Skope ProSpec Series User manual

ProSpec
SKOPE Top Mount Freezer
Hydrocarbon
Service Manual
MAN80368 Rev. 1.0 Aug. 2022

ProSpec
SKOPE Top Mount Freezer
Hydrocarbon
Service Manual
MAN80368
Rev. 1.0 Aug. 2022
© 2022 SKOPE Industries Limited. All rights reserved.
SKOPE Industries Limited reserve the right to alter specifications without notice.
is a registered trademark of SKOPE Industries Limited.
SKOPE INDUSTRIES LIMITED
Head Office
PO Box 1091, Christchurch
New Zealand
NZ: 0800 947 5673
E-mail: [email protected]
Website: www.skope.com
Trademark Infringement
The SKOPE trademark on this product is infringed if the owner, for the time being, does
any of the following:
• Applies the trade mark to the product after its state, condition, get-up or packaging
has been altered in any manner
• Alters, removes (including part removal) or obliterates (including part obliteration) the
trade mark on the product
• Applies any other trade mark to the product
• Adds to the product any written material that is likely to damage the reputation of the
trade mark
Notice of the above contractual obligations passes to:
• Successors or assignees of the buyer
• Future owners of the product

SKOPE ProSpec Upright Series Freezer
Service Manual iii
CONTENTS
1Servicing Hydrocarbon
Overview . . . . . . . . . . . . . . . . . . . . . . . . . . . . . . . . . . . . . . . . . . . . . . .5
SKOPE HC Service Requirements . . . . . . . . . . . . . . . . . . . . . . . . . . . 6
2Specifications
Models. . . . . . . . . . . . . . . . . . . . . . . . . . . . . . . . . . . . . . . . . . . . . . . . . 7
3Electronic Controller
Overview . . . . . . . . . . . . . . . . . . . . . . . . . . . . . . . . . . . . . . . . . . . . . . .8
Apps . . . . . . . . . . . . . . . . . . . . . . . . . . . . . . . . . . . . . . . . . . . . . . . . . .8
SCS Connect Field App . . . . . . . . . . . . . . . . . . . . . . . . . . . . . . . . . 8
SCS Connect Track App . . . . . . . . . . . . . . . . . . . . . . . . . . . . . . . . . 8
SKOPE Connect App . . . . . . . . . . . . . . . . . . . . . . . . . . . . . . . . . . . 8
Controller Faceplate . . . . . . . . . . . . . . . . . . . . . . . . . . . . . . . . . . . . . . 9
Buttons and Display . . . . . . . . . . . . . . . . . . . . . . . . . . . . . . . . . . . . 9
Service Mode . . . . . . . . . . . . . . . . . . . . . . . . . . . . . . . . . . . . . . . . .9
SCS Connect Field App. . . . . . . . . . . . . . . . . . . . . . . . . . . . . . . . . . . 10
Connecting . . . . . . . . . . . . . . . . . . . . . . . . . . . . . . . . . . . . . . . . . .10
App Menu Items . . . . . . . . . . . . . . . . . . . . . . . . . . . . . . . . . . . . . . 11
Faults and Alarms . . . . . . . . . . . . . . . . . . . . . . . . . . . . . . . . . . . . . . .12
4Wiring
Model: ProSpec 1 Door Freezer . . . . . . . . . . . . . . . . . . . . . . . . . .18
Model: ProSpec 2 Door Freezer . . . . . . . . . . . . . . . . . . . . . . . . . .20
5Spare Parts
Main Assembly – 1 Door Freezer . . . . . . . . . . . . . . . . . . . . . . . . . . .23
Main Assembly – 2 Door Freezer . . . . . . . . . . . . . . . . . . . . . . . . . . .24
Cabinet Assembly – 1 Door Cabinet . . . . . . . . . . . . . . . . . . . . . . . . .25
Cabinet Assembly – 2 Door Cabinet . . . . . . . . . . . . . . . . . . . . . . . . .26
Solid Door Assembly . . . . . . . . . . . . . . . . . . . . . . . . . . . . . . . . . . . . .27
Front Panel Assembly . . . . . . . . . . . . . . . . . . . . . . . . . . . . . . . . . . . . 28
1 Door Freezer Cartridge Assembly . . . . . . . . . . . . . . . . . . . . . . . . .29
2 Door Freezer Cartridge Assembly . . . . . . . . . . . . . . . . . . . . . . . . .31
Electronic Controller Assembly . . . . . . . . . . . . . . . . . . . . . . . . . . . . . 33
Electrics Junction Box Assembly. . . . . . . . . . . . . . . . . . . . . . . . . . . .34
6Installation
Installation Guidelines . . . . . . . . . . . . . . . . . . . . . . . . . . . . . . . . . . . .35
Ventilation Requirements . . . . . . . . . . . . . . . . . . . . . . . . . . . . . . . . . 36
Shelves . . . . . . . . . . . . . . . . . . . . . . . . . . . . . . . . . . . . . . . . . . . . . . . 37
Shelf Support Strips . . . . . . . . . . . . . . . . . . . . . . . . . . . . . . . . . . . 37
Repositioning Shelves. . . . . . . . . . . . . . . . . . . . . . . . . . . . . . . . . .37
7Operation
Loading Product . . . . . . . . . . . . . . . . . . . . . . . . . . . . . . . . . . . . . . . .38
Light Switch . . . . . . . . . . . . . . . . . . . . . . . . . . . . . . . . . . . . . . . . . . . .38
Refrigeration Cartridge Type Overview . . . . . . . . . . . . . . . . . . . . . . .39
Hot Gas Defrost . . . . . . . . . . . . . . . . . . . . . . . . . . . . . . . . . . . . . . 39
Refrigeration System Diagnostics – Function Test 1-Door Freezer . 40
Compressor and Inverter Information . . . . . . . . . . . . . . . . . . . . . . . .42
Inverter LED Indication . . . . . . . . . . . . . . . . . . . . . . . . . . . . . . . . . 42
Trouble-shooting . . . . . . . . . . . . . . . . . . . . . . . . . . . . . . . . . . . . . .42
Compressor. . . . . . . . . . . . . . . . . . . . . . . . . . . . . . . . . . . . . . . . . .42
Compressor Inverter . . . . . . . . . . . . . . . . . . . . . . . . . . . . . . . . . . . 43

SKOPE ProSpec Upright Series Freezer
Service Manual
iv
Refrigeration System Diagnostics – Function Test 2-Door Freezer . 45
Compressor. . . . . . . . . . . . . . . . . . . . . . . . . . . . . . . . . . . . . . . . . . . . 47
Compressor Electrical Supply Box . . . . . . . . . . . . . . . . . . . . . . . . 47
Compressor Connections . . . . . . . . . . . . . . . . . . . . . . . . . . . . . . . 47
Crankcase Pressure Regulator . . . . . . . . . . . . . . . . . . . . . . . . . . . 48
8Replacement Procedures
Refrigeration System. . . . . . . . . . . . . . . . . . . . . . . . . . . . . . . . . . . . . 49
Before Servicing . . . . . . . . . . . . . . . . . . . . . . . . . . . . . . . . . . . . . . 49
On-site Work . . . . . . . . . . . . . . . . . . . . . . . . . . . . . . . . . . . . . . . . . 50
Off-site Work . . . . . . . . . . . . . . . . . . . . . . . . . . . . . . . . . . . . . . . . . 50
Refrigeration Cartridge Assembly . . . . . . . . . . . . . . . . . . . . . . . . . 50
Not Cooling Fault . . . . . . . . . . . . . . . . . . . . . . . . . . . . . . . . . . . . . 51
Removing the Cartridge . . . . . . . . . . . . . . . . . . . . . . . . . . . . . . . . 51
Replacing the Cartridge . . . . . . . . . . . . . . . . . . . . . . . . . . . . . . . . 53
Cartridge Electrics Box Assembly. . . . . . . . . . . . . . . . . . . . . . . . . 53
Cartridge Cover Label. . . . . . . . . . . . . . . . . . . . . . . . . . . . . . . . . . 54
Cartridge Cover. . . . . . . . . . . . . . . . . . . . . . . . . . . . . . . . . . . . . . . 54
Condenser Fan . . . . . . . . . . . . . . . . . . . . . . . . . . . . . . . . . . . . . . . 54
Evaporator Fan . . . . . . . . . . . . . . . . . . . . . . . . . . . . . . . . . . . . . . . 56
Replacing the Controller . . . . . . . . . . . . . . . . . . . . . . . . . . . . . . . . 57
Door Switch. . . . . . . . . . . . . . . . . . . . . . . . . . . . . . . . . . . . . . . . . . 59
Control Probe . . . . . . . . . . . . . . . . . . . . . . . . . . . . . . . . . . . . . . . . 59
Evaporator Probe . . . . . . . . . . . . . . . . . . . . . . . . . . . . . . . . . . . . . 60
Condenser Probe . . . . . . . . . . . . . . . . . . . . . . . . . . . . . . . . . . . . . 61
Ambient Probe . . . . . . . . . . . . . . . . . . . . . . . . . . . . . . . . . . . . . . . 62
Replacing Component Notes . . . . . . . . . . . . . . . . . . . . . . . . . . . . 63
Isolating Electrics . . . . . . . . . . . . . . . . . . . . . . . . . . . . . . . . . . . . . . . 64
Lighting . . . . . . . . . . . . . . . . . . . . . . . . . . . . . . . . . . . . . . . . . . . . . . . 64
Doors. . . . . . . . . . . . . . . . . . . . . . . . . . . . . . . . . . . . . . . . . . . . . . . . . 68
Alignment Adjustment . . . . . . . . . . . . . . . . . . . . . . . . . . . . . . . . . . 68
Replacing the Gasket . . . . . . . . . . . . . . . . . . . . . . . . . . . . . . . . . . 68
Removing and Refitting the Door . . . . . . . . . . . . . . . . . . . . . . . . . 68
Replacing the Capstan . . . . . . . . . . . . . . . . . . . . . . . . . . . . . . . . . 69
Cleaning . . . . . . . . . . . . . . . . . . . . . . . . . . . . . . . . . . . . . . . . . . . . . . 70
Cabinet . . . . . . . . . . . . . . . . . . . . . . . . . . . . . . . . . . . . . . . . . . . . . 70
Condenser Coil . . . . . . . . . . . . . . . . . . . . . . . . . . . . . . . . . . . . . . . 70
9Troubleshooting
Electronic Controller . . . . . . . . . . . . . . . . . . . . . . . . . . . . . . . . . . . . . 71
Cabinet and Refrigeration Cartridge . . . . . . . . . . . . . . . . . . . . . . . . . 71
Probe Resistance . . . . . . . . . . . . . . . . . . . . . . . . . . . . . . . . . . . . . . . 74
On-site work procedure by authorised service person . . . . . . . . . . . 76

5
SKOPE ProSpec Upright Series Freezer
Servicing Hydrocarbon
Service Manual
1 Servicing Hydrocarbon
Overview
This cabinet uses hydrocarbon (HC) R290 as its refrigerant. R290 is a natural refrigerant that
has a very low environmental impact.
Special service requirements are needed, as R290 is a flammable refrigerant.
Safety hazards
The main hydrocarbon safety hazards are:
• Flammability
• Venting of hydrocarbon and compressor oil
• Asphyxiation
Service requirements
Do not interfere with the refrigeration system. All refrigeration maintenance and repairs must
be undertaken according to the SKOPE HC Service Requirements. See the “SKOPE HC
Service Requirements” below for more information, including examples of hazardous
activities.
Electrical safety precautions
Correct wiring routing is as important as using correct components for compliance with safety
and radio interference regulations. In order to maintain safety and compliance with regulations,
any wiring that is disturbed during servicing must be replaced and secured in its original
position.

6Servicing Hydrocarbon
Service Manual
SKOPE ProSpec Upright Series Freezer
SKOPE HC Service Requirements
Servicing must only be performed by Approved SKOPE Service Technicians, and must meet all requirements in the SKOPE HC
Service Policy (available from SKOPE), including the following:
Hydrocarbon work – SKOPE Service Policy
It is the responsibility of the service technician to follow SKOPE’s Hydrocarbon equipment service policy
and by accepting a service work order they agree to the following (where applicable):
xMUST – Ensure all workers are trained in the SAFETY of hydrocarbon products to the appropriate
level for the work required.
xMUST – Follow all Local Safety Regulations relevant to flammable refrigerant gases.
oAustralia should reference - AIRAH Flammable Refrigerants – Safety Guide
oNew Zealand should reference – Flammable Refrigerant Safety Documentation
(Refrigerant License NZ)
xMUST – Adhere to all on-site (workplace) Health and Safety requirements
xMUST – Not modify or alter the design of SKOPE equipment in any way
xMUST – In cases where the refrigeration system is not readily removable from the cabinet; then the
entire cabinet MUST be sent to the Hydrocarbon workshop for repair.
xMUST – ONLY use SKOPE OEM Spare Parts; or identical replacement parts. Any variation in
replacement part may render the system non-compliant and unsafe.
xMUST – Follow all best practice work activities for servicing hydrocarbon refrigerants (SKOPE
recommend attending specific hydrocarbon refrigeration handling training courses). Nitrogen must
be used for purging system before commencing “Hot Work” – brazing.
xMUST – Adhere to relevant SKOPE Service Manual. If any contradiction, the local Regulations take
precedence over SKOPE requirements
xMUST – Work only in suitable, safe and compliant work spaces. Personal Protective Equipment
must always be used when working on Hydrocarbon equipment.
xMUST – Service people diagnosing refrigeration faults must always carry and utilise Flammable Gas
detectors when working on Hydrocarbon equipment.
xMUST – Prior to any service work; know where and how to safely and quickly isolate power supply
to cabinet
xMUST – Not perform any Hot Work (brazing etc.) in the field. These are to be completed in a suitable
service depot / workshop (in a dedicated specific Hazardous Work Area compliant to local
flammable gas regulations)
xMUST – Not transport a refrigeration system with a known active leak. If there is an active leak the
refrigerant must be safely removed (with use of Bullet Piercing Valve or Line Tap valves) before
transporting. Valves must be removed at the hydrocarbon service depot once repair is completed.
xMUST – All hydrocarbon workshop areas must have emergency plans; that includes suitable
evacuation and fire control plans and equipment.
xMUST – Only use refrigerant grade hydrocarbon, to precise mass specified on removable
refrigeration system serial label.
xMUST – Be accurate refrigerant charge; The refrigerant mass is ultra-low charge and must only be
measured in by accurate scales to +/- 1.0gram. Refrigerant MUST not be overcharged; or added to
an already charged system.
xMUST – Use identical drier replacement; as any change will affect gas charge volume; and effect
reliability compliance and safety.
xMUST – Any pipework replacement, must be identical to genuine SKOPE parts.
xMUST – Not introduce a sparking device inside a cabinet or inside a removable refrigeration system.
Battery drills should not be used.
xMUST – Not perform any activity that could stress a refrigeration pipe (unless in a workshop).
xMUST – Get customer authorisation to permanently swap a removable refrigeration system.
xMUST – Have the Wellington Drive SCS Field app installed on a Bluetooth enabled device carried by
the service technician (exception is for cabinets that do not utilise the Wellington Drive Controller).
The app should be utilised for safe, accurate diagnosis of the system and it is required to complete
a controller replacement in the field.
xRECOMMENDED – Have the Wellington Drive SCS Track app installed on a Bluetooth enabled device
carried by the service technician. This passive app collects system data from the Wellington Drive
SCS Connect Controller and transmit it to the cloud.
xLogistics companies may be used to transport a complete refrigerator where no separation of the
refrigeration system occurs. Logistics companies are not required to be contracted to this SKOPE
Service Policy.

7
SKOPE ProSpec Upright Series Freezer
Specifications
Service Manual
2 Specifications
Models
This product service manual is applicable to the SKOPE ProSpec top mount upright freezers
detailed in the table below. Refer to the relevant product specification sheet (available on the
SKOPE website: www.skope.com) for specifications.
Series Model SKOPE ID Unit
ProSpec Freezer Series PG21.UPF.1.SD PP1F UTHDNI-0043
PG21.UPF.2.SD PP2F UTHDNI-0051

8Electronic Controller
Service Manual
SKOPE ProSpec Upright Series Freezer
3 Electronic Controller
Overview
The product is fitted with a Wellington Drive SCS Connect electronic controller. The controller
is located above the door/s and visible from the outside of the cabinet.
Controller servicing can be performed via the controller faceplate, or the SCS Connect Field
app.
This does not control the cabinet body and door heater elements
Apps
SCS Connect
Field App The SCS Connect Field app is designed for service techs, and provides access to the
controller from mobile devices with Bluetooth capability. The app provides information on data
logging, alarm notification and diagnostic control.
See “SCS Connect Field App” on page 10 for information on setting up and using the app.
SCS Connect
Track App The SCS Connect Track app is used to upload data from cabinets fitted with a Wellington SCS
Connect electronic controller.
SKOPE
Connect App The SKOPE-connect app is designed for end-users and provides wireless access to the
controller from mobile devices with Bluetooth capability.
The app allows end users to adjust some electronic controller settings including energy saving
modes, open/close hours and preset temperature set points for specific product.
The app may be useful for diagnostics. Download from the Google Play Store, or Apple App
Store.
Apple App
store
Google Play
store

9
SKOPE ProSpec Upright Series Freezer
Electronic Controller
Service Manual
Controller Faceplate
Buttons and
Display The faceplate includes the front display panel and interface buttons.
12 3 4 5
8 7
11
10
96
Table 1: Controller Faceplate
No. Description Use
1Night Mode Indicator On during night mode.
2Display Indicator
Digital display of:
• the cabinet’s air (not product)
temperature.
• alarm messages.
3Light Switch - Night Mode
(back/abort) Button Used during programming.
Press to switch the lights on or off.
Press and hold to switch the fridge
between Day and Night modes.
4Up Button Used during programming.
5Bluetooth Indicator On when ready to connect to a device.
Flashing when connected to a device.
6Defrost Cycle (next/enter) Button Used during programming. Press and hold to start a manual
defrost.
7Down Button Used during programming.
8Fault - Alarm Indicator On during a fault or alarm.
9Compressor Indicator On when the compressor is running.
10 Defrost Mode Indicator On during the defrost cycle.
11 Fan Indicator On when the fans are running.
Service Mode Service mode can be accessed and used via the SCS Connect Field app (see “SCS Connect
Field App” on page 10), or the controller faceplate (see below).
Note: A 9 digit pin code is required to access service mode via the controller buttons. Contact
your User Manager to receive your activation code.
Procedure 1: To enable and use service mode via the controller faceplate
1. Press and hold the up and down buttons simultaneously until prompted to enter the 9 digit pin
code.
2. Enter service mode pin code.
3. Use the up, down, back/abort and next/enter buttons to navigate to the desired category.

10 Electronic Controller
Service Manual
SKOPE ProSpec Upright Series Freezer
There are 5 main service mode categories when accessing and using service mode via the
controller faceplate:
Parameters
Provides access and editing of individual controller parameters.
It is not recommended that parameters are changed unless absolutely necessary. If incorrect
parameter settings are suspected, reload the complete parameter set.
Reset
Returns the controller back to factory settings. Parameter set must be reloaded after
performing a reset.
Manual test
Allows inspection of input values from sensors, and check the effects of output adjustments to
peripherals, and to run preset test routines.
Statistics
Displays logged values and event counts to assist with fine tuning and diagnostics.
About
Lists the properties of the refrigeration system and the controller, including cooler model
codes, firmware, hardware and software versions.
SCS Connect Field App
Connecting The SCS Connect Field app gives authorised service technicians wireless access to the
controller from mobile devices with Bluetooth capability. The app provides data logging, alarm
notification, and control over inputs (probes, switches) and outputs (e.g. relays).
Procedure 2: To install the SCS Connect Field app
Before you start
When you first run the app, you will need to enter an activation code – a 9-digit PIN. If you don’t
already have one, contact SKOPE Customer Services to request an activation code. You will need to
be connected to the internet at the time of activation.
Your activation code is unique to you, and determines your personal level of access for the app. Never
share it with anyone else. The same code will give you access to all SCS apps you are authorised to
use.
1. Download and install the Connect Field app
• Apple App Store:
https://apps.apple.com/nz/app/scs-connect-field/id1172570106
• Google Play Store:
https://play.google.com/store/apps/details?id=air.com.wdtl.scs.diagnostic.mobile
2. Make sure you are connected to the internet, and enter your 9-digit activation code.

11
SKOPE ProSpec Upright Series Freezer
Electronic Controller
Service Manual
App Menu
Items You can find information and make changes to the connected controller and its fridge via the
app menu.
Home screen
Shows a graphic representation of the fridge being controlled.
3. Once activation is complete, you must define a 4-digit PIN. This can be any code unique to you.
Each time you start the app, you will be required to enter this same PIN. This is to prevent other
people accessing the app from an unlocked phone.
Procedure 3: To connect to a controller
1. Check that the Bluetooth logo on the top right of the controller faceplate is unlit, indicating that the
controller is ready to connect to a device.
Note: Aflashing Bluetooth logo indicates that the controller is currently connected to a device.
2. Open the SCS Connect Field app.
3. Select the controller from the list of visible controllers.
Note: This list is filtered by your activation permissions, so devices you are not authorised to
connect to will not be displayed.
4. Select “CONNECT” to connect to the controller.
5. Check that the Bluetooth logo on the top right of the controller faceplate is flashing, indicating that
the controller is connected.
Procedure 2: To install the SCS Connect Field app (continued)
Table 2: SCS Connect Field App Home Screen
Item Description Action
Output control Gives you control of the input sensors and switches,
and output relays.
Edit parameters
Allows you to access and edit individual controller
parameters.
SKOPE does not recommended changing
parameters unless absolutely necessary.
If you edit a parameter, you must:
• select “DISCONNECT” from the menu to apply
the updated parameter.
• record the changes on the warranty/job card.
Load parameter file
Allows you to reload a default parameter set or
change to new parameter set.
SKOPE does not recommended changing
parameters unless absolutely necessary.
1. If you suspect an incorrect parameter setting,
reload the complete parameter set.
2. After loading the new parameter set, select
“DISCONNECT” from the menu to apply the
updated parameters.

12 Electronic Controller
Service Manual
SKOPE ProSpec Upright Series Freezer
Faults and Alarms
If a fault occurs, it is logged, the Fault - Alarm indicator is lit on the controller faceplate, and a
message may be displayed. Faults do not affect product temperature, and do not require
action from the shop owner, unless they turn into an alarm.
If an alarm occurs, it is logged, the Fault - Alarm indicator is lit, and the alarm message is
displayed on the controller faceplate. Alarms may result in abnormal product temperature.
Some faults and alarms can be cleared by the shop owner, and others can only be cleared by
a service technician. Faults and alarms can be cleared by the shop owner by power-cycling
the cabinet. However the fault or alarm will only clear if the problem has been fixed. If the
problem still exists after a power-cycle, a service technician will need to fix the problem.
Statistics
Displays information from the past seven days about
the fridge's activity, including temperatures, door
openings and alarms.
SCS info Displays information about the cabinet and the
controller version.
SCS setup Allows you to add or change SCS info (see above).
Disconnect Allows you to disconnect from the currently
connected controller.
Settings
Allows you to change the app's general settings and
see which databases you have activated. You can
have more than one database activated at the same
time.
To add a new database, select ACTIVATE
ANOTHER DATABASE, and enter the new
database's unique activation code.
Table 3: ProSpec parameter numbers
Model Parameter number
ProSpec Freezer Series PG21.UPF.1.SD 629
PG21.UPF.2.SD 630
Table 2: SCS Connect Field App Home Screen (continued)
Item Description Action
Table 4: Faults
Description Possible root cause Actions
Over-voltage protection
The maximum allowable mains supply
voltage has been exceeded. The
cabinet has temporarily shut down to
prevent damage and will restart once
the supply voltage decreases.
Should be a one-off. If it
continues, consider:
• poor line voltage Test the incoming voltage to ensure it is correct.
The test voltage needs to be between 198 and 264
volts.
• If outside this, the controller will shut the system
down until the voltage returns to between these
measurements.
• If the voltage is correct and the controller is still
showing a fault, replace the controller.
• rural location
• voltage setting parameter • Check the voltage parameter settings are
between 198 and 264 volts. If this parameter is
outside the correct voltage, changing it may
damage the controller.
• controller • The controller may be reading incorrectly and
need replacing.

13
SKOPE ProSpec Upright Series Freezer
Electronic Controller
Service Manual
Under-voltage protection
The mains supply voltage has dropped
below the minimum allowable level.
The cabinet has temporarily shut down
to prevent damage and will restart
once the supply voltage increases.
Should be a one-off. If continues,
consider:
• power supply overloaded Test the incoming voltage to ensure it is correct.
The test voltage needs to be between 198 and 264
volts.
• If outside this, the controller will shut the system
down until the voltage returns to between these
measurements.
• If the voltage is correct and the controller is still
showing a fault, replace the controller.
• poor line voltage
• multi-box use • Check that there are not too many plugs using the
same multi-box adaptor causing the voltage to
drop.
• rural location
• voltage setting parameter • Check the voltage parameter settings are
between 198 and 264 volts. If this parameter is
outside the correct voltage, changing it may
damage the controller.
• controller • The controller may be reading incorrectly and
need replacing.
High condensing temperature
protection
The system was operating at an
elevated temperature and has
temporarily shut down to prevent
damage. Extended operation in this
condition may result in ALARM 15,
increased energy consumption and a
reduction in cabinet life.
Cartridge swap is not required.
• Condenser not clean • Remove and clean the condenser filter.
• Check that the condenser is free of debris.
• If the coil is dirty, clean it with a vacuum cleaner or
soft brush.
• Poor installation or ventilation • Check the installation guidelines.
• If fitted, check the rear stand-offs are extended.
• Condenser fan motor or blade • Check that the condenser fan blades are in place
and all condenser fans are operating correctly.
• Controller The controller may be reading incorrectly and
need replacing.
• Confirm the temperature reading with an
independent thermometer.
• Very high ambient temperature • Check if the probes are faulty and reading
incorrectly.
• Door not self-closing • Open the door and let it go. If it does not close on
its own, repair the self-closing mechanism.
Excessive compressor cycling
protection
The system has been turning on and
off too frequently.
• Blocked condenser • Remove and clean the condenser filter.
• Check that the condenser is free of debris.
• If the coil is dirty, clean it with a vacuum cleaner or
soft brush.
• Poor installation or ventilation • Check the installation guidelines.
• Cartridge or cabinet gasket
seals leaking
• Remove the cartridge and check the integrity of
the gaskets and seals.
• If required, replace the door gasket.
• Hot product • Check if the product has been recently loaded,
and is causing the extra heat.
• Product blocking cabinet airflow • Check if the return air grille is covered by product.
If so, move the product from the grille and
observe.
• Compressor is overloaded from
excess door openings or
ambient temperature
• Ensure that the cabinet is operating in its climate
class.
• Condenser or evaporator fan
motor or blade
• Inspect the condenser and evaporator fans safely,
and replace if faulty.
• Controller • The controller may be reading incorrectly and
need replacing.
• Compressor or gas leak • Swap the cartridge.
Table 4: Faults (continued)
Description Possible root cause Actions

14 Electronic Controller
Service Manual
SKOPE ProSpec Upright Series Freezer
Table 5: Alarms
Code Description Possible root cause Action
8
Estimated product
temperature below
allowable range
The estimated product
temperature has been below
the allowable range for longer
than the permissible time.
• Low ambient temperature • Ensure that the cabinet is operating in its climate
class.
• App settings • Check all app settings, and reinstall the
parameters if required.
• Controller • Check the probe calibration to make sure that the
controller is reading the temperature correctly.
• Excessive door openings
• Door being left open
• Door leaking air (bad gasket or
door not self-closing)
• Open the door and let it go. If it does not close on
its own, repair the self-closing mechanism.
• If required, replace the door gasket.
9
Estimated product
temperature above
allowable range
The estimated product
temperature has been above
the allowable range for longer
than the permissible time.
• Sealed refrigeration system • Consider a cartridge swap.
• Incorrect setpoint • Reload the correct parameters using the SCS
Connect Field app.
• Too much product • If the cabinet is overloaded, remove the excess
product.
• Blocked return air grille • Check if the return air grille is covered by product.
If so, move the product from the grille and
observe.
• Warm product loaded into
cabinet
• Blocked condenser • Remove and clean the condenser filter.
• Check that the condenser is free of debris.
• If the coil is dirty, clean it with a vacuum cleaner or
soft brush.
• Poor installation or ventilation • Check the installation guidelines.
• Frozen or blocked evaporator
coil
• De-ice the coil and check the that evaporator fan
motor is working.
• Check the defrost cycle and that the defrost probe
are working correctly.
• Check that the drain is clear.
• Cartridge gasket leaking (to
cabinet seal or lid seal)
• Check that the gasket is intact and not broken
and leaking.
• Ensure the installation levers are lifting the
cartridge up onto the case correctly.
• Compressor is overloaded from
excess door openings or
ambient temperature
• Ensure that the cabinet is operating in its climate
class.
• Condenser or evaporator fan
motor or blade
• Inspect the condenser and evaporator fans safely,
and replace if faulty.
• Incorrect parameter settings • Use the SCS Field app to check that the correct
setpoint and parameters have been selected.
• Controller • Check the probe calibration to make sure that the
controller is reading the temperature correctly.
• Compressor or gas leak • Swap the cartridge.

15
SKOPE ProSpec Upright Series Freezer
Electronic Controller
Service Manual
15
Excessive condensing
temperature protection
The system was operating at an
excessive temperature and has
shut down to prevent
permanent damage.
Cartridge swap is not required.
• Very high ambient temperature • Ensure that the cabinet is operating in its climate
class.
• Condenser is not clean • Remove and clean the condenser filter.
• Check that the condenser is free of debris.
• If the coil is dirty, clean it with a vacuum cleaner or
soft brush.
• Poor installation or ventilation • Check the installation guidelines.
• Condenser fan motor or blade • Inspect the condenser and evaporator fans safely,
and replace if faulty.
• Incorrectly placed condenser
probe
• Either:
• Measure the probe resistance to make sure it
is within the range.
• Compare the probe’s temperature with the
known temperature, using an external trusted
thermometer.
• Replace the probe if required.
17
Control probe failure
A critical system sensor has
failed and the cabinet can no
longer operate.
Cartridge swap is not required.
• Control probe or circuit • Either:
• Measure the probe resistance to make sure it
is within the range.
• Compare the probe’s temperature with the
known temperature, using an external trusted
thermometer.
• Replace the probe if required.
• Controller • If you have replaced the probe and it is still
reading incorrectly, replace the controller.
18
Electrical over-current
protection activated
The compressor was drawing
too much current and has shut
down to prevent permanent
damage.
• Blocked condenser • Remove and clean the condenser filter.
• Check that the condenser is free of debris.
• If the coil is dirty, clean it with a vacuum cleaner or
soft brush.
• Product blocking cabinet airflow • Check if the return air grille is covered by product.
If so, move the product from the grille and
observe.
• Compressor is overloaded from
excess door openings or
ambient temperature
• Ensure that the cabinet is operating in its climate
class.
• Compressor or gas leak • Swap the cartridge.
Table 5: Alarms (continued)
Code Description Possible root cause Action

16 Electronic Controller
Service Manual
SKOPE ProSpec Upright Series Freezer
19
Failed to reach set
temperature
The refrigeration system has
been operating continuously for
a long period without reaching
the set temperature.
• Blocked condenser • Remove and clean the condenser filter.
• Check that the condenser is free of debris.
• If the coil is dirty, clean it with a vacuum cleaner or
soft brush.
• Poor installation or ventilation • Check the installation guidelines.
• Frozen or blocked evaporator
coil
• De-ice the coil and check the that evaporator fan
motor is working.
• Check the defrost cycle and that the defrost probe
is working correctly.
• Cartridge, cabinet, or door
gasket leaking
• Check that the gasket is intact and not broken
and leaking. If required, replace the door gasket.
• Ensure the installation levers are lifting the
cartridge up onto the case correctly.
• Product blocking cabinet airflow • Check if the return air grille is covered by product.
If so, move the product from the grille and
observe.
• Compressor is overloaded from
excess door openings or
ambient temperature
• Ensure that the cabinet is operating in its climate
class.
• Condenser or evaporator fan
motor or blade
• Inspect the condenser and evaporator fans safely,
and replace if faulty.
• Controller • The controller may be reading incorrectly and
need replacing.
• Compressor or gas leak • Swap the cartridge.
20
Over-cooling product
The internal temperature is too
low. The system has
temporarily shut down until the
temperature has returned to
normal.
• Set temperature has been
raised by a large amount
1. Confirm if really too cold.
2. Change parameters accordingly.
• Controller • The controller may be reading incorrectly and
need replacing.
22 Evaporator fan over-current
protection
The current supplied to the
evaporator fan motor is too
high.
• Faulty fan motor • Replace the fan motor.
• Fan blade fault (imbalance,
debris, blockage)
• Visually inspect the fan blades and replace if
faulty.
23
Condenser fan over-current
protection
The current supplied to the
condenser fan motor is too
high.
• Faulty fan motor • Replace fan motor.
• Fan blade fault (imbalance,
debris, blockage)
• If the fan motor is working correctly, update the
controller firmware to the latest version.
• Controller • The controller may be reading incorrectly and
need replacing.
24
Controller communication
error
Controller has lost
communication channels.
• Parameters • Load the correct parameter settings.
• Controller or circuit • The controller may be reading incorrectly and
need replacing.
25
Controller update failed
Controller update could not be
completed.
• Parameters • Load the correct parameter settings.
• Controller or circuit • The controller may be reading incorrectly and
need replacing.
26 Controller hardware failure
Controller hardware has failed.
• Parameters • Load the correct parameter settings.
• Controller or circuit • Replace the controller.
Table 5: Alarms (continued)
Code Description Possible root cause Action

17
SKOPE ProSpec Upright Series Freezer
Electronic Controller
Service Manual
27
Probe failure
A probe other than the control
probe has failed. The cabinet
will continue to operate with
partial function but requires
service.
Cartridge swap is not required.
• Evaporator probe or
connections
• Either:
• Measure the probe resistance to make sure it
is within the range.
• Compare the probe’s temperature with the
known temperature, using an external trusted
thermometer.
• Replace the probe if required.
• Controller • The controller may be reading incorrectly and
need replacing.
28
No downward tendency
The temperature is no longer
decreasing.
• Blocked condenser • Remove and clean the condenser filter.
• Check that the condenser is free of debris.
• If the coil is dirty, clean it with a vacuum cleaner or
soft brush.
• Poor installation or ventilation • Check the installation guidelines.
• Cartridge or cabinet gasket
seals leaking
• Check that the gasket is intact and not broken
and leaking. If required, replace the door gasket.
• Ensure the installation levers are lifting the
cartridge up onto the case correctly.
• Door not self-closing or door
gasket leaking
• Open the door and let it go. If it does not close on
its own, repair the self-closing mechanism.
• If required, replace the door gasket.
• Product blocking cabinet airflow • Check if the return air grille is covered by product.
If so, move the product from the grille and
observe.
• Compressor is overloaded from
excess door openings or
ambient temperature
• Ensure that the cabinet is operating in its climate
class.
• Condenser or evaporator fan
motor or blade
• Inspect the condenser and evaporator fans safely,
and replace if faulty.
• Controller • The controller may be reading incorrectly and
need replacing.
• Compressor or gas leak • Swap the cartridge.
• Door not self-closing or door
gasket leaking
• Open the door and let it go. If it does not close on
its own, repair the self-closing mechanism.
• If required, replace the door gasket.
30
Excessive automatic
defrosting
The system is automatically
defrosting too frequently.
• Evaporator probe Either:
• Measure the probe resistance to make sure it is
within the range.
• Compare the probe’s temperature with the known
temperature, using an external trusted
thermometer.
• Evaporator motor or fan • Check that the fan motors are working and the fan
blades are not damaged.
• Controller • The controller may be reading incorrectly and
need replacing.
• Blocked drain • Clear the blockage with a wet vacuum.
• Clear the debris to prevent a blockage.
• Defrost setting too high • Reload the correct parameters using the SCS
Connect Field app.
• Compressor or gas leak • Swap the cartridge.
Table 5: Alarms (continued)
Code Description Possible root cause Action

18 Wiring
Service Manual
SKOPE ProSpec Upright Series Freezer
4 Wiring
Model: ProSpec 1 Door Freezer
BU
S18-2 P18-2
P6-1 S6-1
P3-1 S3-1
P3-4 S3-4
P6-4 S6-4
BN
BU
BN
S21-4 P21-4
S21-2 P21-2
Condenser Fan
BN
S18-4 P18-4
Evaporator Fan
BU
BU
BU
S2-1 P2-1
S2-2 P2-2
S2-3 P2-3
S2-5 P2-5
BK
BK
OG
BKBK
BK
BK
BK
Control
Probe
Evaporator
Probe
BN
L
BU
N
BN BU
T1-2
GNYE
E
EMC Filter
BU
BN
P17-2 S17-2
S6-2 P6-2
WDTL
SCS
Controller
L N
C
R
R
SSR
S1
S2
SSR
Comp.
0V
+
1
2
3
AD5
DI1
0V AD1
DI2
0V AD2
DI3
0V AD3
DI4
5V
0V
AD4
BK
BK
BN BU
P3-2 S3-2
S19-2 P19-2
S19-4 P19-4
BN
BK
BK
RD
BN
WH
S4-2 P4-2
BN
P18-1 S18-1
BU
BU
P21-1 S21-1
P19-1 S19-1
BU
BN
WH
RD
Door Switc h
BK
BK
Condenser
Probe
P17-1 S17-1
P16-1 S16-1
P16-2 S16-2
P20-2 S20-2
P20-1 S20-1
S23-4
S23-1
S23-3
P22-1 S22-1
BK
BK
P22-2 S22-2
BK
P7-2 S7-2
S2-4 P2-4
RD
BU
BU
WH
P7-1 S7-1
WH
BK
WH
RD
Ambient
Probe
RD
BK
Programming
Port
BN
BN
BK
BU GNS
BN GNS
BK GNS
BK
OG
S15-2 P15-2
S31-2 P31-2
GNS indicates a Green
sleeve o n the wir e
GN
BK
BU
RD
S25-4 P25-4
S25-2 P25-2
S25-3 P25-3
S25-1 P25-1
WH
RD
GN
BU
LED Power
Supply
N
L
+
-
S24 P24
LED Lighting
WH
S31-1 P31-1
BN
BN
N
Drop In
L
BK
BU
BU
Embraco
VSD
M
Ferrite
P4-1 S4-1
BU
BN
BU
BN
S13-2 P13-2 P13-1 S13-1
Hot Gas Solenoid
indicates connecti ons
internal to junction box
S29-2 P29-2 P29-1 S29-1
BN BU
S5-2
BU
BN
BU
S30-2 P30-2 P30-1 S30-1
BN
BU
Inlet-L Inlet-N
T2-1 T2-1
T1-1
BN BU
Perimeter
elements
S26-2 P26-2 P26-1 S26-1
BN BU
BN
BU
S27-2 P27-2
BN
BN
S28-2 P28-2
BN
P27-1 S27-1
P28-1 S28-1
BU
BU
S5-1
BU
S18-2 P18-2
P6-1 S6-1
P3-1 S3-1
P3-4 S3-4
P6-4 S6-4
BN
BU
BN
S21-4 P21-4
S21-2 P21-2
Condenser Fan
BN
S18-4 P18-4
Evaporator Fan
BU
BU
BU
S2-1 P2-1
S2-2 P2-2
S2-3 P2-3
S2-5 P2-5
BK
BK
OG
BKBK
BK
BK
BK
Control
Probe
Evaporator
Probe
BN
L
BU
N
BN BU
T1-2
GNYE
E
EMC Filter
BU
BN
P17-2 S17-2
S6-2 P6-2
WDTL
SCS
Controller
L N
C
R
R
SSR
S1
S2
SSR
Comp.
0V
+
1
2
3
AD5
DI1
0V AD1
DI2
0V AD2
DI3
0V AD3
DI4
5V
0V
AD4
BK
BK
BN BU
P3-2 S3-2
S19-2 P19-2
S19-4 P19-4
BN
BK
BK
RD
BN
WH
S4-2 P4-2
BN
P18-1 S18-1
BU
BU
P21-1 S21-1
P19-1 S19-1
BU
BN
WH
RD
Door Switc h
BK
BK
Condenser
Probe
P17-1 S17-1
P16-1 S16-1
P16-2 S16-2
P20-2 S20-2
P20-1 S20-1
S23-4
S23-1
S23-3
P22-1 S22-1
BK
BK
P22-2 S22-2
BK
P7-2 S7-2
S2-4 P2-4
RD
BU
BU
WH
P7-1 S7-1
WH
BK
WH
RD
Ambient
Probe
RD
BK
Programming
Port
BN
BN
BK
BU GNS
BN GNS
BK GNS
BK
OG
S15-2 P15-2
S31-2 P31-2
GNS indicates a Green
sleeve o n the wir e
GN
BK
BU
RD
S25-4 P25-4
S25-2 P25-2
S25-3 P25-3
S25-1 P25-1
WH
RD
GN
BU
LED Power
Supply
N
L
+
-
S24 P24
LED Lighting
WH
S31-1 P31-1
BN
BN
N
Drop In
L
BK
BU
BU
Embraco
VSD
M
Ferrite
P4-1 S4-1
BU
BN
BU
BN
S13-2 P13-2 P13-1 S13-1
Hot Gas Solenoid
indicates connecti ons
internal to junction box
S29-2 P29-2 P29-1 S29-1
BN BU
S5-2
BU
BN
BU
S30-2 P30-2 P30-1 S30-1
BN
BU
Inlet-L Inlet-N
T2-1 T2-1
T1-1
BN BU
Perimeter
elements
S26-2 P26-2 P26-1 S26-1
BN BU
BN
BU
S27-2 P27-2
BN
BN
S28-2 P28-2
BN
P27-1 S27-1
P28-1 S28-1
BU
BU
S5-1
LEGEND
Internal Unit Junction Box Sockets/Plugs
Inlet IEC Cabinet Socket/Plug
S1/P1 Not Used
S2/P2 Unit Junction Box to Controller Signal Socket/Plug (6-way)
S3/P3 Unit Junction Box to Controller Power Socket/Plug (Blue 4-way)
S4/P4 Lighting/Heater Wire Unit Socket/Plug (Black 3-way)
S5 Lighting/Heater Wire Unit Socket (Black 3-way) (unused)
S6/P6 Unit Junction Box to Controller Power Socket/Plug (Red 4-way)
S7/P7 Door Sensor Socket/Plug (White 2-way)
S8/P8 Not Used
S9/P9 Not Used
S10/P10 Not Used
S11/P11 Not Used
S12/P12 Not Used
Continued over the page
WIRE COLOURS
BK Black
BN Brown
RD Red
OG Orange
GN Green
BU Blue
GY Grey
WH White
GNYE Green-Yellow
Based upon IEC 757 Standard
Model Number: PG21.UPF.1.SD

LEGEND
S13/P13 Hot Gas Solenoid Unit Socket/Plug (White 3-way)
S14/P14 Not Used
S15/P15 Compressor Unit Socket/Plug (Blue 4-way)
S16/P16 Evaporator Sensor Socket/Plug (Black 2-way)
S17/P17 Cabinet Sensor Socket/Plug (Blue 2-way)
S18/P18 Condenser Motor Unit Socket/Plug (Red 4-way)
S19/P19 Evaporator Motor Unit Socket/Plug (White 4-way)
S20/P20 Condenser Sensor Socket/Plug (Red 2-way)
T1 Unit Terminals
T2 EMI Filter Box Terminals
External Sockets/Plugs
S21/P21 Evaporator Motor Extension Socket/Plug (Red 4-way)
S22/P22 Ambient Sensor Socket/Plug (White 2-way)
S23/P23 Programming/Comms Port Socket (Blue 4-way)
S24/P24 LED Driver DC Out Put Socket/Plug (Red 2-way)
S25/P25 LED Lighting Loom Socket/Plug (White 6-way)
S26/P26 Heater Socket/Plug 1 (Black 3-way)
S27/P27 Heater Socket/Plug 2 (Black 2-way)
S28/P28 Heater Socket/Plug 3 (Black 3-way)
S29/P29 Hot Gas Solenoid Extension Socket/Plug (White 3-way to Molex)
S30/P30 LED Driver AC Extension Fl ex Socket/Plug (White plugged into black 3-way)
S31/P31 Unfiltered VSD Supply Socket/Plug (Yellow 4-way)
19
SKOPE ProSpec Upright Series Freezer
Wiring
Service Manual

20 Wiring
Service Manual
SKOPE ProSpec Upright Series Freezer
Model: ProSpec 2 Door Freezer
GNS indicates a Green
sleeve o n the wir e
indicates connecti ons
internal to junction box
GNS indicates a Green
sleeve o n the wir e
indicates connecti ons
internal to junction box
BU
S18-2 P18-2
P6-1 S6-1
P3-1 S3-1
P3-4 S3-4
P6-4 S6-4
BN
BU
BN
S21-4 P21-4
S21-2 P21-2
Condenser Fan
BN
S18-4 P18-4
Evaporator Fan
BU
BU
BU
S2-1 P2-1
S2-2 P2-2
S2-3 P2-3
S2-5 P2-5
BK
BK
OG
BKBK
BK
BK
BK
Control
Probe
Evaporator
Probe
BN
L
BU
N
BN BU
T1-2
GNYE
E
EMC Filter
BU
BN
P17-2 S17-2
S6-2 P6-2
WDTL
SCS
Controller
L N
C
R
R
SSR
S1
S2
SSR
Comp.
0V
+
1
2
3
AD5
DI1
0V AD1
DI2
0V AD2
DI3
0V AD3
DI4
5V
0V
AD4
BK
BK
BN BU
P3-2 S3-2
S19-2 P19-2
S19-4 P19-4
BN
BK
BK
RD
BN
WH
S4-2 P4-2
BN
P18-1 S18-1
BU
BU
P21-1 S21-1
P19-1 S19-1
BU
BN
WH
RD
Door Switc h
WH
WH
RD
Door Switc h
BK
BK
Condenser
Probe
P17-1 S17-1
P16-1 S16-1
P16-2 S16-2
P20-2 S20-2
P20-1 S20-1
S23-4
S23-1
S23-3
P22-1 S22-1
BK
BK
P22-2 S22-2
BK
P7-2 S7-2
S2-4 P2-4
RD
BU
BU
WH
P7-1 S7-1
WH
BK
WH
RD
Ambient
Probe
RD
BK
Programming
Port
BN
BN
BK
BU GNS
BN GNS
BK GNS
BK
OG
S15-2 P15-2
S31-2
GN
BK
BU
RD
S25-4 P25-4
S25-2 P25-2
S25-3 P25-3
S25-1 P25-1
WH
RD
GN
BU
LED Power
Supply
N
L
+
-
S24 P24
LED Lighting
WH
S31-1
BN
BN
BU
P4-1 S4-1
BUBN
BU
BN
S13-2 P13-2 P13-1 S13-1
Hot Gas Solenoid
S29-2 P29-2 P29-1 S29-1
BN BU
S5-2
S5-1
BN
BN
BU
S30-2 P30-2
P30-1 S30-1
BN
BU
Inlet-L
Inlet-N
T2-1 T2-1
T1-1
BN BU
Pillar element
Compressor
S15-1 P15-1
BU
BU
Perimeter
elements
BN BU
BU
BN
S26-2 P26-2
BN
S28-2 P28-2
BN
P26-1 S26-1
BU
P28-1 S28-1
BU
S27-2 P27-2
BN BU
P27-1 S27-1
BU
BN
BU
BU
S18-2 P18-2
P6-1 S6-1
P3-1 S3-1
P3-4 S3-4
P6-4 S6-4
BN
BU
BN
S21-4 P21-4
S21-2 P21-2
Condenser Fan
BN
S18-4 P18-4
Evaporator Fan
BU
BU
BU
S2-1 P2-1
S2-2 P2-2
S2-3 P2-3
S2-5 P2-5
BK
BK
OG
BKBK
BK
BK
BK
Control
Probe
Evaporator
Probe
BN
L
BU
N
BN BU
T1-2
GNYE
E
EMC Filter
BU
BN
P17-2 S17-2
S6-2 P6-2
WDTL
SCS
Controller
L N
C
R
R
SSR
S1
S2
SSR
Comp.
0V
+
1
2
3
AD5
DI1
0V AD1
DI2
0V AD2
DI3
0V AD3
DI4
5V
0V
AD4
BK
BK
BN BU
P3-2 S3-2
S19-2 P19-2
S19-4 P19-4
BN
BK
BK
RD
BN
WH
S4-2 P4-2
BN
P18-1 S18-1
BU
BU
P21-1 S21-1
P19-1 S19-1
BU
BN
WH
RD
Door Switc h
WH
WH
RD
Door Switc h
BK
BK
Condenser
Probe
P17-1 S17-1
P16-1 S16-1
P16-2 S16-2
P20-2 S20-2
P20-1 S20-1
S23-4
S23-1
S23-3
P22-1 S22-1
BK
BK
P22-2 S22-2
BK
P7-2 S7-2
S2-4 P2-4
RD
BU
BU
WH
P7-1 S7-1
WH
BK
WH
RD
Ambient
Probe
RD
BK
Programming
Port
BN
BN
BK
BU GNS
BN GNS
BK GNS
BK
OG
S15-2 P15-2
S31-2
GN
BK
BU
RD
S25-4 P25-4
S25-2 P25-2
S25-3 P25-3
S25-1 P25-1
WH
RD
GN
BU
LED Power
Supply
N
L
+
-
S24 P24
LED Lighting
WH
S31-1
BN
BN
BU
P4-1 S4-1
BUBN
BU
BN
S13-2 P13-2 P13-1 S13-1
Hot Gas Solenoid
S29-2 P29-2 P29-1 S29-1
BN BU
S5-2
S5-1
BN
BN
BU
S30-2 P30-2
P30-1 S30-1
BN
BU
Inlet-L
Inlet-N
T2-1 T2-1
T1-1
BN BU
Pillar element
Compressor
S15-1 P15-1
BU
BU
Perimeter
elements
BN BU
BU
BN
S26-2 P26-2
BN
S28-2 P28-2
BN
P26-1 S26-1
BU
P28-1 S28-1
BU
S27-2 P27-2
BN BU
P27-1 S27-1
BU
BN
BU
LEGEND
Internal Unit Junction Box Sockets/Plugs
Inlet IEC Cabinet Socket/Plug
S1/P1 Not Used
S2/P2 Unit Junction Box to Controller Signal Socket/Plug (6-way)
S3/P3 Unit Junction Box to Controller Power Socket/Plug (Blue 4-way)
S4/P4 Lighting/Heater Wire Unit Socket/Plug (Black 3-way)
S5 Lighting/Heater Wire Unit Socket (Black 3-way) (unused)
S6/P6 Unit Junction Box to Controller Power Socket/Plug (Red 4-way)
S7/P7 Door Sensor Socket/Plug (White 2-way)
S8/P8 Not Used
S9/P9 Not Used
S10/P10 Not Used
S11/P11 Not Used
S12/P12 Not Used
Continued over the page
WIRE COLOURS
BK Black
BN Brown
RD Red
OG Orange
GN Green
BU Blue
GY Grey
WH White
GNYE Green-Yellow
Based upon IEC 757 Standard
Model Number: PG21.UPF.2.SD
Other manuals for ProSpec Series
3
This manual suits for next models
4
Table of contents
Other Skope Freezer manuals
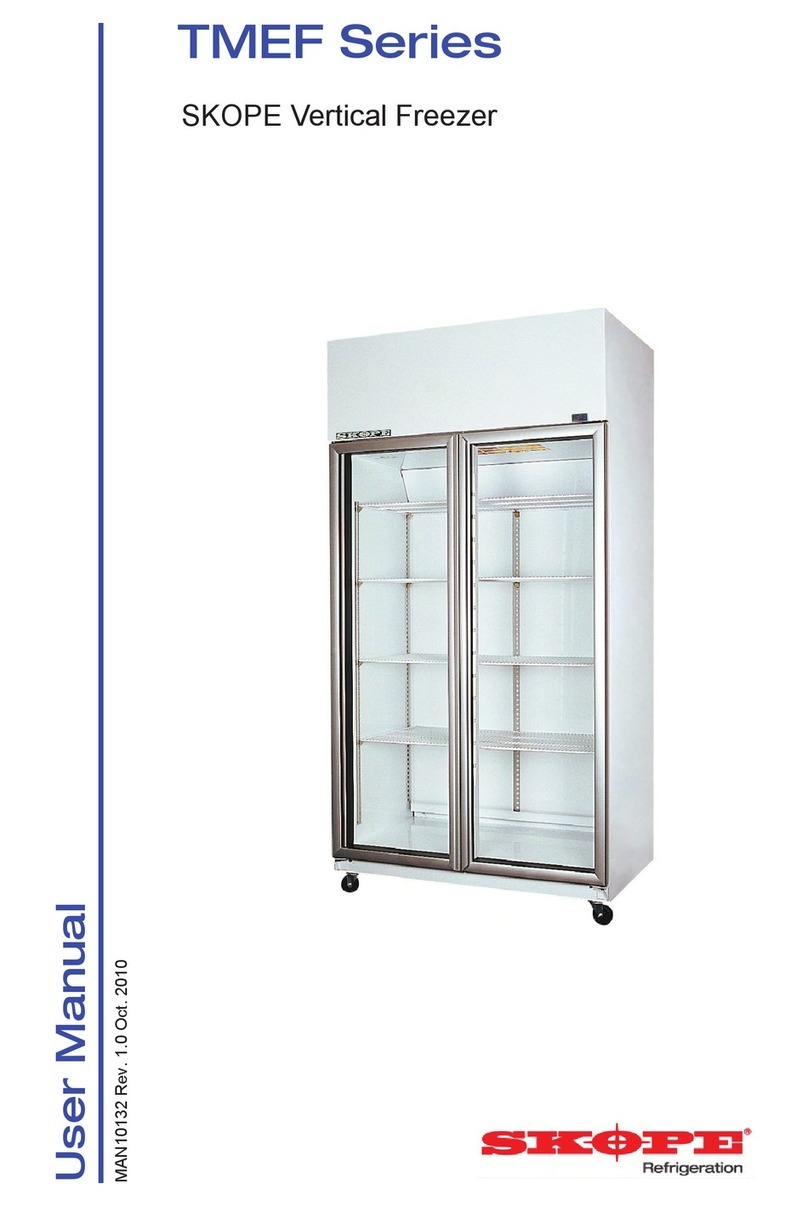
Skope
Skope TMEF Series User manual
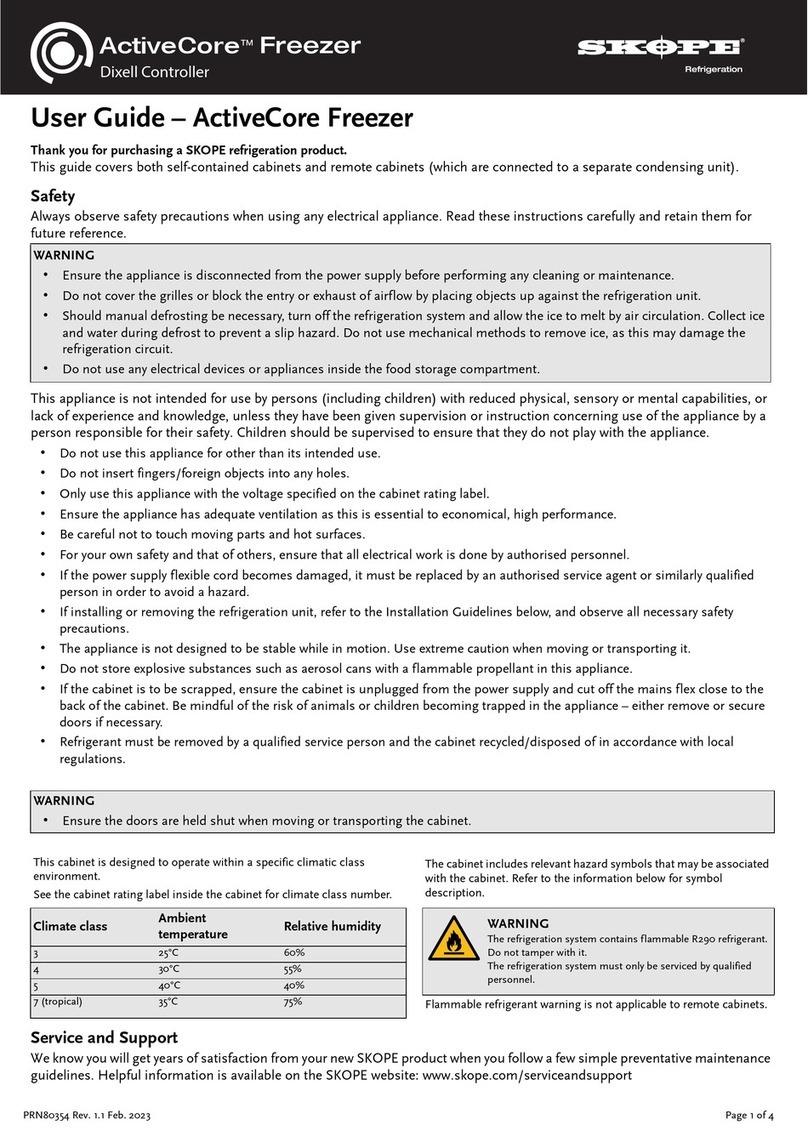
Skope
Skope ActiveCore SKFT1500N-A-WG User manual
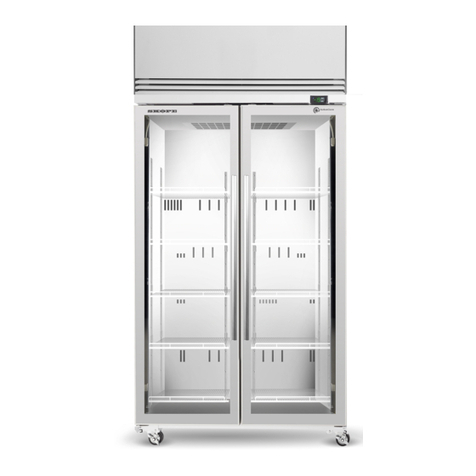
Skope
Skope ActiveCore TMF650N Series User manual

Skope
Skope SERENE SC430N User manual
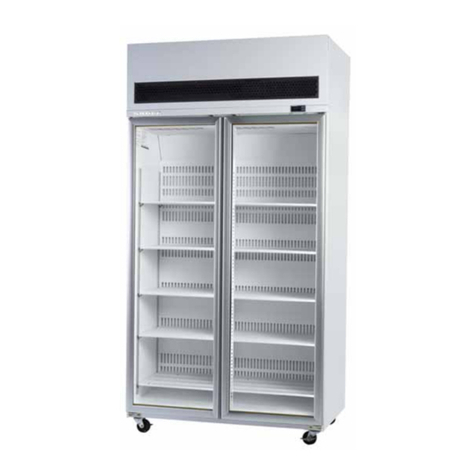
Skope
Skope VF Series User manual
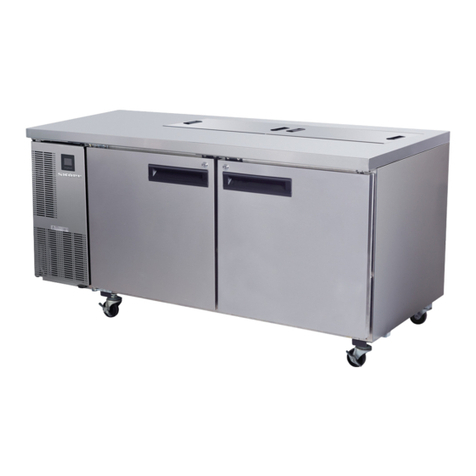
Skope
Skope PG Series User manual
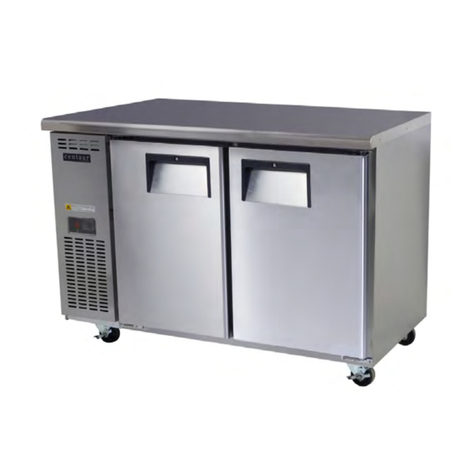
Skope
Skope Centaur Series User manual

Skope
Skope VF650 User manual
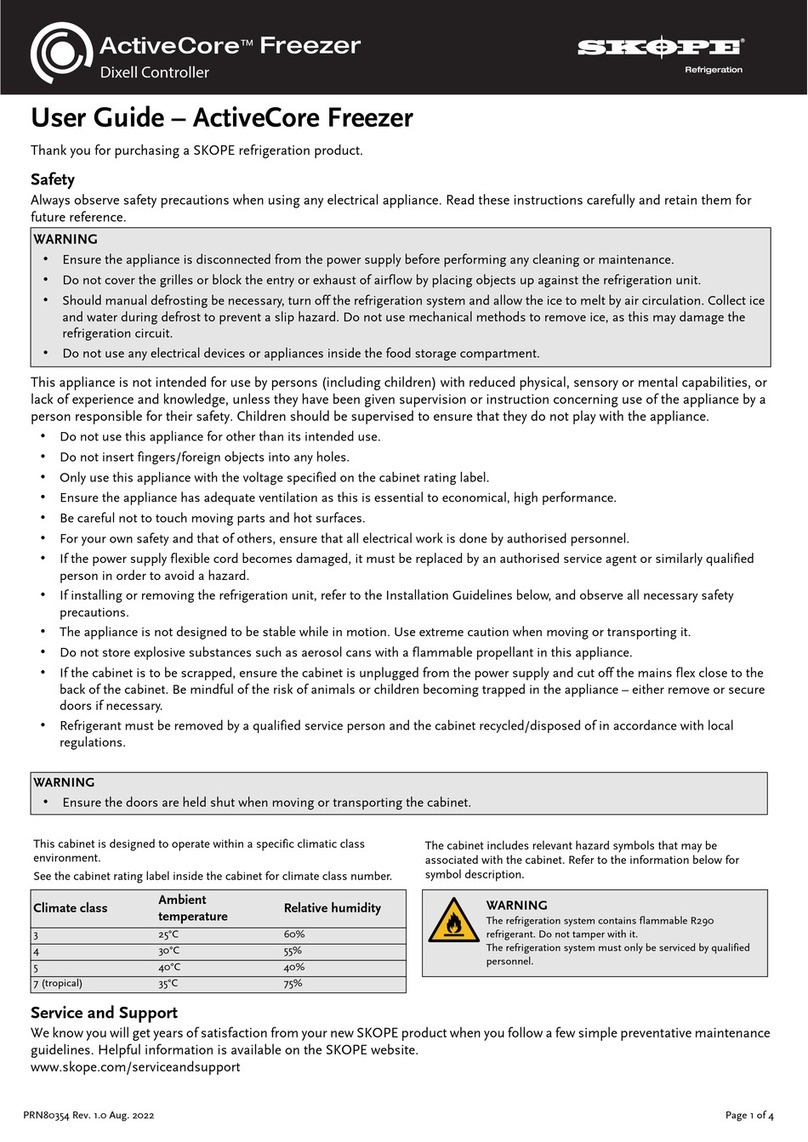
Skope
Skope ActiveCore User manual
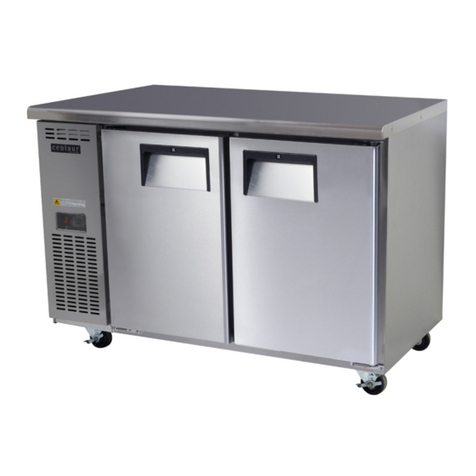
Skope
Skope BC070-CB User manual