SnowPure Electropure EXL Series Installation and operation manual

SNOWPURE, LLC, 2005-2018 VERSION 3.5 (XL+EXL) –FEBRUARY 2018 PAGE 1
OEM Engineering Manual
Electropure™ XL & EXL
Series EDI
Contains information for the successful system engineering, design,
installation, operation, and maintenance of SnowPure’s “Electropure™ XL
and EXL” EDI products by an OEM pure water system integrator.
Pictured: EXL-750 High Flow Industrial EDI
Module
Manual: Version 3.5
Updated: February 2018

SNOWPURE, LLC, 2005-2018 VERSION 3.5 (XL+EXL) –FEBRUARY 2018 PAGE 2
WorldwideHQ(Headquarters):
SnowPureWaterTechnologies
San Clemente, CA 92672, USA
Tel: +1.949.240.2188
www.snowpure.com
SnowPureGlobalSalesOffices:
ChinaSalesOffice
Electropure Environmental
Technology (Shanghai) Co. Ltd.
伊乐科环保科技(上海)有限公司
Tel: +86.21.6167.1860
Email: [email protected]
www.snowpure.com.cn
MiddleEastSalesOffice
SnowPureMiddleEast
Amman, Jordan
Email: info@middle-east.snowpure.com
InternationalDistributors:
Hong Kong(AuthorizedDistributor)
SnowPure International (HK) Ltd.
Hong Kong
Tel: +1.858.692.0664
info@snowpureintl.com
India(Authorized Distributor)
Evergreen Technologies Pvt. Ltd.
Tel: +91.2201.2461
info@evergreenindia.com
Japan(AuthorizedDistributor)
AMP Ionex / Mihama
エイエムピー・アイオネクス株式会社 / 美浜株式会社
Tel: +81.3.4570.3820
info-mhg3@mihama.com
www.amp-ionex.com
Korea(Authorized Distributor)
Innomeditech, Inc.
주식회사 이노메디텍
Tel: +82-31-80022500
www.innomeditech.co.kr
Germany(AuthorizedDistributor)
TES Water Treatment GmbH
Tel: +49.6205.2870.0
info@tes-water.de
Sweden,Finland,Norway, Baltics(AuthorizedDistributor)
PWS Pure Water Scandinavia AB
Tel: +46.23.797.990
lars.wiklund@purewater.se
Switzerland,Austria,Czech Republic,Slovakia
ROC Components AG
Tel: +41.61.461.8303
Ukraine (AuthorizedDistributor)
Nerex PE
Tel: +38.44.223.5636

SNOWPURE, LLC, 2005-2018 VERSION 3.5 (XL+EXL) –FEBRUARY 2018 PAGE 3
WORLDWIDE HQ (HEADQUARTERS):.............................................................................. 2
SNOWPURE WATER TECHNOLOGIES............................................................................................2
SNOWPURE GLOBAL SALES OFFICES:............................................................................ 2
CHINA SALES OFFICE..................................................................................................................2
MIDDLE EAST SALES OFFICE SNOWPURE MIDDLE EAST...............................................................2
INTERNATIONAL DISTRIBUTORS:..................................................................................... 2
HONG KONG (AUTHORIZED DISTRIBUTOR)....................................................................................2
INDIA (AUTHORIZED DISTRIBUTOR)...............................................................................................2
JAPAN (AUTHORIZED DISTRIBUTOR).............................................................................................2
KOREA (AUTHORIZED DISTRIBUTOR)............................................................................................2
GERMANY (AUTHORIZED DISTRIBUTOR) .......................................................................................2
SWEDEN,FINLAND,NORWAY,BALTICS (AUTHORIZED DISTRIBUTOR).............................................2
SWITZERLAND,AUSTRIA,CZECH REPUBLIC,SLOVAKIA .................................................................2
UKRAINE (AUTHORIZED DISTRIBUTOR).........................................................................................2
TABLE OF CONTENTS........................................................................................................3
ELECTROPURE™EDI DESCRIPTION .............................................................................. 6
CHAPTER 1: ELECTROPURE™EDI TECHNOLOGY..............................................................6
ADVANTAGES OF EDI OVER CONVENTIONAL DI............................................................... 6
PROCESS OF ELECTRODEIONIZATION............................................................................. 6
ELECTROPURE™EDI TECHNOLOGY OVERVIEW ............................................................. 7
FIGURE 1: SCHEMATIC DIAGRAM OF THE ELECTROPURE EDI PROCESS.........................................7
DETAILS OF THE ELECTROPURE™EDI PROCESS ........................................................... 8
EDI MODEL:SERIAL REMOVAL OF IONS.........................................................................10
EFFECTS OF CONTAMINANTS IN EDI FEEDWATER: .........................................................11
GLOSSARY OF TERMS ..................................................................................................12
SNOWPURE EDI INTELLECTUAL PROPERTY...................................................................14
EDI TECHNOLOGY SUMMARY .......................................................................................14
CHAPTER 2: PRODUCT DESCRIPTION AND GUIDE..............................................................15
ELECTROPURE™EDI ADVANTAGES:.............................................................................15
ELECTROPURE™EDI PRODUCT GUIDE:........................................................................16
CURRENT ELECTROPURE™EDI PRODUCT LINES:.........................................................16
LEGACY ELECTROPURE™EDI PRODUCT LINES:............................................................16
MODULE RESTACK.......................................................................................................16
APPLICATIONS AND PURITY SPECIFICATIONS .................................................................17
SEMICONDUCTOR ULTRAPURE WATER:......................................................................................17
POWER GENERATION BOILER WATER:.......................................................................................18
ASTM REAGENT WATER:..........................................................................................................18
USP PHARMACEUTICAL WATER:................................................................................................18
CHAPTER 3: NORMAL OPERATION,CONDITIONS,AND SPECIFICATIONS.............................19
STANDARD OPERATING AND TESTING CONDITIONS ........................................................19
GLOSSARY OF TERMS ..................................................................................................19
OPERATING FEED WATER SPECIFICATIONS ...................................................................20
ENVIRONMENTAL CONDITIONS......................................................................................21
DC POWER SUPPLY REQUIREMENTS ............................................................................21
PROJECTION PROGRAM:EDICAD™ .............................................................................22
CHAPTER 4: EFFECTS OF PROCESS VARIABLES ..............................................................23
APPLIED VOLTAGE .......................................................................................................23
Table of Contents

SNOWPURE, LLC, 2005-2018 VERSION 3.5 (XL+EXL) –FEBRUARY 2018 PAGE 4
OPTIMUM VOLTAGE...................................................................................................................23
QUALITY VS VOLTAGE ...............................................................................................................23
CURRENT VS FEED CONDUCTIVITY.............................................................................................23
STEADY STATE OPERATION.......................................................................................................24
IONIC SPECIES.............................................................................................................24
IONIC SIZE................................................................................................................................24
IONIC CHARGE..........................................................................................................................25
SELECTIVITY COEFFICIENTS OF IONS FOR RESIN ........................................................................25
EASY IONS (NA+,CL-,CA+2,H+,AND OH-)..................................................................................25
LARGE,WEAKLY-CHARGED IONS (CARBON DIOXIDE,SILICA,BORON)..........................................25
TEMPERATURE.............................................................................................................26
PRESSURE DROP VS TEMPERATURE..........................................................................................26
STACK RESISTANCE VS TEMPERATURE ......................................................................................26
QUALITY VS TEMPERATURE (RE-OPTIMIZATION OF OPERATING CONDITIONS).................................27
RESISTIVITY MEASUREMENT CORRECTION WITH TEMPERATURE..................................................27
FLOW..........................................................................................................................28
PRESSURE DROP VS FLOW........................................................................................................28
FIGURE 2: XL PRESSURE DROP.................................................................................................29
EFFECT OF OUTLET PRESSURE ON QUALITY AND INTERNAL LEAKAGE..........................................30
FEED CONDUCTIVITY....................................................................................................30
PRODUCT QUALITY (AT DESIGN AND MAXIMUM FLOW):.................................................................30
CHAPTER 5: WATER QUALITY OPTIMIZATION...................................................................31
FUNDAMENTALS...........................................................................................................31
VOLTAGE DRIVING FORCE..........................................................................................................31
CURRENT DENSITIES ....................................................................................................31
IONIC BALANCES AND PH..............................................................................................32
AFFECTING THE LOCATION OF THE “IONIC FRONT”...........................................................32
CHAPTER 6: SYSTEM DESIGN SCHEMATICS AND SAFEGUARDS.........................................33
THE SYSTEM DESIGN IS THE RESPONSIBILITY OF THE OEM. ............................................33
ELECTROPURE EDI PRETREATMENT PHILOSOPHY .........................................................33
ELECTROPURE EDI SIMPLE SYSTEM PHILOSOPHY.........................................................33
EDI SYSTEM PROTECTION AND CONTROLS ...................................................................34
COMPONENT DESCRIPTION OF AN OPTIMUM EDI SYSTEM ..............................................34
P&ID DESIGNATION FOR AN EDI MODULE .....................................................................36
FIGURE 3: BEST PRACTICES P&ID OF A SIMPLE EDI SYSTEM .....................................................37
DESIGNS WITH MULTIPLE MODULES..............................................................................38
DESIGNS WITH 2-PASS RO SYSTEMS............................................................................38
INSTALLATION NOTES...................................................................................................39
SAFETY ....................................................................................................................................39
HANDLING THE MODULE ............................................................................................................39
MOUNTING OPTIONS .................................................................................................................41
MODULE ORIENTATION..............................................................................................................41
PIPE AND TUBING CONNECTIONS...............................................................................................41
POWER CONNECTION &WIRE CONVENTIONS.............................................................................43
BOLT TORQUE ..........................................................................................................................43
MODULE STARTUP ....................................................................................................................44
FEED WATER...............................................................................................................46
CHAPTER 7: CLEANING AND MAINTAINING YOUR EDI MODULES .......................................46
HARDNESS (SCALE)DEPOSITS ......................................................................................46
ION-EXCHANGE RESINS (TOC ORGANIC FOULING)..........................................................46

SNOWPURE, LLC, 2005-2018 VERSION 3.5 (XL+EXL) –FEBRUARY 2018 PAGE 5
PARTICULATE FOULING.................................................................................................46
POWER AND REGENERATION ........................................................................................46
ELECTRODE CONNECTORS...........................................................................................47
XL SERIES BOLTS........................................................................................................47
EXTERIOR CLEANING....................................................................................................47
CHAPTER 8: PROBLEM SOLVING AND TROUBLESHOOTING ...............................................48
CHAPTER 9: AUXILIARY EQUIPMENT AND OPTIONS ..........................................................49
CHAPTER 10: ELECTROPURE MODULE DIMENSIONS ........................................................50
FIGURE 4: XL™ EDI MODULE DRAWING &DIMENSIONS.............................................................50
FIGURE 5: EXL™ EDI MODULE DRAWING &DIMENSIONS...........................................................51
FIGURE 6: XL MOUNTING OPTIONS............................................................................................52
FIGURE 7: EXL MOUNTING OPTIONS..........................................................................................52
FIGURE 8: MANIFOLDING OPTIONS.............................................................................................54
CHAPTER 11: SNOWPURE LLC LIMITED WARRANTY........................................................55
CHAPTER 12: SNOWPURE LLC TERMS AND CONDITIONS.................................................56
CHAPTER 13: SAFETY ....................................................................................................57
ELECTRICAL SAFETY....................................................................................................57
CHEMICAL SAFETY.......................................................................................................57
CHAPTER 14: LABELING AND CERTIFICATIONS .................................................................59
EQUIPMENT LABEL:...................................................................................................................59
EC DECLARATION OF CONFORMITY: ..........................................................................................60
CHAPTER 15: APPENDICES.............................................................................................61
APPENDIX #1: ACID CLEANING PROCEDURE /SCALE IN THE CONCENTRATE STREAM ......61
APPENDIX #2: RESIN CLEANING PROCEDURE/TOC IN THE FEED STREAM.......................63
APPENDIX #3: RESETTING BOLT TORQUES-XL &XL-HTS SERIES ONLY ........................65
FIGURE 8: TORQUE SEQUENCE –XL &XL-HTS ONLY ...............................................................65
APPENDIX #4: XL/EXL MODULE CHEMICAL SANITIZATION PROCEDURE..........................66
APPENDIX #5: XL/EXL MODULE HEAT SANITIZATION PROCEDURE.................................68
APPENDIX #6: MODULE REGENERATION PROCEDURE....................................................70
APPENDIX #7: DATA FORM FOR ELECTROPURE™"XL" EDI MODULE .............................71
APPENDIX #8: EDI POWER CONSUMPTION AND ELECTRICAL COST ................................72
APPENDIX #9-A: SILICA REMOVAL BY RO AND ELECTRODEIONIZATION...........................73
APPENDIX #9-B: SILICA FOULING AND CLEANING IN ELECTROPURE™EDI.....................75
APPENDIX #10: PROCEDURE TO PREVENT FREEZING OF EDI MODULES.........................78
APPENDIX #11: EDI MODULE STORAGE AND EDI SYSTEM SHUTDOWN...........................79
APPENDIX #12: FDA &COMPLIANCE OF MATERIALS IN ELECTROPURE™EDI MODULES.80
APPENDIX #13: CONTINUOUS CONTROL OF CO2 AS RO PRETREATMENT .......................81

SNOWPURE, LLC, 2005-2018 VERSION 3.5 (XL+EXL) –FEBRUARY 2018 PAGE 6
Electropure™ EDI Description
The need to satisfy the increasing demand for high purity water can be achieved using
SnowPure LLC’s proprietary Electropure™ electrodeionization (EDI) equipment.
SnowPure, formerly Electropure and HOH Water Technology, pioneered EDI in the
1980’s. The O’Hare patent1, issued in 1984, forms the basis of all EDI technology.
EDI process systems replace conventional DI mixed resin beds to produce deionized
water. Unlike DI resin, EDI does not require shutdowns for replacing resin beds or for
resin regeneration using chemicals. Because of this, EDI:
minimizes water quality upsets and
minimizes operating costs.
EDI removes ions from aqueous streams, typically in conjunction with reverse osmosis
(RO) and other purification devices. Our high-quality modules continually produce
ultrapure water up to 18.2 MΩ.cm. EDI may be run continuously or intermittently.
AdvantagesofEDIoverConventionalDI
EDI is Continuous, does not require shutdowns or changeovers
Provides water of consistent quality
EDI does not require chemicals (as does DI resin regeneration)
Electropure™ EDI modules are the smallest and lightest per unit flow on the
market; EDI skids are therefore compact
Requires little energy
Economic use of capital—saves operating expense
ProcessofElectrodeionization
The Electropure™ EDI design combines two well-established water purification
technologies—electrodialysis (ED) and ion-exchange resin deionization. Through this
revolutionary technique, dissolved salts can be removed with low energy cost and
without the need for chemical regeneration; the result is high-quality pure water of multi-
MΩ.……cm resistivity which can be produced continuously at substantial flow rates.
Electropure’s EDI removes ions from water by forcing them out of the feed stream into
adjacent streams via an electric potential. EDI is different from ED by using resins in the
diluting chambers—the resins allow for more efficient migration of ions in very low
conductivity water. The resins operate in steady state; they act not as an ion reservoir
but as an ion conduit.
1US 4,465,573
Chapter 1: Electropure™ EDI Technology

SNOWPURE, LLC, 2005-2018 VERSION 3.5 (XL+EXL) –FEBRUARY 2018 PAGE 7
Electropure™ EDI TechnologyOverview
Figure1:SchematicDiagramoftheElectropureEDIProcess
Figure 1: Electropure EDI Technology

SNOWPURE, LLC, 2005-2018 VERSION 3.5 (XL+EXL) –FEBRUARY 2018 PAGE 8
The electrodeionization process uses a combination of ion-selective membranes and
ion-exchange resins sandwiched between two electrodes (anode (+) and cathode (-))
under a DC voltage potential to remove ions from RO-pretreated water.
Ion-selective membranes operate using the same principle and materials as ion-
exchange resins, and they are used to transport specific ions away from their
counterions. Anion-selective membranes are permeable to anions but not to cations;
cation-selective membranes are permeable to cations but not to anions. The
membranes are not water-permeable.
By spacing alternating layers of anion- and cation-selective membranes within a plate-
and-frame module, a “stack” of parallel purifying and concentrating compartments are
created. The ion-selective membranes are fixed to an inert polymer frame, which is filled
with mixed ion-exchange resins to form the purifying chambers. The screens between
the purifying chambers form the concentrating chambers.
This basic repeating element of the EDI, called a “cell-pair,” is illustrated in Figure 1. The
“stack” of cell-pairs is positioned between the two electrodes, which supply the DC
potential to the module. Under the influence of the applied DC voltage potential, ions
are transported across the membranes from the purifying chambers into the
concentrating chambers. Thus, as water moves through the purifying chambers, it
becomes free of ions. This is the pure water product stream.
The RO feed to the Electropure™ EDI module is split into three separate streams:
1. Product stream (up to 99% water recovery)
2. Concentrate stream (typically 10%, may be recovered as RO feed*)
3. Electrode stream (10 l/h, 0.05 gpm, always to drain)
* Note: for recovery of the concentrate stream, we recommend
use of a break tank and pump, and we recommend against a
direct connection.
The electrode stream flows past the anode and cathode sequentially. The anolyte-
bathing stream first flows past the anode (+) through a compartment, formed by a
gasketed monofilament screen, which is located between the anode and an adjacent
anion-selective membrane. In this compartment the pH becomes acidic, and O2(gas)
and a small amount of Cl2 (dissolved) are generated. This acidic stream then flows into
the cathode compartment, formed between the cathode (-) and its adjacent cation-
selective membrane. In this compartment the pH becomes neutral, and H2(gas) is
generated. Thus, the waste stream expels the unwanted chlorine, oxygen, and
hydrogen gas from the electrodes. The unique Electropure™ electrode system is
designed to be non-scaling since neither stream becomes high in pH. The
Electropure™ anode is further engineered to minimize the amount of chlorine (a strong
oxidizer) formed.
Details of the Electropure™ EDI Process
Water from all sources contains impurities including dissolved salts, which are
composed of negatively charged ions (anions) and positively charged ions (cations).

SNOWPURE, LLC, 2005-2018 VERSION 3.5 (XL+EXL) –FEBRUARY 2018 PAGE 9
Typical ions include sodium, calcium, magnesium, chloride, sulfate, nitrate, carbonate,
bicarbonate, etc. Over 98% of these ions can be removed by appropriate reverse
osmosis (RO) treatment. Water sources also contain organics, dissolved gases (e.g.,
O2, CO2), trace metals, and weakly-ionized inorganic compounds (e.g., boron and
silica), which must be removed for use in most industrial processes. The RO system
(and its pretreatment) also removes many of these impurities.
RO permeate (the EDI feedwater) should “ideally” range from 1-6 μS/cm (conductivity),
or a FCE = 1-9 μS/cm. Ultrapure (deionized) water ranges from 2.0-18.2 MΩ.cm
depending on the application. Typically, fewer ions in the EDI feed leads to the highest
quality EDI product water.
Electropure’s EDI process removes the unwanted ions from the water by adsorbing them
on the resins in the purifying chambers, and then transports them into the concentrate
stream. The exchange reaction takes place in the purifying compartments of the module
where the anion-exchange resins trade their hydroxyl ions (OH-) for the anion of the
dissolved salt (e.g., chloride, Cl-). The cation-exchange resins trade their hydrogen ions
(H+) for the cation of the dissolved salt (e.g., sodium Na+).
The adsorption step removes the ions from the influence of the water, whose residence
time in the module is limited (approximately 10-15 seconds). When adsorbed, the ions
are only influenced by force of the external DC potential.
The DC electrical field is applied via the anode (+) and cathode (-) arranged at either end
of the stack. The DC potential attracts or repels the adsorbed ions, forcing movement
along the surface of the resin beads, through the membranes into the concentrating
compartments. The DC potential also “splits” water molecules to form hydroxyl ions and
hydrogen ions:
H2O = OH-+ H+
In Figure 1, the ion-exchange membranes are represented by the vertical lines labeled in
terms of their ionic permeability. Since these ion-selective membranes do not allow
water to permeate through them, they are barriers to water flow.
The negatively-charged anions (e.g., OH-, Cl-) are attracted to the anode (+) and
repelled by the cathode (-). The anions pass through the anion-selective membrane and
into the adjacent concentrate stream. They are blocked by the cation-selective
membrane on the far side of the chamber, and are thus trapped and carried away by the
water in the concentrate stream. The positively-charged cations (e.g., H+, Na+) in the
purifying stream are attracted to the cathode (-) and repelled by the anode (+). The
cations pass through the cation-selective membrane and into the adjacent concentrate
stream, where they are blocked by the anion-selective membrane, and are carried away.
In the concentrate stream, electrical neutrality is maintained. Transported ions from the
two directions neutralize one another’s charge. The current draw from the power supply
is proportional to the number of ions moved. Both the “split” water (H+and OH-) and the
intended ions are transported, and therefore add to the current demand.

SNOWPURE, LLC, 2005-2018 VERSION 3.5 (XL+EXL) –FEBRUARY 2018 PAGE 10
As water moves through the two types of parallel flow compartments, the ions in the
purifying compartments become depleted and are concentrated in the adjacent
concentrating streams, which carry the removed ions from the module.
The use of ion-exchange resins in the purifying and/or concentrate compartments is one
key to the Electropure™ EDI technology and patents. An important phenomenon occurs
in the ion-exchange resins in the purifying compartments. At localized areas of high
potential gradients, significant amounts of H+and OH-are produced by the
electrochemical “splitting” of water. The local production of H+and OH-within the mixed
ion-exchange resins results in constant replenishment of the resins and membranes
without the addition of chemicals.
The water splitting is important in keeping the EDI module bacteria-free, and in keeping
the EDI module in a “polishing” state so it can effectively remove silica and boron.
Proper pretreatment of the EDI feed water is a basic requirement for optimum
performance and trouble-free operation of the EDI process (in fact with any resin-based
deionization process). Contaminants in the feed water can negatively affect the
deionization module and either require maintenance or lessen module lifetime.
Therefore, the quality of the RO system and its pretreatment is critical.
EDIModel:SerialRemovalofIons
Ionic species are not all removed by the EDI process with equal efficiency. This fact
impacts the quality and purity of the product water.
Easy ions are removed first.
The ions with the strongest charge, the smallest mass, and the highest adsorption to the
resins are removed with the highest efficiency. These typically include: H+, OH-, Na+, Cl-,
Ca+2, and SO4-2 (and similar ions).
Upon entry into the first section of the EDI module, these ions are removed preferentially
to other ions. The relative quantity of these ions affects the removal of the other ions.
The pH approaches 7.0 in this section since the H+and OH-ions become balanced.
The first section of the EDI module is known as the “working bed.”
Moderately ionized and polarizable ions are removed next (e.g., HCO3-+ CO2).
CO2is the next most common EDI feedwater constituent. CO2has complex chemistry
depending on the local concentration of protons, and is considered moderately ionized:
CO2+ H2O = H2CO3= H++ HCO3-= 2H++ CO3-2
Since the pH is forced to be near 7.0 in this section, most of the CO2is forced into the
bicarbonate (HCO3-) form. Bicarbonate is weakly adsorbed by the anion resin, so cannot
compete with “easy” ions such as Cl-and SO4-2.

SNOWPURE, LLC, 2005-2018 VERSION 3.5 (XL+EXL) –FEBRUARY 2018 PAGE 11
In the second section of the EDI module, CO2(in all of its forms) is removed
preferentially to weaker ions. The amount of CO2plus HCO3-in the EDI feed strongly
affects the final resistivity of the product water and the efficiency of silica and boron
removal. In this manual, the term “CO2” means the total of CO2plus HCO3-.
In the Electropure™ EDI products, it is found that as long as CO2(in all forms) is less
than 5 mg/l, high quality ultrapure water can be achieved. If the feedwater CO2
concentration is greater than 10 mg/l, it can interfere with the total removal of ions and
strongly impacts the EDI product quality and the silica removal.
Weakly ionized species are removed last (e.g., dissolved silica and boron).
Species such as molecular silica are difficult to remove using any deionization process
because they are very weakly ionized and difficult to adsorb onto the ion-exchange
resin.
If all of the “easy” ions are removed, and all of the CO2is removed, the EDI module can
focus its force on removing these weakly ionized species. The residence time available
in this third section of the module is important. The longer the residence time in the
module, the higher the removal efficiency will be. A long third-section residence time
can be achieved by minimizing the conductivity of the RO product (the quantity of “easy
ions to be removed), ensuring a pH close to 7.0, and minimizing the quantity of HCO3-
and CO2in the RO product.
The second and third sections of the EDI module are known as the “polishing bed.”
The different species in the EDI feed, and their concentration, affect the EDI
performance and efficiency.
EffectsofContaminantsinEDIFeedwater:
Critical contaminants that adversely affect the EDI process include hardness (calcium,
magnesium), organics (TOC), particulates and suspended solids (SDI), active metals
(iron, manganese), oxidants (chlorine, ozone), and carbon dioxide (CO2).
The pretreatment process designed for the RO/EDI system should remove these
contaminants from the feedwater as much as possible. Minimum requirements and
recommended levels are given in the EDI feedwater section (below). Good system
design will further lower the levels of contaminants to enhance EDI performance.
Suggested water treatment strategies are listed later in this manual.
Hardness can cause scaling in the reverse osmosis and EDI units. If this occurs, it will
take place in the concentrate chambers at the high-pH surfaces of the anionic
membrane. Pressure drop in the concentrate stream increases, and current efficiency is
reduced. The Electropure EDI module is designed to avoid scaling; however,
minimization of inlet hardness will lengthen the time between cleanings.
Organics (TOC) adsorb to the surfaces of the resins and membranes. This causes
fouling of the active sites. Fouled resins and membranes are inefficient at removing and
transporting ions. Stack electrical resistance will increase.

SNOWPURE, LLC, 2005-2018 VERSION 3.5 (XL+EXL) –FEBRUARY 2018 PAGE 12
Particulate matter (SDI), colloids, and suspended solids cause plugging and fouling of
the membranes and the resin in the chambers. Plugging of resin interstices increases
the pressure drop across the module.
Iron and other active metals (e.g., Mn) may catalyze resin oxidation, and may strongly
and permanently adsorb to, and reduce the capacity of, the internal resins and
membranes. This happens even in sub-ppm concentrations.
Chlorine (Cl2) and Ozone (O3) attack ion-exchange resins and membrane and cause
de-crosslinking, which results in reduced capacity. Chloramine is a related oxidant.
Oxidation will increase apparent TOC, and the byproducts cause fouling of the anionic
resin and membrane, reducing the ion-transfer kinetics. Oxidation de-crosslinking also
causes the resins to disintegrate and the pressure drop across the module will increase.
Module lifetime will be lessened. The ideal concentration level for oxidants is zero.
CO2, Carbon Dioxide has two effects. First, CO3=reacts with Ca+2 and Mg+2 to form
carbonate scale. This scaling varies with the concentrations, temperature, and pH.
Second, since CO2varies in charge depending on its pH, and its removal by RO and EDI
both depends on charge, its removal efficiency varies. Even low levels of CO2(below 5
ppm) can affect the resistivity of the product water and the removal efficiency of silica
and boron.
GlossaryofTerms
Anion: an ion (electrically charged atom or group of atoms) that carries one or more
negative charges, e.g., Cl, OH, SO42.
Anode: a positively (+) charged electrode that attracts anions, typically a coated
titanium.
Anolyte: the stream of water containing anions and gases collected at the anode.
Cathode:a negatively (-) charged electrode that attracts cations, typically made of
stainless steel.
Catholyte: the stream of water containing cations and gases collected at the cathode.
Cation: an ion that carries one or more positive charges, e.g., Na+, NH4+and Ca2.
Concentrate Stream: the flow of water through the parallel concentrating
compartments, where ions are collected.
Conductivity: the electrical measurement of water’s ability to conduct an electrical
current, which is dependent on the concentration of ions in the water and its
temperature. Units are microsiemens/cm or μS/cm or micromhos/cm, and are
normalized to 25°C.
DC current: current that does not change direction. Amperes in an EDI are proportional
to the number of ions moved, including split water ions.

SNOWPURE, LLC, 2005-2018 VERSION 3.5 (XL+EXL) –FEBRUARY 2018 PAGE 13
DC potential: voltage that does not change polarity. Electrodeionization is only possible
with this form of driving force. There will be some AC component to the DC voltage.
Electrode: a metal plate (anode or cathode) that conducts an electrical field and
catalyzes electrochemical reactions. Electrodes are connected directly to a power
supply via a 3-wire connection.
Electrode Stream: a stream of water that emanates from the electrodes, and includes
ions and electrochemical byproducts. The Electropure technology uniquely combines
both electrode streams in series. This waste stream is small, about 10 l/h.
Feed water: the water that is plumbed into the EDI module, typically RO permeate. It
supplies the product compartments, concentrating compartments, and electrode stream.
GPM (gpm): abbreviation for gallons per minute; a measurement for the flow of water,
where 1.0 gpm is equivalent to 227 liters/hr, and 4.4 gpm is equivalent to 1.0 m3/hr.
Ion-exchange Membrane: a membrane containing ion-exchange groups that is
selectively permeable to either anions or cations, and is impermeable to water.
Ion-exchange Resin:resin beads containing ion-exchange groups that selectively
adsorb either anions or cations.
Megohm:(technically, Megohm.cm or MΩ.cm) the unit of measurement typically used
to quantify the ionic purity of product water produced by a deionization system. It is a
measurement of electrical resistance. Ultrapure water with no impurities may reach
18.24 MΩ.cm at 25°C.
pH: the measurement of the concentration of the hydrogen ion (H). pH values are
expressed as a logarithmic scale from 0 to 14. A value at or near 0 is very acidic, a
value at 7 is neutral, and a value at or near 14 is very basic. The ideal pH feed to an
EDI is 7.0-7.5.
Polarization: the splitting of water molecules into Hand OHions with an electrical
current. This will occur when relatively few ions are present in the diluting compartments
and the applied voltage is excessive, causing water to dissociate in order to conduct
current. Fluctuation of pH in the module is typically associated with polarization.
Polarization of water regenerates the ion-exchange resins.
ppb: parts per billion, or μg/liter. A unit used to quantify very low levels of specific ions of
interest, such as silica, in high-purity produced water.
ppm: parts per million, or mg/liter. The unit used to identify the total dissolved solids
(TDS) in water, and is typically used to quantify the purity of feed water entering the EDI
module. At low conductivity, 1 ppm = ~ 2 microsiemens/cm.
Product (Purified) Stream: the flow of water through the purifying compartments. This
is where deionization occurs. This was formerly known as the Dilute Stream.

SNOWPURE, LLC, 2005-2018 VERSION 3.5 (XL+EXL) –FEBRUARY 2018 PAGE 14
Purified Water: Technically, water purified to USP standards. Purified Water is a
precursor to USP Water-for-Injection (WFI).
Resistivity: the electrical measurement of water’s ability to resist the flow of electrical
current. Resistivity increases as the concentration of ions decreases. It is highly
affected by temperature. This measurement is associated with the level of deionization
achieved with EDI. Ultrapure water with no impurities may reach 18.24 MΩ.cm at 25°C.
Salt: a chemical compound derived from an acid by replacing hydrogen ion wholly or
partly with a metal or electro-positive cation. Examples of salts:
Acid
Ion
Salt
HCl
Sodium ( Na)
NaCl
H2SO4
Calcium ( Ca2)
CaSO4
HNO3
Magnesium ( Mg2)
Mg(NO3)2
H2SO4
Potassium ( K)
KHSO4
TOC: An abbreviation for total organic carbon, a quantitative measure of the level of
organic compounds in a water sample; expressed as ppm, or mg/liter. TOC includes all
organics, and therefore the removal of TOC varies.
USP Purified Water: Water meeting USP (U.S. Pharmacopeia Monograph) quality and
process requirements (now also EP and JP) that has been purified by membranes,
distillation, ion exchange, electrodeionization, and other suitable processes, typically
from sourcewater complying with US EPA drinking water regulations, and contains no
added substances.
SnowPureEDIIntellectualProperty
SnowPure, LLC, formerly HOH Water Technology, holds the O’Hare patent (US
4,465,573) that forms the basis of all EDI technology. It has improvement patents in the
works, and patents issued on its proprietary ion-exchange membrane technology (e.g.,
US 6,503,957).
Other companies hold intellectual property regarding the application of EDI technology in
systems. SnowPure, LLC does not knowingly recommend to its customers the use of
others’ intellectual property, and assumes no obligation on behalf of its customers as
they build, install, or operate EDI in systems of their design as part of their business.
EDITechnologySummary
SnowPure’s patented electrodeionization (EDI) modules have proven to be an effective
component of a continuous deionization process. Electropure™ EDI is an economic
alternative to DI mixed resin bed systems and has several advantages. Though the
capital cost of an EDI system may be higher than a resin bed system, the operating cost
and other process advantages favor the use of Electropure™ EDI.

SNOWPURE, LLC, 2005-2018 VERSION 3.5 (XL+EXL) –FEBRUARY 2018 PAGE 15
Electropure™ EDI Advantages:
The ElectropureTM EDI series of modules is designed to be an economic component in
an OEM’s pure water systems.
Electropure™ modules are designed with the following advantages over other EDI
modules:
Unique Thin-Cell Technology.
Unique Thin-Concentrate Technology (“filled-cell” not required).
Unique Acidic Concentrate prevents scaling.
No resins in concentrate to foul (disadvantage of “filled-cell”)
Unique Non-scaling Electrode System.
Control over Electropure™ Electrode System.
Enable a Simple EDI SystemSM to be built.
No concentrate recirculation needed.
Lightweight and compact.
Waterproof electrical attachment on the opposite face.
Stack and bolts hidden internally.
Membrane is a proprietary membrane made by SnowPure.
The internal design has been improved over many years.
Chapter 2: Product Description and Guide

SNOWPURE, LLC, 2005-2018 VERSION 3.5 (XL+EXL) –FEBRUARY 2018 PAGE 16
Electropure™ EDI Product Guide:
Electropure™ EDI modules come in a variety of product lines, and a range of models
with flow sizes from 10 lph to 8 m3/h (2 gpm to 35 gpm). Each module has a
recommended product flow range. Modules can be arrayed in parallel to produce a
system of almost unlimited size (largest system to date is 400 m3/hr (1760 gpm). Our
high-quality modules deliver 10-18.2 MΩ.cm water depending on feed and operating
conditions.
Current Electropure™ EDI Product Lines:
XL-DER
Dialysis Endotoxin Removal
Since 2013
EXL
High Capacity
Since 2009
XL-R
Improved Torqueing
Since 2006
XL-RL
XL Laboratory Model*
Since 2007
XL-SR
Sanitary (TC) Fittings
Since 2006
XL-HTS w/SS covers
High Temperature Stable
Since 2004
Zapwater
Laboratory (10, 20 l/h)
Since 2005
*only available for XL-060, & XL-100; higher flows not included with this Product Line.
Legacy Electropure™ EDI Product Lines:
EPM/EPX (some repairs)
Status: Legacy
Since 1984 (until 2001)
XL (made to order)
Status: Legacy See XL-R
Since 1999 (until 2006)
XL-S (made to order)
Status: Legacy See XL-SR
Since 1999 (until 2006)
The table below shows the flow ranges for the Electropure™ EDI series of modules.
Product
Lines
(above)
Flow Range,
gpm
Flow Range,
m3/h
Operating
Voltage,
Vdc
Dimensions*
W x H x D
in
Dimensions*
W x H x D
cm
XL-060
0.18 to 0.35
40 to 80 lph
48
8.5 x 22 x 6
22 x 56 x 15
XL-100
¼ to ¾
80 to 150 lph
48
8.5 x 22 x 6.5
22 x 56 x 17
XL-200
½ to 1½
100 to 300 lph
100
8.5 x 22 x 7.5
22 x 56 x 19
XL-300
1½ to 4½
300 to 1000 lph
150
8.5 x 22 x 10
22 x 56 x 26
XL-400
2½ to 7
0.6 to 1.5
200
8.5 x 22 x 11.5
22 x 56 x 29
XL-500
6 to 10
1.3 to 2.3
300
8.5 x 22 x 14.5
22 x 56 x 37
EXL-510
11 to 18
2.5 to 4.0
300
12.4 x 24 x 11.5
31 x 60 x 29
EXL-610
15 to 24
3.5 to 5.5
400
12.4 x 24 x 14.9
31 x 60 x 38
EXL-710
22 to 35
5.0 to 8.0
500
12.4 x 24 x 17.8
31 x 60 x 45
EXL-550
9 to 20
2.0 to 4.5
250
12.4 x 24 x 11.3
31 x 60 x 28
EXL-650
13 to 26
3.0 to 6.0
300
12.4 x 24 x 14.6
31 x 60 x 37
EXL-750
22 to 35
5.0 to 8.0
400
12.4 x 24 x 17.5
31 x 60 x 44
EXL-850
26 to 44
6.0 to 10
500
12.4 x 24 x 20.3
31 x 60 x 51
* see dimensional drawing for exact dimensions in inches and cm
ModuleRestack
The XL and EXL series are designed to be disposable units. It is more environmentally
sound and economic to replace a module than to ship it roundtrip to the facility for a
“restack.”

SNOWPURE, LLC, 2005-2018 VERSION 3.5 (XL+EXL) –FEBRUARY 2018 PAGE 17
ApplicationsandPuritySpecifications
Ultrapure water is used for microelectronic and semiconductor production, for biomedical
and laboratory use, by pharmaceutical compounders, as pretreatment for distillation, for
boiler water makeup during power generation, in the food and beverage industry, and
anywhere in general industry where DI water is advantageous.
Below are typical industry ionic content specifications. These do not represent all of the
specifications for the water in these industries, only those relevant to EDI.
SemiconductorUltrapureWater:
Test
Units
Attainable
Acceptable
Alert
Critical
Resistivity,
25°C
MΩ.cm
18.2
18.2
18.0
17.9
Silica, dissolved
ppb
<0.1
<0.1
>0.5
>1.0
Boron
ppt
50
100
400
>500
(source: Balazs UPW Guideline, 2004, complete guide available at www.snowpure.com)
ElectronicGradeWater(ASTMD-19):
Type E-I
Type E-II
Type E-III
Type E-IV
Resistivity
(minimum, Megohm.cm)
18
(95% of time),
no less than 17
17.5
(90% of time),
no less than 16
12
0.5
SiO2(total maximum, µg/L)
5
10
50
1,000
Particle count (per ml)
1
3
10
100
Viable bacteria (max, ml)
1/1,000 m/L
10/1,000 m/L
10 m/L
100 m/L
TOC (max, µg/L)
25
50
300
1,000
Endotoxins (EU/ml)
0.03
0.25
n/a
n/a
Copper (max, µg/L)
1
1
2
500
Chloride (max, µg/L)
1
1
10
1,000
Nickel (max, mg/L)
0.1
1
2
500
Nitrate (max, mg/L)
1
1
5
500
Phosphate (max, mg/L)
1
1
5
500
Potassium (max, µg/L)
2
2
5
500
Sodium (max, µg/L)
0.5
1
5
1,000
Sulfate (max, mg/L)
1
1
5
500
Zinc (max, µg/L)
0.5
1
5
500
(source: Osmonics Pure Water Handbook, 2nd Edition, 1997)
(source: ASTM International: www.astm.org.)
Type E-I: This water will be classified as microelectronic water to be used in the
production of devices having widths below 1.0 µm. It’s intended that this be the water of
ultimate practical purity produced in large volumes and for the most critical uses.
Type E-II: This water may be classified as microelectronic water to be used in the
production of devices having dimensions below 5.0 µm. This water should be adequate
for producing most high-volume products, which have dimensions above 1.0 µm and
below 5.0 µm.
Type E-III: This grade of water may be classified as macroelectronic water to be used in
the production of devices having dimensions larger than 5.0 µm. This grade may be
used to produce larger components and some small components not affected by trace
amounts of impurities.

SNOWPURE, LLC, 2005-2018 VERSION 3.5 (XL+EXL) –FEBRUARY 2018 PAGE 18
Type IV: Electronics-Grade Water may be classified as electroplating water for non-
critical use and other general applications where the water is in constant contact with the
atmosphere because of tank storage.
PowerGeneration BoilerWater:
Test
Units
Typical
Resistivity,
25°C
MΩ.cm
10-13
Silica, total
ppb
5-20
(specifications depend on boiler pressure and use)
ASTM Reagent Water:
Water Type:
I
II
A
B
Resistivity, M.cm
18.2
1.0
TOC, ppb
10
50
Na, Cl, ppb
1
5
Silica, ppb
3
3
Heterotrophic Bacteria/100 mL
1
10
Endotoxin, EU/mL
<0.03
<0.25
USPPharmaceuticalWater:
Requirements vary depending on national laws (e.g., USP). USP Water for Injection
WFI requires the final treatment to be either distillation or a membrane barrier (e.g., RO)
in the US. USP Purified Water is water meeting USP quality requirements that has been
purified by distillation, ion exchange, electrodeionization, and other suitable processes.
USP is now aligned with other standards under WHO: The International Pharmacopoeia
(PhInt). EDI can be used as a preferred unit operation in either USP water system.
μ ˚
2

SNOWPURE, LLC, 2005-2018 VERSION 3.5 (XL+EXL) –FEBRUARY 2018 PAGE 19
StandardOperatingandTestingConditions
Electropure EDI module performance depends on a variety of operating conditions
including the OEM’s system design. For this reason, SnowPure tests its modules before
shipment under standard conditions; we base our quality program on manufacturing
process control and final testing. SnowPure does not guarantee specific performance in
the OEM’s system, as it has no control over the design or operating conditions.
SnowPure has confidence based on its module design and standard product testing that
excellent performance can be achieved.
The effects of various process variables on quality are discussed in subsequent
chapters.
Standard testing conditions: Electropure™ EDI modules are tested with water that is
treated with active carbon, softening, and fine filtration, followed by standard RO
operating at 65% recovery. RO permeate ranges from 2.0 to 5.0 ppm TDS, and includes
<5 ppm CO2and about 150 ppb silica. Temperature ranges from 18-35C. Applied
voltage and water flows are set at the published nominal for each module. Results of
this test are available for each module, and records are kept in our files for each module.
At the customer’s request, SnowPure will retest a field module under its standard
conditions to confirm quality.
GlossaryofTerms
Applied Voltage: the DC voltage across the anode and cathode of each module. The
voltage required depends primarily on the number of cells in the module.
Current: the DC current through each module. The current depends on the ion load
in the EDI feed, on the module recovery rate, and on the amount of water splitting.
Current is roughly independent of the number of cells.
Module Resistance: applied voltage divided by current, typically expressed in ohms.
Power Requirement: electrical power needed to supply the necessary current and
voltage. Typically expressed as kW/gpm.
Feed stream: feed to the purifying compartments for conversion to product. May
also include feed to the concentrate and electrode compartments.
Purified product stream: product from the purifying compartments.
Concentrate stream: flow in the ion-collecting concentrate compartments. Typically
10% of feed flow.
Electrode stream: flow to the anode and cathode compartments. Typically constant,
independent of the EDI model. See specifications.
Recovery: product stream flow divided by the total feed flow. Typically 99% if the
concentrate stream returns pre-RO. May be 90% if concentrate is sent to drain.
Chapter 3: Normal Operation, Conditions, and Specifications

SNOWPURE, LLC, 2005-2018 VERSION 3.5 (XL+EXL) –FEBRUARY 2018 PAGE 20
OperatingFeedWaterSpecifications
The following are requirements to operate within SnowPure’s limited warranty. Optimum
performance from Electropure™ EDI modules will result if values that are more stringent
are set as design goals.
Specification
Notes
Working
Range
Optimum
Performance
Feedwater Source
RO water, direct feed, or with intermediate
break tank plus filter
EDI Feed
Conductivity
Ionic load determines size of the working bed
and polishing bed within the EDI
1-20 μS/cm
1-6 μS/cm
Feedwater
Conductivity
Equivalent**
FCE = Conductivity + 2.79*CO2+1.94*SiO2
see note below**
< 33 μS/cm
< 9 μS/cm
pH
Low pH feedwater typically indicates the
presence of CO2which will decrease quality.
5.0-9.5
7.0-7.5
Total CO2
Combined CO2and HCO3-
<5 mg/l as CO2
<2 mg/l
Temperature
5°C to 35°C
20 to 30°C
Hardness
Ca+2 and Mg+2 as CaCO3
<1.0 ppm at
90% recovery
Organics
TOC
< 0.5 ppm
Not Detectable
Metals
Fe, Mn, transition metals
< 10 ppb
Not Detectable
Silica, SiO2
Typically dissolved, reactive
< 0.5 ppm
< 0.2 ppm
Oxidizers
Cl2and O3, typically
Not
Detectable
Not Detectable
Particles
Recommended direct feed particle-free RO
permeate, or 1 μm pre-filtration of feed from
intermediate tank
Inlet Pressure
Depends on flow and temperature
5 bar (75 psi)
max
2-3 bar typical
Outlet Pressure
Concentrate and Electrode outlet pressures to
be lower than the Product outlet pressure
** FCE example:
FCE = Conductivity + 2.79*(CO2) + 1.94*(SiO2), so if conductivity=5.0 μS/cm, CO2=3.5 mg/l,
SiO2=0.5 mg/l, then FCE = 5.0 + 2.79*(3.5) + 1.94*(0.5) = 15.7 μS/cm.
This manual suits for next models
14
Table of contents
Popular Water Filtration System manuals by other brands
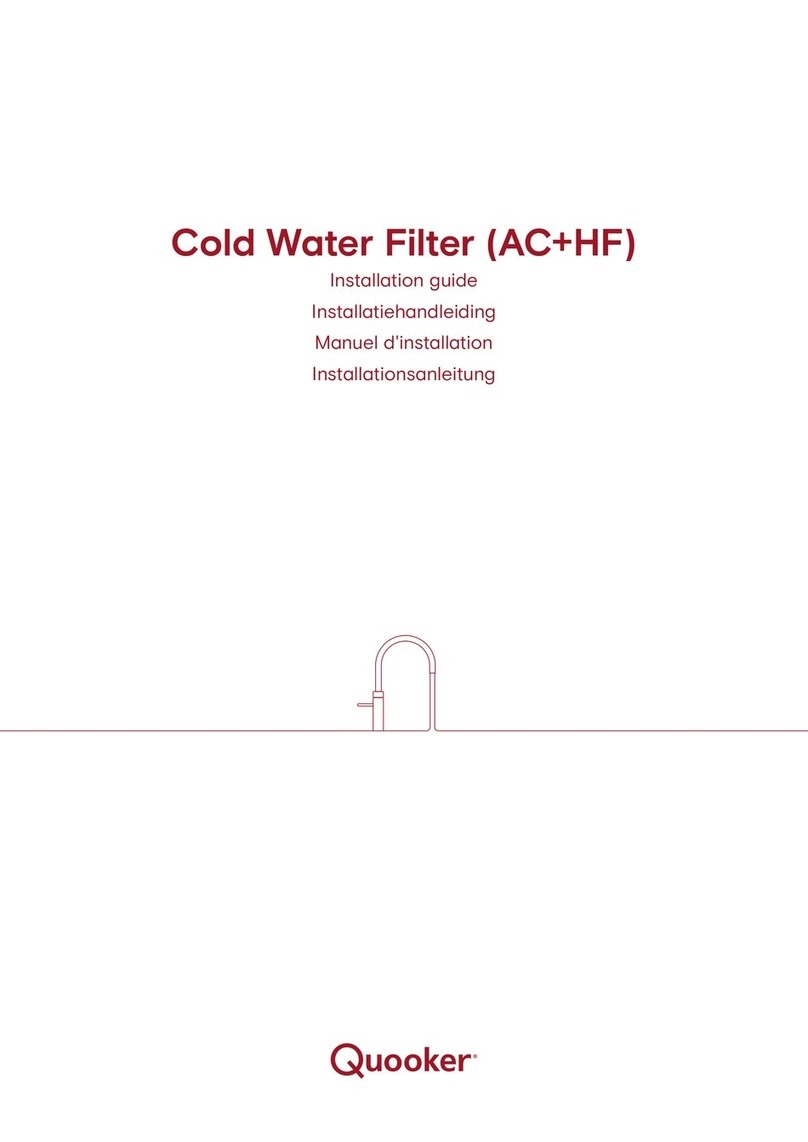
Quooker
Quooker AC+HF installation guide
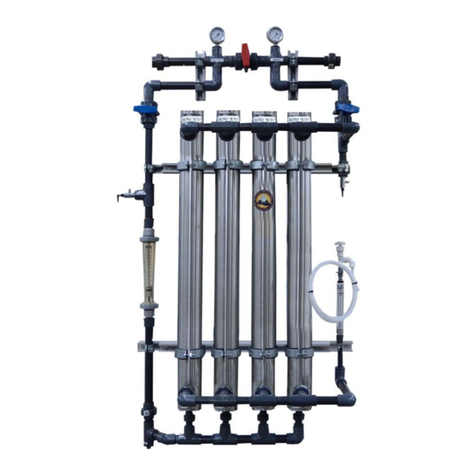
Better Water
Better Water UF17000 Operator's manual
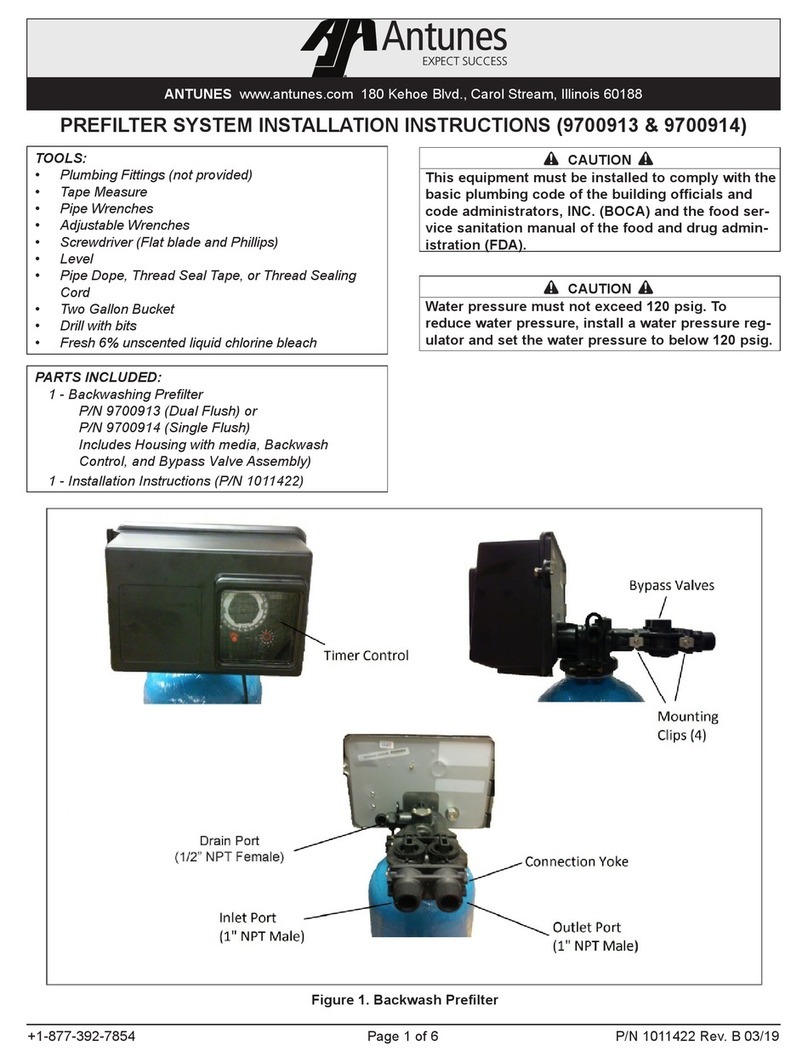
Antunes
Antunes 9700913 installation instructions
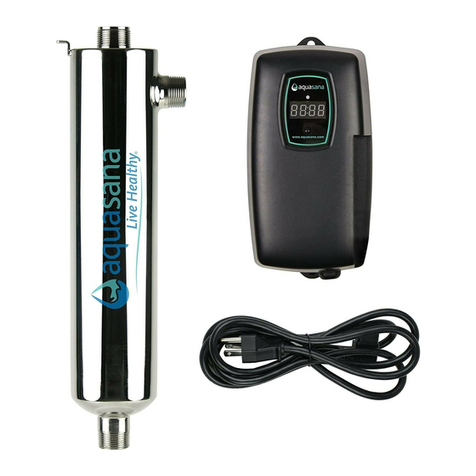
Aquasana
Aquasana AQ-UV-C Series Operation & installation instructions
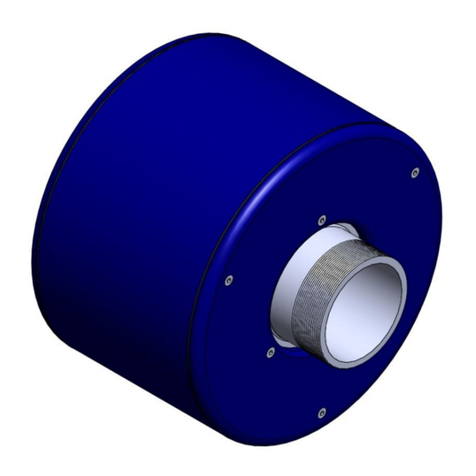
BWT
BWT Liff Powermag PM100S Installation & operating instruction manual
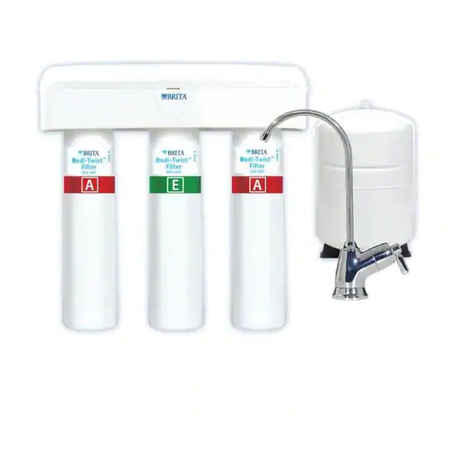
Brita
Brita Redi-Twist USS-335 installation instructions
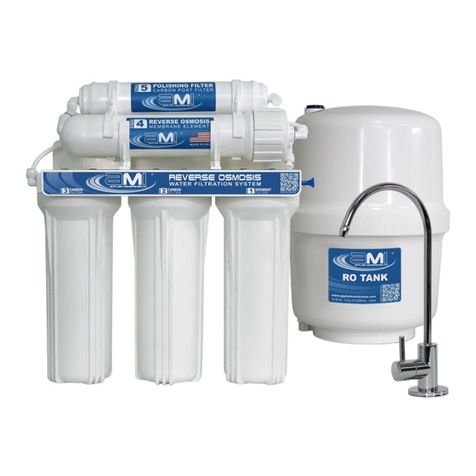
AMI
AMI AAA-RO200A MANUAL FOR INSTALLATION, OPERATION AND MAINTENANCE
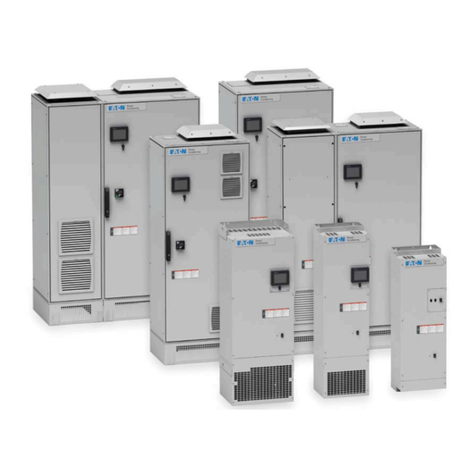
Eaton
Eaton HCU2 installation manual
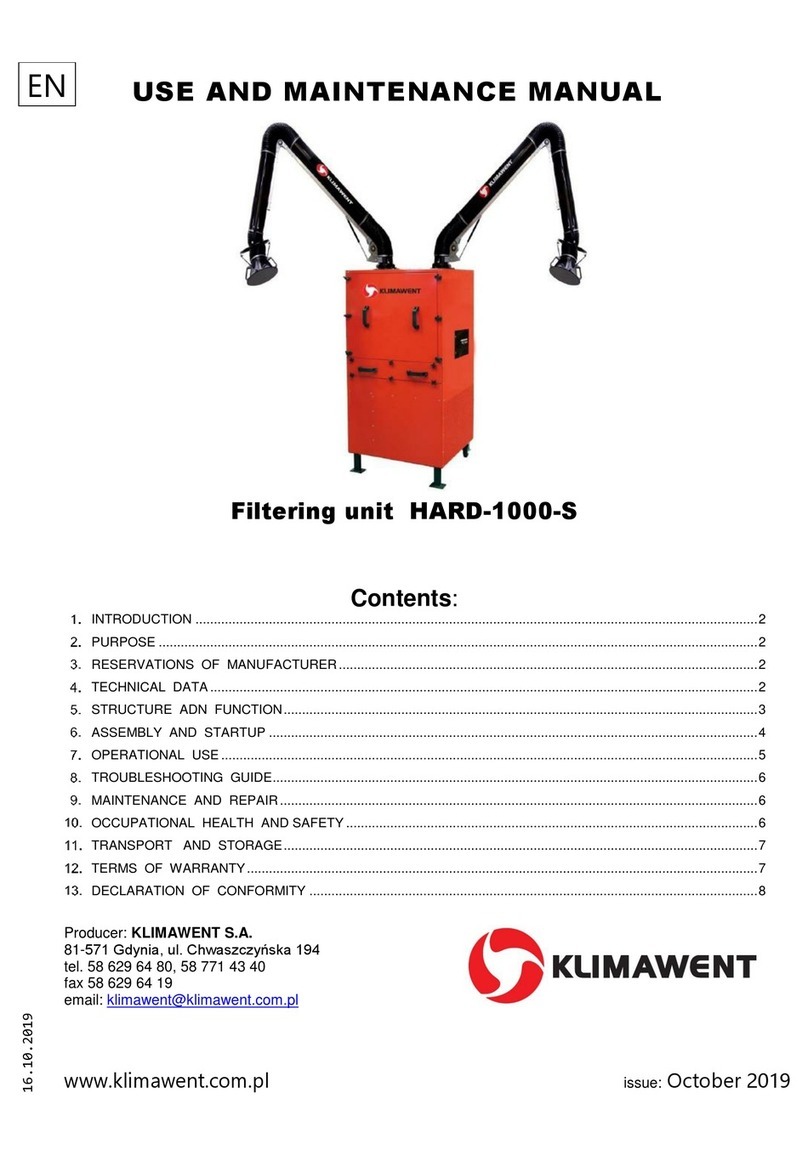
Klimawent
Klimawent HARD-1000-S Use and maintenance manual
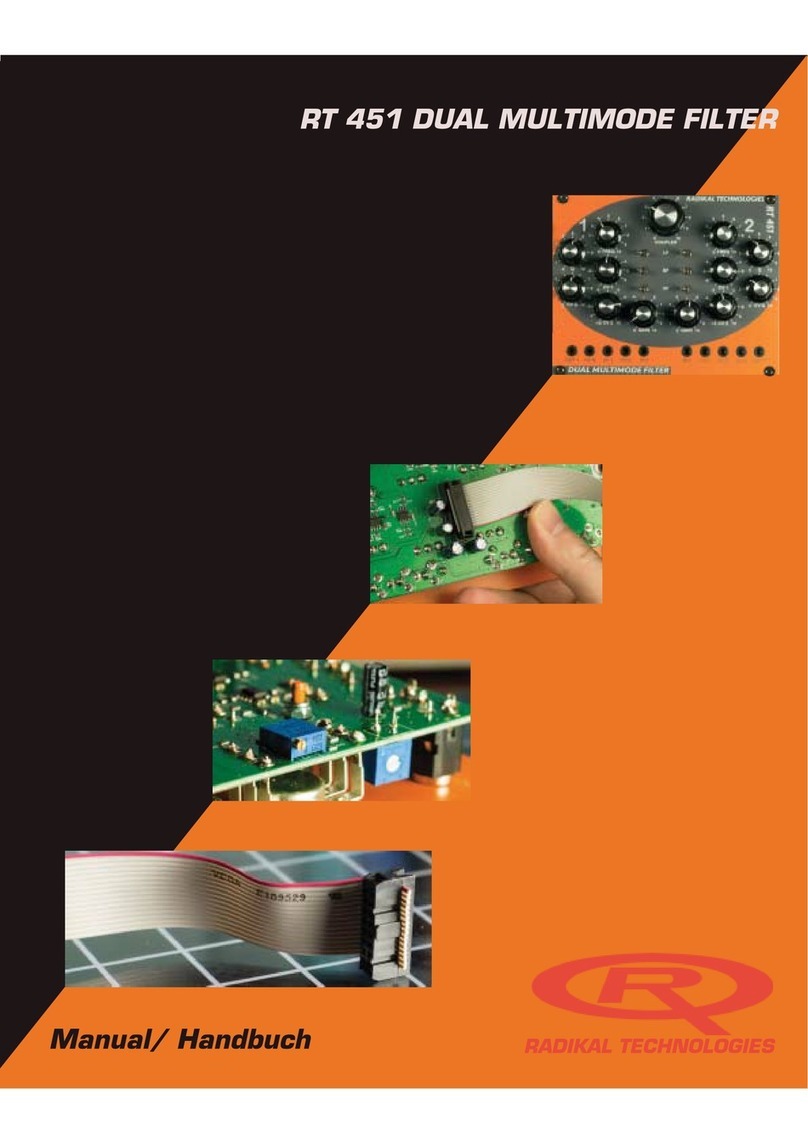
RADIKAL TECHNOLOGIES
RADIKAL TECHNOLOGIES RT 451 manual

Water Maze
Water Maze ALPHA-1500 Operator's manual

WaterClinic
WaterClinic LOTUS-72 user manual