
5.1 Initial Considerations
Installation starts with mounting of the static neutralizing bar. Static bars
are typically installed just ahead of where problems due to static are
occurring. The power supply is installed in a convenient location within
reach of the static bar high voltage cable and visible to the machine
operator. Web monitors (where used) are typically installed where
visible to the machine operator. The web monitor probes are supplied
with a generous amount of hook-up cable and are mounted downstream
of the static bar. Communication modules (where used) may be installed
at any convenient location and connected to the system using the
modular low voltage cable.
5.2 Mounting the Static Neutralizing Bar
CAUTION –Fire Hazard
Do not install or operate static neutralizing bar in close proximity to
any flammable liquids or solvents.
A. Determine location for mounting the static bar. The static bar will
typically be located just ahead of where problems due to static are
occurring. A static audit by a SIMCO representative can determine
the best location for the static bar.
B. The appropriate operating distance, “R”(see Static Bar Installation
diagram) for the PerforMAX static bar is in part determined by the
application:
Speed bars (emitter point spacing: 30mm) are mounted closer to
the web, 50 to 230 millimeters [2 to 9 inches] and may be installed in
more congested areas of the machine, however the web path should
be fixed for the speed bar. Optimum mounting distance for high
speed webs is 100mm [4 inches]. Speed bars can be identified by
an ion emitter to emitter spacing of 30mm [1.18 inches].
Hybrid bars (emitter point spacing: 90mm) are mounted at a
distance to the web, 150 to 460 millimeters [6 to 18 inches] and are
usually installed where the web path is relatively free of obstructions.
The benefit of hybrid bars is that they allow mounting where the web
path is variable. Hybrid bars can be identified by an ion emitter to
emitter spacing of 90mm [3.54 inches].
Distance bars (emitter point spacing: 180mm) are mounted at a
greater distance to the target surface, 300 to 760 millimeters [12 to
30 inches] and must be installed in areas free of obstructions.

5200992 Rev F
18
Operating at a greater range of distances makes distance bars best
suited for areas such as material roll wind-up applications. Distance
bars can be identified by an ion emitter to emitter spacing of 180mm
[7.09 inches].
PerforMAX bars should NOT be installed or operated at distances
less than the minimum distance specified for the particular bar.
The “free area”between the static bar and web should have
approximately equal height and width.
There should be NO grounded metal such as an idler roller
immediately behind the web on the far side from the static bar. The
area behind the static bar should be as free as possible from
grounded metal.
See Static Bar Installation diagram. The effectiveness of any static
bar is determined in part by the distance to and speed of the target.
If a static bar is not performing adequately at a given distance, it may
be necessary to reduce the operating distance accordingly.
C. The PerforMAX static bar includes blue plastic mounting brackets,
perforated metal strips and assorted hardware.
D. Slide the mounting brackets onto the “T”channel on the back of the
static bar.
E. The perforated strip may be installed on the mounting bracket at right
angle to the bar or parallel to the bar. The perforated strip may be
bent or twisted to suit the application and will hold its shape as
installed.
F. Once the static bar is loosely installed, tighten all hardware.
G. Install (2) set screws into the holes in the side of the mounting bracket
using the provided hex key wrench. The set screws engage the “T”
on the base of the bar securing it in place.
See Static Bar Bracket diagram.
5.3 Mounting the Power Supply
A. Locate power supply at a convenient place within reach of the static
bar high voltage cable and visible to the machine operator. Power for

5200992 Rev F
19
the AC adapter and an electrical ground connection must be
available.
B. Secure power supply to the mounting surface (commonly a machine
frame) using M5 or M4 [#10 or #8] hardware (not supplied).
C. Locate AC adapter at a convenient place within reach of the power
supply.
D. Install AC Adapter by cleaning back of adapter and mounting surface
with alcohol. Allow alcohol to dry. Secure AC adapter to mounting
surface with two self-adhesive mounting pads.
NOTE - Do not apply line voltage to the AC adapter until
installation is complete. Also ensure that all input power
switches are in the OFF (0) position.
5.4 Mounting the Web Monitor (optional)
A. Locate web monitor at a convenient place visible to the machine
operator and within reasonable distance to the power supply.
Standard modular cable (black) supplied with unit is 2.13 meters [7
feet] long, however longer cable (not supplied) may be used. .
Special cables fabricated for the web monitor must be 8-conductor
modular cables with RJ-45 connectors wired “crossover”(reference
color: black).
B. Secure web monitor to the mounting surface (commonly a machine
frame) using M5 or M4 [#10 or #8] hardware (not supplied).
C. Locate probe(s) at web, downstream of static bar (see Web Monitor
Probe installation diagram). In order to minimize undesirable
interaction between the static bar and probe; the distance between
the probe and static bar should be greater than the distance between
the static bar and web. Typically the probe will be located 0.3 meters
(12 inches) or greater distance from the static bar.
If multiple static bars are used in the PerforMAX IQ system with web
monitor, the bars must be used on the same web. In these cases, the
probe must be located downstream of the last static bar in the system.
D. The default probe mounting distance is 25mm [1”] from web. If static
charges are excessively high, it may be necessary to mount probe
50mm [2”] or 75mm [3”] from web. Operating distance calibration is
software selectable and may be set in the web monitor.

5200992 Rev F
20
The “free area”between the probe and web should have
approximately equal height and width.
There should be NO grounded metal immediately beneath the web on
the far side from the probe.
See Web Monitor Probe Installation diagram.
E. The PerforMAX web monitor probe includes perforated strips and
assorted hardware.
F. The probe may be mounted on the perforated strip with nuts and lock
washers included. The perforated strip may be bent or twisted to suit
the application and will hold its shape as installed. See Web Monitor
Probe Bracket diagram.
G. In dusty applications or applications with corrosive chemicals, purge
the probe. Connect ¼”OD plastic tubing to the quick connect fitting
on the side of the probe. Apply clean, dry air at a flow rate of 0.14
m3/h [5 CFH] to purge.
To regulate the clean, dry compressed air use a pressure regulator,
such as Norgren model R07-100-RGAA or equal with a flow meter
between the regulator and probe. The flow meter (with needle valve),
such as Key Instruments model MR 3A02-S-V-VT or equal, connects
to the probe. Set the pressure regulator to 34 kPa [5 psi] and adjust
the needle valve on the flow meter for 0.14 m3/h [5 CFH].
5.5 Mounting the Communication Module (optional)
A. Locate communication module at a convenient place within
reasonably close distance to the computer. Standard modular cable
(black) supplied with unit to connect the Communication Module to
the PerforMAX power supply is 2.13 meters [7 feet] long, however
longer cable (not supplied) may be used. Special cables fabricated
for the communication module must be 8-conductor modular cables
with RJ-45 connectors wired “crossover”(reference color: black).
To ensure communication between the communication module and
the computer, maximum recommended cable length between the
communication module and computer is 3 meters [10 feet] or less.
B. Secure communication module to the mounting surface (commonly a
machine frame) using M5 or M4 [#10 or #8] hardware (not supplied).
Table of contents
Other Simco Power Tools manuals
Popular Power Tools manuals by other brands
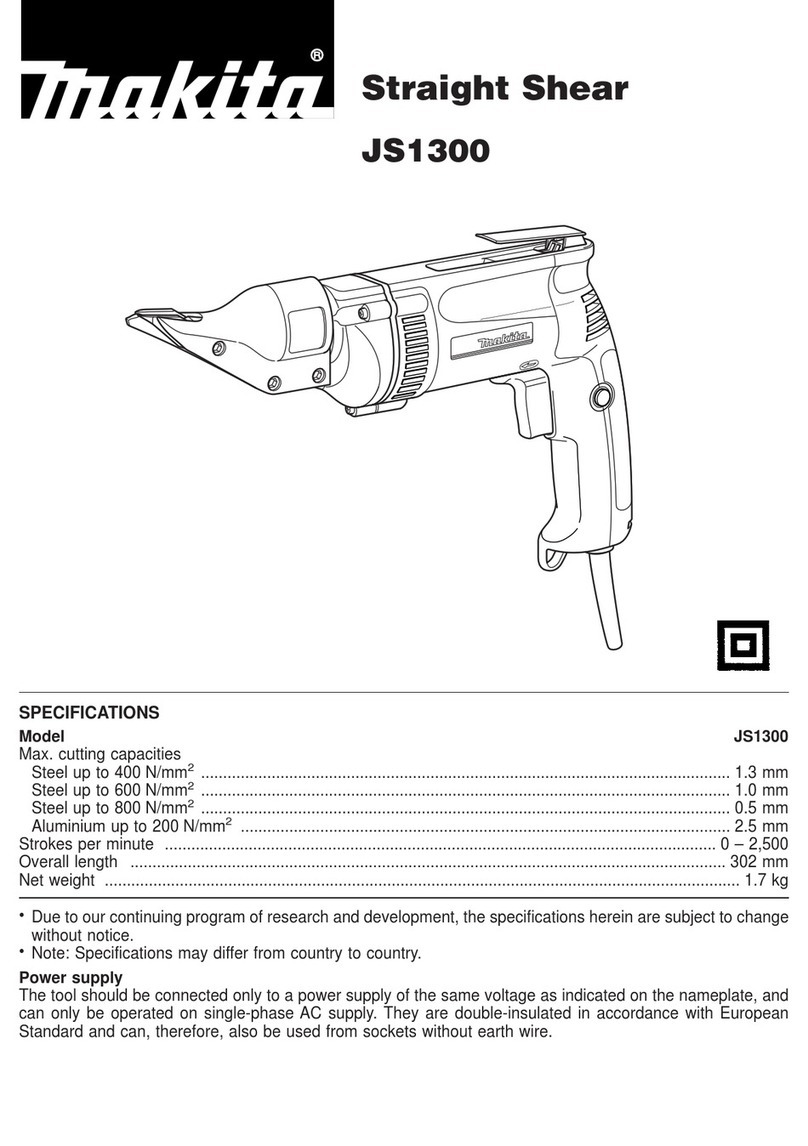
Makita
Makita JS1300 instructions

Brown Products
Brown Products Trench Master R450H Owner's/operator's manual
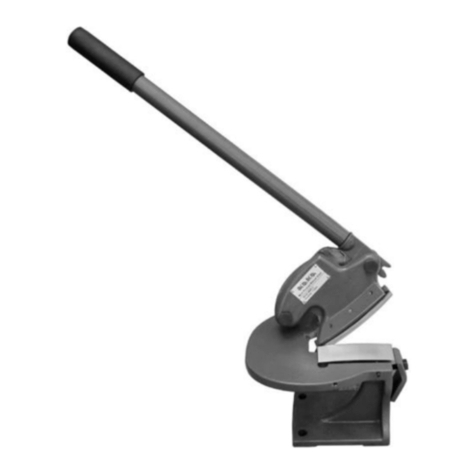
KAKA Industrial
KAKA Industrial MMS-4 Abbreviated operation manual
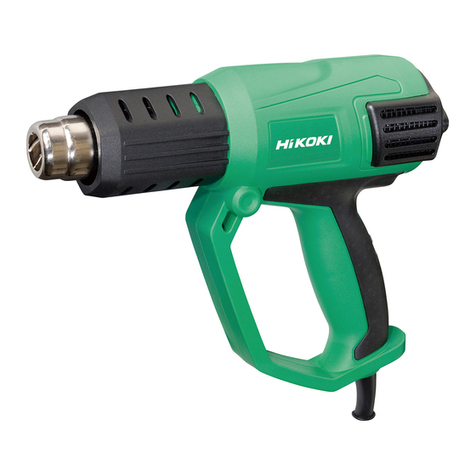
HIKOKI
HIKOKI RH 650V Handling instructions
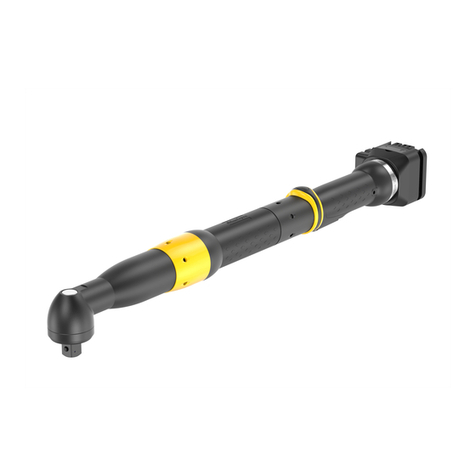
Atlas Copco
Atlas Copco ETV STB63-70-13-IRC-W Product instructions
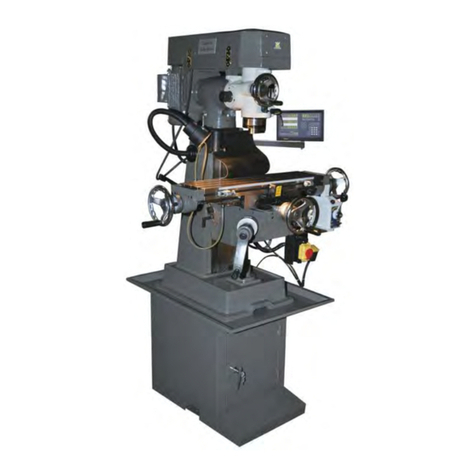
CHESTER
CHESTER 626 TURRET MILL Operation manual